
Для пдф госы
.pdf
Вопрос 4. Требования, предъявляемые к зажимным устройствам станочных приспособлений.
Вопрос 5. Шероховатость поверхности. Параметры шероховатости.
Шероховатость – совокупность микронеровностей с относительно малыми шагами на базовой длине l. Высотные:
Ra – среднее арифметическое отклонение профиля Rz – высота неровностей профиля по десяти точкам
Rmax – наибольшая высота неровности профиля – это расстояние между линией выступов и линией впадин профиля в приделах базовой длины.
Шаговые
Sm– средний шаг неровностей профиля по средней линии – это среднее арифметическое значение шага неровностей профиля в приделах базовой длины.
S – средний шаг неровностей профиля по вершинам – это значение шага неровностей профиля по вершинам в приделах базовой длины.
Комплексные
tP - относительная опорная длина профиля – это отношение опорной длины профиля Р к базовой длине.
Вопрос 6. Перечислите виды шпонок, укажите назначение шпоночных соединений, преимущества и недостатки. Шпоночными соединениями называют разъёмные соединения составных частей изделий с применением шпонок. Шпоночные соединения состоят из вала, шпонки и ступицы колеса.
Типы шпонок
1)Призматические шпонки.
2)Сегментные шпонки.
3)Клиновые шпонки.
4)Цилиндрические
5)Торцовые шпонки
6) Тангенциальные шпонки

Шпоночные соединения применяют для передачи вращающего момента. Их используют при небольших нагрузках, когда соединения могут быть неподвижными или подвижными вдоль оси вала.
Достоинства шпоночных соединений
1)простота конструкции;
2)легкость сборки и разборки соединения.
3)низкая стоимость.
Недостатки шпоночных соединений
1)шпоночные пазы ослабляют вал и ступицу насаживаемой детали (уменьшается сечение детали);
2)Малая нагрузочная способность
3) Ослабление сечения валов шпиндельными пазами 4) Концентрация напряжений из-за неблагоприятной формы шпоночного паза 5) Необходимость индивидуальной пригонки
Билет 9
Вопрос 1. Транспортные устройства автоматических линий.
Устройства для перемещения деталей
В АЛ для перемещения обрабатываемых заготовок с одной рабочей позиции на другую применяют различные транспортные средства: транспортеры, механические руки, лотки, трубы и т.п. Например, для перемещения корпусных деталей, а также для деталей, закрепленных в приспособлениях-спутниках, применяются шаговые транспортеры.
Шаговые транспортеры с собачками (рис. а) получили наибольшее распространение. При работе они совершают периодическое возвратно-поступательное движение. Конструкция такого транспортера представлена на рис. а. На штанге 1, проходящей через весь сблокированный участок АЛ, шарнирно закреплены собачки 3, которые под действием пружины 2 стремятся подняться над уровнем штанги. В момент возврата транспортёра зафиксированные на позициях детали 4 утопляют собачки. Пройдя под деталями, собачки вновь поднимаются и готовы для захвата очередной детали при движении транспортёра вперёд. Преимущество транспортёра с собачками - простота движения и соответствующее ей простота привода от гидроили пневмоцилиндра.
Шаговые штанговые транспортеры с флажками (рис. б) предназначены для перемещения по направляющей приспособлений-спутников с установленными на них заготовками 3. Перемещение осуществляется штангой 1 (круглого сечения) совершающей возвратно-поступательные движения, на которой секциями закреплены флажки 2. При движении штанги вперёд, в том же направлении одновременно перемещаются заготовки 3 на одну позицию по всей линии. После этого штанга поворачивается и возвращается обратно. Поворот штанги и её осевое перемещение осуществляются двумя гидроцилиндрами.
Грейферные шаговые транспортёры (рис. в) применяются реже. У них штанга 1 совершает поочерёдно два возвратнопоступательных движения в перпендикулярных направлениях с чередованием фаз этих движений. Обрабатываемые заготовки 2 перемещаются жесткими (неповорачивающимися) флажками 3. Конструктивно такие транспортеры обычно сложны и применяются только в тех случаях, когда подход к захватываемым деталям может быть произведен лишь с определённой стороны, причем посадка транспортируемых деталей на позициях такова, что для перемещения с позиции на позицию транспортер должен поднять деталь вверх.
Рейнерные шаговые трансформаторы (рис. г) представляют собой усложненный вид грейферных. Детали 3 перемещаются не флажками, а закреплёнными на штанге 1 захватами 2, которые обычно расположены сверху. Эти транспортеры требуют сложных надстроек над линиями.
Вопрос 2. Основные виды опор шпинделей.
В качестве опор шпинделей станков применяют подшипники качения и скольжения.
Подшипники качения:
Шарикоподшипники применяют для быстроходных малонагруженных опор (шпиндели внутришлифовальных станков, небольших токарных станков и автоматов, сверлильных).
Роликовые подшипники с цилиндрическими роликами применяют при повышенных нагрузках и требованиях точности (шпиндели токарных и револьверных станков и автоматов, быстроходных фрезерных станков, тяжелых шлифовальных и резьбошлифовальных).
Конические роликовые подшипники применяют при повышенных нагрузках на шпиндель и средних частотах вращения (шпиндели многорезцовых, фрезерных и других станков).
Подшипники скольжения:
применяют в шпиндельных узлах тех станков, где подшипники качения не могут обеспечить требуемой точности и долговечности работы.
Гидродинамические подшипники применяют в станках с высокими постоянствами или мало изменяющимися скоростями вращения шпинделей при незначительных нагрузках (станки шлифовальной группы).
Вгидростатических подшипниках под давлением подается жидкость, образующая между сопрягаемыми поверхностями равномерную масляную подушку.
Ваэростатических подшипниках подается сжатый воздух, образующий воздушную подушку.
К опорам шпинделей предъявляются следующие требования:
1.Точность
2.Долговечность
3.Жесткость
4.Виброустойчивость
5.Точность опоры
Вопрос 3. Понятие обрабатываемости материалов резанием и пути ее улучшения.
Рабочий процесс обработки металлов резанием заключается в динамическом и кинематическом взаимодействии двух твердых тел – обрабатываемой заготовки и режущего инструмента.
Обрабатываемость – совокупность влияния свойств обрабатываемого материала на процесс резания. Конструкционные материалы разделяются по обрабатываемости резанием, энергоемкости:
-легкообрабатываемые – латуни, бронзы, деформируемые сплавы алюминия, мягкие чугуны;
-средней обрабатываемости – углеродистые и низколегированные конструкционные стали, силумины, чугуны средней твердости;
-ниже средней обрабатываемости – высоколегированные нержавеющие конструкционные стали мартенситного, мартенситно-ферритного, аустенитно-мартенситного классов, твердые чугуны;
-трудно обрабатываемые – высоколегированные конструкционные стали аустенитного класса, жаростойкие и кислотостойкие, специальные никелеферритовые и никелевые сплавы, тугоплавкие сплавы, закаленные стали (после термообработки, шлифовки).
К основным способам улучшения обрабатываемости относятся:
-Оптимизация химического состава материала заготовок, улучшение обрабатываемости сталей может быть достигнуто в результате увеличения содержания серы (автоматные стали) и кальция (кальцевые стали).
-Рациональный выбор материала режущей части инструмента.
-Выбор рационального типа инструмента и геометрии лезвия.
-Применение эффективных смазочно-охлаждающих технологических сред.
-Применение улучшающей термической обработки. При предварительном точении и фрезеровании высокопрочных конструкционных сталей применяют разупрочняющую термическую обработку, которая ухудшает механические характеристики материала.
-Введение в зону резания дополнительной энергии путем пластического деформирования вязких сталей и сплавов, обработки резанием с вибрациями и нагревом.
-Оптимизация режимов обработки.
-Дробление стружки.
Вопрос 4. Недостатки геометрических параметров спиральных сверл и методы их улучшения.

Спиральное сверло работает в более тяжелых условиях, чем резцы и многие другие инструменты. Так как сверло все время погружено в обрабатываемый металл, то затрудняются отвод стружки и доступ охлаждающей жидкости к лезвиям инструмента. Кроме того, сверло, вследствие своих конструктивных особенностей, имеет неблагоприятную геометрию режущих элементов.
Недостатки:
1)отрицательные передние углы на поперечном лезвии (перемычке);
2)недостаточные передние углы на участках, примыкающих к сердцевине сверла;
3)отсутствие заднего угла на направляющих ленточках.
Методы улучшения:
1)подточка перемычки,
2)двойная заточка
3)подточка направляющих ленточек.
Перемычка сверла находится в очень тяжелых условиях: не имея нужных углов, она по существу не режет, а выдавливает, скоблит металл. Естественно, что чем меньше ширина перемычки, тем легче работает сверло и тем выше его стойкость. Однако значительно уменьшить перемычку путем утонения сердцевины сверла нельзя, так как это ведет к снижению прочности последней и может вызвать поломки.
Двойная заточка заключается в образовании на заборной части сверла переходных лезвий длиной 0,2 диаметра сверла, с углом при вершине 70—75°. Благодаря этому, режущие лезвия удлиняются, толщина среза на участках, работающих с наибольшей скоростью резания, уменьшается, а отвод теплоты улучшается. Все это способствует уменьшению износа по «уголкам» сверла и повышению его стойкости.
Двойная заточка увеличивает стойкость сверл до шести раз при обработке чугуна и до трех раз при обработке стали. Особенно хорошие результаты получаются при сверлении чугунов и твердых сталей. Для сверления мягких и вязких сталей двойную заточку применять не следует, так как сильно увеличивается объем, занимаемый стружкой, что затрудняет работу сверла.
Одним из наиболее подверженных износу участков спирального сверла являются места перехода от главных режущих лезвий к направляющим ленточкам («уголки»). Так как ленточки не имеют задних углов, то здесь нередко наблюдается сильный износ сверл по диаметру, приводящий к защемлению и поломкам инструмента. Чтобы уменьшить этот недостаток геометрии сверл, рекомендуется производить подточку ленточек, которая заключается в том, что на небольшой длине ленточки (от 1,5 до 4 мм, в зависимости от диаметра сверла) снимают затылок под углом 6—8°, оставляя только узкую фаску шириной 0,2—0,4 мм. Фаска необходима для сохранения диаметра сверла на участке подточки; иначе, вследствие истирания по диаметру, сверло быстро получит «прямой» конус и будет ломаться.
Вопрос 5. Функции производственной системы. Основные, вспомогательные, специальные.
Последовательность осуществляемых действий на предприятии, связанных с производством продукции, характеризует организованность производственной системы во времени. Эти действия имеют определенные целевые установки. Однородные действия, объединенные по их назначению или роли в организации, называются внутренними функциями Основные функции процесса производства на машиностроительном предприятии реализуются основными цехами предприятия в следующей последовательности:
Заготовительная функция выполняется литейным, кузнечным цехами, участками резки металла. Обработочная реализуется в механическом, термическом, гальваническом цехах.
Сборочная – в механосборочных и сборочных цехах.
Вспомогательные функции выполняют цехи и службы предприятия, которые обеспечивают основные цехи техническими услугами (ремонт оборудования, транспортировка и складирование материалов и продукции), а также энергией (например, электроподстанция), горячей водой (котельная)
Специальные функции управления производством осуществляет заводоуправление, а также линейные руководители в цехах основного производства (начальник цеха, мастер участка). я) и инструментом (инструментальный цех).
Вопрос 6. Назовите отделочные операции при получении заготовок литьем.
- Зачистка состоит в снятии, удалении пригоревшей формовочной и стержневой смеси, литников, выпоров, заливов и другого материала, легко удаляемого с помощью ручных или переносных пневматических инструментов.

- Обрубка представляет собой удаление с помощью пневматических инструментов и проволочных щеток пригоревшей формовочной смеси, неровных кромок, излишнего металла, фрагментов литниковой системы, ужимин или других нежелательных дефектов поверхности, а также ручную очистку отливки с помощью стамесок. Для устранения питателей литниковой системы, заварки литья, а также для кислородно-флюсовой зачистки может применяться сварочное оборудование (ацетилено-кислородная резка, электро-дуговая, воздушно-дуговая и плазменная сварка и резка Дробеструйная. Обработка заготовки в специальной камере потоком дроби (песка) со сжатым воздухом Галтовка – обработка заготовок во вращающемся барабане с галтовочными телами
Билет 10
Вопрос 1. Понятие качества поверхности, связь качества поверхности с эксплуатационными свойствами изделий. Факторы, влияющие на качество обрабатываемой поверхности.
Качество поверхности - совокупность геометрических и физико-механических свойств поверхностного слоя. Геометрические свойства – шероховатость и волнистость Физико-механические – микротвердость поверхности, глубина дефектного поверхностного слоя, остаточные напряжения в поверхности
1 Износостойкость. Влияние шероховатости на износостойкость (На особо чистых поверхностях смазка удерживается плохо
– возможно появление задира) Влияние волнистости (неровностей с большим шагом) на износостойкость (Волнистость уменьшает поверхность контакта между сопрягаемыми деталями, увеличивает предельные нагрузки, что повышает износ). Влияние наклёпа на износостойкость 2 Усталостная прочность. Влияние шероховатости на усталостную прочность (Определяются своеобразными надрезами на
поверхности, концентратами напряжений и могут привести к усталостным трещинам)
Влияние наклепа на усталостную прочность (Наклеп повышает усталостную прочность детали в несколько раз)
Влияние остаточных напряжений на усталостную прочность (Остаточное напряжение сжатия повышает усталостную прочность, а напряжение растяжение – понижает)
3 Коррозионная стойкость. Влияние шероховатости на коррозионную стойкость (Коррозия возникает легче, распространяется быстрее на грубо обработанных поверхностях Влияние наклепа на коррозионную стойкость (Наклеп ускоряет коррозию в 1,5-2 раза)
4 Прочность соединения. Влияние шероховатости на прочность соединения (Чем меньше шероховатость поверхности, тем больше площадь сопряжения)
Факторы:
1 Влияние способа обработки на шероховатость поверхности 2 Влияние режима обработки на шероховатость (Скорость резания - образуется нарост при определенной скорости. Поэтому
необходимо назначать скорость либо до образования нароста, либо после. Подача - чем больше S, тем больше высота гребешков на поверхности (Rz)).
3 Геометрические причины образования шероховатости (Затупление инструмента - при увеличенном затуплении, увеличивается радиус лезвия, что приводит к росту шероховатости, Радиус при вершине - чем больше r, тем меньше Rz,. Углы в плане - больше φ и φ1, тем больше Rz
4 Влияние обрабатываемого материала на шероховатость - вязкие и хрупкие материалы дают более шероховатые поверхности. Необходимо сталь нормализовывать и отпускать тогда шероховатость уменьшается 5 Влияние смазочно-охлаждающих жидкостей на шероховатость - предотвращает схватывание, уменьшает трение, облегчает стружкообразование, уменьшает шероховатость.
6 Влияние жесткости технологической системы на шероховатость - При обработке длинных валов может возникнуть бочкообразность, седлообразность, конусность.
Вопрос 2. Методы получения резьбы.
Резьбу получают тремя основными методами: 1нарезанием лезвийным инструментом, 2нарезанием абразивным инструментом, 3пластическим деформированием (накатыванием).
1 Резьбовые резцы - однолезвийный фасонный режущий инструмент, режущая кромка которого при обработке образует профиль резьбы всеми точками.
2 Метчик - осевой многолезвийный инструмент для образования и обработки резьбы (внутренней). виды: ручные, машинные, гаечные, калиброванные, плашечные, бесстружечные, конические 3 Плашка - осевой многоцелевой инструмент для образования и обработки наружной резьбы.
4 Резьбовые фрезы:
-гребенчатые фрезы - для резьбы с неглубоким профилем.
-дисковые фрезы - для резьбы с крупным профилем.
-гребенчатые - сборные охватывающие.
-головки для скоростного фрезерования резьбы с крупным шагом (Вместо гребенчатой фрезы установлены резцы (вихревой метод).
Для накатывания: резьбонакатные ролики, головки, плашки.
Вопрос 3. Виды образующихся стружек при резании металлов. Факторы, влияющие на вид образующейся стружки.
Сливная (непрерывная) – образуется при резании пластических материалов с высокими скоростями резания и малыми подачами.
Элементная стружка – состоит из отдельных элементов связанных друг с другом, образуется при обработки твердой стали с малыми скоростями и большими подачами.
Стружка надлома – образуется при резании мало пластичных материалов (чугуна, бронзы) и состоит из отдельных кусочков.

На вид образующейся стружки влияет обрабатываемый материал и режимы обработки – температурно-скоростной фактор. Так для сталей при малых скоростях резания и при высоких – образуется элементная стружка, а на средних – сливная.
Вопрос 4. Отклонения формы и их обозначение на чертежах.
Под отклонением формы поверхности понимают отклонение реальной поверхности от номинальной пов-и
Отклонение от круглости – наибольшее отклонение от точек реального профиля до прилегающей окружности. Частные виды: овальность и огранка. Отклонение от цилиндричности – наибольшее расстояние от точек реальной поверхности до прилегающего цилиндра
Отклонение профиля продольного сечения цилиндрической поверхности – наибольшее расстояние от точек реальной поверхности до прилегающей плоскости.
Частные виды: конусообразность – отклонение профиля продольного сечения, при котором образуется прямолинейность, но не параллельность бочкообразность – отклонение профиля продольного сечения, который образуется не параллельно и диаметры увеличиваются от краев к середине
седлообразность – отклонение профиля продольного сечения, который образуется не параллельно и диаметры уменьшаются к середине от краев
Отклонение от прямолинейности – наибольшее отклонение от точек реального профиля до прилегающей прямой. Частные виды: выпуклость, вогнутость
Отклонение от плоскости – определяется как наибольшее отклонение от точек реальной поверхности до прилегающей
плоскости.
Вопрос 5. Кондукторные втулки, назначение, область применения, конструкции, требования.
Кондукторные втулки – элементы приспособлений, служащие для направления режущего осевого инструмента на сверлильных и расточных станках. Применяются для обработки отверстий скоординированных относительно других отверстий или поверхностей заготовок.
Втулки обычно изготавливают из углеродистых инструментальных сталей. Втулки имеют точное отверстие под направление инструмента и точный наружный диаметр для установки в кондукторную плиту.
Втулки бывают:
Постоянные – запрессовываются в кондукторную плиту. Бывают без буртика и с буртиком
Сменные – применяются тогда, когда необходима быстрая их замена в случае износа. Они устанавливаются в переходной втулке по посадке или от проворачивания и подъема при обработке закрепляются винтами или накладками. Переходные втулки запрессовываются по посадке.
Быстросменные – устанавливаются в переходной втулке по посадке и применяются при обработке точных отверстий последовательно несколькими инструментами: сверлом, зенкером, развертками. Для направления каждого из этих инструментов требуется своя быстросменная втулка. Быстросменная втулка, наряду с выемкой для головки крепежного винта, имеет сквозную выемку по всей высоте буртика для быстрого ее удаления без отвинчивания винта. Буртик втулки для удобства снятия и установки имеет накатку.
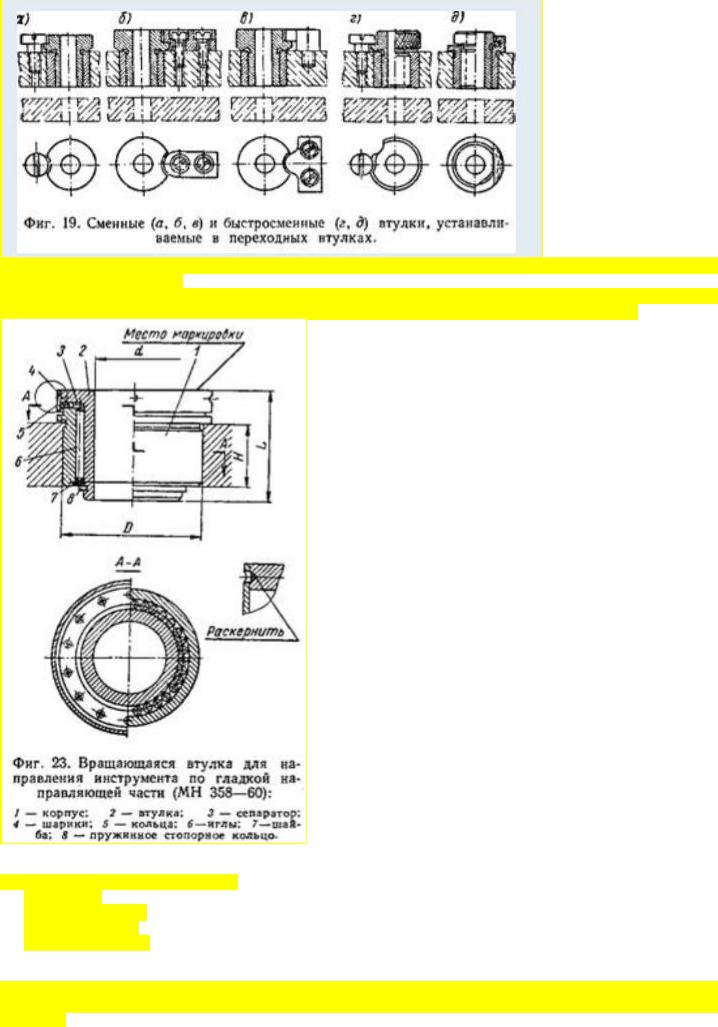
Направляющие втулки под расточной инструмент – служат для направления скалок с резцами или насадным многолезвийным инструментом Вращающиеся втулки – используются для направления расточного инструмента с нижним расположением втулки,
поскольку не позволяют попадать стружке между отверстием втулки и скалкой, что приведет к биению скалки.
Требования к кондукторным втулкам:
1.Точность
2.Износостойкость
3.Экономичность
4.Быстросменность
Вопрос 6. Какими преимуществами и недостатками обладает производство заготовок методами порошковой металлургии? Порошковая металлургия - метод изготовления различного рода заготовок из исходного сырья в виде порошков, которые затем прессуются (формуются) в изделия заданных размеров и подв ергаются термической обработке – спеканию.
Преимущества:

-производство изделий близких к заданным;
-практически полное исключение дополнительных операций;
-высокий коэффициент использования исходного материала ;
-однородность порошка и, следовательно, одинаковый химический состав вследствие равномерной кристаллизации предварительно легиро ванных частиц порошка;
-уникальные композиции и сплавы, изготовляемые благодаря отсутствию плавления, а введение в них специфических частиц дают особые свойства (например, введение кремния и графита в изготовлении тормозных колодках);
-изготовление неравновесных композиций (например, из медно -хромовых сплавов);
-металлургические структуры, как правило, имеют тонкие и однородные структуры:
Недостатки:
-высокая стоимость исходных порошков.
-высокая стоимость инструмента (пресс формы) для формования заготовки.
-размеры заготовок ограничены из-за высокого давления прессования
-невозможность получать изделия сложной формы
-только в массовом производстве
-высокая остаточная пористость у заготовок
Билет 11
Вопрос 1. Явление технологической наследственности, ее количественная характеристика. Влияние технологической наследственности на качество продукции.
Технологическая наследственность – это явление, при котором погрешности, получаемые на предшествующей операции, уменьшаются, но остаются такими же по характеру. Характеризуется коэффициентом уточнения; Для черн. Ку = 0,06для чист. Ку = 0,04.
Ку = i/ i-1
i – погрешность на текущем переходе;
i-1 – погрешность на предыдущем переходе
Проявление технологической наследственности может привести как к улучшению, так и к ухудшению эксплуатационных свойств деталей машин. Причем наследственность оказывает влияние не только непосредственно после финишных операций технологического процесса, но может проявляться и при эксплуатации в результате воздействия тех или иных параметров качества поверхности, созданных в поверхностном слое детали при ее предшествующей обработке.
Вопрос 2. Основные узлы токарного станка и их назначение.
Станина 29 — массивное чугунное основание, где смонтированы основные механизмы станка. Верхняя часть станины состоит из двух призматических и двух плоских направляющих, по которым передвигаются задняя бабка и суппорт. Станина закреплена на двух тумбах.
Передняя (шпиндельная) бабка 1 с коробкой скоростей крепится на левом конце станины. В ней размещена коробка скоростей и шпиндель, которые сообщают заготовке главное движение, а инструменту – движение подачи при выбранной глубине резания.
Шпиндель 7 служит для крепления заготовки с помощью приспособлений и сообщения ей вращательного движения. Вал шпинделя делается полым для размещения в нем обрабатываемого прутка. Передний конец шпинделя имеет конусное отверстие, в которое при необходимости устанавливается центр. К торцу шпинделя крепится на резьбе или болтами кулачковый или поводковый патрон для закрепления обрабатываемых заготовок.
Токарно-винторезный станок модели 1К62: 1 – передняя (шпиндельная) бабка; 2, 3, 4, 5 – рукоятки; 6 – коробка скоростей; 7 – шпиндель; 8 – продольные салазки (каретка); 9 – поперечные салазки; 10 – резцедержатель; 11 – рукоятка; 12 – поворотный суппорт; 13 – рукоятка; 14 – пиноль; 15 – задняя бабка; 16 – переключатель; 17 – маховик; 18 – направляющие станины; 19 – ходовой винт; 20 – ходовой вал; 21, 22 – рукоятки; 23 – кнопки; 24
– рукоятка; 25 – фартук; 26, 27 – маховики; 28 – рукоятка; 29 – станина; 30 – рукоятка; 32 – коробка подач; 33 – рукоятка; 34 – гитара
Коробка скоростей 6 обеспечивает 24 различных числа оборотов шпинделя в минуту. На передней панели коробки скоростей расположены рукоятки 2, 5 для установки числа оборотов шпинделя, рукоятка 3 установки числа заходов резьбы и рукоятка 4 установки правой и левой резьбы.
Коробка подач 32 расположена на передней стороне станины под передней бабкой. Она обеспечивает получение необходимой величины подачи инструмента или шага нарезаемой резьбы с помощью рукояток 30, 33. Передача к коробке подач осуществляется от шпинделя через гитару 34 со сменными зубчатыми колесами. Далее движение через ходовой вал 20 (при точении) или ходовой винт 19 (при нарезании резьбы) передается на суппорт.
Гитара 34 предназначена для настройки станка на требуемую величину подачи или шаг нарезаемой резьбы путем установки соответствующих сменных зубчатых колес.
Суппорт состоит из каретки 8, которая перемещается по направляющим 18 станины, фартука, в котором расположен механизм преобразования вращательного движения ходового вала и ходового винта в прямолинейное движение суппорта, механизма поперечных салазок, механизма резцовых (верхних) салазок, механизма резцедержателя.

Поперечные салазки 9 перемещаются по направляющим продольных салазок при поперечной подаче. На поперечных салазках расположен верхний поворотный суппорт 12 с резцедержателем 10. Верхний суппорт используется при обтачивании конических поверхностей. Для этого его поворачивают на необходимый угол. Подачу суппорта осуществляют рукояткой 13.
Резцедержатель 10 служит для установки и крепления резцов. Он имеет четыре позиции, что позволяет установить одновременно четыре инструмента и менять их, поворачивая резцедержатель рукояткой 11. Фартук 25 крепится к каретке суппорта. В нем расположен механизм, при помощи которого вращательное движение ходового вала 20 или ходового винта 19 преобразуется в поступательное прямолинейное (продольное или поперечное) движение суппорта. Рукоятка 24 служит для включения маточной гайки (при нарезании резьбы). Задняя бабка 15 служит для поддержания обрабатываемой заготовки при работе в центрах, а также для закрепления сверл и других инструментов при обработке осевых отверстий. Корпус задней бабки установлен на направляющих станины и может по ним перемещаться. В отверстии корпуса имеется пиноль 14, которая выдвигается с помощью маховика 17. Корпус задней бабки смещается относительно ее основания в поперечном направлении, что необходимо при обтачивании наружных конических поверхностей.
Электрооборудование станка размещено в шкафу. Включение и выключение электродвигателя, пуск и остановка станка, управление коробкой скоростей и коробкой подач, управление механизмом фартука и т. д. производится соответствующими органами управления (рукоятками, кнопками, маховичками).
Вопрос 3. Требования, предъявляемые к вспомогательной инструментальной оснастке.
•Сокращение потерь времени на замену инструмента;
•Сокращение потерь времени на наладку инструмента;
•Сокращение потерь времени на регулирование инструмента;
•Обеспечение высокой жесткости;
•Обеспечение высокой точности позиционирования (установки) инструмента по отношению к базам станка;
•Гибкость и взаимозаменяемость;
•Способность обслуживания оснастки манипулятором - сменщиком.
Вопрос 4. Методы описания технологической информации в САПР. Способы кодирования, виды структур кода.
Существует 2 кардинально отличающихся подхода к формализации технологической информации в САПР:
1.На основе специальных языков описания
2.На основе классификаций (кодировочных ведомостей)
На сегодняшний день единственным стиандартным языком описания является язык EXPRESS. Причём этот язык предназначен для описания не только технологической информации, но вообще всей информации в течение жизненного цикла продукции. EXPRESS представляет собой объектно-ориентированный язык и используется при формировании файлов стандарта STEP (Standard for Exchange of Productmodeldata).
Также для хранения и обмена технологической информацией используется универсальный язык XML.
Описание технологической информации на основе кодирования широко распространено при использовании типовых и групповых технологий..
Выделяют три типа структур кодов:
1)Иерархический код (моноаспектный, монокод) – значение знака кода зависит от его положения и от значений предыдущих знаков. Примером монокода может служить классификация ЕСКД, классификация МРС. Преимущество иерархического кода заключается в возможности описания большого количества информации при небольшой длине кода. К недостаткам относится сложность кодирования, трудности с изменением кода.
2)Цепной код (многоаспектный код) – значение знака кода не зависит от значений других знаков.
Достоинство цепного кода – простота кодирования, простота изменения кодировки. Недостаток – содержит значительно меньше информации, чем иерархический код.
3) Гибридный код – часть кода имеет иерархическую структуру, часть – цепную. Является предпочтительным в большинстве случаев, поскольку сочетает достоинства двух предыдущих видов кодирования.
Кодирование технологической информации позволяет быстро производить поиск технологических процессов – аналогов, за счёт чего можно значительно повысить производительность процесса проектирования.
Вопрос 5. Обязательная и добровольная сертификация. Отличительные признаки.
Обязательная сертификация - это сертификация продукции, сертификация которой является обязательным требованием в соответствии с законодательством. Применяется обязательная сертификация для подтверждения качества и безопасности, как отечественных, так и зарубежных товаров, а конечным документом является обязательный сертификат соответствия. Обязательная сертификация требуется для оформления продукции на таможне, одновременно с таможенной декларацией предоставляются: обязательный сертификат соответствия и санитарный сертификат (Свидетельство о Государственной Регистрации). В случаях когда товар не подлежит обязательной сертификации, может быть оформлена декларация о соответствии.
Добровольная сертификация - это сертификация только по желанию и личной инициативе изготовителя. В таких случаях изготовитель в праве проводить сертификацию своей продукции на соответствие любым требованиям технической

документации (ГОСТ или Технических Условий для Российского производителя). Добровольная сертификация может проводится юридическими лицами и гражданами на основании договоров между заявителем и органом по сертификации. Так же добровольная сертификация может использоваться для работ, услуг и продукции, выходящей за установленные рамки обязательной сертификации.
Отличия добровольной сертификации от обязательной практически нет, так как в этих двух случаях качество товаров и услуг подтверждается документально, что и есть самое главное. Различаются документы только бланками, на которых эти сертификаты печатаются. В случаях, когда продукция подлежит обязательной сертификации, сертификат печатают на бланке желтого цвета, а для добровольного сертификата используют бланк голубого цвета. После проведения сертификации, продукцию маркируют специальными знаками соответствия, для продукции попавшей под обязательный перечень, маркировка знаком соответствия обязательна. Добровольная сертификация не может заменить обязательную сертификацию, а получение добровольного сертификата на продукцию входящую в перечень обязательной сертификации невозможно, без первоначального получения на данный вид продукции обязательного сертификата или декларации (если продукция попадает в перечень обязательного декларирования продукции). После получения обязательного сертификата соответствия, возможно оформление добровольного сертификата, на соответствие требованиям, дополняющие обязательные.
Вопрос 6. Перечислите основные параметры эвольвентного зубчатого зацепления. Что такое модуль. Диаметр начальной окружности Диаметр вершин и впадин Делительный диаметр Угол зацепления Делительный шаг
Число зубьев шестерни и колеса Модуль зубчатого зацепления Межосевое расстояние Коэффициент торцового перекрытия
da – окружность вершин – это самая большая окружность, ограничивающая вершины головок зубьев колес: её условно изображают сплошной основной линией.
d – делительная окружность, делящая каждый зуб на две неравные части: меньшую – головку зуба и большую – ножку зуба: её условно изображают штрихпунктирной тонкой линией. df – окружность впадин, проходящая по очертаниям впадин между зубьями: её условно изображают сплошной тонкой линией.
dоб – окружность обода, обозначающая внутреннее очертание обода.
dст – окружность ступицы, обозначающая внешнее очертание ступицы.
dв – диаметр окружности отверстия для вала. h– высота зуба.
hа – высота головки зуба. hf – высота ножки зуба.
Pn – нормальный шаг зубьев – кратчайшее расстояние по делительной или начальной поверхности зубчатого колеса между эквидистантными одноименными теоретическими линиями соседних зубьев.
S – толщина зуба.
Z – число зубьев.
m — модуль колеса.
Модулем зацепления называется линейная величина в π раз меньшая окружного шага P
Билет 12
Вопрос 1. Состав и назначение технических устройств для обеспечения автоматической сборки. Бункерно-ориентирующие устройства - кассеты, магазины, бункеры Накопители - устройства создающие запас деталей
Питатели - устройства для передачи деталей от накопителей на сборочные позиции Отсекатели – устройства для поштучной выдачи деталей Устройство для скрепления соединяемых деталей (для запрессовки…)
Устройства, выполняющие спец. функции (устройства смазки, регулировки, заправки…) Устройство контролирующие правильность выполнения сборки (датчик)
Устройства для удаления собранных изделий из автомата в тару или на конвейер.
Вопрос 2. Методы кодирования инструмента в инструментальных магазинах. |
|
|
|
|
|||||
Поиск инструментов в магазине ведется различными способами: |
|
|
|
|
|
||||
1.Инструмент |
раскладывают |
в |
гнездах |
магазина |
в |
порядке |
техпроцесса. |
В |
этом |
случае кодируют угол поворота магазина.