
- •Оглавление
- •ВВЕДЕНИЕ
- •I. ПОЛУЧЕНИЕ ПОРОШКОВ
- •Лекция 16 Восстановление химических соединений металлов из растворов солей и газообразных соединений металлов
- •II. ФОРМОВАНИЕ И СПЕКАНИЕ ИЗДЕЛИЙ ИЗ МЕТАЛЛИЧЕСКИХ И НЕМЕТАЛЛИЧЕСКИХ ПОРОШКОВ
- •Введение
- •Лекция 13 Твердофазное спекание материалов
- •Лекция 20 Жидкофазное спекание и инфильтрация порошковых формовок. Брак при спекании
- •Лекция 25 Методы определения механических характеристик порошковых тел. Заключение
- •ЗАКЛЮЧЕНИЕ
- •БИБЛИОГРАФИЧЕСКИЙ СПИСОК
- •ПРИЛОЖЕНИЯ

I. ПОЛУЧЕНИЕ ПОРОШКОВ
Лекция 16 Восстановление химических соединений металлов из растворов солей и газообразных соединений металлов
Лекция16 Восстановлениехимическихсоединенийметаллов
израстворовсолейигазообразныхсоединенийметаллов
План лекции
1.Получение порошков автоклавным способом.
2.Получение порошков цементацией растворов солей.
3.Получение порошков в кипящем слое.
4.Получение порошков в плазме.
Получениепорошковавтоклавнымспособом
Автоклавная технология используется для производства порошков никеля, меди и кобальта. Соответствующий металл, вытесняемый в растворе из его соединения водородом под давлением, осаждается в виде твердых частиц на дно камеры реактора.
Исходное сырье (рудные концентраты, например, никель-кобальтовый, медно-цинковый, медно-свинцово-цинковый, медно-цинковый скрап или отходы металлообработки) подвергают обработке серной кислотой или окислительному аммиачно-карбонатному выщелачиванию, которое часто проводят при повышенном давлении в автоклавах.
Полученный раствор сульфата или комплексной аммиачной соли металла очищают отпримесей и подают в автоклав на восстановление водородом.
Возможность вытеснения и восстановления ионов металлов водородом из водных растворов была установлена Н.Н. Бекетовым в 1960-х гг.
Реакция восстановления катиона металла
МеZ+ + (z/2) Н2 = Ме0 + zН+ |
(1.59) |
возможна, если потенциал водорода ϕH2 меньше (электроотрицательнее), чем
электродный потенциал металла ϕMe.
В момент равновесия ϕH2 становится равным ϕMe, накапливание массы
образующегося в автоклаве осадка металла прекращается.
Водород переходит в раствор, содержащий катионы МеZ+, по реакции ионизации 0,5Н2 = Н+ + e.
Cдвигать потенциал водорода в отрицательную сторону можно, повышая рН и (или) увеличивая давление водорода в автоклаве; более эффективно изменять рН, повышение которого на единицу эквивалентно изменению давления водорода в 100 раз.
Для металлического электрода
Процессы порошковой металлургии. Курс лекций |
-117- |

I. ПОЛУЧЕНИЕ ПОРОШКОВ
Лекция 16 Восстановление химических соединений металлов из растворов солей и газообразных соединений металлов
lg aMeZ+ = –zpH – (z/2) lg pH – zF ϕ0Me / 2,3RT, |
(1.60) |
2 |
|
где aMeZ+ – активность (концентрация) ионов металла; pH2 – парциальное дав-
ление водорода, что позволяет рассчитать минимальную (равновесную) концентрацию катионов металла в конце процесса восстановления в зависимости от рН раствора при данном давлении водорода; F – число Фарадея.
Известно, что в сильно кислых средах полностью осадить из растворов можно достаточно электроположительные металлы (например, Ag, Cu). Для полного выделения металлов со значениями потенциала, лишь ненамно-
го более положительными по сравнению с ϕH2, необходимо поддерживать
определенный уровень рН, нейтрализуя образующуюся при восстановлении кислоту щелочью.
С увеличением давления водорода несколько снижаются значения рН, при которых возможно сравнительно полное выделение металла из раствора его соли. Для снижения потенциала водорода до нужных отрицательных значений и предотвращения выпадения гидроксидов металлов восстановление целесообразно проводить в аммиачных растворах. Несмотря на то, что концентрация свободных ионов металла в растворе при этом низкая (NH3 – сильный комплексообразующий лиганд) и ϕMe сдвигается в электроотрицательную сторону, восстановление водородом возможно, если потенциал металла остается более положительным, чем потенциал водорода в аммиачной среде.
При восстановлении водородом из аммиачных растворов необходимо поддерживать оптимальными соотношение концентраций NH3 и Ме, рН раствора и давление водорода.
Термодинамические расчеты показывают, что многие металлы, в том числе Сu, Ni и Со, могут быть осаждены восстановлением водородом из растворов при 25 °С и давлении водорода 0,1 МПа.
Однако практическое получение порошка в этих условиях невозможно из-за низкой скорости осаждения металла. В общем случае первой стадией рассматриваемого процесса восстановления является образование зародыша твердой фазы, которое может быть как гомогенным (т.е. самопроизвольным без наличия в растворе посторонних твердых включений), так и гетерогенным (т.е. на зародышах, уже имеющихся в растворе, которыми могут быть не только специально вводимые частицы, но и твердые примеси или даже ионы). Большей частью гомогенное образование зародышей не реализуется вследствие энергетических затруднений, связанных с высокой энергией диссоциации молекулы водорода.
Энергия активации реакций восстановления водородом существенно снижается в присутствии твердых катализаторов (коллоидного графита, некоторых оксидов), и осуществляется гетерогенное зародышеобразование. Иногда вначале происходит медленное гомогенное зародышеобразование, а затем скорость выделения металла из раствора быстро возрастает вследствие
Процессы порошковой металлургии. Курс лекций |
-118- |

I. ПОЛУЧЕНИЕ ПОРОШКОВ
Лекция 16 Восстановление химических соединений металлов из растворов солей и газообразных соединений металлов
его кристаллизации на возникших зародышах твердой фазы; в этом случае процесс зародышеобразования носит автокаталитический характер.
Получение порошков меди. Медь может быть выделена восстановлением водородом как из кислых, так и щелочных растворов. На практике в качестве исходного используют раствор сульфата меди или медно-аммиачной комплексной соли.
Восстановление проводят при суммарном давлении газа в автоклаве 2,4–3,5 или 3,5–4,5 МПа (в том числеpH2 до 1,5–2,5 МПа) и температуре 140–170
или 180–200 °С соответственно. Извлечение меди в осадок составляет около 99 %. Скорость процесса восстановления возрастает с увеличением количества суспендированной меди, тогда как наблюдается и непрерывное образование новых зародышей, т.е. реализуется и гетерогенный, и гомогенный механизмы зародышеобразования.
Для восстановления применяют горизонтальные автоклавы с паровой рубашкой и несколькими вертикальными мешалками; производительность одного автоклава составляет около 3 тыс. т порошка в год.
Получаемые порошки меди имеют насыпную плотность от 0,5 до 3,8 г/см3, причем размер их частиц можно регулировать в пределах от 2–3 до 15–20 мкм, вводя в раствор в автоклаве либо некоторое количество мелкого порошка меди, либо частицы полиакриламида (0,1–0,5 г на 1 л раствора).
После завершения процесса восстановления пульпу из автоклава перекачивают через дроссель, сбрасывающий давление, в реактор, где раствор «вскипает», выделяя растворенный газ; затем пульпу перекачивают через фильтр и промывной аппарат в реактор для обработки мыльным раствором и в камеру сушки.
Себестоимость примерно вдвое меньше себестоимости электролитических порошков меди. Форма частиц самая разнообразная – дендритная, округлая, губчатая и др.
Получение порошков никеля и кобальта. Полное выделение никеля и ко-
бальта возможно лишь при рН > 4, в связи с чем водородное восстановление ведут из растворов, содержащих аммиачные комплексы Ni(NН3)22+ или Со(NH3)22+ и (NH4)2SO4 (для предотвращения гидролиза аммиакатов). Гомогенное зародышеобразование протекает весьма медленно, поэтому прибегают к гетерогенному, вводя в раствор затравку (мелкиепорошки никеля или кобальта).
При восстановлении осуществляются следующие стадии этого процесса:
1)растворение водорода в водном растворе (быстрая стадия);
2)транспорт водорода к поверхности твердой частички затравки (зависит от интенсивности перемешивания);
3)активированная адсорбция водорода на поверхности частички ме- талла-затравки (быстрая стадия);
4)реакция восстановления сорбированных комплексных ионов металла водородом на поверхности твердой частички затравки (медленная стадия);
5)отвод растворимых продуктов реакции в объем раствора (быстрая
стадия).
Процессы порошковой металлургии. Курс лекций |
-119- |

I. ПОЛУЧЕНИЕ ПОРОШКОВ
Лекция 16 Восстановление химических соединений металлов из растворов солей и газообразных соединений металлов
Реакцию восстановления катионов указанных металлов водородом проводят при 180–200 °С и давлении водорода 2,5–3,5 МПа в автоклавах аналогично получению порошка меди.
При рН 2,5 возможно селективное осаждение никеля до его содержания около 0,2 г/л в присутствии ≤ 10 г/л Со.
Автоклавные порошки никеля содержат, %: 99,7–99,9 Ni; 0,1–0,2 Со; а порошки кобальта – 99,5–99,8 Со; 0,1–0,5 Ni.
Получениепорошковцементациейрастворовсолей
Цементация – электрохимический процесс, который часто называют контактным восстановлением или внутренним электролизом. По своей сути процесс сходен с гальваническим процессом: металл с более отрицательным потенциалом вытесняет из раствора металл с более положительным потенциалом, переходя при этом в раствор.
Электрохимическую реакцию между металлом-цементатором и ионами вытесняемого металла в общем виде можно записать следующим образом:
Z MeZ1+ + Z Me0 |
→ Z |
Me0 |
+Z MeZ 2+ , |
(1.61) |
||||
2 |
1 |
1 |
1 |
2 |
1 |
1 |
2 |
|
где Z1, Z2 – заряды ионов или валентности вытесняемого металла и металлацементатора.
Для прохождения подобной реакции слева направо вытесняющий металл должен иметь более отрицательный, нежели у вытесняемого металла, электродный потенциал.
Рассматривая стандартные электродные потенциалы и равновесные соотношения активностей (концентраций) катионов в растворах (табл. 1.6), можно установить, что некоторые металлы можно сравнительно легко выделить из раствора, подбирая соответствующий металл-цементатор.
Таблица 1.6
Стандартные электродные потенциалы и равновесные соотношения активностей катионов для некоторых пар двухвалентных металлов
|
Металл |
|
φ0, В |
AMeА Z 1+ / |
MeZ 2+ |
|
Ме2 |
|
Ме1 |
Ме2 |
Ме1 |
||
|
1 |
2 |
||||
|
|
|
|
|
||
|
|
|
|
|
|
|
Zn |
|
Cu |
–0,763 |
+0,320 |
1,0·10 −33 |
|
Fe |
|
Cu |
–0,440 |
+0,340 |
1,3·10 −27 |
|
Ni |
|
Cu |
–0,230 |
+0,340 |
2,0·10 −20 |
|
Zn |
|
Ni |
–0,763 |
+0,230 |
5,0·10 −19 |
|
Cu |
|
Hq |
+0,340 |
+0,798 |
1,6·10 −16 |
Процессы порошковой металлургии. Курс лекций |
-120- |

I. ПОЛУЧЕНИЕ ПОРОШКОВ
Лекция 16 Восстановление химических соединений металлов из растворов солей и газообразных соединений металлов
Zn |
Cd |
–0,796 |
–0,402 |
3,2·10 |
Zn |
Fe |
–0,796 |
–0,440 |
8,0·10 |
−13
−12
Однако при этом необходимо учитывать и кинетику процесса, в связи с которой термодинамическое равновесие может не достигаться. В результате связывания металлических ионов в комплексы понижается их концентрация в свободном виде, и электродный потенциал осаждающегося металла сдвигается в отрицательную сторону.
Растворение и осаждение металла из раствора регулируется двумя противоположно действующими факторами: электролитической упруго-
стью растворения и осмотическим давлением ионов раствора. Разность этих двух величин определяет значение и величину стандартного электродного потенциала.
При погружении в раствор с ионами вытесняемого металла одни из участков металла-цементатора становятся катодами и на них идет выделение осаждаемого металла, а другие – анодами, где протекает процесс ионизации.
Это связано с различием в уровнях энергии атомов, находящихся на поверхности металла-цементатора. Катодные участки возникают на местах поверхности с наиболее высоким электродным потенциалом. Так как катодные и анодные участки соединены, электроны от анодных участков перетекают к катодным. На рис. 1.26 представлены схема процесса цементации и зависимость скорости цементации V от времени t.
MeZ1+ +z e →Me |
V |
|
||
1 1 |
1 |
|
||
|
|
Me2 − z2e → Me2Z 2+ |
|
|
|
|
|
||
Me1 |
|
|
||
е |
Me2 |
|
||
|
|
|
|
t |
|
а |
|
б |
Рис. 1.26. Схема процесса цементации (а) и зависимость скорости цементации от времени (б)
Процесс цементации металла из его раствора определяется двумя последовательными процессами:
1)доставкой ионов вытесняемого металла к катодной поверхности металла-цементатора через двойной и диффузионный слой;
2)электрохимическим превращением на границе электрод–раствор, протекающим через несколько промежуточных стадий (дегидратацию иона, его сорбцию, разряд иона на металле-цементаторе с образованием атома металла и пр.).
Процессы порошковой металлургии. Курс лекций |
-121- |

I. ПОЛУЧЕНИЕ ПОРОШКОВ
Лекция 16 Восстановление химических соединений металлов из растворов солей и газообразных соединений металлов
Скорость реакции замещения зависит от разницы электродных потенциалов: чем она больше, тем выше скорость цементации. Однако существует ряд других факторов, оказывающих влияние на результат реакции:
1.Цементирующий материал должен образовывать растворимое соединение с анионом, который связан с замещаемым металлом.
2.Металл-цементатор должен находиться в избытке. Это обусловлено тем, что реакция замещения проходит на поверхности, и чем больше эта п о- верхность, тем скорее и полнее протекает реакция.
3.В процессе реакции поверхность металла-цементатора может покрываться выделяемым из раствора металлом, вследствие чего она становится инертной. Поэтому раствор должен циркулировать. В некоторых случаях раствор подвергают действию ультразвука.
4.Повышение температуры не только улучшает условия диффузии, но
иснижает энергию активации реакции.
Аппаратурное оформление процесса. В настоящее время процесс кон-
тактного восстановления осуществляется двумя способами: 1) перемешиванием раствора с цементируемым порошком; 2) просачиванием раствора через слой цементирующего порошка.
В основе этих способов заложен принцип полного противотока. Второй способ получения порошков в большей степени соответствует этому принципу. В этом случае наиболее концентрированный раствор взаимодействует с наиболее отработанной частью порошка и таким образом повышается степень использования цементатора. Однако при этом способе трудно добиться равномерного просачивания раствора через слой порошка.
Способ перемешивания более доступен для механизации и автоматизации процессов.
Получениепорошковвкипящемслое
Порошки металлов высокой чистоты можно получить из низкокипящих хлоридов и фторидов вольфрама, молибдена, рения, ниобия или тантала по реакции
МеГх + 0,5хН2 = Ме + хНГ, |
(1.62) |
где Г – хлор или фтор.
Значения константы равновесия реакции и ее зависимость от температуры можно вычислить из термодинамических параметров реакции; при проведении расчетов необходимо уточнить, из какого именно галогенида (высшего или какого-либо из низших) непосредственно получают металл.
Восстановление газообразных хлоридов или фторидов в кипящем слое проводят на специальных установках, в нижней части реактора которых рас-
Процессы порошковой металлургии. Курс лекций |
-122- |
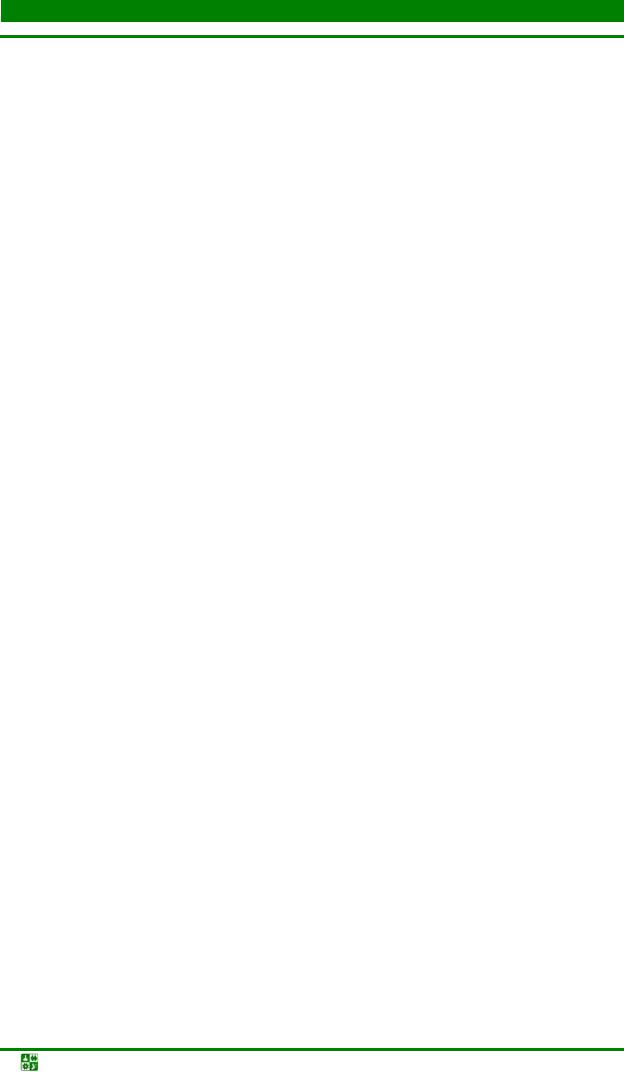
I. ПОЛУЧЕНИЕ ПОРОШКОВ
Лекция 16 Восстановление химических соединений металлов из растворов солей и газообразных соединений металлов
положены металлическая сетка из материала, стойкого к реагентам, или слой мелких осколков (размером 3–5 мм) данного тугоплавкого металла, или пористая подина, спеченная из крупного порошка металла. На пористую подину через вводную трубку подают в виде «затравки» мелкий порошок металла, который предварительно получают, например, измельчением крупного порошка в вихревой мельнице. Под подину вводят водород или смесь водорода
синертным газом с линейной скоростью газового потока, необходимой для приведения порошка в псевдосжиженное состояние (например, 5–10 см/с и
выше в зависимости от соотношения Аr : Н2 в газе, плотности восстанавливаемого металла и задаваемой предельной крупности его частиц).
После этого реактор разогревают до нужной температуры. Можно нагревать и смесь аргона с водородом. Из испарителя в нижнюю часть реактора подают пары галогенида металла. Скорость их подачи регулируют пропусканием смеси аргона с водородом через испаритель. В ряде аппаратов подачу паров хлорида из испарителя в реактор осуществляют током аргона. Образующийся хлористый (или фтористый) водород улавливается в адсорбере, отходящая смесь водорода и аргона поступает в осушитель и затем проходит через нагретую титановую губку, которая поглощает водород. Аргон возвращается в систему.
Насыщенную водородом титановую губку периодически дегидрируют
свыделением чистого водорода. Таким образом, обеспечивают регенерацию
ииспользование всех отходящих газов.
Через патрубок в нижней части реактора образующиеся крупнозернистые металлические порошки периодически или непрерывно выгружают.
Температуру в испарителе устанавливают в соответствии с температурной зависимостью давления паров данного галогенида. Температуру восстановления пентахлорида молибдена (температура плавления 194 °С, а к и- пения 268 °С) поддерживают равной 200–300 °С, так как при более высокой температуре происходит заметная термическая диссоциация хлорида с образованием низших хлоридов при небольшом давлении его паров. Гексахлорид вольфрама (температура плавления 281,5 °С, а кипения 348 °С) испаряют при 300–350 °С. Удобно работать с гексафторидом вольфрама (температура плавления 3 °С, а кипения 17,1 °С), находящимся в баллоне-испарителе в жидком состоянии.
При восстановлении соединений вольфрама и молибдена обычно используют порошки крупностью 20–60 мкм. Более мелкие порошки (2–3 мкм) непригодны, так как их трудно перевести в псевдосжиженное состояние из-за уноса потоком газа. Реакция восстановления может проходить на поверхности частиц, а также в объеме реактора, заполненном газом. Энергия активации взаимодействия веществ в адсорбированном состоянии на поверхности твердых частиц меньше, чем в газовой фазе, в связи с чем на степень осаждения металла на частицы порошка должна сильно влиять температура.
При восстановлении вольфрама из его гексахлорида при 750–800 °С общая степень восстановления достигает 98–99 %, а степень осаждения на
Процессы порошковой металлургии. Курс лекций |
-123- |

I. ПОЛУЧЕНИЕ ПОРОШКОВ
Лекция 16 Восстановление химических соединений металлов из растворов солей и газообразных соединений металлов
порошок – 96–97 %. Небольшая часть мелких кристаллов вольфрама выносится с отходящими газами.
При повышении температуры процесса до 900 °С прекращается «кипение» частиц вольфрама, что объясняется развивающимся процессом спекания частиц. Оптимальные соотношения компонентов парогазовой смеси, обеспечивающие максимальный выход вольфрама в порошок, составляют Н2 : WCl6 = 30–40, Н2 : Аr = 1,75. Содержание кислорода в получаемом порошке вольфрама < 0,01 %.
Пары гексафторида вольфрама восстанавливают в кипящем слое порошка вольфрама с начальным размером частиц 10–50 мкм при 550–600 °С. При молярном отношении в парогазовой смеси Н2 : WCl6 = 15–18 (в 5–6 раз больше теоретически необходимого) обеспечивается практически полное восстановление вольфрама. Для поддержания псевдосжиженного состояния порошка вплоть до образования частиц размером 400–500 мкм необходимо дополнительно подавать аргон. Порошок получается в виде плотных и гладких сферических частиц вольфрама с содержанием примесей менее 0,01 %.
При восстановлении пентахлорида молибдена при температуре 550–600 °С достигается общая степень восстановления до 98 %. При температуре выше 600 °С происходит частичное спекание порошков, а при температуре 780–800 °С «кипение» порошка прекращается. Молекулярное соот-
ношение Н2 : MoCl5 ≥ 30.
Получениепорошковвплазме
Плазма – нейтральный газ, содержащий значительное количество положительных и отрицательных ионов и свободных электронов. Для создания плазмы необходим постоянный подвод энергии, обеспечивающий постоянное образование новых ионов. Это позволяет компенсировать рекомбинацию ионов, которая приводит к образованию нейтрального атома. Благодаря строению энергетических уровней для получения плазмы особенно подходит аргон, обладающий химической инертностью.
Плазмохимические методы объединяют возможности быстрого протекания процессов восстановления и закалки продуктов реакции. Они применяются для получения высокодисперсных порошков металлов или их соединений (карбидов, нитридов и др.).
В качестве восстановителя используют водород, углеводороды или конвертированный природный газ, который получают плазменной конверсией углеводородного сырья.
Низкотемпературную (4 000–10 000 °С) плазму создают путем электродугового разряда высокой интенсивности в среде газа (азот, аргон) или смеси газов.
Высокотемпературную плазму (до нескольких сот тысяч градусов) можно создать путем передачи газу энергии высокочастотного переменного тока посредством магнитной индукции (индуктивно связанная плазма).
Процессы порошковой металлургии. Курс лекций |
-124- |
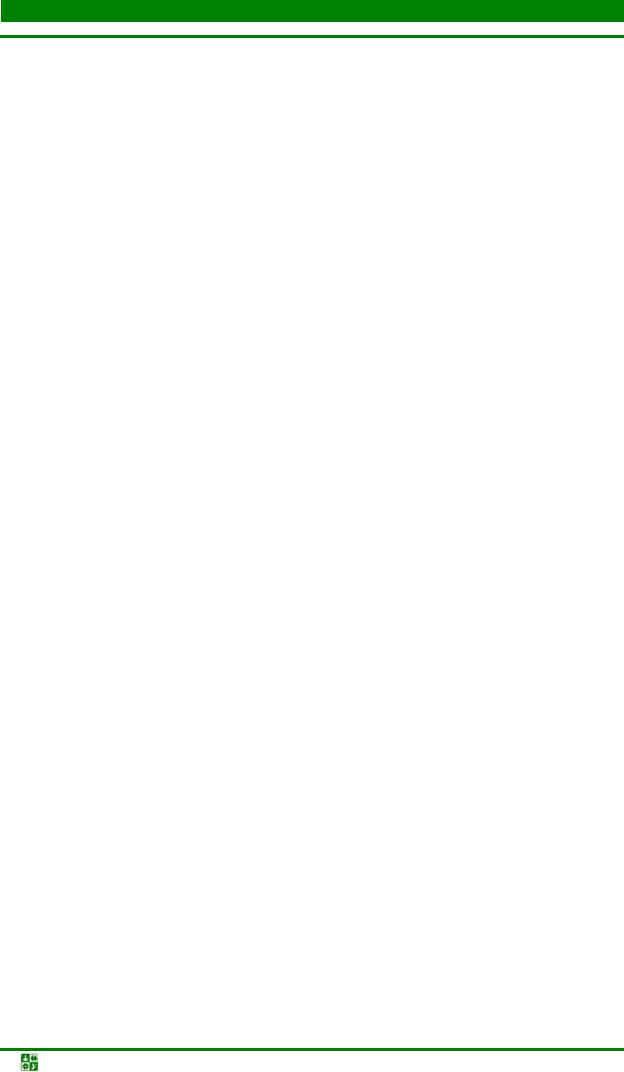
I. ПОЛУЧЕНИЕ ПОРОШКОВ
Лекция 16 Восстановление химических соединений металлов из растворов солей и газообразных соединений металлов
Процесс плазмохимического восстановления и образования целевого продукта в виде частиц дисперсной фазы протекает через ряд сложных физи- ко-химических процессов:
диссоциация исходного соединения с образованием атомарного пара; химическое взаимодействие паров исходного материала с компонентами плазмы (температура плазмы всегда существенно больше температуры
его кипения) с образованием целевого продукта в парообразном состоянии; конденсация и коагуляция парообразного продукта реакции, которые
приводят к образованию ультрадисперсных частиц твердой фазы; кристаллизация, рост частиц и их последующее полиморфное пре-
вращение.
Все эти процессы протекают с очень высокой скоростью и зачастую перекрываются во времени.
Получение порошков вольфрама. Плазмохимическое восстановление кислородных соединений или аммонийных солей вольфрама с получением металлического порошка можно осуществить водородом или продуктами конверсии углеводородов. Так, обрабатывая WО3 в аргоно-водородной плазме при температуре 4 000–5 000 °С, получают порошки вольфрама со средним размером частиц около 0,05 мкм и удельной поверхностью 6–8 м2/г.
При использовании конвертированного газа можно полностью восстановить оксид вольфрама до металла при температуре 4 000–5 000 °С (избыток восстановителя не ниже двукратного).
Для пассивации образующихся высокодисперсных порошков вольфрама, их рафинирования (удаления оксидов, повторно образующихся при охлаждении порошка) и улучшения технологических свойств применяют отжиг порошка в атмосфере осушенного водорода (700–1 000 °С).
Получение порошков никеля. Восстановление оксида никеля проводят в струе плазмы, образованной смесью аргон–водород или аргон–оксид углерода.
Необходимая температура процесса поддерживается за счет регулирования подачи аргона, а восстановитель подают в количестве, близком к стехиометрическому (чтобы избежать его влияния на теплообмен между плазмообразующим газом и частицами восстанавливаемого соединения). Реакция восстановления происходит в объеме струи и лимитируется диссоциацией NiO и, следовательно, скоростью прогрева частиц в реакционном объеме.
Контрольныевопросыизадания
1.Перечислите факторы, определяющие процесс получения порошков из растворов автоклавным методом.
2.Какие растворы используют в автоклавном способе для получения порошков?
3.Порошки каких металлов получают автоклавным способом?
4.На чем основан метод цементации?
Процессы порошковой металлургии. Курс лекций |
-125- |

I. ПОЛУЧЕНИЕ ПОРОШКОВ
Лекция 16 Восстановление химических соединений металлов из растворов солей и газообразных соединений металлов
5.Перечислите факторы, определяющие процесс получения порошков методом цементации.
6.Какие соединения металлов используют при получении порошков методом кипящего слоя?
7.Перечислите основные операции технологии получения порошков в кипящем слое.
8.Что такое плазма?
9.Какие процессы протекают при плазмохимическом восстановлении соединений металлов?
10.Какие восстановители используются при получении порошков в
плазме?
Лекция17 Общиезакономерностипроцессов
производствапорошковэлектролизом
План лекции
1.Общие закономерности процесса электролиза.
2.Факторы, определяющие свойства порошков.
3.Классификация электролитических порошков.
Общиезакономерностипроцессаэлектролиза
Электролитический металлический порошок – это металлический по-
рошок, полученный электролизом растворов или расплавов соединений металлов.
Электролиз представляет собой своеобразный процесс восстановления, осуществляемый не с помощью восстановителей, а за счет использования энергии электрического тока. К преимуществам этого процесса относят универсальность, высокую чистоту получаемых металлических порошков и их хорошие технологические свойства. Недостатки электролиза – большая энергоемкость, низкая производительность, необходимость утилизации большого количества жидких отходов производства.
Электролитическое получение порошков заключается в разложении водных растворов соединений выделяемого металла или его бескислородных расплавленных солей при пропускании через них постоянного электрического тока и последующей разрядке соответствующих ионов металла на катоде.
Используемые при электролизе растворы или расплавы солей называют электролитами и относят к проводникам второго рода.
Сам процесс электрохимического превращения происходит на границе электрод (анод или катод) – электролит (раствор или расплав). Источник
Процессы порошковой металлургии. Курс лекций |
-126- |

I. ПОЛУЧЕНИЕ ПОРОШКОВ
Лекция 17 Общие закономерности процессов производства порошков электролизом
электрического тока играет роль своеобразного «насоса», перекачивающего ионы с одного полюса электроцепи на другой.
Источником ионов выделяемого металла служат, как правило, анод и/или электролит, в составе которого находится растворимое (расплавленное) соединение соответствующего металла. В случае, когда используют нерастворимые аноды, источником выделяемого металла является только электролит.
Ионы в электролите в отсутствие электрического поля движутся хаотично. При наложении электрического поля движение ионов становится более упорядоченным: положительно заряженные ионы (катионы) приближаются к катоду, а отрицательно заряженные ионы (анионы) – к аноду.
Электролиз является одновременно и рафинированием, так как при некотором напряжении на катоде будут (преимущественно) выделяться только катионы определенного металла. В соответствии с величиной напряжения, требуемого для выделения на катоде, металлы образуют «ряд напряжений». Например: цинк, железо, олово, медь, серебро, золото.
Чем левее находится металл в этом ряду, тем он более электроотрицателен или менее благороден, более активен (по отношению к кислороду кислотам, щелочам и пр.) и тем большее напряжение требуется для его выделения на катоде.
Вравновесных условиях (при фиксированном напряжении), пока на катоде выделяется какой-либо металл ионы более электроотрицательных по отношению к нему элементов разряжаться не будут. Однако в реальных условиях в переносе зарядов наряду с ионами выделяемого металла участвуют
иионы более электроотрицательных элементов. А это приводит к их выделению на катоде. Как правило, этот процесс сопровождается повышением напряжения на катоде («перенапряжением»).
Чем больше сродство металла к кислороду, тем труднее его выделить из водного раствора. Поэтому такие металлы, как алюминий, магний, цирконий, титан и прочие, получают путем электролиза расплавленных солей соответствующего металла.
Всоответствии с законом Фарадея, количество катодного осадка, вы-
делившегося при электролизе, пропорционально силе тока, времени его прохождения через электролит и электрохимическому эквиваленту, т.е. количеству металла, выделяемого за один ампер-час (табл. 1.7).
|
|
|
Таблица 1.7 |
||
Электрохимические эквиваленты некоторых металлов |
|||||
|
|
|
|
||
Металл |
Валентность |
Атомная масса |
Электрохимический |
||
эквивалент, г/(А·ч) |
|||||
|
|
|
|||
Алюминий |
3 |
26,98 |
0,3354 |
|
|
Титан |
4 |
47,90 |
0,4467 |
|
|
Молибден |
6 |
95,94 |
0,5969 |
|
|
Ниобий |
5 |
92,91 |
0,6932 |
|
|
Цирконий |
4 |
91,22 |
0,8508 |
|
|
Кобальт |
2 |
58,93 |
1,0993 |
|
|
Никель |
2 |
58,71 |
1,0947 |
|
|
|
|
|
|
|
|
Процессы порошковой металлургии. Курс лекций |
-127- |
|

I. ПОЛУЧЕНИЕ ПОРОШКОВ
Лекция 17 Общие закономерности процессов производства порошков электролизом
Вольфрам |
6 |
183,85 |
1,1440 |
Медь |
2 |
63,54 |
1,1858 |
Цинк |
2 |
65,37 |
1,2195 |
Тантал |
5 |
180,95 |
1,3496 |
Однако реально получаемые при электролизе количества осадка всегда меньше, чем рассчитанные. Это объясняется тем, что в процессе электролиза происходит совместный разряд на катоде ионов нескольких элементов (как правило, двух-трех), частичное растворение выделенного металла и пр. Кроме того, возможна и утечка тока через дефекты электроизоляции. Для оценки степени несовпадения расчетных и реально полученных количеств осадка используют такой показатель, как выход по току, %:
А = (qп/qт)·100, |
(1.63) |
где qп – масса вещества (осадка), реально выделившаяся при прохождении определенного количества электричества через электролит; qт – масса вещества (осадка), которая должна была бы выделиться.
Факторы, определяющиесвойствапорошков
На свойства получаемых порошков оказывают влияние следующие факторы технологического процесса.
Плотность тока. Сила тока на рабочей ванне электролизера является главным фактором, определяющим ее производительность. Плотность тока связывает силу тока с суммарной рабочей поверхностью катодов (катодная плотность тока) или анодов (анодная плотность тока), находящихся в ванне электролизера:
i = I/S, |
(1.64) |
где i – плотность тока, А/м2; I – сила тока на ванне, A; S – суммарная рабочая поверхность катодов или анодов соответственно, м2.
Как правило, катодная и анодная плотности тока в электролизере не совпадают, так как практически всегда не совпадают суммарные рабочие поверхности катодов и анодов.
Выделение металла на катоде начинается в центрах первичной кристаллизации. При большей плотности тока в ванне на единице площади катода разряжается больше ионов, т.е. на катоде создается больше первичных центров кристаллизации. В связи с этим при низкой концентрации катионов в электролите скорость роста каждого из подобных центров уменьшается. Это приводит к получению более мелких (дисперсных) осадков. Однако при
Процессы порошковой металлургии. Курс лекций |
-128- |

I. ПОЛУЧЕНИЕ ПОРОШКОВ
Лекция 17 Общие закономерности процессов производства порошков электролизом
большой плотности тока высоко и напряжение на ванне, что обуславливает выделение на катоде побочных элементов (а не только атомов получаемого металла) и снижению выхода по току. С повышением катодной плотности тока растет и анодная плотность тока, в результате чего на аноде начинается более интенсивная разрядка анионов кислорода (при электролизе водных растворов), хлора или фтора (при электролизе расплавов). Это может привести к проявлению анодного эффекта: электролит как бы отделяется от электрода прослойкой газа и в ней возникает искрение. Выделение металла на катоде практически прекращается. Поэтому необходимо подбирать такие плотности тока, которые позволят избежать появления анодного эффекта.
Плотность тока можно корректировать либо за счет изменения токовых нагрузок на ванне, либо путем изменения суммарной рабочей поверхности катодов (количества катодов).
Концентрация ионов выделяемого металла. Повышение концентра-
ции выделяемых ионов (при низкой плотности тока) создает благоприятные условия для активного питания сравнительно небольшого количества центров, в результате чего формируется плотный осадок. Для образования порошкообразного (рыхлого) осадка нужна пониженная концентрация ионов металла в электролите. Однако при слишком малой концентрации ионы металла перенесут лишь небольшую долю электроэнергии, в связи с чем в процесс электропереноса будут вовлекаться и другие катионы, например водорода, что приведет к снижению выхода по току.
Температура электролита. Повышение температуры увеличивает скорость перемещения ионов и ускоряет их диффузионную подвижность. Это компенсирует обеднение приэлектродной области электролита катионами. Стабильное «питание» центров кристаллизации способствует укрупнению порошков, но одновременно с этим возрастает и интенсивность химического взаимодействия выделяемого металла с электролитом. Это приводит к растворению катодного осадка и снижению выхода по току. Кроме того, увеличивается испарение электролита, что обуславливает ухудшение условий труда. Поэтому электролиз водных растворов ведут при температуре электролита не выше 60 °С, а электролиз расплавов – при температуре, которая должна быть выше температуры плавления электролита (при сохранении электролитом требуемой относительно достаточной жидкотекучести), но ниже температуры плавления выделяемого металла.
Кислотность электролита. Повышение содержания в электролите ионов водорода может привести к их бурному выделению на катоде. Это, с одной стороны, способствует разрыхлению (измельчению) порошка, но, с другой стороны, обуславливает существенное уменьшение выхода по току и возрастание расхода энергии. Кроме того, повышенная кислотность электролита приводит к растворению части металла, выделившегося на катоде.
Межэлектродное расстояние. Увеличение расстояния между электродами (при постоянном напряжении на ванне) способствует повышению
Процессы порошковой металлургии. Курс лекций |
-129- |
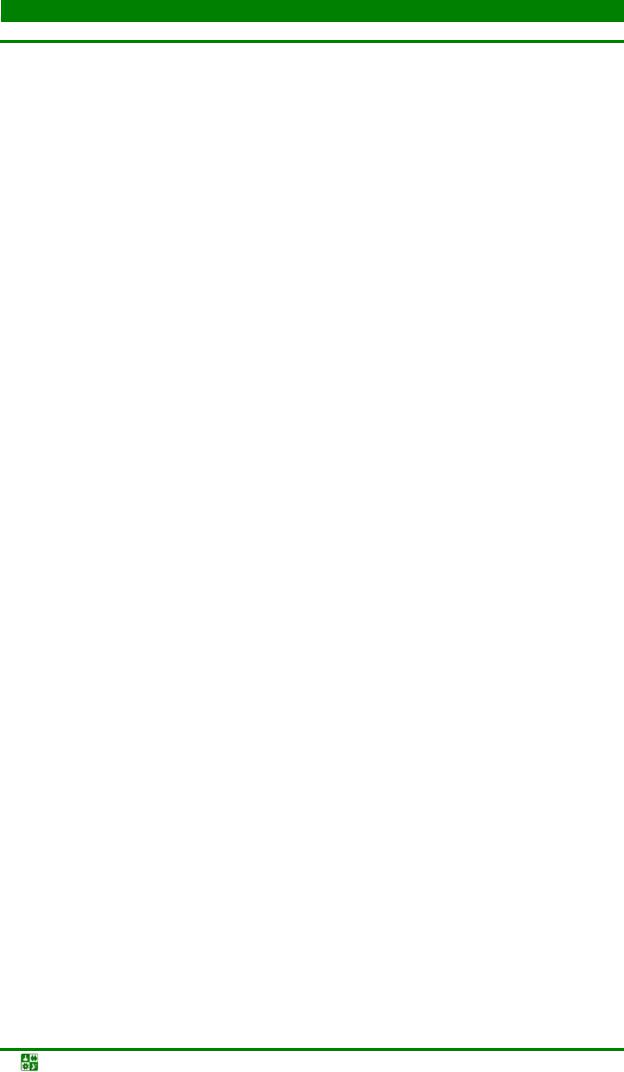
I. ПОЛУЧЕНИЕ ПОРОШКОВ
Лекция 17 Общие закономерности процессов производства порошков электролизом
электросопротивления электролита. При этом падает сила тока на ванне, уменьшается его катодная плотность, что обуславливает получение более крупных порошков. Одновременно снижается относительное количество растворяющегося в электролите катодного осадка и увеличивается выход по току. Однако при чрезмерном увеличении межэлектродного расстояния возрастает количество выделяемого тепла, что может привести к перегреву электролита и уменьшению выхода по току за счет растворения части катодного осадка.
При слишком малом расстоянии между электродами может произойти короткое замыкание, напряжение на ванне упадет до нуля, и выделение порошка на катоде прекратится, хотя сила тока в ней будет такой же, как и в нормально работающих ваннах.
Длительность наращивания слоя порошка на катоде. В процессе рос-
та частиц порошка значительно увеличивается их суммарная поверхность (особенно у рыхлых осадков), а следовательно, возрастает и суммарная поверхность самих катодов. Это, в свою очередь, приводит к снижению плотности тока и образованию на катоде более крупных частиц (на катоде может сформироваться губка или даже плотная корка).
Несвоевременное удаление порошка может стать причиной короткого замыкания электродов через разросшийся катодный осадок.
Циркуляция электролита. В процессе электролиза может произойти частичное расслаивание электролита вследствие различной плотности его составляющих (при электролизе расплавов), обеднение (обогащение) прикатодного (прианодного) пространство катионами (анионами), а также изменение заданной температуры раствора (расплава). Для предотвращения этих нежелательных явлений проводят выравнивание концентрации электролита с помощью системы непрерывной замкнутой циркуляции. Для этого за один час работы электролизера осуществляют примерно 6–8-кратный обмен электролита.
Наличие газообразных и органических примесей. В процессе электро-
лиза в электролите присутствует растворенный кислород, пероксид водорода, а также другие окислители, вызывающие окисление поверхности катода. В результате окисления поверхность катода становится более развитой, что способствует образованию рыхлых осадков. Присутствующие в электролите органические примеси и поверхностно-активные вещества адсорбируются на поверхности растущих граней кристаллов и препятствуют их дальнейшему росту, что также приводит к получению более рыхлых осадков.
Классификацияэлектролитическихпорошков
Процессы порошковой металлургии. Курс лекций |
-130- |

I. ПОЛУЧЕНИЕ ПОРОШКОВ
Лекция 17 Общие закономерности процессов производства порошков электролизом
В зависимости от условий электролиза на катоде получают твердые хрупкие осадки (в виде плотных слоев, чешуек, кристаллов), губчатые мягкие осадки и рыхлые (черные) осадки.
Плотные осадки представляют собой слоистые сростки крупных, хорошо сцепленных кристаллов. Для получения подобных осадков электролиз ведут при незначительных концентрациях водородных ионов, повышенных содержаниях ионов выделяемого металла и низких плотностях тока. Для придания такому осадку хрупкости используют смазку катода различными веществами или введение в раствор специальных добавок. Технология получения чешуйчатых осадков состоит в том, что на катоде послойно (попеременно) осаждаются разнородные металлы, один из которых является подслоем, подлежащим дальнейшему растворению. После растворения подслоя, извлеченного из ванны катодного осадка, второй металл (основной, не растворившийся) образует частицы в виде отдельных чешуек.
Губчатые мягкие осадки представляют собой скопления отдельных мелких кристалликов, легко поддающихся разрушению при растирании. Получению подобных осадков способствуют сравнительно низкие плотности тока, повышение кислотности раствора, уменьшение концентрации в электролите катионов выделяемого металла, наличие примесей ионов более электроположительных металлов и присутствие некоторых окислителей.
Плотные и губчатые осадки подвергают дополнительному измельчению для разделения частиц или уменьшения их размеров.
Рыхлые осадки являются высокодисперсными порошками, получающимися в готовом виде непосредственно в процессе электролиза. Их образованию способствуют высокие плотности тока, низкие концентрации в электролите катионов выделяемого металла, повышенная кислотность электролита и наличие некоторых примесей в нем или осаждаемого металла в составе комплексного аниона.
Для установления математической зависимости между плотностью тока, временем наращивания осадка и концентрацией катионов в электролите О. Кудра и Е. Гитман предложили следующие исходные положения:
1. Выделение плотного слоя металла на катоде происходит до тех пор, пока концентрация С катионов Mez+ у катода не снизится до какой-то определенной величины С0, при которой уже начинает выделяться рыхлый осадок (металл).
2. При включении тока выделяются сразу только близлежащие к электроду ионы Mez+ и притом расположенные в электролите не дальше определенного расстояния h.
3. В момент выделения рыхлого осадка концентрация катионов Mez+ в прилегающем к катоду объеме электролита имеет постоянно возрастающее значение – от С0 у самой поверхности катода до С на расстоянии h от его поверхности.
Процессы порошковой металлургии. Курс лекций |
-131- |

I. ПОЛУЧЕНИЕ ПОРОШКОВ
Лекция 17 Общие закономерности процессов производства порошков электролизом
4. При данной плотности тока и для определенной соли выделяемого металла изменение концентрации dC/dh от С0 до С – величина постоянная, в связи с чем расстояние h меняется пропорционально изменению концентрации С, а с повышением плотности тока возрастает и величина dC/dh (концентрация при более быстром выделении катионов Mez+ у катода не успевает выравниваться).
Таким образом,
dC/dh = Ni,
где N – коэффициент пропорциональности.
При работе с малыми плотностями тока С0 обычно не достигается, так как убыль ионов Mez+ постоянно пополняется (главным образом за счет диффузии), вследствие чего происходит выделение плотных осадков. Наоборот, при больших плотностях тока концентрация ионов Mez+ у катода резко падает и через короткое время достигает значения С0, при котором и начинает выделяться рыхлый осадок.
Между плотностью тока i и временем выделения осадка на катоде τ существует гиперболическая зависимость, означающая, что при любой плотности тока сначала, хотя и очень недолго, должен выделяться плотный осадок. В связи с этим нельзя утверждать, что при какой-либо достаточно высокой плотности тока выделяется только рыхлый осадок.
Результаты многочисленных опытов показывают, что, подбирая плотности тока, соответствующие наибольшему времени τ выделения рыхлых осадков, трудно достичь τ больше 20–25 с. Объясняется это тем, что при достигнутых плотностях тока убыль ионов выделяемого металла у катода успевает постоянно пополняться за счет диффузии, и появление рыхлых осадков не наблюдается. На основании этого устанавливается предельная плотность тока, соответствующая выделению только плотных осадков:
i2 = 0,2КС, |
(1.65) |
где C – концентрация ионов выделяемого металла; К – некоторая постоянная,
К = zF/2N,
здесь z – валентность выделяемого металла;F – число Фарадея, равное 96520. Достаточно наглядная картина получается при графическом изображении (рис. 1.27) зависимости между плотностью тока i и концентрацией раствора С. Если по оси абсцисс отложить концентрацию катионов выделяе-
Процессы порошковой металлургии. Курс лекций |
-132- |

I. ПОЛУЧЕНИЕ ПОРОШКОВ
Лекция 17 Общие закономерности процессов производства порошков электролизом
мого металла, а по оси ординат – плотность тока, то полученные пределы выделения, соответственно, плотных или рыхлых осадков (i = КС и i2 = 0,2КС) будут выражены прямыми, проходящими через начало координат. Эти прямые делят все поле зависимости на три участка.
Для питания электролизеров электроэнергией служат специальные электроподстанции, где устанавливают оборудование для преобразования переменного тока в постоянный ток.
i, А/см22 i, А/см
0,5
0,4
0,3
0,2
0,1
0
I
II
III
0,6 |
1 |
С,,моль/л/л |
|
|
Рис. 1.27. Диаграмма зависимости размеров частиц порошка от плотности тока и концентрации раствора при получении порошков меди: I – область образования рыхлых осадков; II – область образования губчатых осадков; III – область образования плотных осадков
Преобразователями служат мотор-генераторы, игнитроны (ртутные преобразователи) и кремниевые или германиевые выпрямители, имеющие наименьшие электрические потери при работе. Переменный ток промышленной частоты 50 Гц и напряжением 10 000 В преобразуется в постоянный ток силой до 25 000 А при напряжении до 425 В.
Контрольныевопросыизадания
1.Чему равняется количество катодного осадка в соответствии с законом Фарадея?
2.Назовите причины отклонения практически полученного количества осадка от теоретически рассчитанного.
3.Перечислите факторы, определяющие качество катодного осадка.
4.Что представляют собой плотные, губчатые и рыхлые осадки?
Процессы порошковой металлургии. Курс лекций |
-133- |

I. ПОЛУЧЕНИЕ ПОРОШКОВ
Лекция 17 Общие закономерности процессов производства порошков электролизом
5.Что такое «анодный эффект»?
6.При каких условиях электролиза можно получить плотные осадки?
7.При каких условиях можно получить рыхлые осадки?
8.При каких температурах получают порошки металлов их растворов
ирасплавов солей?
Лекция18 Получениепорошковэлектролизомводныхрастворов
План лекции
1.Особенности образования катодных осадков. Получение порош-
ков меди.
2.Получение порошков никеля и серебра.
3.Получение порошков железа.
4.Получение порошков сплавов.
5.Получение порошков из производственных растворов и сточных вод металлургических предприятий.
6.Техника безопасности при проведении работ.
Особенностиобразованиякатодныхосадков. Получениепорошковмеди
Производство металлических порошков методом электролиза водных растворов с успехом конкурирует с другими известными методами. В настоящее время в промышленных масштабах получают порошки меди, серебра, железа, хрома, цинка, никеля, кадмия, свинца, олова, сурьмы, а также их сплавов.
Характер образующихся катодных осадков зависит как от индивидуальных особенностей металлов, так и от состава электролита и условий электролиза. Некоторые металлы (Ni, Zn или Co) образуют равномерные плотные мелкозернистые осадки независимо от природы электролита. Другие (серебро или кадмий) – растут в виде отдельных сильно разветвляющихся кристаллов при электролизе растворов простых солей или выделяются в виде совершенно ровного гладкого слоя из растворов комплексных цианистых солей этих металлов.
Размер частиц и гранулометрический состав порошков определяются (при прочих равных условиях) плотностью тока. Однако наряду с этим на характер образующихся осадков влияет состав электролита. Например, при
Процессы порошковой металлургии. Курс лекций |
-134- |

I. ПОЛУЧЕНИЕ ПОРОШКОВ
Лекция 18 Получение порошков электролизом водных растворов
электролизе комплексных цианистых растворов с крайне низкой концентрацией катионов выделяемого металла следовало бы ожидать образования рыхлых осадков, но на практике подобные осадки не образуются даже при очень высоких плотностях тока.
Электролитический способ получения медного порошка известен с 1865 г. В настоящее время в России этот метод обеспечивает производство медного порошка высокой чистоты, требуемой зернистости, с хорошими технологическими свойствами. Существенными недостатками метода являются сравнительно высокая стоимость получаемых порошков, а также большой расход электроэнергии (при невысокой производительности).
По ГОСТ 4960-75 предусмотрено изготовление порошка меди шести марок, различающихся по свойствам: ПМ – порошок нестабилизированный; ПМС-А, ПМС-1, ПМС-В – порошок стабилизированный; ПМС-К – порошок, стабилизированный конопаточный; ПМС-Н – порошок стабилизированный низкодисперсный.
Производства медного порошка (рис. 1.28) электролизом проводят с использованием кислого раствора сернокислой меди. Анодами (плиты размером 880x980x10 мм) служит чистая катодная медь (ГОСТ 546-79). Плавленую черновую медь не применяют, так как она загрязнена примесями мышьяка, сурьмы и свинца, которые переходят в получаемый медный порошок.
При производстве порошков применяют литые аноды, изготовленные из катодной меди (катоды, получаемые при электрорафинировании черновой меди), либо аноды, изготовленные из медного проката.
Электролит представляет собой сернокислый (125–180 г/л H2SО4; исходная серная кислота марки А) раствор сульфата меди CuSО4. Исходный медный купорос содержит, %: около 90 CuSО4 5H2О; 0,06 Fe; 0,015 As; 0,25 H2SО4. Вещества, составляющие электролит, диссоциируют с образова-
нием катионов меди и водорода, а также анионов SO24− и ОН–. Выделение по-
рошка проводят на медных катодах пластинчатого (листы катодной меди размером 830х930 мм, толщиной 3–4 мм) или стержневого типа (медные трубки диаметром 12–16 мм, с толщиной стенки около 3 мм). При использовании катодов стержневого типа расстояние между ними составляет от 110 до 150 мм.
В некоторых случаях применяют катоды, изготовленные не из меди, а из алюминия, титана или свинцово-сурьмянистого сплава (около 6 % Sb). Катодная плотность тока лежит в пределах от 1 800 до 3 250 А/м2 при напряжении на ванне от 1,3 до 1,7 В.
Анодов в ванне всегда на один больше, чем катодов (для того чтобы любая из поверхностей катодов являлась рабочей).
Для устранения пассивации анодов в электролите поддерживают концентрацию хлор-иона на уровне 0,5–4,0 мг/л. Большее количество хлорионов вредно, так как возможно образование полухлористой меди, образующей коллоидный осадок, который нарушает нормальный ход электролиза.
Процессы порошковой металлургии. Курс лекций |
-135- |

I. ПОЛУЧЕНИЕ ПОРОШКОВ
Лекция 18 Получение порошков электролизом водных растворов
Хлор-ионы в электролит поступают с водой, к которой добавляют поваренную соль NaCl или соляную кислоту НСl.
Серная кислота |
|
|
Катодная медь |
||
Вода |
|
|
|
||
Электролит |
Аноды |
|
|||
|
Высевки |
||||
|
Отработан- |
|
|||
2 |
|
1 |
|||
ный электро- |
Анодные |
|
|||
|
лит |
|
|||
|
|
|
остатки |
Стабилизатор |
|
|
|
3 |
|
||
|
|
Вода |
|
||
|
|
|
|
||
|
17 |
Вода |
|
5 |
|
|
|
|
|||
|
|
Стабилизи- |
|
||
|
|
|
рующий |
|
|
|
|
4 |
раствор |
|
|
|
16 |
|
|
||
|
Крепкий |
|
|
||
|
|
|
|
||
|
|
раствор |
6 |
9 |
|
На станцию ней- |
Слабый |
8 |
10 |
||
11 |
|||||
трализации |
раствор |
|
|||
|
|
Продукты сгора- |
7 |
12 |
|
|
15 |
|
|||
|
ния природного |
|
|
||
|
|
газа |
|
13 |
|
|
|
|
|
||
|
|
|
|
14 |
Рис. 1.28. Типовая аппаратурно-технологическая схема получения медного порошка: 1 – плавильная печь; 2 – узел корректировки состава электролита; 3 – электролизная ванна; 4 – узел промывки, стабилизации и обезвоживания порошка; 5 – установка подготовки стабилизирующего раствора; 6, 9, 12 – бункеры-накопители порошка; 7 – сушка порошка; 8 – элеватор; 10 – измельчение порошка; 11 – классификатор порошка; 13 – смеситель (усреднитель) порошка; 14– упаковка порошка; 15, 16– ловушки (фильт-
ры); 17 – узел регенерации электролита
На практике применяют электролизные ванны ящичного или бункерного типа (рис. 1.29) с каркасом их дерева, металла или железобетона. Рабо-
Процессы порошковой металлургии. Курс лекций |
-136- |

I. ПОЛУЧЕНИЕ ПОРОШКОВ
Лекция 18 Получение порошков электролизом водных растворов
чая поверхность ванны футеруется кислотостойким материалом (винипластом, пластмассой, сурьмянистым свинцом и пр.). Но даже при нормальном (без побочных эффектов) течении процесса прикатодное пространство обед-
няется по катионам меди и обогащается ионами SO24− , а прианодное пространство и электролит – ионами меди.
1 |
2 |
3 |
4 |
5 |
4 |
3 |
6 |
|
|
|
7 |
8
а |
б |
Рис. 1.29. Разрез ванны электролизера ящичного (а) и бункерного (б) типов: 1 – карман для приема электролита; 2 – промежуточная шина; 3 – анод; 4 – катод; 5 – карман для подачи электролита; 6 – лоток для выпуска электролита; 7
– корпус электролизера; 8 – устройство для выгрузки порошка
Ванны включаются в электрическую цепь сериями (15–25 ванн), последовательно, а электроды в них – параллельно. Это позволяет поддерживать на каждой из ванн серии одинаковую силу тока и одинаковое напряжение между электродами.
Максимальное время наращивания порошка на стержневых катодах составляет около 7–8 ч. Время наращивания порошка на пластинчатых катодах – 1–2 ч. Порошок снимают с катода специальными скребками из нержавеющих сталей, пластмасс, полимеризированных смол. В настоящее время разработаны способы механизированного съема порошка с катода: скребком с вращающегося катода; путем пропускания электрического импульса; ультразвуковым разрядом большой мощности и пр.
В процессе электролиза происходит существенное изменение состава электролита. Он обогащается медью за счет некоторого (до 2,0–2,5 %) растворения катодного осадка по реакции Сu + 0,5О2 + H2SО4 = CuSО4 + Н2О и неполного (выход по току составляет 80–90 %) выделения меди из электролита.
Неполное выделение меди из раствора связано с разрядкой на катоде ионов водорода (Сu2+ + 2е = Сu + Н+ + е = 0,5Н2). Эти явления приводят к по-
вышению содержание меди в электролите на 20–30 %/сут (против исходного состава раствора). Кроме того, электролит обедняется по серной кислоте, за-
Процессы порошковой металлургии. Курс лекций |
-137- |

I. ПОЛУЧЕНИЕ ПОРОШКОВ
Лекция 18 Получение порошков электролизом водных растворов
трачиваемой на растворение катодной меди и выделение водорода на катоде. Выравнивание концентрации ионов по объему электролизной ванны и удаление «избытка» ионов меди осуществляют с помощью системы непрерывной замкнутой циркуляции и регенирации раствора (за один час происходит примерно десятикратный обмен раствора).
Часть электролита из ванны через латок выпуска непрерывно сливается в сборник, из которого он поступает в теплообменник и систему регенерационных ванн. В теплообменнике электролит проходит по трубкам из кислотостойкой нержавеющей стали, омываемым холодной водой, и охлаждается до необходимой температуры (48–55 °С).
Одновременно с циркуляцией осуществляют регенерацию электролита, так как в электролите происходит постепенное накапливание примесей (As, Sb, Fe и др.), попадающих в него по мере растворения анода. Для обеспечения постоянства заданного состава проводят корректировку электролита, включая в систему сблокированных ванн специальные регенеративные ванны с нерастворимыми анодами свинцовыми (Pb, Pb + 1 % Ag, Pb + 6 % Sb) или из платинированного титана (например, каждая пятая, шестая или седьмая ванна в серии). Общее (суммарное) требуемое количество регенеративных ванн n можно подсчитать по формуле
n = ∆CCu 2+ V /1,1858 I τ Bt, |
(1.66) |
где ∆CCu2+ – прирост концентрации меди в электролите, г/л, за время электро-
лиза τ, ч; V – суммарный объем электролита во всех ваннах работающих электролизеров, л; I – сила тока, проходящего через электролит, А; Bt – катодный коэффициент полезного использования тока, доли единицы.
В регенерационных ваннах выделение меди на катоде уменьшает концентрацию ее катионов в электролите, а на аноде образуется кислород и проис-
ходит регенерация серной кислоты (SO24− – 2е = SО3 + 0,5О2, SО3 + H2О =
H2SО4). По мере накапливания примесей часть электролита выводят из системы циркуляции, а вместо него вводят свежеприготовленные порции электролита.
Промывка и стабилизация порошка. Медный порошок, снятый с ка-
тодов, выгружают из ванны периодически без ее отключения при помощи гидровакуумной системы. Для удаления механически захваченного электролита порошок промывают горячей водой на нутч-фильтрах или в аналогичных им по конструкции специальных промывателях, в которых вода фильтруется через слой порошка, находящийся на перфорированной (сетчатой) решетке из нержавеющей стали. Для качественной промывки порция порошка должна иметь одинаковую фильтрующую способность по всей высоте
Процессы порошковой металлургии. Курс лекций |
-138- |

I. ПОЛУЧЕНИЕ ПОРОШКОВ
Лекция 18 Получение порошков электролизом водных растворов
и поверхности слоя. Полнота отмывки определяется реакцией на наличие катионов меди в воде после промывки (отсутствие окрашивания раствора желтой кровяной соли или 5 %-го аммиака). Расход воды составляет до 10 м3 на одну тонну порошка.
Пленка воды на частицах порошка приводит к их коррозии (окислению). Поэтому после отмывки порошка водой применяют его стабилизацию
– промывку раствором хозяйственного мыла или мылонафта (получают в процессе очистки керосина; стоимость в 10 раз меньше стоимости мыла), содержащим их в количестве 400 г на 1 м3 воды. После стабилизации на поверхности частиц остается гидрофобная пленка, защищающая медь от коррозии (коррозионная стойкость порошка повышается в несколько десятков раз). Расход стабилизирующего раствора составляет около 6 м3 на одну тонну порошка. Избыток стабилизатора удаляют промывкой порошка холодной водой. Избыточное давление растворов и воды должно быть > 0,5 МПа для слоя порошка высотой 1 м. После промывки порошок обезвоживают и сушат.
Обезвоживание и сушка порошка. Операция обезвоживания позволяет удалить большую часть влаги, что облегчает и ускоряет последующую сушку. Самый простой способ обезвоживания заключается в продувке порошка воздухом под избыточным давлением (0,5–0,6 МПа) в течение 10–30 мин. Наиболее эффективным способом является центрифугирование порошка в какой-либо из промышленных центрифуг с умеренной частотой вращения (1 000–1 200 об/мин). При этом остаточное содержание влаги в порошке составляет 8–10 % против 25–30 % после обработки сжатым воздухом.
Обезвоженный порошок высушивают в вакуумном сушильном аппарате при температуре около 100 °С и остаточном давлении 0,05–0,09 МПа в течение 10–12 ч либо в специальных вращающихся барабанах воздухом при 100 °С или в кипящем слое продуктами конверсии природного газа. Кроме того, на практике применяют сушку в среде конвертированного природного газа в туннельной печи на движущейся непрерывной ленте и сушку продуктами сгорания природного газа.
Если это требуется, то высушенный порошок измельчают в мельницах непрерывного действия, работающих в замкнутом цикле с устройством для рассева порошка на фракции. После просева и опробования формируются партии массой < 1 000 кг путем смешивания отдельных сравнительно небольших порций порошка одной марки (табл. 1.8), изготовленного по одному технологическому режиму. Затем партии порошка массой до 70–85 кг затаривают (по ГОСТ 5044-79) в стальные бочки с внутренним полиэтиленовым мешком (ГОСТ 17811-78). Вместимость барабана бочки составляет 25, 45, 50, 80 дм3 (по согласованию с потребителем тара может быть меньшей вместимости и другой, но по качеству не ниже указанной).
Процессы порошковой металлургии. Курс лекций |
-139- |
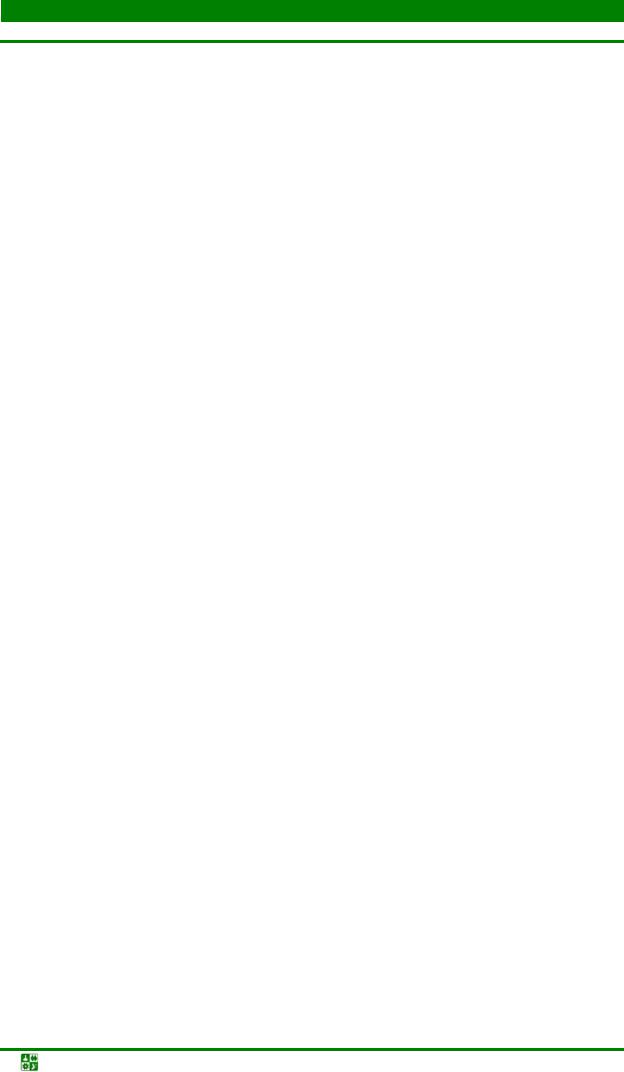
I. ПОЛУЧЕНИЕ ПОРОШКОВ
Лекция 18 Получение порошков электролизом водных растворов
Таблица 1.8 Химический состав и насыпная плотность медных порошков
Марка |
Насыпная |
Медь, %, |
Примеси, %, не более |
|
|
|
|||
плотность, г/см3 |
не менее |
железо |
кислород |
|
ПМС-В |
2,4–2,7 |
99,5 |
0,018 |
0,10 |
ПМ |
1,25–2,0 |
99,5 |
0,018 |
0,30 |
ПМС-1 |
1,25–1,9 |
99,5 |
0,018 |
0,20 |
ПМС-А |
1,3–1,5 |
99,5 |
0,018 |
0,30 |
ПМС-К, ПМС-Н |
2,5–3,5 |
99,5 |
0,06 |
0,50 |
П р и м е ч а н и я: 1. Содержание у всех марок, % (не более): Sb – 0,005; Pb – 0,05; As – 0,003.
2. Для электротехнической промышленности насыпная плотность порошка марок ПМС-А, ПМ – 1,25–1,45 г/см3, ПМС-1 – 1,7–2,0 г/см3.
Влажность медного порошка должна быть < 0,05 %, содержание сернокислых соединений металлов в пересчете на ион SO4 < 0,01 % и прокаленного остатка после обработки азотной кислотой ≤ 0,05 % для марок ПМС-К, ПМС-Н и ≤ 0,04 % для остальных.
Получениепорошковникеляисеребра
Получение порошков никеля. Согласно ГОСТ 9722-97 выпускают по-
рошки никеля марок ПНЭ-1 и ПНЭ-2, содержащие, %: ≥ 99,5 Ni + Co (соответ-
ственно, не более 0,20 и 0,50 Со); 0,02 С; 0,10 О; 0,10 и 0,20 Fe; 0,06 и 0,08 Сu; 0,008 и 0,010 S; 0,03 Si.
Порошок никеля получают электролизом аммиачных растворов сернокислого никеля (исходным материалом является NiSО4·7H2О). Электролит
содержит, г/л:
5–15 никеля (Ni2+); 75–80 сульфата аммония; 2–3 серной кислоты;
40–50 хлористого аммония; до 200 хлористого натрия.
Снижение концентрации сернокислого никеля в электролите приводит к уменьшению среднего размера частиц порошка никеля (повышение – увеличивает средний размер частиц порошка и выход по току).
Хлористый натрий обеспечивает высокую электропроводность раствора, что позволяет использовать при электролизе высокие плотности тока, приводящие к увеличению съема металла с единицы площади катода.
Процессы порошковой металлургии. Курс лекций |
-140- |

I. ПОЛУЧЕНИЕ ПОРОШКОВ
Лекция 18 Получение порошков электролизом водных растворов
Хлористый аммоний в электролите играет роль буферной добавки, поддерживающей требуемое значение рН, но при увеличении его концентрации выше 50 г/л происходит уменьшение растворимости сульфата никеля в электролите и снижение выхода по току. Ионы аммония служат комплексообразователями, связывающими ионы никеля в комплексный ион Ni[NH3]22+, что позволяет устранить явление гидролиза сернокислого никеля у катода в условиях интенсивного выделения водорода и значительного повышения рН раствора.
Ионы натрия, составляя часть внешней обкладки двойного электрического слоя на поверхности катода, затрудняют разряд катионов никеля, что способствует формированию порошкообразного осадка. Ионы хлора препятствуют пассивированию растворимых никелевых анодов, отливаемых из несортового никеля (87,5–90 % Ni, до 9 % Со, до 6,5 % Сu, до 3 %Fe, 0,6–0,7 % S).
Катодами служат пустотелые коробки из меди или нержавеющей стали, охлаждаемые водой. Аноды изготовляют из нержавеющей стали. В некоторых случаях процесс ведут с использованием нерастворимых анодов из графита.
Для улавливания порошка, осыпающегося с катода, применяют фильтрующие катодные диафрагмы.
Электролиз ведут при температуре электролита 35–55 °С, плотности тока 1 000–3 000 А/м2 и напряжении на ванне 10–15 В. Выход по току составляет до 90–94 %, а расход электроэнергии – около 3 000 кВт·ч/т.
Повышение плотности тока до 3 000 А/м2 вызывает обеднение прикатодного слоя электролита ионами никеля и увеличивает количество центров кристаллизации на катоде, что обуславливает измельчение осадка. Повышенная температура электролита способствует более быстрой доставке ионов никеля к катоду, что увеличивает выход по току, а также растворимость сульфата никеля в присутствии хлористого аммония.
Промывка выгруженного из ванны электролизера порошка никеля и его сушка (влажность получаемых порошков никеля < 0,2 %) не требуют особых мер предосторожности, так как никель достаточно стоек против коррозии.
Насыпная плотность для порошка никеля марки ПНЭ-1 < 3,4 г/см3, марки ПНЭ-2 < 5,0 г/см3. Размер частиц порошка марок ПНЭ-1 должен быть < 71 мкм (при содержании частиц размером < 45 мкм 30 % и более от массы партии порошка), а порошка марки ПНЭ-2 < 250 мкм (при содержании частиц размером < 71 мкм 3 % и более от массы партии порошка). Масса партии порошка не должна превышать 500 кг.
Никелевый порошок упаковывают в металлические банки (вместимостью до 3 л), стальные барабаны (бочки), полиэтиленовую тару (объемом до 50 л), а также в другие виды тары. Порошок должен храниться в сухих з а- крытых отапливаемых помещениях при температуре воздуха от 0 до 35 °С. Гарантийный срок хранения –12 мес со дня изготовления.
Получение порошка серебра. Серебряный порошок получают электролизом раствора азотнокислого серебра AgNО3.
Процессы порошковой металлургии. Курс лекций |
-141- |

I. ПОЛУЧЕНИЕ ПОРОШКОВ
Лекция 18 Получение порошков электролизом водных растворов
Используют электролит состава 10–15 г/л азотной кислоты и 40 г/л азотнокислого серебра (25 г/л Ag+) с температурой 35–40 °С. Плотность тока составляет 1 400–1 500 А/м2, напряжение на ванне – 2,0–2,8 В.
Анод – листовое серебро, катод алюминиевый. По ГОСТ 9724-61 производят порошки марок ПС1 и ПС2 ссодержанием серебра > 99,9 %. Содержание примесных элементов, % (не более): 0,02 Сu; 0,001 NО3; 0,005 SО4; 0,04 Fe, Bi, Pb, Sb, Al в сумме. Влажность порошка не должна превышать 0,08 %.
Получениепорошковжелеза
Вряду напряжений железо располагается левее водорода, и в кислых электролитах на катоде интенсивно выделяется водород, существенно снижая выход по току и ухудшая качество порошка железа. Кроме того, в элек-
тролите может образовываться Fe(OH)3, загрязняющий катодный осадок и нарушающий непрерывность процесса электролиза.
Электролит представляет собой сернокислый раствор сульфата железа
сдобавкой хлористого натрия (устраняет пассивацию анода и осаждение из раствора на катоде некоторых примесей) или солянокислый раствор хлорида железа с добавкой хлористого аммония либо смесь таких растворов, так как каждый из них имеет свои достоинства и недостатки.
Хлористый электролит позволяет вести электролиз при небольшом напряжении на ванне электролизера и повышенных плотностях тока, но в нем двухвалентное железо легко окисляется в трехвалентное, образующее осадок Fe(OH)3.
Всернокислых электролитах окисление двухвалентного железа и гидратообразование происходят менее активно, режим электролиза более стабилен, но требуются повышенное напряжение на ванне и повышенный расход электроэнергии по сравнению с применением хлористого электролита.
Растворимые аноды могут быть из чугунного или низкоуглеродистого стального лома, литья, обрезков железных листов, стружки с содержанием углерода < 0,6 % мас. и т.п. Катоды изготавливают из нержавеющей (корр о- зионно-стойкой) стали.
Электролиз ведут на получение либо плотного хрупкого осадка железа, либо его мягкого осадка.
Катодный осадок первого типа может быть получен следующим образом. Аноды, очищенные на пескоструйном аппарате от оксидной пленки, помещают в мешки-диафрагмы для устранения механического засорения катодного осадка анодным шламом. Электролит поступает в железобетонные ванны с винипластовой футеровкой из напорного бака, а из ванн стекает в сливной бак, откуда его вновь перекачивают в напорный бак. Состав элек-
тролита, г/л: 120–140 FeSО4; 0,2–0,28 H2SO4; 40–50 NaCl. Температура элек-
тролита |
50–54 °С, скорость циркуляции 8–10 л/мин. Напряжение на |
|
ванне 1,5–1,7 В, катодная плотность тока 400–500 А/м2. |
|
|
|
|
|
|
Процессы порошковой металлургии. Курс лекций |
-142- |
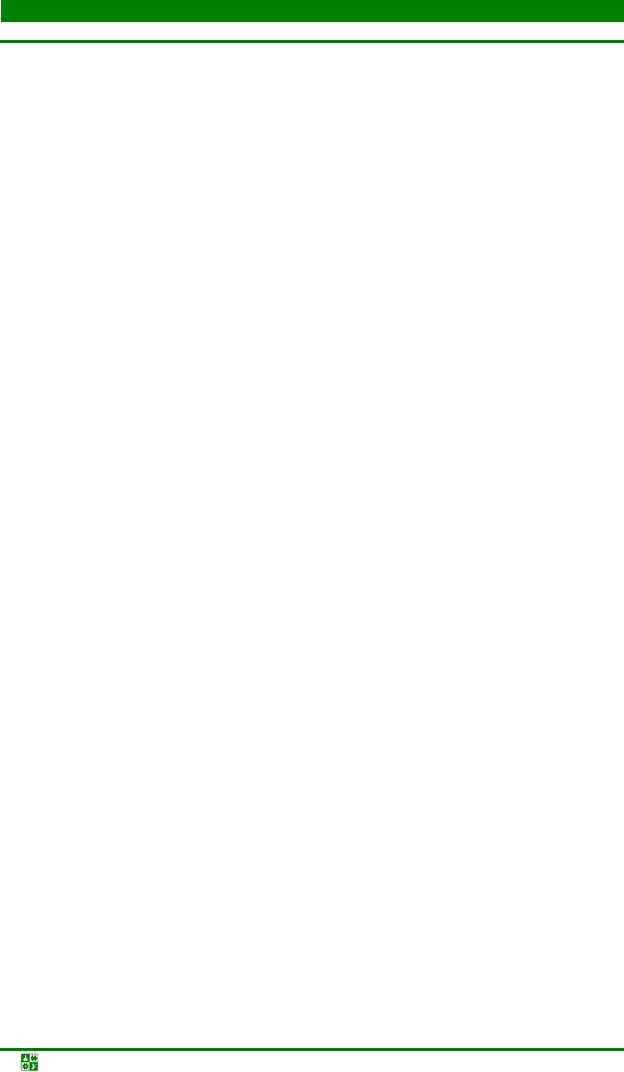
I. ПОЛУЧЕНИЕ ПОРОШКОВ
Лекция 18 Получение порошков электролизом водных растворов
При электролизе анодное растворение (90–95 %) превышает катодное осаждение (80–85 %), вследствие чего концентрация ионов двухвалентного железа в электролите должна непрерывно увеличиваться, а концентрация кислоты падать. Однако одновременно в электролите в результате гидролиза сернокислого железа по реакции FeSО4 + 2Н2О → Fe(OH)2 + H2SО4 и окисления двухвалентного железа кислородом воздуха до трехвалентного идут процессы, приводящие к уменьшению количества Fe2+ и увеличению концентрации H2SО4. Создавая в циркуляционной системе «кислотный напор», удается взаимно сбалансировать указанные процессы: электролит, поступающий в ванны из напорного бака, имеет кислотность 0,32–0,35 г/л и температуру 54–58 °С, в междуэлектродном пространстве ванны он имеет кислотность 0,24–0,27 г/л и температуру 50–54 οС, а в сливе из ванны – кислотность 0,18–0,20 г/л и температуру < 50 °С. В процессе циркуляции электролит охлаждается до 42–45 °С, окисляется воздухом и после подогрева в напорном баке приобретает кислотность 0,32–0,35 г/л. Образующиеся взвешенные гидроксилы железа либо отстаиваются в сливном баке, либо отделяются на фильтр-прессе, расположенном до напорного бака. Скорость циркуляции электролита зависит от его кислотности и температуры в ванне: увеличивается при пониженных кислотности и температуре и уменьшается при повышенных температуре и кислотности.
Цикл наращивания катодного осадка толщиной 2,0–2,5 мм длится около 46–48 ч. Для получения слоистого и хрупкого листа подачу тока на электролизер прерывают на 15–20 мин через каждые 6 ч. Катоды с осадком, извлеченные из ванны, промывают проточной водой, затем механическим способом снимают с катода железные пластины, дробят и размалывают их в шаровых мельницах в жидкой среде при отношении Т : Ж = 1 : 2.
Полученный порошок промывают горячей (60 °С) водой во вращающихся барабанах при Т : Ж = 1 : 4, обеспечивая полноту отмывки электролита.
После просева на сите плюсовую фракцию возвращают на повторное измельчение, а минусовую фракцию обезвоживают в центрифугах. Затем порошок сушат в барабанной печи при 150 °С или в горячей камере распыления, получая так называемый «черный порошок» окисленного железа, содержащий 92–95 % Fe. Этот порошок отжигают во вращающихся трубчатых печах при 680–720 °С в течение 1–3 ч в восстановительной среде (например, в атмосфере генераторного газа), после чего проводят размол в шаровых мельницах, рассев и упаковку. Готовый продукт содержит, %: 98,5–99,0 Fe; 0,02–0,04 С; < 0,03 Si; < 0,03 S; следы марганца и фосфора.
Насыпная плотность порошка 1,8–2,2 г/см3, а размер частиц < 125 мкм. Расход электроэнергии 3 500–4 000 кВт·ч/т.
Для нужд химической промышленности (химические реактивы) и медицины (лекарственный препарат) производят порошки железа реактивного и медицинского.
Процессы порошковой металлургии. Курс лекций |
-143- |

I. ПОЛУЧЕНИЕ ПОРОШКОВ
Лекция 18 Получение порошков электролизом водных растворов
Электролит содержит сульфат железа (50–60 г/л), хлористый аммоний (100 г/л) и серную кислоту (рН 3,5–4,0). Перед загрузкой в ванну электролизера электролит пропускают через специальный тканевый фильтр и нагревают до 40–45 °С.
Электролиз ведут при напряжении на ванне 2,0–2,5 В, катодная плотность тока составляет 1 200–1 250 А/м2. Аноды – пластины железа. Продолжительность цикла электролиза около 4 ч, после чего катоды, изготовленные из хромоникелевой стали, вместе с осадком извлекают из ванны, осадок (порошок) счищают с катода и многократно промывают водой и этиловым спиртом, совмещая промывку с усреднением порошка за счет перемешивания. Промытый порошок размещают тонким слоем на лотках из нержавеющей стали и сушат в вакуумном шкафу в течение 2 ч. После сушки порошок размалывают в шаровой мельнице и просеивают.
Возможно получение рыхлых осадков железа при использовании растворимого железного анода в комбинации с нерастворимым свинцовым анодом и дополнительным электродом (еще одним анодом) из железной сетки. Назначение этого электрода – электрохимическое восстановление ионов Fe3+, образующихся у свинцового анода, до Fe2+, что исключает необходимость в корректировке состава электролита в процессе электролиза.
Применяемый сернокислый электролит (рН 2,75–3,0) имеет состав, г/л: 27–41 FeSО4; 25–40 (NH4)2SО4; 40–50 K2SО4. Сульфат аммония стабилизирует кислотность электролита, a K2SО4 улучшает осыпаемость железного порошка с катода и увеличивает электропроводность раствора. Температура электролита 20–25 °С, катодная плотность тока 400–1 000 А/м2.
Питание электролизера постоянным током осуществляют от двух селеновых выпрямителей с регулируемыми напряжениями. Подобная схема за счет изменения напряжений на выпрямителях позволяет вести независимое регулирование токов, протекающих через каждый из анодов: один из выпрямителей питает цепь железный анод–катод, другой – цепь свинцовый анод–катод.
Меняя условия электролиза, можно получать железные порошки различной структуры и высокой степени чистоты с выходом по току 60–65 %. Полученные на катоде порошки железа извлекают из ванны, отмывают от электролита водой, подкисленной H2SО4, высушивают в вакуумном шкафу при комнатной температуре и отжигают в водороде при 700 °С.
Электролизом можно также получить железный порошок из хлористых ванн (электролитов). Еще в 1935 г. М.Ю. Бальшин установил, что оптимальным является раствор, содержащий 30 г/л хлористого железа; большее содержание этой соли приводило к образованию плотных осадков, меньшее – к образованию сильнодисперсных порошков. Кроме того, было показано, что добавление в электролит хлористого аммония стабилизирует процесс получения осадка нужного типа, делает его мало зависящим от изменения основных условий электролиза; оптимальное количество составляет 100 г/л, так как при большем содержании NH4C1 на катоде образуются гидроксиды же-
Процессы порошковой металлургии. Курс лекций |
-144- |

I. ПОЛУЧЕНИЕ ПОРОШКОВ
Лекция 18 Получение порошков электролизом водных растворов
леза, а при меньшем – снижается электропроводность раствора. При температуре электролита 80 °С и плотности тока 1 000 А/м2 расход электроэнергии составляет 2,7 кВт·ч/кг порошка, выход по току может достигать 95 %
(в среднем около 70 %).
Получениепорошковсплавов
Несмотря на кажущуюся простоту, электролитическое выделение многокомпонентных металлических порошков в промышленных масштабах не осуществляют прежде всего из-за быстрого изменения состава электролита в процессе электролиза, что приводит к получению на катоде порошка меняющегося химического состава и дисперсности.
Перспективным является проведение электролиза с несколькими растворимыми анодами из индивидуальных компонентов, входящих в состав сплава.
Примером подобного процесса является технология получения двухкомпонентного железокобальтового порошка с использованием трех анодов: двух растворимых (железный и кобальтовый) и одного нерастворимого (свинцовый). Нерастворимый анод используется в сочетании с дополнительным электродом из железной сетки. Катод никелевый или из нержавеющей стали. Электролизер питается током от трех выпрямителей с регулируемым напряжением, что позволяет независимо регулировать токи, проходящие через аноды. Электролит представляет собой смешанный подкисленный H2SО4 до рН 2,0–2,5 раствор сульфатов железа FeSО4 и кобальта CoSО4 при суммарном содержании металлических катионов 15 г/л; в раствор добавлены, г/л: 30 (NH4)2SО4 и 40 К2SО4. Температура электролита 20–25 °С, катодная плотность тока 1 000–3 000 А/м2. На катоде совместно разряжаются ионы железа, кобальта и водорода. Для расчета токов Iа, протекающих через кобальтовый и железный анод, используется следующее уравнение:
Ia(Co) / Ia(Fe) = ([Co]/[Fe])pacтв = ([Co]/[Fe])пop,
где [Со], [Fe] – концентрация кобальта или железа в растворе (электролите) и порошке.
Ток на свинцовом аноде должен соответствовать сумме токов на катоде и сетке. Меняя соотношение Co2+/Fe2+ в растворе и соотношение анодных токов, можно получать железокобальтовые порошки любого заданного состава от чистого железа до чистого кобальта с размером частиц от нескольких до сотен микрометров.
Аналогично рассмотренному могут быть получены железоникелевые порошки любого заданного состава. В электролизере располагают два растворимых анода из малоуглеродистого железа и никеля и один нераствори-
Процессы порошковой металлургии. Курс лекций |
-145- |

I. ПОЛУЧЕНИЕ ПОРОШКОВ
Лекция 18 Получение порошков электролизом водных растворов
мый анод из угля или графита, применяемый в сочетании с дополнительным электродом из железной или никелевой сетки.
Электролитом служит подкисленный соляной кислотой до рН 2,5 смешанный раствор сульфатов железа FeSО4 и никеля NiSО4 при суммарном содержании металлических катионов 12–15 г/л; в раствор добавлены, г/л: 12–15 NH4C1 (буферная добавка) и 20–40 NaCl (для устранения пассивации никелевого анода и повышения электропроводности раствора). Температура электролита 20–30 °С.
Катодная плотность тока зависит от соотношения Ni2+/Fe2+ в растворе: при Ni2+/Fe2+ = 0,2–0,5 обеспечивают 400–1 500 А/м2, при Ni2+/Fe2+ = 1 плотность тока находится в пределах от2 000 до 20 000 А/м2, при Ni2+/Fe2 = 2–5 процесс ведут при 4 000–20 000 А/м2. Размер частиц порошка зависит от катодной плотности тока и при ее величине в 3000 А/м2 не превышает 200–300 мкм.
Бронзовый порошок (92 % Сu и 8 % Sn) получают из лимонно-кислого электролита, содержащего CuCl2, SnCl2 и цитрат натрия (комплексообразователь) при соотношении ионов Cu2+/Sn2+ = 1,065; плотность тока 1 600 А/м2, температура электролита 30 °С, рН 2. Можно использовать триполифосфатный электролит, содержащий сульфат меди и хлорид олова.
Необходимо отметить, что опыт промышленного производства электролитических дисперсных порошков сплавов показывает сложность ведения процессов получения порошков сплавов. Это связано и со сложностью аппаратурного оформления процесса и с его нестабильностью.
Получениепорошковизпроизводственныхрастворов источныхводметаллургическихпредприятий
Последние десятилетия характеризуются бурным развитием металлургии, горного дела, металлообработки, машиностроения и особенно химической промышленности. Большое количество разбавленных растворов, содержащих ионы цветных металлов, образуется при выщелачивании руд и отвалов рудников. Громадный объем имеют и промышленные стоки металлургических заводов. Много растворов образуется также в гальванических цехах. Из указанных растворов в настоящее время извлекают многие цветные металлы, используя различные физико-химические методы, в том числе и электролиз. Наличие большого количества производственных растворов повышает требования к увеличению производительности соответствующих способов их переработки. Кроме того, организация извлечения металлов из сильно разбавленных растворов (концентрация металлических ионов < 1 г/л) является технически сложной.
Помимо важных экономических аспектов проблемы, отметим также экологическую сторону выбора способа очистки, так как по существующему в большинстве промышленно развитых стран законодательству имеются
Процессы порошковой металлургии. Курс лекций |
-146- |

I. ПОЛУЧЕНИЕ ПОРОШКОВ
Лекция 18 Получение порошков электролизом водных растворов
строгие ограничения по суммарному содержанию ионов металлов в сточных водах (в странах Западной Европы суммарное содержание цинка, кадмия, меди, железа, никеля не должно превышать 15 10-3 г/л). Такие высокие требования объясняются тем, что ионы цветных металлов, содержащихся в таких стоках, обладают комплексом токсических действий на человека, живую природу и микроорганизмы.
При переходе на современные методы хозяйствования и существующей остроте проблемы обеспечения промышленности сырьем извлечение металлов из разбавленных растворов становится важной технико-экономической задачей. В настоящее время таким образом можно дополнительно получить тысячи тонн цветных металлов, в основном в виде порошков. Особенно актуальна задача разработки и внедрения новых способов для извлечения золота из растворов флотации и гидрометаллургии золотоносных руд; для извлечения серебра из растворов от обработки кино- и фотоматериалов и из отработанных гальванических растворов; для выделения меди, цинка, кадмия, никеля, кобальта, марганца, олова, свинца, ртути из травильных растворов и сточных вод металлургических производств.
В последние годы разработаны принципиально новые электролитические способы извлечения металлов с применением высокоповерхностных электродов. Серьезные исследования привели к созданию в Англии, Франции, Германии, Швейцарии, Голландии, Японии, США и Испании, а также в нашей стране промышленных установок для проведения таких процессов. Их принципиальными преимуществами являются: большая площадь электродной поверхности, что позволяет значительно увеличить силу тока на ванне; высокая скорость массопереноса в объеме электролита, что резко снижает концентрационную поляризацию; возможность непрерывного ввода в процесс обрабатываемого раствора.
Техникабезопасностиприпроведенииработ
Производство порошков электролизом связано с влиянием на окружающую среду и обслуживающий персонал различных (специфических для электролизного производства) факторов опасного для жизни воздействия, к которым в первую очередь можно отнести возможность поражения работающих электрическим током и отравление персонала парами электролита. Правила техники безопасности требуют от рабочих соблюдения мер по охране труда как при работе с электролитом (приготовлении, транспортировке и пр.), так и при обслуживании электролизных ванн.
Категорически запрещается касаться токопроводящих шин на ваннах металлическими предметами, а тем более соединять ими главные токоведущие шины на серии или шины двух соседних серий. Несоблюдение этих требований может привести к удару током или ожогу от вольтовой дуги, возникающей при коротком замыкании.
Процессы порошковой металлургии. Курс лекций |
-147- |

I. ПОЛУЧЕНИЕ ПОРОШКОВ
Лекция 18 Получение порошков электролизом водных растворов
Во избежание ожогов перед включением серии ванн в работу тщательно зачищают рубильник и концы шин, а в момент включения плотно прижимают рубильник к шинам.
При временном разрыве электрической цепи на серии ванн с образованием вольтовой дуги запрещается подходить к этим ваннам, пока не снято напряжение с цепи, в которой произошел разрыв.
Нельзя складывать токопроводящие материалы у шин, питающих серии ванны.
Включение и выключение регенеративных ванн можно производить только при выключенной серии.
Запрещается выбрасывать катоды из работающей регенеративной ванны и проверять ее исправность металлическими инструментами, так как появление искры может вызвать взрыв или возгорание (на ванне одновременно выделяются кислород и водород!).
Зеркало электролита в регенеративных ваннах должно быть покрыто вспенивающимся материалом (например, маслом), предотвращающим распыление электролита в атмосферу цеха. При замене электродов на ваннах надо остерегаться их падения, в особенности при замене отработанных анодов.
В случае попадания на тело серной кислоты или электролита необходимо немедленно смыть их сильной струей воды или нейтрализовать содовым раствором.
Контрольныевопросыизадания
1.Назовите основные факторы процесса получения порошков из рас-
творов.
2.Какие типы электролизеров применяют при производстве порошков?
3.Как с электролизеров удаляют катодный осадок?
4.Из каких растворов получают порошки меди?
5.Перечислите основные технологические операции получения порошков металлов из растворов.
6.Опишите технологическую схему получения порошков железа электролизом водных растворов.
7.Как проводят операцию стабилизации металлического порошка после водной отмывки?
8.Чем объясняется ограниченное применение электролиза при получении порошков сплавов?
9.Что является альтернативным сырьевым источником получения порошков металлов?
Процессы порошковой металлургии. Курс лекций |
-148- |

I. ПОЛУЧЕНИЕ ПОРОШКОВ
Лекция 18 Получение порошков электролизом водных растворов
Лекция19 Получениепорошковэлектролизомрасплавленныхсред
План лекции
1. Факторы, определяющие процесс электролиза расплавленных со-
лей.
2.Получение порошка тантала.
3.Получение порошка ниобия.
4.Получение порошка титана.
5.Получение порошка циркония.
6.Получение порошка железа.
Факторы, определяющиепроцессэлектролизарасплавленныхсолей
Большинство металлических порошков из расплавов получают с использованием хлоридов, фторидов или смеси этих соединений. В герметичных электролизерах создают инертную газовую атмосферу (чаще всего аргон) или вакуум.
Структура катодных осадков зависит от условий их осаждения. При этом большое влияние на характер выделяемого осадка оказывают состав электролита, степень его чистоты, а также материал и состояние поверхности катода. Известно, что при наличии ничтожных следов влаги осадки выделяются в виде губки, а при содержании в электролите небольших количеств примесей железа или марганца образуются осадки в виде черного порошка.
Наличие выделяющегося при электролизе у анода хлора или фтора (при работе ванны с нерастворимым анодом) требует устройства диафрагм для предотвращения взаимодействия такого агрессивного реагента с электролитом или металлическим порошком.
Одним из способов освобождения порошков от находящегося вместе с ними электролита является удаление последнего отгонкой нагреванием или центрифугированием, а также отмыванием.
На выход по току влияют состав и температура электролита, плотность тока, расстояние между электродами и другие факторы.
Состав электролита. Этот фактор на выход по току оказывает наиболее сильное влияние. Одной из основных причин отклонения выхода по току от 100 % является растворимость металла в электролите с последующим окислением анодными продуктами, в связи с чем желательно ее понизить. Так, добавки солей с более электроотрицательными катионами по сравнению с выделяющимся на катоде металлом значительно понижают растворимость металла в расплавленном электролите и этим повышают выход по току.
Процессы порошковой металлургии. Курс лекций |
-149- |

I. ПОЛУЧЕНИЕ ПОРОШКОВ
Лекция 19 Получение порошков электролизом расплавленных сред
Напряжение разложения различных химических соединений металлов при сравнимых концентрациях (при активности каждого из соединений, равной единице) зависит от их химической прочности:
EТ = –∆GT/nF, |
(1.67) |
где ЕТ – напряжение разложения данного соединения металла при температуре Т; ∆GT – свободная энергия образования (энергия Гиббса) данного соединения металла при температуре Т; п – число электрических зарядов выделяемого металла, входящего в данное соединение; F – число Фарадея.
Температура электролита. Электролиз стараются вести при температурах, превышающей температуру плавления компонентов электролита, но ниже температуры плавления выделяемого на катоде металла. Образующиеся продукты реакции (соединения металлов пониженной валентности) обладают высокой упругостью паров, следовательно, с увеличением температуры электролита потери металлов возрастают и по этой причине. Кроме того, с повышением температуры возрастает циркуляция электролита в ванне, способствующая уносу металлов, растворенных в нем после их выделения на катоде, в анодное пространство.
Часто для снижения температуры плавления электролита в него вводят добавки солей (обычно хлористые и фтористые соединения щелочных и щелочно-земельных металлов), у которых катионы электроотрицательнее выделяемого металла.
Плотность тока. Выход по току растет с увеличением плотности тока. Поэтому оптимальное значение плотности тока будет соответствовать наибольшему выходу по току, при котором уменьшение потерь выделяемого металла вследствие его вторичного растворения в электролите не будет сопровождаться сильным повышением разряда катионов металла с более электроотрицательным потенциалом.
Однако слишком высокая плотность тока увеличивает падение напряжения в слое электролита и повышает расход электроэнергии. Кроме того, при высоких плотностях тока возможно также протекание побочных процессов – выделение на катоде наряду с основным металлом другого, более электроотрицательного металла, присутствующего в электролите.
Межэлектродное расстояние. В связи с наличием факторов, вызывающих потери металла при электролизе расплавленных солей (растворением выделенного металла, переносом его от катода к аноду и взаимодействием растворенного металла с газами, образующимися на аноде), расстояние между электродами тоже влияет на выход по току.
С увеличением межэлектродного расстояния перенос растворенного металла от катода к аноду диффузией, конвекцией и циркуляцией затрудняется вследствие удлинения пути перемещения металла, уменьшения градиента концентрации растворенного металла в межэлектродном пространстве, а также из-за уменьшения скорости циркуляции электролита при большем объеме расплава, приводимого в движение одним и тем же количеством
Процессы порошковой металлургии. Курс лекций |
-150- |

I. ПОЛУЧЕНИЕ ПОРОШКОВ
Лекция 19 Получение порошков электролизом расплавленных сред
анодных газов. В результате абсолютные потери металла уменьшаются, а выход по току возрастает.
Анодный эффект. Анодным эффектом называют явление резкого возрастания напряжения на ванне с одновременным падением силы тока и появлением характерных искровых разрядов на аноде. При возникновении анодного эффекта электролит оказывается отделенным от поверхности анода прослойкой выделяющегося на нем газа, т.е. наблюдается ухудшение смачиваемости анода электролитом.
Увеличение в электролите концентрации поверхностно-активных веществ, хорошо смачивающих анод и имеющих небольшое поверхностное натяжение на границе раздела электролит – анод (хлоридов щелочных металлов или растворимых оксидов), приводит к повышению критической силы тока, вызывающей анодный эффект. Это особенно важно для электролизеров, в которых анод, имеющий сравнительно небольшую рабочую поверхность, выполнен из углеграфитовых материалов.
Получениепорошкатантала
Порошок тантала в промышленных масштабах получают с 1922 г. (США). Электролитом чаще всего служит оксифторидный или оксифторид- но-хлоридный солевой расплав, состоящий из фторотанталата калия K2TaF7 (электролиз одного расплавленного фторотанталата калия невозможен из-за возникающего непрерывного анодного эффекта), хлористого и/или фтористого калия (натрия), в котором растворен пентаоксид тантала. Напряжение разложения ЕТ компонентов такого электролита при 750 °С составляет, В: 1,65 для Та2О5; 2,0 для TaF5; 3,4 для КСl; 4,65 для KF. При использовании графитового анода напряжение разложения Та2О5 понижается до 1,41 В за счет вторичного процесса на аноде – образования СО2 и СО, сопровождающегося выделением энергии.
Смесь фторида и хлорида калия обеспечивает легкоплавкость, жидкотекучесть и хорошую электропроводность электролита, а пентаоксид тантала улучшает смачивание графитового анода расплавом. Катод может быть молибденовый, никелевый, нихромовый, чугунный или стальной.
Указанный выше четырехкомпонентный электролит является сложной химической системой, которую можно рассматривать как четверную взаимную систему К, Та || F, О, О.
В расплаве K2TaF7 + КС1 + KF происходит взаимодействие K2TaF7 + KF = = K3TaF8 и K2TaF7 + КС1 = K3TaF7Cl, в связи с чем в электролите нет свободного K2TaF7.
После добавления к расплаву Та2О5 идет реакция его растворения, которую суммарно можно записать как 3K3TaF8 + Та2О5 + 6KF = 5K3TaOF6, или
K3TaF8 + 2Та2О5 + 12KF = 5K3TaО2F4.
Аналогичная реакция возможна и с K3TaF7Cl. Соединения K3TaOF6 и KTaО2F4 неограниченно растворимы в расплавленных KF и K3TaF8.
Процессы порошковой металлургии. Курс лекций |
-151- |

I. ПОЛУЧЕНИЕ ПОРОШКОВ
Лекция 19 Получение порошков электролизом расплавленных сред
Таким образом, в оксифторидно-хлоридных электролитах существуют ионы К+, Cl-, F-, TaF83-, TaОF63- (при содержании в электролите Та2О5 < 5 %) или TaО2F3- (при содержании в электролите > 5 % Ta2О5), TaF7Cl3- и др., в том числе Та5+, образующиеся в результате частичной диссоциации указанных трехвалентных оксифтортанталовых анионов.
На катоде идет разрядка ионов Та5+:
Та5+ + 5ё → Та (Та5+ + 2ё → Та3+ + 3ё→ Та).
Схема анодного процесса может быть такой:
TaOF63- – 2ё = TaF5 + F-+ 0,5О2
(так как О2- – 2ё → 0,5О2).
Электролизу в конечном счете подвергается Та2О5, вводимый в расплав. Реакция окисления графита на аноде, сопровождающаяся выделением энергии, приводит к его деполяризации, снижая количество энергии, требующейся для разложения Та2О5.
Обычно в состав электролита входят, %: 2,5–8,5 Та2О5 (преимущест-
венно 3–5); 8,5–32,5 KТaF; 27,5–57,5 KF; 25,5–55 КС1. Хлористый калий в смеси с KF снижает температуру плавления электролита, а без KF нужно большое количество KTaF7 для обеспечения растворения в нем K3TaOF6 или
K3TaО2F4.
На практике для получения тантала используют электролит (с низкой вязкостью и летучестью), температура плавления которого всего 600 °С (это позволяет вести электролиз при 700 °С). Этот электролит имеет состав, %:
3,0–3,5 Та2О5; 25–30 K2TaF7; 66,5–72,0 NaCl + KCl. В процессе электролиза идет снижение содержания в нем Та2О5. При обеднении электролита по Та2О5 до 1,5–2,0 % возможно проявление анодного эффекта.
Электролизеры могут быть двух типов: графитовый тигель (анод) и металлический стержень (катод), опускаемый в центр тигля, или металлический тигель (катод) и анод в виде графитового стержня или полой перфор и- рованной трубки в центре тигля.
Второй вариант электролизера предпочтительнее, так как в нем Та2О5 подают в ванну через полый анод при помощи автоматического питателя, газы отсасываются через отверстие в боковой стенке электролизера, а электролиз проводят при напряжении 2,5–7,0 В и плотности тока на катоде 3000–5 000 А/м2, а на аноде 12 000–16 000 А/м2. При электролизе на дне и стенках тигля осаждается тантал в форме дендритов. Процесс прекращают при заполнении катодным осадком 2/3 объема тигля. После этого анод поднимают, и электролит вместе с катодным осадком охлаждают. Частицы танталового порошка ока-
Процессы порошковой металлургии. Курс лекций |
-152- |

I. ПОЛУЧЕНИЕ ПОРОШКОВ
Лекция 19 Получение порошков электролизом расплавленных сред
зываются вкраплены в застывший электролит, который является своеобразной защитой тантала от окисления при остывании. Размер частиц порошка составляет 30–120 мкм.
Для выделения порошка тантала обычно катодный продукт дробят в шаровой мельнице, работающей в замкнутом цикле с воздушным сепаратором. В процессе такой обработки сухая смесь составных частей электролита отделяется и может быть непосредственно вновь использована для загрузки в ванну для проведения электролиза. Оставшийся электролит отмывают от порошка тантала на концентрационных столах в струе воды. После этого танталовый порошок обрабатывают в фарфоровых реакторах горячей смесью соляной и азотной кислот (в которой он не растворяется) с целью отмывки примесей молибдена или железа, промывают водой и высушивают.
В бывшем СССР разработан вакуум-термический способ отделения порошка тантала, в котором тигель-катод помещают в специальную реторту, откачивают, заполняют аргоном и при 1 000 °С выплавляют электролит. Затем в тигле создают разряжение, и остаток солей отделяют испарением. На стенках тигля остаются слабоспекшиеся дендриты тантала, которые счищают и измельчают в порошок. Выплавленный электролит возвращают на электролиз. Получаемый электролитический порошок тантала отличается высокой чисто-
той, %: 0,03–0,1 Fe + Ni; 0,03–0,2 С; 0,1–0,2 О; 0,01 F; < 0,1 Si; < 0,01 Ti. Вы-
ход по току составляет 80–83 %, а расход электроэнергии – 2 300 кВт·ч/т. Танталовый порошок может быть получен электролизом расплавов,
содержащих ТаС15 (хлоридный способ). В расплав (NaCl + NaF, NaCl + KCl, NaCl + KCl + KF) с температурой 750–950 °C вводят жидкий или парообразный пентахлорид тантала (в расчете на содержание < 10 % Та).
Напряжение на ванне 6–8 В, катодная плотность тока 27 000 А/м2, анодная плотность тока 2 000 А/м2. Выход по току достигает 85–88 %. Получаемый танталовый порошок достаточно мелкозернист и химически весьма чист (> 99,9 % Та, < 0,02 % О).
Получениепорошканиобия
Хотя крупнотоннажное промышленное производство порошка ниобия электровыделением из расплавов не осуществляют в силу ряда объективных и субъективных причин, физико-химические основы электролиза изучены достаточно полно.
Применяют два типа электролитов: K2NbF7–KCl–KF–Nb2О5 и K2NbF7– –KCl–NaCl (используемый для получения или рафинирования ниобия). В расплаве первого из указанных электролитов до введения Nb2О5 происходит взаимодействие по реакциям K2NbF7 + KF = K3NbF8 и/или K2NbF7 + KCl = = K3NbF7Cl. При добавлении пентаоксида ниобия в присутствии избытка
Процессы порошковой металлургии. Курс лекций |
-153- |
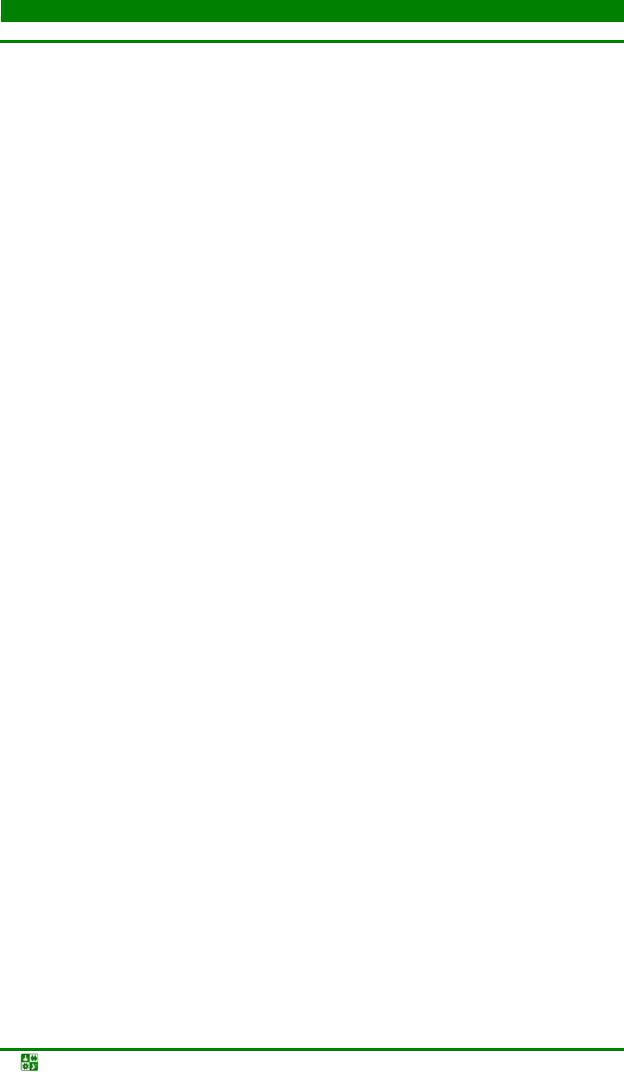
I. ПОЛУЧЕНИЕ ПОРОШКОВ
Лекция 19 Получение порошков электролизом расплавленных сред
KF происходит реакция K2NbF7 + 13KF + 2Nb2О5 = 5K3NbО2F4. Таким образом, в рассматриваемом электролите присутствуют комплексные ниобийсодержащие ионы предположительно вида NbF83–, NbF72– и NbO, F43–. В электролите для рафинирования ниобия его единственным соединением будет K3NbF7Cl, которое диссоциирует на К+, Cl– и NbF72–.
Процесс получения ниобия электролизом оксифторидных расплавов известен с начала 30-х гг. (патенты США 1931 и 1933 гг.) и имеет большое сходство с получением электролитического порошка тантала: очищенные соли расплавляют в никелевом тигле (катоде) и в расплав вводят Nb2О5; анод – графитовый стержень; температура электролита около 750 °С; напряжение на ванне 2,5 В, катодная плотность тока 5 000–6 000 А/м2, выход по току не превышает 30 %. Получаемый осадок крупнозернист и, как правило, загрязнен низшими оксидами ниобия.
Более чистые порошки получают электролизом в хлоридных (NaCl + + KC1) и хлоридно-фторидных (NaCl + NaF, KC1 + NaCl + KF и др.) расплавах с питанием ванны NbCl5 (из расчета 2–3 % Nb в электролите).
В нашей стране порошки ниобия получают в электролите состава: КС1 + NaCl + NaF, насыщаемом парами NbCl5 до содержания 5–8 % Nb. Температура электролита составляет 680–720 °С, катодная плотность тока – 10 000–20 000 А/м2. Выход по току не превышает 60 %. Электрорафинированием в электролите K2NbF7 + KC1 + NaCl при 700–750 °С и катодной плотности тока 1 000–8 000 А/м2 удается получать порошок ниобия, содержание примесей в котором по сравнению с анодным материалом понижено по железу на 1–3, по кремнию на 1–1,5, по углероду на 1–1,5 и по кислороду на 1 порядок.
Получениепорошкатитана
В начале XX в. были предприняты первые попытки электролитического получения титана, а в середине XX в. объем исследований по этой проблеме резко возрос. В настоящее время существует обоснованное мнение об экономической нецелесообразности крупнотоннажного получения титана из его соединений (TiCl4, TiО2 и др.) в хлоридных и фторидных электролитах с применением нерастворимого (графитового) анода, хотя около сорока лет тому назад некоторые фирмы США сообщали о готовности к промышленному внедрению технологии электровыделения титана из его тетрахлорида.
Процессы порошковой металлургии. Курс лекций |
-154- |

I. ПОЛУЧЕНИЕ ПОРОШКОВ
Лекция 19 Получение порошков электролизом расплавленных сред
|
|
|
|
|
|
|
Отходы Ti |
Отработанный |
||||||||
NaCl |
|
|
KCl |
TiCl4 |
электролит магниевого |
|||||||||||
|
|
|
|
|
|
|
производства |
|||||||||
Прокалка |
Ar |
|
Сушка |
|
|
|
|
|
||||||||
|
|
|
|
|
|
|||||||||||
|
Очистка |
|||||||||||||||
|
|
|
|
|
|
|
|
|||||||||
|
|
|
|
|
|
|
|
|
|
|
|
|
|
|
|
|
Смешивание |
Приготовление низших |
|
|
|
|
|
|
|
||||||||
|
|
|
|
|
|
|
||||||||||
|
|
|
|
|
|
|
|
|
|
|
|
|
||||
Плавка |
хлоридов |
|
|
|
|
|
|
|
||||||||
|
|
|
|
|
|
|
|
|
|
|
||||||
|
|
|
|
|
|
|
|
|
|
|
|
|
|
|
|
|
|
|
|
|
|
|
Электролитическое рафинирование |
||||||||||
|
|
|
|
|
|
|||||||||||
|
|
|
|
|
|
|
|
|
|
|
|
|
|
|
|
|
|
|
|
|
|
|
|
Катодный осадок |
|
|
|
|
|
||||
|
|
|
|
|
|
HCl |
Дробление |
|
|
|
|
|
||||
|
|
|
|
|
|
Выщелачивание |
|
|
|
|
|
|
||||
|
|
|
|
|
|
H2O |
|
|
|
|
|
|
||||
|
|
|
|
|
|
|
|
|
|
|
|
|||||
|
|
|
|
|
|
|
|
|
|
|
|
|
|
|
|
|
|
|
|
|
|
|
|
Фильтрация |
|
|
|
|
|
|
|||
|
|
|
|
|
|
|
|
|
|
|
|
|
||||
|
|
|
|
|
|
Классификация фракций |
|
|
|
|
|
|||||
|
|
|
|
|
|
|
|
|
|
|
||||||
|
|
|
|
|
|
|
|
|
|
|
|
|
|
|||
|
≥0,18 мм |
|
|
|
|
|
|
|
|
|
|
|
||||
|
|
Сушка |
|
|
<0,18 мм |
|
|
|
|
|
||||||
|
|
|
|
<0,63 мм |
Кислые стоки |
|||||||||||
|
|
Рассев |
||||||||||||||
|
|
|
|
|
|
≥0,18 мм |
|
|
|
|
|
|||||
|
|
≥0,1мм |
|
|
|
|
|
|
|
|
|
|
|
|||
На выплавку серийных сплавов |
Затаривание |
Утилизация |
Рис. 1.30. Принципиальная технологическая схема производства порошка титана электролитическим рафинированием его отходов
Принципиальная технологическая схема производства порошка титана электролитическим рафинированием его отходов включает следующие операции (рис. 1.30):
1)подготовка компонентов электролита, их плавление и загрузка в электролизер;
2)электролитическое рафинирование;
3)удаление и дробление катодного осадка;
4)выщелачивание остатков электролита;
5)классификация и сушка полученных порошков.
Растворимый анод выполняют из сыпучих (дробленых или измельченных до крупности 5–40 мм) либо измельченных и сбрикетированных титансодержащих материалов. В качестве солевой основы электролита выби-
рают системы типа КС1 + NaCl, KCl + NaCl + MgCl2 или KCl + NaCl + LiCl.
Процессы порошковой металлургии. Курс лекций |
-155- |

I. ПОЛУЧЕНИЕ ПОРОШКОВ
Лекция 19 Получение порошков электролизом расплавленных сред
В растворе также будет находиться небольшое количество низших хлоридов титана, растворение которых в хлористом калии приводит к образованию комплексных соединений K3TiCl6 и KTiCl4 в системе KCl–TiCl3, а также K2TiCl4 и KTiCl3 в системе KCl–TiCl2. Аналогичные соединения образуются в хлористом натрии.
Электролиз ведут при температуре 800–850 °С в атмосфере аргона. При анодном растворении титан переходит в электролит в виде ионов Ti2+ и Ti3+; обычно средняя валентность титана в электролите 2,2–2,3, а концентрация ионов титана в нем 3–6 %. Катод целесообразно изготовлять из жаростойких сталей (например, 1Х18Н10Т).
Напряжение на ванне около 6 В; начальная катодная плотность тока 5 000–15 000 А/м2; анодная плотность тока должна быть в 4–8 раз меньше катодной.
Катодный осадок срезают специальным ножом, измельчают до < 5 мм, отделяют от электролита кислотным (1 %-м водным раствором НС1) выщелачиванием, промывают, размалывают, классифицируют и сушат, например,
ввакуумном сушильном шкафу при 65 °С. Выход по току достигает 90 %, а расход (суммарный) электроэнергии составляет 10–11 кВт·ч/кг.
Впроцессе электролиза примесь кислорода остается в анодном шламе
вформе оксидов титана (ТiO2, Ti2О3). Углерод находится в свободном состоянии на поверхности электролита или в анодном остатке в виде карбида. Азот содержится в анодном остатке в виде нитрида или выделяется с анод-
ными газами; кремний удаляется с газами в виде SiCl4.
Получаемый порошок титана отличается высокой чистотой (не ме-
нее 99,7 %) и содержит, % (не более): 0,1 О, 0,05 N и 0,05 Fe.
Электрорафинирование сплавов на основе титана является более трудной задачей, хотя и проводится практически при тех же условиях электролиза, что и рафинирование отходов титана. Отделение титана от металлических примесей основано на различии их электродных потенциалов. Ниже приведены значения стандартных потенциалов титана и основных легирующих металлов по отношению к серебряному электроду в хлоридных расплавахNaCl + KC1 при активности ионов, близкой к единице, и температуре 850 °С, В:
Mn/Mn2+ |
Zr/Zr2+ |
Ti/Ti2+ |
A1/A12+ |
V/V2+ |
Cr/Cr2+ |
Fe/Fe2+ |
Mo/Mo3+ |
–1,41 |
–1,36 |
–1,36 |
–1,24 |
–1,08 |
–0,97 |
–0,88 |
–0,65 |
Приведенные данные показывают, что титан можно отделить от большинства этих металлов (за исключением Мn и Zr) в условиях, близких к обратимым, особенно если учесть, что содержание каждого из легирующих металлов в титановом сплаве колеблется от 1 до 10 %.
При этом необходимо иметь в виду, что на степень очистки влияют значительная поляризация, в основном определяемая перепадом концентраций ионов титана в порах растущего шламового слоя по мере выработки титана из анода, уменьшение концентрации титана в поверхностных слоях анода и экранирование анода шламовым слоем. Это приводит при определенных
Процессы порошковой металлургии. Курс лекций |
-156- |

I. ПОЛУЧЕНИЕ ПОРОШКОВ
Лекция 19 Получение порошков электролизом расплавленных сред
степенях выработки анода к растворению в электролите вместе с титаном более электроположительных примесей и их осаждению на катоде совместно с титаном.
Электролитическим рафинированием анодных материалов соответствующих составов можно получать и порошки сплавов на основе титана, например сплавов Ti–A1.
Получениепорошкациркония
Электролиз проводят в расплаве NaCl или КС1, содержащем K2ZrF6. Хлористый калий предпочтительнее: напряжение разложения КС1 выше, чем NaCl; у электролита на основе КС1 анодный эффект на графитовых анодах возникает лишь при большой плотности тока; смесь 70 % КС1 + 30 % K2ZrF6 (содержание Zr около 10 %) плавится при 730 °С, что позволяет проводить электролиз при 750–800 °С; растворимость в воде образующегося при электролизе KF больше, чем у NaF, что облегчает отделение электролита от катодного осадка (порошка циркония).
В электролизере у катода (стальной) протекают реакции
ZrF62- → Zr6+ + 6F-,
Zr6+ + ё → Zr3+ + ё → Zr2+ + 2ё → Zr.
У анода разряжаются ионы фтора, но элементарный фтор тотчас же реагирует с ионами натрия или калия:
4F- + 4KCl(4NaCl) – 4ё = 4KF(4NaF) + 2Cl2↑
В результате протекающих реакций в ванне электролизера постепенно накапливается фторид калия или натрия, хотя этот процесс протекает сравнительно медленно, так как значительное количество фторида извлекается из ванны вместе с катодным осадком (время наращивания 2,0–2,5 ч).
Оптимальная катодная плотность тока для электролита 25+30 % К2ZrF6 + + 75+70 % КС1 составляет 35 000–45 000 А/м2. Катодный осадок содержит около 30 % порошка циркония с размером частиц 50–200 мкм, остальное – соли электролита. Его удаляют с катода, дробят и обрабатывают водой, подкисленной соляной кислотой, промывают и сушат в вакууме при 50–60 °С.
Для получения порошка циркония высокого качества исходные фтороцирконат калия и хлористый калий также должны быть высокого качества, а процесс электролиза проводят в атмосфере чистого аргона.
Процессы порошковой металлургии. Курс лекций |
-157- |
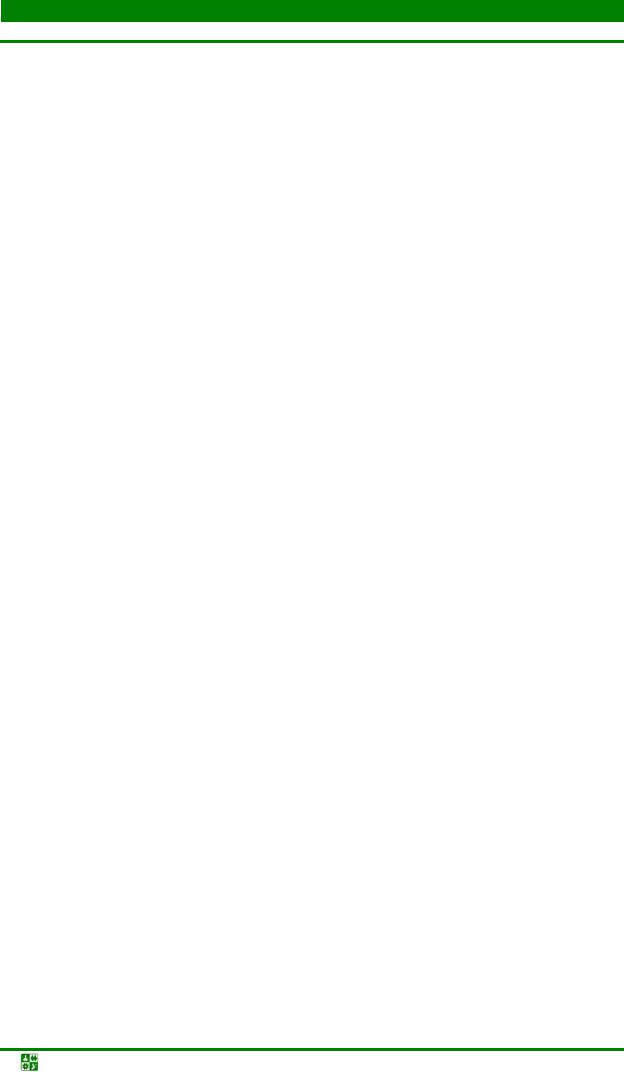
I. ПОЛУЧЕНИЕ ПОРОШКОВ
Лекция 19 Получение порошков электролизом расплавленных сред
Получениепорошкажелеза
Для электровыделения железа используют растворимые аноды из губчатого железа (< 95 % Fe), чугуна (< 90 % Fe) или рудно-угольных окатышей (Fe3О4 + С). Электролитом служат расплавы КС1 + NaCl или КС1 + NaCl + MgCl2, в которых растворен FeCl2 в количестве до 12–14 %. Такой электролит может быть приготовлен плавлением в реторте из нержавеющей стали при 800– 850 °С (в аргоне) смеси NaCl (22 %), КС1 (30–31 %), MgCl2 (33–36 %) и без-
водного FeCl3, к которой добавлен порошок чистого железа для переводаFeCl3 в FeCl4. В процессе электролиза, который ведут в атмосфере азота при 750–900 °С, убыль катионов железа восполняется поступлением ионов железа с растворяющегося анода. В электролите имеется набор катионов железа различной валентности: 87–91 % Fe2+, 8–12 % Fe3+ и примерно 1 % Fe+. Катод железный, напряжение на электролизере 6 В, катодная плотность тока < 50 000 А/м2, а анодная плотность тока на порядок меньше катодной.
Процесс наращивания катодного осадка ведут циклически с остановкой через 1–2 ч для его съема. Выход по току составляет 80–90 %. После извлечения из электролизера катодный осадок (механическая смесь губчатого железа и электролита в соотношении примерно 1:1) измельчают до крупности < 0,5 мм и подвергают магнитной сепарации (немагнитная фракция – возвратный электролит), после чего порошок отмывают от остатков электролита, высушивают, отжигают в водороде и классифицируют. Чистота порош-
ка (99,9–99,94 % Fe; < 0,05 % О; < 0,005 % С; < 0,002 % Р; 0,01 % Si; < 0,01 %
Мn) обеспечивает его высокие технологические свойства.
Существует возможность прямого получения железа из рудных концентратов или оксидов железа, вводимых в расплавленный железный криолит Na3FeF6, в электролизере с анодами из электродного графита или карбида кремния при 850–870 °С в атмосфере азота или аргона. Катодная плотность тока составляет 8 000–20 000 А/м2, анодная – от 2 000 до 8 000 А/м2. Поведение примесных оксидов в процессе электролиза определяется главным образом соотношением напряжений разложения этих оксидов и оксидов железа. По расчетным данным совместное с железом осаждение на катоде кремния, алюминия, марганца и магния невозможно до определенной минимальной концентрации оксидов железа в расплаве, равной 10 %. Выход по току может достигать 85 %. Катодный осадок обрабатывают как указано выше. Получаемый порошок железа имеет крупность частиц < 200 мкм и содержит, %: 99,5–99,7 Fe; < 0,25 SiО2; < 0,02 С; < 0,15 О; < 0,003 Р.
Контрольныевопросыизадания
1.Почему порошки некоторых металлов получают не из растворов, а из расплавов солей?
2.Какие факторы определяют характер осадков, получаемых при электролизе расплавленных сред?
Процессы порошковой металлургии. Курс лекций |
-158- |
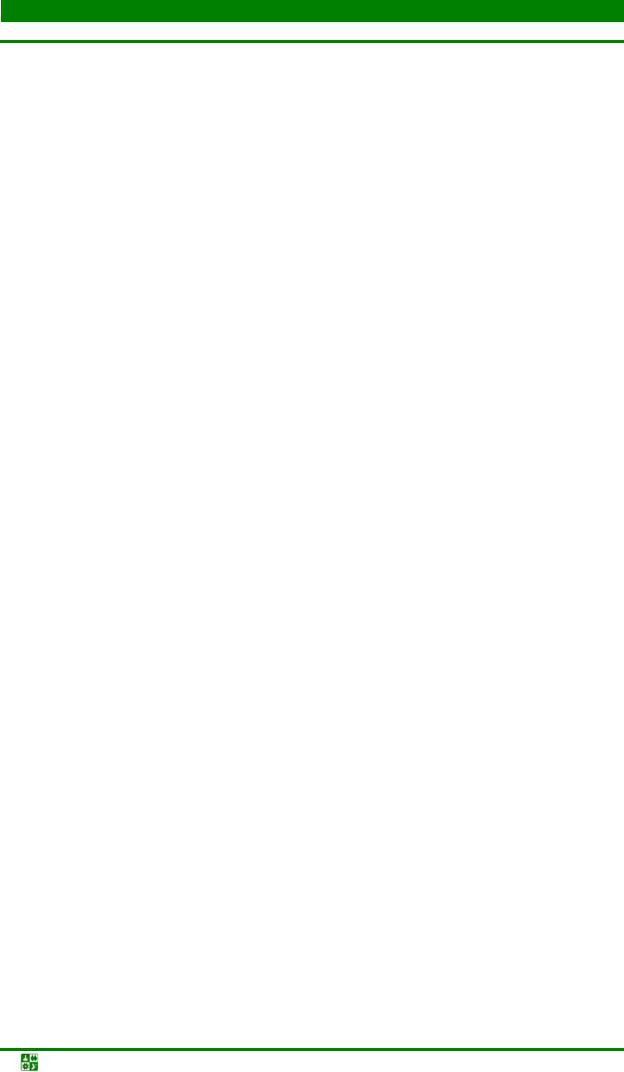
I. ПОЛУЧЕНИЕ ПОРОШКОВ
Лекция 19 Получение порошков электролизом расплавленных сред
3.Какое влияние оказывает наличие следов воды на свойства получаемых порошков?
4.Перечислите основные операции технологий получения порошков титана, ниобия, тантала и циркония.
5.В чем заключается особенность отмывки порошков, полученных электролизом расплавленных сред от электролита?
6.Расскажите о вакуум-термическом способе отделения порошка тантала от электролита.
7.Какие основные компоненты входят в состав электролитов при электролизе расплавленных сред?
8.Опишите конструкцию электролизеров для получения порошков титана, тантала, циркония.
9.В каких средах ведут электролиз расплавленных солей металлов?
10.Назовите средние размеры частиц порошка, получаемого электролизом расплавленных сред.
Лекция20 Получениепорошковметалловметодом
термическойдиссоциациикарбонилов
План лекции
1.Технология карбонил-процесса.
2.Строение и классификация карбонилов.
3.Получение порошков никеля и железа.
4.Получение порошков вольфрама и молибдена.
Технологиякарбонил-процесса
Карбонильный металлический порошок – металлический порошок,
полученный разложением карбонильных соединений металлов. Карбонилами металлов называют химические соединения металлов с
группами (лигандами) СО. Схематически карбонильный метод (карбонилпроцесс) получения порошков может быть представлен как химическая транспортная реакция:
МеаБb + сСО → [bБ] + Меа(СО)с → аМе + сСо
где Me – переходный металл V–VIII групп периодической системы; Б – балластные вещества (кислород, солевой остаток, примеси и т.п.); а, b, с – коэффициенты, численные значения которых зависят от природы Me.
Процессы порошковой металлургии. Курс лекций |
-159- |
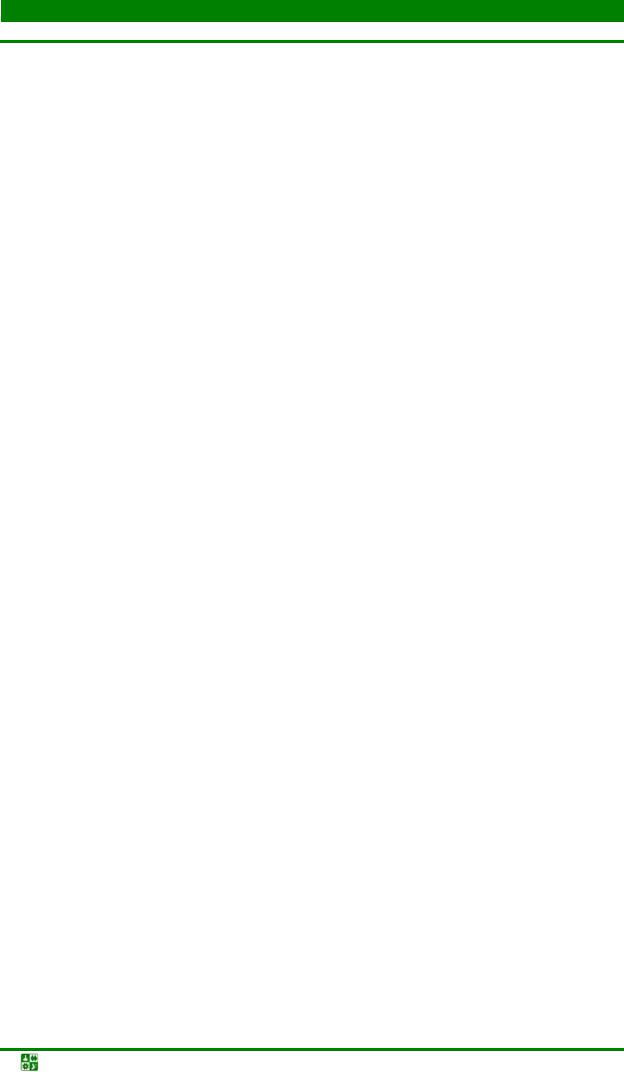
I. ПОЛУЧЕНИЕ ПОРОШКОВ
Лекция 20 Получение порошков металлов методом термической диссоциации карбонилов
Сначала (синтез) исходное сырье МеБb взаимодействует с СО и соответствующий металл Me образует промежуточный продукт – карбонильное соединение Меа(СО)с, которое отделяется от балластной примеси Б и собирается в чистом виде. Затем (стадия термического разложения) полученный карбонил металла при нагреве диссоциирует с выделением чистого металла Me и СО.
Технологически карбонил-процесс основывается на обратимой реакции
аМе + сСО ↔ Меа(СО)с
Вего первой фазе (синтез) реакция идет слева направо с образованием карбонила металла и является всегда экзотермической; во второй фазе процесса (термическое разложение, т.е. диссоциация) реакция идет справа налево с образованием металла и СО и всегда эндотермична.
Процесс образования карбонила Меа(СО)с тесно связан с диффузионными процессами:
с диффузией СО из газовой фазы к поверхности твердого тела; с диффузией молекул образующегося карбонила из глубины твердого
тела к его поверхности, а затем в газовую фазу.
Эффективная площадь поперечного сечения всех трещин и пор у ис-
ходного твердого материала МеаБb непрерывно увеличивается по мере извлечения металла Me со стенок пор и трещин в карбонильную фазу. Изменение площади поперечного сечения пор во времени зависит от многих причин: от состава исходного твердого материала, термической обработки, условий синтеза карбонила и др.
Вто же время опыт показывает, что диффузия СО вглубь твердого материала распространяется, как правило, сплошным фронтом, параллельным внешней поверхности твердого материала. Следовательно, скорость
реакции образования карбонила Меа(СО)с значительно превосходит скорость диффузии СО к реакционной поверхности, которая и лимитирует общий ход процесса.
На образование карбонила металла большое влияние оказывают температурные условия, а также наличие веществ, тормозящих или ускоряющих реакцию. В некоторых случаях при взаимодействии СО с твердым исходным материалом возможно одновременное образование нескольких карбонилов.
Строениеиклассификациякарбонилов
Строение карбонилов металлов объяснимо только с помощью координационной теории, разработанной для комплексных соединений, так как многочисленные попытки объяснить структуру карбонилов металлов в соответствии с положениями, правильными для классических типов связей (ионной, полярной и неполярной), не дали положительных результатов.
Процессы порошковой металлургии. Курс лекций |
-160- |

I. ПОЛУЧЕНИЕ ПОРОШКОВ
Лекция 20 Получение порошков металлов методом термической диссоциации карбонилов
В карбонилах металлов, являющихся координационными соединениями, группа СО как донор электронов занимает одно координационное место и присоединяется через атом углерода непосредственно к металлу координативной одинарной связью. Химическая связь в карбонилах металлов обусловливается сближением атомов металла с атомами углерода лигандов СО. Движение электронов в этих атомах изменяется в сторону увеличения электронной плотности в пространстве между ними с одновременным частичным обобществлением электронов, так как они становятся общими для атомов металла и углерода.
Карбонилы металлов могут быть моно- и полиядерными. Н. Сиджвик предложил использовать понятие эффективного атомного номера (ЭАН – число электронов в конфигурации атома инертного газа, замыкающего тот ряд периодической системы элементов, в котором помещается соответствующий металл, образующий карбонил) для описания строения истинных карбонилов: разность между ЭАН и атомным номером металла показывает количество электронов, которое необходимо приобрести металлу-акцептору у лигандов СО (доноров). Приобретая недостающие электроны, атом метал- ла-комплексообразователя притягивает к себе соответствующее количество лигандов СО, образуя устойчивое соединение с электронной структурой, подобной стоящему за ним ближайшему инертному газу.
В целом в карбонилах металлов возможно существование четырех типов связей:
1)координационно-ковалентная связь Me–СО, при которой атом С отдает металлу электронную пару (σ-связь) и дополнительно связывается с металлом обратной π-связью с участием d-электронов металла;
2)ковалентная связь Me–Me в биметаллических карбонилах, при которой каждый атом металла поставляет для связи один электрон;
3)ковалентная σ-связь между металлом и СО, при которой атом С служит мостиком между двумя атомами металла, образуя связь с каждым из них;
4)связь Me–СО, при которой СО служит мостиком между тремя ат о-
мами металла; эта связь имеется в карбонилах типа Ме6(СО)16, не подчиняющихся правилу ЭАН.
По структурному признаку карбонилы металлов можно разделить на одноядерные и многоядерные.
Одноядерные имеют один атом металла в молекуле (например, Fe(CO)5,
Ni(CO)4, Me(CO)6 и др.).
Общая формула многоядерных карбонилов – Меа(СО)с. Они могут быть: монометаллические – с двумя или более одинаковыми атомами ме-
талла в молекуле (например, Со2(СО)8, Fe2(CO)9, Fe3(CO)12 и др.); полиметаллические – с двумя или более разными атомами металлов в
молекуле (например, Mn2Fe(CO)14, FeRu(CO)12, MnReFe(CO)14 и др.);
смешанные – с атомами металлов и неметаллов (например, CFe5(CO)15
CRu6(CO)17, SCo(CO)9 и др.).
Процессы порошковой металлургии. Курс лекций |
-161- |

I. ПОЛУЧЕНИЕ ПОРОШКОВ
Лекция 20 Получение порошков металлов методом термической диссоциации карбонилов
Летучесть карбонилов обусловлена атомной конфигурацией их молекул, расположением электрического поля в каждой молекуле и зависит от сил сцепления молекул между собой.
Межатомные связи в карбонилах значительно ослаблены из-за использования металлом «чужих» электронов, приобретаемых ими от лигандов СО, которые сами постоянно «перетягивают» электроны от атомов металлов. Это является причиной того, что карбонилы легко разрушаются при сравнительно низких температурах. При термическом воздействии на карбонилы электроны стремятся занять исходное положение, атом металла из возбужденного состояния стремится перейти в нейтральное, что делает карбонилы исключительно удобными исходными объектами для получения металлов путем термической диссоциации по схеме
Меа(СО)с → аМе + сСО
Термическая диссоциация карбонилов наступает еще до достижения ими температуры кипения, что объясняется особым характером взаимодействия между металлами-комплексообразователями и лигандами СО: при нагреве у карбонилов имеет место локальное вытягивание электронных орбит у отдельных лигандов СО, причем эта деформация лигандов сопровождается изменением квантовых чисел. Прочность химических связей в карбонилах металлов выражают двумя способами: средней энергией связи Е или средней энергией диссоциации связи Ед, причем чаще применяют второй способ.
С ростом прочности связи Me–СО повышается и температура, необходимая для термической диссоциации соответствующего карбонила металла. Именно связь металл–лиганды СО предопределяет основные физические свойства карбонилов.
Почти все карбонилы металлов диамагнитные и не обладают дипольным моментом. Исключение составляет карбонил ванадия, который парамагнитен.
Большинство карбонилов металлов высокотоксичны. Особенно ядовиты тетракарбонил никеля Ni(CO)4 и пентакарбонил железа Fe(CO)5. Изменения упругости пара р, мм рт. ст., при изменении температуры Т могут быть описаны для некоторых из карбонилов металлов зависимостями типа
lgp = А~ВТ-1.
Распад молекул карбонила приводит в первый момент к появлению атомов металла и газообразных молекул СО. Дальнейшее формирование агрегатов (частиц) всегда начинается с кристаллизации парообразного металла, состоящей из двух этапов: сначала образуются зародыши, а затем, когда зародыши достигнут критического размера 4–20 нм, формируются металличе-
Процессы порошковой металлургии. Курс лекций |
-162- |

I. ПОЛУЧЕНИЕ ПОРОШКОВ
Лекция 20 Получение порошков металлов методом термической диссоциации карбонилов
ские частички (агрегаты, кристаллы) за счет термического распада на поверхности зародышей оставшихся паров карбонила.
На скорость образования зародышей в единице объема и на скорость формирования металлических кристаллов влияют:
степень разрежения в аппарате; плотность (концентрация) паров образующегося металла; температура.
При относительно низкой температуре образуется значительно меньше зародышей, чем при повышенной, а увеличение плотности пара металла и более глубокое разрежение в аппарате способствуют образованию зародышей.
Условия развития зародышей значительно отличаются от условий их образования, хотя скорость роста кристаллов также зависит от температуры процесса и плотности паров металла. В условиях глубокого вакуума образуются настолько мелкие частицы, что практически они осаждаются на внутренней стенке реактора в виде блестящего металлического зеркала, отдельные кристаллы которого имеют четко выраженную огранку.
Вумеренном вакууме образуется смесь правильных кристаллов самых различных размеров, а в неглубоком вакууме появляются дендриты.
Вначальный период кристаллизации происходит адсорбция паров металла на поверхности зародыша (частицы). За счет выделяющейся теплоты адсорбции температура внешней поверхности металлического зародышачастички всегда выше температуры окружающей среды.
Адсорбированный металлический атом на поверхности металлического зародыша сохраняет подвижность по двум направлениям. Чем выше температура адсорбционного слоя, т.е. поверхности зародыша, тем выше подвижность адсорбированного атома, тем легче он достигает свободного узла кристаллической решетки и тем легче образуется кристалл с правильными гранями.
Вверхней зоне реактора (аппарата-разложителя) субмикроскопиче-
ская частичка металла сталкивается в газовом потоке со множеством атомов металла, молекул карбонила и оксида углерода и адсорбирует их на своей поверхности.
Атомы металла, находясь в адсорбированном слое и сохраняя свободу перемещения в двух направлениях, стремятся занять свободные узлы в кристаллической решетке. Молекулы карбонила в момент соударения с перегретой поверхностью частички получают дополнительный тепловой импульс для немедленной диссоциации. Молекулы оксида углерода на перегретой активной поверхности металлической частички находятся в условиях, наиболее благоприятных для их распада.
В результате всех этих процессов микрокристаллы непрерывно растут, но этот рост носит скачкообразный характер и перемежается с отложением сажи и адсорбционных включений. Этим объясняется специфическое
Процессы порошковой металлургии. Курс лекций |
-163- |

I. ПОЛУЧЕНИЕ ПОРОШКОВ
Лекция 20 Получение порошков металлов методом термической диссоциации карбонилов
строение частичек некоторых карбонильных порошков, например железных, называемое «луковой кожурой».
Размер частиц получаемого карбонильного порошка зависит от температуры и длины горячей зоны, скорости газового потока, концентрации паров металла и зародышей.
Вверхней зоне аппарата-разложителя зародыши-частички очень малы. Поступательная скорость частичек определяется общей скоростью газового потока, движущегося обычно сверху вниз. Однако истинный путь зародышей в сотни тысяч раз больше пути газового потока, и это создает благоприятные условия для столкновения между отдельными зародышамичастичками и атомами металла, что приводит к постепенному укрупнению металлического кристалла. По мере укрупнения частички начинает проявляться ее сила тяжести, направленная, как и общее движение газового потока в аппарате, сверху вниз.
Кристаллизация металла может существенно измениться, если поверхность растущего кристаллика подвергнуть тепловым, химическим или физическим воздействиям.
Например, если пары карбонила разлагать в атмосфере постороннего газа, то образующиеся пары металла (а затем и его зародыши) окажутся окруженными молекулами этого газа-разбавителя. Формирующиеся частички металла, сталкиваясь с огромным количеством молекул постороннего газа, адсорбируют эти молекулы на своей поверхности. Столкновение частички с парами металла и с молекулами карбонила в этих условиях затрудняется, вследствие чего замедляется рост зародышей металла и карбонильные порошки получаются более мелкими.
Впромышленных масштабах карбонил-процесс используют для производства никеля, железа, кобальта, вольфрама, хрома, молибдена и некоторых металлов платиновой группы.
Получениепорошковникеляижелеза
Наибольшее практическое значение в настоящее время карбонильный метод имеет для производства порошков никеля и железа, карбонилы которых Ni(CO)4 и Fe(CO)5 были получены, соответственно, в 1888 и 1891 гг.
В1902 г. в Англии (г. Клайдах, Южный Уэльс) началось промышленное производство карбонильного никеля (метод Монда), при котором синтез
итермическое разложение карбонила ведут при давлении, близком к атмосферному, и температурах 50–60 и 200–250 °С соответственно. Исходным сырьем в процессе служит медно-никелевый штейн (CuS–NiS–FeS), конечный продукт – карбонильный никель Монда, который представляет собой гранулы диаметром 5–10 мм, содержащие 99,5–99,8 % Ni.
В1930-х гг. в Германии была разработана технология производства порошков никеля и железа с размером частиц до 20 мкм.
Процессы порошковой металлургии. Курс лекций |
-164- |

I. ПОЛУЧЕНИЕ ПОРОШКОВ
Лекция 20 Получение порошков металлов методом термической диссоциации карбонилов
|
4 |
6 |
3 |
|
9 |
1 |
|
10 |
|
7 |
|
|
|
11 |
2 |
5 |
8 |
|
|
Рис. 1.31. Схема получения порошка карбонильного никеля: 1 – газгольдер с СО; 2 – компрессор; 3 – ресивер; 4 – колонна синтеза карбонила; 5 – циркуляционный насос; 6 – холодильник; 7 – сборник сконденсированного карбонила; 8 – сборник сырого карбонила; 9 – ректификационная колонна; 10 – сборникиспаритель готового карбонила; 11 – разложитель (диссоциатор) карбонила
В качестве исходного сырья при производстве порошков использовали, соответственно, никелевый файнштейн или губку железа. Реакционный газ (95 % СО и 5 % Н 2) подают подогретым до 150–200 оС в колонну синтеза (рис. 1.31). Колонна синтеза представляет собой цилиндр высотой 9–12 м и диаметром от 0,7 до 1,0 м со стенками толщиной 10–15 см, вмещающий 18–20 т никельсодержащего материала.
Начальное давление газа 5–10 МПа, но по мере обеднения файнштейна никелем давление и температуру газа повышают, соответственно, до 20 МПа и 250 °С. Образовавшийся при синтезе карбонил конденсируется в холодильнике, из которого СО циркуляционным насосом возвращают в колонну синтеза (куда периодически поступают и свежие порции газа), а сырой карбонил стекает последовательно в ряд сборников, где давление постепенно понижается до 0,5 МПа. Для удаления примесей (паров воды, смазки от уплотнений компрессора и насоса) карбонил подвергают дистилляции в ректификационной колонне.
Диссоциацию карбонила никеля проводят при нормальном давлении и температуре 250–400 °С в колоннах разложения (цилиндрических реакторах высотой 5 м и диаметром 1 м), куда его пары поступают в количестве 50–200 кг/ч из змеевикового испарителя.
В РФ осуществляется производство карбонильного никеля с использованием тетракарбонила. Процесс получения карбонила ведут при высоком давлении СО (до 10 МПа), а термическое разложение Ni(CO)4 проводят, как описано выше.
Производство порошков карбонильного железа в СССР начато с конца 30-х гг. прошлого столетия.
Синтез карбонила Fe(CO)5 ведут с использованием в качестве сырьевых материалов губчатого железа, штейна, железной руды, скрапа, стружки.
Процессы порошковой металлургии. Курс лекций |
-165- |

I. ПОЛУЧЕНИЕ ПОРОШКОВ
Лекция 20 Получение порошков металлов методом термической диссоциации карбонилов
Исходное сырье (максимальный размер кусковых материалов 10–25 мм) загружают в колонну синтеза, выполненную из легированной стали и рассчитанную на рабочее давление до 20 МПа. По окончании загрузки исходного сырья вся система впрессовывается сжатым азотом, после чего азот сбрасывают в атмосферу. В нижнюю часть колонны подают сжатый оксид углерода. После заполнения системы до давления СО 5–10 МПа включают циркуляционный насос, обеспечивающий движение реакционного газа через слой загруженного в колонну железосодержащего сырья.
По мере расходования СО на синтез карбонила железа производится периодическая подача газа в систему. Циркулирующий в системе реакционный газ очищается от масла в маслоотделителе (стальной емкости, снабженной штуцерами входа и выхода газа и слива масла) и подогревается до 80–170 °С в теплообменнике типа «труба в трубе». Так как реакция образования Fe(CO)5 экзотермична, рабочая температура в колонне после начала циркуляции сжатого газа поддерживается за счет тепловыделения при взаимодействии железа и СО.
В конце синтеза карбонила температуру и давление газа в колонне поддерживают на верхнем пределе, что улучшает полноту использования исходного сырья. Во время синтеза концентрация СО в циркулирующем газе поддерживается не ниже 80 %. На ход синтеза благоприятно влияют примеси аммиака, водорода, сероводорода и некоторых спиртов при их непродолжительном воздействии.
Образующиеся пары пентакарбонила железа вместе с непрореагировавшим СО очищают от пыли в фильтре, снабженном змеевиком для обогрева паром (предотвращается конденсация паров карбонила) и тканевым рукавом для фильтрации газа. Очищенный газ поступает в холодильникконденсатор, где охлаждается, а пентакарбонил железа конденсируется и охлаждается до 60 °С. Отделение жидкого карбонила железа от циркуляционного газа проводят в сифонном сепараторе, после которого СО проходит через ловушку в фильтр высокого давления для улавливания механических загрязнений и поступает на всасывание в циркуляционный насос.
Жидкий карбонил железа из сепаратора направляется в десорбер, где осуществляется выделение растворенного в нем СО, затем поступает в сборник, проходит через фильтр и идет в емкость продукта.
Окончание синтеза карбонила определяют по прекращению его поступления в сепаратор в течение 30 мин. После окончания процесса продолжается циркуляция газа для охлаждения колонны синтеза примерно до 70 °С, затем СО из системы сбрасывается в атмосферу. Далее колонну синтеза продувают аргоном до полного отсутствия СО в продувочном газе и производят перегрузку колонны синтеза: остатки железосодержащего материала выгружают из колонны и загружают в нее свежую порцию исходного сырья. Так как колонна работает циклически, для осуществления непрерывного производственного процесса в схеме обычно предусматривают не менее трех однотипных реакторов синтеза карбонила.
При производстве порошка железа жидкий карбонил из напорной емкости через фильтрующее и дозирующее устройства направляется в испаритель (рис. 1.32), в котором карбонил подогревается паром, пропускаемым через рубашку испарителя или змеевик.
Пары карбонила из испарителя через обогреваемый при помощи паровой рубашки патрубок («калач») направляют в горловину на крышке аппа-
Процессы порошковой металлургии. Курс лекций |
-166- |
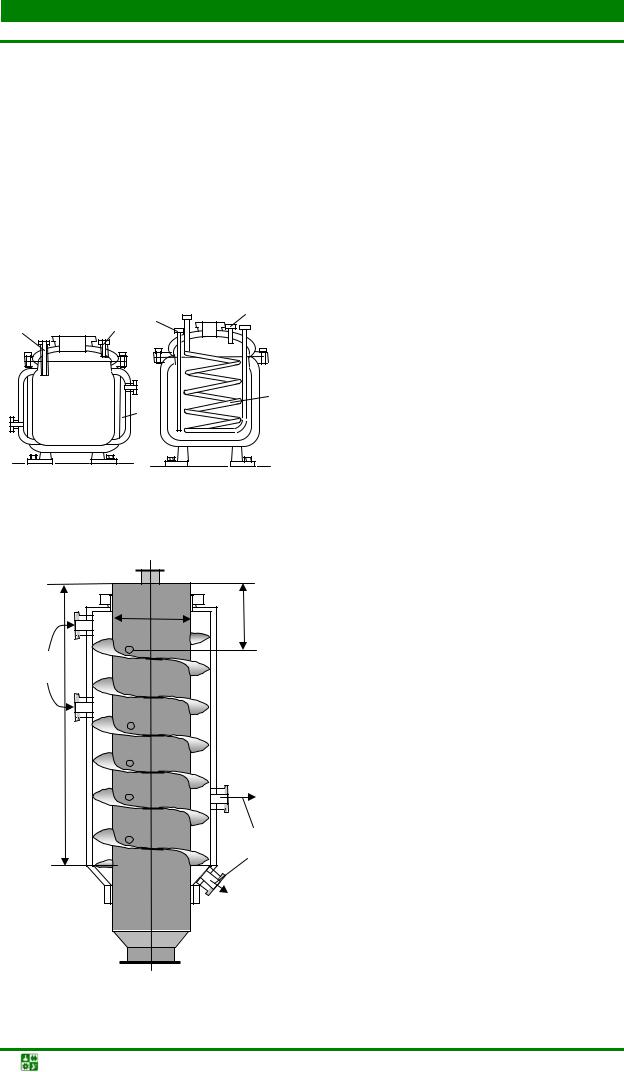
I. ПОЛУЧЕНИЕ ПОРОШКОВ
Лекция 20 Получение порошков металлов методом термической диссоциации карбонилов
рата разложения (рис. 1.33). Далее пар карбонила поступает в свободный объем этого диссоциатора, имеющего высоту 4–5 м. Снаружи аппарат разложения по всей высоте окружен теплообменной рубашкой, обеспечивающей его обогрев за счет циркуляции горячего газа, который движется внутри рубашки аппарата по винтообразным плоскостям. Наличие этих плоскостей позволяет улучшить теплообмен внутри аппарата. Вместо нагрева газовым потоком иногда применяют электрообогрев с раздельной регулировкой по зонам, соответствующим верху, середине и низу аппарата.
При стандартном режиме разложение пентакарбонила железа про-
водят при температурах верхней зоны аппарата разложения (0,8 его высоты) t5 = 295–300 °С, средней зоны (0,6 его высоты) t3 = 305–310 °С, нижней зоны
(0,3 высоты) t2 = 310–345 °С.
1 |
2 |
1 |
2 |
|
|||
|
|
||
|
|
3 |
4 |
|
|
|
|
а |
|
|
б |
|
|
Ǿ 1 000 |
h1 |
|
|
t5 |
|
Ввод |
|
|
|
|
|
|
|
газа |
|
|
|
|
|
t4 |
|
h2 |
|
t3 |
|
|
|
|
|
|
|
t2 |
|
|
|
t1 |
Вывод |
|
|
|
|
|
|
|
газа |
h1 = 5 000 мм |
|
|
h1 = 1 000 мм |
Рис. 1.32. Конструкция испарителейкарбонила: а – испаритель с наружной рубашкой; б – испаритель с внутренним змеевиком;1 – патрубок для ввода карбонила; 2 – патрубок для вывода продувочного газа; 3 – обогреваемая
рубашка; 4 – обогреваемый змеевик
Рис. 1.33. Схема промышленного аппарата разложения с газовым обогревом (t1, t2, t3 ... – точки замера температуры)
Процессы порошковой металлургии. Курс лекций |
-167- |
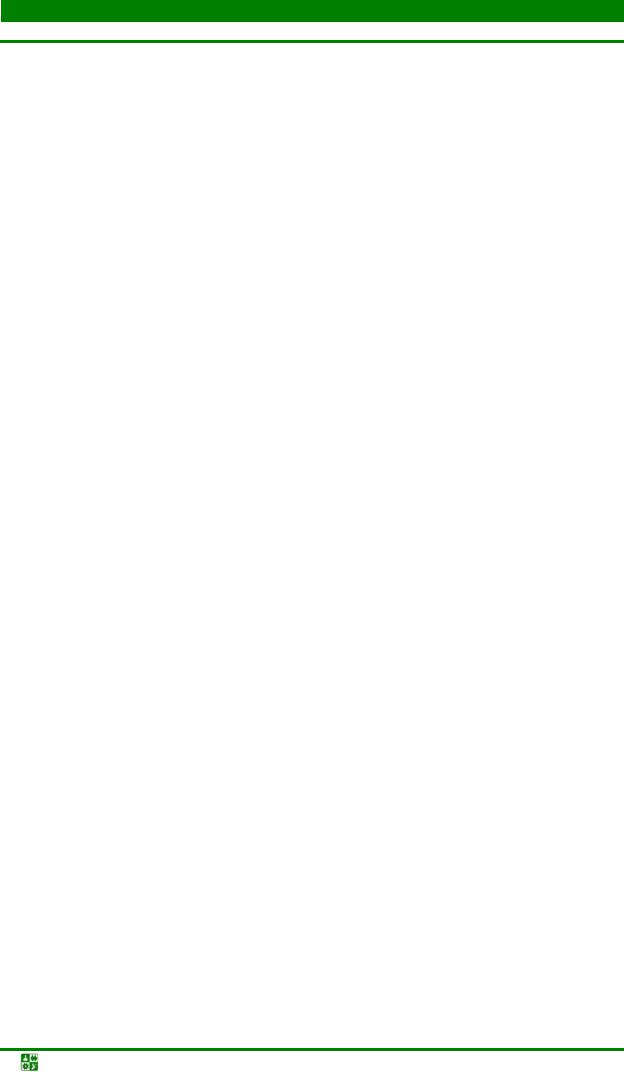
I. ПОЛУЧЕНИЕ ПОРОШКОВ
Лекция 20 Получение порошков металлов методом термической диссоциации карбонилов
Возможны и другие температурные режимы работы диссоциатора: «падающий» режим, при котором по высоте аппарата сверху вниз
создают понижение температуры (градиент температур между зонами 12–
15 °С);
конвекционный режим, когда t5 = t2 = 270–280 °С, а t3 = 280–290 °С.
При «падающем» температурном режиме разложения карбонила получают более чистые порошки (так как в более холодной части аппарата разложения слабее идут побочные реакции), чем при стандартном режиме.
Ваппаратах, работающих в конвекционном режиме, получают более крупные порошки, так как увеличивается продолжительность пребывания в потоке газа образующихся частиц.
Термическую диссоциацию пентакарбонила железа проводят в при-
сутствии газообразного аммиака (20–40 л газа NH3 на 1 л жидкого карбонила), который способствует образованию мелких и более чистых сферических частиц железа, уменьшая количество свободного углерода в порошке. Газообразный аммиак подают через тангенциальную щель в горловине аппарата, на выходе из которой происходит смешивание его с парами карбонила железа.
Ваппарате разложения одновременно с основной реакцией диссоциации карбонила протекают и побочные реакции образования оксидов, нитридов и карбидов железа. В связи с этим частицы железа растут во взвешенном состоянии в диссоциаторе циклическими слоями и равномерно во всех направлениях.
Получаемые порошинки имеют шарообразную (сферическую) форму
ихарактеризуются слоистой («луковичной») структурой. Обычно при сформировавшихся 7–9 слоях масса частицы начинает превышать подъемную силу циркулирующего в диссоциаторе газа, вследствие чего порошинка оказывается в донной части аппарата.
Впорошке железа часто встречаются сростки, образованные двумя, тремя и более частицами. При температуре выше 400 °С в аппарате разложения карбонила могут образовываться волокна (сросшиеся частицы размером в поперечнике 0,2–0,3 мкм и длиной до нескольких миллиметров).
Вобщем случае средний размер порошинки железа зависит от температуры, длины горячей зоны (чем больше, тем крупнее порошок), объемной скорости проходящего через аппарат разложения газового потока (чем выше, тем мельче частицы) и концентрации паров металла (чем меньше, тем мельче частицы).
Образовавшийся при диссоциации карбонила железа оксид углерода удаляется в рукавный фильтр (от 1 до 12 рукавов), увлекая с собой сформировавшиеся частицы металла, не успевшие выпасть в осадок (фильтр оборудован устройством, встряхивающим рукава для удаления застрявших в них частиц). Около 80 % порошка осаждается в приемнике аппарата разложения, 17–18 % порошка задерживается фильтром и 2–3 % улавливается в соединительном коллекторе или в конечном рукавном фильтре.
После фильтра СО поступает на очистку от аммиака в скруббер, пройдя который направляется на синтез пентакарбонила железа. При необходимости получения более мелких порошков (например, для применения в радиоэлектронике) часть отходящего СО возвращают в диссоциатор, уменьшая
Процессы порошковой металлургии. Курс лекций |
-168- |

I. ПОЛУЧЕНИЕ ПОРОШКОВ
Лекция 20 Получение порошков металлов методом термической диссоциации карбонилов
концентрацию поступающего в него карбонила железа и увеличивая в нем объемную скорость реакционного газа.
Порошки железа, получаемые при стандартном режиме разложения карбонила, соответствуют ГОСТ 13610-79 марке Р-10 (из диссоциатора), марке Р-20 (из фильтра) и марке П (из коллектора и конечного фильтра). Размер частиц порошка составляет 2–4 мкм.
Для увеличения дисперсности порошков железа процесс разложения карбонила проводят в присутствии различных инициирующих добавок (тетрахлорэтан, триацетил, толуол, диметилфталат и др.), создающих большое число центров кристаллизации. Их вводят (в виде раствора) в пентакарбонил или через испаритель при стандартных условиях ведения процесса.
Высокодисперсный порошок железа можно получить разложением не газообразного, а жидкого карбонила, распыляемого с помощью форсунок. Для этого в баке, заполненном пентакарбонилом железа, поддерживают постоянное давление инертного газа (азота). Карбонил, прошедший через сифон бака и очищенный от механических примесей в фильтрах грубой и тонкой очистки, поступает в водоохлаждаемую форсуночную головку, которая крепится на верхней крышке аппарата разложения.
Субмикронные порошки железа (размер частиц – сотые доли микрометров) могут быть получены плазменным методом разложения его пентакарбонила, осуществляемым в струе высокоионизированного аргона (температура 4 500–5 000 °С). При такой температуре создается огромное количество центров (зародышей) образования частиц железа в единицу времени, а инертный газ изолирует их друг от друга, исключая (или тормозя) коагуляцию в жидкофазном состоянии.
В последние годы все большее значение приобретает получение карбонильных порошков железоникелевых сплавов разложением смеси паров карбонилов железа и никеля. Испарение такой смеси проводят в аппаратах выпарного типа или типа «труба в трубе». В аппарат разложения можно направить также смесь жидких карбонилов железа и никеля. Кроме смеси этих карбонилов в горловину аппарата вводят и газообразный аммиак. Полученный карбонильный порошок содержит около 5 % Ni.
Получениепорошковвольфрамаимолибдена
Первый промышленный способ получения порошков вольфрама и молибдена, предусматривающий термическое разложение в токе несущих газов (водорода, азота и др.) паров карбонилов W(CO)6 или Мо(СО)6 при атмосферном давлении и температуре 350–1 000 °С, был разработан в Герма- нии в 30-е гг. прошлого века. В нашей стране первая крупная установка (рис. 1.34) для получения карбонильного порошка вольфрама (молибдена) была создана почти пятьдесят лет назад.
Процессы порошковой металлургии. Курс лекций |
-169- |

I. ПОЛУЧЕНИЕ ПОРОШКОВ
Лекция 20 Получение порошков металлов методом термической диссоциации карбонилов
8 |
|
11 |
2 |
3 |
|
1 |
|||
|
|
|||
7 |
9 |
10 |
|
|
|
|
11 |
|
4 |
8 |
|
|
|
|
12 |
13 |
|
|
5 |
|
|
6 |
||
|
|
|
|
Рис. 1.34. Схема установки для получения карбонильных порошков вольфрама и молибдена: 1 – подогреватель водорода; 2 – сублиматор; 3 – теплообменник; 4 – аппарат разложения; 5, 8 – фильтры; 6 – приемник; 7, 12 – баллоны; 9 – колонна с медной стружкой; 10 – холодильник; 11
– осушитель; 13 – колонна с хромоникелевым катализатором
Кристаллический карбонил вольфрама (молибдена) загружают в горизонтальный сублиматор 2 типа «труба в трубе», систему герметизируют и продувают очищенным азотом (технический азот из баллона 7 через фильтр 8 поступает в колонну 9 с медной стружкой, нагретой до 550 °С, затем в холодильник 10 и осушитель 11). Несущим газом является очищенный водород (технический водород из баллона 12 через фильтр 8 поступает в колонну 13 с хромоникелевым катализатором при температуре 20 °С, затем в осушитель11). В сублиматоре 2 карбонил нагревают до 60–135 оС. В подогревателе водорода 1 и теплообменнике 3 поддерживают температуру 100 °С. Горячий водород, захватывая пары карбонила, выносит их в аппарат разложения 4, где при 350–400 °С происходит термораспад карбонила. Порошок собирают на фильтре 5 и в приемнике 6. Размер частиц равен 2–4 мкм.
В начале 60-х гг. XX в. была создана установка с кварцевым аппаратом разложения, позволившим проводить диссоциацию карбонила молибдена при 400–1 400 °С. В зависимости от температуры разложения и газовой атмосферы в аппарате разложения получаемые порошки вольфрама и молибдена содержат различные количества углерода. Размер частиц порошков не
превышает 1–2 мкм; поверхность частиц сильно развита и может составлять до 2,5 м2/г.
Карбонильные порошки металлов, технология которых рассмотрена выше, после выгрузки из аппарата разложения обычно подвергают вторичной обработке: их измельчают (разрушая конгломераты) в виброили шаровой вращающейся мельнице, отжигают (в токе водорода при 400–600 °С или в вакууме) для удаления примесей углерода, азота и кислорода (снижая суммарное количество примесей с 1–3 % до нескольких сотых процента) или
Процессы порошковой металлургии. Курс лекций |
-170- |

I. ПОЛУЧЕНИЕ ПОРОШКОВ
Лекция 20 Получение порошков металлов методом термической диссоциации карбонилов
изолируют поверхность частиц порошка каким-либо соединением (оксидами кремния, фосфатами и др.).
В последние годы все большее значение приобретает карбонильный метод создания покрытий на нагретой поверхности порошинок или изделий из различных материалов.
Расширение производства порошков существенно сдерживается их чрезвычайно высокой стоимостью, так как они в десятки раз дороже восстановленных порошков аналогичных металлов.
Контрольныевопросыизадания
1.Что такое карбонилы?
2.Какова сущность карбонил-процесса?
3.Что влияет на скорость образования зародышей в единице объема и на скорость формирования металлических кристаллов?
4.Перечислите операции получения карбонильных порошков.
5.Порошки каких металлов получают с использованием карбонилпроцесса?
6.Как можно увеличить дисперсность получаемых карбонильных по-
рошков?
7.Как можно получить субмикронные порошки карбонила железа?
8.Назовите температурные режимы работы диссоциатора.
9.Какую структуру имеют карбонильные порошки?
10.Для чего проводят вторичную обработку карбонильного порошка?
Лекция21 Получениепорошковметодами термодиффузионногонасыщения,
межкристаллитнойкоррозии, испарения-конденсации
План лекции
1.Метод термодиффузионного насыщения.
2.Метод межкристаллитной коррозии.
3.Метод испарения-конденсации.
Методтермодиффузионногонасыщения
Порошки сталей и других сплавов, легированные элементами, оксиды которых трудновосстановимы, могут быть получены разработанным около пятидесяти лет назад в ИПМ АН Украины методом термодиффузионного на-
Процессы порошковой металлургии. Курс лекций |
-171- |

I. ПОЛУЧЕНИЕ ПОРОШКОВ
Лекция 21 Получение порошков методами термодиффузионного насыщения, межкристаллитной коррозии, испарения-конденсации
сыщения порошка или губки (основы) легирующими элементами из твердых засыпок или точечных источников.
При использовании способа твердых засыпок источник насыщения, состоящий из порошка легирующего металла, хлористого аммония (NH4Cl) и наполнителя (глинозема А12О3 или кремнезема SiО2), равномерно располагается вокруг насыщаемого порошка (губки) металла чередующимися с ним слоями. Для этого на дно контейнера помещают засыпку (например, 47,5 % А12О3, 5 % NH4C1 и 47,5 % одного или нескольких легирующих металлов), уплотняют ее и сверху насыпают металлический порошок, подвергаемый насыщению. Поверх этого слоя накладывают еще один слой засыпки, закрывают контейнер крышкой и нагревают, обеспечивая диффузионное насыщение металла-основы сплава.
Наиболее существенными недостатками способа получения порошка из твердых засыпок являются: неравномерное распределение насыщающего металла по всей толщине порошка-основы; трудное регулирование состава получаемого порошка, недостаточно полное использование металла из насыщающей засыпки.
Диффузионное насыщение происходит переносом легирующего элемента через газовую фазу в виде хлоридов, йодидов или бромидов, образующихся во время нагрева при взаимодействии металлических компонентов смеси с продуктами разложения соответствующих галоидных солей аммония.
Количество образовавшихся галоидных соединений зависит от содержания в шихте NH4Г (оптимальное количество 10–12 %), герметичности контейнера, температуры и скорости нагрева, температуры агрегатных превращений галогенидов металла-основы и металла легирующего компонента, коэффициентов испарения компонентов шихты и других факторов.
В процессе изотермической выдержки в контейнере взаимодействуют друг с другом исходные и образующиеся твердые, жидкие и газообразные вещества. При встрече газообразного галогенида одного металла с поверхностью частиц другого металла идет реакция замещения, в результате которой образуется газообразный галогенид другого металла и активные атомы насыщающего элемента. Например; выделившиеся на поверхности частиц металлаосновы Ме активные атомы легирующего компонента Ме' сначала адсорбируются на ней, а затем диффундируют вглубь частицы, образуя сплавMe–Ме'.
Процесс формирования частиц сплава будет происходить до достижения ими равновесного состава. В результате последовательного и совмещенного протекания перечисленных процессов за 3–6 ч происходит полное выравнивание концентрации элементов по сечению частиц порошков сплавов. Введенный в шихту галогенид аммония служит не только источником галоида водорода и образующихся затем галогенидов металлов, но и разрыхлителем, препятствующим спеканию частиц порошка в процессе насыщения их соответствующими элементами.
Способ насыщения из точечных источников более эффективен и позволяет получать порошки сплава однородного состава. Способ предусмат-
Процессы порошковой металлургии. Курс лекций |
-172- |

I. ПОЛУЧЕНИЕ ПОРОШКОВ
Лекция 21 Получение порошков методами термодиффузионного насыщения, межкристаллитной коррозии, испарения-конденсации
ривает приготовление смеси из порошков металла-основы и легирующего металла, в которую вводят хлористый аммоний, и по следующий нагрев этой шихты в течение определенного времени. Полученную губку заданного состава размалывают в порошок, который затем отмывают в воде или отжигают в водороде для удаления остатков галоидных соединений. Иногда вместо порошка легирующего металла в шихту вводят его оксид и углерод. В этом случае легирующий элемент образуется в процессе нагрева шихты в результате протекания соответствующей реакции восстановления.
Получение порошков, содержащих три и более металлических компонента, может быть реализовано в два этапа. На первом этапе проводят совместное восстановление смеси легковосстановимых оксидов металлов (например, оксидов железа, никеля, кобальта, вольфрама и др.), на втором – насыщение частиц получаемого сплава хромом, кремнием, титаном, марганцем и другими трудновосстановимыми элементами из точечных источников.
Способ термодиффузионного насыщения из точечных источников используют для получения порошков сталей 40Х, Х5, XI3, ХЗО, Г13, Х23Н18, Х18Н9, Х18Н9Т, 2Х13Н4Г9, нихрома Х20Н80, сплава Fe–P и др.
Получение порошка стали Х30. Исходными материалами служат железный порошок с размером частиц 0,063–0,16 мм, порошок хрома с размером частиц < 0,1 мм, аммоний хлористый и двууглекислый (замена части NH4C1 на NH4HCО3 позволяет значительно снизить количество хлоридов в губке, образующейся при диффузионном насыщении).
Шихту (54,2 % Fe, 29,2 % Сr, 2,5 % NH4C1 и 14,1 % NH4HCО3) сме-
шивают в лопастном смесителе, причем сначала перемешивают металлические порошки, а затем к ним добавляют хлористый и двууглекислый аммоний. Приготовленную шихту переносят в контейнер, засыпают песком и поверх него помещают плавкий затвор толщиной 10–15 мм из плавленого и измельченного натросиликатного порошка.
Диффузионное насыщение проводят в проходных толкательных печах при 1 200–1 220 или 1 100 °С в атмосфере остроосушенного конвертированного природного газа или водорода. Продолжительность пребывания поддонов с контейнерами в горячей зоне печи составляет 4–5 ч.
Полученную легированную губку подвергают дроблению и размолу последовательно в молотковых и шаровых мельницах, рассеивают на вибросите (фракцию > 0,25 мм направляют на доизмельчение), отмывают от остаточных хлоридов и высушивают. Порошок сплава содержит, %: 33,2 Сr;
0,2 С; 0,14 Si; 0,17 А1; 0,02 Мn; остальное – Fe.
Получение порошка сплава Fe–P. Исходный железный порошок смачивают водным раствором диаммонийфосфата (NH4)2(HPO4) и отжигают в водороде при 800 °С. Фосфор, выделяющийся при разложении диаммонийфосфата, диффундирует в железо с образованием легированной губки сплава Fe–P, которую затем измельчают. Порошок марки ЖФ-1 содержит 1,0–1,2 % Р
и > 97 % Fe.
Получение порошка эвтектоидной углеродистой стали. Готовят смесь на основе восстановленного порошка железа с 2 % сажи и 0,5 % Ва-
Процессы порошковой металлургии. Курс лекций |
-173- |

I. ПОЛУЧЕНИЕ ПОРОШКОВ
Лекция 21 Получение порошков методами термодиффузионного насыщения, межкристаллитной коррозии, испарения-конденсации
СО3, загружают ее в поддон с неплотно закрывающейся крышкой и нагревают в защитной среде при 1 030 °С в течение 4 ч. В процессе такой обработки углерод, взаимодействуя с ВаСО3, создает науглероживающую среду по реакции С + ВаСО3 = Ва + СО2 + СО. Образовавшийся газ равномерно обволакивает все частицы железного порошка и науглероживает их. Полученную стальную губку измельчают в порошок, структура частиц которого представляет собой перлит с отдельными небольшими включениями феррита.
Получение порошка сплавов Fe–Ni. Прокатную окалину (содержание Feoбщ около 74,5 %) с размером частиц < 0,1 мм смешивают с углекислым никелем и сажей. Шихту нагревают при 1 100 °С в течение 4 ч в водороде или конвертированном природном газе. Полученную губку с содержанием никеля до 25 % размалывают. Порошок железоникелевого сплава (в дальнейшем) можно использовать для диффузионного насыщения другими легирующими элементами, например хромом, вольфрамом.
Получение порошка коррозионно-стойких сталей аустенитного класса.
В качестве исходных берут порошки железоникелевых сплавов, технология которых рассмотрена выше. Составы приготавливаемых шихт и получаемых порошков приведены в табл. 1.9.
Таблица 1.9
Составы шихт и получаемых порошков коррозионно-стойких сталей
|
Состав исходной шихты, % |
Химический состав |
|||||||
Марка |
|
порошка, % |
|
||||||
|
|
|
|
|
|
||||
порошка |
Порошок спла- |
Cr |
NH4C1* |
NH4HCO3* |
Cr |
|
Ni |
|
С |
|
ва Fe–Ni |
|
|
|
|
|
|
|
|
Х18Н9 |
76 (10,5 Ni) |
24 |
3 |
12 |
18,1 |
|
9,0 |
|
0,11 |
Х18Н15 |
76 (17,3 Ni) |
24 |
3 |
12 |
19,9 |
|
16,4 |
|
0,10 |
Х23Н18 |
70 (22 Ni) |
30 |
3 |
12 |
24,6 |
|
17,7 |
|
0,17 |
*Сверх 100 % массы металлических порошков.
Режимы диффузионного насыщения: Т = 1 100 °С, τ = 5 ч.
Методмежкристаллитнойкоррозии
В основе этого метода лежит разрушение (растворение) межкристаллитных прослоек в сплавах специально подобранными растворами. Исходным материалом для получения порошка служат отходы металлообработки (стружка, обрезки листов и лент и т.п.). Порошки, полученные методом межкристаллитной коррозии, используются при производстве фильтров и конструкционных материалов.
Процессы порошковой металлургии. Курс лекций |
-174- |
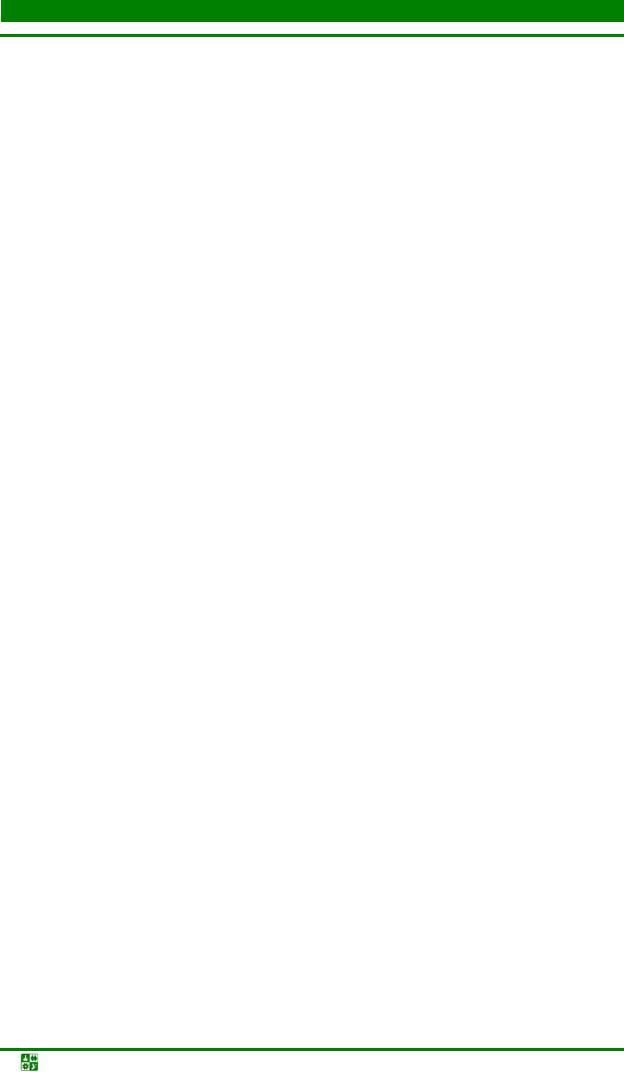
I. ПОЛУЧЕНИЕ ПОРОШКОВ
Лекция 21 Получение порошков методами термодиффузионного насыщения, межкристаллитной коррозии, испарения-конденсации
Метод межкристаллитной коррозии – один из наиболее старых промышленных способов получения легированных железных порошков, но мало распространен в настоящее время.
При использовании в качестве исходного сырья сплавов из двух или более металлов, растворимых один в другом в жидком состоянии и обладающих полной взаимной нерастворимостью (или ограниченной растворимостью) в твердом состоянии, один из металлов удаляется из сплава, а другой – остается в виде порошка. Чувствительность к межкристаллитной коррозии может быть повышена соответствующей термической обработкой сплавов.
По одному из способов отходы литой хромоникелевой стали подвергают термообработке, в результате которой по границам зерен выделяются карбиды хрома, тогда как области вблизи границ обедняются хромом. При обработке термически обработанного сплава 10 %-м раствором H2SО4, содержащим 10–11 % CuSО4, межкристаллитное вещество (прослойки) растворяется, чему способствует возникновение гальванического эффекта: области, обедненные хромом, являются анодом по отношению к центральной части зерна, богатой хромом, и растворяются. Медь, осевшую на образовавшихся частицах, отмывают азотной кислотой.
Существует возможность получения легированных порошков, если несколько элементов растворимы один в другом и нерастворимы в каком-либо другом элементе. Например, сплав, содержащий 72 % Сu, 25 % Fe и 3 % Сr, обрабатывают азотной кислотой; медь, распределенная по границам зерен сплава Fe–Сr, растворяется в кислоте, а порошок сплава остается в осадке. Его промывают водой и спиртом, а затем сушат.
Известны описания «самопроизвольного» разрушения некоторых алюминиевых сплавов при их хранении или воздействии на них паров воды. Например, порошки сплавов на основе системыAl–Mg (35–10 % А1, 30–65 % Mg, 30 % Fe и 3 % Р) получают в результате взаимодействия их с поглощаемой из воздуха влагой, при котором образуется газообразный РН3 и компактный слиток разрушается. По другим данным, слитки алюминиевого сплава, содержащего 13,0–23,5 % Fe, < 2 % С и 1 % Р, при выдержке на воздухе в теч е- ние 90–120 сут «самопроизвольно» разрушаются с образованием порошка, крупность частиц которого составляет от 35 до 270 мкм.
Методиспарения-конденсации
Этот метод предусматривает перевод компактного или жидкого металла в парообразное состояние (первая фаза процесса, связанная с испарением вещества) и последующую конденсацию образовавшихся паров (вторая фаза процесса) на поверхностях, температура которых ниже точки плавления осаждаемого металла. Известно, что в обычных условиях над любой поверхностью наблюдается определенное давление паров вещества, соответствую-
Процессы порошковой металлургии. Курс лекций |
-175- |

I. ПОЛУЧЕНИЕ ПОРОШКОВ
Лекция 21 Получение порошков методами термодиффузионного насыщения, межкристаллитной коррозии, испарения-конденсации
щее равновесию, при котором скорость испарения с поверхности равна скорости конденсации паров на ней. Если же сделать так, чтобы пары вещества стали конденсироваться (осаждаться) не только на этой, но и на какой-либо другой поверхности (например, более холодной по сравнению с первой), то равновесие нарушится и будет происходить непрерывное испарение вещества с более нагретой поверхности со скоростью, определяемой упругостью его паров и их концентрацией вблизи более холодной поверхности осаждения, давлением других газов или паров других веществ в окружающем пространстве.
Образование порошка при конденсации пара осуществляется путем молекулярного формирования частиц твердой фазы. Для конденсации металлического пара в виде дисперсной фазы необходимы два условия:
1.Высокое давление пара, которое вызывает одновременное и множественное возникновение зародышевых центров конденсированной фазы, благодаря чему обедняется паром газовая среда, замедляется рост частиц и система сохраняет дисперсное состояние.
2.Присутствие в конденсирующемся паре нейтрального газа. Ней-
тральный газ служит средой, препятствующей коагуляционному и диффузионному росту частиц. Его давление может колебаться от 10-3 до 102 кПа.
Процесс конденсации металлического пара в порошок может протекать на охлажденной поверхности гетерофазно, а в объеме – гомофазно и ге-
терофазно. Условной границей между гомо- и гетерофазным процессами является интервал пересыщений пара (104–108) относительно равновесного состояния. Ниже величины 104 порошок образуется только на поверхности, выше 106 – в объеме.
Гетерофазный процесс образования порошка представляет собой
массовый рост кристаллических частиц, зарождение которых происходит на макроскопических дефектах поверхности. В гетерофазном процессе в зависимости от условий формируются частицы от долей микрометра до нескольких миллиметров разнообразной формы – дендриты, пластины. Вначале на подложке формируется пленка. Островки кристаллов общим фронтом растут перпендикулярно подложке. Кристаллы приобретают ограненные очертания (в виде пирамид или призм размером 10–20 мкм). Затем в слое кристаллов формируется как бы второй фронт: из общей массы кристаллов быстро выделяются преобладающие частицы, которые прорастают друг через друга.
Гомофазный процесс инициируется пересыщением пара, в результате чего происходит гомо- и гетерофазное образование зародышей частиц порошка. Они растут главным образом коагуляционным путем – слиянием в газовом потоке. Форма и структура частиц зависят от тепло- и массопереноса в газовой среде. Когда температура последней выше 0,7 Тпл металла образуются (по механизму «пар–жидкость–твердое») частицы сферической формы. При температуре ниже 0,77 Тпл металла образуются (по механизму «пар–кристалл») частицы с выраженной огранкой в виде призм, пирамид и сложных изометрических кристаллов по схеме «пар–кристалл».
Смешанный процесс (гомогетерофазный). В этом процессе новая фаза появляется в объеме зоны конденсации, а рост частиц происходит после осаждения их на холодной поверхности. Частично процесс протекает путем
Процессы порошковой металлургии. Курс лекций |
-176- |
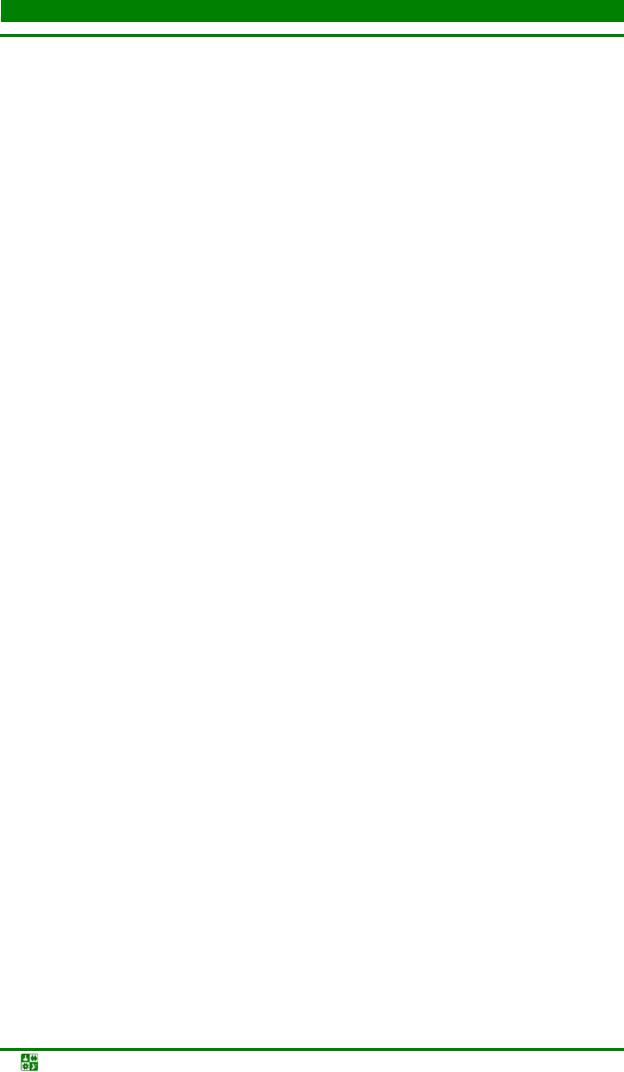
I. ПОЛУЧЕНИЕ ПОРОШКОВ
Лекция 21 Получение порошков методами термодиффузионного насыщения, межкристаллитной коррозии, испарения-конденсации
слияния мелких частиц и ориентированного формирования из них крупных псевдокристаллов или сферолитов, легко разрушаемых при воздействии ультразвуковых колебаний. Для порошков, получаемых в результате смешанного процесса, характерно наличие частиц смешанных форм и структур: гранных, сферических поли- и монокристаллического строения.
Метод испарения-конденсации целесообразно использовать при получении порошков металлов с большим или заметным д авлением паров при сравнительно низких температурах (Zn, Mg, Cd, Be и др.).
Размер частиц (порошинок) колеблется от 10–20 до < 0,1 мкм, а их чистота достаточно высока, несмотря на то, что наблюдается поверхностное окисление.
Получение порошка цинка. Получают конденсацией паров цинка, образовавшихся при углетермическом восстановлении ZnO (температура в печи 1 200–1 300 °С) или при перетекании расплавленного цинка сверху вниз по тарелкам ректификационной колонны (температура в колонне 1 100 °С). Температура в конденсаторе паров цинка должна быть ниже 420 °С.
Получение порошка алюминия. Порошок получают в герметичном аппарате в вакууме или инертном газе (аргоне или гелии). Металл плавят в тигле при температуре 1 200–1 500 °С, а пары конденсируются на холодных стенках аппарата, и порошок алюминия ссыпается с них в бункер. Размер частиц около 0,03 мкм, насыпная плотность порошка 0,08 г/см3, цвет черный. Полученный порошок проявляет значительную склонность к самовозгоранию.
Получение порошка магния. Порошок магния с размером частиц > 100 мкм получают в вертикальных аппаратах с тарельчатым испарителем и кристаллизатором в виде двух автономно охлаждаемых полок, расположенных одна под другой перпендикулярно потоку паров металла. Температура в испарителе до 1 100 °С, а в кристаллизаторе 30–50 °С. Варьируя температуру процесса и длительность пребывания порошка на полках кристаллизатора, меняют дисперсность частиц, имеющих обычно пластинчатую или губчатую форму.
Получение порошка бериллия. Порошки этого металла (губчатый бериллий) получают дистилляцией в высоком вакууме с последующей конденсаций на поверхности молибденового конуса, расположенного над тиглем с расплавом. Полученную губку (в дальнейшем) измельчают в порошок какимлибо механическим методом.
Использование при получении порошков плазменного нагрева с температурами 4 000–10 000 °С позволяет перевести в парообразное состояние практически любые металлы. Диспергируемые металлы, сплавы, тугоплавкие соединения подают в плазменный факел в дисперсном состоянии (порошки, смеси порошков) или в виде расходуемого электрода. Плазмообразующими газами служат водород, азот, аргон и их смеси. Конденсация частиц в осадительной камере может происходить как при атмосферном, так и при пониженном давлении газа. Скорость охлаждения варьируется в широких пределах и при определенных условиях достигает 106 и даже 108 К/с. В ряде методов предусмотрено осаждение паров металлов на подложку, охлаждаемую до сверхнизких температур порядка 77 К.
Процессы порошковой металлургии. Курс лекций |
-177- |
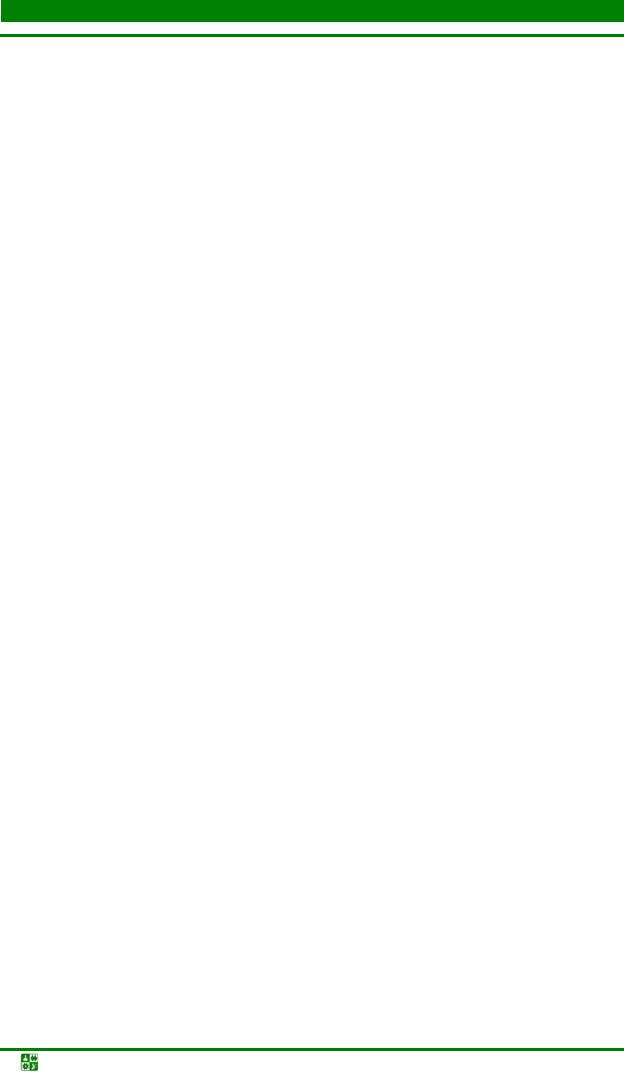
I. ПОЛУЧЕНИЕ ПОРОШКОВ
Лекция 21 Получение порошков методами термодиффузионного насыщения, межкристаллитной коррозии, испарения-конденсации
В мировой практике плазменное испарение металлов, сплавов, металлоподобных соединений чаще всего применяют для получения в достаточно больших количествах ультрадисперсных частиц с размерами от 10 до 100 нм и удельной поверхностью > 10 м2/г.
Нетрадиционным, но достаточно перспективным источником нагрева в методе испарения-конденсации являются оптические квантовые генераторы (лазеры). Так, лазеры с мощностью импульсов 10–30 Дж и длительностью несколько микросекунд позволяют эффективно переводить в паровую фазу железо, титан, никель и другие металлы. При конденсации пара формируются частицы размером от 70 до 10 нм в зависимости от давления газов в камере аппарата (уменьшение этого давления приводит к снижению среднего размера частиц). Наряду с традиционными факторами, влияющими на испарение металла (температуры плавления и кипения, упругость пара и др.), существенную роль играют его светоотражение и теплопроводность.
Контрольныевопросыизадания
1.Что является основой метода межкристаллитной коррозии?
2.Каким образом можно повысить склонность к разрушению металлов травителями?
3.Приведите примеры получения порошков методом межкристаллитной коррозии.
4.В чем заключается сущность метода термодиффузионного насыще-
ния?
5.Какие два способа применяются на практике при получении порошков методом термодиффузионного насыщения?
6.Перечислите компоненты шихты, используемой при термодиффузионном насыщении.
7.Назовите основные условия конденсации металлического пара в виде дисперсной фазы.
8.Приведите примеры получения порошков методом испаренияконденсации.
Лекция22 Методыполученияпорошковтугоплавкихсоединений.
Получениепорошковкарбидовинитридовметаллов
План лекции
1.Классификация и структура тугоплавких соединений.
2.Методы получения порошков карбидов.
3.Методы получения порошков нитридов.
Процессы порошковой металлургии. Курс лекций |
-178- |

I. ПОЛУЧЕНИЕ ПОРОШКОВ
Лекция 22 Методы получения порошков тугоплавких соединений. Получение порошков карбидов и нитридов металлов
Классификацияиструктуратугоплавкихсоединений
Металлоподобные тугоплавкие соединения различных металлов с водородом (гидриды), углеродом (карбиды), азотом (нитриды), бором (бориды) и кремнием (силициды) обладают, как правило, высокими температурой плавления, твердостью, модулем упругости и химической стойкостью, металлическими свойствами (блеск, термические и электрические свойства близки к свойствам металлов) и способностью к сверхпроводимости. Физическая природа таких соединений, среди которых наибольшее значение имеют карбиды, бориды, нитриды и силициды тугоплавких металлов IV–VI групп периодической системы (Ti, Zr, Hf, V, Nb, Та, Mo, W и др.), различна.
Тугоплавкие соединения широко применяются в инструментальной промышленности (для изготовления металлообрабатывающего инструмента, абразивов для шлифовки и полирования различных материалов), наплавочных материалов и материалов для нанесения жаропрочных и износостойких покрытий.
Кроме того, тугоплавкие соединения применяются при получении тонких покрытий из газовой фазы на поверхность различных изделий или инструмента с целью придания им определенных декоративных свойств или защиты от коррозии. Чаще всего для этой цели писпользуют покрытия из карбида и нитрида титана, карбидов молибдена и гафния, а также двухслойные и даже трехслойные покрытия TiC, Ti(CN), TiN.
Многие тугоплавкие соединения используются как конструкционные материалы в агрегатах, работающих в химических производствах (коррози- онно-стойкая арматура в насосах по перекачке химически активных растворов). Детали из тугоплавких соединений находят применение в узлах различных машин, работающих в условиях высоких температур, повышенного газоабразивного износа и др.
Тугоплавкие соединения обладают высокими огнеупорными свойствами – стойкостью при контакте с расплавленными металлами и их солями и поэтому используются при получении тиглей, защитных чехлов термопар, футеровки разливочных машин, электролизных ванн и пр.
Широкое применение имеют тугоплавкие соединения в электро- и радиотехнике (так называемая «тонкая техническая керамика») при получении изоляционных материалов, подложек, сегнето- и пьезоэлектрических материалов.
Структура тугоплавких соединений зависит от соотношения атомных радиусов металла rMe и неметалла (металлоида) rх. По правилу Хэгга, при rMe / rх < 0,59 (rMe / rх > 1,7) образуется структура, очень похожая на ту, которой обладает соответствующий металл, но с неметаллическими атомами, расположенными в междоузлиях кристаллической решетки (так называемые
Процессы порошковой металлургии. Курс лекций |
-179- |

I. ПОЛУЧЕНИЕ ПОРОШКОВ
Лекция 22 Методы получения порошков тугоплавких соединений. Получение порошков карбидов и нитридов металлов
фазы внедрения), а при rMe / rх > 0,59 возникает хотя и металлическая фаза, но с более сложной кристаллической решеткой.
Кремний, атомный радиус которого 0,117 нм, что существенно больше размеров атомов Н, В, С и N , образует с переходными металлами растворы типа замещения, а не внедрения.
Среди методов получения порошков металлоподобных тугоплавких соединений наиболее широко применяют восстановительные процессы и прямой синтез из элементов, в том числе самораспространяющийся высокотемпературный синтез (СВС).
Методыполученияпорошковкарбидов
В зависимости от требований, предъявляемых к карбидам в отношении состава, содержания примесей, стоимости, применяют тот или иной метод их получения. К основным методам получения карбидов относятся(рис. 1.35):
прямой синтез из элементов; восстановление оксидов металлов углеродом с одновременной карби-
дизацией; плазмохимический метод;
осаждение из газовой фазы.
Процессы порошковой металлургии. Курс лекций |
-180- |

I. ПОЛУЧЕНИЕ ПОРОШКОВ
Лекция 22 Методы получения порошков тугоплавких соединений. Получение порошков карбидов и нитридов металлов
Исходные материалы
Прямой синтез
из элементов
|
|
Нагрев при температуре ниже температуры плавления |
|
|
Плавление компонентов шихты |
|
|
Плазмохимический синтез |
|
|
|
|
|
|
|
|
|
|
|
В среде
восстановительного В вакууме газа
Восстановление |
|
Осаждение |
|
Электролиз рас- |
оксидов |
|
из газовой фазы |
|
плавленных сред |
|
|
|
|
|
Восстановление оксидов углеродом |
|
Восстановление оксидов углеродсодержащими газами |
|
Взаимодействие металлов или их оксидов с углеродсодержащими газами |
|
Взаимодействие галогенидов с углеродсодержащими газами |
|
Разложение карбонилов в среде водорода |
|
|
|
|
|
|
|
|
|
|
|
|
В расплаве |
|
При температуре |
|
||||
Спекание методом |
|
|||||||||
|
|
ниже Тпл |
|
|
||||||
горячего |
|
|
|
|
|
|
||||
|
|
|
|
|
|
|
|
|
||
|
|
|
|
|
|
|
|
|
||
прессования |
|
|
|
|
|
|
|
|
|
|
|
|
|
|
|
|
|
||||
|
|
|
|
|
|
|
|
|
|
|
|
|
В восстановительной среде |
|
|
В вакууме |
|||||
|
|
|
|
|
|
|
|
|
|
|
|
|
|
|
|
|
|
|
|
|
|
Рис. 1.35. Классификация методов получения карбидов металлов
Процессы порошковой металлургии. Курс лекций |
-181- |

I. ПОЛУЧЕНИЕ ПОРОШКОВ
Лекция 22 Методы получения порошков тугоплавких соединений. Получение порошков карбидов и нитридов металлов
Исторически первым был способ получения карбидов из смесей соответствующих металлов с углем.
Прямой синтез из элементов. Метод применяется для получения карбидов как в промышленной, так и в исследовательской практике. При этом в зависимости от характеристики исходных материалов и варианта осуществления синтеза можно получить продукт высокой степени чистоты. Технология производства представлена на рис. 1.36.
Металл Оксид Углерод
Смешивание
Брикетирование
Синтез
Размол
Просев (классификация)
Годная фракция |
|
|
|
Крупная фракция |
|
|
|
|
|
|
|
Упаковка порошка
Рис. 1.36. Технологическая схема производства карбидов синтезом из элементов или восстановлением-карбидизацией
В качестве исходных материалов для получения карбидов этим методом используют порошки соответствующих металлов и сажи, взятые в соотношениях, необходимых для получения карбида нужного состава по реакции
Me + С → МеС
Процессы порошковой металлургии. Курс лекций |
-182- |

I. ПОЛУЧЕНИЕ ПОРОШКОВ
Лекция 22 Методы получения порошков тугоплавких соединений. Получение порошков карбидов и нитридов металлов
На полноту протекания процесса и его скорость, гомогенность получаемого продукта при прочих равных условиях оказывает влияние размер частиц исходных порошков металла и сажи. С уменьшением размера частиц скорость процесса повышается.
Взятые в необходимых соотношениях исходные компоненты подвергают смешиванию в смесителях. Длительность смешивания зависит от типа применяемого смесителя и лежит в пределах 2–6 ч, сокращаясь при использовании принудительного перемешивания.
Сбрикетированную (при давлении 50–150 МПа) шихту подвергают нагреву в печах сопротивления в среде защитного газа или в вакууме с целью предотвращения окисления и азотирования при взаимодействии с кислородом и азотом воздуха. Синтез карбидов осуществляется при температурах 1 200–1 600 °С. В этих процессах прямого синтеза существенную роль играет реакционная диффузия углерода: сначала он диффундирует в чистый металл, затем в свой твердый раствор в этом металле, и, наконец, диффузия идет через слой образовавшегося карбида (ее коэффициенты на 2–3 порядка ниже, чем в начале процесса).
Процесс диффузии начинает протекать уже при температуре порядка 1 000 °С и в дальнейшем характеризуется уравнением
D = Aexp(Ea / KT ) ,
где D – коэффициент диффузии углерода в соответствующем металле; А – константа; Еа – энергия активации процесса диффузии углерода в металл.
Превышение температуры синтеза обуславливает спекание образующихся частиц карбида, что затрудняет их дальнейшее измельчение. При производстве карбидов технической чистоты процесс осуществляют в защитной среде, в качестве которой можно использовать водород, конвертированный газ, реже – диссоциированный аммиак или аргон. Процесс проводят в муфельных печах или в печах Таммана (трубчатая печь с трубой из графита). Брикетированную шихту загружают в графитовые контейнеры или в лодочки. В основе процесса карбидизации, как и при синтезе в вакууме, лежит процесс диффузии углерода в металл. Однако скорость процесса несколько выше. Последнее обусловлено тем, что при наличии в среде водорода происходит взаимодействие его с сажей и графитовой оснасткой по реакции 2С + Н2 → С2Н2 с образованием ацетилена, который и взаимодействует с металлом с образованием карбида:
С2Н2 + 2Me = 2МеС + Н2
Кроме рассмотренных вариантов, возможен синтез карбидов в дуговых печах с применением расходуемых электродов или косвенного нагрева
Процессы порошковой металлургии. Курс лекций |
-183- |

I. ПОЛУЧЕНИЕ ПОРОШКОВ
Лекция 22 Методы получения порошков тугоплавких соединений. Получение порошков карбидов и нитридов металлов
шихты в электрической дуге. Однако в этом случае продукт содержит большое количество свободного углерода и неоднороден по составу.
После карбидизации продукт представляет собой спекшуюся губку. Для получения из нее порошка последнюю подвергают дроблению на щековых, валковых или другого типа дробилках до кусков размером 5–20 мм и дальнейшему измельчению в шаровых мельницах. После размола полученный материал классифицируют на вибрационных ситах с целью выделения фракции с размером частиц менее 50 мкм.
Восстановление оксидов металлов углеродом с одновременной карби-
дизацией. Получение карбидов восстановлением оксидов соответствующих металлов углеродом с одновременной карбидизацией по сравнению с прямым синтезом являются более экономичными.
Метод довольно широко используется для получения карбидов тугоплавких металлов IVa и Va подгрупп, а также карбидов хрома и бора.
Для промышленного производства карбидов в качестве исходного сырья используют оксиды металлов и сажу или чистый графит. Сажу или графит, используемые в качестве восстановителей и источников углерода для науглероживания восстановленного металла, предварительно подвергают сушке или прокаливанию с целью удаления влаги и легколетучих примесей. Наличие влаги при карбидизации приводит к обезуглероживанию получаемого продукта.
Приготовленные таким образом исходные материалы подвергаются тщательному смешиванию в шаровой мельнице (углерод берут с избытком 5–10 % по сравнению с теоретически необходимым количеством) и подвергают брикетированию или плотной набивке в графитовые патроны.
Для получения карбидов используют вакуумные печи с графитовым нагревателем или печи Таммана. В последних процесс ведут в среде водорода, осушенного и очищенного от примесей азота.
При получении карбидов в вакууме процесс идет быстрее и продукт получается более чистым по примесям. Более высокая скорость процесса в этом случае обусловлена удалением из реакционного пространства оксида углерода (МеО + С ↔ МеС + СО↑). Наличие вакуума также способствует рафинированию за счет более высокой скорости испарения примесей.
При получении карбидов в среде водорода определенное влияние на скорость процесса оказывает регенерация оксида углерода. Наличие углерода в газовой фазе в виде СО или С 2Н2 значительно увеличивает реакционную поверхность и тем самым ускоряет процессы восстановления и карбидизации.
Поскольку процесс получения карбидов лимитируется процессом диффузии компонентов в твердой фазе, скорость процесса повышается с температурой. Однако повышение температуры и длительности изотермической выдержки τв может привести к обезуглероживанию продукта и получению карбида, отличающегося по составу от стехиометрического (рис. 1.37).
Процессы порошковой металлургии. Курс лекций |
-184- |

I. ПОЛУЧЕНИЕ ПОРОШКОВ
Лекция 22 Методы получения порошков тугоплавких соединений. Получение порошков карбидов и нитридов металлов
Кроме того, высокие температуры процесса приводят к спеканию получаемого продукта, что значительно затрудняет его дальнейшую переработку.
Уменьшение размера частиц восстановителя приводит к значительному ускорению процесса восстановления. На практике чаще всего применяют комплексный восстановитель, в состав которого вводят ламповую сажу, имеющую частицы с наименьшим размером.
Св, % |
|
|
|
|
|
|
|
|
|
|
|
|
|
|
|
|
|
|
|
|
|
18 |
|
1 |
|
|
|
|
|
|
|
|
|
|
|
|
|
|
|
|
|||
|
2 |
|
|
|
|
|
|
|
|
|
14 |
|
|
|
|
|
|
|
|
|
Рис. 1.37. Зависимость содержания связанного |
|
|
|
|
|
|
|
|
|
||
|
3 |
|
|
|
|
|
|
|
углерода в продуктах восстановления TiO2 |
|
10 |
|
|
|
|
|
|
|
|
|
при температуре 1 900 °С в среде водорода |
|
|
|
|
|
|
|
|
|
||
|
|
|
|
|
|
|
|
|
при использовании в качестве восстанови- |
|
|
1 |
2 |
3 |
τв, |
ч |
|||||
|
|
|
|
|
|
|
|
|
|
телей |
сажи 1, газовой сажи 2 и ламповой сажи 3
Однако при выборе режимов получения карбидов следует учитывать, что при высоких температурах частицы сажи способны увеличиваться в объеме, что снижает их реакционную способность. Поэтому процесс необходимо проводить с максимально возможной скоростью нагрева шихты до температуры изотермической выдержки. Условия получения некоторых из карбидов приведены в табл. 1.10. Полученные по оптимальным режимам карбиды в дальнейшем подвергают дроблению, размолу и просеву.
Таблица 1.10
Условия получения (в вакууме) и химический состав карбидов
Карбид |
|
Условия получения |
|
|
Химический состав, % |
|||||
Нагрев |
Температура, °С |
Выдержка, ч |
Me |
|
Собщ |
Cсвоб |
Cсвяз |
Cсвяз. теор |
||
TiC |
Быстрый |
1 100–1 180 |
|
0,5 |
80,15 |
|
19,85 |
0,59 |
19,26 |
20,05 |
|
1,5 ч |
1 450–1 500 |
|
2,5 |
80,20 |
|
19,79 |
0,49 |
19,30 |
20,05 |
ZrC |
Быстрый |
1 000 |
|
1,2 |
88,35 |
|
11,68 |
0,13 |
11,50 |
11,64 |
|
1,5 ч |
1 500 |
|
0,5 |
88,40 |
|
11,63 |
0,11 |
11,52 |
11,64 |
NbC |
Быстрый |
1 700 |
|
3,5 |
88,35 |
|
11,65 |
0,11 |
11,54 |
11,45 |
|
3,2 ч |
1 800 |
|
4,0 |
88,40 |
|
11,60 |
0,16 |
11,44 |
11,45 |
ТаС |
Быстрый |
1 600–1 700 |
|
1,0 |
93,7 |
|
6,31 |
0,10 |
6,21 |
6,22 |
Плазмохимический метод. Данный метод является перспективным для получения порошков тугоплавких соединений с размером частиц менее одного микрометра. Осуществляется этот метод в условиях низкотемпературной плазмы, характеризующейся температурами порядка 5 000–10 000 К.
Процессы порошковой металлургии. Курс лекций |
-185- |

I. ПОЛУЧЕНИЕ ПОРОШКОВ
Лекция 22 Методы получения порошков тугоплавких соединений. Получение порошков карбидов и нитридов металлов
В качестве исходных веществ используют металлы, их оксиды, галогениды, а также углеродсодержащее сырье в виде различных углеводородов, других органических соединений и в некоторых случаях углерод в виде графита. Все компоненты низкотемпературной плазмы переходят в активное состояние, в результате чего взаимодействие между ними происходит с повышенной активностью и высокими скоростями образования целевых продуктов.
Наиболее удобно в настоящее время получать карбиды в дуговом плазмотроне с использованием расходуемых электродов, изготовленных из смеси металла и углерода.
Осаждение из газовой фазы. Этот метод получения карбидов используется при производстве порошков высокой степени чистоты в виде мелких частиц, готовых изделий особенно сложной конфигурации, монокристаллов или плотных покрытий практически на любой подложке.
Метод осаждения карбидов из газовой фазы основан на химических и физических взаимодействиях, возникающих при высоких температурах и протекающих преимущественно на границах раздела фаз и вблизи поверхности твердого тела. Применительно к получению карбидов процесс осуществляется по схеме
MeClx + CnНm + Н2 → МеС + НС1 + Н2
В соответствии с этой схемой восстановителем является водород, а углерод, образующийся в результате разложения углеводорода, связывает металл, выделяющийся вследствие восстановления паров хлорида металла водородом, в карбид.
Методыполученияпорошковнитридов
Основными методами получения нитридов являются: азотирование металлов или их гидридов азотом или аммиаком; метод плазмохимического синтеза;
восстановление оксидов металлов твердым восстановителем (углеродом) в среде азота (аммиака);
осаждение нитридов из газовой фазы.
Азотирование металлов (гидридов металлов). Процесс осуществляет-
ся под воздействием азота, аммиака или какого-либо другого азотсодержащего газа на порошки металлов или их гидридов в муфельных проходных печах при температуре 800–1 200 °С и непрерывной подаче газа. В зависимости от характеристик исходных порошков длительность процесса составляет 1–2 ч.
Существенно влияют на процесс получения нитридов размеры частиц используемых металлических порошков. Поскольку процесс азотирования протекает на границе раздела металл–азот, увеличение поверхности контакта
Процессы порошковой металлургии. Курс лекций |
-186- |

I. ПОЛУЧЕНИЕ ПОРОШКОВ
Лекция 22 Методы получения порошков тугоплавких соединений. Получение порошков карбидов и нитридов металлов
способствует ускорению процесса. Для ускорения процесса образования нитридов необходимо максимально измельчить порошок в тех пределах, когда малый размер частиц не является причиной плохой газопроницаемости шихты. Кроме того, следует иметь в виду, что если металлу свойственно поверхностное окисление, то одновременно с увеличением степени его измельчения будет возрастать относительное содержание кислорода в нем и азотирование затруднится. Последнее обусловлено более высоким коэффициентом диффузии в металл кислорода по сравнению с азотом. По этой же причине необходимо принимать меры для предотвращения попадания кислорода воздуха в зону реакции, а также очищать азот или другой азотсодержащий газ от кислорода.
Применение в качестве исходных материалов гидридов металлов имеет ряд преимуществ, поскольку они являются более хрупкими, чем соответствующие металлы, и легко поддаются измельчению. Кроме того, выделяющийся при разложении гидридов водород восстанавливает оксидные пленки, повышая тем самым активность металла, способствует образованию нитридов высокой степени чистоты. Недостатком применения гидридов является замедление процесса азотирования на начальных стадиях. В этом случае для осуществления азотирования необходимо обеспечить разложение гидрида металла, которое начинается при температуре 900–1 000 °С, что связано с дополнительными затратами энергии.
Применение азота для азотирования предпочтительнее, чем аммиака. Это объясняется тем, что образующийся при диссоциации аммиака водород хотя и является восстановителем, удаляющим с поверхности частиц металла оксидные пленки, но при температуре 400–600 °С он со многими металлами может образовывать гидриды, для разложения которых при более высоких температурах требуется дополнительная затрата энергии.
В основе процесса азотированиялежит механизм диффузии азота вглубь металла с образованием на начальных стадиях твердых растворов. Для повышения подвижности атомов азота в поверхностных слоях рекомендуется ступенчато повышать температуру процесса или вести процесс при повышенных давлениях азота (до 10–25 МПа). Преимущество метода азотирования под давлением состоит в возможности получения нитридов таких металлов, которые не взаимодействуют с азотом при атмосферном давлении (Mo, W).
Для повышения производительности при получении порошков нитридов процесс можно вести в специальных реакторах при температуре 1200–1 400 °С. Реактор представляет собой вертикальную колонну, заполненную азотом. В центре колонны располагается зона нагрева. Дисперсный порошок металла из бункера, находящегося в верхней части колонны, подается в реакционную зону, нагревается, воспламеняется и азотируется. Содержание азота в получаемом таким образом продукте составляет 70–80 % от теоретического.
Метод плазмохимического синтеза. В качестве исходных веществ при этом используются порошки металлов, их галогениды, оксиды, которые вво-
Процессы порошковой металлургии. Курс лекций |
-187- |

I. ПОЛУЧЕНИЕ ПОРОШКОВ
Лекция 22 Методы получения порошков тугоплавких соединений. Получение порошков карбидов и нитридов металлов
дят либо непосредственно в зону разряда, либо в высокотемпературную струю плазмы вне зоны разряда. При этом процесс синтеза нитридов упрощается, поскольку азот, являясь плазмообразующим газом, выступает одновременно в роли одного из компонентов реакции образования нитридов. Среди газов, использующихся в качестве плазмообразующих (Ar, He, H2, N2, O2), азот обладает наибольшей удельной теплотой сгорания в том интервале температур, который поддерживают при плазмохимическом синтезе.
Наиболее высокопроизводительным является использование в качестве исходных материалов галогенидов металлов, в частности хлоридов. При введении хлоридов в плазменную струю они разлагаются, образуя мельчайшие частицы металлов или их пары. Нитриды образуются из газовой фазы при взаимодействии паров металла с азотом. В результате размеры образующихся частиц продукта равняются десяткам нанометров. Так, например, при взаимодействии тетрахлорида титана с азотной плазмой можно получить нитрид титана, состав которого близок к стехиометрическому, размер частиц около 30 нм, а удельная поверхность – 45 м2/г.
Восстановление оксидов металлов твердым восстановителем в среде азота. В основе процесса лежит реакция
МеО + Ме(Х) + N2 → МеN + MeO(XO)
где Me – металл-восстановитель; X – неметаллический восстановитель (C, Si, B).
Чаще всего в качестве восстановителя используют углерод, что приводит, наряду с образованием нитридов, к образованию карбидов восстанавливаемых металлов. Взаимодействие этих компонентов способствует образованию непрерывного ряда твердых растворов. Для уменьшения содержания углерода в получаемом продукте процесс необходимо вести при максимально возможных низких температурах, что снижает вероятность образования карбидов.
Реакции восстановления с последующим азотированием протекают главным образом внутри пор шихты. Поэтому важное значение имеет скорость отвода из зоны реакции СО и доставка в обратном направлении азота. Замедление скорости отвода СО из зоны реакции приведет к повышению его парциального давления в порах и более интенсивному образованию карбидов.
Термическая диссоциация соединений. Процесс получения нитридов можно осуществить в печах сопротивления различного типа, среди которых наиболее широко применяются печи периодического и непрерывного (револьверного типа) действия с виброперемешивающимся слоем гранулированной шихты. Исходные компоненты (оксид, сажа) подвергают смешиванию и при необходимости дополнительно измельчают в шаровых мельницах. Полученную смесь гранулируют или прессуют в таблетки небольших разме-
Процессы порошковой металлургии. Курс лекций |
-188- |

I. ПОЛУЧЕНИЕ ПОРОШКОВ
Лекция 22 Методы получения порошков тугоплавких соединений. Получение порошков карбидов и нитридов металлов
ров, используя в качестве пластификатора водный раствор поливинилового спирта. Подготовленная таким образом шихта обладает хорошими подвижностью и газопроницаемостью, что обеспечивает полноту протекания реакций восстановления и азотирования, непрерывность технологического процесса.
При ведении процесса в печах револьверного типа применяются режимы, представленные в табл. 1.11. Получаемые при этом нитриды по составу близки к расчетным.
Таблица 1.11
Состав и режимы получения нитридов в печах револьверного типа восстановлением оксидов металлов углеродом
с одновременным азотированием
|
|
Время |
|
Содержание, % |
|
|
Нитрид |
Т, °C |
синтеза, |
|
Me |
|
N |
|
|
ч |
Расчетное |
Практическое |
Расчетное |
Практическое |
|
|
|
|
|
|
|
TiN |
1 250 |
1,5 |
87,37 |
78,3–79,0 |
22,63 |
20,0–21,7 |
ZrN |
1 200 |
2 |
86,69 |
87,0–87,5 |
13,31 |
12,5–13,2 |
HfN |
1 200 |
2 |
92,72 |
92,7–93,0 |
7,28 |
6,9–7,3 |
VN |
1 250 |
1 |
88,44 |
78,8–80,8 |
21,56 |
18,0–20,5 |
NbN |
1 200 |
2 |
86,9 |
86,9–87,7 |
13,10 |
12,3–13,0 |
TaN |
1 200 |
1,5 |
92,81 |
92,8–93,2 |
7,19 |
6,7–6,9 |
Cr2N |
1 200 |
1 |
88,14 |
86,7–87,7 |
11,86 |
10,7–11,3 |
Осаждение из газовой фазы. Метод имеет важное значение в связи с возможностью получения продукта высокой степени чистоты в поли- и монокристаллическом состоянии.
Как и при получении других соединений этим методом, в качестве исходных веществ используют галогениды соответствующих металлов.
Процесс ведут при наличии азота высшей степени очистки или аммиака и водорода. Нитриды образуются по одной из схем:
МеCl + NH3 → MeN + НС1 MeOCl2 + NH3 → MeN + Н2О + НС1 MeCl + N2 + H2 → MeN + HC1
Применяемые при этом температурные режимы приведены втабл. 1.12. Чаще всего нитриды осаждаются на нагретой вольфрамовой нити.
Чем тоньше нить, тем быстрее начинается реакция. В большинстве случаев осадок нитрида представляет собой конгломераты, обладающие рыхлой и
Процессы порошковой металлургии. Курс лекций |
-189- |

I. ПОЛУЧЕНИЕ ПОРОШКОВ
Лекция 22 Методы получения порошков тугоплавких соединений. Получение порошков карбидов и нитридов металлов
пористой структурой. Величина образующихся кристаллов зависит от температуры нити. При низких температурах образуются мелкие кристаллы.
|
|
|
Таблица 1.12 |
|
Условия осаждения нитридов из газовой фазы |
||
|
|
|
|
Нитрид |
|
Состав газовой фазы |
Температура процесса, °C |
|
|
|
|
TiN |
TiCl4 : 3N2 : Н2 = 1 : 3 : 2 |
1 100–1 700 |
|
ZrN |
ZrCl4 : 3N2 : Н2 = 1 : 3 : 2 |
1 100–2 700 |
|
ZrN |
ZrCl4 |
: N2 = 1 : 2 |
2 800–3 000 |
HfN |
HfCl4 |
: 3N2 : H2 = 1 : 3 : 2 |
1 100–2 700 |
VN |
VC14 |
: 3N2 : H2 = 1 : 3 : 2 |
1 100–1 600 |
TaN |
TaCl5 |
: N2 = 1 : 2 |
2 400–2 600 |
Возможно также получение нитридов из газовой фазы в виде дисперсных осадков. Так, при получении нитрида титана в основе процесса лежит реакция
2ТiС14 + 2NH3 = 2TiN + 6НС1 + Cl2
которую проводят при температуре свыше 1 000 °С. Сущность подобной технологии состоит в подаче предварительно нагретых до 700–900 °С тетрахлорида титана и аммиака в кварцевую реакционную камеру через форсунку, по внутреннему каналу которой подается тетрахлорид, а по внешнему кольцевому пространству – аммиак. В газовой фазе необходимо обеспечить соотношение 2–4 моль аммиака на один моль TiCl4. Средняя температура в камере должна быть не ниже 750–950 °С, а непосредственно на выходе – 1 000–1 200 °С, что обеспечит высокую степень прохождения реакции. Важным также является обеспечение ламинарных потоков газов в реакционном пространстве при скорости их движения от 2 до 20 м/с. В этих условиях продукт, выходящий из реакционной камеры, представляет собой тонкую взвесь нитрида в газовой среде, состоящей из хлора, паров НС1, непрореагировавших реагентов. Эту смесь охлаждают в трубчатых теплообменниках с последующим отделением нитрида электростатическим осаждением и фильтрацией на керамических фильтрах. Полученный таким образом нитрид представляет собой порошок с размером частиц 0,1–0,6 мкм и содержанием азота 22,2–22,6 %.
Контрольныевопросыизадания
1.Перечислите отличительные свойства и типы структур металлоподобных тугоплавких соединений.
2.Назовите методы получения карбидов металлов.
3.Какие из методов получения карбидов чаще всего применяются на практике?
Процессы порошковой металлургии. Курс лекций |
-190- |

I. ПОЛУЧЕНИЕ ПОРОШКОВ
Лекция 22 Методы получения порошков тугоплавких соединений. Получение порошков карбидов и нитридов металлов
4.Перечислите методы получения нитридов металлов.
5.Назовите основные факторы, определяющие взаимодействие компонентов при получении нитридов.
6.Назовите высокоскоростные методы получения нитридов.
Лекция23 Получениепорошковборидов, силицидовигидридовметаллов
План лекции
1.Методы получения порошков боридов.
2.Методы получения порошков силицидов.
3.Получение порошков гидридов.
Методыполученияпорошковборидов
На практике применяют следующие методы получения боридов: прямой синтез из элементов; металлотермическое восстановление;
восстановление оксидов металлов бором с одновременным борировани-
ем;
электролиз расплавленных сред; осаждение из газовой фазы;
восстановление оксидов металлов углеродом карбида бора (борокарбидный метод);
совместное восстановление смесей оксидов металлов и борного ангидрида углеродом (углетермический метод);
метод плазмохимического синтеза.
Прямой синтез из элементов. Синтез проводят с учетом обеспечения условий прохождения реакции по схеме
Me + В → МеВ
которая может осуществляться как в жидкой фазе путем плавления шихты в дуговых или индукционных печах, так и в твердом состоянии путем спекания этой шихты в печах сопротивления различного типа.
При получении боридов синтезом из элементов без плавления оптимальные температуры лежат в пределах 1 300–2 500 °С. В качестве среды при
Процессы порошковой металлургии. Курс лекций |
-191- |

I. ПОЛУЧЕНИЕ ПОРОШКОВ
Лекция 23 Получение порошков боридов, силицидов и гидридов металлов
низких температурах ведения процесса можно использовать вакуум, при высоких – инертные газы.
Вариантом метода получения боридов синтезом из элементов является спекание смесей горячим прессованием, которое дает возможность получать бориды в виде изделий или полуфабрикатов конечных плотности и размеров.
Разновидностью метода синтеза может быть взаимодействие бора не с чистым металлом, а с его гидридами, нитридами или сульфидами. Однако этот вариант технологии требует соблюдения повышенных мер безопасности в связи с возможностью образования взрывоопасных бороводородов.
Недостаток метода синтеза боридов из элементов состоит в том, что для получения чистых боридов необходимо использовать чистые исходные компоненты.
Металлотермическое восстановление. Этот метод применяется в том случае, когда в качестве исходных материалов используются оксиды металлов, борный ангидрид, а восстановителем служат алюминий, магний, кальций или кремний. Реакция идет по схеме
МеО + В2О3 + Al (Mg, Ca, Si) → МеВ + Al (Mg, Ca, Si)O4
Полноту и скорость прохождения процесса оценивают по величине термичности – отношению теплового эффекта реакции к сумме масс реагирующих веществ (массе шихты). Минимальные значения термичности практически для всех восстановителей должны находиться в пределах 25 Дж/кг шихты.
Наиболее высокопроизводительным для получения боридов является восстановление оксидов магнием и кальцием. С химической точки зрения процесс образования борида происходит таким образом, что вначале магний восстанавливает борный ангидрид до бора, который также восстанавливает оксиды металлов с образованием боридов. Иногда в качестве источника бора применяют борную кислоту, которая в смеси с оксидом металла подвергается обезвоживанию путем медленного нагрева до температуры 800 °С.
Недостатком металлотермического восстановления является сложность разделения продуктов, возможность образования боридов металловвосстановителей.
Восстановление оксидов металлов бором с одновременным борирова-
нием. Процесс протекает по реакции
2МеО + 4В → 2МеВ + В2О2
Для осуществления процесса шихту, состоящую из соответствующего оксида металла и бора, взятых в стехиометрических соотношениях, прессуют в брикеты при давлении 50–100 МПа, загружают в контейнер из иден-
Процессы порошковой металлургии. Курс лекций |
-192- |

I. ПОЛУЧЕНИЕ ПОРОШКОВ
Лекция 23 Получение порошков боридов, силицидов и гидридов металлов
тичного борида и помещают в вакуумную печь. Процесс восстановления и борирования проводят при давлении 10–100 МПа. Для интенсификации удаления образующегося газообразного В2О2 и значительной части летучих примесей, содержащихся в исходных веществах, целесообразно применять вакуумные печи.
Большинство боридов получают при температурах, когда летучесть В2О2 высока, а летучесть В еще незначительна (табл. 1.13).
Таблица 1.13
Режимы получения боридов в изделиях восстановлением оксидов металлов бором в вакууме (время синтеза – 60–150 мин)
Борид |
Температура, °С |
|
Содержание, % |
|
Me |
|
В |
||
|
|
|
||
TiB2 |
1 500 |
69,0 |
|
30,8 |
ZrB2 |
1 600 |
80,3 |
|
19,1 |
HfB2 |
1 700 |
89,0 |
|
10,9 |
VB2 |
1 550 |
80,2 |
|
19,8 |
NbB2 |
1 600 |
80,2 |
|
19,0 |
TaB2 |
1 700 |
88,8 |
|
10,5 |
Недостатком метода восстановления оксидов металлов бором является относительная сложность оборудования и малая производительность, что приводит к высокой стоимости боридов. Поэтому данный метод применяется для получения боридов, используемых в изделиях специального назначения.
Электролиз расплавленных сред. Бориды тугоплавких металлов в виде дисперсных, хорошо закристаллизованных осадков можно получить электролизом расплавов, состоящих из смесей щелочных и щелочно-земельных металлов с их оксидами.
В качестве флюсов используют фториды магния, кальция или лития. Процесс ведут в специальных электролизерах, в которых анодом служит графитовый тигель, а катодом – графитовый или металлический стержень при напряжении 5 В и силе тока 20 А.
Сущность процесса состоит в том, что при электролизе на катоде выделяется элементарный бор, образующийся в результате протекания реакции восстановления ангидрида бора щелочным металлом, возникающим в результате электролиза:
2В2О3 + 3Na → 3NaBO2 + В
Наряду с этим протекает процесс восстановления оксида тугоплавкого металла и взаимодействие восстановленного металла с бором, в результате чего образуется борид.
Процессы порошковой металлургии. Курс лекций |
-193- |

I. ПОЛУЧЕНИЕ ПОРОШКОВ
Лекция 23 Получение порошков боридов, силицидов и гидридов металлов
Химический состав получаемых при электролизе боридов можно регулировать, изменяя состав содержимого ванны. При этом наибольшее влияние оказывает количество оксидов металлов.
Метод получения боридов электролизом отличается простотой технологии, низкими температурами, доступностью исходных веществ. Однако этим методом трудно получить продукты строго определенного состава.
Осаждение из газовой фазы. Метод аналогичен методу получения карбидов и нитридов разложением галогенидов металлов на подогретой подложке при наличии борсодержащих газообразных веществ. Борсодержащими компонентами могут быть бромид или хлорид бора, которые восстанавливаются по реакции
МеСlх + ВС13 + Н2 → МеВ2 + НС1
На процесс формирования осадков влияют температура, скорость прохождения реагентов через реакционное пространство, а также соотношение водорода, хлорида металла и хлорида бора. Метод осаждения боридов из газовой фазы является весьма перспективным для получения боридных покрытий, монокристаллов, а также изделий сложной формы.
Восстановление оксидов металлов углеродом карбида бора (борокар-
бидный метод). Метод является одним из основных промышленных методов получения боридов переходных металлов. В основе этого метода лежат реакции
МеО + В4С4+ С → МехВу + СО Ме(МеН, МеС) + В4С → В2О3 + МеВ + CO
Технологическая схема промышленного получения боридов включает операции приготовления исходных материалов и шихты из них, компактирование шихты, нагрев и последующую переработку полученного продукта путем размола и просева.
Оксиды металлов с целью удаления влаги и примесей органического происхождения прокаливают при температуре ~800 °С в течение 2 ч. Карбид бора сушат при температуре 70–80 °С в течение 4 ч. При использовании крупнозернистого карбида бора производят его размол в шаровых мельницах до размера частиц < 50 мкм. Сажу прокаливают при температуре 400 °С в течение 2 ч. При использовании борного ангидрида промышленных партий его также размалывают в шаровых мельницах до размера частиц < 5 мкм. При этом длительность размола может достигать 15 ч.
Составляя шихту, следует учитывать, что в промышленном карбиде бора соотношение бора и углерода может изменяться чаще всего в сторону увеличения содержания углерода (В % + С % = 100 %). Поэтому при использовании карбида бора, по составу отличающегося от теоретического (78,3% В + 21,7 % С), производят соответствующий перерасчет количества сажи, добавляемой в шихту.
Процессы порошковой металлургии. Курс лекций |
-194- |

I. ПОЛУЧЕНИЕ ПОРОШКОВ
Лекция 23 Получение порошков боридов, силицидов и гидридов металлов
Подготовленные компоненты смешивают в шаровой мельнице в течение 6–8 ч при загрузке барабана 0,3–0,4 объема и отношении массы шихты к массе шаров 1 : 3. После смешивания шихту для разрушения конгломератов и повышения однородности протирают через сито и брикетируют при давлении 50–100 МПа.
Процесс получения боридов можно осуществлять в вакуумных печах с графитовым или металлическим нагревателем или в печах сопротивления с графитовой трубой в среде водорода или конвертированного газа. Процесс получения боридов проводят при начальном давлении в печи 1,5–2,0 Па и температуре 1 500–1 800 °С.
На состав и гомогенность получаемого продукта влияют температура процесса, длительность нагрева до изотермической выдержки. Кроме того, могут оказывать влияние качество исходного сырья и среда нагрева.
Зависимость химического состава получаемого борида от температуры процесса обычно имеет вид, приведенный на рис. 1.38.
C,%
4
80
3
60
2
20
|
|
|
|
|
1 |
|
Рис. 1.38. Зависимость химического соста- |
|
10 |
|
|
|
|
|
|
|
ва борида циркония от температуры про- |
|
|
|
|
|
|
|
||
1600 |
1800 |
2000 Т, °С |
цесса: 1 – Собщ; 2 – В; 3 – Zr; 4 – Σ (Zr, B, |
|||||
|
|
|
|
|
|
|
|
Собщ) |
Оптимальными температурами получения боридов в этом случае являются: для титана, циркония и ниобия – 1 900 °С; ванадия, хрома и вольфрама (W2B5) – 1 800 °С; гафния – 2 000 °С. Длительность изотермической выдержки должна составлять не менее 60 мин.
Длительность подъема температуры до оптимальной оказывает влияние на состав продуктов реакции при длительности изотермической выдержки менее 60 мин. В случае же применения более длительных выдержек скорость нагрева практически не влияет на состав получаемых боридов.
Процессы порошковой металлургии. Курс лекций |
-195- |

I. ПОЛУЧЕНИЕ ПОРОШКОВ
Лекция 23 Получение порошков боридов, силицидов и гидридов металлов
Из свойств исходных компонентов наиболее существенное воздействие оказывают свойства карбида бора и сажи, что прежде всего объясняется влиянием размера частиц и удельной поверхности В4С и сажи на скорость и степень полноты прохождения реакций образования боридов.
В качестве среды печи, в которой образуются бориды, можно использовать водород и конвертированный газ или же проводить процесс в «собственной среде», т.е. в среде газообразных продуктов сгорания графитовой оснастки с образованием оксида углерода. При производстве технически чистых боридов среда практически не влияет на состав получаемого материала. Только при проведении процесса в «собственной среде» наблюдается повышение содержания углерода с 0,2 до 0,4 %.
После нагрева шихты при оптимальных условиях полученный продукт, представляющий собой спекшуюся губку, подвергают размолу в шаровых мельницах и просеву с выделением заданной фракции порошка.
Совместное восстановление смесей оксидов металлов и борного ангидрида углеродом (углеродный метод). Метод также является одним из ос-
новных при производстве боридов в промышленных масштабах. Он основан на реакции
МеО + В2О3 + С → МехВу + СО
иотличается от борокарбидного тем, что в качестве исходного сырья могут быть использованы более дешевые материалы (оксиды, борный ангидрид).
Исходные компоненты смешивают (количество борного ангидрида должно превышать теоретически необходимое) и направляют на синтез (печи Таммана) с использованием защитной среды. Оптимальными температурами процесса получения диборидов в этом случае являются: для титана, циркония
иниобия – 1 900 °С; гафния – 2 000 °С; ванадия и хрома – 1 800 °С; вольфра-
ма (W2B5) – двухстадийное восстановление при 850 °С и выдержка в течение 60 мин, а затем подъем температуры с максимальной скоростью до 1 600 °С. Длительность изотермической выдержки при получении всех боридов составляет 60–120 мин.
Кроме рассмотренных методов бориды можно получать также методом плазмохимического синтеза, аналогично получению нитридов и карби-
дов тугоплавких соединений.
Методыполученияпорошковсилицидов
Для получения силицидов переходных металлов в основном применяют прямой синтез из элементов и восстановление их оксидов с одновременным силицированием.
Прямой синтез из элементов. Данный метод основан на протекании реакции
Процессы порошковой металлургии. Курс лекций |
-196- |

I. ПОЛУЧЕНИЕ ПОРОШКОВ
Лекция 23 Получение порошков боридов, силицидов и гидридов металлов
Me + 2Si = MeSi2
Эта реакция с термодинамической точки зрения проходит легко, поскольку образование силицидов сопровождается значительным экзотермическим эффектом.
Технологическая схема производства силицидов является традиционной для получения тугоплавких соединений и включает операции подготовки исходных материалов, нагрева шихты и дальнейшую переработку путем дробления и размола образовавшегося продукта. При получении силицидов прямым синтезом из элементов в качестве исходного сырья используют порошки соответствующих металлов или их гидридов и порошки кремния. При изготовлении шихты следует учитывать высокую летучесть кремния, вводя соответствующий его избыток в зависимости от условий синтеза.
Исходные компоненты после смешивания для уменьшения объема шихты и увеличения поверхности контакта между реагентами подвергают прессованию в брикеты при давлении 100–150 МПа.
Процесс синтеза можно осуществлять в муфельных печах сопротивления в среде аргона при температуре 1 000–1 200 °С или в вакуумных печах и печах с графитовым нагревателем в среде водорода или конвертированного газа.
В процессе синтеза преобладает реакционная диффузия, а химическая реакция, протекающая на границе раздела силицид–металл, играет в кинетическом отношении второстепенную роль. При этом наблюдается преимущественная диффузия кремния в металл при слабом участии последнего в процессе. Синтез силицидов идет через стадии образования низших силицидов.
Возможно также получение силицидов тугоплавких металлов синтезом из элементов путем спекания исходной шихты горячим прессованием в графитовых пресс-формах.
С целью предотвращения испарения кремния необходимо подбирать такие режимы спекания и свойства исходных порошков, чтобы скорость образования силицида превышала скорость испарения кремния и скорость взаимодействия компонентов шихты с углеродом пресс-формы. Для обеспечения этих условий при горячем прессовании необходимо применять порошки с размером частиц менее 50 мкм и проводить нагрев шихты до температуры спекания с максимальной скоростью. Обычно при горячем прессовании применяют температуры, приведенные ниже, а длительность изотермической выдержки подбирают в зависимости от размеров прессовки и необходимой степени гомогенности и плотности получаемого продукта. Иногда при горячем прессовании, несмотря на максимально допустимые изотермические выдержки, получить гомогенные продукты не удается. Тогда требуется дополнительный гомогенизирующий отжиг в инертной среде в течение нескольких часов.
Процессы порошковой металлургии. Курс лекций |
-197- |
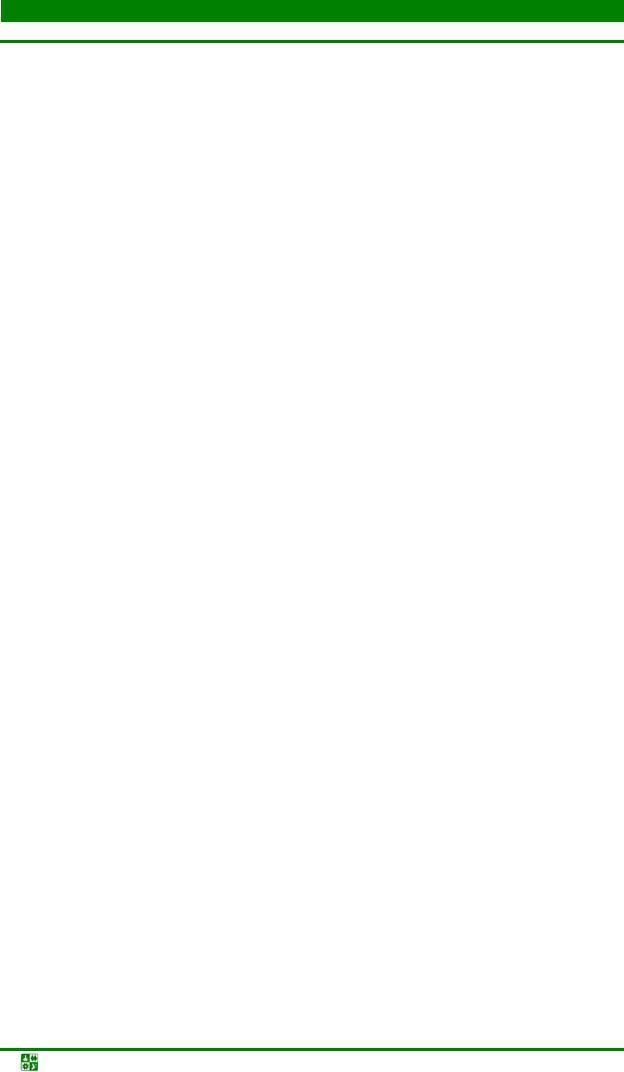
I. ПОЛУЧЕНИЕ ПОРОШКОВ
Лекция 23 Получение порошков боридов, силицидов и гидридов металлов
Восстановление из оксидов с одновременным силицированием. При получении силицидов металлов этим методом можно использовать несколько вариантов:
1)восстановление оксидов металлов кремнием;
2)совместное восстановление оксидов металлов и кремния углеро-
дом;
3)восстановление оксидов металлов карбидом кремния;
4)совместное восстановление оксида кремния, силикатов с оксидами металлов углеродом.
Наиболее широкое применение в производстве силицидов в промышленных масштабах находят первых два варианта, в основе которых лежат реакции
МеО + 3Si → MeSi2 + SiO MeO + 2SiO2 + 5C → MeSi2 + 5CO
Применение первого варианта позволяет получать продукты более чистые по примесям, особенно по углероду. Процесс получения силицидов можно вести в высокотемпературных печах в защитной газовой среде или в вакууме при температуре 1 300–1 800 °С. На скорость и полноту прохождения реакции образования силицидов влияют качество подготовки шихты и ее уплотнение, температура процесса, длительность изотермической выдержки, скорость нагрева до оптимальной температуры, давление в рабочей камере.
Прессование шихты, состоящей из исходных компонентов, даже при минимально возможных давлениях на промышленных прессах дает значительное уплотнение. В результате в процессе нагрева наблюдается спекание продуктов взаимодействия, закупорка пор, и, как следствие, затрудняется удаление образующегося SiO. Последнее является причиной того, что в получаемом силициде всегда содержится до 10–15 % кислорода. Поэтому целесообразно применять гранулированную шихту, что обеспечивает необходимую для удаления газообразных продуктов реакции пористость.
Важное значение имеет скорость нагрева до оптимальной температуры, которая не должна превышать (15±3) град/мин. При более высоких скоростях нагрева образующийся SiO не успевает удаляться из зоны реакции, в результате чего его количество превышает равновесное. Последнее приводит к загрязнению продуктов восстановления промежуточными соединениями, образующимися в процессе реакции.
Оксиды металлов восстанавливаются кремнием, проходя стадии последовательных превращений высших оксидов в низшие с дальнейшим образованием промежуточных кислородсодержащих продуктов, при взаимодействии которых с кремнием образуются в первую очередь богатые кремнием силициды. Далее продукты взаимодействия обогащаются металлом с образованием обогащенных металлом силицидов. Этот процесс можно представить схемой
Процессы порошковой металлургии. Курс лекций |
-198- |
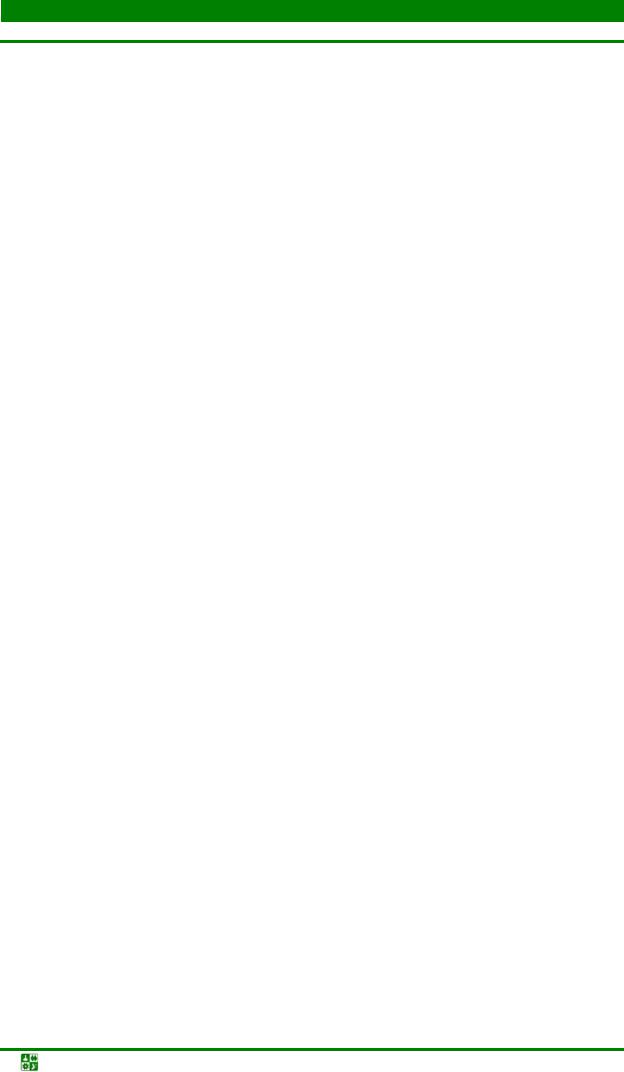
I. ПОЛУЧЕНИЕ ПОРОШКОВ
Лекция 23 Получение порошков боридов, силицидов и гидридов металлов
МеОх → MeОx-n → MeOmSin → MeSip → MeSip-q
Сначала образуются дисилициды как термодинамически более стойкие соединения с сильными ковалентными связями между атомами кремния. С повышением температуры процессы восстановления оксидов металлов и образования силицидов интенсифицируются. Оптимальные режимы получения некоторых силицидов тугоплавких металлов приведены в табл. 1.14.
Этот способ является наиболее пригодным для получения дисилицидов молибдена и вольфрама, поскольку восстановление кремнием для них неприемлемо из-за высокой летучести оксидов молибдена и вольфрама. Используя исходную шихту с некоторым избытком оксида кремния, при температуре 1 900 °С можно получить относительно чистый дисилицид молибдена по реакции МоО3 + 2SiO2 + 7С = MoSi2 + 7CO.
Таблица 1.14 Режимы получения силицидов металлов восстановлением оксидов
Силицид |
Режим получения |
Химический состав, % |
||||
Температура, °С |
Выдержка, ч |
Siобщ |
Siсвоб |
Siсвяз |
||
|
||||||
TiSi2 |
1 350 |
1,0 |
51,9 |
1,7 |
50,2 |
|
VSi2 |
1 550 |
0,5 |
51,5 |
– |
– |
|
NbSi2 |
1 400 |
0,5 |
36,5 |
0,3 |
36,2 |
|
TaSi2 |
1 600 |
0,5 |
20,4 |
0,2 |
20,2 |
При получении силицидов в вакууме на химический и фазовый составы продуктов взаимодействия существенно влияет остаточное давление в печи. Для получения чистых продуктов процесс необходимо проводить восстановлением оксидов кремнием в вакууме при остаточном давлении 1–10 МПа.
На состав образующихся дисилицидов также влияет материал применяемой оснастки. Так, применение графитовых нагревателей и графитовых контейнеров приводит к загрязнению продуктов углеродом и образованию карбида кремния. Чистые дисилициды практически стехиометрического состава можно получать, применяя вакуумные печи с вольфрамовыми нагревателями и тигли из плавленного А12О3.
Получениепорошковгидридов
Порошки гидридовполучают в основном прямым синтезом из элементов. Гидрид титана TiH2 готовят обычно гидрированием при 900 °С титановой губки, полученной магниетермическим восстановлением TiCl4. После
наводораживания губку (гидрид титана) измельчают.
Гидриды циркония получают обработкой его порошка водородом при 400–800 °С. Гидрид, приготовленный при 400 °С, представляет собой ZrH2, а полученный при 800 °С соответствует формуле ZrH, поэтому обычно про-
Процессы порошковой металлургии. Курс лекций |
-199- |
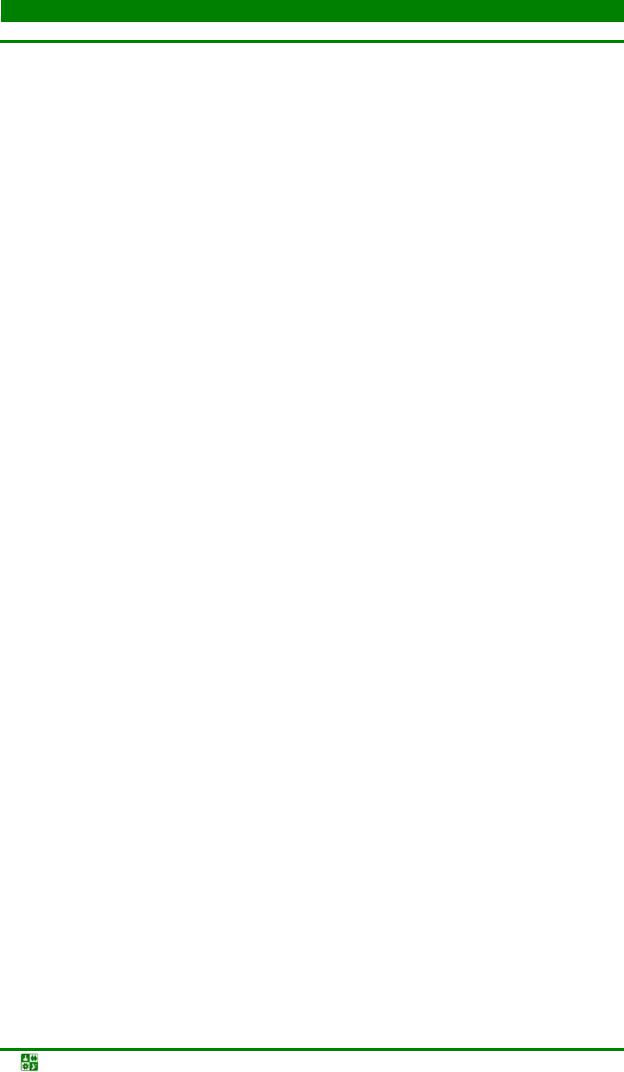
I. ПОЛУЧЕНИЕ ПОРОШКОВ
Лекция 23 Получение порошков боридов, силицидов и гидридов металлов
дукт гидрирования есть смесь этих гидридов. Оба гидрида получают в виде порошков с размером частиц < 40 мкм.
Гидриды гафния состава HfH1,98 и HfН2,1 получают гидрированием металлического гафния при 1 100 °С.
Гидрид ванадия VH, содержащий 16 % ат. водорода, образуется при нагреве порошка металла в водороде при 1 300 °С.
Гидрид ниобия NbH с содержанием 44 % ат. водорода получают при 500–900 °С, а гидриды тантала Та2Н и ТаН – при 800–900 °С.
Контрольныевопросыизадания
1.Назовите методы получения боридов металлов.
2.Какой из методов получения боридов используется для массового производства порошков?
3.Назовите методы получения силицидов металлов.
4.Какие из методов получения силицидов чаще используют на практике?
5.Перечислите факторы процесса, определяющие качество порошков силицидов, полученных методами восстановления оксидов металлов кремнием.
6.Перечислите методы и режимы получения гидридов металлов.
Лекция24 Получениепорошковтугоплавкихсоединенийметодами
самораспространяющегосявысокотемпературного синтезаизоль-гельпроцесса
План лекции
1.Получение порошков методом самораспространяющегося высокотемпературного синтеза.
2.Золь-гель процесс в технологии получения порошков.
Получениепорошковметодомсамораспространяющегося высокотемпературногосинтеза
Метод печного синтеза металлоподобных соединений не позволяет удовлетворить современные требования прикладного материаловедения по чистоте получаемого продукта и производительности. Поэтому активно развиваются другие методы получения таких порошков, среди которых отметим синтез в низкотемпературной плазме, ударно-волновое сжатие и самораспространяющийся высокотемпературный синтез (СВС), имеющий в настоящее время наибольшее значение.
Процессы порошковой металлургии. Курс лекций |
-200- |

I. ПОЛУЧЕНИЕ ПОРОШКОВ
Лекция 24 Получение порошков тугоплавких соединений методом самораспространяющегося высокотемпературного синтеза
В основе СВС лежит явление распространения фронта горения в порошках некоторых тугоплавких химических элементов, приводящее к образованию соответствующих соединений. Метод СВС основан на использовании сильной экзотермичности взаимодействия большинства элементов с бором, углеродом, азотом, кремнием и другими металлоидами, связанной с большой теплотой образования продукта, и высоких значений энергии активации диффузии атомов металлоидов в металлах. Эти особенности процесса позволяют реализовать возможность протекания реакции взаимодействия в узкой зоне, перемещающейся по веществу за счет теплопередачи после локального (местного) инициирования реакции в ненагретой смеси компонентов. Обобщенная химическая схема процесса имеет вид
m |
n |
|
|
∑ai Xi |
+ ∑bjYj |
= Z + Q , |
|
i=1 |
j=1 |
|
|
горючие |
элементы- |
целевой |
тепловой |
элементы |
окислители |
продукт |
эффект |
где X – Ti, Zr, Hf, V, Nb, Та, Mo, W и другие металлы; Y – В, С, N, Si, S, Se, Al
и другие элементы; Z – бориды, карбиды, нитриды, силициды и другие соединения металлов, а также твердые растворы или интерметаллиды.
Элементы X представляют собой порошки металлов, Y применяют в порошкообразном, жидком или газообразном состояниях, а продукт Z является тугоплавким и при температуре процесса находится обычно в твердом состоянии. Химическое взаимодействие элементов протекает в конденсированной фазе, даже если один из реагентов находится в газообразном состоянии.
Кроме обычных вариантов, когда т = 1 и п = 1, реализуются и другие случаи (т ≠ 1, п ≠ 1), приводящие к синтезу более сложных образований (табл. 1.15).
Взависимости от химической природы ведущей реакции горения и агрегатного состояния реагентов все СВС-системы можно разделить на четыре основных класса: безгазовые (без образования газообразных продуктов сгорания), фильтрационные, газовыделяющие, металлотермического типа (с восстановительной стадией).
Вбезгазовых системах (возможно небольшое газовыделение, связанное с самоочисткой от примесей) исходные компоненты, промежуточные и конечные продукты находятся в конденсированном (твердом или расплавленном) состоянии. Синтез можно проводить в вакууме или в инертном газе (состав продуктов горения и его параметры слабо зависят от атмосферы процесса).
Вфильтрационных системах синтез идет в гибридных системах ме-
талл–газ и состав продуктов горения, а также его параметры сильно зависят от давления и состава газовой среды. Большое значение имеют габариты и пористость сбрикетированного металлического порошка, определяющие доставку (фильтрацию) газа в зону реагирования (горения) компонентов, которая может быть организована различным образом.
Процессы порошковой металлургии. Курс лекций |
-201- |
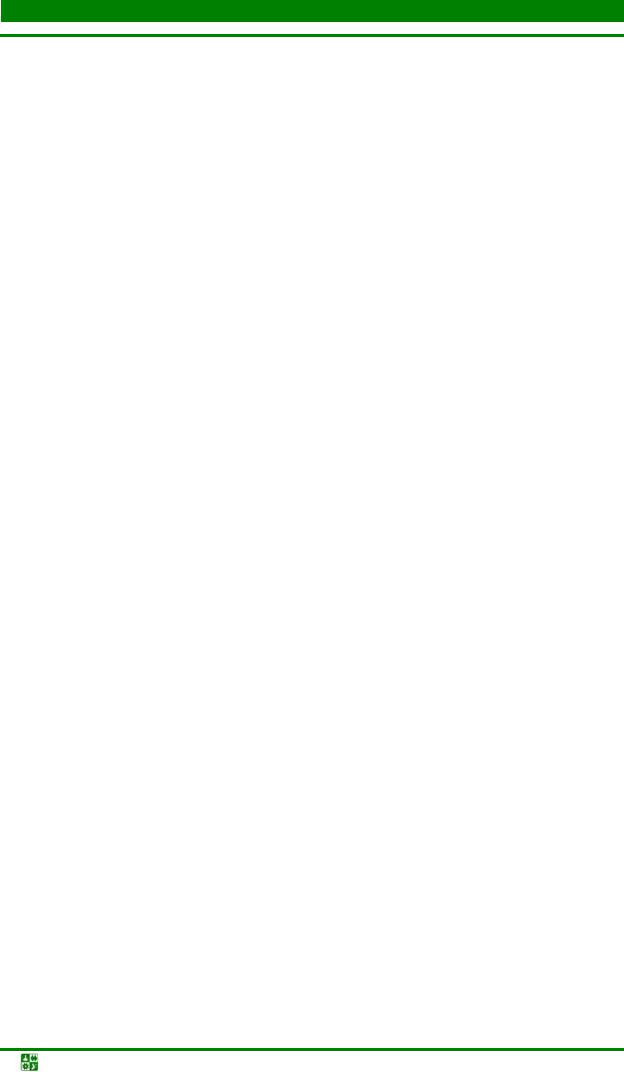
I. ПОЛУЧЕНИЕ ПОРОШКОВ
Лекция 24 Получение порошков тугоплавких соединений методом самораспространяющегося высокотемпературного синтеза
На практике чаще применяют схему, при которой образец с полностью открытой поверхностью помещен в среду газообразного окислителя и фильтрация осуществляется как через исходную шихту, так и через продукты горения.
Таблица 1.15
Тугоплавкие соединения, получаемые при использовании метода СВС
Материал |
Образующиеся соединения |
|
|
|
|
Карбиды |
TiCx, ZrCx, HfC, VC, NbC, Nb2C, TaC, SiC, WC, Cr3C2, Сr7С3, |
|
Мо2С и др. |
||
|
||
Бориды |
TiB2, TiB, ZrB2, ZrB, HfB2, VB2, VB, NbB, NbB2, TaB, TaB2, CrB2, |
|
CrB, MoB, MoB2, WB2 и др. |
||
|
||
Нитриды |
BN, TiN, ZrN, HfN, VN, NbN, TaN (куб), TaN (гексагональный), |
|
Ta2N и др. |
||
|
||
Силициды |
TiSi, TiSi2, ZrSi2, ZrSi, WSi и др. |
|
Халькогениды |
TiSe2, NbSe2, TaSe2, MoSe2, WS2, WSe2 и др. |
|
Твердые растворы |
TiC–Cr3C2, TiC–WC, TiC–TiN, NbC–NbN, MoS2–NbS2, TaC–TaN, |
|
NbхZr1–xСyN1–y и др. |
||
|
||
Интерметаллиды |
Ni3Al, NiAl, TiAl, TiNi, Cu3Al, TiCo, CoAl, Nb3Al и др. |
|
Оксиды: |
|
|
алюминатов |
YA1О3, MgAl2O4 |
|
ниобатов |
LiNbO3, NaNbO3, BaNb2O6 |
|
гранатов |
Y3A15O12, Y3Fe5О12 |
|
ферритов |
CoFe2O4, BaFe2O4, Li2Fe2О4 |
|
титанатов |
BaTiO3, PbTiO3 и др. |
|
молибдатов |
BiMoO6, PbMoO4 и др. |
|
Сверхпроводящая ок- |
YBa2Cu3О7–x, LaBa2Cu3О7–х и др. |
|
сидная керамика |
|
|
Керметы |
TiC–Ni–Mo, TiC–Cr3C2–Ni, TiC–TiN–NiAl–Mo2C–Cr, TiB–Ti и др. |
|
Керамики в системах |
BN, TiC–TiB2, TiB2–Al2О3, A1N–BN, AlN–TiB2, Si3N4–TiN–SiC, |
|
на основе |
SiAlOxNy и др. |
Газвыделяющими являются системы с легколетучими компонентами (S, P, Se и др.) и сжиженным газом (жидким азотом). Целесообразно вести синтез в герметичных емкостях, полностью заполненных твердыми компонентами, так как при их испарении они не покидают реакционный объем, а заполняют лишь поровое пространство.
Всистемах металлотермического типа горение имеет две принци-
пиально различные химические стадии – восстановление оксидов и последующее взаимодействие образовавшихся элементов между собой и с добавками, вводимыми в шихту. Такие СВС-процессы могут быть магнийили алюмотермическими. Должна быть предусмотрена возможность отделения целевого продукта от оксидов восстановителя (MgO или А12О3).
Вобщем случае распространение волны горения является одним из возможных режимов, в котором могут протекать экзотермические реакции;
Процессы порошковой металлургии. Курс лекций |
-202- |

I. ПОЛУЧЕНИЕ ПОРОШКОВ
Лекция 24 Получение порошков тугоплавких соединений методом самораспространяющегося высокотемпературного синтеза
при этом исходная смесь реагентов отделена сравнительно узкой зоной горения от продуктов реакции. Начальная температура шихты низкая (например, комнатная), а температура в зоне реакции, называемая температурой горения, может достигать 3 000–4 000 К.
В стационарных условиях зона горения перемещается в сторону исходной шихты с чрезвычайно высокой постоянной скоростью (до 105–106 К/с), на-
зываемой нормальной скоростью горения.
На рис. 1.39 приведены четыре типичные структуры волны горения: горение с узкой зоной (кривая 1), когда скорость горения определяет-
ся его конечной температурой; горение с широкой зоной (кривая 2), когда сильное торможение реак-
ции взаимодействия компонентов, их полидисперсность и другие причины приводят к тому, что ширина зоны реакции становится больше, чем зоны подогрева;
горение при химическом взаимодействии реагентов (кривая 3), когда полное химическое превращение в шихте происходит в несколько стадий, каждой из которых соответствуют свои тепловой эффект и промежуточный продукт (стадии могут быть пространственно разделены в волне горения – режим «отрыва»);
горение с фазовыми переходами (кривая 4 для двухстадийной реакции), когда, например, при плавлении компонента или продукта реакции одновременно с химическим взаимодействием на температурном профиле волны горения может образоваться плато (изотермическая площадка) с температурой фазового перехода.
|
4 |
|
3 |
1 |
|
4 |
2 |
|
3 |
||
|
2
1
Рис. 1.39. Типы температурных профилей
волны горения при СВС
Т,К
1800
1300
800
0 |
1 |
2 х,мм |
Рис. 1.40. Температурный профиль волны
горения в системе Ti + 3Si (x – расстояние от начала распространения волны горения)
Во многих системах СВС наблюдаются весьма сложные температурные профили волны горения, имеющие перегибы, изотермические площадки и другие особенности, связанные с различными фазовыми переходами, образованием промежуточных продуктов и т.п. (рис. 1.40).
Процессы порошковой металлургии. Курс лекций |
-203- |
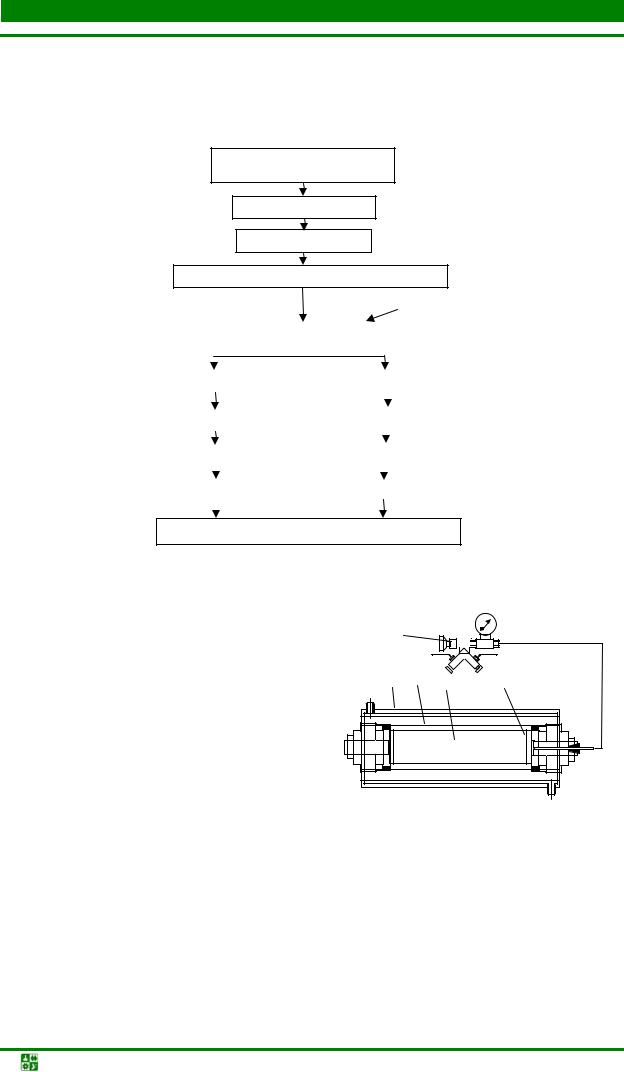
I. ПОЛУЧЕНИЕ ПОРОШКОВ
Лекция 24 Получение порошков тугоплавких соединений методом самораспространяющегося высокотемпературного синтеза
На рис. 1.41 представлена схема СВС-технологии получения порошков, синтез которых проводят в реакторе (рис. 1.42) с различным объемом реакционной зоны (от 1 до 30 л).
Исходные порошки
металлов и неметаллов
Измельчение
Сушка
Шихтовка и смешивание порошков
|
|
|
|
|
Газ |
||
|
|
|
|
|
|
|
|
|
|
Загрузка в реактор |
|||||
|
|
|
|
|
|||
|
|
|
|
|
|
|
|
|
|
|
|
|
|
|
|
Элементный синтез |
|
СВС-магниетермия |
|||||
|
|
|
|
|
|
|
|
|
|
|
|
|
|
|
|
Зачистка спека |
|
Измельчение |
|||||
|
|
|
|
|
|
||
|
|
|
|
|
|
|
|
Измельчение |
|
Кислотное обогащение |
|||||
|
|
|
|
|
|
|
|
|
|
|
|
|
|
|
|
|
Рассев |
|
Сушка |
||||
|
|
|
|
|
|
|
|
|
|
|
|
|
|
|
|
Порошкообразные СВС-продукты
Рис. 1.41. Схема СВС-технологии получения порошков
5
1 2 3 4
Рис. 1.42. Схема СВС-реактора: 1 – корпус; 2 – графитовая футеровка; 3 – реакционная шихта; 4 – грибковый затвор; 5 – газораспределительный узел
Внутреннее устройство реактора зависит от вида синтезируемых СВСпродуктов. При синтезе карбидов, боридов или силицидов внутреннюю поверхность реактора футеруют графитом.
Для синтеза нитридов, карбонитридов и гидридов реактор оснащают специальным устройством, обеспечивающим фильтрацию реагирующего газа в зону реакции; для синтеза халькогенидов, фосфидов и металлотермических процессов устройство реактора позволяет исключить испарение компонентов шихты и их конденсацию на его внутренней поверхности.
Процессы порошковой металлургии. Курс лекций |
-204- |
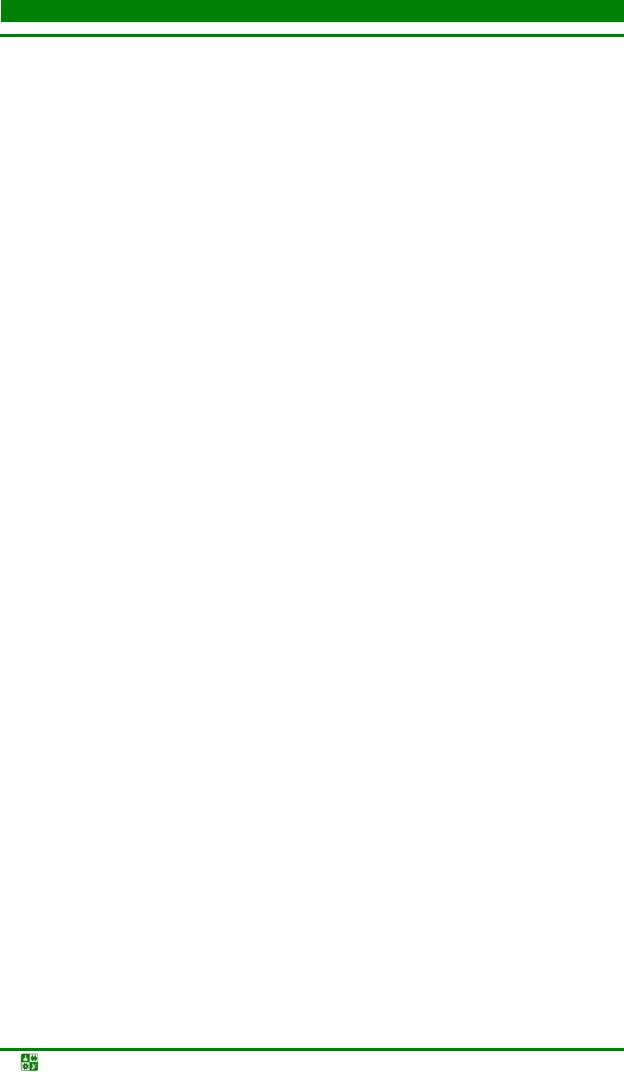
I. ПОЛУЧЕНИЕ ПОРОШКОВ
Лекция 24 Получение порошков тугоплавких соединений методом самораспространяющегося высокотемпературного синтеза
После загрузки шихты, которая может быть предварительно сбрикетирована, реактор закрывают и в зависимости от целевой задачи вакуумируют или заполняют газом (инертным либо участвующим в реакции). Локальное инициирование начала процесса СВС осуществляют с пульта управления подачей кратковременного электрического импульса на вольфрамовую спираль, касающуюся исходной шихты.
Процесс синтеза сопровождается ярким свечением, так как температуры горения в зависимости от конкретной системы составляют 1 500–4 000 °С. Светящаяся зона распространяется либо плавно, либо пульсирует; скорость ее движения составляет обычно 0,5–15,0 см/с. После прохождения фронта горения образец продолжает светиться в течение времени, превышающего длительность охлаждения; это связано с наличием двух макрокинетических стадий протекания химической реакции – в узкой зоне в процессе распространения фронта горения и во всем объеме шихты (брикета).
Получаемые соединения однофазны, хорошо кристаллизованы, хотя иногда получаются и аморфные порошки. Чистота синтезируемых соединений не ниже чистоты исходных реагентов, так как дополнительного загрязнения в процессе СВС не происходит.
Взрывной механохимический синтез (ВМС). Механический метод ак-
тивации (МА) твердофазных химических реакций позволяет проводить их в режиме теплового взрыва. В этом случае роль механической активации заключается в инициировании экзотермической реакции, которая в дальнейшем протекает за счет выделения тепла химической реакции. С использованием ВМС получают сульфиды, карбиды, карбонитриды, силициды и другие тугоплавкие соединения.
Исходные компоненты (стружка, спеки или кусковой материал) подвергают высокоэнергетической механоактивации в герметичном механореакторе энергонапряженной мельницы. Передача энергии происходит за время от нескольких до десятков минут. Тем самым в процессе ВМС осуществляется постепенная «накачка» избыточной энергией реагирующих компонентов. При достижении критических значений этой энергии начинается реакция, протекающая по взрывной кинетике.
Механохимический синтез тугоплавких соединений осуществляется различными методами. Наиболее простой из них – прямой синтез, когда реакция протекает между двумя или несколькими элементами:
m |
n |
MA |
∑ai Xi + ∑bjYj → Z +Q , |
||
i=1 |
j=1 |
|
где X – Hf, Та, Zr, Ti, Nb и др.; Y – С, В, Si, S; Z – химическое соединение; Q – тепловой эффект реакции.
Более сложный синтез представляет собой сочетание реакций восстановления и синтеза:
Процессы порошковой металлургии. Курс лекций |
-205- |

I. ПОЛУЧЕНИЕ ПОРОШКОВ
Лекция 24 Получение порошков тугоплавких соединений методом самораспространяющегося высокотемпературного синтеза
nMe1О + Me2(Me3) + mC → Me2O(Me3O) + MenCm + Q
где Ме1О – оксиды любых металлов и неметаллов, имеющих меньшее химическое сродство к кислороду, чем Ме2(Ме3); Ме2О, Ме3О – образующиеся оксиды металлов Ме2 и Ме3 соответственно; МеnСт – карбиды или другие тугоплавкие соединения (в зависимости от типа окислителя).
Этот способ позволяет использовать дешевое сырье (оксиды), а также получать различные соединения металлов.
Золь-гельпроцессвтехнологииполученияпорошков
В основе этого процесса лежит образование гидроксидов металлов в результате химического превращения высокодисперсных систем (золей) в рыхлые аморфные структуры (гели).
Золи представляют собой системы, в которых частицы высокодисперсной твердой фазы свободно участвуют в броуновском движении, стабилизирующем их во взвешенном состоянии. Различают гидрозоли, органозоли и аэрозоли, у которых дисперсионная среда, соответственно, вода, органическая жидкость или газ.
Золи способны коагулировать, т.е. образовывать крупные агрегаты частиц в виде структурированных систем с последующим разделением фаз – разрушением дисперсной системы. При коагуляции золи превращаются вгели – структурированные системы, в которых частицы соединены в рыхлую пространственную сетку. Коагуляция происходит при удалении лишней воды из системы, вызванном повышением или понижением температуры, воздействием электромагнитных полей, жестких излучений, механическими или химическими воздействиями.
Процессы в водных средах основаны на превращениях, происходящих в такой последовательности: гидролиз → полимеризация → нуклеация → рост.
Результатом гидролиза является связывание некоторых молекулярных групп, содержащих ионы кислорода, с катионами (металлами); в процессе полимеризации происходит образование мостиковых связей между двумя или более катионами посредством лигандов.
Золь-гель процессы можно разделить на коллоидные и полимеризационные. Гелеобразование в коллоидных системах происходит в растворах, содержащих золь одного или более компонентов. Полимеризационный процесс включает процессы поликонденсации с формированием непрерывной полимерной структуры геля, который может содержать катионы различной природы. Полимеризационные процессы происходят с исходными компонентами, которые ионизируются или не ионизируются в растворителе.
При использовании ионизируемых исходных компонентов (солей металлов) катионы металла Me в результате взаимодействия с дипольными молекулами воды образуют группы типа Ме(Н2О)nZ+, которые выделяют протон, сохраняя свое координационное состояние. При взаимодействии образую-
Процессы порошковой металлургии. Курс лекций |
-206- |
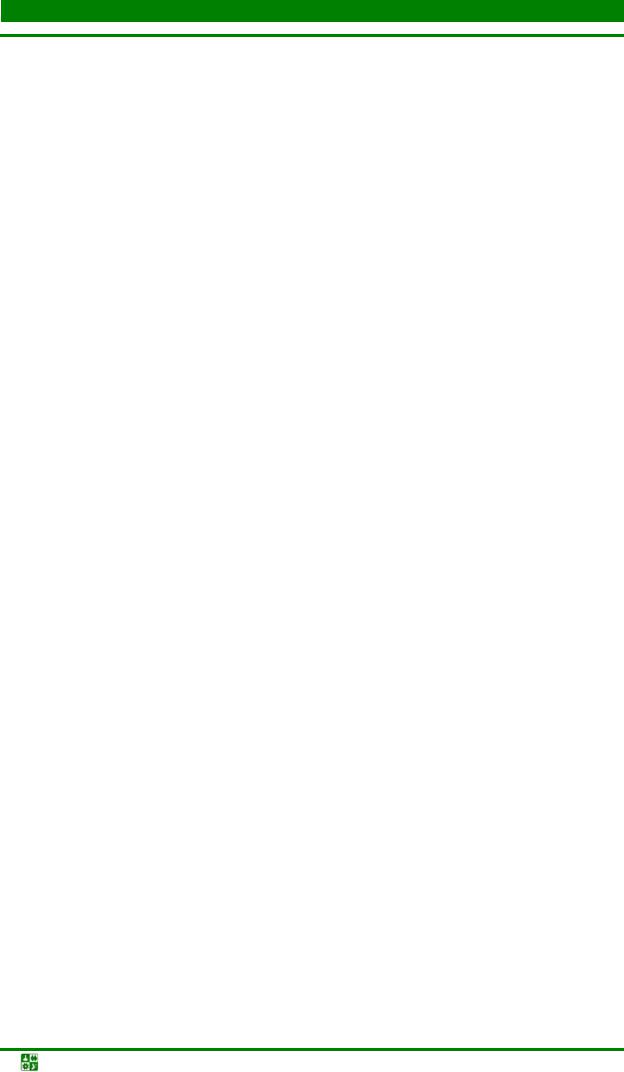
I. ПОЛУЧЕНИЕ ПОРОШКОВ
Лекция 24 Получение порошков тугоплавких соединений методом самораспространяющегося высокотемпературного синтеза
щихся положительно заряженных групп с соответствующими анионами образуются группы, катионы которых могут быть связаны лигандами, включающими О2- (кислородные мостики), ОН- (гидроксильные мостики), Н2О (водные мостики), и анионами А-. Процесс полимеризации зависит от рН среды, температуры (образование комплексов часто ускоряется с повышением температуры), концентрации катионов металлов и природы анионов.
Типичным процессом с неионизируемым исходным компонентом является алкоксидный золь-гель процесс. После гидролиза алкоксида проводят поликонденсацию с дегидратацией:
Me(OR)n + xН2О → Me(ОН)n(OR)n–x + хROH
–Me–ОН + НО–Ме– → –Ме–О–Ме– + Н2О
где Me(OR)n – алкоксид металла; Me – металл валентности п; OR – спиртовая группа; R – углеводородный радикал, соответствующий формуле CmH2m+l.
В результате формируются полимерные макромолекулы (гели) с открытой монолитной структурой.
Размер и распределение частиц порошка зависят от скорости образования статистических зародышей критического размера (нуклеации) и последующего их роста. Для достижения монодисперсности порошков необходимо регулировать или концентрацию исходных компонентов и растворителя (на стадии нуклеации), или извлечение анионов (катионов) из раствора.
Золь-гель методом изготавливают порошки BaTiO3, ZrO2, TiO2, WO3, SrTiO3, Y2O3, A12O3, SiO2, 2Al2O3-2SiO2, Si3N4 и другие, оксидные микросфе-
ры диаметром от 10 до 2 000 мкм и волокна.
Получаемые этим методом порошки активны при спекании. Кроме того, золь-гель метод позволяет получать новые классы материалов, в том числе композиционные, содержащие в матрице дисперсные металлические частицы.
Контрольныевопросыизадания
1.Расшифруйте аббревиатуру СВС.
2.Что лежит в основе метода СВС?
3.На какие классы разделяют СВС-системы?
4.Дайте краткую характеристику видов взаимодействия в СВС-
системах.
5.Какими могут быть процессы в СВС-системах металлотермическо-
го типа?
6.Какой механизм лежит в основе золь-гель процессов?
7.Что такое золи и гели?
8.Какими свойствами обладают золи?
9.Какие материалы изготовляют с применением золь-гель процессов?
Процессы порошковой металлургии. Курс лекций |
-207- |
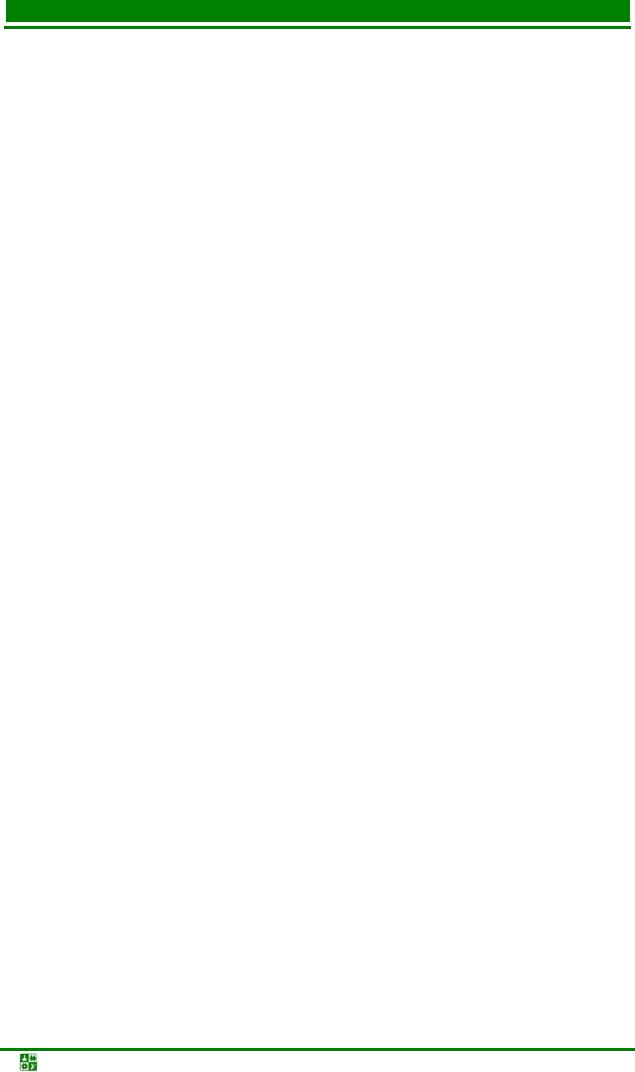
I. ПОЛУЧЕНИЕ ПОРОШКОВ
Лекция25 Методыполученияметаллическихволокон.
Физическиесвойствапорошков
План лекции
1.Технологии получения металлических волокон.
2.Методы определения размеров частиц и гранулометрического состава порошка.
Технологииполученияметаллическихволокон
Порошковое волокно – это разновидность частиц металлического порошка, у которых один из габаритных размеров не менее чем в пять раз превышает остальные.
В связи с развитием техники высоких температур ускоренными темпами растет производство композиционных материалов, армированных волокнами, усами или проволокой из стали, вольфрама, никеля, молибдена, титана и других металлов, графита, оксидов алюминия, бериллия или кремния, карбидов, нитридов, боридов и других соединений тугоплавких металлов. Способы производства волокнистой компоненты таких материалов подразделяют на механические и физико-химические.
Механические способы. Эти способы получили наибольшее распространение при получении волокон.
На практике тонкую проволоку и/или металлическую стружку («шерсть») металла или сплава получают протяжкой более тонкой проволоки через фильеры или путем шабрения и шевингования на станках, дающих непрерывные пряди металла. Как правило, полученные волокна «шерсть» и проволоку режут на специальных приспособлениях на куски определенной (мерной) длины, а затем их обезжиривают в трихлорэтилене, пероксиде натрия или гидроксиде аммония.
Другой разновидностью механических способов является получение волокна из расплава. Например, расплав подают на быстровращающийсядиск, на котором под действием центробежной силы формируются волокна диаметром (поперечным размером) 4–75 мкм, либо выдавливают через отверстие диаметром в несколько десятков микрометров (метод экструзии расплава). При экструзии расплава можно получать как микрокристаллические, так и аморфные волокна большой длины.
Процесс экструдирования проводят следующим образом. Исходный материал расплавляют, перегревая на 50–100 °С, после чего в плавильной емкости создают избыточное давление инертного газа 70–140 кПа или такое, при котором скорость истечения металла из отверстия в ее днище составляет около 2 м/с. Струя металла проходит через замкнутое пространство с вакуумом или определенной атмосферой и попадает в трубу, по которой с такой
Процессы порошковой металлургии. Курс лекций |
-208- |

I. ПОЛУЧЕНИЕ ПОРОШКОВ
Лекция 25 Методы получения металлических волокон. Физические свойства порошков
же скоростью движется охлаждающая жидкость. Выбор охлаждающей жидкости и ее температура зависят от тепловой мощности струи металла. Для экструзии металлов с температурой плавления до 700 °С (Al, Zn, Pb, Sn и др.) применяют воду, с температурой плавления 700–1 000 °С используют 23 %-й водный раствор NaCl, с температурой плавления 1000–1 800 °С – 21,6 %-й раствор MgCl или 51 %-й раствор ZnCl2. Структура затвердевшего волокна зависит от температуры расплава и скорости его охлаждения, которая составляет 103–
105К/с.
Впоследнее время во все более увеличивающихся масштабах производят волокна методами высокоскоростного затвердения расплава (ВЗР).
Существует разработанный почти 60 лет назад непрерывный способ получения тонкой и сверхтонкой проволоки (диаметром < 50 мкм) фонтанированием расплава, разновидностью которого является вытяжка волокон из капли жидкого металла, находящейся в стеклянной трубке-капилляре, подвергаемой вытяжке в длинные нити; стеклянную оболочку с нити затем уд а- ляют травлением.
Особого внимания заслуживает производство нитей диаметром < 1 мм продавливанием смеси порошка исходного материала со связующим через тонкие отверстия. Нити подвергают соответствующей обработке в зависимости от рода связующего с целью его удаления. Таким способом готовят нити вольфрама, молибдена, циркония, бора, кремния, титана, оксидов, карбидов и других металлоподобных соединений.
Физико-химические способы. Их применяют преимущественно для из-
готовления совершенных нитевидных кристаллов высокой прочности. Среди этой группы способов основным является метод получения усов восстановлением различных соединений металлов.
В качестве исходных материалов используют галогениды, сульфиды, оксиды и газообразные или твердые восстановители. Тонкие нитевидные кристаллы растут при определенных условиях восстановления (температура, парциальное давление восстанавливаемого соединения, свойства восстановителя и др.), причем большинство кристаллов при оптимальных условиях процесса получаются гладкими и прямыми, диаметр их 1–20 мкм, а длина – от нескольких сот микрометров до нескольких десятков сантиметров. На практике применяют следующие температурные режимы восстановления галогенидов: для меди – 650 °С, железа – 730–760 °С, никеля – 740 °С, кобальта – 750 °С, марганца – 940 °С. Повышение температуры восстановления сверх оптимальной приводит сначала к возникновению пластинчатых образований, а затем к росту крупных, хорошо развитых кристаллов, тогда как усы не образуются.
Нитевидные кристаллы могут быть получены выращиванием из пересыщенной газовой фазы. Так как в этом случае усы растут за счет притока атомов из газовой фазы, то с повышением температуры скорость роста и диаметр усов увеличиваются. Процесс проводят в предварительно вакуумированной камере, по длине которой создают перепад температур, зависящий от характера (природы) материала получаемых усов. Испарением в вакууме с последующей конденсацией паров получают усы цинка, серебра, платины, бе-
Процессы порошковой металлургии. Курс лекций |
-209- |

I. ПОЛУЧЕНИЕ ПОРОШКОВ
Лекция 25 Методы получения металлических волокон. Физические свойства порошков
риллия, кремния и других металлов. Усы железа, серебра, платины, бериллия, кремния и других металлов можно получить электролитическим осаждением.
Существует несколько методов выращивания усов в твердой фазе. Например, установлено, что на поверхности листов многих металлов (железа, меди, серебра, платины, магния, вольфрама, латуни и др.) при нагреве образуются волокнистые кристаллы диаметром около 2–10 мкм и длиной до нескольких миллиметров. Наиболее интересен метод ускоренного выращивания усов под давлением (метод Фишера). Стальную пластинку толщиной 0,3 см покрывают электролитически слоем олова толщиной 5 мкм и зажимают между двумя жесткими стальными пластинками; края полученного образца шлифуют и полируют. Под действием давления, приложенного к стальным пластинкам, на полированных краях слоя олова происходит ускоренный рост усов, достигающих длины 5 мм при 215 °С. После удаления усов с поверхности их рост начинается снова на прежних местах, что указывает на наличие фиксированных источников (центров) роста усов. Диаметр получаемых усов равен 0,05–5 мкм.
Тонкие металлические волокна можно также получать химическим травлением проволоки до нужного сечения. Например, травлением медной проволоки в азотной кислоте получают волокна диаметром < 1 мкм. Для п о- лучения тонких вольфрамовых волокон успешно применяют метод электролитического травления 15–20 %-м раствором NaOH в поле переменного электрического тока.
Методыопределенияразмеровчастиц игранулометрическогосоставапорошка
Металлический порошок представляет собой совокупность частиц размером от долей микрометра до миллиметра. Практически никогда не встречаются металлические порошки с частицами одного размера.
Совокупность выраженных в процентах количественных содержаний фракций порошка (диапазон размеров частиц между их верхним и нижним значениями) называют гранулометрическим составом порошка; его выражают обычно либо в виде таблиц, либо графически в виде кривой зернистости.
Гранулометрический состав порошка («грансостав») определяют ситовым, микроскопическим, седиментационным, кондуктометрическим и другими методами анализа (рис. 1.43).
Процессы порошковой металлургии. Курс лекций |
-210- |

I. ПОЛУЧЕНИЕ ПОРОШКОВ
Лекция 25 Методы получения металлических волокон. Физические свойства порошков
Кондуктометрический
Рентгеноструктурный
Электронная микроскопия
|
|
|
|
|
|
|
|
|
|
|
||||
|
|
|
|
Оптическая микроскопия |
|
|
|
|
|
|
||||
|
|
|
|
|
|
|
|
|
|
|
|
|
||
|
|
|
|
|
|
Ситовый метод |
|
|
|
|
|
|
||
|
|
|
|
|
|
|
|
|
|
|
||||
|
|
|
|
Сидементационный метод |
|
|
|
|
|
|
||||
|
|
|
|
|
|
|
|
|
|
|
|
|
|
|
|
|
|
|
|
|
|
|
|
|
|
|
|
|
|
0,001 |
0,01 |
0,1 |
1 |
10 |
100 |
1000 |
|
|||||||
|
|
|
|
|
|
|
Диаметр частиц, |
мкм |
Рис. 1.43. Диапазоны определения дисперсного состава порошков различными методами
Ситовый анализ. Анализ грансостава порошка проводят сухим просеиванием в соответствии с межгосударственным стандартом ГОСТ 1831894. Навеску порошка ((100±1) г при насыпной плотности порошка > 1,5 г/см3 или (50±0,5) г в других случаях) просеивают через набор стандартных тканых сеток (сит) с квадратными отверстиями различной величины в соответствии с квалификацией контрольные «К» по ГОСТ 6613-86; номер сетки определяет размер ее отверстия в свету.
Сита должны быть круглыми с диаметром обечайки 200 мм и глубиной от 25 до 50 мм.
Для рассева порошков используют специальное устройство, работающее по принципу вращательного движения со скоростью вращения (300±15) мин-1 при одновременном встряхивании с равномерной частотой (180±10) в минуту.
Просеивание продолжают до окончания рассева или в течение времени, указанного в нормативной документации на конкретный порошок. Время окончания рассева достигается в момент, когда количество порошка, проходящее в течение одной минуты через сито, задерживающее наибольшую его массу, изменяется менее чем на 0,1 % массы пробы для испытания.
Допускается просеивание порошка вручную (его приемы должны быть указаны в нормативной документации на конкретный порошок).
В США применяют свою шкалу сеток. За основу принято сито с размером отверстий в свету 0,074 мм. Есть основной ряд сит с модулем 2 = 1,414 и дополнительный ряд с модулем 4
2 = 1,189. Размер отверстия следующего за основным более крупного сита составляет 0,074
2 = 0,104 мм, затем 0,104
2
=0,147 мм и т.д.
Вэтой системе номер сита указывают в мешах (число меш означает количество отверстий на одном линейном дюйме, равном 25,4 мм). Диаметр
Процессы порошковой металлургии. Курс лекций |
-211- |

I. ПОЛУЧЕНИЕ ПОРОШКОВ
Лекция 25 Методы получения металлических волокон. Физические свойства порошков
проволоки каждого сита равен размеру отверстия d, который определяют по формуле
а = 25,4/2m, |
(1.68) |
где т – число меш.
Например, для сита 200 меш размер отверстия составляет
а = 25,4/(2·200) = 0,0635 мм = 63,5 мкм.
Долю порошка, оставшуюся на сите при просеве, называют плюсовой фракцией, а прошедшую через сито – минусовой фракцией.
Кроме того, часто термином «субситовая фракция» обозначают долю порошка, прошедшего через сетку с наименьшим размером отверстий в данном наборе сит.
Сухие и чистые сита устанавливают одно над другим в такой последовательности, чтобы наверху была сетка с самыми крупными отверстиями, а внизу – с самыми маленькими; набор сит снизу заканчивается обечайкой со сплошным дном-поддоном.
После рассева каждую фракцию порошка, находящуюся на сетке с отверстиями определенного размера, высыпают из сит, начиная с сита с наибольшими отверстиями. Содержимое на сите осторожно стряхивают на одну сторону и пересыпают на глянцевую бумагу. Порошок, приставший к сетке или рамке сита, осторожно протирают мягкой кистью через сетку в следующее сито с меньшими отверстиями. Фракцию, высыпанную на глянцевую бумагу, взвешивают с погрешностью < 0,05 г.
Сумма масс всех фракций должна составлять > 98 % от массы анализируемой пробы. Относительное содержание каждой из фракций X, %, вычисляют с точностью до 0, 1 % по формуле
X = (Gn /G)·100, |
(1.69) |
где Gп – масса данной фракции порошка, г; G – масса испытываемой пробы, г.
Фракцию, количество которой составляет < 0,1 %, обозначают как «следы». Для каждого конкретного порошка количество проб для испытаний должно быть указано в нормативной документации. За величину, характеризующую количество фракции, принимают среднее арифметическое результатов параллельных определений.
Результаты ситового анализа записывают по определенной форме. Например, фракция порошка, прошедшая через сетку с отверстиями 0,125 мм, но оставшаяся на сетке с отверстиями 0,1 мм, обозначается как -
0125...+01 или -125..+100 мкм (запись по ГОСТ 18318-94 имеет вид <125...
≥100 мкм), рядом указывают ее процентное содержание.
Процессы порошковой металлургии. Курс лекций |
-212- |

I. ПОЛУЧЕНИЕ ПОРОШКОВ
Лекция 25 Методы получения металлических волокон. Физические свойства порошков
Для каждой фракции может быть указан средний размер ее частиц dср, определяемый как среднее арифметическое размеров отверстий плюсового и минусового сит.
Зная средний арифметический размер частиц в каждой фракции d1 и ее массу т, можно рассчитать средний размер частиц порошка dn ср.
Благодаря простоте и быстроте выполнения ситовый анализ является основным методом контроля зернистости в порошковой металлургии. Его существенный недостаток заключается в том, что минимальный размер отверстий в сетках составляет 40 мкм (отметим, что в нашей стране есть ограниченное производство сеток с отверстиями 25–30 мкм, а за рубежом выпускают сетки с размером отверстий от 5 мкм), т.е. очень мелкие порошки не поддаются ситовому анализу.
Кроме того, форма частиц может внести искажение в результаты ситового анализа. Например, дискообразные (чешуйчатые) частицы в каком-то количестве задерживаются на сетке с размером отверстий больше их поперечника, а вытянутые иглообразные или дендритные частицы проходят через сито с отверстиями меньше их длины. Поэтому ГОСТ 18318-94 не распространяется на порошки с частицами такой формы, а также порошки с пластификаторами или с размером частиц < 45 мкм.
При работе с ситами, размер отверстий которых < 40 мкм (особенно 5–25 мкм), целесообразно использовать гидравлический метод разделения частиц: навеску порошка в сите помещают под струю воды (или другой смачивающей порошок жидкости) и промывку осуществляют до полного просветления промывающей жидкости.
Возможны и другие приемы воздействия на навеску порошка в наборе сит, например, применение воздушных потоков при ситовом анализе взамен механического воздействия, а также вакуума, ультразвуковых и звуковых колебаний, использование электрического поля и т.д.
Микроскопический анализ. Анализ выполняют по ГОСТ 23402-78 для определения размеров частиц от 1 до 100 мкм при их сферической или полиэдрической форме. Измерение и подсчет количества частиц проводят под оптическим микроскопом визуально или автоматически. За размер частицы принимают при визуальном наблюдении максимальную хорду частицы в горизонтальном или вертикальном направлении; при автоматическом измерении – хорду частицы в горизонтальном направлении.
Для приготовления исследуемого препарата пробу для испытания массой 5–7 г тщательно перемешивают на стеклянной плитке, рассыпают полоской длиной 7–8 см и разделяют на 7 или 8 приблизительно равных частей. Четные части отбрасывают, а нечетные смешивают и повторно сокращают таким же образом, пока не получится проба массой 0,5–1,0 г. Затем переносят на кончике стеклянной палочки небольшое количество порошка на предметное стекло, добавляют 1–2 капли диспергирующей жидкости (вода с 1–2 % поверхностно–активных веществ, глицерин, парафиновое или кедровое масло), распределяют равномерно смесь палочкой по стеклу, накладывают покровное стекло и надавливают на него осторожно во избежание выхода
Процессы порошковой металлургии. Курс лекций |
-213- |

I. ПОЛУЧЕНИЕ ПОРОШКОВ
Лекция 25 Методы получения металлических волокон. Физические свойства порошков
больших частиц за пределы стекла; избыток жидкости удаляют промокательной бумагой.
Увеличение микроскопа подбирают в зависимости от размеров измеряемых частиц; оно должно быть таким, чтобы измеряемые изображения частиц имели размер > 1 мм; для измерения частиц размером 1 мкм требуется увеличение 1 400. Измерение частиц проводят в поле зрения, ограниченном прямоугольником или кругом с нанесенным диаметром; в нем должно находиться < 150 частиц, причем расстояние между ними должно быть не меньше размера большей из соседствующих между собой частиц.
Частицу считают принадлежащей к рассмотренному полю, если она находится внутри его или на половине периметра окружности или прямоугольника, ограничивающего поле зрения
Если порошок содержит частицы в большом интервале размеров и это из-за недостаточной глубины резкости объектива микроскопа не позволяет получать отчетливое изображение одновременно всех частиц, то малые и большие частицы наблюдают при разных увеличениях, но не более трех. При малом увеличении учитывают только большие частицы, а при большом увеличении – только малые.
Количество измеренных частиц или их расчетное количество должно быть > 625 (при выполнении этого условия ошибка измерения < 2 %). Интервал размеров частиц разбивают не менее чем на 6 частей (классов); частицы, размер которых соответствует нижнему пределу класса, относят к более мелкому классу.
Количественное распределение частиц по размерам получают, относя количество измеренных частиц 1-го класса к общему количеству измеренных частиц или к их общему расчетному количеству (если измерения проводили при двух или трех различных увеличениях). Под расчетным количеством измеренных частиц Nрасч понимают их количество, отнесенное к одному выбранному увеличению и определенное по формуле
l |
lср |
(Fср / Fб)2 |
l |
Nрасч = Σб |
Nбi+ Σ Nсрi |
+ Σм Nмi (Fм / Fб)2 |
|
i=1 |
i=1 |
|
i=1 |
(использовано три увеличения), или |
|
|
|
|
l |
l |
|
Nрасч = Σб Nбi+ Σм Nмi (Fм / Fб)2 |
|||
|
i=1 |
i=1 |
|
(использовано два увеличения), где Nбi, Nсрi, Nмi – соответственно, количество частиц i-го класса, измеренных при большом, среднем или малом увеличении; Fср, Fб, Fм – большое, среднее и малое увеличение; Iб, Iср, Iм – число классов, просмотренных при соответствующем увеличении.
Процессы порошковой металлургии. Курс лекций |
-214- |

I. ПОЛУЧЕНИЕ ПОРОШКОВ
Лекция 25 Методы получения металлических волокон. Физические свойства порошков
Число полей зрения, просмотренных при разных увеличениях, должно быть одинаковым.
Если результатом испытаний должно быть массовое (объемное) распределение частиц по размерам, то класс самых крупных частиц, составляющих > 5 %, принимают за контрольный, в котором количество измеренных частиц должно составлять:
Содержание контрольного класса, % |
5–10 |
>10–15 |
>15–24 |
>24 |
Минимальное количество измеренных частиц |
25 |
50 |
75 |
100 |
Если после измерения 625 частиц число их в контрольном классе меньше, чем требуется, как указано выше, то следует на дополнительно выбранных полях зрения или на дополнительных площадях препарата провести дальнейшее измерение частиц с размерами только контрольного класса с тем, чтобы получить необходимое количество частиц.
Средний размер частиц класса равен среднеарифметическому значению размеров верхнего и нижнего пределов класса. Массовое (объемное) распределение частиц по размерам определяют так: возводят в третью степень средний размер частиц класса и умножают результат на количество частиц в этом классе; полученное произведение относят к сумме произведений для всех классов частиц.
Для оценки размеров частиц в интервале 0,001–10 мкм применяют методы электронной микроскопии, которые еще более трудоемки, чем оптическая микроскопия.
Продолжительность микроскопического анализа резко уменьшается при использовании современных сканирующих вспомогательных систем, в том числе на основе обработки информации по телевизионному экрану. Например, при оценке размера частиц порошка по 60 классам продолжительность анализа составляет 8–10 с при ошибке измерения < 2 %.
Классификацию частиц в потоке газа можно провести в приборах разных типов. Один из подобных приборов – элютриатор (рис. 1.44).
Поток воздуха, осушенного в камере 1, проходит U-образную трубку 5 со скоростью V, обеспечивающей транспортировку всей находящейся в трубке навески порошка.
В соответствии с законом Стокса эта скорость должна составлять
V = 29,9·10-4 γп d2, |
(1.70) |
где d – максимальный размер частиц анализируемого порошка.
Процессы порошковой металлургии. Курс лекций |
-215- |

I. ПОЛУЧЕНИЕ ПОРОШКОВ
Лекция 25 Методы получения металлических волокон. Физические свойства порошков
Все элютриаторы дают возможность оценивать грансостав порошка только приближенно.
|
40 |
2,0 |
|
|
1,5 |
|
|
4 |
20 |
|
|
|
30 |
1,0 |
|
|
|
7 |
|
|
10 |
0,5 |
|
|
|
||
|
|
|
|
|
5 |
|
7 |
|
|
|
|
3 |
2 |
5 |
|
|
1 |
|
|
|
|
|
6
8
Рис. 1.44. Прибор для воздушной классификации порошка: 1 – насос; 2 – ротаметр; 3 – осушитель; 4 – измеритель скорости газового потока; 5 – манометр; 6
– U-образная трубка с порошком; 7 – камера; 8 – сборник порошка
Несовершенства разделения порошков на фракции в элютриаторах устранены в приборах, сочетающих газодинамическое воздействие на порошок с центробежным (центрифуга Бако, коническая воздушная центрифуга, коническая аэрозольная центрифуга Гетца и др.).
Кондуктометрический анализ. Метод импульсной кондуктометрии предложен в 1949 г. Коултером. Он предусматривает определение фракционного состава порошка в электрическом поле.
Идея метода проста, но чрезвычайно эффективна: если электропроводящую суспензию (взвесь порошка в электролите) перекачивать из одного объема в другой через короткий канал очень малого диаметра, а металлические электроды поместить раздельно в каждый из этих объемов, то при прохождении частицы через этот канал объем электролита в межэлектродной области изменится и на короткое время резко изменится электросопротивление в канале, что вызовет токовый импульс в цепи нагрузки.
Длительность токового импульса зависит от скорости прохождения частицы по каналу, а амплитуда – от объема частицы (значит, и от ее линейного размера), электропроводности ее материала и некоторых других факторов.
При последовательном прохождении по каналу частиц различного размера возникает последовательность импульсов разной амплитуды, что фиксируется соответствующей аппаратурой. Зная функциональную зависимость, связывающую эти амплитуды с линейным размером частиц, можно определить величину последних.
На рис. 1.45 приведена схема кондуктометрического датчика для измерения размеров частиц. Наиболее ответственной деталью прибора является
Процессы порошковой металлургии. Курс лекций |
-216- |

I. ПОЛУЧЕНИЕ ПОРОШКОВ
Лекция 25 Методы получения металлических волокон. Физические свойства порошков
микроканал, который изготавливают в тонкой сапфировой пластинке, вплавленной в стенку пробирки. Форма канала цилиндрическая, диаметр отверстия равен 2–10 мкм. Кондуктометрический анализ позволяет определять размеры частиц с отношением их диаметра (поперечного размера) к диаметру канала от 0,02 до 0,4–0,5.
|
|
2 |
|
3 |
4 |
|
|
|
|
||
|
|
Кусилителю |
|
|
|
1 |
|
5 |
|
11 |
|
|
|
||
|
|
10 |
|
6 |
|
9 |
|
7 |
12 |
||
8 |
|||
|
|
Рис. 1.45. Схема прибора для измерения размеров частиц порошка кондуктометрическим методом: 1 – стакан с суспензией; 2 – кран; 3 – патрубок насоса; 4
– буферный сосуд; 5 – колено манометра; 6, 7 – контакты счетчика; 8 – пробирка с каналом; 9 – канал; 10, 11 – электроды; 12 – электропроводящая суспензия
Лазерный и рентгеновский методы. Лазерный метод определения фракционного состава порошка основан на явлении рассеивания когерентного монохроматического лазерного луча частицами порошка; величина углового рассеяния лазерных лучей частицами тем больше, чем они мельче.
На рис. 1.46 приведена схема лазерного анализатора размера частиц. Суспензия порошка в нейтральной жидкости непрерывно прокачивается по каналу 2 перпендикулярно лучу от гелий-неонового лазера 1.
Световой поток при прохождении через суспензию равномерно рассеивается частицами порошка по конусу с осью вдоль луча лазера.
С помощью линзы 3 рассеянный поток фокусируется в цилиндрический световой поток, который поступает на плоский вращающийся щелевой фильтр 4. Этот фильтр обеспечивает непрерывную развертку светового луча на также вращающийся перфорированный диск 5, отверстия которого расположены на различных расстояниях от оси вращения по спирали Архимеда. Такое расположение отверстий в сочетании с щелевым фильтром позволяет превращать параллельный световой поток (с изменяющейся плотностью света по сечению) в систему импульсов, отражающих интенсивность различных участков светового потока. Импульсы света, сфокусированные линзой 6, обрабатываются с помощью фотодетектора 7 и микропроцессора8, выдающего гистограммы распределения частиц по размерам в исследуемой навеске порошка.
Процессы порошковой металлургии. Курс лекций |
-217- |

I. ПОЛУЧЕНИЕ ПОРОШКОВ
Лекция 25 Методы получения металлических волокон. Физические свойства порошков
2 |
3 |
4 |
5 |
6 |
7 |
8 |
|
|
|
|
|
|
1
Суспензия
Рис. 1.46. Схема лазерного анализатора размера частиц порошка: 1 – лазер; 2 – кювета с каналом для прокачки суспензии; 3, 6 – линза; 4 – щелевой фильтр; 5 – перфорированный диск; 7 – фотодетектор; 8 – регистрирующее устройство и микропроцессор
Число отверстий во вращающемся диске определяет число групп разделения (количество фракций). Диапазон размеров частиц, в котором эффективна работа лазерного анализатора, составляет от 2 до 170 мкм. Продолжительность анализа – около 2 мин.
На анализе рассеяния рентгеновских лучей, проходящих через среду со взвешенными в ней частицами, основан рентгеновский метод определения малых углов рассеяния (МУР); величина углового рассеяния узкого параллельного пучка рентгеновских лучей может достигать десятков угловых минут на частицах размером 2–100 нм (0,002–0,1 мкм).
Контрольныевопросыизадания
1.Перечислите методы получения металлических волокон.
2.Дайте краткие характеристики методов получения волокон.
3.Перечислите методы выращивания кристаллов из газовой фазы.
4.Расшифруйте понятие «гранулометрический состав».
5.Назовите методы определения гранулометрического состава.
6.Дайте характеристику методов определения гранулометрического
состава.
7.Какие приборы используются для определения гранулометрического состава?
Процессы порошковой металлургии. Курс лекций |
-218- |

I. ПОЛУЧЕНИЕ ПОРОШКОВ
Лекция26 Свойствапорошков. Управлениекачествомпродукции
План лекции
1. Методы определения удельной поверхности порошков.
2. Химические свойства порошков.
3. Принципы управления качеством продукции.
Методыопределенияудельнойповерхностипорошков
Удельная поверхность порошка – это сумма наружных поверхностей всех частиц, составляющих единицу его массы или объема.
Для большинства порошков металлов и неметаллов характерна поверхность от 0,01 до 1 м2/г. Для отдельных порошков (нано- и ультрадисперсных) удельная поверхность составляет 15–25 м2/г. Удельная поверхность зависит не только от размеров порошка, но и от степени развитости (шероховатости) поверхности.
Наиболее часто для определения удельной поверхности используют методы, основанные на измерении газопроницаемости или адсорбционной способности порошка.
Методы измерения проницаемости порошка. Данные методы основа-
ны на оценке фильтрационных процессов при прохождении потока газа через слой порошка с известной относительной плотностью.
Скорость, с которой газ фильтруется через пористый слой порошка, обратно пропорциональна квадрату удельной поверхности.
Фильтрация газа может происходить в двух режимах – вязком и молекулярном. В первом случае просачивание газа через слой порошка осуществляется при давлении, близком к атмосферному, в режиме «просачивания» газовых потоков по порам порошкового тела. Однако в этом случае не учитывается развитая поверхность частиц порошка (вязкое течение проходит только по внешней поверхности частиц порошка). Во втором случае удельную поверхность определяют при просачивании газа через слой порошка в молекулярном режиме – в условиях разряжения, когда длина свободного пробега молекул газа превышает размеры поровых каналов в порошке.
Методы, основанные на фильтрации газа при атмосферном давлении в режиме вязкого течения, могут использоваться для определения удельной поверхности порошков с размерами частиц >10 мкм, а в режиме молекулярного течения – от 3–5 мкм и выше.
На принципе фильтрации газа в режиме вязкого течения работает прибор Товарова (рис. 1.47), а также установки ПСХ и АДЗ. В приборе Тов а- рова пробу засыпают в гильзу и уплотняют, замеряя высоту слоя порошка. Открывая кран сосуда Мариотта, создают постоянный уровень разряжения в нижней части гильзы с порошком. Перепад давлений (степень разряжения)
Процессы порошковой металлургии. Курс лекций |
-219- |

I. ПОЛУЧЕНИЕ ПОРОШКОВ
Лекция 26 Свойства порошков. Управление качеством продукции
определяют с помощью манометра. Удельную поверхность порошка рассчитывают по формуле
Sуд = {14έ1,5/[γп (1 – έ)]}·(F pτ/hμV)0,5,
где έ – коэффициент пористости порошка массой m в слое объемом W, έ = = (Wγп – m)/(Wγп); γп – плотность материала частиц порошка; F – площадь сечения гильзы с порошком; p – величина перепада давления, зафиксированная с помощью манометра; μ – вязкость воздуха; V – объем воздуха, прошедшего за время τ через слой порошка высотой h.
|
1 |
|
1 |
4 |
7 |
|
2 |
5 |
3 |
6 |
|
Рис. 1.47. Схема прибора Товарова: 1 – гильза для порошка; 2 – плунжер; 3 – слой порошка; 4 – сосуд Мариотта; 5 – кран сосуда Мариотта; 6 – стакан для стока воды; 7 – манометр
Прибор Товарова позволяет определить удельные поверхности порошков в диапазоне от 0,3 до 1,5 м2/г.
В приборах ПСХ и АДП разряжение в системе создается с помощью резиновой груши – аспиратора. Удельную поверхность порошка рассчитывают по формуле
Sуд = (А/γп ){ έ3τ / [ (1 – έ )2μ]}0,5,
где А – постоянная прибора (определяется экспериментально по эталонам); γп – плотность материала частиц порошка; τ – время опускания жидкости в манометре между контрольными отметками; μ – вязкость воздуха.
К приборам, работающим по принципу фильтрации газа в режиме молекулярного течения, относится прибор Дерягина (рис. 1.48).
Процессы порошковой металлургии. Курс лекций |
-220- |

I. ПОЛУЧЕНИЕ ПОРОШКОВ
Лекция 26 Свойства порошков. Управление качеством продукции
2 |
3 |
|
|
|
|
4 |
|
|
|
|
17 |
|
|
|
1 |
5 |
6 |
|
7 |
16 |
|
|
|
|
15 |
|
ДН |
8 |
9 |
|
|
|
||
14 |
|
12 |
|
ФН |
|
|
|
|
13 11 10
Рис. 1.48. Схема прибора Дерягина: 1, 3, 4, 8, 10, 13, 17 – вакуумные клапаны (краны); 2, 7, 12 – буферные емкости; 5 – азотная ловушка (для вымораживания воды при откачке порошка); 6 – диффузионный (паромасляный) насос; 9 – форвакуумный насос; 11, 16 – термопарные лампы (для определения степени откачки на вакуум);
14 – трубка с анализируемым порошком; 15 – манометр
В этом приборе анализируемую пробу порошка (с заранее определенной массой) помещают в трубку-держатель между двумя матерчатыми фильтрами и уплотняют до слоя заданной толщины (0,5–5,0 см). Затем осуществляют ступенчатую откачку рабочего объема прибора с помощью форвакуумного и диффузионного насосов до фиксированного давления.
После откачки рабочую трубку с пробой 14 отсекают от вакуумной системы прибора перекрытием кранов 3, 4, 10 и 17 . Баллон 2 заполняют газом до давления порядка 0,1–13,3 гПа (давление в баллоне замеряют вакуумметром 15 или манометром 16). Перед началом измерений кран 1 закрывают и открывают краны 3 и 13, отмечая этот момент как исходную точку отсчета времени. Давление в сообщающихся системах (баллон 2 – проба 14) начинает выравниваться, и возрастание за времяτ давления р под анализируемой пробой фиксируется манометром 11. Время τс, за которое выравнивается давление в буферных емкостях 2 и 12, замеряется с помощью секундомера. Удельную поверхность порошка рассчитывают по формуле
Sуд = {144 έ τс / [13 (1 – έ )h2]} [2RT/(πM)]0,5,
где τс – время запаздывания, отвечающее нестационарной стадии процесса фильтрации газа; h – толщина слоя уплотненного порошка; М – молекулярная масса газа.
Процессы порошковой металлургии. Курс лекций |
-221- |

I. ПОЛУЧЕНИЕ ПОРОШКОВ
Лекция 26 Свойства порошков. Управление качеством продукции
Адсорбционные методы. Эти методы считают наиболее точными и универсальными для определения полной (суммарной) поверхности дисперсных тел. В их основе лежит определение количества вещества (газа), адсорбируемого поверхностью твердых частиц в воде. Если известна площадь, занимаемая отдельной молекулой и масса адсорбированного газа, то может быть рассчитана площадь поверхности исследуемого порошка (площадь, занимаемая адсорбированным газом).
Адсорбционные методы определения удельной поверхности порошков делят на статические (манометрические, гравиметрические или с использованием калиброванного капилляра) и динамические, часто называемые хроматографическими.
Среди статических более распространены манометрические методы. Наиболее известный из них – метод БЭТ, названный по начальным буквам фамилий авторов этого метода (Брунауэр, Эммет, Теллер). Авторы метода предложили в качестве газа-адсорбата взять азот и проводить его адсорбцию на частицах порошка при температуре –196 °С (температура жидкого азота).
|
2 |
|
|
|
5 |
|
|
|
30 |
||
|
|
|
4 |
35 |
|
|
|
|
25 |
|
|
|
|
|
|
||
|
|
|
|
|
|
Рис. 1.49. Схема адсорбционной установки |
|
|
|
20 |
|
|
|
|
15 |
|
|
|
|
|
|
|
|
для определения удельной поверхности по- |
|
3 |
|
|
|
рошков по методу БЭТ: 1 – ампула; 2, 5 – |
1 |
|
|
||
краны; 3 – резервуар; 4 – манометр |
|
|
|
|
|
Измерение удельной поверхности порошка выполняют, помещая навеску порошка (рис. 1.49) в ампулу 1, которую вакуумируют, открывая краны 2 и 5. Затем, наполняя объем ампулы газом, определяют объем пространства над адсорбентом в ампуле и трубопроводах (до крана 2). После вторичной откачки, закрыв кран 2, через кран 5 заполняют азотом резервуар 3, емкость которого известна, фиксируя давление газа манометром 4 и определяя по давлению количество введенного газа. Ампулу с порошком охлаждают, погружая в жидкий азот, и, открыв кран 2, заполняют пространство над порошком газообразным азотом, поступающим из резервуара 3. После установления равновесия адсорбент (порошок) – газ-адсорбат (фиксируется по манометру) вычисляют объем азота, адсорбированный порошком, как разность между объемом азота, введенным в резервуар 3, и объемом остаточного газа. Измерения проводят несколько раз при возрастающих давлениях газа, после чего строят изотерму адсорбции, по которой рассчитывают величину удельной поверхности порошка. В качестве газа-адсорбата можно использовать криптон, бутан, этилен, аргон, метанол, ксенон, аммиак, водород и др.
Общий объем газа V, адсорбированный поверхностью твердого тела, может быть выражен уравнением БЭТ:
Процессы порошковой металлургии. Курс лекций |
-222- |

I. ПОЛУЧЕНИЕ ПОРОШКОВ
Лекция 26 Свойства порошков. Управление качеством продукции
V= Vm cp /{(рs – р)[1+(с – 1)р/ рs ]},
где с – константа прибора; Vm – объем газа-адсорбата в виде монослоя; р – реальное давление газа; ps – давление насыщенного газа.
В линейной форме это выражение может быть записано так:
р/[ V(рs – р)] = 1/с Vm + [(c – 1)/c Vm] p/ рs.
Графическая зависимость р/[V(ps – р)] от p/ps изображается в виде прямой линии с углом наклона (с – 1)/cVm, отсекающей от оси ординат отрезок 1/cVm. Так как с > 1, угол наклона прямой равен 1/Vm. Полученную зависимость, определяющую Vm, можно использовать для анализа изотерм, снятых при отношении p/рs в пределах 0,05–0,35.
Из рассчитанного объема газа Vm, см3, адсорбированного в виде монослоя, рассчитывают поверхность твердых частиц, соответствующую этому монослою:
S = (Vm/Vμ)NAσ.
где Vμ – молекулярный объем одной грамм-молекулы газа, Vμ = 22 414 см3/моль; NA – число Авогадро, NA = 6,023·1023 молекул/моль; σ – площадь, занимаемая одной адсорбированной молекулой газа. При температуре –196 °С адсорбированная молекула азота занимает площадь 0,162 нм2.
Удельная поверхность порошка Sуд = S/m, где т – масса анализируемой пробы порошка.
Во многих случаях объем, занимаемый монослоем адсорбированного газа, может быть определен и графически. Точка перегиба кривой на изотерме адсорбции соответствует моменту образования мономолекулярного слоя газа на поверхности частиц порошка. Количество адсорбированного газа может быть измерено также прямым взвешиванием адсорбента в процессе адсорбции вместе с газом-адсорбатом.
Расчет в этом случае производят исходя из того, что монослой азота на поверхности площадью 1 м2 весит 0,28 мг. В отличие от объемных (манометрических) эти методы называют гравиметрическими.
Статические методы определения удельной поверхности порошка требуют значительных затрат времени, так как процесс установления адсорбционного равновесия весьма длителен.
Более производительными являются динамические методы газовой хроматографии, они основаны на различной адсорбции компонентов газовой смеси поверхностью адсорбента (анализируемого порошка). Среди этих методов наиболее широко используют динамический метод тепловой десорбции газа (ГОСТ 23401-90). Его сущность заключается в измерении количества аргона, адсорбированного на поверхности порошка из аргоно-гелиевой
Процессы порошковой металлургии. Курс лекций |
-223- |
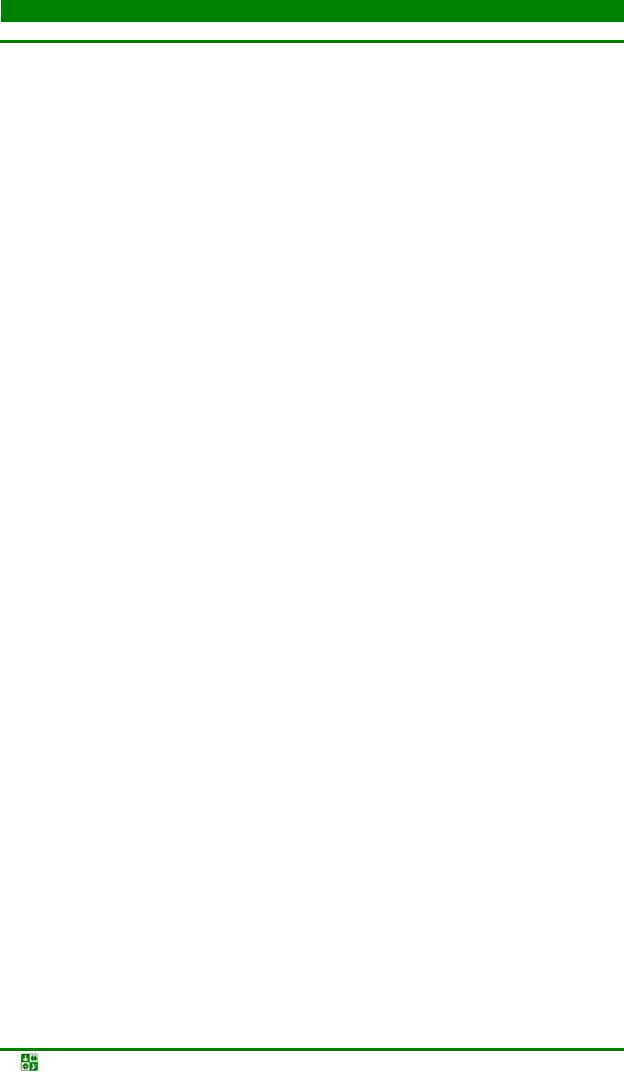
I. ПОЛУЧЕНИЕ ПОРОШКОВ
Лекция 26 Свойства порошков. Управление качеством продукции
смеси (5–7 % Аr, 95–93 % Не) при температуре –196 °С. На начальном этапе анализа газ-адсорбат осаждают на поверхности охлажденного порошка, а затем его десорбируют при нагреве порошка до (20±5) °С.
Объем газа-адсорбата определяют по изменению теплопроводности потока газа-носителя, пропускаемого через анализируемый порошок (фиксируется потенциометром детектора теплопроводности в виде хроматограммы десорбции). Объем адсорбированного газа и площадь удельной поверхности образца вычисляют, сопоставляя площади кривых десорбции анализируемого порошка и образца сравнения (с известной удельной поверхностью).
Масса пробы для испытаний составляет от 5 до 2 г при ожида емой удельной поверхности от 0,1 до 10 м2/г и менее 0,2 до 0,02 г при ожидаемой удельной поверхности 10–50 м2/г.
Метод тепловой десорбции применяют для измерения удельных поверхностей в диапазоне 0,01–1 000 м2/г. Продолжительность одного определения составляет 20–25 мин.
Химическиесвойствапорошков
Оценивая пригодность порошка для изготовления из него материалов и изделий, прежде всего интересуются содержанием основного металла (основных компонентов для порошков сплавов или соединений металлов), примесей, различных механических загрязнений и газов.
Химический состав порошка зависит в основном от метода его производства, а также от степени чистоты исходных материалов. Химический анализ производят по методикам в соответствии с ГОСТами или утвержденной в установленном порядке нормативно-технической документацией; большинство таких методик аналогично применяемым для анализа состава литых металлов и сплавов.
Содержание основного металла в порошке или сумма основных компонентов сплава составляет обычно > 98–99 %, что вполне достаточно для большинства порошковых материалов. Однако при производстве изделий с особыми свойствами (например, магнитными) применяют более чистые металлические порошки.
Количество примесей в порошках определяют по содержанию их в готовой продукции. Исключение сделано для термодинамически неустойчивых (при высоких температурах) оксидов железа, меди, никеля, вольфрама и некоторых других металлов, которые в присутствии восстановителя легко образуют активные атомы соответствующего металла, что приводит к улучшению спекаемости порошка в целом. Поэтому содержание в металлических порошках таких оксидов может быть довольно большим и составлять от 1 до 10 % (0,2–1,5 % кислорода).
Наличие в порошке трудновосстанавливаемых оксидов хрома, марганца, кремния, титана, алюминия и других крайне нежелательно, так как они
Процессы порошковой металлургии. Курс лекций |
-224- |

I. ПОЛУЧЕНИЕ ПОРОШКОВ
Лекция 26 Свойства порошков. Управление качеством продукции
затрудняют в последующем и прессование (формование) порошка, и спекание получаемых заготовок.
Говоря о «нежелательных» примесях, необходимо иметь в виду, что это не касается тех случаев, когда присутствие указанных оксидов придает специальные свойства материалам (дисперсно-упрочненные материалы, керметы и др.).
Определение кислорода в порошках может быть качественным или количественным.
При качественном определении кислорода (по ГОСТ 18897-73) устанавливают потерю массы порции порошка при ее прокаливании в атмосфере сухого водорода или оценивают пикнометрическую плотность частиц порошка.
При количественном определении содержания кислорода навеску анализируемого порошка восстанавливают чистым и хорошо осушенным водородом, улавливают образующиеся пары воды пентаоксидом фосфора, оксидом кальция или каким-нибудь другим активным влагопоглотителем и рассчитывают количество кислорода по привесу соответствующего поглотителя.
Достаточно перспективным для точного определения содержания кислорода является метод нейтронно-активационного анализа.
В металлических порошках содержится значительное количество газов как адсорбированных на поверхности (на каждом квадратном сантиметре
поверхности образуется воздушная пленка массой 0,6·10-6 г), так и попавших внутрь частиц в процессе изготовления или при последующей обработке.
Кроме того, газообразные примеси в порошках появляются также в результате разложения при нагреве загрязнений и добавляемых смазок или связок (используемых для улучшения условий последующего формования заготовок из порошка).
Чем мельче частицы порошка, тем больше газов они адсорбируют. Внутрь частиц газы попадают различными путями. Так, при восста-
новлении химических соединений часть газов-восстановителей и газообразных продуктов реакции не успевает выйти наружу и находится либо в растворенном состоянии, либо в виде пузырей.
Электролитические порошки содержат водород, выделяющийся на катоде совместно с осаждаемым металлом при электролизе водных растворов. В карбонильных порошках присутствуют растворенные кислород и оксиды углерода, а в распыленных – газы, механически захваченные внутрь частиц.
Большое количество растворенных газов увеличивает хрупкость частиц порошков и затрудняет формование (прежде всего в пресс-формах) заготовок, а интенсивное газовыделение при спекании может нарушить процессы, приводящие к формированию свойств изделий (например, стать причиной коробления нагреваемой заготовки). Поэтому целесообразна обработка порошков, особенно высокодисперсных, в вакууме, что обеспечивает эффективное газоотделение.
Газосодержание порошков определяют с использованием сложных методов, основанных на нагреве и плавлении анализируемых проб в вакууме.
Процессы порошковой металлургии. Курс лекций |
-225- |
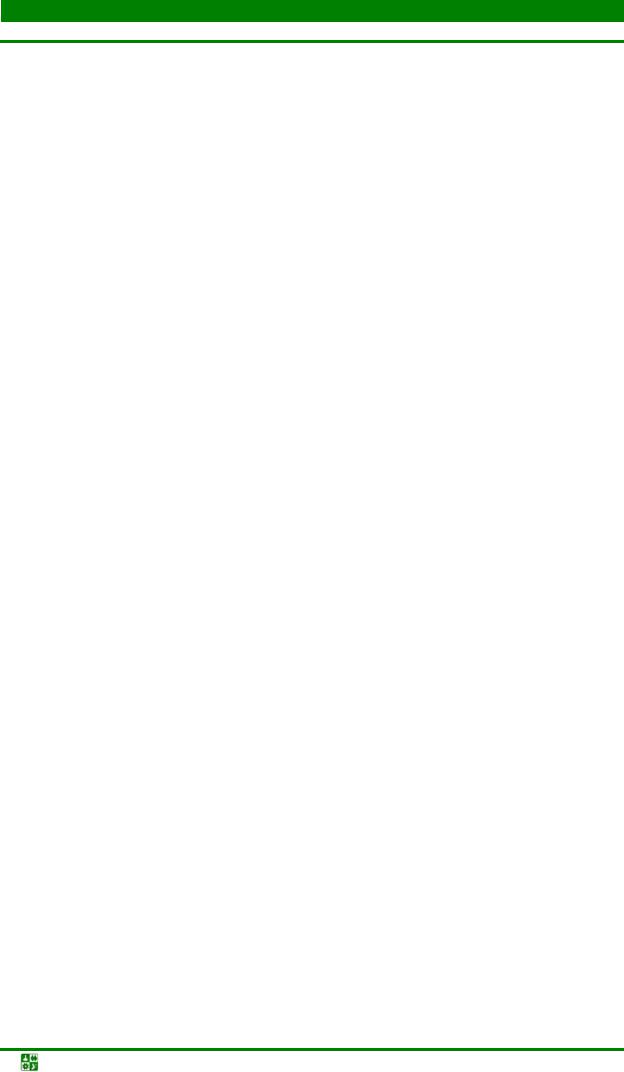
I. ПОЛУЧЕНИЕ ПОРОШКОВ
Лекция 26 Свойства порошков. Управление качеством продукции
Влажность порошка при содержании влаги до 0,1 % определяют высушиванием его навески до установления постоянной массы в электрическом сушильном шкафу. Навеску порошка массой 10 г (погрешность взвешивания < 0,002 г) помещают в предварительно высушенный до постоянной массы стаканчик, закрывают его крышкой и взвешивают. Затем порошок в стаканчике нагревают при 100–105 °С в течение 2 ч, охлаждают и взвешивают, после чего сушку повторяют в течение 0,5 ч, контролируя ее качество.
Содержание влаги X, %, определяют по формуле
X = [(m2 – m3 ) / m1] 100,
где m1, m2, m3 – соответственно, навеска порошка, масса стаканчика с порошком до и после испытания.
Полученные (рассчитанные) значения X округляют до 0,01 %. Содержание в порошке влаги от 0,05 до 0,5 % определяют в соответствии с ГОСТ 18317-73 методом, основанным на отгонке инертным газом при 200 °С из металлического порошка воды и ее взаимодействии с реактивом К. Фишера при электрометрическом титрировании.
Важными химическими особенностями порошков являются их воспламеняемость (пожароопасность), взрываемость и токсичность.
Воспламеняемость порошка. Пожароопасность (часто применяется термин «пирофорность») порошка связана с его способностью к самовозгоранию при соприкосновении с окружающей атмосферой. Подобное взаимодействие при относительно невысоких температурах может привести не только к воспламенению порошка, но и даже к взрыву.
Пожароопасность зависит от химической природы и чистоты металла, крупности и формы частиц порошка, состояния их поверхности (пленки оксидов уменьшают пожароопасность).
В компактном (литом) состоянии лишь немногие металлы пожароопасны и могут воспламеняться при относительно невысоких температурах (например, Mg, Ti, Hf и некоторые другие), тогда как в порошкообразном состоянии пожароопасны очень многие металлы.
Воспламенение может произойти в результате не только окисления, но и других экзотермических реакций, например, образования карбидов или нитридов в процессе взаимодействия металлического порошка с азотом или углеродсодержащим газом. Однако основной причиной воспламенения порошков принято считать их взаимодействие с кислородом (воздухом).
Для порошков некоторых металлов контакт с воздухом может привести к почти мгновенному воспламенению при относительно невысоких температурах; если отсутствуют факторы, подавляющие начавшуюся реакцию (например, на поверхности частиц не возникает плотной защитной пленки оксида, препятствующей дальнейшему непосредственному контакту металла с окружающей средой), воспламенение приводит к устойчивому горению.
Процессы порошковой металлургии. Курс лекций |
-226- |

I. ПОЛУЧЕНИЕ ПОРОШКОВ
Лекция 26 Свойства порошков. Управление качеством продукции
Внешний источник тепла для воспламенения порошка иногда не нужен, если при экзотермической реакции выделяется большое количество энергии. Например, многие высокодисперсные порошки обладают большой удельной поверхностью и способны к самопроизвольному возгоранию при комнатной температуре, в связи с чем их называют пирофорными.
Воспламеняемость порошка зависит от того, находится ли он в свободно насыпанном состоянии (т.е. в виде аэрогеля) или в виде взвеси в окружающей атмосфере (т.е. в виде аэрозоля). Для аэрогелей определяют температуры самонагревания, тления, самовоспламенения и воспламенения, а также энергию воспламенения.
Численные значения показателей воспламеняемости металлических порошков не являются константами вещества, а представляют собой индивидуальные характеристики только конкретного исследуемого порошка при данных условиях испытания и зависят от многих факторов, среди которых решающим является дисперсность порошка.
По мере уменьшения размера частиц температура воспламенения снижается, и высокодисперсный порошок становится пирофорным, т.е. приобретает способность самовоспламеняться при комнатной температуре. Порошок с частицами неправильной формы с выступами и острыми краями (частицы осколочной формы) воспламеняется легче, чем в случае частиц округлой формы.
Взрываемость порошка. Сверхвысокие скорости химического взаимодействия порошка с кислородом приводят к почти мгновенному выделению энергии, которое сопровождается образованием и распространением взрывной волны – происходит взрыв.
Металлические порошки, располагающиеся слоем (аэрогели), не способны взрываться, хотя могут стать источниками взрыва в результате выброса пылевого облачка, его воспламенения и интенсивного горения частиц.
Поэтому, рассматривая взрываемость порошков, имеют в виду взрываемость аэрозолей, т.е. взвеси металлических частиц в газе. Показателями взрываемости порошка могут служить температура воспламенения (при которой происходит возникновение пламени во всем объеме аэрозоля), нижний концентрационный предел (НКП), верхний концентрационный предел (ВКП), конечное давление взрыва и скорость его нарастания.
Практически для оценки степени опасности работы с металлическими порошками достаточно определить для каждого из них температуру воспламенения и нижний концентрационный предел взрываемости (НКПВ), представляющий собой максимальную концентрацию порошка в газе, при которой в случае начавшегося воспламенения группы частиц процесс горения еще не распространяется в аэрозоле самостоятельно.
Характеристики взрываемости в основном зависят от дисперсности металлического порошка, степени его окисленности и содержания кислорода в газовой фазе.
Обычно воспламеняются и взрываются во взвешенном состоянии порошки крупностью частиц < 150–200 мкм.
Процессы порошковой металлургии. Курс лекций |
-227- |

I. ПОЛУЧЕНИЕ ПОРОШКОВ
Лекция 26 Свойства порошков. Управление качеством продукции
Содержание кислорода в газовой фазе (окружающей атмосфере) существенно влияет на характер протекания процесса взрыва аэрозолей металлов, поскольку тепловой взрыв происходит в основном за счет интенсивной экзотермической реакции окисления металла. Уменьшение содержания кислорода обычно понижает взрывную активность аэрозолей металлов. Однако некоторые аэрозоли металлов могут воспламеняться и при отсутствии кислорода в окружающей газовой атмосфере (азот, углекислый газ и др.), с которой металл может реагировать с выделением тепла.
Токсичность порошка. Систематическое вдыхание металлических порошков независимо от их вида может привести к профессиональным заболеваниям. Практически пыль (обычно размер частиц < 4 мкм) любого из металлов, в том числе и совершенно безвредных в компактном состоянии, воздействует на человека и может вызвать патологические изменения в его организме (фиброгенные и аллергические заболевания).
Степень опасности для здоровья человека металлических пылей зависит от их химического состава и степени окисленности, размера частиц, их концентрации, длительности воздействия, путей проникновения в организм и т.д. Технологические и санитарно-технические мероприятия должны поддерживать в производственных помещениях концентрацию пыли на уровне ниже нормы ПДК.
Принципыуправлениякачествомпродукции
Воснове процессов управления качеством продукции производств порошковой металлургии (порошков и изделий) лежат принципы построения систем качества, базирующиеся на формировании процессного подхода.
Методы порошковой металлургии позволяют получать многие виды изделий из обычных материалов, с обычным уровнем свойств, но с лучшими технико-экономическими показателями производства (по сравнению с традиционными технологиями). Одним из достоинств технологий порошковой металлургии является высокая экологичность методов, способствующая снижению загрязнения окружающей среды газами, вредными выбросами, шлаками. В качестве исходных сырьевых материалов для получения порошков используются жидкие и твердые отходы металлургических производств.
Вперечень задач, которые решает порошковая металлургия, входит производство металлических и неметаллических порошков, применяемых при получении красителей, катализаторов, сварочных материалов, пиротехнических средств, абразивных материалов и пр.
Основные операции технологического цикла порошковой металлургии сопряжены с необходимостью контроля качества проводимых процессов. Поэтому выбор адекватных (дающих верное представление о качестве продукции) схем метрологического обеспечения процессов порошковой металлургии является залогом обеспечения их качества.
Процессы порошковой металлургии. Курс лекций |
-228- |

I. ПОЛУЧЕНИЕ ПОРОШКОВ
Лекция 26 Свойства порошков. Управление качеством продукции
В большинстве случаев требования к качеству получаемой продукции регламентируются соответствующими ГОСТами, техническими условия на ее получение или специальными требованиями, выдвигаемыми заказчиками продукции. Показателем качества продукции является соответствие ее этим требованиям. Установить соответствие продукции показателям можно путем анализа свойств получаемых материалов и изделий (структурных, механических, химических и пр.). При этом важное значение имеют как последовательность проведения процедур анализа, так и их периодичность.
Любая технологическая схема процесса представляет собой ряд последовательных операций, которые приводят к изменению свойств материала (изделия). То есть можно сказать, что каждая из операций – это процесс, качество которого можно контролировать, имея набор некоторых входных и выходных данных (необходимо помнить об одном из основных принципов менеджмента качества: то, что нельзя измерить, то и невозможно контро-
лировать!). Правильно разработанная схема метрологического обеспечения (определения свойств материалов или изделий) позволяет выявить (на раннем этапе) некоторые несоответствия процессов и предупредить (свести к минимуму) появление брака (негодной продукции).
Для получения достоверных представлений о ходе процессов большое значение имеет не только выбор адекватного метода определения свойств, но и применение статистических методов обработки результатов анализа. Использование методик статистической обработки позволяет создать предпосылки для научно-обоснованного управления технологическими процессами. А это, в свою очередь, дает возможность снизить материальные и нематериальные издержки производства.
Большое значение для процессов обеспечения качества имеет квалификация персонала. Применение на практике принципов всеобщего управления качеством базируется на непрерывном обучении и «вовлечении» персонала (создании предпосылок для заинтересованного подхода к деятельности), который обеспечивает необходимую культуру производства. Любое подразделение организации – это система взаимодействующего персонала, который на различных этапах производства решает определенный круг задач. Наряду с процессным подходом, для решения задач по управлению качеством продукции целесообразно использовать такую организационную форму взаимодействия, как проект. Типичным глобальным внутренним проектом является разработка и внедрение системы качества. В качестве минипроекта можно рассматривать улучшение отдельного процесса (отдельной технологической операции). Во всех случаях при возникновении проекта кто-то в организации должен взять на себя ответственность за его реализацию и получить полномочия в виде «собственника», или «владельца», проекта. Только в этом случае смогут реализоваться лидерские функции руководителя. Руководитель проекта формирует «команду», ставит задачи и определяет полномочия членов команды (делегирует полномочия). Делегирование полномочий основано на доверии, а доверие – один из самых важных элементов культуры, предназначенный для эффективной работы в условиях производства. Оно создаёт
Процессы порошковой металлургии. Курс лекций |
-229- |

I. ПОЛУЧЕНИЕ ПОРОШКОВ
Лекция 26 Свойства порошков. Управление качеством продукции
предпосылки для открытости информационных потоков в команде, для их прозрачности. Прозрачность информационных потоков, в свою очередь, способствует вовлечённости как персонала, так и делегированию полномочий.
Вовлечённость персонала (прежде всего команды проекта) усиливается при использовании принципов парсипативного управления, т.е. при предоставлении всем членам команды реальной возможности участвовать в управлении. На практике это означает систематическую возможность участия в выработке и реализации управленческих решений. Такая возможность рождает в людях чувство сопричастности, которое резко усиливает мотивацию к творческому труду, являющемуся основой для повышения качества продукции.
Непрерывное повышение квалификации персонала, применение на практике современных методов управления качеством и обоснованный подход к построению схем метрологического обеспечения процессов способно решить многие задачи действующего производства.
Контрольныевопросыизадания
1.Укажите методы определения удельной поверхности.
2.Какие недостатки имеют статические методы определения удельной поверхности?
3.Работа каких приборов построена на принципе фильтрации газа в режиме вязкого течения?
4.Назовите наиболее распространенные статические методы.
5.В чем сущность динамического метода тепловой десорбции газа?
6.Перечислите химические свойства порошка.
7.Какие принципы заложены в основу процессов управления качеством продукции?
8.На чем основывается получение достоверных представлений о ходе процессов?
Процессы порошковой металлургии. Курс лекций |
-230- |