
- •Стали
- •Магниевые сплавы
- •Титановые сплавы
- •Алюминиевые сплавы
- •2.1. Технологичность заготовок
- •Горячештампованные заготовки
- •Литые заготовки
- •Простановка размеров
- •Технологичность основных элементов конструкции деталей
- •Открытые плоскости
- •Сопрягаемые плоскости (колодцы, карманы, пазы, гнезда)
- •Наружные поверхности вращения
- •Внутренняя резьба
- •Фасонные поверхности
- •Монолитные панели
- •Панели, изготовляемые из плит
- •Панели из горячештампованных заготовок
- •Панели из горячепрессованных заготовок
- •Панели из специального литья
- •Крупногабаритные детали из алюминиевых и магниевых сплавов
- •Балки и лонжероны
- •Детали узлов поворота
- •Шпангоуты, рамы и их детали
- •Длинномерные детали из прессованных профилей
- •Фитинги и кронштейны
- •Рычаги и качалки
- •Фланцы и крышки
- •ЛИТЕРАТУРА
Допускаемое коробление, влияющее на величину назначаемых припусков, необходимо указывать на чертеже детали.
На чертеже деталей из штампованных заготовок должно быть согласованное с ОГК указание, разрешающее изготавливать эти детали в опытном производстве из кованых заготовок.
В зависимости от степени ответственности деталям присваивается группа контроля. К первой группе относят особо ответственные детали. Каждая деталь первой группы подвергается полной проверке. Ко второй группе относят ответственные детали, которые подвергаются выборочной проверке (одна или несколько деталей в партии). К третьей группе относят детали, которые не подвергают специальным проверкам и испытаниям, особо оговоренным в конструкторской и технологической документации.
Литые заготовки
Совершенствование существующих способов литья в песчаные и керамические формы, кокили, под давлением, создание новых сплавов, технологических процессов и оборудования для литья крупногабаритных деталей способствуют расширению применения литых деталей в авиационных конструкциях. Главное преимущество литых заготовок – максимальное приближение ее формы к форме готовой детали при возможности получения сложных поверхностей, полостей, выступов при минимальном объеме механической обработки – делает их наиболее выгодными при производстве деталей из труднообрабатываемых материалов.
Не останавливаясь на обсуждении технологических особенностей и области применения различных методов литья и литейных сплавов, сосредоточим свое внимание именно на вопросах, определяющих технологичность литых заготовок, подвергаемых механической обработке.
Общим требованием к конструкции отливки является то, чтобы расположение детали в форме способствовало хорошему заполнению полости формы расплавленным металлом и удалению газов, выделяющихся при заливке. Тонкие стенки и ребра должны располагаться вертикально. В [3] приводятся технологические рекомендации по рациональному проектированию отливок и их конструктивных элементов (бобышек, ребер, стенок их сопряжений, переходов, радиусов закруглений, отверстий), позволяющие исключить образование усадочных и других дефектов.
Правила оформления чертежей отливок включают кроме выполнения общих требований обязательное указание группы контроля, предельных отклонений размеров, требований к качеству литой поверхности, величины литейных уклонов, мест вырезания образцов для металлографического контроля, рентгеновского просвечивания и механических испытаний, мест и порядка маркирования. Для крупногабаритных
31
отливок, формирующих обводы, необходимо указание того, что теоретический профиль следует брать с плаза. В чертежах литейных деталей, не связанных с теоретическим контуром, необходимо указывать все размеры, не ссылаясь на шаблоны, т.к. при изготовлении моделей используются шаблоны, учитывающие усадку металла.
2.2. Общие требования к технологичности конструкции деталей, обрабатываемых резанием
Основными требованиями технологичности деталей, подвергаемых механической обработке на станках с ЧПУ, являются:
–стандартизация и унификация элементов детали;
–унификация радиусов сопряжений поверхностей и канавок для выхода инструментов;
–упрощение геометрических форм контура заготовки;
–минимальное разнообразие диаметров отверстий и технических требований к ним (необходимо стремиться к одинаковым диаметрам и глубине крепёжных отверстий);
–проектирование обрабатываемых поверхностей как плоскостей;
–или криволинейных поверхностей, но таких, профиль которых образован сопряжением кривых с дугами окружности или мог быть аппроксимирован дугами окружностей;
–избегание наклонённых стенок в корпусных деталях;
–возможность обработки поверхности детали по управляющей программе для контурной системы с линейно-круговым интерполятором не более чем по одной или двум координатам;
–сокращение типоразмеров обрабатывающего инструмента и максимально возможная его стандартизация и унификация;
–для обеспечения жесткости и производительности фрезерного инструмента при обработке сопряжения стенок наружных и внутренних обрабатываемых контуров соотношение между радиусами контура и наибольшей высотой стенок контура должно быть: Rтип ≥ (1/5÷1/6) Н;
–максимальная доступность поверхностей для обработки;
–выполнение закона единства конструкторских, технологических и измерительных баз;
–простановка размеров от этих баз в соответствии с принятой системой координат, удобной для программирования обработки детали;
–форма и размеры заготовки должны позволять обработку в непрерывном автоматическом цикле;
–перерывы в программе как результат ручной смены инструмента или контрольного измерения, но не выполнения ручных приёмов управления;
–проставление размеров в чертежах в прямоугольной системе координат;
32
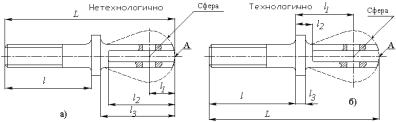
–отверстия необходимо базировать от основных установочных баз;
–привязка крепёжных отверстий к осям координат центрального отверстия, которое они обслуживают;
–обозначение криволинейных поверхностей с указанием координат центров дуг окружностей и точек сопряжения контуров;
–нанесение линейных размеров цепью с соответствующими допусками;
–обработка технологических баз по возможности вне станков с ЧПУ на предварительных операциях.
Большое количество удачных примеров повышения технологичности конструкции деталей, обрабатываемых на станках с ЧПУ, приведено в [2].
Простановка размеров
Наилучшим вариантом простановки размеров является тот, при котором конструктивные базы совпадают с технологическими. При этом отпадает необходимость пересчетов технологических цепочек, упрощаются способы измерения детали, не сужаются допуски на размеры, что обычно наблюдается при введении технологических размеров и подсчёте допусков для них, упрощается конструкция приспособлений и соблюдается наиболее рациональная последовательность технологических переходов и операций.
При проектировании деталей размеры следует задавать от реально существующих точек и поверхностей. Рекомендуется проставлять размеры так, чтобы замер детали можно было произвести прямым методом, без пересчета размеров. Ниже приведены некоторые примеры более рациональной простановки размеров, способствующей упрощению изготовления деталей (рис. 2.16 – 2.21).
Рис. 2.16. Пример нетехнологичной (а) и технологичной (б) простановки размеров вилки
Простановка размеров в случае а ведет к следующим осложнениям
вобработке детали:
–при фрезеровании паза и наружных плоскостей вилки на универсальном приспособлении необходимо настраивать станок на каждую
33

деталь, чтобы выдержать размер l2, т. к. положение вершины сферы будет колебаться в пределах поля допуска на длину L–l;
–усложняются замеры детали, т. к. срезается точка отсчета А, что требует для контроля деталей пересчета размеров;
–при сверлении отверстия точно выдержать размер l2 кромок ушка практически невозможно, т.к. для этого потребуется создание сложного приспособления.
Технологичная простановка размеров упрощает изготовление детали. При этом:
–совпадение технологических и конструктивных баз позволяет производить фрезерование паза и проушин в универсальном приспособлении по настроенному процессу (рис. 2.19);
–замеры детали производятся обычным универсальным инструментом и не вызывают затруднений;
–при сверлении отверстия размер l1 выдерживается стабильно. При этом значительно упрощается конструкция приспособления.
На деталях, изготавливаемых на револьверном станке, рекомендуется проставлять размеры от одного торца, что значительно упрощает настройку оборудования и исключает пересчет технологических размеров.
Рис. 2.17. Рациональная простановка осевых размеров от одного торца
Если наружные и внутренние поверхности вращения детали не могут быть изготовлены на токарном станке за один установ, рекомендуется проставлять размеры от одного торца, который служит базой при обработке поверхности или началом отсчета при создании управляющей программы. Простановка размеров, как показано на рис. 2.18 слева, требует пересчета размеров и сужает поле допуска.
Не рекомендуется проставлять размеры на ушках и вилках от кромок ушка (вилки) или от оси отверстия ушка (вилки). При более рациональной простановке размеров обработка может производиться по настроенному процессу (рис. 2.21).
34
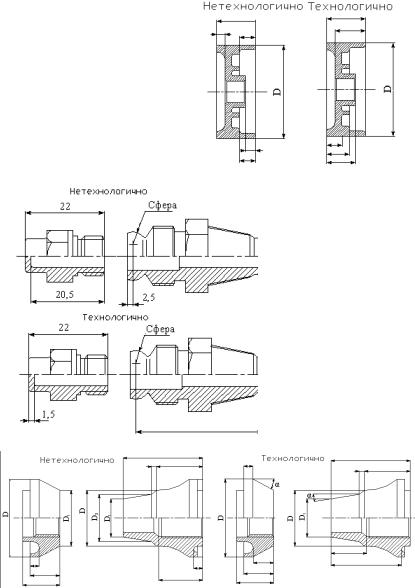
Рис. 2.18. Рациональная простановка размеров, основанная на принципе совмещения конструкторской и технологической баз
Рис. 2.19. Совмещение конструкторских и технологических баз, позволяющее производить обработку по настроенному процессу, обеспечивающему большую точность деталей и стабильность технологического процес-
са
Рис. 2.20. Простановка размеров от технологической базы, улучшающая технологичность механической обработки деталей
Не рекомендуется на чертеже проставлять координаты инструмента, т. к. замеры их весьма осложнены и требуют пересчетов размеров.
35

Рис. 2.21. Пример рациональной простановки размеров на ушках
На рис. 2.22 показана деталь, у которой требуется обработать паз по кривой. В этом случае размеры лучше задавать от оси отверстий, которые будут служить базой для крепления копира. Координация паза от кромок ушка усложняет производственный процесс, т. к. положение паза детали будет колебаться в зависимости от допуска на контур детали.
Рис. 2.22. Пример рационального задания размера паза от оси базового отверстия для установки копира, исключающего погрешность выполнения кромки ушка
При фрезеровании лысок у деталей тел вращения размеры следует проставлять не от оси, а от образующей цилиндра, служащей базой в процессе обработки и измерения (рис. 2.23).
При простановке размеров на уклон рекомендуется задавать высоту и угол (рис. 2.24 и 2.25).
36
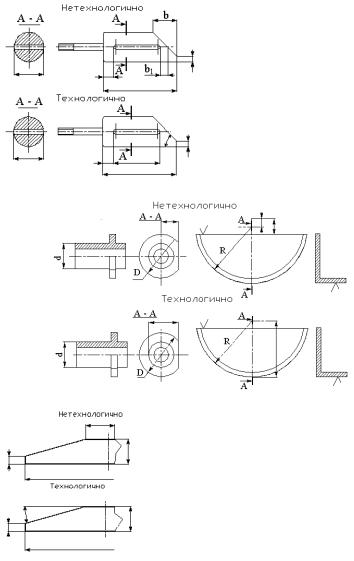
Рис. 2.23. Пример простановки размеров от острых кромок и поверхностей, относительно которых выполнение замеров детали осложнено
Рис. 2.24. Рациональная простановка размеров лысок на деталях – телах вращения использует преимущества принципа совмещения баз Ø
Рис. 2.25. Пример простановки размеров на уклон
Канавки следует задавать углом α и наименьшей шириной b, при этом размер ширины b будет зависеть только от размера площадки инструмента. Размеры большей ширины канавки будут колебаться в зависимости от погрешности глубины врезания и величины допуска на внешний диаметр детали. При размерах не более 160 мм глубину
37

кольцевых канавок желательно задавать диаметром d (рис. 2.27).
Рис. 2.26. Пример указания на конусной поверхности отверстия наибольшего диаметра и угла, позволяющего быстро произвести настройку оборудования, выбрать нужный инструмент без дополнительных пересчетов, не сужая поля допусков
Рис. 2.27. Пример рациональной простановки размеров на кольцевые канавки
При указании размеров на длинномерных деталях из профилей с криволинейным контуром рекомендуется давать развертку, что значительно упрощает изготовление деталей при механической обработке
(рис. 2.28).
Рис. 2.28. Простановка размеров на развертке длинномерных гнутых деталей
38
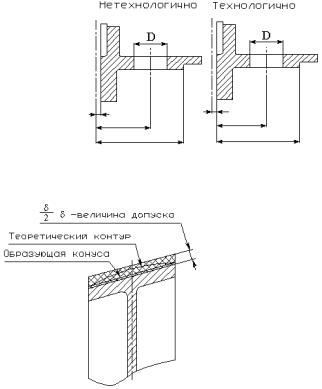
Простановка размеров от реально не существующей линии построения нежелательна. Это вызывает необходимость пересчета размеров при программировании обработки и контроле детали. Рекомендуется размеры задавать от реально существующих плоскостей и ли-
ний (рис. 2.29).
Рис. 2.29. Рациональное задание размеров от реально существующих поверхностей детали
Рис. 2.30. Пример задания поверхности плоскостями или телами вращения с прямолинейной образующей.
Не рекомендуется в размерах механически обрабатываемых деталей делать ссылку на плазовую увязку. В случае, если аэродинамический контур мало отличается от обычных геометрических форм (иногда в пределах поля допуска), следует задавать поверхности плоскостями или телами вращения с прямолинейной образующей (рис. 2.30).
При простановке размеров на подсечке у длинномерных деталей не следует задавать размеры от теоретического контура. Размеры должны быть проставлены от наивысшей плоскости полки так, чтобы легко можно было определить размеры подсечек, толщину полок и общую толщину исходной заготовки (рис. 2.31).
На рис. 2.32 показана простановка размеров, не обеспечивающая и
39
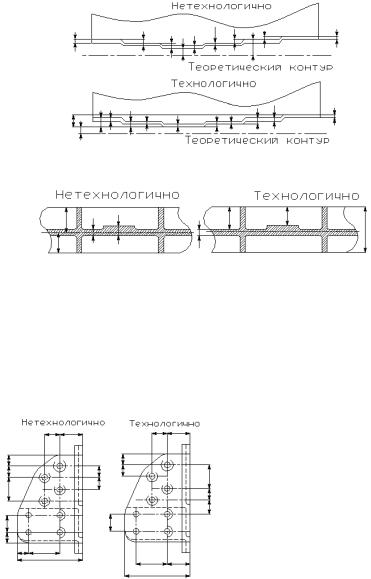
обеспечивающая замер элементов конструкции прямым методом без пересчетов на величину колебаний высоты детали в поле допуска.
Рис. 3.31. Задание размеров на подсечке длинномеров
Рис. 2.32. Схема рациональной простановки размеров с использованием принципа совмещения конструкторской и измерительной баз
Координаты отверстий следует задавать от одной базы, если конструкторские и технологические базы совпадают (рис. 2.33, 2.34). На рис. 2.34, слева, показана деталь, отверстия которой закоординированы и от кромок детали, и от оси. В этом случае требуется применение нескольких кондукторов с различными базами. На этом же рисунке справа приведена деталь, отверстия которой могут быть изготовлены в одном кондукторе.
Õ Рис. 2.33. Пример неудачной простановки координат отверстий – отверстия закоординированы от разных технологических баз
На деталях, у которых базой может служить отверстие, расположенное по оси, или наружная цилиндрическая поверхность, координа-
40
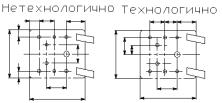
цию остальных отверстий целесообразно производить по окружности
(рис. 2.35).
Рис. 2.34. Пример неудачной простановки координат отверстий – отверстия закоординированы от кромки и от оси Ö
а
б
Рис. 2.35. Рациональная координация отверстий относительно базового отверстия (а) и развитой цилиндрической части (б)
В крупногабаритных тонкостенных деталях с поверхностями вращения (диаметры свыше 500 мм) размер толщины стенки рекомендуется задавать (рис. 2.36):
–наружным и внутренним диаметром со свободными размерами, когда колебания толщины стенки конструктивно допускаются;
–диаметром и толщиной стенки, когда толщину стенки необходимо выполнить в более жестких пределах. При этом допуск на толщину стенки задавать не ниже 14-го квалитета точности.
Вслучае нетехнологичной простановки размеров допуск на толщину стенки 0,12 мм требует выполнения с полем допуска 0,24 мм, которое находится между полем допуска 9-го и 10-го квалитета точности. Выполнение тонкостенных крупногабаритных деталей с такой точностью вызывает большие производственные трудности.
41

Простановку размеров необходимо проводить только между обрабатываемыми поверхностями или только между необрабатываемыми с увязкой их с базовыми поверхностями (рис. 2.37).
Рис. 2.36. Рациональная простановка размеров крупногабаритных тонкостенных тел вращения
Рис. 2.37. Примеры увязки размеров поверхностей с базовыми поверхностями
На рис. 2.38 слева изображен фитинг, у которого обрабатываемая плоскость отдалена от необрабатываемой на 1 мм. По нормали толщина стенки может колебаться в пределах ±1,2 мм, в этом случае обрабатываемая и необрабатываемая поверхности могут быть выполнены как одно целое, что значительно увеличит объем механической обработки.
При простановке размеров между обрабатываемой и необрабатываемой поверхностями номинальный размер должен быть больше, чем
42
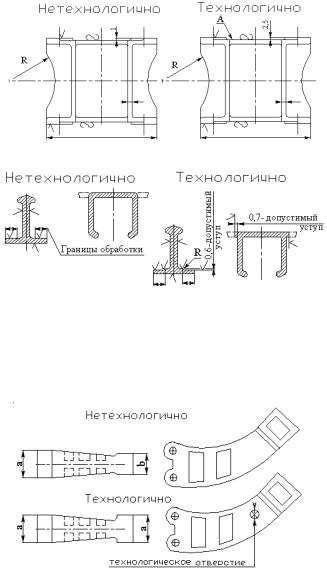
допуск на заготовку. При разделении обрабатываемой поверхности от необрабатываемой или обрабатываемых с разных установов на чертеже следует обозначать уступ и оговаривать величину перепада радиуса R галтели (рис. 2.39).
Рис. 2.38. Рациональные назначение размера ступеньки
Рис. 2.39. Рациональное назначение высоты уступа между обрабатываемой и необрабатываемой поверхностями
При проектировании сложных деталей необходимо предусматривать технологические базы (например, плоскости одного уровня, отверстия и т.д.), что удешевляет оснастку, улучшает качество обработки и снижает ее трудоемкость (рис. 2.40).
Рис. 2.40. Создание специальных технологических баз на детали
43

В чертежах заготовок в случае необходимости рекомендуется предусматривать технологические приливы с отверстиями для установки и ориентации заготовок на станке, что повысит качество деталей, сократит сроки технологической подготовки и снизит расходы по оснастке (рис. 2.41). После удаления технологических приливов размеры целесообразно проставлять, предусматривая уступы.
Рис. 2.41. Создание впоследствии удаляемых технологических приливов с базирующими отверстиями
Назначение точности размеров и шероховатости обрабатываемых поверхностей
Точность размеров деталей непосредственно влияет на трудоемкость механической обработки: с увеличением точности детали резко возрастает трудоемкость (см. рис. 2.42).
Рис. 2.42. Связь относительной себестоимости с допуском на изготовление деталей [3]
Наиболее экономичными будут детали, у которых меньшее количество поверхностей, обрабатываемых с повышенной точностью, что достигается при использовании различных конструктивных мер, ведущих к увеличению допусков, но не ухудшающих эксплуатационные качества изделия.
Повышение точности ведет к увеличению производственного цикла, применению оборудования, приспособлений, мерительного инструмента повышенной точности, более быстрому износу режущего инструмента и привлечению квалифицированной рабочей силы. Конструктивные и технологические решения, связанные с обеспечением заданных точностей параметров деталей, должны быть выполнены наи-
44