
- •Оглавление
- •ВВЕДЕНИЕ
- •I. ПОЛУЧЕНИЕ ПОРОШКОВ
- •Лекция 16 Восстановление химических соединений металлов из растворов солей и газообразных соединений металлов
- •II. ФОРМОВАНИЕ И СПЕКАНИЕ ИЗДЕЛИЙ ИЗ МЕТАЛЛИЧЕСКИХ И НЕМЕТАЛЛИЧЕСКИХ ПОРОШКОВ
- •Введение
- •Лекция 13 Твердофазное спекание материалов
- •Лекция 20 Жидкофазное спекание и инфильтрация порошковых формовок. Брак при спекании
- •Лекция 25 Методы определения механических характеристик порошковых тел. Заключение
- •ЗАКЛЮЧЕНИЕ
- •БИБЛИОГРАФИЧЕСКИЙ СПИСОК
- •ПРИЛОЖЕНИЯ

II. ФОРМОВАНИЕ И СПЕКАНИЕ ИЗДЕЛИЙ ИЗ МЕТАЛЛИЧЕСКИХ И НЕМЕТАЛЛИЧЕСКИХ ПОРОШКОВ
Лекция1 Введение. Классификацияметодовформования
План лекции
1.Введение.
2.Классификация методов формования.
3.Подготовка порошков к формованию.
Введение
Операции формования и спекания порошков являются завершающими операциями технологического цикла получения порошковых изделий. Именно на этих этапах производственного цикла порошковой металлургии формируются основные свойства порошковых материалов. Специфические особенности процессов получения изделий на основе порошков металлов и тугоплавких соединений требуют применения специальных режимов подготовки исходных шихтовых материалов, выбора наиболее эффективных методов формообразования и адекватных температурно-временных параметров процесса спекания.
В общем случае технологическая схема получения изделий методами порошковой металлургии включает ряд операций, которые предваряют или дополняют операции формования и спекания порошковых материалов и порошковых изделий:
подготовка порошков к формованию (подбор фракционного состава порошков, смешивание, введение смазки, засыпку порошка в оболочку, обезгаживание, грануляция и пр.);
послеформовочная доработка изделий (зачистка поверхности, удаление неликвидной части и пр.);
обработка спеченного материала (механическая, химическая, химикотермическая и пр.);
контроль свойств полученного материала.
Классификацияметодовформования
Формование порошка – технологическая операция, в результате которой порошок образует формовку – тело заданной формы, размеров и плотности. В процессе формования порошков изменяется исходный объем материала за счет консолидации отдельных частиц. Наблюдаемое изменение перво-
Процессы порошковой металлургии. Курс лекций |
-231- |

II. ФОРМОВАНИЕ И СПЕКАНИЕ ИЗДЕЛИЙ ИЗ МЕТАЛЛИЧЕСКИХ И НЕМЕТАЛЛИЧЕСКИХ ПОРОШКОВ
Лекция 1 Введение. Классификация методов формования
начального объема порошкового тела является основным отличием этого процесса от процесса деформирования компактного (литого) материала.
Методы формования порошков (рис. 2.1) условно можно разделить на статические и динамические (импульсные).
К статическим методам относятся различные методы холодного и горячего прессования материалов, шликерное литье и прокатка. К динамическим – методы, связанные с мощными импульсными воздействиями на порошковое тело (взрывные, пневмомеханические, электрогидравлические, электромагнитные). Каждая частица порошка обладает шестью степенями свободы, так как может совершать возвратно-поступательное движение по трем координатным осям и вращаться вокруг них. Поэтому частицы будут образовывать стабильную пространственную структуру при условии, что на каждую из них в среднем приходится не менее шести связей.
Если расположение частиц порошкового тела в пространстве равновероятно, то даже при условии, что полиэдрические частицы имеют различные размеры по взаимно перпендикулярным направлениям, т.е. форму, отличную от сфероидальной, можно ожидать, что на единицу длины по любому направлению в порошковом теле окажется примерно одинаковое количество частиц. Такое порошковое тело называют дискретно-изотропным.
Если же вероятность взаимного относительного расположения частиц в пространстве неодинакова, то частицы при образовании структуры порошкового тела будут стремиться занять наиболее вероятное положение. Частицы порошка в прессовке будут стремиться занять такое положение, при котором площадь максимального сечения приблизительно перпендикулярна направлению приложения усилия формования. Поэтому число частиц порошка на единицу длины порошкового тела в этом случае будет зависеть от взаимной ориентации частиц и, следовательно, будет неодинаковым по различным направлениям. Такое порошковое тело характеризуют как дис- кретно-анизотропное. Однако обычно анизотропия свойств порошкового тела выражена незначительно.
В дальнейшем будем считать, что структура порошкового тела не является геометрически правильной, взаимное расположение частиц равновероятно, хаотично, все направления в порошковом теле равноправны.
Процессы порошковой металлургии. Курс лекций |
-232- |

II. ФОРМОВАНИЕ И СПЕКАНИЕ ИЗДЕЛИЙ ИЗ МЕТАЛЛИЧЕСКИХ И НЕМЕТАЛЛИЧЕСКИХ ПОРОШКОВ
Лекция 1 Введение. Классификация методов формования
Методы формования металлических порошков
Статическое формование
|
|
|
|
Одностороннее |
|
|
|
||
|
Холодное |
|
|
||||||
|
|
|
|
|
|
|
|
||
|
прессование |
|
|
|
|
|
Мундштучное |
|
|
|
|
Двустороннее |
|
|
|||||
|
|
|
|
|
формование |
|
|||
|
|
|
|
||||||
|
|
|
|
|
|
|
|
|
|
|
|
|
|
|
|
|
|
|
|
|
|
|
|
Гидростатическое |
|
|
|
||
|
|
|
|
|
|
|
|
|
|
|
Изостатическое |
|
Газостатическое |
|
Инжекционное |
||||
|
формование |
|
|
|
|
|
формование |
||
|
|
|
|
|
|
||||
|
|
|
|
В эластичных втулках |
|
|
|
||
|
|
|
|
|
|||||
|
|
|
|
|
|
|
|
|
|
|
|
|
|
Вертикальная |
|
|
|||
|
|
|
|
|
|
Вибрационное |
|||
|
|
|
|
|
|
|
|
формование |
|
|
|
|
|
Горизонтальная |
|
|
|
||
|
|
|
|
|
|
|
|
|
|
|
Прокатка |
|
|
|
|
|
|
|
|
|
|
Наклонная |
|
|
|
|
|
||
|
|
|
|
|
|
|
|
|
|
|
|
|
|
|
|
|
|
|
|
|
|
|
|
|
|
|
|
||
|
|
|
|
Радиусная |
|
|
|
|
|
Динамическое (импульсное) формование |
|
|
Порохами |
Взрывное |
Бризантными |
|
|
|
взрывными |
|
веществами |
Электромагнит- |
|
ное |
|
Электрогид- |
|
равлическое |
|
Пневмомехани- |
|
ческое |
|
В пористых формах
Шликерное
формование Электрофоретическое
Из термопластичных
шликеров
Рис. 2.1. Классификация методов формования порошков
Процессы порошковой металлургии. Курс лекций |
-233- |

II. ФОРМОВАНИЕ И СПЕКАНИЕ ИЗДЕЛИЙ ИЗ МЕТАЛЛИЧЕСКИХ И НЕМЕТАЛЛИЧЕСКИХ ПОРОШКОВ
Лекция 1 Введение. Классификация методов формования
Каждая прямая, мысленно проведенная через порошковое тело однородной структуры, встретит на заданной длине определенное, примерно одинаковое число частиц и контактов между ними. Число контактов, наклоненных под одним и тем же углом, например к вертикали, не зависит от величины угла.
Уже при засыпании порошка в форму поверхностные слои частиц (как правило, обогащенные примесями или обладающие искаженной кристаллической решеткой, в результате чего их физические свойства могут значительно отличаться от свойств основного материала) воспринимают контактную нагрузку. Поверхность порошинок характеризуется шероховатостью (часто значительной) и наличием микроскопических или субмикроскопических трещин. В результате контакт между соприкасающимися частицами при отсутствии существенного внешнего давления возможен только в отдельных точках. В связи с этим действительные величины контактных давлений в силу малости величины начальных поверхностей соприкосновения (0,001– 0,01 % от общей поверхности контактирующих частиц) достигают таких значений, при которых возникают пластические деформации или местные разрушения, т.е. напряженное состояние материала частицы в окрестностях зоны контакта должно быть близко к предельному. По имеющимся подсчетам, при среднем напряжении в массе частиц 0,1 МПа наибольшее контактное давление составляет 2 000 МПа. При таких давлениях первоначальный точечный контакт переходит в контакт по некоторой небольшой поверхности.
Под контактной поверхностью имеют в виду ту часть общей (суммарной) внешней поверхности всех частиц порошка или прессовки, которая характеризуется соприкосновением частиц между собой и через которую передаются напряжения. Контактная поверхность может быть исследована визуально (например, после разрушения прессовки по отпечаткам на частицах, особенно имеющих сферическую форму) или же путем измерения электросопротивления порошкового тела
Отношение величины контактного сечения Sк к номинальному сечению Sнпорошкового тела называют относительным (безразмерным) контактным сечением αк:
αк = Sк/Sн ≤ 1 (при αк = 10-4–10-5). |
(2.1) |
Сущность процесса прессования заключается в деформировании некоторого объема сыпучего порошкового тела обжатием, при котором происходит уменьшение первоначального объема и формирование заготовки (прессовки) заданной формы, размеров и свойств. При приложении давления к порошку его частицы пытаются занять наиболее устойчивое положение, что должно сопровождаться их контактным смятием и сдвигом, т.е. при
Процессы порошковой металлургии. Курс лекций |
-234- |

II. ФОРМОВАНИЕ И СПЕКАНИЕ ИЗДЕЛИЙ ИЗ МЕТАЛЛИЧЕСКИХ И НЕМЕТАЛЛИЧЕСКИХ ПОРОШКОВ
Лекция 1 Введение. Классификация методов формования
прессовании имеет место самый общий случай нагружения межчастичных контактов комбинированной нормальной и тангенциальной нагрузками.
Объем порошкового тела при прессовании уменьшается (относительная плотность порошкового тела увеличивается) в результате смещения отдельных частиц в пустоты между ними и за счет деформации частиц. Происходит рост прежнего фиксированного участка контакта, в остальных случаях контактные участки смещаются, разрываются и сдвигаются.
Контактные узлы между частицами порошкового тела и взаимосвязь между контактными узлами имеют не жесткофиксированный, а жесткоподвижный характер, причем элементы (звенья) связи между контактными узлами (частицами или долями частицы) являются жесткими, а узлы и места контактов могут смещаться. При таких смещениях атомы на одной стороне контактного участка сменяют своих партнеров на другой его стороне (на другой частице).
Впорошковом теле с жесткими звеньями связи в принципе невозможно существенно и необратимо изменить расстояние между узлами в любом направлении без внутриузловой деформации. Межузловая деформация в таких порошковых телах происходит в значительной мере не за счет деформации звеньев связи, а за счет передвижения и смещения звеньев связи от одних узлов к другим, сопровождающего внутриузловую деформацию.
Впорошковых телах с существенно неравноосными частицами не исключена гибкая и гибко-жесткая деформация звеньев связи между узлами.
Подготовкапорошковкформованию
Формование более чем любая другая операция определяет процесс получения конкретного материала (изделия) методами порошковой металлургии. При этом особое внимание должно уделяться предшествующему процессу формообразования этапу – подготовке порошков к формованию.
Основными операциями подготовки порошков к формованию являются отжиг, классификация (рассев) и смешивание.
Процессы подготовки порошков к формованию занимают весьма важное место в общей схеме производства из них материалов и изделий. Как правило, металлические порошки производят на специализированных заводах и практически невозможно учесть все требования, которые могут предъявлять к порошкам его различные потребители. Почти во всех случаях возникает необходимость в специальных операциях подготовки для придания порошку определенных химических и физических характеристик, обеспечивающих выпуск из него продукции с нужными конечными свойствами. Даже когда порошки производят непосредственно сами потребители, некоторые дополнительные операции перед формованием порошков необходимы.
Процессы порошковой металлургии. Курс лекций |
-235- |

II. ФОРМОВАНИЕ И СПЕКАНИЕ ИЗДЕЛИЙ ИЗ МЕТАЛЛИЧЕСКИХ И НЕМЕТАЛЛИЧЕСКИХ ПОРОШКОВ
Лекция 1 Введение. Классификация методов формования
Основными операциями при подготовке порошков к формованию являются отжиг, рассев (классификация) и смешивание.
Отжиг. Этот вид тепловой (термической) или химико-термической обработки порошков применяют для решения нескольких целевых задач:
удаление оксидных пленок, присутствующих на поверхности; изменение химического состава или улучшение однородности (т.е. по-
вышение гомогенности) распределения химических элементов в объеме частиц; изменение напряженного состояния и укрупнение частиц порошка; уменьшение газонасыщенности порошка.
При отжиге главным образом снимается наклеп, т.е. устраняется искажение кристаллической решетки металла в приповерхностных слоях частиц, и происходит восстановление оксидов, оставшихся при получении порошка или образовавшихся в результате некоторого окисления металла при длительном или неправильном его хранении. В результате повышается пластичность частиц и, следовательно, улучшаются уплотняемость, прессуемость и формуемость порошка.
Нагрев осуществляют в защитной среде (восстановительной, инертной или вакууме) при температуре 0,4–0,6 Тпл металла порошка.
Наиболее часто отжигу подвергают порошки, полученные механическим измельчением твердых материалов, диспергированием расплавов, электролизом и разложением карбонилов. Подобные порошки содержат значительные количества оксидов, растворенных газов и наиболее наклепаны.
Порошки, полученные восстановлением, отжигают только в тех случаях, когда требуется повысить чистоту порошка или при необходимости укрупнения мелких частиц.
Порошки отжигают в проходных печах, подобных печам для восстановления оксидов и спекания заготовок. Для более тщательной очистки порошков от различных примесей часто используют при их отжиге атмосферы с галогенсодержащими добавками.
Классификация. Под классификацией понимают разделение порошка по размерам частиц на фракции, используемые затем либо непосредственно для формования, либо для составления смеси, содержащей требуемый процент частиц нужного размера. При этом некоторые фракции порошка могут оказаться непригодными для прямого использования, поэтому их подвергают какой-либо дополнительной обработке (укрупнению в случае мелких фракций или размолу в случае крупных) или отбрасывают.
Фракционирование порошка проводят обычно в аппаратах, применяемых в химическом производстве и обогатительном деле: просеивание на разделяющей поверхности (рассев, отсеивание, грохочение); гидравлическая классификация в подвижной или неподвижной жидкой среде; сухая классификация в газовых потоках. Чаще всего в порошковой металлургии применяют ситовую классификацию порошков с использованием различных типов сит, основными из которых являются механические сита с электромагнитным
Процессы порошковой металлургии. Курс лекций |
-236- |

II. ФОРМОВАНИЕ И СПЕКАНИЕ ИЗДЕЛИЙ ИЗ МЕТАЛЛИЧЕСКИХ И НЕМЕТАЛЛИЧЕСКИХ ПОРОШКОВ
Лекция 1 Введение. Классификация методов формования
или рычажным вибратором. Сетки классификаторов аналогичны тем, которые применяют в ситовом анализе порошков.
Для классификации порошков применяют также многодечные механические вибросита; движение сетчатых дек осуществляется от электродвигателя через клиноременную передачу (рис. 2.2).
|
7 |
|
1 |
5 |
6 |
|
2 |
4 |
3 |
Рис. 2.2. Многодечное сито (СВЗ – 0,9): 1 – цилиндрическая обечайка; 2– нижняя обечайка; 3 – рама; 4 – двигатель; 5 – рассеивающие поверхности; 6 – разгрузочный патрубок;
7 – загрузочный патрубок
Вибросито содержит набор цилиндрических обечаек с просеивающими поверхностями. Загрузочный и разгрузочный патрубки снабжены резиновыми манжетами для герметичной стыковки с патрубком питающего исходным материалом устройства и желобами, принимающими расклассифицированные порошки. Вибросита выполняются пыленепроницаемым и снабжаются приспособлениями для отбора проб из потока порошка в разгрузочных патрубках. Производительность вибросит зависит от природы материала порошка и размера его частиц.
В некоторых случаях вибросита используют совместно с электромагнитными сепараторами, обеспечивающими очистку просеиваемого порошка от магнитных примесей.
При затрудненности свободного просева порошка используют различные протирочные ситовые устройства, в которых специальное приспособление с небольшим усилием давит на порошок, способствуя его проходу через сетку. Производительность таких протирочных сит значительно меньше обычных вибрационных.
Гидравлическое фракционирование порошков проводят в жидкой среде в потоке, совпадающем (противоположном) или направленным под углом относительно направления основных действующих сил. На первом принципе основаны гравитационные классификаторы (рис. 2.3), на втором – центробежные классификаторы.
Процессы порошковой металлургии. Курс лекций |
-237- |

II. ФОРМОВАНИЕ И СПЕКАНИЕ ИЗДЕЛИЙ ИЗ МЕТАЛЛИЧЕСКИХ И НЕМЕТАЛЛИЧЕСКИХ ПОРОШКОВ
Лекция 1 Введение. Классификация методов формования
3
2
1
Питание
Вода |
4 |
|
|
6 |
|
|
|
|
|
5 |
Слив фракцииоонкой |
|
|
8 |
Вода |
Песок |
7 |
|
Материал |
Выход |
|
|
7 |
|
6 |
|
|
|
5 |
|
|
|
|
|
|
1 |
2 |
|
3 |
|
Вход газа |
|
4 |
|
|
Рис. 2.3. Гидравлический классификатор: 1 – |
Рис. 2.4. Воздушный классификатор: 1 – вер- |
чан; 2– пьезометрические трубки; 3– клапана; |
тикальная труба; 2 – пересыпные полки; 3 – |
4 – патрубок для пульпы; 5 – сифон; 6 – кон- |
тяги; 4 – шлюзовой затвор разгрузочного уст- |
центрический желоб; 7 – подача воды; 8 – |
ройства; 5 – клапан, регулирующий расход |
сливные штуцеры |
газовзвеси; 6– шлюзовой затвор загрузочного |
|
устройства; 7– отводящий патрубок |
Классификацию порошков с размером частиц менее 40 мкм проводят в воздушных сепараторах, высаживающих твердые частицы из несущего газового потока под действием на них силы тяжести.
Ввоздушно-проходном сепараторе разделяемый материал в потоке газа поступает в кольцевое пространство, в котором скорость воздушного потока снижается в несколько раз и наиболее крупные частицы под действием силы тяжести выпадают из него и удаляются через патрубок. Воздушный поток далее проходит через тангенциально установленные лопатки, приобретая вращательное движение; в этот момент оставшиеся в нем более крупные частицы под действием центробежной силы отбрасываются на стенки конического корпуса сепаратора, опускаются по ним и выводятся через другой патрубок. Газовый поток с мелкими частицами поступает в циклон, где они
ивыделяются из него.
Вклассификатор с пересыпными полками (рис. 2.4) порошок поступает через приемный бункер и попадает в движущийся ему навстречу воздушный поток. Крупные частицы порошка разгружаются через нижний шлюзовый затвор, а взвесь более мелких частиц отсасывается в циклон. Разделение частиц по размерам регулируют, изменяя расход воздуха и положение пересыпных полок, угол наклона которых меняют специальными тягами.
Весьма эффективными аппаратами для разделения являются цикло-
ны-сепараторы. В корпус циклона по касательной к окружности (тангенциально) вводят газовый поток, содержащий твердые частицы, который приобретает вращательное движение. На каждую порошинку действует сила
Процессы порошковой металлургии. Курс лекций |
-238- |
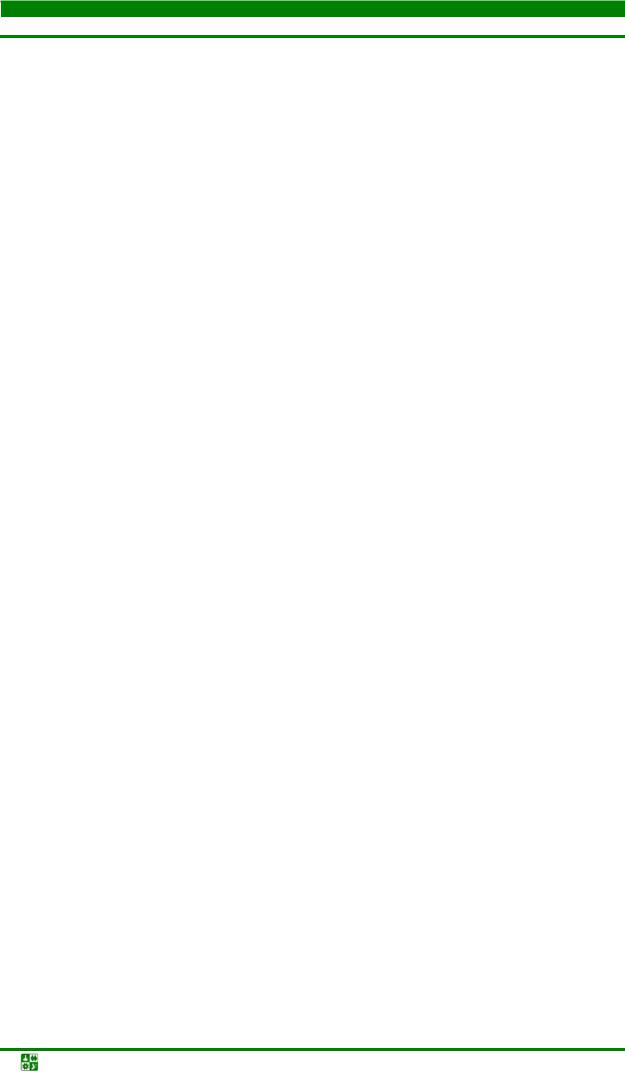
II. ФОРМОВАНИЕ И СПЕКАНИЕ ИЗДЕЛИЙ ИЗ МЕТАЛЛИЧЕСКИХ И НЕМЕТАЛЛИЧЕСКИХ ПОРОШКОВ
Лекция 1 Введение. Классификация методов формования
тяжести, увлекающая ее вниз, центробежная сила, выталкивающая ее в радиальном направлении и сила газового потока, заставляющая ее двигаться по окружности. Под действием этих сил частица движется по спирали и, достигая стенки корпуса, перемещается по его поверхности к выпускному штуцеру. Мелкие частицы выносятся в циклон и выделяются в следующем циклоне. Работу воздушных сепараторов регулируют изменением скорости газового потока.
Смешивание порошков предусматривает приготовление однородной механической смеси из частиц различного (одинакового) химического и(или) гранулометрического состава. На практике применяют различные методы смешивания, которые можно разделить на две группы: механические и химические.
Эффективность смешивания зависит от конструкции смесителей. На практике чаще используют механические смесители (барабанные, шнековые, лопастные, конусные, вибрационные и пр.). Результаты смешивания контролируют либо технологическим опробованием шихты, либо химическим анализом пробы.
Контрольныевопросыизадания
1.Что определяет понятие «формование порошка»?
2.В чем состроит назначение и сущность процесса формования?
3.Назовите основные методы формования.
4.Перечислите основные операции подготовки порошков к формованию.
5.Для чего проводят отжиг порошков?
6.Для чего нужна операция классификации порошков?
7.Перечислите основные методы классификации порошков.
8.Как контролируется качество подготовки смесей порошков?
9.В каком случае применяется химическое смешивание порошков?
Лекция2 Общиезакономерностипроцессовформованияпорошков
План лекции
1.Процессы, сопровождающие формование порошков.
2.Зависимость плотности прессовки от давления прессования. Основные уравнения прессования.
3.Боковое давление.
Процессы порошковой металлургии. Курс лекций |
-239- |

II. ФОРМОВАНИЕ И СПЕКАНИЕ ИЗДЕЛИЙ ИЗ МЕТАЛЛИЧЕСКИХ И НЕМЕТАЛЛИЧЕСКИХ ПОРОШКОВ
Лекция 2 Общие закономерности процессов формования порошков
Процессы, сопровождающиеформованиепорошков
Схема простейшей конструкции пресс-формы для холодного одностороннего прессования порошков показана нарис. 2.5.
1
2
3
Рис. 2.5. Схема пресс-формы для одностароннегохолодного прессования порошков:1 –
пуансон верхний; 2– матрица; 3– порошок; 4 4 – нижний пуансон (неподвижный)
При наполнении ее засыпной полости в порошковом теле отдельные частицы соединены друг с другом разнообразными связями, зависящими от размеров и формы частиц, а также от свойств заполнителя (жидкость или газ) пустот между ними. Такие связи представляют собой: слабые Ван-дер- Ваальсовы силы сцепления, действующие через тонкие остаточные прослойки газа (воздуха) или жидкости в контактах между свободно насыпанными частицами; зацепление, связанное с шероховатостью поверхностей и сложной (например, дендритной) формой частиц; свободное опирание одних частиц на другие и пр.
Каждая пара соприкасающихся частиц в порошковом теле соединена в контакте тремя связями: одной односторонней связью сжатия и двумя связями трения.
Некоторое число таких межчастичных контактов обеспечивает в каждый рассматриваемый момент стабильность несвязанного порошкового тела.
Наиболее доступно продемонстрировать процессы, происходящие в пресс-форме можно, используя для построения имитационной модели сферические высокопластичные тела (например: резиновые шайбы). При свободной насыпке (рис. 2.5) в замкнутом объеме полости матрицы между шайбами сохраняются значительные пустоты, обусловленные арочным эффектом. Под действием прикладываемых внешних сил пустоты заполняются частицами, и достигается наиболее плотная упаковка шайб (рис. 2.6, б).
В случае пластичных металлов дальнейшее уплотнение будет происходить в основном за счет деформации частиц, причем вначале она ограничена приконтактными участками, а затем распространяется в глубь частиц.
Процессы порошковой металлургии. Курс лекций |
-240- |
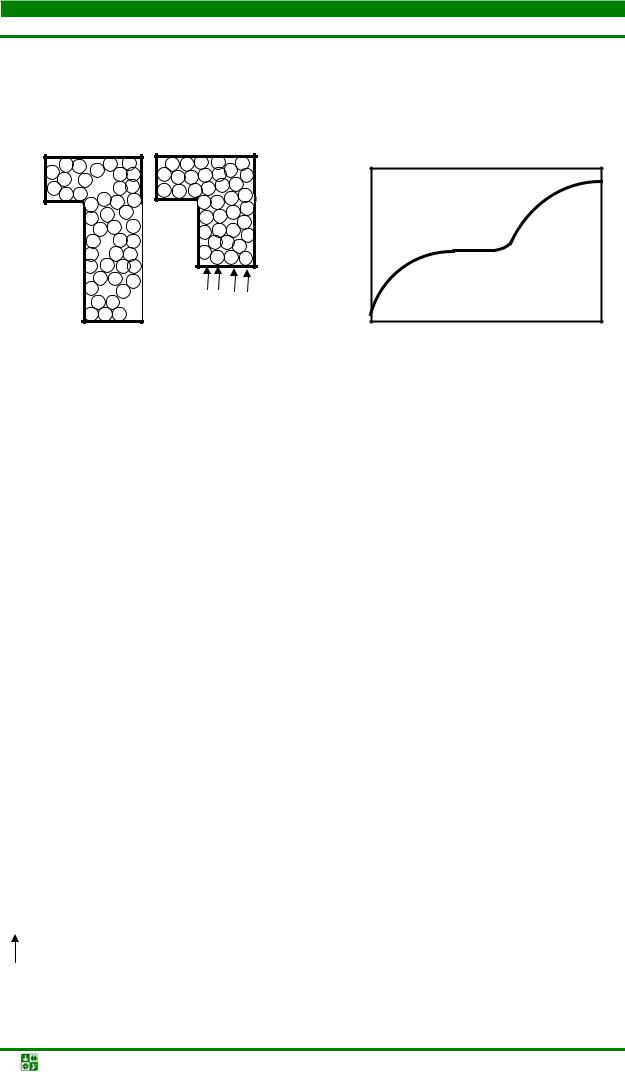
II. ФОРМОВАНИЕ И СПЕКАНИЕ ИЗДЕЛИЙ ИЗ МЕТАЛЛИЧЕСКИХ И НЕМЕТАЛЛИЧЕСКИХ ПОРОШКОВ
Лекция 2 Общие закономерности процессов формования порошков
При прессовании хрупких материалов деформационные (объемные) превращения чаще всего проявляются в разрушении и дроблении выступов на поверхности частиц.
|
γотн |
в |
|
|
б |
|
|
а |
а |
б |
р, МПа |
Рис. 2.6. Модель уплотнения порошка в Рис. 2.7. Идеализированная кривая процесса
процессе прессования: а – свободнонасыуплотнения порошковых тел панный порошок; б – уплотненный порошок (частицы заполнили крупные пустоты)
Если построить график, на котором по оси ординат отложить относительную плотность порошка или прессовки, а по оси абсцисс – давление прессования, то зависимость между этими величинами в общей форме можно было бы выразить идеализированной кривой уплотнения с тремя характерными участками (рис. 2.7).
Из рисунка видно, что наиболее интенсивное уплотнение порошкового тела происходит на первой стадии процесса (участок а кривой), связанной с перераспределением частиц в межчастичные пустоты (арки, полости) и их более плотной упаковкой под действием прикладываемых внешних сил. В связи с этим часто говорят о первой стадии как о структурной деформации порошкового тела.
Эта стадия сопровождается значительной разгрузкой некоторых из межчастичных контактов, происходящей уже в самом начале уплотнения порошковой массы. Такая местная разгрузка на отдельных контактных поверхностях приводит к сокращению площади соприкосновения отдельных частиц и уменьшению силы связи между частицами. А это, в свою очередь, облегчает взаимное смещение частиц и создает условия для дальнейшего пластического деформирования приповерхностных слоев остаточных контактов, которое сопровождается ускоренным нарастанием плотности порошкового тела.
Вторая стадия процесса уплотнения характеризуется тем, что частицы порошка, упакованные максимально плотно, оказывают определенное сопротивление сжатию, в силу того, что давление прессования еще не достаточно велико для преодоления предела текучести (прочности) материала. И хотя давление прессования монотонно возрастает, плотность порошкового тела
Процессы порошковой металлургии. Курс лекций |
-241- |

II. ФОРМОВАНИЕ И СПЕКАНИЕ ИЗДЕЛИЙ ИЗ МЕТАЛЛИЧЕСКИХ И НЕМЕТАЛЛИЧЕСКИХ ПОРОШКОВ
Лекция 2 Общие закономерности процессов формования порошков
некоторое время не увеличивается. На рисунке это эта стадия процесса характеризуется горизонтальным участком б.
Наконец, когда давление прессования превысит предел текучести порошка (участок в кривой), начинается пластическая деформация частиц. С этого момента пластическая деформация охватывает весь объем порошкового тела, смещение межчастичных контактов фактически прекращается и они фиксируются.
Вреальных условиях в процессе прессования происходит взаимное наложение (перекрытие во времени) всех стадий уплотнения порошкового тела, связанное с тем, что частицы имею различные размеры, форму и свойства. Деформация отдельных частиц начинается уже при сравнительно малых давлениях прессования, в то время как скольжение некоторых частиц имеет место и при высоких давлениях прессования.
Всвязи с этим реальная кривая уплотнения, характеризующая процесс прессования большинства металлических порошков, монотонна и в средней части не имеет явно выраженного горизонтального участка.
Поэтому можно говорить только о преимущественном значении для уплотнения порошка перемещения частиц на первой стадии и их пластической деформации на последней стадии.
Энергия прессования расходуется на преодоление межчастичного (между отдельными частицами) и внешнего трения (между частицами и стенкой матрицы или торцами пуансонов пресс-формы), а также на деформирование частиц.
Действие на процесс одностороннего холодного формования внешнего трения, хорошо демонстрирует опыт с прессованием засыпанных в цилиндрическую пресс-форму одинаковых по массе и высоте слоев порошка, разделенных прокладками из тонкой алюминиевой фольги. После уплотнения отдельные слои отличаются один от другого по толщине и форме (рис. 2.8).
|
|
|
Нагрузка |
|
|
|
7,3 |
7,2 |
6,9 |
7,2 |
7,3 |
|
|
|
7,0 |
|
|
|
6,9 |
|
7,1 |
|
6,9 |
|
|
7,2 |
|
||
|
6,8 |
|
|
|
6,8 |
|
6,7 |
|
7,1 |
|
6,7 |
|
|
|
|
||
|
6,4 |
|
7,0 |
|
6,4 |
|
|
|
|
||
Рис. 2.8. Толщина и форма слоев порошка, |
Рис. 2.9. Распределение плотности в нике- |
||||
спрессованного при одностороннем прило- |
левом брикете, спрессованном при давле- |
||||
жении давления сверху |
нии 700 МПа (цифры в поле рисунка – |
||||
|
|
|
г/см3) |
|
|
Процессы порошковой металлургии. Курс лекций |
-242- |

II. ФОРМОВАНИЕ И СПЕКАНИЕ ИЗДЕЛИЙ ИЗ МЕТАЛЛИЧЕСКИХ И НЕМЕТАЛЛИЧЕСКИХ ПОРОШКОВ
Лекция 2 Общие закономерности процессов формования порошков
По вертикали в направлении приложения давления каждый верхний слой оказывается тоньше (т.е. плотнее) нижележащего. Частицы у стенки внутренней полости матрицы пресс-формы продвинулись на меньшее расстояние, чем в центральной части брикета.
В горизонтальном направлении в верхнем слое под подвижным пуансоном плотность нарастает от центра к периферии (рис. 2.9), а в нижнем слое, наоборот, – от периферии к центру.
Неоднородное распределение плотности по объему прессовки обусловлено затратой части усилия прессования на преодоление внешнего трения частиц порошка о стенки внутренней полости матрицы и торцевые поверхности пуансонов.
Межчастичное трение, влияя на величину достигаемой при уплотнении плотности, не вызывает появления градиента плотности по высоте и сечению прессовки, т.е. не приводит к неравноплотности.
Одна из причин наличия в средней части прессовки зоны большего уплотнения связана с формой и направлением распространения очага деформации порошка в процессе прессования. Другая причина этого – выдавливание порошка из углов полости матрицы, вблизи поверхности подвижного пуансона, в радиальном направлении.
Зависимость изменения плотности по высоте прессовки (рис. 2.10) при одно- и двустороннем прессовании порошка показывает, что при двустороннем прессовании более плотными оказываются верхняя и нижняя части прессовки, тогда как в ее середине наблюдается зона наименьшей плотности, на-
зываемая нейтральной.
Рис. 2.10. Изменение плотности по высоте прессовки: 1 – одностороннее прессование; 2 – двустороннее прессование
h, мм |
2 |
1 |
γ,г/см3 |
Неравномерная плотность прессовки может оказать прямое влияние на искажение ее формы и размеров при спекании, а также вызвать нежелательные изменения свойств спеченного порошкового тела.
Процессы порошковой металлургии. Курс лекций |
-243- |

II. ФОРМОВАНИЕ И СПЕКАНИЕ ИЗДЕЛИЙ ИЗ МЕТАЛЛИЧЕСКИХ И НЕМЕТАЛЛИЧЕСКИХ ПОРОШКОВ
Лекция 2 Общие закономерности процессов формования порошков
Зависимостьплотностипрессовкиотдавленияпрессования. Основныеуравненияпрессования
Попытки вывода уравнения прессования, связывающего давление прессования и плотность прессовки, обозначили два основных подхода к его решению.
Один из них характеризуется введением целого ряда упрощающих допущений, которые позволяют решать ту или иную задачу элементарным путем, предлагая во многих случаях достаточно простые уравнения прессования, которые обеспечивают весьма удовлетворительную точность расчетов.
К подобным работам, основанным на использовании гипотезы сплошности, которая не учитывает наличия разрывов в уплотняемой среде, что в целом противоречит представлениям о дискретном строении порошковых тел.
Другой подход базируется на большей физической обоснованности решения поставленной задачи. Он предлагает для описания процесса уплотнения порошкового тела весьма сложные математические зависимости и далеко не всегда приводит к результатам, которые могут быть использованы в инженерной практике. К этому направлению относят теории, основанные на изучении контактных явлений при взаимодействии частиц.
Необходимо отметить, что четко разграничить эти подходы представляется невозможным, так как они зачастую взаимно дополняют друг друга.
Большая заслуга в разработке теоретических положений, связывающих плотность порошкового тела с давлением прессования, принадлежит М.Ю. Бальшину. Он показал, что количественная зависимость плотности прессовки от давления прессования может быть выражена уравнениями:
lgp = –L (V – 1) + lgpmax |
(2.2) |
и |
|
lgp = –m lgV + lgpmax |
(2.3) |
или |
|
lgp = m lgγ + lgpmax , |
(2.4) |
где p – приложенное (текущее) давление прессования; pmax – давление прессования, обеспечивающее получение беспористой прессовки; L, т – постоянные, учитывающие природу прессуемого материала и называемые, соответственно, фактором и показателем прессования; V, γ – соответственно, относительный объем и относительная плотность прессовки.
При выводе этих уравнений М.Ю. Бальшин ввел следующие допуще-
ния:
Процессы порошковой металлургии. Курс лекций |
-244- |

II. ФОРМОВАНИЕ И СПЕКАНИЕ ИЗДЕЛИЙ ИЗ МЕТАЛЛИЧЕСКИХ И НЕМЕТАЛЛИЧЕСКИХ ПОРОШКОВ
Лекция 2 Общие закономерности процессов формования порошков
1) упрочнение при пластической деформации материала частиц порошка в окрестностях контактной зоны отсутствует, т.е. контактное давление к σ постоянно;
2)закон Гука, выражающий зависимость между упругой деформацией
ирастягивающим (сжимающим) напряжением в компактном металле, согласно которому бесконечно малое приращение деформации пропорционально бесконечно малому приращению напряжения, справедлив и для пластической деформации;
3)материал частицы порошка в зоне контакта находится постоянно в напряженном состоянии, близком к одноосному сжатию;
4)деформирование компактного и порошкового тела происходит идентично, что предполагает отсутствие межчастичной (структурной) деформации при уплотнении порошка.
В дифференциальной форме уравнение (2.3) имеет вид
dp/p = l dV, |
(2.5) |
где р – текущее давление прессования; V – относительный объем порошкового тела (прессовки) при давлении р; l – фактор прессования, постоянный в некотором интервале давлений прессования.
После интегрирования выражения (2.5) и замены l на L (L = 0,434·l) получаем уравнение (2.2), которое часто называют первым уравнением прессования Бальшина (полулагорифмическим).
Фактор прессования L связан с величиной контактного давления σк зависимостью
L = 0,434 К' ·hк / (σк ho), |
(2.6) |
где К' – постоянный коэффициент; hк – приведенная высота порошкового тела (прессовки), имеющего плотность 100 %; h0 – первоначальная высота порошкового тела.
Следовательно, L может быть постоянным только приσ к = const, так как hк и ho для отмеренной навески порошка есть величины постоянные. На самом деле σк ≠ const и растет как за счет упрочнения материала частицы порошка в процессе прессования, так и вследствие изменения схемы его напряженного состояния.
Поэтому Бальшин предложил в дифференциальном уравнении (2.5) фактор прессования l выразить в виде функции
I = L/0,434 = m/V, |
(2.7) |
Процессы порошковой металлургии. Курс лекций |
-245- |

II. ФОРМОВАНИЕ И СПЕКАНИЕ ИЗДЕЛИЙ ИЗ МЕТАЛЛИЧЕСКИХ И НЕМЕТАЛЛИЧЕСКИХ ПОРОШКОВ
Лекция 2 Общие закономерности процессов формования порошков
что после интегрирования (2.5) приводит к уравнениям (2.3), (2.4), каждое из которых принято называть вторым (или логарифмическим) уравнением прессования Бальшина.
Для идеального процесса прессования (т.е. при отсутствии внешнего трения) уравнения (2.3), (2.4) примут вид
p(V)m = pmax = pк = const |
(2.8) |
и |
|
p(γ)m = pmax = pк = const, |
(2.9) |
где pк – максимальное (критическое) давление прессования, соответствующее максимальному уплотнению и равное по величине давлению истечения (численно – это твердость материала при максимальной степени его упрочнения).
Показатель прессования т характеризует свойства порошка и может быть определен опытным путем или рассчитан по формуле
m = 2 + γ / γ, |
(2.10) |
где Δγ = γ – γ0, а γ0 – относительная плотность исходного порошкового тела до приложения нагрузки к нему.
Для многих порошков железа и меди величины т сохраняют примерно постоянное значение в довольно большом интервале давлений прессования. Для порошков олова, вольфрама и некоторых других металлов показатель прессования т изменяется, возрастая с увеличением насыпной плотности порошка и твердости исходного материала его частиц. Однако, независимо от свойств материала, m металлических порошков всегда ≥3.
Наиболее приемлемо для анализа поведения порошков при прессовании уравнение (2.3), вывод которого может быть обоснован различными способами. В графической форме при σк = const уравнение (2.3) дает прямую ли-
нию (рис. 2.11).
Тангенс угла наклона прямой к оси абсцисс численно равен показателю прессования т, а отрезок, отсекаемый прямой от оси ординат, равен логарифму максимального давления прессования рmах или в идеальном случае он равен логарифму критического давления рк.
lqp |
lqp = lqpк |
|
|
|
α |
|
lqγ |
Рис. 2.11. Логарифмическая диаграм- |
|
ма процесса прессования (σк = pк) |
как величина и форма частиц порошка, а также его насыпная плотность не оказывают прямого влияния на величину рк. Однако форма частиц и насыпная плотность оказывают влияние на прессуемость порошка. Для получения прессовок заданной плотности необходимое давление увеличивается вместе с ростом дисперсности порошка.
Процессы порошковой металлургии. Курс лекций |
-246- |

II. ФОРМОВАНИЕ И СПЕКАНИЕ ИЗДЕЛИЙ ИЗ МЕТАЛЛИЧЕСКИХ И НЕМЕТАЛЛИЧЕСКИХ ПОРОШКОВ
Лекция 2 Общие закономерности процессов формования порошков
Уравнения прессования М.Ю. Баль-шина не имеют физического смысла в начальный момент прессования и справедливы лишь в области средних и относительно высоких значений давления прессования.
М.Ю. Бальшин полагал, что единое (от свободной насыпки порошка до беспористой прессовки) описание процесса уплотнения невозможно из-за его стадийности (общеприняты предложенные в 1951 г. Зеелигом три стадии: структурная, упругая и пластическая деформации). Г.А. Меерсон постулировал положение, что одна стадия переходит в другую постепенно. Необходимо отметить (учитывая наложение одной стадии на другую), что на различных стадиях прессования механизмы уплотнения не идентичны, но имеют некоторое сходство.
Общей основой механизма уплотнения на всех стадиях является уравновешивание давления прессования в критическом (контактном) сечении. Другая общая черта – наличие давления прессования, которое производит необратимую работу межчастичного трения и обратимую (в известной мере) работу упругой деформации. Однако детали этого механизма для трех стадий неодинаковы. По вопросу о границах и характерных чертах трех стадий процесса уплотнения мнения исследователей расходятся.
Одно из наиболее удачных решений задачи математического описания процесса уплотнения металлического порошка во всем возможном диапазоне давлений предложено Г.М. Ждановичем.
Г.М. Жданович теоретически и экспериментально доказал, что достаточно точно идеальный процесс уплотнения описывает следующая зависимость
p = pк (γn – γ0n )/(1 – γ0n) = pк (Vоn – Vn) /[Vn(Vоn – 1)], |
(2.11) |
где pк – максимальное давление прессования, соответствующее максимальной твердости материала; γ – относительная плотность прессовки; γ0 – относительная плотность исходного порошкового тела до приложения нагрузки (плотности насыпки); V – относительный объем прессовки; Vо – относительный объем исходного порошкового тела (до приложения нагрузки)
Показатель степени и в уравнении (2.11) зависит от всех основных факторов, определяющих характер и особенности процесса прессования металлического порошка (контактного давленияσ к, придела текучестиσ т, придела прочности σ в, коэффициента межчастичного трения, относительной плотности насыпки порошка).
По мнению М.Ю. Бальшина, среднее «интегральное» значение показателя n составляет:
n = 1 + 2/П0, |
(2.12) |
где П0 = 1 – γ0.
Г.М. Жданович полагает, что между давлением идеального и реального процессов прессования существуют зависимости вида:
Процессы порошковой металлургии. Курс лекций |
-247- |

II. ФОРМОВАНИЕ И СПЕКАНИЕ ИЗДЕЛИЙ ИЗ МЕТАЛЛИЧЕСКИХ И НЕМЕТАЛЛИЧЕСКИХ ПОРОШКОВ
Лекция 2 Общие закономерности процессов формования порошков
при одностороннем прессовании
p0 = p(1 + 0,25А·V), |
(2.13) |
при двустороннем прессовании
p0 = p(1 + 0,5А·V). |
(2.14) |
Значение этого коэффициента можно определить, используя следующее уравнение:
А = ξ·f(Lн + Lв )hK/Sн, |
(2.15) |
где ξ – коэффициент бокового давления; f – коэффициент внешнего трения; Lн, Lв – длины периметров или контуров, соответственно, наружной и внутренней (если прессовка с отверстием) боковых поверхностей прессовки; hK
– высота слоя порошка в пресс-форме; Sн – поперечная площадь сечения прессовки.
Боковоедавление
Порошок при приложении к нему значительной по величине нагрузки ведет себя подобно замороженной жидкости. Частицы порошка движутся не только в направлении приложенной нагрузки, но и перемещаются в радиальном направлении, передавая прилагаемое к ним давление на внутреннюю стенку матрицы. Давление, которое возникает при подобном взаимодействии порошка и пресс-формы называется боковым.
В отличие от высокопластичных материалов, равномерно передающих прилагаемое к ним давление по всему объему тела, в порошковом теле наблюдается значительная неравномерность распределения нагрузки (на боковую стенку матрицы передается значительно меньшее давление, чем в направлении прессования). Это связано с проявлением эффекта заклинивания частиц, ограниченностью площади контактов, влиянием на процесс перемещения межчастичного трения и пр. В связи с этим важной характеристикой является так называемый коэффициент бокового давления ξ, представляющий собой отношение бокового давления рб, т.е. усилия оказываемого порошком на единицу поверхности боковой стенки матрицы пресс-формы, к давлению прессования р:
ξ = рб /p ≤1. |
(1.16) |
Процессы порошковой металлургии. Курс лекций |
-248- |

II. ФОРМОВАНИЕ И СПЕКАНИЕ ИЗДЕЛИЙ ИЗ МЕТАЛЛИЧЕСКИХ И НЕМЕТАЛЛИЧЕСКИХ ПОРОШКОВ
Лекция 2 Общие закономерности процессов формования порошков
Для количественного определения ξ рассмотрим упруго-напряженное состояние некоторого объема материала в середине прессовки после того, как уплотнение закончилось и перемещение частиц прекратилось.
В этот момент прессовка находится в стабильном состоянии и сжата под действием приложенного давления прессования и реакции боковой стенки матрицы, равной боковому давлению. Каждая из этих сил вызывает сжатие по координатной оси, совпадающей с направлением ее действия, и растяжение по двум другим координатным осям.
Как известно, деформация упругого сжатия равна частному от деления сжимающего давления (в нашем случае рб или р) на модуль упругости материала Е, а упругое расширение под влиянием упругого сжатия равно деформации сжатия по соответствующей координатной оси, умноженной на коэффициент Пуассона ν. Очевидно, что стабильность упруго-напряженного состояния возможна в случае, если деформация упругого сжатия по каждой из координатных осей равна сумме деформаций упругого расширения под влиянием упругого сжатия по двум другим координатным осям:
pν/ E + рб ν/E = рб/E, |
(2.17) |
где рν/ E – упругое горизонтальное расширение под влиянием упругого вертикального сжатия от приложенного давления прессования; рбν/E – упругое горизонтальное расширение под влиянием упругого горизонтального сжатия от реакции боковой стенки матрицы; рб/E – упругое горизонтальное сжатие от реакции боковой cтенки матрицы.
После преобразования этого равенства находим:
p ν = рб (1 – ν). |
(2.18) |
Отсюда |
|
ξ = рб /p = ν /(1 – ν), |
(2.19) |
а |
|
ν = ξ /(1 – ξ). |
(2.20) |
Значение ξ в области высоких плотностей порошкового тела достаточно велико и обычно составляет 0,2–0,5, причем, чем пластичнее материал частиц порошка, тем больше значение ν, а следовательно, и больше ξ (для вольфрама 0,2, для железа 0,39, для олова 0,49, для меди 0,54, для серебра
0,72, для свинца 0,79).
Коэффициент бокового давления растет с увеличением плотности прессовки, но для разных материалов по-разному: чем пластичнее металл,
тем в большей степени величина ξ связана с давлением прессования.
Процессы порошковой металлургии. Курс лекций |
-249- |

II. ФОРМОВАНИЕ И СПЕКАНИЕ ИЗДЕЛИЙ ИЗ МЕТАЛЛИЧЕСКИХ И НЕМЕТАЛЛИЧЕСКИХ ПОРОШКОВ
Лекция 2 Общие закономерности процессов формования порошков
Объясняется это относительным уменьшением сопротивляемости межчастичных контактов сдвигу, что наблюдается с возрастанием как давления прессования, так и пластичности прессуемого материала. Для малопластичных металлов (например, вольфрама) и хрупких материалов (например,
карбида кремния, нитрида алюминия и пр.) значение ξ несколько возрастает в области низких давлений, а выше 200 МПа остается постоянным. Для мел-
козернистого порошка ξ несколько понижается по сравнению с более крупнозернистым порошком, что объясняется влиянием повышенного межчастичного трения.
Боковое давление уменьшается по высоте прессовок, так как внешнее трение снижает давление прессования, приложенное к порошку в прессформе.
Контрольныевопросыизадания
1.Перечислите этапы уплотнения порошкового тела.
2.Изобразите идеализированную кривую уплотнения порошкового тела.
3.Объясните, почему на идеализированной кривой уплотнения порошкового тела, наблюдается участок, параллельный оси абцисс?
4.В чем отличие идеализированной кривой процесса уплотнения от реальной кривой?
5.Каким образом меняется плотность порошкового тела по высоте от поверхности подвижного пуансона к неподвижному при одностороннем
прессовании?
6.Что является причиной неоднородного распределения плотности по объему прессовки?
7.Приведите количественные зависимости плотности прессовки от давления прессования.
8.Что такое коэффициент бокового давления?
9.Перечислите факторы, от которых зависит коэффициент бокового
давления.
10. Почему у различных металлов, коэффициент бокового давления имеет разное значение?
Лекция3 Общиезакономерностипроцессовформованияпорошков
(продолжение)
План лекции
1.Трение при прессовании.
2.Давление выталкивания и упругое последействие.
3.Прочность прессовок.
4.Брак при прессовании
Процессы порошковой металлургии. Курс лекций |
-250- |

II. ФОРМОВАНИЕ И СПЕКАНИЕ ИЗДЕЛИЙ ИЗ МЕТАЛЛИЧЕСКИХ И НЕМЕТАЛЛИЧЕСКИХ ПОРОШКОВ
Лекция 3 Общие закономерности процессов формования порошков (продолжение)
Трениеприпрессовании
На процессы формообразования изделий при прессовании порошков значительное влияние оказывает трение. На практике различают внешнее и межчастичное трение. Действие внешнего трения (трения частиц порошка о стенки матрицы) приводит к неравномерному распределению плотности материала по объему прессовки, связанному с потерей усилия прессования на его преодоление.
Общее усилие Р, воздействующее на прессовку, будет равно:
Р = р2πD2/4. |
(2.21) |
Так как боковая поверхность цилиндрической прессовки равна πDh, то суммарное усилие Рr, на нее составляет Рr = pб πD2/4 = ξpπDh. Потеря усилия ∆P на преодоление трения частиц порошка о стенки пресс-формы
равна ∆P = f Рr = fξpπDh.
Таким образом, доля усилия прессования, которая тратится на трение порошка о стенки пресс-формы, определяется отношением∆P / Р и составляет:
∆P / Р = fξpπDh/[p(πD2 / 4)] = 4·f·ξ(h/D) . |
(2.22) |
Как правило, численные значения произведения 4fξ по мере возрастания плотности прессовки колеблются в пределах не более ± 3–5 %, т.е. остаются примерно постоянными в широком интервале давлений прессования.
Из этого следует, что доля затрат усилия прессования на преодоление внешнего трения порошка прямо пропорциональна высоте прессовки и обратно пропорциональна ее диаметру (поперечному размеру).
Для данных навески прессуемого порошка и размеров пресс-формы доля давления, теряемая на внешнее трение, – величина постоянная, пропорциональная приложенному давлению; она может составлять от 60 до 100 %.
Межчастичное трение, коэффициент которого fi может в несколько раз превышать коэффициент внешнего трения, при прессовании играет существенную роль, так как на его преодоление также затрачивается работа прессования, но зато давление прессования не теряется. Межчастичное трение определяет уровень достигаемой плотности прессовки, не влияет на ее объемное распределение, т.е. не приводит к неравноплотности прессовки.
Следствием проявления межчастичного трения следует считать затрудненность перемещения частиц порошка под прямым углом к направлению приложения прессующего усилия, в связи с чем невозможно получать высокие плотности в соответствующих зонах прессовки.
В общем случае потери усилия прессования на внешнее трение порошка должны зависеть от коэффициента трения в паре материал частицы
Процессы порошковой металлургии. Курс лекций |
-251- |

II. ФОРМОВАНИЕ И СПЕКАНИЕ ИЗДЕЛИЙ ИЗ МЕТАЛЛИЧЕСКИХ И НЕМЕТАЛЛИЧЕСКИХ ПОРОШКОВ
Лекция 3 Общие закономерности процессов формования порошков (продолжение)
прессуемого порошка – материал пресс-формы, склонности к схватыванию в этой паре, качества обработки внутренней стенки матрицы пресс-формы, наличия смазки, высоты насыпки прессуемого порошка (навески) и диаметра (поперечного размера) прессовки.
Известно, что с ростом плотности прессовки коэффициент межчастичного трения несколько уменьшается.
Помимо внешнего и межчастичного трения при изготовлении прессовки необходимо учитывать и такие параметры процесса прессования, как давление выталкивания и упругое последействие прессовки.
Давлениевыталкиванияиупругоепоследействиеформовок
Внешнее трение прессуемого порошка о стенки внутренней полости матрицы пресс-формы определяет усилие, необходимое для выталкивания прессовки после завершения ее формирования; соответствующее давление называют давлением выталкивания.
Давление выталкивания необходимо знать для решения практических вопросов прессования порошков, в частности для правильного расчета и конструирования пресс-инструмента. Давление выталкивания пропорционально давлению прессования и зависит от коэффициента внешнего трения и коэффициента Пуассона прессуемого порошка; обычно его принимают равным 0,2–0,35 давления прессования, и оно тем больше, чем выше прессовка и меньше площадь ее поперечного сечения.
Давление выталкивания всегда меньше потерь давления на трение порошка о стенку внутренней полости матрицы пресс-формы, что связано с изменением объема прессовки после снятия давления в результате действия внутренних (остаточных) напряжений, возникающих в процессе уплотнения порошка.
Увеличение размеров прессовки в результате действия упругих сил после снятия давления называют упругим последействием.
В связи с этим явлением целесообразно при прессовании выдерживать прессовку под нагрузкой в течение от нескольких секунд до 2–3 мин, что приводит к возрастанию ее плотности.
Основная часть упругого расширения прессовки происходит почти мгновенно при ее выпрессовывании в момент выхода из матрицы, а остальная часть требует определенного времени, вплоть до нескольких дней. Поэтому при изготовлении изделий точных размеров срок хранения прессовок перед спеканием не должен превышать нескольких часов.
Величина упругого последействия зависит от характеристик прессуемого порошка (дисперсности, формы и состояния поверхности частиц, содержания оксидов, механических свойств материала и др.), давления прессования, наличия смазки и ее количества, упругих свойств матрицы прессформы и пуансонов и других факторов.
Процессы порошковой металлургии. Курс лекций |
-252- |

II. ФОРМОВАНИЕ И СПЕКАНИЕ ИЗДЕЛИЙ ИЗ МЕТАЛЛИЧЕСКИХ И НЕМЕТАЛЛИЧЕСКИХ ПОРОШКОВ
Лекция 3 Общие закономерности процессов формования порошков (продолжение)
Относительное изменение линейных размеров прессовки вследствие упругого последействия определяют по выражению, %,
δi = (∆l / l0)100 = [(l1 – l0) / l0]100, |
(2.23) |
где δi – упругое последействие прессовки; ∆l – абсолютное расширение прессовки по длине или диаметру (поперечному размеру); l0 – длина или диаметр (поперечный размер) прессовки, находящейся в матрице пресс-формы под действием давления прессования; l1 – длина или диаметр (поперечный размер) прессовки после снятия с нее давления прессования или выпрессовывания из матрицы пресс-формы.
Объемное упругое последействие прессовки определяют по аналогичной зависимости, %:
δV = (∆V / V0)100 = [(V1 – V0) / V0]100, |
(2.24) |
Эффект упругого последействия по высоте прессовки больше, чем в поперечном направлении, и составляет при одностороннем прессовании до 5–6 % (в поперечном направлении – 1–3 %). Это связано с большим ос е- вым (вертикальным) давлением прессования по сравнению с боковым давлением, а также с упругой деформацией матрицы пресс-формы, благодаря которой после снятия давления высота прессовки также увеличивается.
Потеря давления прессования из-за внешнего трения порошка, приводя к неравноплотности прессовки, влияет также на изменение упругого последействия по ее высоте. Упругое последействие частично снимает напряжения на контактных участках прессовки, что приводит к уменьшению их числа и суммарной площади. Разрыв контактов между частицами на большом протяжении может вызвать нарушение целостности прессовок, называемое расслоем, а иногда и их разрушение.
При переходе от порошкообразной массы к напряженному консолидированному порошковому телу величина упругого последействия изменяется. По мере увеличения давления прессования упругое последействие в направлении приложения давления сначала возрастает (в порошковом теле происходит формирование и увеличение межчастичных контактов), затем снижается из-за повышения прочности контактов между частицами и снова возрастает, так как упругие напряжения растут, а прочность межчастичных контактов изменяется мало.
Упругое расширение прессовки зависит от взаимодействия двух параметров – упругого последействия и прочности контактов между частицами; оно увеличивается под действием факторов, уменьшающих прочность прессовки (меньшая шероховатость поверхности частиц порошка, увеличение содержания в порошке оксидов и примесей, высокая твердость прессуе-
Процессы порошковой металлургии. Курс лекций |
-253- |
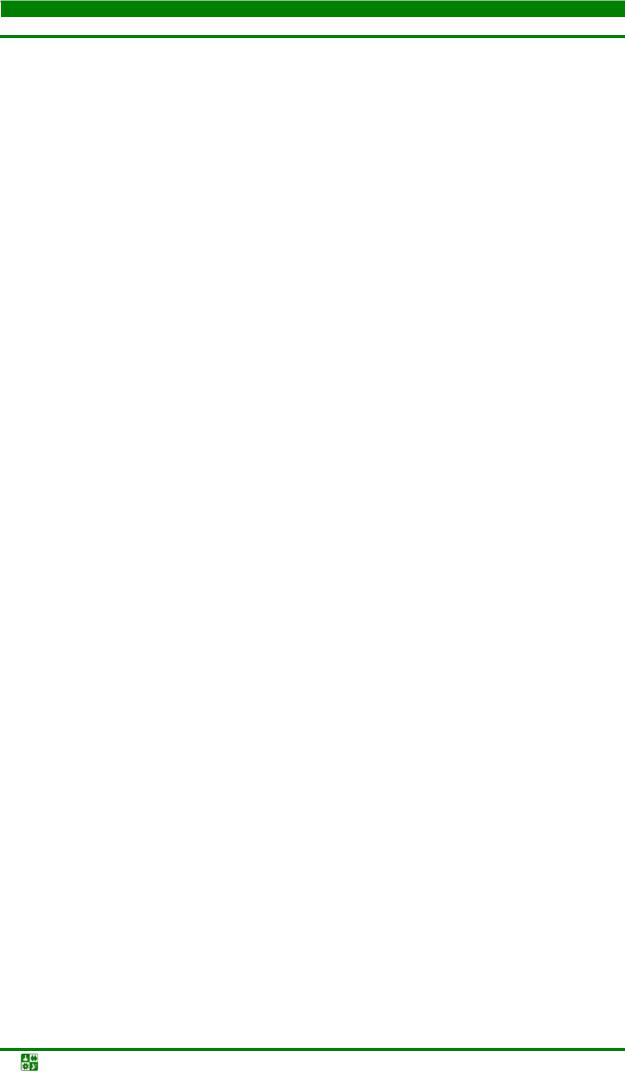
II. ФОРМОВАНИЕ И СПЕКАНИЕ ИЗДЕЛИЙ ИЗ МЕТАЛЛИЧЕСКИХ И НЕМЕТАЛЛИЧЕСКИХ ПОРОШКОВ
Лекция 3 Общие закономерности процессов формования порошков (продолжение)
мого материала). Упругое последействие в прессовках из хрупких и твердых материалов больше, чем у прессовок из мягких и пластичных материалов.
Упругое последействие у порошков хрупких и твердых материалов больше, чем у пластичных материалов. Так как прочность прессовки их твердого материала меньше, то для повышения ее прочности большее значение имеет упругая деформация.
Применение оптимального количества смазки при прессовании позволяет уменьшить величину упругого последействия прессовки, особенно в случае совместного применения смазок и поверхностно-активных веществ.
Прочностьпрессовок
Прочность прессовок определяется как механическим зацеплением так и микросхватыванием отдельных участков (неровностей) частиц порошка. В зависимости от природы порошка, его физических и химических свойств действие тех или иных сил будет проявляться в большей или меньшей степени.
Диаграммы деформации порошковой прессовки качественно не отличаются от диаграмм деформации компактного металла. Прочность прессовок обусловлена главным образом сопротивлением сдвигу межчастичных контактов, и при сжатии она во много раз больше, чем при растяжении, когда разрушение прессовки происходит в результате сдвига и отрыва контактов.
Установлено, что прочность прессовки при сжатии в направлении прессования всегда больше прочности в перпендикулярном к нему направлении, так как направление прессования совпадает с направлением заклинивания частиц, тогда как при растяжении она обычно меньше.
Известно, что прочность компактных литых металлов растет с увеличением твердости, т.е. вольфрам прочнее железа, железо прочнее меди, а медь прочнее олова. Для порошковых прессовок эта зависимость прямо противоположна; прочность их растет не с твердостью, а с мягкостью и пластичностью металла: прессовки из олова прочнее прессовок из меди, из меди прочнее, чем из железа, а из железа прочнее, чем из вольфрама. Это связано с тем, что у пластичных материалов деформационные превращения, сопровождающиеся развитием площади контактов, протекают при более низких давлениях. После снятия давления и выпрессовки из матрицы пресс-формы у твердых материалов в результате упругого последействия контактная поверхность уменьшается и прочность прессовки будет определяться в основном силами механического зацепления частиц.
Так как прочность прессовки пропорциональна контактной поверхности между частицами, она зависит от давления прессования: при низких давлениях прессования (первый этап формирования прочности) прочность прессовки возрастает быстрее давления (скорость роста плотности прессовки высока), при средних давлениях прессования (второй этап) прочность прессовки растет приблизительно пропорционально первой степени давления и при высоких давлениях прессования (третий этап) нарастание прочности прес-
Процессы порошковой металлургии. Курс лекций |
-254- |
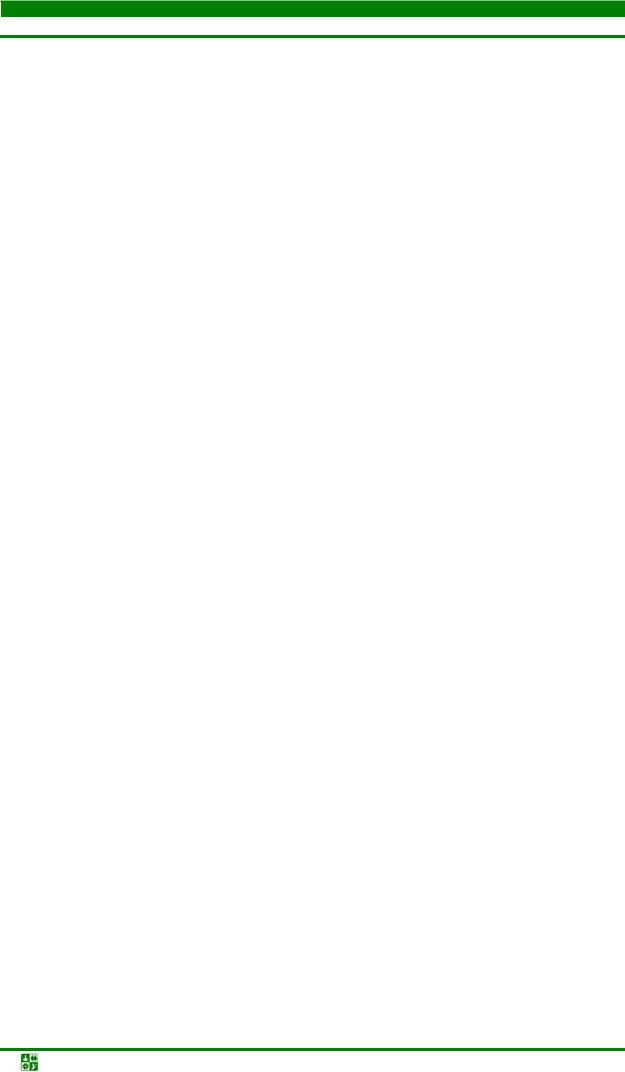
II. ФОРМОВАНИЕ И СПЕКАНИЕ ИЗДЕЛИЙ ИЗ МЕТАЛЛИЧЕСКИХ И НЕМЕТАЛЛИЧЕСКИХ ПОРОШКОВ
Лекция 3 Общие закономерности процессов формования порошков (продолжение)
совки существенно замедляется (плотность прессовки и площадки межчастичных контактов увеличиваются незначительно).
При прочих равных условиях на прочность прессовки значительное влияние оказывают гранулометрический состав и насыпная плотность порошка, точнее коэффициент обжатия К = γп/γнас (где γп – плотность прессовки при данном давлении прессования). Чем больше К при одной и той же плотности прессовки, тем сильнее обжатие порошка и тем прочнее прессовка. Минимальное значение К, необходимое для получения прессовок достаточной прочности из порошков пластичных металлов с сильно шероховатой и разветвленной формой частиц, составляет примерно 1,7–1,8. Прочность прессовок понижается при загрязнении порошков оксидами (при толстой оксидной пленке), что объясняется увеличением твердости поверхностного слоя частиц при одновременном снижении их пластичности и уменьшении металлической контактной поверхности.
Принято характеризовать прессовки прочностью на сжатие и на изгиб, так как их прочность на разрыв (на растяжение) невелика и обычно не превышает нескольких килограммов на квадратный сантиметр.
Бракприпрессовании
Наиболее часто встречающийся на практике и наиболее опасный вид брака прессовок – расслой (поперечные или диагональные трещины). Появление таких трещин обусловлено тем, что при выталкивании прессовки из матрицы пресс-формы происходит ее расширение. Разрушение (возникновение трещин) происходит по границам действия деформаций, вызванных указанными процессами. Наибольшее значение имеют следующие причины образования поперечных или диагональных трещин:
1.Условия прессования, способствующие уменьшению прочности прессовок: использование гладких плоских или сфероидизированных частиц, заметное окисление и наклеп частиц, введение в состав порошка слишком большого количества смазки.
2.Высокие давления прессования (особенно для материалов высокой твердости). Известно, что упругие силы, вызывающие растрескивание, растут пропорционально давлению, а рост прочности межчастичных контактов замедлен.
3.Плохое качество смешивания или использование химически неоднородного материала, вызывающее неравномерное распределение в объеме прессовки примесей или компонентов сложной порошковой смеси.
4.Слишком медленное или слишком быстрое выпрессовывание изделия из матрицы пресс-формы и в особенности остановки во время выпрессовывания. Для ускорения выпрессовывания рекомендуется применять разъемные матрицы. Необходимо, чтобы конструкция матрицы в этом случае пре-
Процессы порошковой металлургии. Курс лекций |
-255- |

II. ФОРМОВАНИЕ И СПЕКАНИЕ ИЗДЕЛИЙ ИЗ МЕТАЛЛИЧЕСКИХ И НЕМЕТАЛЛИЧЕСКИХ ПОРОШКОВ
Лекция 3 Общие закономерности процессов формования порошков (продолжение)
дотвращала сдвиг ее стенок в процессе прессования или выталкивания прессовки.
5.Наличие в прессуемой заготовке тонких стенок или резких переходов.
6.Неравномерное распределением порошка по объему засыпной полости матрицы пресс-формы.
7.Низкое давление прессования или неправильная (заниженная) величина навески порошка.
В некоторых случаях имеет место брак по размерам, связанный с неправильной конструкцией или размерами пресс-формы, неточностью дозирования порошка или нарушением режима прессования (завышением или занижением давления прессования). На поверхности прессовки могут появляться риски из-за неудовлетворительного качества рабочей поверхности матрицы; на торцах прессовки могут наблюдаться сколы, осыпания и образование заусенцев из-за плохой обработки рабочей поверхности пуансонов или выработки их торцовых кромок.
Для снижения брака необходимо установить его причины и принять меры к их устранению. Брак при прессовании обычно составляет около 2–3 %. Бракованные по тем или иным признакам прессовки могут быть возвращены
впроизводство после соответствующего дробления и измельчения. Порошок, полученный в результате измельчения бракованных изделий можно небольшими порциями (до 10–15 %) подмешивать к исходному материалу. Однако при этом может наблюдаться некоторое снижение механических свойств готовых порошковых изделий.
Контрольныевопросыизадания
1.Какие виды трения различают при прессовании порошков?
2.Как можно снизить трение?
3.Как рассчитать долю усилия прессования, затрачиваемого на внешнее трение?
4.Почему внешнее трение больше межчастичного?
5.Что такое «упругое последействие и как оно проявляется?
6.Какие факторы, определяют давление выталкивания?
7.От чего зависит прочность прессовок?
8.Какими показателями характеризуется прочность прессовок?
9.Перечислите виды брака при формовании изделий.
10.Укажите меры по устранению причин брак при прессовании по-
рошков.
Процессы порошковой металлургии. Курс лекций |
-256- |
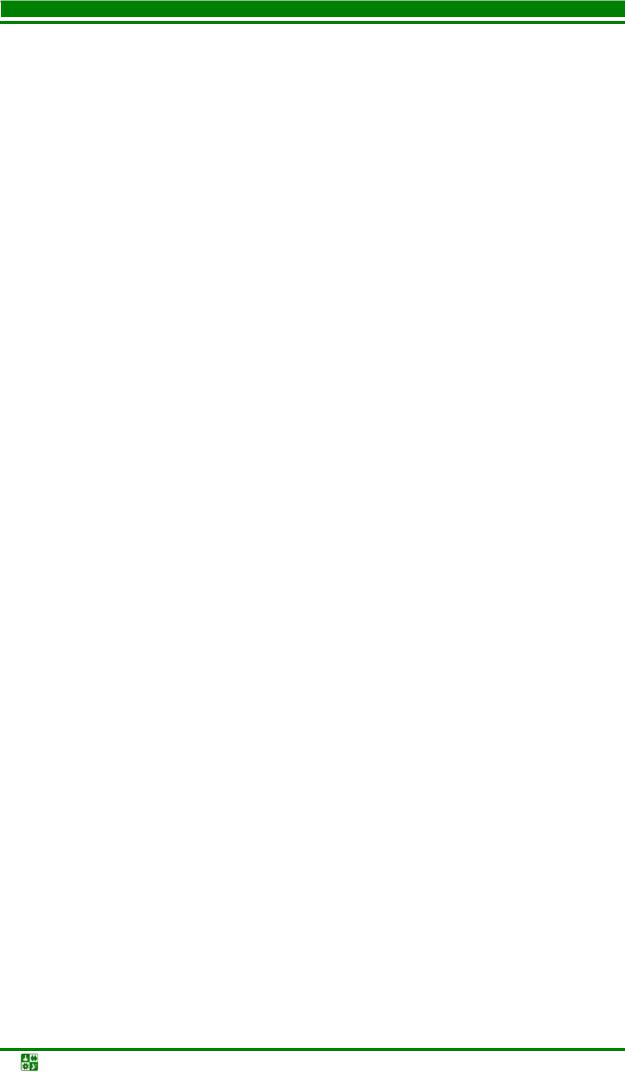
II. ФОРМОВАНИЕ И СПЕКАНИЕ ИЗДЕЛИЙ ИЗ МЕТАЛЛИЧЕСКИХ И НЕМЕТАЛЛИЧЕСКИХ ПОРОШКОВ
Лекция4 Холодноеизостатическоепрессование
План лекции
1.Виды изостатического формования.
2.Оборудование для ХИП.
3.Материалы оболочек.
4.Установки и цикл ХИП.
5.Уплотнение порошка при гидроформировании.
6.Виды брака.
Видыизостатическогоформования
Изостатическое формование – формование металлического порошка в эластичной или деформируемой оболочке в условиях всестороннего сжатия. Изостатическое формование позволяет получать из порошка заготовки (порошковые формовки) с большим отношением длины к диаметру (ширине) и тонкими стенками, обладающие равномерной объемной плотностью.
В настоящее время выделяют три базовые разновидности изостатического формования:
гидростатическое, газостатическое, в эластичных оболочках.
ОборудованиедляХИП
Методом ХИП, который часто называют гидростатическим формованием, получают цилиндры, штабики, трубы, шары и другие изделия как сравнительно простой, так и весьма сложной формы единичной массы от нескольких грамм до нескольких сотен килограмм.
Гидростатическое формование исторически является первым вариантом изостатического формования (1913–1919 гг.), когда порошок в резиновой оболочке сжимали усилием, создаваемым жидкостью в рабочей камере гидростата (рис. 2.12, а). В последующем этот вариант получил название метода
«свободной матрицы (оболочки)», или метод «мокрого» мешка; заполнение матрицы (оболочки) порошком и удаление из нее формовки производят вне установки гидростатического формования.
Процессы порошковой металлургии. Курс лекций |
-257- |

II. ФОРМОВАНИЕ И СПЕКАНИЕ ИЗДЕЛИЙ ИЗ МЕТАЛЛИЧЕСКИХ И НЕМЕТАЛЛИЧЕСКИХ ПОРОШКОВ
Лекция 4 Холодное изостатическое прессование
|
6 |
|
|
|
|
3 |
|
9 |
|
1 |
|
1 |
||
4 |
|
|||
5 |
3 |
|||
|
||||
|
|
|
||
2 |
|
|
2 |
|
1 |
|
4 |
3 |
|
|
||
2 |
7 |
|
8 |
||
|
а б в
Рис. 2.12. Схемы методов холодного изостатического прессования: 1 – контейнер; 2 – жидкость высокого давления; 3 – порошок; 4 – эластичная оболочка; 5 – компрессор; 6, 7
–уплотняющие затворы; 8 – выталкиватель формовки; 9 – матрица типа «сухого мешка»
В1929 г. были запатентованы (патенты США) две разновидности формования изделий жидкостью высокого давления: методом «встроенной или фиксированной матрицы», или метод «сухого мешка» (рис. 2.12, б) и ра-
диальное уплотнение методом «сухого» мешка (рис. 2.12, в). Матрица (обо-
лочка) жестко связана с камерой давления гидростата, и изостатическое уплотнение достигается за счет действия реактивных сил в направлении верхнего уплотнителя или только в результате действия сил в радиальном направлении. На практике используют еще один вариант формования по методу «сухого» мешка, который назван методом «трехосного» формования: сначала порошок подвергают радиальному уплотнению жидкостью по типу «сухого» мешка, а затем, не снимая давления жидкости, допрессовывают в осевом (вертикальном) направлении пуансонами по схеме двустороннего прессования (осевое давление должно превышать давление, создаваемое жидкостью).
За счет применения подобного способа формования можно получить большие значения плотности (на 10–25 %) и прочности формовки, чем при других вариантах холодного изостатического формования.
Широкая промышленная реализация гидростатического формования началась при использовании этого метода в керамической промышленности, для изготовления изделий сложной (ребристой, конической и пр.) формы.
К преимуществам метода гидростатического формования относится то, что большинстве случаев удается получить изделие с более высокой плотностью и прочность формовки при давлениях, сопоставимых с давлениями холодного одно- и двухстороннего прессования. Кроме того, при применении этого метода:
наблюдается высокая равноплотность изделия; напряжения в объеме формовки незначительны из-за отсутствия пре-
имущественного направления приложения усилия уплотнения и практически отсутствующего внешнего трения;
можно формовать порошок без смазки или при ее минимальном коли-
честве;
Процессы порошковой металлургии. Курс лекций |
-258- |
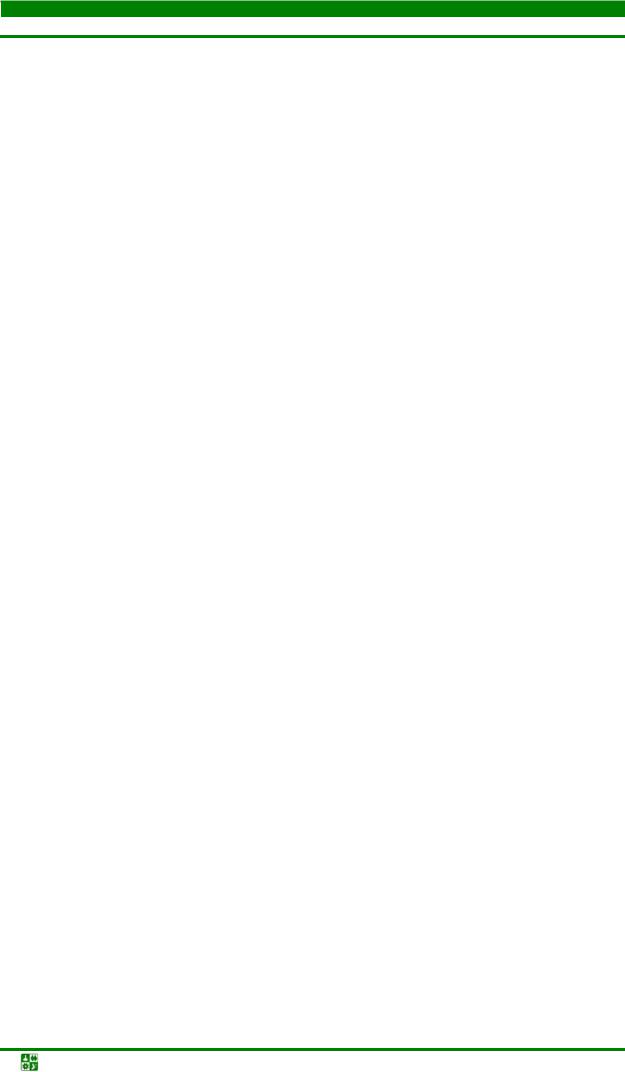
II. ФОРМОВАНИЕ И СПЕКАНИЕ ИЗДЕЛИЙ ИЗ МЕТАЛЛИЧЕСКИХ И НЕМЕТАЛЛИЧЕСКИХ ПОРОШКОВ
Лекция 4 Холодное изостатическое прессование
однородная (без текстуры) структура формовки; уменьшенная усадка при спекании;
более высокая и равномерная плотность заготовки после спекания; можно получать крупногабаритные изделия (ограничения по размеру
связаны только с габаритами гидростата); можно получать изделия сложной формы;
достаточно легко получать изделия из композитов и пр. К недостаткам этого метода относятся:
низкая точность изготовления изделий (необходимость дальнейшей механической обработки неспеченного порошкового тела);
длительность полного цикла формования (по сравнению с другими методами);
высокая чувствительность к химически загрязнениям; быстрый износ эластичных оболочек и пр.
В самом общем случае для организации гидростатического формования необходимы: жидкость, эластичные оболочки и специальные устройства (гидростаты) с системой создания давления жидкости на оболочку с порошком.
Уплотнение порошка, помещенного в эластичную оболочку, осуществляют жидкостью высокого давления (масло, вода с добавками ингибиторов коррозии, водные эмульсии масел, глицерин и др.), к которой предъявляют определенные требования:
1)наименьшая цена и легкая доступность;
2)совместимость с материалом рабочей камеры гидростата и с эластичной оболочкой для формования порошка (например, натуральная резина или материалы на основе полихлорвинила неприемлемы для работы в масле без дополнительного защитного чехла);
3)сжимаемость рабочей жидкости должна быть как можно меньше. При большой сжимаемости жидкости время накачки ее в рабочую камеру гидростата становится слишком большим, возрастают запас энергии в гидростате и опасность его разрушения при возникновении течи под высоким давлением;
4)легкость отделения порошка от рабочей жидкости при прорыве эластичной оболочки с ним.
Материалыоболочек
Правильный выбор материала оболочки весьма важен, так как от него зависят результаты формования. В общем виде такой материал должен обладать следующими свойствами: низким модулем продольной упругости (~10-5 модуля упругости металла); низкой адгезией к порошку; большой усадкой при сжатии; хорошей обрабатываемостью и износостойкостью; стойкостью к маслу и воде и пр.
В табл. 2.1 приведены сведения о некоторых материалах, которые используются для изготовления эластичных оболочек.
Процессы порошковой металлургии. Курс лекций |
-259- |

II. ФОРМОВАНИЕ И СПЕКАНИЕ ИЗДЕЛИЙ ИЗ МЕТАЛЛИЧЕСКИХ И НЕМЕТАЛЛИЧЕСКИХ ПОРОШКОВ
Лекция 4 Холодное изостатическое прессование
|
|
|
Таблица 2.1 |
Материалы для изготовления эластичных оболочек |
|
||
|
|
|
|
|
Метод изготовления |
Пригодность для гидро- |
|
Материал |
статического формования |
||
|
оболочки |
|
|
|
А |
Б |
|
|
|
||
Натуральный и синтетический каучук |
Окунание заготовки |
2–3/0–2 |
0/0 |
Натуральный и синтетический каучук |
Горячее литье |
2–3/1–3 |
2–4/1–2 |
Неопреновая резина |
Окунание |
2/0–2 |
0/0 |
Неопреновая и нитриловая резина |
Горячее литье |
2–4/1–3 |
3–4/1–2 |
Силиконовая резина |
Литье |
0–1/0 |
0/0 |
Поливинилхлорид |
– |
1–2/1–2 |
0/0 |
Однокомпонентный полиуретан |
Горячее литье |
2–3/1–2 |
0–2/0–1 |
Двухкомпонентный полиуретан |
Холодное литье |
1–2/0–1 |
0–1/0 |
П р и м е ч а н и я. 1. А – формование по методу «мокрого» мешка; Б – формование по методу «сухого» мешка.
2. Пригодность: 0 – не рекомендуется; 1 – плохая; 2 – удовлетворительная; 3 – хорошая; 4 – отличная; в числителе – с высокой, хорошей текучестью и распыленных порошков; в знаменателе – с плохой текучестью порошков с частицами высокой твердости и неправильной формы.
Наиболее целесообразна толщина стенки эластичной оболочки 1,5–6 мм (более толстостенные служат дольше, но сложнее в обращении и могут приводить к расслоению формовки).
Для изготовления заготовок сложной формы нужны тонкостенные оболочки, но они быстро выходят из строя (1–2 формовки).
Для ориентировочного определения габаритных размеров эластичной оболочки для получения изделий сравнительно простой формы (стержней, цилиндров или цилиндрических труб), имеющих постоянное сечения можно воспользоваться соотношениями:
для стержней или цилиндров
D = d3 К , L = l,
L = l – l1 («сухой» мешок без осевого сжатия);
для цилиндрических труб с открытыми торцами (заглушки при фор-
мовании жестко закреплены)
D = К(d2 −b2 ) +b2 + b2, d1 = b – d2,
где D – внутренний диаметр эластичной оболочки; d – диаметр формовки; b – внутренний диаметр трубной формовки; d1 – диаметр центрального стержня для формования трубной заготовки; d2 – усадка по диаметру трубной фор-
Процессы порошковой металлургии. Курс лекций |
-260- |

II. ФОРМОВАНИЕ И СПЕКАНИЕ ИЗДЕЛИЙ ИЗ МЕТАЛЛИЧЕСКИХ И НЕМЕТАЛЛИЧЕСКИХ ПОРОШКОВ
Лекция 4 Холодное изостатическое прессование
мовки; L – длина рабочей зоны эластичной оболочки; l – длина формовки; l1 – осевая усадка формовки; К – коэффициент уплотнения (обжатия) порошка, К = γп/γнас (γп – плотность формовки при соответствующем рабочем давлении; γнас – насыпная плотность порошка).
Отклонение размеров формовок от расчетных составляет до 3–4 % (для тонкостенных труб точность выше).
Точный расчет размеров рабочей зоны эластичной оболочки для изделий сложной формы со ступенчатым профилем, переменным сечением и т.п. является практически неразрешимой задачей. В этом случае размеры формы (оболочки) определяются опытным путем (изготавливают пробную формовку, испытывают ее и в дальнейшем проводят корректировку размеров эластичной оболочки).
УстановкиициклХИП
Для ХИП обычно используют следующие установки: специализированные гидростаты; камеры, в которых необходимое давление создается с помощью гид-
равлических прессов (гидростатическое формование); камеры, в которых давление создается при взрыве порохового заряда
(гидродинамическое формование).
Гидростаты. По способу создания давления в рабочей камере гидростаты бывают насосные, плунжерные и мультипликаторные. Они могут быть рамной или безрамной конструкции. В гидростатах рамной конструкции осевое усилие от жидкости через уплотняющие затворы рабочей камеры передается на силовую раму установки. Гидростаты безрамной конструкции снабжены резьбовыми байонетными затворами (рис. 2.13).
Рис. 2.13. Схема гидростата безрамной конструкции: 1 – компрессор; 2 – камера формования; 3 – порошок; 4 – эластичная оболочка; 5 – манометр; 6 – затвор; 7 – клапан
7 |
6 |
|
|
|
5 |
|
4 |
|
|
3 |
1 |
|
2 |
|
|
|
Основными узлами гидростатов являются контейнер (рабочая камера), станина, гидропривод и установка для создания высокого давления жидкости. Гидростаты рамной конструкции изготавливают как с отдельно установ-
Процессы порошковой металлургии. Курс лекций |
-261- |
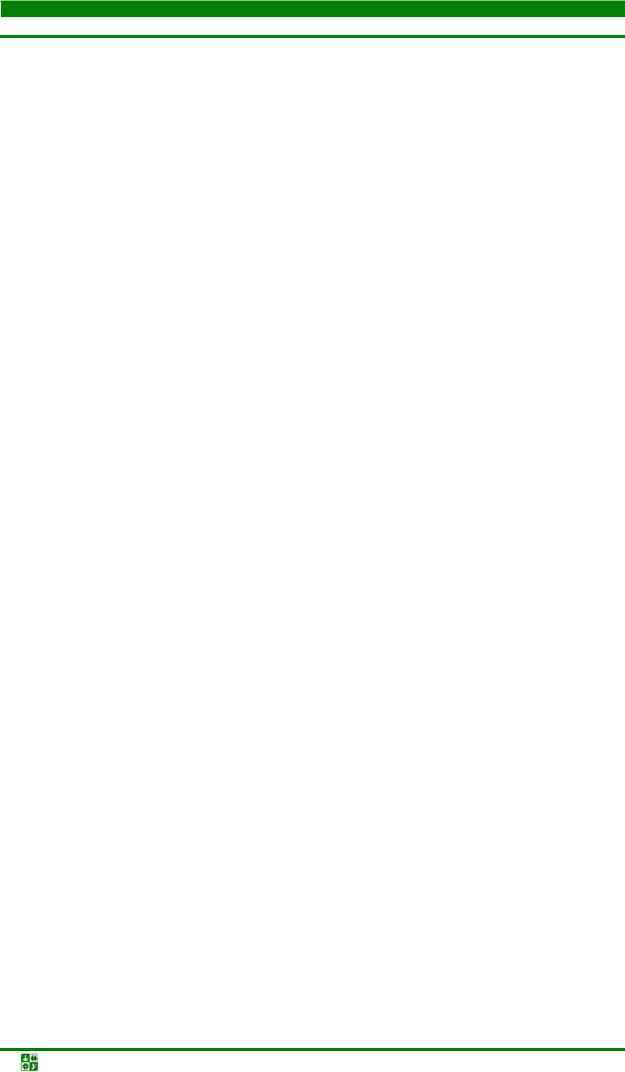
II. ФОРМОВАНИЕ И СПЕКАНИЕ ИЗДЕЛИЙ ИЗ МЕТАЛЛИЧЕСКИХ И НЕМЕТАЛЛИЧЕСКИХ ПОРОШКОВ
Лекция 4 Холодное изостатическое прессование
ленным насосом высокого давления или мультипликатором, так и со встроенным мультипликатоом. Гидростаты безрамного типа имеют меньшую металлоемкость по сравнению с гидростатами других типов. Внутренний диаметр рабочей камеры гидростатов до 1 500 мм, длина – до 25 200 мм, рабочее давление 200–600 МПа.
Гидростатические прессы. В таких установках нагрузка, создаваемая гидравлическим прессом (поршнем пресса), передается через жидкость к уплотняемому порошку, загруженному в эластичную оболочку, которая помещается в рабочей камере. Диаметр рабочей камеры пресса – 40–130 мм, давлении прессования – до 2 000 МПа, максимальная длина формовок– до 500 мм.
Гидродинамические машины. Конструкция этих машин практически аналогична гидростатам, но необходимое давление создается за счет сгорания порохового заряда небольшой массы в рабочей камере. Пороховой заряд, воспламеняясь в изолированной пороховой камере, создает давление на рабочую жидкость, через промежуточный поршень. Подобные установки позволяют получать давления до 1 500 МПа (рабочее давление до 600 МПа). Размеры рабочей камеры: диаметр – 200–350 мм, длина – 500–1 000 мм.
Рабочий цикл ХИП зависит от метода формования. При формовании по методу «мокрого» мешка рабочий цикл включает следующие операции:
1)подготовка шихтового состава порошка (оптимального фракционного состава) и смешивание компонентов шихты;
2)подготовка порции порошка необходимого объема (массы);
3)заполнение подготовленной навеской порошка эластичной оболочки
иего уплотнение(в том числе– с использованием вибрационного уплотнения);
4)герметизация оболочки с порошком;
5)дегазация порошка (вакуумирование оболочки);
6)установка оболочки с порошком в рабочую камеру гидростата;
7)герметизация рабочей камеры гидростата;
8)создание давления рабочей жидкости в камере высокого давления гидростата;
9)выдержка оболочки с порошком под давлением рабочей жидкости в течениие заданного времени (если необходимо);
10)сброс давления;
11)вскрытие рабочей камеры гидростата;
12)извлечение оболочки с формовкой из рабочей камеры гидростата;
13)разгерметизация оболочки и извлечение формовки из оболочки;
14)зачистка поверхности формовки (выравнивание поверхности – устранение дефектов).
При гидростатического формования по методу «сухого» мешка рабочий цикл несколько короче:
1)подготовка шихтового состава порошка (оптимального фракционного состава) и смешивания компонентов шихты;
2)заполнение подготовленной навеской порошка эластичной оболочки и его уплотнения (в том числе – с использованием вибрационного уплотнения);
Процессы порошковой металлургии. Курс лекций |
-262- |

II. ФОРМОВАНИЕ И СПЕКАНИЕ ИЗДЕЛИЙ ИЗ МЕТАЛЛИЧЕСКИХ И НЕМЕТАЛЛИЧЕСКИХ ПОРОШКОВ
Лекция 4 Холодное изостатическое прессование
3)герметизация оболочки с порошком;
4)дегазация порошка (вакуумирование оболочки);
5)герметизация рабочей камеры гидростата;
6)создание давления рабочей жидкости в камере высокого давления гидростата;
7)выдержка оболочки с порошком под давлением рабочей жидкости в течение заданного времени (если необходимо);
8)сброс давления;
9)вскрытие рабочей камеры гидростата, разгерметизация оболочки и извлечение формовки из оболочки;
10)зачистка поверхности формовки (выравнивание поверхности – устранение дефектов).
Уплотнениепорошкапригидроформовани
Жидкость высокого давления всесторонне и равномерно сжимает порошок, находящийся в эластичной оболочке. Потери давления на преодоление трения частиц порошка о стенку оболочки почти отсутствуют. Это связано с тем, что при гидростатическом формовании частицы порошка, прилегающие к поверхности оболочки, перемещаются (в основном) вместе с этой поверхностью. Так как сжатие является всесторонним и равномерным по величине во всех направлениях, то коэффициент бокового давления следует полагать равным единице.
Необходимо отметить, что во внутренних областях сравнительно крупных сферических и цилиндрических заготовок из порошков пластичных металлов или сплавов пористость несколько выше. Это явление связано с наличием в порошковом теле арок, которые не полностью передают давление его внутренним областям и могут сохраняться даже при высокой плотности порошковой формовки.
При гидростатическом формовании обеспечивается не только равномерная плотность заготовок, но и устраняется также анизотропия их структуры, которая при прессовании в пресс-форме связана с ориентированным расположением частиц при одноосном сжатии и проявляется в неодинаковых значениях усадки, прочности, газопроницаемости и других характеристик прессовок в различных направлениях.
При гидростатическом формовании воздух (газ) не имеет выхода из герметично закрытой оболочки, в связи с чем желательна предварительная дегазация (вакуумирование) уплотняемого порошка, например при помощи тонкой иглы со сквозным каналом, вставляемой в оболочку и подключаемой к вакуумной системе. В противном случае газ в порах между частицами порошка сжимается (при изменении пористости порошкового тела с 50 до 5 % давление газа в порах возрастает до 2,5 МПа) и после снятия давления может вызвать нарушение целостности формовки. Поэтому, если порошок перед
Процессы порошковой металлургии. Курс лекций |
-263- |
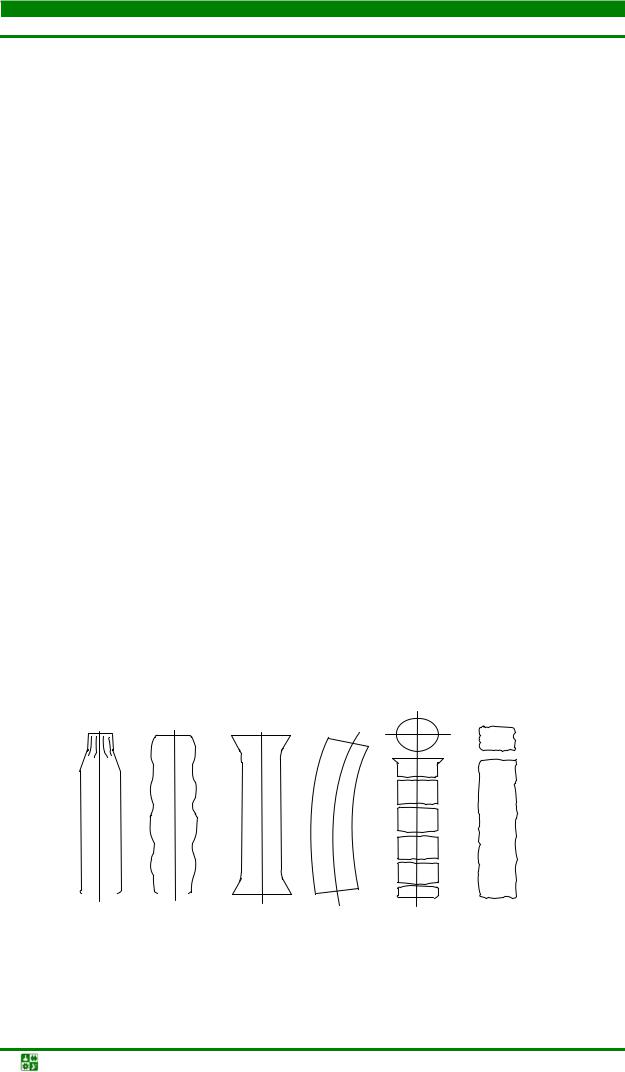
II. ФОРМОВАНИЕ И СПЕКАНИЕ ИЗДЕЛИЙ ИЗ МЕТАЛЛИЧЕСКИХ И НЕМЕТАЛЛИЧЕСКИХ ПОРОШКОВ
Лекция 4 Холодное изостатическое прессование
прессованием не вакуумировали, давление в рабочей камере рекомендуется сбрасывать медленно (в течение нескольких минут).
Исходя из предпосылки о том, что механизмы уплотнения порошков при прессовании и гидростатическом формовании аналогичны (при гидроформовании также можно выделить три стадииуплотнения), то давления гидростатического формования ри и прессования р соответствуют соотношению:
ри/p = (1+ 2ξ)/3,
где ξ – коэффициент бокового давления.
Видыбрака
На рис. 2.14 показаны характерные дефекты заготовок, полученных по методу «мокрого» мешка. Возможные причины появления таких дефектов:
1)нехватка или неконтролируемая усадка порошка, засыпанного в эластичную оболочку;
2)недостаточно жесткая оболочка, которая способна деформировать-
ся при засыпке в нее порошка;
3)неравномерная засыпка порошка в оболочку или его плохая
текучесть;
4)слишком тонкая стенка оболочки;
5)жесткие заглушки для герметизации оболочки с порошком;
6)порошок с излишне высокой уплотняемостью;
7)высокая пластичность частиц порошка;
8)неправильно выбранный материал эластичной оболочки;
9)слишком толстые стенки оболочки;
10)недостаточная плотность формовки;
11)малый радиус скругления углов формовки.
|
|
|
|
|
|
|
|
|
|
|
|
|
|
|
|
|
|
|
|
|
|
|
|
|
|
|
|
|
|
|
|
|
|
|
|
|
|
|
|
|
|
|
|
|
|
|
|
|
|
|
|
|
|
|
|
|
|
|
|
|
|
|
|
|
|
|
|
|
|
|
|
|
|
|
|
|
|
|
|
|
|
|
|
|
|
|
|
|
|
|
|
|
|
|
|
|
|
|
|
|
|
|
|
|
|
|
|
|
|
|
|
|
|
|
|
|
|
|
|
|
|
|
|
|
|
|
|
|
|
|
|
1 |
2 |
3 |
4 |
5 |
6 |
Рис. 2.14. Виды брака заготовок, сформованных ХИП по методу «мокрого мешка»: 1 – образование шейки; 2 – неравномерная усадка; 3 – «ступня слона»; 4 – «банан»; 5 – расслоение; 6 – скол кромок
Процессы порошковой металлургии. Курс лекций |
-264- |

II. ФОРМОВАНИЕ И СПЕКАНИЕ ИЗДЕЛИЙ ИЗ МЕТАЛЛИЧЕСКИХ И НЕМЕТАЛЛИЧЕСКИХ ПОРОШКОВ
Лекция 4 Холодное изостатическое прессование
При гидроформовании по методу «сухого» мешка могут возникать различные дефекты заготовок:
расслоение (осевое) возникает из-за смещения стенок эластичной оболочки при разгрузке;
образование шейки связано с недостаточной загрузкой или усадкой засыпанного в оболочку порошка;
растрескивание и расслоение (радиальное и осевое) происходит из-за высокого давления формования и осевого упругого последействия;
осевое растрескивание имеет место при слишком быстром снятии давления со сформованной заготовки или из-за избыточного количества смазки (пластификатора) в порошке.
Контрольныевопросыизадания
1. В чем заключается суть метода холодного изостатического формо-
вания?
2.Перечислите операции цикла ХИП.
3.Назовите способы ХИП.
4.Из каких материалов изготавливают оболочки, используемые при ХИП порошков?
5.Перечислите основные требования, предъявляемые к рабочей жид-
кости.
6.Какие установки применяют при ХИП порошков?
7.Назовите основные виды брака при ХИП.
Лекция5 Горячееизостатическое(газостатическое) прессование
План лекции
1.Устройство газостатов.
2.Цикл прессования.
3.Технологическая оснастка и оборудование, используемое при прессовании порошков методом ХИП.
4.Режимы горячего изостатического прессования(ГИП) изделий.
Первые исследования процесса формования порошка в деформируемых оболочках одновременным воздействием давления сжатого газа и температуры были выполнены в 50-е гг. XX в. в Беттелевском мемориальном институте (США) при отработке технологии изготовления топливных элементов ядерных реакторов.
Процессы порошковой металлургии. Курс лекций |
-265- |

II. ФОРМОВАНИЕ И СПЕКАНИЕ ИЗДЕЛИЙ ИЗ МЕТАЛЛИЧЕСКИХ И НЕМЕТАЛЛИЧЕСКИХ ПОРОШКОВ
Лекция 5 Горячее изостатическое (газостатическое) прессование
Внастоящее время происходит расширение производственных мощностей этого метода, связанное прежде всего с использованием его для изготовления изделий на основе порошков жаропрочных и инструментальных сплавов, титана и бериллия.
Впроцессе ГИП порошок одновременно спрессовывается (давление до 200 МПа) и спекается (температуры до 1 500–2 000 °С), образуя формовку
сплотностью, близкой к теоретической, и высокими механическими свойствами. Так, например, при изготовлении турбинных дисков газостатической обработкой порошков они имеют повышенную жаропрочность (на 7–15 % выше прочности изделий, полученных литьем с последующей пластической деформацией), а ресурс их работы увеличивается в 1,3–1,8 раза. Припуски на механическую обработку сокращаются в 2–3 раза, уменьшается ее трудоемкость на 30–40 %, снижаются расход металла и стоимость изготовления изделий.
К основным достоинствам метода ГИП порошковых материалов отно-
сят: возможность улучшить служебные свойства получаемых материалов, заготовок и изделий и возможность варьирования параметров обработки
(давления, температуры, времени), обеспечивающих на одном и том же оборудовании получение заготовки и изделий из материалов, имеющих различную химическую природу;
Объективными недостатками ГИП являются сравнительно невысокие давления формования, большая длительность рабочего цикла (относительно
низкая производительность), высокая стоимость оборудования; сравнительно простая форма получаемых изделий.
В качестве рабочей среды при ГИП чаще всего используют аргон, гелий или азот (редко). В некоторых случаях применяют водород, оксиды углерода или сероводород. Любой из этих газов должен иметь высокую чистоту (содержание примесей не выше (1–2)·10-6 % (об.)) и обладать высокой степенью уплотнения. Так как высвобождение энергии, образующейся при сжатии газа, может привести к разрушению рабочей камеры газостата (вследствие возникновения мощной ударной волны), ее изготавливают из силовых элементов повышенной прочности.
Формование изделий в газостате происходит с использованием деформируемых оболочек. Подобная оболочка может быть изготовлена из материала, не взаимодействующего с порошком и обладающего необходимой пластичностью при рабочей температуре процесса. Чаще всего для изготовления оболочек используют фольгу из нержавеющей стали, никеля, молибдена, меди, титана и пр. Для ГИП керамики, тугоплавких соединений могут использовать деформируемые оболочки из борного или кремниевого стекла, кварца. Гораздо реже для изготовления оболочек используют серебро, золото или платину. Основным достоинством подобных оболочек (кроме высокой пластичности) является возможность использования их в повторном цикле. Геометрия и размеры оболочки должны быть такими, чтобы полученная формовка максимально приближалась по конфигурации к готовому изделию.
Процессы порошковой металлургии. Курс лекций |
-266- |

II. ФОРМОВАНИЕ И СПЕКАНИЕ ИЗДЕЛИЙ ИЗ МЕТАЛЛИЧЕСКИХ И НЕМЕТАЛЛИЧЕСКИХ ПОРОШКОВ
Лекция 5 Горячее изостатическое (газостатическое) прессование
Оболочки получают путем выдавливания (штамповки) листовых материалов и последующей сварки отдельных элементов. Толстостенные оболочки из стекла или кварца готовят шликерным формованием водных суспензий с последующей сушкой и обжигом.
Основными конструктивными элементами газостатов являются: рабочая камера высокого давления (контейнер) с нагревательным устройством; системы создания высокого давления газа в рабочей камере; системы управления, контроля и автоматической защиты.
В зависимости от максимальной рабочей температуры газостата его контейнер может быть одним из трех типов (рис. 2.15):
свнешним нагревом (нагреватель расположен снаружи контейнера, рабочая температура внутри контейнера 700–800 °С);
свнутренним нагревом (нагреватель расположен внутри контейнера; максимальная рабочая температура 1 100 °С);
свнутренним нагревом и охлаждаемыми стенками (рабочая темпера-
тура 1 500–2 000 °С).
8 |
6 |
8 |
6 |
8 |
6 |
7 |
|
7 |
1 |
||
7 |
|
|
|||
|
1 |
|
1 |
2 |
|
|
|
2 |
|
2 |
|
|
|
|
|
||
|
|
|
|
3 |
|
|
|
3 |
|
3 |
|
|
|
|
4 |
||
|
|
|
|
||
|
|
|
|
|
|
|
|
4 |
|
4 |
|
|
|
5 |
|
5 |
5 |
а |
|
|
б |
|
в |
Рис. 2.15. Схема конструкций установок для горячего изостатического прессования: 1 – запорная крышка; 2 – камера высокого давления; 3 нагревательный элемент; 4 – уплотняемое порошковое тело; 5 – внешняя изоляция; 6 – термопара; 7 – система охлаждения; 8 – система подачи газа
Камера высокого давления представляют собой систему из нескольких толстостенный цилиндров (контейнеров), вставленных друг в друга. Для обеспечения необходимых мер защиты часто применяют обмотку контейнера холоднотянутой, предварительно напряженной стальной лентой или проволокой.
Нагрузки, возникающие при давлении газа, воспринимаются (в радиальном направлении) боковыми стенками контейнера или (осевые усилия) передаются на стенки контейнера через затвор (резьбовой, байонетный) запорной крышки.
Процессы порошковой металлургии. Курс лекций |
-267- |

II. ФОРМОВАНИЕ И СПЕКАНИЕ ИЗДЕЛИЙ ИЗ МЕТАЛЛИЧЕСКИХ И НЕМЕТАЛЛИЧЕСКИХ ПОРОШКОВ
Лекция 5 Горячее изостатическое (газостатическое) прессование
Ведущими зарубежными фирмами-изготовителями газостатов явля-
ются фирмы ASEA (Швеция), Kobe Steel ltd. (Япония), Autoclave engineers inc. (США). В России основным изготовителем газостатов является ОАО «Всесоюзный научно-исследовательский институт металлургических машин» (ВНИИметмаш).
Рабочую температуру в газостате обеспечивают нагревательные устройства трех типов:
молибденовые ленточные или спиральные нагреватели, работающие только в защитной атмосфере (температуре до 1 500 °С, число рабочих цик-
лов 500–600);
графитовые (при рабочей температуре до 2 000 °С; число рабочих циклов до 1 000);
нагревательные устройства, изготовленные из коррозионно-стойких сплавов (нихром, хромель и пр.), способных работать на воздухе (рабочая температуре до 1 260 °С).
Обычно нагреватели располагают в донной части рабочей камеры газостата. Техническая характеристика некоторых из газостатов приведена в табл. 2.2.
|
|
|
|
Таблица 2.2 |
|
Технические характеристики серийных газостатов |
|||||
|
|
|
|
|
|
Тип газостата |
Рабочее пространство, мм |
Максимальное |
Максимальная |
||
(фирма-изготовитель, |
|
|
давление рабо- |
рабочая темпера- |
|
Диаметр |
Высота* |
||||
страна) |
|
|
чей среды, МПа |
тура, °С |
|
Autoclave engineers inc., |
75–200 |
140–350 |
105; 210; 420 |
1 000–2 000 |
|
США |
1 200–1 700 |
2 920–3 048 |
105; 210; 140 |
1 260–1 426 |
|
Conway pressure systems, |
220–457 |
635–1524 |
105;210 |
595–1 800 |
|
США |
|
|
|
|
|
|
< 600 |
<1800 |
200 |
1 200–1 600 |
|
Kobe Steel, Япония |
84 |
120 |
200 |
2 600 |
|
|
25 |
40 |
1 000 |
1 450 |
|
ASEA pressure systems |
102–254 |
127–762 |
210 |
2 000 |
|
inc., |
254–1 470 |
457–3500 |
< 315 |
< 2 000 |
|
США |
|
|
|
|
|
ASEA, Швеция: |
95; 102; 76 |
150; 127; |
100; 160; 200 |
2 200; 1 450; 1 400 |
|
Q1H-3 |
|||||
|
115 |
|
|
||
Q1H-20 |
|
|
|
||
260–270 |
800–1 700 |
100 |
1 450 |
||
|
|||||
ВНИИметмаш, Россия: |
140 |
100 |
200 |
1 200 |
|
330 |
|||||
ГТС-330 |
140 |
100 |
200 |
2 000 |
|
4,2 |
230; 160 |
300; 160 |
100; 200 |
1 200; 2 000 |
|
450 |
230 |
250 |
100 |
1 500 |
|
ГТС-5000 |
560 |
700 |
200 |
2 000 |
|
ЯО6016 |
900 |
1 800 |
200 |
1 500 |
|
ГУ-40 |
1 800 |
1 500 |
150 |
1 200 |
*Для газостатов ВНИИметмаш указана высота заготовки.
Процессы порошковой металлургии. Курс лекций |
-268- |

II. ФОРМОВАНИЕ И СПЕКАНИЕ ИЗДЕЛИЙ ИЗ МЕТАЛЛИЧЕСКИХ И НЕМЕТАЛЛИЧЕСКИХ ПОРОШКОВ
Лекция 5 Горячее изостатическое (газостатическое) прессование
Для создания рабочего давления внутри контейнера газостата применяют две принципиально разные схемы:
необходимое для работы количество газа хранится вне газостата (в баллонной станции) и подается в рабочую камеру перед началом процесса; емкость с необходимым количеством сжиженного газа устанавливают
непосредственно в контейнер, а затем газ нагревается и испаряется. Устройства для перекачивания газообразной рабочей среды могут
быть механические (компрессоры поршневые и мембранные, мультипликаторы, насосы) и термические (термические компрессоры и криогенные термокомпрессоры). Для перекачивания рабочей среды в сжиженном состоянии используют насосы и криогенные термокомпрессоры. Эти устройства для перекачивания рабочей среды могут быть многоступенчатыми и одноступенчатыми (дожимающими).
Вмногоступенчатой машине давление рабочей среды последовательно повышается в нескольких блоках от начального (0,1–1 МПа) до максимального. В одноступенчатой машине имеется только один блок, в котором давление рабочей среды повышается от 5–60 МПа до требуемой величины.
Одним из способов повышения производительности рассмотренных устройств является создание с их помощью только начального давления газа
врабочей камере газостата и последующее получение требуемого давления в результате разогрева рабочего пространства (начальное давление до 60 МПа
вбольшинстве случаев достаточно для обеспечения 200 МПа при температу-
ре 1 000 °С).
Вэтом случае компрессоры высокого давления служат лишь для корректировки рабочего давления.
Цикл газостатического формования. Рабочий цикл формования по-
рошка в газостате включает в себя следующие основные операции:
сборку садки (расчет навески, отмеривание и загрузка порошка в деформируемую оболочку, вибрирование и вакуумирование ее) и установку на заготовках термопар;
загрузку садки в рабочую камеру газостата, вакуумирование рабочего пространства и промывку рабочим газом;
создание в рабочем пространстве газостата необходимых по технологии давления и температуры;
выдержку садки при рабочих режимах формования; охлаждение садки и выпуск рабочего газа;
выгрузку садки и освобождение сформованного изделия от оболочки. Порошок перед уплотнением подвергают дегазации для удаления большей части газа, адсорбированного поверхностью частиц, и вибрирова-
нию для более плотной упаковки частиц.
Взависимости от технологических требований к конкретному изделию и особенностей конструкции используемого газостата возможны четыре схемы проведения процесса газостатического формования порошка:
Процессы порошковой металлургии. Курс лекций |
-269- |

II. ФОРМОВАНИЕ И СПЕКАНИЕ ИЗДЕЛИЙ ИЗ МЕТАЛЛИЧЕСКИХ И НЕМЕТАЛЛИЧЕСКИХ ПОРОШКОВ
Лекция 5 Горячее изостатическое (газостатическое) прессование
спредварительным подъемом давления газовыми компрессорами
ипоследующим разогревом рабочего пространства при выключенном компрессоре
содновременным подъемом давления и температуры;
спредварительным разогревом рабочего пространства;
спостоянной температурой в рабочем пространстве и предварительным разогревом оболочек с порошковым телом.
Рабочий цикл с предварительным подъемом давления газовыми компрессорами используют наиболее часто. В этом случае возможно использование компрессора, рассчитанного на давление, существенно ниже рабочего. Необходимое давление достигается при расширении нагретого газа (за счет термического расширения газа одновременно с подъемом температуры повышается и давление).
Схема с одновременным подъемом давления и температуры предназначена в основном для формования крупногабаритных заготовок, требующих более длительных выдержек при рабочей температуре формования.
Схема с предварительным разогревом рабочего пространства обеспечивает формование в стеклянных оболочках, а схема с постоянной температурой в рабочем пространстве (при которой оболочки с порошком разогреваются вне газостата) позволяет существенно повысить производительность установки (в 2 раза и более).
Температуру ГИП выбирают в зависимости от давления формования. Повышение давления в 2 раза примерно адекватно увеличению температуры на 50 °С.
При 3–5-часовой изотермической выдержке и давлении 70–100 МПа температура, необходимая для достижения относительной плотности полу-
чаемых заготовок (γ > 0,98), составляет для металлов 0,5–0,6Тплав, а для тугоплавких соединений 0,7Тплав. В табл. 2.3 приведены некоторые данные по применяемым на практике режимам ГИП.
Для изготовления изделий сложной формы целесообразно вначале формовать отдельные фрагменты заготовки, а затем помещать их вместе в соответствующую оболочку.
При эксплуатации газостата опасность представляет возможность его разрушения взрывом деформируемых оболочек с порошком, в которые (при нарушении их герметичности во время рабочего цикла) проникает газ высокого давления. Так как обнаружить разгерметизацию оболочки во время изотермической выдержки невозможно, то при быстром снижении давления в рабочей камере газостата оболочка может раздуться и даже взорваться. А это может привести к разрушению нагревательного устройства или рабочей камеры газостата. При механическом удалении вдутой оболочки с заготовки нужно быть крайне осторожным: высокое давление внутри нее может сохраняться долго (часть дефектов залечивается при изотермической выдержке, некоторые неплотности заполняются порошком и т.п.). Вздутая капсула подобна баллону, наполненному газом высокого давления.
Процессы порошковой металлургии. Курс лекций |
-270- |

II. ФОРМОВАНИЕ И СПЕКАНИЕ ИЗДЕЛИЙ ИЗ МЕТАЛЛИЧЕСКИХ И НЕМЕТАЛЛИЧЕСКИХ ПОРОШКОВ
Лекция 5 Горячее изостатическое (газостатическое) прессование
|
|
|
|
Таблица 2.3 |
|
Параметры ГИП некоторых материалов |
|
||||
|
|
|
|
|
|
|
Давление, |
Температура, |
Время вы- |
Относительная |
|
Материал |
плотность заго- |
||||
|
МПа |
°С |
держки, ч |
товки |
|
|
|
|
|
||
Бериллий |
69–105 |
700–1 100 |
0,5–3 |
1 |
|
Вольфрам |
110 |
1 550 |
1 |
0,98 |
|
70–140 |
1 370–1 700 |
1–5 |
1 |
||
|
|||||
Тантал |
77–155 |
1 425 |
0,4–0,5 |
|
|
Диоксид урана |
115–150 |
700–1 050 |
3 |
0,999 |
|
Диборид циркония |
100 |
13 50 |
– |
1 |
|
Нержавеющая сталь |
84 |
1 200 |
0,3 |
0,98 |
|
Жаропрочный сплав ЖС-6 |
100–180 |
1 150–1 250 |
1–10 |
– |
|
Инструментальная сталь |
100 |
1 100 |
1 |
0,998 |
|
100 |
1 150 |
0,5 |
0,99–1 |
||
|
|||||
Карбид вольфрама |
70–105 |
1 600–1 760 |
– |
1 |
|
Нитрид бора |
105 |
1 500 |
0,1 |
– |
|
Оксид алюминия |
70–140 |
11 50–1 370 |
0,5–0,3 |
0,96–0,99 |
|
Ферриты |
70–105 |
1 095–1 370 |
1–3 |
|
Разновидностью метода ГИП является способ уплотнения предварительно спеченных заготовок с закрытой поверхностной пористостью.
Контрольныевопросыизадания
1.В чем заключается суть методагорячего изостатического формования?
2.Перечислите операции технологического цикла ГИП.
3.Назовите способы ГИП.
4.Из каких материалов изготавливают оболочки, используемые при ГИП порошков?
5.Опишите технологию изготовления оболочек для ГИП порошков.
6.Как получают изделия сложной формы методом ГИП?
7.Перечислите способы создания давления в рабочей камере устано-
вок ГИП.
8.Назовите типы нагревательных устройств установок ГИП.
9.Как классифицируют установки для ГИП?
10.С действием, каких факторов связан брак изделий при ГИП?
Процессы порошковой металлургии. Курс лекций |
-271- |

II. ФОРМОВАНИЕ И СПЕКАНИЕ ИЗДЕЛИЙ ИЗ МЕТАЛЛИЧЕСКИХ И НЕМЕТАЛЛИЧЕСКИХ ПОРОШКОВ
Лекция6 Прессованиевэластичныхоболочках.
Шликерноеформованиевовпитывающиеформы
План лекции
1.Формование порошков в толстостенных эластичных оболочках.
2.Классификация методов шликерного литья изделий.
3.Шликерное формование в пористых адсорбирующихся формах.
Формованиепорошковвтолстостенныхэластичныхоболочках
При формовании порошков этим методом толстостенную (толщина стенки 10–20 мм) эластичную оболочку (втулку) с порошком помещают в матрицу пресс-формы и подвергают одностороннему или двустороннему (рис. 2.16) прессованию.
|
1 |
|
2 |
3 |
5 |
|
|
4 |
7 |
|
6 |
а |
б |
Рис. 2.16. Схема двустороннего прессования в эластичной оболочке: а – в момент приложения давления; б – после прессования: 1 – верхний пуансон; 2 – матрица пресс-формы; 3 – резиновая пробка; 4 – порошок; 5 – эластичная оболочка (втулка); 6 – нижний пуансон; 7 – формовка
Материал оболочки (втулки) должен:
обладать способностью принимать и сохранять определенную форму, соответствующую форме заготовки;
быть достаточно пластичным (для обеспечения эффекта равномерного всестороннего обжатия порошка (коэффициент Пуассона материала должен стремиться к 0,5));
иметь определенную упругость, позволяющую оболочке возвращаться в первоначальное положение после снятия давления и пр.
Процессы порошковой металлургии. Курс лекций |
-272- |

II. ФОРМОВАНИЕ И СПЕКАНИЕ ИЗДЕЛИЙ ИЗ МЕТАЛЛИЧЕСКИХ И НЕМЕТАЛЛИЧЕСКИХ ПОРОШКОВ
Лекция 6 Прессование в эластичных оболочках. Шликерное формование во впитывающие формы
Пригодны для изготовления оболочек (втулок) парафин, воск, водный раствор желатина с добавками глицерина, эпоксидные смолы и резиновые массы. При формовании единичных заготовок целесообразно использовать оболочки из парафина или воска.
Эпоксидная смола требует длительной полимеризации и склеивается с порошком в процессе формования, поэтому ее для изготовления эластичной оболочки применяют крайне редко.
Толстостенные оболочки (втулки) из желатина, каучука и резиновых смесей не имеют остаточной деформации и наиболее эффективны для изостатического (точнее квазиизостатического) формования: желатиновая оболочка позволяет формовать в ней до нескольких сотен однотипных заготовок, а оболочка из каучука или резиновой массы на его основе (95 % каучука) с коэффициентом Пуассона ν = 0,5 (ξ = 1)обеспечивает формование до н е- скольких тысяч заготовок.
Распределение плотности в объеме формовки, полученной в каучуковой оболочке, более равномерное, а абсолютная величина их плотности выше, чем у формовок, полученных в оболочке из желатина.
Условия уплотнения порошкового тела, заключенного в оболочку, аналогичны условиям уплотнения порошков методом гидростатического прессования.
При всестороннем сжатии стенок толстостенной эластичной оболочки в процессе деформации объем порошкового тела и его поверхность сильно уменьшаются, а частицы перемещаются как в объеме заготовки, так и по ее поверхности. В связи с этим применение смазки влияет на плотность заготовок из-за уменьшения как внешнего (между порошком и оболочкой), так и межчастичного трения.
Имеется практический опыт формования в толстостенных оболочках (втулках) твердосплавных смесей в виде равноплотных полых цилиндров с отношением высоты к диаметру от 2 до 4 и толщиной стенки от 2 до 7 мм, стержней с отношением высоты к диаметру до 6. Можно получить заготовки формованием твердосплавных смесей без пластификатора при отношении высоты к диаметру < 3,5 и толщине стенки 4–5 мм.
Метод формования в толстостенных эластичных оболочках (втулках) целесообразно использовать для изготовления изделий несложной конфигурации.
Классификацияметодовшликерноголитьяизделий
Шликер – устойчивая суспензия металлического или неметаллического порошка в жидкой среде. Шликерное формование – формование путем заполнения шликером пористой формы, обеспечивающей удаление жидкости из шликера.
Процессы порошковой металлургии. Курс лекций |
-273- |

II. ФОРМОВАНИЕ И СПЕКАНИЕ ИЗДЕЛИЙ ИЗ МЕТАЛЛИЧЕСКИХ И НЕМЕТАЛЛИЧЕСКИХ ПОРОШКОВ
Лекция 6 Прессование в эластичных оболочках. Шликерное формование во впитывающие формы
Приведенное определение относится только к шликерному формованию в пористых адсорбирующих и неадсорбирующих формах – наиболее распространенной разновидности этого метода.
Другой разновидностью шликерного формования является формование термопластичных шликеров, состоящих из твердой фазы и термопластичной связки, которая при комнатной температуре твердая, а при нагреве плавится и придает шликеру необходимые литейные свойства.
Еще одна разновидность шликерного формования – это электрофоретический метод, при котором заготовку получают путем постепенного наращивания слоя из твердых частиц шликера, которые под влиянием электрического поля перемещаются к электроду-форме и осаждаются на нем.
Шликерное формование (его иногда продолжают называть «шликерное литье») позволяет получать изделия сложных форм, мало- и крупногабаритные, полые с равномерной толщиной стенок, с высокой чистотой поверхности и точных размеров.
Существенными недостатками шликерного формования являются высокая суммарная длительность процесса получения заготовок, необходимость изготовления и хранения больших количеств адсорбирующих форм, потребность в мощном сушильном хозяйстве.
К основным свойствам шликера (реологические свойства), определяющим качество получаемых из него заготовок, относят:
текучесть; седиментационную и агрегативную устойчивость при высоком содер-
жании твердой фазы; способность заполнять форму.
Текучесть шликера – величина, обратная вязкости, – характеризует его способность литься, заполнять форму, набирать массу заготовки.
Устойчивость шликера связана с его способностью не расслаиваться в течение длительного времени. Седиментационная устойчивость определяется скоростью оседания твердых частиц под действием силы тяжести и зависит в основном от размера частиц и их концентрации в шликере. Агрегативная устойчивость связана со склонностью мелких частиц к агрегатированию (слипанию под действием электростатических сил).
Для получения шликеров с хорошими свойствами необходимо, чтобы твердые частицы смачивались жидкой фазой. Улучшение или ухудшение смачивания можно осуществить добавками к шликеру поверхностно-активных веществ (ПАВ).
Дисперсность частиц твердой фазы, распределенных в шликере, определяет его устойчивость, вязкость и влияет на плотность получаемых заготовок. При уменьшении размеров частиц и их плотности стабильность свойств шликера улучшается в связи с уменьшением скорости оседания частиц под действием гравитационных сил.
Жидкая фаза для приготовления шликера должна иметь низкое давление пара, низкие воспламеняемость и токсичность, малую вязкость и не должна активно химически взаимодействовать с твердой фазой.
Процессы порошковой металлургии. Курс лекций |
-274- |
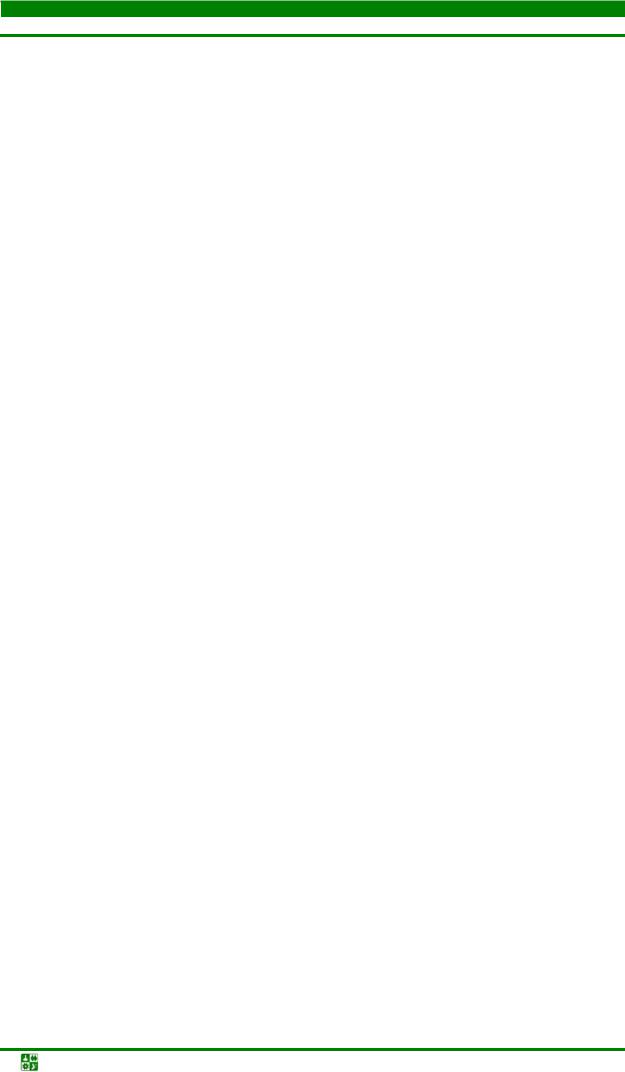
II. ФОРМОВАНИЕ И СПЕКАНИЕ ИЗДЕЛИЙ ИЗ МЕТАЛЛИЧЕСКИХ И НЕМЕТАЛЛИЧЕСКИХ ПОРОШКОВ
Лекция 6 Прессование в эластичных оболочках. Шликерное формование во впитывающие формы
Наиболее часто в качестве основы для получения шликера используют воду (литье в пористые адсорбирующие или неабсорбирующие формы) или парафин (термопластичный шликер).
Парафины, применяемые при изготовлении термопластичных шликеров, являются предельно насыщенными соединениями углерода с водородом с общей формулой СnН2n+2, и представляет собой продукты переменного состава. Плотность парафинов при 100 °С изменяется от 0,71 до 0,77 г/см3, температура плавления - от 54 до 49 °С, а вязкость – от 1 до 8 Па. Кроме технических парафинов могут использоваться церезины и полиэтилен. Полиэтилен хорошо смешивается с парафином, и его часто используют в качестве добавки, увеличивающей устойчивость шликеров, что важно при формовании заготовок из порошков тяжелых металлов и сплавов.
Шликерноеформованиевпористыхадсорбирующихформах
Технологический процесс предусматривает выполнение следующих операций:
изготовление пористой формы; приготовление шликера (подготовка дисперсной фазы, дисперсионной
среды и их смешивание); формование заготовки и извлечение из формы; сушка заготовки; обжиг (спекание) заготовки.
Для изготовления пористых адсорбирующих форм можно использовать любой материал, способный поглощать жидкую фазу шликера, химически инертный к нему и имеющий достаточную прочность.
Наиболее часто для изготовления впитывающих форм используют гипс, который в обезвоженном состоянии активно поглощает воду. Природный гипс CaSО4·2H2О измельчают и сушат при температуре 140–175 °С до состава CaSO4·0,5H2O, после чего гипс измельчают, получая порошок. Из этого порошка путем добавления в него воды готовят кремообразную массу. Заливая эту массу в заранее подготовленную разъемную матрицу с помещенной в нее моделью будущего изделия, получают форму для отливки изделия (рис. 2.17).
Процессы порошковой металлургии. Курс лекций |
-275- |

II. ФОРМОВАНИЕ И СПЕКАНИЕ ИЗДЕЛИЙ ИЗ МЕТАЛЛИЧЕСКИХ И НЕМЕТАЛЛИЧЕСКИХ ПОРОШКОВ
Лекция 6 Прессование в эластичных оболочках. Шликерное формование во впитывающие формы
|
Гипс |
2 |
3 |
|
|
|
5 |
1 |
4 |
|
Рис. 2.17. Схема заливки гипсовой массы: 1– разъемная матрица; 2 – модель изделия; 3 – второй слой гипсовой массы; 4 – первый слой гипсовой массы; 5– тонкий слой смазки
Заливку гипса в матрицу проводят в несколько этапов (не менее двух). После заливки и отверждения первой порции гипса, его поверхность смазывают тонким слоем органического вещества (чаще всего вазелина). Этот слой в дальнейшем позволяет разнимать отдельные части матрицы и извлекать из нее отливку.
После сушки (Т= 50–65 °С, время – от 4 до 150 ч) гипсовая форма содержит не более 10 % воды и ее можно использовать для отливки заготовок.
Для улучшения отделения заготовки от поверхности формы на ее внутреннюю поверхность наносят антиадгезионную пленку из бумаги, графита, талька, бентонитовой глины, альгината натрия.
Повторное (от 70 до 125 циклов до утилизации) использование гипсовых форм для отливки заготовок связано с проявление таких нежелательных явлений, как уменьшение скорости набора массы (из-за заполнения пор частицами шликера), затрудненное извлечение из них заготовок сложной формы, повреждение рабочих поверхностей формы при чистке после их использования.
Подготовка дисперсной фазы шликера включает операцию получения порошков такой дисперсности, которая обеспечивает максимальную плотность их упаковки без ухудшения технологических свойств шликера.
Грубые (достаточно крупные) порошки дают неустойчивые шликеры и заготовки пониженной прочности, а тонкодисперсные порошки обеспечивают шликеру высокую седиментационную устойчивость и достаточную прочность заготовкам, но скорость набора массы заготовки и ее плотность понижены, что приводит к короблению изделия при усадке и проявлению анизотропии свойств после обжига (спекания).
Следовательно, необходимо стремиться к оптимизации дисперсной (твердой) фазы шликера. Для этого путем предварительного измельчения материала получают оптимальный фракционный состав порошков. Измельчение можно проводить как в жидкой среде, так и сухим помолом. Однако при последующем перемешивании измельченного всухую порошка с жидкостью не весь адсорбированный частицами газ удаляется с поверхности частиц, часть его остается, что ухудшает свойства шликера.
Дисперсионной средой при измельчении чаще всего является вода, как правило, предварительно очищенная (обычно вода содержит соли, коли-
Процессы порошковой металлургии. Курс лекций |
-276- |

II. ФОРМОВАНИЕ И СПЕКАНИЕ ИЗДЕЛИЙ ИЗ МЕТАЛЛИЧЕСКИХ И НЕМЕТАЛЛИЧЕСКИХ ПОРОШКОВ
Лекция 6 Прессование в эластичных оболочках. Шликерное формование во впитывающие формы
чество которых меняется в зависимости от времени года). Кроме воды используют спирт, четыреххлористый углерод, изобутил уксусной кислоты и др.
Для металлических порошков, частицы которых быстро оседают в воде, применяют более вязкие жидкости (водные растворы альгинатов аммония или натрия, карбоксил-метилцеллюлозы, поливинилового спирта, масла и др.). В качестве добавок (дефлокулянтов), препятствующих агрегатированию частиц, используют соляную, уксусную и другие кислоты, в ряде случаев щелочи. Необходимо отметить, что дефлокулянты одновременно стабилизируют раствор, придавая ему необходимую седиментационную устойчивость.
Приготовление шликера [содержание твердой фазы около 50–70 % (об.)] осуществляют одностадийным или двустадийным способом, а также способом предельного насыщения с добавкой зернистого наполнителя.
При одностадийном способе предварительно раздробленный материал подвергают мокрому размолу в выбранной дисперсионной среде.
При двустадийном способе вначале проводят сухой помол материала, а затем смешивают полученный порошок с жидкостью. В этом случае шликер имеет большую влажность, плотность и прочность получаемых порошковых заготовок ниже, чем при одностадийном приготовлении шликера.
При подготовке шликера по способу введения зернистого наполнителя, на стадии перемешивания твердой фазы с дисперсионной средой к шликеру добавляют крупнозернистый порошок (зернистый наполнитель). Подобный шликер применяется для получения крупногабаритных и толстостенных изделий, так как обеспечивает большую скорость набора массы заготовки и малую ее усадку при сушке.
Формование заготовок осуществляют «наливным» или «сливным» способами.
Наливной способ используется для получения цельных (не полых) или толстостенных изделий. Шликер наливают в форму в несколько этапов, поддерживая постоянным уровень ее заполнения. Толстостенные изделия получают путем установки в матрицу стержней различного профиля, которые способствуют получению в изделии внутренних полостей правильной формы.
Сливной способ отличается от наливного тем, что после заливки шликера в форму ему дают некоторое время «отстояться», а затем не успевший осесть на стенки формы шликер удаляют из нее, либо переворачивая форму, либо отсасывая шликер с помощью насоса, либо сливая его через отверстие в основании формы.
При использовании этого способа на стенке формы образуется слой порошка определенной толщины.
Набор массы частиц на стенке формы является фильтрационным процессом (рис. 2.18), протекание которого обусловлено скоростью микропотоков жидкой фазы шликера вблизи поверхности пористой формы.
Процессы порошковой металлургии. Курс лекций |
-277- |

II. ФОРМОВАНИЕ И СПЕКАНИЕ ИЗДЕЛИЙ ИЗ МЕТАЛЛИЧЕСКИХ И НЕМЕТАЛЛИЧЕСКИХ ПОРОШКОВ
Лекция 6 Прессование в эластичных оболочках. Шликерное формование во впитывающие формы
I |
II |
III |
Рис. 2.18. Схема формирования стенки изделия из шликера (стрелками указаны направления потоков жидкости)
Медленный поток жидкости (зона III) после подхода к пористой стенке формы (зона I) увеличивает свою скорость и захватывает частицы и укладывает их слоем равномерной толщины (зона II). При этом происходит «вмывание» мелких частиц в поры между крупными зернами. Скорость роста толщины набираемой массы заготовки называют скоростью формования стенки (скорость набора стенки). В большинстве случаев она составляет от 0,5 до 2 мм/мин.
Скорость впитывания жидкости должна быть чуть выше или равной той, с которой она подходит к границе заготовка – гипсовая форма. Если превышение значительно, наружный слой формирующейся заготовки обезвоживается и может образоваться трещина или стенка заготовки отделится от стенки формы. Если скорость впитывания меньше скорости подхода жидкости к стенке формы, то стенки заготовки будут размываться и приклеиваться к поверхности формы.
Время набора массы формирующейся заготовки на стенке формы обычно составляет от 1 до 60 мин. Для повышения скорости диффузии воды в форме, а также скорости отбора влаги из шликера применяют обдув наружной поверхности гипсовой формы теплым воздухом.
Для улучшения процесса формования шликер подогревают до 50–60 °С или вакуумируют. Однако подогрев может ухудшить процесс, если возможно ускорение взаимодействия фаз, загустевание шликера и т.п.
В производственных условиях формование осуществляют на стендах или автоматах. Кроме увеличения производительности, автоматизация процесса улучшает качество изделий благодаря точной дозировке шликера и быстрому удалению его избытка из формы путем отсоса.
Процессы порошковой металлургии. Курс лекций |
-278- |
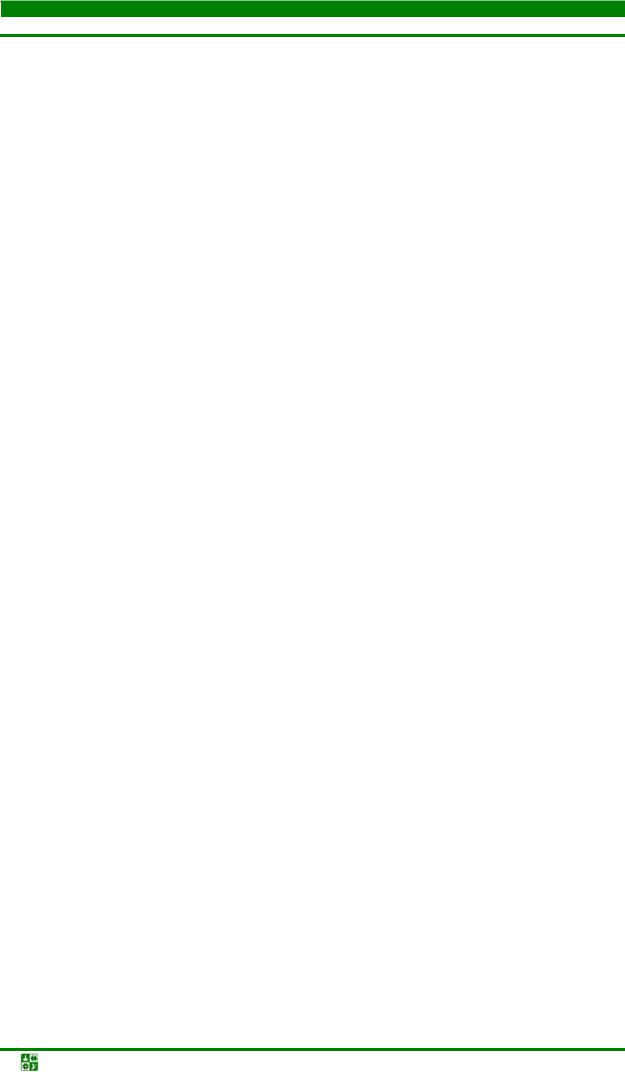
II. ФОРМОВАНИЕ И СПЕКАНИЕ ИЗДЕЛИЙ ИЗ МЕТАЛЛИЧЕСКИХ И НЕМЕТАЛЛИЧЕСКИХ ПОРОШКОВ
Лекция 6 Прессование в эластичных оболочках. Шликерное формование во впитывающие формы
Для придания отлитым изделиям необходимой прочности их подсушивают в форме. При этом происходит усадка отлитого изделия (до 1 %), которая облегчает последующее извлечение заготовки. После извлечения заготовку оправляют (удаляют «прибыльную» часть, зачищают неровности, отдельные сколы) и сушат при температуре 110–150 °С на воздухе в сушильных шкафах или сушилках. Во избежание растрескивания заготовок необходимо осуществить медленный и равномерный прогрев изделий.
Причины растрескивания заготовок: неравномерная скорость высыхания, прилипание к стенкам формы, недостаточная прочность заготовки, негомогенность шликера и его тиксотропия (создает неравномерность свойств по толщине стенки). Относительная плотность заготовок составляет 60–80 % от теоретической. Связь между отдельными частицами обусловлена контактными явлениями и зацеплением.
Обжиг или спекание высушенных заготовок проводят в печах по режимам, зависящим от материала заготовки.
Шликерное формование широко применяют для изготовления изделий из оксидов, карбидов, боридов, силицидов и других тугоплавких соединений, твердых сплавов, керметов и различных композитов, в том числе армированных дискретными волокнами. Существенным достоинством этого метода при получении изделий из тугоплавких материалов является то, что путем оптимизации фракционного состава можно получать изделия с плотностью, равной 0,8–0,9 % теоретической плотности материала.
В отдельных случаях для получения пустотелых изделий (тел вращения) из металлических порошков или сечки (дискретных волокон) используют центробежное формование изделий: подготовленный шликер заливают во вращающуюся форму.
Контрольныевопросыизадания
1. В чем заключается суть метода формования в эластичные оболоч-
ки?
2.Из каких материалов изготавливают эластичные оболочки?
3.Назовите основные преимущества метода шликерного литья.
4.Перечислите свойства шликеров.
5.Назовите основные операции технологического цикла литья изделий в адсорбирующие формы.
6.Из каких материалов, изготавливают впитывающие формы?
7.Назовите два основных способа литья шликеров во впитывающие
формы.
8.С чем связан брак при получении изделий литьем шликеров во впитывающие формы?
Процессы порошковой металлургии. Курс лекций |
-279- |

II. ФОРМОВАНИЕ И СПЕКАНИЕ ИЗДЕЛИЙ ИЗ МЕТАЛЛИЧЕСКИХ И НЕМЕТАЛЛИЧЕСКИХ ПОРОШКОВ
Лекция7 Шликерноеформованиевнеадсорбирующиеформы,
литьеизтермопластичныхшликеров, электрофоретическоелитьешликеров
План лекции
1.Шликерное формование в неадсорбирующих формах.
2.Формование термопластичных шликеров.
3.Электрофоретическое литье.
Шликерноеформованиевнеадсорбирующихформах
Удаление дисперсионной среды из шликера можно осуществить, не прибегая к ее впитыванию материалом формы. Подобный вариант шликерного литья осуществляют различными способами:
1) формованием под вакуумом в перфорированных металлических формах (отверстия диаметром 0,7–1,1 мм, суммарной площадью 30–40 %). Изнутри стенки формы покрывают слоем бумажной массы, а снаружи создают разрежение около 20–25 гПа, которое и обеспечивает отвод жидкости из шликера;
2)формованием под давлением (порядка нескольких мегапаскалей)
вразъемных формах со стенками из пористого материала (спеченный стеклянный порошок, пластик), за которыми находятся полости для отвода вы-
давливающейся из шликера жидкости; 3) вымораживанием жидкости (например, помещая неадсорбирую-
щую форму со шликером в смесь бензина и твердой углекислоты с температурой –40 °С, с последующей «сушкой» (сублимацией) замороженного изделия в вакуумной камере.
Формованиетермопластичныхшликеров
Общая технологическая схема процесса получения изделий по этому способу включает следующие операции:
подготовка дисперсной фазы (чаще всего – измельчение неметаллических тугоплавких материалов (карбидов, боридов, нитридов и пр.)) и термопластической связки (подготовка навески необходимого объема);
приготовление шликера (смешивание термопластичной связки с дисперсной фазой);
подготовка форм к заполнению шликером и формованию (отливки) заготовки;
заполнение шликером формы и отверждение отливки; удаление связки и спекание.
Приготовление дисперсной фазы проводят по технологиям, сходным с технологиями подготовки материала для водных шликеров.
Термопластичная связка должна обеспечить образование текучего шликера с малой вязкостью в жидком состоянии, который хорошо смачивает твердую фазу и не образует вокруг частиц порошка толстых оболочек.
Процессы порошковой металлургии. Курс лекций |
-280- |

II.ФОРМОВАНИЕ И СПЕКАНИЕ ИЗДЕЛИЙ ИЗ МЕТАЛЛИЧЕСКИХ И НЕМЕТАЛЛИЧЕСКИХ ПОРОШКОВ
Лекция 7 Шликерное формование в неадсорбирующие формы, литье из термопластичных шликеров
Для улучшения смачивания частиц твердой фазы в состав связки вводят ПАВ (олеиновую, стеариновую, пальмитиновую кислоты, животные жиры, пчелиный воск, растительные масла и др.). Содержание ПАВ зависит от величины удельной поверхности частиц порошка и обычно не превышает
0,05–0,2 %.
Смешивание составляющих термопластичного шликера осуществляют в специальных смесителях, рабочая камера которых нагревается до температуры, превышающей температуру плавления связки (до 60–120 °С). Содержание связки составляет от 25 до 40 % от общего объема материала (8–15 % по массе).
Формы для литья термопластичными шликерами обычно изготавливают из меди, бронзы, алюминиевых сплавов, стали, термостойких пластмасс и пр. На практике широко применяют формование под давлением из термопластичных шликеров на парафиновой основе. Для литья изделий используют специальные литьевые машины (рис. 2.19), принцип устройства которых сходен с машинами для литья изделий из органических материалов (термореактивных пластиков, пластмасс, полиэтилена).
Термопластичный шликер, разогретый до 70–100 °С, заливают в герметичный резервуар, в котором постоянная температура поддерживается нагревательными элементами. Жидкий шликер для предотвращения расслоения по высоте постоянно перемешивают.
Под давлением сжатого воздуха (0,3–0,6 МПа) шликер из резервуара поступает в металлическую форму, которая помещается на рабочем столе установки. Чтобы в процессе усадки не изменилась форма получаемой заготовки, давление на шликер не снимают до тех пор, пока не произойдет его полного затвердевания. После отверждения шликера форму разнимают и извлекают из нее изделие.
|
2 |
8 |
3 |
|
7 |
4 |
|
|
|
1 |
|
Газ |
|
|
|
5 |
|
9 |
|
|
|
6 |
|
|
Рис. 2.19. Схема установки для литья изделий из термопластичного шликера: 1 – резервуар; 2 – матрица (форма); 3– отливка; 4 – трубка подачи жидкого шликера в форму; 5 – шликер; 6 – нагревательный элемент; 7 – отверстие, для заливки шликера в резервуар; 8 – мешалка; 9 – компрессор
Процессы порошковой металлургии. Курс лекций |
-281- |

II.ФОРМОВАНИЕ И СПЕКАНИЕ ИЗДЕЛИЙ ИЗ МЕТАЛЛИЧЕСКИХ И НЕМЕТАЛЛИЧЕСКИХ ПОРОШКОВ
Лекция 7 Шликерное формование в неадсорбирующие формы, литье из термопластичных шликеров
Из пластифицированных шликеров можно получать тонкостенные заготовки по способу намораживания шликера на холодную поверхность, литьем в кокиль, непрерывной подачей шликера в холодную фильеру (по типу мундштучного формования) и другими способами.
Удаление связки осуществляют путем медленного нагрева заготовок в предварительно прокаленных адсорбентах (оксиде алюминия, оксиде магния), которые активно впитывают расплавленную связку. При повышении температуры происходит плавление связки, пиролиз и испарение, легкие и тяжелых фракции углеводородов и выгорание углеродистого остатка. Продолжительность каждого этапа удаления связки зависит от размеров и конфигурации заготовки, ее свойств, применяемого адсорбента и способа, который может предусматривать удаление связки полностью или частично.
Операцию выжигания связки ведут при поэтапном подъеме температуры и, как правило, совмещают с операцией припекания (начальным этапом процесса спекания) изделия (рис. 2.20). Последняя операция необходима для придания изделию некоторой, сравнительно небольшой, механической устойчивости, обеспечивающей его сохранность при извлечении из засыпки и транспортировки к печи обжига.
Рис. 2.20. Температурная кривая удаления связки и припекания изделия: 1 – зона плавления связки; 2 – зона удаления связки из изделия и частичного испарения легколетучих органических фракций; 3 – зона выжигания остатков
связки; 4 – зона припекания
Т, оС |
|
1000 |
|
800 |
|
600 |
|
400 |
4 |
|
|
200 |
3 |
1 |
2 |
|
Время, ч |
После плавления и частичного удаления (впитывания адсорбентом) жидкой связки образуются поры, по которым остатки связки диффундируют к поверхности заготовки и испаряются. Ориентировочное время выдержки заготовок с толщиной стенки 5, 10, 20 и 40 мм при 180 °С составляет около 4, 8, 18 и 27 ч соответственно.
Электрофоретическоеформование
Этот способ применяют преимущественно для получения тонкостенных и крупногабаритных изделий сравнительно простой конфигурации из керамических шликеров. Изделия получают при пропускании тока (анодная плотность 0,0015–0,03 А/см2, напряжение 2–4 В) через водный шликер. Для
Процессы порошковой металлургии. Курс лекций |
-282- |
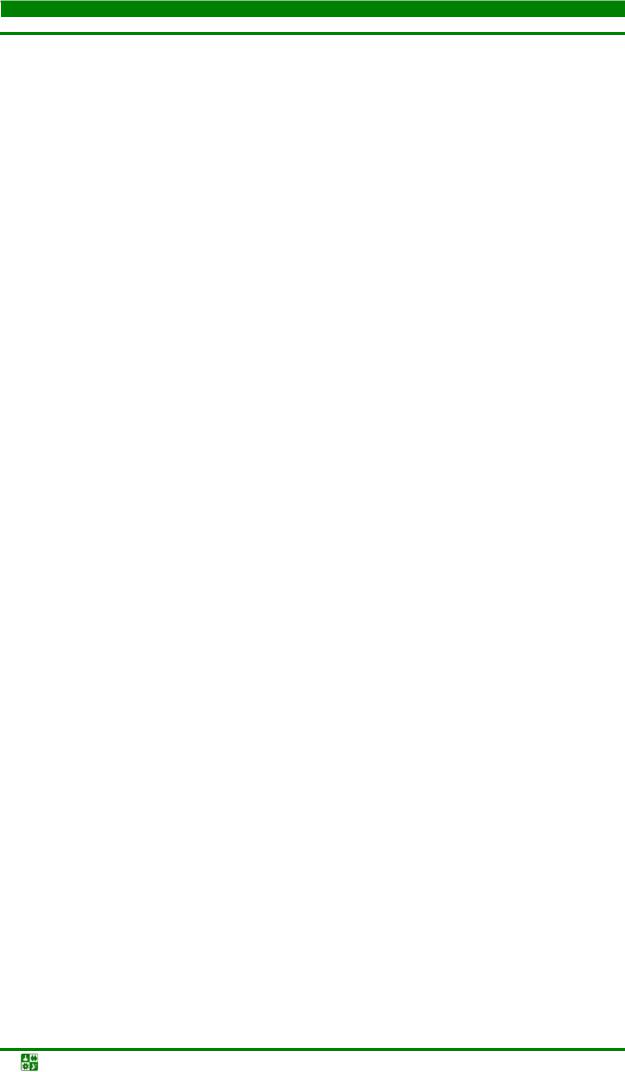
II.ФОРМОВАНИЕ И СПЕКАНИЕ ИЗДЕЛИЙ ИЗ МЕТАЛЛИЧЕСКИХ И НЕМЕТАЛЛИЧЕСКИХ ПОРОШКОВ
Лекция 7 Шликерное формование в неадсорбирующие формы, литье из термопластичных шликеров
осаждения шликера применяют тонкостенные медные формы, которые выполняют функцию анода. Стержневой катод находится в центре формыанода. Объемная масса получаемых заготовок выше, чем у заготовок, полученных в гипсовых формах или формованием термопластичных шликеров. Время формования заготовки зачастую не превышает нескольких минут.
Контрольныевопросыизадания
1.Перечислите основные способы литья шликеров в неадсорбирующие формы.
2.Какие материалы, используют для изготовления неадсорбирующих
форм?
3.Перечислите основные операции технологии литья их пластифицированных шликеров.
4.Какой материал чаще всего используется в качестве термопластичной связки пластифицированных шликеров?
5.Опишите принцип действия машин для литья изделий из термопластичных шликеров.
6.Укажите разновидности способа литья изделий из термопластичных шликеров.
7.Перечислите основные этапы термической обработки изделий на основе пластифицированных масс порошка.
8.Опишите основные этапы формования изделий методом электрофоретического литья шликеров. Опишите установку для получения изделий этим методом.
Лекция8 Мундштучноеиинжекционноеформованиепорошков
План лекции
1.Мундштучное формование порошков.
2.Инжекционное формование порошков.
Мундштучноеформованиепорошков
Мундштучное формование – формование металлического порошка путем продавливания его через отверстие.
Форма отверстия определяет форму и размеры поперечного сечения изделия. Мундштучным формованием готовят прутки, трубы, сверла, профи-
Процессы порошковой металлургии. Курс лекций |
-283- |

II. ФОРМОВАНИЕ И СПЕКАНИЕ ИЗДЕЛИЙ ИЗ МЕТАЛЛИЧЕСКИХ И НЕМЕТАЛЛИЧЕСКИХ ПОРОШКОВ
Лекция 8 Мундштучное и инжекционное формование порошков
ли и другие длинномерные изделия. Достоинством этого метода является возможность получения изделий с равномерной плотностью.
Продавливать через отверстие (рис. 2.21, а) можно не только пор о- шок, но и предварительно спрессованную из него заготовку.
Уменьшить трение порошка о внутреннюю поверхность матрицы и мундштука можно, нанеся на эти поверхности (или вводя в порошок) смазки или пластификаторы (парафин, раствор каучука в бензине, раствор бакелита в спирте, раствор поливинилового спирта в воде, масла, графит и пр.). Выбор той или иной смазки зависит от свойств материала и ее влияния на процесс спекания изделий. Количество вводимой в состав порошка смазки обычно не превышает 6–10 % (по массе). При производстве изделий с постоянным или изменяемым по высоте сечением внутренней полости (отверстия) в мундштук помещается «звездочка». При формовании изделий с постоянным сечением внутренней полости в звездочку вворачивается игла.
1 |
7 |
|
1 |
||
|
||
2 |
|
|
3 |
5 |
|
|
||
4 |
6 |
|
|
||
|
а |
|
|
Р |
|
|
1 |
|
2 |
|
|
|
5 |
|
|
8 |
3 |
4 |
9 |
|
||
|
6 |
|
|
|
|
|
|
б |
Рис. 2.21. Схема пресс-формы для мундштучного формования: а – простых изделий; б – изделий (труб, профилей) с постоянным сечением; 1 – пуансон; 2 – матрица; 3 – держатель мундштука; 4 – мундштук; порошок; 5 – порошок; 6 – сформованное изделие; 7 – плунжер пресса; 8 – звездочка; 9 – ввинченная в звездочку игла
Для получения профиля с переменным сечением внутренней полости игла, изготовленная в форме цилиндра с конусообразным завершением, с помощью специального устройства перемещается по оси в направляющих звездочки. В зависимости от того, какой участок подвижной иглы находится в выходном отверстии мундштука, выдавливается изделие с меньшим или большим внутренним отверстием.
Выходное отверстие мундштука называется «очком». При формовании труб и стержней небольшого диаметра и сечения высота мундштука должна быть в 2,5–4 раза больше диаметра его выходного отверстия,
Процессы порошковой металлургии. Курс лекций |
-284- |

II. ФОРМОВАНИЕ И СПЕКАНИЕ ИЗДЕЛИЙ ИЗ МЕТАЛЛИЧЕСКИХ И НЕМЕТАЛЛИЧЕСКИХ ПОРОШКОВ
Лекция 8 Мундштучное и инжекционное формование порошков
Скорость выдавливания материала через мундштук не должна превышать 5–10 мм/с. Более высокие скорости формования приводят к появлению неравномерной пористости изделий.
Давление мундштучного формования при постоянной степени обжатия минимально при выдавливании материала через мундштук с углом конуса 90°. Обычно это давление составляет несколько сотен мегапаскалей. Степень обжатия материала при выдавливании через очко должна составлять не менее 90 %. Степень обжатия можно рассчитать по формуле
K = [(S – s)/s]100%, |
(2.25) |
где S – площадь сечения матрицы пресс-формы; s – площадь сечения выходного отверстия (очка) мундштука.
После формования заготовки, которые формовали с использованием смазок на основе водных растворов, подвергают сушке (конечная влажность должна составлять не более 4–6 %).
При уплотнении порошка в матрице перед его истечением из очка образуются отдельные слои материала, отличающиеся по напряженному состоянию и плотности, что и является причиной дефектов структуры у получаемых заготовок и спеченных изделий. Целесообразно разделить процесс мундштучного формования на две операции: сначала провести предварительное уплотнение порошка (подпрессовку), а затем обеспечить ему формоизменение при продавливании через очко. При применении предварительной подпрессовки наблюдаются увеличение плотности заготовок, активизация усадки при спекании, снижение пористости спеченных изделий и значительное повышение их механические свойств. Однако с повышением давления предварительной подпрессовки (в определенных пределах) увеличивается необходимое давление истечения материала. Рост начального давления истечения при подпрессовке объясняется увеличением межчастичной контактной поверхности.
Процесс экструзии порошка характеризуется напряжением всестороннего неравномерного сжатия. Под воздействием сжимающих напряжений материал течет в направлении выходного отверстия матрицы, где на свободной поверхности выдавливаемого материала нормальные напряжения равны нулю.
Всестороннее сжатие обеспечивает материалу наиболее высокую пластичность по сравнению с другими процессами обработки металла давлением, однако эта положительная особенность процесса проявляется в условиях крайне неравномерных деформаций и скоростей: не всегда во всем объеме деформируемого материала действуют только сжимающие напряжения, непрерывно уменьшающиеся в направлении экструзии от максимальных значений до нуля.
Процессы порошковой металлургии. Курс лекций |
-285- |

II. ФОРМОВАНИЕ И СПЕКАНИЕ ИЗДЕЛИЙ ИЗ МЕТАЛЛИЧЕСКИХ И НЕМЕТАЛЛИЧЕСКИХ ПОРОШКОВ
Лекция 8 Мундштучное и инжекционное формование порошков
Наличие разности сечений контейнера и очка матрицы, сил внешнего трения и других факторов заставляет двигаться частицы в направлении, поперечном направлению приложения усилий (рис. 2.22), а также приводит к появлению местных напряжений, различных по величине, направлению и знаку (в том числе растягивающих напряжений). К тому же частицы материала перемещаются по траекториям различной длины со скоростью, меняющейся в процессе прохождения ими различных зон. Когда растягивающие напряжения на отдельных участках деформируемого материала превысят предел прочности, появляются дефекты (в том числе трещины) или происходит полное разрушение заготовок.
Мундштучное формование без пластификатора возможно, если выдавливать нагретые металлы или сплавы.
Рис. 2.22. Схема движения порошка при мундштучном прессовании: 1 – пуансон; 2 – матрица; 3 – держатель мундштука; 4 – мундштук; 5 – порошок; 6 – «застойные» зоны
|
1 |
2 |
|
5 |
6 |
3 |
|
|
4 |
При относительно низких температурах (до 600 °С) заготовку или порошок обычно нагревают вместе с матрицей. Такие металлы, как бериллий, цирконий, титан, вольфрам при горячей обработке могут интенсивно окисляться. Поэтому при их нагреве и формовании необходимо применять защитные среды.
В некоторых случаях для защиты заготовок или порошков применяют защитные оболочки, которые могут быть стеклянными, графитовыми и металлическими.
Металлические оболочки особенно хорошо предохраняют от окисления получаемые заготовки до момента их полного охлаждения и служат одновременно смазками, улучшающими процесс истечения. Материалы оболочки должны соответствовать определенным требованиям:
Процессы порошковой металлургии. Курс лекций |
-286- |

II. ФОРМОВАНИЕ И СПЕКАНИЕ ИЗДЕЛИЙ ИЗ МЕТАЛЛИЧЕСКИХ И НЕМЕТАЛЛИЧЕСКИХ ПОРОШКОВ
Лекция 8 Мундштучное и инжекционное формование порошков
материал оболочки не должен взаимодействовать с прессуемым порошком с образованием устойчивых соединений;
пластические свойства и сопротивление деформированию материала оболочки и прессуемого порошка должны быть максимально близкими;
материал оболочки должен обладать хорошими «смазывающими» свойствами.
В зависимости от природы формуемого металлического порошка, оболочки изготавливают из меди, латуни, низкоуглеродистой стали или биметалла в виде медножелезной фольги. После завершения формования оболочки чаще всего удаляют с заготовки механическим путем, хотя возможно также их удаление травлением в растворах, не действующих на порошковый материал.
Инжекционноеформованиепорошков
За последние годы в практике порошковой металлургии все большее распространение находит так называемое инжекционное формование (его также называют «литье под давлением»). В определенной степени этот метод можно рассматривать как разновидность метода литья пластифицированных шликеров. Происходящее в настоящее время расширение применения инжекционного формования объясняется высокой эффективностью массового производства изделий сложной формы из порошков самых различных материалов.
Преимущества инжекционного формования связаны с возможность получения заготовок (деталей) сложной формы, с очень точными размерами и высоким качеством поверхности. Кроме того, настоящий метод имеет малую продолжительность рабочего цикла (около 1,5–2 мин), что обеспечивает массовое производство заготовок и высокую степень автоматизации производства. Методом инжекционного формования обычно изготавливают детали массой от 0,1 до 150 грамм (размеры мелких изделий около 0,75–5 мм).
Порошки для инжекционного формования должны иметь достаточно низкую свободную поверхностную энергию, чтобы хорошо смешиваться со связующим, и одновременно эта энергия должна быть, возможно, более высокой для лучшей спекаемости. Этим требованиям соответствуют сферические порошки (например, карбонильные) с частицами размером до 10 мкм (желательно 1–5 мкм). Обычно содержание твердых частиц в смеси с пластификатором составляет от 40 до 90 % по объему в зависимости от их размера и формы.
Технологическая схема производства изделий методом инжекционного формования включает операции подготовки шихты (смешивания твердой фазы с пластификатором), ее гранулирования, формования изделий, удаления связующего компонента и спекания материала.
Процессы порошковой металлургии. Курс лекций |
-287- |

II. ФОРМОВАНИЕ И СПЕКАНИЕ ИЗДЕЛИЙ ИЗ МЕТАЛЛИЧЕСКИХ И НЕМЕТАЛЛИЧЕСКИХ ПОРОШКОВ
Лекция 8 Мундштучное и инжекционное формование порошков
Важным этапом является выбор связующего компонента, который может быть твердым, жидким или вязким. При инжекционном формовании могут использовать пластификаторы и термопластичные материалы (полистирол, полиэтилен, акриловую смолу, парафин, стеарин, диэтилфталат, дибутилфталат, эфиры жирных кислот и др.), а также смазки (стеариновую кислоту, стеарат цинка, минеральное масло и др.).
Для проведения инжекционного формования используют, как правило, литьевые машины для производства изделий из пластмасс. Обычно литьевая машина состоит из нескольких основных узлов: инжекционного, прессового, привода и управления. Инжекционный узел включает загрузочный бункер для подачи гранулированного порошка в машину и инжектора (цилиндра с соплом). Гранулы материала из бункера с помощью шнека подаются в нагреваемый инжектор, откуда (после плавления материала) под давлением впрыскиваются в разъемную форму. Формы изготовляют из материала с высокой теплопроводностью (меди, латуни и пр.).
Основное назначение инжекционного узла: пластификация формуемой массы (размягчение и нагревание до требуемой температуры), впрыск (перемещение) пластичной (псевдожидкой) массы в форму под действием развиваемого в гидроцилиндром узла впрыска.
Смесь порошка с термопластичным связующим (иногда ее называют «пластизоль») получают путем плавления гранул материала. Температура нагрева пластифицированной массы зависит от свойств связующего и может достигать 160 °С, но она не должна превышать температуру возгорания.
Плотность получаемых заготовок обычно около 70 % от теоретической. Удаление связующего проводят по технологии, близкой к технологии удаления связки из изделий, полученных литьем термопластичных шликеров. После удаления пластификатора заготовку спекают. В процессе спекания формовка может уплотняться до относительной плотности порядка 96 % (усадка при этом достигает 15–20 %).
Контрольныевопросыизадания
1.Дайте определение понятию «мундштучное формование».
2.В чем суть метода мундштучного формования?
3.Какие изделия получают методом мундштучного формования?
4.Назовите способы получения изделий методом мундштучного формования.
5.Как можно снизить внешнее трение порошка при мундштучном формовании и защитить его от окисления?
6.В каком случае возможно мундштучное формование порошка без применения смазок?
7.В чем состоит сущность метода инжекционного формования?
8.Какими отличительными особенностями обладает метод инжекционного формования порошков?
Процессы порошковой металлургии. Курс лекций |
-288- |

II. ФОРМОВАНИЕ И СПЕКАНИЕ ИЗДЕЛИЙ ИЗ МЕТАЛЛИЧЕСКИХ И НЕМЕТАЛЛИЧЕСКИХ ПОРОШКОВ
Лекция 8 Мундштучное и инжекционное формование порошков
9.Перечислите операции получения изделий методом инжекционного формования.
10.Как удаляют пластификатор, из изделий, полученных инжекцион-
ным формованием?
Лекция9 Вибрационноеформованиепорошков
План лекции
1.Способы виброформования.
2.Схемы вибрационного формования.
3.Режимы и установки для виброформования.
Способывиброформования
Первые сведения о применении вибрационного формования появились в конце 40-х гг. прошлого столетия. Было обнаружено, что применение вибрации при засыпке и утряске порошка в пресс-форме или в процессе уплотнения позволяет значительно уменьшить давление прессования и повысить равноплотность получаемых прессовок сложной формы.
При вибропресовании порошок приобретает свойства, подобные свойствам жидкости. Он как бы начинает «течь», увеличивая свою плотность. Положительное воздействие вибрации на процесс уплотнения порошка связано с преобразованием исходной структуры (в частности, разрушением арок) и улучшением взаимоподвижности частиц, в результате чего достигается высокая плотность их укладки (90 % и выше от теоретически возможной).
Наиболее эффективно вибрация проявляется при уплотнении порошков, представляющих собой набор фракций частиц различного размера. Так, для шариков одного размера (монофракционных, монодисперсионных) независимо от их диаметра и природы материала под воздействием вибрации плотность укладки достигает 60–64 %.
Если рассматривать многофракционную (рис. 2.23) смесь из крупных, средних и мелких частиц, то для получения наиболее плотной укладки размер частиц каждой последующей фракции должен быть в 5–10 раз меньше размера частиц предыдущей фракции. Количество этой более мелкой фракции можно оценить равенством Андреазена:
q = (d/D)0,5,
Процессы порошковой металлургии. Курс лекций |
-289- |

II. ФОРМОВАНИЕ И СПЕКАНИЕ ИЗДЕЛИЙ ИЗ МЕТАЛЛИЧЕСКИХ И НЕМЕТАЛЛИЧЕСКИХ ПОРОШКОВ
Лекция 9 Вибрационное формование порошков
где q – количество более мелкой фракции (следующей за более крупной); d – размер частиц этой (более мелкой) фракции; D – размер частиц предшествующей (более крупной) фракции.
Способы вибрационного формования различают по следующим основным признакам:
по характеру динамического воздействия на прессуемый порошок (вибрационное и виброударное формование);
по соотношению между статической и динамической составляющими усилия прессования (силами трения, препятствующими перемещению частиц, и вибрационными силами, способствующими преодолению сил трения);
Рис. 2.23. Модель пространственной укладки сферических частиц порошка трех фракций
по характеру процесса: дискретное (прерывистое) вибрационное формование в закрытом пресс-инструменте; непрерывное вибрационное формование (в установках шликерного формования, прокатки порошка и др.);
по схеме (циклограмме) процесса.
Схемывибрационногоформования
На практике используют следующие схемы получения заготовок:
1)с предварительным вибрационным уплотнением и последующим статическим прессованием;
2)с вибрационным воздействием на порошок в течение всего процесса прессования (без выдержки под давлением);
3)с вибрационным или виброударным воздействием на порошок в течение всего цикла прессования, включая выдержку под давлением.
При вибрационном формовании возможны различные варианты процесса: холодное или горячее прессование; прессование без смазки или со смазкой; прессование с вакуумированием порошка и т.п.
Пресс-инструмент для осуществления прессования различается
по способу передачи энергии вибрации порошку (соединения элементов фор-
мы с вибратором); по жесткости опоры матрицы (неподвижная или «пла-
Процессы порошковой металлургии. Курс лекций |
-290- |
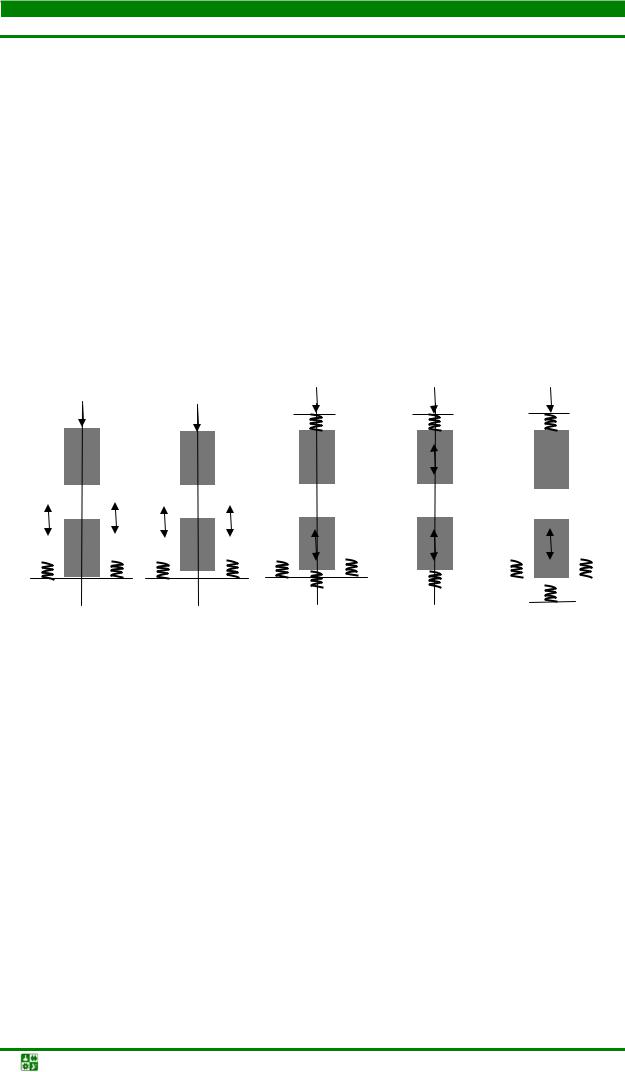
II. ФОРМОВАНИЕ И СПЕКАНИЕ ИЗДЕЛИЙ ИЗ МЕТАЛЛИЧЕСКИХ И НЕМЕТАЛЛИЧЕСКИХ ПОРОШКОВ
Лекция 9 Вибрационное формование порошков
вающая»); по жесткости систем передачи статического усилия прессования на верхний пуансон (жесткая и упругая); по принципу соединения вибратора с пресс-инструментом (жесткое соединение вибратора с пуансонами и матрицей, упругое соединение вибратора с матрицей); по количеству прессую-
щих пуансонов (с одним, и двумя).
Схемы «вибрирующего контейнера» (рис. 2.24, а, б) и «вибрирующих пуансонов» (рис. 2.24, в, г) позволяет достичь высокой и практически одинаковой плотности по всему объему прессовки с очень большим отношением высоты к диаметру. Схема, когда уплотнение порошка происходит под воздействием вибрации только одного из пуансонов (рис. 2.24, в), применяется при получении изделий с небольшим отношением высоты к размеру поперечного сечения. На практике применяют и схему, при которой вибрационные колебания предаются порошку сразу от нижнего пуансона и мат-
рицы (рис. 2.24, г).
р'о |
р'о |
р'о |
р'о |
р'о |
|
|
|
|
|
|
|
|
|
|
|
|
|
|
|
|
|
|
|
|
|
|
|
|
|
|
|
|
|
|
|
|
|
|
|
|
|
|
|
|
|
|
|
|
|
|
|
|
|
|
|
|
|
|
|
|
|
|
|
|
|
|
|
|
|
|
|
|
|
|
|
|
|
|
|
|
|
|
|
|
|
|
|
|
|
|
|
|
|
|
|
|
|
|
|
|
|
|
|
|
|
|
|
|
|
|
|
|
|
|
|
|
|
|
|
|
|
|
|
|
|
|
|
|
|
|
|
|
|
|
|
|
|
|
|
|
|
|
|
|
|
|
|
|
|
|
|
|
|
|
|
|
|
|
|
|
|
|
|
|
|
|
|
|
|
|
|
|
|
|
|
|
|
|
|
|
|
|
|
|
|
|
|
|
|
|
|
|
|
|
|
|
|
|
|
|
|
|
|
|
|
|
|
|
|
|
|
|
|
|
|
|
|
|
|
|
|
|
|
|
|
|
|
|
|
|
|
|
|
|
|
|
|
|
|
|
|
|
|
|
|
|
|
|
|
|
|
|
|
|
|
|
|
|
|
|
|
|
|
|
|
|
|
|
|
|
|
|
|
|
|
|
|
|
|
|
|
|
|
|
|
|
|
|
в |
|
|
|
г |
|
|
|
|
|
|
||||
|
а |
|
б |
|
|
|
|
|
|
|
|
|
|
д |
|
Рис. 2.24. Схемы пресс-инструмента для вибрационного прессования
(двунаправленной стрелкой помечен вибрирующий элемент)
Вибратор может быть гидравлический, пневматический, электромагнитный, магнитно-стрикционный, электромеханический (дебалансный, двухвальный дебалансный направленного действия и др.).
Для производственных процессов более приемлемы электромеханические вибраторы с динамическим возбуждением колебаний, позволяющие получать значительные величины возмущающих сил при простой конструкции.
При выборе схемы пресс-инструмента для вибрационного прессования стремятся к тому, чтобы энергия вибрации передавалась от вибратора к порошку через возможно более жесткую систему и преимущественно поглощалась им.
Экспериментально установлено, что более эффективны схемы с вибрирующей матрицей; при этом всегда должно выполняться условие подвиж-
Процессы порошковой металлургии. Курс лекций |
-291- |

II. ФОРМОВАНИЕ И СПЕКАНИЕ ИЗДЕЛИЙ ИЗ МЕТАЛЛИЧЕСКИХ И НЕМЕТАЛЛИЧЕСКИХ ПОРОШКОВ
Лекция 9 Вибрационное формование порошков
ности пуансонов (как и условие подвижности матрицы при вибрировании пуансонов).
Наиболее эффективно применение вибрации проявляется в случае уплотнения порошков малопластичных материалов (например, карбидов или боридов тугоплавких металлов), для которых удается получить плотные (75–85 % от теоретической плотности) и прочные прессовки при небольшом давлении (0,3–0,6 МПа).
Это объясняется тем, что вибрация, придавая частицам порошка высокую подвижность, способствует их наиболее плотной укладке, а небольшое давление прессования обеспечивает заклинивание частиц в этом положении, в результате чего образуются сравнительно прочные заготовки с незначительными внутренними напряжениями. Для порошков различных металлов статическое давление, прикладываемое одновременно с вибрацией, обычно составляет 0,5–5,0 МПа. Отсутствие давления может привести не к уплотнению, а к разрыхлению порошка.
Необходимо отметить, что плотность укладки частиц все же в основном зависит от параметров вибрирования.
Режимыиустановкидлявиброформования
Импульсная энергия вибрирования расходуется как на преодоление инерции и упругого сопротивления вибрирующей системы, так и на преодоление инерции и сил трения и сцепления уплотняемого порошка. Если у п- лотняемая масса порошка невелика, то основную роль будет играть инерция и упругие свойства системы (ее собственная частота колебаний); поэтому для обеспечения наиболее выгодного режима уплотнения следует выбирать вынужденную частоту вибрирования ближе к собственной частоте колебаний системы.
При уплотнении больших масс порошка значительную роль будут играть собственная частота колебаний слоя частиц и силы связи между ними; в этом случае частоту вибрирования нужно выбирать ближе к резонансной относительно или вибрирующей системы, или уплотняемой массы порошка.
Режим вибрирования принято характеризовать частотой колебаний W (количество колебаний тела за одну минуту), ускорением а, см/с2, и амплитудой А, см, которые связаны между собой выражением
А = a/(πW/30)2.
Для данного порошка при одинаковой амплитуде плотность укладки частиц возрастает с повышением частоты вибрирования, что свидетельствует о приближении к резонансным значениям между частотой вынужденных колебаний вибратора и собственных колебаний слоя порошка.
Процессы порошковой металлургии. Курс лекций |
-292- |

II. ФОРМОВАНИЕ И СПЕКАНИЕ ИЗДЕЛИЙ ИЗ МЕТАЛЛИЧЕСКИХ И НЕМЕТАЛЛИЧЕСКИХ ПОРОШКОВ
Лекция 9 Вибрационное формование порошков
Для небольших объемов порошка с частицами размером > 100 мкм эффективнее частоты от 6 000 до 12 000 колебаний в 1 мин, с частицами размером 1–100 мкм – порядка 12 000–18 000 колебаний в 1 мин, с частицами размером < 1 мкм – более 18 000 колебаний в 1 мин. С уменьшением размера частиц необходимо не только увеличивать частоту вибрирования, но и увеличивать нагрузку на порошок. Увеличение нагрузки необходимо и при нарастании шероховатости поверхности (при значительных отклонениях от сферической формы).
При этом для порошков с частицами размером < 10 мкм с увеличением частоты вибрирования ускорение также должно возрастать, чтобы в соответствии с приведенной выше взаимозависимостью A, W и а не произошло существенного уменьшения амплитуды.
Для порошков хрупких материалов необходимо выбирать более высокую частоту и меньшую амплитуду вибрирования (при сохранении постоянной величины ускорения).
Рис. 2.25. Типовая схема вибропресса с одним силовым цилиндром: 1, 3 – траверсы; 2 – направляющие; 4 – стол; 5 – рабочий цилиндр; 6 – возвратные пружины; 7 – плунжер; 8 – обмотка электромагнита; 9 – пружина пульсатора; 10 – сердечник электромагнита; 11, 15 – штоки пульсатора; 12 управляющий золотник; 13 – корпус; 14 – магистраль; 16 – поршень; 17 – прессформа
Процессы порошковой металлургии. Курс лекций |
-293- |

II. ФОРМОВАНИЕ И СПЕКАНИЕ ИЗДЕЛИЙ ИЗ МЕТАЛЛИЧЕСКИХ И НЕМЕТАЛЛИЧЕСКИХ ПОРОШКОВ
Лекция 9 Вибрационное формование порошков
На рис. 2.25 приведена схема вибропресса с одним силовым цилиндром (ИВПМ), а в табл. 2.4 – технические характеристики прессов для вибрационного формования порошков.
Таблица 2.4 Технические характеристики вибропрессов ИВПМ и ИВПС
Характеристика |
|
Тип вибропресса |
|||
|
|
|
|
||
ИВПМ-20 |
ИВПМ-32 |
ИВПС-20 |
|||
|
|||||
|
|
|
|
|
|
Номинальное рабочее усилие, кН |
200 |
|
320 |
200 |
|
Интервал установочного регулирования частот, Гц |
10–40 |
|
15–30 |
10–30 |
|
Пределы регулирования амплитуды колебаний, мм |
0,5–3 |
|
2–6 |
0,5–3 |
|
Максимальное ускорение на рабочем органе, м/с2 |
180 |
|
200 |
200 |
|
Рабочий ход траверсы, м |
0,8 |
|
0,6 |
0,8 |
|
Мощность привода, кВт |
17 |
|
34 |
17 |
|
Давление в гидросистеме, МПа |
32 |
|
32 |
32 |
|
Подача насоса, дм3/с |
0,6 |
|
1,2 |
0,6 |
|
Максимальные размеры формуемой заготовки, м |
0,7x0,8 |
|
0,7x0,8x0,6 |
0,7x0,8x0,6 |
Уплотнение порошков под воздействием вибрации происходит достаточно быстро, в основном не более чем за 30 с. Оптимальная укладка частиц достигается, как правило, за 2–10 с.
Увеличение времени вибропрессования больше оптимального дает незначительное повышение плотности прессовки и приводит к существенному возрастанию внутренних напряжений.
С увеличением объема прессовки с 10 до 100 см3 длительность вибровоздействия, необходимая для достижения одинаковой плотности укладки частиц по объему заготовки, возрастает всего примерно в 1,5–2,0 раза.
Продолжительность укладки частиц существенно зависит от их формы (чем частицы ближе по форме к сферичесчкой, тем быстрее уплотняется порошок) и гранулометрического состава порошка (частицы одинакового размера уплотняются хуже, чем порошок, содержащий частицы разного размера).
Для уменьшения сил трения между частицами в процессе уплотнения применяют смазки, количество которых не должно быть большим (в противном случае произойдет существенное снижение прочности формовки из-за разобщения частиц толстыми пленками смазки).
Для неактивных и слабоактивных смазок (вазелиновое масло, глицерин, поливиниловый спирт) оптимальное количество смазки составляет 0,5–1,5 % (по массе) при размере частиц порошка 1–5 мкм, а для поверхност- но-активных смазок (олеат натрия, олеиновая кислота и др.) это количество в несколько раз меньше. При введении в состав порошка смазки плотность прессовок повышается примерно 6–12 %.
Процессы порошковой металлургии. Курс лекций |
-294- |
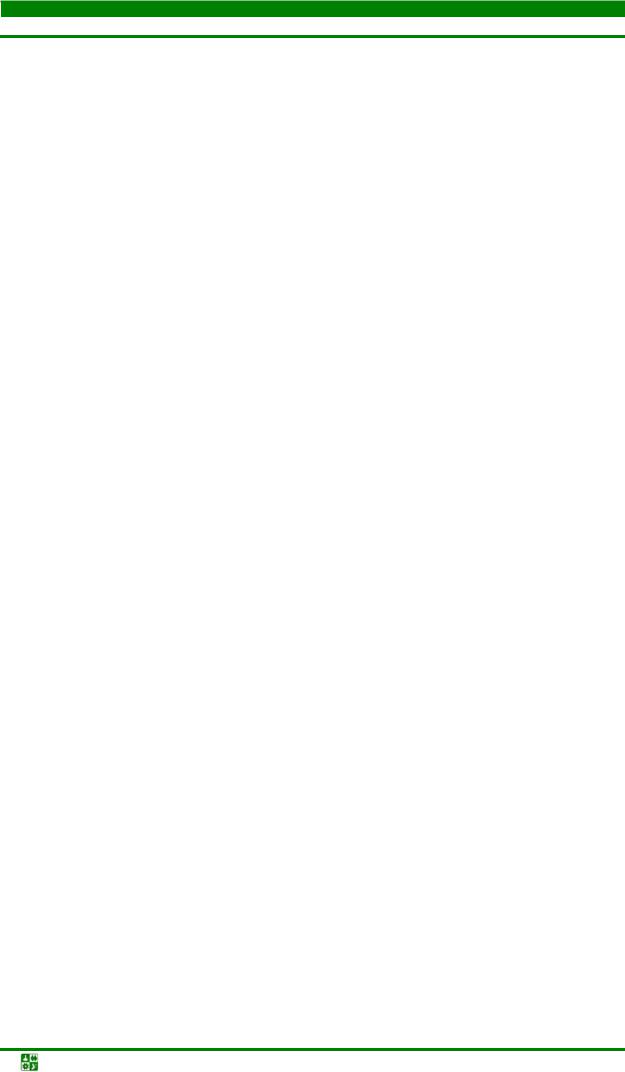
II. ФОРМОВАНИЕ И СПЕКАНИЕ ИЗДЕЛИЙ ИЗ МЕТАЛЛИЧЕСКИХ И НЕМЕТАЛЛИЧЕСКИХ ПОРОШКОВ
Лекция 9 Вибрационное формование порошков
Контрольныевопросыизадания
1.Расскажите об основных закономерностях вибропрессования.
2.Какие преимущества имеет метод вибрационного формования?
3.В чем суть метода вибрационного формования?
4.Перечислите схемы вибропрессования.
5.Классифицируйте пресс-инструмент по способу приложения виброусилий.
6.Укажите диапазон частот виброусилий и давлений при формовании порошков.
Лекция10 Импульсноеформование
План лекции
1.Методы взрывного формования.
2.Электрогидравлическое формование порошков.
3.Электромагнитное формование.
4.Пневмомеханическое формование.
Методывзрывногоформования
Импульсное формование металлического порошка или порошковой формовки это формование, при котором уплотнение производится ударными волнами за время, не превышающее 1 с.
Определяющий и характерный признак импульсного формования – высокие скорости приложения нагрузки (5–10 м/с и выше). Продолжительность процесса уплотнения порошка составляет от нескольких сотых до нескольких тысячных или даже стотысячных долей секунды.
В промышленных масштабах этот метод применяют с середины 50-х гг. прошлого века (взрывная штамповка, получение слоистых структур).
Преимуществами высокоскоростного формования порошков перед традиционными методами является возможность создания чрезвычайно высоких давлений, возможность получения больших плотностей формовки (вплоть до 100 %), возможность сращивания слоев разнородных материалов.
При высоких скоростях формования порошка теплота, выделяющаяся в результате деформации частиц, межчастичного и внешнего (если оно есть) трения, приводит к локальному нагреву межчастичных контактов и их свариванию.
Процессы порошковой металлургии. Курс лекций |
-295- |

II. ФОРМОВАНИЕ И СПЕКАНИЕ ИЗДЕЛИЙ ИЗ МЕТАЛЛИЧЕСКИХ И НЕМЕТАЛЛИЧЕСКИХ ПОРОШКОВ
Лекция 10 Импульсное формование
Взависимости от вида источника энергии, обеспечивающего высокую скорость приложения нагрузки, различают взрывное, электрогидравлическое, электромагнитное и пневмомеханическое формование.
Вфизическом смысле взрыв – очень быстрое выделение энергии, связанное с внезапным изменением агрегатного состояния вещества (переходом из твердого состояния в газообразное). Взрыв, как правило, сопровождается образованием ударной волны.
Один из источников взрыва – химическая энергия (другими являются атомная, тепловая или электрическая энергия). Химический взрыв характеризуется крайне быстрым самораспространяющимся превращением некоторых механических смесей различных элементов с выделением теплоты и газообразных продуктов; такие вещества или смеси называют взрывчатыми веще-
ствами (ВВ).
Так, при взрыве 1 кг тротила, происходящего за 10 -6 с, образуется на-
гретый до 3 000 °С газ, который при нормальных условиях занимал бы объем 8,4 м3. Однако скорость химической реакции его превращения настолько ве-
лика, что образовавшийся газ не успевает заметно расшириться и его объем (в начальный период) соответствует объему твердого тротила 6,6·10-4 м3, создавая в нем давление продуктов взрыва, равное 1,3 ГПа. Нагретые газообразные продукты взрыва, расширяясь, сжимают окружающую среду и вызывают перемещение ее частиц (молекул) во все стороны от очага взрыва. Резкое расширение газа вызывает появление ударной волны огромной силы, которая способна разрушить находящийся на ее пути материал.
Возникшие в результате действия ударной волны напряжения на поверхности обрабатываемого материала распространяются внутрь его в виде локализованных волнообразных возмущений.
По мере продвижения ударной волны ее скорость уменьшается (из-за расхода кинетической энергии на нагревание окружающей среды, на трение
ит.п.), и на некотором расстоянии от очага взрыва она переходит в звуковую. ВВ удобны для создания ударной волны с высокой интенсивностью и
обеспечивают высокую скорость деформации порошкового тела.
В методах взрывного формования применяют заряды метательных (порохов) и бризантных взрывчатых веществ.
При применении метательных ВВ возможны различные варианты создания нагрузки на порошковое тело: передача энергии взрыва через подвижное, твердое тело – ударник, поршень (дистанционный метод); непосредственное воздействие ударной волны (контактный метод); передача давления через жидкую среду (дистанционный метод).
Ствольные системы, часто называемые пороховыми копрами, позволяют разгонять снаряд (ударник) до скорости 20–600 м/с. В другом случае кинетическая энергия сообщается порошковому телу ударной волной, созда-
Процессы порошковой металлургии. Курс лекций |
-296- |
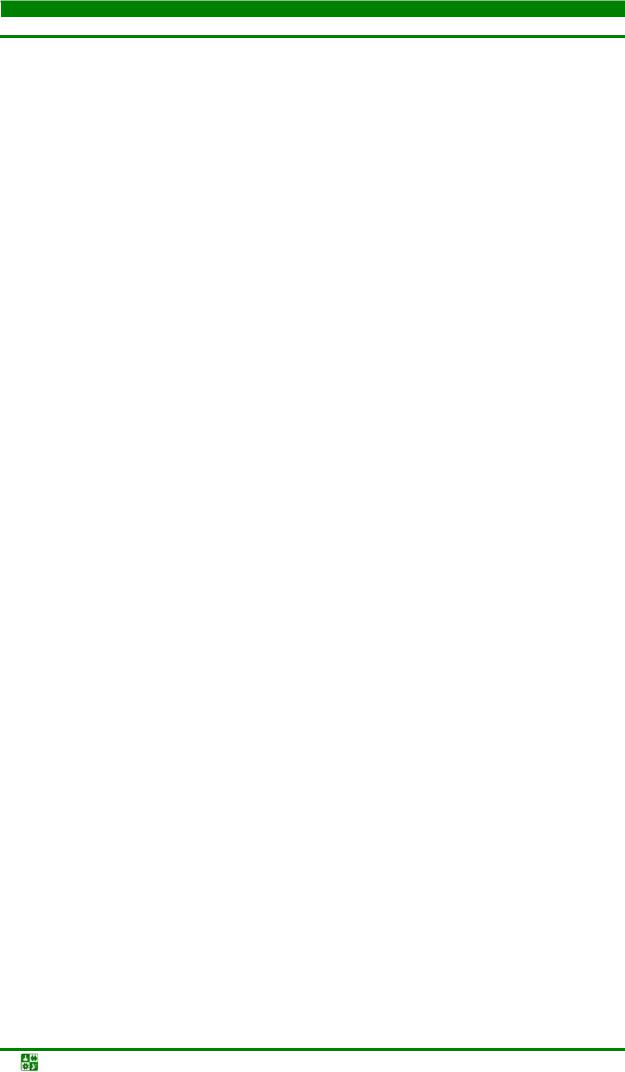
II. ФОРМОВАНИЕ И СПЕКАНИЕ ИЗДЕЛИЙ ИЗ МЕТАЛЛИЧЕСКИХ И НЕМЕТАЛЛИЧЕСКИХ ПОРОШКОВ
Лекция 10 Импульсное формование
ваемой в гидродинамических машинах (максимальное давление формования
500–1 500 МПа).
Первая установка для взрывного формования порошка в жидкости запатентована в США в 1953 г. Аналогичные машины появились вСССР в 1976 г. Эти машины, рама и контейнер которой выполнены с обмоткой из высокопрочной ленты, конструктивно напоминает современный гидростат, но вместо насосов высокого давления и мультипликаторов для сжатия жидкости в рабочей камере используют небольшой заряд пороха.
При инициировании (воспламенении) заряда давление пороховых газов передается в рабочую камеру через разделительный поршень и обеспечивает уплотнение порошка, расположенного в рабочей жидкости (смесь воды и эмульсола) в эластичной герметизированной оболочке. Максимальное импульсное давление в рабочей камере машины составляет около 600 МПа, длительность действия импульса давления обычно не более 5 10-2 с. Продолжительность рабочего цикла – не более 2–4 мин.
Метод гидродинамического формования можно использовать для изготовления крупногабаритных фильтров из порошков титана и нержавеющей стали, заготовок из вольфрама и молибдена, имеющих равномерную объемную плотность. Кроме того, этот метод можно использовать для получения изделий из порошков оксидов, нитридов и других материалов.
Характер уплотнения порошков аналогичен имеющему место при гидростатическом формовании, но увеличение скорости нагружения приводит к возрастанию сопротивления металлических частиц деформированию, из-за чего плотность получаемых формовок оказывается несколько ниже, чем
узаготовок, полученных в гидростате.
Вто же время при одинаковой плотности формовок прочность на сжатие и ударная вязкость заготовок после взрывного формования повышаются на 20–30 % за счет разрушения поверхностных оксидных пленок и образования чисто металлических связей, в том числе и типа сварки, благодаря плавлению металла частиц за счет высокой температуры на контактах в связи с локальным выделением тепла.
Контактные методы взрывного формования более эффективны при ис-
пользовании в качестве энергоносителя заряда бризантных ВВ. Взрывное превращение в этом случае происходит в форме детонации – цепной экзотермической реакции, распространяющейся по ВВ с постоянной и наибольшей для данных условий скоростью, называемой скоростью детонации. Величина скорости детонации для большинства промышленных ВВ составляет 3000–8 000 м/с. Температура продуктов взрыва достигает 3 000–5 000 К, плотность их возрастает примерно на 30 % по сравнению с исходной, а пиковое давление за фронтом детонации достигает 3–28 ГПа.
Время действия импульсных давлений при взрыве заряда бризантных ВВ не превышает обычно (5–9)·10-6 с. Типовые схемы взрывного формования предусматривают расположение заряда ВВ на поверхности контейнера с по-
Процессы порошковой металлургии. Курс лекций |
-297- |

II. ФОРМОВАНИЕ И СПЕКАНИЕ ИЗДЕЛИЙ ИЗ МЕТАЛЛИЧЕСКИХ И НЕМЕТАЛЛИЧЕСКИХ ПОРОШКОВ
Лекция 10 Импульсное формование
рошком, либо формование порошка металлическим поршнем с накладным зарядом ВВ, который разгоняется до скорости около 1 500 м/с.
Взрывное формование порошков пластичных материалов обеспечивает получение заготовок с относительной плотностью 92–95 % при интенсивной пластической деформации частиц и образовании прочных связей между ними. Структура сформированной заготовки зависит от скорости приложения нагрузки (рис. 2.26).
а |
б |
в |
Рис. 2.26. Микроструктура брикетов из сферического медного порошка (фракция –300…+160 мкм) при статическом нагружении (а) и скорости детонации ВВ 3 500 (б) и 7 000 м/с (в)
Формование порошков низкопластичных металлов, сплавов и туг о- плавких соединений сопровождается разрушением хрупких частиц, их структурной перестройкой и механическим расклиниванием при значительном повышении: твердости, уровня микродеформаций, плотности дислокаций и других дефектов кристаллической решетки.
В общем случае при взрывном формовании зарядом бризантных ВВ имеют место эффекты ударного сжатия, а разгрузка сжатого материала носит волновой характер.
Электрогидравлическоеформованиепорошков
Метод основан на возбуждении ударной волны при токовом разряде в жидкости. При искровом разряде между электродами, погруженными в жидкость, образуется токопроводящий канал, частично заполненный ионизированным газом; его первоначальное сечение мало, а энергия в нем нарастает со скоростью 104 м/с и процесс приобретает характер взрыва. Под влиянием быстрого расширения искрового канала в жидкости возникает ударная волна, скорость распространения которой значительно превышает скорость расширения искрового канала, и через 0,5–1,5 мкс фронт ударной волны отрывается от расширяющегося канала. На процесс распространения ударной волны существенное влияние оказывает электропроводность жидкости.
Превращение электрической энергии в механическую в жидкой среде можно осуществить двумя основными методами: разрядом конденсатора че-
Процессы порошковой металлургии. Курс лекций |
-298- |

II. ФОРМОВАНИЕ И СПЕКАНИЕ ИЗДЕЛИЙ ИЗ МЕТАЛЛИЧЕСКИХ И НЕМЕТАЛЛИЧЕСКИХ ПОРОШКОВ
Лекция 10 Импульсное формование
рез зазор между двумя электродами, погруженными в жидкость, и разрядом через проводник, перекрывающий зазор между электродами, погруженными в жидкость.
Батарея конденсаторов заряжается с помощью специального устройства, имеющего выпрямитель тока и регулятор напряжения. При разрядке конденсатора через электроды в жидкости величина пробиваемого межэлектродного промежутка определяется не только напряжением, но зависит также от проводимости среды и формы электродов; обычно используют напряжение 10–30 кВ.
При применении проводника, инициирующего разряд между погруженными в жидкость электродами, его размеры и природа материала (металл, пастообразная смесь, нить из непроводящего носителя и проводящей обмотки и др.) существенно влияют на выделяемую энергию, давление (до 250 МПа) и скорость распространения ударной волны.
Разряд через проводник позволяет осуществлять лучшее по сравнению с предыдущим управление процессом формования, так как путь электрического разряда может быть предопределен. Кроме того, этот метод обеспечивает более эффективное превращение энергии и дает возможность снижать рабочие напряжения, так как при наличии проводника одно и то же напряжение перекрывает большее межэлектродное расстояние, чем без него. Недостаток метода – необходимость заменять проводник после каждого разряда.
Полезная работа, совершаемая при преобразовании электрической энергии в механическую, составляет 10–40 % выделенной энергии.
Электромагнитноеформование
Метод основан на использовании для уплотнения порошков энергии мощного импульсного магнитного поля (при напряженности поля 300 кЭ развивается давление порядка 400 МПа).
В этом методе электрическая энергия, запасенная конденсатором, при его разряде преобразуется посредством индуктора в энергию импульсного магнитного поля, воздействующего на порошковое тело (порошок или предварительно сформованная заготовка): деформирование электропроводящего порошкового тела обеспечивают силы, создаваемые взаимодействием инициируемых в нем вихревых токов с током, проходящим через индуктор. Для получения магнитных импульсов различной конфигурации применяют плоские, спиральные, соленоидные и другие индукторы.
Выделение накопленной в конденсаторе энергии происходит очень быстро (10–30 мкс), и некоторая ее часть тратится на нагрев обрабатываемого порошкового тела.
Процессы порошковой металлургии. Курс лекций |
-299- |

II. ФОРМОВАНИЕ И СПЕКАНИЕ ИЗДЕЛИЙ ИЗ МЕТАЛЛИЧЕСКИХ И НЕМЕТАЛЛИЧЕСКИХ ПОРОШКОВ
Лекция 10 Импульсное формование
Эффективность магнитно-импульсного формования зависит от удельного электросопротивления материала частиц порошка. Наиболее подходящими для деформирования являются металлы с высокой электропроводностью, такие как золото, серебро, медь, алюминий, малоуглеродистые стали и другие, имеющие удельное электросопротивление < 15 мкОм/см.
При обработке материалов с низкой электропроводностью для создания нужных усилий используют спутники из хорошо проводящих материалов, помещаемые между заготовкой (порошковым телом) и индуктором и играющие роль «движителя». Большое значение имеет расстояние между индуктором и порошковым телом. Наибольшая эффективность достигается при зазоре между ними < 1 мм.
Так как электромагнитное поле почти не взаимодействует с непроводниками, электромагнитный импульс может быть сообщен формуемому порошку (порошковому телу) через непроводящую оболочку.
Пневмомеханическоеформование
Для уплотнения порошкового тела используют энергию, выделяющуюся при адиабатическом расширении сильно сжатого газа (воздух, азот и др.). Пневмомеханические высокоскоростные машины относятся к одному из прогрессивных типов металлообрабатывающего оборудования и отличаются простотой действия.
Типовая установка двустороннего ударного прессования имеет гидравлические и пневматические цилиндры. Гидравлический цилиндр является вспомогательным и служит для восстановления энергии сжатого газа, израсходованного при ударе. Номинальное давление газа в пневмоцилиндре до 12 МПа, номинальное усилие гидроцилиндра 30 кН.
На практике применяются машины, представляющие собой гибрид высокоскоростного пресса и двигателя внутреннего сгорания. Поршень камеры сгорания соединен с пуансоном пресс-формы. В камеру сгорания через впрыскиватель подается топливо, воспламеняемое при помощи свечи, после воспламенения давление в камере сгорания увеличивается в 5–7 раз и поршень пресс-формы с порошком начинает перемещаться, уплотняя последний.
При импульсном формовании большое значение имеет скорость нагружения порошкового тела: с ее увеличением развитие пластической деформации, требующее времени, уменьшается, растет доля упругих деформаций межчастичных контактов и на 40–50 % увеличивается упругое последействие по сравнению со статическим формованием. В большинстве случаев формовки, полученные импульсными методами, обладают более высокими прочностными характеристиками. Так, при взрывном формовании железного порошка прочность формовок оказалась на 10–15 %, а с увеличением скорости приложения нагрузки на 30 % выше по сравнению с прочностью брикетов, полученных при статическом прессовании. Это объясняется влиянием
Процессы порошковой металлургии. Курс лекций |
-300- |

II. ФОРМОВАНИЕ И СПЕКАНИЕ ИЗДЕЛИЙ ИЗ МЕТАЛЛИЧЕСКИХ И НЕМЕТАЛЛИЧЕСКИХ ПОРОШКОВ
Лекция 10 Импульсное формование
давлений и температур, развивающихся в зонах контактов частиц, которые при условии меньшей площади контакта способны приводить к образованию металлической связи типа сварки, обладающей высоким сопротивлением сдвигу контактов частиц порошкового тела.
Импульсное формование тем выгоднее, чем выше исходные плотность и твердость частиц порошка. После формования наблюдается значительное искажение кристаллической решетки уплотняемого материала (напряжения второго рода повышаются в 2–2,5 раза, плотность дислокаций увеличивается в 4–6 раз), что заметно сказывается на формировании свойств изделия при спекании.
Контрольныевопросыизадания
1.Дайте определение понятию «импульсное формование».
2.Какие преимущества имеет метод импульсного формования по-
рошков?
3.Перечислите и дайте характеристику взрывным методам прессования порошков.
4.Какие системы используются для создания необходимого давления
вметоде взрывного формования?
5.Назовите типовые схемы взрывного формования в соответствии с расположением заряда.
6.Дайте краткую характеристику методу электрогидравлического формования порошков.
7.Расскажите о электромагнитном и пневмомеханическом методах импульсного формования.
8.Назовите факторы, определяющие качество формовок при применении методов импульсного формования.
Лекция11 Получениеизделийметодомпрокаткипорошков
План лекции
1.Виды прокатки.
2.Параметры прокатки.
3.Уплотнение порошкового тела при прокатке.
4.Виды брака при прокатке.
Видыпрокатки
Процессы порошковой металлургии. Курс лекций |
-301- |

II. ФОРМОВАНИЕ И СПЕКАНИЕ ИЗДЕЛИЙ ИЗ МЕТАЛЛИЧЕСКИХ И НЕМЕТАЛЛИЧЕСКИХ ПОРОШКОВ
Лекция 11 Получение изделий методом прокатки порошков
Прокатка порошка – это метод получения заготовок (изделий) из металлического порошка путем его обработки с использованием валков прокатного стана.
Широкое промышленное применение этого метода началось около 60 лет тому назад (в России с 1948 г.). В настоящее время прокатку порошков применяют для получения заготовок конструкционных материалов (полосы, ленту и профили), а также для производства фильтров, электрохимических электродов и других пористых изделий.
Прокатка порошка обеспечивает высокую производительность при сравнительно низкой энергоемкости процесса, возможность получения тонких с большой поверхностью заготовок, отличающихся изотропностью свойств и равномерностью плотности. Затраты энергии на прокатку существенно меньше затрат на получение заготовок той же площади, холодным прессованием.
Себестоимость тонкой ленты, прокатанной из порошка, в 2 раза ниже, чем при прокатке слитков. Это объясняется резким сокращением числа операций технологического цикла: исключаются плавка металла, отливка слитков, нагрев их и горячая прокатка. Число проходов при прокатке сокращается в 8–10 раз.
Процесс прокатки порошков существенно отличается от процесса прокатки компактных металлов, хотя и имеет с ним ряд аналогий. Коренным отличием прокатки порошков является изменение свойств прокатанного материала по сравнению со свойствами исходного (переход от сыпучего к жесткому пористому телу).
Различают четыре основных вида прокатки: вертикальную (рис.2.27, а– в), при которой оси прокатных валков расположены в одной горизонтальной плоскости; горизонтальную (рис. 2.27, г, д), при которой оси валков расположены в одной вертикальной плоскости; наклонную (рис. 2.27, е), при которой оси валков расположены в плоскости, наклоненной под углом (обычно 30–60°) к горизонту; радиусную (рис. 2.27, ж, з), когда порошок уплотняется в зазоре между валком и внешним кольцом.
Процессы порошковой металлургии. Курс лекций |
-302- |

II. ФОРМОВАНИЕ И СПЕКАНИЕ ИЗДЕЛИЙ ИЗ МЕТАЛЛИЧЕСКИХ И НЕМЕТАЛЛИЧЕСКИХ ПОРОШКОВ
Лекция 11 Получение изделий методом прокатки порошков
а |
б |
в |
|
|
г |
д |
е |
ж з
Рис. 2.27. Способы прокатки порошка
Силами трения о поверхность валков, вращающихся навстречу один другому, порошок увлекается в зазор между ними и спрессовывается в полосу (ленту, пластину и т.п.) с определенной плотностью и прочностью.
Параметрыпорошков
Важнейшими параметрами прокатки металлических порошков являются центральные углы, определяющие положение некоторых поперечных сечений очага деформации. Очаг деформации ограничен сверху сечением, в котором имеется контакт между порошком и обоими валками, а снизу – сечением выхода проката из зазора между валками.
Выделяют несколько зон и углов, характерных для прокатки порошка
(рис. 2.28):
1-я зона (угол αн может быть> 90°) – зона подачи порошка (определяется толщиной слоя порошка при вертикальной прокатке);
2-я зона (уголα 1) – граничная зона (перед зоной уплотнения порош-
3-я зона (αр ~ 15°) – зона первичного уплотнения порошка α( р - центральный угол, на длине дуги которого под силовым воздействием валков происходит формирование проката из порошка);
4-я зона (уголαп ) – зона спрессовывания (переход порошка от сыпучего состояния к жесткому пористому);
Процессы порошковой металлургии. Курс лекций |
-303- |
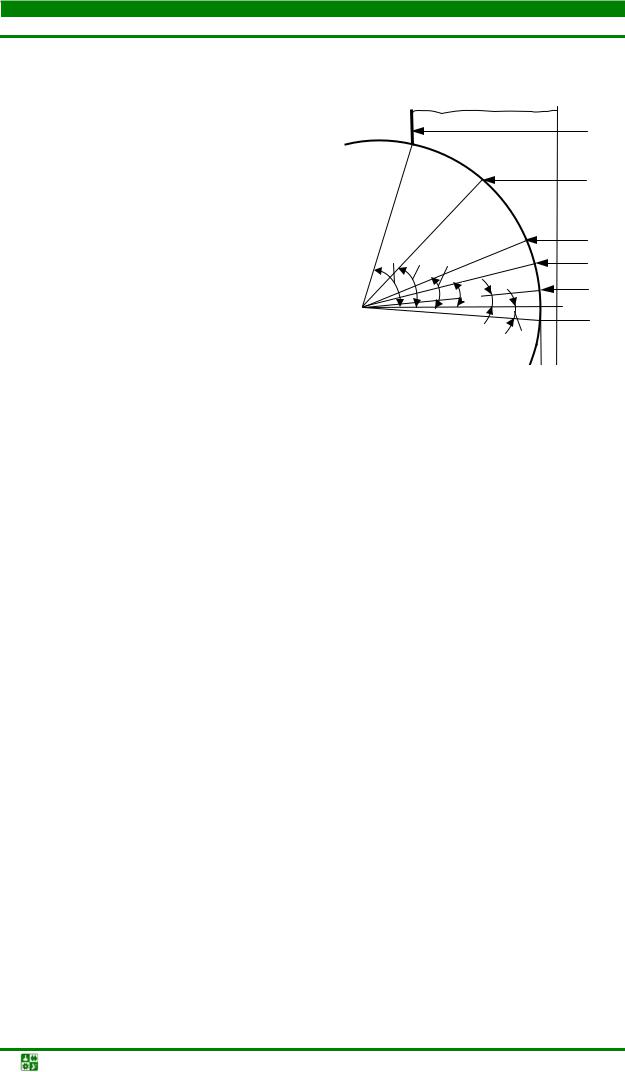
II. ФОРМОВАНИЕ И СПЕКАНИЕ ИЗДЕЛИЙ ИЗ МЕТАЛЛИЧЕСКИХ И НЕМЕТАЛЛИЧЕСКИХ ПОРОШКОВ
Лекция 11 Получение изделий методом прокатки порошков
5-я зона – зона, в которой окружная скорость валков равна скорости движения проката.
|
|
Н |
|
|
|
|
1 |
|
|
|
2 |
αН α1 |
αр |
|
3 |
|
4 |
||
|
|
αп γ |
|
|
|
5 |
|
|
|
|
|
Рис. 2.28. Зоны и угловые параметры про- |
|
|
αсж |
|
|
|
|
катки порошка |
|
|
|
Зоне 5 соответствуют два угла: нейтральный угол γ, определяемый точками нулевого скольжения (чаще всего, не более 1°) и αсж – угол упругого сжатия валков (1–2°), который характеризует увеличение зоны деформации.
Величину углов прокатки определяют: диаметры валков; ширина проката; свойства порошка (форма и размер частиц порошка, насыпная плотность и плотность утряски порошка валков, текучесть порошка); коэффициент внешнего трения (между порошком и поверхностью валков); скорость прокатки; направление прокатки; жесткость рабочей клети стана и др.
В очаге деформации происходит сближение частиц, и порошок уплотняется, т.е. объем исходного порошка в процессе прокатки изменяется, хотя объем, занимаемый собственно частицами деформируемого материала, остается постоянным. Каждая частица порошка обладает свойствами компактного металла и способна при прокатке деформироваться.
Прокатку порошка по ее физической природе можно рассматривать как непрерывное формование, начинающееся в той части очага деформации, которая определяется углом прокатки αр и кончающееся на выходе проката из зазора между валками.
На процесс прокатки большое влияние оказывает сыпучесть порошка: чем она лучше, тем легче вести процесс прокатки. При плохой сыпучести и неправильно выбранной скорости прокатки (линейная скорость поверхности валков существенно больше скорости поступления порошка в очаг деформации) порошок не прокатывается в сплошную заготовку.
Поступление порошка в очаг деформации может быть свободным (гравитационным) и активным. В первом случае порошок поступает в очаг деформации из бункера-питателя на валках под действием собственной мас-
Процессы порошковой металлургии. Курс лекций |
-304- |

II. ФОРМОВАНИЕ И СПЕКАНИЕ ИЗДЕЛИЙ ИЗ МЕТАЛЛИЧЕСКИХ И НЕМЕТАЛЛИЧЕСКИХ ПОРОШКОВ
Лекция 11 Получение изделий методом прокатки порошков
сы, а во втором случае порошок подается принудительно роторным, конвейерным, шнековым и другими питателями.
Прокатка может быть периодической и непрерывной: при периодической прокатке в бункер стана засыпают определенную порцию порошка и получают прокат заданной массы, а при непрерывной прокатке порошок в бункер подают постоянно, получая длинномерную заготовку.
Движение порошка в бункере-питателе подобно движению вязкой жидкости, т.е. отсутствуют какие-либо разрывы непрерывности перемещений и скоростей отдельных частиц порошка, несмотря на значительную неравномерность перемещений его отдельных слоев.
Характер движения порошка в бункере при вертикальной прокатке зависит от отношения толщины подачи порошка Н к диаметру валков D: при Н/D ≤ 0,5 (рис. 2.29, а) горизонтальные слои порошка, опускаясь, изгибаются выпуклостью вверх и затем превращаются в петлю, располагающуюся по центру бункера (скорость движения частиц вблизи рабочей поверхности валков больше, чем в центральной части бункера).
а |
б |
Рис. 2.29. Характер движения слоев порошка при вертикальной прокатке:
а – Н/ D ≤ 0,5; б – H/D ≥ 1
При H/D ≥ 1 (в таких бункерах облегчается наполнение бункера свежими порциями порошка) горизонтальные слои порошка в осевой части бункера по мере понижения уровня порошка изгибаются выпуклостью вниз, а на четверти толщины бункера – выпуклостью вверх (рис. 2.29, б).
При горизонтальной прокатке движение порошка в бункере-питателе отличается от рассмотренного выше для вертикальной прокатки (рис. 2.30). В общем случае при прокатке на порошок действуют два усилия: радиальное усилие, создающее давление прокатки и уплотняющее порошок, и усилие, стремящееся вытолкнуть порошок из очага деформации в направлении продольной оси валков.
Процессы порошковой металлургии. Курс лекций |
-305- |
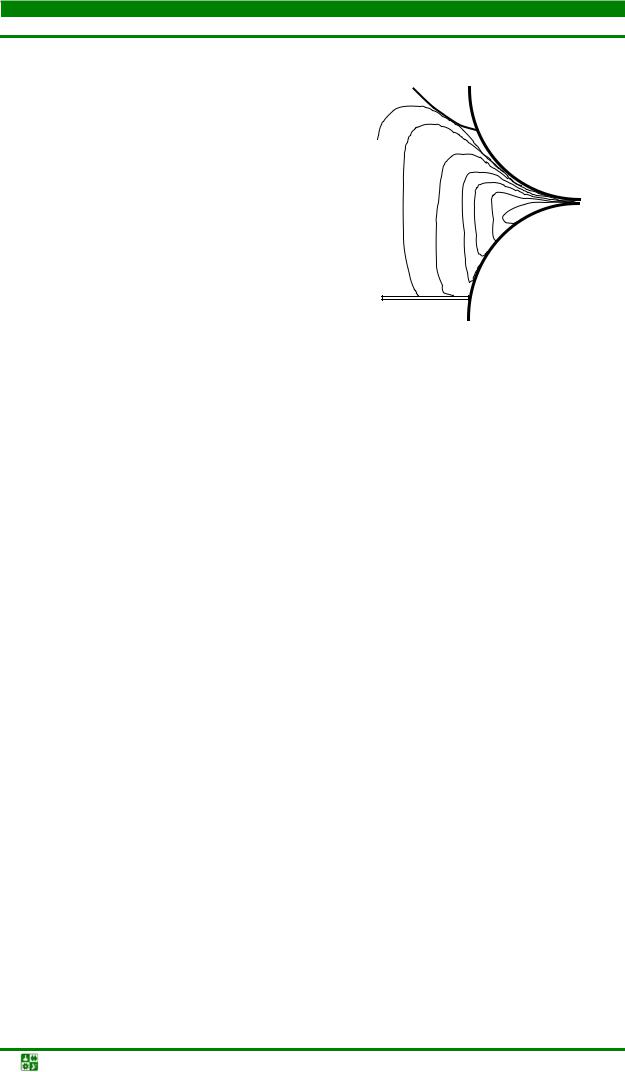
II. ФОРМОВАНИЕ И СПЕКАНИЕ ИЗДЕЛИЙ ИЗ МЕТАЛЛИЧЕСКИХ И НЕМЕТАЛЛИЧЕСКИХ ПОРОШКОВ
Лекция 11 Получение изделий методом прокатки порошков
Рис. 2.30. Движение порошка в бункерепитателе при горизонтальной прокатке
Скорость прокатки обычно составляет от 1–3 до 20–25 м/мин.
Уплотнениепорошковоготелаприпрокатке
В результате прокатки порошок уплотняется от γнас или γутр до плотности проката γп. Отношение γп к этим плотностям порошка называют, соответственно, степенью уплотнения Ζ и коэффициентом уплотнения Ζуп:
Ζ = γп / γнас , |
Ζуп = γп / γутр. |
Уравнение прокатки порошков основано на применении универсального закона постоянства массы, имеющий вид:
γп = γнас(1 + αр прив R/hп),
где αр прив – приведенный или условный угол прокатки порошка при коэффициенте вытяжки λ =1, рассчитываемый по известным γнас и R (радиусу валков) и определяемым экспериментально γп и hп (толщине проката). Коэффициент вытяжки определяется как отношение объема порошка зоны уплотнения αсж к объему порошка в самом начале этой зоны αр.
Рассчитанные значения αр прив для некоторых порошков, которые прокатывали между гладкими шлифованными горизонтально расположенными валками (вертикальная прокатка) без смазки при свободной (гравитационной) подаче, составляют для железного порошка различных марок 8°20'– 9°40', для медного порошка – 10°50', для титанового порошка – 12°20', для порошка карбонильного никеля – 12°40'.
Можно выделить три стадии уплотнения порошка при прокатке, которые (фактически) совпадают со структурной деформацией при прессовании порошка в пресс-форме. Первая стадия уплотнения – перераспределение частиц порошка (удаление арок, проникновение мелких частиц в поры между
Процессы порошковой металлургии. Курс лекций |
-306- |

II. ФОРМОВАНИЕ И СПЕКАНИЕ ИЗДЕЛИЙ ИЗ МЕТАЛЛИЧЕСКИХ И НЕМЕТАЛЛИЧЕСКИХ ПОРОШКОВ
Лекция 11 Получение изделий методом прокатки порошков
крупными); вторая стадия – уменьшение объемов пор за счет увеличения контактных поверхностей; третья стадия – объемная деформация частиц.
Для построения диаграмм уплотняемости порошков при прокатке можно использовать эмпирическое уравнение:
γп = γутр + рmax/(m + npmax), |
(2.26) |
где т, п – коэффициенты, зависящие от материала порошка (табл. 2.5).
Таблица 2.5 Величины коэффициентов т и п для некоторых порошков
Порошок |
т |
п |
|
|
|
Железный марки ПЖВ2.160.23 |
4,56 |
0,165 |
Медный восстановленный |
2,37 |
0,146 |
Никелевый восстановленный |
7,97 |
0,149 |
Алюминиевый распыленный |
3,12 |
0,660 |
Расчеты по уравнению (2.26) хорошо коррелируют с эксперименталь-
ными результатами в широком интервале контактных напряжений.
Видыбракаприпрокатке
Экспериментально установлено, что пористость по толщине порош-
кового проката распределяется неравномерно.
Влентах (полосах) малой толщины (1,6–2,5 мм) пористость непрерывно уменьшается по мере удаления от поверхности к центру сечения; разница между пористостью у поверхности проката и в центре уменьшается с увеличением его средней плотности и уменьшением толщины.
Вболее толстых (> 2,5 мм) полосах в приповерхностных слоях пористость уменьшается по мере удаления от внешней поверхности, а в центральном слое пористость приблизительно постоянна. Это обусловлено, по-видимому, неравномерностью напряженно-деформированного состояния порошкового тела в очаге уплотнения, так как в поверхностных слоях проката обнаружены сравнительно большие остаточные растягивающие напряжения.
Следствием этого является также часто наблюдаемое расслоение проката на две или три (при прокатке толстых полос) части, зарождающееся еще до выхода проката из валков.
Отмечают два вида такого расслоения:
образование гладких поверхностей расслоения, наиболее характерное для крупных частиц порошка и малой плотности проката (исчезает при ее увеличении);
образование бугристых поверхностей расслоения с выходом поперечных трещин на поверхность проката, имеющее место при прокатке дисперсных порошков с размером частиц 2–5 мкм (карбонильный никель) и 5–20 мкм (молибден).
Процессы порошковой металлургии. Курс лекций |
-307- |

II. ФОРМОВАНИЕ И СПЕКАНИЕ ИЗДЕЛИЙ ИЗ МЕТАЛЛИЧЕСКИХ И НЕМЕТАЛЛИЧЕСКИХ ПОРОШКОВ
Лекция 11 Получение изделий методом прокатки порошков
На расслоение проката влияют гранулометрический состав порошка, наличие оксидов на поверхности частиц, форма частиц и их физическое состояние (например, наклеп).
Контрольныевопросыизадания
1.Расскажите о сущности метода получения изделий прокаткой по-
рошков.
2.Назовите преимущества этого метода.
3.Перечислите основные виды прокатки.
4.Охарактеризуйте угловые параметры процесса прокатки порошков.
5.Представьте схемы движения порошка в бункере при горизонтальной и вертикальной прокатке.
6.Напишите основные уравнения прокатки.
7.Каким образом меняется плотность порошкового тела при прокатке?
8.От чего зависит плотность порошкового тела при прокатке?
9.Назовите основные виды брака при прокатке.
Лекция12 Прокаткапорошка. Горячеепрессование
План лекции
1.Схемы подачи порошка при прокатке.
2.Оборудование для прокатки порошков.
3.Горячее прессование.
Схемыподачипорошкаприпрокатке
Плотность проката зависит от химического и гранулометрического состава порошка, формы его частиц, конструкции дозатора порошка, давления порошка на валки, состояния поверхности валков и скорости их вращения, направления прокатки и других факторов.
При прокатке металлических порошков с их гравитационной (свободной) подачей толщина лент практически не превышает 1 % от диаметра валка. Плотность проката уменьшается с увеличением его толщины и уменьшением коэффициента спрессовывания ε.
Плотность проката можно повысить путем увеличения толщины слоя порошка в бункере, а также вакуумированием, принудительной подачей порошка, повышением шероховатости валков и другими способами.
Для получения из порошков ленты заданной пористости и толщины применяют специальные устройства, регулирующие уровень порошка или толщину его захвата в зоне деформации (рис. 2.31).
Процессы порошковой металлургии. Курс лекций |
-308- |

II. ФОРМОВАНИЕ И СПЕКАНИЕ ИЗДЕЛИЙ ИЗ МЕТАЛЛИЧЕСКИХ И НЕМЕТАЛЛИЧЕСКИХ ПОРОШКОВ
Лекция 12 Прокатка порошка. Горячее прессование
а |
б |
в |
г |
|
Рис. 2.31. Схемы устройств для регулирования уровня порошка |
|
вбункере прокатного стана
Всхеме, представленной на рис. 2.31, а порошок изолируется от рабочей поверхности валков с помощью специальных накладок, которые могут
перемещаться; расстояние между накладками определяет толщину захвата порошка. По этой схеме можно в широких пределах регулировать толщину захвата порошка независимо от скорости прокатки. Недостаток схемы заключается в переменном уровне порошка над сечением его захвата, а также в трудности изготовления качественных накладок.
Схемы (рис. 2.31, б, в) предусматривают регулирование уровня порошка в зоне деформации путем изменения ширины щели между передвигающимися или поворотными заслонками и рабочей поверхностью валков. Замена объемной заслонки (рис. 2.31, в) на вертикальную пластинчатую, позволяет получать биметаллический прокат. Уровень порошка поддерживается подбором соотношения между производительностью прокатки и расходом порошка. Недостатками этих схем являются сложность контроля за уровнем порошка в зоне деформации и необходимость увязки ширины щели бункера с порошком со скоростью прокатки.
По схеме, приведенной на рис. 2.31, г, уровень порошка между валками регулируют величиной щели в дне бункера. На практике применяют устройства с механическим регулированием расхода порошка. С помощью используемого в этом устройстве шнека можно постепенно менять расход порошка.
Оборудованиедляпрокаткипорошков
В промышленности, для прокатки порошков в горизонтальном направлении часто используют листовые прокатные станы, оборудованные приспособлениями для принудительной подачи порошка в валки (рис. 2.32). Максимальное давление в камере шнека 0,1 МПа. Давление подпора порошка в очаге деформации создается за счет разности производительности шнека и пропускной способности стана.
Процессы порошковой металлургии. Курс лекций |
-309- |

II. ФОРМОВАНИЕ И СПЕКАНИЕ ИЗДЕЛИЙ ИЗ МЕТАЛЛИЧЕСКИХ И НЕМЕТАЛЛИЧЕСКИХ ПОРОШКОВ
Лекция 12 Прокатка порошка. Горячее прессование
Рис. 2.32. Приспособление для принудительной подачи порошка в валки: 1 – валки; 2 – камера с порошком; 3– шнек; 4 – бункер; 5 – шкив двигателя; 6– клиноременная передача; 7 – двигатель
1 |
|
4 |
|
|
|
6 |
|
|
|
|
|
2 |
3 |
5 |
7 |
|
При расположении продольных осей валков в одной вертикальной плоскости бункер с порошком может быть помещен перед прокатным станом и подача порошка осуществляется по вспомогательной ленте. Возможна также подача порошка под действием собственного веса по наклонному желобу.
Существует схема прокатки порошков через вертикально расположенные валки с конвейерной подачей (рис. 2.33).
Металлический порошок из бункера, установленного на одном конце конвейера, через дозирующее устройство, задающее высоту слоя порошка, подается на ленту конвейера. Нижний валок имеет прижимные ролики, а верхний валок – бортики, между которыми проходят боковые кромки конвейера для металла.
Порошки прокатывают как в холодном, так и в нагретом состоянии. Г.И. Аксенов предложил следующие температурные границы дефор-
маций в зависимости от температуры плавления металла Тпл: область холодной деформации – 0–0,25; область между холодной и горячей деформацией – 0,25–0,5; область горячей деформации – 0,5–1,0.
2 |
3 |
4 |
|
||
|
|
1
5 7
6
8
Рис. 2.33. Схема устройства для подачи порошка в волки с помощью конвейера: 1 – лента конвейера; 2 – бункер с порошком; 3 – дозирующие устройство; 4 – верхний валок с бортиком; 5, 6 – прижимные ролики; 7 – нижний валок; 8 – устройство для натяжения ленты конвейера
Процессы порошковой металлургии. Курс лекций |
-310- |

II. ФОРМОВАНИЕ И СПЕКАНИЕ ИЗДЕЛИЙ ИЗ МЕТАЛЛИЧЕСКИХ И НЕМЕТАЛЛИЧЕСКИХ ПОРОШКОВ
Лекция 12 Прокатка порошка. Горячее прессование
|
|
Пористый прокат |
|
|
|
|
2 |
1 |
|
|
|
1 |
|
4 |
1 |
|
2 |
3 |
|
|
5 |
||
|
|
|
|
|
|
|
|
Беспористый прокат |
|
|
|
|
4 |
6 |
|
|
|
3 |
3 |
1 |
|
|
|
|
|
3 |
|||
|
|
|
|
4 |
|
|
|
|
|
|
|
6 |
7 |
|
6 |
7 |
4 |
|
4 |
4 |
||
|
|
|
Рис. 2.34. Схемы технологических линий для получения проката из металлических порошков: 1 – валки; 2 – камерная печь; 3 – устройства для намотки проката; 4 – проходная печь; 5 – листовой прокат; 6 – валки для уплотняющей прокатки; 7 – водоохлаждаемые валки
При горячей прокатке станы снабжают дополнительными устройствами для нагрева порошка перед процессом прокатки, а сам порошок часто помещают в камеру с защитным газом во избежание окисления при нагреве.
При использовании непрерывной схемы получения ленты из порошка (прокатанная лента сразу поступает в печь для спекания) для защиты ее от окисления, на выходе из печи устанавливают валки для уплотнения и медные водоохлаждаемые валки.
Технологические линии получения проката из металлических порошков, в зависимости от вида получаемой продукции (пористых или беспористых листов и лент), включают такие виды оборудования, как прокатные станы, печи для спекания материала, устройства для правки, намотки и охлаждения лент и полос (рис. 2.34). Беспористые ленты и листы получают из пористой ленты после дополнительной уплотняющей прокатки в холодном или горячем состоянии.
Методом прокатки можно получать многослойный прокат. Для этого различные порошки или порошки и компактный листовой материал прокатывают одновременно.
Прокатку порошков химически активных или особо чистых материалов ведут в вакууме или инертном газе. Кроме того, на практике используют
Процессы порошковой металлургии. Курс лекций |
-311- |

II. ФОРМОВАНИЕ И СПЕКАНИЕ ИЗДЕЛИЙ ИЗ МЕТАЛЛИЧЕСКИХ И НЕМЕТАЛЛИЧЕСКИХ ПОРОШКОВ
Лекция 12 Прокатка порошка. Горячее прессование
горячую прокатку порошка, который помещают в герметичный контейнер (оболочку).
Применение оболочек предупреждает загрязнение порошка кислородом, азотом и другими газами. После прокатки защитную оболочку удаляют с поверхности проката механически или стравливают.
Горячеепрессование
Горячее прессование – прессование металлического порошка или порошковой формовки при температуре, превышающей температуру рекристаллизации основного компонента.
Горячее прессование представляет собой совмещение процессов прессования и спекания и проводится при температурах 0,5–0,95Тпл основного (матричного) компонента порошкового материала. Оно позволяет практически реализовать наблюдаемое при повышении температуры увеличение текучести материала и получать фактически беспористые порошковые изделия.
Одним из первых примеров промышленного применения горячего прессования можно считать технологию платиновых изделий, разработанную П.Г. Соболевским.
Наиболее существенным результатом горячего прессования является максимально быстрое уплотнение порошкового тела и получение заготовок (изделий) с минимальной пористостью при сравнительно малых давлениях прессования.
Изменение плотности порошкового тела при горячем прессовании связано с пластической деформацией, нестационарным и стационарным диффузионным крипом. Силы внешнего давления при горячем прессовании суммируются с капиллярными давлениями, приводящими к развитию межчастичного сцепления и уменьшению пористости порошкового тела. Практически каждой температуре горячего прессования соответствует вполне определенное минимальное давление, при котором может быть получено малопористое (П < 1–2 %) порошковое изделие в течение короткого времени (10–30 мин).
В случае, когда напряжения, возникающие при приложении нагрузки, выше предела текучести прессуемого материала, усадка осуществляется за счет пластической деформации; если эти напряжения ниже предела текучести, уплотнение протекает за счет нестационарного (неотожженные порошки) или близкого к стационарному (отожженные порошки) крипа. Механизм уплотнения идентичен наблюдаемому при спекании: образование межчастичного контакта, рост плотности с одновременным увеличением размера частиц и дальнейший рост частиц при незначительном дополнительном уплотнении.
Свойства горячепрессованных порошковых изделий существенно зависят от условий прессования. Как правило, такие изделия обладают более высоким пределом прочности, большим удлинением, повышенной твердо-
Процессы порошковой металлургии. Курс лекций |
-312- |

II. ФОРМОВАНИЕ И СПЕКАНИЕ ИЗДЕЛИЙ ИЗ МЕТАЛЛИЧЕСКИХ И НЕМЕТАЛЛИЧЕСКИХ ПОРОШКОВ
Лекция 12 Прокатка порошка. Горячее прессование
стью, лучшей электропроводностью и более точными геометрическими размерами, чем изделия, полученные путем раздельного прессования и спекания. Кроме того, подобные изделия отличаются мелкозернистой структурой и нередко по механическим свойствам не уступают изделиям из литых металлов (сплавов).
Для нагрева порошка или порошковой формовки используют, как правило, электрический ток. Различают следующие способы нагрева порошка при горячем прессовании:
прямым пропусканием тока через порошок или пресс-форму; индукционным нагревом порошка, пресс-формы или промежуточного
экрана; импульсным током высокого напряжения.
Наиболее распространенным материалом для изготовления прессформ является графит, в том числе силицированный. Ориентировочный расчет матриц графитовых пресс-форм проводят по нижнему значению справочных данных о прочности графита на растяжение. Практически матрицы из наиболее доступных сортов графита выдерживают максимальное осевое давление порядка 40 МПа, а рабочее давление формования зачастую не превышает 20–25 МПа. Бандажирование графитовых матриц не дает ощутимых результатов, так как при нагреве до высоких температур исчезает необходимое натяжение в соединении металлического бандажа и матрицы (коэффициент линейного расширения металлов и сплавов больше, чем у углеграфитовых материалов).
При сравнительно низких температурах прессования (до 900– 1 000 °С) используют металлические пресс-формы из жаропрочных сплавов, например на основе никеля и молибдена. Постепенно расширяется применение пресс-форм из тугоплавких оксидов, силикатов и других химических соединений. Для предотвращения взаимодействия прессуемого материала с материалом пресс-формы внутреннюю поверхность последней покрывают ка- кими-либо инертными составами (жидким стеклом, эмалью, нитридом бора и др.) или защищают металлической фольгой.
Некоторые из защитных составов могут одновременно играть роль смазок, уменьшающих внешнее трение. Кроме того, для предохранения прессуемого материала от окисления применяют защитные среды (восстановительные, инертные) или вакуумирование.
Важную роль при прессовании играют режимы приложения и снятия нагрузки. Целесообразно сначала нагреть порошок до некоторой температуры (обычно половина требуемой для изотермической выдержки), а затем прикладывать давление и продолжать нагрев, который следует проводить как можно быстрее. В этом случае обеспечивается более полное удаление газов, адсорбированных порошком, что способствует его уплотнению.
Прессы, используемые для горячего прессования, могут быть рычаж- но-механическими (рис. 2.35), гидравлическими или пневматическими.
Процессы порошковой металлургии. Курс лекций |
-313- |
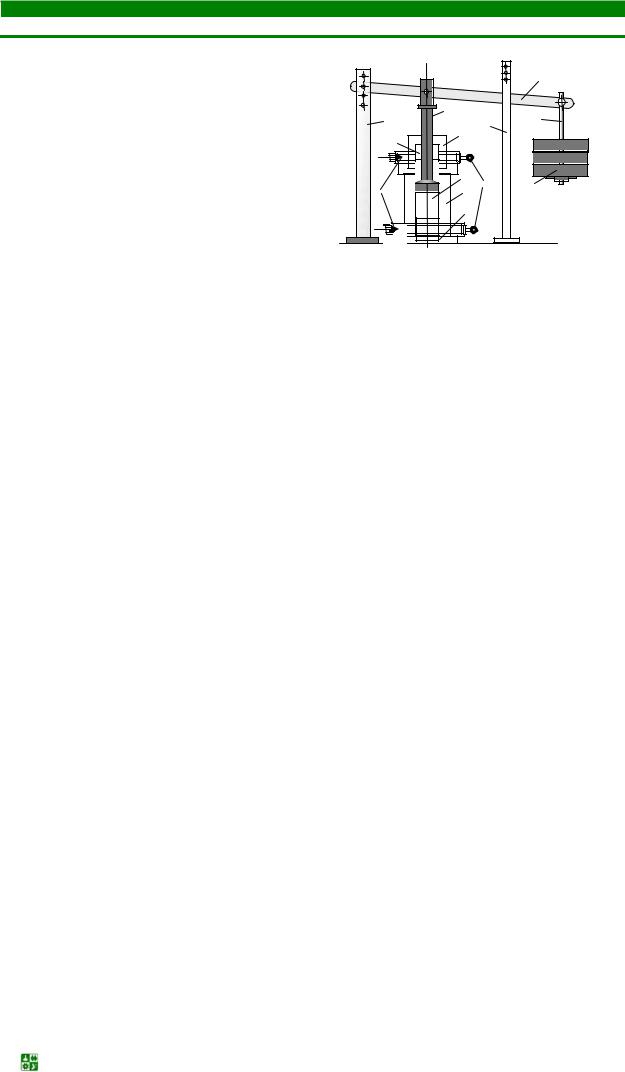
II. ФОРМОВАНИЕ И СПЕКАНИЕ ИЗДЕЛИЙ ИЗ МЕТАЛЛИЧЕСКИХ И НЕМЕТАЛЛИЧЕСКИХ ПОРОШКОВ
Лекция 12 Прокатка порошка. Горячее прессование
Рис. 2.35. Схема рычажно–механического пресса для горячего прессования: 1 – медные водоохлаждаемые контакты; 2 – графитовая пресс–форма; 3 – центральная втулка; 4 – верхний пуансон; 5 – направляющая втулка; 6 – токоподводы; 7 – изолирующая подкладка; 8, 9 – опорные стойки; 10 – рычаг; 11
– прессуемый порошок; 12 – подвеска; 13 – груз
|
|
|
10 |
|
8 |
4 |
9 |
12 |
|
3 |
||||
5 |
|
|||
1 |
1 |
6 |
13 |
|
2 |
|
|||
|
7 |
|
|
Прессуемый порошок помещают в пресс-форму, зажимаемую между двумя медными водоохлаждаемыми контактами; пресс-форма нагревается пропускаемым через нее электрическим током.
Груз, подвешенный к рычагу, передающему усилие на верхний пуансон, создает давление на порошок до 30 МПа.
Для уменьшения потерь тепла излучением пресс-форма защищена теплоизолирующим графитовым экраном (максимальная рабочая температура составляет до 2 700 °С).
В промышленности для горячего прессования широко используют специальные гидропрессы, в которых порошок нагревается переменным электротоком, подводимым через водоохлаждаемые контактные плиты к графитовым конусным пуансонам, между которыми устанавливается прессформа. Такие прессы снабжены блокировкой, предохраняющей детали от расплавления в случае прекращения подачи охлаждающей воды. Развиваемое усилие достигает 1 500 кН, температура прессования – до 2 500 °С (табл. 2.6).
Таблица 2.6
Технические характеристики прессов горячего прессования
Габариты рабочей |
|
Максимальные |
|
|
|
||
камеры, мм |
Диаметр |
Усилие |
Темпера- |
Потребляе- |
Атмосфера в рабочем |
|
|
|
|
прессов- |
прессова- |
мая мощ- |
пространстве |
|
|
Диаметр |
Высота |
ки, мм |
ния, кН |
тура, К |
ность, кВА |
|
|
|
|
|
|
1 573 |
6 |
|
|
140 |
220 |
50 |
100 |
2 073 |
15 |
Окислительная, вос- |
|
2 473 |
25 |
становительная |
|
||||
|
|
|
|
|
|||
|
|
|
|
2 773 |
35 |
|
|
200 |
280 |
80 |
180 |
1 573 |
10 |
Окислительная, вос- |
|
250 |
80 |
180 |
2 473 |
35 |
становительная |
|
|
|
|
||||||
|
|
|
|
1 573 |
40 |
|
|
315 |
315 |
150 |
800 |
2 073 |
70 |
Окислительная, вос- |
|
2 473 |
100 |
становительная |
|
||||
|
|
|
|
|
|||
|
|
|
|
2 773 |
120 |
|
|
400 |
400 |
200 |
1 100 |
1 573 |
60 |
Окислительная, вос- |
|
2 073 |
100 |
становительная |
|
||||
|
|
|
|
|
|||
|
|
|
|
|
|
|
|
|
Процессы порошковой металлургии. Курс лекций |
-314- |
|

II. ФОРМОВАНИЕ И СПЕКАНИЕ ИЗДЕЛИЙ ИЗ МЕТАЛЛИЧЕСКИХ И НЕМЕТАЛЛИЧЕСКИХ ПОРОШКОВ
Лекция 12 Прокатка порошка. Горячее прессование
|
|
|
|
2 473 |
120 |
|
|
|
|
|
|
1 573 |
100 |
Окислительная, вос- |
|
500 |
500 |
250 |
1 500 |
2 073 |
120 |
||
становительная |
|||||||
|
|
|
|
2 473 |
160 |
||
|
|
|
|
|
Пресс-форма с изделием после ее охлаждения до 500–600 °С (гидравлический пресс) или до 150–200 °С (вакуумный пресс) удаляется из пресса, изделие извлекается и зачищается на шлифовальном станке.
С середины 60-х гг. XX в. большое распространение получило динамическое горячее прессование (ДГП): предварительно спрессованные и спеченные при низких температурах (до 0,5–0,6Тпл основного компонента) пористые заготовки допрессовывают при достаточно высокой температуре.
Все факторы, облегчающие пластическое деформирование, способствуют уплотнению заготовок при ДГП. На процесс уплотнения влияют температура ДГП, характер и величина действующих напряжений, продолжительность их действия, скорость приложения нагрузки и схема напряженного состояния. Качество поверхности изготавливаемых методом ДГП порошковых изделий определяется качеством рабочих поверхностей матрицы и пуансонов, наличием и видом применяемой смазки, выбранной схемой прессования и выталкивания; можно получать изделия с чистотой поверхности 7–8 класса.
Особым случаем горячего прессования является электроразрядное или электроимпульсное (искровое) спекание: через порошок с помощью электро- дов-пуансонов, к которым приложено давление, пропускают сильный электрический разряд (рис. 2.36).
1 |
|
6 |
7 |
|
2 |
|
|
8 |
|
|
|
4 |
||
|
|
|
||
|
|
3 |
+ |
|
|
14 |
|
||
13 |
5 |
9 |
||
|
||||
|
|
|
12 |
11
10
Рис. 2.36. Схема установки электроразрядного спекания с электромагнитным измерителем-дозатором засыпаемого порошка: 1 – устройство для создания механического давления; 2, 12 – электроды-пуансоны; 3 – трубопровод; 4, 5 – измерительные электроды; 6 – порошок; 7 – бункер; 8 – источник питания электроцепи; 9 – устройство для съема сигналов от электродов4, 5; 10 – усилитель; 11
Процессы порошковой металлургии. Курс лекций |
-315- |

II. ФОРМОВАНИЕ И СПЕКАНИЕ ИЗДЕЛИЙ ИЗ МЕТАЛЛИЧЕСКИХ И НЕМЕТАЛЛИЧЕСКИХ ПОРОШКОВ
Лекция 12 Прокатка порошка. Горячее прессование
– источник тока спекания; 13 – матрица пресс-формы; 14 – рабочая полость матрицы
При этом наряду с движущими силами, характерными для обычного спекания и горячего прессования, действуют электромеханические силы и проявляются эффекты, порождаемые током.
В зависимости от электросопротивления прессуемого материала, массы прилегающего к контакту вещества, его теплоемкости и теплопроводности, а также силы проходящего через данный контакт тока, приконтактное вещество (металл, сплав или металлоподобное соединение) может оставаться в твердом состоянии или частично расплавиться; возможны даже частичный переход его в газовую фазу или превращение в плазму. Массоперенос в порошковом теле при прохождении через него импульсного электротока резко возрастает.
Процесс электроразрядного спекания включает, как правило, две стадии. Первая стадия (искровая) включает пропускание электрического тока плотностью несколько ампер на квадратный сантиметр через слабоспрессованный (давление < 10 МПа) порошок. На многих межчастичных контактах возникает искрение, сопровождающееся разрушением поверхностных оксидных пленок, и создаются предпосылки для припекания частиц одна к другой.
Вторая стадия протекает при плотности тока порядка нескольких килоампер на квадратный сантиметр и под более высоким давлением, чем первая стадия (однако это повышенное давление в конце процесса в 10–20 раз ниже давления при холодном прессовании). Температура достигает максимального значения в конце периода повышенного давления. После этого ток отключают, давление медленно понижают в течение периода охлаждения порошковой заготовки.
Контрольныевопросыизадания
1.Какие факторы процесса прокатки определяют плотность проката?
2.Перечислите основные схемы и устройства для дозирования подачи порошка в валки.
3.Назовите схемы подачи порошка в валки при горизонтальной про-
катке.
4.Назовите основные виды оборудования, использующегося при прокатке порошков.
5.Опишите виды технологических линий прокатки.
6.Что представляет собой горячее прессование порошковых тел?
7.Какие процессы совмещаются при горячем прессовании материалов?
8.Укажите достоинства и недостатки метода горячего прессования.
9.Из каких материалов изготовляют формы для горячего прессования порошков?
10.В чем состоит суть метода электроразрядного спекания порошков?
Процессы порошковой металлургии. Курс лекций |
-316- |