
Для пдф госы
.pdf
Методы повышения точности МРС
1.снижение отрицательной роли упругих перемещений за счет применения замкнутых систем (порталы, люнеты, дополнительные поддержки, уменьшение числа стыков в соединениях узлов станка, применение предварительных натягов в сопряжениях и т.д.);
2.целесообразное распределение потоков тепла от внешних источников и применение СОТС;
3.создание конструкций станков с целесообразным балансом плюсовых и минусовых погрешностей при их сборке;
4. |
уменьшение и выравнивание сил трения в направляющих, особенно для станков |
с требованиями точного |
позиционирования и точных перемещений исполнительных органов; |
|
|
5. |
применение систем исправления и компенсации погрешностей за счет автоматической коррекции. |
Н - нормальной точности; П - повышенной точности; В - высокой точности; А - особовысокой точности;
С - особоточные (сверхточные) станки; Т - сверхвысокого класса точности;
К - более высокого класса точности.
Станки классов В, А, С, Т, К являются прецизионными, установленными в специальных помещениях.
Вопрос 3. Пути повышения работоспособности режущих инструментов.
1)Применение смазывающе-охлаждающих средств.
Анализ известных исследований показывает, что влияние смазочно-охлаждающих технологических сред (СОТС) на процесс резания металлов заключается в снижении пластической деформации обрабатываемого материала, уменьшении сил и мощности резания, повышении качества обработанной поверхности (изменении микро- и макрогеометрических, а также физико-механических характеристик), уменьшении износа режущего инструмента, повышении его стойкости и, как следствие, в увеличении производительности обработки.
Поверхностно-активные (СОТС) вещества также проникают в микротрещины поверхностного слоя обрабатываемой детали и образуют там тончайшие ( адсорбционные) пленки, оказывающие расклинивающее воздействие, в результате чего облегчается пластическая деформация срезаемого слоя металла.
2)Нанесение износостойких покрытий.
Инструментальные многослойные покрытия придают высокую неоксиляемость и износостойкость, а также значительно снижают коэффициент трения. Многослойные структуры состоят из комбинации обычных твердых материалов, таких, как TiC, TiN, Ti(C,N) и Al2O3. Подобные покрытия могут быть иногда из 10 и более слоев, причем соответствующие отдельные слои отчасти тоньше 0,2 мкм. Они имеют при высокой скорости резания и соответственно высоких температурах хорошую износостойкость. Методы нанесения покрытий путем осаждения делятся на две большие группы: физические (PVD) и химические (CVD). Внутри этих двух основных групп существует довольно большое количество разновидностей.
3)Ионная имплантация.
Ионная имплантация — способ введения атомов примесей в поверхностный слой пластины или эпитаксиальной пленки путем бомбардировки его поверхности пучком ионов c высокой энергией (10—2000 КэВ). Технология ионного имплантирования разрешает внедрить заданное количество практически любого химического элемента на заданную глубину, позволяя таким образом сплавлять металлы, которые в расплавленном состоянии не смешиваются, или легировать одно вещество другим в пропорциях, которые невозможно достичь даже при использовании высоких температур. Возможно создавать композиционные системы с уникальными структурами и свойствами, существенно отличными от свойств основной массы детали.
4)Оптимизация геометрических параметров.
Форма режущей части инструмента не только обеспечивает его механическую прочность, теплостойкость, но и влияет на условия процесса резания: степень пластической деформации срезаемого слоя, количества образующейся теплоты, условия ее отвода, силы резания. Указанные факторы часто оказывают противоречивое действие на процесс резания. Так, уменьшение переднего угла делает режущую часть резца более массивной, но при этом одновременно увеличиваются силы резания, так как затрудняется процесс образования стружки, выделяется большое количество теплоты, интенсивность износа резца возрастает, стойкость снижается. Увеличение переднего угла облегчает процесс резания, но ухудшает условия отвода тепла, уменьшает прочность его режущей части; при этом стойкость резца также уменьшается.
5)Оптимальные режимы резания.
Вопрос 4. Погрешности измерений. Классификация погрешностей измерений.
Погрешность измерения — оценка отклонения измеренного значения величины от её истинного значения. Погрешность измерения является характеристикой (мерой) точности измерения.
По форме представления Абсолютная погрешность — ΔX является оценкой абсолютной ошибки измерения. Величина этой погрешности зависит от способа её вычисления, который, в свою очередь, определяется распределением случайной величины Xmeas.
Относительная погрешность — погрешность измерения, выраженная отношением абсолютной погрешности измерения к действительному или измеренному значению измеряемой величины Приведённая погрешность — погрешность, выраженная отношением абсолютной погрешности средства измерений к
условно принятому значению величины, постоянному во всем диапазоне измерений или в части диапазона.
По причине возникновенияИнструментальные / приборные погрешности — погрешности, которые определяются погрешностями применяемых средств измерений и вызываются несовершенством принципа действия, неточностью градуировки шкалы, ненаглядностью прибора.Методические погрешности — погрешности, обусловленные несовершенством метода, а также упрощениями, положенными в основу методики.Субъективные / операторные / личные погрешности — погрешности, обусловленные степенью внимательности, сосредоточенности, подготовленности и другими качествами оператора.
По характеру проявленияСлучайная погрешность — погрешность, меняющаяся (по величине и по знаку) от измерения к измерению. Случайные погрешности могут быть связаны с несовершенством приборов (трение в механических приборах и т. п.), тряской в городских условиях, с несовершенством объекта измерений (например, при измерении диаметра тонкой проволоки, которая может иметь не совсем круглое сечение в результате несовершенства процесса изготовления), с особенностями самой измеряемой величины (например при измерении количества элементарных частиц, проходящих в минуту через счётчик Гейгера).

Систематическая погрешность — погрешность, изменяющаяся во времени по определённому закону (частным случаем является постоянная погрешность, не изменяющаяся с течением времени). Систематические погрешности могут быть связаны с ошибками приборов (неправильная шкала, калибровка и т. п.), неучтёнными экспериментатором.
Прогрессирующая (дрейфовая) погрешность — непредсказуемая погрешность, медленно меняющаяся во времени. Она представляет собой нестационарный случайный процесс.
Грубая погрешность (промах) — погрешность, возникшая вследствие недосмотра экспериментатора или неисправности аппаратуры (например, если экспериментатор неправильно прочёл номер деления на шкале прибора или если произошло замыкание в электрической цепи).
По способу измерения
Погрешность прямых измерений
где : t = Sxαs ; Sx — Средняя квадратическая погрешность среднего арифметического, а αs — коэффициент Стьюдента, а А
— число, численно равное половине цены деления измерительного прибора.
Погрешность косвенных воспроизводимых измерений — погрешность вычисляемой (не измеряемой непосредственно) величины:
Если F = F(x1,x2...xn), где xi — непосредственно измеряемые независимые величины, имеющие погрешность Δxi, тогда:
Вопрос 5. Организация перехода на выпуск новой продукции. Сущестуют три основных метода перехода на выпуск новой продукции:
1 – последовательный; 2 – параллельный; 3 – параллельно-последовательный
1.Последовательный метод перехода – производство новой продукции начинается после полного прекращения выпуска продукции, снимаемой с производства а) прерывно-последовательный и б) непрерывно-последовательный
2.Параллельный метод перехода постепенное замещение снимаемой с производства продукции вновь осваиваемой. Одновременно с сокращением объемов производства старой модели происходит нарастание выпуска новой продукции ( Т – величина отрезка времени совмещения)
3.Параллельно-последовательный метод характерен для массового производства при освоении новой продукции, существенно отличающейся по конструкции от снимаемой. Необходимо всегда обеспечить для данных условий минимум потерь. Но рецепта единого нет: для сложных изделий массового производства – параллельно-последовательный метод перехода может оказаться наилучшим, а для простых, при высокой степени унификации – даже последовательный.
Вопрос 6. Перечислите основные литейные свойства металлов и сплавов.
Жидкотекучесть – способность расплавленного металла течь по каналам литейной формы, заполнять ее полости и четко воспроизводить контуры отливки. При высокой жидкотекучести сплавы заполняют все элементы литейной формы.
Усадка – свойство металлов и сплавов уменьшать объе м при охлаждении в расплавленном состоянии, в процессе затвердевания и в затвердевшем состоянии при охлаждении до температуры окружающей среды.
В результате объемной усадки появляются усадочные раковины и усадочная пористость в массивных частях отливки. Линейная усадка определяет размерную точность полученных отливок
Газопоглощение – способность литейных сплавов в расплавленном состоянии растворять водород, азот, кислород и другие газы.
Ликвация – неоднородность химического состава сплава в различных частях отливки.
Заполняемость - Она характеризует способность металлов и сплавов воспроизводить контур о тливок в особо тонких сечениях
Характер затвердевания. Характер затвердевания металлов и сплавов определяет особенность перехода металла из жидкого состояния в твердое.
Характер формирования литой поверхности . Под характером формирования литой поверхности металлов и сплавов подразумевают их способность воспр оизводить профиль поверхности формы (шероховатость,
механический пригар), склонность к образованию макронеровностей (спаи), склонность к химическому взаимодействию с формой (химический пригар).
Трещиностойкость - способность металлов и сплавов к релаксации (ослаблению, уменьшению) напряжений, возникающих в отливке при затвердевании и охлаждении, в результате усадки, фазовых превращений или температурного перепада.
Свариваемость. От свариваемости сплавов зависит качество исправления дефектов отливок и надежн ость соединения литых деталей методом сварки.
Билет 25
Вопрос 1. Задачи и последовательность отработки конструкции на технологичность. Виды технологичности.
Под технологичностью конструкции изделия понимается совокупность свойств конструкции изделия, определяющих ее приспособленность к достижению оптимальных затрат при производстве, техническом обслуживании, ремонте и утилизации.
Задачи отработки конструкции на технологичность (ГОСТ 14.201-83):
1— снижение трудоемкости изготовления изделия.
2— стандартизация составных частей изделия. Используя в конструкции изделия стандартные составные части, обеспечивают их взаимозаменяемость;
3— унификация составных частей изделия (использование в проектируемых изделиях составных частей конструкций, обработанных на технологичность и освоенных в производстве)
4— унификация элементов конструкции деталей – посадок, шероховатости поверхностей, резьб, шлицев, шпонок, модулей зубьев, диаметров отверстий и др;
5— обеспечить возможность применения типовых технологических процессов
Последовательность отработки:
1.подбор и анализ исходных материалов для оценки
2.уточняют объем выпуска
3.анализируют показатели технологичности изделий аналогичной конструкции
4.определяют показатели производственной и эксплуатационной технологичности
5.приводят сравнительную оценку показателей
6.разрабатывают мероприятия по их улучшению
Виды технологичности:
1)производственная, определяемая применительно к изготовлению изделия;
2)эксплуатационная, определяемая применительно к выполнению технического обслуживания и ремонта изделия;
3)при техническом обслуживании — эксплуатационная технологичность конструкции, определяемая применительно к подготовке и обслуживанию изделия соответственно при функционировании, транспортировании и хранении;
4)ремонтная, определяемая удобством и простотой ремонта.
Если Ку.э.> 0,6 - деталь технологична. 2. Коэффициент использования металла: Ким = mд / mз
где mд - масса детали, кг; mз - масса заготовки, кг.
В массовом производстве Ким →1; в серийном Ким=0,6…0,8.
Вопрос 2. Как осуществляется расчет привода главного движения в МРС.
1 Графоаналитический расчёт привода главного движения (выбор аналога станка, определение мощности двигателя, частот вращения, построение структурной сетки, картины частот вращения).
2 Расчёт привода главного движения (расчёт крутящих моментов, диаметров валов, модулей зубчатых колёс, числа зубьев). 3 Определение конструктивных размеров привода (определение ресурса работы элементов привода, клиноремённой передачи, относительной погрешности, расчёт зубчатых передач, выбор муфт, определение размеров валов и способ смазки). 4 Компоновка привода главного движения (развёртка, расчёт валов на прочность, расчёт подшипников, проектирование корпуса коробки скоростей, построение свёртки).
Вопрос 3. Инструменты для нарезания конических зубчатых колес с прямым зубом.


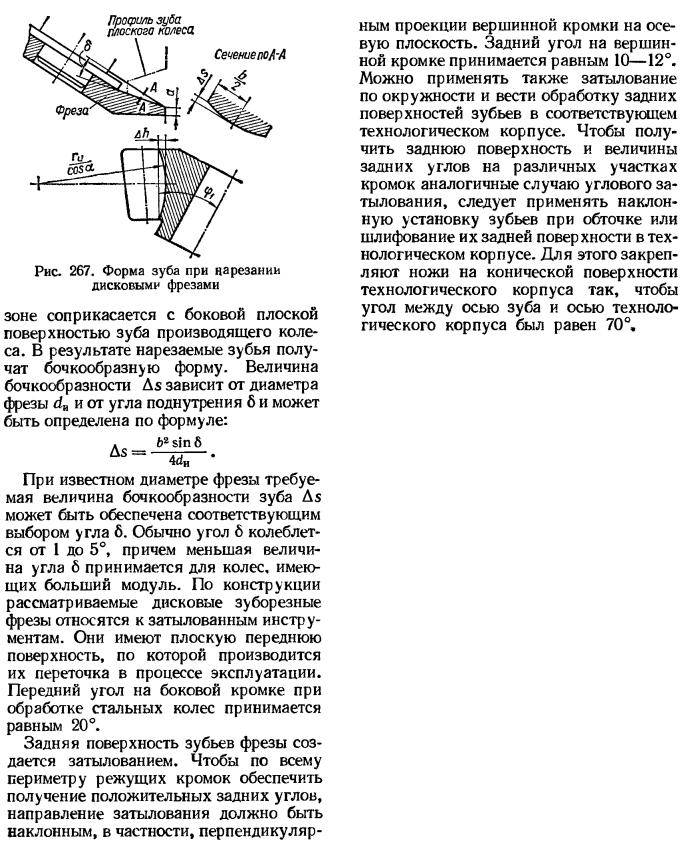
Вопрос 4. Классификация САПР по отраслям (применениям). Классификация машиностроительных САПР по целевому назначению. Классификация машиностроительных САПР по функциональным возможностям.
По применениям (по отраслям):
1.САПР для применения в отраслях общего машиностроения. Их часто называют машиностроительными САПР или MCAD (Mechanical CAD) системами. Область их применения – разработка изделий и процессов в машиностроении.
2.САПР для радиоэлектроники – ECAD (Electronic CAD) или EDA (Electronic Design Automation) системы. Назначение – проектирование принципиальных и монтажных схем, печатных плат, автоматическое размещение элементов изделий.
3.Электротехнические – разработка принципиальных схем и схем подключения электротехнического оборудования, его пространственная компоновка, ведение баз данных готовых изделий.
4.САПР в области архитектуры и строительства. Область применения - трехмерное проектирование архитектурностроительных конструкций, расчет специальных конструкций типа крыш, типовые статические расчеты строительных конструкций, ведение баз данных стандартных элементов, планирование территорий под строительство.
5.САПР оборудование промышленных установок и сооружений – создание принципиальных схем установок, пространственная разводка трубопроводов и кабельных трасс, проектирование систем отопления, водоснабжения, канализации, электроснабжения, вентиляции и кондиционирования, ведение баз данных оборудования, трубопроводной арматуры, готовых электротехнических изделий.
По целевому назначению машиностроительные САПР подразделяют на:
1.CAD – Computer-AidedDesign – системы автоматизированного проектирования изделий (AutoCAD, Компас,
SolidWorks)
2.CAM – Computer-AidedManufacturing – системы автоматизированной подготовки управляющих программ для оборудования с ЧПУ (СПРУТ, Гемма-3D, SolidCAM)
3.CAE – Computer-AidedEngineering – системы автоматизированного инженерного анализа деталей и машин (ANSYS,
NASTRAN, DesignSpace)
4.Системы автоматизированного контроля – предназначены для автоматизированного контроля изделий при помощи контрольно-измерительных машин (PowerINSPECT).
5.АСТПП (TDM – TechnologicDataManagement, CAPP – Computer-AidedProductProcessing) – системы, предназначенные для автоматизированного проектирования технологических процессов изготовления изделий, подготовки технологической документации и управления ею (САПР ТП2, ТехноПро).
Многие программные пакеты объединяют в себе сразу несколько видов MCAD: CAD/CAM/CAPP,ADEM, CAD/CAM/CAE,PTC,ProEngineer.
Системы, позволяющие решать широкий спектр задач на различных этапах технической подготовки производства называют сквозными. Примерами таких систем являются: CAD/CAM,Unigraphics + PDM,iMan, CAD/CAM/CAE,CATIA, CAD/CAM/CAPP,ADEM + «Парус».
По функциональным возможностям Mechanical CAD делятся на:
1.Лёгкие системы – предназначенные для решения узкого круга задач, например для подготовки УП для одного конкретного вида обработки – фрезерования (СПРУТ). Сфера применения – отдельные автоматизированные рабочие места с оборудованием ЧПУ, небольшие группы проектировщиков.
2.Системы среднего уровня – предназначенные для решения широкого круга задач, обладающие определённой универсальностью. Их функциональные возможности ограничены определённым количеством и сложностью объектов проектирования – числом деталей в сборке, сложностью обрабатываемых поверхностей (Компас, ADEM, AutoCAD). Сфера применения – отделы предприятия, группы проектировщиков.
3.Тяжёлые системы (системы верхнего уровня) – предназначенные для широкого круга задач и позволяющие проектировать объекты, сложность которых фактически ограничена только возможностями аппаратного обеспечения. Такие системы являются сквозными или комплексными, имеют возможности адаптации к конкретным задачам проектирования и могут применяться в качестве базовой системы проектирования в масштабах всего предприятия.
Вопрос 5. Дайте классификацию гидравлических насосов, перечислите основные их параметры. Существуют динамические и объёмные насосы.
В объёмных насосах энергия передаётся за счёт изменения объёма рабочей камеры, которая периодически сообщается с входом и выходом насоса. К этим насосам относятся: поршневые, шестерённые, пластинчатые, радиально-поршневые, аксиально-поршневые и др.
Динамические насосы: жидкость перемещается за счёт действия гидродинамических сил, при этом рабочая камера постоянно сообщается с входом и выходом насоса: центробежные, осевые, вихревые, струйные.
Основные параметры насоса:
1 Подача - количество жидкости, перекачиваемой насосом за единицу времени 2 Перепад давления, создаваемый насосом 3 Мощность, развиваемая насосом 4 Мощность, потребляемая насосом
5Напор, создаваемый насосом
6КПД насоса - полный КПД складывается из 3-х составляющих: гидравлического, объёмного и механического КПД.
Вопрос 6. Перечислите основные механические свойства металлов и сплавов.
Прочность — способность материала сопротивляться воздействию сил, не разрушаясь и не изменяя допустимой формы.
Твердость — способность материала противостоять проникновению в него другого, более твердого тела. Упругость — способность тела восстанавливать свою первоначальную форму после прекращения действия
сил, вызвавших это изменение. Примером упругого тела может служить с тальная пружина, которая после прекращения сил воздействия восстанавливает свою прежнюю форму.

Пластичность — способность материала изменять свою форму под воздействием сил не разрушаясь и не восстанавливать прежней формы после прекращения действия сил.
Вязкость — способность материала выдерживать механические воздействия (удары) не разрушаясь. Очень вязка, например, малоуглеродистая сталь, употребляемая для неответственных деталей.
Хрупкость — качество, противоположное вязкости, способность тела легко разр ушаться при механических воздействиях (ударах).
Билет 26
Вопрос 1. Способы отделочной обработки и их характеристика.
1 Тонкое (алмазное) точение - для обработки деталей из цветных металлов и сплавов, чугуна и стали. Обработка алмазными резцами или резцами из твёрдого сплава с большой скоростью резания, малой подачей и глубиной. Точность 7 квалитет и выше. Rа = 0,63 - 0,08 мкм
2Шлифование - обдирочное - тонкое
- точное (предварительное и чистовое) Точность до 6 квалитета. Ra = 1,25 и точнее.
3Притирка (доводка) - служит для окончательной доводки поверхностей, обеспечивает низкую шероховатость, высокую точность расположения поверхности.
Инструмент - чугунный (бронзовый или медный) притир.
4Суперфиниширование – особо чистый способ доводки поверхности - 14 класс точности, Rz = 0,05 -0,025 мкм
Инструмент - абразивные бруски.
5 Полирование - процесс чистовой обработки поверхности мягким кругом. На круг наносится мелкозернистый порошок, смешанный со смазкой. Шероховатость меньше, чем у суперфиниширования: Ra = 0,04 - 0,02 мкм до Rz = 0,1 - 0,05 мкм. 12 - 13 класс точности.
6 Выглаживание - процесс обработки поверхности давлением (шариком или алмазом).
Вопрос 2. Расчетные нагрузки, действующие на шпиндель МРС.
1.Вес заготовки
2.Силы резания
3.Усилия от закрепления заготовок (например, задний центр через заготовку давит на шпиндель)
4.Усилия от механических передач на шпинделе – например от зубчатой передачи, передающей крутящий момент на шпиндель
5.Динамические силы – от неуравновешенных заготовок, дисбаланса самого шпинделя
Шпиндели МРС рассчитываются:
1.на прочность – только шпиндели тяжело нагруженных обдирочных станков;
2.жесткость – шпиндели всех металлорежущих станков;
3.виброустойчивость – только высокоскоростные и токарные станки;
4.износостойкость трущихся поверхностей для сверлильных и расточных станков;
5.температурную деформацию для прецизионных станков.
6.Расчет шпинделей на жесткость,
Вопрос 3. Основные характеристики абразивного инструмента, определяющие его режущие свойства.
ПП 500x50x305 24А 10-П С2 7 К5 35м/с А 1 кл ГОСТ 2424-83
Здесь: ПП - тип круга; 500 х 50 х 305 - наружный диаметр х высота х диаметр посадочного отверстия; 24А - марка шлифовального материала; 10-П - зернистость; С2 - степень твердости; 7 - номер структуры; К5 - марка связки; 35 м/с - рабочая окружная скорость; А - класс точности круга; 1 кл - класс неуравновешенности.
Вопрос 4. Организация научно-исследовательских работ. Эффективность НИР.
Научно-исследовательские работы (НИР), или научные исследования – это специфический вид целенаправленной профессиональной интеллектуальной деятельности, задача которой состоит в создании (получении) новой информации об объектах, явлениях или процессах, происходящих в природе, обществе или технике.
Различают:
1)фундаментальные научные исследования (экспериментальная или теоретическая деятельность, направленная на получение новых знаний об основных закономерностях строения);
2)поисковые научные исследования (направлены на создание научного задела в целях его дальнейшего использования в прикладных разработках);
3)прикладные научные исследования (направленные преимущественно на применение новых знаний для достижения практических целей и решения конкретных задач).
Совокупность работ, выполняемых при проведении научных исследований по определенной проблеме, обычно называется темой. Под стадией понимается логически обоснованный раздел темы, имеющий самостоятельное значение и являющийся объектом планирования и финансирования. Можно выделить три типовых стадии НИР:
1)разработка технического задания (ТЗ) (формулируются цели, устанавливаются методы и условия проведения исследования, этапы, сроки, состав исполнителей; выполняется технико-экономическое обоснование целесообразности проведения темы, после чего производится подбор и анализ имеющихся материалов по исследуемой проблеме, проводятся патентные исследования, разрабатывается общая методика проведения исследований, формулируются конкретные задания исполнителям темы);
2)проведение теоретических и экспериментальных исследований (осуществляют теоретические разработки темы, если определена необходимость проведения экспериментальных работ, осуществляют проектирование и изготовление макетов и экспериментального образца, после чего проводят стендовые и полевые испытания экспериментального образца по разработанным программам и методикам, анализируют результаты испытаний, определяют степень соответствия полученных данных на экспериментальном образце расчетным и теоретическим выводам.);
3)оформление результатов НИР (формулируются выводы по проведенным исследованиям; оформляется в окончательном виде отчетная научно-техническая документация (отчет о НИР, конструкторская и технологическая документация, программная продукция, методики и т.д.), результаты исследования предъявляются заказчику в том виде и объеме, который был оговорен при заключении договора; документально оформляется сдача-приемка работы заказчику).
Эффективность НИР может быть оценена с учетом различных видов проявления эффекта, получаемого при использовании результатов научных исследований:
1)социального (Повышение безопасности для жизни и здоровья населения);
2)оборонного (Вероятность выполнения боевой задачи, степень защищенности объектов от поражения противником);
3)научно-технического (Повышение научно-технического задела в виде научных публикаций, диссертаций);
4)экономического (Снижение себестоимости производимой продукции, работ, услуг).
Вопрос 5. Перечислите способы управления скоростью движения выходных звеньев гидродвигателей.
Управление осуществляется изменением количества жидкости, поступающей в гидродвигатель в единицу времени, то есть изменением расхода. Для этого могут применяться регулируемые насосы или гидроаппараты управления расходом (дроссель). Соответственно 1 вид управления называется объёмным (машинным), 2 вид - дроссельным.
Гидроприводом с объёмным управлением называется гидропривод, в котором управление скоростью движения выходного звена гидродвигателя осуществляется при помощи регулируемого насоса или гидромотора или обеими гидромашинами.
Это управление осуществляется изменением количества жидкости, поступающей в гидродвигатель в единицу времени, то есть изменением расхода.
Дроссельное регулирование гидропривода — способ регулирования скорости движения штока гидроцилиндра или частоты вращения вала гидромотора (или угловой скорости вала поворотного гидродвигателя) за счёт изменения эффективного сечения потока через гидродроссель.
Возможно два принципиально разных варианта дроссельного регулирования:
1.изменением эффективного сечения потока через гидродроссель, включённый параллельно гидродвигателю
2.изменением эффективного сечения потока через гидродроссель, включённый последовательно гидродвигателю
В сравнении с объёмным регулированием гидропривода, при дроссельном регулировании хуже регулировочные характеристики (зависимость скорости движения выходного звена гидродвигателя от нагрузки), ниже КПД гидропривода и выше энергетические потери.
Однако гидросистемы с дроссельным регулированием намного дешевле гидросистем с объёмным регулированием. Поэтому дроссельное регулирование применяется в гидроприводах малой мощности, а также в гидроприводах, имеющих малое время работы и длительное время простоя.
Кроме того, гидросистемы с дроссельным регулированием менее инерционны, что позволяет применять их в гидроприводе станков, в которых часто требуется изменение скорости движения вала гидромотора или штока гидроцилиндра по достаточно сложному закону. Последнее реализуется за счёт кинематической связи запорно-регулирующего элемента гидродросселя с вращающимся кулачком требуемой формы.
Ещё одним преимуществом гидросистем с дроссельным регулированием является то, что они позволяют изменять подачу жидкости в гидродвигатель, а значит и скорость выходного звена гидродвигателя на очень небольшую величину. В