
- •Оглавление
- •ВВЕДЕНИЕ
- •I. ПОЛУЧЕНИЕ ПОРОШКОВ
- •Лекция 16 Восстановление химических соединений металлов из растворов солей и газообразных соединений металлов
- •II. ФОРМОВАНИЕ И СПЕКАНИЕ ИЗДЕЛИЙ ИЗ МЕТАЛЛИЧЕСКИХ И НЕМЕТАЛЛИЧЕСКИХ ПОРОШКОВ
- •Введение
- •Лекция 13 Твердофазное спекание материалов
- •Лекция 20 Жидкофазное спекание и инфильтрация порошковых формовок. Брак при спекании
- •Лекция 25 Методы определения механических характеристик порошковых тел. Заключение
- •ЗАКЛЮЧЕНИЕ
- •БИБЛИОГРАФИЧЕСКИЙ СПИСОК
- •ПРИЛОЖЕНИЯ

I. ПОЛУЧЕНИЕ ПОРОШКОВ
Лекция1 Историяразвитияпорошковойметаллургии.
Классификацияметодовполученияпорошков
План лекции
1. Основные этапы развития порошковой металлургии.
2. Классификация методов получения порошков.
Основныеэтапыразвитияпорошковойметаллургии
Материальные памятники, характеризующие этапы развития человеческого общества, свидетельствуют о том, что порошки золота, меди и бронзы применялись людьми 8–10 тыс. лет назад. Еще в бронзовом веке люди умели получать и использовать некоторые виды порошков, а также применять горячую ковку порошковой массы. Этот опыт был использован около 5 тыс. лет назад для изготовления железных орудий труда и вооружения. Начинался век железа, пришедший на смену бронзовому веку.
Колыбелью древней металлургии как цветных металлов, так и железа считают Ближний Восток. Видимо, отсюда, через Кавказ, технология железа и железных изделий проникла в Европу (II–I тыс. до н. э.) и на восток Азии, вплоть до Индии.
Первые следы производства железа датируют 3000 г. до н. э. (ЧегерБезер, Ирак – территория бывшей Финикии), а найденные археологами стальные мечи относят к 2700 г. до н. э. Отд ельные виды изделий из железа по торговым путям попадали и на территорию других государств. Например, в гробнице египетского фараона Тутанхамона (XIV в. до н. э.) были найдены кованые железные кинжалы, украшенные порошковым золотом, и амулет из железа.
Изделия из железа, которое значительно более тугоплавко (температура плавления 1 539 оС), чем медь (температура плавления 1 083 оС), не могли быть получены литьем, так как вплоть до XIX в . не были известны способы создания необходимых для плавления железа высоких температур. В распоряжении металлургов в основном были температуры 1 000–1 100 оС, получаемые за счет горения древесины.
Позже стали использовать кричный метод и ковку заготовки в нагре-
том состоянии. Сначала в шахтных печах (домницах) при температуре порядка 1 100 оС восстановлением богатой или обогащенной окисленной руды железа древесным углем получали крицу (губчатую массу железа), а затем проковывали ее в нагретом состоянии.
Процессы порошковой металлургии. Курс лекций |
-12- |
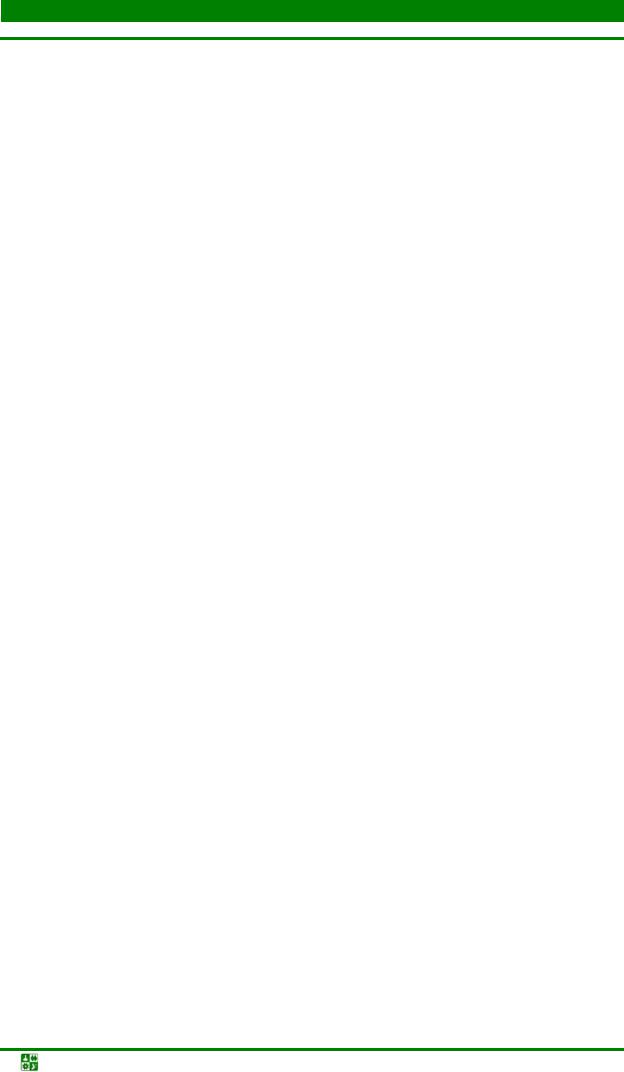
I. ПОЛУЧЕНИЕ ПОРОШКОВ
Лекция 1 История развития порошковой металлургии. Классификация методов получения порошков
Для уменьшения пористости откованное железо повторно нагревали в печи, а иногда и снова проковывали. Такое железо называли сварочным. В целом объем его производства достигал сотен тысяч пудов, обеспечивая потребности развивающегося земледелия в лемехах, мотыгах, серпах, косах, топорах и пр.
На территории нашей страны (Прикамье, Волжско-Окский бассейн) железо и изделия из него впервые были получены около 1000 г. до н. э. Через 500 лет эту технологию освоили и на территории Сибири, Алтая и Украины. Исследования археологов показывают, что в 950–1000 гг. в Киевской Руси, Рязани и Новгороде из железной крины изготовляли различные предметы быта, оружие и др.
Вотдельных отдаленных районах России (Карелии, Якутии) производство сыродутного железа в домницах сохранялось вплоть до XIX в.
Научные основы порошковой металлургии разработал в 1752–1763 гг. М.В. Ломоносов. Он описал, например, процессы получения порошкового свинца, способы перевода различных материалов в порошкообразное состояние, дал понятие спекания как операции перевода «порошкообразного тела, которому по желанию придана известная форма, в каменистое вещество».
В1827 г. на торжественном собрании Ученого комитета по горной и соляной части (г. Санкт-Петербург) 21 марта 1827 г. выступил П.Г. Соболевский (1782–1841), сообщивший о создании им нового способа получения различных изделий из порошка платины. Им были продемонстрированы медали, жетоны, чаши, тигли, бруски массой до 2,4 кг, различные украшения, полученные путем прессования предварительно сформованной и нагретой до «белого каления» заготовки из губчатой платины. П.Г. Соболевский отмечал
всвоем докладе, что «от одного удара кружок платины вовсе изменяет вид свой; зернистое сложение его становится плотным и оный делается совершенно ковким. После обжатия кружки проковываются в полоски или прутки желаемого вида обыкновенным образом».
П.Г. Соболевский является основоположником широко распространенного в настоящее время направления в металлургии – порошковой металлургии.
Петр Григорьевич Соболевский родился в Петербурге в феврале 1782 г. в семье врача и ботаника Григория Федоровича Соболевского. Образование П.Г. Соболевский получил в Петербургском сухопутном кадетском корпусе, но почти сразу после его окончания он оставил военную службу и занялся решением сложных научно-технических проблем. Работая на Урале, П.Г. Соболевский прославил свое имя успешной инженерной и научной деятельностью в области осветительной техники (создал в 1811 г. «термоламп» – прибор для газового освещения и отопления), черной и цветной металлургии (усовершенствовал и внедрил в 1816 г. способ пудлингования чугуна), химической технологии, конструирования машин и судов (самодувные печи, обжимные молоты, безбалансирная паровая машина; в 1817 г. по Волге и Каме
Процессы порошковой металлургии. Курс лекций |
-13- |
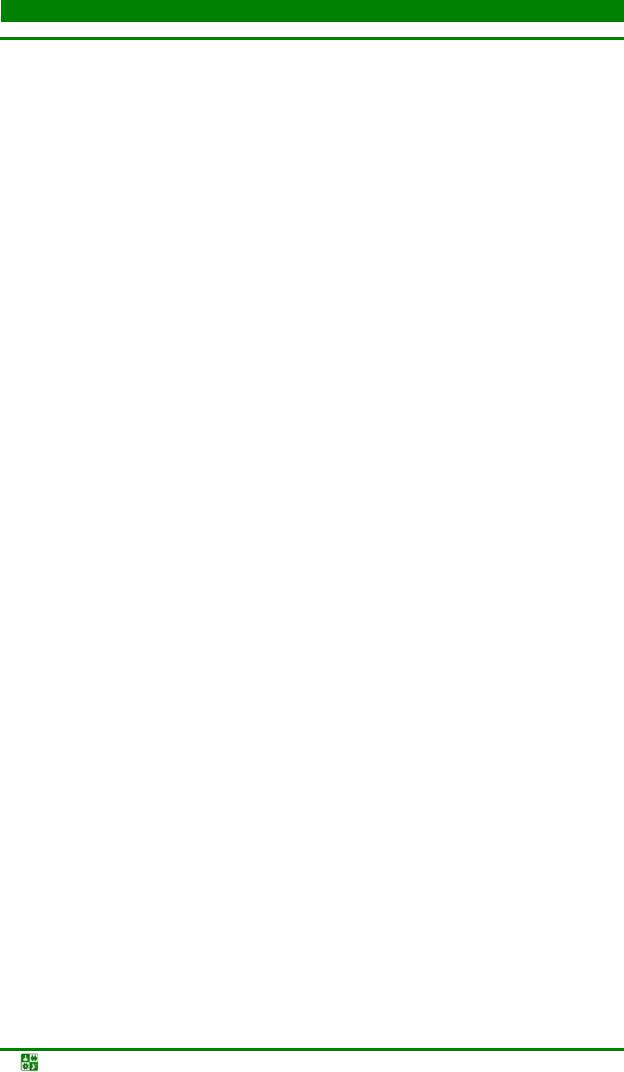
I. ПОЛУЧЕНИЕ ПОРОШКОВ
Лекция 1 История развития порошковой металлургии. Классификация методов получения порошков
пошли первые пароходы, построенные по его проекту) и др. В 1825 г . П.Г. Соболевский по поручению Горного департамента приступил к решению проблемы платины, которую в то время не могли обрабатывать из-за высокой температуры плавления этого материала.
Именно с этим тугоплавким металлом (температура плавления 1 773 оС) связано зарождение порошковой металлургии.
Академик Петербургской академии наук, физик Н.П. Щеглов (1793– 1831) отметил: «Все почти европейские знаменитости химии в течение семидесяти лет старались найти простейший способ отделить чистую платину от сопровождающих ее обыкновенно в природе других минералов и приводить в ковкое состояние, но доселе усилия их были безуспешны».
Хотя платина была известна еще в древности, а ее разработка началась в XVIII в. в Колумбии, для России проблема получения платиновых и з- делий стала актуальной лишь в начале XIX в. На Урале сначала были открыты ее месторождения в виде спутника золота (1819 г.), а затем богатейшие в мире запасы чистой платиновой россыпи (1825 г.), причем только за один 1825 г. добыча платины в России составила 110 пудов (в Америке с 1741 по 1825 гг. было добыто 65–70 пудов).
Поэтому П.Г. Соболевскому было поручено построить и возглавить Соединенную лабораторию Горного кадетского корпуса, явившуюся первым в России химико-металлургическим центром. Именно здесь П.Г. Соболевский при участии помогавшего ему химика В.В. Любарского (1795–1852) в течение 1826 г. создал новый способ получения платиновых изделий, названный затем порошковой металлургией. Он состоял в прокаливании хлорплатината аммония и последующем горячем прессовании полученного платинового порошка в цилиндрические заготовки.
С использованием способа, разработанного П.Г. Соболевским, в 1826 г. было обработано 40 фунтов платины, а с 1828 г. налажена массовая чеканка платиновых монет достоинством 3, 6 и 12 руб. на серебро, продолжавшаяся до 1845 г. (всего за 18 лет было выпущено монет на сумму более четырех миллионов рублей), которая и стала первым промышленным применением порошковой металлургии.
Однако после смерти П.Г. Соболевского чеканка платиновых монет вскоре была прекращена, добыча платины заметно сократилась, появились печи с кислородно-водородным пламенем (что позволило развивать температуры более 1 800 оС).
До начала ХХ в. сохранялось лишь эпизодическое применение металлических порошков для различных целей (свинцовых порошков в аккумуляторах, железных – в химических производствах и пр.).
Возрождение интереса к порошковой металлургии было прежде всего связано с необходимостью удовлетворения потребностей быстро развивавшейся электротехники. Электроламповой промышленности были нужны ту-
Процессы порошковой металлургии. Курс лекций |
-14- |
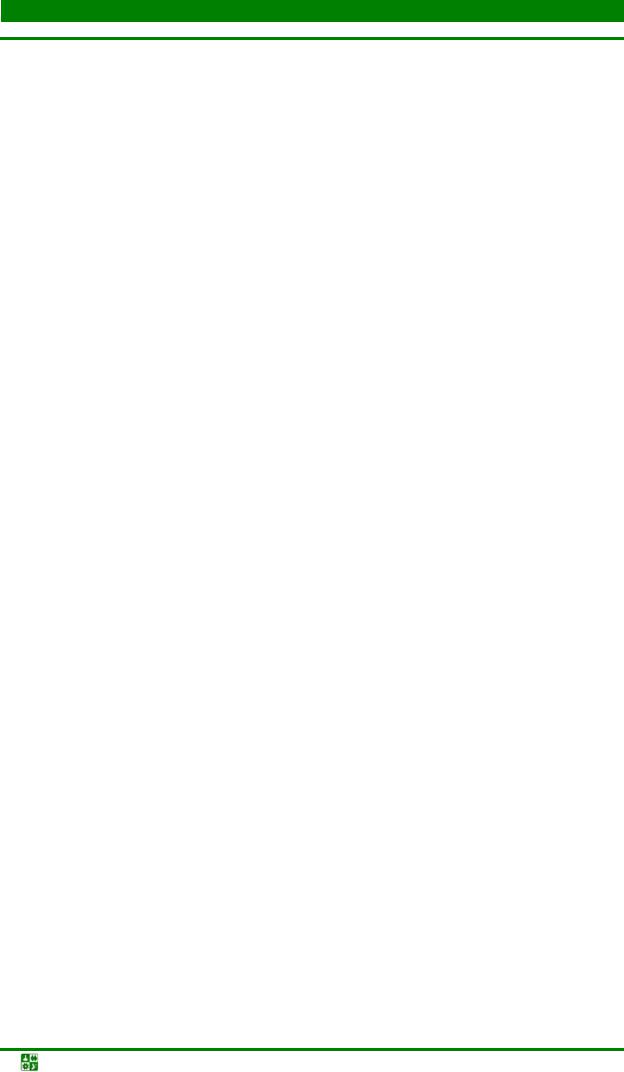
I. ПОЛУЧЕНИЕ ПОРОШКОВ
Лекция 1 История развития порошковой металлургии. Классификация методов получения порошков
гоплавкие материалы для нитей ламп накаливания, электромашиностроению были необходимы меднографитовые щетки и т.п.
В1900 г. наш соотечественник А.Н. Ладыгин на Всемирной Парижской выставке демонстрировал электрическую лампочку с телом накала из вольфрамовой проволоки, полученной методом порошковой металлургии.
Решение этих и других трудных технических задач послужило мощным толчком к налаживанию производства порошковых самосмазывающихся подшипников, твердых сплавов, магнитных, электроконтактных и конструкционных материалов, а также многих других видов продукции.
Кначалу 1950-х гг. мировое ежегодное производство металлических порошков, материалов и изделий из них составляло примерно несколько десятков тысяч тонн. Началось быстрое развитие порошковой металлургии, связанное с созданием крупных специализированных производств порошков
иизделий из них.
Впоследующие тридцать лет темпы роста продукции порошковой металлургии в разных странах в среднем составляли 6–10 %, достигая в отдельные периоды 15–20 % (США, ФРГ, Япония и др.).
Всередине 1980-х гг. было реализовано металлических порошков и изделий из них в мире на пять миллиардов долларов, в том числе в США б о- лее чем на один миллиард долларов. По оценкам экспертов, ежегодный прирост объема реализации изделий из порошков составляет не менее 5–7 %.
Мировое производство металлических порошков в настоящее время превышает один миллион тонн, а изделий из них – 650–750 тыс. т. В бл и- жайшее десятилетие можно ожидать увеличения производства в 1,5–2 раза.
Основные направления развития порошковой металлургии связаны прежде всего с преодолением затруднений в осуществлении литья тугоплавких металлов и изделий со специфическими свойствами (дисперсноупрочненных, фрикционных, антифрикционных, износостойких, высокопористых и других материалов).
Изготовление порошковых изделий взамен полученных из литых металлов позволяет значительно (60–70 %) снизить потери металла, количество обрабатывающего оборудования и обслуживающего его рабочего персона, а также энергозатраты на производство единицы продукции.
Начавшееся в 1950-е гг. быстрое развитие технологий порошковой металлургии обусловило необходимость унификации понятий в этой специфической области знаний.
В1947 г. для разработки международных стандартов, задачей которых являлось облегчение международного товарооборота и расширение сотрудничества в области интеллектуальной, научной, технической и экономической деятельности, двадцатью пятью странами была создана Международная организация по стандартизации (International Organization for Standardization – ISO). В настоящее время насчитывается уже более 100 участников – стран мира этой организации. В составе ISO в 1966 г. был создан технический ко-
Процессы порошковой металлургии. Курс лекций |
-15- |
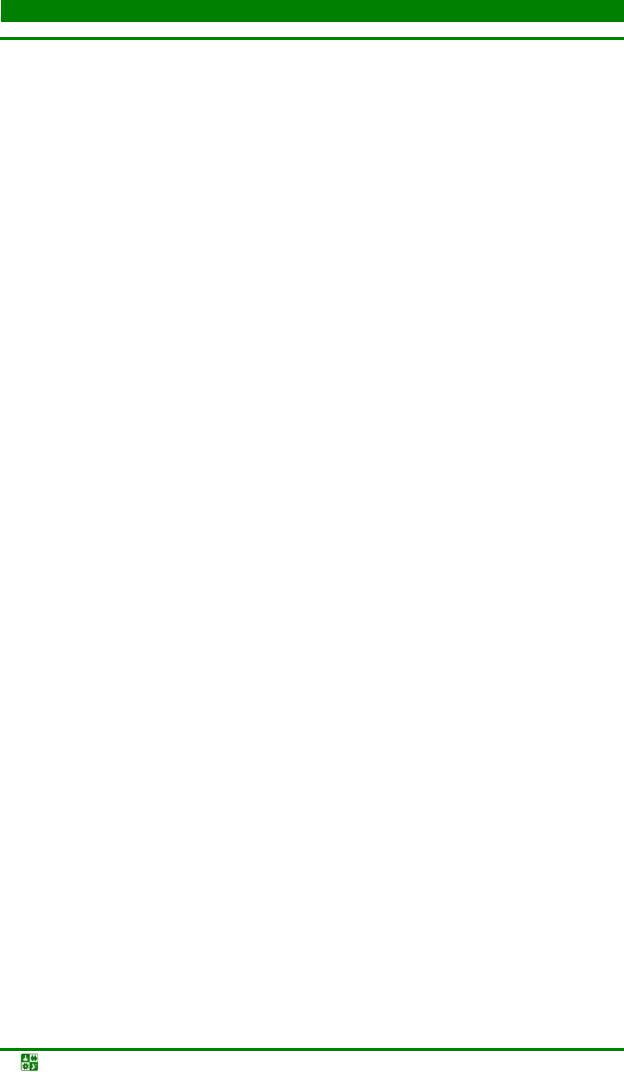
I. ПОЛУЧЕНИЕ ПОРОШКОВ
Лекция 1 История развития порошковой металлургии. Классификация методов получения порошков
митет 119, занимающийся стандартизацией в области порошковой металлургии (ИСО/ТК 119 «Порошковая металлургия, с секретариатом в Швеции»). Россия входит в состав 13 активных членов технического комитета.
В настоящее время в РФ действует ГОСТ 17359-82 «Порошковая металлургия. Термины и определения», разработанный на основе Международного стандарта ИСО 3252.
Классификацияметодовполученияпорошков
Металлический порошок – совокупность частиц металла, сплава или металлоподобного соединения размерами до одного миллиметра, находящихся во взаимном контакте и не связанных между собой.
Металлические порошки – основа порошковой металлургии, технология которой начинается с их получения. Метод производства и природа соответствующего металла, сплава или металлоподобного соединения определяют химические (содержание основного металла, примесей и загрязнений, пирофорность и токсичность), физические (форма, размер, удельная поверхность, истинная плотность и микротвердость частиц) и технологические (насыпная плотность, текучесть, уплотняемость, прессуемость и формуемость порошка) свойства получаемого металлического порошка.
Часто свойства порошка одного и того же металла существенно изменяются в зависимости от метода производства. Порошки, идентичные по химическому составу, могут иметь разные физические характеристики и резко различаться по технологическим свойствам, что приводит к значительным изменениям условий дальнейшего превращения порошка в готовые изделия и влияет на их свойства. Разнообразие требований, предъявляемых к порошкам в зависимости от области их применения, а также свойства (природа) самих металлов объясняют существование большого числа различных методов производства металлических порошков.
Общепринятым является условное деление этих методов на физикохимические и механические (табл. 1.1).
К физико-химическим методам относят технологические процессы производства порошков, связанные с глубокими физико-химическими превращениями исходного сырья. В результате получаемый порошок по химическому составу и структуре существенно отличается от исходного материала.
Механические методы обеспечивают превращение исходного материала в порошок без существенного изменения его химического состава. Чаще всего используют размол твердых материалов в мельницах различных конструкций и диспергирование расплавов.
Процессы порошковой металлургии. Курс лекций |
-16- |
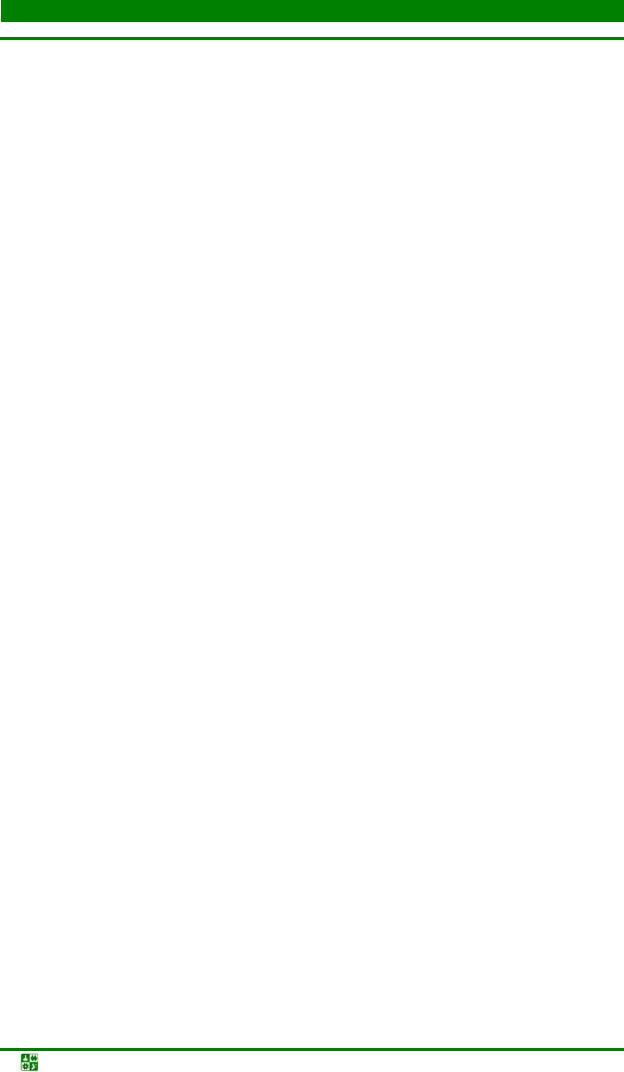
I. ПОЛУЧЕНИЕ ПОРОШКОВ
Лекция 1 История развития порошковой металлургии. Классификация методов получения порошков
|
|
|
Таблица 1.1 |
|||
|
Основные методы промышленного производства |
|
|
|||
|
|
металлических порошков |
|
|
|
|
|
|
|
||||
Методы получе- |
Характеристика метода |
Получаемые |
||||
ния порошков |
порошки |
|||||
|
||||||
|
|
Механические методы |
|
|
|
|
|
|
|
||||
Дробление и раз- |
Измельчение стружки, обрезков и компакт- |
Железо, медь, |
||||
мол твердых ма- |
ных материалов проводят в шаровых, вихре- |
марганец, латунь, |
||||
териалов |
|
вых, молотковых и других мельницах, КПД ко- |
бронза, |
хром, |
||
|
|
торых сравнительно невелик |
алюминий, стали |
|||
Диспергирование |
Струю расплавленного металла диспергиру- |
Алюминий, сви- |
||||
расплава |
|
ют механическим способом (воздействием цен- |
нец, цинк, бронза, |
|||
|
|
тробежных сил и др.) или действуя на нее по- |
латунь, железо, чу- |
|||
|
|
током энергоносителя (газа или жидкости) |
гун, сталь |
|
||
Обработка твердых |
Получают крупные порошки. При станочной |
Сталь, латунь, |
||||
(компактных) ме- |
обработке литых металлов или сплавов подби- |
бронза, магний |
||||
таллов резанием |
рают такой режим резания, который обеспечи- |
|
|
|
||
|
|
вает образование частиц, а не стружки |
|
|
|
|
|
|
Физико-химические методы |
|
|
|
|
|
|
|
|
|
||
Химическое вос- |
|
|
|
|
||
становление: |
|
|
|
|
||
оксидов и других |
Один из наиболее распространенных и эко- |
Железо, |
медь, |
|||
твердых соедине- |
номичных способов. Восстановителями служат |
никель, |
кобальт, |
|||
ний металлов |
газы (водород, конвертированный природный |
вольфрам, |
молиб- |
|||
|
|
газ и др.), твердый углерод (кокс, сажа и др.) и |
ден, титан, тантал, |
|||
|
|
металлы (натрий, кальций и др.). Исходным |
цирконий, |
уран, |
||
|
|
сырьем являются окисленные руды, рудные |
сплавы, |
а |
также |
|
|
|
концентраты, отходы и побочные продукты ме- |
соединения с не- |
|||
|
|
таллургического производства (например, про- |
металлами (карби- |
|||
|
|
катная окалина), а также различные химиче- |
ды, бориды и др.) |
|||
|
|
ские соединения металлов |
|
|
|
|
различных со- |
Один из самых экономичных способов, по- |
Медь, |
никель, |
|||
единений металлов |
зволяющий получать высококачественные ме- |
кобальт, |
серебро, |
|||
из водных |
раство- |
таллические порошки. Восстановитель – водо- |
золото |
|
|
|
ров |
|
род или оксид углерода. Исходное сырье – сер- |
|
|
|
|
|
|
нокислые или аммиачные растворы солей соот- |
|
|
|
|
|
|
ветствующих металлов |
|
|
|
|
газообразных |
Газообразные соединения металлов восста- |
Вольфрам, мо- |
||||
соединений раз- |
навливают водородом в реакторе кипящего |
либден, никель |
||||
личных металлов |
слоя или в плазме |
|
|
|
||
Электролиз водных |
На катоде под действием электрического то- |
Медь, |
никель, |
|||
растворов или рас- |
ка осаждают из водных растворов или распла- |
железо, |
серебро – |
|||
плавленных |
солей |
вов солей чистые порошки практически любых |
из водных раство- |
|||
различных |
метал- |
металлов. Стоимость порошков высока из-за |
ров; тантал, титан, |
|||
лов |
|
больших затрат электроэнергии и сравнительно |
цирконий, |
желе- |
||
|
|
низкой производительности электролизеров |
зо – из расплав- |
|||
|
|
|
ленных сред |
Процессы порошковой металлургии. Курс лекций |
-17- |
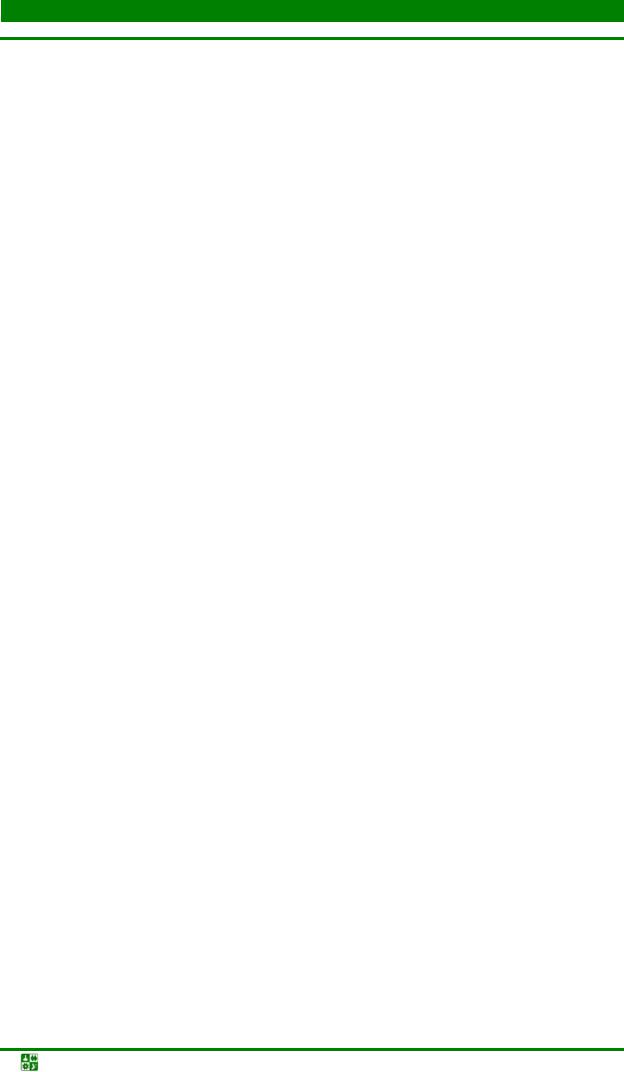
I. ПОЛУЧЕНИЕ ПОРОШКОВ
Лекция 1 История развития порошковой металлургии. Классификация методов получения порошков
Продолжение табл. 1.1
Методы получе- |
Характеристика метода |
Получаемые |
||
ния порошков |
порошки |
|||
|
||||
Диссоциация |
Соединение металла с СО типа Меа(СО)c |
Железо, |
никель, |
|
карбонилов |
разлагают нагреванием. Применяют в про- |
кобальт, вольфрам, |
||
|
мышленности для производства высококачест- |
молибден |
|
|
|
венных дисперсных порошков, стоимость ко- |
|
|
|
|
торых очень велика |
|
|
|
Термодиффузион- |
Чередующиеся слои или смесь порошков |
Латунь, |
сплавы |
|
ное насыщение |
разнородных металлов нагревают до темпера- |
на основе |
хрома, |
|
|
туры, обеспечивающей их активное взаимодей- |
высоколегиро- |
||
|
ствие |
ванные стали |
||
|
|
|
||
Испарение конден- |
Для получения порошка металл испаряют и |
Цинк, кадмий и |
||
сация |
затем конденсируют его пары на холодной по- |
другие металлы с |
||
|
верхности. Порошок является тонкодисперс- |
невысокой темпе- |
||
|
ным, но содержит большое количество оксидов |
ратурой испарения |
||
Межкристаллит- |
В компактном (литом) металле или сплаве |
Коррозионно- |
||
ная коррозия |
при помощи химического травителя разрушают |
стойкие и хромо- |
||
|
межкристаллитные прослойки |
никелевые стали |
К механическим методам получения порошков относится и грануляция расплава (образование порошка происходит при сливании расплавленного металла в жидкость). Однако получаемые частицы имеют размеры больше одного миллиметра (до 2–5 мм). С помощью этого метода получают гранулы таких металлов, как олово, свинец, цинк, висмут и пр. Совокупность методов их получения и превращения в изделия относится к другой области металлургического производства – гранульной металлургии.
Выбор метода получения металлического порошка проводят на основе анализа требований, предъявляемых к конечной продукции, и экономической оценки процессов, влияющих на его себестоимость (размер капиталовложений, затрат энергии, стоимости исходного сырья и пр.).
В зависимости от размеров частиц порошки весьма условно подразделяют на следующие группы: нано- (размер частиц < 0,01 мкм), ультра- (0,01–0,1 мкм), высокодисперсные (0,1–10 мкм), мелкие (10–40 мкм), средние (40–250 мкм) и крупные (250–1 000 мкм).
Контрольныевопросыизадания
1.Из какого сырья получали железные изделия до XIV в.?
2.Кто из наших соотечественников разработал в XIX в. способ получения изделий из платины?
3.Назовите причины возрождения интереса к порошковой металлургии в конце XIX в.
Процессы порошковой металлургии. Курс лекций |
-18- |
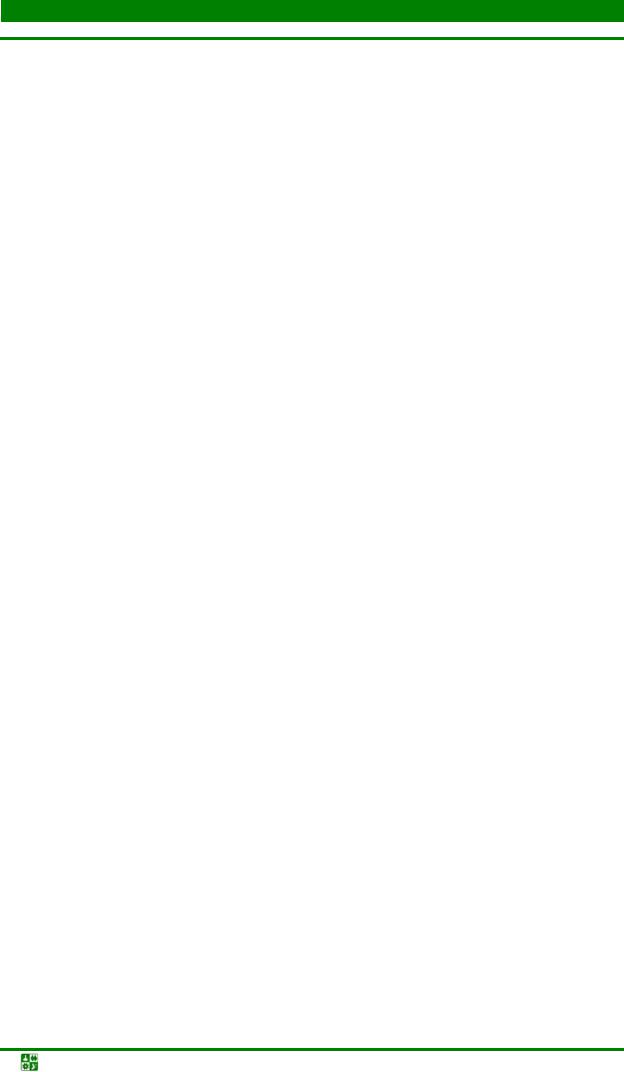
I. ПОЛУЧЕНИЕ ПОРОШКОВ
Лекция 1 История развития порошковой металлургии. Классификация методов получения порошков
4.Укажите основные переделы и преимущества порошковой металлургии перед традиционной металлургией.
5.На какие основные группы делятся методы производства порош-
ков?
6.Перечислите механические методы получения порошков.
7.Перечислите физико-химические методы получения порошков.
8.Назовите основные группы порошков и их соответствие размерно-
му ряду.
9.Что определяют международные стандарты в области порошковой металлургии?
10.Решению каких задач способствуют международные стандарты серии ИСО в области порошковой металлургии?
Лекция2 Восстановителиизащитныесреды
План лекции
1.Классификация восстановителей и защитных сред.
2.Методы получения и характеристики твердых и газообразных восстановителей (защитных сред).
3.Методы получения и характеристики газообразных сред сложного
состава.
Классификациявосстановителейизащитныхсред
Технологические режимы многих процессов порошковой металлургии сопряжены с использованием восстановительных и защитных сред. Восстановителями обычно служат газы (чистый CО, Н2 или среды, содержащие эти газы в различной пропорции), твердый углерод и металлы (Ca, Na, Mg). При спекании порошковых изделий восстановители играют роль защитных сред. Методы получения и очистки восстановителей и защитных сред идентичны. Основное отличие восстановителей от защитных сред состоит в том, что в качестве защитных сред могут использоваться нейтральные (инертные) газы, а также сыпучие инертные материалы (чаще всего оксиды алюминия и магния).
Защитные среды позволяют исключить взаимодействие порошковых изделий с кислородом и азотом, а также придать изделиям необходимые свойства (например, упрочнить поверхность изделий). Они подразделяются на газовые, сыпучие и комбинированные (состоящие из твердых засыпок и защитного газа). К защитным средам относится вакуум.
Процессы порошковой металлургии. Курс лекций |
-19- |
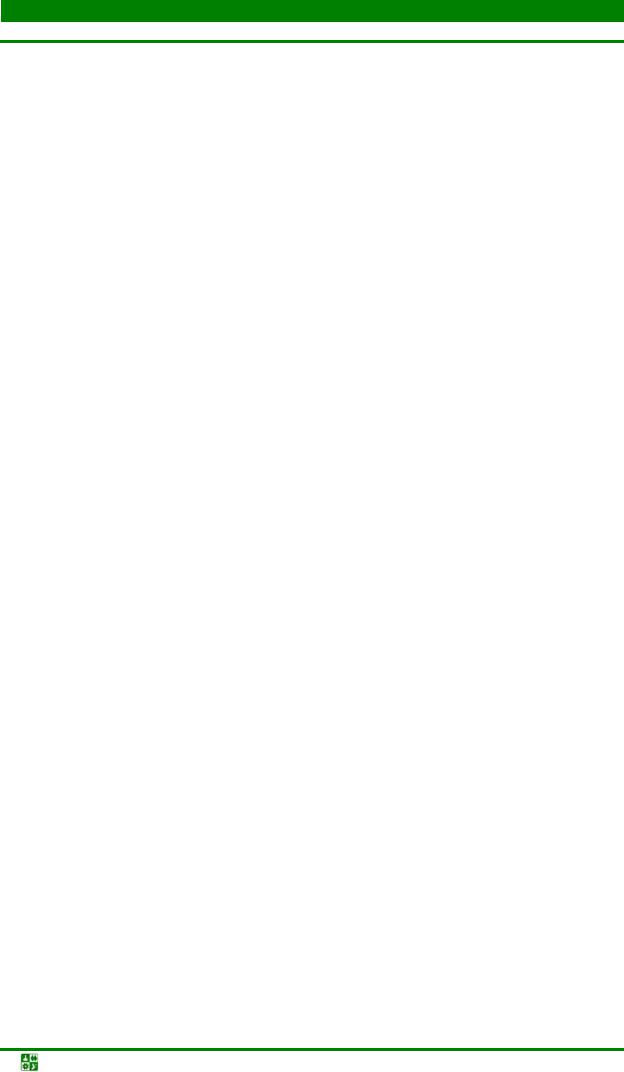
I. ПОЛУЧЕНИЕ ПОРОШКОВ
Лекция 2 Восстановители и защитные среды
По составу газовые защитные среды можно разделить на следующие системы:
Н2–Н2О;
H2–Н2О–N2;
СО–СО2–N2;
СО–СО2–H2–H2О–N2;
СО–СО2–Н2–Н2О–СН4–N2;
азот, инертные газы (аргон, гелий), вакуум.
Выбор восстановительной или защитной среды для восстановления химических соединений металлов и спекания порошковых материалов с целью получения заданных свойств определяется термодинамическими характеристиками систем пористое твердое тело – защитный газ (восстановитель). При этом учитывается особенность порошковых материалов, удельная поверхность пористых тел, наличие оксидных пленок на поверхности частиц и в порах.
Для создания надежного контакта между спекаемыми частицами сформованного изделия необходимо обеспечить максимальное восстановление окисных пленок на их поверхности, поэтому защитная газовая среда при спекании должна быть восстановительной, т.е. содержать газы-восстановители (Н и/или СО).
Условие равновесия, при котором соотношение металла и его оксидов с течением времени остается неизменным, характеризуется константами равновесия:
К1 = РН2 /РН2О; К2 = РСО/РСО2. |
(1.1) |
При спекании (восстановлении) порошковых изделий состав защитной газовой среды выбирают по значению констант равновесия для того элемента, у которого они наибольшие.
По условиям взаимодействия с восстановительными газами Н2, СО, Н2 + СО металлы можно разделить на три группы.
К первой группе относятся медь, никель, кобальт, молибден, вольф-
рам и железо, восстановление оксидов которых возможно при использовании любой из указанных газовых сред. С повышением температуры константы равновесия возрастают для меди, никеля, кобальта, т.е. снижаются равновесные содержания Н2О и СО 2, что создает опасность окисления в области высоких температур.
Во вторую группу объединяют хром, марганец, кремний и ванадий,
восстановление оксидов которых возможно только водородом. Константы равновесия понижаются с ростом температуры, т.е. равновесные содержания Н2О и СО2 в защитном газе повышаются, облегчая восстановление оксидов.
К третьей группе относятся алюминий, бериллий, титан, цирконий,
восстановление оксидов которых возможно только остро осушенным водородом в присутствии геттеров.
Процессы порошковой металлургии. Курс лекций |
-20- |
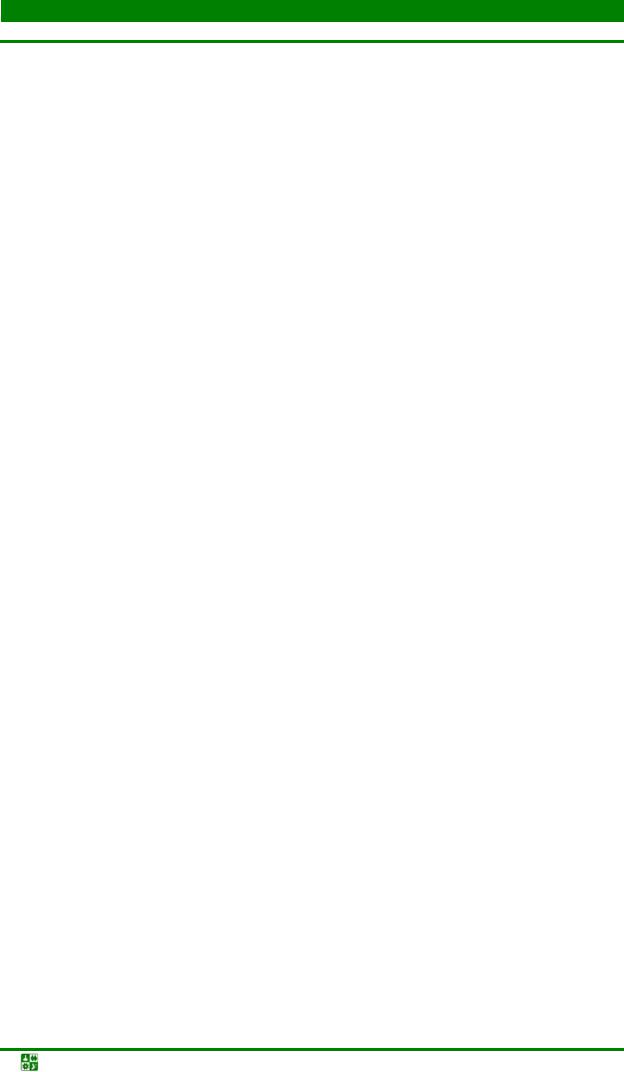
I. ПОЛУЧЕНИЕ ПОРОШКОВ
Лекция 2 Восстановители и защитные среды
Методыполученияихарактеристикитвердых игазообразныхвосстановителей(защитныхсред)
Водород – один из наиболее распространенных элементов (составляет около 1 % от общей массы Земли). Водород входит в состав воды (около 11 % мас.), нефти, природных газов. В свободном состоянии практически не встречается. С кислородом водород образует гремучую смесь при содержании водорода 4–74 % (температура воспламенения в смеси с воздухом
550–590 °С).
Технический водород получают электролизом, каталитическим разложением углеводородов, железоконтактным (железопаровым) методом.
При электролитическом методе через водный электролит (слабых водных растворов гидроксида натрия, калия, NаСl, раствора серной кислоты
– чистая вода плохо проводит ток) пропускают электрический ток, в результате чего получают водород, а также кислород, хлор или сернистый газ.
Пропускание электрического тока через растворы ведут в моноили биполярных электролизерах, в которых идет разрядка ионов Н+ и гидроксильных групп ОН-, образующихся при разложении воды по реакции
Н2О → Н2 + ОН-
Ионы водорода перемещаются к катоду, где превращаются в атомы, которые практически мгновенно образуют молекулу Н2, в результате чего на перфорированном катоде начинается выделение газообразного водорода, который удаляется через отверстия в теле катода. На аноде ионы гидроксида образуют воду и кислород (2ОН- – 2е → Н2О + 0,5О2).
Теоретические расчеты показывают, что на производство одного кубического метра водорода необходимо затратить 2,95 кВт·ч электроэнергии. Однако практически тратится около 5–6 кВт·ч, так как приходится подавать на ванну более высокое напряжение, избыток которого тратится на преодоление сопротивления электролита, раствора и электродов. Воду, которая подается в электролизер, предварительно очищают от примесей путем паровой перегонки или на ионообменных смолах.
В железоконтактном методе водород получают путем взаимодействия нагретого до температуры 800–900 оС железа с водяным паром. Для производства водорода используют установки (рис. 1.1), которые вырабатывают примерно 500 м3 водорода в час. Образующиеся в процессе восстановления газы используют для создания необходимого теплового режима подогревателя.
Процессы порошковой металлургии. Курс лекций |
-21- |
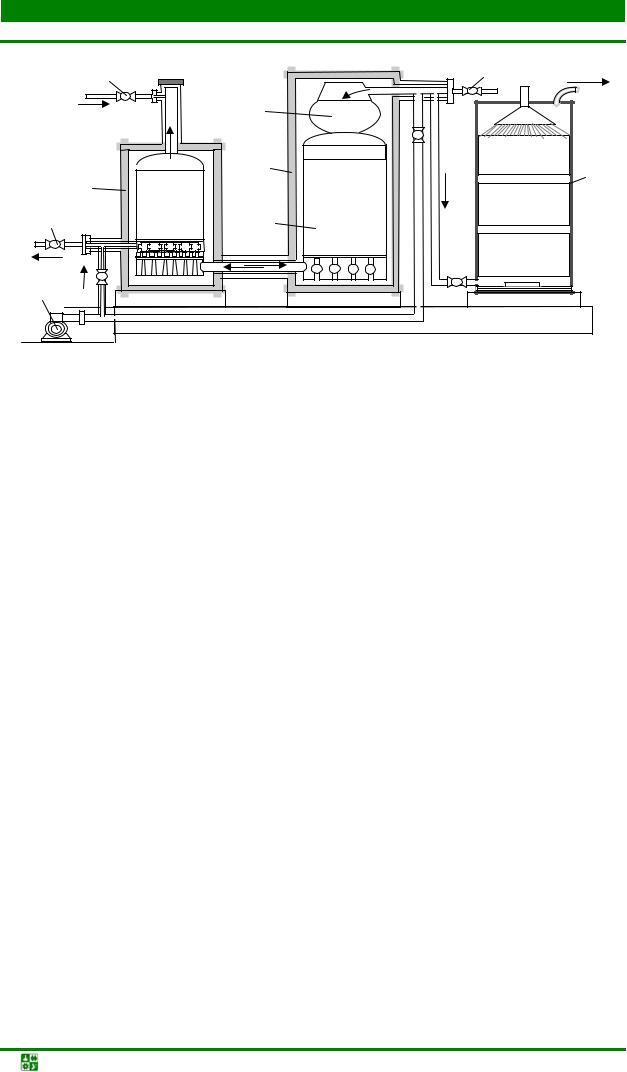
I. ПОЛУЧЕНИЕ ПОРОШКОВ
Лекция 2 Восстановители и защитные среды
4
2
7
8
|
4 |
К газгольдеру |
|
|
|
3 |
|
|
1 |
|
6 |
5 |
|
|
Рис. 1.1. Схема установки для производства водорода железоконтактным методом: 1
– колонна-генератор водорода; 2 – подогреватель пара; 3 – теплообменник; 4 – клапаны подачи первичного водяного пара; 5 – отделение генерации водорода, заполненное железосодержащим порошковым материалом; 6 – скруббер; 7 – клапан регулировки давления подогретого пара; 8 – насос
На втором этапе в установку через предварительно разогретый подогреватель подают первичный водяной пар, который, нагреваясь до температуры около 900 оС, поступает в генератор, где разлагается с выделением водорода по реакции
Fe2O3 + Н2О → FeхO + Н2 |
(1.2) |
Смесь водорода и неразложившегося водяного пара охлаждается, проходя через теплообменник, до температуры 300–400 оС и поступает в скруббер, а затем в газгольдер. Полученный этим методом водород имеет высокую стоимость, поэтому подобные установки используются редко.
Применение водорода рекомендуется при восстановлении (спекании) изделий из порошков металлов, образующих трудновосстановимые окислы бериллия, ванадия, кремния, марганца, хрома, циркония, а также твердых сплавов. В этих случаях водород должен подвергаться острой осушке и удалению остатков кислорода в присутствии геттеров.
Технический оксид углерода обычно получают газификацией малосернистого кокса или древесного угля с применением кислородного дутья. В некоторых случаях для восстановления химических соединений могут использовать газообразные выбросы фосфорных заводов, содержащие до 80 % СО,
Процессы порошковой металлургии. Курс лекций |
-22- |
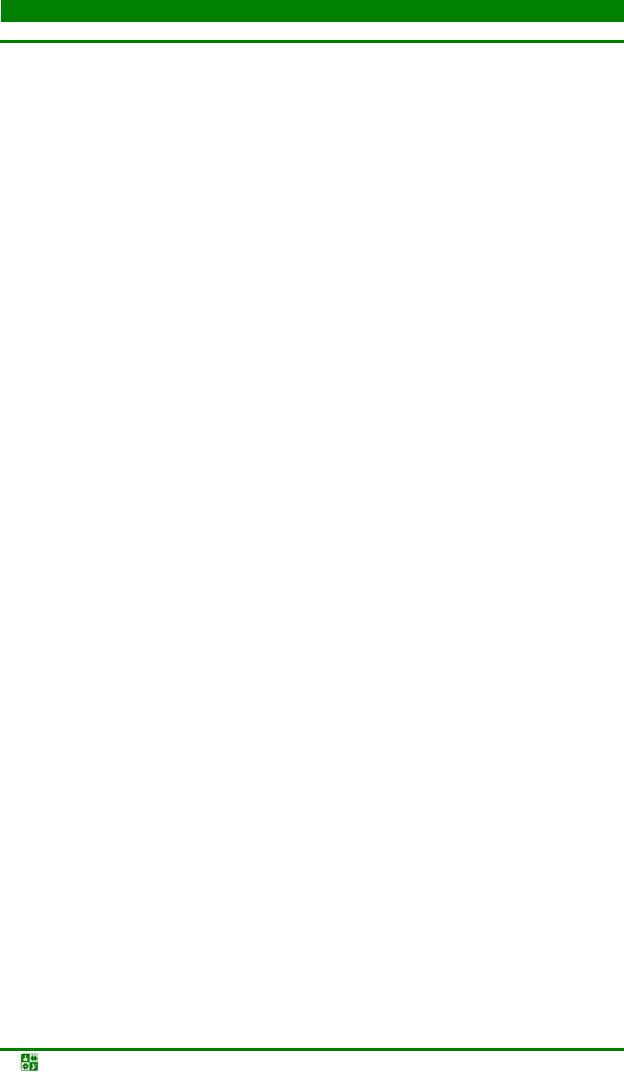
I. ПОЛУЧЕНИЕ ПОРОШКОВ
Лекция 2 Восстановители и защитные среды
около 0,5–1,0 % таких газов, как Н2 и N2, и до 18–20 % СО2. Оксид углерода ядовит и взрывоопасен. Предельно допустимая концентрация СО в помещении составляет 0,02 мг/м3. Температура воспламенения СО в смеси с воздухом равна 610–658 оС.
Кокс получают коксованием продуктов нефтепереработки. Он содержит до 93–98 % С и до 3 % Н2 (в углеводородных соединениях), около 2–4 % S, до 1 % золы.
Термошлыб представляет собой мелкие отходы термоантрацитного производства. Термошлыб содержит до 75–80 % углерода, около 10–15 % золы, 3,0–3,5 % серы, до 5 % органических летучих веществ и небольшое количество влаги (менее 1 %).
Древесный уголь получают путем сжигания древесины с недостатком воздуха. Он чище нефтяного кокса по сере (менее 0,03 %), но имеет более высокую зольность (до 4,5 %). Кроме того, древесный уголь содержит большое количество летучих органических соединений (около 15–20 %) и влагу (3–5 %).
Сажу получают либо сжиганием (при температуре 1 200 оС) жидких нефтепродуктов (солярного дистиллята, лигроина, очищенного керосина) в фитильных горелках-лампах (ламповая сажа), либо сжиганием природного газа в специальных камерах с недостатком воздуха (газовая сажа). Газовая сажа чище ламповой по сере (менее 0,16 %), имеет более высокое содержание углерода (99,5 %), но «грязнее» по золе (около 0,16 %).
Высокая химическая активность сажи объясняется тем, что это весьма мелкий порошок трубчатого строения. Длина отдельных частиц-трубочек составляет сотые доли микрометра, а диаметр – тысячные доли микрометра. Удельная поверхность этого восстановителя может быть до 25 м3/г.
Методыполученияихарактеристики газообразныхсредсложногосостава
В большинстве случаев для получения металлических порошков или защиты изделий при спекании используются восстановители (газовые защитные среды) сложного состава (табл. 1.2).
Диссоциированный аммиак содержит 75 % Н2 и 25 % N2. В большин-
стве случаев является хорошим заменителем водорода. Не рекомендуется при спекании хромистых, нержавеющих сталей и сплавов, содержащих титан, ниобий и молибден, в связи с возможностью образования хрупких нитридов.
Процессы порошковой металлургии. Курс лекций |
-23- |
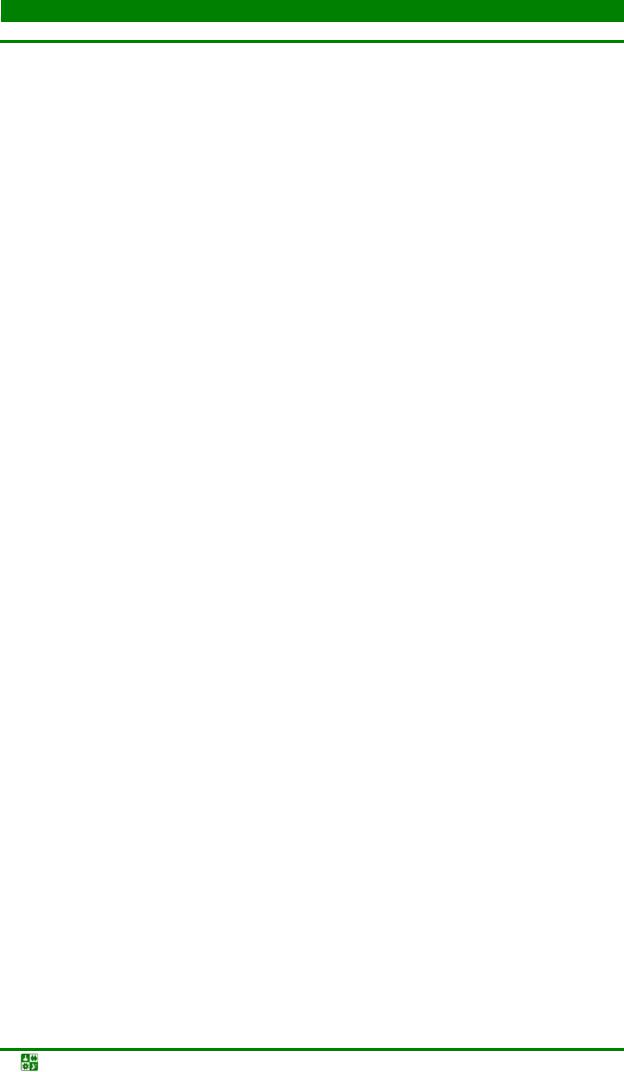
I. ПОЛУЧЕНИЕ ПОРОШКОВ
Лекция 2 Восстановители и защитные среды
Таблица 1.2
Способы получения применяемых восстановителей (защитных газовых сред) сложного состава
Тип среды |
Исходное |
Способ получения среды |
|
соединение |
|||
|
|
||
Н2–Н2О–N2 |
Диссоциированный |
Разложение в диссоциаторе. |
|
Частичное сжигание при αвз = 0,7–0,9 и |
|||
аммиак |
|||
|
осушка силикагелем или цеолитом |
||
|
|
||
|
|
Получение из древесного угля при темпе- |
|
СО–СО2 |
Генераторный газ |
ратуре 1 000 °С и осушка силикагелем или |
|
|
|
цеолитом |
|
|
Эндотермический газ |
Неполное сжигание (αвз = 0,25–0,30) при- |
|
|
родного газа или пропана |
||
|
Экзотермический газ |
Неполное сжигание (αвз = 0,6) углеводоро- |
|
СО–СО2–Н2–Н2О–N2 |
дов, охлаждение, очистка от СО2, сушка с и- |
||
|
ликагелем или цеолитом |
||
|
Доменный газ |
Очистка от СО2, сушка силикагелем или |
|
|
цеолитом |
||
|
|
||
|
Конвертированный |
Высокотемпературная парогазовая кон- |
|
|
природный газ |
версия (1 100 °С при СН4:Н2О = 1:1) |
|
СО–СО2–Н2–Н2О– |
Науглероживающий |
Неполное сжигание (αвз = 0,4) углеводоро- |
|
–СН4–N2 |
газ |
дов с последующей добавкой природного газа |
П р и м е ч а н и е. αвз – коэффициент, характеризующий отношение компонентов газовой смеси (содержание воздуха, приведенное к единице).
Операция получения диссоциированного аммиака включает испарение жидкого аммиака, отделение масла, подогрев в теплообменнике и разложение в диссоциаторе с дисперсным катализатором при подводе тепловой энергии извне.
Газовая смесь диссоциации поступает в теплообменник для подогрева жидкого аммиака и подвергается после этого осушке силикагелем до точки росы (от –40 до –50 °С).
Генераторный газ получают пропусканием воздуха или паровоздушной смеси через раскаленный уголь с последующей очисткой и осушкой. Может применяться при науглероживающем спекании или цементации порошковых изделий конструкционного назначения.
Конвертированный природный газ получают конверсией метана при-
родного газа с водяным паром:
СН4 + Н2О = СО + 3Н2 |
(1.3) |
Конверсия происходит при 1 100 °С в присутствии катализаторов, содержащих никель. Нагрев парогазовой смеси сопровождается реакциями об-
Процессы порошковой металлургии. Курс лекций |
-24- |
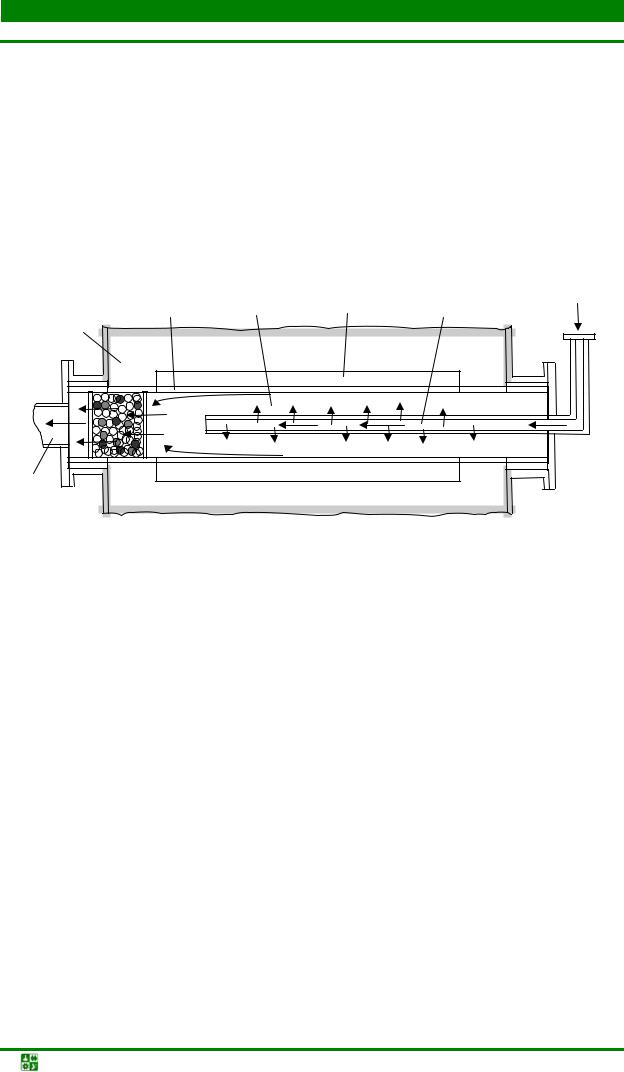
I. ПОЛУЧЕНИЕ ПОРОШКОВ
Лекция 2 Восстановители и защитные среды
разования СО2, диссоциации метана, горения углерода, выделяющегося при распаде СН4 и пр. Доля этих побочных реакций зависит от температуры процесса, соотношения СН4 и Н2О, качества катализатора, конструкции аппарата конверсии. Конвертированный природный газ хорошего качества получают в печах, трубчатый реактор которых изготовлен из стеклоуглерода или карбофракса (рис. 1.2). Внутри реактора устанавливается трехсекционный шамотный муфель таким образом, чтобы между ним и внешней трубой сохранялся зазор. В качестве катализатора реакции используются порошки никеля, введенные в поры муфеля.
|
|
|
|
Парогазовая |
2 |
3 |
4 |
5 |
смесь |
|
1
6
Рис. 1.2. Схема рабочей зоны установки выработки конвертированного природного газа: 1 – тепловая изоляция рабочей зоны печи; 2 – реактор; 3 – шамотный муфельсердечник с никелевым катализатором; 4 – топочные зазоры для нагрева реактора; 5 – перфорированная труба для подачи парогазовой смеси в муфель; 6 – труба для транспортировки восстановителя
Парогазовую смесь для конверсии готовят насыщением разогретого до 85 °С природного газа в скруббере, орошаемом горячей водой (температура воды около 93–98 °С). Из скруббера парогазовая смесь направляется в подогреватель установки, где разогревается и через канал в центре шамотного муфеля поступает в печь. Обогрев печи осуществляется газовыми горелками.
После конверсии исходных продуктов полученный восстановитель через кольцевой зазор поступает в трубопровод и направляется к газовой подстанции печи восстановления.
Конвертированный природный газ значительно дешевле водорода, а его качество может быть улучшено последующими операциями очистки и осушки. После осушки и очистки конвертированный газ применяют при получении порошков восстановлением металлов из оксидов, а также при спекании порошков изделий на основе углеродистых сталей.
Эндотермический газ получают при сжигании углеводородного сырья в условиях, при которых газовоздушная смесь содержит 25–35 % от теоретического необходимого на полное сжигание газа воздуха (коэффици-
Процессы порошковой металлургии. Курс лекций |
-25- |
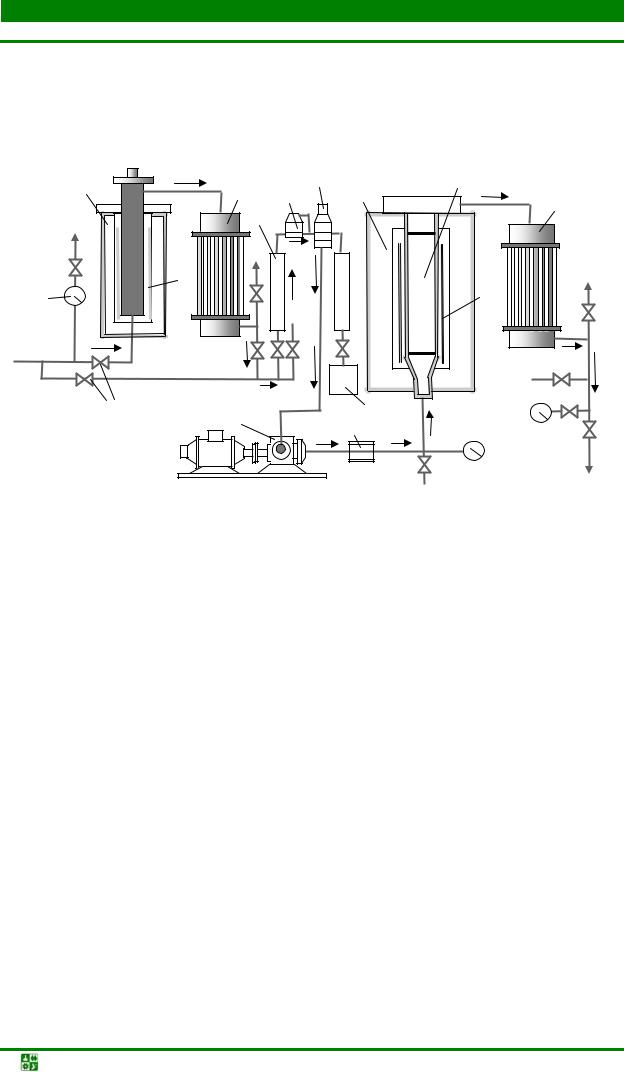
I. ПОЛУЧЕНИЕ ПОРОШКОВ
Лекция 2 Восстановители и защитные среды
ент αвз = 0,25–0,35). Для поддержания процесса извне подводится тепловая энергия.
Исходный газ подается в установку через регулятор давления и попадает в камеру сероочистки (рис. 1.3).
1 |
3 |
5 |
6 |
7 |
8 |
|
|
|
4 |
|
|
|
9 |
|
|
|
|
|
|
|
|
14 |
|
|
|
|
|
2 |
|
|
|
|
|
14 |
13 |
10 |
|
|
11 |
12 |
|
|
|
|
|
|
||
|
|
|
|
|
|
К печи
Рис. 1.3. Схема установки для получения эндогаза (установка ЭН-60): 1 – камера сероочистки; 2 – манометр; 3 – холодильник; 4 – ротаметр; 5 – регулятор давления; 6 – смесительный клапан; 7 – газогенератор; 8 – катализатор; 9 – холодильник; 10 – газодувка; 11 – заслонка; 12 – гидрозатвор; 13 – клапаны; 14 – нагревательный элемент
В камере сероочистки газ проходит через фильтр-катализатор, заполненный смесью оксидов цинка и хрома и нагретый до температуры 300–350 °С. Нагрев катализатора до необходимой температуры проводится с помощью нихромового нагревателя. Очищенный газ охлаждается в холодильнике и подается в газосмесительный аппарат, в котором газ и воздух смешиваются в определенной пропорции. Приготовленная газовоздушная смесь через гидрозатвор и аппарат защиты смеси от воспламенения (пламягаситель и обратный клапан) поступает в газогенератор.
Газогенератор представляет собой стальную трубу с толщиной стенки 15 мм, заключенную в кожух из профилированной стали. Корпус газогенератора внутри футеруется легковесным огнеупором.
Парогазовая смесь поступает снизу в реторту, размещенную в центральной части реактора и заполненную порошком никеля (катализатором). Реторту с помощью ленточного нагревателя разогревают до температуры около 1 050 °С. Для генераторов производительностью более 125 м3/ч применяют газовый обогрев.
Процесс сжигания исходного газа ведут в две стадии. На первой стадии метан взаимодействует с кислородом по реакции
Процессы порошковой металлургии. Курс лекций |
-26- |
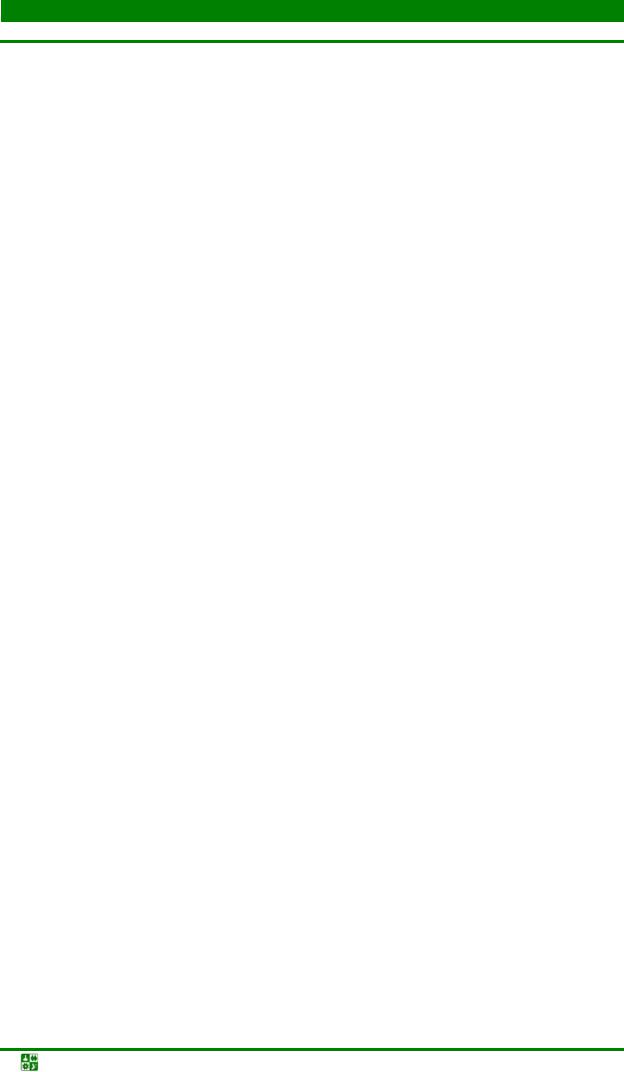
I. ПОЛУЧЕНИЕ ПОРОШКОВ
Лекция 2 Восстановители и защитные среды
СН4 + 2О2 = СО2 + 2Н2О + Q |
(1.4) |
на второй – избыточный метан взаимодействует с продуктами первой реакции с образованием водорода и СО:
СН4 + СО2 = 2СО + 2Н2 – Q |
(1.5) |
СН4 + Н2О = СО + 3Н2 – Q |
(1.6) |
Суммарный тепловой эффект этих реакций отрицательный, поэтому процесс требует подведения тепла извне. Полученный эндогаз (18–20 % СО, 38–40 % Н2, около 1 % СО2 и СН4, 34–38 % N2) подвергают охлаждению, осушке и очистке.
Экзотермический газ получают частичным сжиганием углеводородов с таким количеством воздуха (αвз= 0,6–0,9), при котором горение протекает за счет тепла, выделяемого в процессе реакции.
«Богатый» экзогаз (полученный из смеси с αвз = 0,6) содержит
10–13 % СО, 4–5 % СО2, 15–18 % Н2, до 1 % О2 и около 63–70 % N2.
«Бедный» экзогаз (полученный из смеси сαвз =0,9)содержит до 1 %СО, 10–13 % СО2, 0,7 % Н2, остальное – азот.
Генераторный и водяной газы образуются при взаимодействии нагретого до температуры около 1 000–1 100 °С кокса, каменного или древесного угля с воздухом или водяным паром.
Генераторный газ содержит 28–30 % СО, около 0,5 % СО2, до 5 % Н2, до 1 % О2 и углеводородов, 63–65 % N2.
Водяной газ содержит около 36 % СО, до 48–49 % Н2 и до 16 % N2,
СО2, СН4 и Н2О.
Вакуум бывает низким (1–10 Па), средним (1–1 000 мПа), высоким (1–1 000 мкПа) и сверхвысоким (< 1 мкПа).
Контрольныевопросыизадания
1.Для чего нужны защитные среды?
2.Какие защитные среды применяют на производствах порошковой металлургии?
3.Перечислите составы газовых защитных сред.
4.Назовите жидкие защитные среды.
5.Чем определяется выбор защитной среды?
6.Перечислите основные методы получения газовых защитных сред.
7.Что является основой газовых защитных сред?
8.Назовите наиболее активные восстановители.
Процессы порошковой металлургии. Курс лекций |
-27- |
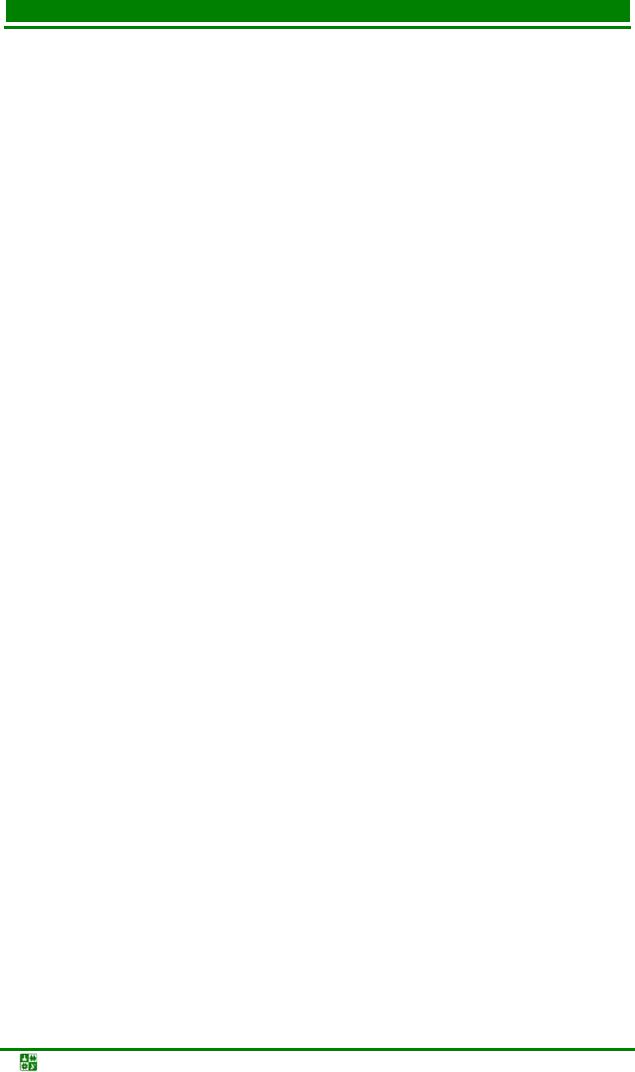
I. ПОЛУЧЕНИЕ ПОРОШКОВ
Лекция3 Восстановителиизащитныесреды
План лекции
1.Жидкие и сыпучие защитные среды и восстановители.
2.Оборудование для восстановления и спекания материалов.
3.Методы очистки и осушки защитных газовых сред.
Жидкиеисыпучиезащитныесредыивосстановители
Жидкие защитные среды образуются при плавлении солей металлов, шлаков, стекол, легкоплавких окислов.
Стеклянный расплав применяется при спекании изделий из порошков химически активных металлов, например, при спекании магнитных материалов. Спекание производят на воздухе под слоем расплава оконного стекла при 1 150–1 200 °С. В стеклянном расплаве рекомендуется спекать изделия с пористостью не более 18 %, при большей пористости наблюдается пропитка поверхности деталей стеклянным расплавом. Для удаления стекла со спеченных изделий производят их подстуживание от температуры 300 °С в воду с последующей выдержкой на воздухе в течение 1–3 ч.
Твердые защитные засыпки обычно состоят из порошков химически активных металлов и их соединений (Al, Mg, Ti, Cr, гидрид титана) и при необходимости инертного наполнителя (прокаленный глинозем, оксид магния и др.), а также из прокаленного глинозема с добавкой углерода в виде сажи, древесного угля.
Металлы и их соединения. При сопоставлении термодинамических параметров восстанавливаемых соединений и восстановителей выясняется, что образование соединений кальция, магния, алюминия, натрия, калия, циркония и бериллия сопровождается максимальной убылью свободной энергии.
Однако по определенным условиям (дороговизна металлического порошка, высокая температура плавления и восстановления и пр.) на практике чаще всего используют только несколько из этих металлов – кальций, натрий и магний.
Выбор этих металлов для металлотермического восстановления определяется следующими факторами:
высокой летучестью паров металлов; отсутствием реакций образования устойчивых соединений с большин-
ством металлов; сравнительно низкой стоимостью;
Процессы порошковой металлургии. Курс лекций |
-28- |
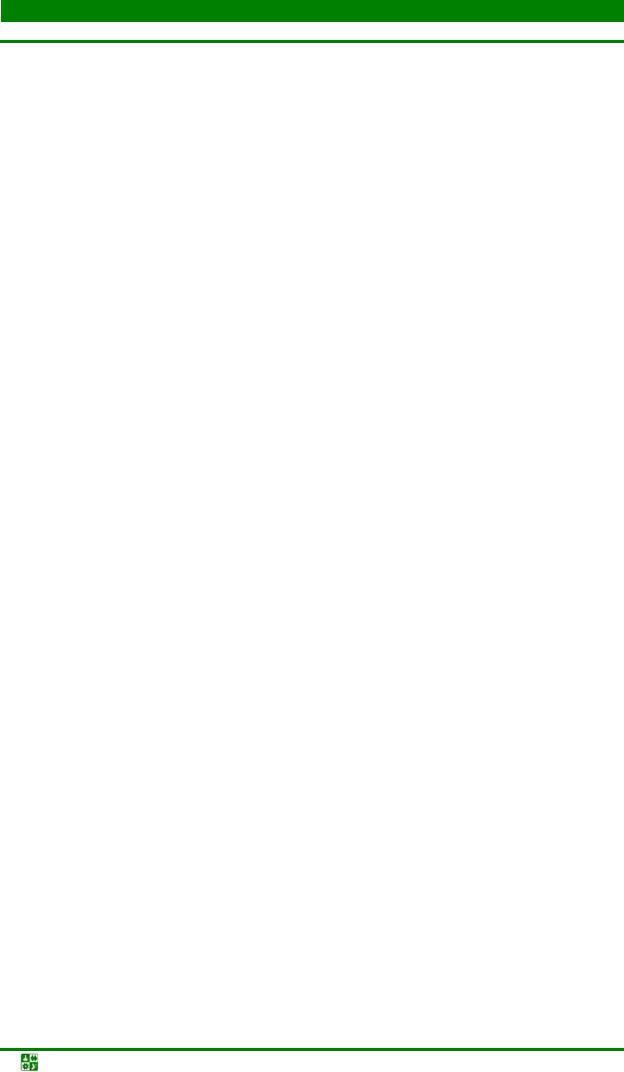
I. ПОЛУЧЕНИЕ ПОРОШКОВ
Лекция 3 Восстановители и защитные среды
возможностью довольно простого (легкого) отделения соединения ме- талла-восстановителя от полученного порошка или спекаемого изделия и пр.
В ряде случаев для восстановления используют не сами металлы, а их гидриды или карбиды, в частности гидрид или карбид кальция.
Оборудованиедлявосстановленияиспеканияматериалов
Для получения порошков и спекания порошковых формовок используют печи, различающиеся как по конструкции, так и по способу нагрева. Выбор типа печи зависит от многих факторов:
характера защитной среды, температуры и выдержки при спекании, режима нагрева и охлаждения, требуемой производительности и т.п.
Получение порошков и спекание изделий из порошков чаще всего проводят в печах непрерывного действия (муфельных, трубчатых и пр.), в которые газообразный восстановитель подается по принципу противотока (навстречу движению материала). Обычно для печей непрерывного действия характерно наличие трех рабочих зон:
1)зоны нагрева,
2)горячей зоны (зоны максимальной температуры),
3)зоны охлаждения.
При спекании изделий из порошков в первой зоне печи происходит испарение или выжигание и удаление смазки (пластификатора), введенной в
шихту перед формованием порошка, а также снятие (релаксация) напряжений, имеющихся в порошковой формовке. В горячей зоне осуществляется собственно спекание, а в третьей зоне – охлаждение материала (изделия) с заданной скоростью до температуры, обеспечивающей безокислительную выгрузку на воздух.
При непрерывной транспортировке материалов через печь используют различные загрузочные устройства (конвейеры, лодочки, тигли и пр.). Перемещение материалов через печное пространство обеспечивается с помощью роликов (рольгангов), толкателей различного типа.
В некоторых случаях восстанавливаемый материал или спекаемые заготовки укладывают в поддоны или непосредственно на конвейерную ленту из окалиностойкой проволоки. Общая длина печей различного типа лежит в пределе от 5–6 до 15–25 м, при длине зоны спекания от 3 до 6 –15 м. Рабочая температура в печи зависит от материала нагревательных элементов и составляет 1 000–2 000 °С.
Толкательные муфельные или трубчатые печи наиболее просты по своей конструкции. Продвижение лодочек (поддонов) из графита, стали, кар-
Процессы порошковой металлургии. Курс лекций |
-29- |
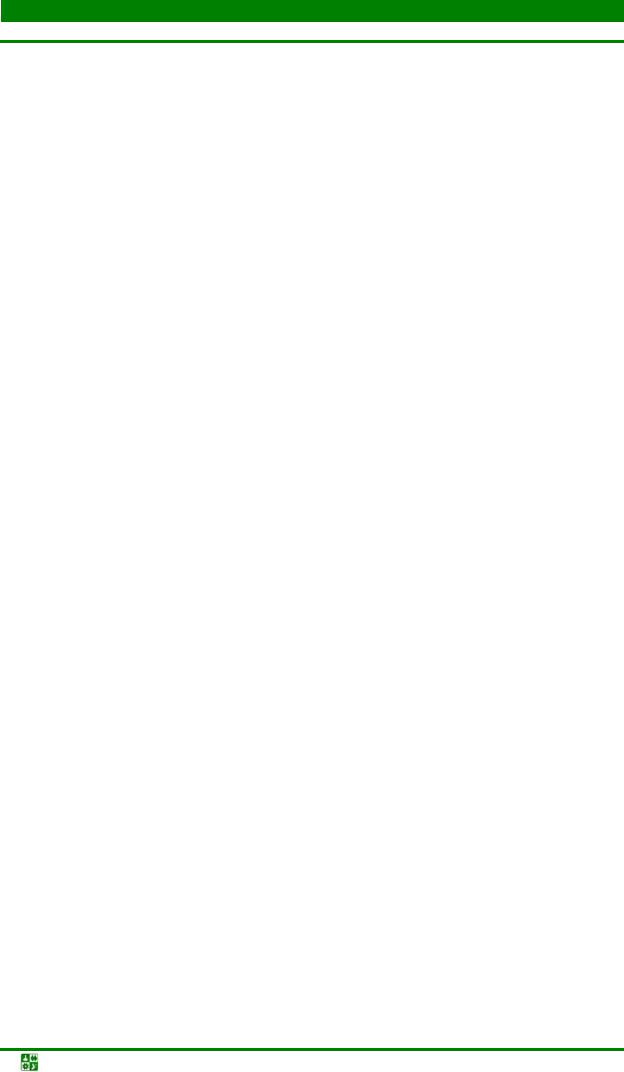
I. ПОЛУЧЕНИЕ ПОРОШКОВ
Лекция 3 Восстановители и защитные среды
бида кремния, в которые загружены восстанавливаемый материал или спекаемые изделия, производится механическим толкателем.
Печи непрерывного действия экономичны и обеспечивают равномерное распределение температур в зоне нагрева, благодаря чему порошковые изделия после спекания имеют однородные свойства.
Электропечи периодического действия широко применяют в порош-
ковой металлургии при проведении металлотермических процессов восстановления. Они могут быть прямого или косвенного электронагрева, а также индукционные.
Спекание в водороде, нейтральном газе или вакууме при температуре до 2 500 °С можно осуществлять в электропечах косвенного нагрева. В камерных печах загрузку и выгрузку изделий выполняют через дверцу, расположенную в передней стенке печи. В шахтных печах загрузку изделий в цилиндрическую вертикальную шахту – рабочую зону печи – осуществляют сверху, опуская изделие на стационарную подставку, находящуюся в нижней части шахты. В элеваторных печах изделия вдвигают в цилиндрическую вертикальную рабочую зону снизу, на подставке, конструктивно объединенной со съемным днищем печи. В колпаковых печах (колпаков у одной печи может быть несколько) изделие перед началом нагрева устанавливают на стационарной подставке и накрывают колпаком, внутри которого смонтированы нагреватели, тепловая изоляция и другие конструктивные элементы печи.
В таких электропечах косвенного нагрева применяют в основном нагреватели трех типов:
проволочные или ленточные зигзагообразные на изоляторах; проволочные или листовые, соединенные с водоохлаждаемыми токо-
подводами, входящими в горячую зону печи; проволочные или листовые, соединенные через неохлаждаемый вывод
из тугоплавкого металла с водоохлаждаемыми токоподводами.
Для спекания порошковых изделий применяют контейнеры с плавким затвором (рис. 1.4) из натроили боросиликатного стекла (полуфабриката при получении жидкого стекла). Во время нагрева контейнера воздух и выделяющиеся из засыпки и прессовок газы свободно выходят через пористые материалы (песок и порошок силикатной глыбы), которыми заполнена полость затвора.
Процессы порошковой металлургии. Курс лекций |
-30- |
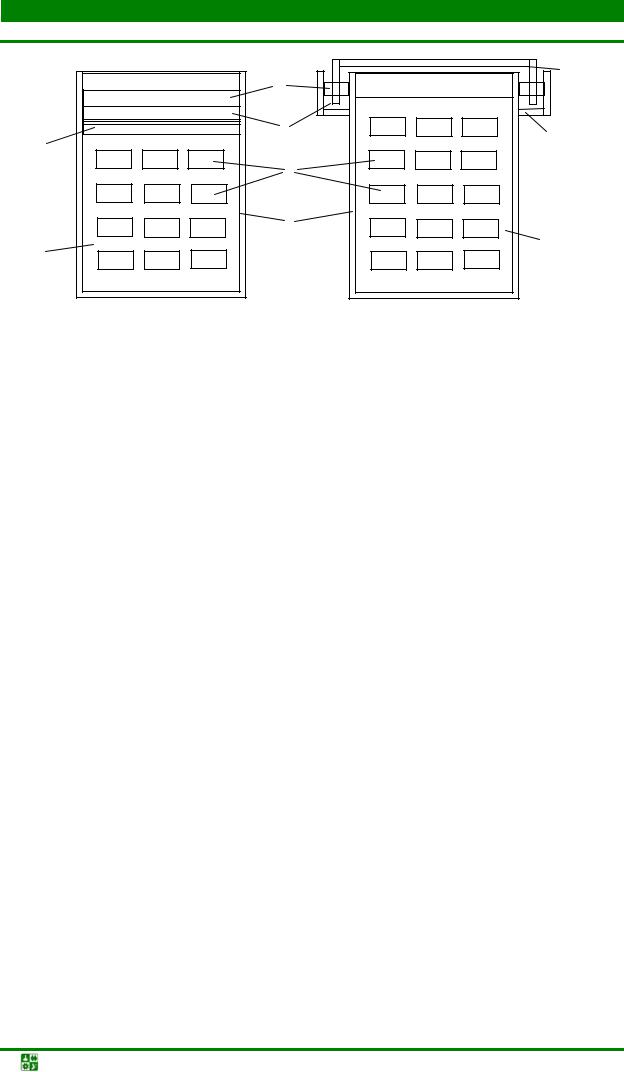
|
I. ПОЛУЧЕНИЕ ПОРОШКОВ |
|
|
Лекция 3 Восстановители и защитные среды |
|
|
1 |
6 |
|
|
|
7 |
5 |
4 |
|
||
|
3 |
|
|
2 |
8 |
8 |
|
|
|
|
|
а |
б |
|
Рис. 1.4. Конструкция контейнеров с плавким затвором: а – контейнер с верхним затвором без карманов; б – контейнер с верхним затвором карманного типа; 1 – гранулы материала плавкого затвора; 2 – контейнер; 3 – обрабатываемые детали; 4 – карман; 5 – песок; 6 – верхняя крышка контейнера; 7 – асбестовая прокладка; 8 – засыпка
При достижении температуры плавления материала плавкого затвора из натросиликатной глыбы контейнер из нержавеющей стали герметизируется от печной атмосферы, что обеспечивает предохранение спекаемых изделий от окисления.
Методыочисткииосушкизащитныхгазовыхсред
Очистку газовых сред осуществляют для удаления вредных примесей (диоксид углерода, сернистый водород и др.), осушку – с целью удаления остатков влаги.
Одновременную очистку от диоксида углерода и сернистого водорода
производят пропусканием защитной среды через 15 %-й водный раствор этаноламина с последующей регенерацией этого раствора.
При очистке газа от кислорода, СО2, HCN и других примесей с помощью этаноламина образуются неразлагающиеся соединения.
Этаноламины представляют собой бесцветные вязкие гигроскопические жидкости, смешиваемые с водой и низшими спиртами во всех концентрациях.
Химические реакции взаимодействия СО2 с моноэтаноламиномимеютвид
CO2 + 2RNH2 + H2O ↔ (RNH3)·2CO3 |
(1.7) |
CO2 + (RNH3)·2CO2 + H2O ↔ 2RNH3HCO3 |
(1.8) |
где R – группа ОН–СН2–СН2.
Процессы порошковой металлургии. Курс лекций |
-31- |
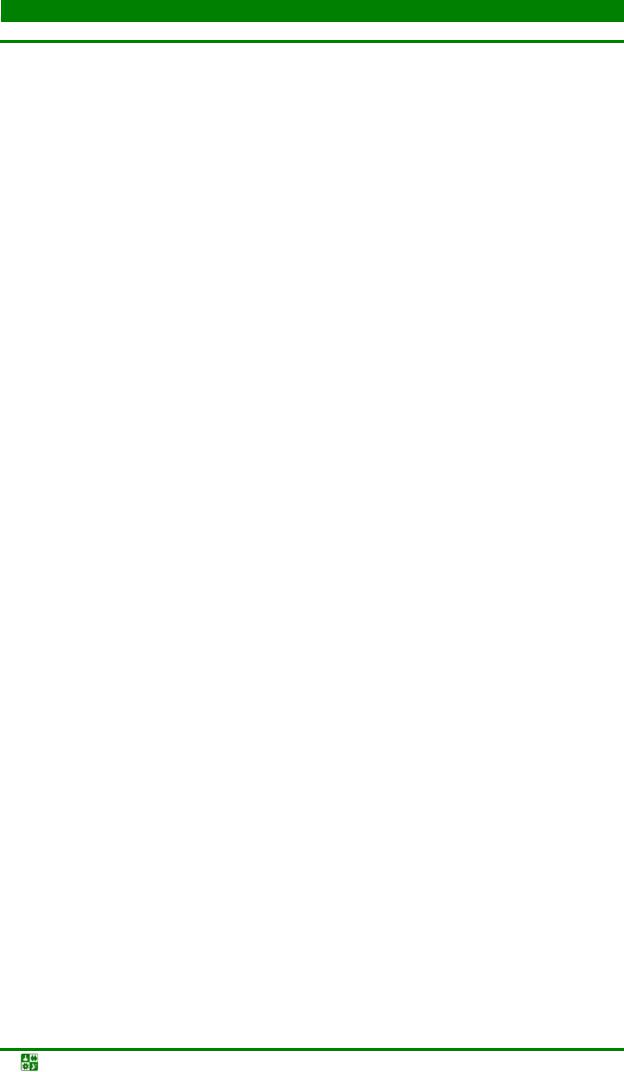
I. ПОЛУЧЕНИЕ ПОРОШКОВ
Лекция 3 Восстановители и защитные среды
Для более тонкой очистки защитных газовых сред (точка росы вплоть до –120 °С) используют химические, адсорбционные, диффузионные, ректификационные и каталитические методы.
К химическим методам относится очистка газов с помощью гидрата оксида железа (смесь болотной руды, 0,5 % гашеной извести с древесными опилками в соотношении 1:1, содержащая до 30–40 % Н2О), силикагеля или алюмогеля, геттеров.
Использование металлической меди позволяет очистить защитные газовые среды от кислорода при нагреве до 400–500 °С. Процесс активизируется при использовании губчатой меди или меди, нанесенной на диатомит. Оксид меди может применяться для очистки от водорода при температуре
350–400 °С.
Кальций интенсивно поглощает кислород при 450–500 °С, азот – при 650–750 °С; титан поглощает азот при 800–1 050 °С, водород – при 350–500 °С, воду – при 700–1 050 °С, кислород – при 700–1 050 °С.
Адсорбционные методы очистки основаны на способности твердых поверхностей сорбировать газы. К промышленным адсорбентам относятся активные угли, активный оксид алюминия, силикагели, кристаллические алюмосиликаты – цеолиты.
Ректификация основана на различии состава пара над жидкостью в равновесном состоянии и состава жидкой фазы.
Диффузионные методы очистки основаны на проницаемости металлических пористых перегородок для атомных газов и непроницаемости для молекулярных газов. Эффективна очистка водорода с использованием сорб- ции-десорбции на палладии.
Хорошим средством для очистки газов являются цеолиты, поглощающие СО2 и Н2О из продуктов сгорания. Применение цеолитов упрощает оборудование и исключает его коррозию, снижает капитальные и эксплуатационные затраты, повышает степень очистки от СО2. Наилучшие результаты получают при использовании цеолитов с размером пор 5 нм. Регенерация цеолитов состоит в их нагреве до 250–320 °С с последующей продувкой сухим газом и охлаждением или в сушке в вакууме 0,5–5 кПа.
При необходимости сохранения содержания углерода в спеченных изделиях постоянным целесообразно применять аргон или остроосушенный водород. В зависимости от углеродного потенциала конвертированного газа он может науглероживать или обезуглероживать спекаемые детали.
Контрольныевопросыизадания
1.Перечислите жидкие защитные среды.
2.Назовите жидкие восстановители.
3.Что входит в состав сыпучих защитных сред?
4.Какие печи применяются при получении порошков и спекании из-
делий?
5.Дайте характеристику печей спекания непрерывного действия.
6.Для чего (в основном) используютсяпечи периодического действия?
Процессы порошковой металлургии. Курс лекций |
-32- |
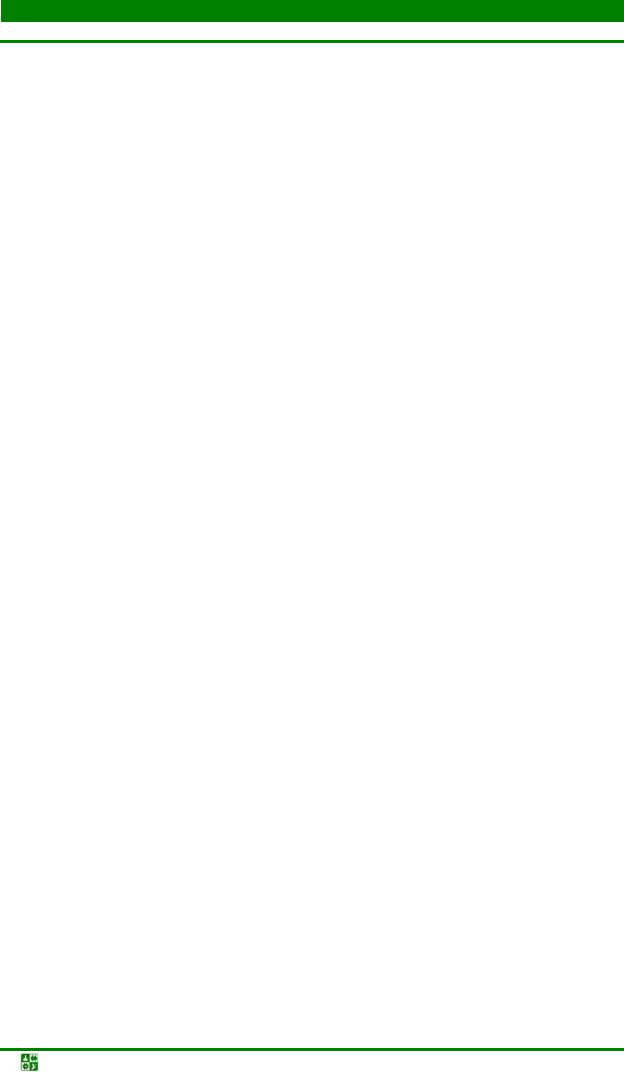
I. ПОЛУЧЕНИЕ ПОРОШКОВ
Лекция 3 Восстановители и защитные среды
7.Какие методы тонкой очистки газовых сред применяют на практике?
8.Что используют для одновременной очистки газовой среды от диоксида углерода и сернистого водорода?
9.Какие вещества применяют для осушки газовых сред?
Лекция4 Охранатрудаиокружающейсреды
впорошковойметаллургии
План лекции
1.Основные операции процессов порошковой металлургии и виды воздействия на персонал производств.
2.Пожаро- и взрывоопасность порошков. Мероприятия по охране труда и защите персонала.
Основныеоперациипроцессовпорошковойметаллургии ивидывоздействиянаперсоналпроизводств
Разработка защитных мероприятий по охране труда и окружающей среды на предприятиях порошковой металлургии связана со специфическими (для этой отрасли промышленности) факторами операций технологических процессов получения порошков и изделий на их основе. Основными операциями технологий порошковой металлургии являются:
размол исходных материалов и полученной губки в производстве порошков методом восстановления;
распыление расплавленных металлов в порошок; смешивание и рассев металлических и неметаллических порошков;
электролиз растворов при получении порошков методом электролиза и при нанесении гальванических покрытий;
формование изделий методами прессования, прокатки и др.; спекание изделий в газовых защитных средах; термическая и механическая обработка изделий (резанием, шлифова-
нием, калиброванием); пропитка пористых изделий смазками, расплавленными металлами и др.
При их выполнении возможно загрязнение воздуха различными веществами в пыле- и газообразном состояниях, часть из которых являются вредными для человека или пожаро- и взрывоопасными.
В технологические процессы порошковой металлургии вовлекаются такие вещества, как порошки железа, меди, графита, вольфрама, молибдена, олова, цинка, свинца, порошки различных соединений – карбидов, нитридов, боридов, сульфидов, ферросплавов, оксидов железа, кремния, цинка, алюминия, порошки сложных соединений – асбеста, муллита, слюд и др.
К газовым средам относятся водород, диссоциированный аммиак, конвертированный природный газ, эндо- и экзогазы и др. Применяются и хи-
Процессы порошковой металлургии. Курс лекций |
-33- |
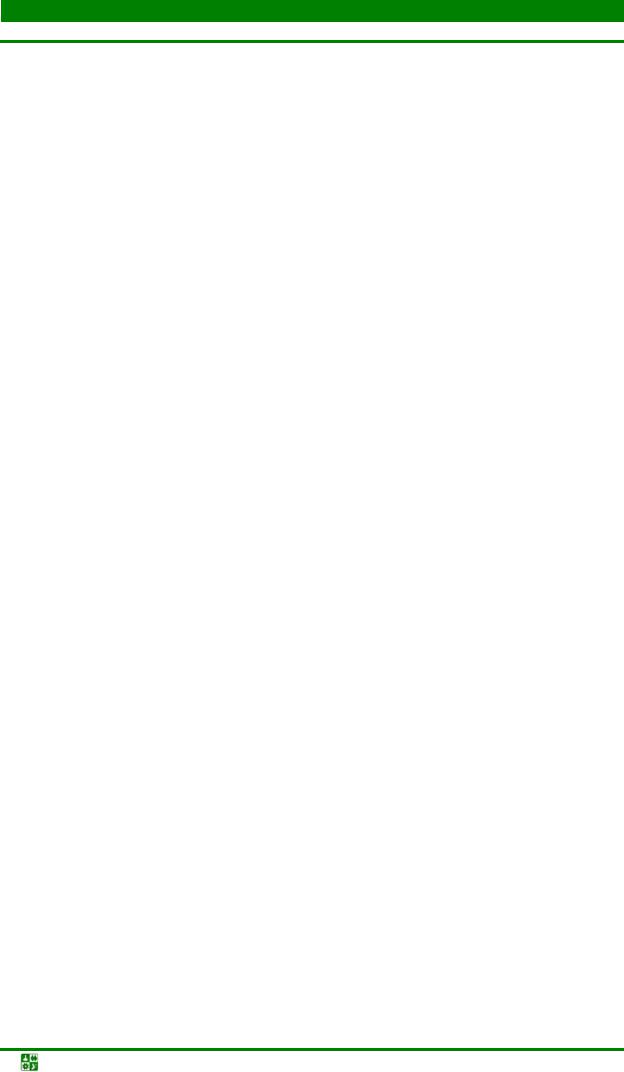
I. ПОЛУЧЕНИЕ ПОРОШКОВ
Лекция 4 Охрана труда и окружающей среды в порошковой металлургии
микаты – серная и соляная кислоты, цианистые соли, едкий натрий, а также спирт, бензин и др.
Выполнение технологических операций осуществляется с помощью прессов, прокатных станов, вибросит, печей, металлообрабатывающих станков и другого оборудования.
Для обеспечения безопасной работы в производствах порошковой металлургии применяются меры по охране труда и технике безопасности, существующие в металлургическом и химическом производстве, в гальванических и механических цехах, а также правила, специально разработанные для технологических процессов порошковой металлургии.
Последние предусматривают защиту работающих от токсического, теплового, взрывного, шумового и вибрационного воздействий.
Производство изделий методами порошковой металлургии по степени вредности и безопасности можно отнести к категории «В».
Для технологии порошковой металлургии характерно загрязнение атмосферы на рабочих местах пылеобразными металлами или различными соединениями. Загрязнения отмечаются при размоле, просеве и смешивании порошков, дозировании шихты, транспортировке порошковых материалов, прессовании, разгрузке и обработке спеченных изделий шлифованием. Пыль, загрязняющая атмосферу, имеет размер частиц менее 4 мкм. Содержание пыли на рабочих местах определяется соответствующей операцией производства порошков или изделий (табл. 1.3).
Систематическое вдыхание металлических и неметаллических порошков и газов может приводить к профессиональным заболеваниям.
Таблица 1.3
Содержание пыли на рабочих местах при изготовлении изделий методами порошковой металлургии, мг/м3
Операции |
Изделия на основе |
||
железа |
меди |
||
|
|||
Просев порошка железа |
10,2 |
|
|
Просев порошка графита |
15,8 |
|
|
Загрузка вибросита вручную и просев материа- |
|
|
|
ла (без укрытия) |
|
166,6 |
|
Просев бронзографитовой смеси в укрытии |
|
11,3 |
|
Прессование железографитовых изделий: |
|
|
|
на полуавтоматических прессах |
0,32 |
|
|
на гидравлических прессах |
2,7 |
|
|
Ручная дозировка железографитовой смеси |
19,5 |
|
|
Загрузка бункера полуавтоматического пресса |
|
58,9 |
|
Прессование изделий: |
|
|
|
на полуавтомате |
|
69,5 |
|
вручную |
|
86,3 |
|
Шлифовка изделий: |
|
|
|
влажная |
|
16,6 |
|
сухая |
|
584,6 |
Процессы порошковой металлургии. Курс лекций |
-34- |

I. ПОЛУЧЕНИЕ ПОРОШКОВ
Лекция 4 Охрана труда и окружающей среды в порошковой металлургии
Пыль медного порошка способствует заболеванию органов дыхания, сердечно-сосудистой системы, желудочно-кишечного тракта, может вызывать отравления с поражением органов дыхания, печени и др. Еще более вредное влияние на организм человека оказывает оксид меди, который кроме токсичного оказывает фиброгенное воздействие.
Особое внимание должно быть уделено вопросам охраны труда при производстве медного порошка методом электролиза. На основных операциях производства – электролизе, промывке, стабилизации, сушке, размоле, просеве, смешении и упаковке – часто допускается большое количество ручных трудоемких операций. Все операции обработки медного порошка сопровождаются значительным пылеобразованием.
Вредное воздействие медного порошка на организм человека является причиной повышенной заболеваемости рабочих гриппом, острым гастритом и бронхитом.
Порошки и пыль чистого железного порошка малотоксичны. Однако при систематическом их вдыхании они могут быть причиной пневмокониотических изменений и способствовать развитию хронических бронхитов. Соединения железа обладают значительной токсичностью.
Токсичны порошки свинца. Стабилизированный свинец находится в виде тонкодисперсного порошка и легко переходит в пыль при встряхивании и перемешивании.
Допустимая концентрация свинца по утвержденным в нашей стране нормам составляет 10 мг/м3 воздуха, что в пять раз ниже норм, принятых в некоторых зарубежных странах.
Свинец может быть причиной острых и хронических отравлений, сопровождающихся поражением многих систем и органов человека. При работе со свинцом должны быть разработаны четкие инструкции по упаковке, хранению и обработке порошка, снижающие содержание пыли свинца в воздухе. Необходимо также обеспечить систематический медицинский контроль и обслуживание работающих.
Аналогичным токсическим действием обладают порошки марганца и ферромарганца, которые при попадании в организм человека могут быть причиной острых и хронических заболеваний.
Пыль никеля и оксида обладает выраженным общетоксическим действием и может вызвать острые и хронические отравления с преимущественным поражением легких, в основе которого лежит резкое сосудистое расстройство. Возможно также появление аллергической сыпи. Допустимое содержание пыли этих веществ в воздухе составляет 0,5 мг/м3.
Из всех порошков, используемых в производстве твердых сплавов, наибольшей токсичностью обладает кобальт. Смеси пылевидных частиц вольфрама, титана и кобальта действуют аналогично кобальту, однако в присутствии вольфрама активность кобальта увеличивается.
Возгоны цинка, образующиеся при нанесении цинковых покрытий методом напыления и при термообработке изделий с цинковыми покрытиями, вызывают в человеческом организме лихорадочное состояние.
Процессы порошковой металлургии. Курс лекций |
-35- |
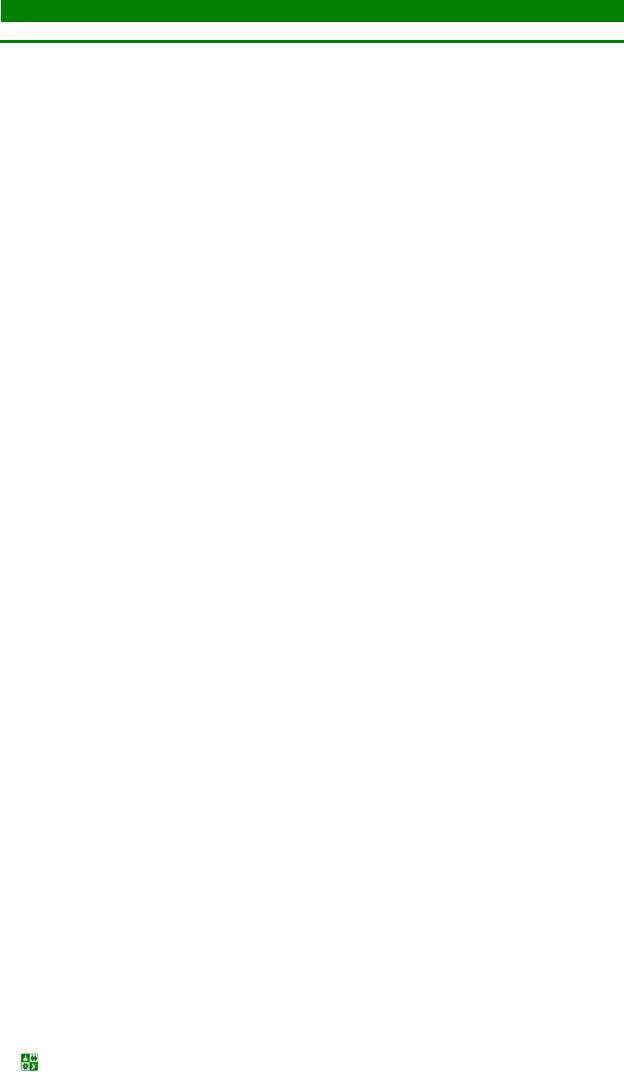
I. ПОЛУЧЕНИЕ ПОРОШКОВ
Лекция 4 Охрана труда и окружающей среды в порошковой металлургии
Порошки хрома могут быть причиной аллергической сыпи и появления язв на коже и в носовой полости. Фиброз легких может быть следствием длительного контакта с порошками алюминия.
Титан и его диоксид имеют слабо выраженную токсичность. Гидрид титана проявляет умеренно выраженное пневмокониотическое и общетоксическое действие, превышающее таковое титана и его оксида. Рекомендуемая
предельно допустимая концентрация (ПДК) гидрида титана составляет 6 мг/м3.
В производстве тарированного вольфрама используется азотнокислый торий или диоксид тория, которые являются источником радиоактивного излучения. Радиационный фактор меньше в том случае, когда используется азотнокислый торий, а не диоксид тория.
Пыль диоксида кремния, особенно с дисперсностью менее 5 мкм, способствует заболеванию силикозом, пыль асбеста приводит к легочным заболеваниям, пыль олова и оксида олова способствует заболеванию туберкулезом.
Вредное действие на организм человека оказывает также пыль порошка нитрида бора (слабо выраженное фиброгенное действие), карбидов кремния и бора (поражение органов дыхания, слизистой оболочки, органов обоняния).
Рабочие, занятые в производстве ферритов, подвергаются воздействию неблагоприятных факторов (пыли, шума, инфракрасного излучения, токсичных газов). Наиболее отрицательно сказывается пыль ферритов.
Ее воздействие на организм характеризуется слабовыраженным фиброгенным и общетоксическим действием. У работающих в производстве ферритов без достаточных защитных мер отмечается повышенный уровень заболеваемости органов дыхания.
Установлены предельно допустимые концентрации для различных веществ (табл. 1.4).
Таблица 1.4
Значения предельно допустимых концентраций для различных веществ
Вещество |
ПДК, |
Вещество |
|
ПДК, |
|
мг/м3 |
|
мг/м3 |
|
||
Медь |
0,5 |
Аммиак |
|
0,02 |
|
Оксид меди |
0,1 |
Бензин |
|
0,3 |
|
Медь с добавками графитадо 30 %, |
|
Оксид углерода |
|
0,02 |
|
олова до 10 %, никеля до 30 % |
0,5 |
Серная кислота |
|
0,001 |
|
Марганец (в пересчете на МnО4) |
0,3 |
Спирт этиловый |
|
1,0 |
|
Железо восстановленное с со- |
|
Цианистый водород и соли си- |
|
|
|
держанием до 3 % графита |
6,0 |
нильной кислоты (в пересчете на |
|
|
|
Оксид железа |
6,0 |
НСN) |
|
0,0003 |
|
Свинец |
0,01 |
Аммиак |
|
0,02 |
|
Оксид алюминия |
2,0 |
Бензол |
|
0,05 |
|
Карбид бора |
2,0 |
Оксид азота (в пересчете |
на |
|
|
Карбид кремния |
5,0 |
N2O5) |
|
0,05 |
|
Нитрид бора |
6,0 |
Сернистый газ |
|
0,02–0,04 |
|
Дисульфид молибдена |
10,0 |
Сероводород |
|
0,01 |
|
|
|
|
|
|
|
Процессы порошковой металлургии. Курс лекций |
-36- |
|
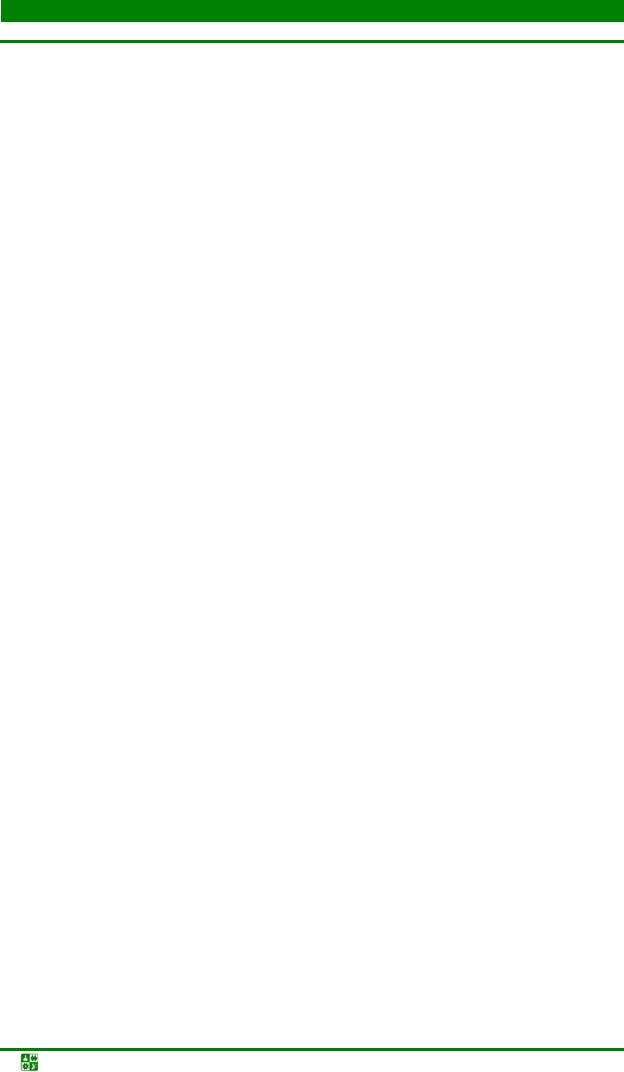
I. ПОЛУЧЕНИЕ ПОРОШКОВ
Лекция 4 Охрана труда и окружающей среды в порошковой металлургии
Степень опасности порошков и промышленных пылей для здоровья человека определяется многими факторами: химическим составом, размером частиц, концентрацией, длительностью воздействия, путями проникновения в организм человека.
Пожароивзрывоопасностьпорошков. Мероприятияпоохранетрудаизащитеперсонала
Пожаро- и взрывоопасность процессов порошковой металлургии обусловлена применением тонкодисперсных порошков, а также легковоспламеняющихся и хорошо горящих основных и вспомогательных материалов (водород, диссоциированный аммиак, конвертированный природный газ).
Пирофорность порошков (способность при определенных условиях воспламеняться под действием внутренних экзотермических процессов) и их взрываемость зависят от природы порошка, его дисперсности, формы частиц и др.
Взрывная активность смеси порошков повышается при возрастании содержания наиболее активной примеси, снижении степени окисленности, уменьшении размера частиц, повышении их удельной поверхности. Большинство порошков взрывоопасны при размере частиц меньше 200 мкм и концентрации от десяти до десятков тысяч граммов на кубический метр.
Наибольшее давление взрыва наблюдается при концентрации 500–2 000 г/м3 и размере частиц менее 50 мкм.
Пирофорность порошков зависит от их дисперсности и химического состава (табл. 1.5).
Таблица 1.5
Показатели пирофорности и взрываемости металлических порошков
|
Диаметр |
Порошок в слое |
Взвешенная в воздухе пыль |
|||
|
|
|
|
|
||
Материал |
частиц |
Температура |
Температура |
Температура |
Нижняя концентра- |
|
|
Dч, мкм |
самовозго- |
воспламене- |
воспламене- |
ция пылевой взвеси |
|
|
|
рания Тсв, °С |
ния Тв,°С |
ния Тв,°С |
(НКПВ), г/м3 |
|
Железо восста- |
< 50 |
475 |
350 |
300 |
66 |
|
новленное |
||||||
|
|
|
|
|
||
Кремний |
< 74 |
790 |
… |
770 |
100 |
|
Ферромарганец |
< 74 |
240 |
… |
450 |
130 |
|
Медь |
< 44 |
… |
…. |
700 |
…. |
Взрывным процессам присущи высокие скорости распространения. Над слоем осевших порошковых активных металлов возможно распространение взрывной волны со сверхзвуковыми скоростями. Воспламенение пыли, состоящей из различных взрывоопасных материалов, включая металлы, может привести к взрыву.
Процессы порошковой металлургии. Курс лекций |
-37- |
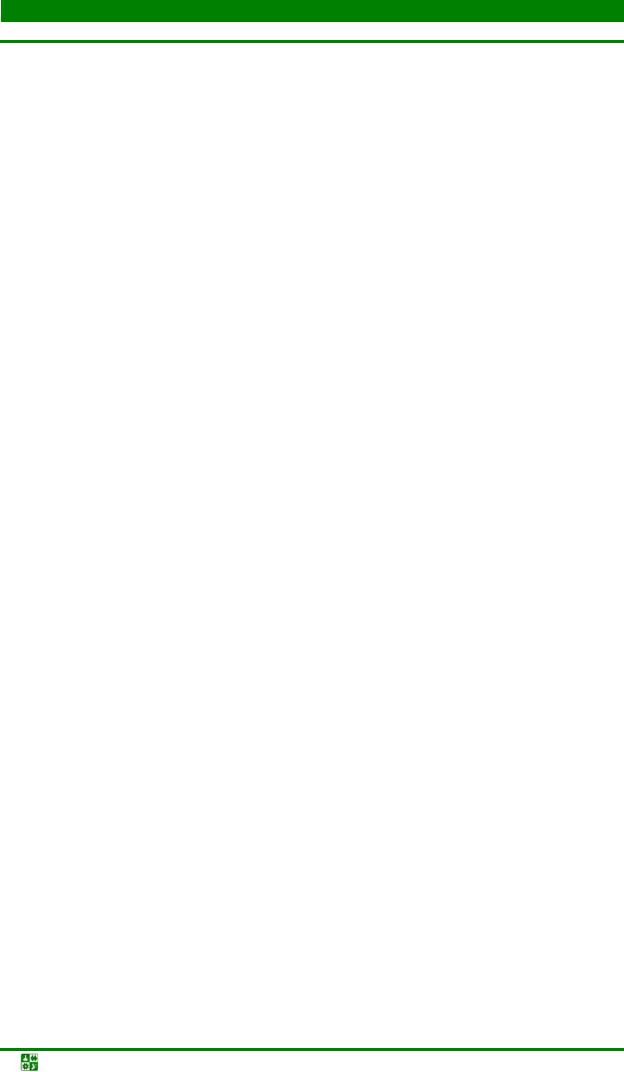
I. ПОЛУЧЕНИЕ ПОРОШКОВ
Лекция 4 Охрана труда и окружающей среды в порошковой металлургии
Взрыв происходит при строго определенной концентрации огнеопасных материалов, находящихся во взвешенном состоянии в воздухе. Для предотвращения пирофорности и взрываемости порошков применяют ихпассивацию.
Наличие специфических факторов опасного воздействия на организм человека требует проведения в производстве мероприятий санитарнотехнического и технологического порядка, предупреждающих выделение пыли, газов и испарений и доведение их концентрации до допустимых норм.
К этим мероприятиям относятся: использование менее токсичных материалов, герметичной аппаратуры, эффективных пылеуловителей, замена сухих способов производства мокрыми, применение средств индивидуальной защиты работающих (масок, респираторов, перчаток, одежды).
Наиболее радикальным решением проблемы обеспечения безопасности труда является автоматизация операций, представляющих опасность для здоровья рабочего.
Контрольныевопросыизадания
1.Назовите основные операции процессов порошковой металлургии.
2.К какой категории по степени вредности и безопасности относятся производства порошковой металлургии?
3.Перечислите факторы вредного воздействия на организм персонала производств порошковой металлургии.
4.Назовите наиболее опасные факторы воздействия.
5.Какие размеры имеют частицы порошка, находящиеся в пылевой
массе?
6.При выполнении каких операций наблюдается большое содержание пылевой фракции на рабочих местах?
7.Что такое пирофорность порошков?
8.От чего зависит пирофорность порошков?
9.При каких условиях порошок может взорваться?
10.Что является радикальным решением проблем обеспечения безопасности труда?
Лекция5 Механическиеметодыполученияпорошков
План лекции
1.Теоретические основы процессов разрушения твердых материалов.
2.Предварительное измельчение крупных сырьевых материалов в щековых, валковых, конусных дробилках и молотковых мельницах.
3.Получение порошков резанием металлических заготовок.
Процессы порошковой металлургии. Курс лекций |
-38- |
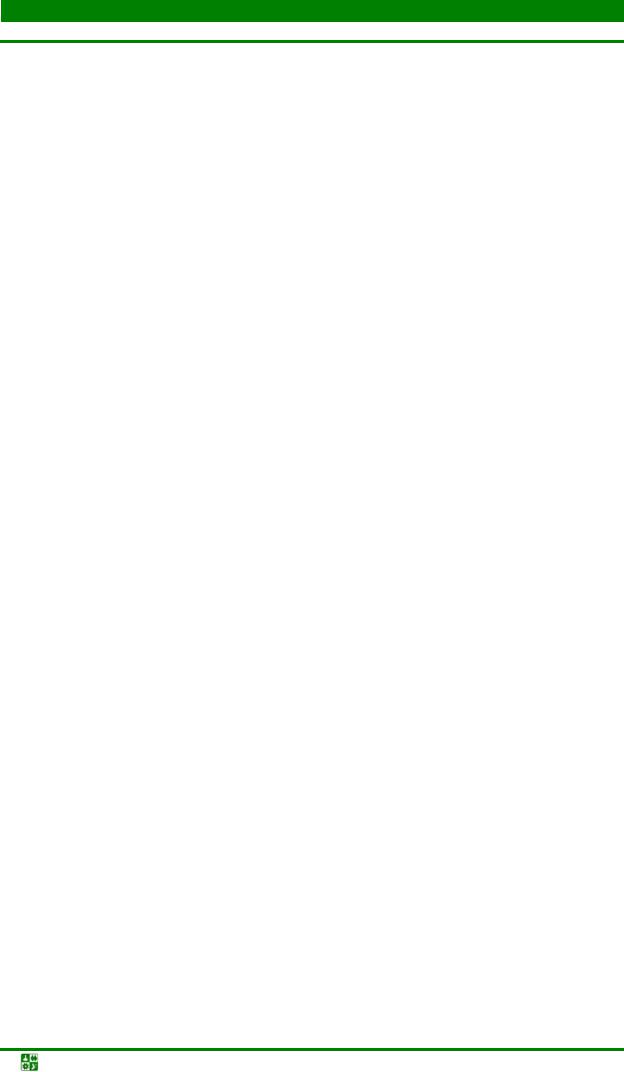
I. ПОЛУЧЕНИЕ ПОРОШКОВ
Лекция 5 Механические методы получения порошков
Теоретическиеосновыпроцессовразрушения твердыхматериалов
Метод механического измельчения твердых компактных материалов широко применяется в порошковой металлургии. Этим способом можно превратить в порошок практически любой из металлов, их окислов и тугоплавких неметаллических соединений (боридов, нитридов, карбидов и пр.).
Под измельчением понимают уменьшение начального размера частиц материала путем разрушения их действием внешних усилий. Измельчение дроблением, размолом или истиранием является старейшим методом перевода твердых веществ в порошкообразное состояние.
Наиболее целесообразно применять механическое измельчение при производстве порошков хрупких металлов, сплавов и неметаллических соединений (кремний, бериллий, хром, марганец, ферросплавы, оксиды, бориды, карбиды и др.). Размол таких металлов, как медь, алюминий, серебро, золото, затруднен, что объясняется их высокой пластичностью.
В процессе измельчения на материал действуют различные разрушающие усилия – раздавливающие (расплющивающие), ударные, истирающие. При механическом измельчении твердых материалов затрачиваемая энергия расходуется на деформацию (упругую и пластическую) и на увеличение поверхности измельчаемого материала, которое свидетельствует об уменьшении размеров частиц, что и является основной целью процесса.
Процесс деформации твердых тел заключается в том, что под действием внешней статической нагрузки в твердом теле начинается движение дислокаций. Движущиеся дислокации образуют дислокационные «стенки», столкновение которых приводит к появлению зародышей трещин. Образованию трещин способствуют и многочисленные дефекты на поверхности частиц твердого тела («нарушенный слой»), а также на его межзерновых границах. Действие динамических ударных нагрузок приводит к быстрому увеличению этих микротрещин. Однако при «снятии» внешней нагрузки трещины под действием сил межатомарного взаимодействия могут смыкаться («самозаживляться», релаксировать).
Разрушение твердого тела (его отдельной частицы) происходит только в том случае, когда внешние воздействия настолько велики, что трещины непрерывно «развиваются», распространяясь по всему сечению тела в одном или нескольких направлениях. В момент разрушения напряжения в деформирующемся теле превышают некоторое предельное значение («предел прочности материала»), упругая деформация сменяется деформацией разрушения и происходит уменьшение размеров (измельчение) исходных агрегатов.
Согласно теории дробления, предложенной П.А. Ребиндером, работа, затрачиваемая на измельчение, в общем случае представляет собой сумму энергии, расходуемой на образование новых поверхностей раздела при разрушении твердого тела, и энергии затраченной на деформацию.
Процессы порошковой металлургии. Курс лекций |
-39- |
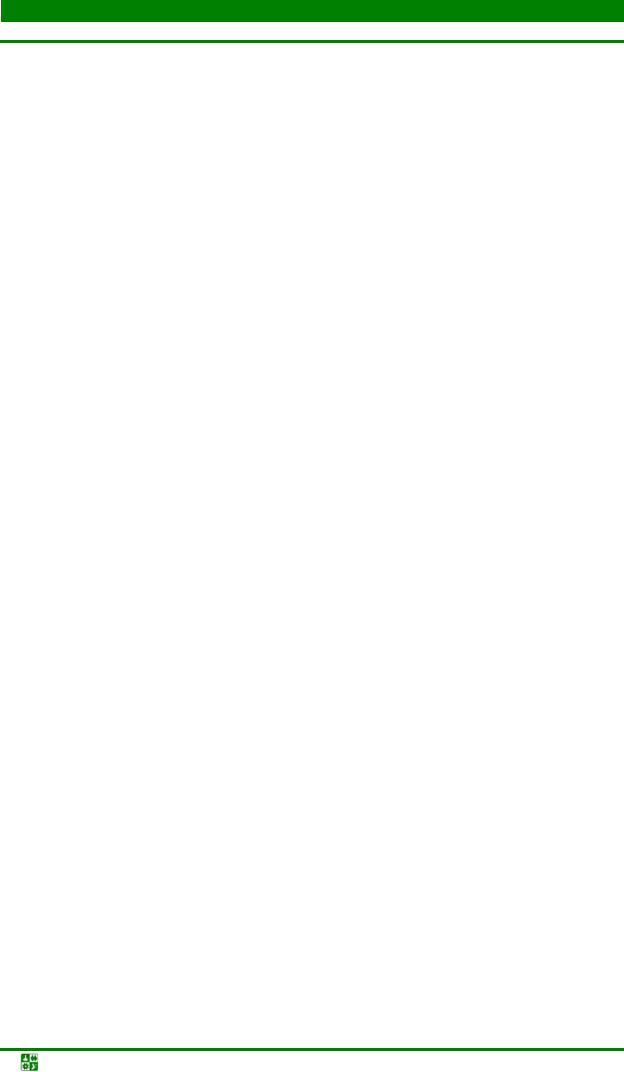
I. ПОЛУЧЕНИЕ ПОРОШКОВ
Лекция 5 Механические методы получения порошков
При крупном дроблении вновь образующаяся поверхность невелика, так как получаемые частицы имеют сравнительно большие размеры. В связи с этим эн ергия, затрачиваемая на образование новой поверхности, намного меньше энергии деформации, а расход энергии на дробление приблизительно пропорционален объему разрушаемого тела.
При тонком измельчении вновь образующаяся поверхность очень велика. Поэтому расход энергии на измельчение приблизительно пропорционален вновь образующейся поверхности. Однако сама работа диспергирования всегда незначительна, так как почти вся энергия измельчающего устройства затрачивается на деформацию разрушаемого тела и на образование теплоты. Коэффициент полезного действия любого такого устройства очень низок.
Поведение материала при измельчении является следствием двух соперничающих процессов – разрушения (дезинтеграции) и агрегатирования (интеграции) частиц. Проявление второго процесса связано с явлениями адгезии, физико-химических и физико-механических реакций, протекающих в процессе измельчения. Действие этих сил (помимо «заживления» трещин) приводит к агрегатированию и комкованию порошка. Поэтому в подавляющем большинстве случаев предельный размер частиц, которые удается получить при механическом измельчении материала, не превышает 0,1 мкм.
Среди методов измельчения твердых материалов наибольшее распространение получили обработка металлов резанием, измельчение металла в шаровых, вихревых, молотковых и других мельницах, ультразвуковое диспергирование.
Предварительноеизмельчениекрупныхсырьевыхматериалов вщековых, валковых, конусныхдробилках
имолотковыхмельницах
Щековые, валковые и конусные дробилки применяются для предварительного измельчения крупных (до нескольких сантиметров) кусковых материалов с пределом прочности до 300–400 МПа. В дальнейшем предварительно измельченные в этих агрегатах материалы поступают на доизмельчение другими методами.
Щековые дробилки применяют для измельчения спекшейся губки, осадков с электродов, крупных кусков рудных концентратов и т.п. Размол материала в щековых дробилках до размера частиц 1–4 мм происходит за счет раздавливания кусков между неподвижной и подвижной (качающейся с нижней или верхней осью подвеса) щеками установки. Рабочее пространство между щеками называют «пастью» дробилки.
Измельчение материала до крупности частиц 0,5–1 мм обеспечивают валковые дробилки, один или оба валка которых могут совершать возвратнопоступательное движение по направляющим вдоль оси опорной рамы. Валки вращаются навстречу друг другу от отдельных приводов с окружной скоростью 2–4 м/с, причем разность их скоростей обычно не превышает 2 %;при дробле-
Процессы порошковой металлургии. Курс лекций |
-40- |
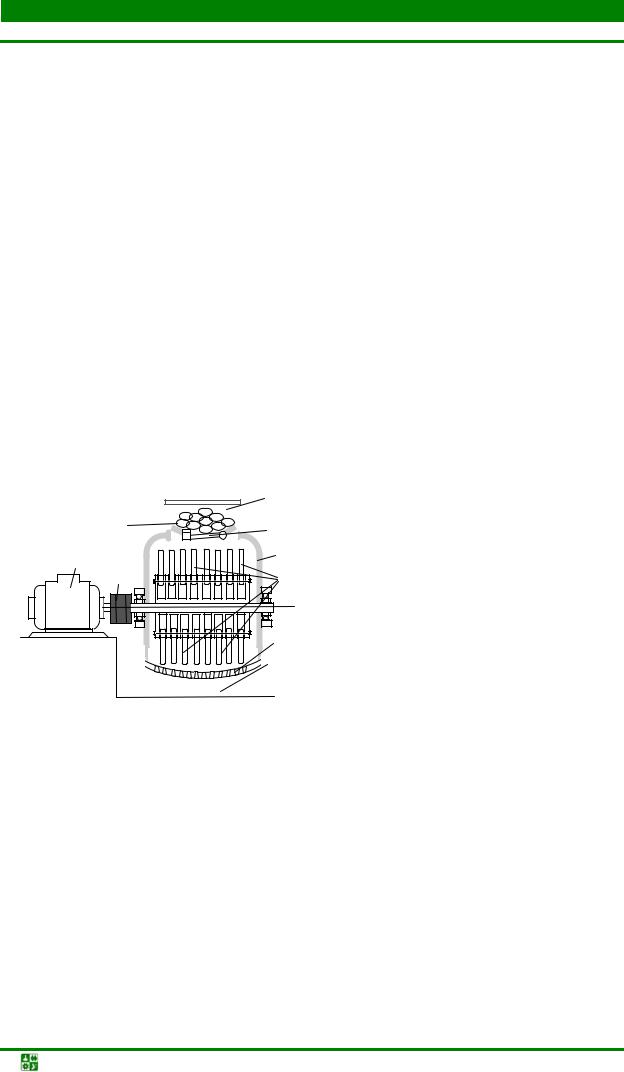
I. ПОЛУЧЕНИЕ ПОРОШКОВ
Лекция 5 Механические методы получения порошков
нии вязких материалов разность этих скоростей может доходить до 20 %. Эффективность работы валковых дробилок в большой степени зависит от условий подачи материала, особенно от непрерывности его поступления в щель между валками и равномерности распределения по их длине. Валки могут быть гладкими, рифлеными или зубчатыми.
В конусных дробилках измельчение материала осуществляется в кольцевой полости между рабочей частью поверхности конуса и соответствующей частью внутренней поверхности корпуса дробилки (в камере дробления). Конусные дробилки обеспечивают измельчение материала до крупности частиц 1–2 мм.
Молотковые дробилки в основном используются для измельчения губчатых материалов (спекшихся при восстановлении порошков, катодных осадков и пр.). Измельчение обрабатываемого материала в них осуществляется за счет удара молотков (бил), укрепленных шарнирно на валу, вращающемся в рабочей камере с достаточно высокой скоростью (около 1 500 об/мин).
Исходный кусковой материал загружают в приемный бункер установки (рис. 1.5), откуда он поступает в рабочую камеру мельницы, в нижней части которой имеется отверстие, закрытое сеткой; после размола частицы проваливаются через ситовое полотно в сборник порошка.
|
4 |
|
3 |
5 |
|
|
|
|
1 |
6 |
|
|
|
|
2 |
7 |
|
|
|
Рис. 1.5. Молотковая мельница: 1– электродви- |
|
8 |
гатель; 2 – муфта; 3 – губка; 4 – загрузочный |
|
9 |
бункер; 5 – загрузочный люк с защелкой; 6 – |
|
|
корпус мельницы; 7 – била; 8 – металлическая |
|
|
решетка с ситовым полотном; 9 – порошок |
Размол губки в молотковой мельнице происходит в течение нескольких минут, и получаемый порошок мало наклепывается, что исключает необходимость его последующего отжига.
Более тонкое измельчение обеспечивают бесколосниковые молотковые мельницы, рабочим органом которых является ротор с шарнирно закрепленными на нем тонкими пластинчатыми молотками.
Получениепорошковрезаниемметаллическихзаготовок
Специальное получение стружки или опилок для дальнейшего изготовления из них изделий экономически не очень выгодно и поэтому на практике используется крайне редко. Однако образующиеся при обработке ме-
Процессы порошковой металлургии. Курс лекций |
-41- |
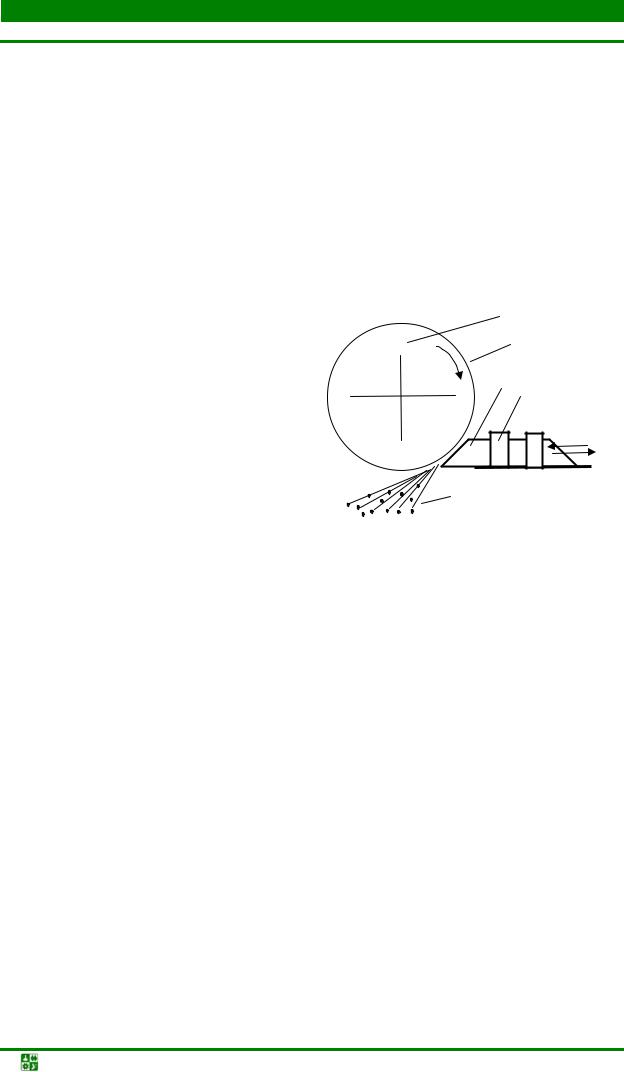
I. ПОЛУЧЕНИЕ ПОРОШКОВ
Лекция 5 Механические методы получения порошков
таллов резанием отходы в виде мелкой стружки и опилок целесообразно использовать для последующего измельчения в мельницах различных типов.
Мелкую стружку железа, стали и чугуна размером около одного миллиметра (стружка сверления, фрезерования и др.) можно использовать для изготовления изделий без ее дополнительного измельчения.
Чаще всего метод резания применяется при получении порошков металлов, которые весьма активны по отношению к кислороду, особенно в состоянии высокой дисперсности (например, магниевый порошок).
Для получения порошка магния используется так называемая кратцмашина (рис. 1.6), которая представляет собой металлический вращающийся барабан с укрепленной на его поверхности царапающей лентой.
1
2
3 4
Рис. 1.6. Схема установки для получения |
|
порошка магния с использованием кратц- |
|
машины: 1 – барабан ратцмашины; 2 – ца- |
|
рапающая лента; 3 – слиток металла; 4 – |
5 |
держатель слитка металла; 5– металличе- |
|
ский порошок |
|
Пластину магния подают в установку через специальное отверстие и прижимают к царапающей ленте. Равномерность истирания достигается применением непрерывного возвратно-поступательного движения пластины.
Крупность порошка можно регулировать диаметром щетки, числом и величиной зубьев, а также скоростью подачи магниевой пластины.
Минимальный размер частиц получаемого с помощью кратцмашины магниевого порошка составляет около 200 мкм. Если требуется более мелкий порошок, то полученные на кратцмашине частицы измельчают в шаровых мельницах в среде углекислого газа.
Кроме того, порошок магния можно получить обработкой его литых заготовок на фрезерных станках при комбинированном снятии мелкой стружки сразу двумя работающими фрезами – вертикальной и горизонтальной. Фрезерование ведут при больших скоростях перемещения фрезы (до 30–40 м/с), получая порошок с частицами размером до 100 мкм в довольно широких размерных пределах в зависимости от режима работы станка. Отфрезерованный порошок отсасывается в циклон и через шлюзовый затвор поступает на вибрационный грохот для разделения частиц по размерам (рассева на фракции). Мелкие частицы порошка, не осевшие в циклоне, проходят через сепаратор и улавливаются самоочищающимися фильтрами.
Процессы порошковой металлургии. Курс лекций |
-42- |
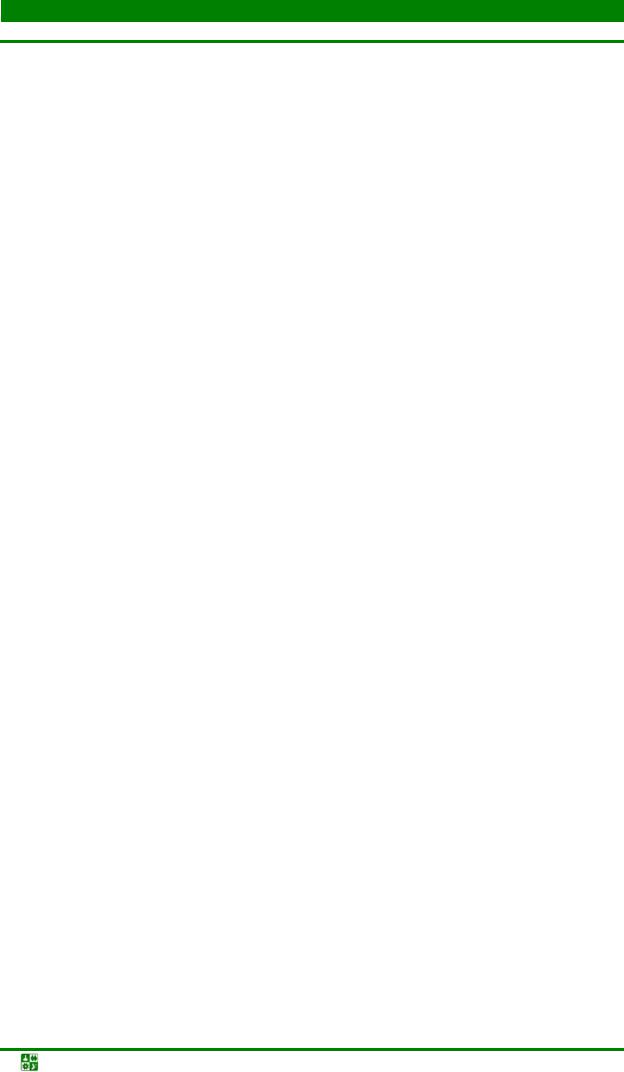
I. ПОЛУЧЕНИЕ ПОРОШКОВ
Лекция 5 Механические методы получения порошков
Контрольныевопросыизадания
1.Какие усилия действуют в процессе разрушения материалов?
2.С какими основными изменениями структурного состояния связана деформация твердых тел?
3.Чему равна работа, затрачиваемая на измельчение твердых порошкообразных материалов?
4.Рассмотрите принцип устройства валковых, щековых и молотковых дробилок.
5.В каких случаях для получения порошков применяется метод ре-
зания?
6.Каковы предельные размеры частиц, получаемых при использовании кратцмашины?
Лекция6 Измельчениематериаловвшаровыхмельницах
План лекции
1.Устройство и основные элементы шаровых мельниц. Классификация мельниц.
2.Понятие критической скорости вращения барабана мельницы.
3.Факторы, определяющие степень измельчения.
4.Режимы измельчения материалов.
5.Управление процессом измельчения.
Устройствоиосновныеэлементышаровыхмельниц. Классификациямельниц
Простейший аппарат для измельчения дробленых твердых материалов– шаровая вращающаяся мельница, которая представляет собой металлический цилиндрический барабан.
Внутри барабана находятся размольные тела полиэдрической или округлой формы (чаще всего стальные или твердосплавные шары). Применение при размоле тел цилиндрической формы предпочтительно в связи с большей площадью контактной поверхности. При вращении мельницы размольные тела (под действием сил трения о стенки барабана мельницы) поднимаются на определенную высоту в направлении вращения до тех пор, пока угол подъема не превысит угол естественного откоса, после чего они скатываются или падают вниз, измельчая материал, находящийся в пустотах между ними.
Процессы порошковой металлургии. Курс лекций |
-43- |
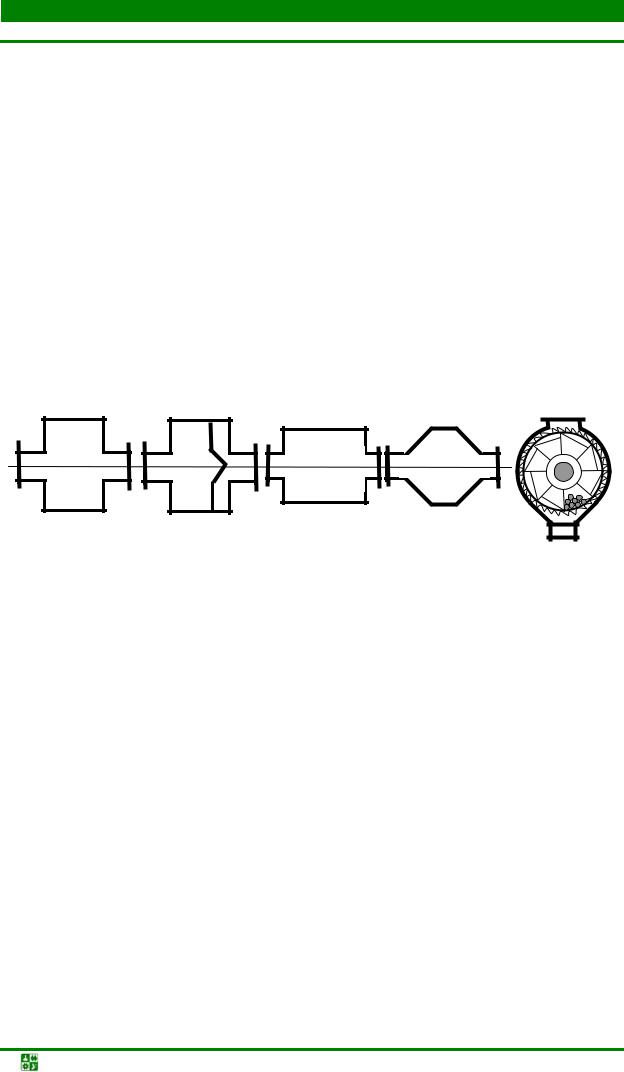
I. ПОЛУЧЕНИЕ ПОРОШКОВ
Лекция 6 Измельчение материалов в шаровых мельницах
Соотношение между дробящим и истирающим действием размольных тел в мельнице в значительной мере определяется отношением диаметра барабана D к его длине L. Известно, что в мельницах одинакового объема при L:D > 3 преобладает дробящее действие размольных тел, что полезно для из-
мельчения твердых и хрупких материалов, а при L:D ≤ 3 – истирающее, более эффективное при измельчении пластичных металлов.
В практике порошковой металлургии в большинстве случаев используют шаровые мельницы с периодической загрузкой и разгрузкой, вращение которых осуществляют либо непосредственно от электродвигателя, либо путем установки барабанов на валки.
Известны также мельницы с центральной разгрузкой измельченного материала через полую цапфу, с торцевой разгрузкой через диафрагму – поперечную решетку, установленную у разгрузочного конца барабана, или с периферической разгрузкой через щели в барабане и окружающее его цилиндрическое сито (рис. 1.7).
а |
б |
в |
г |
д |
Рис. 1.7. Схемы шаровых вращающихся мельниц: а, в – с центральной загрузкой барабана через цапфу; б – с торцевой загрузкой (цилиндро-коническая); г – с периферической загрузкой и выгрузкой материала через сита; д – разрез шаровой мельницы постоянного действия
Шаровые мельницы, для которых D:L = 0,5–1, часто работают по замкнутому циклу совместно с классификатором, отделяющим недоизмельченный продукт после выхода из мельницы и возвращающим его на повторное измельчение.
Производительность мельницы при этом повышается, а расход электроэнергии на измельчение уменьшается.
Решающее влияние на интенсивность и механизм размола оказывают: скорость вращения барабана мельницы, число и размер размольных тел, масса измельчаемого материала, среда размола.
Понятиекритическойскоростивращениябарабанамельницы
С увеличением скорости вращения мельницы в связи с ростом центробежной силы и угла подъема размольные тела падают вниз с большей высоты, производя главным образом дробящее действие. При дальнейшем увеличении скорости вращения мельницы центробежная сила может настолько
Процессы порошковой металлургии. Курс лекций |
-44- |
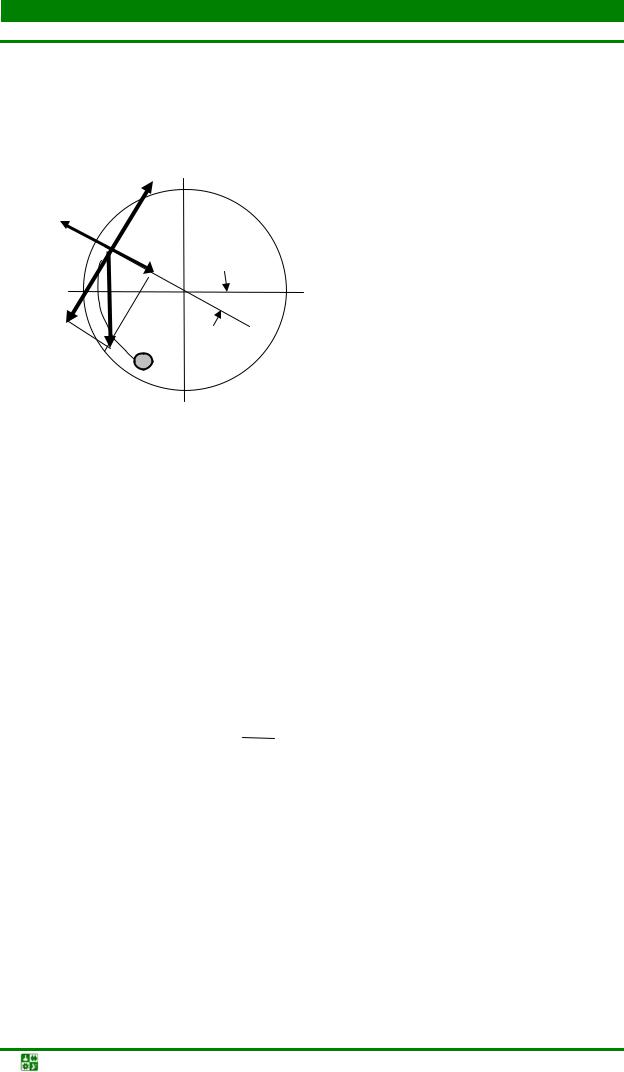
I. ПОЛУЧЕНИЕ ПОРОШКОВ
Лекция 6 Измельчение материалов в шаровых мельницах
возрасти, что размольные тела будут вращаться вместе с барабаном и материал практически не будет измельчаться. Скорость, при которой наблюдается подобный режим работы мельницы, называют критической скоростью вра-
щения nкр.
mv2/R
m Psinα
Pcosα
P α
Рис. 1.8. Схема к расчету критической скорости вращения барабана шаровой мельницы
Для вывода критической скорости вращения рассмотрим поведение единичного размольного тела, например шара (рис. 1.8), находящегося в барабане работающей мельницы.
Одиночный шар весом Р на поверхности барабана мельницы, вращающегося со скоростью V, м/с, в точке т будет находиться под действием центробежной силы, равной РV2/gR, где g – ускорение силы тяжести, м/с2; R – внутренний радиус барабана мельницы, м.
При угле подъема α сила собственного веса шара может быть разложена на силы, одна из которых направлена по радиусу и равна Рsin α, а другая – по касательной и равна Рсos α. При этом число оборотов барабана
мельницы nкр, об/мин, а V = πDnкр/60, поэтому π2D2n2кр / 602 = gD/2, где D – внутренний диаметр барабана мельницы, м. Отсюда находим
|
|
|
|
|
nкр = √g/2π2 (60/√D) = 42,4/√D. |
(1.9) |
Не принимая во внимание трение, можно установить, что одиночный шар будет удерживаться на стенке барабана до тех пор, пока (РV2)/gR ≥ Рsin α, или (V2/gR) ≥ sin α. В связи с этим рассчитанное по формуле (1.9) nкр надо понимать как условную величину, в долях которой удобно выражать число оборотов барабана мельницы, характеризующее принятый режим размола. Если скорость вращения V такова, что в момент прохождения шара через зе-
нит, при котором α = 90°, шар остается на стенке барабана, то sin 90° = V2/gR = 1, или V2 = gR.
Фактически при nкр шар еще не сможет в зените удержаться на стенке барабана мельницы вследствие скольжения по ее поверхности. При скорости
Процессы порошковой металлургии. Курс лекций |
-45- |
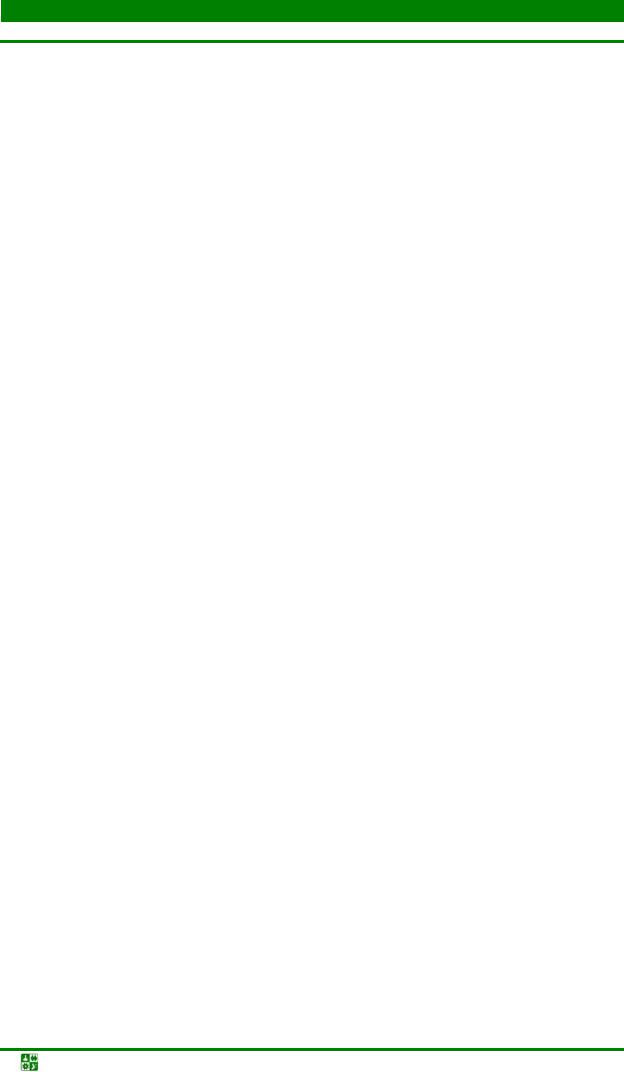
I. ПОЛУЧЕНИЕ ПОРОШКОВ
Лекция 6 Измельчение материалов в шаровых мельницах
вращения, равной nкр, происходит проскальзывание одного ряда шаров относительно другого.
Факторы, определяющиестепеньизмельчения
На процесс измельчения большое влияние оказывают масса (коэффициент заполнения барабана) размольных тел и отношение массы (объема) размольных тел к массе (объему) измельчаемого материала. Оптимальный коэффициент заполнения ϕ барабана мельницы размольными телами составляет 0,4–0,5. При больших значениях ϕ уменьшается объем пространства в мельнице, необходимый для свободного падения или перекатывания размольных тел. Уменьшение длины свободного падения размольных тел приводит к потере кинетической энергии, с которой они действуют на измельчаемый материал. При меньшем коэффициенте заполнения снижается производительность мельницы, что связано как с уменьшением объемов загружаемого материала (его должно быть столько, чтобы он не превышал объема пустот между размольными телами), так и переходом мельницы в другой режим работы (менее интенсивный). Из-за уменьшения площади трения сегмента из размольных тел о внутреннюю поверхность барабана размольные тела поднимаются на меньшую высоту, а следовательно, снижается эффект от их действия на измельчаемый материал.
Если материала будет больше объема пустот между размольными телами, то часть его, не вмещающаяся в зазоры, измельчается менее интенсивно. Кроме того, размольные тела будут падать как бы на «подушку» из лишнего материала, что также снижает эффект от их действия.
Для интенсификации процесса размола его проводят в жидкой среде, которая препятствует распылению материала в свободном объеме барабана мельницы и обратному слипанию тонких частиц благодаря диэлектрическим свойствам. Кроме того, проникая в микротрещины частиц, жидкость создает большое капиллярное давление, способствуя измельчению. Жидкость также уменьшает трение как между размольными телами, так и между частицами обрабатываемого материала, благодаря чему интенсифицируется их перемещение относительно друг друга. Жидкой средой обычно служат спирт, ацетон, вода, некоторые углеводороды и пр.
Полезный эффект от размола в жидкости усиливается при добавлении в нее поверхностно-активных веществ (ПАВ). Количество жидкости должно быть таким, чтобы она достигала верхнего уровня размольных тел,находящихся в барабане мельницы, что составляет 0,15–0,25 л на 1 кг размольных тел.
Обычно в мельницу загружают 1,7–1,9 кг стальных шаров на один литр ее рабочего объема, а соотношение между массой размольных тел и массой измельчаемого материала составляет 2,5–3,0. При интенсивном измельчении это соотношение увеличивается до 6–12 и даже больше.
Процессы порошковой металлургии. Курс лекций |
-46- |
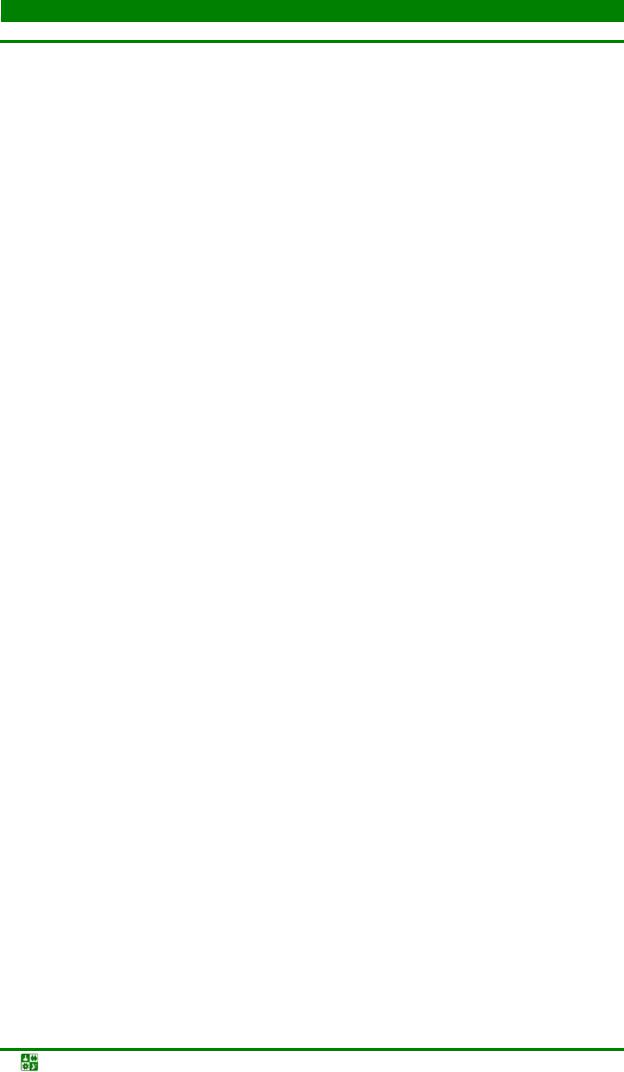
I. ПОЛУЧЕНИЕ ПОРОШКОВ
Лекция 6 Измельчение материалов в шаровых мельницах
Если плотности измельчаемого материала и размольных тел близки (как, например, при размоле стальной стружки стальными шарами), указанное соотношение должно составлять 5–6.
Если плотности измельчаемого материала и размольных тел значительно отличаются, то определить необходимое для эффективной работы мельницы количество материала можно расчетным путем. Известно, что при свободной насыпке сферических размольных тел равного диаметра в барабан мельницы объем пустот между размольными телами составляет около 50 %. Это тот объем, который и может занимать измельчаемый материал. Следовательно, зная объем мельницы и коэффициент заполнения ее размольными телами, можно определить оптимальный объем измельчаемого материала, а зная насыпную плотность материала, – массу. Аналогичным путем можно установить и объем заливаемой в мельницу жидкости.
Размер размольных тел (диаметр шаров) также оказывает влияние на процесс размола. По приближенной оценке его максимальное значение должно быть в пределах 5–6 % внутреннего диаметра барабана мельницы. Интенсивность измельчения с уменьшением размера размольных тел возрастает до тех пор, пока усилие от воздействия каждого из них оказывается достаточным для разрушения частиц обрабатываемого материала или нарушения целостности их поверхности. На практике для повышения эффективности помола применяют набор различных по размерам размольных тел (например, при соотношении размеров 4 : 2 : 1).
Производительность шаровых вращающихся мельниц во многом зависит от их габаритных размеров и от характера измельчаемого материала.
Длительность размола колеблется от нескольких часов до нескольких суток. Для предотвращения быстрого износа стенок барабана и загрязнения в результате этого измельчаемого материала применяют защиту (футеровку) внутренних поверхностей барабана износостойкими материалами: марганцовистыми сталями, твердыми сплавами, наплавочными материалами.
Для шаровых вращающихся мельниц соотношение средних размеров частиц порошка до и после измельчения, называемое степенью измельчения, составляет 50–100. Форма частиц, получаемая в результате размола в шаровых вращающихся мельницах, обычно осколочная, т.е. неправильная, с острыми гранями, а шероховатость их поверхности невелика.
Режимыизмельченияматериалов
При измельчении материалов стараются поддерживать такие режимы работы мельницы, при которых на измельчаемый материал (со стороны размольных тел) действовали бы максимальные усилия. На практике чаще всего применяют два основных режима работы шаровых мельниц: режим интенсивного измельчения, при котором на материал действуют в основном раздавливающие и ударные усилия, либо режим перекатывания, при котором на материал действуют истирающие и раздавливающие усилия. Первый ре-
Процессы порошковой металлургии. Курс лекций |
-47- |
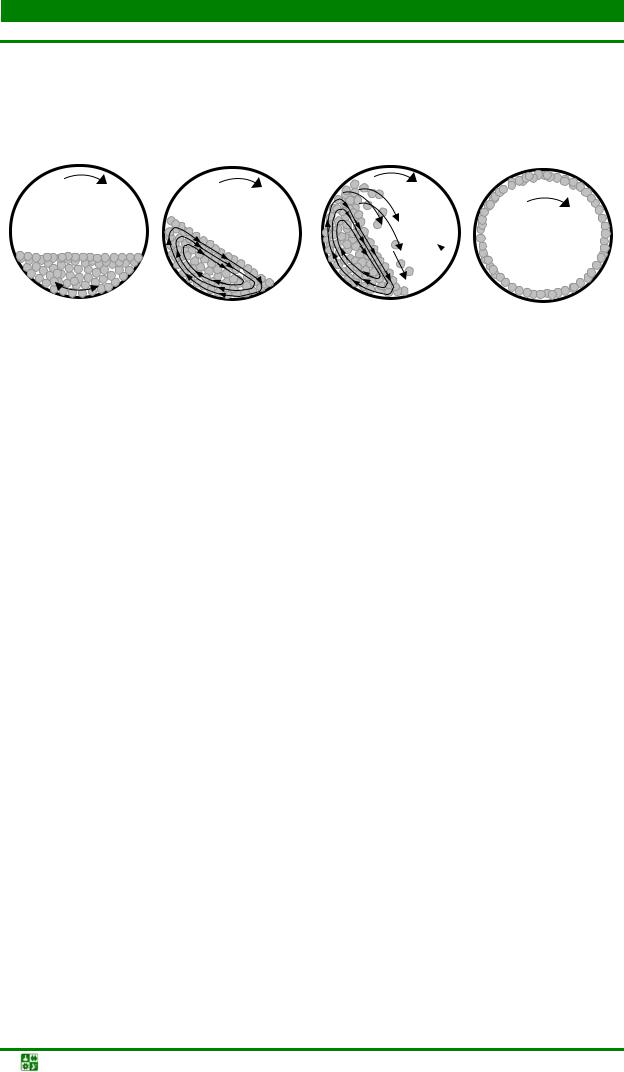
I. ПОЛУЧЕНИЕ ПОРОШКОВ
Лекция 6 Измельчение материалов в шаровых мельницах
жим применяется для получения грубых, крупных порошков, второй – для тонкого измельчения материала. Переход в тот или иной режим достигается вариацией скоростей вращения барабана мельницы (рис. 1.9).
а |
б |
в |
г |
Рис. 1.9. Схема движения шаров в барабане шаровой мельницы при различной скорости его вращения: а – режим скольжения при n ≤ 0,2 nкр; б – режим перекатывания при n ≤ 0,4–0,6 nкр; в – режим интенсивного измельчения (водопадный режим) при n ≤ 0,75–0,85nкр; г – движение шаров при n ≥ nкр
При получении измельченных материалов с размером частиц порядка одного микрометра размол путем дробления падающими шарами не эффективен. Это связано с тем, что в процессе измельчения материала значительно уменьшается количество ударных воздействий, испытываемых за единицу времени каждой отдельной частицей. Кроме того, у мелких порошков в более значимой степени, чем у крупных, проявляется склонность к комкованию, агрегатированию и релаксации напряжений.
Поэтому на предприятиях после сравнительно непродолжительной (несколько часов) работы мельницы в режиме интенсивного измельчения, ее переводят в режим перекатывания шаров, при котором они не падают, а поднимаются вместе со стенкой вращающегося барабана мельницы и затем скатываются по наклонной поверхности, образованной их массой (рис. 1.9, в).
Измельчаемый материал истирается между шарами, циркулирующими в объеме, занимаемом их массой. При режиме перекатывания различимы четыре зоны движения шаров:
зона их подъема по стенке барабана с некоторой не очень высокой скоростью;
зона скатывания с наибольшей скоростью; зона встречи скатившихся шаров со стенкой барабана
центральная застойная зона, в которой шары почти неподвижны. Увеличивая скорость вращения барабана мельницы, можно повысить
эффективность режима перекатывания путем сужения или полной ликвидации застойной зоны в шаровой загрузке. Наконец, может быть созданеще один вариант режима размола, получивший название режима скольжения. При и с- пользовании мельниц с гладкой внутренней поверхностью барабана и при небольшой относительной загрузке размольные тела не циркулируют внутри ба-
Процессы порошковой металлургии. Курс лекций |
-48- |
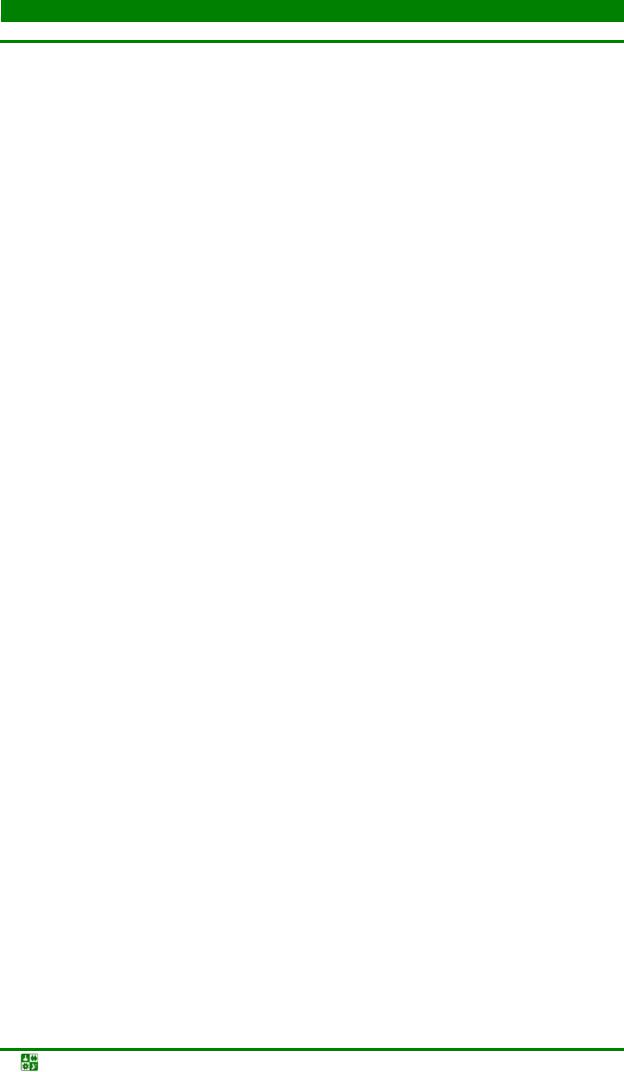
I. ПОЛУЧЕНИЕ ПОРОШКОВ
Лекция 6 Измельчение материалов в шаровых мельницах
рабана мельницы. Вся масса размольных тел скользит по поверхности вращающегося барабана, а их взаимное перемещение отсутствует (рис. 1.9, а). Измельчение материала при таком режиме размола малоэффективно, так как происходит путем истирания его лишь между внешней поверхностью сегмента размольных тел и стенкой барабана мельницы.
Управлениепроцессомизмельчения
Наличие перекатывания или скольжения размольных тел при вращении барабана мельницы зависит (при прочих равных условиях) от относительной загрузки ϕ. При загрузке большого числа шаров (или размольных тел другой формы, но обязательно полиэдрической) происходит перекатывание, а при малой загрузке – скольжение.
В практике размола величина ϕ иногда определяется местными условиями (например, наличием загрузочного люка в торцовой стенке барабана мельницы или количеством измельчаемого материала). Изменяя величину загрузки мельницы размольными телами, можно получать в одних случаях режим перекатывания, а в других – режим скольжения, причем в зависимости от устанавливающегося режима эффективность размола будет различной.
Для управления процессом размола необходимо знать условия перехода режима скольжения в режим перекатывания и обратно.
Рассмотрим поведение шаров в барабане мельницы, работающей в режиме скольжения. В неподвижном барабане в состоянии покоя шары занимают положение в его нижней части. При вращении барабана шары под действием силы трения продвигаются в направлении вращения. Для упрощения расчетов будем считать, что объем, занимаемый шарами, ограничен плоской поверхностью. При постоянной и не слишком высокой скорости вращения барабана поверхность массы шаров займет наклонное положение
(рис. 1.10).
Угол этого наклона β определяется равенством моментов двух сил: силы трения, перемещающей шары из положения покоя в направлении вращения барабана, и силы тяжести, препятствующей подъему шаров вместе со стенкой барабана.
Процессы порошковой металлургии. Курс лекций |
-49- |
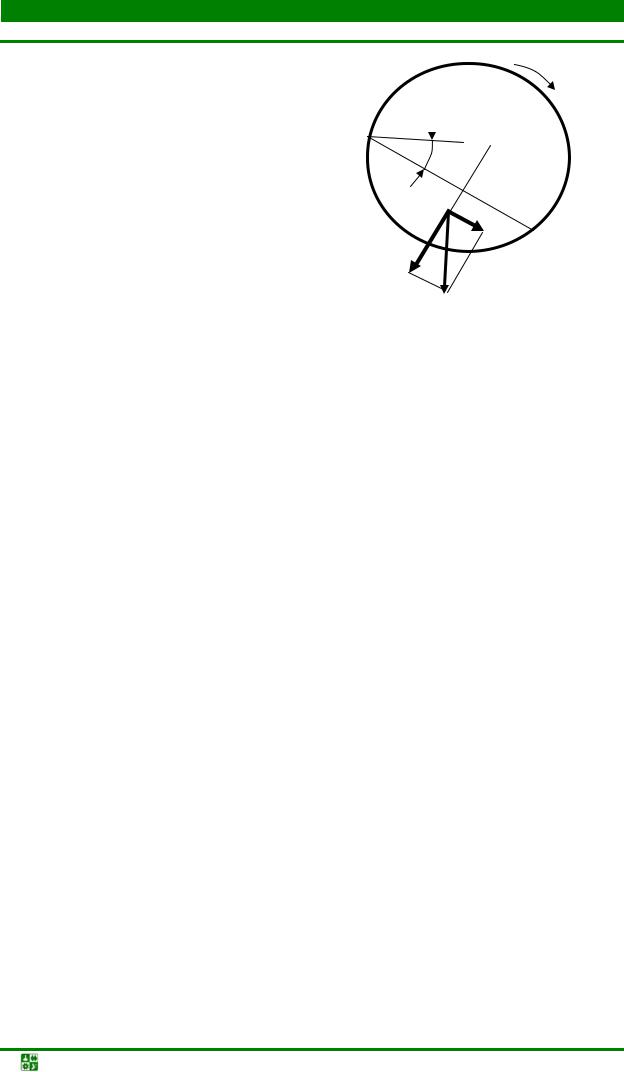
I. ПОЛУЧЕНИЕ ПОРОШКОВ
Лекция 6 Измельчение материалов в шаровых мельницах
|
|
β |
А |
|
|
||
|
|
|
|
|
|
|
0 |
Рис. 1.10. Направление силы тяжести Р и ее |
|
|
Р1 |
составляющих Р1 и Р2 при наклонном поло- |
|
|
|
|
|
|
|
жении внешней габаритной поверхности мас- |
Р2 |
|
|
сы размольныхтел во вращающемся барабане |
|
Р |
|
мельницы |
|
|
|
|
|
|
Максимальный вращающий момент силы трения равен произведению силы трения на радиус цилиндрической стенки барабана мельницы (влиянием трения шаров о торцовые стенки барабана пренебрегаем).
Сила трения в первом приближении не зависит от площади скольжения и определяется лишь общей нагрузкой и коэффициентом трения. Если вес шаровой загрузки Р, коэффициент трения f и радиус внутренней поверхности барабана мельницы R, то момент сил, увлекающих шары во вращательное движение, равен М1 = fPR.
При скольжении взаимное перемещение шаров отсутствует, поэтому совокупность шаров можно рассматривать как жесткое тело и считать, что сила тяжести приложена к центру тяжести шаровой загрузки. Момент сил, препятствующих вращению шаров d месте с барабаном мельницы, равен произведению составляющей силы тяжести P1, направленной перпендикулярно радиусу, проходящему через центр тяжести шаровой загрузки, и длины отрезка, равного расстоянию от центра тяжести до оси вращения барабана мельницы.
При неподвижном барабане мельницы свободная габаритная поверхность массы шаров горизонтальна и центр тяжести шаровой загрузки лежит на вертикали, проходящей через горизонтальную ось вращения барабана мельницы. После пуска мельницы по мере увеличения наклона этой габаритной поверхности и отдаления центра тяжести шаровой загрузки от вертикали, проходящей через ось вращения барабана, возрастает составляющая силы тяжести (при неподвижном барабане мельницы она равна нулю).
Следовательно, с увеличением наклона свободной габаритной поверхности массы шаров растет момент сил, препятствующий движению шаров вместе с барабаном мельницы.
Наклон этой поверхности будет увеличиваться до тех пор, пока момент сил, препятствующих движению шаров вместе с барабаном, не станет равным моменту сил трения. Соответствующий этому равенству наклон свободной габаритной поверхности шаровой загрузки остается постоянным при
Процессы порошковой металлургии. Курс лекций |
-50- |
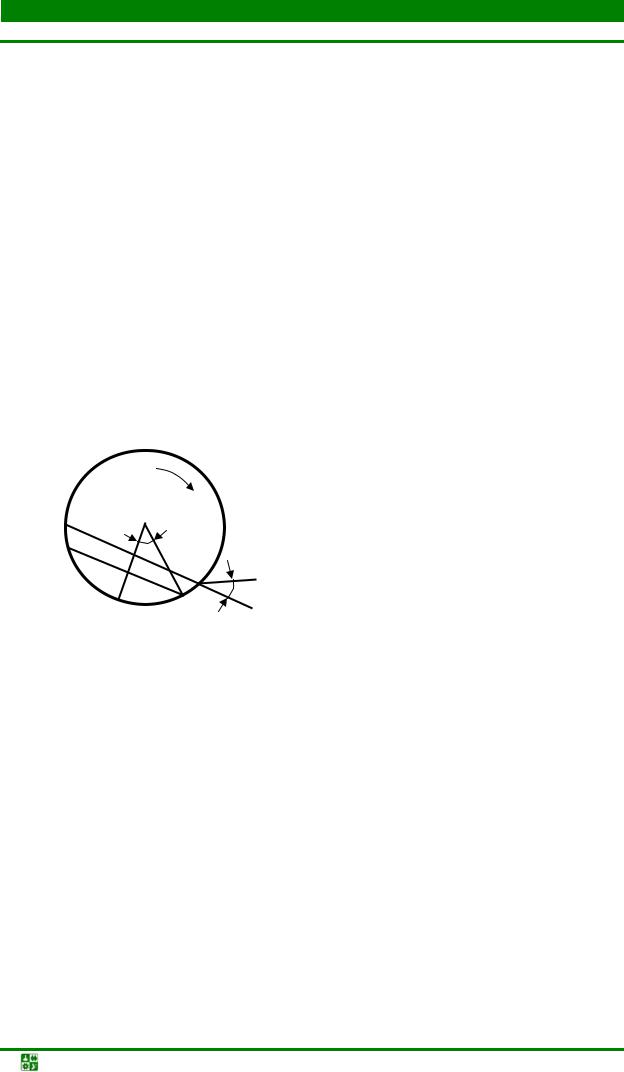
I. ПОЛУЧЕНИЕ ПОРОШКОВ
Лекция 6 Измельчение материалов в шаровых мельницах
непрерывном вращении барабана мельницы с постоянной скоростью, обеспечивающей равенство этих моментов. Фактически при режиме скольжения шары совершают колебания около положения равновесия каждого из них, а наклон рассматриваемой поверхности шаровой загрузки колеблется около некоторого среднего положения, определяемого равенством указанных моментов сил.
Момент сил, препятствующий движению шаров вместе с барабаном мельницы, равен М2 = Р1 d, где d – длина отрезка ОА. Величина d может быть выражена через радиус барабана мельницы R и угол α1. (рис. 1.11). Сегмент ВFС соответствует доле объема барабана мельницы, заполненного шарами. Если через центр тяжести шаровой загрузки провести хорду DЕ, па-
раллельную хорде ВС и делящую площадь сегмента ВFС пополам, то угол α1 будет равен углу половины дуги, отсекаемой хордой DЕ, проходящей через центр тяжести. Из построения, показанного на рисунке, следует, что
d = R соs α1, Р1 = P sin β и M2 = PR cos α1.
|
|
|
А |
|
|
|
|
B |
|
|
|
||
|
|
|
|
|
|
|
|
|
|
О α1 |
|
|
|
|
|
|
|
|
|
|
|
D |
|
|
|
|
|
|
|
|
|
|
|
|
|
|
|
|
|
C |
Рис. 1.11. Схема к определению зависимо- |
|
|
|
|
|
||
|
|
|
F |
E |
β |
сти режимов движения размольных тел от |
|
|
|
|
угла их загрузки α1 в барабане мельницы |
||
|
|
|
|
|
При установившемся наклоне свободной габаритной поверхности шаровой загрузки моменты М1 и M2 равны: fPR = PR cos α1 sin β, откуда
sin β = f / cos α1. |
(1.10) |
Таким образом, устанавливающийся при вращении барабана мельницы наклон свободной габаритной поверхности шаровой загрузки зависит только от двух величин: коэффициента трения f и угла α1. В свою очередь, угол α1 зависит только от относительной загрузки барабана мельницы шарами, т.е. от коэффициента ϕ.
По мере увеличения шаровой загрузки угол α1 возрастается от 0 до 90°, а cos α1 уменьшается от 1 до 0. Отсюда следует, что sin β и β возрастают по мере увеличения шаровой загрузки в барабане мельницы. По формальному требованию sin β не может быть больше единицы. Для сохранения режи-
Процессы порошковой металлургии. Курс лекций |
-51- |
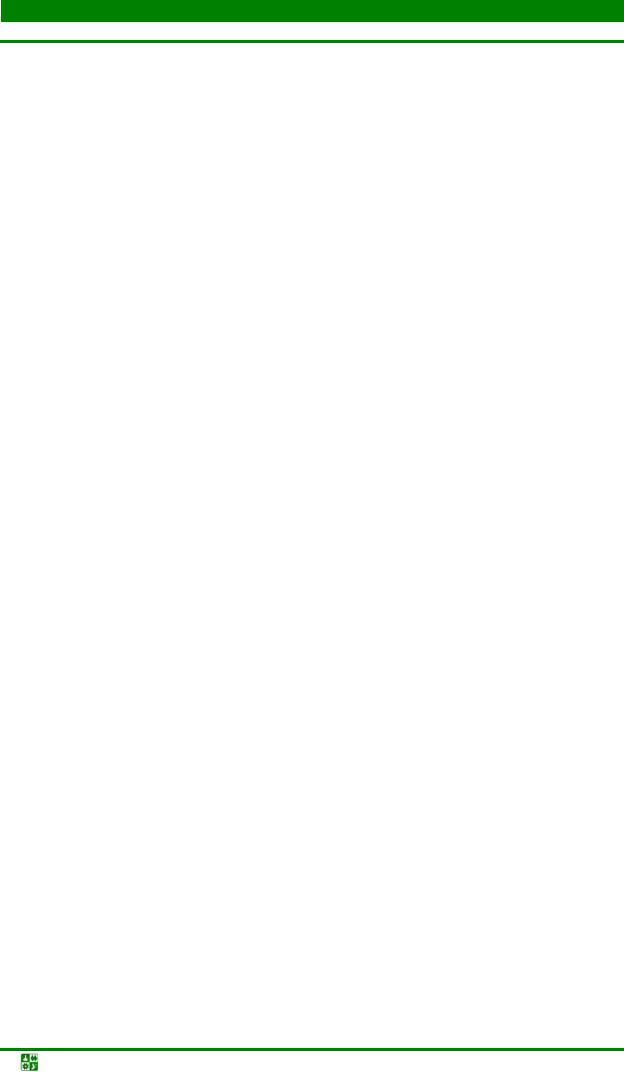
I. ПОЛУЧЕНИЕ ПОРОШКОВ
Лекция 6 Измельчение материалов в шаровых мельницах
ма скольжения размольных тел угол α1 должен определяться величиной f из условия f /соs α1 ≤ 1.
Формула (1.10) свидетельствует о том, что наклон свободной габаритной поверхности шаровой загрузки должен непрерывно возрастать по мере увеличения ее объема, но практически он не может возрастать беспредельно: при некотором наклоне шары уже не будут удерживаться на рассматриваемой наклонной поверхности, они будут срываться и скатываться вниз.
Увеличение наклона по мере возрастания объема их загрузки в барабане мельницы будет происходить до тех пор, пока угол наклона β не достигнет величины угла естественного откоса для массы шаров.
При дальнейшем увеличении загрузки шаров наклон не будет возрастать, так как скатывающиеся шары будут обеспечивать сохранение наклона свободной габаритной поверхности шаровой нагрузки, соответствующего углу естественного откоса для нее (или для поверхности размольных тел любой другой полиэдрической формы).
Основное условие сохранения скольжения для массы шаров при этом нарушится: из-за недостаточной величины угла β момент силы тяжести в этих условиях не может быть равным моменту сил трения и будет меньше его. Вследствие этого скольжение шаров полностью прекратится, все шары будут подниматься вместе со стенкой барабана мельницы и скатываться по наклонной поверхности, ограничивающей шаровую загрузку.
Если известны угол естественного откоса и коэффициент трения шаров (или размольных тел другой формы) о стенку барабана мельницы, то можно рассчитать ту их критическую загрузку, при превышении которой вместо скольжения шаров начинается их перекатывание. Коэффициент трения f удобнее всего находить экспериментально для конкретного типа размольных тел и барабана мельницы.
Определив экспериментально угол наклона β при небольшой относительной загрузке барабана, заведомо обеспечивающей скольжение размольных тел, можно рассчитать коэффициент трения f и, используя его значение, установить наклон (угол β) при любой относительной загрузке барабана мельницы или по углу естественного откоса размольных тел угол α1, соответствующий критической загрузке барабана мельницы.
Режим перекатывания обеспечивает более высокую интенсивность размола, чем режим скольжения размольных тел. Его применение позволяет резко увеличить загрузку мельницы размалываемым материалом и ускоряет процесс размола. Преимущество режима перекатывания представляется естественным, так как в этом случае в работе истирания участвуют все размольные тела, в то время как при режиме скольжения работает лишь небольшая их доля (размольные тела, соприкасающиеся со стенкой барабана мельницы).
Знание условий перехода режима скольжения в режим перекатывания позволяет избегать при разработке новых режимов размола случайного установления режима скольжения, снижающего эффективность размола и повышающего износ стенок барабана мельницы.
Процессы порошковой металлургии. Курс лекций |
-52- |

I. ПОЛУЧЕНИЕ ПОРОШКОВ
Лекция 6 Измельчение материалов в шаровых мельницах
Контрольныевопросыизадания
1.Для измельчения каких материалов целесообразно использовать шаровые мельницы?
2.Назовите основные виды шаровых мельниц.
3.Чему равна критическая скорость вращения барабана мельницы?
4.Назовите основные факторы, определяющие степень помола в шаровых мельницах.
5.Укажите механизмы перехода мельницы в различные режимы.
6.Назовите основные режимы работы шаровых мельниц.
7.Какие усилия (в основном) действуют на измельчаемый материал в режимах интенсивного измельчения и истирания?
8.Как можно предотвратить пыление и агрегатирование порошка при его размоле?
Лекция7 Получениемеханолегированныхпорошков.
Измельчениематериаловввибрационных, вихревых, планетарныхигироскопическихмельницах
План лекции
1.Получение механолегированных порошков в шаровых мельницах и аттриторах.
2.Размол материалов в вибрационных мельницах.
3.Размол материалов в планетарных центробежных и гироскопических мельницах.
4.Размол материалов в вихревых и струйных мельницах.
Получениемеханолегированныхпорошков вшаровыхмельницахиаттриторах
Несмотря на то, что режим работы шаровой мельницы при скорости вращения барабана больше критической считается крайне неэффективным, на практике применяются высокоскоростные шаровые мельницы, работающие и при этих режимах. Для перевода размольных тел в рабочее состояние, внутри барабана мельницы установлен ряд лопастей. При вращении барабана со скоростью, равной или большей nкр, размольные тела оказываются прижатыми к его цилиндрической поверхности, а лопасти перемешивают их и возвращают в рабочую зону. В такой мельнице получают композитные порошки
Процессы порошковой металлургии. Курс лекций |
-53- |
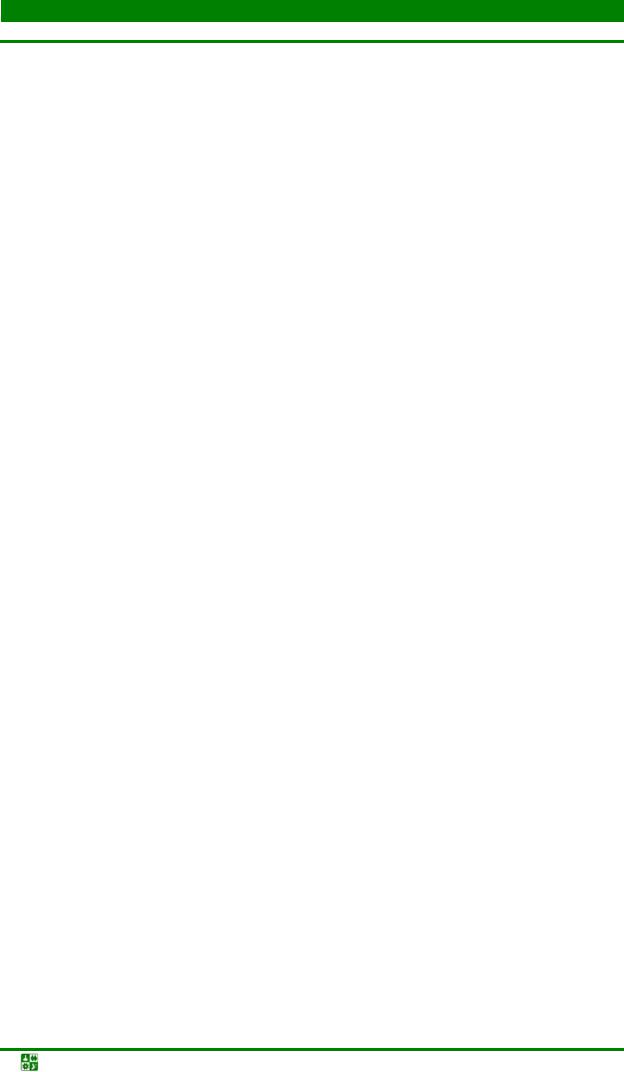
I. ПОЛУЧЕНИЕ ПОРОШКОВ
Лекция 7 Получение механолегированных порошков
методом механического легирования путем совмещенного размола двух и более металлов. Отношение массы размольных тел к массе смеси порошков составляет 6 : 1.
Процесс механического легирования во времени можно условно раз-
делить на пять стадий. На первой стадии (≤ 12 мин) происходит расплющивание и размол отдельных частиц. Вторая стадия (12–30 мин) представляет собой чередование разрушения и перестройки структуры частиц за счет холодного сваривания разнородных частиц с образованием «склепанных» частиц с характерной слоистой структурой. На третьей стадии (30–60 мин) эти «склепанные» частицы разрушаются и исчезают частицы исходных порошков, превращаясь в композиционные частицы со слоистой структурой. В течение четвертой стадии (60–100 мин) нарушается параллельность в расположении слоев в структуре композиционных частиц, а напятой стадии (> 100 мин) повышается внутренняя однородность (гомогенность) частиц, причем слои разнородных компонентов истончаются, а их число растет. Механическое легирование перспективно для получения порошков дисперсно-упрочненных материалов или таких композиций, компоненты которых обладают малой взаимной растворимостью либо резко различаются температурами плавления.
Одной из разновидностей шаровых мельниц являются так называемые
аттриторные устройства (рис. 1.12).
Размольные тела загружают в вертикальный (или горизонтальный) неподвижный барабан, внутри которого со скоростью более 100 об/мин вращается вертикальная лопастная мешалка.
Гребки, наклонно укрепленные на лопастях мешалки, обеспечивают циркуляцию размольных тел и истирание измельчаемого материала. Аттриторные мельницы конструктивно просты, удобны в эксплуатации и позволяют вести процесс измельчения непрерывно. В результате размола получают порошок с более равномерным распределением частиц по размерам.
Необходимая дисперсность достигается в несколько раз быстрее, чем в обычных шаровых вращающихся мельницах. Аттриторы весьма эффективны при приготовлении смеси высокодисперсных порошков разнородных компонентов, а также могут применяться для получения механолегированных порошков. В отдельных случаях аттриторы используются при получении материалов методом высокотемпературного самораспространяющегося синтеза.
Процессы порошковой металлургии. Курс лекций |
-54- |
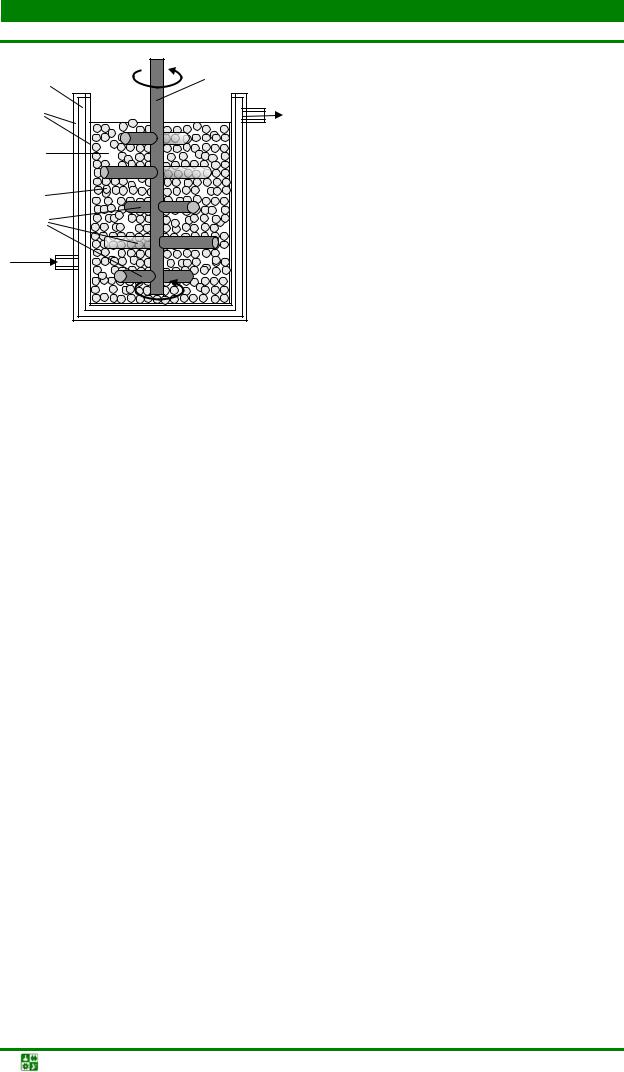
I. ПОЛУЧЕНИЕ ПОРОШКОВ
Лекция 7 Получение механолегированных порошков
1 |
3 |
|
|
2 |
|
4 |
|
5 |
|
6 |
|
Рис. 1.12. Схема аттритора: 1– корпус мельницы (размольная емкость); 2 – водоохлаждаемые стенки корпуса мельницы; 3 – вал мешалки аттритора; 4 – измельчаемый материал; 5 – размольные тела; 6 – лопасти мешалки
Увеличение скорости вращения вала до нескольких сотен оборотов в минуту приводит к проявлению эффекта механолегирования. Отношение массы шаров к массе порошка лежит в пределах от 12 : 1 до 40 : 1. Диаметр размольных тел (чаще всего из хромистоуглеродной стали) – от 4 до 10 мм. Продолжительность процесса – до нескольких десятков часов.
Размолматериаловввибрационныхмельницах
В практике порошковой металлургии широко используют вибрационные мельницы, обеспечивающие быстрое и тонкое измельчение обрабатываемых материалов, например карбидов и других тугоплавких соединений различных металлов, при производстве твердых сплавов и др. При производстве порошков используют вибромельницы различных типов и конструкций, различающиеся главным образом по технологическим и конструктивным признакам. В соответствии с технологическими признаками их подразделяют по типу размола (сухое измельчение или мокрое) и характеру работы (периодического действия или непрерывного). К конструктивным признакам относят тип возбудителя колебаний (эксцентриковые или дебалансные), форму корпуса мельницы (цилиндрический, прямоугольный), тип ее опоры и т.д.
Наиболее распространены вибрационные дебалансные мельницы, (рис. 1.13), дебалансный вал которых приводится во вращение от электродвигателя через эластичную муфту.
Процессы порошковой металлургии. Курс лекций |
-55- |
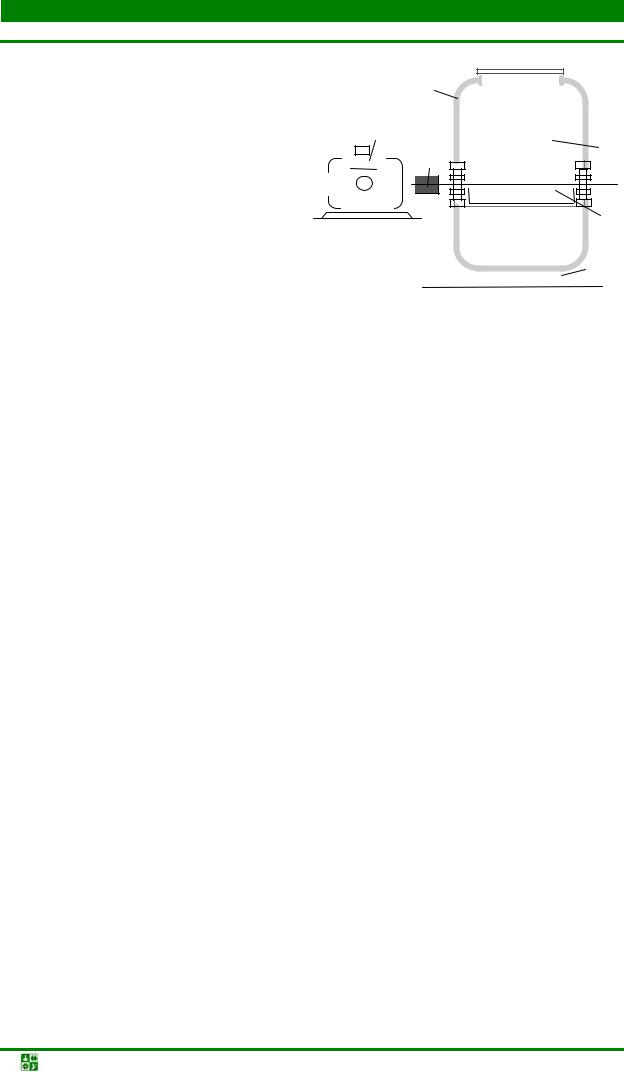
I. ПОЛУЧЕНИЕ ПОРОШКОВ
Лекция 7 Получение механолегированных порошков
4
|
|
|
3 |
|
|
|
|
|
||||||||||||
|
|
|
1 |
|
|
|
|
|
|
|
|
5 |
||||||||
|
|
|
|
|
|
|
|
2 |
||||||||||||
|
|
|
|
|
|
|
|
|||||||||||||
|
|
|
|
|
|
|
|
|
|
|
|
|
||||||||
|
|
|
|
|
|
|
|
|
|
|
|
|
||||||||
|
|
|
|
|
|
|
|
|
|
|
|
|
|
|
|
|
|
|
|
|
|
|
|
|
|
|
|
|
|
|
|
|
|
|
|
|
|
|
|
|
|
|
|
|
|
|
|
|
|
|
|
|
|
|
|
|
|
|
|
|
|
|
|
|
|
|
|
|
|
|
|
|
|
|
|
|
|
|
1 |
|
|
||
|
|
|
|
|
|
|
|
|
|
|
|
|
|
|
|
|||||
Рис. 1.13. Схема вибрационной мельницы: |
|
|
|
|
|
|
|
|
|
|
|
|
|
|||||||
|
|
|
|
|
|
|
|
|
|
|
|
|
|
|
|
|
|
|||
|
|
|
|
|
|
|
|
|
|
|
|
|
6 |
|||||||
|
|
|
|
|
|
|
|
|
|
|
|
|
||||||||
1 – электродвигатель; 2 – соединительная |
|
|
|
|
|
|
|
|
|
|
|
|
|
|
|
|
|
|
||
муфта; 3 – корпус мельницы; 4 – загрузоч- |
|
|
|
|
|
|
|
|
|
|
|
|
|
7 |
||||||
ный люк; 5 – размольные тела; 6 – деба- |
|
|
|
|
|
|
|
|
|
|
|
|
|
|||||||
лансный вал; 7 – амортизаторы (пружины) |
|
|
|
|
|
|
|
|
|
|
|
|
|
|
|
|
|
|
||
|
|
|
|
|
|
|
|
|
|
|
|
|
|
|
|
|
|
Вращение дебалансного вала вызывает колебания корпуса мельницы, загруженной размольными телами и измельчаемым материалом. Частота вращения вала составляет от 1 000 до 3 000 об/мин, амплитуда колебаний корпуса мельницы – 2–4 мм.
Размольные тела, получая частые импульсы от стенок корпуса мельницы, совершают сложные движения. Они подскакивают, соударяются и скользят по стенкам корпуса мельницы. В результате трения о стенки мельницы они начинают вращаться. На частицы измельчаемого материала действуют ударные, сжимающие и срезывающие усилия переменной величины. Ударный импульс единичного размольного тела в вибромельнице по сравнению с ударным импульсом в шаровой вращающейся мельнице относительно невелик.
Однако большое число размольных тел в единице объема корпуса мельницы и высокая частота их колебаний обеспечивают интенсивное измельчение обрабатываемого материала. Суммарное число импульсов i, сообщаемых размольным телам в единицу времени, можно оценить по формуле
i = V k ϕ·n z B, |
(1.11) |
где V – объем корпуса мельницы, дм3; k – число размольных тел, размещающихся в 1 дм 3 объема корпуса мельницы; ϕ – коэффициент заполнения корпуса мельницы размольными телами (обычно составляет 0,75–0,85); n – частота вращения вала, об/мин (обычно 1 000–3 000 об/мин); z – число импульсов, сообщаемых каждому из размольных тел корпусом мельницы за одно его круговое качание; В – коэффициент, учитывающий дополнительное число импульсов, сообщаемых за один оборот вала каждому размольному телу соседними размольными телами.
Если условно принять k = 1 250 шт./дм3 (при среднем диаметре шаров 10 мм), ϕ = 0,8, n = 1 500 об/мин, z = 1 (за один оборот вала каждому из размольных тел сообщается только один импульс), B = 1 (т.е. не учитывать
Процессы порошковой металлургии. Курс лекций |
-56- |
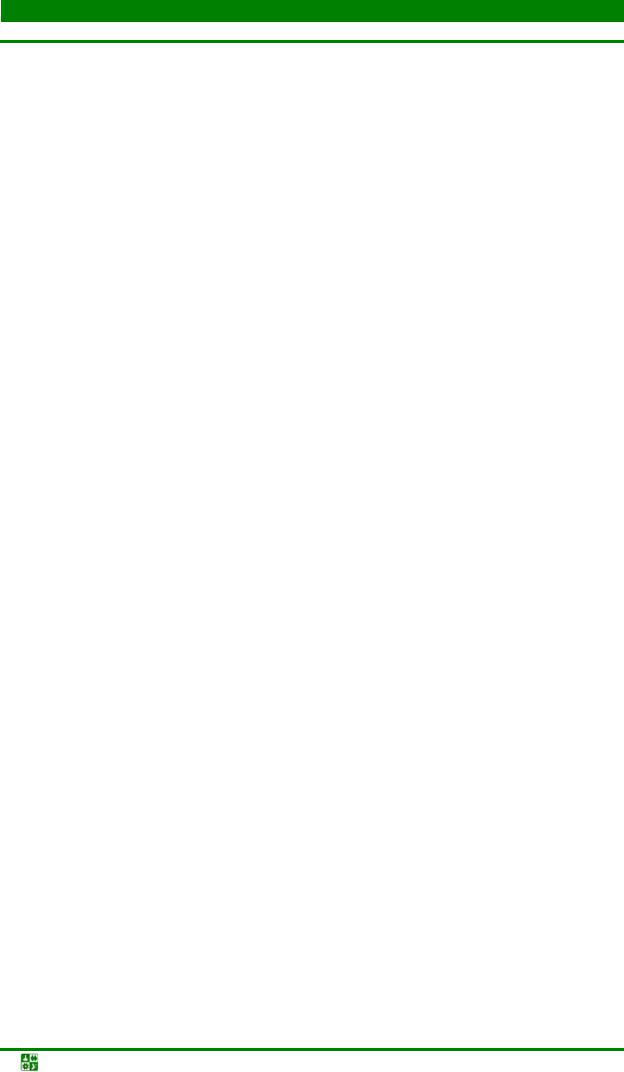
I. ПОЛУЧЕНИЕ ПОРОШКОВ
Лекция 7 Получение механолегированных порошков
увеличение частоты воздействия за счет импульсов, дополнительно сообщаемых каждому шару соседними с ним шарами), то число импульсов, сообщаемых размольным телам в корпусе мельницы объемом 200 дм3, составит i = 200 ·1 250·0,8·1 500 = 3·108 импульсов в минуту.
Это на несколько порядков выше числа импульсов, сообщаемых размольным телам при измельчении материала в шаровой барабанной мельнице. Благодаря высокой частоте воздействий релаксация материала (самозаживление трещин под действием сил межатомарного сцепления) в вибрационных мельницах проявляется в меньшей степени, а процесс измельчения протекает значительно быстрее. Время измельчения материала до высокодисперсного состояния (в большинстве случаев) не превышает нескольких часов (5–6 ч). Исследования порошка, полученного в вибрационной мельнице, показывают наличие большого числа частиц округлой формы, что свидетельствует о существенной роли истирающих воздействий на измельчаемый материал как со стороны размольных тел, так и со стороны частиц самого материала (явление самоистирания).
Основные показатели режима виброразмола (коэффициент заполнения рабочего объема корпуса мельницы размольными телами и измельчаемым материалом, соотношение между ними, продолжительность процесса и др.) обычно устанавливают экспериментально с учетом свойств измельчаемого материала и требуемой дисперсности получаемого порошка.
Размолматериаловвпланетарныхцентробежных игироскопическихмельницах
Планетарные центробежные (ПЦМ) и гироскопические мельницы используются для получения сравнительно небольших объемов нано- и ультра-
дисперсных порошков. В планетарных центробежных мельницах тонкое из-
мельчение трудноразмалываемых материалов производится во много раз быстрее, чем в мельницах других типов. Время измельчения материалов в ПЦМ чаще всего не превышает нескольких десятков минут (10–30 мин).
Наиболее распространенный вариант ПЦМ состоит из корпуса-шкива, на котором установлены обоймы для крепления барабанов мельницы (рис. 1.14). Электродвигатель приводит во вращение корпус оси промежуточных зубчатых колес и обоймы.
Закрепленные в обоймах барабаны вращаются вместе с корпусомшкивом и одновременно вокруг своей оси в направлении, противоположном направлению вращения корпуса. В процессе вращения корпуса-шкива барабаны получают ускорение до 35g.
Процессы порошковой металлургии. Курс лекций |
-57- |
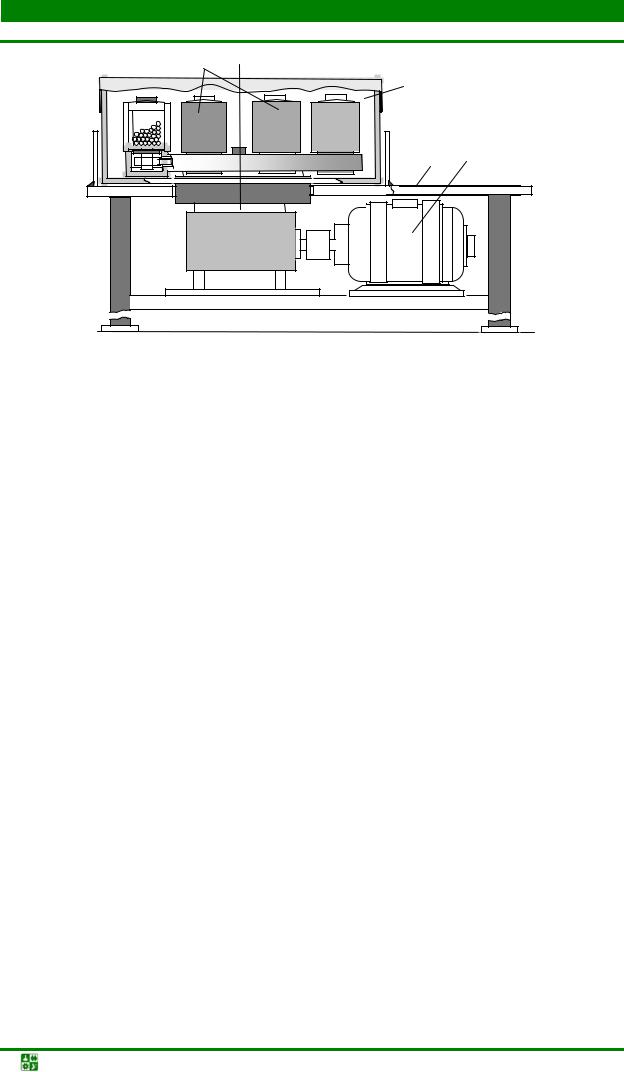
I. ПОЛУЧЕНИЕ ПОРОШКОВ
Лекция 7 Получение механолегированных порошков
4 |
|
3 |
|
2 |
5 |
1
Рис. 1.14. Схема планетарной центробежной мельницы: 1 – редуктор; 2 – опорный стол; 3 – корпус-шкив с механизмом привода барабанов; 4 – барабан с размольными телами, обоймы для установки барабанов; 5 – электродвигатель
Во время вращения барабана размольные тела в нем располагаются в виде сегмента, форма и положение которого не изменяются во времени, массив шаров движется вместе с барабаном, а каждый шар (единичное размольное тело) движется по окружности, центром которой является ось барабана.
По достижении «зоны отрыва» размольные тела начинают перекатываться в сегменте и вращаться вокруг собственных центров тяжести, что обеспечивает измельчение обрабатываемого материала за счет его истирания.
На эффективность помола в ПЦМ оказывают влияние геометрические параметры агрегатов мельницы (расстояние от оси корпуса-шкива до оси барабана, диаметр барабана), угловая скорость корпуса-шкива, скорость вращения барабана. Для эффективной работы ПЦМ («отрыва» размольных тел) экспериментально подбирается оптимальное соотношение скоростей вращения корпуса-шкива и барабанов (передаточное отношение).
Наиболее существенный недостаток размола в ПЦМ и гироскопических мельницах – значительное загрязнение измельчаемого порошка примесью, образующейся результате истирания стенок барабанов и размольных тел.
Для того чтобы увеличить срок службы барабанов мельницы и уменьшить загрязнение измельчаемого порошка, рабочую поверхность барабанов покрывают керамической клепкой. Размольные тела, применяемые для работы мельницы также изготавливают из керамики на основе диоксида циркония, стабилизированного оксидом иттрия.
Для тонкого измельчения материалов наряду с ПЦМ используют и так называемые гироскопические мельницы. Барабан этих мельниц одновременно вращается относительно горизонтальной и вертикальной осей. Размольные тела внутри барабана совершают сложные движения, аналогичные движению раз-
Процессы порошковой металлургии. Курс лекций |
-58- |
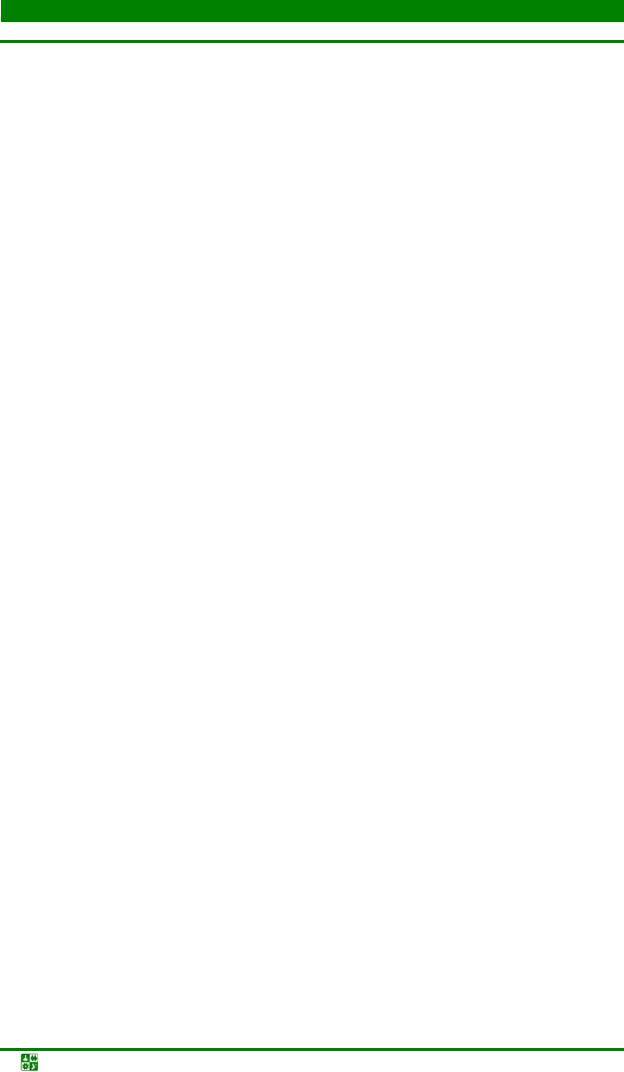
I. ПОЛУЧЕНИЕ ПОРОШКОВ
Лекция 7 Получение механолегированных порошков
мольных тел в ПЦМ. Оптимальное соотношение скоростей вращения барабана относительно вертикальной и горизонтальной осей составляет от 1 : 1 до 1 : 5.
Размолматериаловввихревых иструйныхмельницах
При измельчении в таких мельницах ударные и истирающие усилия возникают при соударении частиц обрабатываемого материала; загрязнение порошка материалом рабочего органа и стенок мельницы существенно уменьшается, а также устраняются явления, связанные с привариванием к стенкам мельницы обкованных, но не измельченных частиц.
Врабочей камере вихревой мельницы друг против друга расположены пропеллеры или била (рис. 1.15), вращающиеся в противоположных направлениях при высоких (порядка 3000 об/мин), но обязательно равных скоростях.
Мерные отрезки металлической проволоки из бункера поступают в вихревой поток, создаваемый пропеллерами или билами, сталкиваются друг с другом и измельчаются. Насосом в рабочую камеру нагнетается газ (воздух, азот и др.), с помощью которого уже измельченные частицы удаляются из рабочего пространства мельницы и направляются в ее приемную камеру.
Скорость газового потока регулируют так, чтобы из рабочей камеры мельницы удалять частицы определенных размеров (чаще всего в интервале
60–350 мкм).
Когда сила струи газа, подаваемого в рабочую камеру, превысит инерционные (гравитационные) силы, действующие на частицу измельчаемого материала, она будет вынесена из рабочего пространства мельницы.
Вприемной камере мельницы крупные частицы оседают на дно и периодически возвращаются в рабочую камеру, где подвергаются дальнейшему измельчению. Более мелкие частицы вместе с потоком газа поступают в отсадочную камеру, где выпадают, накапливаются и периодически выгружаются в емкости для порошка.
Частицы порошка, полученного в вихревых мельницах, могут быть осколочной, чешуйчатой или сферической формы, однако во многих случаях на поверхности частиц материала наблюдаются характерные углубления, отчего их форма напоминает тарелку. Поэтому частицы подобной формы получили название тарельчатых.
Для измельчения стружки металлообработки пропеллеры заменяют одним центральным валом со специальными билами.
Врезультате вихревого измельчения могут получаться достаточно мелкие, проявляющие склонность к самовозгоранию (пирофорные) порошки. Для предотвращения самовозгорания в рабочую камеру мельницы вводят ка- кой-либо инертный или нейтральный к материалу порошка газ, к которому добавляют до 5 % кислорода. Кислород, содержащийся в газе, образует на поверхности частицах порошка защитную оксидную пленку.
Процессы порошковой металлургии. Курс лекций |
-59- |

I. ПОЛУЧЕНИЕ ПОРОШКОВ
Лекция 7 Получение механолегированных порошков
5
2
3 1
7
8
6
4
Рис. 1.15. Вихревая мельница: 1 – рабочая камера мельницы; 2 – бункер для загрузки измельчаемого материала; 3 – приемная камера; 4 – пропеллеры; 5 – отсадочная камера; 6 – насос для подачи газа в рабочую камеру; 7 – порошок; 8 – емкость для выгрузки порошка из отсадочной камеры
Производительность вихревых мельниц сравнительно невелика – не более 15 кг порошка в час у мельницы мощностью около 30 кВт. Более эффективны и производительны струйные мельницы, обеспечивающие сверхтонкое измельчение материала за счет энергии вводимых в рабочую камеру мельницы (со звуковой и даже сверхзвуковой скоростью) потоков сжатого газа (воздуха, азота и др.) или перегретого пара. Материал, подаваемый в рабочую камеру мельницы, находится в постоянном движения, испытывая многократные соударения, которые приводят к его интенсивному истиранию (самоизмельчению). Так же как и в вихревых мельницах, измельченный материал (частицы размером от 1 до 5 мкм) удаляется из рабочей камеры пото-
ком газа или пара.
Контрольныевопросыизадания
1.Перечислите основные этапы получения механолегированных по-
рошков.
2.Какие преимущества имеют механолегированные порошки перед обычными?
3.Что такое аттритор?
4.Объясните принцип устройства вибрационных мельниц.
Процессы порошковой металлургии. Курс лекций |
-60- |
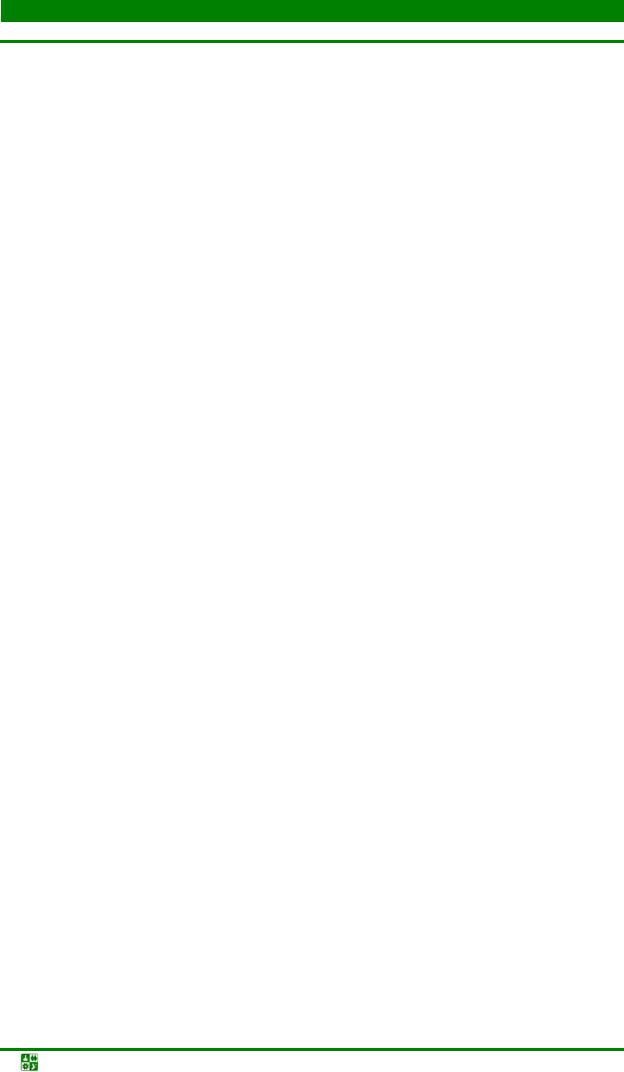
I. ПОЛУЧЕНИЕ ПОРОШКОВ
Лекция 7 Получение механолегированных порошков
5.Какие усилия действуют на материал при его измельчении в вибрационных мельницах?
6.Опишите механизм измельчения материалов в вихревых и струйных мельницах.
7.Каким образом измельченный порошок удаляется из рабочей камеры вихревой мельницы?
8.Объясните принцип действия центробежных и гироскопических
мельниц.
9.Каковы размеры частиц порошка, получаемого в центробежных и гироскопических мельницах?
10.Назовите достоинства и недостатки измельчения порошков в центробежных и гироскопических мельницах.
Лекция8 Получениепорошковультразвуковымизмельчением
вжидкихсредах. Измельчениематериалов ваппаратахмагнитногоиндукционноговращателя
План лекции
1.Измельчение ультразвуком.
2.Измельчение в аппаратах магнитного индукционного вращателя.
Измельчениеультразвуком
Металлические порошки различной крупности могут быть получены ультразвуковым диспергированием твердого вещества в жидкости.
Ультразвук представляет собой упругие колебания и волны, частота которых лежит в пределах от 10 кГц до нескольких десятков гигагерц (низкочастотные колебания – 15–100 кГц, средних частот – 100 кГц–10 МГц, высокочастотные – 10 МГц–1 ГГц; свыше 1 ГГц – гиперзвук).
Распространяясь в жидкости, твердом веществе или газе, упругие колебания создают звуковую волну, которая образует в соответствующей среде сгущения и разрежения с частотой налагаемых колебаний. Наличие в данной среде примесей (прежде всего микрочастиц) приводит к возникновению в ней давления, избыточного по отношению к атмосферному.
В жидкостях помимо твердых примесей имеется огромное число газовых пузырьков размером от десятых долей до сотен микрометров. Под воздействием ультразвука определенной мощности эти пузырьки (полости) активно пульсируют, растягиваясь и сжимаясь в фазе разрежения или сгущения ультразвуковых колебаний.
Процессы порошковой металлургии. Курс лекций |
-61- |
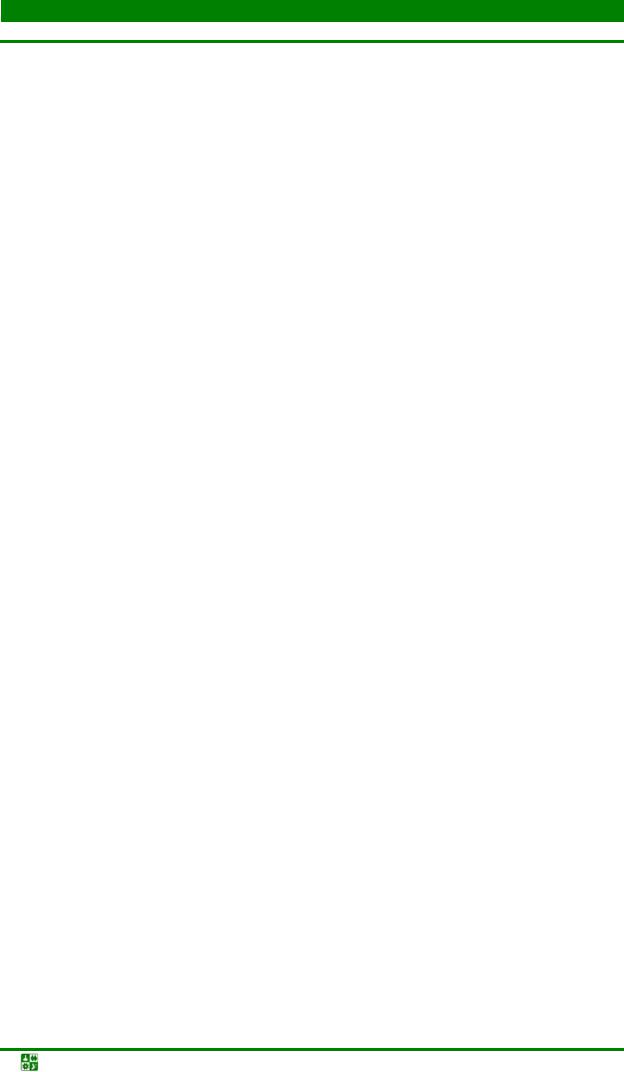
I. ПОЛУЧЕНИЕ ПОРОШКОВ
Лекция 8 Получение порошков ультразвуковым измельчением в жидких средах
Эти пульсирующие полости (пузырьки) называют кавитационными, а процесс их развития во времени – ультразвуковой кавитацией. Однако кавитационные процессы наступают лишь для тех пузырьков, начальный радиус которых R0 больше критического радиуса Rкр, но меньше резонансного Rрез (т.е. такого размера, когда частота собственного колебания пузырька совпадает с частотой налагаемого поля). При R0 < Rкр пузырьки вследствие действия сил поверхностного натяжения не участвуют в кавитации (при данной частоте колебаний), а при R0 ≥ Rрез они вытесняются на поверхность жидкости. При R0 ≥ Rкр пузырек теряет устойчивость и выходит из состояния равновесия. Значение Rкр определяют по выражению
Rкр = 1,33σ / (0,7 Pa + Pp – Po), |
(1.12) |
где σ – коэффициент поверхностного натяжения жидкости; Pa – звуковое давление; Pp – упругость пара жидкости; Po – статическое давление в объеме жидкости.
Для колебаний частотой 20 кГц, распространяющихся в воде, Rкр составляет десятые доли микрометра, а Rрез – сотни микрометров; для колебаний частотой 1 МГц Rрез – несколько микрометров. То есть с повышением частоты ультразвука количество пузырьков, вовлекаемых в кавитационный процесс, уменьшается. Это обстоятельство предопределяет выбор диапазона частот для ультразвукового диспергирования. Чаще всего для измельчения материалов в водной среде используют ультразвуковые колебания частотой от 18 до 22 кГц.
Ультразвуковое диспергирование может протекать по механизму кавитационного и/или гидроабразивного разрушения материала. Кавитационное разрушение происходит под воздействием энергии, освобождающейся при захлопывании (в фазе сжатия) кавитационных пузырьков. Гидроабразивное – при взаимодействии частиц, перемещаемых в жидкой среде акустическими потоками различной масштабности, возникающими при захлопывании пузырьков.
Пульсация кавитационных полостей приводит к заполнению жидкостью поверхностных дефектов (углублений, миктротрещин и пр.) частицы. Одновременно с жидкостью в эти дефекты поступают и пузырьки газа, имеющие различные размеры. В момент захлопывания газового пузырька изза отклонения формы их поверхности от сферической образуется ударная волна и/или микроструя жидкости. Давление, возникающее при действии на частицу измельчаемого материала этих потоков, составляет 102–103 МПа. Учитывая, что у частиц измельчаемого материала наблюдается пониженная (из-за наличия различного рода дефектов) прочность, подобного давления вполне достаточно для диспергирования исходного материала.
Процессы порошковой металлургии. Курс лекций |
-62- |

I. ПОЛУЧЕНИЕ ПОРОШКОВ
Лекция 8 Получение порошков ультразвуковым измельчением в жидких средах
Гидроабразивное разрушение является следствием как прямого удара о поверхность, так и скольжения, сопровождающегося ударами о микронеровности. Скорости микропотоков, возникающих при вторичном расширении кавитационной полости, в технологических установках, работающих при частотах от 15 до 44–45 кГц, достигают 1 500–2 000 м/с, т.е. скорости звука в жидкости; возможны даже сверхзвуковые скорости порядка 104 м/с. Скорость образующихся при кавитации микроструй жидкости, радиус которых по порядку величины соответствует минимальному радиусу кавитационных пузырьков, близка к скорости их захлопывания (от сотен до нескольких тысяч метров в секунду).
Однако скорость перемещения частиц порошка под действием этих потоков и микроструй зависит от размеров частиц. Для того чтобы частица могла перемещаться со скоростью соответствующего потока, ее размер не должен превышать 100 мкм, а для того чтобы она перемещалась со скоростью распространения микроструи – 0,1 мкм.
Кроме частоты ультразвуковых колебаний, существенное влияние на процесс диспергирования оказывают свойства жидкости (эрозионная активность, вязкость, температура) и объемная концентрация частиц твердой фазы в жидкости, а также исходное состояние частиц измельчаемого материала (наличие пористости в объеме частиц и примесей на границах между зернами).
Эрозионная активность воды значительно выше, чем у большинства органических жидкостей, которые имеют более высокие значения упругости паров. Повысить эрозионную активность жидкости можно путем введения в
ее состав поверхностно-активных веществ, улучшающих смачиваемость поверхности и способствующих проникновению жидкости в микротрещины и неровности на поверхности частиц.
Повышение вязкости жидкости снижает, как правило, ее эрозионную активность из-за потерь акустической энергии. Однако при больших интенсивностях ультразвука (т.е. энергии, излучаемой в среду с единицы излучающей поверхности в секунду) и высоковязких жидкостей (50–100 Па с) эрозионная активность повышается, так как силы вязкого трения, играя роль избыточного статического давления, ускоряют захлопывание кавитационной полости и возникновение ударной волны.
Процессы порошковой металлургии. Курс лекций |
-63- |
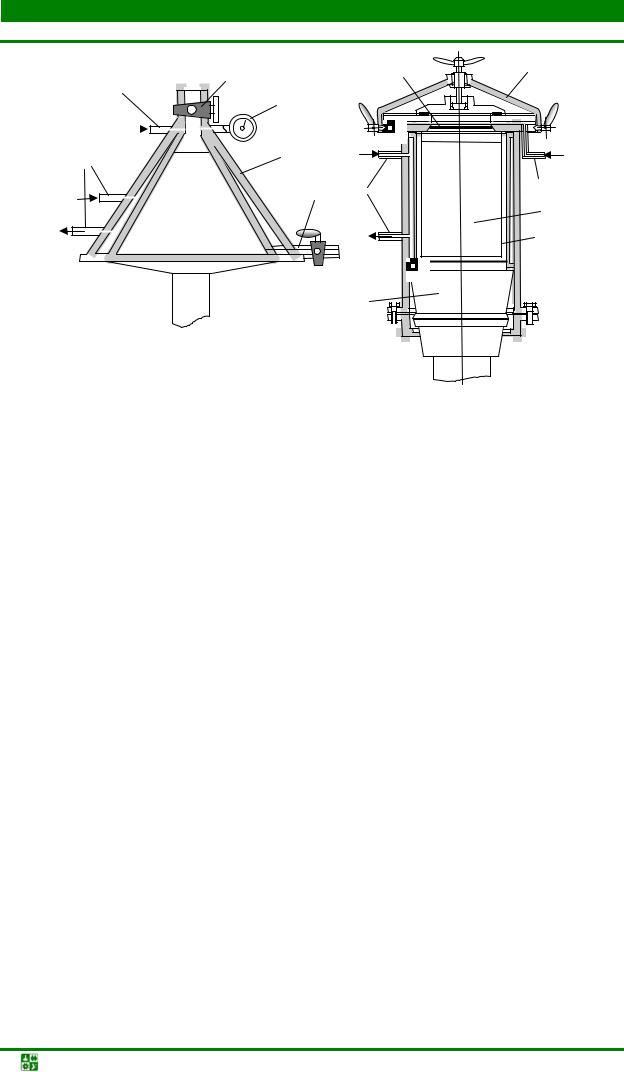
I. ПОЛУЧЕНИЕ ПОРОШКОВ
Лекция 8 Получение порошков ультразвуковым измельчением в жидких средах
5 |
7 |
|
|
|
|
6 |
|
газ |
|
|
|
50 |
0 |
10 |
|
|
60 |
5 |
|
|
40 |
30 |
20 |
4 |
2 |
3 8
1
а
4 |
5 |
|
6 |
7 |
|
3 |
||
|
||
|
2 |
|
1 |
|
|
|
б |
Рис. 1.16. Схемы ультразвуковых установок: а – установка с рабочей ванной конической формы: 1 – излучатель магнитострикционного преобразователя; 2
– корпус ванны; 3 – суспензия порошка; 4 – патрубки для подачи и удаления охлаждающей жидкости; 5 – патрубок для подачи газа; 6 – манометр; 7 – вентиль для подачи суспензии; 8 – патрубок для удаления суспензии измельченного порошка; б – установка с ванной цилиндрической формы: 1 – излучатель магнитострикционного преобразователя; 2 – сменный стакан; 3 – суспензия порошка; 4 – душирующее устройство; 5 – съемная крышка; 6 – патрубки для подачи и удаления охлаждающей жидкости; 7 – патрубок для подачи газа
С повышением температуры жидкости снижается растворимость в ней газа, увеличивается число зародышей кавитации, но одновременно возрастает и упругость пара, что уменьшает кинетическую энергию при захлопывании пузырька. Поэтому на практике для каждой из жидкостей выбирают оптимальную рабочую температуру, при которой наблюдается максимальная интенсивность кавитационного воздействия. Так, для воды и водных растворов она составляет 35–50 °С; для большинства органических жидкостей с высокой упругостью пара (спирт, бензин, четыреххлористый углерод, ацетон и др.) – 15–20 °С; а для органических жидкостей с низкой упругостью пара (глицерин, масла) – 80–85 °С.
Объемная концентрация твердых частиц в жидкости (концентрация суспензии) соответствует обычно отношению Т : Ж от 1 : 8 до 1 : 20 (чем концентрированнее суспензия, тем крупнее получаемый порошок при прочих равных условиях; большая дисперсность достигается при меньшем коэффициенте заполнения суспензией рабочего объема ванны диспергирования). Время, необходимое для измельчения материала до требуемой дисперсности, зависит от
Процессы порошковой металлургии. Курс лекций |
-64- |
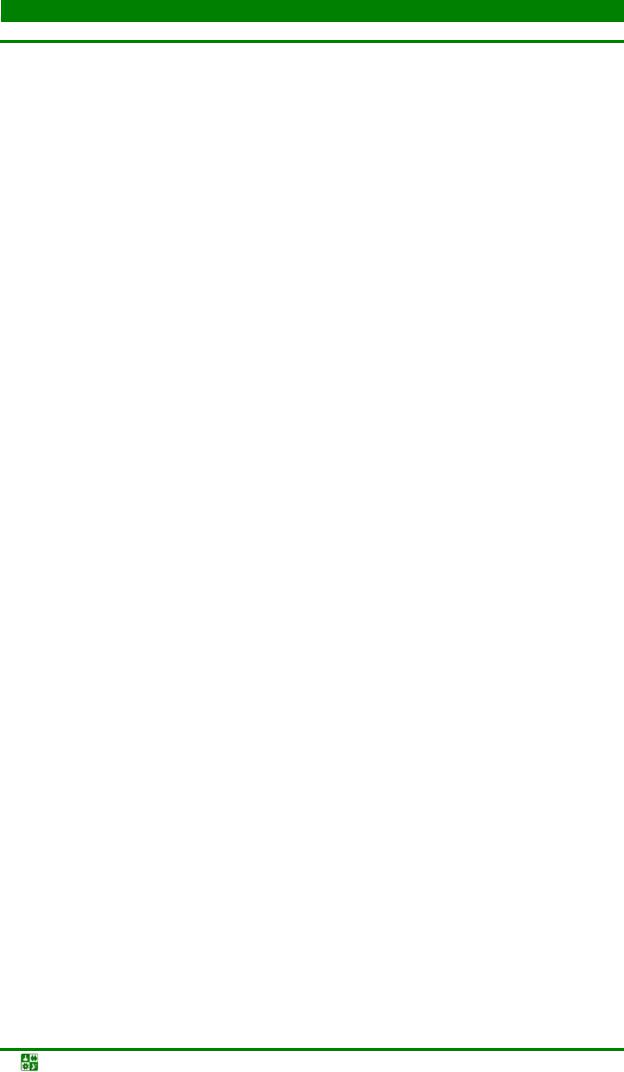
I. ПОЛУЧЕНИЕ ПОРОШКОВ
Лекция 8 Получение порошков ультразвуковым измельчением в жидких средах
физических и механических свойств его частиц, а также интенсивности ультразвуковой кавитации. Обычно оно составляет от 5–10 до 30–60 мин: при меньшей длительности обработки измельчение недостаточно, а при более длительной возникает агрегация частиц с образованием крупных конгломератов.
Ультразвуковое диспергирование чаще всего проводят в установках, работающих под повышенным статическим давлением. Их обычно изготовляют с вертикальным расположением рабочей ванны цилиндрической или конической формы (рис. 1.16), дно и стенки которой являются излучающими поверхностями ультразвуковых магнитострикционных преобразователей.
Наибольшее распространение имеют установки с ванной цилиндрической формы, выполненной из коррозионно-стойкой стали (например, установка марки УЗВД-6), дно которых является излучающей поверхностью. Для создания избыточного статического давления в установку подается газ (давление газа 0,5–0,6 МПа).
Порошки, получаемые ультразвуковым диспергированием в жидкости, не имеют существенных химических загрязнений. Их частицы отличаются высокой дисперсностью, отсутствием поверхностных неровностей и округлой формой, часто близкой к сферической.
Измельчениеваппаратахмагнитногоиндукционноговращателя
Измельчение материала в аппаратах магнитного индукционного вращателя (МИВ) происходит во вращающемся магнитном поле, в котором движется масса ферромагнитных размольных тел.
Диспергирование осуществляется главным образом самоизмельчением частиц обрабатываемого материала при их многократно повторяющихся соударениях со сдвигом. Строго дозированное импульсное давление на частицы с их одновременным сдвигом обеспечивает высокую эффективность аппаратов магнитного индукционного вращателя и практически исключает загрязнение измельчаемого материала посторонними примесями.
Принцип работы таких аппаратов состоит в том, что в емкость прямоугольного сечения из диамагнитного материала загружается обрабатываемый материал и цилиндрические размольные тела. Затем возбуждается вращающееся магнитное поле, вызывающее подскоки и вращение размольных тел вокруг собственного центра тяжести, что в результате приводит к измельчению обрабатываемого материала.
На эффективность их работы большое влияние оказывает скорость вращения размольных тел, которая лежит в пределах от 3 000 до 8 000 об/мин. Основным элементом аппарата МИВ является полая кольцевая рабочая камера, в которой с помощью вращающихся магнитов возбуждается магнитное
Процессы порошковой металлургии. Курс лекций |
-65- |
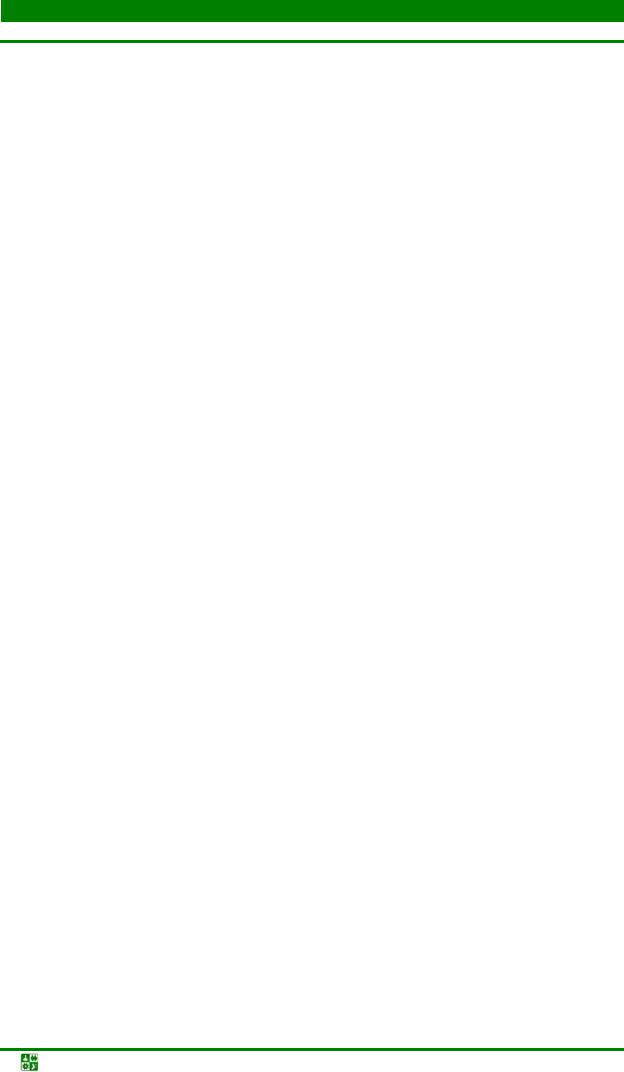
I. ПОЛУЧЕНИЕ ПОРОШКОВ
Лекция 8 Получение порошков ультразвуковым измельчением в жидких средах
поле. Оно воздействует на находящиеся в камере рабочие цилиндрические ферромагнитные тела таким образом, что они переворачиваются, ударяются о поверхность камеры и, подскочив на определенную высоту, в свободном полете вращаются вокруг собственного центра тяжести.
Для эффективного ведения процесса тонкого и сверхтонкого измельчения материалов требуются размольные тела малой толщины (например, диаметром 0,9 мм и длиной 11 мм), которые располагаются ближе друг к другу, что диктуется максимумом энергии системы.
Процесс самоизмельчения материала происходит в зазорах между вращающимися размольными телами, куда он втягивается под воздействием аэродинамического эффекта разрежения.
Экспериментально доказано, что чем больше масса размольных тел, тем интенсивнее идет измельчение. Вместе с тем при определенной ее критической величине аппарат МИВ перестает работать, что объясняется эффектом экранирования магнитного поля индукторов самими размольными телами и материалом. Установлено, что аппарат МИВ устойчиво работает при массе размольных тел, равной 80 % их критической массы. Критическую массу размольных тел определяют при холостой работе аппарата, т.е.без загрузки в него измельчаемого материала.
Контрольныевопросыизадания
1.Что такое кавитационные полости?
2.Какие процессы развиваются в жидкостях под действием ультразву-
ка?
3.Каковы оптимальные частоты ультразвукового разрушения материалов в водной среде?
4.Перечислите механизмы разрушения материалов под действием ультразвука.
5.Назовите основные свойства дисперсионных сред.
6.При каких температурах осуществляют ультразвуковое измельчение материалов в различных средах?
7.Перечислите основные факторы, определяющие измельчение материалов в аппаратах МИВ.
Процессы порошковой металлургии. Курс лекций |
-66- |
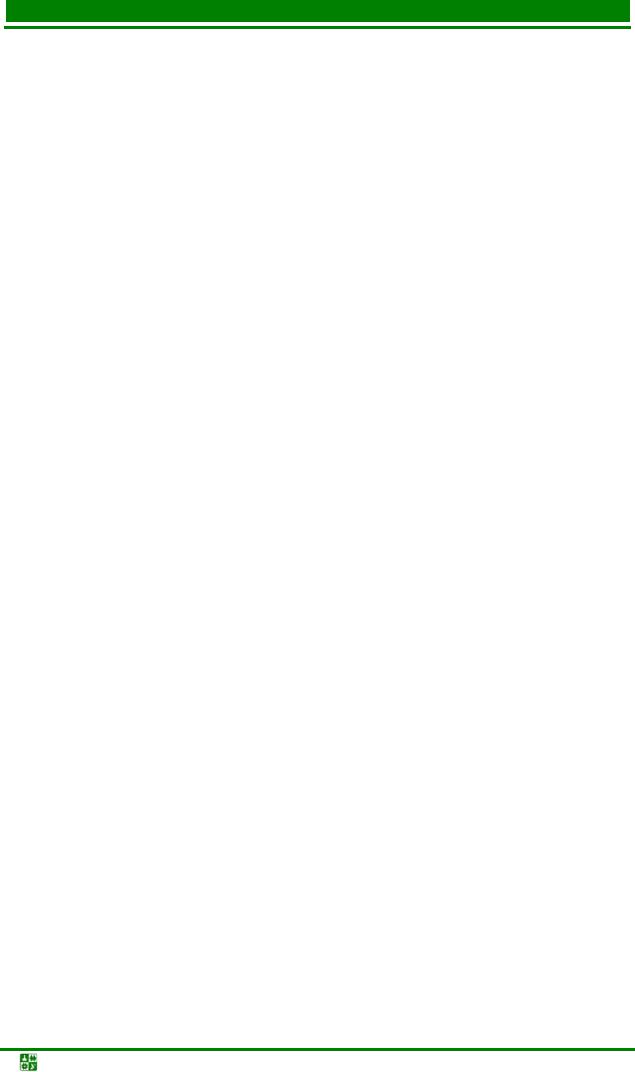
I. ПОЛУЧЕНИЕ ПОРОШКОВ
Лекция9 Диспергированиерасплавов
План лекции
1.Физико-химические и механические процессы при диспергировании расплавов.
2.Классификация методов диспергирования расплавов.
Физико-химическиеимеханическиепроцессы придиспергированиирасплавов
Диспергирование расплавленного металла или сплава струей сжатого газа, жидкости или механическим способом позволяет получать порошки, называемые распыленными. Процесс характеризуется высокой производительностью, технологичностью, степенью автоматизации и сравнительно малыми энергозатратами, экологической чистотой. Метод диспергирования расплава дает возможность также оперативно увеличить производство металлического порошка с контролируемыми свойствами при относительно низких затратах (в том числе капитальных) и использовать в качестве исходного материала отходы металлообрабатывающей промышленности.
Промышленное производство распыленных порошков началось в конце 1930-х гг., но до середины 1950–1960-х гг. оно оставалось малотоннажным. Однако уже в 1960-х гг. производство распыленных порошков стало активно развиваться в таких странах, как США, Канада, ФРГ, Англия, Японии и Швеция. С 1978 г. производство порошков диспергированием широко использовалось на предприятиях бывшего СССР. Мировой объем производства порошков диспергированием расплавов непрерывно возрастает. В настоящее время около 60–70 % всего объема порошков производится именно с помощью этого метода.
Метод распыления широко используют для получения не только порошков железа, сталей и сплавов на основе железа, но и порошков цветных металлов и сплавов (алюминия, меди, свинца, цинка, титана, вольфрама идр.).
Распыление весьма эффективно при производстве порошков многокомпонентных сплавов и обеспечивает получение порошков с аморфной структурой, которая позволяет достичь равномерного химического состава композиции, даже при содержании легирующих компонентов выше их предела растворимости в основном компоненте сплава. Кроме того, порошки, полученные с использованием методов диспергирования расплавов, имеют оптимальное строение и тонкую структуру каждой образующейся частицы. Это связано с кристаллизацией дисперсных капель расплава с высокими скоростями охлаждения (до нескольких десятков и даже сотен миллионов градусов в секунду).
Все металлические расплавы обладают близкой к нулю механической прочностью, относительно небольшой вязкостью и склонны к хрупкому раз-
Процессы порошковой металлургии. Курс лекций |
-67- |
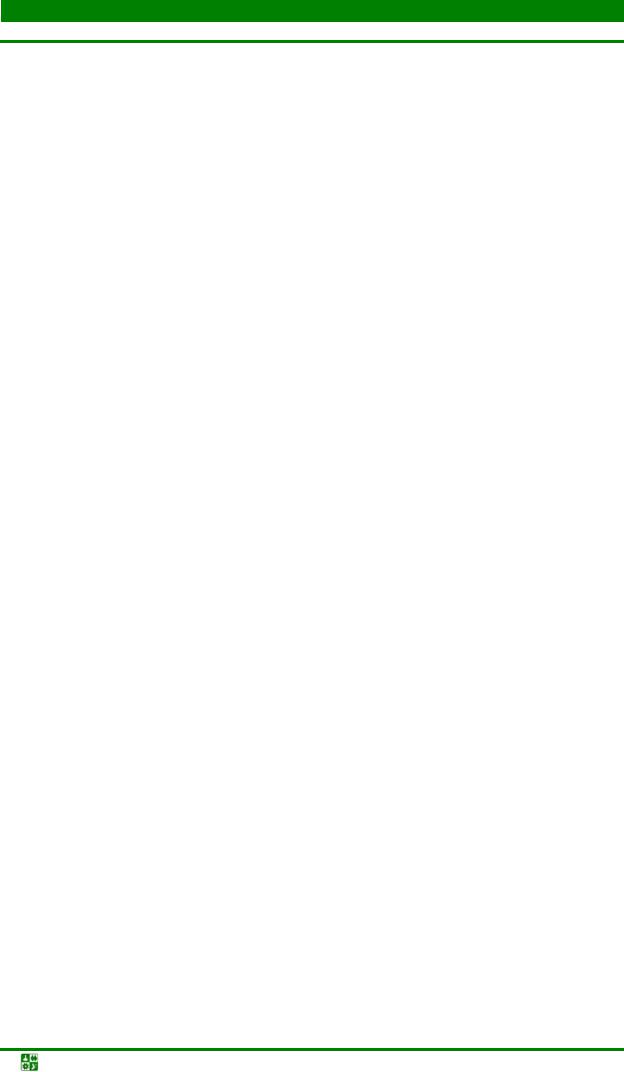
I. ПОЛУЧЕНИЕ ПОРОШКОВ
Лекция 9 Диспергирование расплавов
рушению при воздействии на их струю потока газа или жидкости. По современным представлениям плавление, разрушая кристаллическую решетку как жесткую систему колебаний атомов, нарушает межатомные связи дальнего порядка, но сохраняет ближний порядок, т.е. упорядоченность атомов, присущую соответствующей решетке.
Я.И. Френкель сформулировал положение, согласно которому с термодинамической точки зрения металлическую жидкость вблизи точки кристаллизации можно рассматривать как твердое, но сильно разрыхленное тело с множеством разрывов (дыр) между некоторыми соседними атомами при наличии связи со всеми остальными; дыры быстро залечиваются и появляются вновь.
Для процесса диспергирования наиболее важны вязкость, поверхностное натяжение и плотность расплава.
Вязкость или обратное ей свойство текучесть характеризует сопротивление жидкости сдвигу, объясняется наличием у нее свободного, т.е. дополнительного по отношению к твердому телу , объема и определяется главным образом прочностью межатомной связи и плотностью упаковки атомов. Для гомогенной жидкости она зависит от температуры, а для гетерогенной жидкости – еще и от формы, размеров и числа включений.
Поверхностное натяжение расплава характеризует работу образования физической поверхности раздела фаз, отнесенную к единице поверхности, и существенно влияет на процессы, сопровождающие диспергирование. Оно зависит от температуры расплава, уменьшаясь с ее повышением.
Плотность расплава линейно зависит от температуры нагрева, уменьшаясь с ее повышением из-за увеличения объема металлической жидкости и появления в ней новых «дырок».
Таким образом, на структуру, физические свойства и форму частиц распыленного порошка большое влияние должен оказывать перегрев распла-
ва над ликвидусом.
Истекающая из отверстия струя жидкости при отсутствии видимого внешнего воздействия как бы самопроизвольно разрушается. Происходит это вследствие неустойчивости ее движения при воздействии малых возмущений, создаваемых шероховатостью стенок канала и отклонением формы его выходного отверстия от идеальной, нестабильностью скорости истечения струи, а также неоднородностью трения на границе жидкость – окружающая среда.
Возникающая в струе расплава пульсация рождает волну с растущей амплитудой. Размер капли зависит от длины этой волны и соответствует ее оптимальной величине.
Внешнее воздействие на струю (обдув потоком газа или жидкости, электромагнитными волнами, мощными импульсами тока и пр.) интенсифицирует процесс ее разрушения и повышает дисперсность капель. При этом жидкость (массивный объем расплава) необходимо преобразовать в такую форму, которая бы обладала наибольшей поверхностной энергией (тонкая струя, пленка) и, соответственно, максимальной неустойчивостью.
Процессы порошковой металлургии. Курс лекций |
-68- |
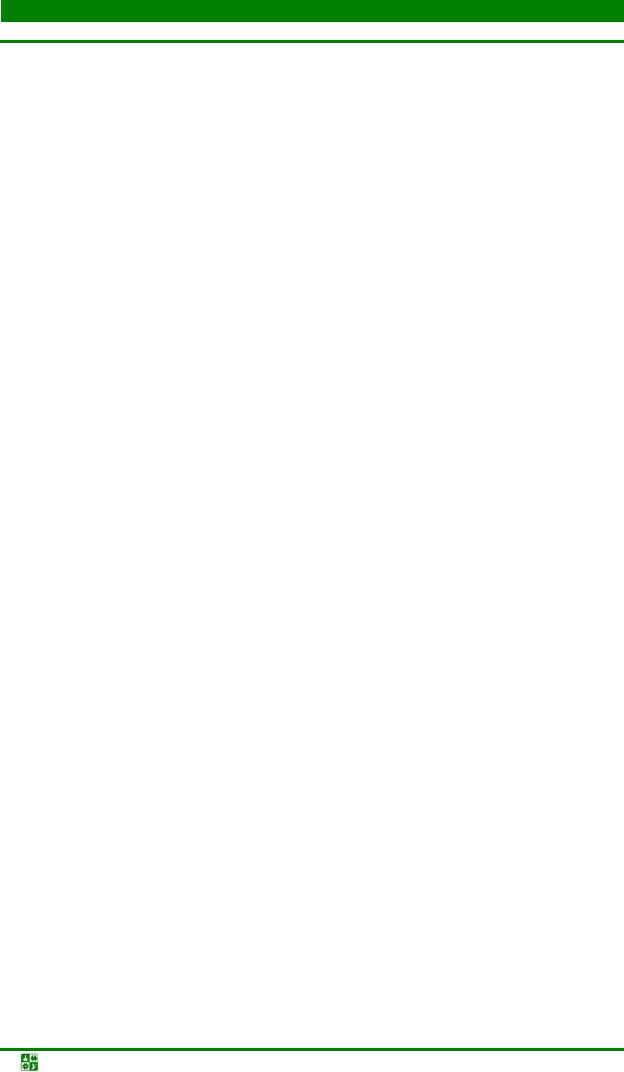
I. ПОЛУЧЕНИЕ ПОРОШКОВ
Лекция 9 Диспергирование расплавов
Более интенсивное и упорядоченное дробление струи жидкости с сечением любой формы обеспечивает наложение высокочастотных колебаний как на нее, так и на распыливающий газ-энергоноситель. Вторичное диспергирование образовавшихся первичных крупных капель при пневмоакустическом распылении (акустическая энергия подводится к струе или пленке расплава через газ) связано с воздействием на них ультразвуковых колебаний и ударных волн, генерируемых излучателем. Крупная капля по мере движения в направлении излучателя деформируется, затем останавливается, расплющивается, вытягиваясь в пленку в вертикальной плоскости, и дробится на более мелкие капли. Эти возникающие мелкие капли попадают в поток газа, где происходит их дальнейшее разрушение под воздействием его аэродинамического скоростного потока (как это осуществляется и при распылении сжатым газом, рассмотренном выше).
Эффективное диспергирование металлического расплава требует поддержания его высокой температуры (обеспечения перегрева) и сохранения в допустимых пределах значений основных физико-химических параметров на протяжении всего процесса распыления. Это существенно усложняет технологию, так как указанные выше физические параметры расплава значительно изменяются в ходе диспергирования, и, если расплав дополнительно не подогревать, процесс распыления может прекратиться.
Механизм диспергирования расплава водой высокого давления принципиально отличается от механизма распыления сжатым газом, так как жидкость имеет высокую плотность (примерно в 1 000 раз выше плотности воздуха), происходит образование пара в зоне непосредственного контакта воды с расплавом (меняются теплофизические характеристики процесса), наблюдается более интенсивное охлаждение образовавшихся капель-частиц.
Непосредственное воздействие на струю расплава и отдельные капличастицы из нее в зоне эффективного дробления оказывает сжатый перегретый пар, плотность которого существенно ниже плотности воды. При этом струя расплава дробится на капли, которые затем вторично диспергируются через окружающую их паровую оболочку (пленку).
При распылении струи металлической жидкости газовым потоком возникшие двухфазные системы газ–жидкость и газ–твердое образуют металлогазовый факел, представляющий собой непрерывно пульсирующую двухили трехфазную смесь жидких и твердых металлических частиц в газе. В нем происходит взаимодействие газового потока с расплавом, теплофизические характеристики и агрегатное состояние которого меняются (расплав и капли остывают, взаимодействуют с окружающей средой и пр.), и отдельных капель между собой. Эти процессы по существу определяют свойства получаемого порошка, прежде всего размер и форму его частиц.
Распад струи ньютоновской жидкости под действием газового потока можно описать с помощью следующей критериальной функции:
d/D = f (Wе, Lр, M, N),
Процессы порошковой металлургии. Курс лекций |
-69- |
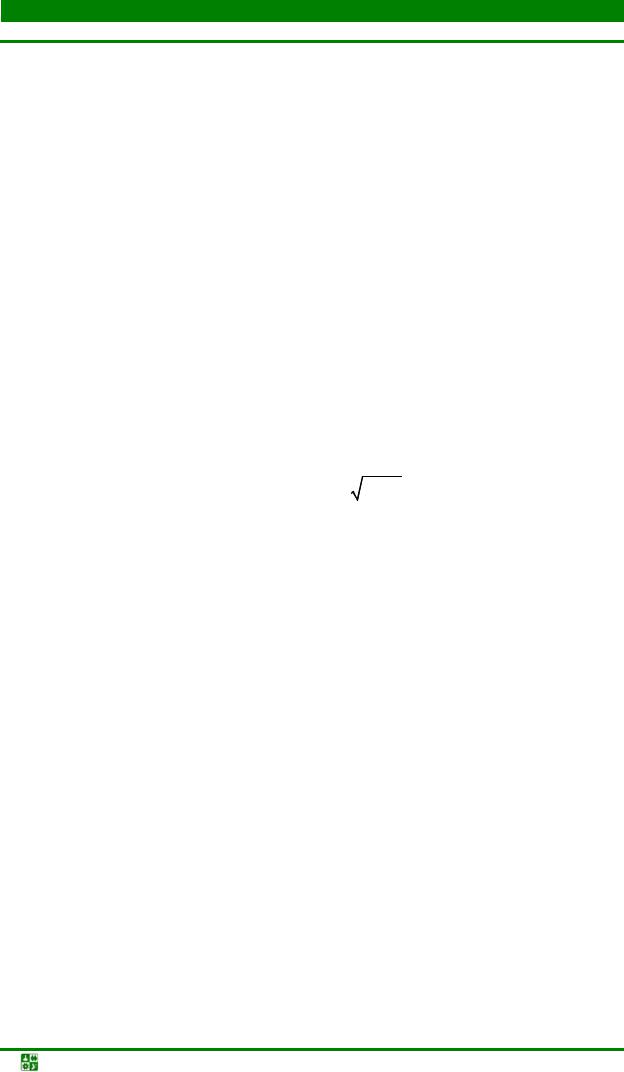
I. ПОЛУЧЕНИЕ ПОРОШКОВ
Лекция 9 Диспергирование расплавов
где d – средний диаметр частиц-капель; D – диаметр струи расплава; Wе – критерий Вебера (характеризует соотношение сил инерции и поверхностного натяжения); Lр – критерий Лапласа (характеризует соотношение сил вязкости и поверхностного натяжения); M, N – критерии, характеризующие соотношение плотности газа-энергоносителя и расплава, вязкости газаэнергоносителя и расплава.
Приведенные критерии можно определить, используя следующие отношения:
Wе = V2г γг D0 /σ; Lр = η2ж / (σ γж D0); |
(1.13) |
M = V2г γг / (γж V2ж); N = ηг / ηж, |
где Vг, Vж – скорости газового потока и расплава; γг, γж – плотности газа и расплава; ηг, ηж – вязкости газа и расплава; σ – поверхностная энергия; D0 – диаметр первоначальной пряди расплава.
Размер образующихся частиц порошка можно оценить по эмпирической формуле
d = (585/ΔV)(σж/γж)0,5 + 597 (ηж/ |
|
)0,45(1000Gж/Gг), |
(1.14) |
σжγж |
где V – относительная скорость газового потока; σж, γж, ηж, Gж – соответственно, поверхностная энергия, плотность, вязкость и удельный расход расплава; Gг – удельный расход газа-энергоносителя.
Существует физический предел диспергирования металлических жидкостей, в связи с чем повышение параметров процесса диспергирования (скорости и температуры газа или температуры расплава) не приводит к получению более дисперсных порошков. Установлено, что величина перегрева расплава и температура газа-энергоносителя влияют на фракционный состав порошка.
В первый момент образования любые капли (крупные первичные, средние и мелкие вторичные) жидкого металла имеют неправильную форму и под действием сил поверхностного натяжения стремятся к минимизации поверхности, т.е. принять сферическую форму. Однако стремление капель к сфероидизации может не реализоваться, если она быстро затвердеет. Поэтому, если время сфероидизации капли меньше времени ее затвердевания, то она успеет принять форму шара, если же это не так, то образуются твердые частицы неправильной формы.
Приближенная оценка времени сфероидизации может быть проведена с использованием следующей формулы:
τсф = 3πηж(R – r)/ σж, |
(1.15) |
Процессы порошковой металлургии. Курс лекций |
-70- |
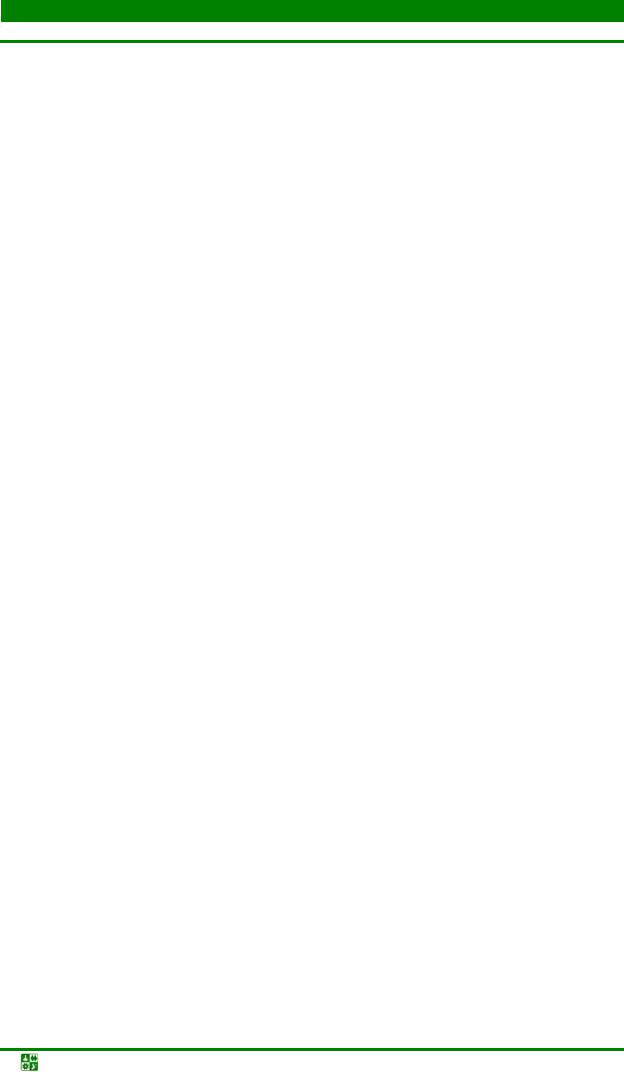
I. ПОЛУЧЕНИЕ ПОРОШКОВ
Лекция 9 Диспергирование расплавов
где R – радиус шара, образовавшегося из указанной пряди (цилиндра); r – радиус пряди, возникшей в первый момент диспергирования (если принять, что она имеет форму цилиндра с отношением длины к диаметру, равным 10).
Расчет по приведенной формуле дает заниженное значение τсф, так как не учитывает взаимодействие расплава с окружающей средой (например, окисление его поверхностного слоя) и некоторые другие факторы.
Время затвердевания τзатв жидкой капли диаметром d складывается из времени ее охлаждения до температуры затвердевания τохл и времени выде-
ления скрытой теплоты кристаллизации τкр. Приближенно его можно оценить по уравнению
τзатв = τохл + τкр = d (cжγж/6α) ln[(Tпов – Tг)/(Tпл – Tг)] + mL/gS , (1.16)
где cж – теплоемкость расплава; α – коэффициент теплоотдачи от расплава к энергоносителю; Tпов, Tпл, Tг – температуры, соответственно, поверхности расплава, плавления диспергируемого материала и энергоносителя; m, S – масса и поверхность образующейся капли; L – удельная теплота кристаллизации расплава; g – тепловой поток с поверхности капли.
Во многих случаях τохл = 0,01–0,1 с, τкр /τохл = 3,7. Скорость охлажде-
ния зависит от условий теплообмена капли расплава с окружающей средой и может составлять от 103 до 1010 °С/с.
При распылении расплава водой высокого давления размер частиц порошка зависит от ее скорости и удельного расхода. По эмпирической форму-
ле для стали средний диаметр капли dср, мкм, равен |
|
dср = (14900/Wв)(1/n)1/3 , |
(1.17) |
где Wв – скорость потока воды, м/с; n – число капель расплава, образующихся при ударе с каплей воды (n = 1, когда каждая капля воды вызывает образование одной капли расплава).
Критическую скорость потока воды можно оценить по выражению
Wвкp = 7,7σж0,75/dкр0,25. |
(1.18) |
Например, для получения частиц стали с максимальным диаметром dкр = 100 мкм значение Wвкp, ниже которого будут образовываться частицы большего размера, должно составлять 112 м/с (соответствующее давление воды 6,4 МПа).
Оценить τохл можно аналогично случаю распыления расплава газом, а τсф – по уравнению
Процессы порошковой металлургии. Курс лекций |
-71- |
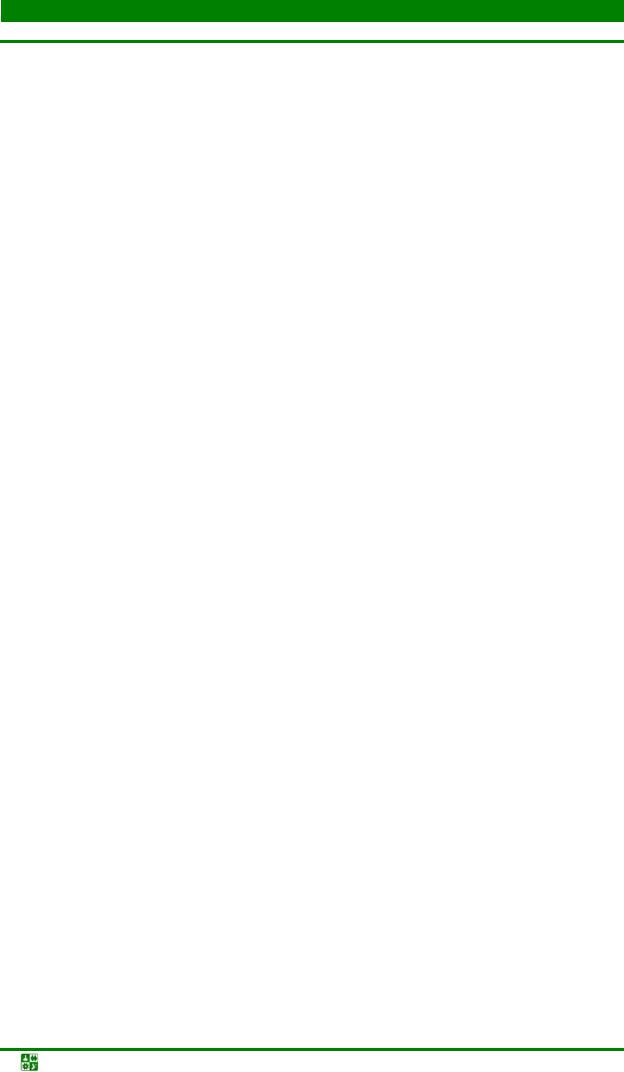
I. ПОЛУЧЕНИЕ ПОРОШКОВ
Лекция 9 Диспергирование расплавов
τсф = 0,75 π2ηжγв(R4 – r4)/υкσжγвозд, |
(1.19) |
где υк – объем капли расплава; γв, γвозд – плотности воды и воздуха соответственно.
Ориентировочно при температуре расплава выше 500 °С отношение
τохл /τсф > 1 и получают порошок со сферической формой частиц, а при температуре расплава ниже 400 °С это отношение меньше единицы и форма образующихся частиц неправильная.
На форму частиц порошка большое влияние оказывают скорость, удельный расход и угол атаки струи воды-энергоносителя, физические свойства расплава и другие факторы.
Распылении неизбежно связано с изменением состава расплава из-за взаимодействия металла с энергоносителем или охлаждающей средой. Для распыления наиболее важны процессы взаимодействия расплава с кислоро-
дом (окисление), азотом (азотирование) и водородом (наводораживание).
При взаимодействии расплава с кислородом образование первичных оксидных пленок происходит практически мгновенно. Структура такой пленки может быть как аморфной, так и кристаллической. Плотные тугоплавкие оксидные пленки существенно влияют на процесс формообразования частиц, подавляя действие сил поверхностного натяжения, определяющих процесс сфероидизации капли. В итоге это приводит к формированию частиц неправильной формы с рельефной развитой поверхностью.
Водород в зоне распыления может образовываться в результате диссоциации паров воды при высоких температурах. При снижении температуры растворенный водород выделяется из металла, являясь в ряде случаев причиной пористости распыленных порошков и изделий из них.
Азот попадает в расплав практически на всех этапах технологии. Он хорошо растворяется в железе, хроме, ванадии, марганце, молибдене, титане, цирконии и других металлах с образованием нитридов, что приводит к повышению твердости и снижению пластичности порошков, в связи с этим азот является нежелательной примесью. Медь, никель, серебро, золото, вольфрам не растворяют азот и не взаимодействуют с ним.
Для получения высококачественных, чистых по кислороду и азоту порошков жаропрочных сталей, титана, циркония и других металлов в технике в качестве технологических сред широко используют инертные газы (аргон, гелий) и вакуум.
Классификацияметодовдиспергированиярасплавов
Методы распыления металлического расплава различаются: по виду энергии, затрачиваемой на его создание (нагрев индукционный или косвенный, электродуговой, электронный, лазерный, плазменный и др.); виду силового воздействия на расплав при диспергировании (механическое воздействие, энергия газовых и водяных потоков, силы гравитационные, центробежные или магнитогидродинамические, воздействия ультразвука и т.д.); по типу среды, исполь-
Процессы порошковой металлургии. Курс лекций |
-72- |
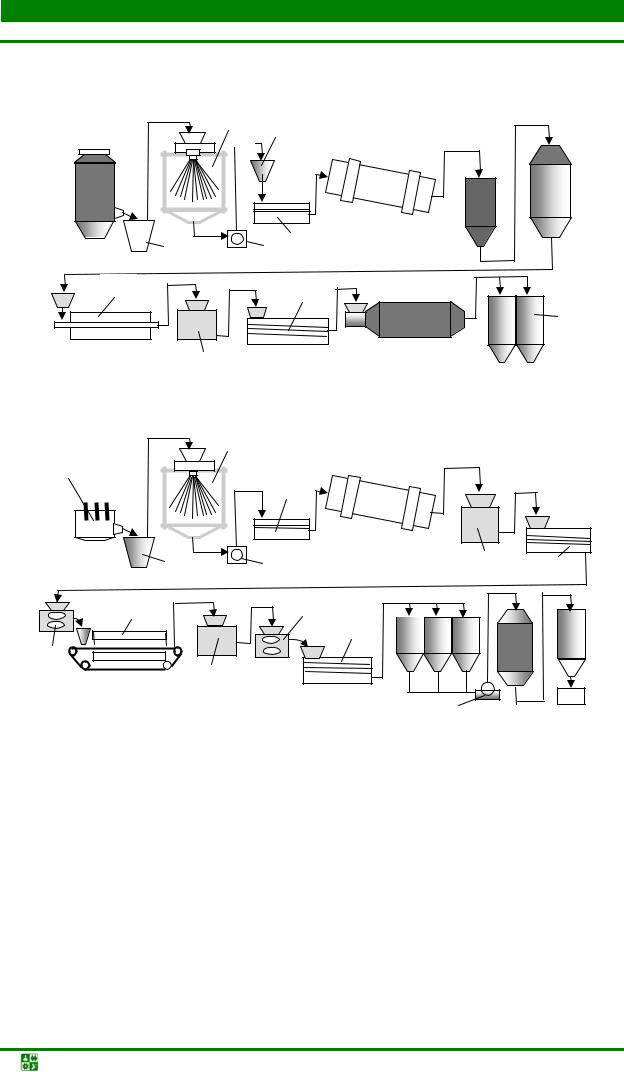
I. ПОЛУЧЕНИЕ ПОРОШКОВ
Лекция 9 Диспергирование расплавов
зуемой при создании и диспергировании расплава (восстановительная, окислительная, инертная или какая-либо иная среда заданного состава, вакуум).
|
|
3 |
|
5 |
|
|
|
|
|
|
|
|
|
1 |
|
|
|
7 |
8 |
9 |
|
|
|
|
|
|
|
2 |
|
|
4 |
6 |
|
|
|
|
|
|
|
||
10 |
|
|
|
12 |
|
|
|
|
|
|
13 |
|
14 |
|
11 |
|
|
а |
|
|
|
|
|
|
|
|
3
1 |
|
5 |
6 |
|
2 |
4 |
7 |
|
8 |
10 |
12 |
|
|
|
9 |
13 |
14 |
16 |
17 |
|
|
|
||
11 |
|
|
|
|
|
|
|
|
|
|
б |
15 |
|
|
Рис. 1.17. Типовые аппаратурно-технологические схемы получения порошков железа: а – распыление расплава воздухом в воду: 1 – печь; 2 – емкость для расплава металла; 3 – установка распыления; 4 – насос для перекачки пульпы порошка; 5 – гидроциклон; 6 – фильтр; 7 – вращающаяся сушильная печь; 8 – бункер для хранения высушенного порошка; 9 – двойной конусообразный смеситель; 10 – печь для восстановления порошка (печь с шагающим подом); 11 – молотковая мельница; 12 – классификатор; 13 – смеситель (для усреднения порошка); 14 – бункеры для хранения порошка перед упаковкой; б – распыление расплава водой в воду: 1 – печь; 2 – емкость для расплава металла; 3 – установка распыления; 4 – насос; 5 – гидроциклон; 6 – сушильная печь; 7 – мельница; 8, 13 – классификатор; 9, 12– магнитный сепаратор; 10– печь для восстановления порошка (конвейерная); 11 – молотковая мельница; 14– бункеры для хранения порошка;
15 – весы; 16 – смеситель; 17– бункер для хранения порошка перед упаковкой
Процессы порошковой металлургии. Курс лекций |
-73- |
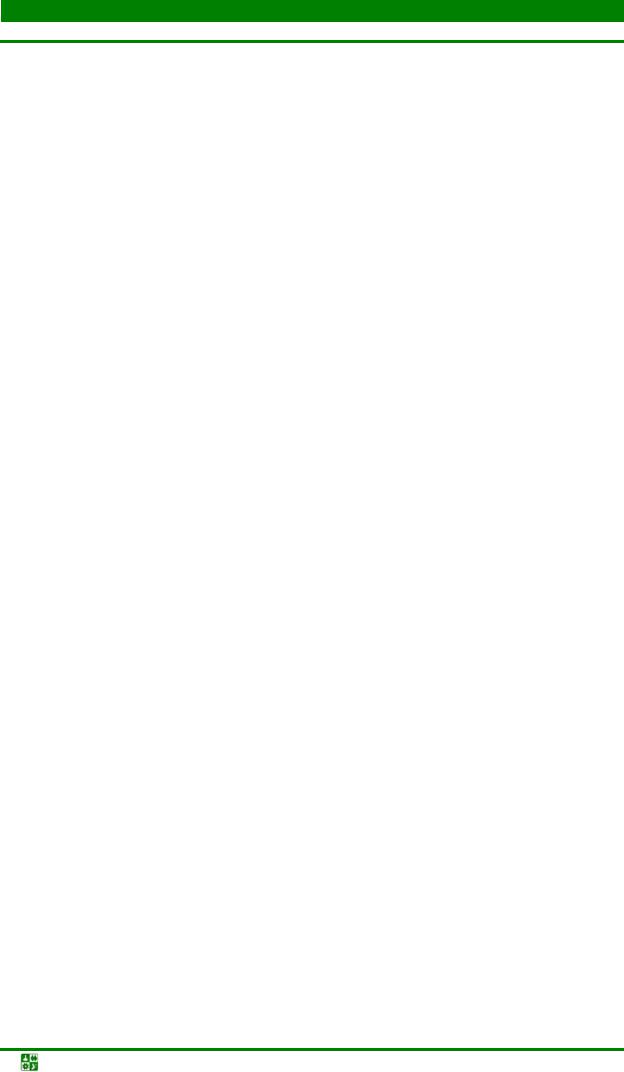
I. ПОЛУЧЕНИЕ ПОРОШКОВ
Лекция 9 Диспергирование расплавов
Типовая технологическая схема распыления расплавов газом (аргоном, азотом, воздухом) или жидкостью (чаще всего водой) включает сле-
дующие основные операции:
1)подготовка расплава;
2)транспортировка расплава к установке распыления и диспергирования расплава;
3)классификация частиц полученного порошка;
4)усреднение состава нескольких партий порошка;
5)упаковка порошка.
Взависимости от конкретной технологии диспергирования к перечисленным операциям могут добавляться следующие:
сушка (обезвоживание) порошка (в гидроциклонах, на фильтрах, во вращающихся печах, в сушильных шкафах и пр.),
дробление, магнитная сепарация, восстановление,
взвешивание и пр. (рис. 1.17).
Влюбом случае сущность получения металлических порошков из расплава заключается в нарушении сплошности его потока (струи или пленки) под действием различных источников возмущений с возникновением дисперсных частиц.
Все методы диспергирования расплавов условно можно разделить на пять групп: методы центробежного распыления; методы ультразвукового распыления; методы распыления расплава потоками энергоносителей; бесконтактные методы распыления; высокоскоростные методы распыления.
Контрольныевопросыизадания
1.Каков удельный объем порошков, получаемых методами диспергирования, в общем объеме всех производимых порошков?
2.Что представляет собой расплав?
3.Перечислите основные факторы, определяющие свойства порошков получаемых диспергированием.
4.Что может использоваться в качестве энергоносителя?
5.Существует ли предел диспергирования расплавов энергоносите-
лями?
6.От чего зависит скорость охлаждения расплава при диспергиро-
вании?
7.Перечислите основные технологические операции распыления расплавов энергоносителями.
8.Назовите основные группы методов диспергирования расплавов.
Процессы порошковой металлургии. Курс лекций |
-74- |
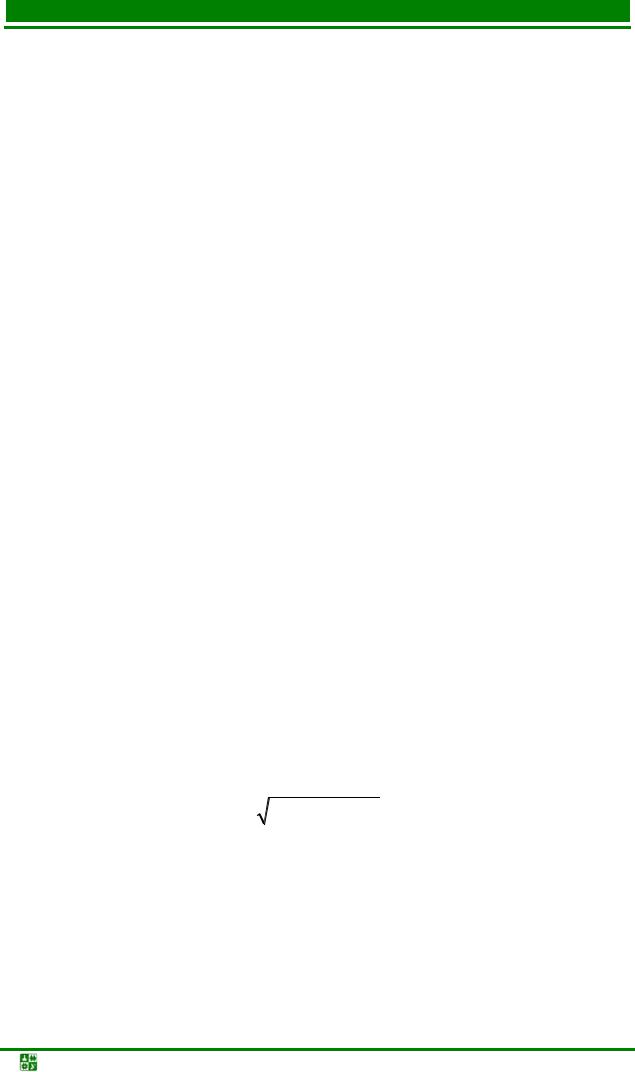
I. ПОЛУЧЕНИЕ ПОРОШКОВ
Лекция10 Методыдиспергированиярасплавов
План лекции
1.Методы центробежного распыления расплавов.
2.Методы ультразвукового распыления расплавов.
3.Методы диспергирования расплавов потоками энергоносителей.
4.Бесконтактные методы распыления расплавов.
5.Методы высокоскоростного охлаждения расплавов.
Методыцентробежногораспылениярасплавов
Центробежное распыление представляет собой один из основных видов диспергирования расплавов металлов, имеющих высокое сродство к кислороду. На практике используют три способа (рис. 1.18):
способ быстровращающегося электрода; способ вращающегося диск;
способ вращающегося перфорированного стакана.
По способу вращающегося электрода (рис. 1.18, а) распыление расплава проводят с торца расходуемой быстровращающейся (со скоростью 2 000–20 000 об/мин) заготовки цилиндрической формы. Образование на торце заготовки тонкой пленки расплавленного металла (10–30 мкм) происходит за счет действия на нее электрической дуги, потока плазмы или мощного электронно-лучевого зонда.
При других схемах диспергирования (рис. 1.18, б) плавление металла проводят автономно, вне зоны распыления. Струю расплава подают на вращающийся со скоростью до 24 000 об/мин диск, на его вогнутой поверхности образуется пленка жидкого металла, от которой затем отрываются капличастицы размером < 100 мкм. Кристаллизация капель происходит в атмосфере инертного газа. Скорость кристаллизации – 105–10 6 °С/с.
Толщина пленки расплава на торце вращающегося электрода определяется по выражению
δ = 2 |
3 |
′ |
2 |
2 |
2 |
|
(1.20) |
|
Gжηж / ω |
Dс |
γж , |
где Gж – удельный расход жидкости; ω, Dс – угловая скорость вращения и диаметр электрода; ήж, γж – вязкость и плотность расплава соответственно.
При выдавливании расплава из отверстий в стенке контейнера, вращающегося со скоростью 1 000–5 000 об/мин, капли-частицы формируются в момент их отрыва от внешней поверхности стенки контейнера.
Процессы порошковой металлургии. Курс лекций |
-75- |
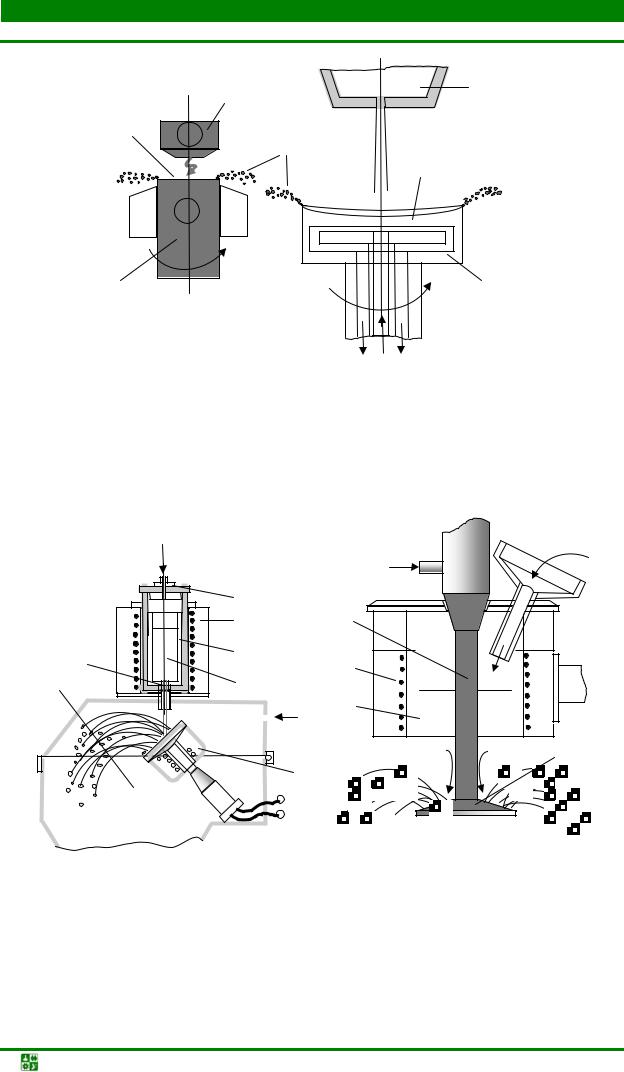
I. ПОЛУЧЕНИЕ ПОРОШКОВ
Лекция 10 Методы диспергирования расплавов
1 |
3 |
|
3 |
А |
Капли - частицы |
|
|
2 |
|
К |
|
2 |
|
1 |
|
|
Вода |
|
а |
б |
Рис. 1.18. Схемы установок для центробежного распыления расплавов металлов: а – способ вращающегося электрода: 1– противоэлектрод; 2 – быстровращающийся электрод; 3 – пленка расплавленного металла; б – способ вращающегося диска: 1 – водоохлаждаемый диск; 2 – пленка металла; 3 – тигель с расплавом металла
|
|
Газ |
|
|
1 |
|
|
2 |
|
5 |
3 |
|
4 |
|
8 |
|
|
|
|
Газ
6
7
а
Расплав
металла
Вода
1
2
3
4
б
Рис. 1.19. Схемы ультразвукового диспергирования расплавов металлов: а – установка с вынесенным излучателем: 1 – система подачи газа; 2 – печь; 3 – графитовый стакан; 4 – расплав металла; 5 – твердосплавное сопло; 6 – излучатель ультразвуковых колебаний; 7 – нагреватель излучателя; 8 – камера распыления; б – установка с излучателем, проходящим через емкость с расплавом: 1 – концентратор колебаний;
2 – нагревательное устройство; 3 – контейнер с расплавом; 4 – излучатель
Процессы порошковой металлургии. Курс лекций |
-76- |
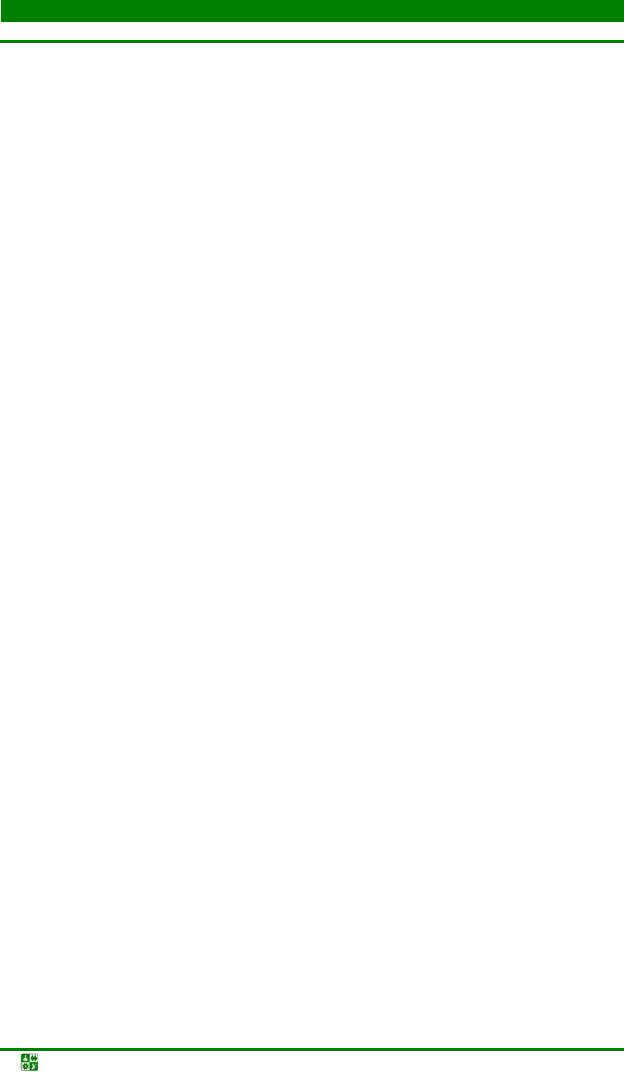
I. ПОЛУЧЕНИЕ ПОРОШКОВ
Лекция 10 Методы диспергирования расплавов
Методыультразвуковогораспылениярасплавов
Ультразвуковой метод распыления расплавов (рис. 1.19) применяют при диспергировании легкоплавких металлов и сплавов (Тпл< 1 000 °С). По одному из вариантов (рис. 1.19, а) струя или капля расплава подается на обогреваемую поверхность излучателя, растекается по ней в виде пленки (толщина пленки порядка 2–3 мм) и разрушается с образованием капельчастиц размером в несколько десятков микрометров (преимущественно 40–60 мкм). Рабочая частота ультразвуковых колебаний установки распыления – 18–22 кГц, амплитуды колебаний – 10–30 мкм.
По другой схеме (рис. 1.19, б) распыление тонкой пленки расплава происходит с внешней поверхности конической части ультразвуковой насадки, проходящей через емкость с расплавленным металлом. Как в первом, так и во втором случаях, распыление расплава осуществляется в закрытой камере, наполненной защитным газом (образующиеся капли-частицы охлаждаются струей инертного газа).
Методыдиспергированиярасплавовпотокамиэнергоносителей
Методы диспергирования расплава потоком энергоносителя широко применяют для производства больших объемов различных порошков.
На практике при использовании газа используют три основные схемы подачи (направления на расплав) энергоносителя:
поток газа обтекает струю расплава соосно; поток газа направлен к струе расплава под некоторым углом (наибо-
лее распространено распыление с углом атаки от 20 до 60°); поток газа направлен к струе расплава под прямым углом.
Для распыления свободно истекающей струи металла или сплава с точкой ликвидуса до 1 600 °С используют схему с вертикальным расположением форсуночного устройства (рис. 1.20, а). Подобная схема обеспечивает высокую производительность процесса. Кроме того, эта схема позволяет применять различные энергоносители (воздух, азот, аргон, гелий, углекислый газ). В некоторых случаях газообразные энергоносители специально подогреваются.
Легкоплавкие металлы (с ликвидусом до 800 °С) могут распыляться путем подачи энергоносителя через горизонтальные, расположенные друг напротив друга трубы (рис. 1.20, б), с множеством отверстий для выхода газа. Расплав металла подается в зону распыления сразу из нескольких последовательно расположенных металлоприемников.
Процессы порошковой металлургии. Курс лекций |
-77- |
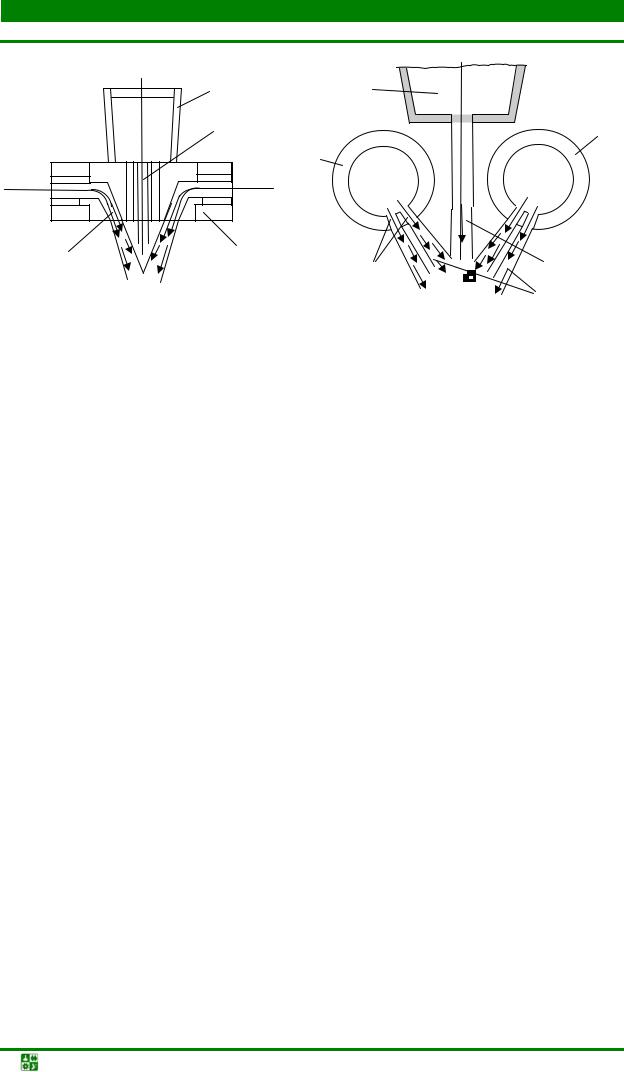
|
|
I. ПОЛУЧЕНИЕ ПОРОШКОВ |
|
|
|
|
Лекция 10 Методы диспергирования расплавов |
|
|
|
|
1 |
1 |
|
|
|
2 |
2 |
2 |
Газ |
|
Газ |
Газ |
|
|
Газ |
|||
|
4 |
3 |
3 |
4 |
|
|
|||
|
|
|
||
|
|
|
|
5 |
|
|
а |
б |
|
|
|
|
|
|
Рис. 1.20. Схемы распыления расплава воздействием струи газа: а – схема с вертикаль- |
||||
ным расположением форсуночного устройства: 1 – металлоприемник; 2 – струя рас- |
||||
плава; 3 – форсуночное устройство; 4 – кольцевое сопло Лаваля; б – схема много- |
||||
струйного форсуночного элемента трубчатого типа: 1 – металлоприемник; 2 – трубо- |
||||
проводы; 3 – отверстия для выхода газа; 4 – струя расплава; 5 – струи газа |
|
Ограниченное распространение имеет схема с горизонтальным расположением форсуночного устройства инжекционного типа. Подобная схема предусматривает подачу расплава непосредственно из плавильного пространства печи под давлением газа. Подобную схему в основном применяют для получения порошков алюминия, свинца, олова, цинка и некоторых припоев.
В последние десятилетия в качестве энергоносителя все более активно используют воду. Скорость водных потоков, направляемых на расплав, достигает 100–150 м/с при давлении до 15–25 МПа. Высокая скорость воды в зависимости от конструкции форсунки сохраняется на расстоянии до 500 мм, что позволяет подобрать наиболее эффективную схему распыления расплава. Струи воды могут направляться на расплав с одной или нескольких сторон. На практике применяются схемы, в которых диспергирование расплавов осуществляется коаксиальными потоками энергоносителя под углом от 5–15 до 60–70°. В большинстве случаев для распыления металлов используют сопловые, кольцевые-щелевые или плоскощелевые форсунки.
При контакте воды с расплавом, нагретым выше 100 °С, происходит интенсивное парообразование. Это существенно изменяет теплофизические характеристики процесса, так как плотность пара существенно меньше плотности воды и паровая оболочка хуже отводит тепло, чем вода. Однако скорость охлаждения образующихся капель-частиц лежит не ниже 104–107 °С/с.
Процессы порошковой металлургии. Курс лекций |
-78- |
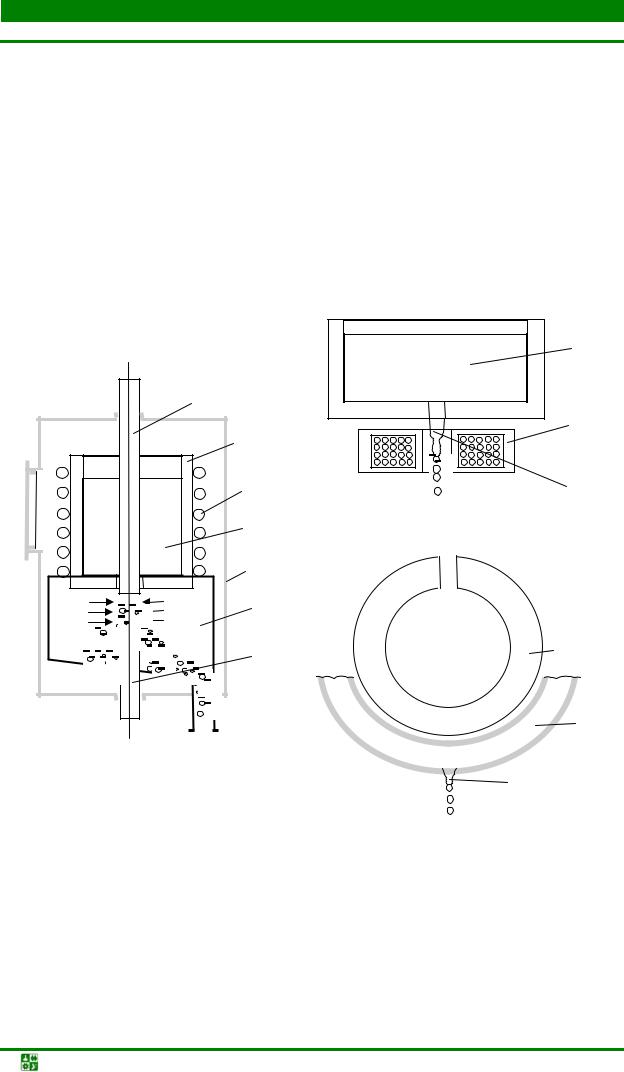
I. ПОЛУЧЕНИЕ ПОРОШКОВ
Лекция 10 Методы диспергирования расплавов
Бесконтактныеметодыраспылениярасплавов
Бесконтактные методы диспергирования расплава основаны на использовании мощных импульсов электрического тока, пропускаемых через твердый или жидкий металлический проводник, а также электромагнитных полей. Если пропустить разряд тока большой величины через тонкую металлическую проволоку, то она практически мгновенно испарится с образованием атомарного пара металла, конденсация которого приведет к формированию отдельных частиц порошка. Размеры частиц будут зависть от величины токового импульса, диаметра проволоки, атмосферы, в которой произошло распыление.
|
1 |
2 |
|
1 |
2 |
|
|
3 |
3 |
|
|
4 |
б |
5 |
|
6 |
|
2 |
2 |
|
1 |
|
3 |
а в
Рис. 1.21. Схемы бесконтактных методов распыления расплава: а – пропускание тока по струе расплава: 1 – тигель; 2 – электроды; 3 – индуктор; 4 – расплав; 5 – камера; 6 – сборник порошка; б, в – при наложении электромагнитного поля (б – на струю, в
– на расплав): 1 – металлоприемник; 2 – электромагнитная катушка; 3 – струя раслава
Если ток проходит по жидкому проводнику (рис. 1.21, а), то возникает магнитное давление, направленное по радиусу к центру струи расплава, приводящее к ее распаду на капли-частицы размером 10–500 мкм. При диспер-
Процессы порошковой металлургии. Курс лекций |
-79- |
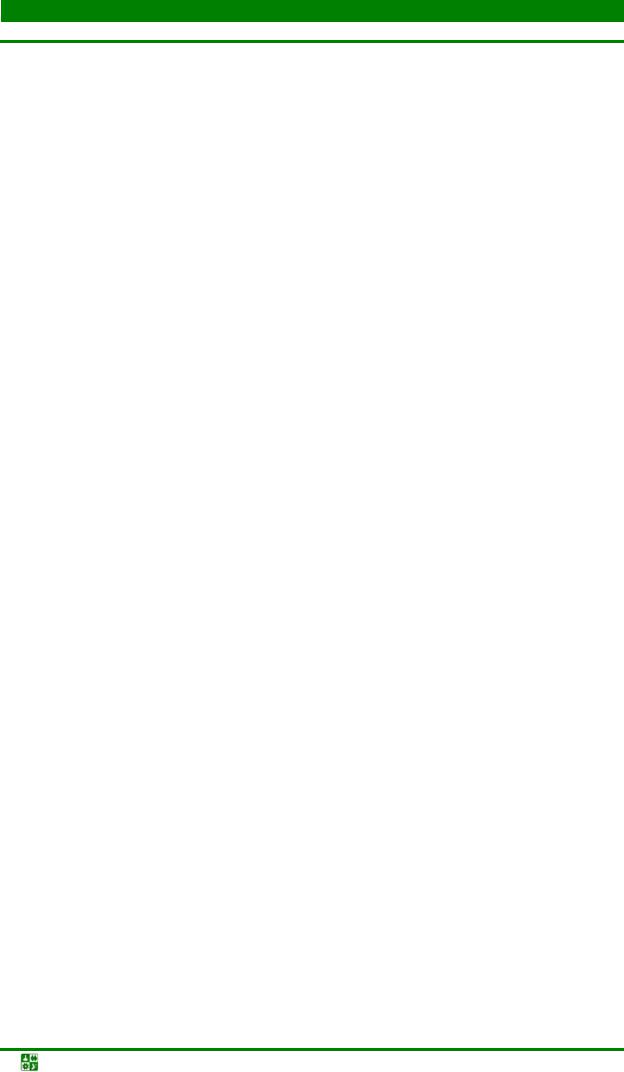
I. ПОЛУЧЕНИЕ ПОРОШКОВ
Лекция 10 Методы диспергирования расплавов
гировании жидкого металла с помощью электромагнитного поля силы, которые инициируются в индукционной катушке, действуют либо на струю, сжимая и разрушая ее (рис. 1.21, б), либо непосредственно на расплав, выдавливая его по каплям из отверстия в канале (рис. 1.21, в).
Методывысокоскоростногоохлаждениярасплавов
В настоящее время активно развиваются методы распыления расплавов, обеспечивающие возможность получения порошков с аморфной структурой. Затвердевание металлического расплава со скоростью больше 106 °С/с связано с излучательной потерей энергии или конвекцией тепла. Передача тепла путем непосредственного контакта капли расплава с теплопроводящей поверхностью позволяет достичь скоростей порядка 1010 °С/с.
Один из применяемых на практике методов высокоскоростной закалки позволяет обеспечить быстрое (107–108 °С/с) затвердевание жидкой капли расплава за счет ее попадания на водоохлаждаемый экран, который устанавливается под углом от 15 до 45° к направлению ее движения.
При ударе об экран капля расплава перемещается по его поверхности и кристаллизуется в виде частицы пластинчатой формы. Этим методом получают так называемые РИБЗ-порошки (распыленные и быстрозакаленные). Распыление расплава (чаще всего) производят с использованием перфорированного быстровращающегося тигля.
Разновидностью этого метода является способ высокоскоростной закалки (ВСЗ), при котором капли расплава, выдуваемого аргоном из отверстия в графитовом тигле, попадают на медный кристаллизатор, вращающийся со скоростью до 104 об/мин. Встречная скорость движения капли, выдуваемой из отверстия в дне графитового тигля аргоном, с поверхностью кристаллизатора составляет около 500 м/с. Распыление расплава ведут в вакууме или в атмосфере инертного газа.
Высокоскоростное затвердевание капель жидкого металла может обеспечиваться при извлечении небольших объемов материала кромкой быстровращающегося в вертикальной плоскости, погруженного в контейнер с расплавом диска. Скорость вращения диска – 2 000–5 000 об/мин. Скорость охлаждения металла на различных этапах процесса диспергирования составляет от 103 до 108 °С/с. Придавая рабочей поверхности диска (кромке) различный рельеф рисунка, можно извлекать из расплава частицы различной формы (чешуйчатой, игольчатой, волокнистой).
Контрольныевопросыизадания
1.Назовите способы центробежного распыления расплавов.
2.Какие факторы определяют размер частиц порошка, полученного методом центробежного распыления расплавов?
Процессы порошковой металлургии. Курс лекций |
-80- |
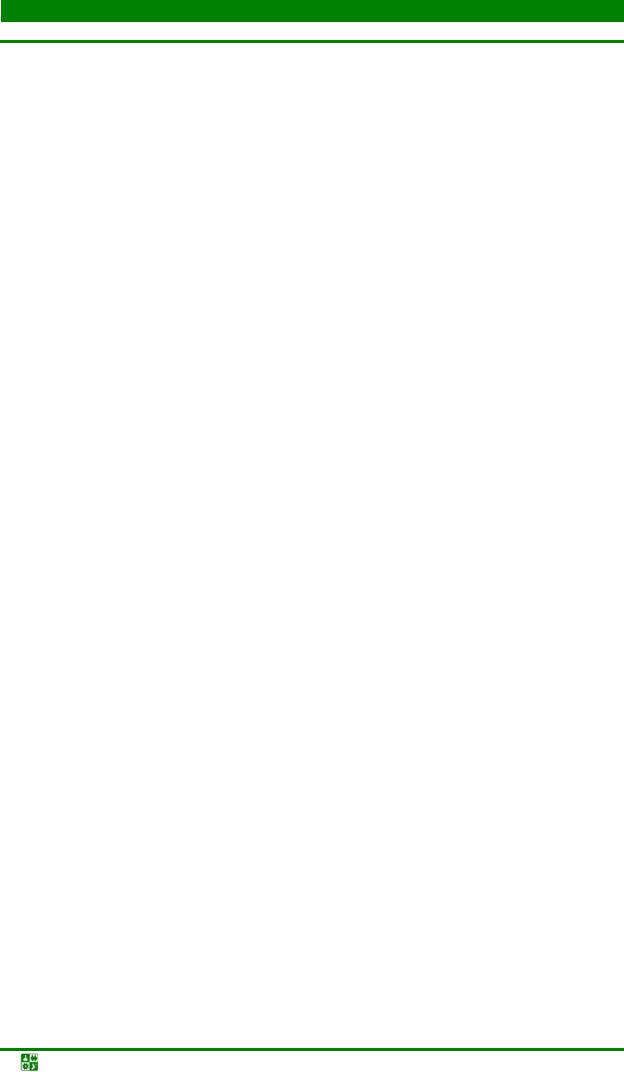
I. ПОЛУЧЕНИЕ ПОРОШКОВ
Лекция 10 Методы диспергирования расплавов
3.Назовите способы ультразвукового распыления расплавов.
4.Какое оборудование используют при распылении расплавов энергоносителями?
5.Назовите схемы распыления металлических расплавов энергоноси-
телями.
6.В чем особенность распыления расплавов водой?
7.Перечислите основные способы бесконтактного метода получения порошков.
8.Какие скорости кристаллизации частиц расплава наблюдаются при распылении расплавов водой и газами?
9.Что такое РИБЗ-порошки?
10.В чем особенность метода ВСЗ?
Лекция11 Восстановлениехимическихсоединенийметаллов.
Получениепорошковжелезавосстановлением оксидовуглеродом
План лекции
1.Общие закономерности процессов восстановления.
2.Металлотермическое восстановление.
3.Кинетика процесса восстановления.
4.Механизм восстановления химических соединений металлов.
5.Получение порошков железа и его сплавов восстановлением оксидов углеродом.
6.Основные технологические варианты получения порошков железа с использованием в качестве восстановителя углерода.
Общиезакономерностипроцессоввосстановления
Под восстановлением в порошковой металлургии понимают процесс получения металла из его химического соединения путем отнятия неметаллической составляющей (кислорода, солевого остатка и др.) при помощи ка- кого-либо вещества, называемого восстановителем.
Всякий процесс восстановления одновременно является и процессом окисления: когда исходное химическое соединение металла теряет неметаллическую составляющую (восстанавливается), восстановитель вступает с ней во взаимодействие (окисляется).
В общем случае простейшую реакцию восстановления можно представить как
МеА + X ↔ Ме + ХА ± Q,
Процессы порошковой металлургии. Курс лекций |
-81- |

I. ПОЛУЧЕНИЕ ПОРОШКОВ
Лекция 11 Восстановление химических соединений металлов. Получение порошков железа восстановлением оксидов углеродом
где Ме – металл, порошок которого хотят получить; А – неметаллическая составляющая (кислород, хлор, фтор, солевой остаток и др.) восстанавливаемого соединения МеА; X – восстановитель; Q – тепловой эффект реакции.
В ходе реакции возможно одновременное существование соединений восстанавливаемого металла МеА и восстановителя ХА, а также повторное образование соединения МеА в результате взаимодействия полученного металла Ме с образовавшимся соединением ХА.
Восстановитель – это вещество, которое при заданной температуре процесса обладает большим химическим сродством к неметаллической составляющей восстанавливаемого соединения, чем металл, входящий в это соединение.
Для оценки возможности протекания реакции восстановления сравнивают величины, характеризующие прочность химических связей в соединениях МеА и ХА. Количественной мерой этих величин (принято говорить «мерой химического сродства») служит величина свободной энергии Гиббса
∆Q0T, высвобождающейся при образовании соответствующего химического соединения: чем больше высвобождается энергии, тем прочнее химическое соединение. Поэтому реакция восстановления пойдет слева направо, т.е. в сторону восстановления МеА, если при образовании соединения восстановителя ХА выделяется энергии больше, чем при образовании соединения МеА по реакции Ме + А = МеА.
Впростейшем виде для стандартных условий (компоненты находятся
вчистом виде, давление газа в реакционном пространстве равно атмосфер-
ному) выражение для ∆Q0T реакции имеет вид
∆Q0T = ∆Q0XA – ∆Q0MeA = –R·T·lnKр, |
(1.21) |
где ∆Q0XA, ∆Q0MeA – стандартные свободные энергии образования соединений ХА и МеА при температуре Т; R – газовая постоянная; Т – температура проведения процесса восстановления; Kр – константа равновесия реакции.
В ряде случаев реакция восстановления сопровождается образованием промежуточных соединений. Если их не учитывать, то при сопоставлении
величин ∆Q0XA и ∆Q0MeA можно прийти к неправильному выводу о возможном результате реакции восстановления.
Когда реакция идет с участием газообразных веществ, для ее развития в нужном направлении наряду с температурой важно отношение их парциальных давлений.
Если число участвующих в реакции молекул газа-восстановителя не равно числу молекул газа-продукта реакции, константа равновесия реакции изменяется не только с изменением температуры, но и с изменением общего давления в системе (повышение давления сдвигает реакцию в сторону уменьшения общего объема газообразных реагентов). В тех случаях, когда
Процессы порошковой металлургии. Курс лекций |
-82- |
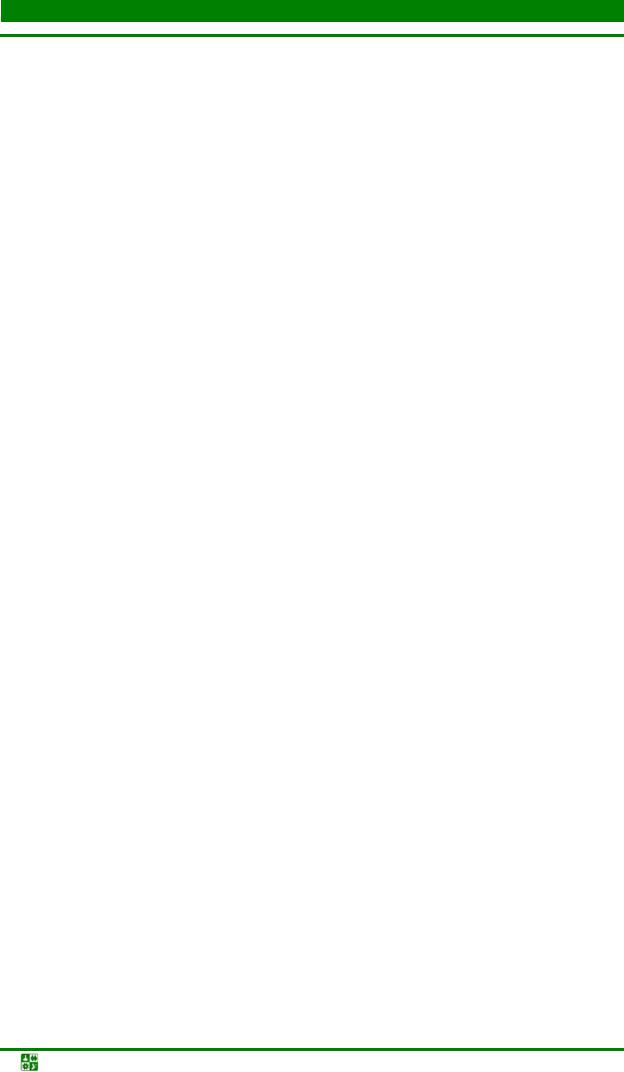
I. ПОЛУЧЕНИЕ ПОРОШКОВ
Лекция 11 Восстановление химических соединений металлов. Получение порошков железа восстановлением оксидов углеродом
исходные (твердые) или образующиеся (твердые или жидкие) конденсированные фазы имеют переменный состав с определенной областью гомогенности (например, твердые растворы), условия равновесия при данных температуре и давлении определяются не только парциальными давлениями газообразных веществ, но и изменяющимся составом конденсированной фазы.
Металлотермическоевосстановление
При восстановлении металлами (металлотермия) реакция восстановления принимает вид
МеА + Ме' – Ме + Ме'А ± Q, |
(1.22) |
где Ме' – металл-восстановитель. Для ее протекания слева направо необходим положительный тепловой эффект, т.е. разность теплот образования Ме'А и МеА должна быть существенной.
Количество тепла, приходящееся на единицу массы исходной шихты,
называют термичностью процесса:
q = Q/(MMeA + AMe), |
(1.23) |
где MMeA – молекулярная масса восстанавливаемого соединения МеА; AMe – атомная масса металла-восстановителя Ме'.
При стехиометрическом соотношении компонентов, участвующих в реакции, термичность процесса максимальна, как при избытке любого из них она снижается вследствие нерационального расхода тепла на нагрев и расплавление избытка вещества, не участвующего в реакции; при наличии в шихте каких-либо дополнительных компонентов величина q, как правило, уменьшается.
Величина минимальной термичности, необходимой для эффективного протекания процесса восстановления, зависит от ряда факторов: размера частиц реагирующих компонентов, степени окисления металла-восстановителя, качества смешивания шихты, относительной поверхности теплоотдачи реагирующих компонентов и др.
Для многих процессов металлотермического восстановления оксидов термичность составляет 2,5–2,9 кДж/г суммарной массы реагирующего материала и шлакообразующих присадок, что достаточно для протекания начавшегося процесса восстановления без подвода тепла извне.
В некоторых случаях тепловой эффект реакции настолько велик и она идет так бурно, что может произойти выброс шихты из реактора, если он не герметичен, или разрушение реактора, если он герметичен. Для регулирова-
Процессы порошковой металлургии. Курс лекций |
-83- |
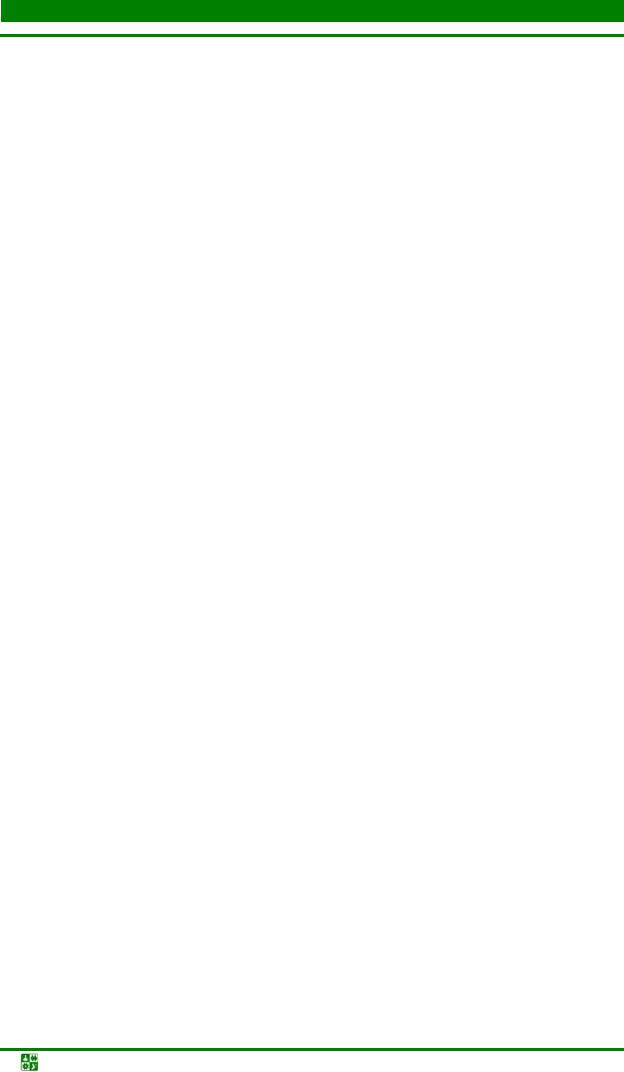
I. ПОЛУЧЕНИЕ ПОРОШКОВ
Лекция 11 Восстановление химических соединений металлов. Получение порошков железа восстановлением оксидов углеродом
ния реакции в исходную шихту могут добавлять флюсы, которые поглощают часть тепла и замедляют восстановление вследствие разубоживания шихты. Иногда флюсы добавляют с целью получения легкоплавкого шлака, защищающего образующийся металл от окисления при высоких температурах, или для частичного или полного растворения в легкоплавком флюсе возникающих тугоплавких соединений металла-восстановителя (например, СаО), препятствующих образованию крупных частиц порошка восстанавливаемого металла. Это особенно важно в тех случаях, когда мелкие частицы получаемого металла могут заметно окисляться при последующей отмывке порошка от побочных продуктов восстановления водой или водными растворами кислот.
В случаях, когда удельного теплового эффекта реакции недостаточно для ее самоподдержания, в шихту вводят подогревающие добавки, представляющие собой комбинацию активных окислителей с металлами. В качестве таких окислителей используют нитраты бария, калия или натрия, перекиси бария и натрия, сульфаты кальция и натрия, перхлорат калия и некоторые другие соединения.
Кинетикапроцессавосстановления
Наряду с термодинамикой для любого процесса восстановления большое значение имеет скорость протекания реакции (кинетика процесса), характеризующаяся количеством вещества, прореагировавшего в единицу времени.
В каждый момент времени в реакции участвуют не все имеющиеся в системе атомы или молекулы, а только те из них, энергия которых достаточна для преодоления энергетического барьера при переходе от МеА к Ме (или, что то же самое, от -Х к ХА, или от Ме' к Ме'А). В соответствии с этим ск о- рость химического взаимодействия пропорциональна числу атомов или молекул, обладающих требуемой активностью. Энергия, необходимая реагирующим атомам или молекулам для достижения соответствующей активности, называется энергией активации. Для практического применения нужны быстро протекающие процессы. Существенное влияние на кинетику процесса восстановления оказывают поверхностные явления в связи со значительной удельной поверхностью исходных веществ, твердых восстановителей и образующихся металлических порошков: адсорбция, хемосорбция, химическое взаимодействие в адсорбированных слоях, каталитическое действие развитых и контактных поверхностей, десорбция газообразных продуктов реакции, диффузионные процессы и т.д.
Механизмвосстановленияхимическихсоединенийметаллов
Процессы порошковой металлургии. Курс лекций |
-84- |
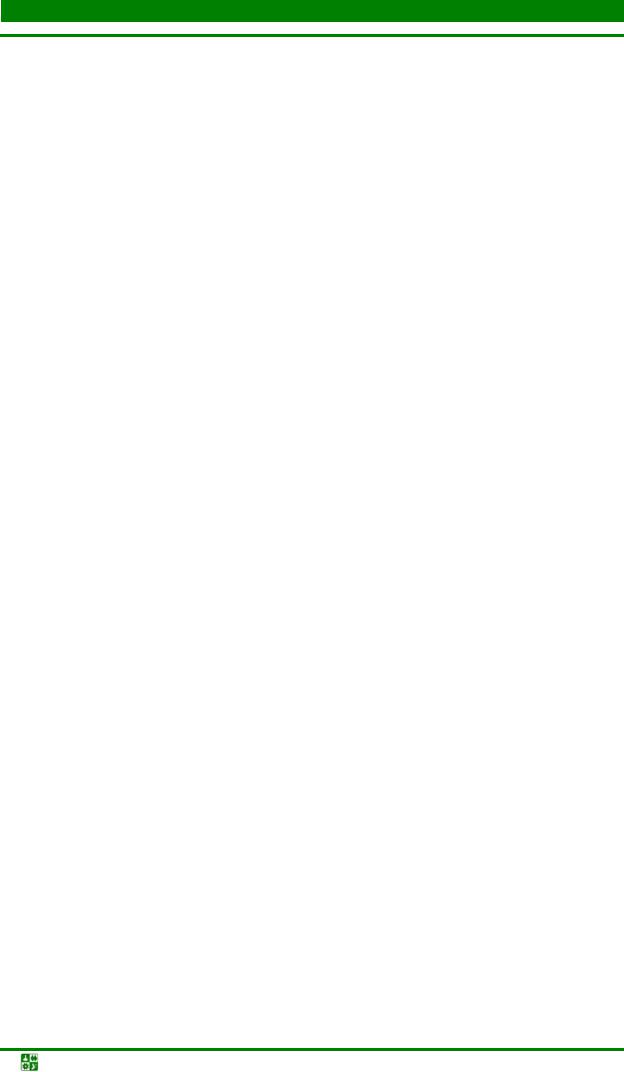
I. ПОЛУЧЕНИЕ ПОРОШКОВ
Лекция 11 Восстановление химических соединений металлов. Получение порошков железа восстановлением оксидов углеродом
Для выяснения механизма реакции важное значение имеет исследование влияния температуры на изменение скорости реакции, которое выражается уравнением Аррениуса:
lnК = –E/RT + lnC,
где К – константа скорости реакции; Е – энергия активации; С – постоянная. Графически уравнение Аррениуса изображается прямой линией; отклонение от прямолинейной зависимости указывает на изменение механизм процесса. По величине энергии активации можно составить представление о
преобладающем механизме процесса – химическом, диффузионном и т.п. Механизм восстановления химических соединений металлов тверды-
ми или газообразными восстановителями базируется на адсорбционноавтокаталитической теории. Согласно адсорбционно-автокаталитической теории, основные этапы реакции, проходящей на поверхности раздела двух фаз, сопровождаются последовательными превращениями в твердом состоянии. Эти реакции приводят к образованию вещества с другой, отличной от решетки исходного соединения, кристаллической структурой. Процесс превращения протекает в определенной последовательности.
1.Внешняя диффузия молекул газообразного восстановителя к поверхности восстанавливаемого соединения и физическая адсорбция молекул на этой поверхности. На этом этапе происходит поляризация (переориентация) молекулы относительно твердой поверхности под действием электростатического силового поля отдельных участковвосстанавливаемого соединения.
2.Активирование адсорбированных молекул за счет усиления действия на них силового поля кристаллической решетки. Этот этап сопровождается деформацией молекулы восстановителя и отрывом от нее отдельных атомов или групп атомов.
3.Отдача адсорбированными атомами электронов в решетку восстанавливаемого соединения. Электроны замещают образующиеся в результате разрыва связей между ионами вакансии в катионной подрешетке металла, в результате чего образуются нейтральные атомы металла (на поверхности восстанавливаемого соединения), ионы восстановителя и ионы неметаллической составляющей восстанавливаемого соединения.
4.Отрыв неметаллических ионов от поверхности восстанавливаемого соединения и их переход на более выгодные (с энергетической позиции) места в молекуле восстановителя.
5.Десорбция нейтральных (энергетически пассивных) молекул соединения восстановителя с поверхности раздела фаз и их диффузия вглубь газообразного слоя восстановителя под давлением активных молекул.
Процесс восстановления сопровождается разрыхлением поверхностного слоя и диффузией образовавшихся катионов восстанавливаемого металла вглубь решетки соединения, с образованием промежуточных форм,
Процессы порошковой металлургии. Курс лекций |
-85- |
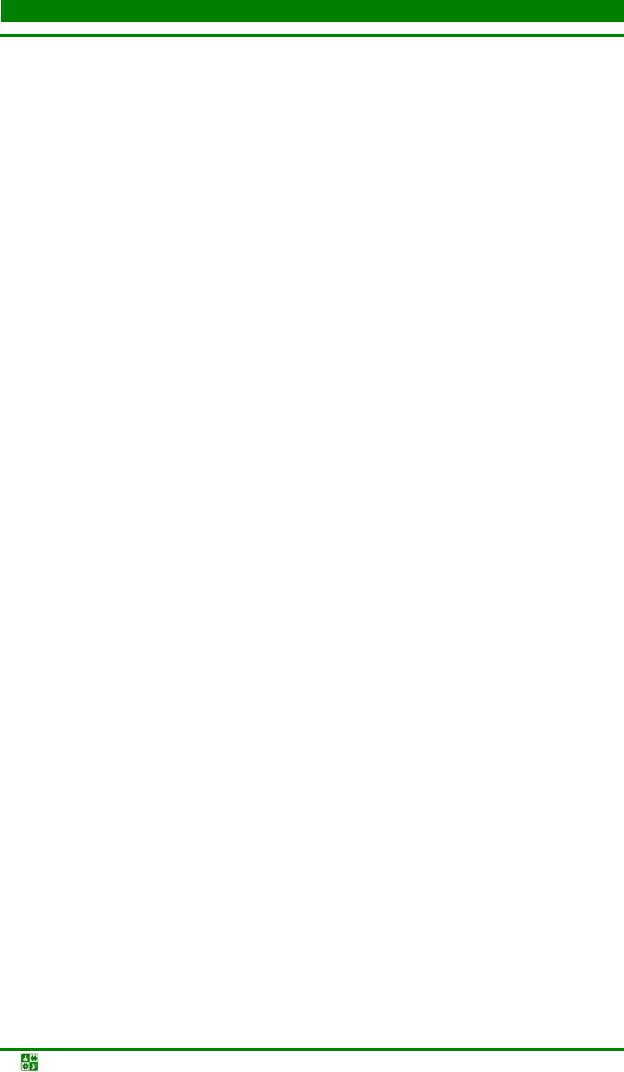
I. ПОЛУЧЕНИЕ ПОРОШКОВ
Лекция 11 Восстановление химических соединений металлов. Получение порошков железа восстановлением оксидов углеродом
имеющих более низкую валентность. Одновременно с диффузией катиона вглубь решетки восстанавливаемого соединения идет диффузия ионов неметаллической составляющей к поверхности раздела фаз.
Так как процесс зарождения новой фазы требует преодоления определенного энергетического барьера, то на начальном этапе процесс восстановления замедлен. Образование очагов металлической фазы (катализаторов) переводит реакцию в автокаталитическую стадию, при которой восстановление ускоряется.
В зависимости от температуры, пористости, размеров частиц исходной шихты и ее газопроницаемости, скорость процесса восстановления будет лимитироваться диффузией газов (как восстановителя, так и продукта реакции восстановления) через пористый слой образующегося металла к поверхности исходного соединения.
Получениепорошковжелезаиегосплавов восстановлениемоксидовуглеродом
Доля производства порошков железа и сплавов на его основе составляет более 80 % всего производства металлических порошков. Для получения железных порошков или сплавов железа применяются разнообразные методы. Методы восстановления обеспечивают производство примерно половины всех потребляемых промышленностью порошков железа.
Сырьем для порошковой металлургии служат оксиды железа, рудные концентраты или его хлористые соединения.
В соответствии с диаграммой состояния системы железо–кислород существуют три оксида железа: Fe2O3, или гематит (30,06 % О); Fe3O4, или магнетит (27,64 % О); FeO, который должен содержать 22,27 % О. Однако в реальных условиях последнего соединения не существует в связи с тем, что на диаграмме состояния Fe–O в данной области присутствует соединение с широкой областью гомогенности на основе FeO, обогащенное кислородом. Он называется вюститом, а его общая формула – FeхO. При температуре ниже 572 °С вюстит неустойчив и распадается на α-железо и Fe3O4.
Химически чистые оксиды железа в качестве сырья применяются крайне редко и только при получении каких-либо специальных материалов (например, сплава системы W–Ni–Fe), так как подобные порошки дороги.
Наиболее распространенным сырьем являются окисленные руды железа или прокатная окалина. В высокообогащенном рудном концентрате железо находится в виде гематита, магнетита, лимонита (HFeO2) и сидерита (FeCO3). Однако эти концентраты дороже прокатной окалины и уступают ей по содержанию железа, но содержат меньше серы и окиси марганца.
Окалина, образующаяся при прокатке углеродистых сталей, содержит 70–75 % Fe, до 0,4 % C, а также окислы кремния и марганца (до 0,5 %), пр и- меси серы и фосфора.
Процессы порошковой металлургии. Курс лекций |
-86- |
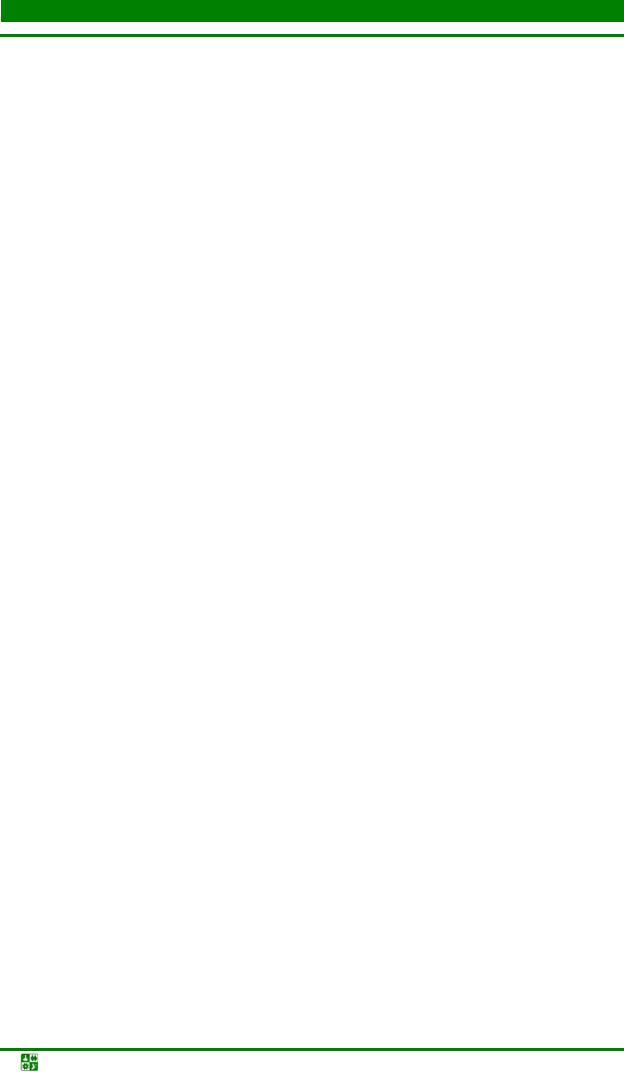
I. ПОЛУЧЕНИЕ ПОРОШКОВ
Лекция 11 Восстановление химических соединений металлов. Получение порошков железа восстановлением оксидов углеродом
Перспективным сырьем для производства железных порошков являются осадки, полученные из отработанных травильных растворов. Растворы, содержащие около 8 % серной кислоты и сернокислое железо, перерабатывают на так называемых «купаросных установках» с извлечением кристаллов FeSO4·7H2O, которые сушат при температуре 100–300 °С и разлагают при температуре 600–800 °С, получая чистый Fe2O3.
Солянокислые растворы железа подвергают высокотемпературному разложению в шахтной печи, в верхнюю часть которых (через разбрызгиватель) подается исходный раствор. Полученные в результате разложения частицы оксида железа собираются в нижней части печи и направляются на восстановление либо твердым углеродом, либо водородом. Хлористый водород поступает в систему регенерации, где он поглощается водой с образованием раствора соляной кислоты.
Восстановление твердым углеродом. Реакция восстановления оксидов железа твердым углеродом протекает по следующему механизму:
3Fe2O3 + C = 2Fe3O4 + 2CO |
(1.24) |
6Fe2O3 +C = 4Fe3O4 +CO2 |
(1.25) |
xFe3O4 + C = 3 FexO + CO2 |
(1.26) |
2Fe3O4 + C = 6FexO + CO2 |
(1.27) |
FexO + C = xFe + CÎ |
(1.28) |
2FexO + C = 2xFe + CO2 |
(1.29) |
Fe3O4 + 4C =3Fe + 4CO |
(1.30) |
Fe3O4 + 2C =3Fe +2CO2 |
(1.31) |
Однако непосредственное взаимодействие твердых частиц железа с углеродом развивается слабо из-за малой поверхности взаимодействия частиц шихты. Прямая химическая реакция между твердыми компонентами шихты наблюдается только в самом начале процесса. Как только в местах контакта углерода и оксида железа образуются очаги металлической фазы, прямая химическая реакция резко замедляется. Это объясняется тем, что она переходит в диффузионную стадию, при которой атомам углерода необходимо «пробиваться» к поверхности восстанавливаемого оксида через слой об-
разовавшегося металла.
Восстановление оксидом углерода. Практическое восстановление ок-
сидов железа на всех последующих этапах процесса обеспечивает СО, образующийся при окислении углерода:
Процессы порошковой металлургии. Курс лекций |
-87- |
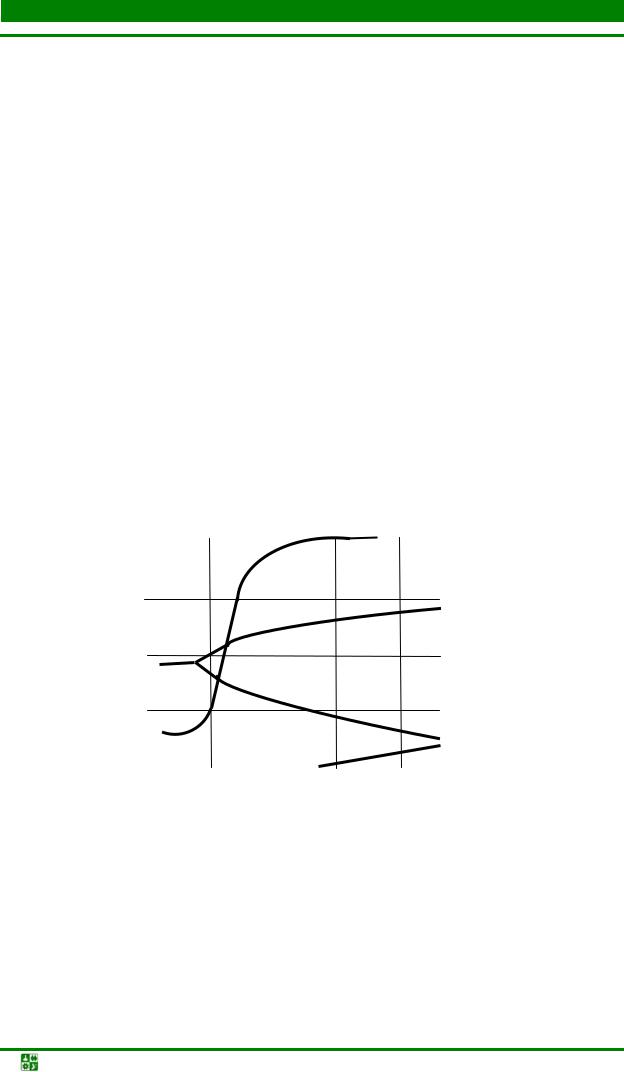
I. ПОЛУЧЕНИЕ ПОРОШКОВ
Лекция 11 Восстановление химических соединений металлов. Получение порошков железа восстановлением оксидов углеродом
C +O2 =CO2 |
(1.32) |
C +CO2 = 2CO |
(1.33) |
2C +O2 = 2CO |
(1.34) |
Реакции, протекающие с участием газовой фазы, выглядят следующим образом:
2Fe2O3 +CO = 2Fe3O4 +CO2 + Q |
(1.35) |
xFe3O4 +CO =3FexO +CO2 −Q |
(1.36) |
FexO + CO = xFe + CO2 +Q |
(1.37) |
Все приведенные реакции являются суммарными, идущими с образованием окислов углерода:
|
|
MeO +CO = Me +CO2 |
|
|
||
|
|
C +CO2 = 2CO |
|
|
||
|
|
2MeO +C = 2Me +CO2 |
|
|
|
|
СО, % |
|
|
|
|
|
СО2, % |
Р = 1 атм |
|
|
|
|||
90 |
|
|
|
10 |
||
1 |
|
2 |
|
|
||
|
|
|
|
|
||
60 |
|
|
FeO (вюстит) |
|
40 |
|
|
|
|
|
|
||
30 |
|
|
3 |
|
|
70 |
|
|
|
4 |
|
|
|
|
|
|
|
|
|
|
400 600 |
800 1000 1200 |
Т, °С |
Рис. 1.22. Кривые равновесия реакций восстановления оксидов железа окислом углерода: 1) С + СО2 = 2СО; 2) FeO + CO = Fe + CO2; 3) Fe3O4 + CO = 3FeO + CO2; 4) 3Fe2O3 + CO = 2Fe3O4 + CO2
Исходя из кривых равновесия реакций восстановления оксидов железа окислом углерода (рис. 1.22), можно сделать вывод, что производство железного порошка целесообразно вести при температурах не ниже 690 °С и концентрации СО в пределах от 60 до 100 %.
Процессы порошковой металлургии. Курс лекций |
-88- |
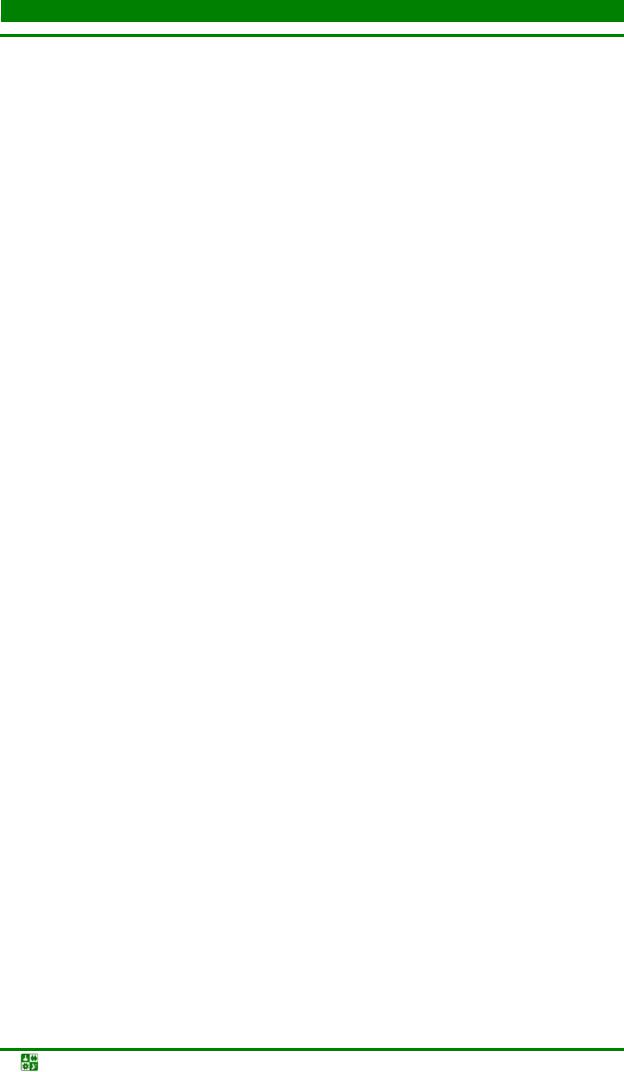
I. ПОЛУЧЕНИЕ ПОРОШКОВ
Лекция 11 Восстановление химических соединений металлов. Получение порошков железа восстановлением оксидов углеродом
Основныетехнологическиевариантыполученияпорошковжелеза сиспользованиемвкачествевосстановителяуглерода
Восстановление твердым углеродом. В качестве восстановителя ис-
пользуется молотый графит, кокс или термошлыб. В случае использования в качестве восстановителя термошлыба или кокса в состав шихты вводят известняк (СаСО3), который связывает серу в этих компонентах.
Окисленное сырье и восстановительную смесь засыпают кольцевыми, несмешивающимися слоями в тигли из карбида кремния (высота тигля около 1,5 м, диаметр – около 0,4 м) таким образом, чтобы слой сырья располагался между слоями восстановителя. Примерный состав шихты в тигле: 60–69 % оксидного сырья, 25–33 % термошлыба или кокса, 6–7 % известняка. Подготовленный тигель накрывают крышкой и загружают в печь, где выдерживают при температуре 1 175–1 200 °С в течение 30–40 ч.
Общее время прибывания тиглей в проходной тоннельной печи может составлять до 90 ч. Необходимо отметить, что рассматриваемый способ получения порошков железа основан на восстановлении оксидного сырья газообразным восстановителем (СО). Твердый углерод взаимодействует с сырьем только на начальном этапе процесса восстановления, что приводит к образованию сравнительно малочисленных очагов зарождения новой металлической фазы.
После выгрузки из печи контейнеры без крышек поступают на самообезуглероживающий отжиг при температуре 770–850 °С в течение 15–20 ч. Образовавшуюся губку, в виде трубы с толщиной стенки до 80 мм, извлек а- ют из контейнера, зачищают от остатков восстановителя, разламывают на части и подвергают дроблению, магнитной сепарации и рассеву на фракции. После этих операций проводят отбор проб материала, которые поступают на операцию определения характеристик полученного порошка(форма частиц, насыпная плотность, плотность утряски и пр.) на соответствие их ГОСТ 9849-86. Полученные порошки усредняют по химическому и гранулометрическому составу и упаковывают в полиэтиленовые мешки.
В некоторых случаях для повышения качества металлического порошка (рафинирования по кислороду и углероду и снятия наклепа) его подвергают восстановительному отжигу в водороде. Отжиг проводят в конвейерных печах при температуре 800–900 °С.
Для очистки порошков от примесей в виде небольших количеств оксидов металлов (SiO2, MnO, NiO и пр.), которые могут затруднять процесс формования, порошки обрабатывают смесью плавиковой и соляной кислот, в которую добавлен специальный ингибитор, подавляющий коррозию железа. Обработку порошка осуществляют в специальном шнековом реакторе, в который одновременно с порошком подается раствор кислот. Образующаяся густая пульпа из порошка и травителя перемещается шнеком к хвостовой части реактора, откуда поступает в следующий реактор, а затем на промывку в специальную ванну, снабженную пропеллерными мешалками. Промытый
Процессы порошковой металлургии. Курс лекций |
-89- |
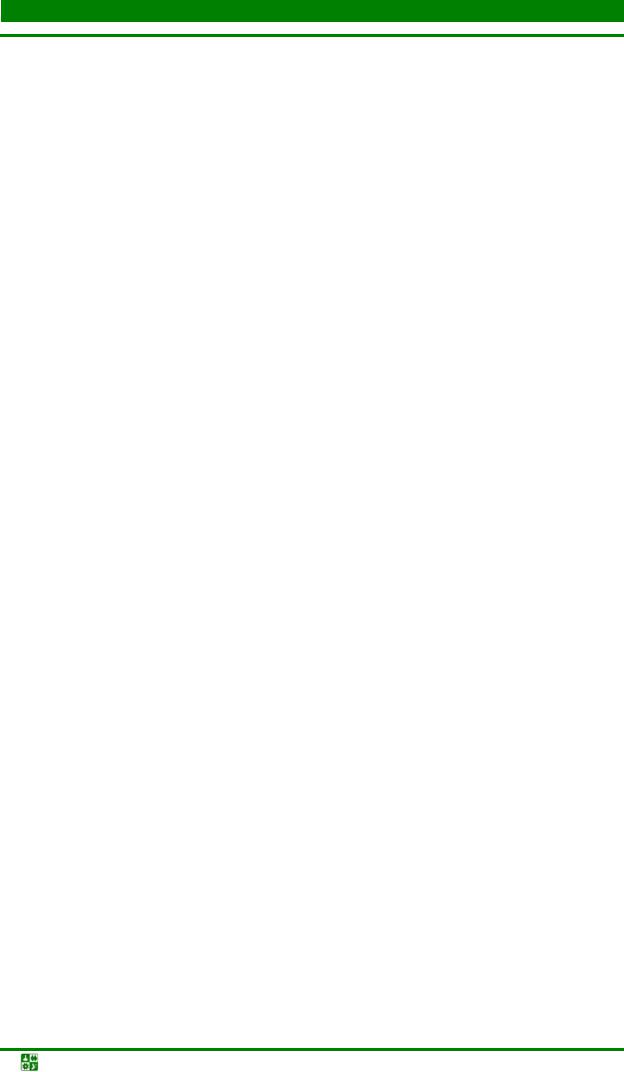
I. ПОЛУЧЕНИЕ ПОРОШКОВ
Лекция 11 Восстановление химических соединений металлов. Получение порошков железа восстановлением оксидов углеродом
порошок подают в отстойник, извлекают из него, сушат и отжигают при температуре около 1 000–1 100 °С в атмосфере водорода (время отжига – 6–7 ч).
Восстановление сажистым железом. Сажистое железо получают пу-
тем термокаталитического разложения углеводородных газов в порах железной губки при температуре 700–900 °С. Оптимальное содержание углерода в сажистом железе составляет от 20 до 50 %, наибольшая активность восстановителя наблюдается при 20–25 % С, а максимальная удельная поверхность (около 7 м2/г ) при содержании 50 % С. Основная масса углерода в сажистом железе находится в свободном состоянии в виде отдельных субмикронных частиц сажи (размеры трубочек сажи около нескольких десятков нанометров, а диаметр – единицы нанометров). Введение сажистого железа в восстанавливаемую щихту позволяет ускорить процесс восстановления и уменьшить его температуру на 100–200 °С. Это связано с тем, что добавка к традиционному восстановителю (коксу или термошлыбу) около 15 % сажистого железа приводит к образованию на начальном этапе восстановления большого количества центров активации процесса (зародышей металлической фазы), действующих каталитически. Кроме того, значительная удельная поверхность сажи способствует быстрой регенерации газообразного восстановителя. Применение сажистого железа позволяет приблизительно на 20–30 % снизить себестоимость продукции.
Комбинированное восстановление. Сущность этого метода состоит в одновременном действии на исходное окисное сырье твердого и газообразного восстановителя.
Количество твердого восстановителя в шихте (10–12 % мас.) эквивалентно примерно 60 % содержания кислорода в окисном сырье, остальные 40 % кислорода удаляются действием газа-восстановителя, поступающего в печь.
Комбинированное восстановление позволяет получать порошок с пониженным содержанием углерода (менее 0,1 %). Кроме того, существенно ускоряется процесс восстановления за счет газопроницаемости слоя шихты и активной регенерации газообразного восстановителя. Процесс восстановления ведут либо в печах шахтного типа, муфельных вертикальных печах, либо в горизонтальных печах конвейерного типа. Исходные компоненты шихты (рудный концентрат – гематит, окалину, древесный уголь, каменноугольный пек, нефтяной кокс, возврат железного порошка) подвергают перемешиванию или размолу, совмещенному с перемешиванием. После этого подготовленную смесь брикетируют или окомковывают.
При использовании муфельных горизонтальных печей брикеты помещают на сплошной или перфорированный стальной поддон. В некоторых случаях перфорированный поддон представляет собой спеченный слой железной губки. Применение перфорированного поддона, размалываемого в дальнейшем вместе с восстановленным материалом, позволяет ускорить процесс восстановления приблизительно в 1,2–1,5 раза. Процесс восстановления ведут при температуре 1 100–1 150 °С в течение 6–8 ч. В печь по принципу противотока подают холодный или разогретый газ-восстановитель. После выбивки из поддона губчатое железо подвергают дроблению и размолу до
Процессы порошковой металлургии. Курс лекций |
-90- |
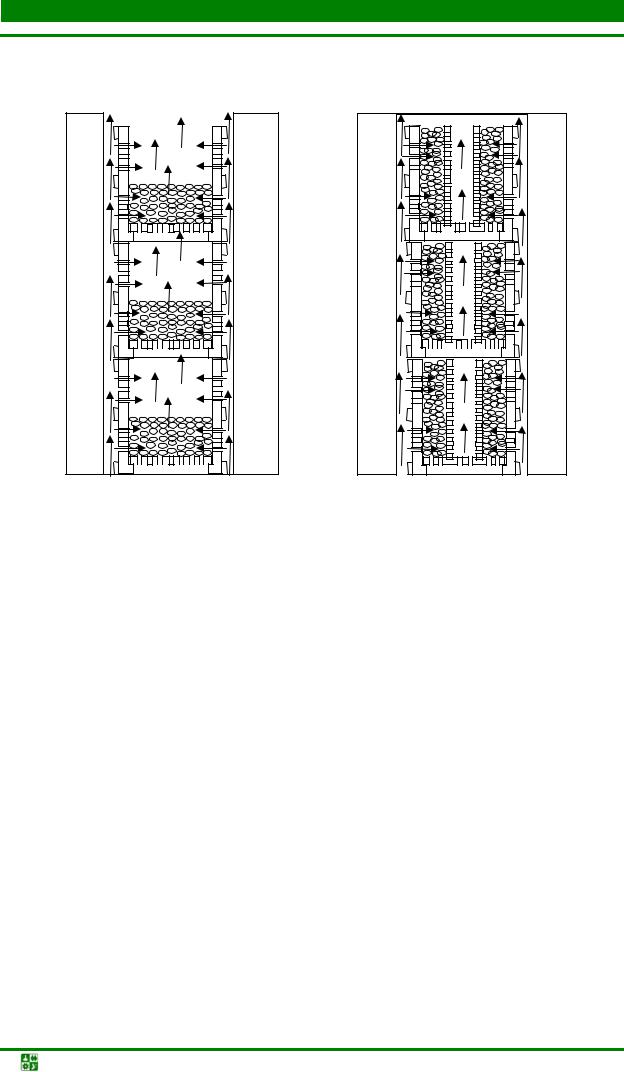
I. ПОЛУЧЕНИЕ ПОРОШКОВ
Лекция 11 Восстановление химических соединений металлов. Получение порошков железа восстановлением оксидов углеродом
крупности частиц менее 0,5 мм. После этого полученный порошок подвергают магнитной сепарации и рассеву на фракции.
а |
б |
Рис. 1.23. Схема размещения брикетированной шихты в муфеле шахтной печи при использовании простых (а) и кольцевых (б) перфорированных стаканов
При использовании вертикальных муфельных печей брикеты загружают в простые или перфорированные стаканы (масса шихты в каждом из стаканов более 100 кг). Стаканы загружают в печь (рис. 1.23), которая работает по принципу противотока: навстречу движущемуся вниз стакану подается газ восстановитель.
Восстановление ведут при температуре 1 100–1 150 °С. Время восстановления – 9–10 ч. После восстановления полученное губчатое железо дробят и размалывают, а полученный порошок рассеивают на фракции. Мелкий порошок (менее 150 мкм) направляют на магнитную сепарацию и операцию усреднения по составу.
В конвейерных печах подготовленные брикеты или окатыши подаются прямо на ленту печи слоем до 300 мм. Восстановление ведут при температуре 950–1 150 °С. Время восстановления составляет около 2,0–2,5 ч (время пнахождения в зоне восстановления – 50–75 мин).
Легированные железные порошки получают из окалины проката легированных сталей. Исходную шихту смешивают с сажей и возвратом железного порошка в соотношении 80:10:10. Шихту восстанавливают при температуре 1 100–1 150 °С конвертированным природным газом или водородом в течение 5–8 ч.
Процессы порошковой металлургии. Курс лекций |
-91- |
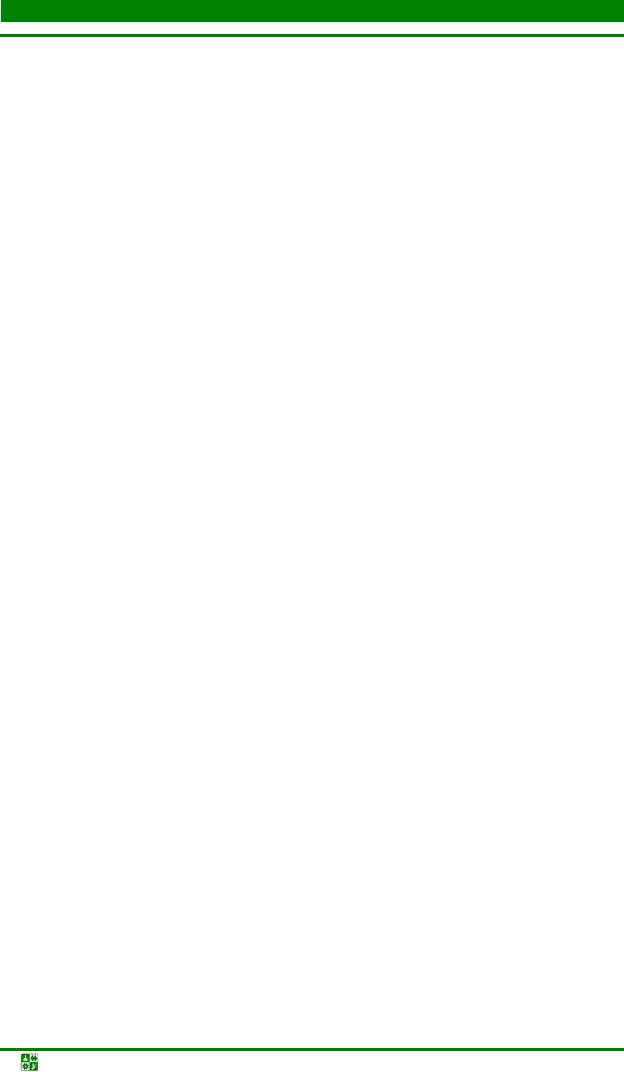
I. ПОЛУЧЕНИЕ ПОРОШКОВ
Лекция 11 Восстановление химических соединений металлов. Получение порошков железа восстановлением оксидов углеродом
Содовый способ. Сущность содового способа заключается в совмещении процесса восстановления и химического рафинирования железосодержащего сырья кальцинированной содой (Na2CO3). Процесс восстановления осуществляют при нагреве шихты из смеси оксида железа, углерода и соды до температуры выше 700 °С. Примеси, содержащиеся в шихте (кислородные соединения кальция, кремния, марганца, мышьяка, фосфора и пр.), образуют растворимые в воде и разбавленных кислотах соединения на основе натрия (Na2O·Al2O3·2SiO2, Na2SiO3, Na3PО4 и пр.), соду берут с четырехили пятикратным избытком от необходимого на связывание примесей. Сода при восстановлении действует каталитически, ускоряя газификацию углерода и кристаллохимические превращения в восстанавливаемом материале.
Исходные компоненты шихты (железосодержащий материал, с размерами частиц около 100 мкм – 80 %, нефтяной кокс – 10 % и соду – 10 %) смешивают в смесителе с шарами в течение 5–7 ч. При наличии операции окомкования соду в шихту вводят в виде водного раствора. Это позволяет равномерно распределить ее по объему материала.
Восстановление проводят в муфельной печи (температура– 950–1 000 °С, время восстановления – 11–12 ч) либо в конвейерной печи (температура – 1 050–1 100 °С, время восстановления – 5–6 ч). Полученный спек измельчают в молотковой дробилке и подвергают мокрому размолу в шаровой мельнице до размеров частиц около 200 мкм. Полученную пульпу обрабатывают водой и слабокислыми растворами в три этапа. После этого порошок обезвоживают, сушат и отжигают в атмосфере водорода (температура – 1 100 °С, время отжига – 6–7 ч). Отжиг проводят в муфельной печи. После отжига спекшуюся губку дробят, а полученный порошок рассеивают на фракции и упаковывают.
Контрольныевопросыизадания
1.Дайте определения восстановителя.
2.Какие факторы определяют вероятность прохождения реакции восстановления?
3.Что такое металлотермия?
4.Что определяет понятие «кинетика процесса»?
5.Что определяет адсорбционно-автокаталитическая теория процессов восстановления?
6.Перечислите основные этапы реакции, проходящей на поверхности раздела двух фаз.
7.Перечислите основные виды сырья, применяемого при получении порошков железа.
8.Назовите основные технологические варианты получения порошков железа восстановлением оксидов углеродом.
Процессы порошковой металлургии. Курс лекций |
-92- |
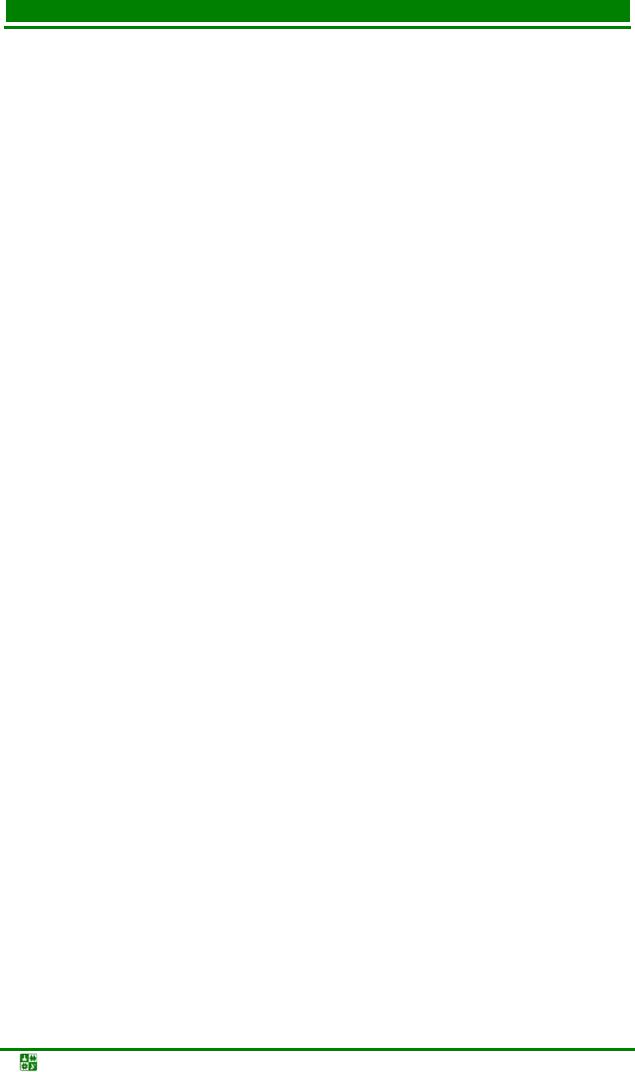
I. ПОЛУЧЕНИЕ ПОРОШКОВ
Лекция12 Получениепорошковжелезавосстановлением
химическихсоединений
План лекции
1.Методы восстановления оксидов железа водородом.
2.Хлоридный способ получения порошков железа.
3.Металлотермические методы получения порошков железа.
Методывосстановленияоксидовжелезаводородом
Процесс восстановления Fe2O3 до железа происходит по трехступенчатой (свыше 572 °С) Fe2O3 → Fe3O4 → FexO → Fe или двухступенчатой (ни-
же 572 °С) Fe2O3 → Fe3O4 → Fe схеме:
3Fe2O3 + H2 |
= 2Fe3O4 + H2O + Q |
(1.38) |
xFe3O4 + H2 = 3FexO + H2O – Q |
(1.39) |
|
FexO + H2 = xFe + H2O – Q |
(1.40) |
|
Fe3O4 + 4H2 |
= 3Fe + 4H2O – Q |
(1.41) |
Принимая неизменными упругости паров твердых (конденсированных) фаз, константы равновесия для реакций (1.38), (1.39), (1.40) можно выразить уравнением Kр = рH2O /рH2, а для реакции (1.41) – уравнением Kр =
р4H2O /р4H2. Реакция (1.38) в отличие от других экзотермична, в силу чего с
ростом температуры равновесная газовая фаза должна обедняться парами воды и обогащаться водородом. Однако значения констант равновесия этой реакции настолько велики, что можно без особых погрешностей говорить о необратимости восстановления оксида железа до магнетита в случае любого, сколь угодно исчезающе малого присутствия водорода в равновесной газовой фазе. По реакции (1.39) сначала образуется обогащенный кислородом вюстит, который затем в процессе восстановления обедняется кислородом до нижней границы своей области гомогенности при данной температуре, а уже затем по реакции (1.40) образуется железо.
На рис. 1.24, изображающем равновесный состав газовой фазы, в системе Fе–О–Н в зависимости от температуры приведены четыре кривые и четыре области, соответствующие существованию определенных фаз.
Процессы порошковой металлургии. Курс лекций |
-93- |
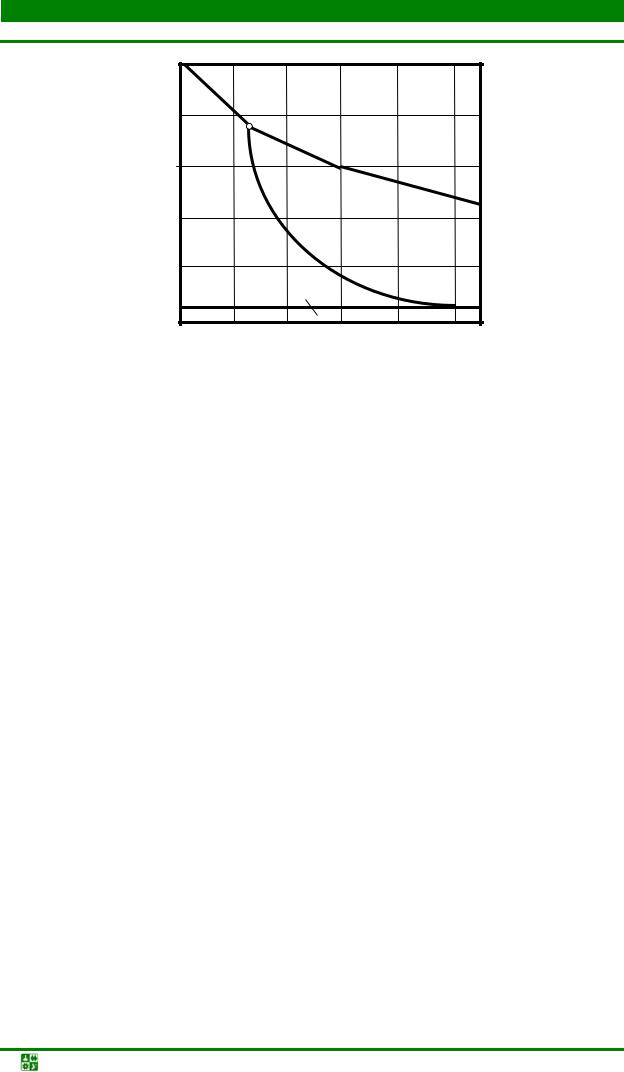
|
I. ПОЛУЧЕНИЕ ПОРОШКОВ |
|
|
||||
Лекция 12 Получение порошков железа восстановлением химических соединений |
|||||||
СН2, % |
|
|
|
|
|
|
|
80 |
4 |
а |
|
|
D |
|
|
|
|
|
|
|
|
||
60 |
|
|
|
3 |
|
|
|
|
|
|
|
|
|
|
|
40 |
B |
|
|
|
C |
|
|
|
|
|
|
2 |
|
|
|
20 |
|
|
|
|
|
|
|
|
|
|
|
|
|
|
|
|
|
1 |
A |
|
|
|
|
300 |
500 |
|
700 |
900 |
1100 |
1300 |
T, оC |
Рис. 1.24. Кривые равновесия реакции восстановления |
|||||||
|
оксидов железа водородом |
|
|
Кривая 1 соответствует равновесию Fe2O3–Fe3O4, кривая 2 – равновесию Fe3O4–FexO, кривая 3 – равновесию FexO–Fe и кривая 4 – равновесию Fe3O4–Fe. Область А соответствует существованию Fe2O3, область В – Fe3O4, область С – существованию вюстита и область С – существованию железа. В точке а при 572 °С одновременно сосуществуют Fe3O4, FexO и Fe.
Механизм восстановления оксидов железа водородом идентичен механизму восстановления оксидов железа СО. Процесс зарождения кристаллов новой фазы в результате кристаллохимической перестройки исходного оксида железа по мере пересыщения его ионами металла требует преодоления энергетического барьера, что проявляется в замедленном развитии процесса в его начальном периоде.
Образование достаточного количества металлической фазы действует автокаталитически, и процесс ускоряется. Когда внешняя диффузия газов, адсорбция восстановителя, десорбция газообразных продуктов реакции проходят с достаточной скоростью, что наблюдается при повышенных температурах, диффузия ионов через слои твердых продуктов реакции и внутри кристаллов оксида железа может лимитировать суммарную скорость всего процесса в целом.
В зависимости от температуры, характера пористости и газопроницаемости шихты суммарный процесс может лимитироваться диффузией газов (как восстановителя, так и продуктов реакции) через слой образовавшегося металла и его исходного соединения.
На скорость процесса восстановления оксидов железа водородом существенное влияние оказывает концентрация паров воды в реакционной зоне, так как ее увеличение препятствует развитию реакций из-за адсорбции молекул воды на поверхности частиц оксида железа. Поэтому следует стремиться к снижению концентрации паров воды в реакционной зоне, что будет положительно влиять на скорость восстановления.
Процессы порошковой металлургии. Курс лекций |
-94- |

I. ПОЛУЧЕНИЕ ПОРОШКОВ
Лекция 12 Получение порошков железа восстановлением химических соединений
Железный порошок, получаемый восстановлением окисного сырья водородом, отличается высокой чистотой и повышенной активностью при спекании.
На практике используют несколько основных вариантов процесса восстановления оксида железа водородом. К их числу относятся:
1.Восстановление в стационарном слое. Процесс проводят в проход-
ных муфельных или трубчатых печах с внешним электрообогревом. Оксиды железа помещают в поддоны или лодочки, которые непрерывно продвигают через горячую зону печи. Водород подают со стороны холодильника печи, и принцип противотока обеспечивает наиболее полное восстановление. Продолжительность процесса восстановления – от 30 мин до нескольких часов. Температура восстановления составляет 700–1 000 °С.
2.Восстановление во вращающейся печи. Процесс восстановления ве-
дут в наклонной вращающейся трубчатой печи из нержавеющей стали. Исходное сырье подают шнеком в трубу навстречу потоку газа-восстановителя. Температура восстановления – 975–1 025 °С.
3. Восстановление в кипящем слое. Исходным сырьем служит обога-
щенный рудный концентрат, измельченный в шаровой мельнице до крупности 0,15 мм и подвергнутый магнитной сепарации (содержание железа около 72 %), который нагревают до температуры 480 °С во вращающейся печи и транспортируют в загрузочный бункер реактора под давление азота, куда под давление 3,5 МПа подают водород. Реактор представляет собой металлическую колонну высотой 29 м и диаметром 1,7 м. Восстановление ведут при температуре 540 °С на трех горизонтальных подовых решетках. Загрузка новой порции концентрата в верхнюю часть реактора, пересыпка материала с решетки на решетку и выгрузка порошка из нижней части реактора проводится периодически. Осушенный и подогретый водород под давлением 2,8 МПа нагнетается в нижнюю часть реактора. Скорость его подачи регулируется таким образом, чтобы частицы порошка находились во взвешенном состоянии.
Выгруженный порошок для уменьшения пирофорности нагревают в среде защитного газа до температуры 800 °С. При этом происходит укрупнение частиц порошка и снижается его пирофорность.
Хлоридныйспособполученияпорошковжелеза
Сущность этого гидрометаллургического метода заключается в растворении исходного железосодержащего материала в соляной кислоте с образованием раствора хлористого железа (примеси и балластные вещества отделяются в виде нерастворимого остатка) и последующем его восстановлении водородом с получением чистого порошка железа. В основе процесса лежит реакция Fe + 2HCl = FeCl2 + H2 – Q, протекающая в первой фазе пр о- цесса (растворение железа, содержащегося в исходном материале) слева направо, а на заключительной стадии (восстановление полученного хлорида
Процессы порошковой металлургии. Курс лекций |
-95- |
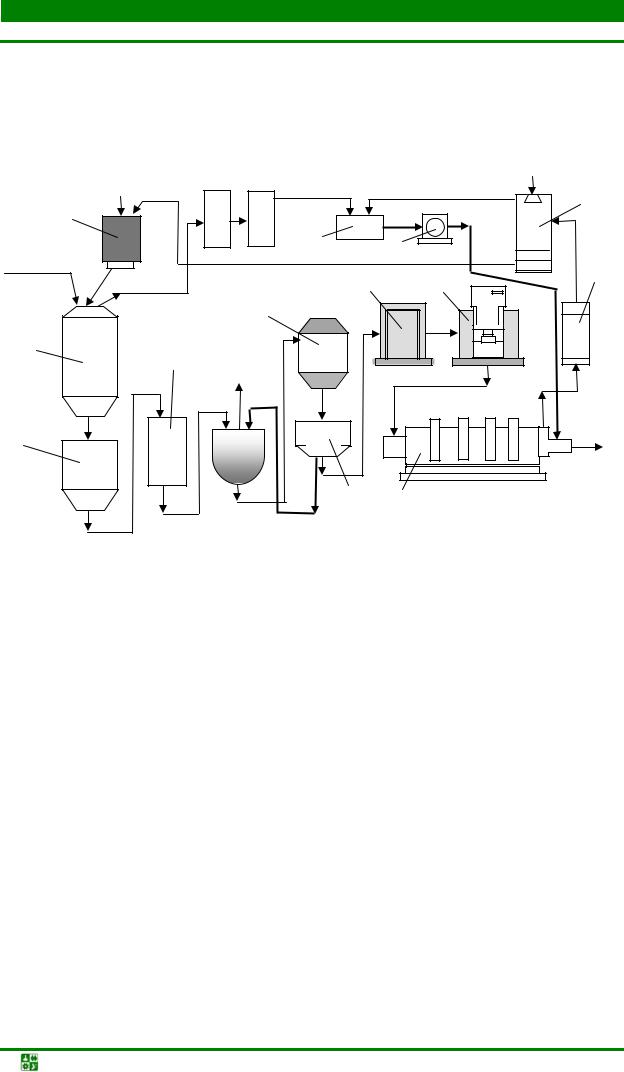
I. ПОЛУЧЕНИЕ ПОРОШКОВ
Лекция 12 Получение порошков железа восстановлением химических соединений
железа водородом) справа налево. Промежуточные стадии процесса (фильтрация раствора хлорида железа, его упаривание и кристаллизация) осуществляются с изменением агрегатного, но не химического состояния перерабатываемого продукта.
|
Раствор НCl |
|
|
|
|
Влажный водород |
12 |
1 |
|
|
|
|
|
|
|
|
15 |
15 |
13 |
|
|
|
|
Железо- |
|
|
|
|
14 |
|
|
содержащее |
|
|
|
|
|
||
сырье |
|
|
Раствор НCl |
|
|
11 |
|
|
|
|
8 |
9 |
|||
|
Выделившийся при |
|
|
|
|||
|
6 |
|
|
|
|
||
|
растворении сырья |
|
|
|
|
||
|
водород |
|
|
|
|
|
|
2 |
4 |
|
|
|
|
|
|
|
Пары воды |
|
|
|
|
||
|
|
|
|
|
|
3 |
5 |
|
7 10
Железный
порошок
Рис. 1.25. Аппаратурно-технологическая схема получения железного порошка хлоридным способом: 1 – емкость с раствором соляной кислоты; 2 – реактор с кислотостойкой футеровкой; 3 – отстойник; 4 – фильтр; 5 – упариватель; 6 – кристаллизатор; 7 – центрифуга; 8 – сушильная камера; 9 – пресс для брикетирования кристаллов хлористого железа; 10 – восстановительная печь; 11 – пылеуловитель; 12 – скруббер; 13 – осушитель; 14 – компрессор; 15 – очиститель для улавливания HCl и H2S
Одна из возможных технологических схем (рис. 1.25) хлоридного способа включает операции загрузки в обогреваемый паром герметичный реактор (с кислотостойкой футеровкой), стального (чугунного) скрапа, стружки, лома или дешевой железной губки, заливки его 15–20 %-й соляной кислотой и слива раствора хлорида железа в отстойник через фильтр.
После этого раствор направляют в упариватель, где при разрежении 400–650 гПа и температуре 60 °С получают насыщенный горячий раствор, который направляют в кристаллизатор, где при охлаждении до 5 °С выпадают кристаллы FeCl2·4H2O, в которые переходит до 75 % Fе.
Примеси, присутствующие в исходном железосодержащем материале, остаются в отвальном кеке после фильтрации раствора, а небольшое количество некоторых примесей, перешедших в раствор (Са, Мg и др.), остается в маточном растворе.
Выпавшие кристаллы хлорида железа после центрифуги обезвоживают в сушильной камере при температуре до 60 °С и разрежении 250–400 гПа
Процессы порошковой металлургии. Курс лекций |
-96- |
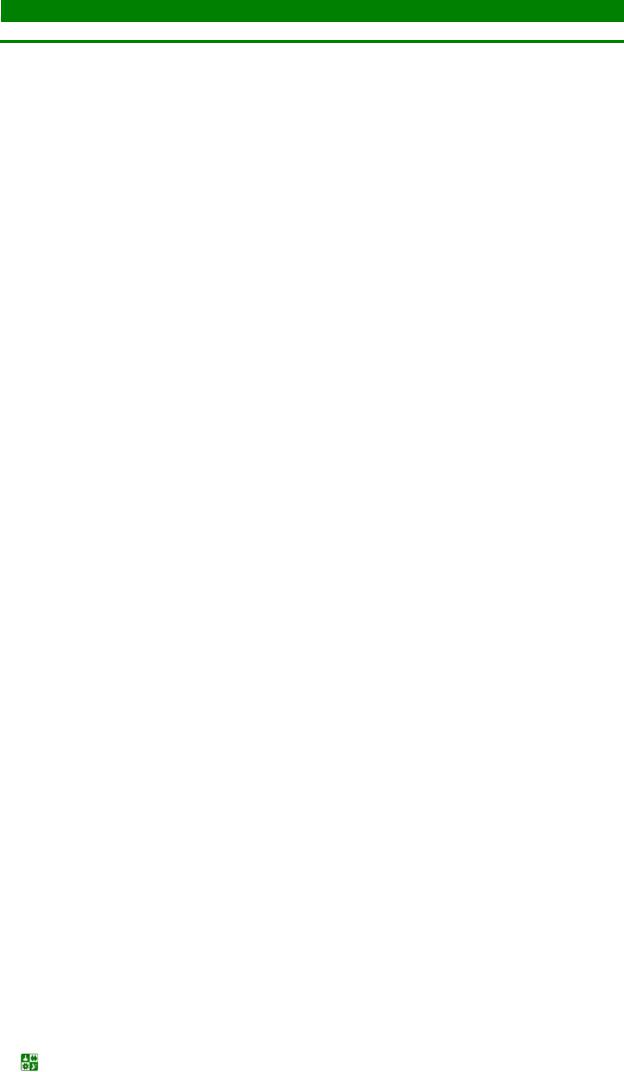
I. ПОЛУЧЕНИЕ ПОРОШКОВ
Лекция 12 Получение порошков железа восстановлением химических соединений
до состава FeCl2·2H2O или FeCl2 и брикетируют на прессе, после чего направляют в восстановительную печь.
Хлорид железа плавится при 673 °С, поэтому восстановление ведут подогретым водородом при 550–600 °С в шахтной печи периодического действия с загрузкой большого числа брикетов. Равновесное парциальное давление водорода в 7-8 раз выше парциального давления хлористого водорода, это вынуждает подавать водород в печь с большим избытком по отношению к количеству образующегося в единицу времени хлористого водорода.
Продукт восстановления (слабо сцепленные частицы) подвергают измельчению в молотковой или вихревой мельнице. Получаемый мелкозернистый порошок железа содержит, % (не более): 0,1 О, 0,015 С; 0,005 С1; 0,006 Si.
Избыточный водород и пары хлористого водорода, выходящие из восстановительной печи, через пылеуловитель поступают в водяной скруббер, где хлористый водород поглощается водой; раствор соляной кислоты перекачивают в напорный бак с соляной кислотой, расположенный над реактором.
Водород, выходящий из скруббера, поступает по трубам через осушитель, присоединяется к очищенному водороду, выходящему из реактора, и подается в восстановительную печь.
Таким образом, соляная кислота и водород регенерируются в замкнутом цикле. Некоторые случайные потери водорода и соляной кислоты компенсируют подачей их свежих порций в систему.
Хлоридный способ применяют также для получения природнолегированных (2,5–8,0 % легирующих элементов) порошков железа.
Металлотермическиеметодыполученияпорошковжелеза
К данной группе методов относятся карбидотермический и гидриднокальциевый методы.
Карбидотермический метод. Железные порошки высокой чистоты могут быть получены восстановлением прокатной окалины или богатой окисленной железной руды карбидом кальция.
Исходные железосодержащий материал и карбид кальция размалывают в шаровой мельнице до крупности частиц около 100 мкм, после чего смешивают их в барабанном смесителе в течение 3 ч (количество карбида кальция определяют расчетом с учетом условия полного восстановления оксидов железа).
Железосодержащий компонент шихты перед смешиванием тщательно просушивают, так как влага может привести к взрыву из-за ее взаимодействия с СаС2. Шихту восстанавливают при 1 100–1 150 °С в течение 2–3 ч.
В процессе нагрева при 800–900 °С карбид кальция диссоциирует с образованием металлического кальция и свободного углерода. Восстановительные процессы протекают по следующим суммарным реакциям:
Fe2O3 + 3Са = 2Fe + 3СаО |
(1.42) |
|
|
Процессы порошковой металлургии. Курс лекций |
-97- |
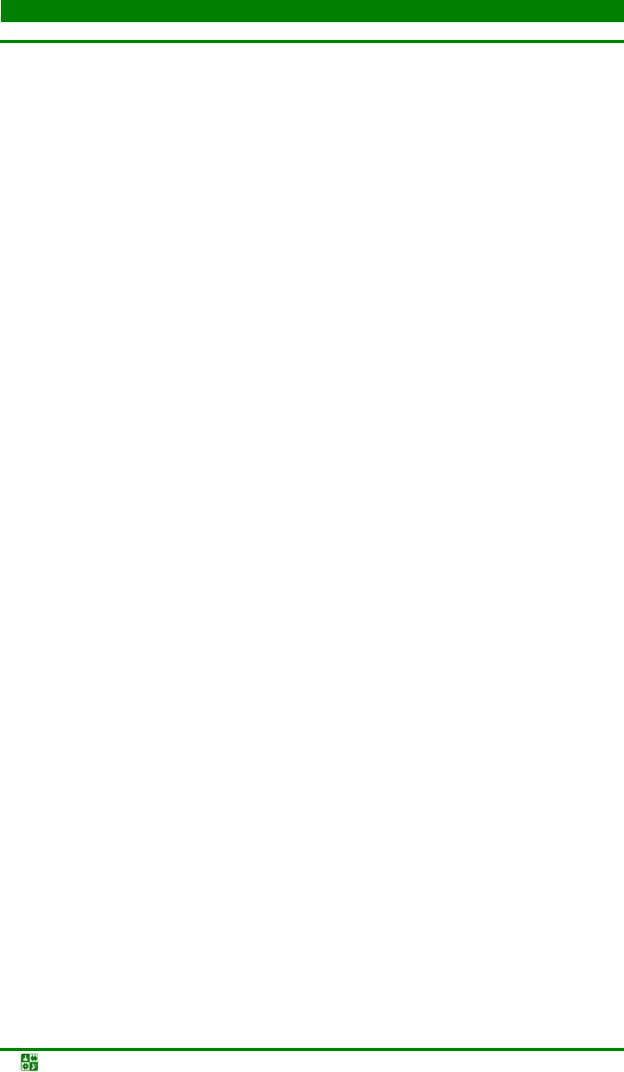
I. ПОЛУЧЕНИЕ ПОРОШКОВ
Лекция 12 Получение порошков железа восстановлением химических соединений
Fe2O3 + 3С = 2Fe + 3СО |
(1.43) |
Образующийся оксид кальция взаимодействует с металлическими примесями, формируя оксидный шлак.
Полученную при восстановлении спеченную губку измельчают в шаровой мельнице в жидкой среде (Т : Ж = 4 : 1) в течение 2 ч до крупно сти частиц < 100 мкм, после чего проводят мокрую магнитную сепарацию (Т : Ж = 1 : 4).
Обогащенный железный порошок обезвоживают на вакуум-фильтрах и высушивают при 50–60 °С. Без восстановления такой порошок в зависимости от вида исходного сырья содержит 98,7–99,1 % Fe. Его качество может быть улучшено отмывкой примесей при обработке порошка соляной кислотой.
Гидридно-кальциевый метод. Порошки сталей и сплавов сложного состава получают совместным восстановлением смеси оксидов (или смеси оксидов и металлических порошков) гидридом кальция. Этот процесс в общем виде можно представить следующей суммарной реакцией:
k |
|
|
k |
k |
k |
k |
∑ An (Mean |
Ob ) + ∑ Anbn (CaH2 ) =∑ Anbn (CaO) + ∑ Anbn (H2 ) + ∑ AnanMen , |
|||||
n=1 |
n |
n |
n=1 |
n=1 |
n=1 |
n=1 |
|
|
где n – порядковый номер (от 1 до k) компонента шихты (оксида) и соответствующего ему металла в готовом продукте (порошке сплава); k – максимальное число оксидов в шихте; Аn – количество грамм-молекул в соответствии с заданным составом сплава; an – число атомов металла в молекуле соответствующего оксида (от 1 до 3); bn – число атомов кислорода в молекуле соответствующего оксида (от 1 до 5, для компонента, вводимого в виде металлического порошка, bn = 0).
Компоненты получаемого сплава, оксиды которых легковосстановимы, целесообразно вводить в шихту в виде порошков соответствующих металлов (например, Fe, Cu, Ni, W, Mo и др.), так как при этом сокращается расход дорогостоящего гидрида кальция.
Трудновосстановимые оксиды, входящие в шихту, восстанавливаются гидридом кальция практически при одной и той же температуре(1 150–1 200 °С), причем в реакторе из нержавеющей стали начиная с 400 и вплоть до 1 200 °С поддерживается атмосфера сухого и чистого водорода (при 400 °С гидрид кальция диссоциирует, выделяя водород, а при более высоких температурах
– взаимодействует с водой, образующейся при восстановлении оксидов). Когда шихта содержит мало трудновосстанавливаемых оксидов, в нее рекомендуется вводить «разъединитель» (оксид кальция, хлористый натрий и др.), что облегчает последующую обработку спека, образовавшегося после проведения реакции.
В процессе восстановления происходит агломерация металлических частиц, которой оксид кальция препятствует, а хлористый натрий способст-
Процессы порошковой металлургии. Курс лекций |
-98- |
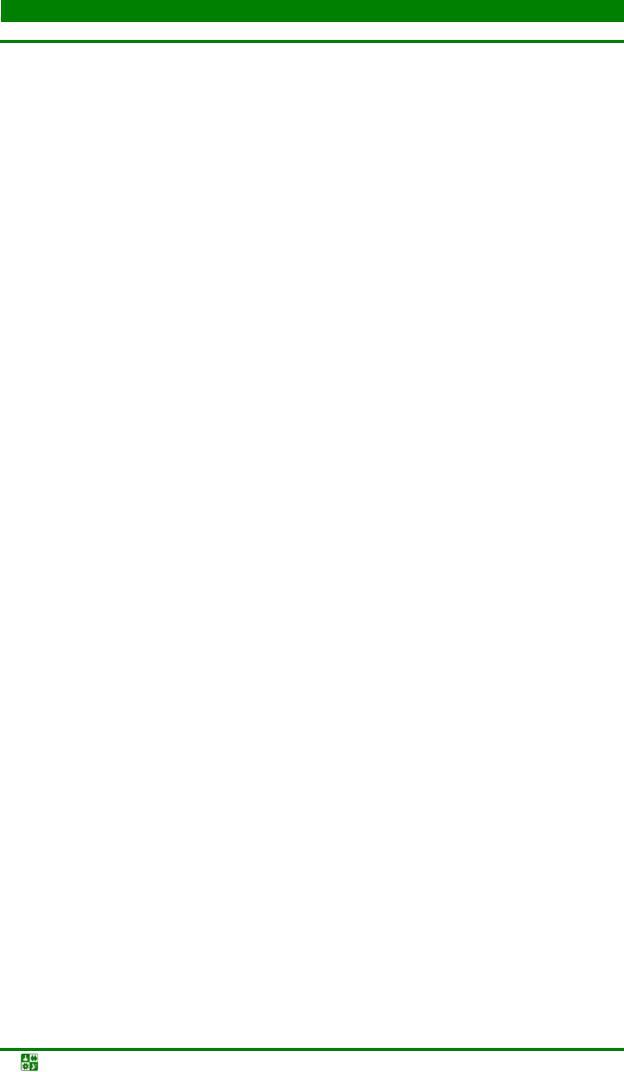
I. ПОЛУЧЕНИЕ ПОРОШКОВ
Лекция 12 Получение порошков железа восстановлением химических соединений
вует. Выдержка при температуре восстановления зависит от скорости процесса диффузионного образования сплава и должна быть установлена экспериментально; обычно она составляет 6–8 ч.
Разгрузку спека из реактора осуществляют либо струей воды под давлением 0,15–0,2 МПа, причем одновременно происходит его гашение, либо механически (тогда выгруженный из реактора спек дробят, размалывают и гасят большим избытком воды).
Пульпу, полученную после гашения спека и содержащую порошок сплава и гидроксид кальция, подвергают обогащению в гидроциклонах, позволяющих удалить 60–70 % Са(ОН)2. Затем пульпу обрабатывают разбавленной соляной кислотой, переводят оставшийся в пульпе гидроксид кальция в хорошо растворимый в воде хлористый кальций, который отмывают. После отмывки металлический порошок обрабатывают на центрифугах и высушивают в вакуумных сушильных шкафах при 60–70 °С.
Указанным методом получают порошки высоколегированных сталей и сплавов.
Контрольныевопросыизадания
1.Перечислите методы восстановления оксидов железа водородом.
2.Сколько ступеней в технологической схеме водородного восстановления при температуре ниже 572 °С?
3.Какие преимущества имеют методы водородного восстановления оксидного сырья?
4.Перечислите основные операции хлоридного способа получения железных порошков.
5.Каким путем осаждают из раствора кристаллы хлорида железа?
6.Какую операцию применяют при получении из кристаллов хлорида железа металлических порошков?
7.Назовите металлотермические методы получения порошков желе-
за.
8.Какой метод металлотермического восстановления оксидного сырья используют при получении порошков сплавов и сталей?
9.Перечислите основные операции гидридно-кальциевого метода получения порошков железа.
Процессы порошковой металлургии. Курс лекций |
-99- |
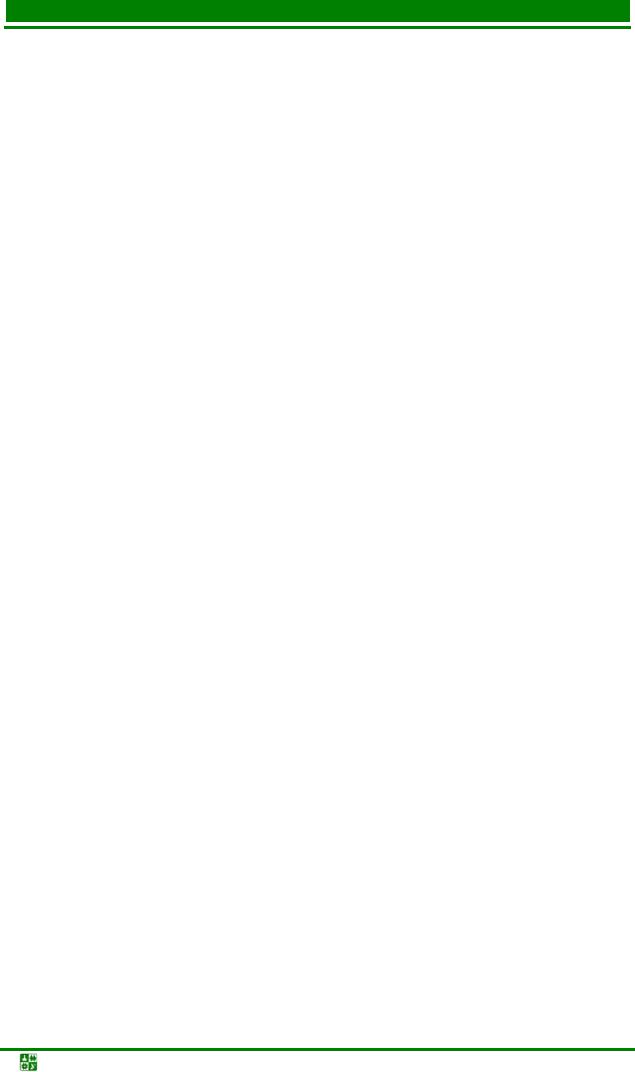
I. ПОЛУЧЕНИЕ ПОРОШКОВ
Лекция13 Получениепорошковвольфрамавосстановлением
оксидовводородомиуглеродом
План лекции
1.Оксиды и кристаллические модификации вольфрама.
2.Восстановление вольфрамового ангидрида водородом.
3.Восстановление вольфрамового ангидрида твердым углеродом.
Оксидыикристаллическиемодификациивольфрама
Наиболее часто исходным материалом для получения порошкообразного вольфрама служит вольфрамовый ангидрид с размером частиц от десятых долей до 10–15 мкм, а в качестве восстановителя используют водород или твердый углерод (сажу).
В системе W–O достоверно установлено существование четырех оксидов вольфрама: WO3 (α-оксид с областью гомогенности WO3–WO2,96) желто-
го цвета; WO2,9 или W20O58 (β-оксид с областью гомогенности WO2,9–WO2,83) синего цвета; WO2,72 или W18O49 (γ-оксид с областью гомогенности WO2,72–
WO2,66) фиолетового цвета; WO2 (δ-оксид с областью гомогенности WO2,03– WO2) темно-коричневого цвета.
Оксид вольфрама WO3 имеет три кристаллические модификации: моноклинную, устойчивую ниже 720 °С, тетрагональную, устойчивую в интервале 720–1 100 °С, и кубическую, устойчивую выше 1 100 °С. При 800–850°С WO3 заметно возгоняется и в паровой фазе находится в форме полимерных молекул, преимущественно W3O9. Оксид вольфрама WO2,9 нестабилен ниже 484 °С и диспропорционирует с образованием WO2 и WO3, а WO2,72 нестабилен ниже 585 °С. Сублимация WO2 наблюдается при 1 000–1 050 °С и сопровождается разложением твердой фазы.
Степень возгонки всех оксидов вольфрама возрастает в присутствии паров воды из-за образования гидратных комплексов, заметно сублимирующих при 500–600 °С.
Восстановлениевольфрамовогоангидридаводородом
Суммарная реакция восстановления
WO3 + 3H2 = W + 3H2O |
(1.44) |
Процессы порошковой металлургии. Курс лекций |
-100- |
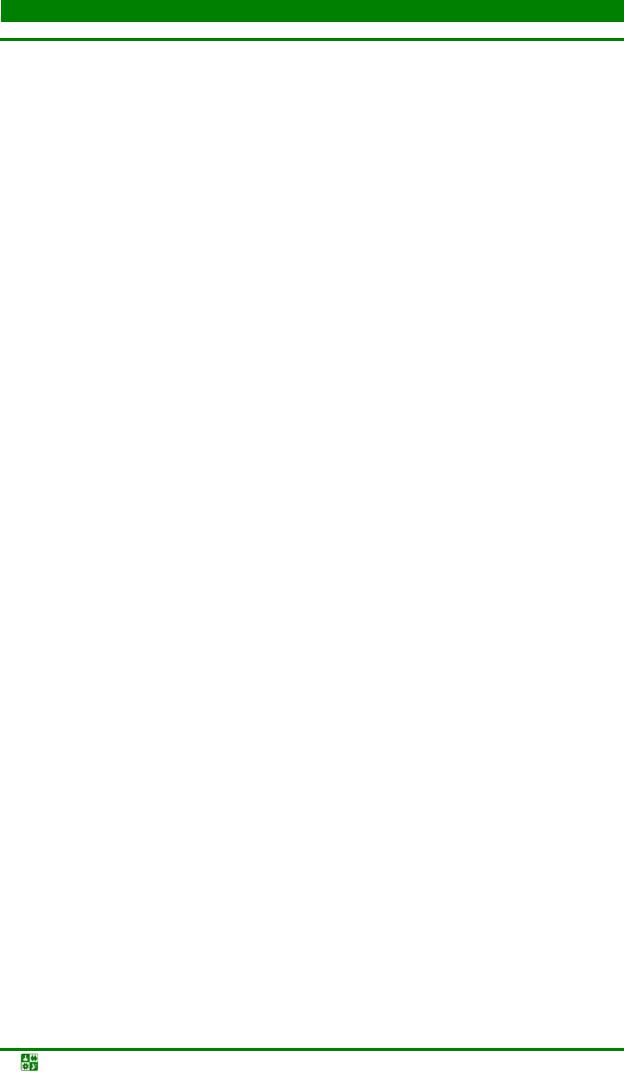
I. ПОЛУЧЕНИЕ ПОРОШКОВ
Лекция 13 Получение порошков вольфрама восстановлением оксидов водородом и углеродом
складывается из последовательно протекающих реакций восстановления промежуточных оксидных соединений.
Восстановление WO3 до W термодинамически возможно при довольно высоких концентрациях паров воды (например, при 800 °С равновесный состав газовой фазы 35 % H2O и 65 % H2), а в условиях, близких к равновесным, реакция протекает медленно. Поэтому в производственных условиях необходимо использовать хорошо осушенный водород, подавая его в печь с большим избытком и скоростью, обеспечивающей удаление паров воды из реакционной зоны.
Восстановление вольфрамового ангидрида ведут в основном в м у- фельных или трубчатых печах при непрерывном проталкивании лодочек с WO3 (высота слоя 20–50 мм) с определенной скоростью вдоль муфеля (трубы) печи; температура вдоль муфеля (трубы) печи постепенно повышается в направлении движения лодочек, а водород подают навстречу им. Таким образом, лодочки с вольфрамовым ангидридом перемещаются в сторону более высоких температур и уменьшающихся концентраций паров воды, что создает наиболее благоприятные условия для последовательных превращений в
ряду WO3–WO2,9–WO2,72–WO2–W.
Скорость восстановления на стадиях WO2,72–WO2 и WO2–W в значительной мере контролируется диффузией паров воды через слой порошка к его внешней габаритной поверхности, что подтверждается расположением слоев образующихся фаз.
В зависимости от условий восстановления как из крупнокристаллического, так и из мелкого порошка WO3 можно получать и мелкие, и крупные порошки вольфрама. Установлено, что решающее влияние на размер частиц вольфрама оказывает размер зерен образующегося WO2, так как из его одного зерна получается, как правило, одно зерно W3. Изучение механизма образования зерен WO2 и, соответственно, W разной величины позволило установить две основные группы явлений:
1)перенос через газовую фазу,
2)кристаллохимические (структурные) превращения в твердых фазах. Так, при определенных условиях восстановление мелкозернистого
вольфрамового ангидрида может приводить к образованию крупных порошков WO2 и W, что объясняется переносом оксидов через газовую фазу: часть загруженного WO3, не успевая полностью восстановиться в низкотемпературных зонах печи, попадает в зону температур более 600 °С и улетучивается в основном в форме соединения WO2,9Н2О, которое при наличии избытка водорода восстанавливается на поверхностях первично образовавшихся зерен WO2 (действует как катализатор), увеличивая их размер.
В ряде случаев (например, для специальных марок твердых сплавов) требуется крупнозернистый порошок вольфрама. Его получают одностадийным высокотемпературным восстановлением при 1 100–1 200 °С, при кот о- ром находящиеся в паровой фазе оксиды вольфрама могут восстанавливаться и непосредственно на поверхности образовавшихся частиц вольфрама, увеличивая их размер.
Процессы порошковой металлургии. Курс лекций |
-101- |
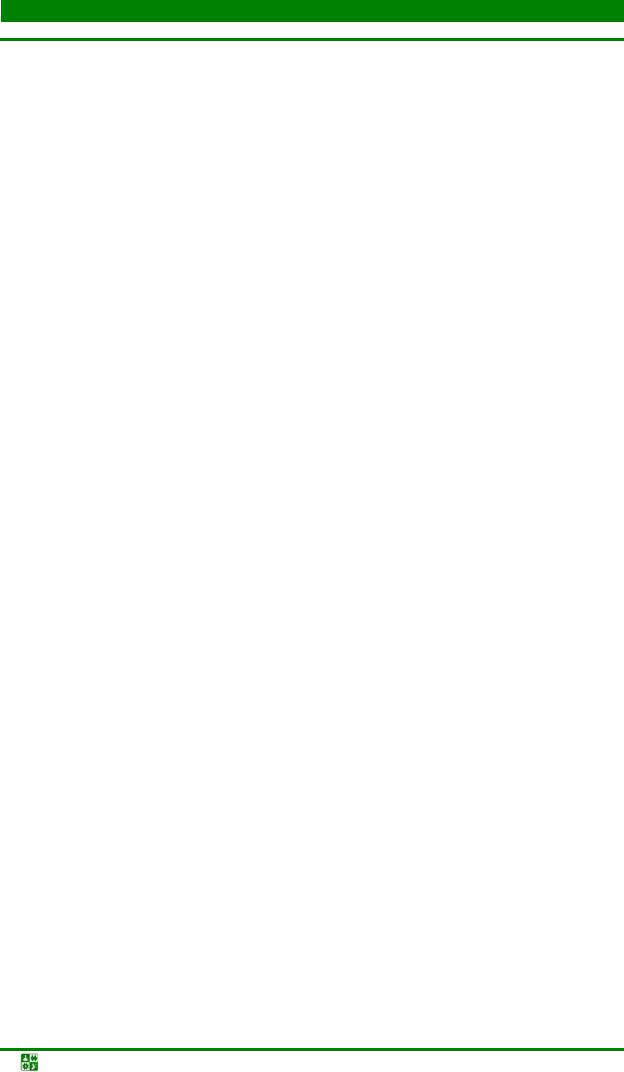
I. ПОЛУЧЕНИЕ ПОРОШКОВ
Лекция 13 Получение порошков вольфрама восстановлением оксидов водородом и углеродом
Получению более крупных частиц вольфрама способствуют следующие технологические факторы:
высокая температура восстановления и быстрое ее повышение по длине печи;
высокий слой WO3 в лодочке; повышенная влажность водорода; малая скорость подачи водорода;
большая скорость продвижения лодочек с WO3 через печное пространство.
Высокий слой вольфрамового ангидрида в лодочке, а также повышенная влажность водорода и малая скорость его подачи в печь задерживают процесс восстановления в низкотемпературных зонах и увеличивают концентрацию оксидов вольфрама в паровой фазе.
Рост частиц WO2 возможен также за счет окислительно-восстанови- тельного переноса оксидов вольфрама в порах порошка. Быстрое развитие реакции восстановления на разветвленных поверхностях частиц оксидов вольфрама в их слое создает в значительной части пор концентрацию влаги, близкую к равновесной для реакции.
Однако для самых мелких, первично образовавшихся частиц WO2, обладающих более высокой поверхностной химической активностью по сравнению с более крупными частицами, концентрация паров воды в некоторых порах порошка может оказаться выше равновесной, отчего мелкие частицы WO2 будут окисляться с образованием летучих оксидов вольфрама и соединений WOx·nH2О.
При нагреве порошка металлического вольфрама в сухом водороде заметного укрупнения зерен не наблюдается вплоть до 1 200 °С. Однако если прокаливание проводить в водороде с примесью паров воды, то при температуре выше 1 000 °C происходит заметное укрупнение частиц порошка вольфрама. Это объясняют тем, что в некоторых порах порошка вольфрама создается достаточная концентрация влаги для окисления самых мелких его частиц, поскольку они обладают более высокой поверхностной энергией, чем крупные частицы. Образующийся WO2 при температуре около 1 200 °С возгоняется и затем восстанавливается водородом на поверхностях крупных частиц вольфрама, увеличивая их размер.
Таким образом, перенос оксидов вольфрама через газовую фазу,уменьшая удельную поверхность образующихся при восстановлении порошков WO2 и W, понижает общий запас свободной поверхностной энергии системы в целом, что и направляет процесс в сторону укрупнения частиц.
Концентрация паров воды, образующихся в порах порошка, зависит от температуры и скорости ее повышения на первой стадии восстановления, скорости подачи водорода в печь, толщины слоя порошка, его газопроницаемости. В свою очередь, эти факторы связаны с удельной поверхностью, насыпной плотностью и химической активностью исходного материала, определяемыми условиями его получения. Повышение температуры восстановле-
Процессы порошковой металлургии. Курс лекций |
-102- |
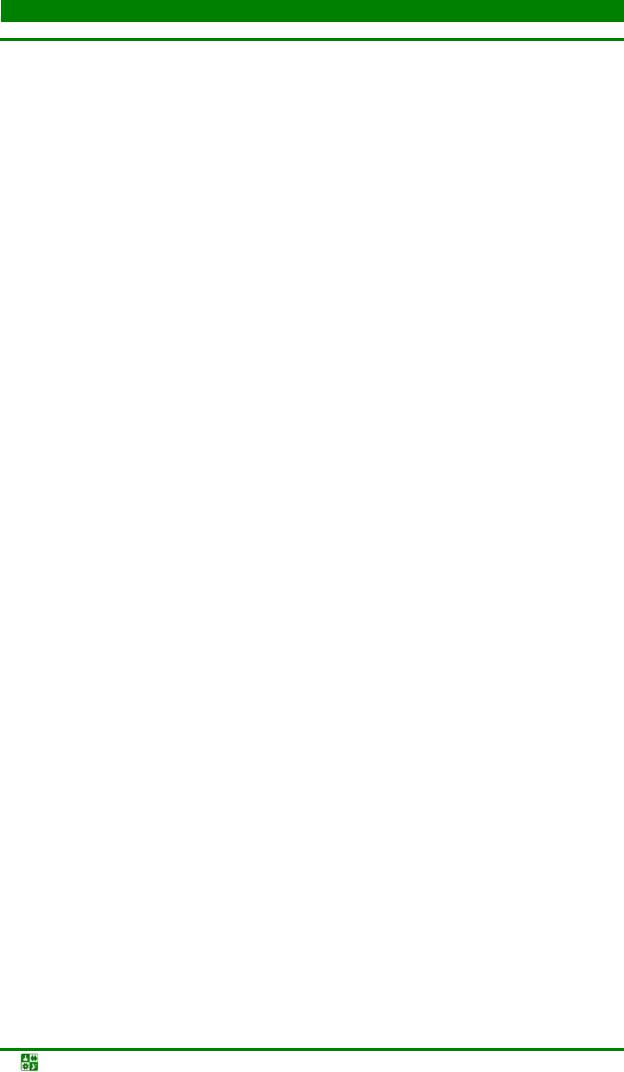
I. ПОЛУЧЕНИЕ ПОРОШКОВ
Лекция 13 Получение порошков вольфрама восстановлением оксидов водородом и углеродом
ния или быстрый ее подъем на стадии образования синего оксида приводит к ускоренному удалению из него атомов кислорода, т.е. к повышению концентрации дефектов в кристалле и увеличению числа возможных центров образования WO2. Поэтому при достаточной скорости противоточной подачи водорода и невысоком слое порошка, т.е. при ограничении концентрации паров воды в его порах, повышение температуры или увеличение скорости ее подъема на первых стадиях восстановления может привести к измельчению образующихся частиц WO2.
Размер частиц восстановленного порошка вольфрама весьма чувствителен к примесям. Некоторые из них, такие как мышьяк и сурьма, ускоряют восстановление, а фосфор в виде фосфорной кислоты заметно повышает требуемую температуру восстановления.
В процессе восстановления WO3 до W объем загрузки лодочки уменьшается более чем вдвое из-за изменяющейся насыпной плотности. Поэтому на практике с целью лучшего использования объема лодочек (следовательно, и объема рабочего пространства печи) восстановление проводят в две стадии: в печах первой группы WO3 восстанавливают до WO2, а затем в п е- чах второй группы WO2 восстанавливают до W. Двухстадийное восстановление облегчает получение порошка вольфрама с нужным набором частиц по размерам. Однако разбивка процесса восстановления на две операции связана с дополнительной загрузкой и выгрузкой порошков, приводящими к увеличению механических потерь металла. Обслуживание большого числа печей также требует значительного числа рабочих.
Наиболее распространено восстановление вольфрамового ангидрида водородом в электропечах либо стационарного толкательнаго типа, либо с вращающейся трубой.
Для получения мелкозернистого (около 95 % частиц размером< 1 мкм) и среднезернистого (около 25 % частиц размером 1–4 мкм, остальные < 1 мкм) порошка вольфрама восстановление ведут в две стадии: первую– при 600–700 °С (получение мелкозернистых порошков вольфрама) или 700–800 °С (полу- чение среднезернистых порошков вольфрама), вторую – при 750–850 или 800–950 °С для мелко- и среднезернистых порошков соответственно. Длительность восстановления на первой стадии в 1,2–2 раза меньше, чем на второй (2–3 ч на первой стадии и 3–4 ч на второй), а масса загрузки в лодочки примерно одинакова.
Использование прямоугольных лодочек обеспечивает бóльшую однородность свойств получаемого порошка вольфрама, чем цилиндрических, благодаря одинаковой высоте насыпки слоя оксида в любом их сечении.
Для получения грубозернистых порошков вольфрама (около 25 % частиц размером 1–4 мкм, до 10 % частиц размером 4–12 мкм, до 10 % частиц размером 12–40 мкм, остальные частицы размером < 1 мкм) восстановление проводят в одну стадию при 1 100–1 200 °С в печи с прямоугольными керамическим (алундовым) муфелем и молибденовым нагревателем.
Процессы порошковой металлургии. Курс лекций |
-103- |
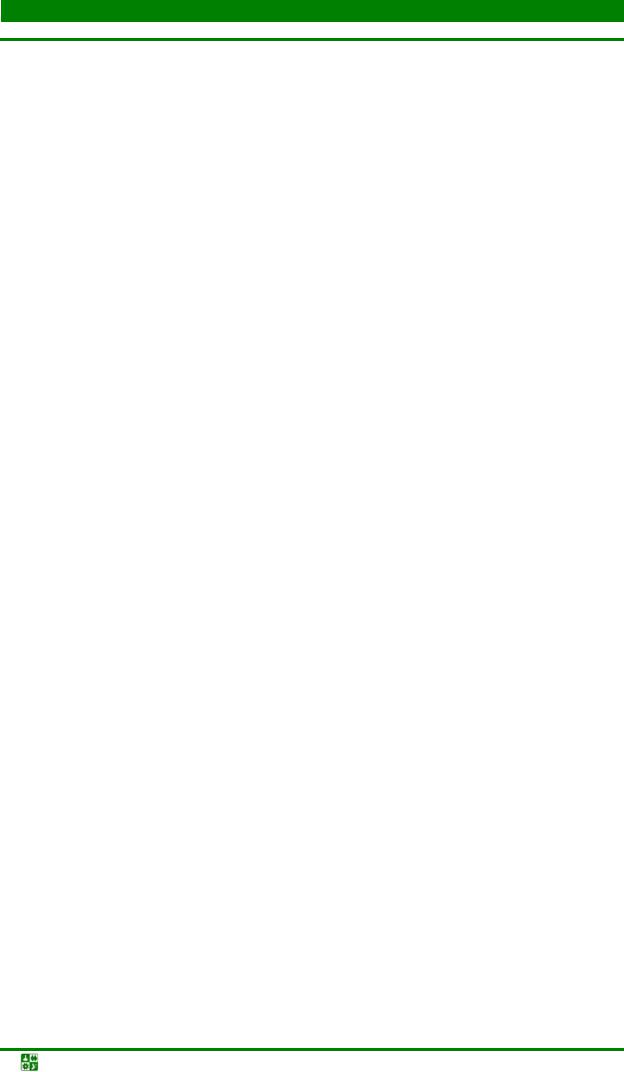
I. ПОЛУЧЕНИЕ ПОРОШКОВ
Лекция 13 Получение порошков вольфрама восстановлением оксидов водородом и углеродом
Во всех случаях в печь восстановления подают водород с большим избытком (до 8–10 раз выше стехиометрически необходимого по реакции взаимодействия с соответствующим оксидом вольфрама).
Прежде чем пустить водород в печь, необходимо очистить ее внутреннее пространство от воздуха. Лучше всего это сделать продувкой азотом (если печь уже разогрета, это обязательно!), хотя холодную печь можно продуть и водородом, но тогда необходима проверка отсутствия в муфеле (трубе) печи гремучей смеси.
Получаемые мелко- и среднезернистые порошки вольфрама, просеивают через сетку № 016-025. Грубозернистый вольфрам размалывают в шаровых вращающихся мельницах и просеивают через сетку № 016-02.
Восстановлениевольфрамовогоангидридатвердымуглеродом
Метод восстановления WO3 сажей используется лишь в том случае, если в вольфраме допустима примесь углерода. Суммарная реакция восстановления имеет вид
WO3 + 3С = W + 3СО |
(1.45) |
В действительности восстановление протекает с участием газообразного СО по схеме, аналогичной приведенной ранее для оксидов железа.
Реакции восстановления углеродом, а точнее его оксидом, проходят через ряд стадий, соответствующих существованию нескольких оксидов вольфрама, причем последней стадией является восстановление низшего оксида вольфрама. Ниже 730 °С WO3 не может быть восстановлен углеродом до металла, так как в равновесных условиях невозможно достичь такой концентрации СО, которая необходима для превращения WO3 в вольфрам.
Чтобы обеспечить высокую концентрацию СО в газовой среде, сдвигающую реакцию в сторону образования вольфрама, а также для ускорения восстановления процесс следует проводить при высоких температурах (выше 1 000 °С), когда газовая фаза состоит почти целиком из СО.
Зернистость порошка вольфрама зависит от технологических режимов восстановления вольфрамового ангидрида. В отличие от восстановления водородом, при углеродном восстановлении мелкозернистые порошки получаются даже при температурах 1 400–1 500 °С. При этом возможно быстрое продвижение лодочек с шихтой в высокотемпературную зону печи, а длительное пребывание шихты в горячей зоне печи не допускается, так как при этом наблюдаются спекание и рост соприкасающихся частиц вольфрама.
При получении мелкозернистого вольфрама в исходную шихту вводят небольшой избыток сажи по сравнению со стехиометрическим количеством, необходимым по реакции, с целью исключения спекания и роста частиц вольфрама при 1 500 °С и выше. Образование мелкозернистого порошка в
Процессы порошковой металлургии. Курс лекций |
-104- |

I. ПОЛУЧЕНИЕ ПОРОШКОВ
Лекция 13 Получение порошков вольфрама восстановлением оксидов водородом и углеродом
таких условиях объясняется наличием в шихте высокодисперсных частиц сажи, являющихся очень хорошим адсорбентом и служащих центрами восстановления. Пары оксидов вольфрама восстанавливаются в первую очередь на поверхностях частиц сажи, а не на поверхностях первичных кристаллов вольфрама или его низших оксидов. Так как число центров восстановления (частиц сажи) очень велико, кристаллы вольфрама возникают в большом числе и оказываются небольших размеров.
Когда требуются крупнозернистые порошки вольфрама, в шихту не вводят избыточного количества сажи и процесс восстановления ведут при более высокой температуре (1 700–1 800 °С).
Восстановление вольфрамового ангидрида углеродом удобнее всего проводить в угольно-трубчатых печах, производительность которых по порошку вольфрама достигает 200 кг/сут.
Контрольныевопросыизадания
1.Назовите основные оксиды вольфрама.
2.Перечислите кристаллические модификации вольфрамового ангидри-
да.
3.Какие факторы способствуют образованию крупнодисперсного порошка вольфрама?
4.Почему получение мелко- и среднедисперсного порошка вольфрама проводят в две стадии?
5.В каком случае допускается восстановление вольфрамового порошка углеродом?
6.Что добавляют в вольфрамовый ангидрид при его восстановлении углеродом для получения мелких порошков?
Лекция14 Получениепорошковмолибдена, титанаициркония
восстановлениемхимическихсоединений
План лекции
1.Технология получения порошков молибдена.
2.Методы получения порошков титана.
3.Методы получения порошков циркония.
Технологияполученияпорошковмолибдена
Исходным материалом служит чистый триоксид молибдена МоО3, получаемый прокаливанием при 450–500 °С парамолибдата аммония (3(NH4)2O× × 7MoO3·4H2O) в муфельных печах или печах с вращающейся трубой. Про-
Процессы порошковой металлургии. Курс лекций |
-105- |
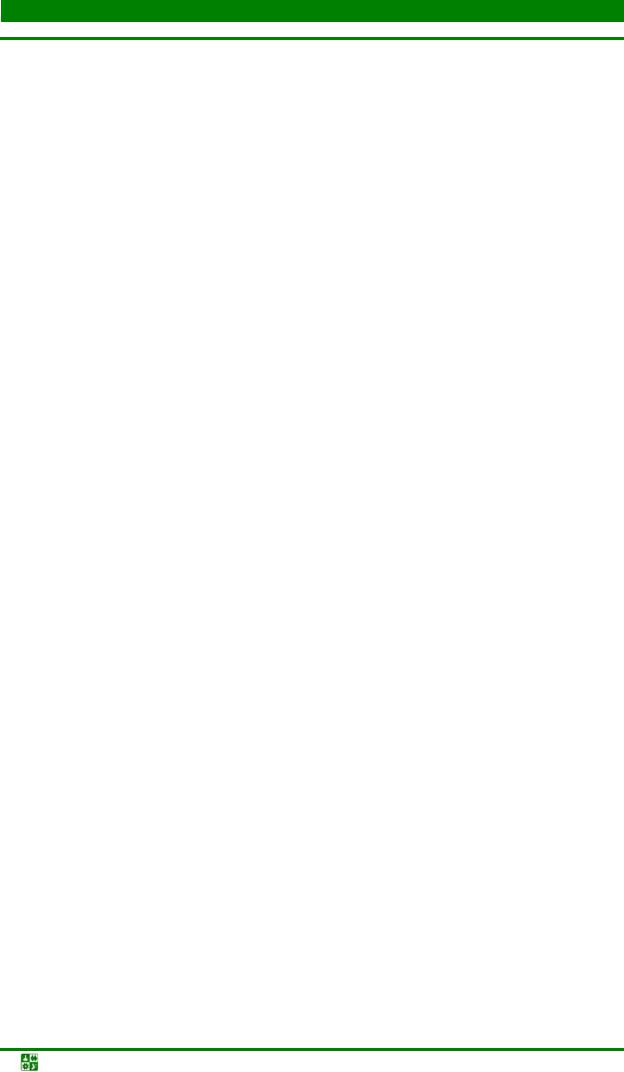
I. ПОЛУЧЕНИЕ ПОРОШКОВ
Лекция 14 Получение порошков молибдена, титана и циркония восстановлением химических соединений
цесс образования триоксида молибдена из парамолибдата протекает по следующей схеме:
90−100С о |
200Со |
|
(NH4)6Mo7O24 ·4H2O →(NH4)6Mo7O24 → |
|
|
200Со |
280−450С о |
(1.46) |
→ (NH4)2Mo4O13 |
→ Mo7O24 |
Промышленный способ производства порошка молибдена предусматривает восстановление МоО3 хорошо осушенным водородом. Этот процесс реально протекает по схеме МоО3–МоО2–Мо, хотя молибден с кислородом образует и промежуточные оксиды Мо4О11, Мо8О23 и др.
Первую стадию восстановления МоО3–МоО2 проводят при более низкой температуре (400–650 °С), чем восстановление WО3 до WО2. Для того чтобы образование МоО2 закончилось при температуре 500–550 °С, приходится обеспечивать медленное повышение температуры по длине печи (многотрубчатой горизонтальной или с наклонной вращающейся трубой). При несоблюдении этого температурного режима произойдет расплавление материала, связанное с образованием плавящейся при 550–600 °С эвтектики системы МоО3–МоО2 (возможно Мо4О11–МоО2).
Вторую стадию восстановления МоО2–Мо проводят в трубчатых или муфельных горизонтальных печах при 650–950 °С хорошо осушенным водородом (точка росы не ниже –40 °С) при его многократном избытке; движение лодочек должно быть замедленным, чтобы в результате длительного пребывания в высокотемпературной зоне (850–950 °С) получаемый порошок молибдена содержал не более 0,1–0,2 % О.
Скорость продвижения лодочек на второй стадии восстановления в 2–2,5 раза меньше, чем на первой стадии, а скорость водорода – в 1,5–2 раза выше. Для увеличения производительности печи на второй стадии движение лодочек можно ускорить, но тогда порошок молибдена будет содержать до 0,5–1,5 % О. В этом случае потребуется дополнительное третье восстановление при 1 000–1 100 °С, после которого содержание кислорода в порошке не превышает 0,2 %. Условия восстановления не благоприятствуют образованию заметных концентраций паров МоО3 в более высокотемпературных зонах печи, в связи с чем молибденовый порошок получается обычно более мелкозернистый (размер частиц до 2–3 мкм), чем вольфрамовый.
Первые две стадии восстановления проводят в тех же условиях и на том же оборудовании, что и при получении порошка вольфрама. Третью стадию восстановления осуществляют в печах, стальные трубы которых помещены в герметичный кожух, заполненный водородом (хромоникелевые стали не выдерживают длительной эксплуатации на воздухе при 1 000–1 100 °С). Защитная среда предохраняет от заметного окисления также и нихромовые нагреватели или нагреватели из жаростойких железохромалюминиевых сплавов (фехраль и др.). Иногда третью стадию восстановления проводят в печах
Процессы порошковой металлургии. Курс лекций |
-106- |
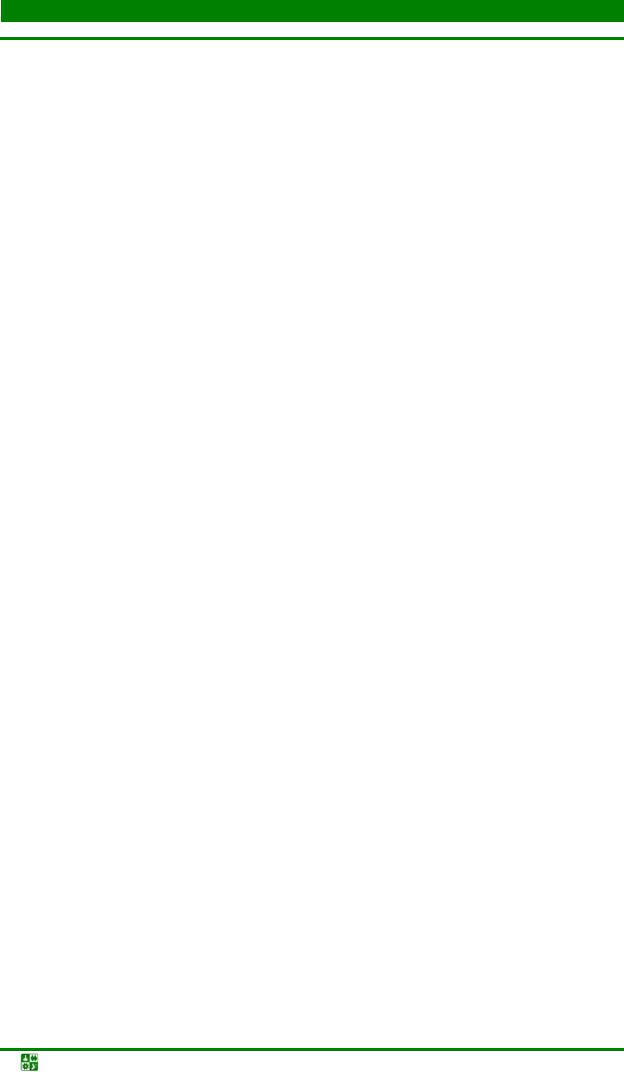
I. ПОЛУЧЕНИЕ ПОРОШКОВ
Лекция 14 Получение порошков молибдена, титана и циркония восстановлением химических соединений
с алундовой трубой или муфелем и молибденовым нагревателем, работающим в водородной среде.
Методыполученияпорошковтитана
Для получения порошков титана используют следующие методы: восстановление диоксида титана кальцием или его гидридом; восстановление хлорида титана натрием или его гидридом.
Восстановление диоксида титана кальцием. Сродство титана к ки-
слороду высоко, что предопределяет необходимость применения наиболее активного восстановителя – кальция, который должен быть химически чистым, прежде всего по азоту (допустимое содержание не более 0,15 %) из-за опасности азотирования частиц порошка титана.
Восстановление проходит по суммарной реакции
ТiО2 + 2Са = Тi + 2СаО + Q |
(1.47) |
Кальций берут с избытком 25–100 % по сравнению с требуемым п о реакции, что обеспечивает достаточную полноту восстановления диоксида титана. Термичность этой реакции невелика, и для ее успешного проведения необходим внешний подогрев. На практике используют температуры 1000–1 100 °С, при которых жидкий кальций достаточно хорошо контактирует с частицами; этому также способствует и большое давление паров кальция при указанных температурах процесса восстановления (при 1 000 °С и Р = 15 гПа).
Во время реакции вместе с частицами титана образуется оксид кальция, препятствующий их укрупнению, в результате чего получаемый порошок титана мелкий (размер частиц 2–3 мкм). При последующей отмывке водой или слабой кислотой от СаО и избыточного кальция такой мелкозернистый порошок заметно окисляется (суммарная поверхность частиц велика), и содержание кислорода в нем составляет до 0,3 %. Поэтому стараются вести процесс таким образом, чтобы в результате восстановления получился более крупный порошок, окисляющийся в меньшей степени.
Для этих целей в исходную шихту в качестве флюса чаще всего добавляют хлористый кальций, который при указанных температурах расплавляется и растворяет СаО (при 1 000 °С в СаС12 растворяется 25 % СаО), частично или полностью переводя его в расплав.
Получаемый порошок титана имеет размер частиц 10–15 мкм и более. Действие СаС12 не ограничивается только растворением СаО, а изменяет механизм восстановления: в жидком СаС12 происходит частичное растворение ТiО2 (при 1 000 °С несколько процентов) с образованием небольших количеств ТiС14 и низших хлоридов титана.
Чтобы избежать возможного окисления и нитрирования образующегося титана, восстановление осуществляют в герметичном реакторе из жаро-
Процессы порошковой металлургии. Курс лекций |
-107- |
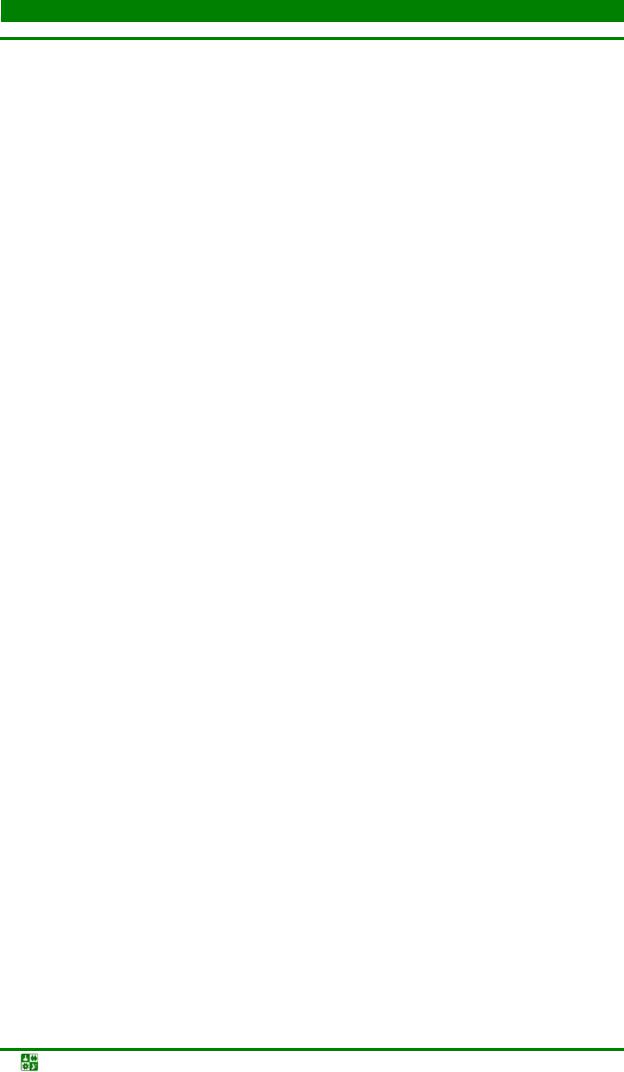
I. ПОЛУЧЕНИЕ ПОРОШКОВ
Лекция 14 Получение порошков молибдена, титана и циркония восстановлением химических соединений
стойкой стали, который после загрузки брикетированной смеси ТiО2 с кальцием (в виде стружки) и откачки воздуха заполняют аргоном. Процесс можно вести в вакууме, но разрежение будет способствовать частичному (а при наличии холодной верхней крышки реактора и значительному) удалению газообразного кальция из зоны реакции. Кроме того, при наличии вакуума усложняется конструктивная задача герметизации крышки реактора. Для нагрева реактора с шихтой чаще используют тигельные печи с силитовыми нагревателями.
После выдержки при 1 000–1 100 °С в течение 1 ч реактор вынимают из печи и, дав ему остыть, выгружают из него сплав с вкраплениями частиц металла. Сплав измельчают и обрабатывают большим избытком холодной воды во избежание сильного разогрева в процессе гашения оксида кальция и избыточного кальция. Затем его промывают разбавленной кислотой (уксусной, соляной или азотной) до полного растворения хлористого кальция, гидроксида кальция и металлического кальция (если сохранился). После отмывки порошок титана подвергают сушке в вакуумном шкафу.
Для снижения расхода дорогостоящего кальция предложен комбинированный процесс: первоначальное восстановление ТiО2 осуществляют магнием, а затем, после кислотной отмывки образовавшегося оксида магния, полученный продукт восстанавливают кальцием.
Восстановление диоксида титана гидридом кальция. Разновидностью кальцийтермического метода получения порошка титана является восстановление ТiО2 гидридом кальция. Особенностью этого метода является возможность получения порошка титана и его гидрида, который при водной и кислотной обработках окисляется меньше, чем чистый металл.
Спекание в вакууме брикета, спрессованного из порошка гидрида титана, идет более активно, чем спекание брикета из порошка металлического титана, так как при диссоциации гидрида создаются контакты между частицами по свежим, активным металлическим поверхностям.
В некоторых случаях гидрид титана находит и непосредственное техническое применение, например для раскисления при изготовлении сплавов, при пайке неметаллических материалов друг с другом и с металлами (в частности, при пайке кремниевых деталей в полупроводниковой технике), в качестве источников чистейшего водорода в некоторых приборах электровакуумной техники и т.д.
При температуре выше 800 °С гидрид кальция полностью разлагается на кальций и водород.
Суммарную реакцию восстановления диоксида титана гидридом кальция можно записать в виде
ТiО2 + 2СаН2 = Тi + 2СаО + 2Н2 |
(1.48) |
Процессы порошковой металлургии. Курс лекций |
-108- |
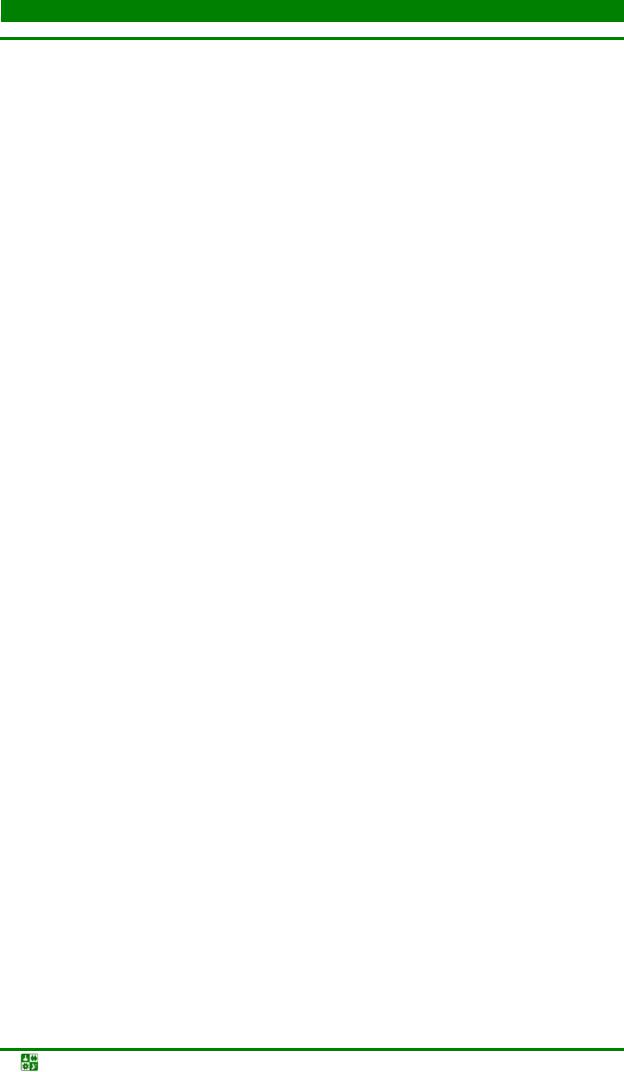
I. ПОЛУЧЕНИЕ ПОРОШКОВ
Лекция 14 Получение порошков молибдена, титана и циркония восстановлением химических соединений
Первый этап реакции протекает при проведении процесса восстановления в реакторе, заполненном водородом. Исследования показали, что основным восстановителем является кальций, а не атомарный водород, образовавшийся в первый момент при диссоциации СаН2.
Восстановление ТiО2 гидридом кальция ведут примерно при тех же температурах, что и восстановление кальцием, с использованием аналогичных реакторов и приемов последующей обработки спека.
Восстановление хлорида титана натрием или магнием. Металличе-
ский титан впервые был получен в 1910 г. восстановлением его тетрахлорида натрием, имеющим высокое сродство к хлору. Четыреххлористый титан – сравнительно дешевый и недефицитный продукт, получаемый хлорированием рудных концентратов рутила, ильменита или продуктов их первичной обработки (например, шлаков или карбидов).
Впромышленной практике восстановление ТiС14 натрием ведут в интервале 801–883 °С, ограниченном точкой плавления хлористого натрия и температурой кипения натрия. Взаимодействие должно происходить между
газообразным ТiС14 и жидким натрием. Однако в действительности процесс протекает с участием образующихся низших хлоридов титана, которые растворяются в хлористом натрии.
Частицы титана образуют в расплаве сростки. Отметим, что восстановление протекает не только в расплаве, но и в газовой фазе.
Современный промышленный процесс восстановления ведут в герметичном реакторе из нержавеющей стали, заполненном аргоном и нагретом в печи до 500–600 °С. В реактор одновременно подают ТiС14 и жидкий натрий
всоотношении, близком к стехиометрическому для реакции – на 2,06 кг
ТiС14 1 кг Nа. Через некоторое время, когда в реторте накопится жидкий расплав, печь отключают и ведут процесс за счет теплоты реакции, поддерживая температуру 850–880 °С (реактор обдувают воздухом, отводя избыточное тепло).
Впервый период восстановление в большей мере идет в газовой фазе с образованием мелких частиц титана и его низших хлоридов. Хлориды растворяются в NаС1 и восстанавливаются в расплаве натрием с образованием частиц титана, оседающих на дне реактора.
Для обеспечения полноты восстановления низших хлоридов титана и укрупнения частиц металла в конце процесса включают печь и выдерживают реактор при 950–1 000 °С в течение 4–6 ч. Остывшую реакционную массу (17 % Тi, 83 % NaС1) и небольшое количество непрореагировавшего натрия) выбирают из реактора на станке специальной фрезой, пропускают через грохот с отверстиями 10 мм, измельчают и выщелачивают водой, подкисленной соляной кислотой (до 1 %). Затем титановый порошок отделяют от раствора на центрифуге и сушат в вакуумной сушилке.
Применяют и другую технологическую схему процесса, при которой
жидкий ТiС14 и расплавленный натрий подают в реактор с температурой 850–900 °С после разогрева и плавления эвтектической смеси NaС1 + КС1.
Процессы порошковой металлургии. Курс лекций |
-109- |
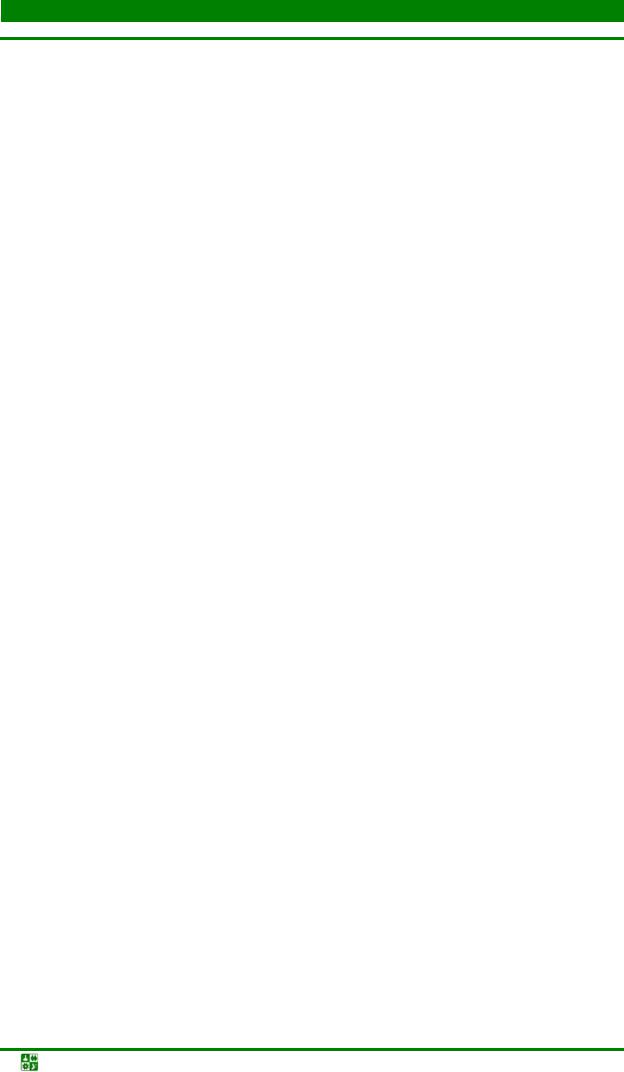
I. ПОЛУЧЕНИЕ ПОРОШКОВ
Лекция 14 Получение порошков молибдена, титана и циркония восстановлением химических соединений
Более экономичен процесс восстановления ТiС14 магнием (процесс Крапля). Реакционное взаимодействие протекает по суммарной реакции
ТiС14 + 2Мg = 2МgС12 + Тi + Q |
(1.49) |
Этим способом получают большую часть производимого в мире титана, правда, в виде губки, а не порошка.
Можно заменить магний его легкоплавким (температура плавления около 500 °С) эвтектическим сплавом c кальцием (82 % Мg, 18 % Са). Такой сплав в виде порошка или дроби подают в верхнюю часть камеры, заполненной парами тетрахлорида титана. Реакция протекает настолько быстро, что за время опускания сплава-восстановителя на дно камеры процесс заканчивается и продукты реакции успевают охладиться; титан образуется в форме тонкого порошка высокой чистоты.
Восстановление титана можно проводить из газовой фазы в результате взаимодействия паров ТiС14 с парами магния, разбавленными инертным газом. Продукты реакции переносятся потоком аргона из реактора в зону быстрого охлаждения, откуда они выходят в виде свободно текущего порошка.
Методыполученияпорошковциркония
Для получения порошков циркония используют восстановление диоксида циркония кальцием или его гидридом, а также восстановление фтороцирконата калия натрием.
Восстановление диоксида циркония кальцием или его гидридом.
Реакцию
ZrO2 + 2Са = Zr + 2СаО |
(1.50) |
проводят в герметичном реакторе, заполненном аргоном, при 1 000–1 100 °С. Для снижения содержания кислорода берут кальций с избытком 50–100 % и применяют длительные выдержки при восстановлении. Для регулирования зернистости получающегося порошка циркония в шихту можно добавлять хлористый кальций. После охлаждения спек извлекают из реактора, измельчают и обрабатывают в избытке дистиллированной воды, отмывая избыточный кальций и образовавшийся его оксид, а также СаС12 (если он был введен в шихту).
Восстановление проводят при 900–1 000 °С в атмосфере сухого водорода. При остывании спека в атмосфере водорода получают порошок гидрида циркония. При продувании реактора аргоном в конце восстановления и
Процессы порошковой металлургии. Курс лекций |
-110- |
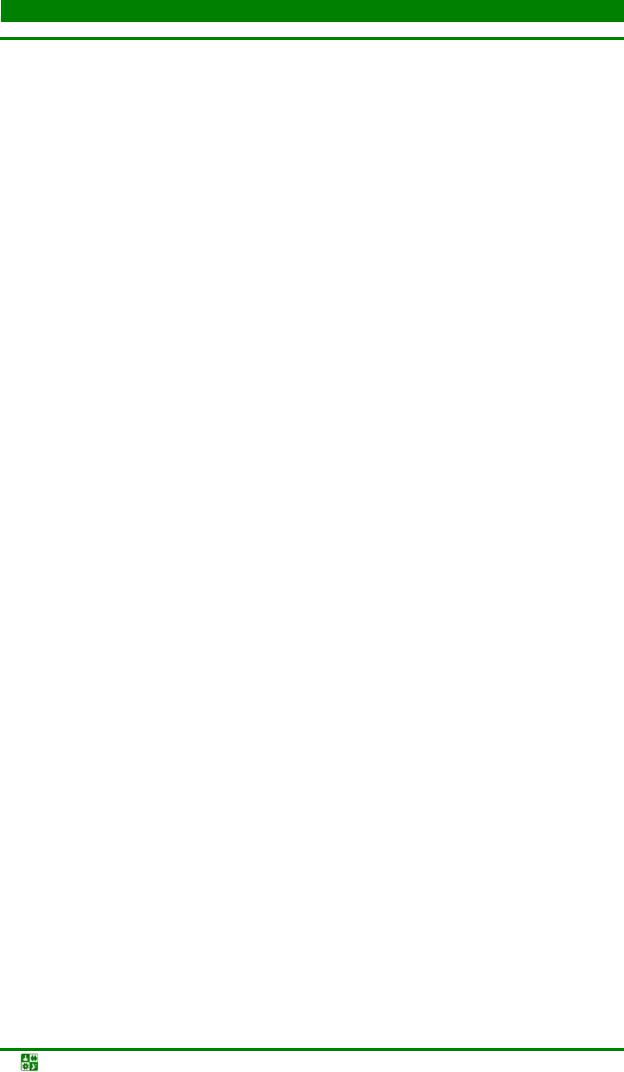
I. ПОЛУЧЕНИЕ ПОРОШКОВ
Лекция 14 Получение порошков молибдена, титана и циркония восстановлением химических соединений
последующем остывании спека в аргоне получают порошок циркония с минимальным содержанием водорода.
При хранении порошка циркония необходимо соблюдать особую осторожность из-за его чрезвычайно высокой пирофорности; емкость с порошком целесообразно заполнить дистиллированной водой.
Восстановление фтороцирконата калия натрием. Если порошок циркония предназначен для непосредственного использования в пиротехнике или в качестве геттера в электровакуумной технике, то его можно получать восстановлением фтороцирконата калия К2ZrF6 натрием, К2ZrF6 не гигроскопичен и поэтому устойчив на воздухе.
Обычно восстановление проводят при 15–20 %-м избытке натрия в герметичных стальных реакторах в вакууме или в аргоне при 800–900 °С.
После охлаждения спек выбивают из реактора пневматическим молотком, обрабатывают его водой или раствором NH4С1 для растворения остатков натрия, измельчают в воде в шаровых мельницах и выщелачивают KF и NaF водой в реакторах с мешалкой.
Во избежание возгорания остатков натрия и образующегося при его отмывке водорода измельченный спек подают в воду или в раствор хлористого аммония небольшими порциями. Для отмывки от железа порошок циркония обрабатывают разбавленной соляной кислотой, промывают водой, фильтруют и сушат в вакууме при 60 °С.
Контрольныевопросыизадания
1.Какой восстановитель используют при получении порошков мо-
либдена?
2.В чем заключается особенность технологической схемы получения порошков молибдена?
3.Для чего используют третий этап восстановления оксидов молибде-
на?
4.Какие печи используют при восстановлении оксидов молибдена?
5.Перечислите методы получения порошков титана.
6.Чем восстанавливают хлорид титана?
7.Назовите методы получения порошков циркония.
Лекция15 Получениепорошковтантала, ниобия, меди,
кобальта, никеляилегированныхсплавов
План лекции
1.Методы получения порошков тантала и ниобия.
2.Методы получения порошков меди, кобальта и никеля.
3.Получение легированных порошков.
Процессы порошковой металлургии. Курс лекций |
-111- |
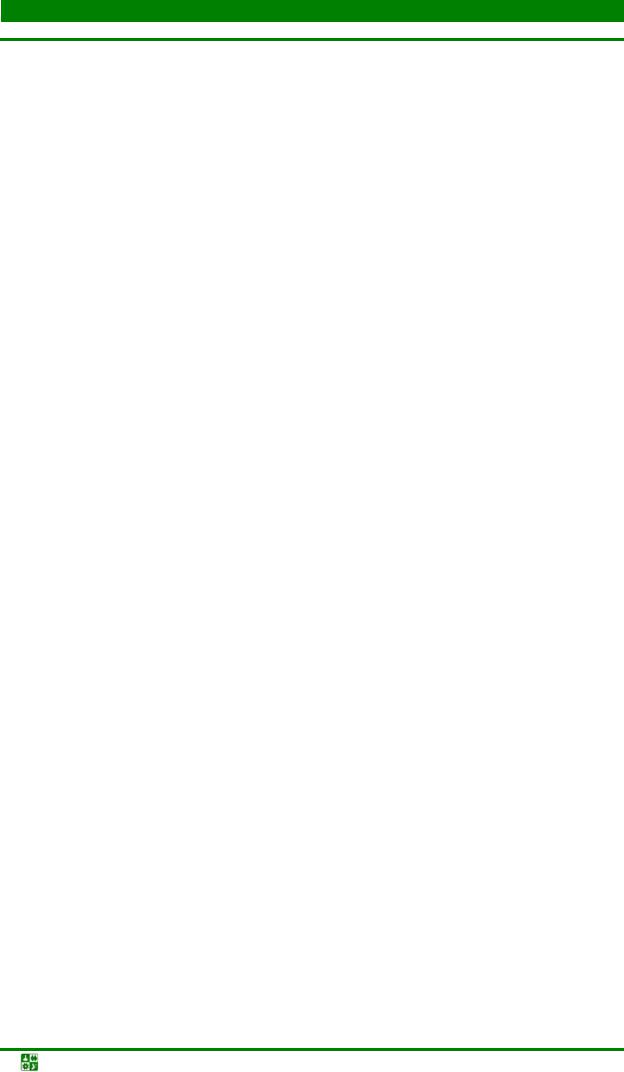
I. ПОЛУЧЕНИЕ ПОРОШКОВ
Лекция 15 Получение порошков тантала, ниобия, меди, кобальта, никеля и легированных сплавов
Методыполученияпорошковтанталаиниобия
Порошки тантала получают восстановлением фторотанталата калия натрием или хлорида тантала магнием.
Восстановление фторотанталата калия натрием. Восстановление
K2TaF7 натрием является одним из наиболее распространенных промышленных методов получения порошка тантала. Реакция восстановления имеет вид
K2TaF7 + 5Nа = Та + 5NaF + 2КF |
(1.51) |
Если шихту K2TaF7 + 5Nа, загруженную в тигель, подогреть через стенку в одном месте до 450–500 °С, то начавшаяся реакция быстро распространится по всему объему материала.
Восстановление проводят в стальном тигле, куда послойно загружают указанную фтористую соль и натрий. Для обеспечения полноты восстановления берут 20–50 %-й избыток натрия посравнению с теоретически необходимым.
Поверх шихты насыпают слой хлористого натрия, который с фтористым натрием и фтористым калием, получающимися в результате реакции при восстановлении, образует низкоплавкую смесь, предохраняющую танталовый порошок от взаимодействия с атмосферой. Это позволяет проводить восстановление в реакторе без его герметизации и без подачи в него защитного газа.
После окончания процесса металлический тантал находится в спеке в виде частиц размером до 3 мкм (размер основной массы частиц < 0,6 мкм).
После охлаждения реакционной массы эти частицы оказываются вкрапленными в застывший солевой расплав, в котором находится также оставшийся неиспользованным избыток металлического натрия. Всю эту массу выгружают из реактора, измельчают и небольшими порциями при перемешивании загружают в емкость с большим избытком холодной воды.
Металлический натрий взаимодействует с водой (образуется раствор едкого натра и выделяется водород), а большая часть солей растворяется. Затем порошок тантала отделяют от образовавшегося водного раствора, промывают разбавленной соляной кислотой и снова водой, но уже дистиллированной, отфильтровывают и сушат при 110–120 °С.
Извлечение тантала из исходного фторотанталата калия в порошок составляет 90–94 %. Качество порошка тантала можно улучшить, если проводить процесс восстановления при нагреве тигля (реактора) с шихтой в печи, выдерживая некоторое время по завершении процесса при 1 000 °С.
Восстановление хлорида тантала магнием. Технология такого про-
цесса подобна описанной выше для титана и основана на реакции
2ТаС15 + 5Мg = 2Та + 5МgС12 + Q |
(1.52) |
Процессы порошковой металлургии. Курс лекций |
-112- |
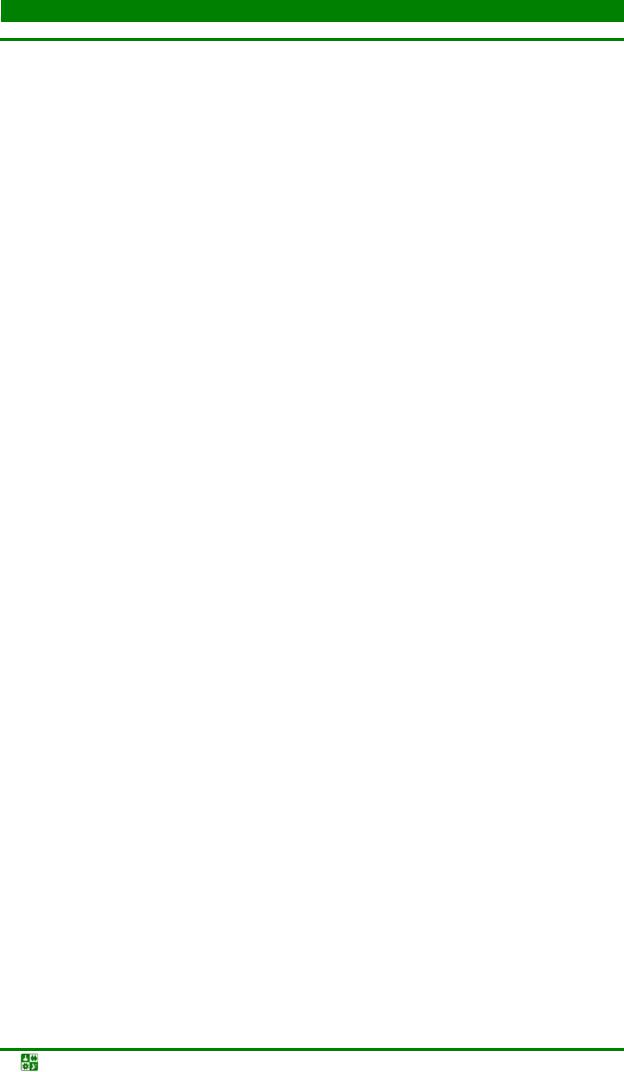
I. ПОЛУЧЕНИЕ ПОРОШКОВ
Лекция 15 Получение порошков тантала, ниобия, меди, кобальта, никеля и легированных сплавов
Реактор (тигель) со смесью ТаС15, магниевой стружки и флюса (хлориды натрия и калия) загружают в шахтную печь, разогретую до 750 °С.
Реакция протекает быстро. Порошок тантала отмывают от хлористых солей и избытка магния, обрабатывая сначала водой, а затем разбавленной соляной кислотой. Извлечение тантала в порошок составляет примерно 98 %, а размер его частиц – 1–10 мкм.
Аналогично описанному можно получать порошок ниобия из NbCl5. Также для получения порошков ниобия можно использовать восстановление фторониобата калия натрием или пентаоксида ниобия углеродом.
Восстановление фторониобата калия натрием. Процесс восстанов-
ления
K2NbF7+ 5 Nа = Nb + 2КF + 5NаF |
(1.53) |
ведут в стальном тигле, в который послойно загружают шихту, содержащую избыток натрия (15–20 %). Сверху шихту засыпают слоем хлористого натрия. Тигель загружают в разогретую до 600 °С шахтную печь и выдерживают в течение 1,0–1,5 ч при 900–1 000 °С. В дальнейшем порошок отмывают водой (сначала холодной, а затем горячей), разбавленной азотной или соляной кислотой (для удаления железа, частично титана и других примесей) и 2,5 %-й холодной плавиковой кислотой (для уменьшения содержания оксида ниобия). Время обработки раствором плавиковой кислоты не превышает 5–15 мин.
Порошок ниобия худшего качества может быть получен из оксифторониобата калия (K2NbOF6) в условиях, подобных вышеописанным.
Восстановление пентаоксида ниобия углеродом. Ниобий может быть получен восстановлением Nb2O5 углеродом при 1 800–1 900 °С в вакууме (остаточное давление < 1,3 Па) по суммарной реакции
Nb2O5 +5С = 2Nb + 5СО |
(1.54) |
На практике проводят восстановление пентаоксида ниобия углеродом в две стадии с участием образующегося на первой стадии карбида ниобия (способ называют карботермическим).
Такой двухстадийный процесс имеет следующие преимущества перед одностадийным восстановлением:
первую стадию можно проводить в угольно-трубчатых печах сопротивления при атмосферном давлении;
вторая стадия идет со значительно большей производительностью вакуумной печи.
Процессы порошковой металлургии. Курс лекций |
-113- |
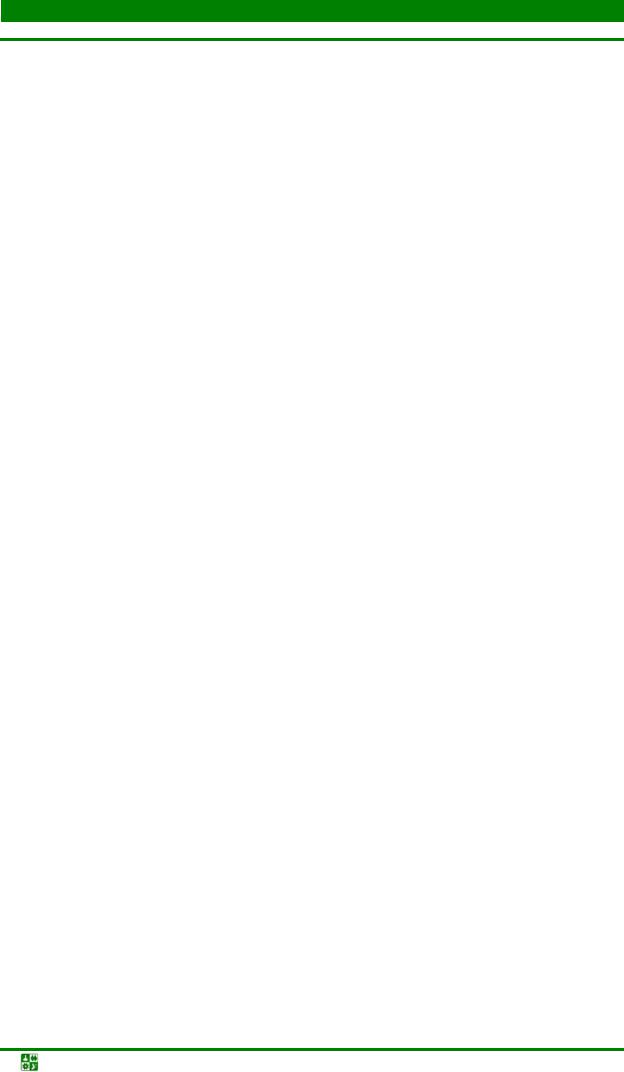
I. ПОЛУЧЕНИЕ ПОРОШКОВ
Лекция 15 Получение порошков тантала, ниобия, меди, кобальта, никеля и легированных сплавов
На первом этапе восстановления (при температуре 1 100–1 300 °С),
врезультате взаимодействия Nb2O5 с углеродом образуется NbO2. При этом
впроцессе восстановления образуется карбид ниобия NbС (по реакции
Nb2С + С = 2NbС). Взаимодействие карбида с NbO2 на втором этапе восстановления, приводит к образованию сначала NbО, а затем и Nb.
Вблизи температуры плавления (1 532 °С) Nb2O5 диссоциирует, и выделяющийся кислород соединяется с углеродом. В присутствии оксидов нио-
бия его высший карбид NbС разлагается на Nb2С и углерод, взаимодействующие с оксидами ниобия. Пары оксидов ниобия адсорбируются на частицах углерода и карбидов ниобия, где и восстанавливаются.
Получение карбида ниобия из Nb2O5 ведут при 1 800 °С, проталкивая через печь графитовые патроны с шихтой Nb2O5 + 7С за 1,0–1,5 ч. Слегка спекшийся карбид ниобия измельчают в порошок и смешивают его с Nb2O5, взятым с избытком 3–5 % против требуемого по реакции. Затем эту смесь спрессовывают в брикеты при давлении 100 МПа и прокаливают в вакуумной печи при 1 900 °С и остаточном давлении 1,3–0,13 Па в течение 6 ч.
Карботермический способ можно использовать для получения порошков сплавов ниобия с танталом и другими тугоплавкими металлами, восстанавливая смесь соответствующих оксидов.
Методыполученияпорошковмеди, кобальтаиникеля
Получение порошков меди. Порошок меди может быть получен твердофазным взаимодействием ее кислородсодержащих соединений или солей с реагентом-восстановителем.
Сырьем обычно служат окалина, образующаяся при производстве медного проката или проволоки, или высший оксид меди СuО, а восстановителем – либо газ (водород, конвертированный природный газ, диссоциированный аммиак), либо твердый углерод (графит, древесный уголь). Основными компонентами окалины являются металлическая (70–75 %) и оксидная (30–25 %) фазы, она, как правило, содержит до 4,0–4,5 % влаги и загрязнена техническими маслами (до 1,0–1,5 %).
Оксиды меди легко восстанавливаются водородом при 300–400 °С и выше по реакции
CuO + H2 = Cu + H2O |
(1.55) |
Реакция является автокаталитической. В начальный период восстановления скорость реакции незначительна из-за невысокой скорости хемосорбции водорода (протекает в первую очередь на активных участках поверхности оксида меди). По мере возрастания степени дефектности структуры оксидов меди и образования новых участков активации процесса реак-
Процессы порошковой металлургии. Курс лекций |
-114- |
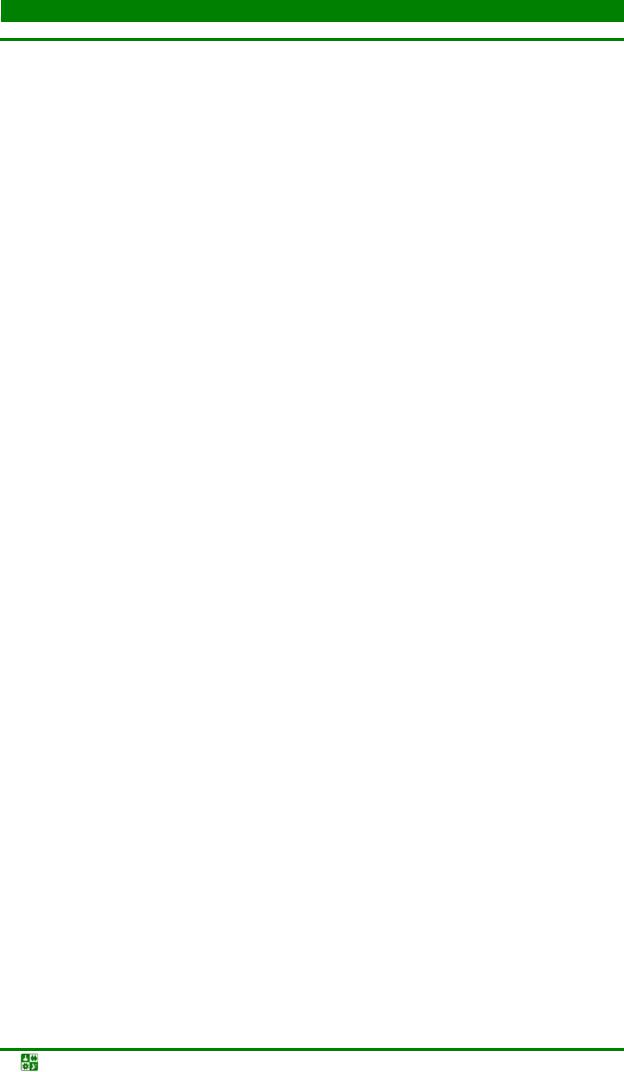
I. ПОЛУЧЕНИЕ ПОРОШКОВ
Лекция 15 Получение порошков тантала, ниобия, меди, кобальта, никеля и легированных сплавов
ции первичного взаимодействия ускоряются и заканчиваются образованием металлической фазы.
Ее появление приводит к увеличению поверхности раздела фаз CuO–Cu2O, что ускоряет процессы хемосорбции и атомизации водорода на свежевосстановленной поверхности оксида меди и повышает скорость суммарной реакции. Однако утолщение образующейся металлической пленки вызывает уменьшение скорости процесса восстановления.
Для восстановления оксида меди чаще всего используют проходные муфельные или трубчатые печи непрерывного действия с внешним электрообогревом (идентичные или аналогичные печам для получения порошков вольфрама или молибдена). Толщина слоя материала в лодочке (поддоне) составляет 20–30 мм. Перед восстановлением окалину обычно обжигают в окислительной атмосфере при 250–300 °С (возможен обжиг при 550–600 °С) и размалывают до крупности < 100 мкм. Восстановление проводят при 550–650 °С водородом или конвертированным природным газом. Полученный медный порошок измельчают и рассевают; он имеет насыпную плотность 2,2–3,4 г/см3 и частицы размером<100 мкм (преимущественно < 50 мкм).
Известен способ получения порошка меди комбинированным восстановлением окалины газообразным и твердым (графит) восстановителями. Окалину сушат, измельчают, смешивают с графитом, усредняют и восстанавливают при 600 °С. Порошки имеют частицы губчатой формы и пригодны для производства некоторых фрикционных изделий.
Получение порошков кобальта. Оксид кобальта Со2О3 или Со3О4 вос-
станавливают водородом в трубчатых или муфельных электропечах при 500–700 °С в течение 3–5 ч:
Со2О3 |
+ 3H2 |
= 2Со + 3H2O |
(1.56) |
или |
|
|
|
Со3О4 |
+ 4H2 |
= 3Со + 4H2O |
(1.57) |
Мягкие, легко рассыпающиеся брикеты при растирании и просеве на вибросите через сетку 004 превращаются в порошок с частицами размером 1–5
мкм, насыпной плотностью < 0,75 г/см3 и содержанием кислорода ≤ 0,7 %. Получение порошков никеля. Оксид никеля NiO восстанавливают во-
дородом или водородсодержащим газом при 700–750 °С в течение 1–2 ч по реакции
NiО + Н2 = Ni + Н2О |
(1.58) |
Полученный спек (никелевую губку) дробят и рассевают на фракции. Так как кобальт является структурным аналогом никеля, то полученный по-
Процессы порошковой металлургии. Курс лекций |
-115- |
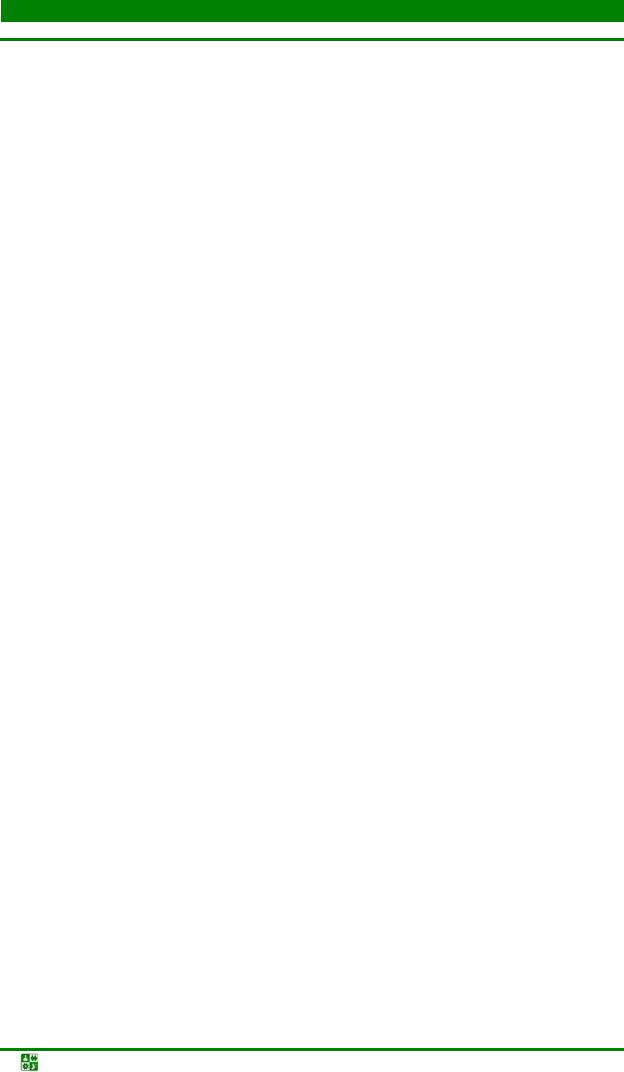
I. ПОЛУЧЕНИЕ ПОРОШКОВ
Лекция 15 Получение порошков тантала, ниобия, меди, кобальта, никеля и легированных сплавов
рошок никеля содержит небольшое количество этого металла (около 0,5 %). Суммарное содержание Ni и Со в порошке составляет не менее 99,5 %.
Получениелегированныхпорошков
Порошки сплавов, содержащих металлы, обладающие сравнительно невысоким сродством к кислороду (Fe, Ni, Со, Мо, W и др.), можно получать совместным восстановлением качественно приготовленной смеси оксидов соответствующих металлов водородом (в том числе диссоциированным аммиаком) или конвертированным природным газом в интервале между температурами восстановления наиболее и наименее стойких оксидов.
В процессе восстановления происходит взаимная диффузия образующихся металлов и формируются частицы порошка сплава заданного состава. Например, из смеси оксида никеля, оксида железа и триоксида молибдена восстановлением водородом при 600–900 °С получают порошки никелевых сплавов (60 % Ni, 20 % Fе, 20 % Мо). Из механической смеси окcидов никеля и Fe2O3 при 500–800 °С можно получить механическую смесь порошков никеля и железа без заметного образования твердого раствора, тогда как из высокодисперсной смеси этих же оксидов, полученной химическим смешиванием (совместным выпариванием и прокаливанием азотнокислых солей никеля и железа), в процессе восстановления при 500–800 °С образуются гомогенные порошки соответствующих сплавов благодаря интенсивной диффузии одного компонента в другой.
При получении композитных порошков металл или оксид основного компонента смешивают с водным раствором соли металла-добавки, затем раствор упаривают, а шихту восстанавливают. На каждой частице основного компонента располагается слой металла-добавки.
Контрольныевопросыизадания
1.Какие соединения используют при получении порошков тантала и
ниобия?
2.Назовите методы получения порошков тантала и ниобия.
3.Чем восстанавливают фторониобат и фторотанталат калия?
4.Чем восстанавливают пентаоксид ниобия?
5.Как получают карбид ниобия?
6.Какое сырье и восстановитель используют при получении порошков меди?
7.Чем восстанавливают оксиды кобальта и никеля?
8.Как получают порошки сплавов цветных металлов?
Процессы порошковой металлургии. Курс лекций |
-116- |