
Учебник Спецсуда
.pdfсистемы, судовые системы и др.) и типа изоляции. Последний фактор является определяющим при разработке технологии монтажа.
Перед монтажом любого типа изоляции на изолируемых поверхностях должны быть установлены и приварены доизоляционные детали, вырезаны отверстия для прохода труб и кабеля, очищены шпигаты в наборе для стока конденсатных вод, изолируемые поверхности должны быть испытаны на герметичность и непроницаемость (если это предусмотрено конструкторской документацией) и надежно защищены от коррозии (загрунтованы и окрашены) по схемам, рассчитанным на длительную эксплуатацию. До приклейки изоляции ЛКП должно быть выдержано в соответствии с нормативной документацией. При выполне- НИИ изоляционных работ в зимнее время изолируемые поверхности посредственно перед установкой изоляции должны быть очищены И протерты ЧИСТОЙ тряпкой ИЛИ ветошью, смоченной смесью ЭТИлового спирта и ацетона в соотношении 1:1.
В зависимости от вида применяемой изоляции технология монтажа выполняется следующим образом.
Плиточные изоляционные материалы типов П-1, П-2. Раскрой пластин и заготовка профильных деталей изоляции набора выполняют в цехе или на заказе на механическом оборудовании исходя из габарита плит, размеров профиля и изолируемой поверхности. При изоляции поверхностей, имеющих кривизну, плиты разрезают на полосы шириной 100-500 мм (в зависимости от радиуса кривизны). Подгонка и вырезка в элементах изоляции должны быть минимальными, необходимо стремиться, чтобы доизоляционные детали насыщения попадали в швы изоляции.
Подгонка и приклейка пластин между набором. Подгонка и приклейка деталей изоляции набора. На период схватывания клея плиточные материалы там, где это возможно, плотно и равномерно прижимаются к изолируемой поверхности специальными прижимами или деревянными распорками и клиньями. Время нахождения изоляции под прижатием зависит от марки клея, указываемого в чертеже, плотности изоляции и температуры окружающей среды и колеблется от 1 до 10 дней. На криволинейных поверхностях изоляция из полос приклеивается без раскрепления клеем повышенной вязкости.
Клей (НДС, КС-Ф и др.) в зависимости от консистенции наносится шпателем или кистью, толщина наносимого слоя не более 2 мм, за исключением клеев, толщина которых оговаривается особо.
При приклеивании материалов с относительно большой плотностью (пеностекло, базальтовая плита), а также на поверхностях с большим насыщением клей наносится сплошным ровным слоем на обе склеиваемые поверхности, а для материалов с невысокой плотностью (ФС-7-2 и др.) клей наносится только на изолируемый материал сплошным слоем или частично (60% площади пластины). При всех способах приклеивания материалов их торцы должны быть промазаны клеем на всю толщину.
При многослойной изоляции каждый слой приклеивается отдельно, а клей наносится на одну из склеиваемых поверхностей сплошным слоем или частично (50-60%). Пластины каждого последующего слоя должны перекрывать стыки предыдущего слоя не менее чем на 100 мм.
Толщина изоляции должна быть одинаковой по всей изолируемой поверхности, допуск на толщину ± 5 мм.
Заделка стыков и мест прохода деталей насыщения. После приклейки изоляции и схватывания клея производится шпатлевка или оклейка полосками ткани шириной 50 мм всех швов и мест прохода доизоляциониого насыщения. Для этой цели применяют шпатлевку «Целалит», а также мастики на клее с измельченным приклеиваемым изоляционным материалом или мастику «ТИММ-1».
Нанесение гидрозащитного покрытия на поверхность изоляции.
Поверхность плиточной изоляции должна иметь гидрозащитное покрытие для предотвращения увлажнения изоляционного материала от проникновения внутрь его паров влаги из воздуха помещения. Операция по нанесению гидрозащитного покрытия выполняется в несколько этапов:
выравнивание плит под приклейку ткани шпатлевкой «Целалит»;
приклейка ткани и окраска.
Проведение каждого последующего этапа работ следует производить после высыхания предыдущего слоя шпатлевки, клея с тканью и каждого слоя JIKM.
Волокнистые изоляционные материалы типа В-2.
Монтаж волокнистых материалов, играющих роль теплозвукоизолирующих, выполняют на корпусных конструкциях ПЛ, как правило, путем приклеивания или установки на шпильках предварительно изготовленных в цехе из матов пакетов необходимой толщины с защитной оболочкой из гидрозащитной пленки. Размеры пакетов соответствуют по ширине шпации, а по длине - не более 1 м. Кромки пакетов склеиваются ' клеем или свариваются.
Волокнистые материалы в процессе монтажа необходимо уплотнять: материалы с плотностью 25 кг/м3 и менее устанавливают с уплотнением в 1,5 раза; с плотностью от 25 до 80 кг/м3 - с уплотнением в 1,1 раза; а материалы плотностью 80 кг/м3 и более не уплотняют, уплотнение производят вручную. Для установки изоляции с защитным уплотнением заготовки волокнистых материалов (пакеты) делают с повышением по толщине по отношению к предусмотренной чертежом. Торцы вырезов изоляции под проход деталей доизоляционного насыщения обшиваются стеклотканью или склеиваются клеем. Установленная изоляция зашивается перфорированными листами из АМг, которые окрашиваются под цвет помещения.
Наибольшее применение волокнистые материалы находят при тепловой изоляции трубопроводов, оборудования, арматуры, систем и т.д.
Процесс монтажа волокнистыми материалами состоит из следующих
технологических операций:
подготовка поверхности под изоляцию;
раскрой и пошив матов;
изоляция горячих (холодных) поверхностей.
Подготовка поверхности под изоляцию выполняется с целью удаления с нее пыли, грязи, масла, ржавчины. Пыль удаляется волосяной щеткой, грязь - сухой ветошью, жировые пятна и масло - ветошью смоченной раствором синтанола или уайт-спиритом. Ржавчина удаляется любым способом, применяемым на заводе.
Изоляция труб длиной до 0,3 м выполняется в цехе. Перед монтажом изоляции трубы покрывают противокоррозионным покрытием (лакокрасочное или гальваническое). Трубы диаметром свыше 197 мм изолируют матами из волокнистых материалов, а меньшего диаметра - полосами из волокнистых материалов шириной 50-250 мм (размер полосы зависит от диаметра трубы).
Последовательность изготовления матов: на раскроенную по габаритам трубы кремнеземную ткань (два слоя) с припуском по каждой стороне по 20 мм для обшивки торцов мата насыпают или укладывают равномерным слоем наполнитель из волокнистых материалов из расчета заданной толщины и объемной массы с учетом уплотнения и накрывают вторым полотнищем. Затем мат простегивают в шахматном порядке кремнеземной нитью, концы ткани загибают внутрь от 15 до 20 мм и прошивают. Затем мат утрамбовывают вручную или грузом и простегивают в шахматном порядке кремнеземной нитью, шаг простежки зависит от типа наполнителя и колеблется от 60 до 100 мм. Допуск на толщину мата - 5, + 8 мм.
По краям матов для съемной изоляции пришиваются крючки для их шнуровки при монтаже медной или латунной проволокой толщиной 1,5- 2 мм. Во избежание провисания и проворачивания матов при монтаже поверх них устанавливаются бандажи из мягкой проволоки диаметром 1,0-2,0 мм с шагом 300-400 мм.
При монтаже многослойной изоляции маты устанавливаются так, чтобы последующие слои перекрывали все продольные и поперечные швы предыдущих. На рис. 10.1 представлены узлы многослойной изоляции матами из волокнистых материалов.
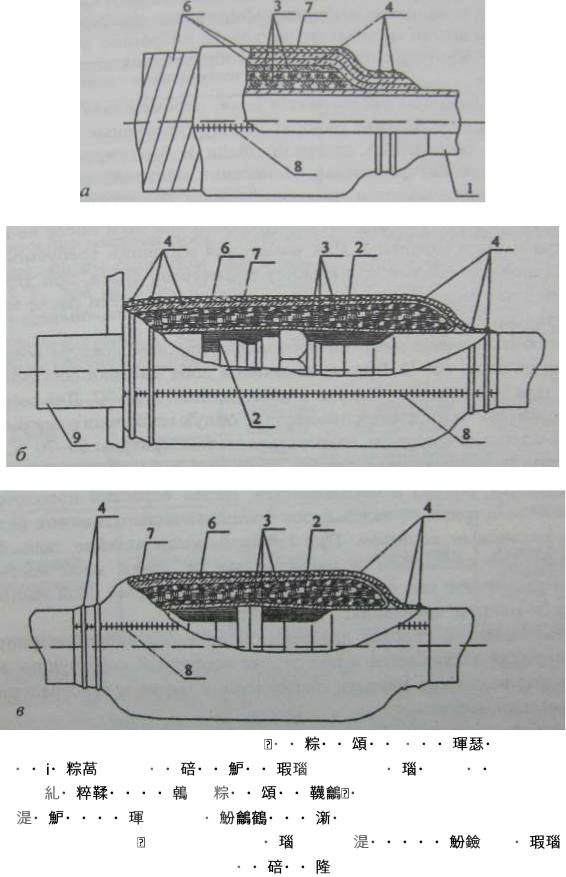
. 10.1. |
|
|
|
154 - |
; 154 - |
154; |
154 - |
; 1 - 154; 2 - |
|
|
|
|
154; 3 - к- |
|
154; 4 - |
|
|
{ — 2 |
); 5 - 88 ; 6 - |
|
|
|
|
|
; 7 - |
154; 8 |
- |
; 9 - |
Мастичные изоляционные материалы. Мастичные изоляционные материалы на ПЛ применяют в ка теплоизоляционных И вибродемпфируюших. В качестве теплоизоляции они предназначены для изоляции труднодоступных мест и насыщения прочного корпуса, в качестве вибродемпфирующих (вибропоглощающих) материалов мастики ослабляют звуковую вибрацию от работающих механизмов и оборудования путем преобразования колебательной энергии в тепловую.
Мастичную теплоизоляцию готовят в цехе, перемешивая компоненты в растворомешалке. Мастику наносят на загрунтованные металлические поверхности, очищенные от грязи, пыли и обезжиренные уайт-спиритом или раствором синтанола. Нанесение мастики производится шпателем. До укладки мастики на изолируемую поверхность наносят клей или поливинилацетатную эмульсию, толщина одного слоя мастики составляет до 35 мм, трещины на поверхности мастики после ее высыхания должны быть заделаны. Для нанесения изоляции требуемой толщины последовательно наносят нужное количество слоев, при этом последующий слой изоляции наносят примерно через сутки после затвердевания предыдущего.
Работы по нанесению мастики производят при температуре воздуха в помещении не ниже +5 °С. Время высыхания слоя мастики составляет от 1 до 4 сут при температуре воздуха в помещении 1Q-20 °С. Для сокращения продолжительности сушки производят обдув мастичного покрытия в течение 24 ч теплым воздухом, разогретым до температуры
60-70 °С.
Поверхность готового мастичного покрытия либо окрашивается, либо оклеивается тканью и окрашивается. Перед окраской поверхность тщательно осматривают, заделывают трещины и выравнивают аналогичным мастичным составом. При необходимости оклейки тканью ее предварительно смачивают и накладывают на сырой слой мастики, ткань разглаживают так, чтобы через нее продавливался слой мастики. Окраску по мастике производят через 3—4 сут.
Технологический процесс нанесения мастичного вибродемпфирующего покрытия заключается в подготовке корпусной конструкции или изделия под нанесение мастики определенной марки и непосредственном нанесении мастики.
Все работы, связанные с нанесением мастичных материалов, должны производиться после проведения сборочно-сварочных работ. Перед нанесением мастики поверхность протирается от загрязнений и пыли и при необходимости обезжиривается водным раствором синтанола. Механическим способом или вручную наждачной шкуркой средней зернистости очищают поверхность от ржавчины и непрочно держащегося межоперационного грунта, образовавшуюся на поверхности пыль убирают пылесосом, и поверхность обезжиривают ветошью, смоченной в уайт-спирите. Подготовленная поверхность перед нанесением мастики окрашивается в соответствии с рекомендациями табл. 10.1.
|
|
Таблица 10.1 |
|
Материал конструкции |
Схема грунтования |
Количество |
|
|
|
слоев |
|
|
|
|
|
Сталь |
Гр. ФЛ-03К |
2 |
|
|
|
|
|
|
Шп. ЭП-0010 |
2 |
|
Алюминиевые сплавы |
Гр. ВЛ-02 |
1 |
|
Медь и ее сплавы |
Гр. ВЛ-02 |
1 |
|
Титановые сплавы, нержавеющая |
Не грунтуются |
сталь, стеклопластик |
|
|
|
Нанесение мастики производят послойно вручную шпателем или механизированным способом при температуре воздуха и конструкции не ниже 5 °С, при наличии приточно-вытяжной вентиляции, обеспечивающей предельнодопустимые концентрации вредных веществ и удаление испаряющейся воды. В качестве примера в табл. 10.2 представлена схема нанесения мастики АДЕМ.
|
|
|
|
Таблица 10.2 |
|
|
Способ |
Толщина |
Выдержка до нанесения |
|
|
|
слоев |
|
|||
Слой |
нанесен |
сырого |
|
||
Естественная |
Обдув воздухом |
|
|||
|
ия |
слоя |
|
||
|
сушка |
с f - +30 °С |
|
||
|
|
|
|
||
1-й грунтовоч- |
Кисть |
— |
От 0,5 до 2 ч |
— |
|
ный |
|
|
|
|
|
|
|
|
|
|
|
2-й грунтовоч- |
Шпатель |
Не более 2 |
Не менее 20 ч |
Не менее 7 ч |
|
ный |
|
мм |
|
|
|
1-й основной и |
Шпатель |
Не более 4 |
1 слой в сутки |
2 слоя в |
|
последующие |
|
мм |
|
сутки не |
|
|
|
|
|
ранее чем |
|
|
|
|
|
через 6-7 ч |
|
|
|
|
|
|
|
Разбавление мастики для придания ей малярных свойств при необходимости производится водой. При нанесении мастики учитывают ее усадку по толщине, которая составляет 15-25%. Допустимая толщина гухого слоя мастики, нанесенной за одни сутки, - не более 6 мм, что достигается нанесением двух слоев мастики толщиной сырого слоя не более 4 мм.
Готовое мастичное покрытие, нанесенное толщиной в соответствии с требованием конструкторской документации, в дальнейшем может бытьокрашено штатными лакокрасочными покрытиями и на него могут наклеиваться с помощью штатных клеев изоляция, линолеум, керамическая плитка. Подготовка поверхности под нанесение указанных покрытий заключается в обработке наждачной шкуркой поверхности мастики, уборке пыли пылесосом и в обезжиривании раствором синтанола.
10.3.Монтаж специальных покрытий
10.3.1.Назначение, классификация и конструкция
специальных покрытий
Специальные покрытия применяются для акустической защиты и повышения скрытности ПЛ, по своему функциональному назначению они делятся на три типа:
противогидролокационные;
звукоизолирующие;
комбинированные (совмещают обе перечисленные выше функции).

Противогидролокационные покрытия предназначены для поглощения акустических сигналов, которые могут излучаться поисковыми станциями кораблей и ПЛ, минно-торпедным вооружением, стационарными гидроакустическими станциями, т.е. эти покрытия обеспечивают поглощение сигналов с несущими частотами из различных диапазонов. Они устанавливаются на наружной поверхности корпуса.
Звукоизолирующие гидроакустические покрытия (ГАП) предназначены для снижения уровня шума, передающегося от работающих механизмов и оборудования через корпус ПЛ в водную среду, и являются последней преградой на пути распространения собственных внутренних шумов ПЛ.
На рис. 10.2 показан принцип действия противогидролокационного покрытия, а на рис. 10.3 - схема образования и передачи на корпус ПЛ внутренних шумов.
Впервые наружное акустическое покрытие было применено в Германии во время Второй мировой войны для снижения гидролокационной заметности ПЛ (покрытие «Альберих»). В последующие годы интерес к этой проблеме возрастал, и в пятидесятые годы прошлого столетия было также установлено, что наружные покрытия еще и эффективно снижают шум, излучаемый в воду корпусными конструкциями ПЛ при их возбуждении работающими механизмами, и уменьшают шум, обусловленный воздействием гребного винта на корпус.
Рис. 10.2. Схема действия противогидролокационного покрытия

Рис. 10.3. Принцип образования и передачи на корпус ПЛ внутренних шумов
Конструктивно ГАП представляют собой различные наборные резиновые покрытия, состоящие из нескольких слоев монолитной, перфорированной или рупорной резины и их различных комбинаций.
Массогабаритные характеристики ГАП могут меняться в весьма широких пределах, и при достаточно полной облицовке корпуса ПЛ общий вес покрытий может составлять многие тонны и существенно влиять на ее водоизмещение.
При создании ГАП любого назначения рассматриваются две основные задачи:
поглощение звука внутри покрытия;передача звука без отражения из внешней среды в покрытие и
обеспечение требуемой звукоизоляции путем максимального отражения акустической энергии на границе корпус-внешняя среда и обратно в корпусные металлоконструкции.
Эти задачи решаются путем создания воздушных полостей в резиновом массиве покрытия. В зависимости от конструкции покрытия делятся на резонансные и нерезонансные. Резонансные покрытия обычно имеют цилиндрические отверстия разных размеров в каждом слое резины, а нерезонансные - один толстый слой с воздушными полостями обычно рупорной формы.
На рис. 10.4 схематично представлены покрытия резонансного и нерезонансного типов.
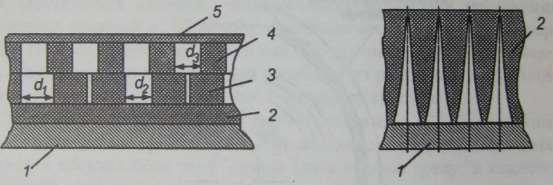
Рис. 10.4. Схема акустических покрытий: а - резонансное; б - нерезонансное; 1 - корпусная конструкция; 2-5 - листы резины; d| и<1з - диаметры отверстия
При погружении ПЛ воздушные полости могут сжиматься, меняя свой объем, что изменяет их акустические свойства. Поэтому в покрытиях применяют армирующие слои из жестких материалов. По типу армирующих элементов ГАП делятся на неармированные, с непрерывным и дискретным армированием. В качестве армирующих материалов применяются стеклопластик, специальные катушки из легкого металла и др.
Схемы расположения и конструкции покрытий, устанавливаемых на ПЛ, определяются проектной документацией.
10.3.2. Технология монтажа специальных покрытий
Спецпокрытия монтируют на корпусные конструкции ПЛ клеевым, механическим или клеемеханическим способами. Конструктивно узлы крепления пластин назначаются проектантом. Как правило, крепление пластин на конструкциях наружного корпуса осуществляется клеевым способом, а в междубортном пространстве - механическим и клеемеханическим способами. На наружном корпусе установка спецпокрытий производится в два этапа: предварительно (на килевых, бортовых и секциях надстройки и ограждениях рубки после их сборки в цехе) и окончательно на стапеле после заварки монтажных стыков конструкций. На прочных конструкциях установка покрытий производится после их гидравлических испытаний.
При клеевом способе крепление спецпокрытий осуществляется на клеях марок 88С, 51-К-10ВМ или на эпоксидной шпатлевке ЭП-0010; при механическом способе - с помощью привариваемых к корпусу металлических шпилек или бонок.
Установка пластин клеевым способом производится в такой технологической последовательности:
разметка и приварка на корпусные конструкции в соответствии с разрабатываемыми схемами технологических бонок, предназначенных для закрепления прижимной оснастки;
очистка и консервация корпусных конструкций;подготовка пластин покрытия и материалов для крепления пластин;
подготовка поверхности корпусных конструкций в районе установки покрытия;
установка пластин на корпусные конструкции, контроль качества монтажа и герметизация стыков покрытия.
Установку и приварку технологических бонок выполняют при предварительной сборке конструкций с учетом обеспечения зазоров между пластинами от 8 до 12 мм. В случае попадания бонки на сварной шов она сдвигается в ту или другую сторону на расстояние 30-50 мм от заданного схемой положения. Размер технологических бонок и марка материала назначаются рабочими чертежами на установку покрытия. На период хранения конструкций до установки покрытия внутреннюю резьбу бонок защищают технологическими болтами.
Очистка и консервация корпусных конструкций производится после приварки на их поверхности насыщения, технологических бонок, а также испытания сварных швов на «мел-керосин» на непроницаемость для конструкций наружного корпуса. Поверхность, подлежащую облицовке, очищают от ржавчины и межоперационного грунта дробеструйным способом, создавая на ней шероховатую поверхность со средней высотой неровностей 50-80 мк и степенью очистки Sa 2V2. Это достигается путем обработки поверхности металла чугунной колотой дробью ДЧК с помощью дробеструйных аппаратов «Каскад» или «АД-160М». Размеры частиц дроби ДЧК зависят от марки материала обрабатываемой поверхности и колеблются от 0,8 до 1,5 мм. При очистке резьбовые отверстия и поверхности насыщения должны быть защищены от попадания дроби (резиной или брезентом).
Втруднодоступных местах, при невозможности использования дробеструйных аппаратов, допускается очистка металлическими щетками, кругами «Дюрекса» или вручную шлифовальной шкуркой зернистостью 50-80 ед. Подготовленную таким образом поверхность очищают от остатков дроби и пыли пылесосом или щетками и обезжиривают бензином.
Втечение 24 ч на очищенную поверхность должно быть установлено покрытие. Если это невозможно, то поверхность консервируется слоем эпоксидной шпатлевки ЭП-0010 грунтовочного состава, в том числе консервируют и бонки, избегая попадания шпатлевки на резьбу внутри бонок. Консервирующий слой необходимо просушить не менее 24 ч. При наличии на поверхности сварных швов высотой усиления до 5 мм и в районах разной толщины металла производят выравнивание поверхности эпоксидной шпатлевкой ЭП-0010 с введением в качестве наполнителя хризотилового асбеста. Шпатлевочный слой просушивается в течение 24 ч. Срок хранения законсервированных поверхностей не ограничен при условии сохранности консервирующего слоя от механических повреждений.