
Для пдф госы
.pdf
вычерчивание траектории движения режущих инструментов; расчет припусков и режимов резания; выбор режущих инструментов и приспособлений. Программирование:
кодирование программы. На многоцелевых станках:
Применение многоинструментальных последовательных схем обработки. Применение приспособлений спутников toдо 80% от tшт.
3 Определение последовательности и возможности переходов во времени
4 Окончательный выбор средств технологического оснащения
Выбор станка
1.Тип станка задается методом обработки.
2.Основные размеры станка определяются размерами заготовки и обрабатываемой поверхности.
3.Модель станка определяется степенью концентрации технологических переходов; точностью обрабатываемой поверхности; производительностью, необходимой мощностью и т.д.
4.После выбора станка необходимо получить сведения о его основных характеристиках:
а) мощность привода главного движения; б) КПД станка; в) ряд чисел оборотов шпинделя (полный);
г) ряд продольных и поперечных подач; д) высота центров (токарные станки);
е) размеры стола (фрезерные станки), характеристики Т-образных пазов; ж) наибольший диаметр обрабатываемого прутка (токарно-револьверные станки). Выбор режущего инструмента
1.Тип определяется методом обработки.
2.Размеры РИ определяются межоперационным размерам. Выбор измерительного инструмента
1.В зависимости от типа производства,
2.Вида измеряемой поверхности
3.Требуемой точности поверхности.
Единичное производство: линейки, штангенциркули, микрометры, нутромеры и глубиномеры и т. д.Серийное и массовое производство: специальный измерительный инструмент - калибры, шаблоны и т.д.
5 Назначение режимов резания
Режимы резания назначают на все операции по всем переходам.
6 Определение норм основного технологического времени
Определение норм основного (технологического) времени Основное (технологическое) время – это время, в течение которого производится снятие стружки, т.е. происходит изменение формы, размеров и внешнего вида заготовки.
7 Составление схемы наладок на операции
Вопрос 2. Основные виды тяговых устройств МРС.
Тяговые устройства предназначены для перемещения рабочих органов по направляющим станка, они обычно являются конечными звеньями механизмов подач и реже вспомогательных устройств.
Виды:
1 Механические
- с постоянной скоростью передачи (винт–гайка, шарико-винтовые передачи, червяк-рейка, шестерня–рейка) обеспечивают высокую точность перемещения рабочего органа - с переменной скоростью передачи (кулачковые, кривошипно-шатунные, рычажно-шарнирные).
2 Электромагнитные
-линейный развернутый электродвигатель
-бесконтактная электромагнитная подача
3 Гидравлический - гидроцилиндр или гидромотор Выбор тягового устройства зависит от необходимой величины тяговых усилий, от требований закона перемещения по
скорости или по траектории, требований точности рабочего органа.
Вопрос 3. Конструкция сверла одностороннего резания. Область применения данного инструмента.

Используются для получения точных отверстий малого диаметра с прямолинейной осью (до 20мм), глубиной до 100 диаметров. Сверла одностороннего резания с внутренним подводом СОЖ состоят из твердосплавной режущей части (колоска), припаянной к трубчатой
хвостовой части (стеблю) V-образного сечения, соединенного с переходной втулкой для закрепления на станке
Вопрос 4. Влияние режимов резания и геометрии инструмента на шероховатость обработанной поверхности.
Наибольшее влияние на шероховатость обработанной поверхности оказывают подача, износ инструмента по задней поверхности и скорость резания. Глубина резания в меньшей степени влияет на шероховатость.
Увеличение подачи будет способствовать увеличению шероховатости обработанной поверхности как геометрический фактор процесса резания. Износ инструмента по задней поверхности несколько снижает ее, т.к. при этом за счет возрастания площади контакта инструмента с обрабатываемой поверхностью происходит не только формообразование, но и выглаживание формируемой поверхности. Скорость резания оказывает меньшее влияние на величину шероховатости, а глубина резания фактически на нее не влияет. С увеличением скорости шероховатость уменьшается, однако в области малых скоростей резания шероховатость увеличивается вследствие явления наростообразования Шероховатость увеличивается при увеличении подачи и увеличении главного угла в плане и вспомогательного угла в плане
Вопрос 5. Структура процесса проектирования: иерархические уровни, аспекты описания, стадии проектирования Основная цель разбиения на иерархические уровни – информация, обрабатываемая САПР должна быть обозрима и воспринимаема одним человеком.
-системный уровень, на котором решают наиболее общие задачи проектирования систем, машин и процессов; результаты проектирования представляют в виде структурных схем, генеральных планов, схем размещения оборудования, диаграмм потоков данных и т.п.;
-макроуровень, на котором проектируют отдельные устройства, узлы машин и приборов; результаты представляют в виде функциональных, принципиальных и кинематических схем, сборочных чертежей и т.п.;
-микроуровень, на котором проектируют отдельные детали и элементы машин и приборов.
Помимо разбиения на иерархические уровни применяется разбиение на аспекты описания.
Аспект описания (страта) – описание системы или ее части с некоторой оговоренной точки зрения, определяемой функциональными, физическими или иного типа отношениями между свойствами и элементами.
Стадия проектирования – законченная часть процесса проектирования, в результате которой появляется новое промежуточное или окончательное описание ОП.
1. Технического предложения.
Эти три стадии являются научно-исследовательской работой, здесь определяют назначение, основные принципы ОП и формулируют техническое задание на основании изучения потребности общества, научно-технических достижений, имеющихся ресурсов и т.д.

2. Эскизного проекта, здесь проверяется корректность и реализуемость основных принципов и положений, определяющих функционирование объекта.
3. Технического проекта, здесь выполняется проработка всех частей проекта конкретизируются и детализируются технические решения.
4. Рабочего проекта, здесь формируется вся необходимая документация для изготовления изделия, затем создается и испытывается опытный образец и происходит внедрение.
Вопрос 6. Перечислите виды резьб и их назначение.
Резьба — равномерно расположенные выступы или впадины постоянного сечения, образованные на цилиндрической или конической поверхности по винтовой линии с постоянным шагом.
Резьбы классифицируются по нескольким признакам:
1. В зависимости от формы профиля – треугольные, трапецеидальные, прямоугольные, круглые. 2. По форме поверхности, на которой нарезана резьба – конические и цилиндрические.
3.По расположению на поверхности стержня или отверстия
– наружные (на стержне)
– внутренние (в отверстии)
4.По направлению нарезки – правые и левые.
5.По назначению
–крепёжные (метрические, дюймовые);
–крепёжно-уплотнительные (трубные, конические);
–ходовые (трапецеидальные, упорные, прямоугольные);
–санитарно-технические (круглые) и др.
6. По числу заходов – однозаходные и многозаходные (двухзаходные, трёхзаходные и т. д.).
Метрическая резьба является основным типом крепежной резьбы. Профиль резьбы представляет собой равносторонний треугольник с углом профиля α = 60°.
Дюймовая резьба. В настоящее время не существует стандарт, регламентирующий основные размеры дюймовой резьбы. Дюймовая резьба применяется при ремонте оборудования, поскольку в эксплуатации находятся детали с дюймовой резьбой. Трубная цилиндрическая резьба. Профиль трубной резьбы - равнобедренный треугольник с углом при вершине, равным 55 град. Трубную резьбу применяют для соединения труб, а также тонкостенных деталей цилиндрической формы.
Трубная коническая резьба. Применяется резьба для резьбовых соединений топливных, масляных, водяных и воздушных трубопроводов машин и станков.
Трапецеидальная резьба имеет форму равнобокой трапеции с углом между боковыми сторонами, равным 30° Трапецеидальная резьба применяется для преобразования вращательного движения в поступательное при значительных нагрузках и может быть одно- и многозаходной (ГОСТ 24738–81 и 24739–81), а также правой и левой.
Упорная резьба стандартизованная ГОСТ 24737–81, имеет профиль неравнобокой трапеции, одна из сторон которой наклонена к вертикали под углом 3°, т. е. рабочая сторона профиля, а другая – под углом 30°. Применяется при больших односторонних усилиях, действующих в осевом направлении.
Круглая резьба стандартизована. Профиль круглой резьбы образован дугами, связанными между собой участками прямой линии. Угол между сторонами профиля α = 30°. Резьба применяется ограниченно: для водопроводной арматуры, в отдельных случаях для крюков подъемных кранов, а также в условиях воздействия агрессивной среды.
Прямоугольная резьба не стандартизована, так как наряду с преимуществами, заключающимися в более высоком коэффициенте полезного действия, чем у трапецеидальной резьбы, она менее прочна и сложнее в производстве. Применяется при изготовлении винтов, домкратов и ходовых винтов.
Билет 17
Вопрос 1. Дать определение технологической подготовки производства. Ее задачи.
Технологическая подготовка производства - совокупность мероприятий обеспечивающих технологическую готовность производства (наличие на предприятии полных комплектов конструкторской и технологической документации и СТО, необходимых для изготовления заданного кол-ва изделий, c необходимыми технико-экономическими показателями)
Задачи ТПП
1 Обеспечение технологичности изделия
2 Разработка техпроцесса 3 Проектирование и изготовление СТО (станки, приспособления, вспомогательный, мерительный и режущий инструмент).
4 Организация и управление ТПП.
Задачей ТПП является обеспечение полной технологической готовности фирмы к производству новых изделий с заданными технико-экономическими показателями (высоким техническим уровнем, качеством изготовления, а также с минимальными трудовыми и материальными издержками при конкретном техническом уровне предприятия и планируемых объемах производства).
В процессе ТПП решаются следующие основные задачи:
–отработка изделия на технологичность;
–разработка технологических маршрутов и процессов;
–разработка специальной технологической оснастки;
–технологическое оснащение производства;
–техническое сопровождение изготовления опытной партии, установочной серии и установившегося серийного производства.
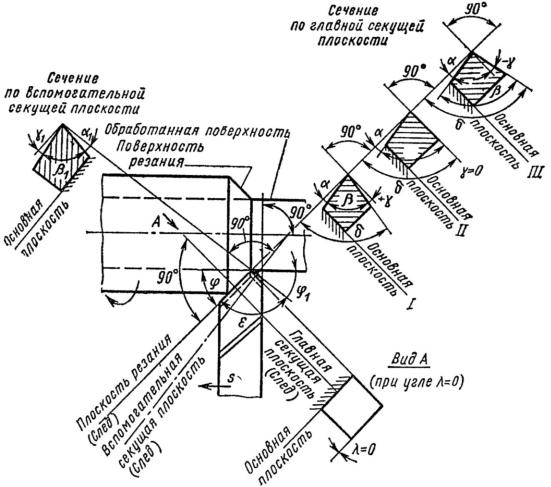
Вопрос 2. Дайте определение углов резца в главной и вспомогательной секущей плоскостях. Изобразить эти углы Главная секущая плоскость – плоскость, перпендикулярная линии пересечения основной плоскости и плоскости резания (перпендикулярная проекции главной режущей кромки на основную плоскость).
Вспомогательная секущая плоскость – плоскость, перпендикулярная проекции вспомогательной режущей кромки на основную плоскость.
Главный передний угол γ — угол между передней поверхностью резца и плоскостью, перпендикулярной плоскости резания, проведённой через главную режущую кромку. Служит для уменьшения деформации срезаемого слоя. С увеличением переднего угла облегчается врезание резца в металл, уменьшается сила резания и расход мощности. Резцы с отрицательным γ применяют для обдирочных работ с ударной нагрузкой. Преимущество таких резцов на обдирочных работах заключается в том, что удары воспринимаются не режущей кромкой, а всей передней поверхностью.
Главный задний угол α — угол между главной задней поверхностью резца и плоскостью резания. Служит для уменьшения трения между задней поверхностью резца и деталью. С увеличением заднего угла шероховатость обработанной поверхности уменьшается, но при большом заднем угле резец может сломаться. Следовательно чем мягче металл, тем больше должен быть угол.
Угол заострения β — угол между передней и главной задней поверхностью резца. Влияет на прочность резца, которая повышается с увеличением угла.
Угол резания δ=α+β.
Вспомогательные углы измеряются во вспомогательной секущей плоскости.
Вспомогательный задний угол α1 — угол между вспомогательной задней поверхностью резца и плоскостью, проходящей через его вспомогательную режущую кромку перпендикулярно основной плоскости.
Вспомогательный передний угол γ1 — угол между передней поверхностью резца и плоскостью, перпендикулярной плоскости резания, проведённой через вспомогательную режущую кромку Вспомогательный угол заострения β1 — угол между передней и вспомогательной задней плоскостью резца.
Вспомогательный угол резания δ1=α1+β1.
Углы в плане измеряются в основной плоскости. Сумма углов φ+φ1+ε=180°.
Главный угол в плане φ — угол между проекцией главной режущей кромки резца на основную плоскость и направлением его подачи. Влияет на стойкость резца и скорость резания. Чем меньше φ, тем выше его стойкость и допускаемая скорость резания. Однако при этом возрастает радиальная сила резания, что может привести к нежелательным вибрациям.
Вспомогательный угол в плане φ1 — угол между проекцией вспомогательной режущей кромки резца на основную плоскость и направлением его подачи. Влияет на чистоту обработанной поверхности. С уменьшением φ1 улучшается чистота поверхности, но возрастает сила трения.
Угол при вершине в плане ε — угол между проекциями главной и вспомогательной режущей кромкой резца на основную плоскость. Влияет на прочность резца, которая повышается с увеличением угла.
Угол наклона главной режущей кромки измеряется в плоскости, проходящей через главную режущую кромку перпендикулярно к основной плоскости.

Угол наклона главной режущей кромки λ — угол между главной режущей кромкой и плоскостью, проведенной через вершину резца параллельно основной плоскости. Влияет на направление схода стружки.
Вспомогательный угол – те же определения, только вместо «в статической главной секущей плоскости» поменять на «в статической вспомогательной секущей плоскости»
Вопрос 3. Самоторможение зажимных механизмов станочных приспособлений. Винтовые зажимы
Винтовые зажимы применяют в приспособлениях с ручным закреплением заготовки, в приспособлениях механизированного типа, а также на автоматических линиях при использовании приспособлений-спутников. Они просты, компактны и надежны в работе.
Условие самоторможения: |
Для стандартных метрических резьб |
поэтому все механизмы с |
метрической резьбой самотормозящие. Клиновые зажимы
Клин применяется в следующих конструктивных вариантах:
1.Плоский односкосый клин.
2.Двускосый клин.
3.Круглый клин.
4) кривошипный клин в форме эксцентрика или плоского кулачка с рабочим профилем, очерченным по архимедовой спирали;
Рис. 3.5. Кривошипный клин: а – в форме эксцентрика; б) – в форме плоского кулачка.
5)винтовой клин в форме торцевого кулачка. Здесь односкосый клин как бы свернут в цилиндр: основание клина образует опору, а его наклонная плоскость - винтовой профиль кулачка;
6)в самоцентрирующих клиновых механизмах (патроны, оправки) не пользуются системы из трех и более клиньев.
где: - угол трения.
где: –коэффициент трения; то ; .
Для клина с трением только по наклонной поверхности условие самоторможение:
с трением на двух поверхностях:
Имеем: ;
или :
;
.

Тогда: условие самоторможение для клина с трением на двух поверхностях:
для клина с трением только на наклонной поверхности:
Эксцентриковые зажимы
Такие зажимы являются быстродействующими, но развивают меньшую силу, чем винтовые. Обладают свойством самоторможения. Основной недостаток: не могут надежно работать при значительных колебаниях размеров между установочной и зажимаемой поверхностью обрабатываемых деталей.
Условие самоторможения эксцентрика:
Круглые эксцентрики представляют собой Диск или валик с осью вращения, смещенной на размер эксцентриситета е; условие самоторможения обеспечивается при соотношении
Вопрос 4. Понятие о сертификации. Цели и принципы. Органы по сертификации.
Сертификация - это процедура подтверждения соответствия результата производственной деятельности, товара, услуги нормативным требованиям, посредством которой третья сторона документально удостоверяет, что продукция, работа (процесс) или услуга соответствует заданным требованиям.
Основными целями сертификации являются:
•создание условий для деятельности организаций и предпринимателей на едином товарном рынке Российской Федерации, а также для участия в международном экономическом, научно-техническом сотрудничестве и международной торговле;
•содействие потребителям в компетентном выборе продукции;
•содействие экспорту и повышение конкурентоспособности продукции;
•защита потребителя от недобросовестности изготовителя (продавца, исполнителя);
•контроль безопасности продукции для окружающей среды, жизни, здоровья и имущества;
•подтверждение показателей качества продукции, заявленных изготовителем.
Сертификация в России осуществляется на следующих принципах:
•добровольность;
•бездискриминационный доступ к участию в процессах сертификации;
•объективность оценок;
•воспроизводимость результатов оценок;
•конфиденциальность;
•информативность;
•специализация органов по сертификации;
•обязательность проверки выполнения требований, предъявляемых к продукции (услуге) в законодательно регулируемой сфере;
•достоверность доказательств со стороны заявителя соответствия системы качества нормативным требованиям.
Органы по серт-и создаются на базе организаций, имеющих статус юриди-го лица и явл-ся третьей стороной. Назначение руководителей органов согласуется с ГОСТ РФ.( ВНИИС, Госстандарт и Госстрой России, Ростест, )
Вопрос 5. Стадии и этапы опытно-конструкторских разработок.
Комплекс работ по конструированию нового продукта обычно включает три относительно самостоятельные стадии ОКР: 1) подготовительную; 2) разработку проектной документации; 3) разработку рабочей документации.
– Подготовительная - обоснование необходимости создания нового продукта и согласование состава его основных технико-экономических параметров. Результаты расчетов и согласований отражаются в утверждаемом техническом задании (ТЗ) на выполнение ОКР.
– Разработка проектной документации - предусматривает выполнение комплекса работ, определяющих концептуальные решения по новому продукту. Эта стадия проектирования продукта включает выполнение трех этапов разработки
(1)технического предложения (совокупность конструкторских документов, содержащих технико-экономическое обоснование разработки необходимой документации изделия на основании анализа ТЗ, различных вариантов возможных конструкторских решений, патентных исследований и т.д.;
(2)эскизного проекта (включает документы, содержащие принципиальные конструкторские решения, которые дают представление об устройстве и принципе работы изделия, а также данные, определяющие его основные параметры и габаритные размеры;
(3)технического проекта (совокупность документов, которые должны содержать окончательные технические решения, дающие полное представление об устройстве изделия, и исходные данные для разработки рабочей документации. При необходимости изготавливаются и испытываются макеты экспериментальных образцов.
– Разработки рабочей документации - осуществляется подготовка комплекта конструкторской документации, необходимой для материального воплощения проектируемого изделия.
Вопрос 6. Перечислите виды шлицев, укажите назначение шлицевых соединений, преимущества и недостатки. Классификация шлицевых соединений:
По форме зубьев:
1.прямобочные;
2.эвольвентные;
3.треугольные.
По способу центрирования ступицы относительно вала:
1.центрирование по наружному диаметру (наиболее экономичный и простой)
2.центрирование по внутреннему диаметру (точное центрирование, высокая соосность)
3.центрирование по боковым поверхностям зубьев (для больших крутящих моментов) По характеру соединения:
1.неподвижные (для закрепления на вале),
2.подвижные (допускают перемещения детали вдоль вала)
Назначение: передача крутящего момента.
Преимущества:
1.большая нагрузочная способность (большая рабочая поверхность и равномерное давление по высоте зубьев),
2.большая усталостная прочность вала (более низкая концентрация напряжений за счет скругления в основании выступов и впадин),
3.лучшее центрирование детали на вале
4.уменьшается число деталей соединения
5.уменьшается длина ступицы.
Недостатки:
1. более сложная технология изготовления
2. более высокая стоимость
Билет 18
Вопрос 1. Понятие автоматизации и механизации производства. Стадии автоматизации производства.
Механизация - применение энергии неживой природы в производственном процессе или его составных частях полностью управляемых людьми и осуществляемая в целях сокращения трудовых затрат и улучшений условий труда.
Автоматизация - применение энергии неживой природы в производственном процессе или его составных частях для их выполнения и управления ими без непосредственного участия человека.
Автоматизация
–жесткая (при серийном и массовом производстве) станки автоматы (специальные)
агрегатные станки автоматические линии
–гибкая (единичное и мелкосерийное производство) станки с ЧПУ многооперационные станки гибкие производственные системы
Стадии автоматизации производства:
1 Частичная автоматизация - автоматизация отдельных технологических операций.
2 Комплексная автоматизация - автоматизация производственных процессов изготовления деталей и сборки изделия 3 Полная автоматизация - предусматривает полное отсутствие человека, все функции выполняют машины.
Вопрос 2. Реверсивные механизмы, применяемые в МРС.
Устройства, предназначенные для изменения направления движения исполнительных органов, называются реверсивными. Реверсирование может осуществляться:
1.электродвигателем (N до 4,5 кВт);
2.гидродвигателем;
3.цилиндрическими и коническими зубчатыми колесами (трензелями).


Вопрос 3. Преимущества и недостатки фасонных резцов. Преимущества фасонных резцов
1.Высокая производительность, благодаря значительной экономии машинного и вспомогательного времени. Экономия машинного времени достигается сокращением пути резания, экономия вспомогательного времени обеспечивается простотой установки и наладки резца при его смене
2.Высокая точность получаемых осевых и диаметральных размеров, которая определяется точностью изготовления и установки резца
3.Идентичность формы изготовляемых деталей
4.Меньшее количество брака
5.Простота заточки (заточка фасонных резцов осуществляется по переденей поверхности)
6.Высокая долговечность, которая достигается благодаря большому количеству допускаемых переточек
Основные недостатки фасонных резцов обусловлены достаточно высокой сложностью их проектирования и изготовления, высокой стоимостью и практически полным отсутствием универсальности. Фасонные резцы проектируются для обработки строго определенной поверхности конкретной детали, вследствие чего их применение экономически оправдано только в условиях крупносерийного и массового производства. Фасонные резцы требуют точной и определенной установки на станке и не обеспечивают одинаковых условий для работы различных участков режущей кромки, что приводит к ее неравномерному износу
Вопрос 4. Явление наростообразования при резании металлов. Условия возникновения и существования нароста. Влияние нароста на процесс резания.

Размеры нароста не являются стабильными и одинаковыми вдоль всей режущей кромки даже при условиях, особенно благоприятных для его образования. Вследствие сильного трения между стружкой и наростом и трения в месте контакта нароста с обработанной поверхностью и поверхностью резания частицы нароста уносятся стружкой и этими поверхностями; при этом нарост, разрушаясь частично или полностью, периодически восстанавливается за счет новых частиц металла из основной его массы. Подвергаясь действию сил в
Вопрос 5. Виды и методы измерений. Классификация видов измерений. Различают прямые, косвенные и совокупные измерения.
Прямые измерения - измерения, при которых искомое значение физической величины определяется непосредственно из опытных данных путем экспериментального сравнения. Например, определение значения тока в цепи при помощи амперметра, длину линейкой Косвенные измерения - измерения, при которых измеряется не сама физическая величина, а величина, функционально
связанная с ней. Измеряемая величина определяется на основе прямых измерений величины, функционально связанной с измеряемой, с последующим расчетом на основе известной функциональной зависимости. Например, измерение мощности постоянного тока при помощи амперметра и вольтметра с последующим расчетом мощности по известной зависимости Р =
V*I.