
- •Стали
- •Магниевые сплавы
- •Титановые сплавы
- •Алюминиевые сплавы
- •2.1. Технологичность заготовок
- •Горячештампованные заготовки
- •Литые заготовки
- •Простановка размеров
- •Технологичность основных элементов конструкции деталей
- •Открытые плоскости
- •Сопрягаемые плоскости (колодцы, карманы, пазы, гнезда)
- •Наружные поверхности вращения
- •Внутренняя резьба
- •Фасонные поверхности
- •Монолитные панели
- •Панели, изготовляемые из плит
- •Панели из горячештампованных заготовок
- •Панели из горячепрессованных заготовок
- •Панели из специального литья
- •Крупногабаритные детали из алюминиевых и магниевых сплавов
- •Балки и лонжероны
- •Детали узлов поворота
- •Шпангоуты, рамы и их детали
- •Длинномерные детали из прессованных профилей
- •Фитинги и кронштейны
- •Рычаги и качалки
- •Фланцы и крышки
- •ЛИТЕРАТУРА

класса чистоты возможно только при очень большом увеличении трудоемкости, а в некоторых случаях совершенно невозможно, особенно в деталях, имеющих теоретический обвод, большую длину или малые переходные радиусы (рис. 2.53). Достижение высоких классов чистоты в этих случаях возможно чрезвычайно трудоемкой доводкой или механизированными средствами (виброударным, пневмодинамическим методами и др.).
Рис. 2.52. Улучшение технологичности конструкции замка путем сварки из двух деталей
Рис. 2.53. Пример нетехнологичного задания высоких классов шероховатости на поверхности тонкостенных нежестких деталей, имеющих теоретический контур или переходные поверхности
Сопрягаемые плоскости (колодцы, карманы, пазы, гнезда)
Для улучшения технологичности колодцев, карманов, пазов, гнезд и других элементов деталей с сопрягаемыми плоскостями рекомендуется руководствоваться рядом следующих технологических требований.
Размеры элементов с сопрягаемыми плоскостями должны быть увязаны с размерами нормальных концевых фрез (рис. 2.54). Для этого при конструировании необходимо учитывать:
– наибольшая глубина элементов (колодцев, карманов, пазов, гнезд) должна быть на 4–5 мм меньше режущей части фрезы. В деталях из конструкционных сталей глубину элементов рекомендуется предусматривать не более 1,5 D фрезы, а в деталях из нержавеющих сталей и титановых сплавов – не более D фрезы.
50

–радиус у дна элемента следует выбирать равным радиусу фрезы R
уторца, который не должен превышать значений, указанных в табл. 2.4, 2.5. Желательно переходные радиусы у дна элемента заменять фасками; это особенно важно при работе фрез, оснащенных твердым сплавом.
Рис. 2.54. Увязка размеров сопрягаемых плоскостей с размерами концевых фрез
Таблица 2.4
Глубина фрезерования в зависимости от радиуса закругления и диаметра концевых фрез из быстрорежущей стали
|
|
|
R |
|
|
D |
0,5–3 |
0,5–4 |
0,5–5 |
0,5–6 |
0,5–10 |
|
|
Нмакс |
|
|
|
14 |
25 |
|
|
|
|
16–18 |
|
30 |
|
|
|
20–22 |
|
|
35 |
|
|
25–32 |
|
|
|
40 |
|
36 |
|
|
|
|
45 |
40 |
|
|
|
|
50 |
45–50 |
|
|
|
|
60 |
Таблица 2.5
Глубина фрезерования в зависимости от радиуса закругления и диаметра концевых фрез с твердосплавными пластинами
|
|
|
R |
|
|
D |
0,5–2 |
1–2,5 |
|
1–4 |
1–5 |
|
|
Нмакс |
|
|
|
10–12 |
12 |
|
|
|
|
14–16 |
14 |
|
|
|
|
18 |
|
14 |
|
35 |
|
20–22 |
|
16 |
|
|
|
24–25 |
|
|
|
16 |
|
28–36 |
|
|
|
|
20 |
51
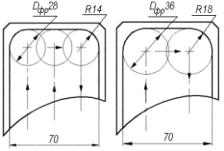
40–50 |
|
|
|
24 |
– радиус сопряжения боковых сторон R = Dфр/2 следует назначать из расчета, чтобы обработка проводилась за минимальное количество проходов. Так, колодец, который может быть обработан за три прохода фрезой ø28 (рис. 2.55), обработан за два прохода фрезой ø36 вследствие увеличения радиуса сопряжения боковых поверхностей. Кроме этого радиусы сопряжения колодцев и карманов желательно выполнять одинаковыми, т.к. обработка при этом производится одним инструментом
Рис. 2.55. Увеличение радиуса сопряжения боковых сторон позволяет использовать концевую фрезу большего диаметра и уменьшить количество проходов при обработке карманов и ко-
лодцев
Конструкция пазов и прорезей малой ширины должна предусматривать обработку их дисковыми фрезами. Обработка узких пазов и прорезей более производительна дисковыми фрезами, чем концевыми. Открытые пазы, а также ушки, обрабатываемые дисковыми фрезами, должны быть согласованы с размерами нормальных дисковых фрез. В табл. 2.6, 2.7 приведена наибольшая глубина фрезерования обрабатываемых пазов в зависимости от их ширины и размеров нормальных и радиусных дисковых фрез.
Таблица 2.6
Глубина обрабатываемых пазов в соответствии с их шириной и размерами нормальных пазовых фрез из быстрорежущей стали
Радиус |
Ширина паза, B |
|
|
|
Диаметр фрезы, D |
|
|||
90 |
110 |
|
130 |
150 |
175 |
200 |
250 |
||
закругления, R |
|
||||||||
|
|
|
Глубина паза, Hмакс |
|
|||||
|
|
|
|
|
|||||
1 |
3 |
20 |
|
|
|
|
|
|
|
1 |
4; 4,5; 5; 5,5 |
20 |
27 |
|
|
|
|
|
|
1;1,5 |
6 |
|
27 |
|
38 |
|
|
|
|
1,5 |
7; 8; 9 |
|
|
|
38 |
|
|
|
|
1,5 |
10; 11 |
|
|
|
|
46 |
|
|
|
1,5;3 |
12 |
|
|
|
|
46 |
50 |
|
|
3 |
13; 14; 15 |
|
|
|
|
|
50 |
|
|
3 |
16; 18; 20 |
|
|
|
|
|
|
65 |
80 |
52
Таблица 2.7
Глубина обрабатываемых пазов в соответствии с их шириной и размерами нормальных полукруглых фрез из быстрорежущей стали
|
|
|
|
Диаметр фрезы, D |
|
||||
Ширина паза, B |
|
|
|
|
|
|
|
|
|
75 |
90 |
110 |
130 |
150 |
175 |
200 |
225 |
250 |
|
|
|
|
|
|
|
|
|
|
|
|
|
|
|
Глубина паза, Hмакс |
|
||||
2,0; 2,5 |
18 |
|
|
|
|
|
|
|
|
3,0 |
18 |
20 |
26 |
|
|
|
|
|
|
4,0; 4,5; 5; 5,5 |
|
|
26 |
|
|
|
|
|
|
6,0; 7,0 |
|
|
|
35 |
|
|
|
|
|
8,0; 9,0 |
|
|
|
35 |
45 |
|
|
|
|
10 |
|
|
|
|
45 |
50 |
|
|
|
11; 12 |
|
|
|
|
|
50 |
|
|
|
13; 14; 15 |
|
|
|
|
|
|
64 |
|
|
18; 20 |
|
|
|
|
|
|
|
70 |
|
22; 24; 26 |
|
|
|
|
|
|
|
70 |
80 |
Примечание. Количество типоразмеров используемых фрез может быть дополнительно сокращено отраслевыми ограничительными нормалями.
Форма переходных поверхностей паза зависит от требуемой точности, класса шероховатости и материала детали. Показанные на рис. 2.56 формы переходной поверхности паза могут быть изготовлены дисковыми фрезами из быстрорежущей стали (а) и оснащенными ножами из твердого сплава (б) в деталях из цветных и титановых сплавов и стали с σв<800 МПа. Это позволяет получить пазы 10–12 квалитета точности с шероховатостью не лучше R а = 5 мкм. Такая же форма
переходной поверхности может быть получена и для стальных деталей с σв>800 МПа со свободными размерами паза (13 квалитет точности и ниже R а = 5 мкм), т. к. паз фрезеруется до термической обработки,
когда предел прочности заготовки не превышает 800 МПа.
Пазы могут обрабатываться и в термически обработанных деталях из титановых сплавов и стали с σв<1200 МПа (без предварительной обработки до закалки). При этом переходная поверхность паза должна быть выполнена в виде фаски, поскольку паз фрезеруется дисковой фрезой, оснащенной ножами из твердого сплава. Заточка радиусных переходов дисковых фрез, особенно оснащенных ножами из твердого сплава, представляет в производстве большую трудность. В работе такие фрезы не стабильны и быстро изнашиваются.
Фрезами, оснащенными твердым сплавом, могут обрабатываться пазы в деталях из стали с σв = 1800–2000 МПа. Шероховатость фрезе-
53
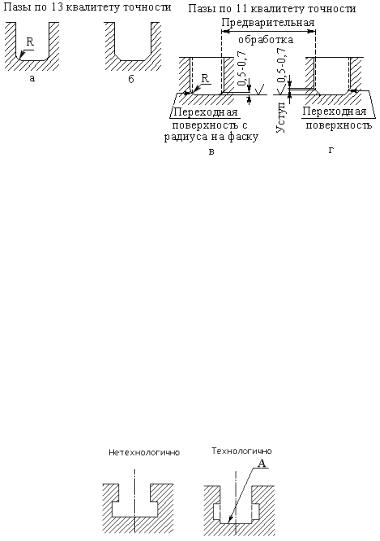
рованной поверхности термически обработанных деталей из стали может быть равной Rа = 2,5 мкм.
Рис. 2.56. Переходные поверхности пазов, прорезаемых дисковыми фрезами
При обработке пазов в деталях из титановых сплавов и стали с σв>1200 МПа, имеющих классные размеры, необходимо предусматривать переходные поверхности с учетом предварительной обработки паза (рис. 2.56, в и г). Фрезерованием можно изготовить пазы по 11-му и 12-му квалитету точности. Большая точность достигается при последующем шлифовании или протягивании. Образующиеся при этом формы переходных поверхностей необходимо обозначать на чертеже, особо оговаривая, что шероховатость дна паза не превосходит Ra = 5 мкм, т. к. при чистовой обработке дно не обрабатывается.
В конструкции оснастки часто предусмотрено выполнение Т- образных пазов. Учитывая, что рабочие поверхности таких пазов обрабатываются малопроизводительными фрезами специальной формы, желательно уменьшать размеры окончательно обрабатываемых поверхностей. На рис. 2.57 (справа) показана конструкция паза, в которой размеры рабочих поверхностей уменьшены путем введения выемки А, образуемой фрезой при предварительном прорезании паза.
Рис. 2.57. Улучшение технологичности Т-образного паза путем введения выемки, образуемой дисковой фрезой
Изготовление длинных узких пазов повышенной точности (выше 13-го квалитета) и шероховатостью поверхности выше Rа = 5 мкм вызывает технологические трудности из-за возникающих вибраций
54
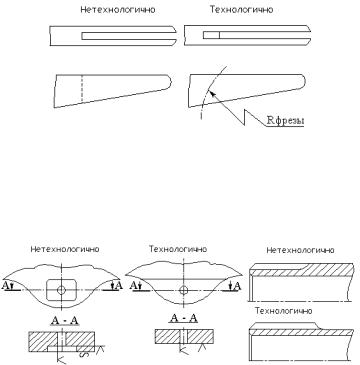
вследствие недостаточной жесткости системы СПИД. В случае применения таких пазов необходимо учитывать выход дисковой фрезы. Доработка основания паза концевой фрезой затруднена, а иногда и невозможна (рис. 2.58).
Рис. 2.58. Учет выхода дисковой фрезы при прорезании узкого паза с целью улучшения технологичности конструктивного элемента
Следует избегать в конструкции детали закрытых пазов и гнезд. Применение открытых пазов позволяет вести обработку по настроенному процессу, улучшает шероховатость и точность изготовления
(рис. 2.59).
а |
б |
Рис. 2.59. Применение в конструкции детали закрытых пазов и гнезд, ухудшающее ее технологичность
Аналогично при проектировании треугольных шлиц на шейке вала всегда необходимо предусматривать полный выход фрезы (рис. 2.60).
Форму пазов на деталях тел вращения задается в зависимости от размеров этих деталей. На деталях малого диаметра при небольшой ширине стенки паза желательно проектировать параллельно друг другу, т. к. обработка производится за один проход (рис. 2.61). На деталях большого диаметра при большой ширине стенки паза необходимо проектировать радиально, т. к. обработка паза производится на поворотном столе (рис. 2.62).
При сопряжении наклонного ребра с основанием необходимо в месте сопряжения предусматривать уступ, что исключает слесарную
55
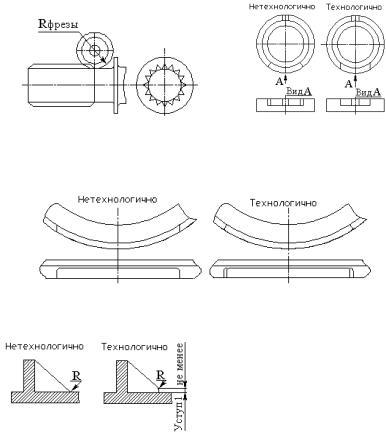
доработку и предохраняет от зарезания плоскости при механической обработке ребра (рис. 2.63).
Рис. 2.60 Полный выход фрезы, преду- |
Рис. 2.61 Выполнение параллель- |
сматриваемый при обработке треугольных |
ных стенок пазов на телах враще- |
шлиц |
ния малого диаметра |
Рис. 2.62. Радиальное расположение стенок паза на детали большого диаметра, улучшающее технологичность обработки паза
Рис. 2.63. Формирование уступа в месте сопряжения наклонного ребра с плоскостью, улучшающее технологичность механической обработки сопряжения
При сопряжении ребра с ребром (или другими элементами детали), образующими угол, рекомендуется в месте сопряжения предусматривать площадку с уступом для подхода инструмента, что исключает слесарную доработку в месте сопряжения (рис. 2.64).
Для исключения слесарных доработок, улучшения технологичности и качества механической обработки следует по возможности избегать сопряжения двух наклонных ребер. При необходимости одно из них делать перпендикулярным основанию и показывать линию стыка
(рис. 2.65).
Внежестких деталях с колодцами и карманами больших габаритов
итонкими донышками рекомендуется вводить дополнительные ребра жесткости, что повышает жесткость детали, упрощает конструкцию
56
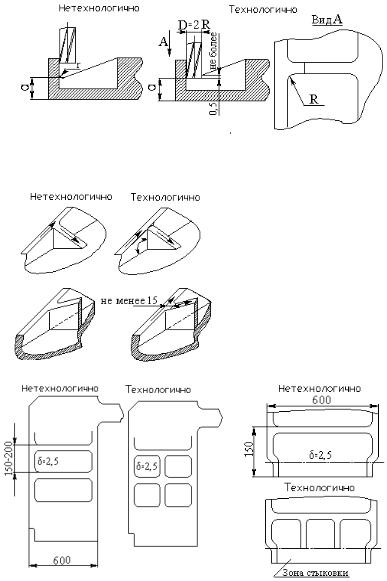
оснастки и снижает трудоемкость за счет увеличения режимов обработки (рис. 2.66).
Рис. 2.64. Выполнение площадки для подхода концевой фрезы в местах примыкания ребра к другим ребрам
Рис. 2.65. Указание в местах примыкания двух наклонных ребер линии стыка, положение которой должно исключать необходимость слесарных доработок
а |
б |
|
Рис. 2.66. Дополнительные ребра в широких колодцах (а) и карманах (б), по-
57
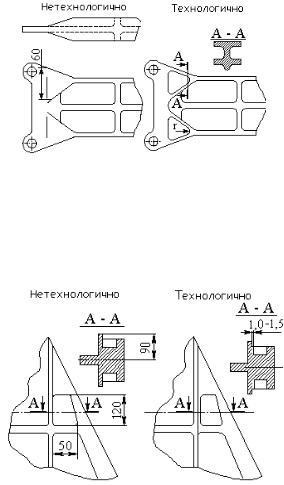
вышающие технологичность обработки панелей
На наклонных ребрах большой ширины для уменьшения веса и снижения трудоемкости фрезерования рекомендуется делать колодцы без механической обработки (рис. 2.67).
Рис. 2.67. Создание необрабатываемых колодцев на широких наклонных ребрах, улучшающее технологичность их механической обработки
Если к карману прилегают полки с высокими ребрами, необходима фреза с режущей частью, превышающей высоту большого ребра. При введении небольших изменений (рис. 2.68) высота режущей части фрезы сокращается вдвое, возрастает ее жесткость и повышается производительность.
Рис. 2.68. Смещение колодца на 1–3 мм в сторону от высокого ребра, позволяющее обработать колодец фрезой с меньшей длиной режущей части
Для получения тонкостенных элементов деталей (менее 2,5 мм), ограниченных сопрягаемыми плоскостями, экономически целесообразно использовать размерное химическое травление, оставляя после механической обработки припуск на химическое травление, тем самым
58