
Для пдф госы
.pdf
2.Кодируют |
инструмент |
при |
помощи |
кодовых |
колец. |
Кольца |
имеют |
в |
различных |
||||
сочетаниях выступы и впадины. Их устанавливают в хвостовую часть инструмента. |
|
|
|
|
|
||||||||
3.Кодирование |
гнезда |
под |
инструмент |
при |
помощи |
кодового |
ключа |
с |
выступами |
и |
|||
впадинами. |
|
|
|
|
|
|
|
|
|
|
|
|
|
Применяют различные методы распознавания блоков:
1)без кодирования, но с расположением инструментов в последовательности обработки;
2)кодирование оправки инструмента;
3)кодирование гнезд магазина (постоянное, переменное).
Первый вариант используется при небольшом количестве инструментов и отсутствии повторного использования в одном цикле обработки. Инструментальные блоки в этом случае располагаются в магазине или револьверной головке в соответствии с технологическим процессом. Такая система поиска инструмента допускает пропуски гнезд, оставляя их без инструментов. После каждого цикла смены инструмента магазин совершает поворот до подхода в позицию загрузкивыгрузки следующего инструмента. После выполнения всех операций обработки окажется, что инструменты сохранили первоначальную последовательность, сместившись в магазине на один или несколько шагов по сравнению с исходным положением. Вместе с тем этот простой и надежный способ кодирования усложняет изготовление оправок и вызывает снижение их жесткости и точности обработки вследствие удлинения оправок, что приводит к некоторому увеличению массы оправок и ухудшению динамических качеств механизма поворота магазина. Кроме того, при большом числе инструментов увеличивается время поиска (при отсутствии реверса), невозможна смена инструментов больших диаметров с пропуском двух соседних гнезд.
Кодирование оправок осуществляется с помощью установки набора кодовых колец, от которых при движении магазина с оправками считывающее устройство получает сигнал (подобно тому, как для разных дверных замков делают ключи с различным сочетанием выступов и впадин. При повороте магазина оправка, проходя мимо конечного выключателя-датчика, замыкает кольцами его контакты-щупы. При совпадении кода оправки, т.е. комбинации колец, с кодом, записанным в программе обработки, магазин останавливается. При этом гнездо магазина с требуемым инструментом будет находиться в позиции смены инструмента. Поиск инструмента при вращении магазина осуществляется во время работы станка.
При кодировании гнезд магазина команда для его останова в определенной позиции с необходимым инструментом подается ключом, вставленным в магазин напротив соответствующего инструмента, или комбинацией штифтов (кулачков), воздействующих на микропереключатели и считывающие устройства. Ключи имеют вид пластин или валиков с проточками. Кодирование гнезд магазина может быть постоянным и переменным. Постоянное кодирование характеризуется тем, что во избежание ошибки при установке инструмента в гнездо оправки предусмотрены устройства для механической блокировки, т.е. каждая оправка может быть вставлена только в свое гнездо.
При переменном кодировании в системе настраиваются коды гнезда и инструмента, который вставляется в это гнездо. Кодирование гнезд получило применение в связи с удешевлением инструментальных оправок и повышением их жесткости, некоторым уменьшением времени поиска инструмента вследствие возможности выбора кратчайшего пути для вращения магазина, возможности применения увеличенных диаметров инструментов с пропуском двух соседних гнезд.
Вопрос 3. Встречное и попутное фрезерование, их характеристика. Достоинства и недостатки. Картинку рисовать обязательно!!!!!!!!!!!!!
Попутное фрезерование Достоинства:
1.Сила резания прижимает заготовку к столу. Отсюда более упрощенное использование зажимных приспособлений.
2.Износ инструмента (задней поверхности зуба) происходит менее интенсивно, что позволяет вести фрезерование с большими скоростями резания. Стойкость инструмента больше, чем при встречном фрезеровании.
3.Стружка легко удаляется, т. к. остается позади фрезы. Обработанная поверхность имеет лучшее качество.
Недостатки:
1.Не может применяться при обработке заготовок с коркой (литье, поковка, горячекатаный прокат). Твердая корка с различными включениями может привести к повышенному износу и повреждению инструмента.
2.Из-за высокой ударной нагрузки, при врезании режущих зубьев в заготовку, станок и приспособления должны обладать достаточной жесткостью.
3.Зазор в механизме перемещения стола должен отсутствовать.

Встречное фрезерование Достоинства:
1. Плавный и мягкий процесс резания. Нагрузка на станок нарастает постепенно и не зависит от рельефа поверхности заготовки.
Недостатки:
1.Необходимость надежного закрепления заготовки, т.к. фреза стремится вырвать ее из приспособления.
2.Более быстрый износ инструмента (задней поверхности зуба фрезы) из-за высокого трения при снятии стружки минимальной толщины в начале резания.
3.Затруднено удаление стружки, т.к. она падает перед фрезой. При этом некоторая ее часть увлекается режущими зубьями за собой, что может привести к ухудшению обработанной поверхности.
Вопрос 4. Виды и конструкция основных зажимных механизмов.
Зажимные механизмы приспособлений делят на простые и комбинированные. К простым (или элементарным) механизмам относятся: винтовые, клиновые, эксцентриковые, рычажные, шарнирно-рычажные, пружинные. Комбинированные состоят из двух-трех сблокированных последовательно простых приспособлений. По числу точек приложения силы зажима механизмы делят на единичные и много кратные. Многократные механизмы зажимают одну деталь по нескольким точкам или несколько деталей одновременно и с равными силами.
По степени механизации зажимные механизмы делят на:
1)ручные – требующие применения мускульной силы и утомляющие рабочего; их применяют в единичном и мелкосерийном производствах;
2)механизированные – работающие от силового привода, в связи с этим нередко называют механизмами-усилителями; их применяют в серийном и массовом производствах;
3)автоматизированные – приводящиеся в действие перемещающимися частями станков, силами резания или центробежными силами вращающихся масс; осуществляют зажим и раскрепление заготовки без участия рабочего; их применяют в крупносерийном и массовом производствах.
Нужно рисовать картинки!!!!!!!!!!
А) клиновой Б) Винтовой
В) Эксцентриковый Г) Рычажный
Вопрос 5. Инструменты для чистовой обработки зубчатых колес.
-Шеверы - многолезвийные инструменты в виде зубчатого колеса или рейки с лезвиями на боковых сторонах зубьев. Шеверы предназначены для чистовой обработки цилиндрических и червячных зубчатых колес с m=0,2...8,0 мм с целью повышения точности на одну степень. При этом исправляются профиль зубьев, шаг и до Ra=0,69...0,32 мкм снижается шероховатость поверхности зубьев; накопленная погрешность окружного шага колеса и радиальное биение зубчатого венца при шевинговании исправляется хуже.
-Для обработки цилиндрических колес применяются дисковые и реже реечные шеверы, а червячные шеверы – для червячных колес.
-Абразивные червячные круги. Предназначены для шлифования зубчатых колес методом обкатки. -Фасонные абразивные круги – профиль повторяет форму впадины зуба (работают методом копирования) -Хонингование - для чистовой обработки зубьев с м=1.5-6мм. Уменьшает шероховатость.
-Холодное прокатывание – окончательная обработка профиля зубьев без снятия стружки путём пластического деформирования метала в холодном состоянии в зацеплении с эталонным колесом.
Вопрос 6. Для чего применяют штамповочные и литейные уклоны и радиусы.
Для (предотвращения) облегчения извлечения поковок из штампа, его боковые стенки выполняют с уклонами - штамповочные уклоны, при этом поковка получается с напусками. Применяются штамповочные уклоны 1...10 Если предусматривается выталкиватель, то уклоны - 1...3, если выталкиватель отсутствует, то - 5...7. Значение уклонов внешних и внутренних назначают по ГОСТ.

На пересекающихся поверхностях поковки делают закругления - радиусы закругления, которые делятся на внутренние и внешние (наружные). Обычно Rвн=1...6 мм, Rн=1...8 мм. Величина закругления зависит от массы поковки и глубины полости ручья. Чем больше то и другое, тем больше значение радиуса.
Сопряжения необрабатываемых поверхностей должны быть оформлены радиусами, которые необходимы как для улучшения условий заполнения металлом полостей штампа (внутренние радиусы), так и для повышения стойкости штампов (наружные радиусы).
Билет 13
Вопрос 1. Дать определение качества продукции. Какими показателями характеризуется качество.
Качество продукции - совокупность свойств, обуславливающих ее пригодность удовлетворять определенные потребности в соответствии с ее назначением.
В понятие качества входят
1.Эксплуатационные показатели машин.
2.Экономические показатели машин.
3.Технологичность машин.
1. Эксплуатационные показатели машин:
A.Технический уровень машин (соответствие лучшим мировым образцам).
B.Надежность машины (свойство изделия сохранять свою работоспособность характеризуется безотказностью, долговечностью, ремонтопригодностью).
Эстетические показатели (цвет, дизайн).
D.Эргономические показатели (удобство управления)
2. Экономические показатели
A.Трудоемкость. Затраты рабочего времени на изготовления единицы продукции или на выполнения определенной работы
(мин).
B.Себестоимость. Затраты на потребленные средства производства и на оплату труда.
C.Капитальные вложения. Вклад инвестиций в воспроизводство основных фондов.
3. Технические показатели
Показатели назначения (функциональные требования). Характеризуют способность продукции эффективно выполнять свою функцию. Их можно разделить на следующие группы:
требования производительности. Включают показатели необходимой мощности, грузоподъемности, развиваемой скорости и другие, которые характеризуют выполняемую функцию; требования эффективности. Характеризуют степень эффективности использования изделия по назначению, например,
показатели энергетические (КПД, потери), кинематические (точность перемещения), силовые (стабильность нагрузки) и т. п.;
4. Показатели надёжности.
Состоят из сочетаний следующих свойств: безотказности; долговечности; ремонтопригодности; сохраняемости;
Вопрос 2. Пути повышения производительности МРС при конструировании.
1.увеличение технологической производительности: V, S, t, применение СОТС и прогрессивных материалов режущих инструментов.
2.совмещение рабочих и вспомогательных переходов по времени - применение многошпиндельных станков, станков для непрерывной обработки (с круглыми столами).
3.сокращение времени на вспомогательное движение: увеличение скорости холостых ходов, но могут возникнуть динамические нагрузки (возникают инерционные силы).
4.автоматизация смены инструмента.
5.повышение надёжности станка за счёт снижения числа отказов.
Вопрос 3. Основные части протяжки для обработки внутренних поверхностей и их назначение.

Вопрос 4. Коэффициент надежности (запаса) закрепления, его расчет.
Вопрос 5. Методы расчета размерных цепей.
Размерная цепь - совокупность размеров, образующих замкнутый контур и участвующих в решении поставленной задачи. 1. Метод расчета размерных цепей обеспечивающих полную взаимозаменяемость - способ равных полей допусков (применяется для размеров входящих в один интервал.)
При подборе допусков необходимо использовать стандартные поля допусков, этот способ прост, но недостаточно точен, так как корректировка допусков составляющих звеньев произвольна. Можно использовать для предварительных расчетов.
- способ допусков одного квалитета. Предполагается, что все размеры между собой выполнены по одному квалитету.
Расчет размерных цепей методом полной взаимозаменяемости может оказаться экономически целесообразным лишь для машин не высокой точности 2. Метод расчета размерных цепей при неполной взаимозаменяемости
-метод регулирования. Под методом регулировки понимают такой расчет размерных цепей, при котором назначенная точность замыкающего звена достигается преднамеренным изменением (регулированием) одного из составляющих размеров
– его называют компенсирующим.
-метод пригонки. При этом методе заданная точность исходного размера достигается дополнительной обработкой при сборке деталей по заранее намеченным составляющим размеров цепи. Чтобы пригонка осуществлялась за счет предварительно выбранного размера необходимо по этому размеру оставлять припуск на пригонку.
-метод групповой взаимозаменяемости Сущность этого метода заключается в изготовлении деталей со сравнительно широкими технологически выполнимыми допусками, в сортировки деталей на равные числа групп с более узкими групповыми допусками и сборки по одноименным группам.
Вопрос 6. Перечислите основные типы подшипников и области их применения.
Подшипник — изделие, являющееся частью опоры или упора, которое поддерживает вал, ось или иную подвижную конструкцию с заданной жёсткостью. Фиксирует положение в пространстве, обеспечивает вращение, качение или линейное перемещение с наименьшим сопротивлением, воспринимает и передаёт нагрузку от подвижного узла на другие части конструкции.
В зависимости от принципа действия подшипники делят на два основных вида: подшипники качения и подшипники скольжения (шарнирные). В первом случае в качестве основного узла, уменьшающего трение выступают тела качения (шарики или ролики). Во втором случае тела качения отсутствуют и трение уменьшается за счет гладких, как правило смазываемых поверхностях.
Классификация подшипников качения осуществляется на основе следующих признаков: 1. По виду тел качения
-Шариковые,
-Роликовые (игольчатые, если ролики тонкие и длинные); 2. По типу воспринимаемой нагрузки
-Радиальные (нагрузка вдоль оси вала не допускается).
-Радиально-упорные, упорно-радиальные. Воспринимают нагрузки как вдоль, так и поперек оси вала.
-Упорные (нагрузка поперек оси вала не допускается).
-Линейные. Обеспечивают подвижность вдоль оси, вращение вокруг оси не нормируется или невозможно. Встречаются рельсовые, телескопические или вальные линейные подшипники.
-Шариковые винтовые передачи. Обеспечивают сопряжение винт-гайка через тела качения.
3.По числу рядов тел качения - Однорядные, - Двухрядные, - Многорядные;
4.По способности компенсировать несоосность вала и втулки - Самоустанавливающиеся.
- Несамоустанавливающиеся.
Подшипники скольжения разделяют:
1.в зависимости от формы подшипникового отверстия: - одно или многоповерхностные,
- со смещением поверхностей (по направлению вращения) или без (для сохранения возможности обратного вращения), - со смещением или без смещения центра (для конечной установки валов после монтажа);
2.по направлению восприятия нагрузки:
-радиальные
-осевые (упорные, подпятники),
-радиально-упорные;
3. по конструкции:
-неразъемные (втулочные; в основном, для I-1),
-разъемные (состоящие из корпуса и крышки; в основном, для всех),
-встроенные (рамовые, составляющие одно целое с картером, рамой или станиной машины); 4. по количеству масляных клапанов:
-с одним клапаном,
-с несколькими клапанами;
5.по возможности регулирования: - нерегулируемые, - регулируемые.
6.По виду трения:
-сухого трения
-полусухого трения
-жидкостного трения
Билет 14
Вопрос 1. Способы обработки поверхностно-пластическим деформированием и их характеристики.
Повышение качества инструмента при механическом упрочнении обеспечивается за счет геометрических (округление кромок, округление вершин, шероховатость кромок, высота микронеровностей поверхности, анизотропия и форма микрорельефа) и физических факторов(удаление тонких дефектных поверхностных слоев, повышение плотности дислокации и вакансий, создание мелкоблочной структуры, релаксация напряжений, аллотропические превращения,
дисперсионное твердение). При этом увеличивается запасенная энергия поверхностного слоя, сглаживаются или «залечиваются» технологические концентраторы напряжений.
1.Обкатывание и раскатывание роликами или шариками.
Шарики и ролики из сталей ШХ15, ХВГ, 9Х (твердость 62…65 HRC) V=30…150 м/мин, S=0,2…0,6 мм/об, СОЖ – машинное масло, сульфофрезол (5% эмульсия), чугун – без охлаждения. Повышает твердость на 20 – 50%, износостойкость в 1,5 – 2 раза, усталостную прочность до 2 раз. Шероховатость Ra0,2…0,8 мкм (при исходной шероховатости Ra0,8…6,3).
2.Калибрование отверстий (дорнование, деформирующее протягивание) Чистовая операция обработки отверстии деталей машин пластическим деформированием. Основной параметр – натяг: i=dин-dо, где dо – диаметр отв.до обработки (i<0,5 мм). V=2–25м/мин. При l/d≤7 – метод прошивания (а и б), а при l/d>7 – метод протягивания (в-д).Инструмент – ВК15, ВК15М. Повышается точность размера на 30-35 %, уменьшается шероховатость.
3.Алмазное выглаживание. Алмаз, прижимается с определенной силой к обрабатываемой поверхности.
Инструмент: наконечник с алмазом и державка, алмаз анизотропен, поэтому при креплении алмаза его ориентируют по риске, которую наносят на корпусе наконечника в направлении
скорости. V=50-150м/мин, S=0,05-1 мм/об, Р=100-400Н. Шероховатость уменьшается в несколько раз (Ra0,1…0,05мкм), микротвердость увеличивается на 5-60%, глубина наклепа до 0,4 мм, возникают напряжения сжатия. Высокая изностойкость и усталостная прочность.
4.Вибронакатывание (ВН) Процесс обработки плоских, цилиндрических, сферических поверхностей деталей шариком, алмазным индентором при наличии дополнительного осциллирующего движения. Позволяет сглаживать шероховатость (а), образовывать систему канавок (б), новый микрорельеф (в), регулярную волнистость (г).
Оборудование – токарные, вертикально-фрезерные станки. Р=100…800Н, i=nдв.х./nд – определяет форму неровностей. Гильзы цилиндров двигателя, прецизионные направляющие, подшипники скольжения, направляющие станин, шейки валов под манжетные направляющие, утюги.
5.Обработка дробью (ОД). Воздействие дроби на обрабатываемую поверхность. Используется для упрочнения деталей, сложной формы и малой жесткости: зубьев шестерен, листовых рессор, пружин, лопаток турбин.
Скорость подачи дроби – 1…100м/с, давление воздуха 0,1…0,5МПа Повышение твердости на 20-30%, глубины наклепа до
0,5-1мм.
6.Виброударная обработка (ВиУО) Метод, осуществляемый соударением частицобрабатывающей среды (в виде стальных закаленных шаров, роликов, абразивной среды) с поверхностью обрабатываемых деталей, помещенных в вибрирующую рабочую камеру. Полированные шары из ШХ15O1…16мм.Для тонкой отделки прим.шарики из высококачественного стекла. Уменьшение шероховатости до Ra0,2.Повышение микротвердости на 20…60% , долговечности в 3-10 раз, сопротивления усталости на 15…70%.
7.Ударно-импульсная обработка (УИО) ППД при возвратно-поступательном движении инструмента перпендикулярно обрабатываемой поверхности.
8.Ультразвуковая обработка (УЗО) Ультразвуковая обработка(УЗО)К инструменту (шарику, ролику, алмазному выглаживателю),установленному в концентраторе, наряду с силой прижима к поверхности, сообщают ультразвуковые колебания, создаваемые генератором. Прим. для чистовой обработки термообработанных сталей, инструментов из твердых сталей, деталей малой жесткости. Р=30…300Н, А=5…30 мкм, f=18…24 кГц На поверхности детали формируются маслоемкий микрорельеф, повышающий износостойкость.
Вопрос 2. Основное назначение многоцелевых станков.
Предназначены для комплексной обработки заготовки на одной рабочей позиции последовательно с разных сторон. Смена инструментов производится автоматически. Станки оснащаются комбинированными СЧПУ. Отличаются от ранее рассмотренных станков наличием инструментального магазина, который может быть расположен на станке или рядом. Широко применяются дисковые, барабанные и цепные магазины. Инструмент располагают в гнездах магазина предварительно настроенных на размер.
Многоцелевые станки отличаются особо высокой концентрацией обработки. На них производят черновую, получистовую и чистовую обработку сложных корпусных заготовок, содержащих десятки обрабатываемых поверхностей, выполняют самые разнообразные технологические переходы: фрезерование плоскостей, уступов, канавок, окон, колодцев; сверление, зенкерование, развертывание, растачивание гладких и ступенчатых отверстий; растачивание отверстий инструмента с тонким регулированием на размер; обработку наружных и внутренних поверхностей и др. Для осуществления этих операций на станке необходимо иметь большой запас металлорежущих инструментов. У станков с ЧПУ и автоматической сменой инструмента запас инструментов создается обычно в револьверных головках.
Вопрос 3. Перечислите основные виды фрез и укажите область их применения. 1 Цилиндрические фрезы – для обработки плоскостей 2 Концевые фрезы – для обработки уступов, пазов, окон, колодцев, плоскостей
3 Шпоночные фрезы – для фрезерования шпоночных пазов.
4Пазовые и дисковые фрезы бывают 2-х и 3-х сторонние. Для обработки мерных пазов
5Угловые фрезы – обработка фасок, наклонных плоскостей, для фрезерования ласточкина хвоста.
6Торцовые фрезы – для обработки плоскостей
7Отрезные фрезы – для разрезки заготовок различного профиля
8Червячные – для обработки зубчатых колес и шлицевых валов
9Плунжерные фрезы – для обработки полостей с осевой подачей
10Фасонные фрезы для обработки поверхности с прямолинейной направляющей, тела вращения
11Наборы фрез – для обработки сложных фасонных профилей
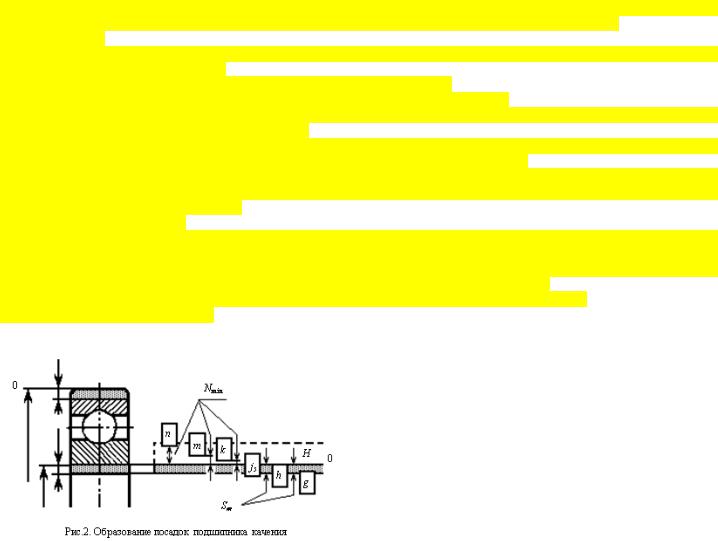
Вопрос 4. Методы измерения температуры при резании металлов. Естественные и искусственные термопары, преимущества и недостатки.
Калориметрический метод заключается в том, что стружка собирается в калориметре с водой. Зная количество воды в калориметре, вес стружки и ее теплоемкость, можно определить среднюю температуру стружки по разности температуры воды в калориметре до, и после резания.
Температуру поверхности инструмента за пределами зоны его контакта с обрабатываемым изделием или стружкой можно определить с помощью термочувствительных красок, которые изменяют свой цвет при нагревании до определенной температуры.
Металлографический метод. Данный метод основан на изменении свойств инструментального материала (например, микротвердости) под воздействием температуры. Метод требует разрушения инструмента – инструмент разрезают по главной секущей плоскости, изготавливают шлифы и измеряют микротвердость. Далее по тарировочному графику определяют температуру.
Бесконтактный (оптический) метод – используются тепловизоры – приборы, фиксирующие инфракрасное излучение от нагретых тел Пневматический – через отверстие в нагретом теле (например, резце) пропускают поток воздуха. Из-за изменения
температуры меняется вязкость и перепад давления. По изменению перепада давления судят о температуре.
Метод термопар.
Заключается в том, что в спаянных между собой разнородных проводниках при нагреве одного спая возникает ЭДС, по величине которой судят о температуре.
Естественная термопара – один электрод – инструмент, а второй – заготовка. Достоинства – позволяет определять среднюю температуру в зоне резания, не требуется.
Недостатки: необходимость тарировки, малые значения термоЭДС, непостоянство контакта, наводки в цепи термопары от станка и другого оборудования, нужны токосъемники Полуискусственной называется термопара, один из элементов которой естественно присутствует в процессе резания, а
другой искусственно вводится или в инструмент или заготовку для измерения температуры.
Преимущества – можно получать температурные поля в режущем клине инструмента, определять локальные и контактные температуры (температуры на передней и задней поверхностях), полуискусственную термопару можно использовать для измерения температуры при шлифовании.
Недостатки – требует тарировки Искусственной называется термопара, у которой оба элемента искусственно вводятся в инструмент или заготовку для
измерения температуры. Для измерения температуры, например, при токарной обработке, в корпусе резца сделано отверстие, в которое вставлена термопара, подключенная к показывающему прибору. Спай термопары регистрирует температуру в режущем клине инструмента на некотором расстоянии от передней поверхности.
Преимущества – термопара обычно протарирована при ее изготовлении, большие значения термоЭДС Недостатки – сложность встраивания
Вопрос 5. Система допусков и посадок подшипников качения. Обозначение на чертежах.
Подшипники качения являются наиболее распространенными
стандартными узлами. |
|
|
|
Точность |
подшипников |
определяется:- |
точностью |
присоединительных размеров d, D, B для радиально-упорных подшипников, точностью монтажной высоты T- точностью формы и взаимного расположения поверхностей колец и их шероховатостью - точностью формы и размеров тел качения и
их шероховатостью поверхности- |
точностью |
вращения |
характеризующуюся радиальным и осевым биением |
5 |
классов точности подшипников - Р0 , Р6 , Р5 , Р4 , Р2 Посадку выбирают в зависимости от типа и размера
подшипника, условий его эксплуатации, величины и характера действующих нагрузок и вида нагружения колец.
Различают 3 вида нагружения колец:
-местное – кольцо воспринимает постоянную нагрузку Fr одним и тем же ограниченным участком окружности дорожки качения и передает ее соответствующему участку посадочной поверхности вала или корпуса
-циркуляционное – кольцо воспринимает результирующую радиальную нагрузку Fr последовательно всей окружностью дорожки качения и передает ее также последовательно всей посадочной поверхности вала или корпуса
-колебательное – не вращающееся кольцо воспринимает равнодействующую Fr+с двух радиальных нагрузок (Fr - постоянная по направлению, Fс - меньшая по величине вращения) ограниченным участком дорожки качения и передает соответствующему ограниченному участку посадочной поверхности вала или корпуса. Посадки нужно выбирать так, чтобы вращающееся кольцо подшипника было смонтировано с натягом, а другое кольцо с зазором. При такой посадки устраняется заклинивание тел качения. В подшипниках качения различают исходный, монтажный и рабочий зазор. При расчете посадок подшипников работающих в условиях повышенных температур необходимо учитывать неравномерный нагрев внутреннего кольца подшипника и вала и выбирать посадку с натягом тем больше, чем выше рабочая температура. Класс точности подшипника выбирается исходя из требований, предъявляемых к точности вращения и усилиям работы механизма.
Вопрос 6. Расшифровать марки конструкционных материалов: (38Х2МЮА, БрА9Ж4Н4Мц1, ВТ6, У10А).
38Х2МЮА – Конструкционная легированная сталь. Сталь содержит 0,38% углерода, 2% хрома, 1% молибдена, 1% алюминия и сталь высококачественная (буква А в конце)

БрА9Ж4Н4Мц1 бронза, 9% алюминий, 4% железо, 4% никель, 1% марганец, остальное медь
ВТ6 - Титановый деформируемый сплав, 6 – порядковый номер
У10А – Углеродистая инструментальная сталь. У – означает, что сталь углеродистая, 10 – содержание углерода в десятых долях процента (1% в этой марки), А – показывает что сталь высококачественная
Билет 15
Вопрос 1. Дать определение ГПМ, ГПС, ГАЛ, ГАУ, ГАЦ.
Гибкий производственный модуль (ГПМ) Единица технологического оборудования для производства изделий произвольной номенклатуры в установленных пределах значений их характеристик с программным управлением, автономно функционирующая, автоматически осуществляющая все функции, связанные с их изготовлением, имеющая возможность встраивания в гибкую производственную систему.
Гибкая производственная система (ГПС) Совокупность в разных сочетаниях оборудования с ЧПУ, роботизированных технологических комплексов, гибких производственных модулей, отдельных единиц технологического оборудования и систем обеспечения их функционирования в автоматическом режиме в течение указанного интервала времени, обладающая свойством автоматизированной переналадки при производстве изделий произвольной номенклатуры в установленных пределах значений их характеристик.
Гибкая автоматизированная линия (ГАЛ) Гибкая производственная система, в которой технологическое оборудование расположено в принятой последовательности технологических операций.
Гибкий автоматизированный участок (ГАУ) Гибкая производственная система, функционирующая по технологическому маршруту, в котором предусмотрена возможность изменения последовательности использования технологического оборудования.
Гибкий автоматизированный цех (ГАЦ) Гибкая производственная система, представляющая собой в различных сочетаниях совокупность гибких автоматизированных линий, роботизированных технологических комплексов, гибких автоматизированных участков, роботизированных технологических участков для изготовления изделий заданной номенклатуры.
Вопрос 2. Узлы для компоновки агрегатных станков.
Агрегатными называют многоинструментальные станки, скомпонованные из нормализованных и частично специальных агрегатов. Эти станки применяются в крупносерийном и массовом производстве. На агрегатных станках можно выполнять сверление, рассверливание, зенкерование, растачивание, фрезерование, нарезание внутренних и наружных резьб, некоторые виды токарной обработки. Агрегатные станки в основном используются для изготовления корпусных деталей.
Преимущества агрегатных станков:
1)короткие сроки проектирования;
2)простота изготовления, благодаря унификации узлов, механизмов и деталей;
3)высокая производительность, обусловленная многоинструментальной обработкой заготовок с нескольких сторон одновременно;
4)возможность многократного использования части агрегатов при смене объекта производства;
5)возможность обслуживания станков оператором низкой квалификации.
Станины. Основным несущим элементом агрегатных станков являются станины. На агрегатных станках применяются станины круглые, прямоугольные, односторонние, двусторонние, трехсторонние, средние и боковые.
Поворотные и делительные устройства. Для перемещения деталей с позиции на позицию или для поворота ее на определенный угол (деления) на агрегатных станках используют разнообразные устройства. Э обработки на нем, необходимостью в быстрой переналадке с одного числа рабочих позиций на другое и т. п.).
Конструкции поворотных и делительных устройств определяется в основном их целевым назначением и типом привода. В соответствии с этим устройства можно подразделить:
1.по виду движения детали — на устройства для прямолинейного и кругового перемещения детали;
2.по типу привода — на механические, пневматические, пневмогидравлические, гидравлические и гидромеханические. Инструментальные бабки. При использовании для компоновки агрегатных станков силовых столов различных типов в комплекте с ними применяют соответствующие инструментальные бабки. Они предназначены для сообщения режущим инструментам вращательного движения. При сверлении, зенкеровании, развертывании применяют сверлильные бабки, при фрезеровании — фрезерные бабки.
Гидравлические головки. При создании агрегатных станков наибольшее применение получили силовые головки с гидравлическим механизмом подач. Это объясняется их большими преимуществами по сравнению с головками других типов.
Пневматические головки. Пневматические силовые головки не получили широкого распространения, так как пневматический механизм подачи не обеспечивает достаточно равномерного движения поршня в цилиндре вследствие сжимаемости воздуха.

Пневмогидравлические головки. Комбинированные пневмогидравлические головки получили значительно большее применение в промышленности, чем пневматические. В них поршень перемещается сжатым воздухом, а скорость его перемещения регулируется маслом, вытесняемым поршнем из цилиндра.
Пневмогидравлические головки отличаются компактностью и сравнительно несложны по конструкции. Они надежно работают при наличии хорошо осушенного сжатого воздуха.
Механизмы управления. В агрегатных станках системы автоматического управления служат для воспроизведения несложных технологических циклов, выполняемых в определенной последовательности. С помощью системы управления агрегатных станков осуществляют необходимые установочные и рабочие перемещения.
Силовые головки с механическим приводом подач. Силовые головки являются основными узлами агрегатных станков и автоматических линий. Силовые головки с механическим приводом подач предназначены в основном для выполнения сверлильных, резьбонарезных и расточных операций, а при достаточной жесткости конструкции — для фрезерных работ. Для фрезерования силовые головки оснащаются специальными насадками. Силовые головки монтируются на станинах или стойках агрегатных станков параллельно, перпендикулярно или наклонно к плоскости их столов.
Вопрос 3. Дайте определение углов резца в плане. Изобразить эти углы.
Главный угол в плане φ — угол между проекцией главной режущей кромки резца на основную плоскость и направлением его подачи.
Вспомогательный угол в плане φ1 — угол между проекцией вспомогательной режущей кромки резца на основную плоскость и направлением его подачи. Влияет на чистоту обработанной поверхности. С уменьшением φ1 улучшается чистота поверхности, но возрастает сила трения.
Угол при вершине в плане ε — угол между проекциями главной и вспомогательной режущей кромкой резца на основную плоскость. Влияет на прочность резца, которая повышается с увеличением угла.
Вопрос 4. Система допусков и посадок метрических резьб. Обозначение на чертежах. Применяется для разъемного соединения деталей машин.
Главное требование - обеспечить прочность соединения и сохранить плотность стыка в процессе длительной эксплуатации
Параметры резьбы: |
|
|
1 |
Профиль резьбы |
|
2 |
Наружный диаметр резьбы D (d) - это диаметр резьбы, образующие которого проходят по вершине резьбы |
|
3 |
Средний диаметр |
D2 (d2 ) - диаметр цилиндра, образующая которого делит профиль резьбы так, что ширина впадины |
резьбы равна ширине выступа |
||
4 |
Внутренний диаметр D1 (d1 ) - диаметр цилиндра, образующая которого проходит по впадинам резьбы |
|
5 |
Шаг P / ход Pn |
P n , n – число заходов в многозаходной резьбе |
6 |
Угол профиля α , |
α 60 |
7 |
Высота исходного треугольника H |
|
8 |
Угол наклона сторон профиля β,γ |
|
9 |
Угол подъема резьбы |
10 Длина свинчивания
M12 1 LH 6H6g 30
M - метрическая резьба, диаметром 12, шаг мелкий 1 мм, LH - левая, 6H - поле допуска гайки, 6g - поле допуска болта, длиной – 30 мм Посадка в резьбовом соединении обозначается дробью, в числителе которой указывают обозначение поля допуска
внутренней резьбы, а в знаменателе - обозначение поля допуска наружной резьбы. Система допусков резьбы предусматривает: допуски диаметров резьбы; положения полей допусков диаметров резьбы; классификацию длин свинчивания; поля допусков резьбы и их выбор с учетом длин свинчивания.
Вопрос 5. Контрольные приспособления, назначения и требования, предъявляемые к ним.
Контрольные приспособления служат для определения точности деталей и узлов машин на промежуточных этапах изготовления и при окончательной приемке. Они способствуют повышению производительности труда контролеров, а также повышению качества и объективности контроля.
Контрольные приспособления бывают:
стационарные (для мелких деталей);
переносные (для крупных деталей);
одномерные (за одну установку проверяется один параметр);

многомерные (за одну установку проверяется несколько параметров);
пассивные, которые используют для контроля после обработки детали;
активные, которые установлены на станке и контролируют деталь в процессе обработки, давая сигнал на органы станка или рабочему на прекращение обработки или изменение условий ее проведения. Они часто являются составной частью станка. Наиболее широкое использование приборы активного контроля
получили на станках, выполняющих финишные операции.
Основные требования, предъявляемые к контрольным приспособлениям, определяются необходимостью обеспечения: а) точности и производительности контроля; б) удобства эксплуатации;
в) технологичности изготовления и износостойкости; г) экономической целесообразности.
Вопрос 6. Приведите примеры типичных деталей, штампуемых на ГКМ. Их отличие от штамповок, получаемых на прессах.
Штамповкой на ГКМ в открытых и закрытых штампах из круглого прутка получают поковки типа стержня с утолщениями, колец, втулок, гильз, стаканов, подпятников с г лухой полостью; полые длинные изделия высаживают из труб. Штамповку на ГКМ в наборных ручьях выполняют с учетом основных правил высадки, исключающих возникновение продольного изгиба высаживаемой части прутка и брак по зажимам.
Особенностью штамповки на горизонтально-ковочных машинах (ГКМ) является наличие двух разъемов в штампе. В отличие от молотов и прессов на ГКМ штампуют менее разнообразные поковки. Однако благодаря разъему штампа в двух плоскостях, представляется возможным наряду с традиционными типами поковок (стержни с утолщениями, кольца, стаканы и др.) вести штамповку деталей типа тройников, т.е. с элементами поперечного выдавливания.
Билет 16
Вопрос 1. Последовательность построения технологической операции.
1 Исходные данные (маршрут обработки заготовки, схема установки и закрепления заготовки, припуски на обработку)
1.Маршрут обработки заготовки.
2.Схема установки и закрепления заготовки.
3.Общие припуски на обработку.
2 Уточнение содержания операции
1.В тяжелом машиностроении:
Целесообразны сложные многопереходные операции без специальных приспособления с установкой по выверке. Оборудование с широкими технологическими возможностями.
Применение переносных станков.
2.На автоматических линиях:
Параллельно - последовательная схема (заготовка подается с одной позиции на другую последовательно, на каждой позиции обрабатывается несколькими инструментами, обрабатываются разные поверхности).
Необходимо решать задачи по транспортировке заготовок. Контроль в автоматическом режиме.
3.На станках с ЧПУ:
Построение операций в два этапа: технологическая подготовка, программирование. Технологическая подготовка: