
- •Стали
- •Магниевые сплавы
- •Титановые сплавы
- •Алюминиевые сплавы
- •2.1. Технологичность заготовок
- •Горячештампованные заготовки
- •Литые заготовки
- •Простановка размеров
- •Технологичность основных элементов конструкции деталей
- •Открытые плоскости
- •Сопрягаемые плоскости (колодцы, карманы, пазы, гнезда)
- •Наружные поверхности вращения
- •Внутренняя резьба
- •Фасонные поверхности
- •Монолитные панели
- •Панели, изготовляемые из плит
- •Панели из горячештампованных заготовок
- •Панели из горячепрессованных заготовок
- •Панели из специального литья
- •Крупногабаритные детали из алюминиевых и магниевых сплавов
- •Балки и лонжероны
- •Детали узлов поворота
- •Шпангоуты, рамы и их детали
- •Длинномерные детали из прессованных профилей
- •Фитинги и кронштейны
- •Рычаги и качалки
- •Фланцы и крышки
- •ЛИТЕРАТУРА

стий. Изменение формы этих выемок на цилиндрическую позволяет заменить трудоемкое фрезерование фрезой малого диаметра обработкой зенкерованием.
Рис. 2.139. Нетехнологичность конструкции кронштейна, обусловленная наличием закрытых фасок отверстий
Рис. 2.140. Изменение формы выемок для замены фрезерования более производительным зенкерованием
Аналогично этому для применения производительного процесса торцевого фрезерования целесообразно предусматривать в конструкциях кронштейнов и фитингов большее количество открытых бесступенчатых плоскостей.
Конструкция фитингов и кронштейнов может быть весьма сложной, причем для облегчения детали этого типа имеют различные выборки, затрудняющие базирование при обработке. При отсутствии необходимых конструктивных элементов, которые могли бы быть использованы для базирования (протяженных плоскостей – установочной базы, классных отверстий – двойной опорной или двойной направляющей базы и т.п.) в заготовке необходимо предусматривать временные технологические базы (платики, поверхность которых образует плоскость, отверстия), удаляемые после завершения механической обработки.
Рычаги и качалки
Детали данного типа изготавливаются из стали, алюминиевых, магниевых и титановых сплавов. Основными видами заготовок для рычагов и качалок являются штамповки и литье. Однако заготовки для рычагов и качалок сложной конфигурации, например, из труднообра-
99

батываемых материалов (жаропрочных сталей, титановых сплавов), рациональнее изготавливать не горячей штамповкой, а точным литьем (рис. 2.141). Это повышает коэффициент использования металла с 0,3 до 0,7–0,9 и значительно снижает трудоемкость механической обработки.
а
б
Рис. 2.141. Снижение трудоемкости изготовления деталей сложной формы за счет замены штампованной заготовки литьем
Сложная конструкция рычагов и качалок в некоторых случаях может быть выполнена сварной, как это показано на рис. 2.4, 2.5.
Механическая обработка заготовок рычагов и качалок должна быть сведена, в основном, к разделке отверстий под подшипники, болты, втулки и частично – к фрезерованию плоскостей сопряжения. При этом обрабатываемые поверхности рекомендуется располагать на разных уровнях с необрабатываемыми. Величина уступа должна быть несколько больше допуска на необрабатываемую поверхность, но не менее 0,5 мм (рис. 2.142).
При наличии параллельных плоскостей (сопряжения по концам рычагов и качалок и др.) следует предусматривать возможность обработки набором стандартного режущего инструмента на проход
100

(рис. 2.143).
Рис. 2.142. Образование уступа между обрабатываемыми и необрабатываемыми поверхностями
Рис. 2.143. Технологичный вариант вилки, выполненной фрезерованием на проход набором дисковых фрез
Применение в отверстиях механически обрабатываемых выточек и канавок вынуждает применять для их обработки токарные станки, оснащенные специальными приспособлениями.
Рис. 2.144. Исключение канавки в отверстии рычага
Отверстия в рычагах и качалках под подшипники следует проектировать сквозными, что позволяет применять производительный метод получения точных отверстий – протягиванием (рис. 2.144). Распор подшипников при таком выполнении отверстий может быть обеспечен распорными втулками. С целью сокращения применяемого режущего и мерительного инструмента посадки в отверстиях рычагов и качалок под подшипники должны быть максимально унифицированы. Ушковые и вильчатые элементы в конструкциях рычагов и качалок также необходимо унифицировать с целью применения универсальной переналаживаемой технологической оснастки и высокопроизводительного оборудования (горизонтально-фрезерные и протяжные станки).
101

Фланцы и крышки
Фланцы и крышки изготавливают из черных и цветных металлов. В качестве исходных заготовок применяются горячие штамповки, отливки, прутки, трубы и др.
Фланцы и крышки сложных форм целесообразнее выполнять из отливок, полученных, в частности, методами точного литья. Некоторые типы фланцев и крышек лучше проектировать сварными или изготовленными из листа методом холодной штамповки (рис. 2.145).
а
б
Рис. 2.15. Примеры технологичных конструкций фланца (а) и крышки (б), изготовленных из листового материала
Для снижения трудоемкости цековку отверстий на торце фланца и крышки следует заменять сплошной подрезкой торца.
У фланцев втулок ступенчатой формы цилиндрические поверхности должны по возможности располагаться в порядке возрастания размеров от одного торца к другому (рис. 2.146, а); радиусы в местах сопряжений ступенчатых цилиндрических поверхностей рекомендуется делать одинаковыми (рис. 2.146, б); что уменьшает номенклатуру применяемого режущего инструмента.
102

Во фланцах и крышках с глухими резьбовыми отверстиями (рис. 2.147) рекомендуется предусматривать для выхода инструмента вместо канавок сбег резьбы, исключающий необходимость обработки канавок. В глухих отверстиях, обрабатываемых осевым инструментом (сверлом, зенкером, разверткой), следует предусматривать длину отверстия с учетом заборной части инструментов.
а |
б |
Рис. 2.146. Технологичное оформление фланцев и крышек с ступенчатыми цилиндрическими поверхностями
Рис. 2.147. В глухом отверстии под резьбу должны быть предусмотрены сбег и длина заборной части осевого инструмента
Шлицевые отверстия во фланцах не должны иметь внутренних выточек. Это обеспечивает безударную работу инструмента и уменьшает частоту его поломок (рис. 2.148).
103
Рис. 2.148. Выточки в шлицевых отверстиях, ухудшающие качество обрабатываемой поверхности и приводящие к поломке протяжного инструмента
2.4. Пример анализа технологичности особо ответственной детали вертолета
Проанализируем с точки зрения технологичности деталь «Фитинг» (рис. 2.149). Наличие карманов, колодцев, ребер жесткости, сложного контура, классного и большого числа крепежных отверстий делают предпочтительной обработку детали на станках с ЧПУ.
Рассмотрим размерное описание детали.
Согласно техническим условиям на деталь теоретический контур следует брать по шаблонам, снятым с плаза. Но для программирования УЧПУ необходимо знать координаты всех точек контура относительно заданных баз. Отсутствие этих размеров делает необходимым пересчет кривых, снятых с шаблонов, в координаты опорных точек и параметры соединяющих их сплайнов (в зависимости от применяемого типа интерполяции), отработка которых заложена в УЧПУ.
Измерение размера 48 между центром отверстия 41 и осью шпангоута 3Н затруднительно, т. к. он проставлен от не существующей на детали поверхности.
В сечении Д – Д дан размер, указывающий толщину стенки. Этого недостаточно – должен быть показан размер всех её частей, а не только крайней левой части.
Указание технических условий о необходимости брать теоретический контур по шаблонам, снятым с плаза, следует пересмотреть, рассчитать координаты опорных точек, уравнения кривых между ними и описать их теми функциями, которые имеются в применяемой системе управления ЧПУ (линейная, круговая или параболическая интерполяция).
Рассмотрим конструкцию детали с точки зрения технологии обработки.
Деталь имеет сложную форму. Средняя часть детали жесткая с центральным классным отверстием 41. Отверстие сквозное, l/D = 2, точность – 8-ой квалитет, шероховатость поверхности Ra1,6. Точность и шероховатость отверстия обеспечиваются стандартными технологическими приемами.
Отверстие 41 может быть использовано в качестве центрирующей (двойной опорной) базы, лишающей заготовку двух степеней свободы. Оно же может быть использовано и в качестве двойной направляющей базы (4 степени свободы), т. к. l/D = 2. Вопрос об использовании её в качестве той или иной базы надо решать при проектировании технологического процесса в конкретных условиях.
104
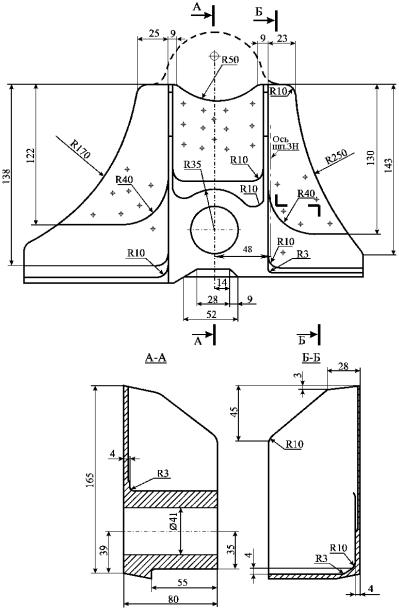
Рис. 2.149. Эскиз фитинга
Если использовать схему базирования «установочная база – двойная опорная база – опорная база» (на плоскость и два отверстия), то в
105
качестве установочной базы может быть использована поверхность А, лишающая заготовку трех степеней свободы. Недостатком этой поверхности является малая толщина, что наложит ограничения на режимы обработки, усложнит схему приложения зажимного усилия из-за недопустимости возникновения деформаций под действием сил зажима. Двойной опорной базой (лишает двух степеней свободы) может служить отверстие Б. Удобной точки в детали для лишения шестой степени свободы нет, т. к. все поверхности требуют обработки. В качестве такой точки можно было бы выбрать поверхность колодца, но он расположен очень близко к центральному отверстию. Эта особенность конструкции ухудшает технологичность детали. В данном случае следует создать искусственную технологическую базу – точку, возможно дальше удаленную от двойной опорной базы – отверстия Б. Для этого можно выполнить второе базовое отверстие на центральной оси симметрии детали над радиусной выкружкой R50. Таким образом будет материализована стандартная схема базирования, характерная для корпусных деталей: базирование детали по плоскости А и двум отверстиям – на один цилиндрический и второй срезанный пальцы. После обработки искусственная технологическая база легко удаляется фрезерованием с образованием свободной несопрягающейся поверхности
R50.
С точки зрения обеспечения геометрической точности обработка наружного контура детали не представляет затруднений, т. к. контур образован радиусными и прямолинейными участками. Однако толщина фрезеруемого контура накладывает дополнительные ограничения на режимы фрезерования, повышает требования к качеству заточки, тщательности наблюдения за износом инструмента и своевременностью его замены. Увеличение сил резания может привести к смятию кромки контура и образованию больших заусенцев. Этот факт ухудшает технологичность обработки наружного контура детали.
Наличие глухого колодца глубиной 45 мм без свободного входа инструмента требует дополнительного сверления отверстия для входа фрезы. Кроме этого, на чертеже детали не указан радиус сопряжения боковых стенок с дном колодца. Этот элемент детали также является не технологичным.
Боковые поверхности карманов (полостей между ребрами) являются не технологичными ввиду того, что фрезерование с глубиной >80 мм представляет определенные трудности. Дополнительно это осложнено малой толщиной ребер – 4 мм.
Крепежные отверстия 2,5 в малке (вид не показан) не перпендикулярны её поверхности. Это вызовет затруднения при сверлении, т. к. необходимо применение специального кондуктора, предотвращающего увод и поломку сверл.
В детали отсутствует симметричность правой и левой частей, что
106