
- •Введение
- •Основные положения, понятия и определения
- •Жизненный цикл изделий машиностроения и его технологическая составляющая
- •Основные термины
- •Понятие о машине и ее служебном назначении
- •Качество и экономичность машины
- •Понятие о точности
- •Точность детали
- •Точность машины
- •Отклонения характеристик качества изделий от требуемых величин
- •Положение теории вероятностей и математической статистики, используемые в технологии машиностроения
- •Тема 3. Связи в машине и производственном процессе её изготовления
- •Связи в машине и производственном процессе её изготовления
- •Определение понятия "связь"
- •Свойства связей
- •Тема 4. Базирование и базы в машиностроении (2 часа лекции)
- •Базирование и размерные цепи
- •Основы базирования
- •Классификация баз
- •Рекомендации к решению задач по базированию
- •Тема 5. Теория размерных цепей (2 часа лекции)
- •Теория размерных цепей
- •Термины и определения
- •Основные понятия
- •Звенья размерных цепей
- •Виды размерных цепей
- •Размеры и отклонения
- •Расчетные коэффициенты
- •Методы достижения точности замыкающего звена
- •Задачи и способы расчета размерных цепей
- •Конструкторские и технологические размерные цепи
- •Тема 6. Порядок построения размерных цепей. (2 часа лекции)
- •Порядок построения размерных цепей
- •Последовательность построения размерной цепи
- •Нахождение замыкающего звена, его допуска, и координаты середины поля допуска
- •Выявление составляющих звеньев размерной цепи
- •Методы достижения точности замыкающего звена
- •Метод полной взаимозаменяемости
- •Метод неполной взаимозаменяемости
- •Метод групповой взаимозаменяемости
- •Метод пригонки.
- •Метод регулирования
- •Методика и примеры расчета размерных цепей
- •Основные расчетные формулы
- •Последовательность расчетов
- •Примеры расчетов допусков (прямая задача)
- •Тема 8. Формирование свойств материала детали. (2 часа лекции)
- •Формирование свойств материала и размерных связей в процессе изготовления детали
- •Формирование свойств материала детали
- •Свойства материала заготовок
- •Воздействия механической обработки на свойства материала заготовок
- •Влияние смазочно-охлаждающей жидкости (СОЖ).
- •Обработка методами поверхностно-пластического деформирования (ППД).
- •Воздействия на свойства материала заготовок термической и химико-термической обработок
- •Обеспечение требуемых свойств материала детали в процессе изготовления
- •Тема 9. Обеспечение точности детали (2 часа лекции)
- •Достижение требуемой точности формы, размеров и относительного положения поверхностей детали в процессе изготовления
- •Три этапа в выполнении операции
- •Сокращение погрешности установки Определенность и неопределенность базирования заготовки.
- •Тема 10. Точность технологической системы (2 часа лекции)
- •Настройка и поднастройка технологической системы
- •Сокращение погрешности динамической настройки технологической системы
- •Информационное обеспечение производственного процесса
- •Свойства технологической информации и информационные связи
- •Технологическая задача и информационное обеспечение ее решения
- •Структура информационных связей в производственном процессе
- •Задачи технологов в разработке информационных процессов
- •Тема 12. Временные связи в производственном процессе (2 часа лекция)
- •Компоненты временных связей
- •Виды и формы организации производственного процесса
- •Основы технического нормирования
- •Пути сокращения затрат времени на выполнение операции
- •Пути сокращения подготовительно-заключительного времени
- •Сокращения штучного времени
- •Вспомогательное время
- •Структуры временных связей в операциях технологического процесса
- •Тема 13. Разработка технологических процессов сборки (4 часа лекции)
- •Основы разработки технологического процесса изготовления машины
- •Последовательность разработки технологического процесса изготовления машины
- •Разработка технологического процесса сборки машины
- •Исходные данные для проектирования
- •Выбор вида и формы организации производственного процесса сборки машины
- •Изучение и анализ чертежей изделия
- •Размерный анализ изделия и выбор метода достижения точности замыкающего звена
- •Анализ технологичности конструкции изделия
- •Разработка последовательности сборки машины
- •Разработка технологических схем сборки
- •Составление перечня работ и их нормирование.
- •Уточнение типа и организационной формы производства.
- •Проектирование операций условий среднего производства
- •Построение циклограммы сборки
- •Разработка компоновки и планировки сборочного цеха (участка)
- •Тема 14. Разработка технологического процесса изготовления детали (8 часов лекции)
- •Разработка технологических процессов изготовления деталей
- •Выбор вида и формы организации производственного процесса изготовления деталей
- •Выбор полуфабриката и технологического процесса изготовления заготовок
- •Изучение служебного назначения детали. Анализ технических требований и норм точности
- •Переход от служебного назначения изделия к техническим условиям на отдельные детали
- •Выбор технологических баз
- •Выбор способов обработки и числа необходимых переходов.
- •Расчет припусков и межпереходных размеров
- •Выбор режимов обработки заготовки
- •Формирование операций из переходов, выбор оборудования и нормирование
- •Оформление документации
- •Тема 15. Современный этап развития технологии машиностроения. (2 часа лекции)
- •Заключение
Устанавливаем координаты середин полей допусков:
|
m 1 |
|
|
|
о 0 |
i |
(11.9) |
|
i 1 |
|
|
ºβ = -0,01/300 (заведомо гарантируемый наклон оси шпинделя); |
|
||
ºβ |
= 0 (так удобно); |
|
|
ºβ2 |
= ºβ3 = ? (принимаем за неизвестное); |
|
|
ºβ4 |
= -0,015/300; |
|
|
ºβ5 |
= 0. |
|
|
После подстановки числовых значений координат середины полей допусков получим:
-0,01 = -0 - ºβ2 - ºβ3 + (-0,015) + 0. |
(11.10) |
Отсюда 2Δºβ2 = -0,005;
ºβ2 = ºβ3 = -0,0025/300.
Параметры точности изделия и технические условия на детали представлены в табл. 2.
|
|
|
Таблица 11.3 |
Параметры точности изделия и технические условия на детали |
|||
|
|
|
|
Расчеты |
Т-эконом. Соображения, деление допуска |
На основе выбора метода |
|
|
на изготовление и эксплуатацию |
достижения точности |
|
|
|
|
|
Служебное назначение |
Функц. параметр |
ТУ на сборочную |
ТУ на отдельные |
|
|
единицу |
детали |
|
|
|
|
|
|
|
|
Эксплуатационные |
0,025 |
0,01 |
β1 = 0º ± 0,0075/300 |
параметры |
β = 90 0,045 /300 |
β =90 0,03 /300 |
|
|
|
|
|
β =90º ± 0,05/300 |
|
|
β2 = 0º 0,0,00750125 /300 |
|
|
|
|
|
|
|
и т.д |
|
|
|
|
Выбор технологических баз
Последовательность выполнения первых этапов проектирования техно-логического процесса изготовления детали, включая выбор технологических баз, представлена на схеме (рис.
37).
Основные положения выбора технологических баз
1.Выбору технологических баз предшествует анализ служебного на-значения детали и обоснование технических условий на ее изготовление, позволяющие четко сформулировать задачи обработки.
2.Анализируя функции поверхностей деталей (исполнительные по-верхности, основные и вспомогательные конструкторские базы, свободные поверхности) и размерные связи между ними, находят поверхности, относительно которых заданно положение большинства других ее поверхностей. Для достижения заданной точности требуемых размерных связей поверхностей детали кратчайшим путем следует именно эти поверхности использовать в качестве технологических баз на большинстве операций технологического процесса.
3.Чаще положение большинства поверхностей задается относительно основных конструкторских баз детали. Поэтому в соответствии с принципом единства баз, как правило, в качестве технологических баз выбирают основ-ные базы детали.
4.В зависимости от сформулированных задач обработки соответствую-щим выбором баз реализуют преимущества координатного и цепного методов достижения точности.
5.Реализация принципа постоянства баз, т. е. обработка большинства поверхностей заготовки с использованием одного постоянного комплекта технологических баз, позволяет использовать преимущества координатного метода достижения точности. При координатном методе исключается влияние погрешности установки на точность относительных поворотов поверхностей и устраняются дополнительные погрешности, возникающие при смене баз.
6.В зависимости от конкретной ситуации и задачи обработки возможны отступления от принципа единства и постоянства баз в частности, если:
положение большинства поверхностей детали задано не относительно основных баз, а относительно других поверхностей, например, вспомогательных баз (станина токарного cтанка);
габаритные размеры основных баз детали недостаточны для создания надежного комплекта технологический баз обеспечения определенности базирования) или их физически неудобно использовать в качестве технологических баз;
принципы единства и постоянства баз и координатный метод получения размеров не обеспечивают или: затрудняет обеспечение заданной точности отдельных размеров, заданных от поверхностей, которые не являются основными базами. Для достижения точности этих размеров на соответствующих операциях в качестве технологических баз используют те поверхности, относительно которых они непосредственно заданы. В данном случае целесообразно использовать преимущество цепного метода, обеспечивающего кратчайшую размерную цепь и наибольшую точность указанных размеров.
7. Выбор технологических баз определяет реализацию принципа кратчайшего пути при достижении точности (минимизацию количества составляющих звеньев в размерной цепи, обеспечивающей точность заданного раз-мера). Высокие требования к точности обеспечиваются самым кратчайшим путем, когда достигаемый размер является замыкающим звеном в технологической размерной цепи системы «станок − приспособление − инструмент − заготовка».

Анализ служебного назначения изделия (сборочной единицы)
Анализ служебного назначения детали
Обоснование технических условий на изготовление детали
Анализ функций поверхностей детали
Анализ размерных связей между поверхностями детали
Разработка |
|
|
|
Выбор рационального |
|
|
|
||
последовательности |
|
|
|
варианта базирования |
|
|
|
||
изготовления детали |
|
|
|
|
|
|
|
Выбор комплекта посто- |
|
|
|
|
|
|
|
||||
|
|
|
|
янных технологических |
|
|
|
|
баз для большинства опе- |
|
|
|
|
раций технологического |
|
|
|
|
процесса |
|
|
|
|
|
|
|
|
|
Выбор баз для первой |
|
|
|
|
(первых) операций |
|
|
|
|
технологического |
|
|
|
|
процесса |
|
|
|
|
|
Рис. 11.23. Последовательность выполнения первых этапов проектирования технологического процесса изготовления детали
8.В первую очередь технологические базы выбирают для обеспечения точности относительных поворотов поверхностей детали, а затем − точности расстояний. Это объясняется тем, что точность относительных поворотов обеспечивается на станках методами взаимозаменяемости, что практически исключает возможность коррекции, а точность расстояний
−методом регулирования, при котором возможна компенсация отклонений.
9.Выбранный комплект технологических баз должен обеспечивать выполнение правила шести точек и условий определенности базирования детали.
10.При отсутствии надежного комплекта технологических баз, недостаточных габаритах или физическом неудобстве использования основных баз в качестве технологических, создают искусственные технологические базы в виде приливов, центровых отверстий и т. д.
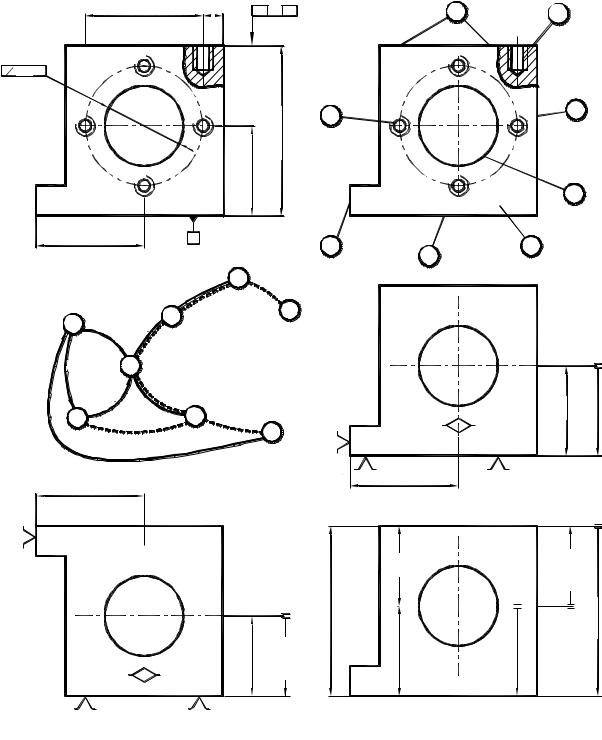
11. Если деталь невозможно обработать с одной установки, задача выбора технологических баз решается в две стадии:
выбирается схема базирования для большинства операций технологического процесса;
выбирается база для первой (первых) операции.
|
|
|
|
150 0,2 |
|
17 |
|
0,1 |
А |
|
К2 |
В2 |
|
|||
0,03 А |
|
|
|
|
|
|
|
|
|
|
|
|
|
|
|
|
|
|
|
|
|
|
|
|
|
|
0,05 |
0,3210 |
К1 |
|
|
|
С1 |
|
|
|
|
|
|
|
|
|
|
|
|
|
|
|||
|
|
|
|
|
|
|
|
|
|
|
|
|
|
|
|
|
|
|
|
|
|
|
|
|
|
|
|
|
|
|
|
|
|
|
|
|
|
|
|
|
|
|
|
120 |
|
|
|
|
|
В1 |
|
|
|
|
|
|
|
|
|
|
|
|
|
|
|
|
|
|
|
120 |
|
|
|
А |
|
|
|
|
02 |
|
|
03 |
|
|
|
|
|
|
|
|
|
|
|
|
|
|
|
01 |
|
||
а |
|
|
|
|
|
|
|
|
|
|
|
|
б |
|
|
|
|
|
|
|
|
|
|
|
|
К2 |
|
|
|
|
|
||
|
|
|
|
|
|
|
|
|
|
|
|
|
|
|
||
|
|
|
|
|
|
|
|
|
|
|
|
|
|
|
||
|
|
|
|
|
|
|
|
|
|
|
|
|
|
|
|
|
|
|
|
|
|
В2 |
|
Р |
5 |
|
Р5 |
С1 |
|
|
|
|
|
|
03 |
|
|
|
|
|
|
|
|
|
|
|||||
|
|
|
|
|
|
|
|
|
|
|
|
|
||||
|
|
|
|
|
|
|
|
|
|
|
|
|
|
|
|
|
|
|
|
|
|
|
Р2 |
|
|
|
|
|
|
|
|
|
|
|
|
|
01 |
|
|
|
|
|
|
|
|
|
|
|
||
|
|
|
|
|
|
|
|
|
|
|
|
|
|
|
|
|
|
|
|
|
|
|
Р1 |
|
|
|
|
|
|
|
|
|
|
|
02 |
|
Р4 |
|
В1 |
|
Р4 |
|
|
|
|
Б |
|
|||
|
|
|
|
|
|
|
|
|
|
|
|
|
||||
|
|
|
|
|
|
|
|
|
|
|
К1 |
4,5 |
|
|
6 |
|
|
|
|
|
|
|
|
|
|
|
|
|
|
|
|
||
|
|
|
|
|
|
|
|
|
|
|
|
|
|
|
|
|
в |
|
Г |
|
|
|
|
|
|
|
|
|
г |
1 |
Г |
2,3 |
|
|
|
|
|
|
|
|
|
|
|
|||||||
|
|
|
|
|
|
|
|
|
|
|
|
|
|
|||
4,5 |
|
|
|
|
|
|
|
|
|
|
|
|
|
|
|
|
|
|
|
|
|
|
|
|
|
|
|
|
|
|
|
2 |
|
|
|
|
|
|
|
|
|
|
|
|
|
|
Б |
|
|
|
|
|
|
|
|
|
|
|
|
|
|
|
|
|
|
|
|
|
|
|
|
|
|
|
|
|
|
|
|
Б |
|
|
|
|
|
|
|
|
|
|
|
|
|
|
|
|
|
|
|
|
1 |
|
|
|
|
|
|
|
|
|
|
|
2 |
|
|
|
|
|
|
|
|
|
|
|
6 |
|
|
|
Б |
|
|
Б |
|
|
|
д |
1 |
|
|
|
|
2,3 |
|
|
|
|
е |
|
|
|
||
|
|
|
|
|
|
|
|
|
|
|
|
|
Рис. 11.24. Выбор технологических баз для корпуса сверлильной головки
Анализ функционального назначения поверхностей и размерных связей между ними можно облегчить и сделать путем построения графа связи поверхностей детали (рис. 11.24). Для
этого поверхности детали обозначают индексами из букв O, В, К, С и цифр, которые устанавливаю функциональное назначение поверхности и ее номер. Буквы, входящие в индекс, обозначают:
О − основные базы,
В − вспомогательные базы,
К − крепежные и резьбовые отверстия,
С − свободные поверхности детали, включая и необрабатываемые.
Для поверхностей основных баз нумерацию делают в порядке уменьшения числа располагаемых на них опорных точек.
Например: 01 − установочная база, 02 − направляющая или двойная опорная, 03 − опорная. Для остальных поверхностей цифры обозначают последовательность их нумерации.
Построения графа связи поверхностей начинают с нанесения узлов, определяющих функциональное назначение поверхностей деталей. Затем узлы соединяют ребрами, которые обозначают наличие размерных и угловых связей между соответствующими поверхностями детали. Размерные связи наносят штриховыми линиями, а угловые – сплошными со стрелкой, направление которых указывает на базу. На ребрах могут быть проставлены также номиналы и допуски соответствующих размеров и относительных поворотов поверхностей деталей. На рис. 38 приведен пример построения графа связи поверхностей для корпуса сверлильной головки. Анализ приве-денных связей показывает, что положение главных отверстий (В1) и других обрабатываемых поверхностей (В2) определяется по отношению к основным базам корпуса.
В соответствии с принципом единства баз для корпуса сверлильной головки в качестве технологических баз для большинства операций целесообразно использовать плоскость основания 01 и плоскости 02, 03, образующие координатный угол.
Если при обработке отверстий в корпусе сверлильной головки в ка-честве установочной технологической базы взять противолежащую поверх-ность В2 (рис. 38, д), то возникают более длинные технологические размер-ные цепи. Точность параметров Б∆ и β , определяющих положение отверстия В1 относительно плоскости 01, в этом случае будет зависеть не только от точности операции расточки отверстия 01 (т. е. точности звеньев Б2 и β2), но и от точности операции фрезерования плоскости К2 (звенья Б1 и β1):
Б∆ = Б1 – Б2, |
β∆ = β1 + β2, |
ωБ∆ = ωБ1 – ωБ2, |
ωβ∆ = ωβ1 + ωβ2. |
Необходимость получения допуска δБ∆ = 0,1 и δβ∆ = 0,03/300 потребует в этом случае ужесточить допуски на межоперационные размеры:
δБ1 = 0,07, |
δБ2= 0,03 |
δβ1 = 0,015/300, |
δβ2= 0,015/300 |
δБ∆ = 0,07 + 0,03 = 0,1 ,
δβ∆ = 0,015/300 + 0,015/300 = 0,03/300.
Выполнить это не всегда представляется возможным. Поэтому необходимо стремиться к тому, чтобы на основе принципа единства баз наиболее ответственные параметры точности детали
с жесткими допусками получались при обработке как замыкающие звенья технологической системы (станок − приспособление − инструмент – заготовка) одного станка.
Решив задачу выбора баз для обработки большинства поверхностей заготовки, необходимо определить технологические базы для выполнения первой или первых операций технологического процесса. На этих операциях обрабатывают поверхности, которые затем используют в качестве технологических баз на большинстве последующих операций технологического процесса. При выборе технологических баз на первой операции необходимо исходить из решения следующих задач:
1.Установление связей, определяющих расстояния и повороты поверхностей, получаемых в результате обработки, относительно свободных необрабатываемых поверхностей.
2.Обеспечение равномерного распределения фактического припуска на поверхностях, подлежащих обработке.
Первая задача определяется техническими условиями, вытекающими из служебного назначения детали. Вторая задача определяется требованиями технологии. При решении второй задачи при выборе баз на первой операции руководствуются двумя основными положениями:
необходимостью сохранения наиболее качественного слоя материала на поверхностях детали, подвергающихся при ее работе в машине интенсивному износу;
необходимостью обеспечения равномерного распределения припуска на обработку поверхностей (прежде всего, отверстий). При обработке плоскостей равномерный припуск позволяет снять минимально необходимый слой материала и сохранить наиболее качественную зону поверхностного слоя материала.
При обработке отверстий равномерный припуск (рис. 11.25) позволяет устранить колебания упругих отжатий инструмента и вызываемые ими погрешности геометрической формы и за счет этого уменьшить необходимое количество технологические переходов, необходимых для достижения заданной точности геометрической формы.
Таким образом, в качестве количественных критериев для сравнения вариантов базирования на первой или первых операциях принимают точ-ность связи между обрабатываемыми и необрабатываемыми поверхностями и равномерность припуска на обработку.

Ось вращения расточного
инструмента
Ось отверстия
в заготовке
Ось вращения расточного
инструмента
Ось отверстия
в
заготовке
Рис. 11.25. Распределение припуска на обработку отверстия: а − равномерный припуск;
б − неравномерный припуск, вызванный несовпадением оси литого отверстия и оси вращения расточного инструмента
Для выбора наиболее предпочтительного варианта базирования необ-ходимо проанализировать возможные их схемы путем выявления и расчета возникающих технологических размерных связей. Для этого в первую очередь надо определять то место в технологическом процессе, где поставленная задача находит свое окончательное решение. Так, если стоит задача обеспечения требуемой точности положения обрабатываемой поверхности относительно свободных необрабатываемых поверхностей, то ее решение следует искать на операции окончательной обработки этой поверхности. Если же стоит задача обеспечения равномерного припуска при обработке определенной поверхности заготовки, то ее решение проявляется на операции обработки этой поверхности.

44 |
|
|
66 |
5 |
|
|
|
5 |
|
|
|
1 |
А |
А |
2,3 |
2, 3 |
|||
|
A2 |
A |
|
|
А |
|
|
|
A1 |
|
|
a)а
Б 1 |
Б2 |
|
А11 |
||
Б |
А |
=Б |
6 |
4 |
5 |
|
|
|
6 |
|
|
|
1 |
2,3 |
|
|
2, 3 |
АА==В
11
4 |
1 |
б)
5 |
2,3
2, 3
в) 66
Рис. 11.26. Анализ вариантов базирования при обработке
корпуса статора электродвигателя
Определив операцию, на которой решается поставленная задача, т. е. место получения замыкавшего звана, необходимо выявить все составляющие звенья этой технологической размерной цепи. Для этого следует найти те межпереходные размеры, полученные на данной и предшествующих операциях, и те размеры заготовки, которые влияют на точность замыкающего звена.
Пример. Обеспечить в процессе изготовления корпуса статора электродвигателя симметричность отверстия относительно необрабатывае-мых наружных поверхностей в горизонтальной плоскости (рис. 40).
Несимметричность А∆ обнаружится при выполнении расточной операций и через составляющее звено А1 будет зависеть от принятой схемы базирования детали на первой операций, в которой обрабатываются плоскость основания и установочные отверстия. На (рис. 40, б, в) приведены два варианта базирования детали на первой операции, отличающиеся только тем, что в первом варианте опорная база (точка 6) создана на боковой поверхности корпуса, а во втором варианте в качестве опорной базы принята плоскость симметрии наружных поверхностей корпуса. Скрытая опорная база во втором варианте может быть создана с помощью самоцентрирующего приспособления, губки которого условно показаны стрелками, обеспечи-вающего точность расположения обрабатываемых установочных отверстий относительно плоскости симметрии.
Проанализировав технологические размерные цепи и оценив возможные погрешности их составляющих звеньев, получим:
в первом варианте
ωА∆ = ωА1 + ωА2 = ωБ1 + ωБ2 + ωА2 = 0,1 + 2,4 + 0,1 = 2,6 мм;
во втором варианте
ωА∆ = ωА1 + ωА2 = ωВ∆ + ωА2 = 0,3 + 0,1 = 0,4 мм.
Пример. При обработке корпуса (рис. 11.27) необходимо обеспечить равномерность припуска в отверстии D.
Неравномерность припуска обнаружится на операции растачивания отверстия. Для большинства операций обработки корпуса в качества технологических баз используется основание и два технологически отверстия. При избранной схеме базирования детали на расточной операции неравномерность припуска проявится как относительное смещение оси отверстия в заготовке и оси вращения борштанги с резцом (рис. 11.27, а). Рассматривая решение этой задачи в вертикальной плоскости, такое смещение можно представить замыкающим звеном А∆ размерной цепи А, составляющими звеньями которой будут: A1 − расстояние между осью отверстия в заготовке и установочной технологической базой детали и А2 − расстояние между осью обработанного отверстия (осью вращения борштанги с резцом) и той же базой детали. Точность расстояния А2 зависит только от расточной операции. Расстояние А1 установится при обработке основания К на первой операции технологического процесса. Точность расстояния A1 будет зависеть от схемы базирования на первой операции. При обработке поверхности К могут быть использованы различные варианты базирования детали.
По первому варианту (рис. 11.27, б) в качестве установочной базы можно использовать поверхность полок (т. 1, 2, 3), а в качестве направляющей и опорной технологических баз – боковые поверхности основания детали.

При такой схеме базирования детали на первой операции расстояние А1 получается как замыкающее звено Б∆ трехзвенной размерной цепи Б:
|
|
ωА1 = ωБ∆ = ωБ1 + ωБ2. |
|
|
|
|
|||
|
|
|
|
|
|
К |
|
|
|
|
|
|
|
|
|
K |
|
|
|
d |
|
|
|
|
4 |
|
|
|
|
|
|
|
|
6 |
5 |
|
Б2 |
|
|
|
|
|
|
|
|
|
|||
|
|
|
|
|
|
|
|
Б |
|
|
|
|
|
|
|
|
3 |
Б1 |
Б=Б |
|
|
|
|
|
1,2 |
|
1 |
||
|
|
|
|
|
|
|
А |
||
|
|
|
|
|
|
|
Б |
=1 |
|
|
|
|
|
|
|
|
|
А |
|
|
|
|
А |
|
|
|
|
|
|
D |
|
|
А |
|
|
|
|
|
|
D |
|
|
|
|
|
|
|
|
|
5 |
|
|
А |
А |
|
|
|
|
|
|
|
6 |
А1 |
А2 |
|
|
|
|
|
4 |
|
|
|
|
|
|
|
|
|
,2 |
К |
3 |
|
|
|
|
|
|
|
K |
|
|
|
|
|
|
|
||
1,2 |
|
|
|
|
|
|
|
|
|
а) |
|
|
|
|
б) |
К |
|
|
|
|
|
|
|
|
|
|
|
|
|
|
|
|
|
|
|
K |
|
|
|
|
|
|
|
6 |
|
|
|
|
|
|
|
|
|
|
|
|
|
=Г |
|
|
|
|
|
|
|
|
|
= |
|
|
|
|
|
|
|
|
|
11 |
|
|
|
|
|
|
|
|
|
А |
|
|
|
|
|
|
3 |
4 |
|
А |
|
|
|
|
|
|
|
|
|
||
|
|
|
|
|
1 |
|
2 |
|
|
|
|
|
Б11=В |
В1 |
|
|
|
|
|
|
|
|
Б |
|
|
|
|
|
|
|
|
|
В2 |
В |
|
|
5 |
|
|
|
|
|
В |
|
|
|
|
|
|
в) |
|
|
|
|
|
гг) |
|
|
|
Рис. 11.27. Анализ вариантов базирования при обработке отверстий в корпусной детали
Составляющее звено Б2 – это выдерживаемый размер при обработке детали на настроенном станке, а звено Б1 – размер, принадлежащий заготовке. Его точность достигается в процессе получения заготовки и зависит от простановки размеров на чертеже заготовки. Если размеры заготовки будут проставлены и выдержаны в процессе ее получения так, как показано на рис. 42, в, то размер Б1 будет формироваться как замыкающее звено В∆ размерной цепи В и его погрешность ωБ1 будет равна погрешности ωВ∆, представляющей сумму погрешности составляющих звеньев В1 и В2:
ωБ1 = ωВ∆ = ωВ1 + ωВ2.
В соответствии с выявленной схемой образования погрешности ωА∆ в первом варианте базирования детали на первой операции
ωА∆ = ωА2 + ωА1 = ωА2 + ωБ2 + ωБ1 =ωА2 + ωБ2 + ωВ1 + ωВ2.
Численные значения возможных погрешностей: ωА2, ωБ2, ωВ1, ωВ2, – могут бать определены с помощью нормативов средне экономической точ-ности используемых методов