
Учебник Спецсуда
.pdf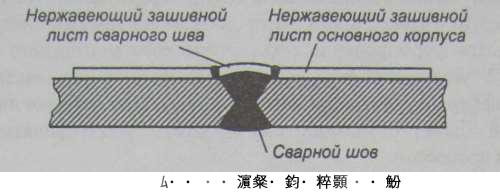
слой свинца на поперечных переборках, ограничивающих реакторный отсек; съемные блоки биологической защиты, расположенные сверху ППУ; цистерны, заполненные водой и расположенные снаружи ОК. Биологическая защита представляет собой композитное сочетание легких и тяжелых элементов из бетона, свинца, полиэтилена и соединений бора. Реакторный отсек с замыкающими его поперечными переборками входит в отдельный блок корпуса ПЛ. Для обеспечения погрузки агрегата ППУ в отсек после проведения гидравлических испытаний блока предусматривается его разделение на два блок-модуля по технологическому резу.
Монтаж агрегата ППУ выполняется в три этапа. На первом этапе осуществляются предварительные работы по заливке свинца на поперечные переборки, испытаниям всех замкнутых объемов на непроницаемость и герметичность. На втором этапе устанавливаются свинцовая изоляция по контуру поперечных переборок; производятся монтаж зашивных листов из нержавеющей стали по основному корпусу в районе размещения БЖВЗ (рис.8.2), установка бортовых направляющих для погрузки агрегата ППУ и предварительная стыковка блок-модулей ПЛ с обработкой монтажных кромок в чистый размер. Третий этап предусматривает непосредственный монтаж агрегата ППУ. Стенд с агрегатом ППУ, установленный на транспортные тележки, соединенные единой гидравлической системой, перемещается к открытому торцу блокмодуля. Стенд и блок-модуль выравниваются по ДП, крену и дифференту и соединяются между собой прочными связями. Стыкуются транспортные пути, установленные внутри блок-модуля и под агрегатом ППУ. При помощи гидравлических толкателей агрегат ППУ постепенно перемещается на штатное место внутри отсека и раскрепляется. Стенд отсоединяется от блок-модуля и откатывается от него на место штатного хранения. Второй блок-модуль подается к первому (рис. 8.3) и выполня-
ется сборка и сварка технологического стыка. После этого приступают к выравниванию агрегата ППУ по ДП, крену, дифференту, длине и высоте. Затем причерчиваются и обрезаются припуски по вертикальному килю, поперечным бракетам и крыше БЖВЗ. Агрегат ППУ устанавливается на штатное место и приваривается к опорным конструкциям. Затем выполняются все предусмотренные технологическим процессом испытания.
.8.2.
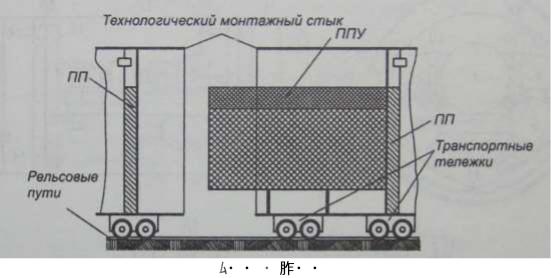
.8.3. |
|
8.3.Монтаж агрегата паротурбинной установки
Всостав паротурбинной установки (ПТУ) входит главная турбина, редуктор, главный упорный подшипник, турбогенераторы, различные насосы и компенсаторы (рис.8.4). Все оборудование крепится на каркасе объемной конструкции с помощью амортизаторов. Агрегат ПТУ формируется на специальном стенде, с помощью которого его впоследствии перемещают к месту погрузки и монтажа в блок-модуль. На стенде формируется каркас объемной конструкции, фундаменты и другие несущие конструкции, в состав которых включается часть цистерн. Перед началом монтажа ПТУ производится обработка опорных поверхностей фундаментов. Затем после предмонтажной подготовки выполняется последовательный монтаж оборудования на стенде и устанавливаются специальные устройства для перемещения агрегата ПТУ по транспортным путям стенда в блок-модуль. Стенд вместе с агрегатом ПТУ перемещается к месту монтажа и выравнивается гидравлическими домкратами тележек по ДП, крену, дифференту и высоте. Транспортные пути стенда стыкуются с путями блок-модуля, а сам стенд раскрепляется
кего корпусу. Агрегат ПТУ при помощи гидравлических толкателей последовательно перемещается в блок-модуль, поднимается над транспортными путями и раскрепляется. Стенд отводится на штатное место в цехе, а вместо него подводится второй блок-модуль турбинного отсека и производится формирование технологического монтажного стыка. Агрегат ПТУ устанавливается на штатное место, выравнивается по ДП, крену, дифференту и высоте. Затем выполняется пробивка линии вала и остальной объем работ по монтажу в соответствии с принятым технологическим процессом.
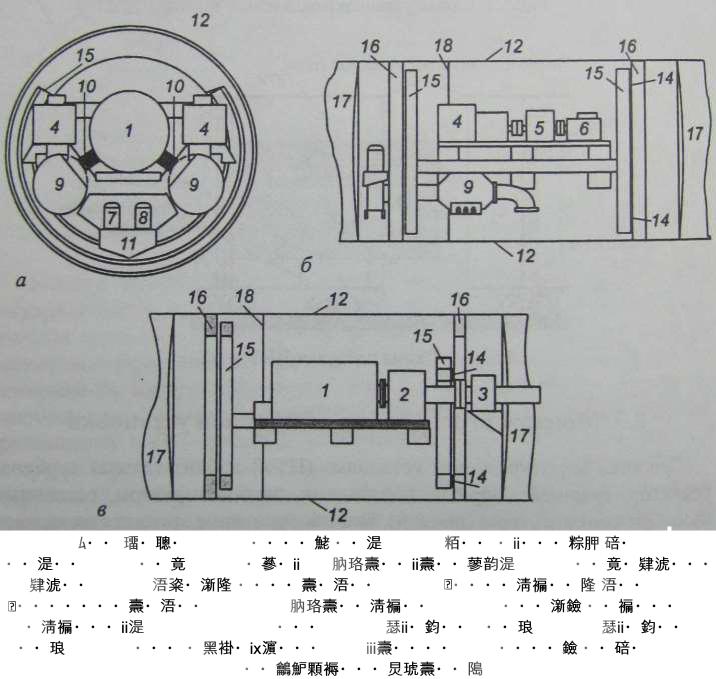
.8.4. |
: - |
|
123; - |
|
123; 123 - |
|
|
|
; 1 - |
123; 2 - |
; 3 - |
|
123; 4 - |
|
|
5 - |
123; 6 - |
|
( -1)7- |
|
( -5);8 |
||
|
|
( -3); 9 - |
|
123; 10 - |
|
; 11 |
- |
|
|
123; 12 - |
; 13 - |
I |
123; 14 - |
II |
|
|
123; 15 - |
|
; 16 - |
; 17 - |
|
123; 18 - |
|
8.4. Технология монтажа блок-вагонов
Для монтажа зональных блоков применяются специальные блоквагоны (рис.8.5). В качестве несущих конструкций таких зональных блоков используются штатные настилы, платформы, переборки, выгородки и каркасы, расположенные в соответствующем отсеке ПЛ. В собранном виде такие конструкции часто называются «этажерка» (рис.8.6).

.8.5. |
- : 1 - |
- |
|
; 2 - |
124; 3 - |
|
|
|
; 4 - |
124; 5 - |
|
|
|
124; 6 - |
124; |
|
|
7 - |
|
.8.6. |
и |
Несущие конструкции этажерки изготавливают на специальных сбо. рочных стендах, позволяющих обеспечить установленные конструктив, ные допуски для беспригоночного их монтажа в блок-вагон. Монтажный стенд, фиксирующий этажерку в положении, аналогичном ее положению внутри корпуса ПЛ, устанавливают на единой раме оборудованной транспортными тележками.
При формировании блок-вагона монтажный стенд выставляется и проверяется по базовым плоскостям. На него устанавливается и закрепляется сначала нижняя несущая конструкция, к которой раскрепляются продольные и поперечные несущие конструкции первого яруса. После этого последовательно формируются конструкции вышерасположенных ярусов и производится сварка сначала вертикальных швов, затем гори-
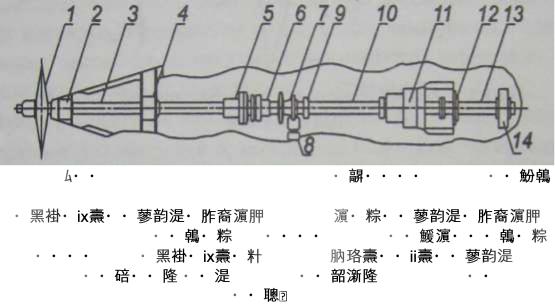
зонтальных в направлении от середины к краям. Наносятся базовые и контрольные линии и выполняется предмонтажная подготовка, обеспечивающая погрузку оборудования. Через открытые торцы «этажерки» производится погрузка различных сборочно-монтажных единиц и их предварительный монтаж. Блок-вагон перемещается к открытому торцу блок-модуля, выравнивается по базовым плоскостям и раскрепляется. Затем с помощью тяговых систем зональный блок по роликовым опорным направляющим перемещается в отсек на штатное место, центруется и раскрепляется,
8.5. Особенности монтажа валопроводов
Валопровод ПЛ представляет собой систему расположенных друг за другом и связанных между собой различных валов, механизмов и устройств. Типовая схема валопровода и размещение его основных элементов приведены на рис.8.7. До начала монтажа валопровода должны быть пробиты все базовые и вспомогательные плоскости, а опорные поверхности фундаментов предварительно обработаны. После проведения гидравлических испытаний основного корпуса в проницаемую кормовую часть оконечности загружаются румпели, баллеры и другое оборудование. Кормовой блок временно нагружается в соответствии с расчетом имитации неустановленного по технологическим соображениям оборудования и выставляется в требуемое положение по основным плоскостям. По оптическим приборам пробиваются положения теоретических осей валопроводов, мортир рулей и стабилизаторов. По торцам всех мортир и на переборках основного корпуса наносятся контрольные окружности и фиксируются базовые плоскости. Одновременно произво-
.8.7. |
1 - |
|
125; 2 - |
||
|
; 3 - 125; 4 - |
|
|||
|
|
; 5 - |
|
|
|
; 6 - |
; 7 - |
125; 8 - |
|
; |
|
9 - |
; 10 - |
125; 11 - |
|
|
125; |
12 - |
|
125; 13 - |
|
125; 14 |
- а |
|
|
|
|
|
|
дится подготовка оборудования валопровода к погрузке и монтажу, включая обработку фундаментов. Затем выполняется пробивка фактической оси валопровода с помощью оптического прибора, установленного и отцентрированного по оси кормового фланца главного двигателя или главного упорного подшипника. Для этого при повороте фланца фиксируется отклонение светового или лазерного луча от теоретического положения оси валопровода, нанесенной на кормовом шергене. По полученной фактической оси на торцах мортир и поперечных
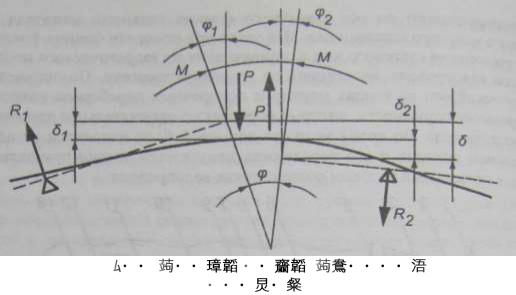
переборках наносятся контрольные окружности, которые определяют окончательное положение оси валопровода. Во время монтажа кормовой блок находится на одной стапельной позиции и его передвижка допускается только при застопоренных отжимными болтами подшипниках валопровода.
Одной из важнейших технологических операций при монтаже валопровода является его центровка, заключающаяся в совмещении осей отдельных валов с осью валопровода. Для обеспечения нормальной работы валов необходимо, чтобы они имели общую ось вращения. Для этого в статическом состоянии требуется совместить оси на величину S= S\ + Si усилием Р и повернуть фланцы валов на угол ф = фі + <р2, приложив момент М. Это усилие и момент вызовут реакции опор R\ и R- 2 и нормальные напряжения в валах, величина которых зависит от их размеров, жесткости и несоосности. Аналогичное происходит при перемещении подшипников по высоте. Схема деформаций и усилий при жестком соединении несоосных валов представлена на рис.8.8.
Технологическими параметрами при оценке качества центровки являются расчетные нагрузки на подшипники и изломы и смещения, измеренные на фланцах валов. Эти параметры рассчитываются из условия получения оптимальных нагрузок на подшипники валопровода с учетом остаточных деформаций корпуса в результате перераспределения остаточных сварочных деформаций и изменения нагрузки в процессе эксплуатации.
.8.8. |
, |
|
е
Метод центровки по нагрузкам на подшипники заключается в определении фактических нагрузок, оптимальные величины которых устанавливаются расчетом в зависимости от конструктивной схемы валопровода. При центровке нагрузки на опорные подшипники измеряются и регулируются с помощью динамометров (рис.8.9) при собранных фланцевых соединениях валов. Для этого поворотом контргаек отжимных болтов, на которые опираются лапы подшипника, регулируют вертикальное положение подшипника и его нагрузку. Перемещения вала в процессе центровки из-за зазора между крышкой подшипника и шейкой вала ограничиваются установкой неметаллической прокладки. Во время

центровки подшипник кормовой мортиры с кормового торца удерживается с помощью динамометров концентрично контрольной окружности при допускаемом отклонении 1 мм в любом направлении.
Рис.8.9. Установка динамометров: 1 - прокладка; 2 - лапы подшипника; 3 - динамометр; 4 - неметаллическая прокладка
Фактическая вертикальная нагрузка на подшипник RB равна
где - нагрузки на динамометрах, установленных в правой и левой лапах подшипника; G - сила тяжести подшипника.
При центровке разница нагрузок на правый и левый динамометры не должна превышать 5%.
Производится последовательное нагружение динамометров в несколько приемов. При первом нагружении нагрузка на подшипники составляет до 80% от расчетного значения. При достижении заданных нагрузок фиксируется положение подшипников валопровода с помощью отжимных болтов. Затем нагрузки с динамометров переводятся на отжимные болты, которые закрепляются контргайками.
Метод центровки по изломам и смещениям заключается в определении изломов ф и смещений 5, замеренных на фланцах последовательно присоединяемых валов (рис.8.10). При центровке промежуточные и упорные валы последовательно устанавливаются по контрольным рискам, нанесенным на их фланцы с обеспечением зазора между ними в 1 мм. Затем выполняется попарная последовательная центровка фланцевых соединений перемещением опорных, упорных и монтажных подшипников с помощью отжимных болтов. Производятся измерения изломов и смещений в четырех точках: верх - низ, левый борт - правый борт. При повороте валов на передний ход через каждые 90° измеряются
• изломы и смещения, величины которых должны соответствовать расчетным значениям центровки, регламентированным нормативно-

технической документацией. Промежуточные валы сдвигаются до соприкосновения фланцев и собираются на болтах.
После центровки валопровода подшипники закрепляются, для чего измеряется расстояние между опорными поверхностями фундаментов и опорных лап подшипников в местах расположения выравнивающих подкладок. Производится подгонка прокладок по месту и их закрепление к фундаменту с помощью призонных болтов. Крепление подшипников осуществляется с помощью конусных колец, непосредственной за-
прессовкой или с применением полимерных материалов.
.8.10. |
|
м |
При использовании конусных колец мортира линии вала изготавливается в чистый размер, а подшипники крепятся на торцах разрезными конусными кольцами (рис.8.11), которые запрессовываются в мортиру с помощью домкратов.
.8.11. 1 - 128; 2 - 128; 3 -
128; 4 -
В случае крепления непосредственной запрессовкой мортира изготавливается с припуском и выполняется ее расточка по фактической оси вала переносными станками с использованием борштанги. Расточка выполняется черновым и чистовым проходом, после чего подшипник запрессовывается в мортиру.
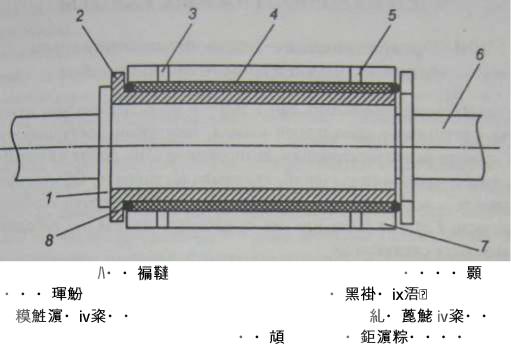
При креплении подшипников с использованием полимерных материалов мортира изготавливается в чистый размер, в нее устанавливаются технологические уплотнения (резиновые кольца) и монтажный зазор заполняется полимерной композицией (рис.8.12).
.8.12. |
|
|
|
: 1 - ; 2 - |
; 3 - |
||
|
129; 4 - 129; 5 - |
|
|
129; 6 - 129; 7 - |
129; 8 - |
|
Для обеспечения точности монтажа валопровода предусматривается установка компенсирующего звена, в качестве которого принимается один из промежуточных валов или уравнительное кольцо, устанавливаемое между торцом носовой мортиры и дейдвудным сальником. В первом случае фланец промежуточного вала изготавливается с припуском, который затем удаляется по данным замеров расстояний между фланцами валов, с которыми этот промежуточный вал соединяется. При' применении в качестве компенсирующего звена уравнительного кольца после центровки валопровода снимаются размеры, по которым изготавливается уравнительное кольцо с учетом неперпендикулярности и смещения оси валопровода относительно торца носовой мортиры. После изготовления кольцо устанавливается в состав валопровода и к нему крепится дейдвудный сальник.
9.ЭЛЕКТРОМОНТАЖНЫЕ РАБОТЫ
9.1.Организационно-технологические схемы выполнения
электромонтажных работ
К электромонтажным работам (ЭМР) в кораблестроении относятся работы, связанные с прокладкой кабеля, монтажом электрооборудования и средств радиоэлектроники. Выполнение этих работ на кораблях и судах всех классов и назначений, как правило, типовое. Объем, последовательность и технология проведения работ определяются особенностями проекта. Главными из них на подводных лодках на сегодняшний день являются следующие:
рост объема и сложности работ в связи с тенденциями в совершенствовании и разработке новых видов вооружения, автоматики, радиоэлектронного, акустического и навигационного оборудования;
необходимость доводки основных радиоэлектронных систем на последних этапах строительства заказов;
рост требований к качеству и надежности систем;
ухудшение условий труда электромонтажников в связи с уменьшением свободных объемов на заказах;
увеличение длины прокладываемых кабелей.
Электромонтажные работы, как правило, выполняет не судостроительный завод, а организации-контрагенты завода. В России такой организацией является предприятие ЭРА («Электрорадиоавтоматика»), имеющее цехи или филиалы на всех судостроительных заводах.
Предприятие ЭРА выполняет заказ необходимых материалов, комплектацию, подготовку, установку, монтаж, наладку и испытание всех электрических систем и устройств (источники электроэнергии, пускорегулирующая аппаратура, радионавигационное оборудование, устройства электроавтоматики, распределительные устройств) и производит прокладку всех кабелей.
Трудоемкость и продолжительность ЭМР характеризуется не только длиной всех прокладываемых на корабле кабелей, но и количеством помещений, их насыщенностью электрооборудованием, кабельными коробками, числом отрезков кабелей и другими показателями, определяющими условия и степень сложности выполнения монтажа электрооборудования.
До недавнего времени трудоемкость ЭМР на судах составляла немногим более 10% от общей трудоемкости постройки судна. В связи с увеличением мощности судовых энергетических систем, использовани-
ем средств автоматизации, расширением применения радиоэлектроники этот показатель возрос и составляет 12-18% от общей трудоемкости постройки заказа.