
ДМ / Розрахунок та конструювання зубчастих передач (2)
.pdf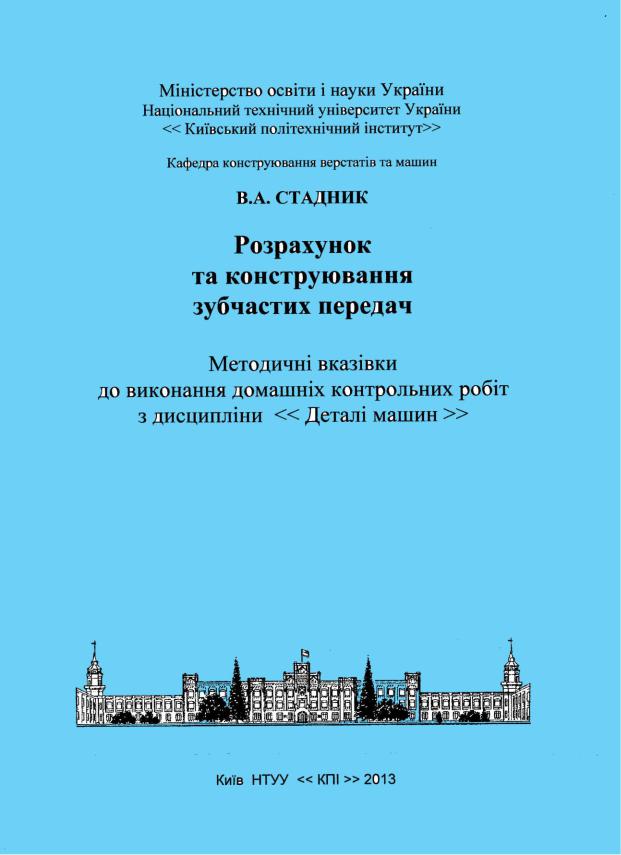
Міністерство освіти і науки України
Національний технічний університет України << Київський політехнічний інститут >>
Кафедра конструювання верстатів та машин
В.А. СТАДНИК
РОЗРАХУНОК ТА КОНСТРУЮВАННЯ ЗУБЧАСТИХ ПЕРЕДАЧ
Методичні вказівки
до виконання домашніх контрольних робіт з дисципліни “Деталі машин”
для студентів машинобудівних спеціальностей усіх форм навчання
Затверджено Вченою Радою Механіко-машинобудівного інституту НТУУ “КПІ” Протокол № 8 від 26 березня 2013 р.
Київ НТУУ <<КПI>> 2013
1
Розрахунок та конструювання зубчастих передач : Методичні вказівки до виконання домашніх контрольних робіт з дисципліни “Деталі машин” для студентів машинобудівних і механічних спеціальностей усіх форм навчання : Електронне навчальне видання /Уклад.:В.А.Стадник-К.: НТУУ << КПІ >>2013.112с.
Розрахунок та конструювання
зубчастих передач
Укладач: В. А. Стадник, канд. техн. наук. доц.
Відповідальний Редактор: Ю.М. Кузнєцов, докт.техн.наук,проф.
Рецензенти: Ю.М.Данильченко, докт. техн. наук, проф. Ю.П. Горбатенко, ст. викл.
© НТУУ << КПІ>> , 2013
© В.А. Стадник, 2013
2
Вступ
Вивчення курсу “Деталі машин” супроводжується практичними заняттями,
важливу роль у яких відіграє самостійне виконання студентами домашніх контрольних робіт. Це сприяє глибшому засвоєнню матеріалу, прищеплює студентам уміння самостійно і творчо розв’язувати інженерно-технічні задачі,
а також готує їх до виконання курсового проекту, захистом якого закінчується вивчення курсу “Деталі машин”.
Ці та видані раніше методичні вказівки [1-2] і спеціальна література [3 –
15] сприятимуть досягненню означеної мети.
В основу методичних вказівок покладено міждержавний стандарт ГОСТ 21354 – 87 на розрахунок зубчастих передач та ДСТУ 2330 – 93 і
ДСТУ 2825 – 94, які донині не знайшли відображення в підручниках і навча-
льних посібниках для вищих навчальних закладів України.
Уведено спрощення стандартної методики розрахунку зубчастих передач,
які мало впливають на результати розрахунку в більшості випадків практики.
Враховуючи відсутність відповідної літератури, позначення коефіцієнтів за старим стандартом ГОСТ 21354 – 75, які мають такий же смисл, але інші поз-
начення ніж у чинному стандарті ГОСТ 21354 – 87, збережено, а нові коефіці-
єнти введено відповідно до існуючого стандарту.
Особливу увагу приділено визначенню допустимих напружень, яке суттєво відрізняється від попереднього стандарту ГОСТ 21354 – 75 і в більшій мірі відповідає міжнародним стандартам ISO.
У методичних вказівках використано українську технічну термінологію,
затверджену ДСТУ 2330 – 93 і ДСТУ 2825 – 94.
3
1. Вибір матеріалів і термічної обробки зубчастих коліс
Основними матеріалами для виготовлення зубчастих є якісні вуглецеві конструкційні сталі (міждержавний стандарт ГОСТ 1050 – 74) та леговані конструкційні сталі (міждержавний стандарт ГОСТ 4543 – 71), які допускають зміцнювальну термічну (ТО) або хіміко-термічну обробку (ХТО). Сталеві зубчасті колеса забезпечують високу несучу здатність та довговічність зубчастих передач.
Вибір марки сталі та її ТО залежать від допустимих габаритних розмірів, навантажувальної здатності, вартості, а також від технічного рівня виробництва та кількості виготовлюваних коліс. Залежно від твердості робочих поверхонь зубців після ТО зубчасті колеса відносять до двох основних груп:
1.Колеса із твердістю робочих поверхонь Н 350 НВ. Таку твердість одержують після (ТО) нормалізації або поліпшення, гартування з високотемпературним відпуском. Зубці нарізають після кінцевої ТО.
2.Колеса із твердістю робочих поверхонь зубців Н > 350 НВ. Ці колеса застосовують для високонавантажених зубчастих коліс відносно невеликих розмірів. Зубці нарізають до ТО або ХТО (об’ємне та поверхневе гартування струмом високої частоти (СВЧ), цементація, нітроцементація, азотування). Застосування після нарізування зубців ТО або ХТО спричиняє короблення зубців та викривлення їх профілів. Тому для виправлення форми зубців потрібні додаткові дорогі фінішні операції (шліфування, притирання за допомогою спеціальних паст та ін.). Це призводить до значного збільшення вартості коліс другої групи порівняно з вартістю коліс першої групи. Крім того, зубчасті колеса з високою твердістю погано припрацьовуються, що вимагає підвищеної точності виготовлення та монтажу передачі, значно більшої жорсткості валів та їхніх опор.
Ці труднощі простіше подолати в умовах великосерійного та масового виробництва зубчастих коліс, де значно легше окупаються спеціальні обладнання, інструменти, верстати.
В умовах індивідуального і дрібносерійного виробництва, передбаченого технічними завданнями (ТЗ) на курсовий проект, у мало- і середньонавантажених передачах, якщо не ставляться жорсткі вимоги до габаритних розмірів передач, а також у передачах з великими колесами (відкритих) застосовують
зубчасті колеса з твердістю матеріалу Н 350 НВ. При цьому забезпечується можливість чистового нарізування зубців після ТО, висока точність виготовлення і добре припрацьовування. Для рівномірного спрацьовування зубців і ліпшого їх припрацьовування твердість шестірні НВ1 назначається більшою від твердості колеса НВ2. Різниця середніх твердостей робочих поверхонь зубців шестірні і колеса в передачах з прямими і непрямими зубцями:
НВ1с НВ2с = 20…50, |
(1.1) |
де НВ1с і НВ2с–середні твердості шестірні і колеса (визначаються як середнє арифметичне граничних значень твердості вибраних матеріалів).
4
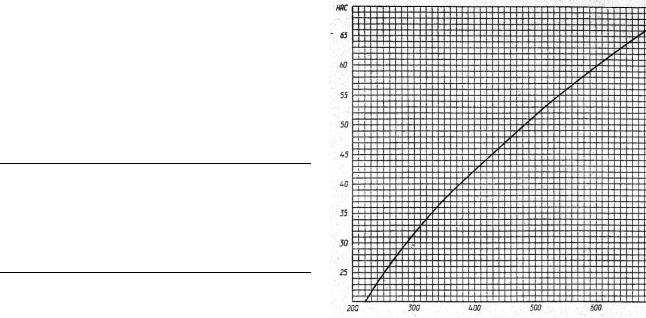
У ряді випадків для збільшення навантажувальної здатності передачі, зменшення її габаритів і металомісткості досягають різниці середніх твердостей
НВ1с НВ2с 70.
Твердість робочих поверхонь зуб-
ців колеса НВ2с 350 НВ, а зубців шестірні НВ1с 350 НВ; вимірюють за шкалою Роквелла, якщо вона більша 45 HRC. Співвідношення твердостей в одиницях НВ і HRC визначають за графіком (рис.
1.1).
Механічні характеристики деяких ма-
рок сталей, які використовуються для виготовлення зубчастих коліс, наведено у табл. 1.1, а основні розміри заготовок зображено на рис. 1.2.
_____________________________
Рис. 1.1. Графік співвідношення твердостей, виражених в одиницях НВ і HRC
Таблиця 1. Механічні характеристики деяких сталей для зубчастих коліс редукторів загального призначення.
|
Найбільший розмір |
|
Твердість заготовки |
Границя |
|||
Марка |
|
плиннос- |
|||||
заготовки |
Термообробка |
|
|
||||
сталі |
|
|
ті σп, |
||||
|
|
|
поверхні |
серцевини |
|||
|
Дгр, мм |
Sгр, мм |
|
МПа |
|||
|
|
|
|
||||
1 |
2 |
3 |
4 |
5 |
6 |
7 |
|
35 |
Будь-який |
Будь-який |
Нормалізація |
163…192НВ |
163…192НB |
270 |
|
40 |
120 |
60 |
Поліпшення |
192…228 HВ |
192…228Н |
400 |
|
|
Будь-який |
Будь-який |
Нормалізація |
179…207 НВ |
179…207 НВ |
320 |
|
45 |
125 |
80 |
Поліпшення |
235…262 НВ |
235…262 НВ |
540 |
|
|
80 |
50 |
Поліпшення |
269…302 НВ |
296…302 НВ |
650 |
|
|
280 |
125 |
Поліпшення |
235…262 НВ |
235…262 НВ |
640 |
|
40Х |
125 |
80 |
Поліпшення |
269…302 НВ |
269…302 НВ |
750 |
|
125 |
80 |
Поліпшення та |
45…50 HRC |
269…302 НВ |
750 |
||
|
|||||||
|
гартування СВЧ |
||||||
|
|
|
|
|
|
||
|
315 |
200 |
Поліпшення |
235…262 НВ |
235…262 НВ |
630 |
|
40ХН |
200 |
125 |
Поліпшення |
269…302 НВ |
269…302 НВ |
750 |
|
200 |
125 |
Поліпшення та |
48…53 HRC |
269…302 НВ |
750 |
||
|
|||||||
|
гартування СВЧ |
||||||
|
|
|
|
|
|
||
|
315 |
200 |
Поліпшення |
235…262 НВ |
235…262 НВ |
670 |
|
35ХМ |
200 |
125 |
Поліпшення |
269…302 НВ |
269…302 НВ |
790 |
|
200 |
125 |
Поліпшення та |
48…53 HRC |
269…302 НВ |
790 |
||
|
|||||||
|
гартування СВЧ |
||||||
|
|
|
|
|
|
||
40ХНМА |
125 |
80 |
Поліпшення та |
50…56 HRC |
269…302 НВ |
980 |
|
азотування |
|||||||
|
|
|
|
|
|
||
|
|
|
|
|
Продовження табл. 1.1. |
||
|
|
|
|
|
|
|
5
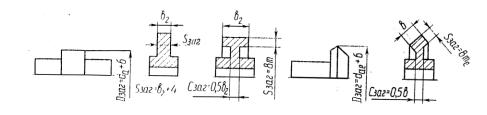
1 |
2 |
3 |
4 |
5 |
6 |
7 |
|
20Х |
|
|
|
|
|
|
|
20ХНМ |
|
|
|
|
|
|
|
18ХГТ |
200 |
125 |
Цементація |
56…63 HRC |
300…400 НВ |
800 |
|
12ХНЗА |
|
|
|
|
|
|
|
25ХГНМ |
|
|
|
|
|
|
|
25ХГМ |
200 |
125 |
Нітроцемента- |
58…63 HRC |
300…400 НВ |
800 |
|
25ХГТ |
ція |
||||||
|
|
|
|
|
|||
|
|
|
|
|
|
|
Для одержання при термічній обробці прийнятих для розрахунку механічних характеристик матеріалів коліс потрібно, щоб розміри заготовок коліс (Дзаг, Sзаг) не перевищували гранично допустимих значень Дгр, Sгр (табл. 1.1):
Дзаг Дгр; Sзаг Sгр, |
(1.3) |
де Дзаг – діаметр заготовки шестірні або черв’яка; Sзаг – товщина заготовки обода або диска колеса; Дгр – гранично допустимий діаметр шестірні або черв’яка; Sгр – гранично допустима товщина заготовки обода або диска колеса.
При суцільних дисках коліс Sзаг = b2.
Рис. 1.2. Основні розміри заготовок зубчастих коліс і черв’яка
Для виготовлення шестірні та колеса можна брати однакові або різні марки сталей. У табл. 1.2 наведено рекомендації щодо вибору різних варіантів матеріалів для шестірні і колеса та доцільних видів ТО і твердості.
Таблиця 1.2. Рекомендації щодо вибору варіантів матеріалів для шестірні та колеса
Ва |
|
Шестірня |
|
|
|
|
|
Колесо |
|
|
рі- |
Марка сталі |
Термообробка |
|
Твердість |
Марка сталі |
Термообробка |
Твердість |
|||
ант |
|
|||||||||
|
|
|
|
|
|
|
|
|
||
1 |
40Х,45, |
Поліпшення |
|
269…302 НВ |
40Х, |
|
45, |
Поліпшення |
235…262 НВ |
|
40ХН |
|
40ХН |
|
|
||||||
|
|
|
|
|
|
|
|
|||
2 |
40Х, 40ХН, |
Поліпшення |
та |
40…53 HRC |
40Х, |
40ХН, |
Поліпшення |
269…302 НВ |
||
35ХМА |
гартування СВЧ |
35ХМА |
|
|||||||
|
|
|
|
|
||||||
|
40Х, 40ХН, |
Поліпшення |
та |
|
40Х, |
40ХН, |
Поліпшення |
|
||
3 |
45…53 HRC |
та гартування |
45…53 HRC |
|||||||
35ХМ |
гартування СВЧ |
35ХМ |
|
|
||||||
|
|
|
|
СВЧ |
|
|||||
|
|
|
|
|
|
|
|
|
||
|
|
Поліпшення, |
|
|
40Х, |
40ХН, |
Поліпшення |
|
||
4 |
20Х, 20ХНМ |
цементація та |
|
57…63 HRC |
та гартування |
45…53 HRC |
||||
|
35ХМ |
|
|
|||||||
|
|
гартування |
|
|
|
|
СВЧ |
|
||
|
|
|
|
|
|
|
|
|||
|
|
Поліпшення, |
|
|
20Х, |
|
|
Поліпшення, |
|
|
5 |
20Х, 20ХНМ |
цементація |
та |
56…63 RC |
|
|
цементація та |
56…63 НRC |
||
20ХНМ |
|
|||||||||
|
|
гартування |
|
|
|
гартування |
|
|||
|
|
|
|
|
|
|
|
6
2. Визначення допустимих напружень
Міждержавний стандарт ГОСТ 21354 – 87 рекомендує такі розрахунки зубців передач:
а) на контактну витривалість з метою попередження втомного викришування активних поверхонь зубців;
б) на контакту міцність під час дії максимального навантаження для попередження залишкової деформації або крихкого руйнування поверхневого шару;
в) на витривалість при згині для попередження втомного злому зубців; г) на міцність при згині максимальним навантаженням для захисту зубців від залишкової деформації або крихкого злому.
Суттєвий вплив на значення допустимих напружень має характер зміни навантаження зубчастих коліс у часі, який оцінюється еквівалентним числом циклів напружень.
За постійного режиму навантаження еквівалентне число циклів напружень не залежить від навантаження і відповідає дійсному числу циклів навантаження за строк служби зубчастої передачі, тобто
NHE NK 60 n t,
де n – частота обертання колеса, хв-1; t – строк служби передачі, год.
На практиці в більшості випадків роботи зубчастої передачі має місце змінний у часі режим навантаження. В цьому випадку еквівалентне число циклів напружень залежить як від значення змінних навантажень, так і від характеру зміни їх у часі.
Згідно з ГОСТ 21354 – 87 існує три методи врахування змінних у часі навантажень:
1)метод еквівалентного числа циклів;
2)метод еквівалентних моментів;
3)метод еквівалентних напружень.
У практиці курсового проектування найчастіше використовують метод еквівалентного числа циклів. Використання цього методу орієнтовано на приведення змінного навантаження до двох і більше ступенів циклограми режимів навантаження за весь строк експлуатації зубчастої передачі (рис. 2.1), які виявляють найбільшу пошкоджуючи дію на передачу.
7
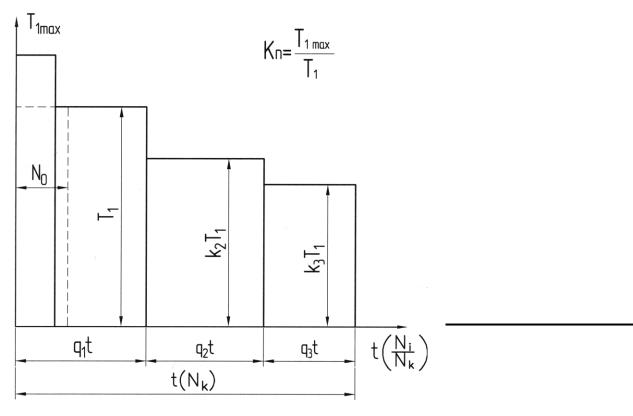
Рис. 2.1. Циклограма навантаження шестірні зубчастої передачі
де: t – строк служби передачі, год; ti – час дії змінних напружень на і-му ступені циклограми, год; Nk – число циклів напружень відповідно до заданого строку служби передачі, Nі – число циклів зміни напружень на і-му ступені циклограми; Ті – найбільший момент з числом циклів зміни напружень не меншим 0,03 NН0 або 5 104 при розрахунку відповідно на контактну міцність і на згин; Тmax > Т1 – максимальний момент з числом циклів зміни на-
пружень N0 меншим 0,03 NН0 |
або 5 104 при розрахунку відповідно на контактну міцність і |
|
на згин, де NН0 – базове число циклів зміни напружень, яке відповідає границі витривалості |
||
на |
контактну |
міцність; |
q і k – коефіцієнти. q |
ti |
= |
Ni |
і k |
|
|
Ti |
. |
k = 1. k2 .......kn < 1 |
|
|
|
|
i |
|
||||||
i |
t |
N |
|
|
|
T1 |
|
|||
|
k |
|
|
|
|
|||||
|
|
|
|
|
|
|
|
|
|
|
Навантаження крутним моментом Тmax > Т1 |
враховують у розрахунках коефіцієнтом пе- |
|||||||||
ревантаження KП = T1 max/T1. |
|
|
|
|
|
|
|
|
2.1.Визначення вихідного розрахункового навантаження
при розрахунку на контакту витривалість
За вихідне розрахункове навантаження беруть найбільше (Т1) із підведених до передачі (див. рис. 2.1), для якого число зміни напружень не менше 0,03 NН0. Розрахунковий момент для колеса визначають за формулою Т2 = Т1 и. Базове число циклів зміни напружень NН0, яке відповідає границі витривалості, визначають за графіком (рис. 2.2) або за формулою
NН0= 30НВ2,4 |
(2.1) |
8
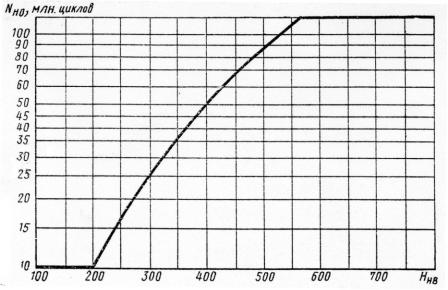
Рис. 2.2. Графік для визначення базового числа зміни напружень NН0
2.2. Визначення еквівалентного числа циклів напружень при розрахунку на контактну витривалість
Еквівалентні числа циклів напружень, відповідні вибраним навантаженням
1 |
і 2 , визначають за формулами (11): |
2.2. |
|
|
для шестірні: 1 1 |
01 |
|
|
для колеса: NHE2 = µH2 |
NH02 |
(2.3) |
де 1 і 2 – коефіцієнти, що враховують характер циклограм навантаження, а 01 і NHO2– базові числа циклів зміни напружень відповідно шестірні і
колеса. Для спрощення розрахунків можна враховувати тільки ту частину циклограми, в якій число циклів навантаження не більше 2 01, 2 .
Послідовність розрахунку коефіцієнтів 1 |
і 2 : |
||||||||||||||||||||||||||
|
|
|
|
|
|
|
|
|
|
|
|||||||||||||||||
Визначають число циклів напружень відповідно до заданого строку |
|||||||||||||||||||||||||||
служби передачі: |
|
|
|
|
|
|
|
|
|
|
|
|
|
|
|
|
|
|
|
|
|
|
|
|
|||
для шестірні 1 |
|
60 n1 |
t : |
|
|
для колеса 2 |
60 n2 t |
||||||||||||||||||||
|
|
|
|
|
|
|
|
|
in |
|
|
3 |
|
|
|
|
i |
|
|
|
|
|
|
|
|||
Якщо |
|
|
|
, то |
|
|
|
|
|
|
|
1i |
|
|
|
|
|
|
|
|
|
|
(2.4) |
||||
1 |
1 |
1 |
|
|
|
|
|
|
|
|
|
|
|
|
|
||||||||||||
|
|
|
|
|
|
1 |
|
|
|
1 |
|
|
|
||||||||||||||
|
|
|
|
|
|
|
|
|
i 1 |
|
|
|
|
|
|
|
|
||||||||||
|
|
|
|
|
|
|
|
|
in |
|
|
|
3 |
|
|
|
i |
|
|
|
|
|
|||||
Якщо |
|
|
|
, то |
|
|
|
|
2i |
|
|
|
|
|
|
(2.5) |
|||||||||||
2 |
2 |
2 |
|
|
|
|
|
|
|
|
|
||||||||||||||||
|
|
|
|
|
|
|
2 |
|
|
|
|
|
2 |
|
|
|
|||||||||||
|
|
|
|
|
|
|
|
|
i 1 |
|
|
|
|
|
|
|
|
де in – повне число ступенів навантаження в циклограмі;
i – число циклів напружень на i му ступені навантаження.
9