
- •Оглавление
- •ВВЕДЕНИЕ
- •I. ПОЛУЧЕНИЕ ПОРОШКОВ
- •Лекция 16 Восстановление химических соединений металлов из растворов солей и газообразных соединений металлов
- •II. ФОРМОВАНИЕ И СПЕКАНИЕ ИЗДЕЛИЙ ИЗ МЕТАЛЛИЧЕСКИХ И НЕМЕТАЛЛИЧЕСКИХ ПОРОШКОВ
- •Введение
- •Лекция 13 Твердофазное спекание материалов
- •Лекция 20 Жидкофазное спекание и инфильтрация порошковых формовок. Брак при спекании
- •Лекция 25 Методы определения механических характеристик порошковых тел. Заключение
- •ЗАКЛЮЧЕНИЕ
- •БИБЛИОГРАФИЧЕСКИЙ СПИСОК
- •ПРИЛОЖЕНИЯ

II. ФОРМОВАНИЕ И СПЕКАНИЕ ИЗДЕЛИЙ ИЗ МЕТАЛЛИЧЕСКИХ И НЕМЕТАЛЛИЧЕСКИХ ПОРОШКОВ
Лекция 20 Жидкофазное спекание и инфильтрация порошковых формовок. Брак при спекании
Лекция20 Жидкофазноеспеканиеиинфильтрацияпорошковыхформовок.
Бракприспекании
План лекции
1.Спекание порошковых тел с жидкой фазой, исчезающей в процессе спекания.
2.Инфильтрация порошковых формовок.
3.Брак при спекании и меры по его предупреждению.
Спеканиепорошковыхтелсжидкойфазой, исчезающейвпроцессеспекания
При спекании систем с жидкой фазой, исчезающей в процессе изотермической выдержки (с образованием твердого раствора или тугоплавкого соединения на основе фаз компонентов А и В), пока существует расплав, спекание является жидкофазным и частицы тугоплавкого компонента А могут стягиваться силами поверхностного натяжения, что проявляется в усадке порошкового тела.
В определенных условиях при жидкофазном спекании имеет место объемный рост порошкового тела, который может быть связан с преимущественной диффузией жидкой фазы в частицы тугоплавкого компонента. Это на ранних этапах спекания приводит к росту частиц тугоплавкого компонента и увеличению размеров пор. Увеличение пористости можно оценить следующим аналитическим выражением:
П = П0 + С(1 – П0), |
(2.60) |
где П0, П – пористость порошкового тела до и после спекания соответственно; С – объемная концентрация легкоплавкой добавки (доли единицы).
Выражение (2.60) справедливо при достаточно малых значениях исходной пористости порошкового тела и количествах жидкой фазы < 40 % (об.).
Инфильтрацияпорошковыхформовок
Инфильтрация (до 1982 г. применяли термин «пропитка») – это процесс заполнения пор порошковой формовки расплавленным металлом или сплавом.
Сущность метода инфильтрации достаточно проста: из порошка более тугоплавкого компонента формуют пористый каркас, а затем заполняют его пустоты (поры) расплавленным более легкоплавким компонентом (металлом
Процессы порошковой металлургии. Курс лекций |
-365- |
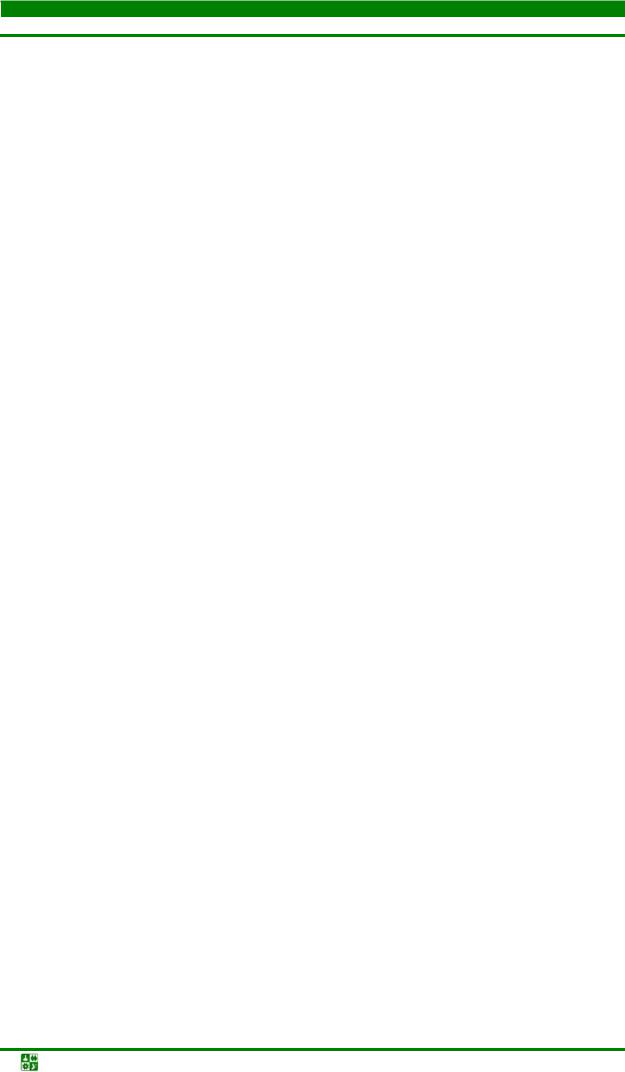
II. ФОРМОВАНИЕ И СПЕКАНИЕ ИЗДЕЛИЙ ИЗ МЕТАЛЛИЧЕСКИХ И НЕМЕТАЛЛИЧЕСКИХ ПОРОШКОВ
Лекция 20 Жидкофазное спекание и инфильтрация порошковых формовок. Брак при спекании
или сплавом). Для улучшения инфильтрации к порошку тугоплавкого компонента перед формованием добавляют небольшое количество (2,5–5,0 %) порошка инфильтруемого (или любого другого легкоплавкого) компонента. Температура инфильтрации должна быть на 100–150 °С выше температуры плавления легкоплавкого металла.
Скорость инфильтрации составляет десятые доли миллиметра в секунду, а толщина слоя зависит от свойств расплава и длительности его контакта с твердым каркасом:
h = (1/π) (σж cos θ rэ τ /ηж)0,5, |
(2.61) |
где rэ – эффективный радиус поровых каналов; ηж – вязкость расплава. Термодинамическое условие инфильтрации (в результате заполнения
пор расплавом свободная энергия системы должна уменьшаться) можно выразить следующим образом:
σж cos θ > 0. |
(2.62) |
Поскольку σж всегда больше нуля, то основным условие осуществления инфильтрации является то, что угол смачивания θ должен быть < 90°. При θ > 90° инфильтрация происходить не будет (например, пористое тело из оксида алюминия невозможно пропитать такими жидкими металлами, как медь, никель или железо).
Инфильтрацию из внешних источников ведут по методу наложения или по методу погружения.
По методу наложения пористый каркас из порошка тугоплавкого компонента вместе с помещенным на нем требуемым количеством твердого (для инфильтрации) легкоплавкого металла помещают в печь с защитной атмосферой и нагревают до необходимой температуры (объем легкоплавкого компонента рассчитывают исходя из объема пор каркаса). Образующийся расплав впитывается порами каркаса.
По методу погружения пористый каркас опускают в предварительно расплавленный легкоплавкий компонент.
После инфильтрации получаемый композиционный материал практически не содержит пор и легко поддается последующей деформации.
Бракприспеканииимерыпоегопредупреждению
При спекании появляется не только брак, вызванный нарушением технологии, но и выявляется брак предыдущих операций изготовления порошка, порошковых смесей и формовок.
Процессы порошковой металлургии. Курс лекций |
-366- |

II. ФОРМОВАНИЕ И СПЕКАНИЕ ИЗДЕЛИЙ ИЗ МЕТАЛЛИЧЕСКИХ И НЕМЕТАЛЛИЧЕСКИХ ПОРОШКОВ
Лекция 20 Жидкофазное спекание и инфильтрация порошковых формовок. Брак при спекании
Скрытый расслой – проявление трещин, образующихся в результате неправильного режима формования в виде небольших нарушений сплошности, невидимых невооруженным глазом. Брак неисправим.
Коробление и искажение формы – нарушение требуемых геометрических размеров порошкового изделия. Часто наблюдается в плоских изделиях, толщина которых незначительна по сравнению с длиной, особенно в случае изготовления изделий из высокодисперсных порошков, дающих значительную усадку при спекании. Появлению такого вида брака способствует плохое смешивание компонентов шихты, неравноплотность порошковой формовки и слишком быстрый ее нагрев при спекании. Этот брак может быть исправлен (хотя и не всегда) последующей холодной или горячей обработкой давлением.
Пережог – нарушение нормальной структуры порошкового изделия, проявляющееся в виде ее загрубления (чрезмерного роста частиц), повышения пористости или растрескивания из-за существенного превышения заданной температуры спекания. Брак неисправим.
Недопекание – нарушение требований плотности и прочности порошкового изделия после спекания в связи с заниженной температурой или длительностью выдержки при нагреве. Брак может быть исправлен повторным спеканием.
Окисление – появление на поверхности порошкового изделия цветов побежалости, окалины или коррозии. Этот вид брака связан в основном с нарушением состава защитной атмосферы при спекании и в ряде случаев может быть исправлен повторным нагревом в восстановительной атмосфере. При наличии в составе порошкового материала компонентов, образующих трудновосстановимые оксиды, такой брак неисправим.
Корочка – дефект при спекании порошковой формовки, заключающийся в образовании в поверхностном слое структуры, отличающейся от заданной. Например, это может иметь место из-за разложения органических связок, вводимых в порошок. Брак неисправим. Для предупреждения его появления необходим медленный и равномерный нагрев порошковой формовки, тщательное ее укрытие засыпкой и достаточный расход защитного газа.
Вспучивание – образование пузырей на поверхности спеченной заготовки из-за интенсивного газовыделения при жидкофазном спекании или местных перегревов в связи с неравномерностью нагрева порошковой формовки в печи, вызывающих расплавление компонентов при твердофазном спекании. Брак практически неисправим. Предупредить его появление можно подбором порошков, изменением режима спекания и способа нагрева порошковой формовки.
Выпотевание – выделение жидкой фазы на поверхности порошкового изделия при жидкофазном спекании из-за плохой или ухудшающейся смачиваемости расплавом тугоплавкой составляющей материала. Брак неисправим. Для предупреждения его появления химический состав материала должен быть скорректирован.
Процессы порошковой металлургии. Курс лекций |
-367- |
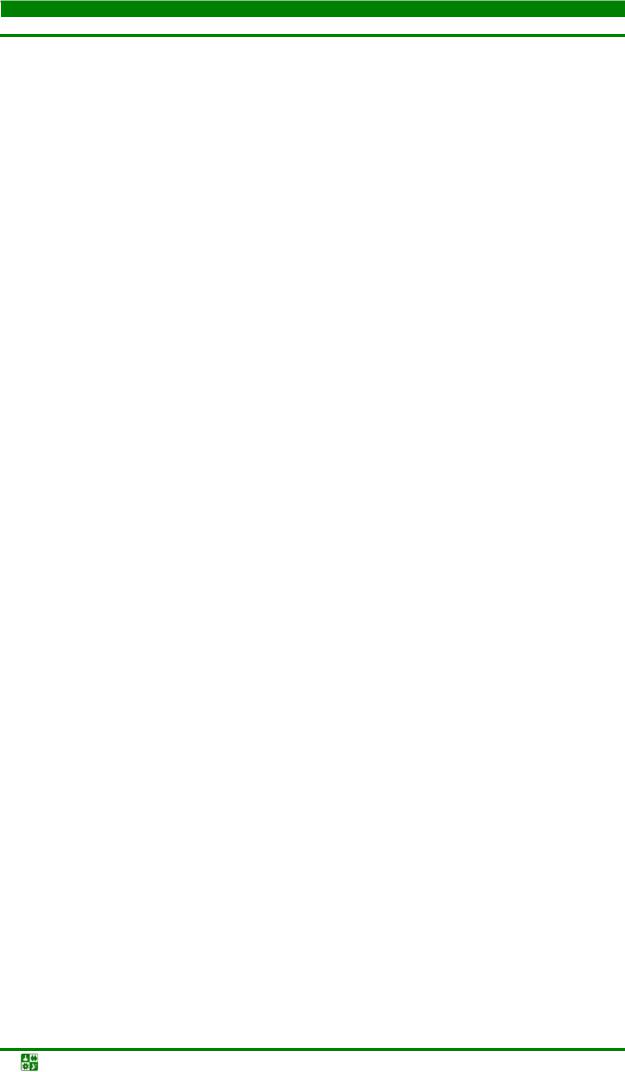
II. ФОРМОВАНИЕ И СПЕКАНИЕ ИЗДЕЛИЙ ИЗ МЕТАЛЛИЧЕСКИХ И НЕМЕТАЛЛИЧЕСКИХ ПОРОШКОВ
Лекция 20 Жидкофазное спекание и инфильтрация порошковых формовок. Брак при спекании
Диффузионная пористость – пористость, возникающая при спекании порошковой формовки, состоящей из компонентов, обладающих различными коэффициентами взаимной диффузии.
Обезуглероживание – уменьшение содержания углерода в поверхностных слоях порошкового изделия, в основном из-за повышенного содержания окислителей в атмосфере горячей зоны печи. Для предупреждения опасности обезуглероживания изделий лодочки (поддоны) с порошковыми формовками закрывают металлическими или графитовыми крышками, а также применяют защитные засыпки, содержащие углерод. Слабо обезуглероженные порошковые изделия можно исправить, спекая их повторно в углеродсодержащей засыпке при минимальном токе водорода.
Сажистый налет – образование на поверхности порошковой формовки темного налета в результате разложения оксида углерода, метана или других углеводородов. Этот вид брака может появиться из-за наличия на поверхности порошковой формовки тяжелых масел и других веществ, запекающихся при нагреве с образованием углеродсодержащих налетов.
Сульфидная пленка – образование на поверхности порошкового изделия налета, содержащего соединения серы.
Разъедание и шероховатость поверхности – нарушение цельности поверхности порошкового изделия в результате разложения или восстановления каких-либо химических соединений, которые были на поверхности порошковой формовки или образовались при ее нагреве в печи.
Контрольныевопросыизадания
1.С чем связан рост порошковой формовки при жидкофазном спекании?
2.Напишите уравнение, которое позволяет оценить рост порошковой формовки при жидкофазном спекании.
3.Что такое «инфильтрация»?
4.Что является термодинамическим условием инфильтрации?
5.При каком угле смачивания инфильтрация проходить не будет?
6.Назовите факторы, влияющие на инфильтрацию пористого каркаса жидкой фазой.
7.Назовите методы инфильтрации порошковых тел.
8.Перечислите виды брака, проявляющиеся при спекании порошко-
вых тел.
9.Назовите виды брака при спекании, которые можно исправить.
10.С чем может быть связано проявление брака спеченных изделий?
Лекция21 Обработкаспеченныхпорошковыхизделий
Процессы порошковой металлургии. Курс лекций |
-368- |

II. ФОРМОВАНИЕ И СПЕКАНИЕ ИЗДЕЛИЙ ИЗ МЕТАЛЛИЧЕСКИХ И НЕМЕТАЛЛИЧЕСКИХ ПОРОШКОВ
Лекция 21 Обработка спеченных порошковых изделий
План лекции
1. Методы термической обработки порошковых изделий.
2. Химико-термическая обработка порошковых изделий.
Методытермическойобработкипорошковыхизделий
Требования, предъявляемые к механическим и физико-химическим свойствам порошковых изделий, непрерывно возрастают. Повысить соответствующие свойства порошковых материалов можно изменением их структуры, различными видами термической, химико-термической, термомеханической и дисперсионно-упрочняющей обработки, защитой от коррозии и механической обработкой для придания изделиям требуемых размеров и формы.
Под термической обработкой (ТО) понимается совокупность операций нагрева, выдержки при высоких температурах и охлаждения с различной скоростью с целью изменения структуры и обрабатываемости материала, улучшения комбинации его механических и физических свойств.
Практика показывает, что такому воздействию должны подвергаться многие порошковые изделия различного назначения, в первую очередь конструкционные на железной основе. Cущественное отличие структуры порошкового материала от структуры материала, полученного по традиционным технологиям (прежде всего – наличие пористости), не позволяет автоматически переносить закономерности тепловых процессов в компактном материале на порошковый.
Обладая большей суммарной поверхностью, пористые изделия при нагревании более склонны к обезуглероживанию, окислению и т.д., поэтому при их обработке необходимо применять либо более быстрый нагрев, при котором за счет меньшего времени теплового воздействия химическое взаимодействие затрагивает меньшие объемы, либо осуществлять нагрев в защитных (нейтральных, восстановительных) атмосферах или в углеродсодержащих засыпках. Наличие в порошковых материалах пор, заполненных газом, существенно снижает тепло- и температуропроводность изделий. В связи с этим при прочих равных условиях их скорости нагрева и охлаждения, а также другие характеристики процессов ТО будут отличаться от аналогичных показателей для беспористых изделий.
Поры, являясь концентраторами напряжений, при резком охлаждении вызывают появление значительных неравномерно распределенных термических и фазовых напряжений, приводящих к изменению структуры материала,
атакже к появлению трещин.
Входе многочисленных исследований обнаружено, что повышенная дефектность порошковых изделий, неоднородность распределения легирующих элементов по объему заготовки, большая суммарная поверхность существенно изменяют термодинамическое состояние материала, увеличивая запас свободной энергии и снижая работу образования зародышей новой фазы.
Процессы порошковой металлургии. Курс лекций |
-369- |

II. ФОРМОВАНИЕ И СПЕКАНИЕ ИЗДЕЛИЙ ИЗ МЕТАЛЛИЧЕСКИХ И НЕМЕТАЛЛИЧЕСКИХ ПОРОШКОВ
Лекция 21 Обработка спеченных порошковых изделий
Исследования структуры порошковых материалов, прошедших ТО, показали, что основные закономерности этого процесса в порошковых композициях аналогичны закономерностям в кованых и литых материалах, однако особенности первых оказывают влияние как на кинетику процесса, так и на температуру, инкубационный период и общее время превращения. С увеличением пористости время, необходимое на проведение операций ТО, уменьшается. Дисперсность исходных порошков оказывает такое же влияние, но в меньшей степени, чем пористость.
Термическая обработка порошковых материалов делится на предварительную (различные виды отжига и нормализация) и окончательную (закалка с отпуском). В некоторых случаях отжиг и нормализация могут быть окончательной ТО.
Предварительная обработка проводится как на порошках, так и на сформованных, спеченных и откалиброванных заготовках с целью улучшения их структуры, технологических и механических свойств (снижения твердости, улучшения обрабатываемости резанием, уменьшения и полного снятия остаточных напряжений). Окончательной обработке обычно подвергают готовые изделия с целью улучшения или формирования заданной структуры и придания необходимых свойств.
Для порошковых материалов с гетерогенной или неоднородной структурой важное значение имеет диффузионный отжиг, так как он позволяет обеспечить одинаковые свойства по всему сечению изделия.
Закалка порошковых изделий позволяет не только повысить механические свойства, но и улучшить физико-химические свойства: магнитные, антикоррозионные и т.д.
Порошковые материалы на основе цветных металлов также могут подвергаться отжигу, закалке и отпуску.
Латуни (в том числе и порошковые) склонны к коррозии под действием остаточных напряжений, поэтому не рекомендуется использовать неотожженные детали, полученные холодной деформацией спеченных заготовок, а также прошедшие обработку резанием (точением, фрезерованием, шлифованием, сверлением, нарезкой отверстий). Низкотемпературный отжиг латуней проводится в интервале 400–500 °С, при этом размер деталей практически не изменяется и сохраняется высокая чистота поверхности. Перед механической обработкой с большой степенью деформации (например, при нанесении резьбы накаткой) проводится отжиг при 850 °С в течение одного часа.
Химико-термическаяобработкапорошковыхизделий
Химико-термическая обработка (ХТО) заключается в нагреве и выдержке металлов и сплавов при высокой температуре в активных газовых, жидких или твердых средах. Она обеспечивает изменение свойств поверхно-
Процессы порошковой металлургии. Курс лекций |
-370- |

II. ФОРМОВАНИЕ И СПЕКАНИЕ ИЗДЕЛИЙ ИЗ МЕТАЛЛИЧЕСКИХ И НЕМЕТАЛЛИЧЕСКИХ ПОРОШКОВ
Лекция 21 Обработка спеченных порошковых изделий
сти порошковых изделий, в том числе ее химического состава, при диффузионном насыщении частиц материала-основы каким-либо легирующим элементом.
При ХТО пористых изделий повышается их твердость, приобретаются специальные свойства, а также на их поверхности может происходить залечивание пор, играющее в ряде случаев большую роль для повышения всего комплекса свойств при сохранении массы и размеров изделий. В случае высокоплотных порошковых материалов можно совмещать ХТО со спеканием или нагревом перед каким-либо видом горячего формообразования.
После некоторых видов ХТО проводят термическую обработку, улучшающую свойства сердцевины и поверхности изделия. В некоторых случаях ХТО предшествует ТО.
Распространенными видами химико-термической обработки порошковых материалов являются цементация, азотирование и сульфидирование – насыщение изделий, соответственно, углеродом, азотом или серой. Кроме этого, в практике порошковой металлургии используют так называемую диффузионную металлизацию – введение в состав порошкового материала хрома, алюминия, титана и т.д. Нередко ведут насыщение сразу несколькими элементами – цианирование (С + N), карбохромирование (С + Сr), карбохромсилицирование (С + Сr + Si).
Химико-термическая обработка включает в себя следующие этапы: образование во внешней среде диффундирующего элемента в активном атомарном состоянии; контакт активных атомов с поверхностью насыщаемого материала, адсорбцию их и возникновение химической связи с атомами обрабатываемого материала; твердофазную диффузию от поверхности в объем изделия.
Особенности строения порошковых материалов способствуют интенсификации диффузии. В порошковых изделиях диффузия осуществляется от всей активной (суммарной) поверхности частиц, что существенно уменьшает расстояние, на которое должны переместиться атомы для достижения требуемого результата (рис. 2.59). Для технологии это означает сокращение времени всего процесса. При достаточно большой временной выдержке и открытой пористости ХТО, изначально предназначенная для поверхностной обработки, может привести к объемному насыщению изделия легирующими элементами.
Процессы порошковой металлургии. Курс лекций |
-371- |

II. ФОРМОВАНИЕ И СПЕКАНИЕ ИЗДЕЛИЙ ИЗ МЕТАЛЛИЧЕСКИХ И НЕМЕТАЛЛИЧЕСКИХ ПОРОШКОВ
Лекция 21 Обработка спеченных порошковых изделий
а |
б |
Рис. 2.59. Схема насыщения легирующим элементом частиц (зерен) беспористых (а) и пористых порошковых (б) материалов
Поскольку насыщение поверхностного слоя обрабатываемого материала легирующими элементами – процесс диффузионный, то его результаты будут зависеть от температуры, скорости, длительности нагрева, дисперсности исходного порошка (более дисперсные порошки создают в заготовке более мелкие поры, что обеспечивает повышение скорости диффузии, особенно в начальный период насыщения), природы легирующего элемента и др.
Глубина диффузионного слоя в порошковых материалах существенно зависит еще и от такой специфической величины, как кривизна насыщаемой поверхности. Наибольшая глубина насыщения наблюдается на выпуклых поверхностях, меньшая – на плоских и особенно на вогнутых.
Структура диффузионных слоев определяется диаграммой состояния основного металла (сплава) и насыщающего элемента в пределах от нуля до максимальной его концентрации. Если в двойной системе растворение диффундирующего элемента в металле-основе не вызывает в процессе насыщения фазовых превращений, то микроструктура слоя после охлаждения мало чем отличается от первоначальной (исходной). Глубину слоя в этом случае можно приблизительно установить по различному травлению частиц (зерен) или более сложными рентгеновскими и электронно-микроскопическими методами.
Состояние и физико-химическая природа насыщающих сред при ХТО оказывают большое влияние на результаты процесса. От их агрегатного состояния зависит глубина и строение слоев. Кроме этого, они не должны быть агрессивными к обрабатываемым материалам и ухудшать механические свойства изделий.
Вкачестве рабочих сред при химико-термической обработке применяют твердые, жидкие и газообразные вещества. Наиболее эффективными являются газовые среды, обеспечивающие максимально быстрый подвод насыщающего элемента к поверхности.
Вжидких средах насыщение происходит вследствие либо прямого контакта расплава с поверхностью обрабатываемого изделия, либо за счет газов или элементов в атомарном виде, выделяющихся в результате протекающих в расплаве реакции или электролиза.
Насыщение в твердых средах характеризуется весьма малой скоростью, так как активность твердых тел невелика, а основное взаимодействие развивается только в местах непосредственного контакта насыщающего элемента с обрабатываемой поверхностью. Часто для ускорения процесса к
твердым средам добавляют активаторы типа NH4C1, NH4Br, BaCO3 и др., с помощью которых формируется активная газовая фаза, принимающая участие в образовании соответствующего насыщенного слоя.
Процессы порошковой металлургии. Курс лекций |
-372- |

II. ФОРМОВАНИЕ И СПЕКАНИЕ ИЗДЕЛИЙ ИЗ МЕТАЛЛИЧЕСКИХ И НЕМЕТАЛЛИЧЕСКИХ ПОРОШКОВ
Лекция 21 Обработка спеченных порошковых изделий
При диффузионном насыщении в формирующемся слое может образоваться пористость, а обрабатываемое изделие, соответственно, может увеличить свои линейные размеры, что часто вызывает коробление. Поэтому необходимо строго контролировать процесс насыщения, обеспечивая его равномерность по всей обрабатываемой поверхности.
Для предотвращения коррозии после ХТО изделия тщательно промывают, а в некоторых случаях подвергают отжигу в защитной атмосфере до полного удаления из пор всех остатков насыщающей среды.
Насыщение поверхностных слоев изделия углеродом (цементацию) проводят в углеродсодержащих средах (карбюризаторах), которые могут быть твердыми (древесный уголь), газовыми (природный, светильный и конвертированный газы, эндо- и экзогазы и др.) и жидкими (соляные ванны типа ВаСО3 + NaCl с добавкой 10–15 % карбида кремния, карбида кальция, кокса и других науглероживающих веществ). Наиболее прогрессивной является газовая цементация. Оптимальное сочетание механических свойств (высокой прочности и твердости на поверхности при относительно высокой ударной вязкости сердцевины) в цементованных изделиях обеспечивается последующей термической обработкой – закалкой и отпуском.
Часто на практике требуется подвергнуть цементации не всю поверхность детали, а ее часть. В этом случае ненауглероживаемую поверхность гальванически покрывают медью или обмазывают смесью огнеупорной глины, асбеста и жидкого стекла.
Насыщение поверхностных слоев изделия азотом (азотирование) с целью получения высокой поверхностной твердости, износостойкости, коррозионной стойкости и усталостной прочности. Его проводят при относительно низких температурах в течение длительного времени (десятки часов), что вызвано достаточно малой скоростью диффузии в металлах. Этот вид ХТО, которому подвергают порошковые изделия, прошедшие окончательную термическую обработку, проводят в диссоциированном аммиаке со степенью диссоциации от 30 до 60 %.
Нитроцементацию – насыщение поверхностных слоев материала (изделия) одновременно азотом и углеродом – проводят при использовании смесей науглероживающих и азотирующих газов (например, смеси диссоциированного аммиака с 20–30 % природного газа). После проведенной нитроцементации поверхностные слои изделия (материала) приобретают повышенную твердость и износостойкость (большую, чем у цементованных изделий) за счет образования карбонитридов.
Насыщение поверхностных слоев изделия серой (сульфидирование) проводят с целью улучшения прирабатываемости, уменьшения коэффициента трения и повышения сопротивляемости износу. В настоящее время распространены три способа проведения этой обработки:
Процессы порошковой металлургии. Курс лекций |
-373- |

II. ФОРМОВАНИЕ И СПЕКАНИЕ ИЗДЕЛИЙ ИЗ МЕТАЛЛИЧЕСКИХ И НЕМЕТАЛЛИЧЕСКИХ ПОРОШКОВ
Лекция 21 Обработка спеченных порошковых изделий
1.Погружение изделия в расплавленную серу (температура 130–160 °С) на 10–20 мин с последующим диффузионным отжигом при 400–750 °С в защитной среде.
2.Газовое сульфидирование в токе сероводорода.
3.Насыщение серой в твердых засыпках или в газовых смесях, полученных крекингом сернистых соединений и аммиака (совмещение сульфидирования с нитроцементацией или азотированием).
Образующиеся в процессе обработки сульфиды располагаются в виде мелкодисперсных включений в порах и на поверхности изделия.
Насыщение поверхностных слоев изделия хромом (хромирование), алюминием (алитирование), ванадием (ванадирование), цинком (цинкование)
идругими элементами носит название диффузионной металлизации. Поверхностное легирование обеспечивает экономию легирующих
элементов, не снижая эксплуатационных характеристик изделий, работающих в условиях активной коррозии, трения и износа. Наибольшее распространение имеет хромирование, которое повышает механические свойства изделий, их износо-, жаро- и коррозионную стойкость, увеличивает поверхностную твердость и образует декоративное покрытие.
Хромирование порошковых материалов (изделий) можно проводить в твердом металлизаторе на основе хрома или феррохрома или в газовых средах. Во втором случае сначала образуются летучие галогениды хрома (например, при взаимодействии хрома с хлористым водородом, получающимся в результате разложения NH4C1), а затем протекают обменные реакции между галогенидами и основным металлом конкретного материала.
Количество хрома, продиффундировавшего в пористый образец, и глубина хромированного слоя обратно пропорциональны относительной плотности порошкового материала.
Хромирование можно совмещать с процессом спекания заготовок или проводить на готовых изделиях после спекания или горячего прессования. Перспективно совмещение хромирования с цементацией и азотированием (карбохромазотирование), позволяющее повысить износостойкость и эрозионную стойкость порошковых изделий.
Для повышения износо-, окалино- и коррозионной стойкости порошковых материалов применяют и другие виды ХТО – борирование, фосфатирование, силицирование и пр.
Контрольныевопросыизадания
1.Перечислите виды обработки порошковых изделий.
2.Назовите виды химико-термической обработки спеченных изделий.
3.В чем состоит особенность ХТО порошковых изделий, по сравнению с компактными (литыми) материалами?
Процессы порошковой металлургии. Курс лекций |
-374- |

II. ФОРМОВАНИЕ И СПЕКАНИЕ ИЗДЕЛИЙ ИЗ МЕТАЛЛИЧЕСКИХ И НЕМЕТАЛЛИЧЕСКИХ ПОРОШКОВ
Лекция 21 Обработка спеченных порошковых изделий
4.Перечислите факторы, которые определяют величину насыщенного слоя пористого порошкового тела.
5.Как называются среды, в которых проводят насыщение поверхностных слоев порошкового изделия углеродом?
Лекция22 Обработкапорошковыхизделий
План лекции
1.Термомеханическая обработка порошковых изделий.
2.Дисперсионно-упрочняющая термическая обработка.
3.Противокоррозионная обработка изделий из порошков.
4.Механическая обработка.
Термомеханическаяобработка
Термомеханическая обработка (ТМО) – эффективный способ повышения комплекса механических свойств порошковых материалов различного назначения, заключающийся в сочетании термической обработки с пластической деформацией. Применяемые схемы ТМО представляют собой варианты трех основных процессов: высокотемпературной (ВТМО), низкотемпературной (НТМО) и предварительной (ПТМО) термомеханической обработки. Любой вид ТМО участвует в формировании структуры при формообразовании порошковых изделий.
При ВТМО деформацию материала с большой степенью обжатия (до 80–90 %) осуществляют прокаткой, экструзией, штамповкой и т.д., совмещая ее с уплотнением порошкового материала или обработкой малопористых материалов. При изготовлении материалов по технологии двойного прессования-спекания второе спекание после допрессовки можно заменить нагревом под горячую деформацию. Проведение горячей штамповки в рамках ВТМО позволяет получить упрочнение изделий, не требующее, как правило, дополнительной механической обработки. Упрочнение, достигаемое при ВТМО, зависит от способа, степени и температуры деформации, длительности последеформационной выдержки, закалочной среды, состава обрабатываемого материала и других факторов. В случае пористых заготовок существенное влияние оказывает размер частиц порошка. Частицы более мелкого порошка деформируются в большей доле объема, что приводит к образованию однородной и мелкозернистой структуры. После ВТМО структура материала более устойчива, а прочность выше, чем непосредственно после закалки.
Процессы порошковой металлургии. Курс лекций |
-375- |
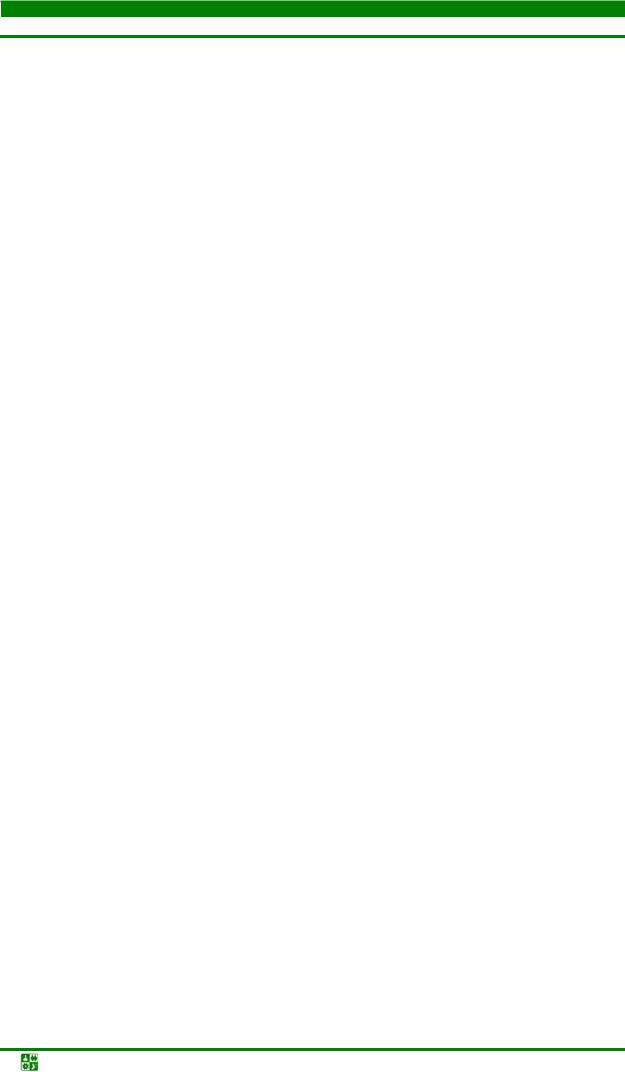
II. ФОРМОВАНИЕ И СПЕКАНИЕ ИЗДЕЛИЙ ИЗ МЕТАЛЛИЧЕСКИХ И НЕМЕТАЛЛИЧЕСКИХ ПОРОШКОВ
Лекция 22 Обработка порошковых изделий
НТМО в основном применяют только для обработки легированных сталей с большой устойчивостью переохлажденного аустенита. Сталь нагревают, затем подстуживают до температуры максимальной устойчивости переохлажденного аустенита и в этом состоянии, при температуре ниже порога рекристаллизации, деформируют с обжатием 30–40 %, после чего немедленно закаливают.
При ПТМО деформация и нагрев под закалку разделены во времени: материал вначале подвергают механической деформации в холодном состоянии, а затем закалке и отпуску. Иногда ПТМО предшествует ВТМО. Холодная пластическая обработка приводит к уплотнению пористой заготовки: при обжатии до 30 % пористость порошковых материалов уменьшается до 4–2 %, а после деформации на 50 % изделия получаются практически беспористыми. ПТМО обеспечивает повышение прочности при некотором снижении пластичности, она наиболее технологична и не требует специального оборудования.
Дисперсионно-упрочняющаятермическаяобработка
Дисперсионно-упрочняющая термическая обработка (ДУТО) возможна для материалов, компоненты которых при температуре спекания имеют ограниченную взаимную растворимость, уменьшающуюся при снижении температуры в процессе охлаждения после изотермической выдержки. ДУТО складывается из двух этапов:
закалка с температур выше линии предельной растворимости компонентов на диаграмме состояния (быстрое охлаждение при закалке в этом случае фиксирует при комнатной температуре пересыщенный неустойчивый твердый раствор);
старение сплавов, при котором происходит распад пересыщенного твердого раствора, полученного в результате закалки, и выделение избыточной фазы в виде очень мелкодисперсных частиц химического соединения или твердого раствора.
Старение сплава приводит к повышению его прочности и твердости, а также снижению пластичности. Максимальное значение твердости и прочности может быть получено только при относительно низкой температуре старения, которая для каждого сплава своя. Повышение температуры старения приводит к коагуляции выделяющихся частиц и падению прочностных свойств до значений, более низких, чем полученные при закалке.
Наличие пористости в порошковых материалах (изделиях) влияет на процесс твердения, который замедляется при ее возрастании. Повторное прессование и спекание заготовок ускоряет процесс твердения в начальный период, но снижает его конечные результаты.
Процессы порошковой металлургии. Курс лекций |
-376- |

II. ФОРМОВАНИЕ И СПЕКАНИЕ ИЗДЕЛИЙ ИЗ МЕТАЛЛИЧЕСКИХ И НЕМЕТАЛЛИЧЕСКИХ ПОРОШКОВ
Лекция 22 Обработка порошковых изделий
Защитапорошковыхизделийоткоррозии
Коррозионная стойкость порошкового материала является одной из важнейших характеристик, зачастую определяющей саму возможность применения деталей из него в соответствующих конструкциях. Исследования показали, что в основном поведение порошковых материалов подчиняется общим закономерностям окисления и электрохимической коррозии, однако особое состояние пористых тел обусловливает некоторые специфические особенности. Наличие пор и поровых каналов приводит к увеличению активной поверхности материала, что вызывает развитие коррозионных процессов одновременно на внешней и внутренней (в объеме порошкового тела) поверхностях.
С целью защиты поверхности порошковых изделий от коррозии на нее наносят различные химические или электролитические покрытия: химическое никелирование, фосфатирование, электрохимическое никелирование, меднение, цинкование, кадмирование, хромирование и др.
Для предотвращения внутренней коррозии из-за попадания в поровые каналы химических растворов, используемых при создании защитного покрытия, пористые порошковые изделия (пористостью > 5–6 %) предварительно пропитывают разными веществами (смолами, битумными лаками, различными химически стойкими веществами). Они образуют на поверхности пор плотные пленки, которые препятствуют действию химически активных растворов (электролитов), обладают достаточной электропроводностью и легко удаляются с поверхности изделия. Одним из лучших материалов для заполнения пор порошкового тела перед покрытием его поверхности защитным слоем является гидрофобная кремнийорганическая жидкость (ГКЖ-94), растворяющаяся в бензине или четыреххлористом углероде. В процессе взаимодействия этой жидкости с поверхностью обрабатываемого материала образуется тонкая полимерная пленка, которая не смывается водой.
Представляют интерес и защитные паротермические пленки, хотя в этом случае надо учитывать сложность получения хорошего сцепления слоя осаждаемого металла с окисленной поверхностью обрабатываемого порошкового материала.
В последние годы для закрытия поверхностных пор расширяется применение так называемых анаэробных (т.е. способных полимеризоваться в отсутствии кислорода воздуха) герметиков. Такие анаэробные материалы используют без отвердителей и растворителей. Они обладают хорошей проникающей и всасывающей способностью. В их состав входят полимеризацион- но-активное соединение-ингибитор (основа композиции), инициатор и модифицирующие добавки. При попадании в поровые каналы при отсутствии воздуха происходит полимеризация смолы, ее затвердевание и сцепление с металлической поверхностью. В России выпускается пропитывающая композиция ПК-80, представляющая собой однокомпонентную низковязкую жидкость на основе акрилового мономера. Ее применяют для закрытия пор и защиты от коррозии порошковых изделий; она позволяет заполнять поры размером до
Процессы порошковой металлургии. Курс лекций |
-377- |

II. ФОРМОВАНИЕ И СПЕКАНИЕ ИЗДЕЛИЙ ИЗ МЕТАЛЛИЧЕСКИХ И НЕМЕТАЛЛИЧЕСКИХ ПОРОШКОВ
Лекция 22 Обработка порошковых изделий
0,3 мм за один цикл и до 0,5 мм за два цикла. Пропитку ведут в вакууме, затем изделия промывают в холодной воде для удаления избытка герметика с их поверхности и проводят отверждение герметика в воде при 92±2 °С (анаэробная жидкость полимеризуется в порах изделия). Анаэробные герметики в полимеризованном состоянии характеризуются высокой химической стойкостью к агрессивным средам. Заполнение ими пор существенно улучшает некоторые механические свойства порошковых изделий и повышает чистоту обработки их поверхности.
Механическаяобработка
Одно из важных преимуществ порошковой металлургии – получение изделий, не требующих дополнительной механической обработки. Однако в ряде случаев целесообразно изготовлять из порошка заготовки сравнительно простой формы, получение которых не требует применения сложной и дорогой оснастки для формования, а последующее усложнение их формы и повышение точности размеров обеспечивать после спекания калиброванием и обработкой резанием.
Калибрование. Этот вид обработки представляет собой своеобразное допрессовывание спеченных заготовок. При его проведении происходит пластическая деформация поверхностных слоев обрабатываемой заготовки, которая приобретает требуемые размеры с точностью не менее 6–7-го квалитетов и 7-го класса шероховатости.
Припуск на калибрование не может быть большим (обычно 0,5–2,0 % от калибруемого размера), причем наружные и внутренние поверхности деталей следует калибровать с разными припусками: наружные – по возможности с большими, а внутренние – с меньшими.
Калибрование проводят как в пресс-формах, в которых осуществляли прессование, так и в специальных калибровочных пресс-формах, что предпочтительнее.
Резание. Одним из условий применения обработки порошковых заготовок резанием является требование обеспечения точности размеров изделий и шероховатости поверхности (< 40 мкм). Обработку резанием используют для изготовления деталей нецилиндрической или какой-либо усложненной геометрической формы с выточками, каналами, отверстиями (в том числе располагающимися перпендикулярно или под углом к оси прессования), резьбой и т.д. Обработку проводят на токарных, фрезерных, сверлильных и других металлообрабатывающих станках. Любой вид механической обработки порошковых материалов приводит к их упругой и пластической деформации, сопровождается трением и тепловыми явлениями, уплотнением или разрыхлением поверхностного слоя.
Точность и чистота механической обработки порошкового материала зависят от его пористости, химического состава, прочности, твердости и структуры. Из-за низкой пластичности порошковых материалов стружка, об-
Процессы порошковой металлургии. Курс лекций |
-378- |

II. ФОРМОВАНИЕ И СПЕКАНИЕ ИЗДЕЛИЙ ИЗ МЕТАЛЛИЧЕСКИХ И НЕМЕТАЛЛИЧЕСКИХ ПОРОШКОВ
Лекция 22 Обработка порошковых изделий
разующаяся в результате резания, при отрыве от основной массы обрабатываемой заготовки дробится на небольшие кусочки, похожие на стружку надлома. Наличие в порошковом материале пор сильно затрудняет его обработку резанием, снижает стойкость инструмента, хотя в этом случае усилия резания всегда меньше, чем при обработке литых металлов и сплавов. Затрудненная обработка порошковых материалов связана с нестабильностью резания из-за наличия пор, нарушающих сплошность материала, пониженной теплопроводности (в зоне резания возрастает температура) и повышенной склонности пористых тел к окислению. Поэтому опыт обработки компактных (литых) металлов и сплавов нельзя автоматически переносить на обработку пористых порошковых материалов (при исходной пористости порядка нескольких процентов это возможно).
Обработку резанием порошковых материалов обычно проводят твердосплавным инструментом, так как алмазная обработка существенно удорожает получаемые изделия, а инструмент из быстрорежущей стали во многих случаях имеет низкую стойкость.
При обработке пористых порошковых материалов нельзя применять обычные охлаждающие и смазочно-охлаждающие жидкости (СОЖ) на водной основе, а также жидкости, содержащие щелочь или кислоты, так как их попадание в поры изделий вызывает коррозию как при хранении, так и при последующей эксплуатации. Для охлаждения порошковых изделий при их обработке резанием применяют масла, эмульсии или инертные газы.
Пропитка порошковых изделий маслом при последующей обработке резанием снижает шероховатость их поверхности, в 1,3–1,5 раза уменьшает усилие резания и позволяет в 2,5–4,0 раза повысить уровень допустимых скоростей резания.
С повышением пористости порошковых изделий от 15 до 30 % повышается шероховатость их поверхности, но одновременно снижается усилие резания в 1,6–1,7 раза.
При обработке резанием структура и свойства поверхностных слоев порошковой детали изменяются. Правильно выбранный режим резания позволяет обеспечить на поверхности обрабатываемого изделия требуемые пористость, степень наклепа и уровень остаточных напряжений, а также исключить появление микротрещин и прожогов, предотвратить отслаивание материала. В общем случае стремятся уменьшить глубину захвата металла режущим инструментом. Это предотвращает значительную деформацию материала на поверхности изделий (прежде всего уменьшает «забиваемость пор»), что позволяет сохранить исходную структуру материала.
Точение. Выбор инструментального материала для точения порошковых изделий определяется экономической эффективностью, стойкостью и производительностью: пористые материалы на основе железа или меди (бронзы) целесообразно обрабатывать твердыми сплавами группы ВК. Для материалов с повышенной пористостью можно использовать минералокера-
Процессы порошковой металлургии. Курс лекций |
-379- |

II. ФОРМОВАНИЕ И СПЕКАНИЕ ИЗДЕЛИЙ ИЗ МЕТАЛЛИЧЕСКИХ И НЕМЕТАЛЛИЧЕСКИХ ПОРОШКОВ
Лекция 22 Обработка порошковых изделий
мику, а в случае материалов высокой твердости рекомендуется применять сверхтвердые инструментальные материалы.
Скорость резания зависит от состава порошкового материала и типа инструментального материала – для резцов из твердого сплава она составляет 50–200 м/мин. Низкие скорости резания (до 60 м/мин) не рекомендуются для обработки пористых изделий на основе железа из-за большой шероховатости получаемой поверхности. При скорости резания > 80 м/мин шероховатость поверхности сильно снижается, отсутствует наростообразование. Стойкость резцов тем выше, чем ниже скорость резания.
Для получения поверхностей с малой высотой микронеровностей порошковые детали обрабатывают с подачей < 0,1–0,12 мм/об. (чем больше пористость, тем меньше подача; например, при пористости > 25 % рекомендуется подача 0,035 мм/об, а при пористости < 24 % – 0,07 мм/об.). Оптимальная глубина резания составляет при обработке порошковых деталей 0,2–
0,3 мм.
Сверление и развертывание отверстий. Для этих видов резания по-
рошковых деталей применяют сверла и развертки из быстрорежущей стали или оснащенные пластинками из твердых сплавов группы ВК. В качестве критерия износа принят износ по задней поверхности режущего инструмента в 0,3 мм (сверла) и 0,2–0,3 мм (развертки).
При сверлении порошковых железографитовых материалов пористостью > 10 % целесообразно применять быстрорез, а с пористостью < 5 % – твердый сплав. Геометрические параметры сверл и структура обрабатываемых порошковых материалов оказывают на стойкость сверл более резкое воздействие, чем на стойкость резцов. Необходимо помнить об уплотнении поверхностного слоя порошковой детали при сверлении.
Развертывание отверстий в порошковых деталях после их сверления применяют с целью исправления формы, получения высоких чистоты поверхности и точности размеров. Развертки из быстрорежущей стали имеют недостаточную стойкость, особенно при скоростях > 30–40 м/мин, поэтому более предпочтительны твердосплавные развертки. При развертывании отверстий необходимо применять специально-охлаждающие жидкости (СОЖ).
Шлифование. При этом виде механической обработки поверхностный слой порошковой детали уплотняется, что существенно изменяет его свойства, особенно повышая износостойкость. На уплотнение поверхностного слоя значительно влияет пористость: чем она выше, тем больше уплотнение.
Изменяя режим шлифования, можно регулировать свойства поверхностного слоя порошковых деталей. Так, увеличение глубины шлифования с 0,01 до 0,1 мм приводит к росту микронапряжений на 15–30 %. Одновременное увеличение подачи и уменьшение скорости стола станка при плоском шлифовании кругами из карбида кремния или электрокорунда приводит к снижению микротвердости в тонких поверхностных слоях порошковых изделий.
Процессы порошковой металлургии. Курс лекций |
-380- |

II. ФОРМОВАНИЕ И СПЕКАНИЕ ИЗДЕЛИЙ ИЗ МЕТАЛЛИЧЕСКИХ И НЕМЕТАЛЛИЧЕСКИХ ПОРОШКОВ
Лекция 22 Обработка порошковых изделий
Высокую степень уплотнения шлифуемой поверхности при использовании корундовых кругов дает следующий режим: поперечная подача 0,3–0,6 мм/ход, скорость хода стола 13–15 м/мин, глубина шлифования 0,05–0,1 мм. Если уплотнение поверхности порошковой детали нежелательно или не требуется, то поперечная подача должна составлять 1,7–3 мм/ход, скорость хода стола – 6–12 м/мин, а глубина шлифования – 0,01–0,03 мм.
Контрольныевопросыизадания
1.Перечислите виды термомеханической обработки.
2.Укажите, для каких металлов, сплавов или материалов может применяться тот или иной вид ТМО.
3.Какие процессы лежат в основе ТМО порошковых изделий?
4.Назовите этапы дисперсно-упрочняющей обработки порошковых тел.
5.Перечислите виды механической обработки порошковых тел.
6.Какие охлаждающие жидкости используют при механической обработке спеченных порошковых изделий?
7.Как изменяется усилие резания при повышении пористости спеченных изделий?
8.Назовите режимы шлифования порошковых изделий.
Лекция23 Структураисвойствапорошковыхизделий
План лекции
1.Особенности строения порошковых тел.
2.Взаимосвязь параметров и свойств материалов.
3.Особенности структуры порошковых изделий.
Особенностистроенияпорошковыхтел
Одна из главных задач массового производства в порошковой металлургии – получение изделий в условиях постоянной и строгой воспроизводимости их свойств. Решение этой задачи охватывает совокупность процессов, предшествующих консолидации (производство исходных металлических порошков, их смешивание и др.) и приводящих к ней (формование, спекание, дополнительная термическая обработка и др.). М.Ю. Бальшин обратил внимание на то, что при консолидации сосуществуют процессы неавтономной (увеличивающей и фиксирующей контакты) нагружающей деформации и ав-
Процессы порошковой металлургии. Курс лекций |
-381- |

II. ФОРМОВАНИЕ И СПЕКАНИЕ ИЗДЕЛИЙ ИЗ МЕТАЛЛИЧЕСКИХ И НЕМЕТАЛЛИЧЕСКИХ ПОРОШКОВ
Лекция 23 Структура и свойства порошковых изделий
тономной (уменьшающей и нарушающей контакты) разгружающей деформации. Поэтому очень многие свойства порошкового тела зависят не только от его относительной плотности, но и от безразмерного контактного (критического) сечения αк, характеризующего долю объема пористого тела, в которой концентрируются направленные напряжения или процессы.
Это происходит потому, что пористое тело в самом общем виде является двухфазной объемной конструкцией, состоящей из твердой фазы и пустоты (точнее, из пор).
Для пористого тела характерны следующие особенности:
1) передача энергии и напряжений через пористое тело практически полностью концентрируется в твердой фазе, причем только в активной части его объема, характеризуемой αк;
2)такие свойства фазы «пустоты», заполняющей поры, как прочность, электропроводность, звукопроводность и т.п., по сравнению со свойствами твердой фазы, исчезающе малы и ими можно пренебречь;
3)если твердая фаза сама состоит из нескольких разнородных компонентов, априорная (т.е. до проведения эксперимента) оценка свойств порошкового тела значительно усложняется, так как возможна преимущественная концентрация энергии и напряжений в одном из компонентов (более того, главным образом в его активной части).
Взаимосвязьпараметровисвойствматериалов
Наиболее характерной отличительной чертой порошковых материалов (изделий) является наличие остаточной пористости, что часто решающим образом влияет на весь комплекс их свойств, существенно ограничивая области применения. Форма пор может быть различной и зависит от размера и формы частиц исходных порошков, режима изготовления и термической обработки порошкового изделия. Наиболее правильную форму пор и равномерное их распределение имеют изделия, изготовленные из порошков со сферической формой частиц.
Мелкие, замкнутые, округлой формы поры понижают механические свойства порошковых изделий в меньшей степени, чем соединяющиеся между собой щелевидные поры, которые выполняют роль внутренних надрезов (трещин). На размер пор и их форму большое влияние оказывают атмосфера и скорость нагрева при спекании.
В общем виде зависимость относительного свойства порошкового телаχ от относительной плотности ρотн приведена на рис. 2.60 (схема БальшинаХюттига) и выражается как χ ~ ρmотн, где т принимает значения от 0 до 10.
Процессы порошковой металлургии. Курс лекций |
-382- |

II. ФОРМОВАНИЕ И СПЕКАНИЕ ИЗДЕЛИЙ ИЗ МЕТАЛЛИЧЕСКИХ И НЕМЕТАЛЛИЧЕСКИХ ПОРОШКОВ
Лекция 23 Структура и свойства порошковых изделий
Рис. 2.60. Зависимость относительного свойства χ порошкового тела от ρотн: 1 – свойства, не зависящие от пористости; 2 – аддитивные характеристики; 3 – свойства типа проводимости; 4 – структурночувствительные характеристики
χ |
|
1 |
|
|
|
|
|
|
|
0,5 |
2 |
|
|
|
|
|
|
|
|
|
|
3 |
|
4 |
|
|
|
|
|
|
0,25 |
0,50 |
0,75 |
ρотн |
Обычно выделяют четыре группы свойств:
1)не зависящие от пористости (т = 0) – микротвердость, температура плавления и коэффициент термического расширения материала частиц;
2)аддитивные характеристики (т = 1), зависящие только от количества материала – теплоемкость, магнитная восприимчивость;
3)свойства типа проводимости (т = 1,5–2,0) – электро- и теплопроводность, модуль упругости, диэлектрическая и начальная магнитная проницаемость;
4)структурно-чувствительные свойства (т = 3–10) – прочность, пластичность, максимальная магнитная проницаемость, ударная вязкость и др.
Безразмерные свойства пористого тела С/Ск (где С – свойство пористого тела, отнесенное к его номинальным параметрам, например к номиналь-
ному сечению или длине, Ск – свойство компактного тела) являются масштабом М искажения данного свойства в пористом теле (С/Ск = М, С = МС к). Зная (определив) масштаб какого-либо из свойств пористого образца, можно рассчитать для него и другие характеристики (например, модули упругости, сдвига, всестороннего сжатия, коэффициент Пуассона, скорость звука, электропроводность и др.), величины, которых зависят не от пористости, а только от значений соответствующих свойств материала частиц.
В общем виде между различными параметрами и свойствами одного и того же образца существует количественная взаимосвязь:
αк /ρотн = (l / lк)-2, αк = E / Eк,
где l – истинный путь процесса в пористом теле; lк – условный (номинальный) путь процесса в пористом теле; Е, Ек – модуль упругости пористого и беспористого тела соответственно.
Оценка свойств порошковых материалов или изделий показывает, что их величина при заданной плотности определяется не только статистическими, но и физико-технологическими факторами.
Процессы порошковой металлургии. Курс лекций |
-383- |

II. ФОРМОВАНИЕ И СПЕКАНИЕ ИЗДЕЛИЙ ИЗ МЕТАЛЛИЧЕСКИХ И НЕМЕТАЛЛИЧЕСКИХ ПОРОШКОВ
Лекция 23 Структура и свойства порошковых изделий
Особенностиструктурыпорошковыхизделий
На свойства порошковых материалов (изделий), решающим образом определяющие область их применения, существенное влияние оказывают макро- и микроструктура, формирование которых происходит при отсутствии расплавления основы либо только в твердой фазе, либо при наличии ограниченного объема жидкой фазы. Поэтому для таких материалов структурообразование зависит от условий получения и свойств металлических порошков, состава порошковой шихты, метода формования, температуры, скорости нагрева и времени спекания, скорости охлаждения после спекания, состава защитной среды, последующей термической обработки и многих других факторов.
Для свойств кристаллизующихся из жидкого состояния литых металлов и сплавов наиболее важны химический состав, дисперсность, распределение и количественное соотношение фаз, размеры и форма зерен. Эти факторы в определенной мере сказываются на свойствах и порошковых материалов, но наряду с ними большое влияние на уровень механических и физико - химических свойств изделий из металлических порошков оказывают форма частиц, величина межчастичных контактов и пористость, являющаяся самостоятельным структурным фактором.
Структурными составляющими порошковых материалов являются металлическая фаза (фазы), неметаллические включения (графит, оксиды и т.п.) и поры. Влияние свойств исходных порошков на структуру неоднозначно и проявляется в различной мере при осуществлении разнообразных вариантов технологических процессов получения материалов (изделий) из них. Так, форма частиц и рельеф (шероховатость) их поверхности определяют не только качество самих формовок, но и особенности формирования структуры материала на межчастичных контактных поверхностях на всех этапах получения порошковых изделий.
Увеличение размеров частиц приводит к формированию крупнозернистой структуры с большими порами неправильной формы, а увеличение дисперсности порошков, активируя процессы массопереноса при спекании и обеспечивая получение более плотной (малопористой) структуры, может приводить к повышению содержания в материале неметаллических включений в связи с повышенной окисленностью исходного порошка.
Большое влияние на формирование структуры оказывают химический состав и внутризеренная структура самих частиц порошка, особенно в случае наличия в них трудновосстановимых оксидов А12О3, SiO2 и др. У материалов (изделий) из смесей, содержащих порошки отдельных компонентов, структура, как правило, гетерогенна из-за неполной гомогенизации при спекании и образования внутричастичных пор вследствие различия скоростей диффузионного обмена в частицах разных металлов (эффект Киркендала). Поэтому предварительно легированные порошки или порошки сплавов, предварительно полученные тем или иным способом, обеспечивают значительное повышение однородности структуры, уровня и стабильности свойств.
Процессы порошковой металлургии. Курс лекций |
-384- |

II. ФОРМОВАНИЕ И СПЕКАНИЕ ИЗДЕЛИЙ ИЗ МЕТАЛЛИЧЕСКИХ И НЕМЕТАЛЛИЧЕСКИХ ПОРОШКОВ
Лекция 23 Структура и свойства порошковых изделий
На конечную структуру порошковых материалов (изделий) существенно влияют условия формования, при котором порошки уплотняются, частицы деформируются, изменяется состояние поверхностей и площади межчастичных контактов, развиваются межчастичные связи. Холодное прессование и последующее длительное спекание приводят к образованию более равновесной, но и сравнительно крупнозернистой структуры, тогда как при статическом горячем прессовании формируется более мелкозернистая структура, а при динамическом горячем прессовании – еще более дисперсная.
В зависимости от состава материала и условий нагрева, микроструктура порошковых материалов может быть гомогенной или гетерогенной, а также может представлять собой механическую смесь металлических и неметаллических частиц. Для обеспечения полной гомогенизации структуры требуются более высокие температуры и достаточно длительные (многочасовые) выдержки при спекании. Например, гомогенная структура порошкового железоникельмедного материала достигается за 3 ч при 1 250 °С, а более низкие температуры или менее длительные выдержки при спекании приводят к гетерогенной структуре, состоящей из зерен твердых растворов различного химического состава, так как диффузионные процессы протекают не полностью. Большие затруднения в получении равновесных структур возникают при изготовлении материалов (изделий) из компонентов, имеющих ограниченную взаимную растворимость. Равновесность структуры таких материалов возрастает при увеличении длительности изотермической выдержки при спекании. При получении сплавов из порошков отдельных компонентов в них всегда наблюдается большая или меньшая гетерогенность.
Исследование структуры порошковых материалов (изделий) производят визуально (изучение макроструктуры по излому), а также с применением оптических и электронных микроскопов, часто оснащенных различными аналитическими приставками (изучение микроструктуры). При визуальном изучении излома можно определить наличие раковин, расслоений, оценить размеры пор и размер зерна; по виду излома можно достаточно квалифицированно судить о равномерности спекания и однородности строения изделия по сечению, о наличии оплавления, обезуглероживания и других видах брака.
Методы исследования микроструктуры – наиболее надежные методы оценки не только качественных, но и количественных изменений, происходящих со структурными составляющими порошкового материала. Плоскость шлифа должна быть параллельной направлению прессования и проходить вблизи оси порошкового изделия, а при его сложной форме необходимо изготовлять несколько шлифов.
Сочетание в порошковом материале твердых составляющих и пор требует особых мер при изготовлении шлифов и подготовке их поверхности. Чтобы избежать искажений микроструктуры (рис. 2.61), необходимо предотвратить деформацию и разрушение кромок пор, что требует применения особо твердых инструментов (в том числе и алмазосодержщих).
Процессы порошковой металлургии. Курс лекций |
-385- |

II. ФОРМОВАНИЕ И СПЕКАНИЕ ИЗДЕЛИЙ ИЗ МЕТАЛЛИЧЕСКИХ И НЕМЕТАЛЛИЧЕСКИХ ПОРОШКОВ
Лекция 23 Структура и свойства порошковых изделий
а |
б |
в |
г |
Рис. 2.61. Искажение формы и изменение действительных размеров пор в плоскости шлифа: а – пластическая деформация кромки поры при шлифовке; б – искажение (разрушение) контура поры; в – попадание продуктов шлифовки в пору и образование из нее нескольких мелких пор; г – увеличение контура поры с округлением ее краев: 1 – действительный размер; 2 – контур поры, видимый на шлифе
Разрушение кромок часто является следствием изменяющегося прижимного усилия, поэтому весьма желательно использовать автоматические шлифовальные устройства, поддерживающие равномерное давление. Во избежание скругления кромок пор следует применять не слишком мягкие полировальные материалы. Пригодна и вибрационная полировка, в ходе которой получают поверхности без разрушения кромок. В ряде случаев целесообразно использовать комбинацию механической и электролитической полировки.
Неизбежное попадание продуктов шлифовки и полировки в поры заставляет применять специальные методы очистки, например ультразвук.
Степень засорения шлифа существенно уменьшается при мокром шлифовании, но в этом случае жидкость, попавшая в поры, затрудняет последующую обработку и может вызвать крайне нежелательные коррозионные процессы.
Изменения формы и размеров пор, а также попадания коррозионных жидкостей в них при изготовлении шлифа в значительной степени можно избежать, если заполнять поры веществом, которое, с одной стороны, обладало бы невысокой вязкостью для легкого проникновения в тонкие и извилистые поровые каналы, а с другой стороны, – достаточной твердостью, позволяющей избежать замазывания поверхности шлифа.
Данным условиям удовлетворяют парафины, термопластичные полимеры, бакелит. Перед пропиткой пористых материалов эти вещества нагревают для снижения вязкости или вообще расплавляют. Очень удобными для фиксации формы и размеров пор при изготовлении шлифов спеченных и особенно спрессованных заготовок оказались двухкомпонентные клеи-компаунды. Добавление к основному компоненту клея растворителя (ацетона) перед введением отвердителя дополнительно снижает вязкость компаунда, что в сочетании с предварительной пропиткой образца тем же растворителем позволяет заполнять поры размером до 5 мкм. Следует отметить, что растворители увеличивают время полного отверждения клея с 3–5 ч до 2–3 сут; однако в ряде случаев это оправдано.
Процессы порошковой металлургии. Курс лекций |
-386- |
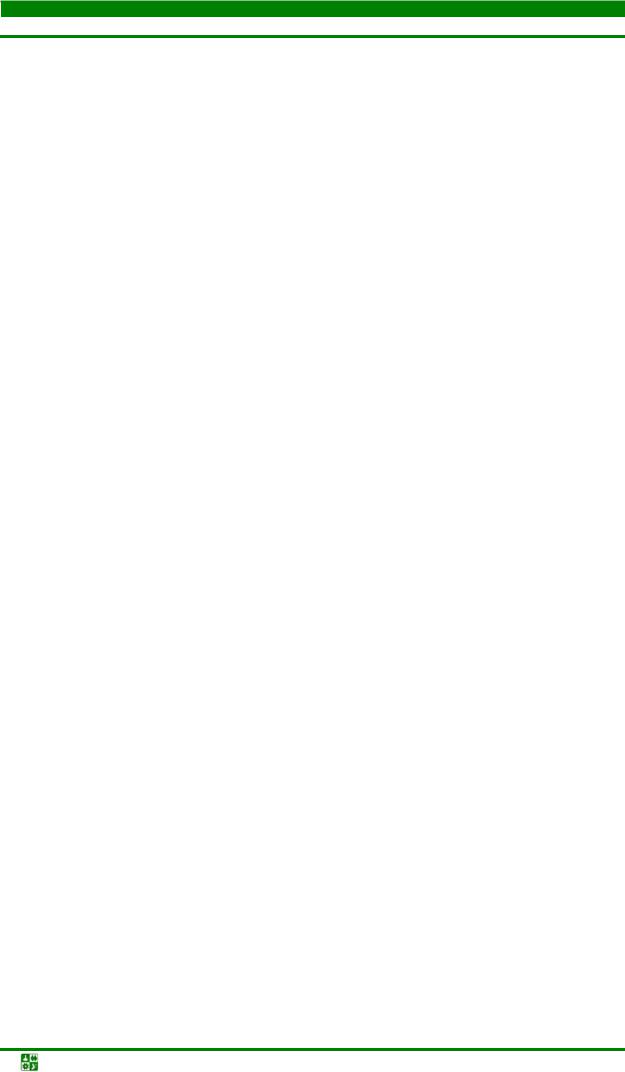
II. ФОРМОВАНИЕ И СПЕКАНИЕ ИЗДЕЛИЙ ИЗ МЕТАЛЛИЧЕСКИХ И НЕМЕТАЛЛИЧЕСКИХ ПОРОШКОВ
Лекция 23 Структура и свойства порошковых изделий
Металлографический анализ (с использованием методов оптической и электронной микроскопии) позволяет с большой объективностью оценить качество порошковых материалов (изделий), а также контролировать правильность проведения различных операций, предусмотренных технологией при их изготовлении.
Оценку размеров пор и изучение неметаллических структурных составляяющих лучше всего производить на нетравленых шлифах, а изучение металлических фаз и структурных составляющих – на травленых. Травление шлифов порошковых материалов для выявления микроструктуры производят обычно теми же реактивами, что и при исследовании микроструктуры литых материалов аналогичного состава.
В настоящее время для количественного анализа микроструктуры порошковых материалов применяют три способа – точечный, линейный и планиметрический. В первом случае выборку проводят с помощью системы точек, во втором – случайными прямыми, в третьем – случайными плоскостями.
Контрольныевопросыизадания
1.Перечислите специфические особенности порошкового тела.
2.Назовите четыре группы свойств порошковых тел. Приведите их характеристику.
3.Напишите уравнение, связывающее параметры и свойства одного и того же образца.
4.Перечислите структурные составляющие порошкового тела.
5.Назовите основные факторы, определяющие структуру порошко-
вого тела.
6.Какой из известных вам методов, позволяет провести оценку качественных и количественных изменений, происходящих со структурными составляющими порошкового материала?
7.Назовите методы, позволяющие сохранить исходную микроструктуру порошкового тела при подготовке микрошлифов?
8.Перечислите методы количественного анализа микроструктуры порошкового материала.
Лекция24 Свойствапорошковыхизделий
План лекции
1.Физические свойства порошковых изделий.
2.Механические свойства.
Процессы порошковой металлургии. Курс лекций |
-387- |

II. ФОРМОВАНИЕ И СПЕКАНИЕ ИЗДЕЛИЙ ИЗ МЕТАЛЛИЧЕСКИХ И НЕМЕТАЛЛИЧЕСКИХ ПОРОШКОВ
Лекция 24 Свойства порошковых изделий
Физическиесвойствапорошковыхизделий
Плотность и пористость изделий. Определение плотности и по-
ристости сформованных и спеченных изделий (кроме твердосплавных) регламентировано ГОСТ 18898-89 и предусматривает применение расчетного и гидростатического методов. Для твердых сплавов плотность определяют по ГОСТ 20018-74 гидростатическим методом, а пористость – по ГОСТ 9391-80 металлографически. Определяют эти характеристики при комнатной температуре, если не оговорены другие условия. Перед проведением испытаний изделие (заготовку, образец) необходимо очистить от загрязнений и осмотреть визуально для определения качества поверхности. Изделия, имеющие трещины, раковины, сколы и скрашивающиеся кромки, к испытаниям не допускаются. Испытания проводят не менее чем на трех образцах.
Расчетный метод. Этот метод, предусматривающий измерение объема и массы изделия, допускается применять только в том случае, если изделие имеет простую геометрическую форму. Линейные размеры, по которым рассчитывают объем, замеряют мерительным инструментом (микрометром, штангенциркулем и др.) с точностью до ± 0,001 мм. Массу изделия определяют взвешиванием на воздухе с погрешностью не более 0,01 %. Плотность изделий γ, г/см3, вычисляют делением массы изделия, г, на его объем, см3. Допустимое расхождение результатов анализа не должно превышать 5 %.
Общую пористость П, %, вычисляют как П1 = 100 – ρотн, где ρотн – относительная плотность изделия, %.
Гидростатический метод. Этот метод является более универсальным, поскольку позволяет определить плотность изделия сложной и даже неправильной формы, а также оценить величину открытой (т.е. сообщающейся с поверхностью изделия) пористости (при общей пористости > 10 %).
Для определения плотности изделие взвешивают на воздухе на лабораторных весах с погрешностью не более 0,01 %. После этого поверхностные поры изделия закрывают путем обработки (пропитки) его в расплавленном парафине или покрывая его поверхность тонким слоем вазелина или лака. Изделие снова взвешивают, сначала на воздухе, а затем в воде. При взвешивании в воде не допускается образование пузырьков воздуха на поверхности изделия; при их появлении массу изделия не фиксируют, его вынимают из воды, сушат, подвергают повторной обработке с целью закрытия пор и снова взвешивают на воздухе и в воде. Плотность γ вычисляют, деля массу необработанного изделия (m1) на его объем, рассчитанный по формуле
V = (m2 – m3)/ γв,
где т2, т3 – суммарная масса подвеса и обработанного изделия, соответственно, на воздухе и в воде, г; γв – плотность дистиллированной воды при
Процессы порошковой металлургии. Курс лекций |
-388- |

II. ФОРМОВАНИЕ И СПЕКАНИЕ ИЗДЕЛИЙ ИЗ МЕТАЛЛИЧЕСКИХ И НЕМЕТАЛЛИЧЕСКИХ ПОРОШКОВ
Лекция 24 Свойства порошковых изделий
температуре испытания, г/см3. Образец и вода должны иметь температуру от
+15 до +30 °С.
Для определения объема образца V можно воспользоваться пикнометром с дистиллированной водой. Сначала на лабораторных весах взвешивают (вместе или раздельно) образец с закрытыми поверхностными порами и пикнометр, наполненный водой до риски или до отверстия в пробке. Затем часть воды из пикнометра удаляют, помещают туда образец, встряхивают пикнометр для отрыва пузырьков воздуха и доводят уровень воды до риски или до отверстия в пробке. После этого пикнометр с образцом снова взвешивают. Объем рассчитывают по формуле
V = (m4 – m5)/ γв,
где т4 – суммарная масса обработанного образца и пикнометра, заполненного водой до риски или отверстия в пробке, г; т5 – масса пикнометра с образцом и водой, г.
Для определения открытой пористости образец взвешивают (m1) на воздухе на лабораторных весах. Затем его пропитывают жидкостью (дегазированным или обычным индустриальным маслом, ксилолом, бензиловым спиртом или дистиллированной водой), выбор которой зависит от материала и размера пор анализируемого образца. Пропитанный жидкостью образец взвешивают (m6) на воздухе. Открытую пористость П2, %, вычисляют по формуле
П2 = [(m6 – m1)100/γжV,
где γж – плотность пропитывающей жидкости, г/см3; V – объем образца, см3. Результат записывают с точностью до 0,1 %.
Закрытую пористость П3 вычисляют как разность между общей П и открытой П2 пористостями изделия (образца): П3 = П1 – П2.
При определении гидростатическим методом плотности твердосплавного изделия образец (объемом > 0,5 см3 и массой < 200 г) взвешивают на воздухе с погрешностью < 0,001 г, после чего его подвешивают на нити или проволоке из некорродирующего материала (диаметром < 0,25 мм) или помещают в корзинку и погружают в сосуд с дистиллированной водой; на образце и нити не должно быть пузырьков воздуха. Образец взвешивают в воде с такой же погрешностью, что и на воздухе. Плотность образца рассчитывают по формуле
γ = m1γв /(m1 – m2),
Процессы порошковой металлургии. Курс лекций |
-389- |

II. ФОРМОВАНИЕ И СПЕКАНИЕ ИЗДЕЛИЙ ИЗ МЕТАЛЛИЧЕСКИХ И НЕМЕТАЛЛИЧЕСКИХ ПОРОШКОВ
Лекция 24 Свойства порошковых изделий
где m1, m2 – масса образца, взвешенного, соответственно, на воздухе и в воде, г; γв – плотность воды, г/см3. Отличие этого метода от описанного выше состоит в том, что поверхность образца ничем не покрывается, поскольку в твердом сплаве уровень пористости очень низкий (< 0,2 %) и вся пористость закрытая.
Металлографический метод. Пористость твердосплавных изделий определяют на металлографическом микроскопе. Подготовленные образцы не должны иметь следов шлифования, полирования или выкрашивания структурных составляющих. Шлиф изготовляют по поперечному сечению (излому) целого изделия или части его площадью < 2 см2.
Уровень пористости определяют просмотром нетравленой поверхности шлифа при увеличении в 100 или 200 раз для пор размером до 10 мкм и в 100 раз для пор размером до 50 мкм. Участок, полностью представляющий исследуемую площадь шлифа, сравнивают с микрофотографиями шкалы А (для пор размером до 10 мкм), В (для пор размером до 30 мкм) и D (для пор размером до 50 мкм). Оценку пористости проводят со ссылкой на соответствующую микрофотографию шкалы А, В или D, указывая объемное процент-
ное содержание пор; например, А 0,02; А 0,04; В 0,08; В 0,04; D 0,2; D 0,4.
Поры размером > 50 мкм определяют просмотром нетравленой поверхности шлифа при увеличении в 50–100 раз на всей поверхности шлифа (если площадь шлифа > 1 см2, допускается исследование его площади в 1 см2, прилегающей к рабочей части образца). Подсчитывается суммарная длина пор с указанием их числа на 1 см2 и размера пор по максимальной длине в интервале размеров 51–75, 76–100 и > 100 мкм: например, одна пора размером 55 мкм, две поры размером 80 мкм на площади 1 см2.
Электрические, тепловые и магнитные свойства. Электро- и теп-
лопроводность порошковых материалов зависят от их пористости и структуры. Эти свойства повышаются пропорционально плотности и асимптотически приближаются к соответствующему значению для компактного металла или сплава того же химического состава. В табл. 2.8 в общем виде приведены известные уравнения, позволяющие оценить влияние пористости П на свойства типа проводимости ω, где ω и ω к – значения свойства, соответственно, для пористого и беспористого материала.
Таблица 2.8
Влияние пористости на свойства типа проводимости
Автор |
Выражение |
Применимость выражения |
|
|
|
В. И. Оделевский |
ω = ωк (1 – 1,5П) |
0 ≤ П ≤ 0,66 |
|
ω = ωк [1 – ЗП/(2 + П)] |
Для матричных систем |
М. Ю. Бальшин |
ω = ωк (1 – П)1/5 |
Для матричных систем |
|
ω = ωк (1 – П)2 |
Для статистических смесей |
Процессы порошковой металлургии. Курс лекций |
-390- |

II. ФОРМОВАНИЕ И СПЕКАНИЕ ИЗДЕЛИЙ ИЗ МЕТАЛЛИЧЕСКИХ И НЕМЕТАЛЛИЧЕСКИХ ПОРОШКОВ
Лекция 24 Свойства порошковых изделий
Явления электрической проводимости и теплопроводности, имеющие одинаковую физическую сущность, для компактных материалов описываются обычно одними и теми же аналитическими зависимостями.
Эта закономерность сохраняется и для пористых тел, поэтому зависимости, приведенные втабл. 2.8, можно использовать для расчета обеих величин.
Связь между теплопроводностью и электрической проводимостью металлов и сплавов определяется числом Лоренца:
L = λρэ /T,
где λ – теплопроводность, Вт/(мК); ρэ – электропроводность, Ом м.
Для большинства металлов и сплавовL находится в пределах от 2,1 10-8 до 2,8 10-8 Вт Ом/К2 при 20 °С.
Расчет числа Лоренца по экспериментальным значениям теплопроводности и удельного электрического сопротивления пористых порошковых материалов показывает, что его значения не зависят от пористости в широком диапазоне температур (290–1 170 К). Это позволяет вычислять теплопроводность (удельное электрическое сопротивление) металлов любой пористости и при любой температуре, зная для них только величину L и температурную зависимость удельного электрического сопротивления (теплопроводности) в беспористом состоянии или при определенной пористости.
Известно, что поры достаточно заметно снижают тепло- и электропроводность. Например, практически для всех пористых материалов на основе железа до 500 °С электропроводность снижается почти в 3 раза, а теплопроводность – на 20–40 %.
На магнитные свойства порошковых материалов существенное влияние оказывают величина пористости, форма пор, содержание примесей, дисперсность структуры и наклеп. Поры ухудшают магнитные свойства, снижая магнитную проницаемость и уменьшая магнитную энергию соответствующих материалов. Магнитная проницаемость порошковых изделий зависит не только от их пористости, но и от условий спекания и свойств исходного порошка, в связи с чем при одной и той же пористости она может изменяться почти в 2 раза. Большое влияние на магнитные свойства оказывает среда спекания, взаимодействие которой с нагреваемым материалом с образованием каких-либо химических соединений (например, нитридов) может заметно ухудшить соответствующие характеристики порошковых изделий.
Механическиесвойства
Механические свойства и их конкретные значения наиболее важны для оценки эксплуатационной пригодности порошковых материалов, поскольку именно они обусловливают возможность работы изделий как при
Процессы порошковой металлургии. Курс лекций |
-391- |
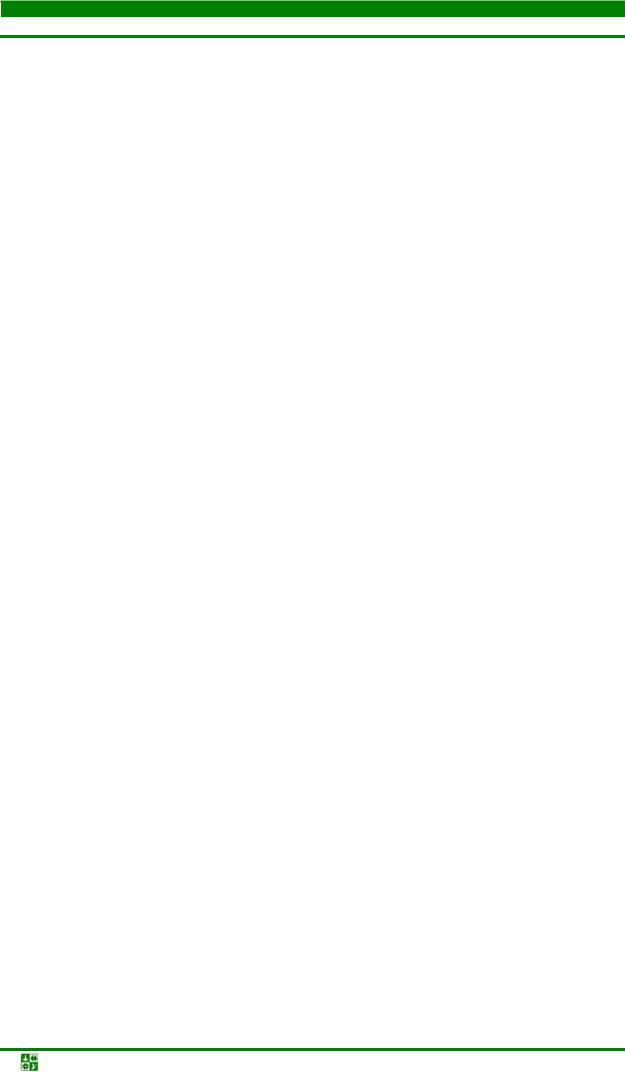
II. ФОРМОВАНИЕ И СПЕКАНИЕ ИЗДЕЛИЙ ИЗ МЕТАЛЛИЧЕСКИХ И НЕМЕТАЛЛИЧЕСКИХ ПОРОШКОВ
Лекция 24 Свойства порошковых изделий
статических, так и при динамических нагрузках. Механические свойства таких материалов зависят от пористости, формы пор, величины контактной поверхности и характера контакта между частицами. В свою очередь, величина контактного сечения и микронеоднородность напряжений в нем зависят от физико-химических характеристик исходных порошков, условий формования заготовок, температуры и продолжительности спекания, последующей термической обработки. В связи с этим механические свойства пористых порошковых изделий отличаются от свойств литых материалов аналогичного химического состава, а при одинаковой пористости их свойства могут различаться, если изделия изготовлены из порошков с разными свойствами или получены либо различными методами, либо по разным технологическим режимам.
Наличие пористости приводит к разрушению по специфическим механизмам, отличными от тех, которые свойственны литым материалам, поэтому для оценки механических свойств порошковых изделий необходимы специальные методики.
Неметаллические включения (их форма, размеры, количество и распределение по объему порошкового изделий), нарушают сплошность металлической матрицы и способствуют снижению всех механических свойств материала в еще большей степени, чем поры, и тем заметнее, чем выше плотность порошкового материала (изделия). На уровень и стабильность механических свойств оказывают влияние также защитные среды, используемые при спекании.
Обычно принято оценивать прочность, ударную вязкость и твердость порошковых изделий (материалов).
Прочность. Наиболее объективным показателем качества порошкового изделия является его предел прочности при растяжении, представляющий собой частное от деления максимальной нагрузки на номинальную площадь поперечного сечения испытуемого образца и характеризующий величину и прочность контактов между частицами (для литых материалов прочность при растяжении является мерой их сопротивления изменению формы под действием внешних сил). С ростом пористости прочность порошкового материала и ее отношение к пределу прочности при растяжении аналогичного литого (компактного) материала падают.
В теоретическом плане связь между структурно-чувствительными свойствами, к которым относится прочность, и плотностью (пористостью) изучается достаточно давно, однако большинство полученных математических зависимостей носят эмпирический характер. Некоторые из них представлены в табл. 2.9, где σ и σк – соответственно, предел прочности при растяжении пористого и компактного материалов; П – пористость порошкового материала, β – параметр, характеризующий неоднородность распределения напряжений по сечению образца (обусловлена неравномерностью распределения пор).
Процессы порошковой металлургии. Курс лекций |
-392- |

II. ФОРМОВАНИЕ И СПЕКАНИЕ ИЗДЕЛИЙ ИЗ МЕТАЛЛИЧЕСКИХ И НЕМЕТАЛЛИЧЕСКИХ ПОРОШКОВ
Лекция 24 Свойства порошковых изделий
Таблица 2.9
Аналитические зависимости прочности от пористости
Автор |
Выражение |
Значение констант и примени- |
|
мость выражения |
|||
|
|
||
Бальшин |
σ = σк (1 – П)m |
m = 3–6 |
|
Красовский |
σ = σк (1 – П/Пн) m |
Пн – пористость порошка в состоя- |
|
|
|
нии свободной насыпки |
|
Рышкевич |
σ = σк ехр(–b П) |
b = 4–7 |
|
Щербань |
σ = σк (1 – П2)ехр(–b П) |
|
|
Трощенко и Красовский |
σ = σк (1–1,5П)/ (1–1,5βП) |
β = 2; П < 0,66 |
|
Хейнес |
σ = σк (1 – П) / (1 – b П) |
b = 5 для стали |
|
Вейл |
σ = σк (1 – П) / (1 + АП) |
А – параметр |
|
Харвей |
σ = σк (l – k)3 / [(k3 + (l – k)3] |
k = [3П/(4π)]1/3 |
|
Герман |
σ = K(1 – П)m σк/D |
m = 4–7; П = 0,1–0,4; D = 4–6 мкм |
Обилие зависимостей видаσ = f(П) объясняется, с одной стороны, сложностью проблемы, требующей учета большого числа факторов, а с другой,
– возможной несопоставимостью опытных данных для образцов с различной пористостью, поскольку форма пор, величина зерна, содержание примесей для мало- и высокопористых материалов могут существенно различаться.
Контрольныевопросыизадания
1.Назовите методы определения плотности и пористости спеченного
изделия.
2.Кратко охарактеризуйте расчетный, гидростатический и металлографический методы определения пористости изделий.
3.Напишите уравнение, характеризующее связь между теплопроводностью и электрической проводимостью в порошковом теле.
4.Какое влияние оказывают поры на электро- и теплофизические свойства порошкового тела?
5.Какое влияние оказывают поры на магнитные свойства порошко-
вых тел?
6.Перечислите факторы, оказывают влияние на механические свойства порошковых тел?
7.Как изменяется прочность порошкового тела при увеличении по-
ристости?
8.Существует ли строгая математическая зависимость между прочность и пористостью порошкового тела?
Процессы порошковой металлургии. Курс лекций |
-393- |