
Для пдф госы
.pdf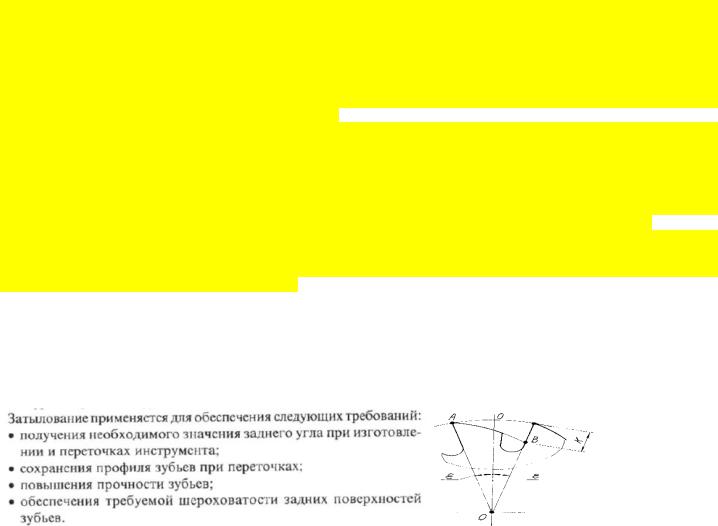
Системы автоматического управления обеспечивают работу станка по заранее заданной программе. Главное отличие автомата от обычного универсального станка состоит в том, что он по точной, заранее составленной программе выполняет определенный повторяющийся цикл работы.
Системы управления автоматов и полуавтоматов можно различать по следующим признакам: по принципу синхронизации, степени централизации управления, по методу воздействия, числу управляемых координат, виду программоносителя, по наличию или отсутствию обратной связи и т.д.
Централизованные системы управления характеризуются тем, что управление всем технологическим циклом осуществляется с центрального командного устройства (командоаппарата, пульта, распределительного вала, лентопротяжного устройства) независимо от действия и положения ИО. У таких систем управления (СУ) продолжительность рабочего цикла для каждого ИО является, как правило, величиной постоянной. Благодаря простоте схемы управления, надежности в работе удобству обслуживания и наладки централизованные СУ получили наибольшее применение в автоматах и полуавтоматах. К числу недостатков подобных систем можно отнести необходимость иметь дополнительные предохранительные устройства, так как команды с центрального пульта подаются вне зависимости от действия и положения исполнительных и рабочих органов.
Децентрализованные СУ, называемые иногда путевыми, осуществляют управление при помощи датчиков (чаще всего путевых переключателей и конечных выключателей), включаемых движущимися ИО. Эти системы основаны на управлении упорами. Все ИО связанны между собой так, что каждое последующее движение одного может происходить только лишь после окончания движения предыдущего ИО. Преимуществом этой системы управления является отсутствие блокировки, так как команды подаются только лишь после окончания предыдущей операции. Однако датчики расположены в рабочей зоне станков и нередко выходят из строя из-за попадания стружки, пыли, масла и выдают неправильные команды вследствие закорачивания электрических цепей. Кроме того, такие датчики являются еще недостаточно надежными в работе.
Смешанные СУ являются комбинацией первых двух систем. Здесь управление некоторыми элементами цикла осуществляется как в децентрализованной системе, а другими (остальными) от центрального командного, командного устройства. Например, управление всем циклом обработки детали осуществляется централизованно, а контроль выполнения очередных команд - при помощи путевых датчиков.
Вопрос 3. Затылование зубьев инструмента. Определение величины затылования.
Затылование – это придание задней поверхности зубьев инструмента такой формы, которая при заточке по передней поверхности, лежащей в осевой плоскости инструмента, позволяет сохранять профиль изделия до полного его износа и постоянство заднего угла.
K |
D tg |
|
Величина затылования: |
z |
, где D - диаметр, z - число зубьев, - задний угол |
Вопрос 4. Конструкции корпусов приспособлений и требования, предъявляемые к ним.
Корпуса приспособлений предназначены для установки на них опорных и зажимных устройств, а также других элементов, т.е. является основным базовым изделием приспособления. Корпуса приспособлений выполняют литыми или сварными. Литые корпуса используются в случаях, когда необходимо получить сложную форму корпуса либо когда приспособления выпускаются в относительно больших количествах. В остальных случаях используют сварные корпуса.
Чаще всего используют корпуса с конструкцией в виде плиты, либо коробчатой конструкцией (жесткость конструкции). Требования:
1Точность
2Прочность
3Жесткость
4Экономичность
5Низкая металлоемкость
Вопрос 5. Интеграция средств автоматизации проектирования. CALS и PLM. Проблемы интеграции.
Существует большое количество различных систем автоматизации различных аспектов проектирования в машиностроении, в связи с чем возникает потребность эффективного обмена информацией между ними. Для реализации данной задачи разработаны специальные методы интеграции различных компонентов средств автоматизации проектирования Интеграция CAD и CAM
Интеграция CAD и CAM имеет, как правило, односторонний характер: системы CAM используют геометрические модели, разработанные в CAD.
В CAM-системы передаются следующие виды информации из CAD:
1.Геометрическая информация о моделях поверхностей изделия, подлежащих обработке. Может передаваться как 2- мерная, так и 3-мерная информация.
2.Дополнительная геометрия изделия: модели заготовок, контуры и зоны обработки и т. д.
3. Информация о СТО, влияющих на параметры технологического объекта: инструмент, элементы приспособлений и т. д. Для того чтобы наладить интеграцию между CAD и CAM, необходимо осуществить не только возможность импорта–экспорта файлов данных, но выполнить ряд других требований:
1.Ассоциативность геометрической и технологической моделей изделия – при изменении геометрической модели в CAD, в CAM должна перестраиваться управляющая программа. Как правило, реализуется только параметрическая ассоциативность, т.е. имеется возможность автоматически перестроить УП, только при изменении параметров модели (размеры поверхностей), но не их структуры (добавление/удаление объектов).
2.Автоматическое отслеживание изменений в геометрической модели – CAM-система должна «знать» какие изменения внесены в модель и автоматически перестраивать УП.
Следует различать интеграцию CAD/CAM и их совместимость. Совместимость предполагает возможность обмениваться данными на уровне файлов, причём форма представления данных в этих системах может отличаться. Такие отличия часто приводят к ошибкам, возникающим в геометрической модели в результате их импорта-экспорта (нарушение связности моделей, появление нетолерантных рёбер, инверсия нормалей поверхностей и т. д.). В связи с этим, CAM-системы должны иметь в своём составе инструменты для устранения («лечения») ошибок в геометрических моделях.
Наибольшую степень интеграции имеют интегрированные CAD/CAM-системы, использующие общий формат файлов для хранения как конструкторской, так и технологической информации (ADEM, Unigraphics), поскольку именно этот способ позволяет решить проблемы обмена информацией и реализовать ассоциативность.
CALS – Continuous Acquisition and Lifecycle Support (непрерывная поддержка жизненного цикла изделия).
В процессе внедрения полной информатизации деятельности предприятия возникает ряд сложностей, связанных с различиями в формах представления информации в различных информационных системах. Для решения данной проблемы разрабатывается концепция CALS.
CALS – это стратегия систематического повышения эффективности, производительности и рентабельности процессов хозяйственной деятельности предприятия за счёт внедрения современных методов взаимодействия участников жизненного цикла продукции.
Основой CALS являются стандарты, устанавливающие способы обмена информацией между участниками жизненного цикла. Основной стандарт CALS – ISO 10303. Промышленные системы автоматизации и их интеграция.
CALS направлена на осуществление обмена данными между системами автоматизации независимо от их разработчика PLM – технология управления жизненным циклом изделий, заключающаяся в том, что для беспрепятственного обмена данными между системами автоматизации используется набор систем от одного разработчика.
PLM – технология, которая гарантирует беспрепятственный обмен данными, однако навязывает пользователям определенные наборы программного обеспечения. В использовании PLM заинтересованы в первую очередь крупные корпорации-разработчики САПР.
Т.е. CALS и PLM – два кардинально отличающихся подхода к решению одной задачи - обмена информацией между участниками жизненного цикла.
Вопрос 6. Рабочие жидкости гидроприводов. Требования к рабочим жидкостям для гидроприводов.
Рабочая жидкость гидропривода является средой, передающей энергию от насоса к гидродвигателю. Кроме того, рабочие жидкости гидроприводов выполняют следующие функции:
1.используются для смазывания трущихся поверхностей гидромашин
2.отводят тепло от нагретых элементов гидромашин
3.уносят продукты изнашивания и прочие частицы загрязнений
4.защищают гидропривод от коррозии.
Исходя из этих функций, к рабочим жидкостям предъявляют следующие требования:
-хорошие смазочные свойства;
-малое изменение вязкости при изменении температуры и давления;
-инертность в отношении конструкционных материалов деталей гидропривода;
-оптимальная вязкость, обеспечивающая минимальные энергетические потери и нормальное функционирование уплотнений;
-малая токсичность самой рабочей жидкости и её паров;
-малая склонность к вспениванию;
-антикоррозийные свойства; способность предохранять детали гидропривода от коррозии;
-оптимальная плотность;
-долговечность;
-оптимальная растворимость воды рабочей жидкостью: плохая для чистых минеральных масел; хорошая для эмульсий и т.п.
-невоспламеняемость;
-малая способность поглощения или растворения воздуха;
-хорошая теплопроводность;
-малый коэффициент теплового расширения;
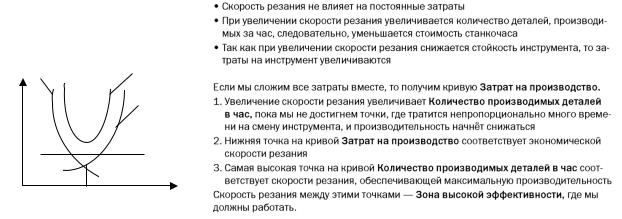
-способность хорошо очищаться от загрязнений;
-совместимость с другими марками рабочей жидкости;
-низкая цена;
Билет 6.
Вопрос 1. Технологические размерные цепи. Виды размерных связей в автоматизированном производстве Размерной цепью называется совокупность взаимосвязанных размеров, непосредственно участвующих в решении
поставленной задачи, образующих замкнутый контур и определяющих взаимное положение поверхностей (или осей) одной или нескольких деталей.
Технологические размерные цепи решают задачу по обеспечению точности при изготовлении деталей машин, устанавливают связь размеров деталей на разных этапах технологического процесса.
Измерительные размерные цепи решают задачу обеспечения точности при измерении, устанавливают связь между звеньями, которые влияют на точность измерения.
Виды размерных связей в автоматизированном производстве: 1 Установочные размерные связи 2 Операционные размерные связи
-размеры, получаемые мерным инструментом (при сверлении, развёртывании, протягивании)
-размеры, получаемые формообразующим движением (растачивание отверстий резцом на многоцелевых станках)
-размеры, получаемые от технологических баз до обработанных поверхностей
-размеры между поверхностями детали обработанные за один установ
-размеры, получаемые от измерительных баз
-размеры деталей, получаемые с использованием активного контроля
-прочие размеры
3 Межоперационные размерные связи
Установочные размерные связи (УРС): действуют в процессе автоматической установки заготовок в приспособления, кассеты, станки и т.д. УРС не влияют на достижение качественных показателей изделия, но определяет возможность автоматического транспортирования заготовок, загрузки и выгрузки станков.
-Замыкающими звеньями являются допустимые отклонения расположения технологических баз заготовки и исполнительных поверхностей приспособления, при которых возможно осуществить автоматическую установку заготовки.
-Составляющими звеньями являются размеры заготовки и приспособления, которые выявляются при построении размерных цепей по общей методике размерного анализа конструкции. УРС аналогичны сборочным размерным связям и рассчитываются точно так же. Разница состоит лишь в том, что допуски размеров при установке заготовок или изделий в различные приспособления м/б, как правило, значительно больше, чем при сборке изделий, и поэтому их легче обеспечить.
Операционные размерные связи (ОРС): возникают в процессе получения каждого размера детали при ее изготовлении.
-Замыкающим звеном является получаемый размер детали - операционный размер. В зависимости от вида размерной связи составляющими звеньями могут быть различные размеры технологической системы: размеры инструмента, станка, приспособления, установочные размеры заготовки, инструмента, приспособления.
От ОРС зависят: операционные размеры, получаемые размеры детали, настроечные размеры станка, режущего инструмента и приспособления, которые необходимо обеспечить при технологической подготовке производства. ОРС описывают и обеспечивают получение требуемых операционных размеров детали на каждой рабочей позиции автоматической обрабатывающей системы.
Межоперационные размерные связи (МРС): объединяют в единое целое весь технологический процесс изготовления детали, связывая различные операционные размеры детали с размерами заготовки и припусками на обработку. Межоперационные размерные связи описывают все этапы преобразования размеров от заготовки до детали.
-Замыкающими звеньями являются припуски на обработку и те размеры детали, которые непосредственно не получаются, как операционные размеры ни на одной из операций тех. процесса.
Составляющими звеньями являются операционные размеры детали, получаемые на операциях тех.процесса, а также размеры заготовки.
Вопрос 2. Понятие экономической скорости резания Экономическая скорость резания это такая скорость, при которой себестоимость продукции, зависящая от времени
обработки детали, числа заточек инструмента и стоимости расхода инструмента, была бы минимальной.
1
2
3
0 V

График, показывающий зависимость себестоимости от скорости резания кривая 1 - показывает изменение стоимости машинного времени обработки кривая 2 - затраты на инструмент, его замену и наладку кривая 3 - непроизводительные затраты кривая 4 - суммарная кривая всех затрат
Vэк V TTэк m - экономическая скорость резания - скорость, обеспечивающая min себестоимость операции
Т - стойкость инструмента m - показатель степени Пути повышения Vэк:
1 Сокращением потерь времени вызванных износом инструмента: (быстрая смена инструмента, механизмы автоматической замены инструмента).
-сокращение потерь времени на наладку инструмента (бесподналадочная смена мерного инструмента).
-сокращение потерь времени на регулирование инструмента (устройство для автоматического регулирования размера).
2 Повышение стойкости инструмента (использование СОЖ, износостойких покрытий, инструмента с подвижной режущей кромкой).
Вопрос 3. Влияние режимов резания и геометрии инструмента на силу резания при точении. Влияние скорости резания: На участке от V1-V2 скорость резания уменьшается ,т.к. появляется нарост на инструменте, что приводит к увеличению переднего угла и уменьшению усадки стружки и соответственно к уменьшению силы. На участке V2-V3 происодит срыв нароста, что увеличивает усадку и увеличивает силы резания. При скорости
более V3коэф усадки уменьшается, а следовательно уменьшаются силы резания. Pz=c/V0.15 ;Py=c/V0,3
Влияние глубины резания: С увеличением глубины рез увеличивается длина активной части реж кромки, а так же площадь поперечного сечения среза, что приводит к увеличению объёма пластической деформации, следовательно увеличиваются силы резания Pz=ctx
Влияние подачи: Увелич объем срезаемого мат-ла, что приводит к увеличению сил резания, но пластич деформация с увеличением толщины меньше, а значит и работа затраченная на пластическую деформацию меньше, следовательно, меньше силы резания.Pz=c2Sy
Влияние переднего угла: Т.к. реж кромка становится острее, что приводит к уменьшению усадки стружки след-но уменьш. силы резания.
Влияние главного угла в плане: С увеличением угла φ сила резания уменьшается т.к. уменьшается длина активной части режущей кромки и соответственно уменьшается сопротивление, силы резания уменьшаются. При увеличении угла φ возрастает толщина среза и длина криволинейного уч-ка режущей кромки. Угол в плане влияет на направление силы резания
Вопрос 4. Вычислительные сети САПР: задачи и классификация Вычислительная сеть – совокупность технических средств (станций), объединённых в единое целое при помощи
специальных каналов связи (среда передачи данных). Основное назначение вычислительных сетей – обмен информацией между компонентами сети.
Вычислительные сети решают следующие задачи: 1 Обмен информацией между станциями сети
2 Осуществление распределённых вычислений (когда одна трудоёмкая задача решается при помощи одновременного использования нескольких рабочих станций)
Классификация вычислительных сетей Вычислительные сети классифицируют по различным признакам. 1. По протяжённости:
-локальные вычислительные сети (ЛВС – LAN – LocalAreaNetwork) – сети, занимающие ограниченную территорию;
-глобальные вычислительные сети (WAN – WideAreaNetwork) – сети, занимающие обширную территорию, как правило, соединяющие между собой ЛВС.
2. По топологии (по способу соединения станций сети):
-общая шина (Ethernet 10Base-2);
-звездообразная, иерархическая (FastEthernet 100Base-TX);
-кольцевая (TokenRing).
3. По методам управления ресурсами среды:
- маркерная сеть – сеть, в которой станции передают данные через специальный пакет информации, называемый маркером;

-сеть с тактированным доступом – сеть, в которой данные между станциями передаются тактами в регулярные интервалы времени синхронно для всех станций;
-сеть со случайным доступом – сеть, в которой методом доступа к физической среде служит коллективный доступ с опознаванием несущей и обнаружением конфликтов.
Вопрос 5. Виды посадок и их характеристики. Обозначение на чертежах.
Посадка - характер соединения деталей, определяемый величиной получающихся зазоров и натягов, и характеризующий свободу относительного перемещения деталей.
Посадка с зазором – посадка, при которой обеспечивается зазор в соединении (поле допуска отверстия расположено выше
поля допуска вала) Smin Dmin dmax Smax Dmax dmin
Посадка с натягом – посадка, при которой обеспечивается натяг в соединении (поле допуска отверстия расположено ниже
поля допуска вала) Nmax dmax Dmin Nmin dmin Dmax
Переходная посадка - это посадка, в которой возможно получить как зазор, так и натяг (поля допусков отверстия и вала
частично перекрываются). Nmax dmax Dmin Smax Dmax dmin
Допуск посадки - это разность между наибольшим и наименьшим допускаемыми зазорами (в посадках с зазорами), или
наибольшим и наименьшим допустимым натягом (в посадках с натягом). TS Smax Smin TN Nmax Nmin |
|
В переходных посадках допуск определяется суммой наибольшего зазора и наибольшего натяга. TS TN Smax |
Nmax |
Вопрос 6. Перечислите основные преимущества и недостатки гидроприводов. Преимущества
1.Имеет малые габариты при больших создаваемых усилиях.
2.Бесступенчатое регулирование скорости движения выходного звена гидропередачи и обеспечение малых устойчивых скоростей. Минимальная угловая скорость вращения вала гидромотора может составлять 2…3 об/мин.
3.Время разгона, благодаря меньшему моменту инерции вращающихся частей не превышает долей секунды в отличие от электродвигателей, у которых время разгона может составлять несколько секунд.
4.Частое реверсирование движения выходного звена гидропередачи. Например, частота реверсирования вала гидромотора может быть доведена до 500, а штока поршня гидроцилиндра даже до 1000 реверсов в минуту. В этом отношении гидропривод уступает лишь пневматическим инструментам, у которых число реверсов может достигать 1500 в минуту.
5.Большое быстродействие
6.Автоматическая защита гидросистем от вредного воздействия перегрузок благодаря наличию предохранительных клапанов.
7.Простота преобразования вращательного движения в возвратно-поступательное и возвратно-поворотные без применения каких-либо механических передач, подверженных износу.
Недостатки
1.Утечки жидкости из гидросистем
2.Изменение вязкости применяемых жидкостей от температуры, что приводит к изменению рабочих характеристик гидропривода и создает дополнительные трудности при эксплуатации гидроприводов (особенно при отрицательных температурах).
3.Необходимость изготовления многих элементов гидропривода по высокому классу точности для достижения малых зазоров между подвижными и неподвижными деталями, что усложняет конструкцию и повышает стоимость их изготовления.
4.Взрыво- и огнеопасность применяемых минеральных рабочих жидкостей.
5.Невозможность передачи энергии на большие расстояния из-за больших потерь на преодоление гидравлических сопротивлений и резкое снижение при этом КПД гидросистемы.
Билет 7
Вопрос 1. Что такое жесткость технологической системы? Погрешности, возникающие вследствие недостаточной жесткости ТС и методы их снижения.
Технологическая система – замкнутая, упругая, механическая система, включающая в себя станок, приспособление, обрабатываемую заготовку и режущий инструмент.
Жесткость технологической системы – способность системы сопротивляться смещению под действием внешней силы. j = Py/y , [ j ]=Н/мм
где Py – радиальная составляющая силы резания; y – деформация, вызываемая этой силой.
Погрешности возникающие при недостаточной жесткости ТС
1.Отклонения размеров.

2. Погрешности формы. Отклонение размеров.
Погрешности формы.
седлообразность
конусность+бочкообразность Меры снижения погрешностей от упругих деформаций
1.Повышение жесткости ТС (уменьшение вылетов, люнеты, уменьшать количество стыков)
2.Снижение сил, вызывающих деформации
3.Повышение однородности механических свойств материала заготовки (рассеяние твердости в партии заготовок может достигать 30-40%).
4.Повышение точности исходных заготовок (погрешность формы заготовки копируется на обрабатываемую деталь).
Вопрос 2. Нагрузки, действующие на станок при его эксплуатации.
1.Статические нагрузки, действующие в динамической системе станка, могут быть двух видов:
— силы резания и трение, вызывающие рассеяние энергии (диссипативные процессы) в системе;
—силы, изменяющие потенциальную энергию системы. К ним относятся вес и силы упругости деформируемых элементов или сжатого рабочего тела.
2.Динамические нагрузки также бывают двух видов:
—основные, соответствующие принятым законам движения рабочих органов и изменениям во времени сил резания;
—дополнительные, вызванные конструктивными и другими факторами. Например, удары, вызванные зазорами в передачах.
1.Статические нагрузки - когда станок неподвижен.
2.Динамические нагрузки возникают в процессе работы станка под воздействием силы резания и вибрации станка.
Вопрос 3. Основные виды инструментальных материалов и область их применения.
1. Углеродистые инструментальные стали (У8, У10, У12А) – это стали с высоким содержанием углерода, для того, чтобы обеспечить высокую твёрдость при закалке. Углерод содержится в 10-х долях 1-1,2% С, остальное железо + примеси, А – высококачественные.
Изготавливают: ножовочные полотна, мелкозернистый инструмент, сверла - нулевки, все осевые инструменты, метчики, плашки, развертки
2.Легированные инструментальные стали (9ХС, ХВГ) – углерод содержится в 10-х долях. Температура нагрева t = 260º - красностойкость.
9ХС (0,9% С, 1%-хрома, 1%-кремния) – для мелких инструментов (плашки), мелкозернистая структура; ХВГ (Хром+Ванадий+Марганец) – длинные крупные инструменты – протяжки, сверла, зенкер.
3.Быстрорежущие инструментальные стали – основным легирующим элементом является вольфрам (Р) до 19%. Хрома до 4,5%..
- Стали обычной производительности t = 600º÷610º (Р9, Р18, Р6М5, Р18Ф2 – 9%, 18%, 6% вольфрама, 5% молибдена, 1% углерода, Ф-ванадий 2%). Изготавливают резцы, протяжки.
- Стали повышенной производительности t = 650º (Р6М5К5, Р6К5 – 6%вольфрама, 5% молибдена, 5% кобальта, 1% углерода) – узкая область применения (сверла, зенкеры, метчики, развертки, плашки, концевые фрезы, протяжки, резьбо- и зуборезный инструмент).
4.Твердые сплавы (металлокерамические твердые сплавы) – в качестве связки применяют кобальт. Изготавливают резцы и фрезы. Порошок: кобальт, карбид вольфрама.
А) Однокарбидные - вольфрамокобальтовые (WC+CO). Кобальта от 2 – 8%, t = 850º. ВК2, ВК3, ВК3М, ВК4, ВК6, ВК6М, ВК8О, ВК8ОМ.
Цифра - % кобальта, остальное карбид вольфрама., О – мелкозернистая структура, ОМ – особо мелкозернистая. ВК6 – 6% кобальта, 94% WC карбид вольфрама;
ВК8 – черновая обработка (работа по корке, с ударами), Чистовая – чугун, ВК2, бронза ВК3, ВК3М Получистовая – ВК4, ВК6, ВК6М.
Б) Двухкорбидные – титано-вольфрамо-кобальтовые (Ti+WC+Co), t = 870º÷900º
Т60К2 – алмазное растачивание, 60% карбидаTi; 2% кобальта Со, 38% WC карбида вольфрама Т30К4 - чистовая, 30% карбида титана, 4% кобальта, 66% карбида вольфрама Т15К6 – получистовая; Т5К10 – черновая обработка.
В) Трёхкарбидные - тантало-титано-вольфрамо-кобальтовые
ТТ7К14 - 7% карбидTi+карбидTa, 14% Со, 79% WC карбида вольфрама.
Применяют в тяжелом машиностроении, для снятия больших сечений. Промежуточная марка между быстрорежущими сталями и твердыми сплавами.
Г) Безвольфрамовые – на основе карбида титана ТН20. Н – никель. КНТ16-карбо-нитрид титана.
5.Минералокерамические инструментальные материалы (Al2O3)
ЦМ-332 (оксидная группа) – применяется в условиях плавного точения, для тонкой и чистовой обработки черных металлов с высокой скоростью резания.
В1, В3 – черного цвета ВОК-63 (вольфрамо - оксидная керамика), ВШ-75
6. Алмазные инструментальные материалы
Для обработки цветных металлов и сплавов, чистовая и тонкая обработка, получение низкой шероховатости.
Шаржируют Al2, применяют алмазные шлифовальные круги (хром+медь+связка) – для заточки, доводки, отделочной обработки.
Бывают искусственные алмазы t = 700º и природные t = 750º.
7. Сверхтвёрдые инструментальные материалы – основу составляет кубический нитрид бора (КНБ). Выдерживает t = 1300-1400º.
Эльборовые круги. Химически стоек, не взаимодействует с щелочью, не теряет режущих свойств.
-для чистовой, отделочной обработки твердых, черных металлов (шлифовальные круги, резцы, фрезы);
-финишное шлифование (“-“ повышенная хрупкость, тяжелое крепление).
Композит – 01 – эльбор, Композит – 05 Композит – 1,0
“-“ не может работать с большими сечениями
Вопрос 4. Сущность стандартизации. Цели и принципы стандартизации.
Стандартизация - это деятельность по установлению правил и характеристик в целях их добровольного и многократного использования, направленная на достижение упорядоченности в сферах производства и обращения продукции, работ и услуг.
Общей целью стандартизации является защита интересов потребителей и государства по вопросам качества продукции, процессов и услуг. Кроме того, стандартизация осуществляется в следующих целях:
–повышения уровня безопасности жизни или здоровья граждан, имущества физических или юридических лиц, государственного или муниципального имущества, экологической безопасности, безопасности жизни или здоровья животных или растений и содействия соблюдению требований технических регламентов;
–повышения уровня безопасности объектов с учетом риска возникновения чрезвычайных ситуаций природного и техногенного характера;
–обеспечения научно-технического прогресса;
–повышения конкурентоспособности продукции, работ и услуг;
–рационального использования ресурсов;
–технической и информационной совместимости;
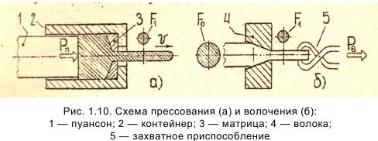
–сопоставимости результатов исследований (испытаний) и измерений, технических и экономико-статистических данных;
–взаимозаменяемости продукции.
Принципы:
1Добровольное применение стандартов и обеспечение условий для их единообразного применения. 2.Применение международного стандарта как основы разработки национального стандарта.
3.Сбалансированность интересов сторон, разрабатывающих, изготавливающих, предоставляющих и потребляющих продукцию (услугу).
4.Системность стандартизации. Системность — это рассмотрение каждого объекта как части более сложной системы. 5.Динамичность и опережающее развитие стандарта.
6.Недопустимость создания препятствий производству и обращению продукции, выполнению работ и оказанию услуг в большей степени, чем это минимально необходимо для выполнения целей стандартизации.
7.Эффективность стандартизации.
8.Принцип гармонизации. Этот принцип предусматривает разработку гармонизированных стандартов и недопустимость установления таких стандартов, которые противоречат техническим регламентам.
9.Четкость формулировок положений стандарта.
10.Комплексность стандартизации взаимосвязанных объектов.
11.Объективность проверки требований.
12.Обеспечение условий для единообразного применения стандартов.
Вопрос 5. Цель менеджмента предприятия и организации. Функции цели. Требования к цели.
Одна из центральных и ключевых задач менеджмента предприятия - это выработка цели. Цель определяет и регулирует действия, служит эталоном, главным критерием в деятельности предприятия и подчиняет все стороны управляющего воздействия. Цель - это те основные результаты, к которым предприятие стремится в своей деятельности на протяжении длительного времени.
Функции цели:
1)отражают философию предприятия, концепцию его деятельности и развития;
2)уменьшают неопределённость текущей деятельности, как предприятия, так и отдельного человека;
3)составляют основу критериев для выделения проблем, принятия решения, контроля и оценки деятельности предприятия, направленных на их реализацию, а также материального и морального поощрения наиболее отличившихся сотрудников. Требования к цели:
1)цель должна быть конкретной, т.е. выражена не только качественными, но и количественными показателями.
2)цель должна быть реальной, достижимой в данных условиях.
3)цель должна быть гибкой, способной к трансформации и корректировке в соответствии сменяющимися условиями деятельности предприятия.
4)цель достигается в результате совместной деятельности всего персонала, так как оказывает существенное влияние на мотивацию работников, которые хотят достичь реализации цели, установленной для предприятия. Если цель не достижима, стремление работников к успеху будет заблокировано и их мотивация ослабнет, т.к. в повседневной жизни принято связывать вознаграждение и повышение по службе с достижением цели предприятия.
5)цели должны быть совместимыми друг с другом во времени и пространстве и не ориентированы на действия, противоречащие друг другу.
6)цель должна быть измеряемой.
Вопрос 6. Перечислите способы получения заготовок давлением.
Основных способов шесть: прокатка, прессование, волочение, ковка, объемная и листовая штамповка. ПРОКАТКА — процесс получения машиностроительных профилей и фасонных изделий путем пластической деформации металла между вращ ающимися валками прокатного стана ПРЕССОВАНИЕ (рис. 1.10, а) — процесс получения машиностроительных профилей путем выдавливания
металла из замкнутой полости через профилирующее отверстие. Применяют три схемы: прессования: прямое, обратное и комбинированное.
ВОЛОЧЕНИЕ (рис. 1.10, б) — процесс отделочной обработки машиностроительных профилей путем протягивания металла через калибрующее отверстие. Всегда без нагрева.
КОВКА — |
процесс получения |
фасонных изделий |
путем целенаправленного |
мног ократного |
и |
последовательного деформирования |
нагретой исходной заготовки с помощью универсального подкладного |
||||
инструмента (прошивни, обжимки, оправки, топоры) между бойками молота или пресса. |
|
|
|||
ГОРЯЧАЯ |
ОБЪЕМНАЯ ШТАМПОВКА — процесс |
получения фасонных изделий путем деформирования |
|||
нагретой исходной заготовки в ручье — замкнутой полости инструмента — штампа (см. рис. 1.14, с. |
15). |
||||
Конфигурация и размеры ручья полностью предопределяют конфигурацию и размеры получаемой поковки. |
|

ЛИСТОВАЯ ШТАМПОВКА — процесс получения плоских и объемных тонкостенных изделий из листового материала на прессах с помощью штампов.
Достоинства процессов обработки давлением являются :
- экономия металла за счет малых припусков и небольших технологических отходов на операц иях;
-высокая производительность за счет больших скоростей обработки;
-БОЛЬШАЯ ТОЧНОСТЬ изделий;
-УЛУЧШЕНИЕ ЭКСПЛУАТАЦИОННЫХ СВОЙСТВ изделий за счет создания при деформировании МЕЛКОЗЕРНИСТОЙ и ВОЛОКНИСТОЙ целенаправленной СТРУКТУРЫ металла .
НЕДОСТАТОК — относительно ВЫСОКАЯ СТОИМОСТЬ изделий.
,0Билет 8
Вопрос 1. Назовите составляющие штучного и штучно-калькуляционного времени. Раскрыть содержание каждой составляющей.
Штучное время – время на изготовление одной детали.
Штучное время = основное + вспомогательное +обслуживания + отдых и личные надобности
ТШТ tо tв tобсл tотд (массовый тип производства)
t |
о |
- основное время - время в течение, которого происходит снятие стружки |
|
|
|
t |
в |
- вспомогательное время - время на контрольные измерения + время на установку и снятие + время, связанное с |
|
|
переходом + время на приемы, не вошедшие в комплексы t обсл - время обслуживания рабочего места
t отд - время на отдых и личные надобности
Штучно-калькуляционное = штучное + подготовительно-заключительное / число деталей в партии запуска
ТШТ-К ТШТ ТП. З. n (для серийного типа производства)
ТП. З. - подготовительно-заключительное время – время, затрачиваемое на подготовительные и заключительные работы на
партию,
n - количество деталей в партии запуска
Вопрос 2. Принцип работы и настройка зубофрезерного станка.
Станок служит для фрезерования зубьев цилиндрических, прямозубых и косозубых, также червячных колёс методом обкатки зубьев червячной фрезой и обрабатываемой заготовки. Вращение червячной фрезы на один оборот соответствует перемещению зубчатой рейки на один шаг или поворот обрабатываемого зубчатого колеса на один зуб. Станок может использоваться для фрезерования шлицев.
Настройка станка производится на различные способы подачи: радиальная, тангенциальная, диагональная.
Например, для нарезания цилиндрических колёс фреза устанавливается под углом, равным углу подъёма витков фрезы и осуществляется вертикальная подача и согласованное вращение фрезы и заготовки.

При нарезании червячных колёс можно применить также способ тангенциальной подачи (рис. Б) или способ радиальной подачи (рис. А) - когда стол перемещается к червячной фрезе в радиальном направлении.
При тангенциальной подаче червячная фреза и заготовка установлены на заданном межосевом расстоянии, и заготовка перемещается вдоль оси червячной фрезы при их совместном вращении.
Диагональный способ - при нарезании косозубых зубчатых колёс совершается совместное перемещение вдоль оси и вертикальная подача (червячная фреза работает узкими участками на длине 3-5 зубьев, поэтому износ зубьев червячной фрезы происходит не на всей длине).
Делают на специальных зубофрезерных станках, которые могут двигать фрезу сразу в двух направлениях
Впонятие настройка зубофрезерного станка входит расчет передаточных отношений сменных зубчатых колес настраиваемых гитар, подбор колес и установка их на станке. Вообще, там составляется уравнение кинематического баланса станка, а по нему подбираются передаточные числа и колеса!
Впонятие наладка станка входят подготовительные работы, связанные с установкой червячной фрезы на оправке, установкой подсобранной оправки во фрезерном суппорте и выверкой ее до необходимой точности. Сюда также относится установка и очень тщательная выверка на станке приспособления или оправки для точной фиксации и крепления заготовок нарезаемых колес. И, наконец, установка подвижной стойки станка на глубину нарезания зубьев, а также автоматического выключателя подачи на нужное положение.
Вопрос 3. Зенкеры, их классификация, назначение, геометрические параметры.
Зенкеры – осевой режущий инструмент, предназначенный для повышения точности формы отверстия, полученных после сверления, отливки, ковки, штамповки, а также для обработки торцовых поверхностей бобышек, выступов и др. Зенкеры для обработки цилиндрических отверстий применяют для окончательной обработки отверстий с допуском по 11-, 12-му квалитетам и обеспечивают параметр шероховатости поверхности Ra=20...40 мкм или для обработки отверстий под последующее развертывание.
Классификация зенкеров.
1)По методу закрепления на шпинделе станка:
a)Хвостовые с коническим хвостовиком;
b)Насадные с коническим отверстием и торцевой шпонкой.
2)По инструментальному материалу режущей части:
a)Из углеродистой и легированной стали, — применяются очень редко;
b)Из быстрорежущей стали — наиболее распространенные;
c)Оснащенные твердым сплавом.
3)По конструкции:
a)Цельные;
b)Составные:
. Сварные — быстрорежущая сталь;
. С припаянными пластинами твердого сплава;
c)С вставными ножами из инструментального материала;
4)По форме отверстия делятся на:
А) Цилиндрические Б) Конические В) Зенковка Г) Торцовые Д) Цековки