
- •Оглавление
- •ВВЕДЕНИЕ
- •I. ПОЛУЧЕНИЕ ПОРОШКОВ
- •Лекция 16 Восстановление химических соединений металлов из растворов солей и газообразных соединений металлов
- •II. ФОРМОВАНИЕ И СПЕКАНИЕ ИЗДЕЛИЙ ИЗ МЕТАЛЛИЧЕСКИХ И НЕМЕТАЛЛИЧЕСКИХ ПОРОШКОВ
- •Введение
- •Лекция 13 Твердофазное спекание материалов
- •Лекция 20 Жидкофазное спекание и инфильтрация порошковых формовок. Брак при спекании
- •Лекция 25 Методы определения механических характеристик порошковых тел. Заключение
- •ЗАКЛЮЧЕНИЕ
- •БИБЛИОГРАФИЧЕСКИЙ СПИСОК
- •ПРИЛОЖЕНИЯ
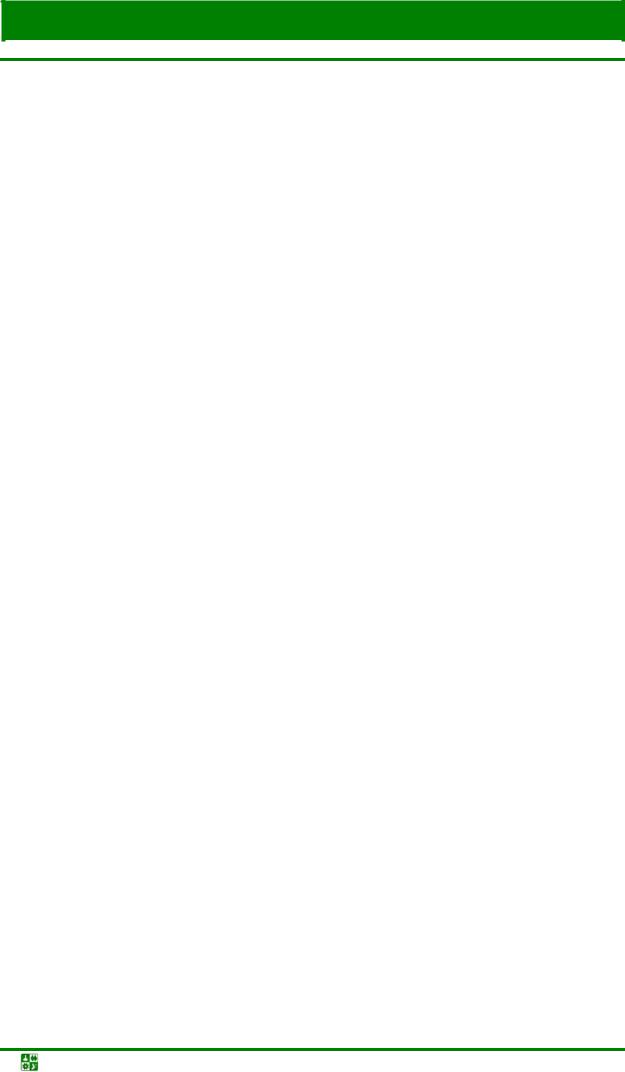
II. ФОРМОВАНИЕ И СПЕКАНИЕ ИЗДЕЛИЙ ИЗ МЕТАЛЛИЧЕСКИХ И НЕМЕ-
ТАЛЛИЧЕСКИХ ПОРОШКОВ
Лекция 13 Твердофазное спекание материалов
Лекция13 Твердофазноеспеканиематериалов
План лекции
1.Стадии процесса спекания.
2.Спекание однокомпонентных систем
3.Движущие силы процесса спекания.
Стадиипроцессаспекания
Твердофазное спекание – это спекание порошкового тела без образования жидкой фазы.
Твердофазное спекание применяется для получения изделий на основе одноили многокомпонентных систем, поведение которых при нагреве во многом зависит от природы и химической чистоты соответствующих компонентов.
Необходимо отметить, что любой так называемый однокомпонентный металлический порошок из-за наличия в нем примесей по существу представляет собой многокомпонентную систему. Количество примесей, входящих в состав порошка, необходимо учитывать при проектировании технологических процессов и режимов спекания материалов.
Нагрев порошкового тела вызывает в нем определенные структурные изменения, среди которых можно выделить несколько основных стадий процесса спекания. Подобные изменения связаны с объективными причина-
ми (движущими силами процесса спекания), от которых зависит перемеще-
ние вещества в нагреваемом порошковом теле, т.е. механизм массопереноса. Нагрев порошкового тела до заданной температуры и выдержка при
этой температуре, сопровождается его уплотнением.
Всю сложную последовательность процессов, происходящих при нагреве порошкового тела, обычно стараются разделить на отдельные стадии, для каждой из которых можно достаточно точно указать движущие силы и наиболее существенные механизмы массопереноса.
Хотя подобное деление удобно для описания процесса уплотнения порошкового тела, но оно (в значительной мере) условно, так как, в зависимости от начальных свойств формовки и условий спекания, какие-то явления будут происходить последовательно или одновременно, перекрывая одну или даже несколько стадий.
Процессы порошковой металлургии. Курс лекций |
-317- |
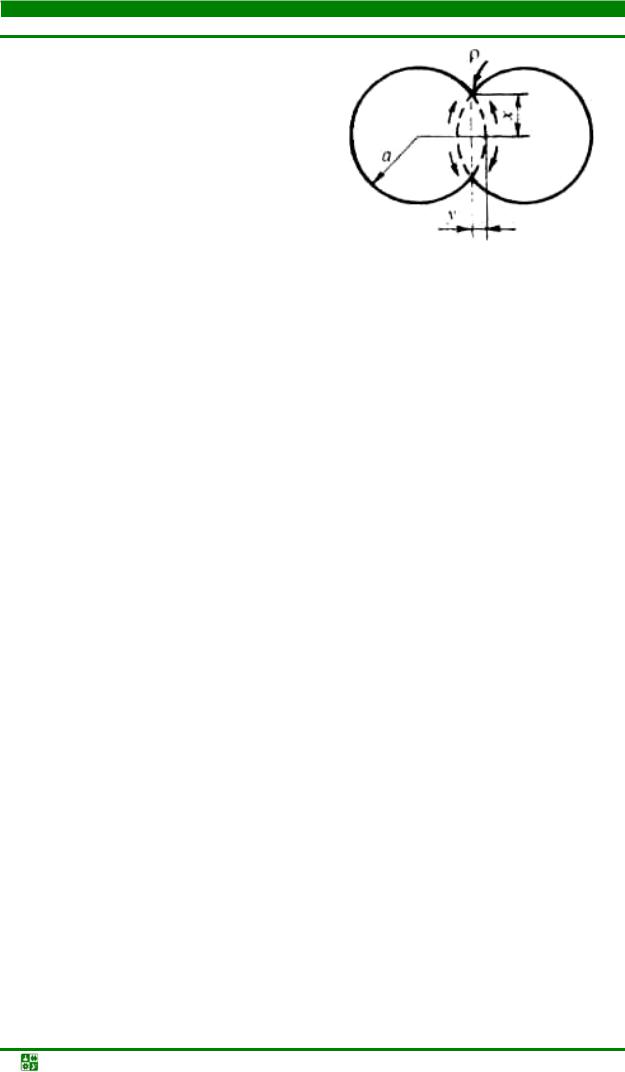
II. ФОРМОВАНИЕ И СПЕКАНИЕ ИЗДЕЛИЙ ИЗ МЕТАЛЛИЧЕСКИХ И НЕМЕТАЛЛИЧЕСКИХ ПОРОШКОВ
Лекция 13 Твердофазное спекание материалов
Рис. 2.37. Модель спекания двух частиц: а – радиус частицы;ρ – радиус «шейки»; х – радиус сечения образующегося контакта; у – половина отрезка, на который сближаются частицы
Для спекаемого порошкового тела характерны некоторые геометрические элементы (рис. 2.37), определяемые понятиями «шейка», «межчастичный контакт», «изометрическая пора» и др.
При описании структуры спекаемого материала выделяют три принципиально отличных состояния порошкового тела, каждое из которых соответствует определенной стадии.
На первой (начальной) стадии происходит припекание порошинок (частиц) к друг другу, сопровождающееся увеличением площади контакта между ними. Однако каждая частица сохраняет структурную индивидуальность, т.е. граница между ними сохраняется и с ней сохраняется понятие «контакт между частицами».
На второй стадии пористое тело может быть представлено в виде совокупности двух фаз – фазы вещества (частицы) и фазы «пустоты» (поры).
На этом этапе спекания происходит формирование сквозных (сообщающихся друг с другом) пор. Выраженные границы (контакты) между отдельными частицами исчезают или располагаются на местах, не соответствующих их начальному положению.
Для третьей стадии характерной является структура замкнутых (изолированных) пор. Число и общий объем этих пор может изменяться (уменьшаться).
Необходимо отметить, что эти весьма укрупненные три стадии не могут иметь четкого разграничения: замкнутые (изолированные) поры встречаются в реальном порошковом теле на ранней стадии нагрева (например, еще при формовании заготовки), а некоторые начальные контакты между частицами сохраняются вплоть до третьей стадии спекания.
Для более детального анализа процессов, сопровождающих нагрев порошковых тел, часто выделяют следующие этапы спекания:
1)возникновение и развитие связей между частицами;
2)образование и рост «шеек» на месте межчастичных контактов;
3)закрытие сквозной пористости (образование изолированных пор);
4)сфероидизация изолированных пор;
5)уплотнение порошкового тела за счет усадки изолированных пор;
6)укрупнение (коалесценция) изолированных пор.
Процессы порошковой металлургии. Курс лекций |
-318- |
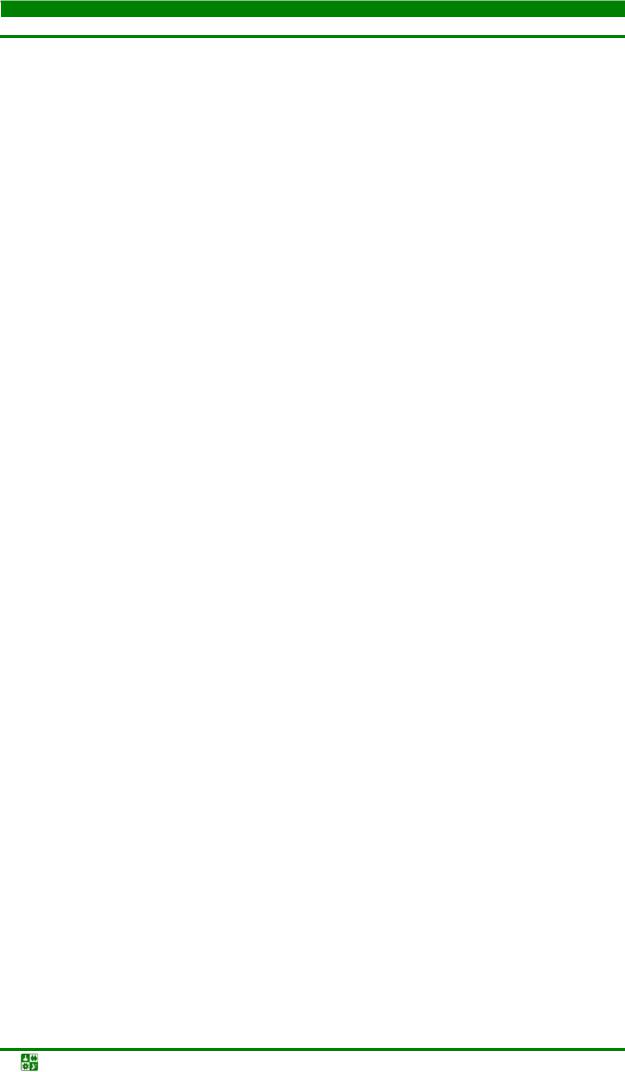
II. ФОРМОВАНИЕ И СПЕКАНИЕ ИЗДЕЛИЙ ИЗ МЕТАЛЛИЧЕСКИХ И НЕМЕТАЛЛИЧЕСКИХ ПОРОШКОВ
Лекция 13 Твердофазное спекание материалов
Развитие связей между частицами начинается сразу с нагревом порошкового тела, т.е. на самом раннем этапе спекания. Это диффузионный процесс, приводящий к образованию и развитию связей на межчастичных границах и, следовательно, увеличению прочности порошкового тела. Результат этой стадии – образование развитых контактных поверхностей между частицами.
Рост контактов и образование «шеек» – естественное продолжение процесса межчастичного взаимодействия. Этот процесс сопровождается переносом вещества в область межчастичного контакта. Он может происходить при проявлении различных механизмов массопереноса, которые вызывают или не вызывают уплотнение порошкового тела. Однако независимо от того, происходит ли уплотнение порошкового тела или нет, прочность его будет повышаться.
В какой-то момент времени приконтактный угол между частицами (первоначально острый) притупляется, и межчастичные границы начинают смещаться относительно своего первоначального расположения. Спекаемое тело по структуре приближается к состоянию, которое соответствует двум фазам – вещества и пустоты. В нем появляются сообщающиеся друг с другом поры, которые пронизываю все тело и выходят на его поверхность.
Обычно считают, что рост «шеек» происходит довольно быстро и характеризует начальный этап спекания, который в некоторых случаях (например, при спекании порошков из металлов и туго плавких соединений) может оказаться заключительным. В то же время рост «шеек» может наблюдаться и на более поздних стадиях спекания.
Закрытие сквозной пористости (сквозных поровых каналов) является результатом продолжающегося роста «шеек» и приводит к появлению изолированных групп пор или даже отдельных пор. При этом общий (суммарный) объем пор в порошковом теле уменьшается и происходит повышение его плотности, сопровождающееся усадкой. Чаще всего технологический процесс спекания заканчивают на этом этапе формирования структуры порошкового тела. Это объясняется тем, что последующее спекание, связанное со сфероидезацией, объединением и исчезновением пор требует значительных (во много раз больших, чем все предыдущие этапы) временных и энергетических затрат.
Сфероидизация пор, как и предыдущая стадия, связана с ростом «шеек»: вещество с различных участков поверхности пор перемещается в область межчастичного контакта, а сами поры (как изолированные, так и сообщающиеся) округляются, приобретая сферичность. При достаточно длительной изотермической выдержке и высокой температуре спекания можно получить идеальные сферические поры.
Усадка изолированных пор – одна из стадий спекания, требующая высоких температур и большого времени изотермическом выдержки (например, несколько сотен часов).
Процессы порошковой металлургии. Курс лекций |
-319- |
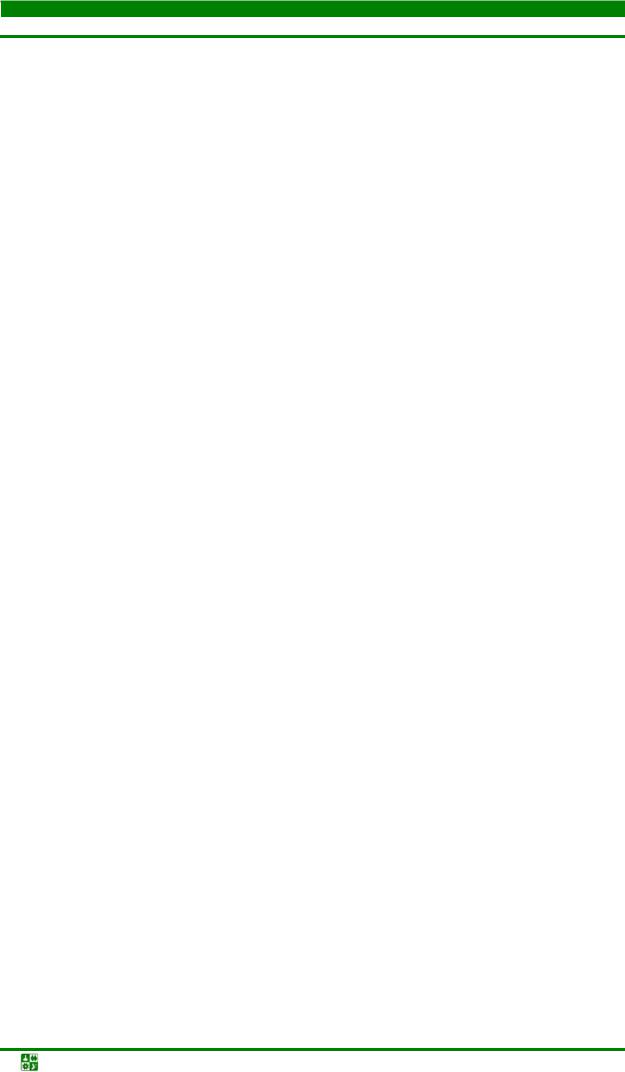
II. ФОРМОВАНИЕ И СПЕКАНИЕ ИЗДЕЛИЙ ИЗ МЕТАЛЛИЧЕСКИХ И НЕМЕТАЛЛИЧЕСКИХ ПОРОШКОВ
Лекция 13 Твердофазное спекание материалов
Укрупнение (коалесценция) пор заключается в росте крупных пор за счет уменьшения размеров и исчезновения мелких, изолированных пор. Общая пористость при этом сохраняется неизменной, а число пор уменьшается при увеличении их среднего размера. Уплотнение порошкового тела на этой стадии спекания не происходит.
Движущиесилыспекания
В исходном состоянии (до нагрева) порошковое тело представляет собой систему, удаленную от состояния термодинамического равновесия одновременно по многим параметрам. При нагреве свободная энергия порошкового тела должна понижаться за счет изменений, связанных с уменьшением свободной поверхности порошка и концентрации микродефектов.
Существуют два основных подхода, дающих представление о движущих силах процесса спекания.
Один из них основан на том, что процесс превращения порошкового тела в плотное (малопористое или беспористое) рассматривается как аналог химической реакции, которую можно характеризовать термодинамическим уравнением понижения свободной энергии E
E = H – T S,
где H, S – изменение теплосодержания и энтропии системы соответственно. Так как при спекании однофазной системы не происходит заметного изменения ее химического состава, необходимое для превращения исходной пористой массы в плотное тело понижение свободной энергии полностью связано с уменьшением свободной поверхности, свойственной спекаемому порошковому телу. Уменьшение площади поверхности соответствует уменьшению доли поверхностной энергии в общей (суммарной) свободной энергии системы. Другими словами, нагреваемая масса порошка подвергается изменениям, стремящимся минимизировать в ней свободную поверхность. С этой точки зрения можно рассмотреть любую из шести описанных выше стадий и убедиться, что на каждой из них происходит уменьшение поверхно-
сти.
Другой подход, в основе которого тоже лежат принципы химической термодинамики, связан с более «механическим» представлением движущих сил спекании: при высоких температурах в связи с высокой подвижностью атомов поверхностная энергия эквивалентна поверхностному натяжению, т.е. силе, стремящейся уменьшить площадь поверхности и понизить избыток энергии, связанный с величиной поверхности.
Для описания поведения дисперсной порошковой массы при спекании используют классическое термодинамические уравнения капиллярности, свя-
Процессы порошковой металлургии. Курс лекций |
-320- |
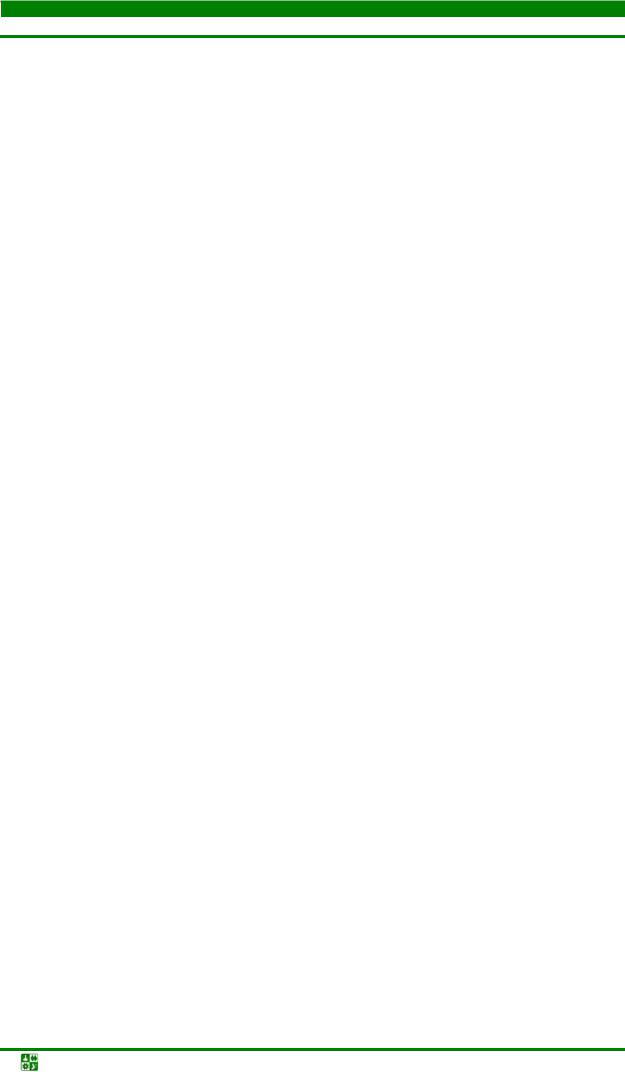
II. ФОРМОВАНИЕ И СПЕКАНИЕ ИЗДЕЛИЙ ИЗ МЕТАЛЛИЧЕСКИХ И НЕМЕТАЛЛИЧЕСКИХ ПОРОШКОВ
Лекция 13 Твердофазное спекание материалов
зывающие поверхностное натяжение, кривизну поверхности и внутреннее давление.
Механическое равновесие на границе двух фаз, разделенных неплоской поверхностью, можно оценить уравнением Лапласа. Искривление поверхности означает изменение поверхностной энергии, так как происходит изменение площади поверхности. С искривленной поверхностью раздела фаз связана сила или поверхностное (межфазное) давление р, являющееся разностью давлений р1 и р2 на границе раздела со стороны соответствующих фаз:
р = р1 – р2 = 0. |
(2.27) |
Равновесие фаз не предполагает равенства давлений со стороны каждой из фаз и будет наблюдаться, когда в них будут равны температуры (Т1 = Т2 = Т) и химические потенциалы:
μ1(р1, Т) = μ2(р2, Т) = μ при V1 + V2 = const, |
(2.28) |
где V1, V2 – объемы сосуществующих фаз;μ1, μ2 – химические потенциалы фаз. Термодинамический потенциал системы с учетом граничной энергии
имеет вид
Φ = – p1V1 – p2V2 + α1,2S, |
(2.29) |
где α1,2 – удельная поверхностная энергия на границе раздела фаз; S – площадь этой поверхности раздела.
Давление р можно найти из условия минимума термодинамического потенциала (при dФ = 0 и V1 + V2 = const):
р = р1 – р2 = α1,2(dS/dV). |
(2.30) |
Учитывая, что для каждой точки поверхности межфазной границы справедливо выражение
dS/dV = (1/R1) + (1/R2), |
(2.31) |
где R1, R2 – главные радиусы кривизны поверхности, уравнение (2.30) можно записать как
р = р1 – р2 = α1,2 (dS/dV) = α1,2 [(1/R1) + (1/R2)] = γ[(1/R1) + (1/R2)], (2.32)
Процессы порошковой металлургии. Курс лекций |
-321- |
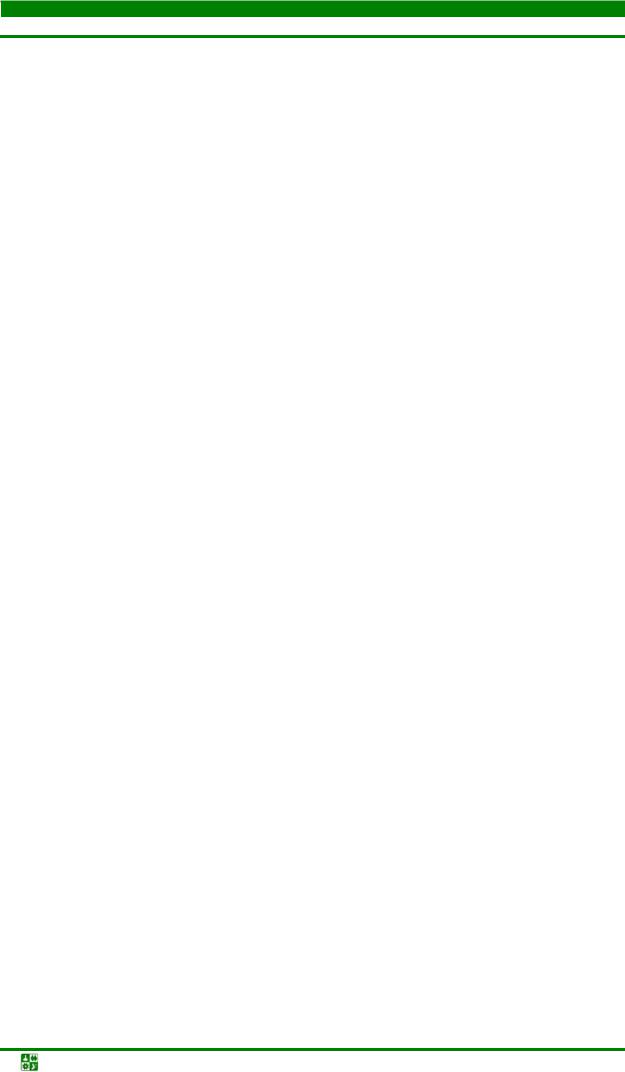
II. ФОРМОВАНИЕ И СПЕКАНИЕ ИЗДЕЛИЙ ИЗ МЕТАЛЛИЧЕСКИХ И НЕМЕТАЛЛИЧЕСКИХ ПОРОШКОВ
Лекция 13 Твердофазное спекание материалов
где γ – поверхностное натяжение (сила, стремящаяся уменьшить площадь поверхности), которое для температур спекания примерно соответствует α1,2
т.е. γ ≈ α1,2.
Частный случай уравнения (2.32) для сферической поверхности, когда R1 = R2 = R, имеет вид
р = 2α1,2 /R = 2γ/R. |
(2.33) |
Равновесие на внешней поверхности «шейки» можно описать выражением
рт = рп – γ [(1/ρ) – (1/х)], |
(2.34) |
где рт – давление (напряжение) в твердом теле (частице); рп – давление со стороны поры.
Так как х « а, а ρ « х уравнение (2.34) принимает вид
рт = рп – γ/ρ. |
(2.35) |
Величина γ/ρ представляет собой растягивающее напряжение, стремящееся сдвинуть (растянуть) край «шейки» в сторону поры, а рп есть давление со стороны поры, препятствующее расширению «шейки». Если растягивающее напряжение преобладает над рп, то контакт между частицами увеличивается.
В большинстве случаев пористость спекаемого порошкового тела в период роста «шеек» является открытой. Величина давления со стороны поры рп практическиравна атмосферному давлению (около 0,1 МПа) и радиус ρ обычно очень мал. Поэтому в начале спекания движущая сила рт велика – она тем больше, чем выше поверхностное натяжение и меньше размер «шейки». С ростом «шейки» и увеличением радиуса ρ эта движущая сила уменьшается.
Механическое равновесие межфазных давлений для изолированной сферической поры радиуса r можно выразить как
рт = рп – 2γ/r , |
(2.36) |
где величина 2γ/r представляет собой напряжение, стремящееся уменьшить поверхность поры путем уменьшения ее размера.
В случае 2γ/r>рп усадка поры возможна и ее движущей силой является величина – рт, которую можно рассматривать как сжимающее напряжение,
Процессы порошковой металлургии. Курс лекций |
-322- |
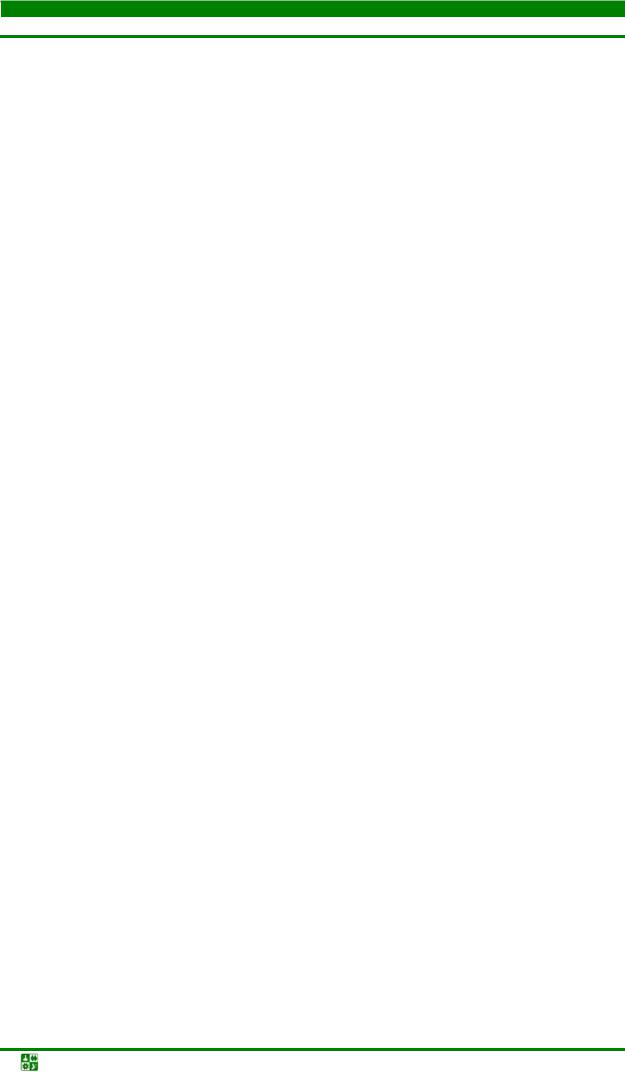
II. ФОРМОВАНИЕ И СПЕКАНИЕ ИЗДЕЛИЙ ИЗ МЕТАЛЛИЧЕСКИХ И НЕМЕТАЛЛИЧЕСКИХ ПОРОШКОВ
Лекция 13 Твердофазное спекание материалов
действующее на межфазную границу со стороны твердого тела в области, окружающей пору.
Заранее определить величину рп сложно. В результате уменьшения объема поры, образования паров воды в связи с восстановлением оксидов на поверхности поры, испарения вещества и прочих факторов эта величина может быть >0,1 МПа. Однако вследствие возможного окисления частиц спекаемого вещества, давление газа в замкнутой поре может быть < 0,1 МПа.
Кривизна поверхности частицы и «шейки» определяет существование еще двух движущих сил спекания, одна из которых – отличное от равновесного давление пара над твердым веществом, а другая связана с неравновесной концентрацией вакансий вблизи изогнутой поверхности.
Отклонение от равновесного давления паров вещества над вогнутой поверхностью «шейки» и выпуклой поверхностью частицы можно выразить уравнениями:
p − p0 |
|
= − |
γV0 |
|
|
, |
(2.37) |
||
|
p |
RTρ |
|||||||
|
|
|
|
|
|||||
0 |
|
|
|
|
|
|
|
|
|
|
p − p0 |
= |
2γV0 |
, |
|
(2.38) |
|||
|
p |
|
|||||||
|
|
RTa |
|
|
|
|
|||
0 |
|
|
|
|
|
|
|
|
где р – давление пара вещества над изогнутой поверхностью; р0 – давление пара вещества над плоской поверхностью; V0 – объем атома или молекулы вещества частицы в твердом состоянии; R – газовая постоянная.
Зная, что величина 1/х, которая много меньше 1/ρ, уравнение (2.37) принимает вид
p − p0 |
= − |
γV0 |
, |
(2.39) |
|
p |
RTρ |
||||
|
|
|
|||
0 |
|
|
|
|
Давление пара над вогнутой поверхностью «шейки» меньше (р < р0), а над выпуклой поверхностью частицы больше (р > р0), чем над плоской поверхностью. Разница в давлении паров вещества над поверхностями различной кривизны создает движущую силу механизма его переноса через газовую фазу. Эта движущая сила увеличивается с возрастанием значения поверхностного натяжения и кривизны поверхности и уменьшается на протяжении спекания.
Формулы (2.37), (2.38), (2.39) не содержат массы частиц и, следовательно, могут быть применимы к частицам, масса которых равна нулю, т.е. к узловым вакансиям в кристаллической решетке вещества или к порам.
Б.Я. Пинес для оценки отклонения концентрации вакансий от равновесной из-за кривизны межфазной границы предложил уравнения для области «шейки» и выпуклой поверхности частицы:
Процессы порошковой металлургии. Курс лекций |
-323- |
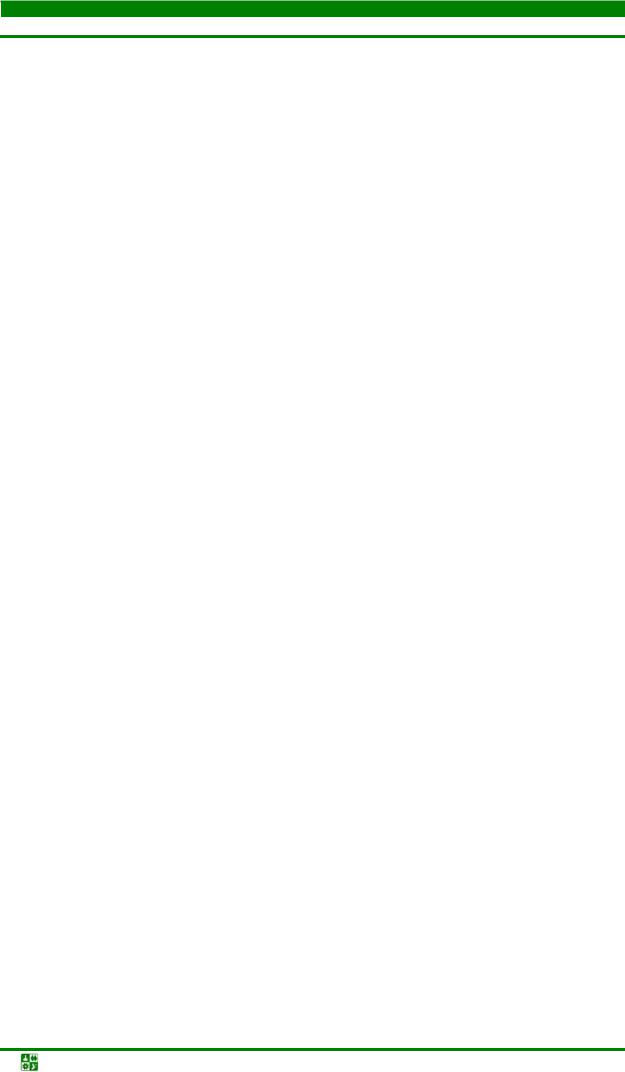
II. ФОРМОВАНИЕ И СПЕКАНИЕ ИЗДЕЛИЙ ИЗ МЕТАЛЛИЧЕСКИХ И НЕМЕТАЛЛИЧЕСКИХ ПОРОШКОВ
Лекция 13 Твердофазное спекание материалов
C −C0 = |
γV0 |
, |
|
(2.40) |
|
|
|
||||
C |
|
kTρ |
|
|
|
0 |
|
|
|
|
|
C −C0 |
= − |
2γV0 |
, |
(2.41) |
|
C |
|
kTa |
|
|
|
0 |
|
|
|
|
|
где С – концентрация вакансий в приконтактной области вещества вблизи «шейки» или выпуклой поверхности частицы; С0 – равновесная концентрация вакансий; k – постоянная Больцмана).
При температуре плавления вещества С0 обычно составляет величину не выше 10-3–10-4, а при комнатной температуре порядка – 10-15.
Таким образом, существует разность (градиент) концентраций вакансий между различными по расположению в объеме порошкового тела поверхностями и между поверхностями разной кривизны. Этот градиент концентраций вакансий представляет собой еще одну движущую силу диффузионного транспорта вещества. На протяжении спекания эта движущая сила уменьшается, так как убывает градиент концентраций вакансий между различными участками порошкового тела.
Диффузионный транспортный механизм может быть связан еще с одной движущей силой, определяемой неравновесностью концентраций вакансий вблизи изолированной сферической поры радиуса r:
C −C0 |
= |
γV0 |
. |
(2.42) |
|
||||
C |
|
kTr |
|
|
0 |
|
|
|
|
В твердом веществе вблизи рассматриваемой поры концентрация вакансий выше равновесной и тем больше, чем меньше размер поры. Следовательно, между областями спекаемого порошкового тела, удаленными от поверхностей мелких сферических пор, и этими поверхностями, а также между соседними порами разного размера также существуют градиенты концентраций вакансий, определяющие направление диффузионного переноса вещества.
Градиент концентраций вакансий может быть также связан с тем, что внутри частиц межзеренные (межкристаллитные) границы находятся под напряжением и концентрация вакансий вблизи них отличается от равновесной:
C = C0 exp(σV0/kT), |
(2.43) |
где σ – напряжение, действующее на межзеренной (межкристаллитной) границе (положительное в случае растягивающего и отрицательное в случае сжимающего усилия).
Процессы порошковой металлургии. Курс лекций |
-324- |
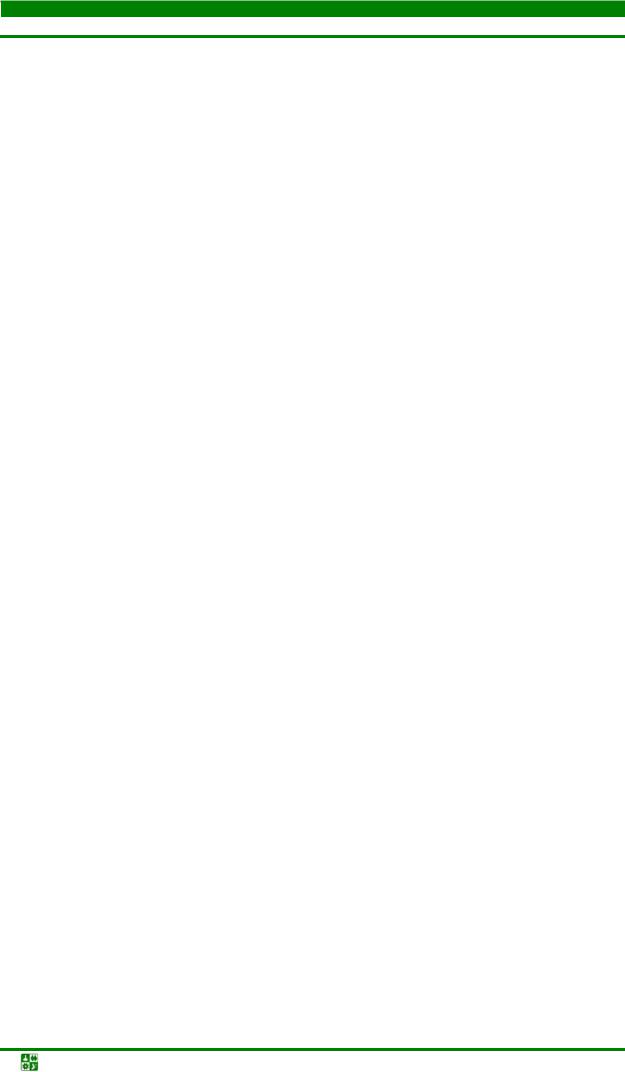
II. ФОРМОВАНИЕ И СПЕКАНИЕ ИЗДЕЛИЙ ИЗ МЕТАЛЛИЧЕСКИХ И НЕМЕТАЛЛИЧЕСКИХ ПОРОШКОВ
Лекция 13 Твердофазное спекание материалов
Возникающий градиент концентраций вакансий между границами зерен, находящимися под разными по величине или знаку напряжениями, представляет собой движущую силу механизма переноса вещества, связанного с процессом диффузионной ползучести.
Контрольныевопросыизадания
1.Перечислите основные стадии процесса спекания.
2.Что образуется на второй стадии процесса спекания?
3.Чем характеризуется завершающая стадия процесса спекания?
4.Назовите основные этапы твердофазного спекания порошкового тела.
5.Дайте характеристику этапам твердофазного спекания.
6.Что такое коалесценция?
7.Назовите основные подходы, дающие представление о движущих силах процесса спекания.
8.Напишите и объясните суть уравнения, определяющего равновесие фаз на внешней поверхности шейки.
9.Назовите основные движущие силы процесса спекания.
10.Кто разработал систему уравнений для оценки отклонения концентрации вакансий от равновесной из-за кривизны межфазной границы?
11.Что является движущей силой механизма переноса вещества, связанного с процессом диффузионной ползучести?
Лекция14 Механизмымассопереносапритвердофазномспекании
План лекции
1.Механизм испарение-конденсация
2.Массоперенос при поверхностной диффузии.
3.Объемная диффузия вещества
4.Вязкое течение вещества при спекании
Механизмиспарение-конденсация
В порошковом теле (при его спекании) возможны следующие механизмы транспорта вещества:
перенос через газовую фазу (испарения-конденсации); поверхностная диффузия;
Процессы порошковой металлургии. Курс лекций |
-325- |
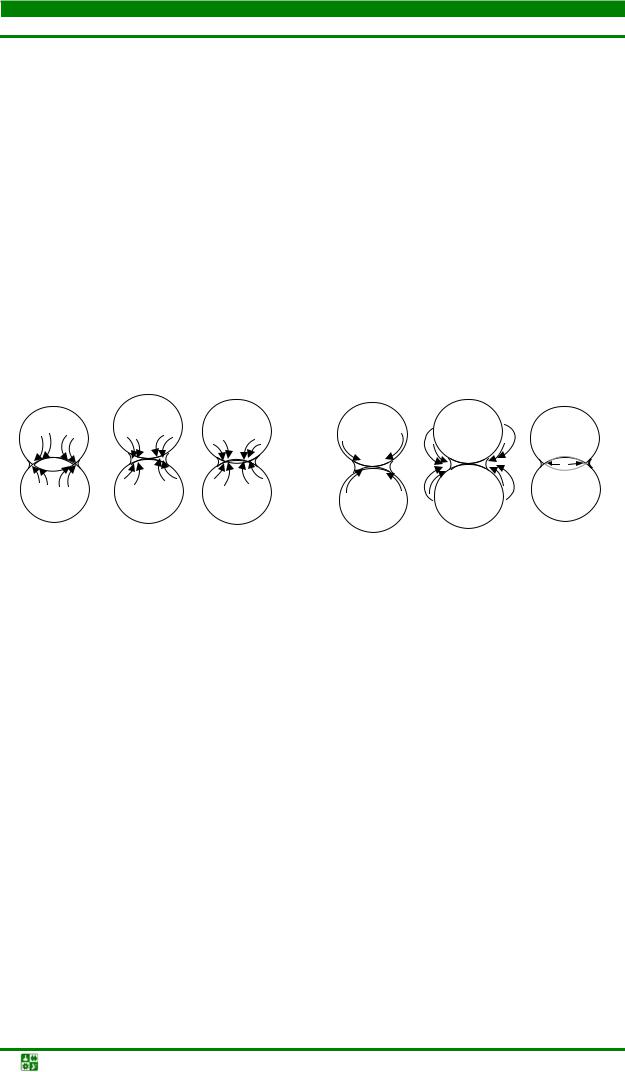
II. ФОРМОВАНИЕ И СПЕКАНИЕ ИЗДЕЛИЙ ИЗ МЕТАЛЛИЧЕСКИХ И НЕМЕТАЛЛИЧЕСКИХ ПОРОШКОВ
Лекция 14 Механизмы массопереноса при твердофазном спекании
объемная диффузия; вязкое течение;
течение, вызываемое внешними нагрузками (вязкое течение под давлением).
Идеальная модель, демонстрирующая перенос вещества через газовую фазу, приведена на рис. 2.38, д. В связи с зависимостью упругости пара над поверхностью от ее кривизны, вещество испаряется с выпуклых участков частиц и конденсируется на вогнутой поверхности контактных перешейков. Этот механизм часто еще называют «испарение–конденсация». Он должен приводить к росту «шеек» и сфероидизации пор и будет действовать до тех пор, пока в порошковом теле сохраняется заметная разница в кривизне между отдельными участками поверхности раздела вещество–пора. Направленный перенос вещества в зону межчастичного контакта приводит к упрочнению порошкового тела, но не может вызвать изменение его объема (усадку).
х2~τ; l ≠ 0 х5~τ; l = 0 х5~τ; l ≠ 0 |
7 |
|
|
5 |
|
|
4 |
|
l ≠ 0 |
|||||||||||||||||
|
|
|
|
|
|
|
|
|
|
|
|
|
х ~τ; |
l = 0 х ~τ; |
l = 0 х ~τ; |
|||||||||||
|
|
|
|
|
|
|
|
|
|
|
|
|
|
|
|
|
|
|
|
|
|
|
|
|
|
|
|
|
|
|
|
|
|
|
|
|
|
|
|
|
|
|
|
|
|
|
|
|
|
|
|
|
|
|
|
|
|
|
|
|
|
|
|
|
|
|
|
|
|
|
|
|
|
|
|
|
|
|
|
|
|
|
|
|
|
|
|
|
|
|
|
|
|
|
|
|
|
|
|
|
|
|
|
|
|
|
|
|
|
|
|
|
|
|
|
|
|
|
|
|
|
|
|
|
|
|
|
|
|
|
|
|
|
|
|
|
|
|
|
|
|
|
|
|
|
|
|
|
|
|
|
|
|
|
|
|
|
|
|
|
|
|
|
|
|
|
|
|
|
|
|
|
|
|
|
|
|
|
|
|
|
|
|
|
|
|
|
|
|
|
|
|
|
|
|
|
|
|
|
|
|
|
|
|
|
|
|
|
|
|
|
|
|
|
|
|
|
|
|
|
|
|
|
|
|
|
|
|
|
|
|
|
|
|
|
|
|
|
|
|
|
|
|
|
|
|
|
|
|
|
|
|
|
|
|
|
|
|
|
|
|
|
|
|
|
|
|
|
|
|
|
|
|
|
|
|
|
|
|
|
|
|
|
|
|
|
|
|
|
|
|
|
|
|
|
|
|
|
|
|
|
|
|
|
|
|
|
|
|
|
|
|
|
|
|
|
|
|
|
|
|
|
|
|
|
|
|
|
|
|
|
|
|
|
|
|
|
|
|
|
|
|
|
|
|
|
|
|
|
|
|
|
|
|
|
|
|
|
|
|
|
|
|
|
|
|
|
|
|
|
|
|
|
|
|
|
|
|
|
|
|
|
|
|
|
|
|
|
|
|
|
|
|
|
|
|
|
|
|
|
|
|
|
|
|
|
|
|
|
|
|
|
|
|
|
|
|
|
|
|
|
|
|
|
|
|
|
|
|
|
|
|
|
|
|
|
|
|
|
|
|
|
|
|
|
|
|
|
|
|
|
|
|
|
|
|
|
|
|
|
|
|
|
|
|
|
|
|
|
|
|
|
|
|
|
|
|
|
|
|
|
|
|
|
|
|
|
|
|
|
|
|
|
|
|
|
|
|
|
|
|
|
|
|
|
|
|
|
|
|
|
|
а |
б |
в |
г |
д |
е |
Рис. 2.38. Схемы различных механизмов спекания частиц: а – вязкое течение; б – объемная диффузия не приводящая к усадке; в – объемная диффузия при наличии стока в области контакта; г – поверхностная диффузия; д – перенос вещества через газовую фазу; е – припекание под действием внешней нагрузки ( l – величина, на которую изменяется расстояние между частицами; хn – изменение радиуса межчастичного контакта за время τ изотермической выдержки)
Перенос вещества через газовую фазу активируется с увеличением температуры, парциального давления пара вещества и поверхностного натяжения.
Этот механизм играет существенную роль лишь для материалов с относительно высоким давлением паров (не ниже 1–10 Па) при высокой температуре спекания, т.е. когда количество перенесенного через газовую фазу материала может быть значительным, либо для спекания металлов с восстанавливающимися или диссоциирующими оксидами.
Массопереносприповерхностнойдиффузии
Перенос вещества в этом случае (рис. 2.37, в) происходит к поверхности образующихся перемычек, как это показано стрелками, и частицы сближаются, вызывая общую усадку всей системы. Увеличение контактной по-
Процессы порошковой металлургии. Курс лекций |
-326- |
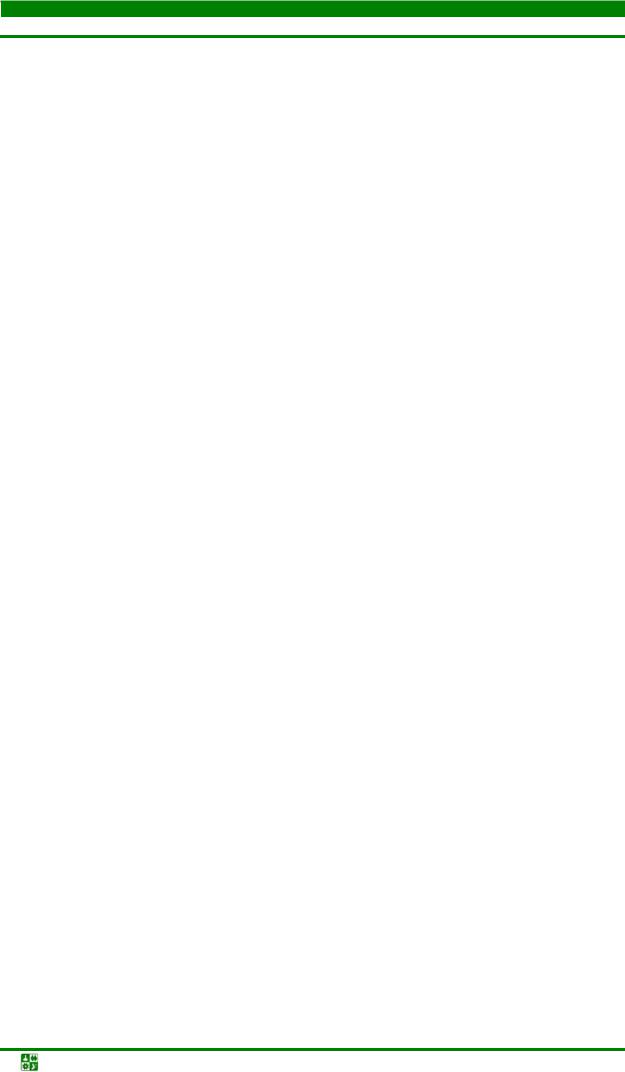
II. ФОРМОВАНИЕ И СПЕКАНИЕ ИЗДЕЛИЙ ИЗ МЕТАЛЛИЧЕСКИХ И НЕМЕТАЛЛИЧЕСКИХ ПОРОШКОВ
Лекция 14 Механизмы массопереноса при твердофазном спекании
верхности и сближение частиц (усадка) при спекании по этой схеме в основном связано с перемещением атомов в тонком дефектном по структуре поверхностном слое.
Подвижность поверхностных атомов зависит от занимаемого ими места: наименее подвижны атомы, лежащие внутри контактных участков. Далее, в порядке возрастания подвижности, идут атомы на границах контактных участков, атомы в углублениях и впадинах поверхности, атомы на ровных участках и, наконец, атомы на выступах поверхности. Так как атомы внутри контактных участков менее подвижны, обладая меньшим запасом свободной энергии, чем на всех других участках поверхности, то от свободных, неконтактных участков к контактным переходит значительно больше атомов, чем в обратном направлении. В результате происходит расширение контактного участка с одновременным сближением геометрических центров соприкасающихся частиц, т.е. происходит усадка.
Если рассматривать не две, а три соприкасающиеся частицы, образующие пору, то можно установить, что под влиянием поверхностной миграции атомов пора будет сфероидизироваться, не изменяясь в объеме. Поэтому усадка порошкового тела в процессе поверхностной диффузии наблюдаться не будет – количество атомов, ушедших с выпуклой поверхности поры, будет равно количеству атомов, перешедших на приконтактные участки.
Поверхностная диффузия атомов вызывает сглаживание поверхности соприкасающихся частиц, что увеличивает поверхность контакта и приводит к сфероидизации пор. Кроме того, поверхностная диффузия обеспечивает перемещение атомов с поверхностей крупных пор на поверхность мелких (при сообщающихся порах).
Объемнаядиффузиявещества
Перемещение атомов в объеме частицы представляет собой транспортный механизм, который является основой многих процессов, происходящих как в твердом кристаллическом теле, так и в порошковом.
Формулирование и развитие основных представлений о механизме диффузионного блуждания атомов в кристаллической решетке связано с работами Я.И. Френкеля: перемещение атомов в кристаллической решетке есть последовательное замещение ими вакансий, причем коэффициент диффузии атомов D связан с равновесной концентрацией вакансий С0 и коэффициентом их диффузии D' выражением
D = C0D'. |
(2.44) |
С учетом величин C0 = e-Eв/kT и D' = D0 e-Eа/kT
Процессы порошковой металлургии. Курс лекций |
-327- |

II. ФОРМОВАНИЕ И СПЕКАНИЕ ИЗДЕЛИЙ ИЗ МЕТАЛЛИЧЕСКИХ И НЕМЕТАЛЛИЧЕСКИХ ПОРОШКОВ
Лекция 14 Механизмы массопереноса при твердофазном спекании
D = D0 e -(Eв+Еа)/kT =D0 e-Eо/kT, |
(2.45) |
где Е0 – энергия активации диффузии.
Величина энергии образования вакансий Ев для большинства металлов составляет порядка 1/3 от энергии активации диффузии Е0.
Наличие избыточных вакансий (С > С0) приводит к увеличению коэффициента диффузии и, как правило, к понижению ее энергии активации Е0.
Диффузионные потоки атомов описывают два уравнения Фика:
m = –DS(ðC/ðx) |
(2.46) |
и
ðС/ðt = D(ð2C/ðx2), |
(2.47) |
где т – количество вещества, диффундирующее в единицу времени через площадку S при градиенте концентрации вакансий дС/дх (знак «минус» означает, что диффузия атомов происходит в сторону убывания их концентрации).
Нужно сказать, что навстречу потоку атомов движется равный им по величине (но не массе!) поток вакансий.
В общем случае принято рассматривать не сколько механизмов движения вакансий, которые характеризуются различными источниками и стоками вакансий (табл. 2.7). Рассмотрим детальные характеристики всех случаев:
1. Вогнутая поверхность «шейки» – выпуклая поверхность частиц.
Вакансии движутся из области их высокой концентрации вблизи вогнутой поверхности «шейки» в область более низкой их концентрации на выпуклой поверхности частиц. При этом атомы движутся в противоположном направлении. Результатом этого транспортного пути является рост приконтактных участков, сфероидизации пор. Если атомы, «стекающие» к вогнутой поверхности «шеек», идут лишь с поверхности частиц, то, как это следует из ранее рассмотренной модели из трех частиц, не следует ожидать усадки спекаемого порошкового тела.
2. Вогнутая поверхность «шейки» – границы зерен.
Вакансии движутся через кристаллическую решетку из области контакта к границам зерен, существующим внутри частиц, где концентрация вакансий ниже.
Вакансии по сетке границ зерен могут выходить на габаритную поверхность спекаемого порошкового тела. Атомы, двигаясь в противоположном направлении, достигают приконтактных участков, способствуя росту «шеек» и сфероидизации пор. Если атомы двигаются от внешней поверхности зерен, находящихся внутри частицы, возможна усадка в результате транспорта материала по этому пути. Отметим, что движение атомов вдоль
Процессы порошковой металлургии. Курс лекций |
-328- |
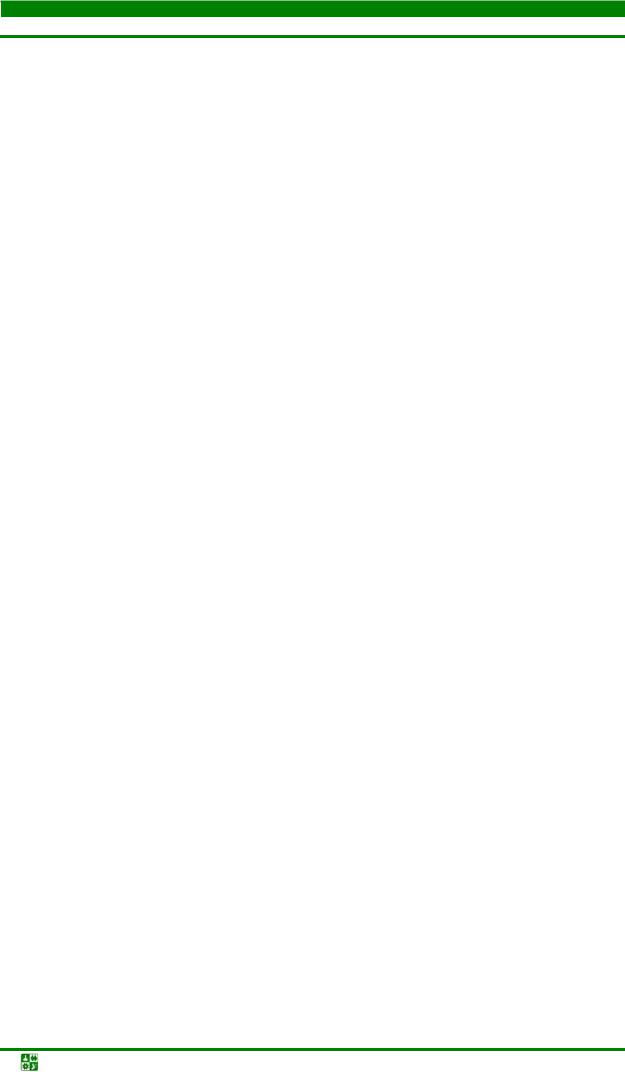
II. ФОРМОВАНИЕ И СПЕКАНИЕ ИЗДЕЛИЙ ИЗ МЕТАЛЛИЧЕСКИХ И НЕМЕТАЛЛИЧЕСКИХ ПОРОШКОВ
Лекция 14 Механизмы массопереноса при твердофазном спекании
границ зерен противоречит теории механизма диффузионного перемещения, так как границы зерен, строго говоря, не являются кристаллическими телами.
Таблица 2.7
Источники и стоки избыточных вакансий
Слу- |
Источник избыточных |
Стоки для избыточ- |
Эффекты от диффузии |
|
чай |
вакансии |
ных вакансий |
атомов |
|
1 |
Вогнутые поверхности |
Выпуклые поверх- |
Рост «шеек», сфероидизация |
|
«шеек» |
ности частиц |
пор |
||
2 |
Вогнутые поверхности |
Границы зерен |
Рост «шеек», сфероидизация и |
|
«шеек» |
усадка пор |
|||
3* |
Вогнутые поверхности |
Дислокации |
Рост «шеек», сфероидизация и |
|
«шеек» |
усадка пор |
|||
4 |
Поверхность сферических |
Поверхности более |
Укрупнение (коалесценция) |
|
пор |
крупных пор |
пор |
||
5 |
Поверхность сферических |
Границы зерен |
Укрупнение и усадка пор |
|
пор |
||||
6 |
Поверхность сферических |
Дислокации |
Укрупнение и усадка пор |
|
пор |
||||
7* |
Дислокации |
Границы зерен |
Укрупнение и усадка пор |
|
8* |
Дислокации |
Поверхности час- |
Рост «шеек», сфероидизация |
|
тиц |
пор |
|||
|
|
|||
9 |
Границы зерен |
Границы зерен |
Рост «шеек», усадка пор |
* – случай считается маловероятным.
3. Вогнутая поверхность «шейки» – дислокации.
Диффузионные потоки по этому пути по своей сущности и результатам могут быть описаны аналогично предыдущему случаю, однако считаются маловероятными.
4. Мелкие сферические поры – крупные поры.
С учетом зависимости концентрации вакансий от радиуса поры (2.42), следует признать наличие градиентов концентрации вакансий между поверхностями пор разного размера. В результате диффузии через кристаллическую решетку вещество переносится с поверхности крупных пор на поверхность мелких, мелкие поры исчезают (растворяются), а более крупные увеличиваются в размерах; при этом общий суммарный объем пор не меняется, т.е. усадка не имеет места.
5. Сферические поры – границы зерен.
Движение вакансий через кристаллическую решетку вещества и далее по границам к поверхности может приводить к усадке пор. Если же граница выходит к крупной поре, то скорее следует ожидать укрупнения (коалесценции) этой поры.
6. Сферические поры – дислокации.
Диффузия по этому пути может приводить к тем же результатам, что и в предыдущем случае, однако сам этот случай считается маловероятным.
7 и 8. Случаи считаются маловероятными.
Процессы порошковой металлургии. Курс лекций |
-329- |
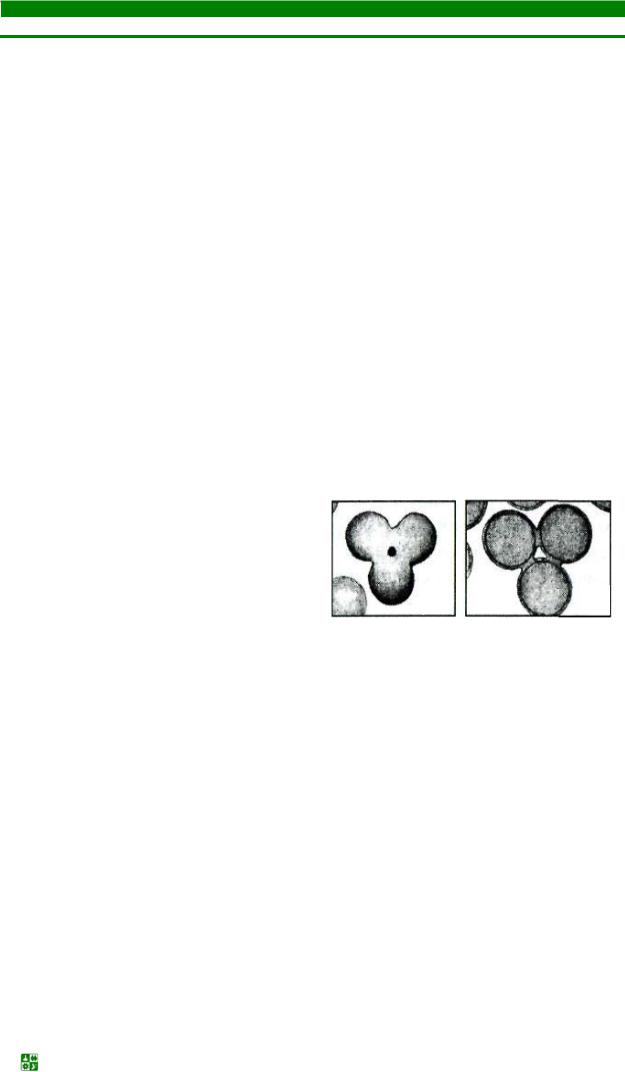
II. ФОРМОВАНИЕ И СПЕКАНИЕ ИЗДЕЛИЙ ИЗ МЕТАЛЛИЧЕСКИХ И НЕМЕТАЛЛИЧЕСКИХ ПОРОШКОВ
Лекция 14 Механизмы массопереноса при твердофазном спекании
9. Границы зерен. Границы зерен могут быть и источниками, и стоками для вакансий в зависимости от величины действующих на них напряжений. Теория крипа (вязкого течения) по Набарро-Херрингу основана на этих представлениях и может быть применена к спеканию. На границах, где действуют растягивающие напряжения, концентрации вакансий более высоки в сравнении со сжатыми границами. Для спекаемого порошкового тела с сильно развитой сеткой границ зерен диффузия атомов по этому механизму может приводить к росту «шеек» и усадке порошкового тела.
Анализируя возможные пути диффузии, можно сделать вывод о том, что существенную роль при спекании по механизму объемной диффузии имеют границы зерен (если исключить из рассмотрения четыре диффузионных пути с участием дислокаций).
Принято считать, что с позиции массопереноса по механизму объемной диффузии наиболее важными являются случаи 1, 2, 4 и 5.
Подтверждение, что объемная диффузия является механизмом, обычно контролирующим скорость спекания порошковых тел, было получено многими исследователями, изучавшими кинетику припекания частиц на моделях, причем во многих случаях результаты экспериментов удовлетворительно совпадают с предсказанными по теории.
Рис. 2.39. Структуры контактных областей, |
|
|
возникающих при взаимном припекании мед- |
|
|
ных проволок: а – поликристаллическая про- |
|
|
волока; б– монокристаллическая проволока |
а |
б |
|
Изучение структуры контактных областей, возникающих при взаимном припекании медной проволоки (рис. 2.39), показало, что рост площади контактного перешейка сопровождается сближением центров контактирующих проволок лишь в случае наличия в нем межзеренной границы.
Б.Я. Пинес предложил выражение, оценивающее время τп полного исчезновения («диффузионного» зарастания) изолированной сферической поры начального радиуса r0, находящейся в объеме вещества, где нет других источников вакансий, а их стоком является его внешняя габаритная поверхность:
τп = (kT/6γDV0)r03. |
(2.47) |
В любой момент времени изотермической выдержки τ при спекании такая изолированная сферическая пора будет иметь радиус r, равный
r3 = r03 – (6γDV0/ kT)· τ. |
(2.48) |
|
|
Процессы порошковой металлургии. Курс лекций |
-330- |
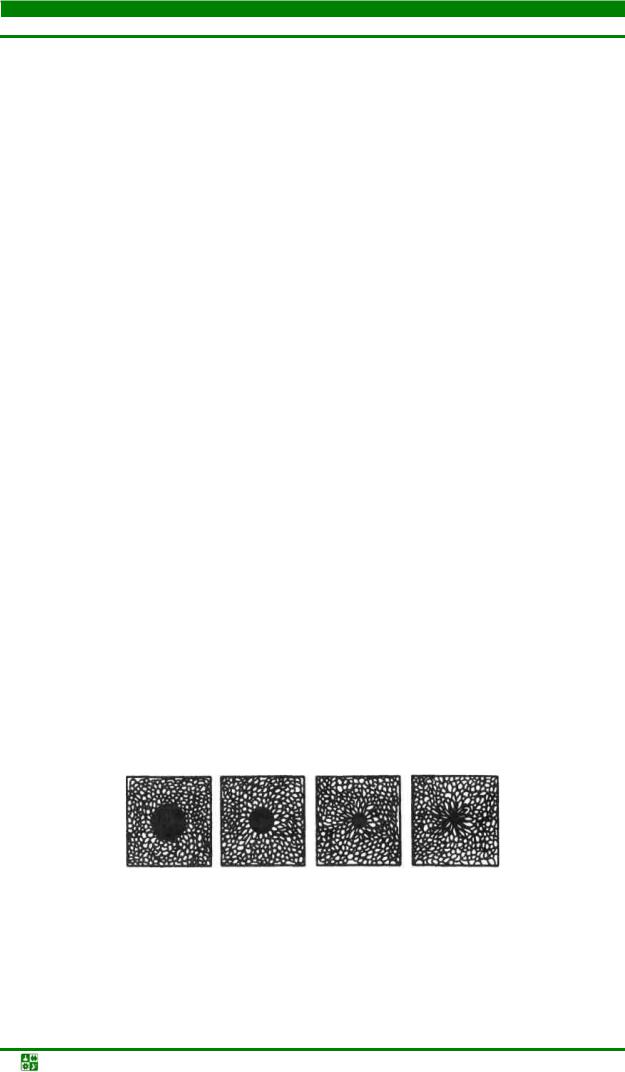
II. ФОРМОВАНИЕ И СПЕКАНИЕ ИЗДЕЛИЙ ИЗ МЕТАЛЛИЧЕСКИХ И НЕМЕТАЛЛИЧЕСКИХ ПОРОШКОВ
Лекция 14 Механизмы массопереноса при твердофазном спекании
Вязкоетечениевеществаприспекании
Вязкое течение. Около шестидесяти лет тому назад Я.И. Френкель сформулировал и количественно решил две задачи, связанные с реализацией при спекании порошкового тела механизма массопереноса путем вязкого течения: о заплывании изолированной поры и о слиянии двух соприкасающихся порошинок (сфер).
Фундаментальное положение его теоретических представлений – аналогия между вязким течением аморфных (происходящих по механизму непороговой ползучести путем кооперативного перемещения атомов) и кристаллических тел (также является процессом непороговой ползучести, но перемещение атомов не является процессом кооперативным). Вязкое течение кристаллических тел есть результат независимых элементарных актов (скачкообразных перемещений атомов) под влиянием капиллярного давления, вызванного кривизной поверхности частиц или различием напряжений в объеме порошкового тела по величине или знаку.
Для полного слияния двух контактирующих сфер (x = a0) необходимо время τп, равное
τп = (2/3 а0) (η/γ), |
(2.49) |
где а0 – начальный размер сферы; η – коэффициент вязкости вещества при данном состоянии структуры.
Для полного заплывания изолированной сферической поры (рис. 2.40) начального радиуса r0, который больше размера зерна или блока, где она расположена, необходимо время
τп = (4/3) (η/γ) а0. |
(2.50) |
Рис. 2.40. Этапы заполнения поры веществом вследствие диффузионно-вязкого течения
Радиус r такой поры в процессе изотермической выдержки τ равен
r = r0 – (3/4)( γ/η) τ. |
(2.51) |
Процессы порошковой металлургии. Курс лекций |
-331- |
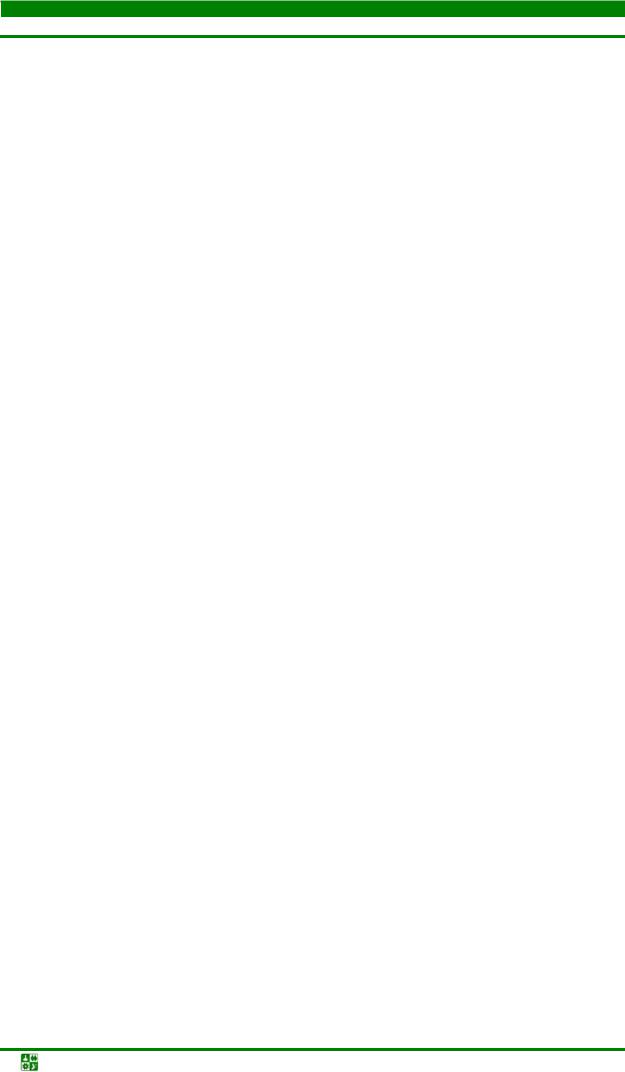
II. ФОРМОВАНИЕ И СПЕКАНИЕ ИЗДЕЛИЙ ИЗ МЕТАЛЛИЧЕСКИХ И НЕМЕТАЛЛИЧЕСКИХ ПОРОШКОВ
Лекция 14 Механизмы массопереноса при твердофазном спекании
Вязкое течение под давлением – это течение вещества, вызываемое внешними нагрузками и связанное с деформацией частиц.
Контрольныевопросыизадания
1.Перечислите механизмы транспорта вещества при спекании порошков.
2.Опишите механизм испарения конденсации вещества. Дайте его характеристику.
3.Опишите механизм поверхностной диффузии вещества при спекании частиц.
4.Приводит ли поверхностная диффузия к усадке порошкового тела?
5.С каким явлением деформационных превращений кристаллического тела связан механизм объемной диффузии?
6.Назовите возможные источники и стоки вакансий при спекании по механизму объемной диффузии.
7.Перечислите наиболее вероятные механизмы движения вакансий при спекании порошкового тела.
8.Приведите пример, доказывающий значительную роль границ при спекании порошкового тела.
9.Что такое вязкое течение?
Лекция15 Ползучестькристаллическихтел
План лекции
1.Механизмы непороговой и пороговой ползучести.
2.Признаки механизмов ползучести.
3.Проявление ползучести в спекаемом теле.
4.Диффузионно-вязкое течение по механизмам Набарро-Херринга- Лифшица и диффузионно-аккомодационному механизму.
Я.Е. Гегузин, излагая физическую природу явлений, сопровождающих нагрев порошкового тела, сформулировал следующее определение: «Спека-
ние – диффузионная ползучесть под воздействием сил поверхностного на-
тяжения». Такое понимание родственности процессов спекания и ползучести возникло еще у Я.И. Френкеля, а затем было развито в работах Набарро, Херринга, Пинеса и Кучинского.
Процессы порошковой металлургии. Курс лекций |
-332- |
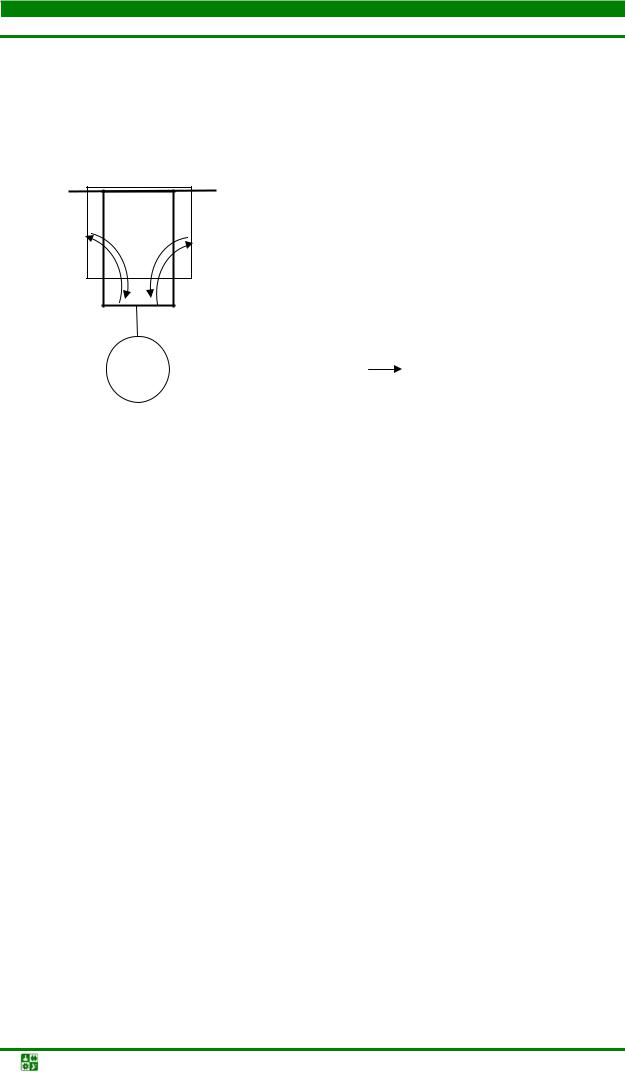
II. ФОРМОВАНИЕ И СПЕКАНИЕ ИЗДЕЛИЙ ИЗ МЕТАЛЛИЧЕСКИХ И НЕМЕТАЛЛИЧЕСКИХ ПОРОШКОВ
Лекция 15 Ползучесть кристаллических тел
Для того чтобы понять, что такое «ползучесть», рассмотрим поведение не имеющего внутренних границ и дефектов тела (идеального монокристалла) в форме цилиндра, один конец которого жестко закреплен, а к другому подвешен груз (рис. 2.41).
Рис. 2.41. Модель механизма ползучести (стрелками указаны направления потоков вакансий ( ) и атомов ( ), возникающих под действием создаваемых напряжений)
Масса этого груза меньше той, которая способна создать напряжения, превышающие σт монокристалла. Предполагается, что напряжения в любых точках объема кристалла совершенно одинаковы. Различия в напряжениях ощутимы только на поверхности: за счет подвешенного груза в торцевых поверхностях кристалла (по оси груза) возникают растягивающие, а в боковых
– сжимающие напряжения.
Таким образом, вблизи торцевых поверхностей концентрация вакансий по сравнению с равновесной повышена, а на боковых поверхностях понижена. Градиент концентрации вакансий инициирует их движение – от торцевой поверхности кристалла к его боковым поверхностям. Навстречу потоку вакансий (в противоположном направлении) движется поток атомов. В результате этих процессов кристалл удлиняется – атомы уходят с боковой на торцевую поверхность. Это и есть ползучесть кристалла, связанная с диффузионным механизмом перемещения атомов, поэтому ее называют диффузионной ползучестью.
Спекание порошкового тела, содержащего соприкасающиеся порошинки и пустоту (поры), сопровождается ползучестью вещества (материала) этого тела.
Механизмы ползучести (деформирования) кристаллического тела в области достаточно высоких температур спекания могут быть различными. Выделяют непороговые механизмы, определяющие деформирование при сколь угодно малых напряжениях, и пороговые механизмы, проявляющие себя при напряжениях, превосходящих некоторое предельное.
При непороговом механизме деформирования кристаллическое тело ведет себя подобно ньютоновской жидкости, отличаясь от нее тем, что коэффициент текучести его вещества зависит от структурного состояния тела и
Процессы порошковой металлургии. Курс лекций |
-333- |
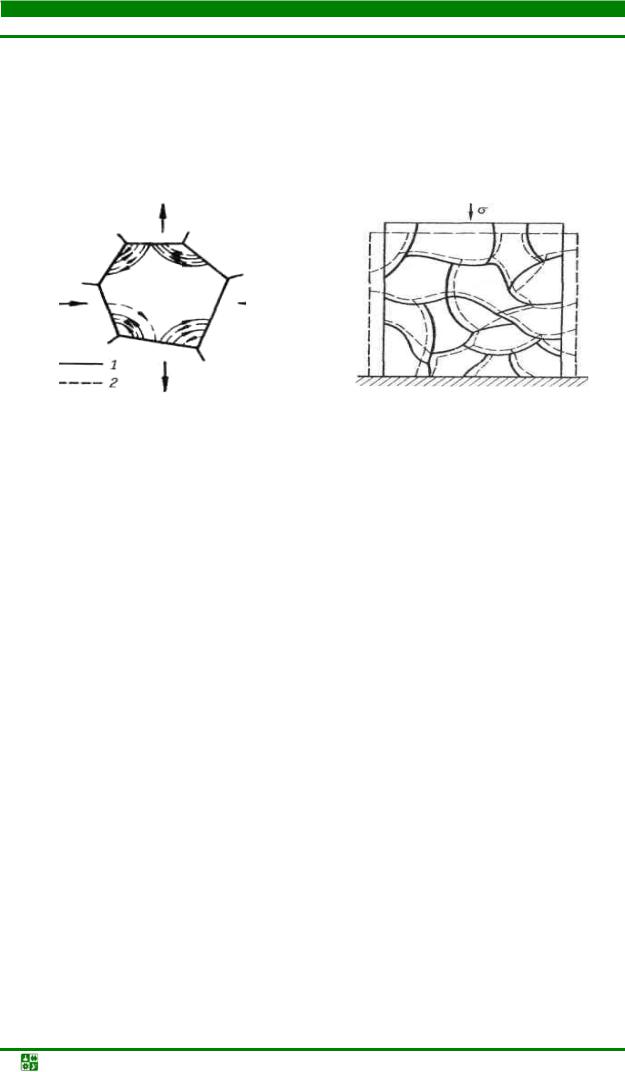
II. ФОРМОВАНИЕ И СПЕКАНИЕ ИЗДЕЛИЙ ИЗ МЕТАЛЛИЧЕСКИХ И НЕМЕТАЛЛИЧЕСКИХ ПОРОШКОВ
Лекция 15 Ползучесть кристаллических тел
может изменяться во времени. При превышенииσ т возбуждаются пороговые механизмы, при которых ползучесть может являться следствием перемещения дислокаций, которые преодолевают различные препятствия (дислокационные стенки, микровключения и пр.). Необходимо отметить, что одновременно с действием механизмов пороговой ползучести могут действовать и механизмы непороговой ползучести.
Рис. 2.42. Схема диффузионных |
Рис. 2.43. Схема деформирования поликри- |
потоков вакансий (1) и атомов (2) |
сталлического образца вследствие диффу- |
|
зионно-вязкого преобразования формы зерен |
Общим признаком всех механизмов непороговой ползучести является направленный диффузионный поток вакансий (или, что то же самое, поток атомов в противоположном направлении), который возникает в пределах каждого из элементов структуры из-за градиента концентраций вакансий
(рис. 2.42).
Этот поток может привести к изменению формы отдельного зерна без изменения его объема. Существенным в этом процессе является то, что диффузионные потоки в пределах отдельного зерна не создают потока в масштабах всего порошкового тела. Деформирование всего порошкового тела как целого является процессом самосогласованным в том смысле, что на их гр а- ницах раздела не возникают нарушения сплошности и изменение формы зерна зависит от изменения формы зерен, находящихся с ним в непосредственном соседстве (рис. 2.43).
Можно сравнить этот процесс с деформированием тела, состоящего из множества соприкасающихся эластичных оболочек, которые заполнены песком, – движение (пересыпание) песчинок в каждой из оболочек приводит к изменению формы всего тела.
Самосогласованное изменение формы элементов структуры (отдельных частиц) порошкового тела приводит к направленному перемещению их центров тяжести, которое подобно перемещению молекул при течении вязкой жидкости.
И.М. Лифшиц показал, что этот процесс должен сопровождаться скольжением кристаллов (частиц) друг относительно друга. Таким образом, вязкое течение кристаллических тел при малых нагрузках и диффузионное
Процессы порошковой металлургии. Курс лекций |
-334- |
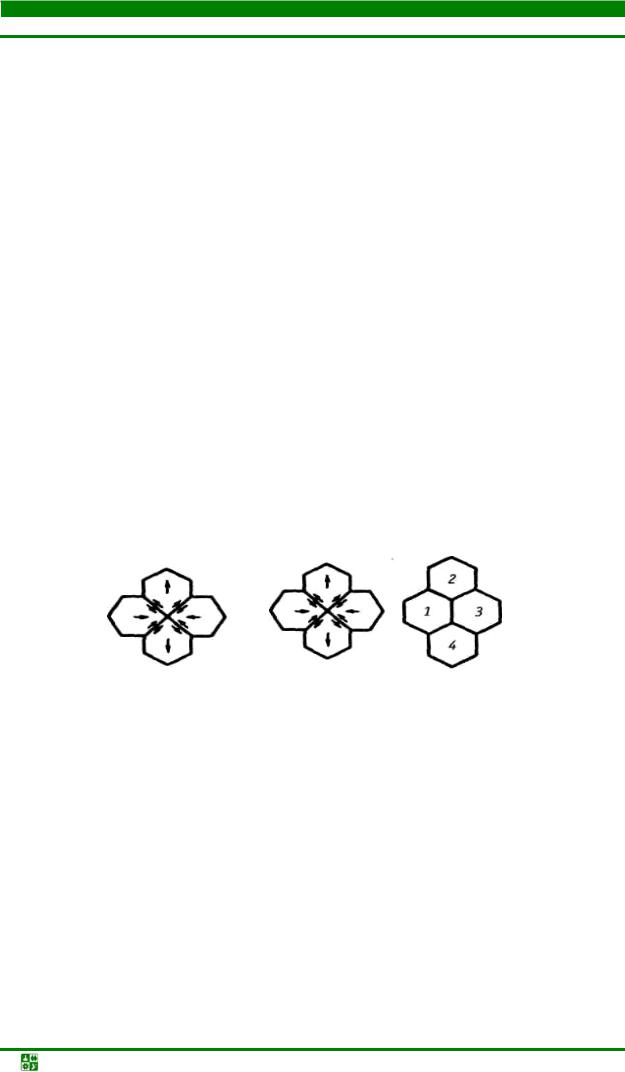
II. ФОРМОВАНИЕ И СПЕКАНИЕ ИЗДЕЛИЙ ИЗ МЕТАЛЛИЧЕСКИХ И НЕМЕТАЛЛИЧЕСКИХ ПОРОШКОВ
Лекция 15 Ползучесть кристаллических тел
перераспределение вещества за счет градиента концентраций вакансий в объеме элементов его структуры – идентичные процессы, в основе которых лежит вакансионный механизм. Поэтому принято говорить о диффузионновязком течении (диффузионной ползучести) порошковых тел при спекании.
Рассмотренный механизм деформирования порошкового тела носит название механизма Набарро-Херринга-Лифшица. Он относится к идеализированному кристаллическому телу, где сетка «аморфизованных» границ является единственным признаком неравновесности, тогда как в реальных порошковых телах имеется значительное количество одиночных краевых дислокаций, движение («переползание») которых в поле напряжений может существенно определять кинетику ползучести. С этим связана наблюдаемая неустановившаяся ползучесть в режиме непорогового деформирования и ее зависимость от предыстории образца.
Около сорока лет тому назад М.Ф. Эшби и Р.А. Ферралла предложили диффузионно-аккомодационный механизм течения поликристаллических структур, согласно которому деформация каждого зерна может нарушать их соседство (в отличие от механизма диффузионно-вязкого течения по Набар- ро-Херрингу-Лившицу, когда каждое зерно, деформируясь, не меняет своих соседей). В этом процессе макроскопическая деформация является следствием двух процессов – взаимного скольжения соприкасающихся зерен и диффузионной подстройки (аккомодации) их формы к форме зерен непосредственного окружения (рис. 2.44).
Рис. 2.44. Последовательность этапов преобразования формы соседних зерен по механизму диффузионной подстройки
Для осуществления аккомодации зерен необходим диффузионный перенос массы вещества, составляющей около 14 % от объема зерна, как механизмом объемной, так и механизмом граничной диффузии. Принципиально важным является взаимное смещение зерен как целого с учетом возможности появления и залечивания зерно-граничных пор, существенно облегчающих аккомодацию. Диффузионно-аккомодационный механизм может отчетливо проявляться в пористых структурах, где в связи с наличием пустоты аккомодационная подстройка должна быть существенно облегчена
(рис. 2.45).
Процессы порошковой металлургии. Курс лекций |
-335- |
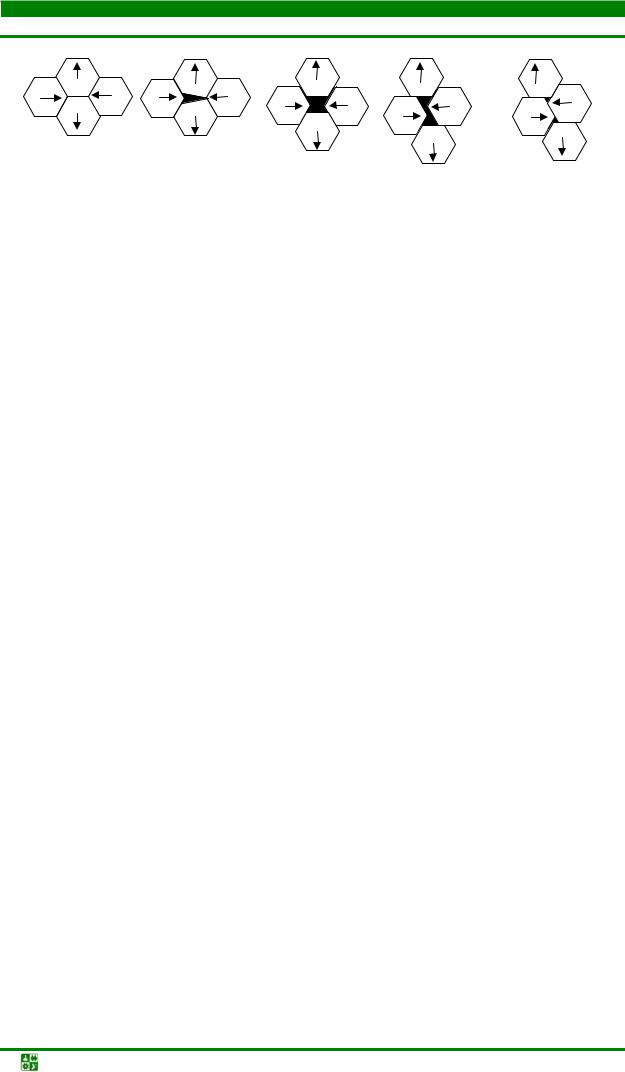
II. ФОРМОВАНИЕ И СПЕКАНИЕ ИЗДЕЛИЙ ИЗ МЕТАЛЛИЧЕСКИХ И НЕМЕТАЛЛИЧЕСКИХ ПОРОШКОВ
Лекция 15 Ползучесть кристаллических тел
|
A |
2 E |
A |
B |
E |
1 |
B |
||||
|
D |
3 |
|
D |
|
|
C |
4 F |
C |
|
F |
A |
B D |
|
2 |
|
B |
D |
3 |
||
|
B D |
1 |
|
|
|
B |
D |
||
|
|
|
4 |
I |
II |
III |
IV |
V |
Рис. 2.45. Последовательные этапы (I –V) изменения взаимного расположения зерен с участием в процессе межзеренной граничной пористости
Пороговая ползучесть кристаллических тел связана с проявлением механизмов, действующих при напряжениях, которые превосходят величину напряжений, необходимых для преодоления препятствий, сдерживающих движение дислокаций.
Торможение дислокаций может быть связано с их взаимодействием друг с другом или обусловлено различными локализованными дефектами (стопорами), расположенными в плоскости движения дислокации. К таким дефектам относят точечные дефекты и их скопления, выделения посторонней фазы (например, оксидов на поверхности частиц), дислокации в других системах скольжения, пересекающих плоскость, в которой движется рассматриваемая дислокация. Сами стопоры могут обладать различной степенью подвижности, в том числе быть и неподвижными.
На ползучесть кристаллических тел при спекании существенное влияние оказывает дефектность их структуры. Известно, что деформация порошкового тела обнаруживается уже в процессе его нагрева до температуры изотермического режима.
Ее называют неустановившейся ползучестью (когда скорость процесса убывает со временем), и она может быть значительной, если в исходном состоянии структура порошкового тела существенно искажена и его нагрев осуществляют под нагрузкой.
В изотермических условиях спекания установившемуся (стационарному) режиму ползучести также предшествует этап неустановившейся ползучести, отличный от указанного для режима нагрева. Ползучесть, происходящая при нагреве порошкового тела, зависит от режима нагрева, который влияет также на кинетику ползучести в наступившем изотермическом режиме.
Процессы, происходящие при неустановившейся ползучести в изотермическом режиме, обычно связывают с «залечиванием» неравновесных дефектов кристаллической решетки, имея в виду не только дефекты, локализованные в ее объеме, но и различные неровности (искривления) поверхностей, ограничивающих элементы структуры порошкового тела. Отметим, что в объектах, нагрев которых не сопровождается изменением состояния их
Процессы порошковой металлургии. Курс лекций |
-336- |
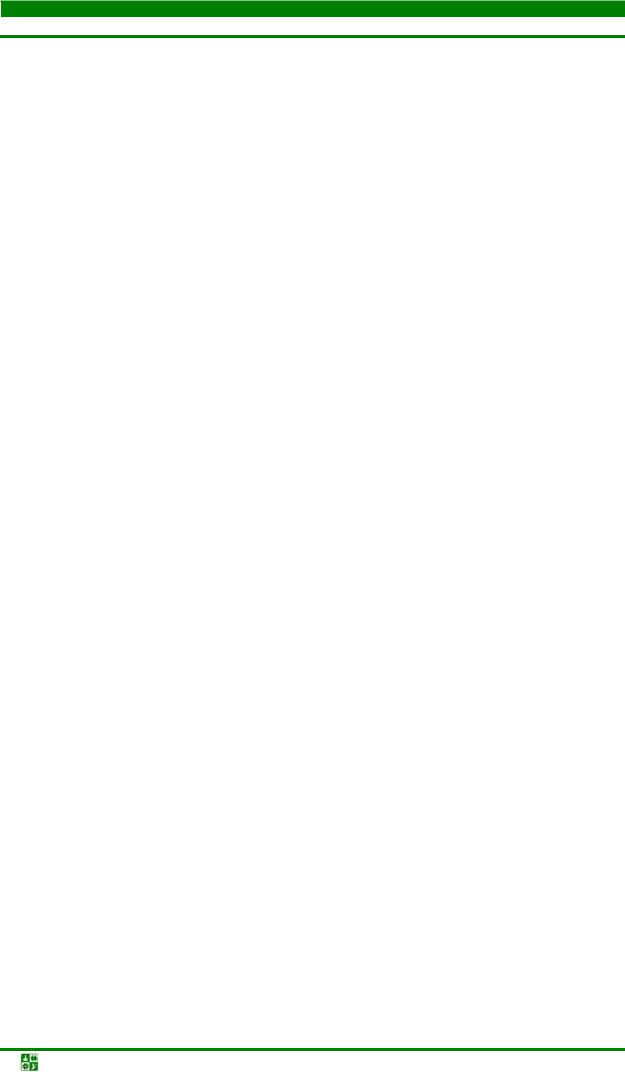
II. ФОРМОВАНИЕ И СПЕКАНИЕ ИЗДЕЛИЙ ИЗ МЕТАЛЛИЧЕСКИХ И НЕМЕТАЛЛИЧЕСКИХ ПОРОШКОВ
Лекция 15 Ползучесть кристаллических тел
кристаллической решетки («равновесные» структуры), режим нагрева не влияет на кинетику ползучести в изотермическом режиме.
В процессе изотермического спекания текучесть вещества не остается постоянной и с увеличением длительности нагрева уменьшается, что связано с восстановлением искажений кристаллической решетки. Поэтому повышенная текучесть порошкового тела в начале спекания обусловливается большой концентрацией в нем дефектов, исправление которых резко ускоряет диффузию, постепенно уменьшающуюся во времени.
Считается установленным, что уплотнение нагреваемого порошкового тела происходит в результате как диффузионно-вязкого течения (диффузионной ползучести), так и обычных процессов объемной диффузии.
Контрольныевопросыизадания
1.Что такое ползучесть?
2.Связано ли явление ползучести с изменение объема (усадкой) порошкового тела?
3.Назовите известные вам механизмы ползучести.
4.Чем обусловлено торможение процессов непороговой ползучести?
5.В каком случае проявляется механизм пороговой ползучести?
6.Что влияет на механизм ползучести?
7.Охарактеризуйте особенности общепризнанных механизмов ползу-
чести.
8.Что такое диффузионно-вязкое течение?
Лекция16 Укрупнениечастицприспекании. Уплотнениепорошковоготела
План лекции
1.Рекристаллизация частиц порошкового тела при спекании.
2.Объемные изменения при спекании.
3.Стадии уплотнения.
4.Зональное обособление при усадке.
Рекристаллизациячастицпорошковоготелаприспекании
При нагреве порошковых тел происходит рост (укрупнение) частиц, называемый рекристаллизацией. Образование частиц, более крупных по размеру, чем исходные, протекает при этом так же, как и рост зерен в литых ме-
Процессы порошковой металлургии. Курс лекций |
-337- |

II. ФОРМОВАНИЕ И СПЕКАНИЕ ИЗДЕЛИЙ ИЗ МЕТАЛЛИЧЕСКИХ И НЕМЕТАЛЛИЧЕСКИХ ПОРОШКОВ
Лекция 16 Укрупнение частиц при спекании. Уплотнение порошкового тела
таллах. Вместе с тем процессы рекристаллизации в компактных металлах и в нагреваемых металлических порошках тождественны не полностью из-за наличия в порошковых телах большой свободной поверхности.
Крупные частицы образуются за счет переноса вещества при общей границе с частицы меньшего размера на частицу большего размера, который происходит путем перемещения атомов через межчастичные границы в сторону частиц с меньшей величиной свободной энергии и поперек контактных участков.
Движущая сила рекристаллизации определяется стремлением системы перейти в более равновесное состояние с меньшей суммарной поверхностью границ. Разница свободных энергий частиц по обе стороны границы между ними определяет направление движения границы к центру ее кривизны.
Установлена закономерность, согласно которой кристаллы, имеющие больше шести граней, будут расти до некоторого предельного размера; если же этих граней меньше шести, то кристалл будет уменьшаться в размере до его полного исчезновения. Схема роста кристаллов приведена на рис. 2.46 (цифры обозначают число границ кристалла, стрелки – направления движения границ). Кристаллы с шестью и более гранями в сечении образуют вогнутые границы, а если граней меньше шести, то их поверхности выпуклы.
Рис. 2.46. Схема роста частицв порошковом теле при рекристаллизации
Скорость роста частиц обратно пропорциональна радиусу кривизны границы и может быть описана выражением
d – d0 = K τ0,5, |
(2.52) |
где d0 – линейный размер частицы до начала роста; d – линейный размер частицы, выросший за время т; К – коэффициент, учитывающий природу материала.
С ростом межчастичных контактов границы получают возможность передвигаться (прорастать) из одной частицы в другую; этот процесс называют межчастичной собирательной рекристаллизацией.
Практически рост частиц продолжается до некоторого их среднего размера в связи с тормозящим влиянием посторонних включений, находящихся
Процессы порошковой металлургии. Курс лекций |
-338- |
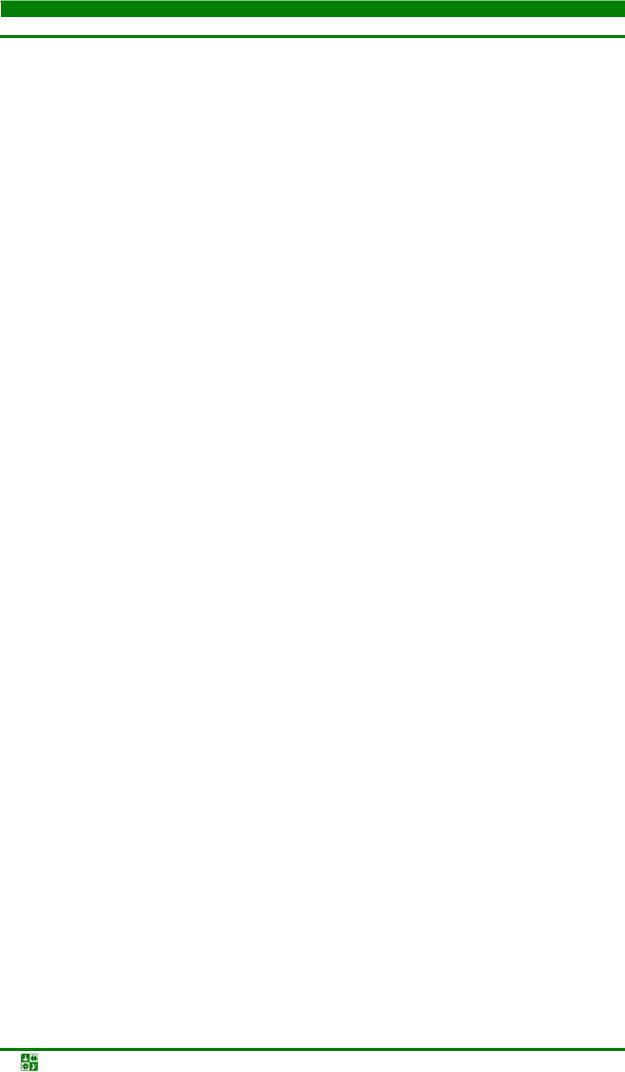
II. ФОРМОВАНИЕ И СПЕКАНИЕ ИЗДЕЛИЙ ИЗ МЕТАЛЛИЧЕСКИХ И НЕМЕТАЛЛИЧЕСКИХ ПОРОШКОВ
Лекция 16 Укрупнение частиц при спекании. Уплотнение порошкового тела
по границам частиц (пор, пленок на поверхности порошинок, межкристаллитного вещества и т.п.).
Спеченные порошковые тела характеризуются сравнительно небольшими размерами частиц. Межчастичная собирательная рекристаллизация в значительной степени зависит от размера частиц порошка, так как с его увеличением возрастает и размер пор в порошковом теле, а их тормозящее влияние на движение межчастичных границ уменьшается. При нагреве порошковых тел из мелких порошков контуры отдельных частиц исчезают раньше, чем в случае более крупных порошков.
В процессе спекания имеет место также рекристаллизация обработки, связанная с ростом частиц, деформированных перед нагревом. У пористых порошковых тел рекристаллизация обработки проявляется значительно меньше, чем у беспористых материалов: в пористом теле при его обработке деформируются прежде всего участки контактов между частицами, а внутри частиц напряжения могут не измениться сколько-нибудь существенно, и значительного воздействия предварительной обработки на структуру полученного материала не наблюдается.
Для большинства металлических порошков температура начала роста частиц и их конечный размер почти не зависят от давления прессования.
Рекристаллизация в пористых порошковых телах начинается при температуре 0,3–0,4Тпл и при 0,75–0,85Тпл она протекает интенсивно, завершая формирование структуры спекаемого изделия. Процесс рекристаллизации идет одновременно с усадкой и другими явлениями, имеет с ними косвенную связь и в значительной степени зависит от них. Необходимо отметить, что рост частиц вызывает лишь перемещение и перераспределение вещества в пределах объема пористого порошкового тела, но не приводит к сокращению объема пор и уплотнению спекаемого изделия.
Объемныеизмененияприспекании
В результате спекания плотность порошкового тела в подавляющем большинстве случаев возрастает и происходит уменьшение его размеров (линейная усадка) и объема (объемная усадка) как следствие «зарастания» пор, приводящего к сокращению их числа и суммарного объема.
Однако в начальный период спекания в порошковой формовке могут развиваться процессы, приводящие к ее расширению в направлении, противоположном сжатию при формовании (рис. 2.47).
Процессы порошковой металлургии. Курс лекций |
-339- |
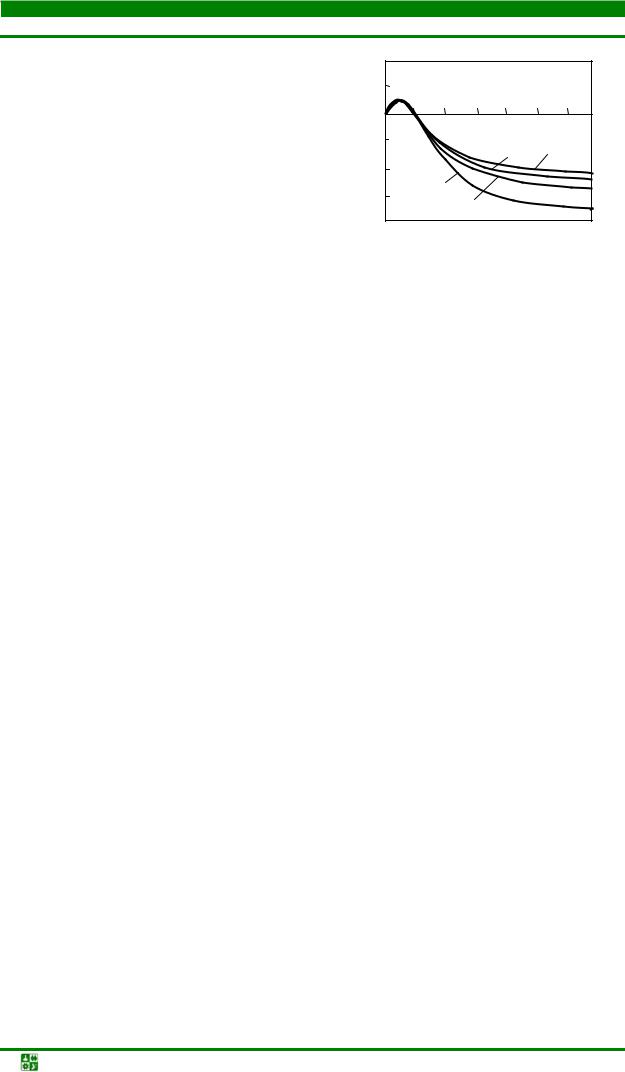
II. ФОРМОВАНИЕ И СПЕКАНИЕ ИЗДЕЛИЙ ИЗ МЕТАЛЛИЧЕСКИХ И НЕМЕТАЛЛИЧЕСКИХ ПОРОШКОВ
Лекция 16 Укрупнение частиц при спекании. Уплотнение порошкового тела
Рис. 2.47. Линейная усадка брикетов железа, спрессованных при разных давлениях,
МПа: 1 – 400; 2 – 600; 3 – 800; 4 – 1 000
Усадка, % Рост, %
1 |
|
|
|
|
0 |
1 |
2 3 4 |
5 τ, ч |
|
1 |
||||
|
3 |
4 |
||
3 |
|
|||
|
1 |
|
||
5 |
|
|
||
|
2 |
|
Это имеет место при удалении паров воды и газов вследствие десорбции, испарения или выгорания смазок (связок) и релаксации (снятия) упругих напряжений, которые приводят к разрушению межчастичных связей и уменьшению суммарной площади межчастичных контактов.
С повышением температуры нагрева до 0,4–0,5Тпл заканчивается релаксация упругих напряжений, продолжается дегазация и выгорание смазок (связок), а имеющиеся на поверхности частиц пленки оксидов восстанавливаются, в результате чего неметаллические межчастичные контакты заменяются металлическими, их площадь увеличивается, а прочность порошкового тела резко возрастает. При температуре >0,6Тпл наступает заключительная (изотермическая) стадия спекания, во время которой завершается восстановление оксидов, контакты между частицами становятся полностью металлическими и имеют место все основные процессы, характеризующие нагрев, – сглаживание поверхности частиц, сфероидизация и коалесценция пор, рекристаллизация частиц и, прежде всего, упрочнение порошкового тела.
Стадииуплотнения
Условно процесс усадки (уплотнения) порошкового тела при изотермическом спекании можно разделить на три последовательные стадии.
Ранняя стадия. Плотность порошкового тела мала и скорость уплотнения определяется процессами, происходящими в приконтактных областях, структура и геометрия которых играют существенную роль. Скорость смещения и объемного деформирования частиц высока.
Промежуточная стадия. Плотность порошкового тела достаточно велика и уменьшение объема каждой из пор может происходить практически независимо. Пористая матрица из частиц ведет себя как вязкая среда, и ее уплотнение равномерно по всему объему (при равномерном распределении пор).
Поздняя стадия. Порошковое тело содержит отдельные изолированные поры, которые залечиваются (зарастают) в результате диффузионного растворения в матричном веществе с выходом вакансий на внешнюю (габаритную) поверхность спекаемой заготовки.
Резкой и отчетливой границы между этими тремя стадиями (первая из которых характерна и для неизотермического спекания) нет, и на промеж у-
Процессы порошковой металлургии. Курс лекций |
-340- |
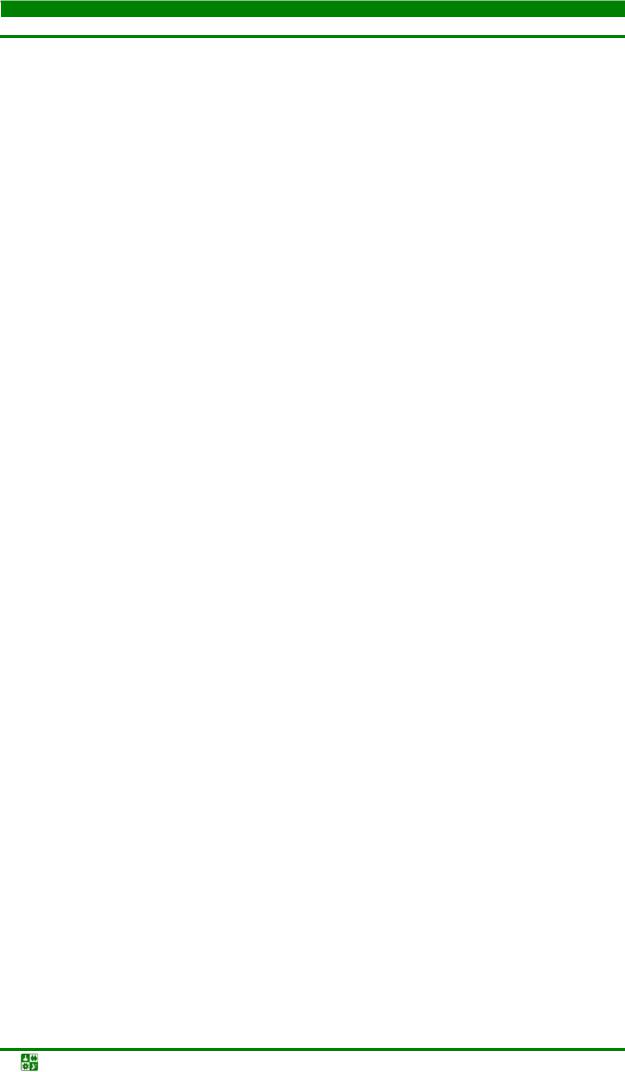
II. ФОРМОВАНИЕ И СПЕКАНИЕ ИЗДЕЛИЙ ИЗ МЕТАЛЛИЧЕСКИХ И НЕМЕТАЛЛИЧЕСКИХ ПОРОШКОВ
Лекция 16 Укрупнение частиц при спекании. Уплотнение порошкового тела
точной стадии уплотнение порошкового тела может определяться процессами, характерными для ранней и (или) поздней стадии.
Одной из характерных особенностей усадки нагреваемого порошкового тела является замедление ее скорости при изотермической выдержке: с увеличением температуры спекания скорость повышения плотности увеличивается, но и уменьшение этой скорости с повышением температуры спекания происходит более интенсивно.
В.А. Ивенсен показал, что при изотермическом спекании любых металлических порошков снижение скорости сокращения объема пор закономерно связано с уменьшением их объема. Отношение скоростей сокращения объема пор в два произвольно взятые момента времени τ1 и τ2 для данного изотермического спекания равно
(dV/dτ)1/(dV/dτ)2= (V1/V2)n, |
(2.53) |
где V1, V2 – суммарные объемы пор в моменты времени τ1 и τ2; n – показатель, характеризующий интенсивность торможения усадки.
Из выражения (2.53) вытекает уравнение кинетики изменения порис-
тости:
V = Vн (q·m·τ + 1)-1/m, |
(2.54) |
где V – объем пор после изотермической выдержки в течение времениτ; Vн – начальный объем пор; m – константа, характеризующая интенсивность снижения скорости сокращения объема пор во времяспекания, равная m = n – 1; q – константа, имеющая значение скорости относительного сокращенияединицы объема пор в момент начала изотермического спекания, равнаяq = – (dV/dτ)н/(1/Vн) и имеющая размерность «время-1».
Для порошков металлов и неметаллов значение всегда уменьшается с ростом температуры, если процесс спекания не проходит с образованием закрытых пор.
Существенной особенностью усадки является то, что в случае дальнейшего повышения температуры (после длительной изотермической выдержки, когда уже наблюдалось снижение усадки), скорость усадки снова возрастает
(рис. 2.48).
Необходимо отметить, что способность порошкового тела к усадке не может быть охарактеризована каким-либо одним параметром. Высокая начальная скорость уплотнения может сочетаться с торможением усадки в конце процесса, и достигнутая в этом случае плотность может быть меньше, чем при низкой начальной скорости уплотнения и ее менее интенсивном снижении в процессе спекания.
Процессы порошковой металлургии. Курс лекций |
-341- |
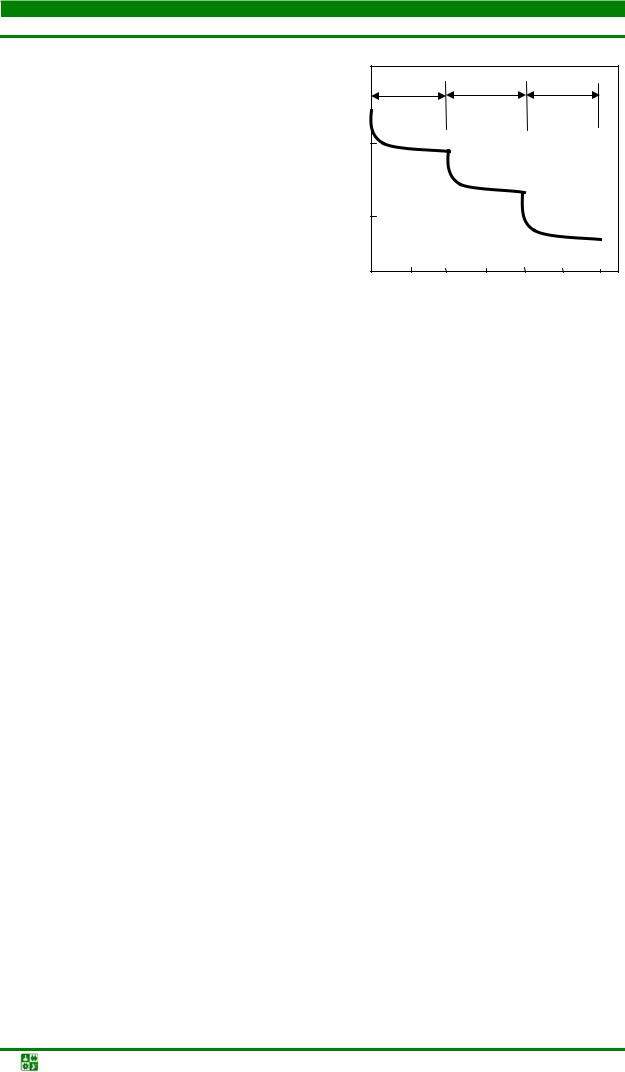
II. ФОРМОВАНИЕ И СПЕКАНИЕ ИЗДЕЛИЙ ИЗ МЕТАЛЛИЧЕСКИХ И НЕМЕТАЛЛИЧЕСКИХ ПОРОШКОВ
Лекция 16 Укрупнение частиц при спекании. Уплотнение порошкового тела
Рис. 2.48. Усадка при изотермическом спекании при ступенчатом подъеме температуры
(по В.А. Ивенсену):а – 600 оС; б – 740 оС;
в – 880 оС
H |
|
|
|
|
|
|
V/V |
|
|
|
|
|
|
|
а |
|
б |
|
в |
|
0,8 |
|
|
|
|
|
|
0,4 |
|
|
|
|
|
|
0 |
1 |
2 |
3 |
4 |
5 |
6 |
|
|
|
|
|
Время, ч |
Стабилизация кристаллической структуры, уменьшающая величину усадки, и увеличение плотности нагреваемого порошкового тела, сопровождающееся повышением его микроскопической вязкости, влияют на кинетику уплотнения. Влияние дефектов называют структурным фактором (по М.Ю. Бальшину), а влияние упрочнения (увеличение плотности пористого порошкового тела уменьшает его деформацию) – геометрическим фактором (по В.А. Ивенсену).
Зональноеобособлениеприусадке
Вреальных формовках из полидисперсных порошков всегда имеются поры разных размеров, набор которых случаен (хотя во многих случаях распределение пор по размеру в объеме формовки близко к нормальному закону). Такое неоднородное объемное распределение пор по размерам является причиной часто встречающейся неоднородной усадки порошковой формовки, когда ее отдельные локальные объемы с мелкими порами уплотняются при нагреве в большей степени, чем соседние с ними объемы формовки с более крупными порами. Это явление локализации уплотнения М.Ю. Бальшин назвал зональным обособлением усадки при спекании порошковых тел.
Впроцессе спекания обычно наблюдается обособление частиц в отдельные зоны (группы), поэтому усадка имеет место в пределах многих зон (групп), в каждой из которых частицы стягиваются к ее геометрическому центру. Это ведет к сближению частиц и уменьшению пористости внутри группы, но одновременно и к обособлению групп, их взаимному удалению и росту межгрупповой пористости. Зональное обособление тормозит усадку спекаемого порошкового тела и задерживает рост его контактного сечения.
Процесс зонального обособления усадки может привести к росту наиболее крупных межгрупповых пор при одновременном уменьшении наиболее мелких внутригрупповых пор и к повышению газопроницаемости отдельных
Процессы порошковой металлургии. Курс лекций |
-342- |
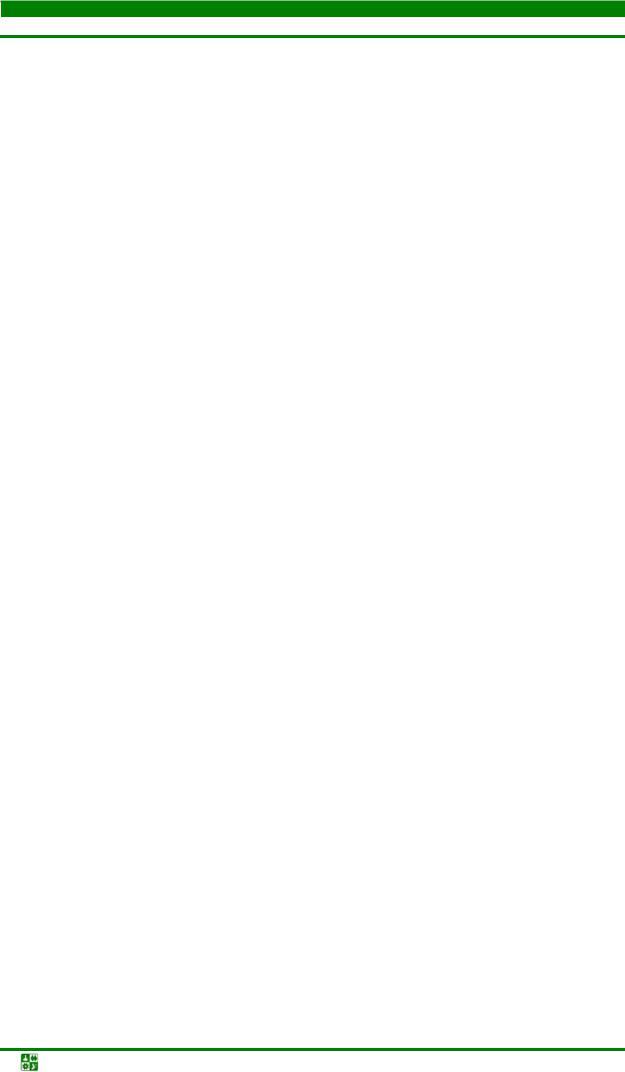
II. ФОРМОВАНИЕ И СПЕКАНИЕ ИЗДЕЛИЙ ИЗ МЕТАЛЛИЧЕСКИХ И НЕМЕТАЛЛИЧЕСКИХ ПОРОШКОВ
Лекция 16 Укрупнение частиц при спекании. Уплотнение порошкового тела
участков спеченного материала по сравнению с исходной у порошковых формовок.
Контрольныевопросыизадания
1.Что является движущей силой процесса рекристаллизации?
2.Перечислите основные закономерности процесса рекристаллиза-
ции.
3.Что такое «рекристаллизация обработки»?
4.Назовите температуру начала процесса рекристаллизации.
5.Почему на ранней стадии процесса спекания порошкового тела наблюдается увеличение его объема?
6.Перечислите стадии уплотнения порошкового тела при спекании и охарактеризуйте их.
7.Назовите параметры порошкового тела, которые характеризуют структурный и геометрический факторы.
8.С чем связано зональное обособление усадки при спекании порошкового тела?
Лекция17 Влияниетехнологическихфакторов
напроцессспеканияоднокомпонентныхсистем. Спеканиемногокомпонентныхсистем
План лекции
1.Факторы, определяющие процесс спекания порошкового тела.
2.Активирование процессов спекания.
Факторы, определяющиепроцессспеканияпорошковоготела
К технологическим факторам, влияющим на процесс спекания, относят: свойства исходных порошков, давление формования, температуру, продолжительность и атмосферу спекнаия.
Свойства исходных порошков. Условия получения и дисперсность металлических порошков определяют их поведение при спекании. Так, с увеличением дисперсности порошка процесс спекания формовок, изготовленных из него, ускоряется и он считается более активным, а механические и электрические свойства спеченных изделий растут. Интенсификации спекания
Процессы порошковой металлургии. Курс лекций |
-343- |
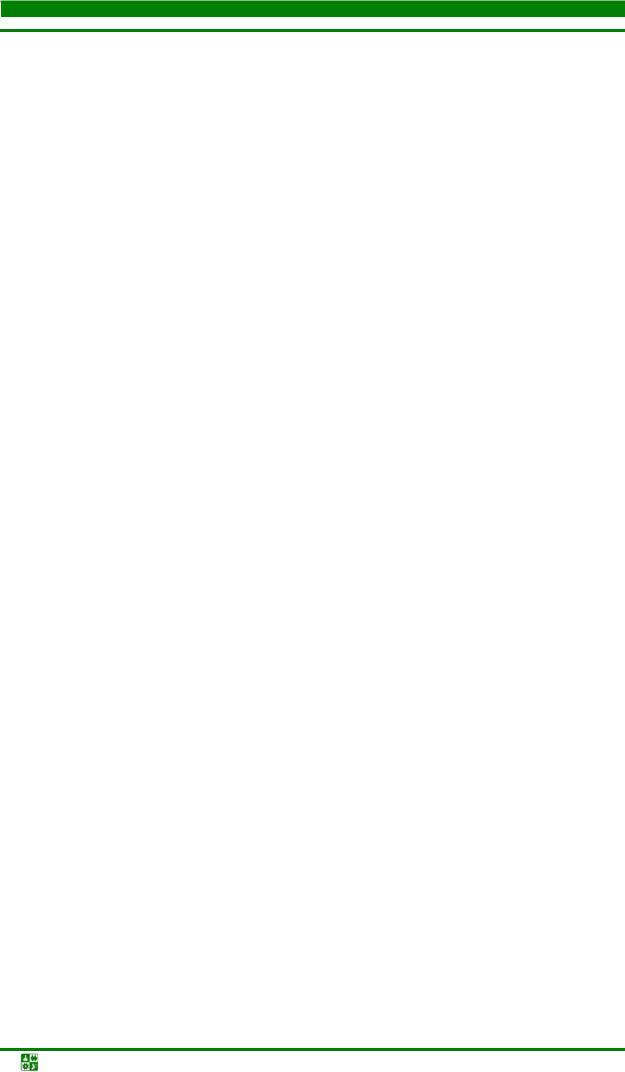
II. ФОРМОВАНИЕ И СПЕКАНИЕ ИЗДЕЛИЙ ИЗ МЕТАЛЛИЧЕСКИХ И НЕМЕТАЛЛИЧЕСКИХ ПОРОШКОВ
Лекция 17 Влияние технологическихфакторов на процессспекания однокомпонентных систем. Спекание многокомпонентных систем
способствуют оксиды, содержащиеся в большем количестве в мелких порошках и восстанавливающиеся в процессе нагрева при спекании. Наиболее эффективная толщина оксидных пленок на поверхности частиц меди, железа и молибдена составляет, соответственно, 40–50, 40–60 и около 60 нм (более толстые слои оксида затрудняют металлизацию контакта между частицами).
Губчатая металлическая поверхность, образующаяся после исчезновения оксида, оказывается более активной, чем поверхность, изначально свободная от оксидной пленки. С увеличением удельной поверхности исходного порошка усадка формовки при спекании возрастает. Наличие выступов и впадин на поверхности частиц активирует усадку за счет повышения содержания дефектов вблизи впадин и образования микропор с малым радиусом кривизны на стыках частиц.
Структура изделий, спеченных из высокодисперсных порошков, отличается наличием большого числа крупных зерен, выросших в процессе спекания. Усадка при спекании уменьшается, если исходный порошок или формовку из него подвергнуть отжигу, при котором происходит сглаживание рельефа поверхности частиц, их срастание и устранение дефектов кристаллического строения.
В общем случае на изменение плотности и свойств порошковых формовок при спекании влияют величина частиц, состояние их поверхности и степень несовершенства кристаллического строения, химический состав порошка и другие факторы.
Давление формования. Его влияние на результаты спекания проявляется главным образом через следующие факторы: изменение общей площади контактов и плотности порошковой формовки; упругие и пластические свойства материала частиц порошка; деформацию или разрушение поверхностных слоев частиц порошка; захлопывание в изолированных порах порошковой формовки воздуха и других газов.
С увеличением исходной плотности формовок их объемная и линейные усадки при спекании уменьшаются. Одна из возможных причин этого заключается в том, что порошковое тело с большей относительной плотностью характеризуется большим коэффициентом вязкости, что и затрудняет усадку. Другая причина – наблюдаемое постоянство отношения объема пор в нагреваемом порошковом теле до и после спекания. Пределы давлений прессования, в которых наблюдается постоянство объемов, зависят от пластичности металла.
Если плотность формовки неодинакова по высоте, то после спекания можно часто наблюдать «талию» (усадка в средней части формовки больше, чем у ее торцов, если начальная пористость вблизи них была меньше). Однако в случае спекания мелкозернистых порошков происходит «выравнивание» пористости как между формовками с разной исходной плотностью, так и между местами с неодинаковой плотностью каждой изформовок.
Усадки при спекании прессовок в направлении приложения давления и в поперечном направлении, как правило, не совпадают, что связано с раз-
Процессы порошковой металлургии. Курс лекций |
-344- |
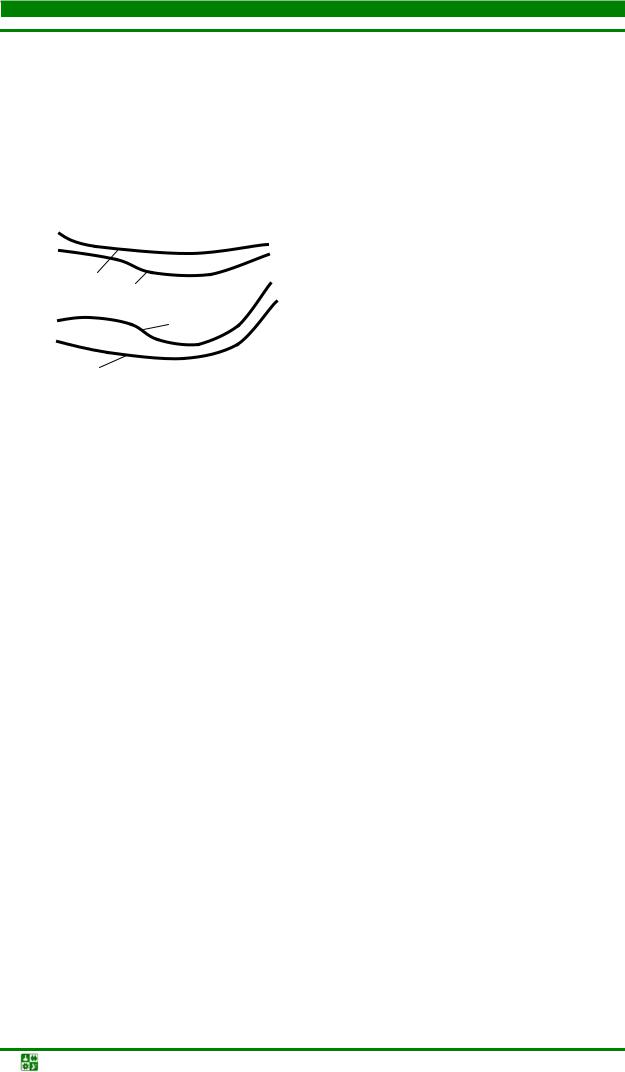
II. ФОРМОВАНИЕ И СПЕКАНИЕ ИЗДЕЛИЙ ИЗ МЕТАЛЛИЧЕСКИХ И НЕМЕТАЛЛИЧЕСКИХ ПОРОШКОВ
Лекция 17 Влияние технологическихфакторов на процессспекания однокомпонентных систем. Спекание многокомпонентных систем
личной величиной поверхностей контактов, формой и структурой частиц, природой их материала. Увеличение давления формования приводит к повышению всех показателей физических и механических свойств спеченных порошковых изделий – твердости, прочности на разрыв и при сжатии и др.
Температура спекания. Плотность порошковых изделий возрастает с повышением температуры спекания тем быстрее, чем ниже было давление формования заготовки из порошка (рис. 2.49).
Относительная плотность, %
4 |
3 |
Рис. 2.49. Влияние температуры спекания на |
|
|
2 |
относительную плотность: 1 – свободно на- |
|
|
сыпанный порошок; 2 – порошок, спрессо- |
||
|
|
ванный при малых давлениях; 3 – порошок, |
|
1 |
|
спрессованный при высоких давлениях; 4 – |
|
|
порошок, спрессованный при очень высоких |
||
|
|
||
|
|
давлениях |
|
Температура спекания, оС |
|||
|
На процесс спекания значительное влияние оказывает скорость подъема температуры. При быстром подъеме температуры в крупногабаритных порошковых формовках могут наблюдаться местные обособления усадки изза местных различий в температуре, что, в конечном счете, может привести к искажению их формы.
Прочность, как и плотность, обычно повышается с ростом температуры спекания. Показатели пластичности порошковых материалов увеличиваются с повышением температуры изотермической выдержки при спекании даже при падении их плотности и прочности (если это имело место).
Продолжительность спекания. Выдержка порошковой формовки при заданной температуре спекания вызывает сначала резкий, а затем более медленный рост ее плотности (рис. 2.50) и других свойств (рис. 2.51). Максимальная прочность достигается за довольно короткое время изотермической выдержки и при дальнейшем спекании она остается на том же уровне или даже несколько снижается. Достижение большей пластичности требует более длительного времени спекания, по-видимому, из-за необходимости обеспечения полного удаления кислорода из спекаемого материала.
Процессы порошковой металлургии. Курс лекций |
-345- |
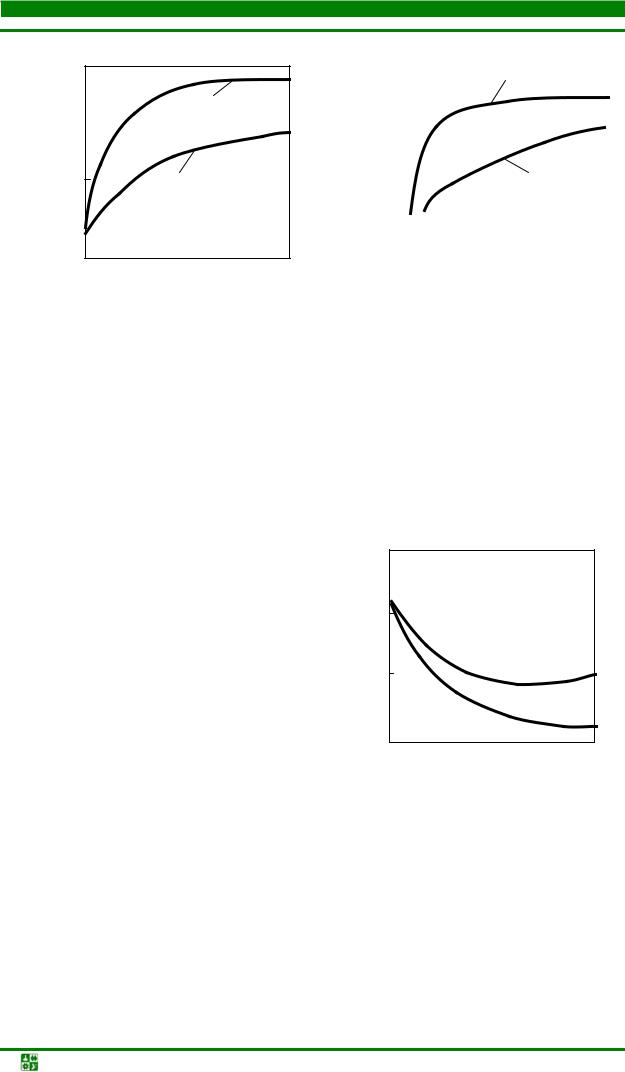
II. ФОРМОВАНИЕ И СПЕКАНИЕ ИЗДЕЛИЙ ИЗ МЕТАЛЛИЧЕСКИХ И НЕМЕТАЛЛИЧЕСКИХ ПОРОШКОВ
Лекция 17 Влияние технологическихфакторов на процессспекания однокомпонентных систем. Спекание многокомпонентных систем
100 |
|
Относительная плотность, % |
2 |
|
|
90 |
1 |
Время спекания
Рис. 2.50. Зависимость относительной плотно-
сти прессовок от длительности выдержки при изотермическом спекании: 1 – средние температуры спекания;2 – высокие температуры спекания
- |
|
1 |
|
Плотностьили относи |
тельноеудлинение |
||
2 |
|||
|
|
||
|
|
|
|
|
|
Время спекания, ч |
Рис. 2.51. Изменение прочности (1) и относи-
тельного удлинения (2) прессовок в зависимости от длительности выдержки при изо-
термическом спекании
На практике выдержка при спекании варьируется в довольно широких пределах (от нескольких десятков минут до нескольких часов) в зависимости от состава материала, исходной и требуемой плотности порошковой формовки, ее размера, типа и состава защитной среды, конструкции печи и т.д.
Рис. 2.52. Зависимость пористости прессовок из порошка меди от продолжительности выдержки при спекании в водороде и аргоне при 1 000 °С
Пористость, %
40 |
|
|
20 |
Ar |
|
0 |
H2 |
|
Время спекания, ч |
||
|
Атмосфера спекания. Сравнение результатов спекания порошковых тел, проводимого в различных средах, показывает, что при спекании в восстановительной среде достигается их большая плотность, чем при спекании в нейтральной среде (рис. 2.52). Восстановление оксидных пленок активирует миграцию атомов металла к контактным участкам не только на поверхности частиц, но и в их объеме, что способствует процессам, приводящим к уплотнению.
Очень полно и быстро проходит спекание в вакууме, которое по сравнению со спеканием в нейтральной среде в большинстве случаев начинается
Процессы порошковой металлургии. Курс лекций |
-346- |
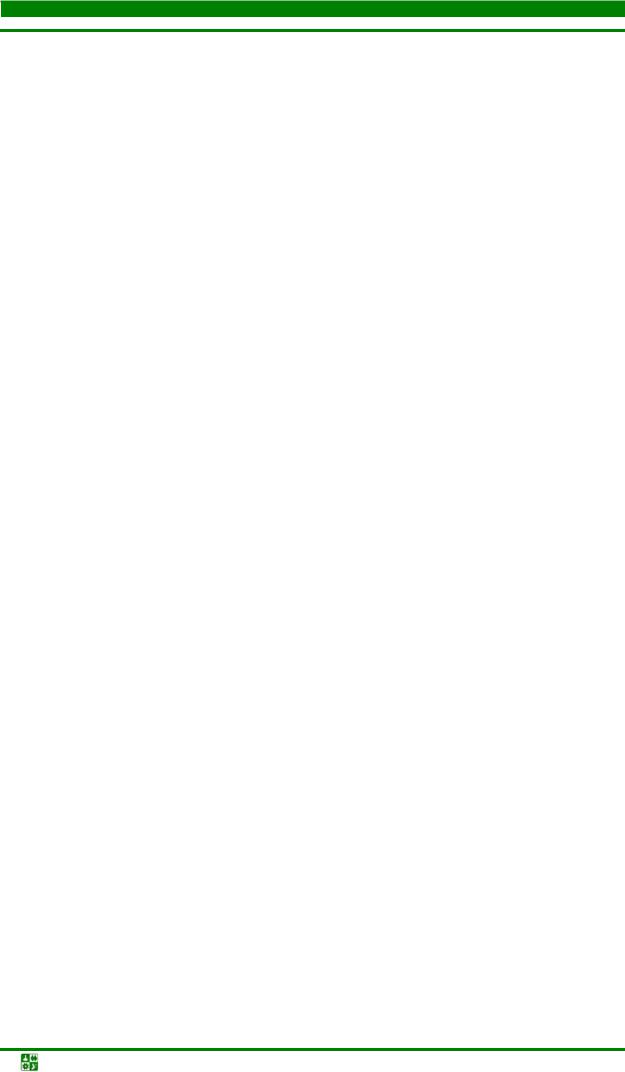
II. ФОРМОВАНИЕ И СПЕКАНИЕ ИЗДЕЛИЙ ИЗ МЕТАЛЛИЧЕСКИХ И НЕМЕТАЛЛИЧЕСКИХ ПОРОШКОВ
Лекция 17 Влияние технологическихфакторов на процессспекания однокомпонентных систем. Спекание многокомпонентных систем
при более низких температурах и дает повышенную плотность получаемого порошкового изделия.
Практика спекания в производственных условиях и экспериментальные результаты исследовательских работ показывают, что характер влияния газовых сред на уплотнение разных порошковых материалов может быть существенно различным и не все наблюдаемые изменения скорости усадки поддаются рациональному объяснению.
В.А. Ивенсен выделяет три наиболее характерных вида (механизма) такого влияния:
1)адсорбционное воздействие на величину энергии поверхности пор
иуровень действующих капиллярных сил;
2)травящее воздействие, повышающее шероховатость поверхности пор (при химическом взаимодействии с образованием летучих веществ;
3)торможение уплотнения, вызванное образованием пленки нелетучего соединения в результате химического взаимодействия вещества частиц порошка с компонентами газовой среды (происходит снижение поверхностной энергии порошкового тела и одновременно возможно непосредственное препятствование образованию и росту контактов между частицами спекаемого вещества).
Укажем также и на возможность различного поведения газовых сред, оказавшихся в какой-то момент внутри изолированных пор, возникших в порошковом теле в процессе спекания.
Активированиепроцессовспекания
По терминологии ГОСТ 17359-82, активированное спекание – это процесс спекания порошковой формовки при воздействии химических и физических факторов, вызывающих интенсификацию спекания. Необходимо отметить, что увеличение температуры и длительности выдержки не рассматриваются как активирующие физические факторы, так как их воздействие на результаты спекания является естественным.
В самом общем случае активирование спекания связано с более эффективным осуществлением транспортных механизмов благодаря тому, что изменяется состояние поверхности или контакта между частицами порошка, понижается энергия активации действующего транспортного механизма, изменяется тип транспортного механизма или меняются транспортные пути.
Например, известно, что если в состав связки или в атмосферу спекания ввести некоторые химические соединения (галогенид – хлористые или фтористые соединения), то можно значительно усилить усадку порошкового тела в процессе спекания.
Обычно методы активирования спекания подразделяют на две основные группы:
Процессы порошковой металлургии. Курс лекций |
-347- |
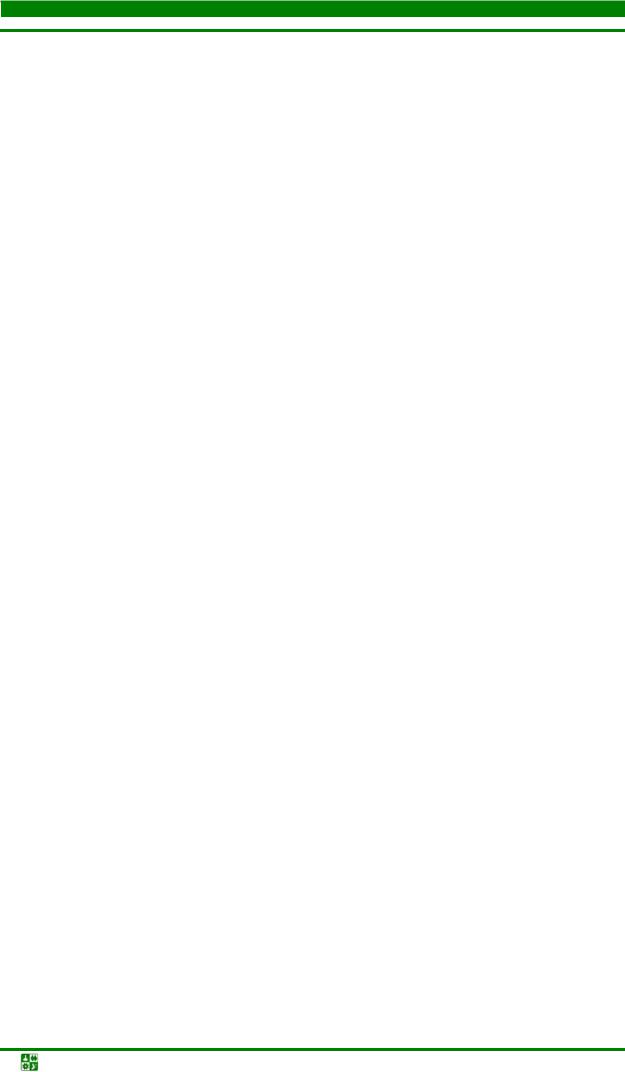
II. ФОРМОВАНИЕ И СПЕКАНИЕ ИЗДЕЛИЙ ИЗ МЕТАЛЛИЧЕСКИХ И НЕМЕТАЛЛИЧЕСКИХ ПОРОШКОВ
Лекция 17 Влияние технологическихфакторов на процессспекания однокомпонентных систем. Спекание многокомпонентных систем
химические, основанные на использовании окислительно-восстанови- тельных реакций, процессов диссоциации химических соединений, химического транспорта спекаемого вещества и др.;
физические, связанные с интенсивным измельчением порошка, воздействием на него облучением, циклическим изменением температуры при спекании (циклическое спекание), наложением магнитного поля на нагреваемую формовку и др.
Химические методы активированияспекания можно классифицировать:
по составу активаторов, их источникам (из газовой фазы, из засыпки или из примесей в спекаемом материале); по этапу введения (до спекания или в его процессе); поведению (активаторы остаются в спеченном изделии или нет).
К химическим способам активирования спекания относится изменение его атмосферы. Это один из наиболее простых и в то же время эффективных способов упрочнения получаемых порошковых изделий. Атомы металла на выступах поверхностей частиц (как наиболее активные) реагируют с соединениями, добавляемыми в атмосферу спекания. Образующееся соединение металла затем восстанавливается, и атомы металла конденсируются в местах с минимальным запасом свободной энергии (впадины на поверхности частиц, области межчастичных контактов и др.), благоприятствуя переносу вещества. Активированная атмосфера может благоприятно влиять на процесс спекания также вследствие удаления примесей и рафинирования спекаемого материала.
Активировать процесс спекания можно и вводя в состав порошка небольшое количество твердых примесных веществ – порошков металлов или неметаллов (в случае спекания керамики). Выполненные различными исследователями работы по химическому активированию спекания позволили сформулировать требования к подобной добавке:
1. Температура плавления добавки должна быть ниже, чем основного порошка, что обеспечивает большую диффузионную подвижность атомов добавки по сравнению с основой.
2. Вещество добавки должно быть поверхностно-активным по отношению к основному металлу, т.е. должно диффундировать по границам его зерен, образуя межзеренные прослойки. Это достигается при применении в качестве добавки переходных металлов (оксидов переходных металлов – в случае спекания керамики). При получении керамики в состав материала может вводиться от нескольких десятых до нескольких процентов добавок. Необходимо иметь в виду, что нужно тщательно измельчать материал подобной добавки – удельная поверхность частиц добавки должна быть равна удельной поверхности частиц основной фазы.
В случае использования в качестве добавок чистых металлов, основной металл должен хорошо растворяться и диффундировать в добавляемом, а добавляемый металл не должен растворяться в основном, что позволяет легкодеформируемым межзеренным прослойкам устойчиво существовать.
Процессы порошковой металлургии. Курс лекций |
-348- |
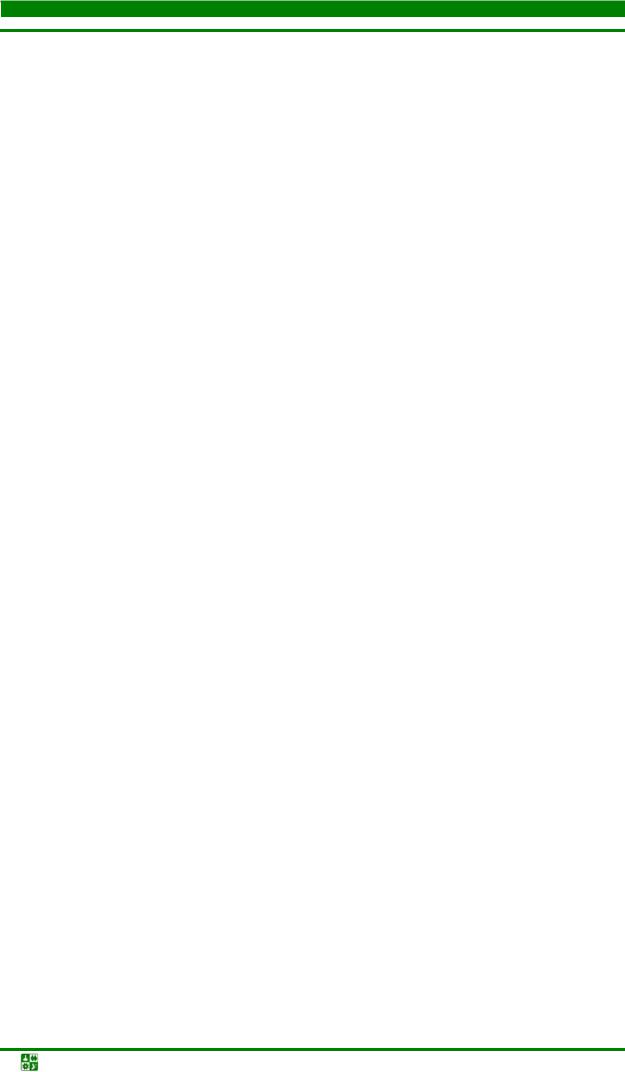
II. ФОРМОВАНИЕ И СПЕКАНИЕ ИЗДЕЛИЙ ИЗ МЕТАЛЛИЧЕСКИХ И НЕМЕТАЛЛИЧЕСКИХ ПОРОШКОВ
Лекция 17 Влияние технологическихфакторов на процессспекания однокомпонентных систем. Спекание многокомпонентных систем
Физические методы активирования спекания связаны, прежде всего, с
увеличением дисперсности порошка и дефектности кристаллической решетки вещества его частиц. Интенсивное измельчение частиц увеличивает их суммарную поверхность, повышая запас избыточной энергии порошка и увеличивая толщину «нарушенного слоя». Это, в свою очередь, способствует действию такого механизма массопереноса, как «поверхностная диффузия».
При спекании частиц, размер которых меньше нескольких десятых микрометра (величина «нарушенного слоя» сопоставима с размером частицы), возможно снижение температуры спекания на 150–200 оС. Кроме того, у металлических частиц такого размера наблюдается снижение температуры плавления (например, при диаметре частиц 10 нм примерно 30 % атомов находятся на поверхности частиц, что нарушает симметрию в распределении сил и масс по сравнению с объемом частиц). Кинетика уплотнения при активном спекании высокодисперсных металлических порошков отличается от кинетики объемных изменений при нагреве обычных (неактивных) порошков. При средних температурах нагрева (0,5–0,7Тпл) кинетика уплотнения соответствует пороговому механизму течения поликристаллического материала под действием капиллярных сил и зависит от проскальзывания зерен по границам и подстройки их формы путем зернограничного диффузионного переноса массы вещества.
Контрольныевопросыизадания
1.Перечислите факторы технологического процесса спекания, от которых зависят свойства получаемых изделий.
2.Какое влияние на процесс спекания оказывают свойства порошка?
3.Нарисуйте кривые, характеризующие влияние температуры спекания на относительную плотность спеченного тела для порошков, спрессованных при различных давлениях. Поясните ход этих кривых.
4.Изобразите зависимость относительной плотности прессовок от длительности выдержки при изотермическом спекании.
5.Как изменяется прочность прессовок в зависимости от длительности выдержки при изотермическом спекании?
6.Как влияет длительности выдержки при изотермическом спекании на относительное удлинение прессовок?
7.Как влияет среда при спекании на пористость спеченного изделия?
8.Перечислите методы и способы активирования процессов спекания.
Лекция18 Твердофазноеспеканиемногокомпонентныхсистем
План лекции
Процессы порошковой металлургии. Курс лекций |
-349- |

II. ФОРМОВАНИЕ И СПЕКАНИЕ ИЗДЕЛИЙ ИЗ МЕТАЛЛИЧЕСКИХ И НЕМЕТАЛЛИЧЕСКИХ ПОРОШКОВ
Лекция 18 Твердофазное спекание многокомпонентных систем
1.Виды твердофазного спекания многокомпонентных систем.
2.Спекание систем с полной взаимной растворимостью компонентов.
3.Спекание систем с ограниченной растворимостью компонентов.
4.Спекание систем с нерастворимыми (невзаимодействующими) компонентами
Видытвердофазногоспеканиямногокомпонентныхсистем
Порошковые материалы, используемые в различных отраслях техники, в подавляющем большинстве случаев представляют собой многокомпонентные системы, образование в которых необходимого сплава (фазового состава – для керамики) чаще всего происходит непосредственно при спекании.
Главная отличительная черта таких материалов – наличие неравенства концентрацией компонентов в различных объемах (микрообъемах) исходного порошкового тела (градиент химического состава).
Процесс спекания разнородных частиц также более сложен: одновременно с самодиффузией, обусловливающей перенос массы в область приконтактного перешейка, должна происходить гетеродиффузия (взаимодиффузия разнородных атомов), обеспечивающая выравнивание концентраций компонентов в пределах порошкового тела и зачастую приводящая к торможению его уплотнения при нагреве, а также формирующая межфазные поверхности.
В пористых порошковых телах, где кроме непосредственного контакта между частицами разнородных и взаиморастворимых металлов имеются свободные поверхности, кинетика процесса диффузионной гомогенизации осложняется одновременным осуществлением различных механизмов переноса массы, рассмотренных выше. Физические и механические свойства спеченных порошковых тел зависят от полноты гетеродиффузии, в связи с чем полезны все факторы, ей благоприятствующие: применение более дисперсных порошков; хорошее качество смешивания компонентов; повышение температуры спекания; удаление адсорбированных газов и пленок оксидов; увеличение исходной плотности формовок и пр.
Вместе с тем такие процессы, как десорбация газов, рафинирование нагреваемого материала от примесей, снятие остаточных напряжений (возникших при формовании), сглаживание рельефных пор и т.п. аналогичны соответствующим процессам, происходящим в однокомпонентных системах.
Процессы, сопровождающие нагрев многокомпонентной системы, в значительной мере определяются характером соответствующих диаграмм состояния. Поэтому принято различать следующие виды твердофазного спекания многокомпонентных систем:
спекание компонентов, обладающих полной (неограниченной) взаимной растворимостью;
спекание компонентов, обладающих ограниченной взаимной растворимостью;
Процессы порошковой металлургии. Курс лекций |
-350- |
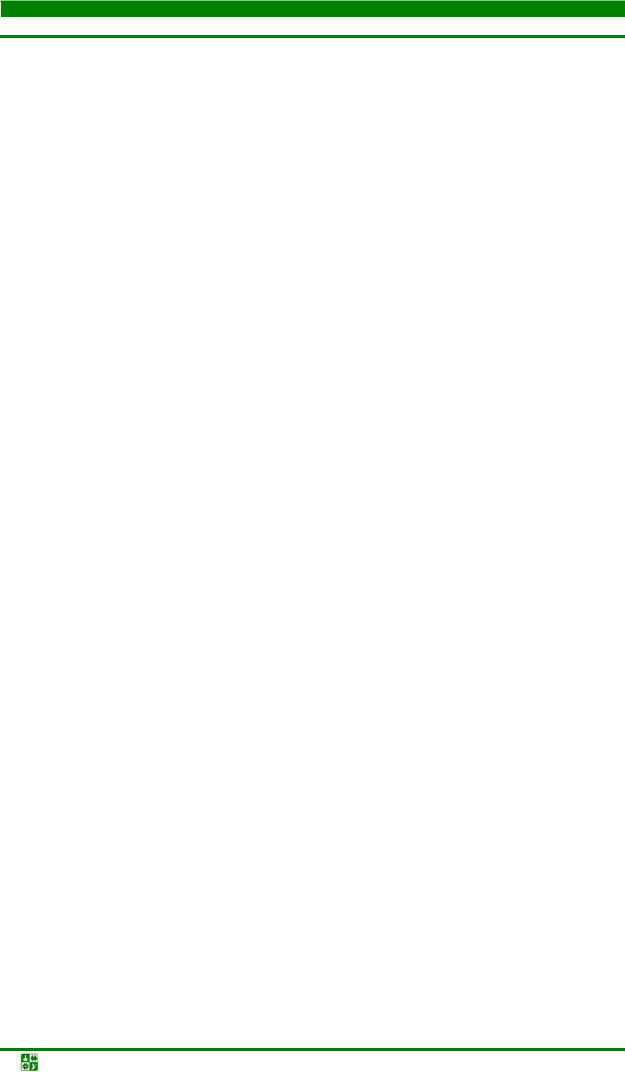
II. ФОРМОВАНИЕ И СПЕКАНИЕ ИЗДЕЛИЙ ИЗ МЕТАЛЛИЧЕСКИХ И НЕМЕТАЛЛИЧЕСКИХ ПОРОШКОВ
Лекция 18 Твердофазное спекание многокомпонентных систем
спекание компонентов, взаимно нерастворимых (невзаимодействующих).
Спеканиесистемсполнойвзаимнойрастворимостьюкомпонентов
В результате спекания таких систем образуется одна фаза (взаимный твердый раствор); на промежуточных стадиях спекания существуют несколько фаз: частицы исходных металлов и твердые растворы переменной концентрации.
Временная зависимость сокращения объема пор при спекании в условиях развития гетеродиффузии резко отличается от закономерности, присущей однофазному порошковому телу. Усадка порошкового тела при нагреве, как правило, меньше аддитивной, рассчитанной с учетом из возможной усадки каждого из компонентов. Это объясняется более низкой подвижностью атомов в твердых растворах по сравнению с чистыми металлами и невозможностью получить при смешивании исходных компонентов абсолютно однородную смесь, из-за чего при нагреве имеется большое количество контактов, скорость диффузии атомов через которые неодинакова.
Так, например, в системе Cu–Ni по мере повышения содержания никеля в меди усадка уменьшается и может происходить даже рост порошкового тела (проявление эффекта Френкеля). Это связано с большей в несколько раз величиной коэффициента диффузии меди в никель по сравнению с величиной коэффициента диффузии никеля в медь: в частицах меди образуются избыточные вакансии, коалесцирующие в поры, а частицы никеля увеличиваются в размерах из-за преобладания притока атомов меди над оттоком атомов никеля.
Интенсивность диффузионного взаимодействия компонентов при спекании растет с увеличением межфазной поверхности, которая максимальна при 50 %-м содержании фаз.
Кинетические закономерности уплотнения выявляют различия в поведении при спекании сплавов в зависимости от содержания второго компонента: для чистых металлов и малолегированных сплавов усадка практически исчерпывается за короткое время и наступает насыщение, а для высоколегированных сплавов скорость уплотнения остается значительной в течение длительного времени. Замедление насыщения процесса уплотнения в этом случае связано с образованием дополнительной диффузионной пористости.
Существенная особенность спекания заключается в том, что некоторые из контактов между одноименными и разноименными порошинками могут нарушаться (разрываться). Причины этого – напряжения в зоне контакта диффузионного происхождения, «исчезновение» порошинки (вследствие испарения или перемещения наповерхность другой порошинки) и др.
Для решения практических задач важен вопрос о необходимой степени гомогенизации по составу сплавов, образующихся при спекании: так как многие свойства порошковых тел определяются величиной и состоянием контактных поверхностей между частицами, в ряде случаев достижение полной гомогенизации сплава внутри частиц оказывается ненужным.
Процессы порошковой металлургии. Курс лекций |
-351- |
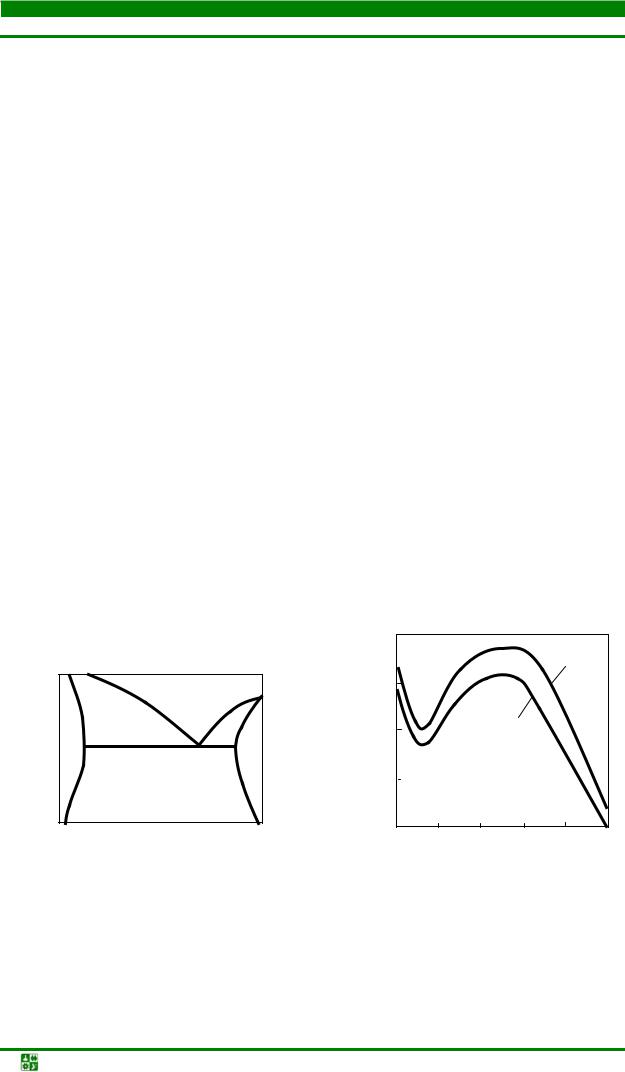
II. ФОРМОВАНИЕ И СПЕКАНИЕ ИЗДЕЛИЙ ИЗ МЕТАЛЛИЧЕСКИХ И НЕМЕТАЛЛИЧЕСКИХ ПОРОШКОВ
Лекция 18 Твердофазное спекание многокомпонентных систем
Гомогенизация шихты перед прессованием обеспечивает при спекании более полную и однородную усадку, а также более однородный состав и свойства изделий по всему объему. Больший эффект достигается приприменении вместо смеси порошков индивидуальных компонентов порошка, представляющего собой гомогенный сплав заданного состава.
Спеканиесистемсограниченнойрастворимостьюкомпонентов
В практике порошковой металлургии такие системы встречаются наиболее часто. Для них характерны диаграммы состояния как с эвтектикой и перитектикой, так и с химическими соединениями. При нагреве на промежуточных стадиях гомогенизации в порошковом теле присутствуют все фазы, имеющиеся на диаграмме состояния, практически независимо от исходного состава смеси порошков. Зависимости усадки от содержания элементов в сплаве отличны от линейных, а их характерный вид (направление выпуклости) может быть различным.
Системы с эвтектикой. В двухфазной области подобных систем кривая усадки имеет ярко выраженный максимум (рис. 2.53), соответствует примерно 50 %-му содержанию разнородных фаз, т.е. их наибольшей межфазной поверхности и, следовательно, максимальному диффузионному межфазному взаимодействию. Снижение усадки в области твердых растворов связано с обычным снижением диффузионной подвижности в них атомов.
В эвтектических системах при практическом отсутствии (или чрезвычайно малой) растворимости между фазами нет зависимости усадки от величины межфазной поверхности.
|
V/V, % |
|
1 |
|
|
|
|
|
10 |
|
|
α |
6 |
2 |
|
β |
|
|
|
|
|
|
|
|
2 |
|
|
|
α + β |
|
|
|
Cu 20 |
60 |
Ag |
|
а |
б |
|
Рис. 2.53. Диаграмма состояния (а) и концентрационная зависимость усадки (б) в системе Cu–Ag при температуре 700 °С и выдержке 30 (1) и 15 мин (2)
Процессы порошковой металлургии. Курс лекций |
-352- |
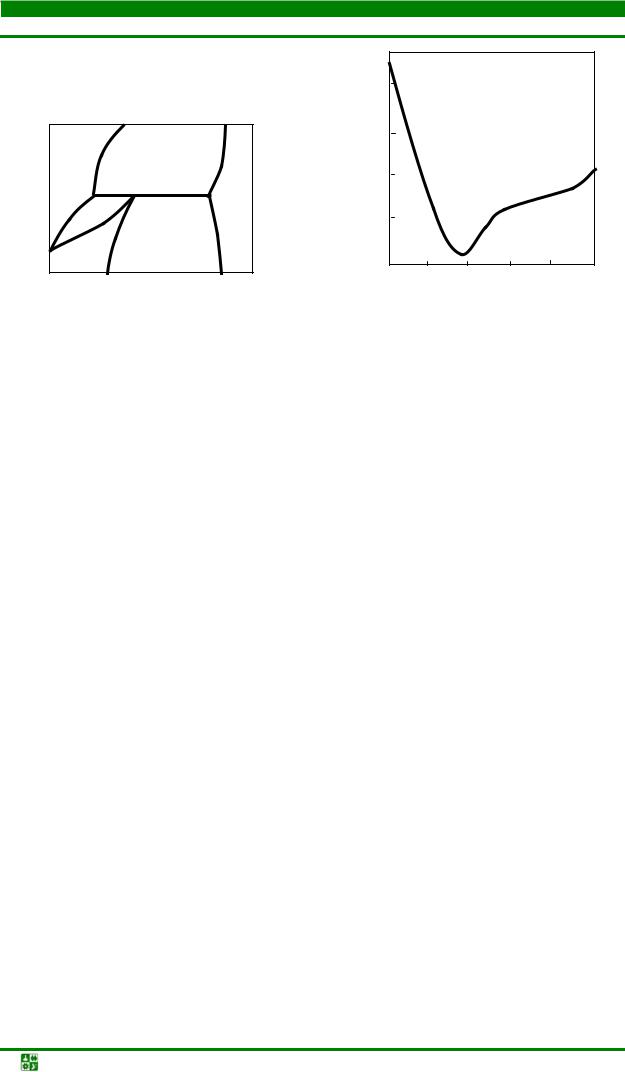
II. ФОРМОВАНИЕ И СПЕКАНИЕ ИЗДЕЛИЙ ИЗ МЕТАЛЛИЧЕСКИХ И НЕМЕТАЛЛИЧЕСКИХ ПОРОШКОВ
Лекция 18 Твердофазное спекание многокомпонентных систем
|
|
V/V,% |
|
|
|
|
25 |
|
|
|
|
15 |
|
|
|
|
0 |
|
|
|
|
β |
|
|
|
|
-15 |
|
|
α |
α + β |
-25Ag 20 |
|
|
|
|
60 |
Pt |
|
|
а |
|
б |
|
Рис. 2.54. Диаграмма состояния (а) и концентрационная зависимость усадки (б) в системе Ag–Pt при температуре 900 °С
Системы с перитектикой. В таких системах усадка в двухфазной области имеет четко выраженный минимум (рис. 2.54) из-за увеличения объема порошкового тела при спекании. По этой причине диффузионное межфазное взаимодействие в двухфазных перитектических системах осуществляется очень слабо. В этом случае создаются условия для беспрепятственного проявления эффекта Френкеля именно в области средних концентраций компонентов порошковых систем.
Системы с химическими соединениями. Взаимодействие компонентов смеси порошков с образованием в процессе спекания химических соединений или интерметаллидов обычно существенно усложняет вид концентрационной зависимости усадки, и ход кривых может быть самым различным и до выполнения эксперимента обычно непредсказуем.
Специфичной разновидностью такого спекания многокомпонентных систем может служить так называемое реакционное спекание, когда при нагреве порошковой формовки совмещают процессы собственно спекания и образования химического соединения. Например, при спекании формовки из порошка кремния в среде азота происходит образование Si3N4, которое сопровождается увеличением ее объема на 22 % , и за счет этого происходит частичное заполнение порового пространства.
Плотность порошкового тела после реакционного спекания зависит от исходной пористости формовки, фракционного состава порошка кремния, температурно-временных условий спекания. В общем случае свойства материалов после спекания зависят от целого ряда факторов: полноты гомогенизации в области ограниченных твердых растворов, пористости, совершенства межфазных и однофазных контактов и др.
Роль гетеродиффузии сводится к обеспечению выравнивания концентраций элементов в областях ограниченной растворимости, причем достижение гомогенности в большинстве случаев желательно (при предельных кон-
Процессы порошковой металлургии. Курс лекций |
-353- |
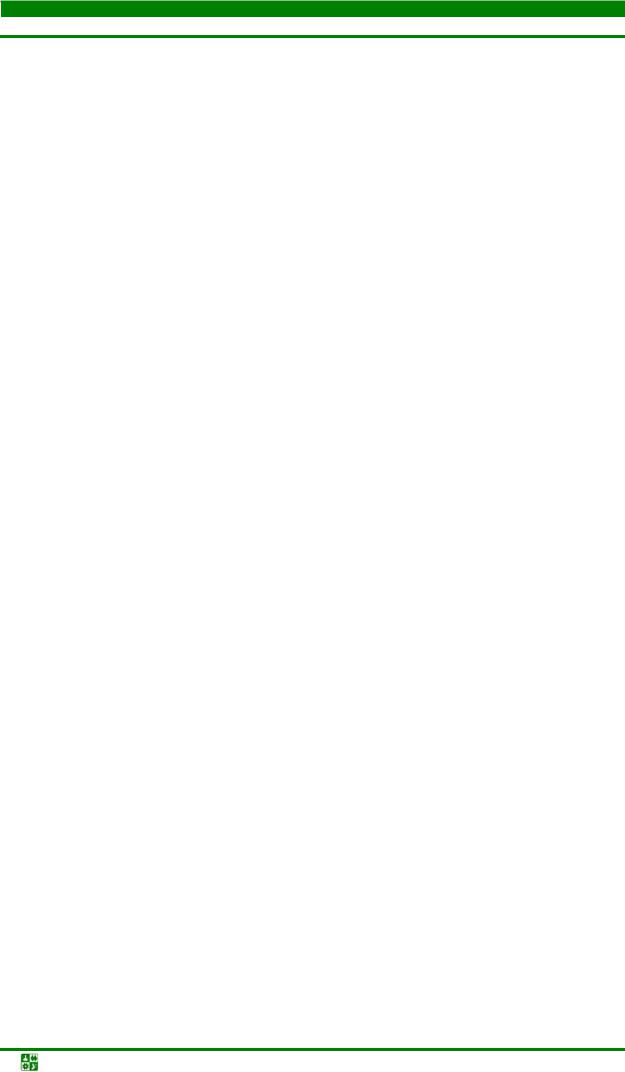
II. ФОРМОВАНИЕ И СПЕКАНИЕ ИЗДЕЛИЙ ИЗ МЕТАЛЛИЧЕСКИХ И НЕМЕТАЛЛИЧЕСКИХ ПОРОШКОВ
Лекция 18 Твердофазное спекание многокомпонентных систем
центрациях многие свойства ограниченных твердых растворов максимальны).
Спеканиесистемснерастворимыми (невзаимодействующими) компонентами
Б.Я. Пинес сформулировал термодинамическое условие припекания двух частиц разнородных невзаимодействующих компонентов:
αАБ < (αА + αБ), |
(2.55) |
т.е. поверхностная энергия образовавшейся межфазной границы АВ должна быть меньше, чем сумма поверхностных энергий частиц А и В; в противном случае порошковое тело спекаться не будет.
Механизм и кинетика припекания оказываются существенно различными для двух возможных случаев при соблюдении условия (2.55):
αАБ < (αА – αБ) |
(2.56) |
αАБ >(αА – αБ). |
(2.57) |
В случае, когда выполняется соотношение (2.57), энергетически целесообразно покрытие поверхности частицы вещества с большей поверхностной энергией веществом с меньшей поверхностной энергией (рис. 2.55). Вначале частица такого вещества покроется слоем атомов второго вещества (с помощью механизма поверхностной диффузии или переносом через газовую фазу), а затем контактная площадь между частицей А и частицей Б, покрытой слоем вещества А, увеличивается, что сопровождается уменьшением суммарной поверхности в системе А–Б и, соответственно, ее свободной энергии. Кинетика этого этапа припекания близка к кинетике припекания двух однородных сферических частиц, хотя вещество в область приконтактного перешейка будет поступать от одной порошинки А, а не от обеих частиц А и Б. Слияние сферических частиц А и Б должно завершиться образованием сферического тела, ядром которого будет частица Б.
Процессы порошковой металлургии. Курс лекций |
-354- |
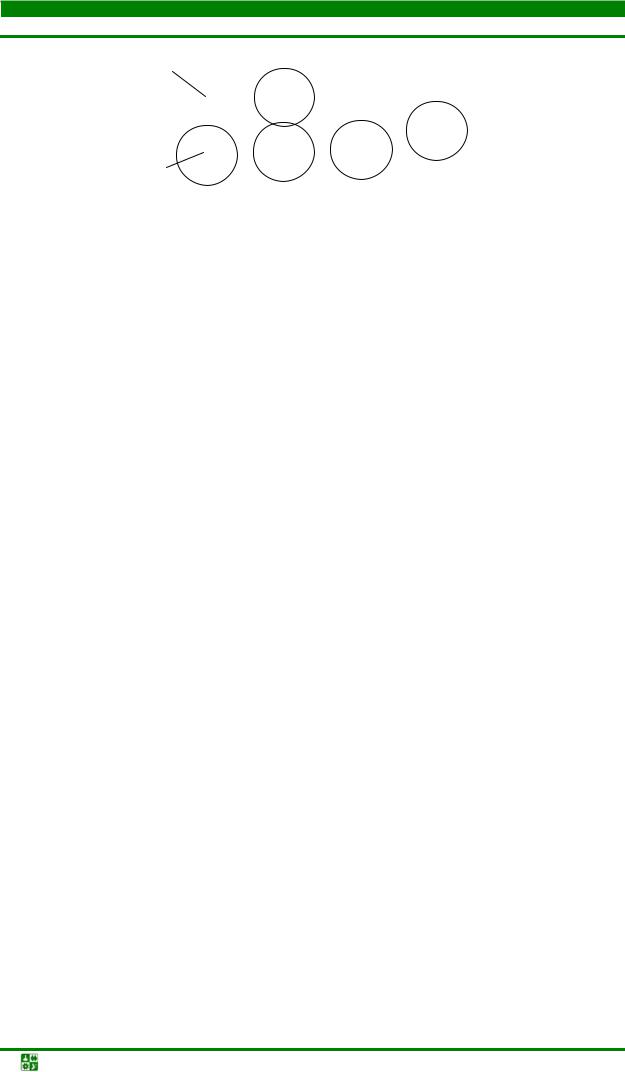
II. ФОРМОВАНИЕ И СПЕКАНИЕ ИЗДЕЛИЙ ИЗ МЕТАЛЛИЧЕСКИХ И НЕМЕТАЛЛИЧЕСКИХ ПОРОШКОВ
Лекция 18 Твердофазное спекание многокомпонентных систем
А
Б
а |
б |
в |
г |
Рис. 2.55. Схематическое изображение этапов (а–г) припекания частиц
Когда нижняя граница величины αАБ задается условием (2.56) (более распространенный случай), припекание частиц существенно отличается от рассмотренного выше. Распределение вещества А и Б в области контактного перешейка определяется границей, имеющей форму участка сферы с выпуклостью в сторону частицы с меньшей поверхностной энергией, и порошинка вещества с большей поверхностной энергией как бы вдавливается в порошинку вещества с меньшей поверхностной энергией. Полное уплотнение порошкового тела при этом не достигается.
Контрольныевопросыизадания
1.Назовите виды твердофазного спекания многофазных систем.
2.В чем различие процессов твердофазного спекания многокомпонентных и однокомпонентных систем?
3.Почему усадка порошкового тела при нагреве, как правило, меньше аддитивной?
4.Как выглядят кривые усадки порошкового тела для систем эвтектического и перитектического типов?
5.Что такое реакционное спекание?
6.Напишите термодинамическое условие припекания двух частиц разнородных невзаимодействующих компонентов.
7.Назовите и поясните возможные механизмы припекания двух частиц, состоящих из разнородных невзаимодействующих компонентов.
Лекция19 Жидкофазноеспекание
Пан лекции
1.Особенности процессов жидкофазного спекания порошков.
2.Стадии жидкофазного спекания.
Процессы порошковой металлургии. Курс лекций |
-355- |
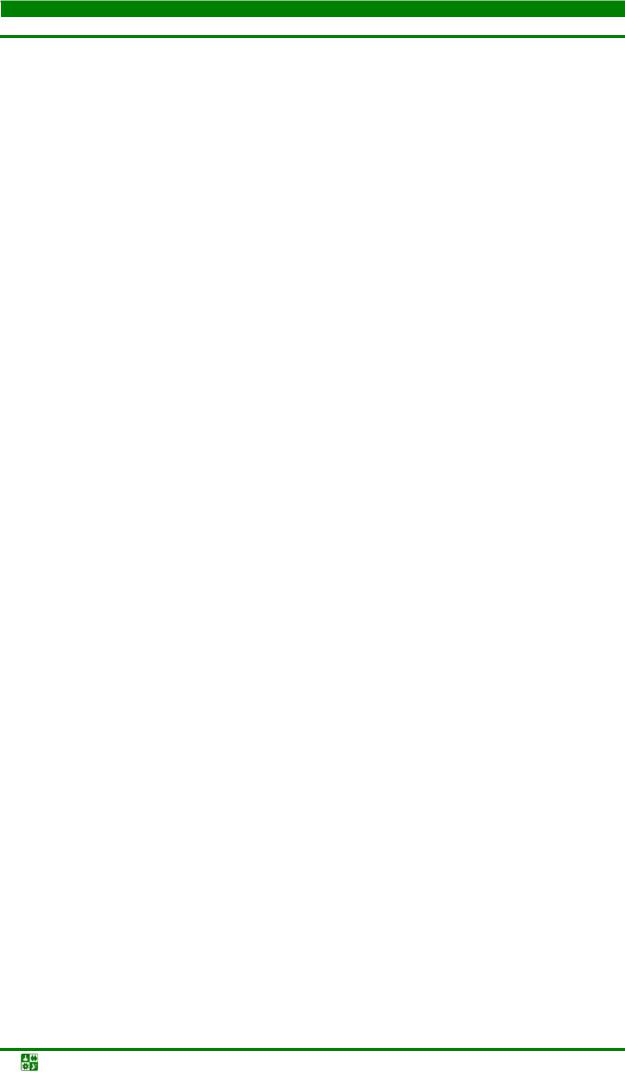
II. ФОРМОВАНИЕ И СПЕКАНИЕ ИЗДЕЛИЙ ИЗ МЕТАЛЛИЧЕСКИХ И НЕМЕТАЛЛИЧЕСКИХ ПОРОШКОВ
Лекция 19 Жидкофазное спекание
3. Спекание с жидкой фазой, присутствующей до конца спекания
Особенностипроцессовжидкофазногоспекания. Взаимодействиевсистеме
Жидкофазное спекание – спекание порошкового тела при температуре, обеспечивающей образование жидкой фазы.
Спекание с участием жидкой фазы имеет широкое техническое применение при производстве различных типов порошковых композиционных материалов. Термодинамическим условием эффективного жидкофазного спекания является стремление многокомпонентной системы к минимуму свободной поверхностной энергии и химического потенциала, как и при твердофазном спекании. Но в отличие от твердофазного при жидкофазном спекании из-за большей подвижности системы «жидкое–твердое» более наглядно проявляется действие основных движущих сил объемного уплотнения порошкового тела – сил капиллярного стягивания. В присутствии жидкой фазы при определенных условиях облегчается развитие сил сцепления между отдельными частицами порошка и может сформироваться малопористая (П < 1%) структура. При жидкофазном спекании в порошковом теле возникает своего рода капиллярная система (размеры частиц порошка соизмеримы с поперечными размерами поровых каналов), состоящая из твердой, жидкой и газообразной фаз.
В связи с этим большое значение приобретает смачивание твердых частиц жидкой фазой (рис. 2.56), мерой которого является величина краевого угла смачивания θ:
cos θ = (σт – σт-ж ) / σж, |
(2.58) |
где σт, σт-ж, σж – соответственно, поверхностные энергии на границах раздела твердое тело-газ, твердое тело-жидкость и жидкость-газ.
Термодинамическим условием смачивания является уменьшение свободной энергии системы при превращении границ раздела твердое тело-газ и жидкость–газ в границу раздела твердое тело–жидкость, т.е. работа адгезии должна быть положительна.
При полном смачиванииθ = 0°,при полном несмачиванииθ = 180°, при θ < 90° смачивание считают хорошим, а при θ > 90° смачивание плохое и образовавшаяся жидкая фаза тормозит спекание, препятствуя уплотнению порошкового тела.
Процессы порошковой металлургии. Курс лекций |
-356- |
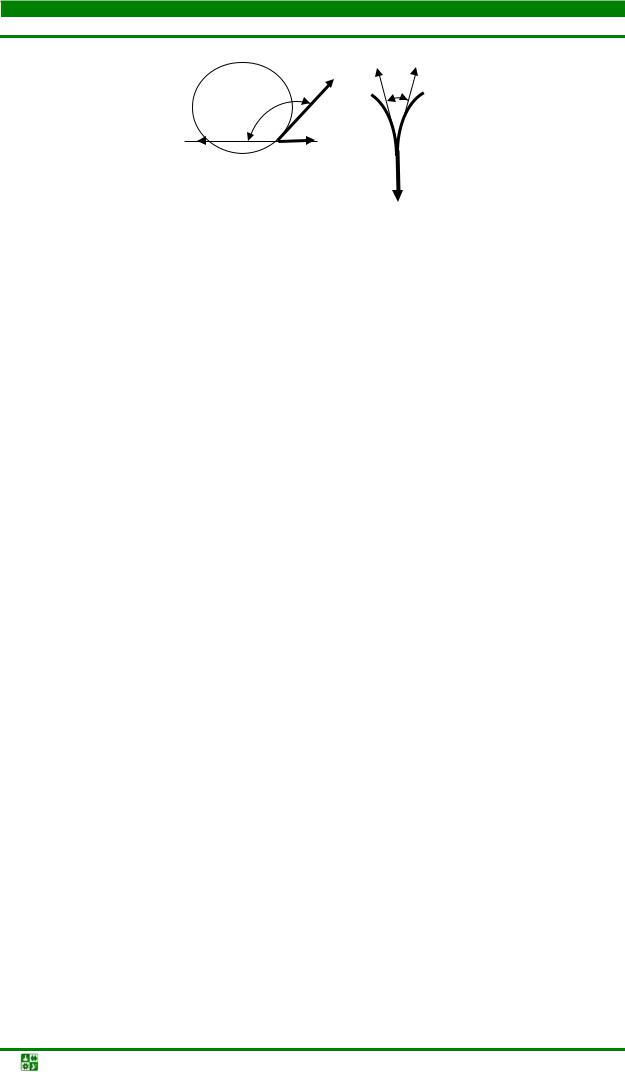
II. ФОРМОВАНИЕ И СПЕКАНИЕ ИЗДЕЛИЙ ИЗ МЕТАЛЛИЧЕСКИХ И НЕМЕТАЛЛИЧЕСКИХ ПОРОШКОВ
Лекция 19 Жидкофазное спекание
|
αж |
|
αт-ж |
ψ |
θ |
|
|
||
|
|
|
||
|
|
αт |
|
αтр |
αт-ж |
|
|||
|
|
|||
|
|
|
Рис. 2.56. Равновесие жидкой капли на твердой поверхности
Смачивание улучшается (уголθ уменьшается) при уменьшении σт-ж (например, при наличии в контактирующих фазах поверхностно-активных веществ или при изменении температуры). Изменение величины σт-ж может также быть следствием изменения величин σт и σж (экспериментально установлено, что с ростом σт растет и σт-ж,). При увеличении времени контакта жидкое–твердое и температуры краевой угол уменьшается и смачивание улучшается.
Врамках термодинамической теории смачивания, основанной на существовании химического взаимодействия на межфазной границе твердое тело-жидкость, это объясняется условиями прохождения химической реакции на этой границе. Повышение температуры приводит к уменьшению сво-
бодной энергии системы и уменьшению величины σт-ж, а влияние времени связано с продолжительностью установления равновесия при химическом взаимодействии фаз.
Величина краевого угла смачивания зависит от окружающей атмосферы, степени её очистки, способности к образованию веществом поверхностных пленок. Известно, что жидкие металлы хорошо смачивают чистые металлические поверхности (краевой угол смачивания обычно не превышает 30– 40° и часто наблюдается полное смачивание) и поверхности тех неметаллических или металлоподобных компонентов (оксидов, боридов, карбидов и нитридов различных металлов, графита и др.), с которыми они вступают в химическое взаимодействие.
Появление жидкой фазы при нагреве связано с расплавлением более легкоплавкого компонента или структурной составляющей (например, эвтектики) спекаемого материала, а также с «контактным» плавлением, когда жидкая фаза возникает при температуре, более низкой, чем температура плавления указанных составляющих порошкового тела. При этом механизм спекания с участием жидкой фазы зависит от характера диаграммы состояния соответствующей системы компонентов. Чем лучше смачивание, тем большие количества жидкой фазы могут удерживаться в порошковом теле во время спекания, не вытекая и не искажая его форму.
Вприсутствии жидкой фазы существенно увеличивается скорость само-
игетеродиффузии атомов, что ускоряет сплавообразование, и облегчается перемещение твердых частиц относительно друг друга, способствуя заполне-
Процессы порошковой металлургии. Курс лекций |
-357- |
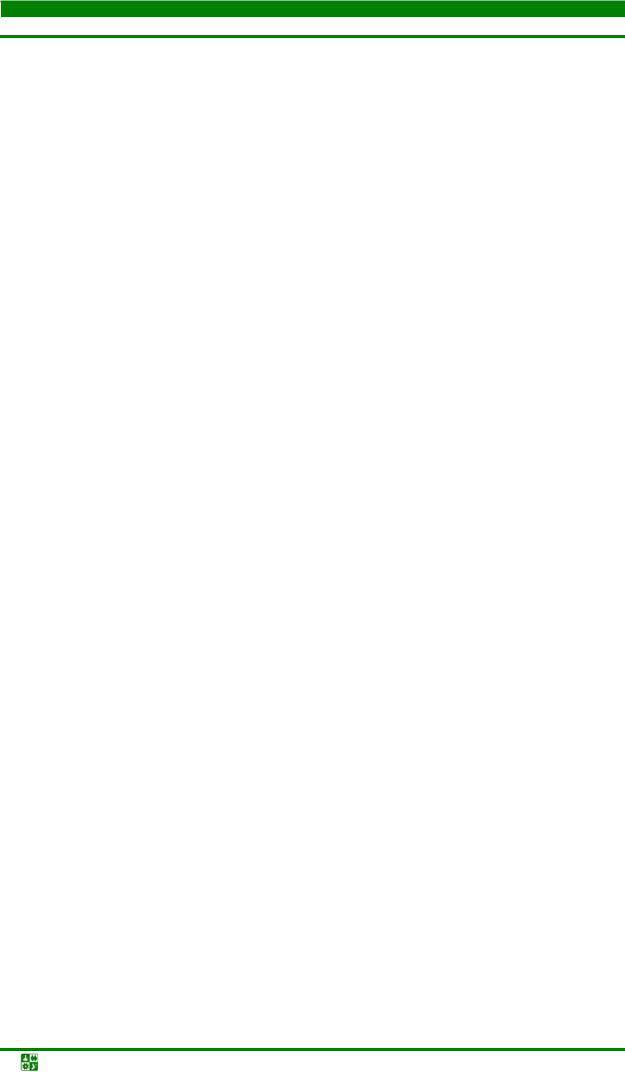
II. ФОРМОВАНИЕ И СПЕКАНИЕ ИЗДЕЛИЙ ИЗ МЕТАЛЛИЧЕСКИХ И НЕМЕТАЛЛИЧЕСКИХ ПОРОШКОВ
Лекция 19 Жидкофазное спекание
нию пор веществом. В связи с этим при жидкофазном спекании можно обеспечить получение практически беспористых порошковых изделий (материалов).
Различают спекание порошкового тела с присутствием жидкой фазы до конца изотермической выдержки и с ее исчезновением вскоре после появления (хотя нагрев продолжается), а также специфическую разновидность первого типа процесса жидкофазного спекания, которую называют инфильтрацией порошковой формовки.
В любом случае объем образующейся при нагреве жидкой фазы должен составлять от 3–5 до 50 % (оптимальное количество – 25–35 %). Если жидкой фазы образуется слишком много, то порошковая формовка может «поплыть» – потерять свою форму. При низком содержании жидкой фазы теряются преимущества жидкофазного спекания – требуются большее время на спекание, большая температура, получается пористое изделие и пр.
Рассмотрим основные особенности, характерные для спекания в присутствии жидкой фазы.
1.Образование жидкой фазы при спекании, как правило, сопровождается интенсификацией усадки, что в принципе позволяет получить спеченный материал с очень высокой плотностью и малой остаточной пористостью при относительно коротком времени процесса; в связи с этим спекание в присутствии жидкой фазы часто представляет собой альтернативу использованию высоких давлений формования или больших температуры и длительности выдержки при спекании для получения материала высокой плотности. Для некоторых порошков очень твердых материалов или сплавов жидкофазное спекание может быть единственно возможным способом получения высокой плотности конечного продукта.
2.Эффект увеличения усадки зависит как от физико-химических характеристик компонентов, так и от количества жидкой фазы, размера частиц тугоплавкой составляющей и начальной пористости брикетов. Увеличение количества легкоплавкой составляющей способствует усадке, но при наличии некоторой взаимной растворимости компонентов изменение плотности при жидкофазном спекании может осложняться процессами гетеродиффузии; использование более мелких фракций тугоплавкой составляющей способствует увеличению усадки.
3.Значительную роль при спекании играет величина исходной пористости. Усадка брикетов с большой начальной пористостью затрудняет получение изделий с высокой точностью размеров, а спекание брикетов с низкой исходной пористостью может привести даже к их росту при спекании. Это связано с тем, что при образовании жидкой фазы могут образовываться изолированные поры, давление газа в которых может повыситься (из-за восстановления оксидных пленок), что будет препятствовать усадке.
4.В некоторых случаях жидкая фаза присутствует при спекании лишь
втечение ограниченного времени и спекание осуществляется в основном в твердой фазе. Это связано с тем, что протекание диффузионных процессов с участием жидкой фазы может привести к образованию других, более тугоплавких фаз или к растворению жидкой фазы в твердой.
Процессы порошковой металлургии. Курс лекций |
-358- |
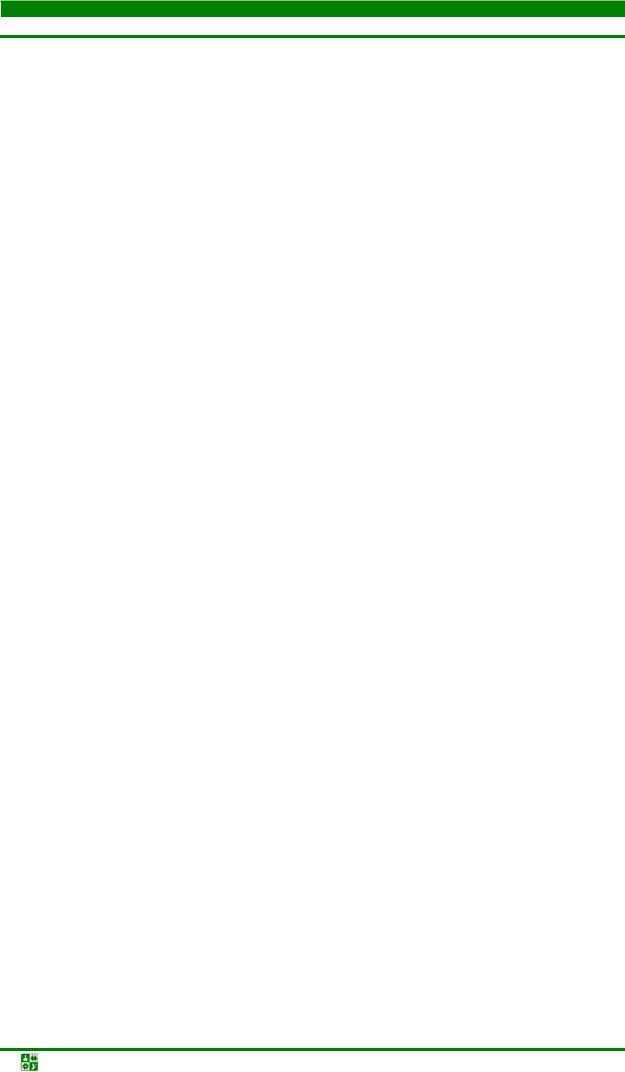
II. ФОРМОВАНИЕ И СПЕКАНИЕ ИЗДЕЛИЙ ИЗ МЕТАЛЛИЧЕСКИХ И НЕМЕТАЛЛИЧЕСКИХ ПОРОШКОВ
Лекция 19 Жидкофазное спекание
5. Процесс жидкофазного спекания часто используют для получения специальных структур, обладающих особенными механическими свойствами (например, антифрикционных материалов). Это возможно в том случае, если фаза, являющаяся жидкой во время спекания, сохраняет свои индивидуальные характеристики и в спеченном материале.
6. Управление объемными изменениями при жидкофазном спекании, позволяет получить высокопористые порошковые материалы и изделия с размерами, практически равными размерам исходных прессовок. Для этого требуется создание бипористой структуры порошкового тела, содержащей мелкие естественные поры и крупные искусственные поры. Образование крупных пор происходит за счет улетучивающегося порообразователя (двууглекислого аммония), вводимого в состав порошковой композиции на этапе прессования формовки.
Стадиижидкофазногоспекания
В 1938 г. Прайс, Смителс и Вильямс сформулировали представление об уплотнении при жидкофазном спекании как следствие двух последовательных стадий. По их мнению, при появлении жидкой фазы сначала (первая стадия) твердые частицы перемещаются до состояния плотной укладки под влиянием сил поверхностного натяжения смачивающей их жидкости; частицы смещаются относительно друг друга благодаря возникновению отрицательного капиллярного давления в жидкостных «мостиках» (манжетах), соединяющих эти частицы. На второй стадии (после завершения периода свободного перемещения частиц) происходит дальнейшее уплотнение материала благодаря перекристаллизации твердой фазы через жидкую, при условии наличия растворимости твердой фазы в жидкой.
Позднее (1953 г., Кеннон и Ленел) был установлен еще один механизм, приводящий к уплотнению при жидкофазном спекании: на заключительной стадии спекания в процессе завершения перекристаллизации или сразу после завершения первой стадии (при отсутствии растворимости твердой фазы в жидкости) развивается процесс срастания частиц тугоплавкого компонента в жесткий каркас («скелет»).
Было также отмечено, что уплотнение при перекристаллизации происходит еще и потому, что одновременно с ростом зерен изменяется и их форма. Результатом этого процесса является более плотное примыкание частиц друг к другу.
Современные теоретические разработки по жидкофазному спеканию базируются на указанных выше представлениях о трех возможных механизмах уплотнения, развивающихся с появлением жидкой фазы последовательно при частичном наложении (рис. 2.57) процессов:
жидкофазное течение (механическая перегруппировка), т.е. перемещение частиц под действием капиллярных сил;
Процессы порошковой металлургии. Курс лекций |
-359- |
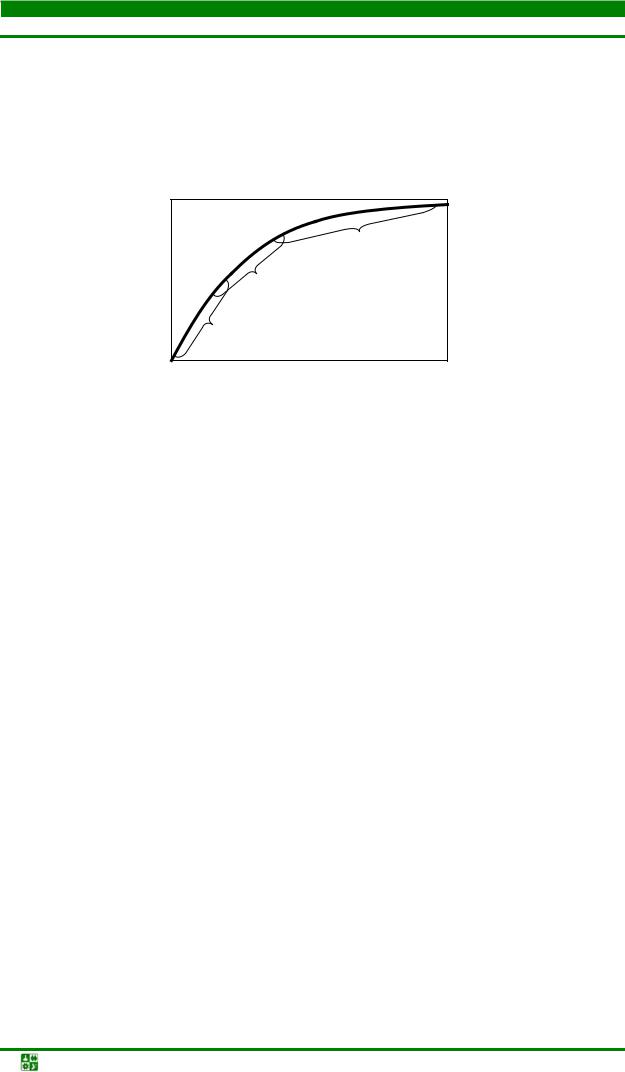
II. ФОРМОВАНИЕ И СПЕКАНИЕ ИЗДЕЛИЙ ИЗ МЕТАЛЛИЧЕСКИХ И НЕМЕТАЛЛИЧЕСКИХ ПОРОШКОВ
Лекция 19 Жидкофазное спекание
растворение–осаждение (перекристаллизация или химическая перегруппировка частиц тугоплавкой фазы), т.е. перенос через жидкость растворенного в ней вещества тугоплавкой фазы с поверхности частиц меньшего размера на поверхность частиц большего размера;
твердофазное спекание, т.е. срастание частиц тугоплавкой фазы (образование жесткого каркаса или «скелета»).
∆П
3
2
1
Т
Рис. 2.57. Кривая усадки при жидкофазном спекании: 1 – жидкое течение; 2 – растворение и осаждение; 3 – твердофазное спекание
Кинетика этих процессов существенно зависит от степени однородности смеси компонентов, начальной пористости порошкового тела, количества образующейся жидкой фазы, линейного размера порошинок, характера смачивания твердой фазы жидкостью, взаимной растворимости фаз и достаточно большого количества других факторов.
Наибольшая степень уплотнения достигается на этапе перегруппировки частиц. Для систем с невзаимодействующими компонентами этот механизм является основным. При этом количество жидкой фазы в подобной системе должно быть максимальным [35–50 % (об.)].
Для систем с взаимодействующими компонентами эффективное уплотнение достигается при меньшем количестве жидкой фазы. В этом случае заметное уплотнение достигается за счет дополнительной усадки по механизму химической перегруппировки.
Первая стадия. Жидкая фаза заполняет зазоры между твердыми частицами и, играя роль жидкой смазки, облегчает взаимное перемещение частиц, приводящее к уплотнению порошкового тела. Такое перемещение частиц, сопровождающееся уменьшением свободной поверхности жидкости, происходит под влиянием давления, обусловленного кривизной поверхности возникающей жидкостной «манжеты» (т.е. поверхности раздела жидкость– газ), образуемой объемом расплава, заключенного между смежными частицами (порошинками).
При хорошем смачивании под вогнутой поверхностью в этом объеме жидкости создается отрицательное капиллярное давление, стягивающее твердые частицы с одновременным их поворотом относительно точки межчастичного контакта. Вместе с поворотом частиц происходит перемещение
Процессы порошковой металлургии. Курс лекций |
-360- |
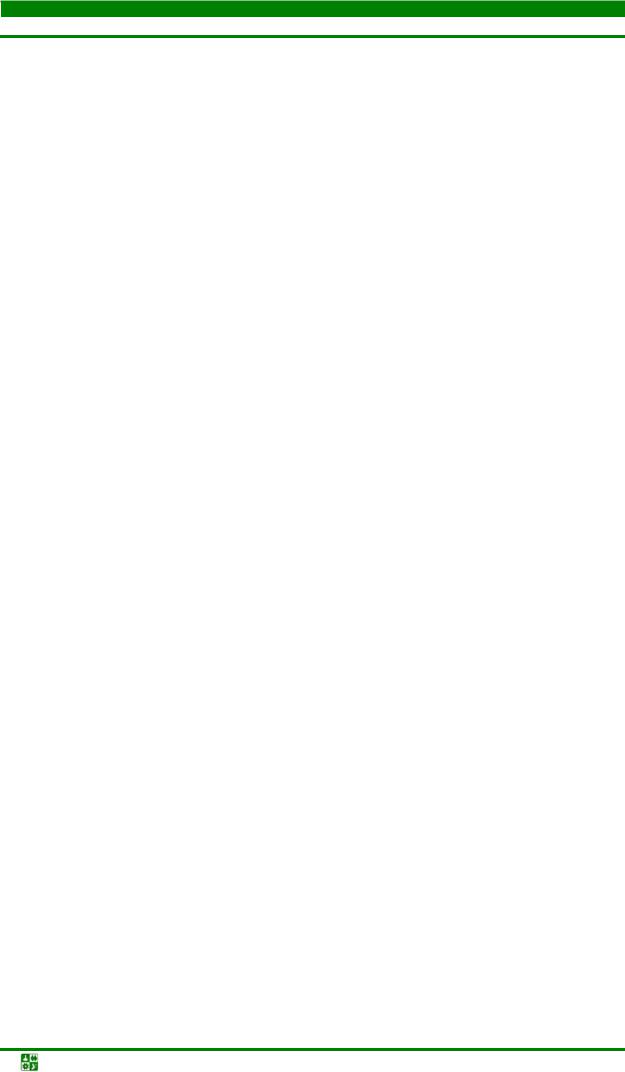
II. ФОРМОВАНИЕ И СПЕКАНИЕ ИЗДЕЛИЙ ИЗ МЕТАЛЛИЧЕСКИХ И НЕМЕТАЛЛИЧЕСКИХ ПОРОШКОВ
Лекция 19 Жидкофазное спекание
объема жидкости, и область отрицательного капиллярного давления распространяется на новые участки поверхности твердых частиц, ускоряя их поворот и взаимный сдвиг.
При полном смачивании поверхность «манжеты» имеет наибольшую кривизну, приводящую к максимальному значению отрицательного капиллярного давления в жидкости и силы, сжимающей твердые частицы. при ухудшении смачивания кривизна вогнутой поверхности «манжеты» уменьшается, капиллярные силы убывают и при θ > 65–85° поверхность жидкостной «манжеты» становится выпуклой, знак капиллярного давления меняется и вместо стягивания твердых частиц появляется сила, стремящаяся их раздвинуть.
При плохом смачивании «манжета» может не образоваться, а будет происходить стягивание жидкости в капли на поверхности частиц твердой фазы.
Если появляющаяся жидкая фаза распределена в объеме порошкового тела равномерно, то возникающие капиллярные силы по влиянию на процесс перегруппировки эквивалентны действию давления всестороннего сжатия.
Для образования жидких прослоек в приконтактной области между твердыми частицами необходимо, чтобы они хорошо разделялись жидкостью, так как без подобного разделения невозможно свободное перемещение частиц, т.е. процесс их перегруппировки. Чем ниже исходная плотность порошкового тела, тем меньше вероятность образования в нем прочного жесткого каркаса на начальной стадии спекания и тем легче идет процесс перегруппировки частиц.
При относительно большом содержании легкоплавкого компонента [10–30 % (об.)], малом размере частиц твердой фазы и достаточно высокой температуре спекания процесс перегруппировки частиц с их перемещением до состояния плотной упаковки составляет основной механизм уплотнения. После его завершения пространство между твердыми частицами оказывается почти полностью заполненным жидкой фазой.
Вклад процесса механической перегруппировки в общую объемную усадку спекаемого порошкового тела увеличивается с ростом количества жидкой фазы и уменьшением размера частиц тугоплавкой фазы, так как при этом уменьшается вероятность заклинивания твердых частиц при их взаимном перемещении.
Вторая стадия. Существенную роль этот процесс может играть лишь в системах, где твердая фаза имеет некоторую растворимость в жидкой фазе. Поскольку растворимость твердого вещества в жидкости увеличивается с увеличением кривизны (с уменьшением размера частиц твердой фазы), мелкие частицы растворяются и исчезают, в то время как крупные растут, принимая более правильную форму (например, округлую или ограненную), обеспечивающую минимизирование поверхностной энергии.
Транспорт материала происходит путем быстрой диффузии через жидкую фазу. Возможно, что этот процесс непосредственно не приводит к усадке, однако способствует ей, позволяя частицам легче перемещаться в процессе вязкого течения жидкости на первой стадии спекания.
Процессы порошковой металлургии. Курс лекций |
-361- |
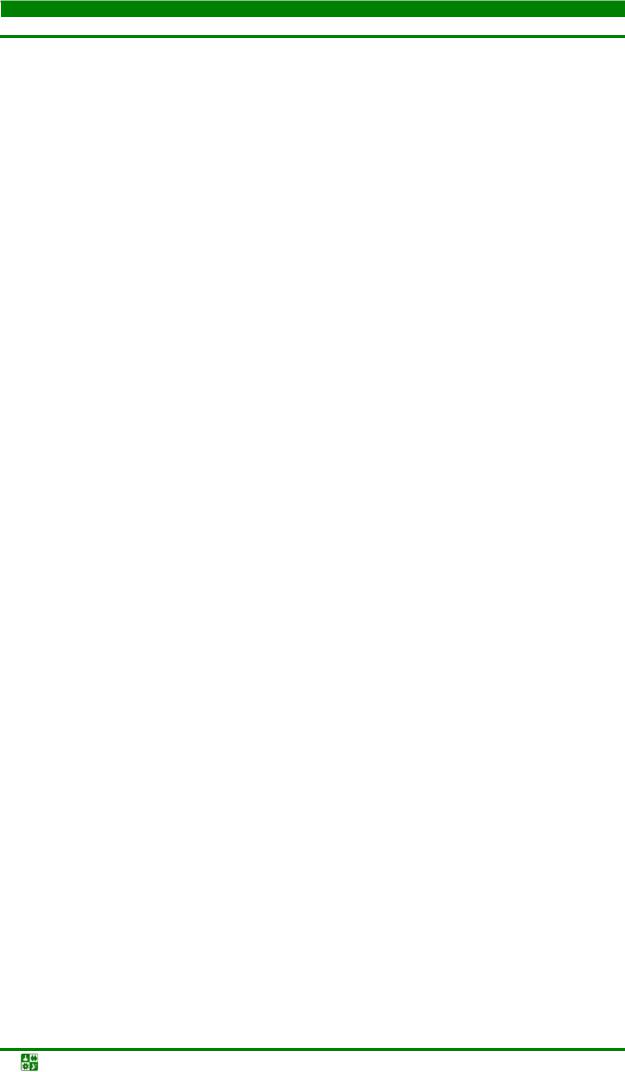
II. ФОРМОВАНИЕ И СПЕКАНИЕ ИЗДЕЛИЙ ИЗ МЕТАЛЛИЧЕСКИХ И НЕМЕТАЛЛИЧЕСКИХ ПОРОШКОВ
Лекция 19 Жидкофазное спекание
Процесс перекристаллизации включает не менее трех элементарных процессов:
1)растворение вещества мелких частиц, т.е. переход атомов с поверхности этих частиц в раствор (процесс, часто называемый реакцией на межфазной поверхности);
2)диффузию растворенных атомов в жидкости между поверхностями мелких и крупных частиц;
3)отложение растворенного вещества на поверхности крупных час-
тиц.
Рост зерен по этому механизму при жидкофазном спекании подчиняется той же временной зависимости, что и рост зерна при собирательной рекристаллизации в общем виде
dn – d0n = Kτ, |
(2.59) |
где dn, d0n – текущая и начальная средняя величина зерна (частицы) соответственно; τ – время спекания; K – константа.
Показатель степени зависит от того, какой элементарный акт определяет скорость всего процесса; например, если это первый из указанных выше, то п = 2, а если второй, то п = 3. Отметим, что значение п не всегда целочисленно и в некоторых случаях оно может меняться во времени. При малом с о- держании жидкой фазы контакт между частицами твердой фазы значительно усложняет кинетику их роста.
Процесс уплотнения связан с перекристаллизацией косвенно и в относительно небольшой степени, хотя часто кажется, что прямая и существенная связь есть.
Механизм растворения–осаждения практически оказывается существенным, когда количество жидкой фазы составляет > 5 % (об.). В случае малых количеств жидкой фазы (< 3–5 %), которые не могут вызвать механическую перегруппировку, но обеспечивают наличие химической перегруппировки, уплотнение порошкового тела может иметь место за счет уменьшения объема тугоплавкой фазы, связанного с растворением некоторого объема частиц в жидкой фазе.
Третья стадия. На этой стадии существенно возрастает количество твердых частиц, не разделенных жидкой прослойкой, которые взаимно припекаются (срастаются) и в порошковом теле образуется жесткий «скелет»; к тому же в какой-то момент нагрева жидкая фаза может исчезнуть (закристаллизоваться вследствие обогащения ее тугоплавким компонентом или раствориться в тугоплавкой фазе). В любом из этих случаев кинетика усадки будет определяться закономерностями твердофазного спекания, которые рассмотрены ранее.
Отметим, что срастание частиц (порошинок) может быть следствием нескольких механизмов перемещения вещества, некоторые из которых при-
Процессы порошковой металлургии. Курс лекций |
-362- |
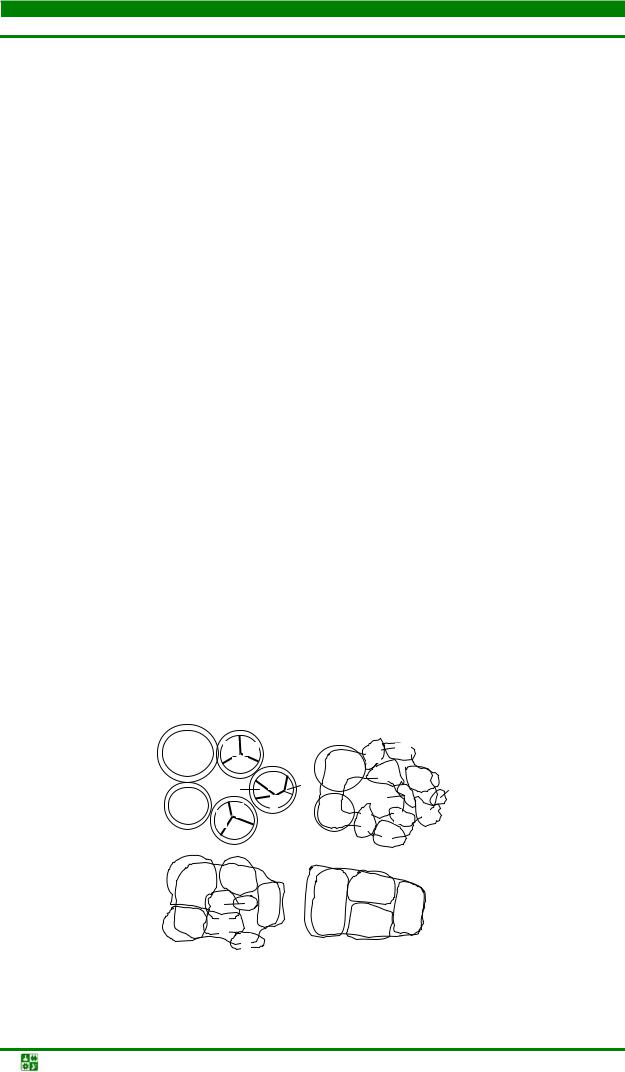
II. ФОРМОВАНИЕ И СПЕКАНИЕ ИЗДЕЛИЙ ИЗ МЕТАЛЛИЧЕСКИХ И НЕМЕТАЛЛИЧЕСКИХ ПОРОШКОВ
Лекция 19 Жидкофазное спекание
водят к уплотнению пористого порошкового тела, а некоторые нет. Такие процессы, как диффузия через жидкую фазу (основной процесс, обеспечивающий рост частиц) или самодиффузия в приповерхностном слое частиц твердой фазы, вызывая рост контакта, не приводят к уменьшению объема пор в спекаемом порошковом теле и, соответственно, к уплотнению. Так же, как при твердофазном спекании, уплотнение после завершения перегруппировки частиц при жидкофазном спекании может обеспечить только объемное течение вещества частиц твердой фазы.
Спеканиесжидкойфазой, присутствующейдоконцаспекания
При таком спекании в процессе изотермической выдержки жидкая фаза постоянно присутствует в порошковом теле.
Рассмотрим модель подобного процесса. Пусть двухфазная система состоит из частиц более тугоплавкого компонента А и частиц более легкоплавкого компонента В, в расплаве которого компонент А частично растворяется (рис. 2.58).
При появлении жидкой фазы она заполняет поры и капилляры, смачивая частицы компонента А и стягивая их, а также растворяет более мелкие частицы компонента А (раствор А в В не насыщен по отношению к ним из-за большей, по сравнению с равновесной, их растворимостью в связи с повышенной кривизной поверхности). В результате перекристаллизации на крупных частицах компонента А выделяется вещество А из пересыщенного по отношению к ним раствора А в В. Это приводит к росту крупных частиц за счет мелких и приобретению ими правильной (равновесной) формы; что связано с анизотропией поверхностной энергии для различных типов кристаллических структур. Отметим, что огранка или округление частиц облегчает их аккомодацию при перегруппировке и сближении.
1 |
|
12 11 |
|
|
|
12 |
11 |
|
|
|
|
10 |
|
|
1 |
10 |
|
8 |
|
|
|
|
8 |
9 |
|
|
|||
|
|
6 |
|
|
9 |
||||
|
|
|
6 |
|
|||||
2 |
|
7 |
|
|
|
|
|||
|
5 |
|
2 |
|
7 |
|
|||
3 |
|
3 |
5 |
|
|||||
|
|
|
|
||||||
|
|
4 |
|
|
|
4 |
|
|
|
|
|
|
|
|
|
|
|
|
|
1 |
|
10 |
|
|
|
10 |
|
|
|
|
6 |
|
8 |
|
1 |
|
|
|
|
|
|
|
3 |
8 |
|
|
|||
2 |
3 |
|
|
|
|
|
|||
|
|
|
|
|
|
||||
|
|
4 |
|
|
|
|
|
|
|
Рис. 2.58. Схема усадки прижидкофазном спекании порошковой системы
Процессы порошковой металлургии. Курс лекций |
-363- |
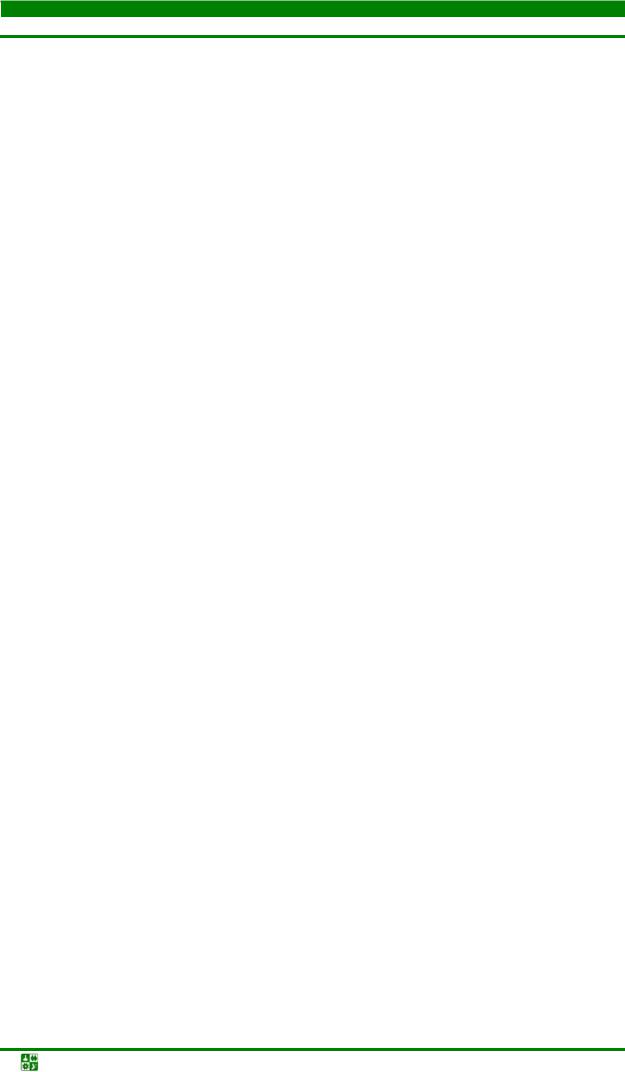
II. ФОРМОВАНИЕ И СПЕКАНИЕ ИЗДЕЛИЙ ИЗ МЕТАЛЛИЧЕСКИХ И НЕМЕТАЛЛИЧЕСКИХ ПОРОШКОВ
Лекция 19 Жидкофазное спекание
При полной смачиваемости и заметной растворимости тугоплавкой фазы в жидкой уплотнение достигается уже в первые несколько (1–10) мин изотермической выдержки и сравнительно небольшом [10–20 % (об.)] количестве жидкой фазы. Стадия механической перегруппировки частиц характеризуется дезинтеграцией поликристаллических частиц, которая наблюдается при плавлении фазы В (стадия II), и их интенсивным перемещением. Химическая перегруппировка вначале (стадия III) приводит к коалесценции и росту более крупных частиц за счет более мелких, а затем (стадия IV) и к окончательному уплотнению системы.
Жидкая фаза может оставаться в порошковом теле до конца нагрева при температуре спекания и в том случае, если компоненты А и В взаимно нерастворимы.
Расплавившийся легкоплавкий компонент В затекает в поры между частицами компонента А и стягивает их. Если частицы при формовании образовали жесткий скелет, то усадка под действием расплава В либо не происходит, либо она весьма незначительна.
Нужно иметь в виду, что при спекании реальных металлических порошков технической чистоты всегда необходимо учитывать возможность образования жидкой фазы за счет примесей. Даже при весьма малых количествах жидкой фазы, присутствующей в порошковом теле в каждый данный момент, в течение всего процесса через нее могут прореагировать (или перекристаллизоваться) большие массы твердой фазы, если она растворима в расплаве.
Контрольныевопросыизадания
1.Что является мерой смачивания твердых частиц жидкой фазой?
2.Назовите особенности спекания порошковых тел в присутствие жидкой фазы.
3.Что такое «бипористая структура» порошкового тела?
4.От чего зависит усадка порошкового тела при жидкофазном спекании?
5.Назовите стадии спекания порошкового тела.
6.При каком минимальном количестве жидкой фазы механизм раство- рения–осаждения оказывает практическое влияние на усадку порошкового тела?
7.Опишите процесс жидкофазного спекания порошкового тела в случае присутствия жидкой фазы до конца изотермической выдержки. Изобразите исходную и конечную структуры спекаемого порошкового тела.
Процессы порошковой металлургии. Курс лекций |
-364- |