
- •Оглавление
- •ВВЕДЕНИЕ
- •I. ПОЛУЧЕНИЕ ПОРОШКОВ
- •Лекция 16 Восстановление химических соединений металлов из растворов солей и газообразных соединений металлов
- •II. ФОРМОВАНИЕ И СПЕКАНИЕ ИЗДЕЛИЙ ИЗ МЕТАЛЛИЧЕСКИХ И НЕМЕТАЛЛИЧЕСКИХ ПОРОШКОВ
- •Введение
- •Лекция 13 Твердофазное спекание материалов
- •Лекция 20 Жидкофазное спекание и инфильтрация порошковых формовок. Брак при спекании
- •Лекция 25 Методы определения механических характеристик порошковых тел. Заключение
- •ЗАКЛЮЧЕНИЕ
- •БИБЛИОГРАФИЧЕСКИЙ СПИСОК
- •ПРИЛОЖЕНИЯ

II. ФОРМОВАНИЕ И СПЕКАНИЕ ИЗДЕЛИЙ ИЗ МЕТАЛЛИЧЕСКИХ И НЕМЕТАЛЛИЧЕСКИХ ПОРОШКОВ
Лекция 25 Методы определения механических характеристик порошковых тел. Заключение
Лекция25 Методыопределениямеханическиххарактеристик
порошковыхтел. Заключение
План лекции
1.Эксплуатационная пригодность порошковых тел и методы ее опре-
деления.
2.Определение твердости порошковых тел.
3.Заключение
Для порошковых материалов из малопластичных составляющих, у которых разрушение связано с появлением микротрещины или какого-либо другого дефекта критического размера, быстро распространяющегося по всему сечению и вызывающего хрупкое разрушение, прочность является переменной величиной (чем больше размер образца, тем больше вероятность встретить в нем опасный дефект и тем меньше его прочность).
Для порошковых материалов предел прочности при растяжении повышается с увеличением поперечного сечения и уменьшением длины испытуемого образца. В связи с этим для получения данных, объективно характеризующих свойства различных сравниваемых материалов, в соответствии с ГОСТ 18227-85 применяют образцы, получаемые двусторонним прессованием и спеканием в тех же условиях, что и готовые изделия.
Размеры и форма образцов для испытаний на растяжение показаны на рис. 2.62. Толщина образцов должна быть 5,7±0,3 мм, разность наибольшей и наименьшей толщины по длине рабочей части < 0,04 мм. Допускается изготавливать образцы для испытаний механической обработкой готовых изделий, при этом диаметр их рабочей части должен быть > 4 мм.
Вариант 1
|
R 25,0 |
8,7±0,2 |
R 4,35 |
5,7±0,02 |
5,7±0,25
32,0
81,0±0,5
89,7±0,5
Вариант 2
Рис. 2.62. Вид образцов для испытаний порошковых материалов на растяжение
90о
81,0±0,5
89,7±0,5
Процессы порошковой металлургии. Курс лекций |
-394- |

II. ФОРМОВАНИЕ И СПЕКАНИЕ ИЗДЕЛИЙ ИЗ МЕТАЛЛИЧЕСКИХ И НЕМЕТАЛЛИЧЕСКИХ ПОРОШКОВ
Лекция 25 Методы определения механических характеристик порошковых тел. Заключение
Весьма часто для оценки эксплуатационной пригодности определяют прочность при сжатии на цилиндрических образцах с отношением высоты к поперечному размеру > 1 (максимальную нагрузку делят на номинальную площадь поперечного сечения образца) и при изгибе по ГОСТ 18228-94 на штабике прямоугольного сечения в условиях трехточечного нагружения.
Приспособление для испытаний на изгиб состоит из двух цилиндрических опор (роликов), установленных на расстоянии 25,0 ± 0,2 мм, и изгибающего (нагружающего) ролика, располагающегося на одинаковом расстоянии от опор.
Ролики должны иметь диаметр 3,0 ± 0,1 мм, длину > 20 мм и твердость > 700 HV. Испытания проводят на штабиках толщиной 6,0+ 0,2 мм, спрессованных в пресс-форме с размерами полости матрицы 30 х 12 мм. Различия в толщине по длине образца не должны превышать 0,1 мм. Допускается использовать образцы с размерами 30 х 12x6 мм, полученные механической обработкой готовых изделий. Предел прочности при поперечном изгибе Rtr, Н/мм2 (МПа), вычисляют по формуле
Rtr = 32bhP 2l ,
где Р – нагрузка, необходимая для изгиба и измеренная в момент разрушения образца, Н; l – расстояние между осями цилиндрических опор, мм; b – ширина образца, мм; h – высота (толщина) образца, измеренная в направлении, параллельном приложению нагрузки, мм.
За предел прочности при поперечном изгибе принимают среднее арифметическое результатов не менее пяти определений, округленное до ближайших 10 Н/мм2.
При пониженных температурах σв и σт порошковых материалов, как правило, увеличиваются, так как структурные дефекты в основном сдерживают развитие и распространение трещин.
При относительно невысокой пористости порошковые материалы можно считать пригодными к работе в условиях повторно-переменного нагружения. Уровень усталостных свойств определяется количеством, формой, размерами, ориентировкой пор и неметаллических включений, размером зерна, субмикроструктурой, распределением внутренних напряжений и другими факторами, а также масштабным фактором, конфигурацией изделий и условиями их обработки.
Предел выносливости материала σ-1 можно повысить измельчением зерна, уменьшением числа неметаллических включений, изменением их формы, использованием упрочняющей обработки. Например, снижение пористости порошковой стали с 4 до 1 % способствует повышениюσ -1 на 15–20 %, а дальнейшее снижение пористости практически не изменяет ее усталостных свойств.
Процессы порошковой металлургии. Курс лекций |
-395- |

II. ФОРМОВАНИЕ И СПЕКАНИЕ ИЗДЕЛИЙ ИЗ МЕТАЛЛИЧЕСКИХ И НЕМЕТАЛЛИЧЕСКИХ ПОРОШКОВ
Лекция 25 Методы определения механических характеристик порошковых тел. Заключение
В настоящее время для оценки работоспособности материала в изделии широко применяют термин «конструктивная прочность». Одним из показателей этой прочности является вязкость разрушения материала, или критический коэффициент интенсивности напряжений Кic, который характеризует способность материала сопротивляться разрушению при наличии трещины или трещиноподобного дефекта. Например, по коэффициенту Кic можно вычислить предельно допустимое напряжение или длину трещины, при которых разрушение конструкции еще не наступает. Вязкость разрушения зависит от исходной пористости, химического состава и условий получения материала, а также свойств исходных порошков. С увеличением пористости вязкость разрушения материала снижается. Существует тенденция к одновременному росту прочности и вязкости разрушения, так как трещина в порошковых материалах распространяется путем коалесценции микропор при разрыве связей между частицами. Повысить сопротивляемость материалов хрупкому разрушению можно высокотемпературной термомеханической обработкой (ВТМО), после которой излом образцов имеет ярко выраженные элементы вязкого разрушения.
Существует ряд методик определения Кic, среди которых наиболее простым способом в случае высокопрочного порошкового материала является испытание цилиндрических образцов диаметром D с круговым надрезом (диаметр надреза d должен быть таким, чтобы его дальнейшее уменьшение не приводило к снижению предельной нагрузки Рmax) или, что лучше, с круговой усталостной трещиной. Если размеры образца для испытания подобраны таким образом, что d/D = 0,707, то вязкость разрушения составит, МПа м0,5:
Кic = 0,414 σND0,5,
где σN = Pmax/Fd, МПа: F – площадь образца в плоскости надреза, м2; Pmах – максимальная (разрушающая) нагрузка на образец, Н.
Должно соблюдаться соотношение σN < 1,1σ0,2 (σ0,2 – предел текучести материала, МПа; если σN > l,lσ0,2, то, увеличивая D и сохраняя d/D = 0,707, обеспечивают требуемое условие).
Для материалов со средними значениями показателей прочности величину Кic можно определить по результатам испытаний образцов (рис. 2.63) со специально наведенной усталостной трещиной при статическом изгибе и внецентровом растяжении (длина надреза с трещиной а = 0,45–0,55; длина трещины > 0,5а или 1,3 мм; толщина образца В должна удовлетворять соотношению В >2,5Кic/σ0,2).
Процессы порошковой металлургии. Курс лекций |
-396- |
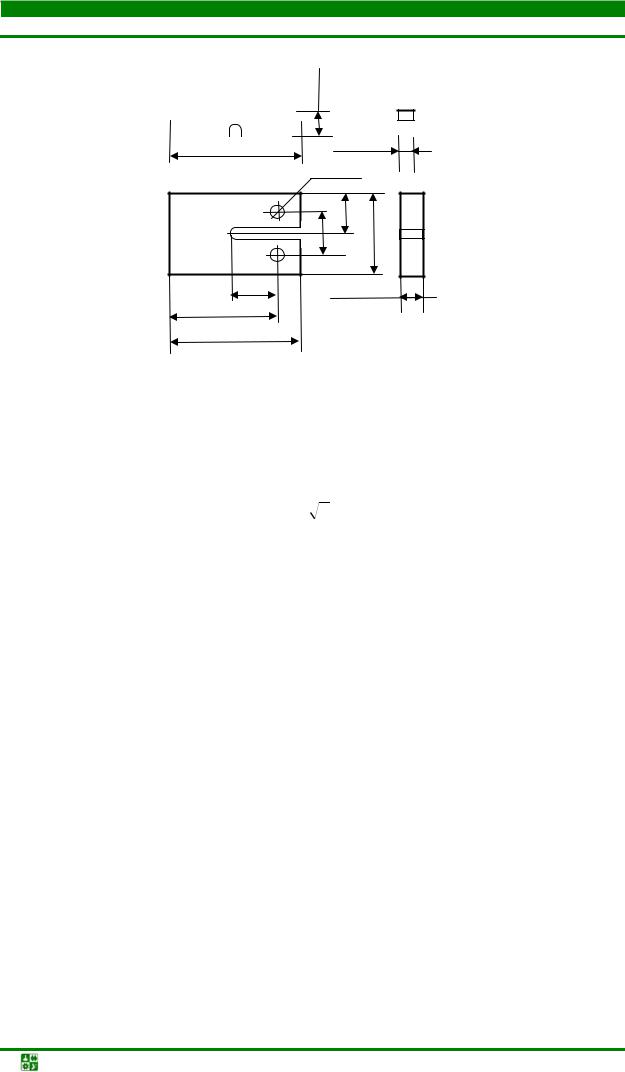
II. ФОРМОВАНИЕ И СПЕКАНИЕ ИЗДЕЛИЙ ИЗ МЕТАЛЛИЧЕСКИХ И НЕМЕТАЛЛИЧЕСКИХ ПОРОШКОВ
Лекция 25 Методы определения механических характеристик порошковых тел. Заключение
|
|
W±0,25 |
|
|
|
B = W/2±0,25W |
|
|
|
|
|
H ≥ 4,4 |
W |
|
|
|
|
аǾ 0,25W
|
0,55W 0,6W 1,2W |
a |
B = W/2±0,25W |
W±0,25
1,25W
б
Рис. 2.63. Образцы для испытаний на вязкость разрушения:
а– при изгибе; б – при внецентровом растяжении
Впоследнее время расширена практика определения Кic по результатам усталостных испытаний:
Kic = σó π lê f ,
где σу – предел усталости материала, МПа; lк – критическая длина наведенной трещины; f – число циклов испытаний.
Описанные методы определения Кic применимы к порошковым материалам с прочностью > 700 МПа и пористостью < 3 %. При пористости > 10 % образцы можно испытывать без трещины (надреза).
Ударная вязкость (ударный изгиб). По ГОСТ 26528-85 испытаниям на ударный изгиб с последующим определением работы удара или ударной вязкости подвергаются образцы порошковых материалов в виде штабиков квадратного сечения 10х10 мм (±0,2 мм) длиной 55 ± 1 мм без надрезов, так как роль надрезов играют поры.
Для малопористых и беспористых материалов допускается использование образцов с надрезом по ГОСТ 9454-78. Обычно для нагружения применяют маятниковые копры мощностью 0,5–10 кгс м; плоскость качания маятника вертикальная и проходит на одинаковом расстоянии от опор, где свободно располагается образец. Показатель ударной вязкости КС (Дж/м2) получают делением работы К, Дж, затраченной на разрушение, на номинальное поперечное сечение образца S, м2:
КС = K/S = m l (cos β – cos α) / S,
Процессы порошковой металлургии. Курс лекций |
-397- |

II. ФОРМОВАНИЕ И СПЕКАНИЕ ИЗДЕЛИЙ ИЗ МЕТАЛЛИЧЕСКИХ И НЕМЕТАЛЛИЧЕСКИХ ПОРОШКОВ
Лекция 25 Методы определения механических характеристик порошковых тел. Заключение
где т – масса маятника; l – расстояние центра тяжести маятника от оси вращения; β, α – угол подъема маятника, соответственно, до и после разрушения испытуемого образца.
Сравнительно низкие значения ударной вязкости порошковых материалов (единицы или десятки единиц и очень редко несколько сотен единиц кДж/м2) обусловлены спецификой их структуры: поры и неметаллические включения способствуют зарождению и распространению трещин в объеме материала. С повышением плотности порошкового материала его ударная вязкость возрастает. Повысить ударную вязкость можно термообработкой порошкового материала, обеспечивающей формирование мелкозернистой структуры, залечиванием микропор и очистку границ зерен от примесей. Например, при повышении температуры закалки или проведения отжига и нормализации ударная вязкость порошковых сталей существенно увеличивается.
Твердость. Для порошковых материалов, пористость которых, как правило, существенна, твердость является функцией прочности частиц, сил связи между ними и плотности материала. Однако у порошковых материалов, в отличие от литых, определенного соотношения между твердостью и временным сопротивлением при растяжении не наблюдается. Обычно макротвердость порошкового материала измеряют по Бринеллю, Виккерсу или Роквеллу; можно измерять микротвердость отдельных структурных или фазовых составляющих.
По методу Бринелля твердость оценивают по сопротивлению материала вдавливанию в его поверхность стального шарика (число твердости НВ
– частное от деления нагрузки на площадь отпечатка).
Метод Виккерса основан на вдавливании в материал под действием определенной нагрузки (от 1 до 100 кгс) четырехгранной алмазной пирамидки с квадратным основанием и углом между противоположными гранями при вершине 136 ± 0,5°. На поверхности образца образуется отпечаток, имеющий вид квадрата, диагонали которого измеряют.
Твердость по Виккерсу (HV) рассчитывают по формуле
HV = 1,854 P/d2,
где Р – нагрузка, кгс; d – среднее арифметическое значение результатов измерения длины обеих диагоналей отпечатка, мм.
Разность диагоналей одного отпечатка не должна превышать 2 %. Если нагрузка выражается в ньютонах, то коэффициент в формуле меняется на 0,189. По ГОСТ 2999-75 каждый образец испытывают в точках, расположенных так, чтобы расстояние между центром данного отпечатка и краем образца или краем соседнего отпечатка было бы > 2,5 длины диагонали отпечатка.
Определение твердости по Роквеллу – статический метод механических испытаний, при котором в материал с определенной силой медленно
Процессы порошковой металлургии. Курс лекций |
-398- |

II. ФОРМОВАНИЕ И СПЕКАНИЕ ИЗДЕЛИЙ ИЗ МЕТАЛЛИЧЕСКИХ И НЕМЕТАЛЛИЧЕСКИХ ПОРОШКОВ
Лекция 25 Методы определения механических характеристик порошковых тел. Заключение
и непрерывно вдавливают алмазный конус с закругленной вершиной и углом 120° или стальной шарик диаметром 1,588 мм.
Суммарная нагрузка складывается из двух: предварительной (10 кгс) и основной (50, 90 или 140 кгс в зависимости от твердости материала исследуемого образца). Выдержка под нагрузкой составляет несколько секунд. После плавного снятия нагрузки по индикатору прибора измеряют остаточную глубину проникновения индентора (алмазного конуса или стального шарика). Твердость по Роквеллу выражается условными единицами HRA (шкала А) и HRC (шкала С) при вдавливании алмазного конуса и HRB (шкала В) при вдавливании стального шарика. Число твердости по Роквеллу размерности не имеет; измеренные при разных нагрузках для одного и того же образца числа твердости будут разными.
Микротвердость Hμ определяют вдавливанием индентора (чаще всего алмазной пирамидки с квадратным основанием и углом между противоположными гранями при вершине 136°) в испытуемый образец с нагрузкой от 2 до 200 г, которую выбирают в зависимости от размера структурных (фазовых) составляющих и их твердости. Метод микротвердости применяют для оценки хрупкости фаз и структурных составляющих и решения некоторых металловедческих задач.
Контрольныевопросыизадания
1.Какие факторы определяют уровень усталостных свойств порошкового материала?
2.Что характеризует коэффициент интенсивности напряжений?
3.Как можно повысить предел выносливости материала?
4.С чем связано разрушение малопластичных составляющих порошковых тел?
5.Как влияет на придел прочности при растяжении материала снижение температуры?
6.Что такое «ударная вязкость» и как ее можно повысить?
7.Перечислите методы определения твердости порошковых изделий.
8.Какие характеристики составляющих порошкового тела позволяет определить измерение микротвердости?
Процессы порошковой металлургии. Курс лекций |
-399- |