
мат_модели_logistics
.pdfГЛАВА 3. ПРОИЗВОДСТВЕННАЯ ЛОГИСТИКА ЛЕКЦИЯ 5
3.1. Общие понятия
Материальный поток на своём пути от первичного источника сырья до конечного потребителя проходит ряд производственных звеньев. Управление материальным потоком на этом этапе имеет свою специфику и носит название производственной логистики.
Целью производственной логистики является оптимизация ма- териальных потоков внутри предприятий. Участников логистическо- го процесса в рамках производственной логистики связывают внут- рипроизводственные отношения.
К производственным логистическим системам можно отнести:
–промышленное предприятие;
–оптовое предприятие;
–узловую грузовую станцию;
–узловой морской порт.
Производственные логистические системы можно рассматри- вать на макро- и микроуровнях. В первом случае производственные логистические системы выступают в качестве элементов макрологи- стических систем. Они задают ритм работы этих систем, являются источником материальных потоков.
На микроуровне производственные логистические системы представляют собой ряд подсистем, находящихся в отношениях и связях друг с другом и образующих определенную целостность: за- купка, склады, запасы, производство, транспорт, информация, сбыт, кадры. Эти подсистемы обеспечивают вхождение материального по- тока в систему, прохождение внутри неё и выход из системы.
Впроизводственной логистике основной задачей является упо- рядочение материальных потоков, которое позволяет сократить:
1) простои станочного оборудования;
2) время межоперационного хранения деталей;
3) затраты труда на изготовление деталей.
Врезультате снижаются общая длительность производственного периода и сумма замороженных на это время средств. Например, по опубликованным данным, в средней автомобильной фирме США согласно статистике запасы деталей, находящихся в изготовлении, составляет примерно 500 долл. в расчете на один выпускаемый авто- мобиль, а в аналогичной японской фирме только 77 долл. за счет ис-
40

пользования более прогрессивной системы управления «Канбан». При математическом моделировании производственного про-
цесса приходится решать большое число задач логистического ха- рактера, например:
–оптимизация состава станочного парка для каждого из произ- водственных участников;
–оптимизация графика запуска деталей в производство;
–расчёт длительности производственного цикла при обработке партии деталей и его сокращение за счет интенсивности;
–оптимизация размера партии деталей;
–оптимизации качества продукции;
– выполнение доставки «точно в срок».
3.2. Толкающие и тянущие системы управления материальными потоками
Управление материальными потоками в рамках производствен-
ных логистических систем может осуществляться двумя различными способами.
Первый вариант носит название «толкающая система» и пред- ставляет собой систему организации производства, в которой пред- меты труда, поступающие на производственный участок, непосред-
ственно этим участком у предыдущего технологического звена не заказываются. Материальный поток «выталкивается» получателю по команде, поступающей на предыдущее звено из центральной систе- мы управления производством (см. рис. 3.1).
Покупатель
заказ
товара
Система управления, формирующая задание для всех отделов и цехов
Склад |
|
|
… |
|
|
Цех |
|
Цех №1 |
Цех № N |
|
|||
сырья |
|
|
|
|
|
сборки |
|
|
|
|
|
|
|
Р и с. 3.1
41
Толкающие модели управления потоками характерны для тра- диционных методов организации производства. Возможность их
применения для логистической организации производства появилась в связи с массовым распространением вычислительной техники. Эти системы, первые разработки которых относятся к 1960 гг., позволили
согласовывать и оперативно корректировать планы и действия всех подразделений предприятия – снабженческих, производственных и сбытовых – с учетом постоянных изменений в реальном масштабе времени. Результаты внедрения таких систем можно образно охарак- теризовать фразой: «Теперь мы можем разработать план производст- ва, на который нам требовались недели, за несколько часов».
На практике реализованы различные варианты толкающих сис- тем, известные под названием МРП (МРП-1, МРП-2). МРП – это планирование потребности в материалах. Эти системы характеризу- ются высоким уровнем оптимизации управления, позволяющим реа- лизовывать следующие основные функции:
–обеспечивать текущее регулирование и контроль производст- венных запасов;
–в реальном масштабе времени согласовывать и оперативно корректировать действия различных служб предприятия — снабжен- ческих, производственных, сбытовых.
В современных вариантах систем МРП решаются также различ- ные задачи прогнозирования. В качестве метода решения задач ши-
роко применяются имитационное моделирование и другие методы исследования операций.
Второй вариант организации логистических процессов на произ- водстве носит название «тянущая система» и представляет собой систему организации производства, в которой детали и полуфабри- каты подаются на последующую технологическую операцию с пре- дыдущей по мере необходимости (см. рис. 3.2). Здесь центральная система управления не вмешивается в обмен материальными пото- ками между различными участками предприятия, не устанавливает для них текущих производственных заданий. Производственная про-
грамма отдельного технологического звена определяется размером заказа последующего звена. Центральная система управления ставит задачу лишь перед конечным звеном производственной технологиче- ской цепи.
На практике к тянущим внутрипроизводственным логистиче- ским системам относят систему «Канбан» (в переводе с японского –
42

карточка), разработанную и реализованную фирмой «Тойота» (Япо- ния). Система «Канбан» не требует тотальной компьютеризации производства, однако она предлагает высокую дисциплину поставок, а также высокую ответственность персонала, так как централизован- ное регулирование внутрипроизводственного логистического про- цесса ограничено. Система «Канбан» позволяет существенно снизить производственные запасы, ускорить оборачиваемость оборотных средств, улучшить качество выпускаемой продукции.
|
|
|
|
|
|
|
заказ товара |
|
|
|
Покупатель |
|
|
||
|
Система управления |
|
|
|
|
|
|
||||||||
|
|
|
|
|
|
|
|
|
|||||||
|
|
|
|
|
|
|
|
|
|
|
|
|
|
|
|
|
|
|
|
|
|
|
|
|
|
|
|
|
|
|
|
|
|
|
|
|
|
|
|
|
|
|
|
|
готовые |
||
|
|
|
|
материал |
заготовка |
|
|
детали |
изделия |
||||||
|
|
|
|
|
|
|
|
|
|||||||
|
Склад |
|
|
|
Цех №1 |
|
Цех № N |
|
|
|
Цех |
|
|
||
|
сырья |
|
|
|
|
|
|
|
сборки |
|
|
||||
|
|
|
|
|
|
|
|
|
|
|
|
|
|
||
|
заказ |
|
на матери- |
заказ на заго- |
|
заказ |
на детали |
|
|
||||||
|
|
|
|
||||||||||||
|
|
|
|
ал |
товку |
|
|
|
|
|
|
|
|
материальный поток
информационный поток
Р и с. 3.2
Тянущая система имеет некоторые преимущества перед тол- кающей, так как персонал отдельного цеха в состоянии учесть гораз- до больше специфических факторов, определяющих размер опти- мального заказа, чем это могла бы сделать центральная система управления.
К сильным сторонам МРП относятся:
1)уменьшение объёмов запасов, что даёт экономию денег, пло- щадей, складских работ;
2)повышение скорости оборачиваемости запасов;
3)повышение качества обслуживания потребителей, поскольку нет задержек, вызываемых нехваткой материала.
43
Таким образом, МРП улучшает общие показатели деятельности организации:
–коэффициент использования оборудования;
–производительность;
–качество обслуживания;
–скорость реагирования на изменившиеся рыночные условия. К недостаткам МРП можно отнести:
1) большой объём информации и необходимых вычислений, на-
личие сложных систем;
2)отсутствие резерва для покрытия ошибок, то есть не преду- смотрено страхование запаса;
3)негибкость.
3.3. Качественная и количественная гибкость производственных процессов
Производство в условиях рынка может укрепить свои позиции лишь в том случае, если оно способно быстро реагировать на изме- нение спроса. До 70-х гг. XX века предприятия решали эту задачу за счёт наличия на складах запасов готовой продукции. В настоящее время логистика предлагает адаптироваться к изменяющимся усло- виям за счёт запаса производственных мощностей.
Запас производственной мощности возникает при наличии каче- ственной и количественной гибкости производственных систем. Ка-
чественная гибкость обеспечивается за счёт наличия универсального обслуживающего персонала и гибкого производства.
Количественная гибкость может обеспечиваться за счёт резерва рабочей силы и резерва оборудования. В условиях конкуренции по- ступление заказов от потребителей является непредсказуемым и мо- жет изменяться, т.е. возрастать и уменьшаться и приобретать новые качества. Удовлетворять такие колебания потребительского спроса только за счёт наличия товарных запасов невозможно.
Основная задача логистики на производстве – это организация движения материальных потоков между производственными едини- цами с тем, чтобы минимизировать производственные издержки. Однако существуют такие виды межоперационных запасов, которые не могут быть сведены к нулю, так как они обуславливаются самой сущностью технологического процесса. В этом случае речь должна
44
идти об их наилучшем использовании. Идеальным решением в этом случае является система JIT (just in time) – «точно в срок».
JIT была внедрена как способ сокращения запасов, что позволи- ло некоторым организациям сократить запасы на 90 %. Кроме того, JIT дала ряд других выгод, таких как:
–сокращение площади, на которой выполняются работы (до
40%);
–уменьшение затрат на снабжение (до 15 %);
–снижение инвестиций в запасы и т.д.
Концепция «точно в срок» реализуют и система МРП, и система «Канбан».
45

ГЛАВА 4. МЕТОДЫ СЕТЕВОГО ПЛАНИРОВАНИЯ И УПРАВЛЕНИЯ
ЛЕКЦИЯ 6
Сетевые методы планирования и управления относятся к классу процедур, которые широко используются для решения задач упоря- дочения, координации и оптимального управления сложными ком- плексами работ. Эти методы стали возможными лишь при использо- вании современной электронно-вычислительной техники с примене- нием экономико-математических методов.
Сетевые методы представляют комплекс работ, направленных на достижение намеченной цели, реализуются в виде сетевого графика, отображающего взаимосвязь между отдельными работами, парамет- ры и последовательность выполнения работ.
4.1. Элементы сетевого графика
Сетевой график представляет собой ориентированный ациклич- ный граф, в котором дуги соответствуют работам комплекса, а вер- шины событиям.
Графом G (x,u) |
называется объект, |
представленный множест- |
||||
вом вершин x |
и множеством связей между вершинами u . Один из |
|||||
способов представления графа – графический (рис. 4.1). |
|
|||||
Вершины |
графа обозначаются |
|
|
|
|
|
прямоугольниками |
или кружками, |
1 |
|
|
3 |
|
связи между ними – стрелками. На- |
|
|
|
|
||
|
|
|
|
|||
правленную связь называют дугой, а |
|
|
|
|
||
граф, имеющий только направленные |
|
|
|
|
||
связи, называют ориентированным. |
|
|
|
|
||
Если направление связи не игра- |
2 |
|
|
4 |
||
|
|
|||||
ет роли, вершины соединяют нена- |
|
|
|
|
||
правленными связями – ребрами. |
|
Р и с. 4.1 |
|
|||
Граф, имеющий только ненаправлен- |
|
|
|
|
||
ные связи, называют неориентированным. |
|
|
|
|
Путём в ориентированном графе G называют такую последова- тельность дуг S = (u1,u2 ,...,uk ) , в которой конец каждой предыдущей дуги совпадает с началом следующей.
Иногда каждой дуге ui приписывают некоторое число l (ui ) , на-
46
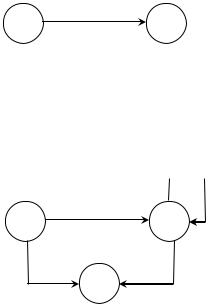
зываемое длиной дуги (или весом дуги). Обычно длины дуги пока- зывают над дугой (рис. 4.2).
|
l (Ui ) |
|
Петлей или циклом называют та- |
|
А |
В |
кую связь, которая начинается и за- |
||
|
||||
|
канчивается в одной и той же вершине |
|||
|
|
|
||
|
Р и с. 4.2 |
|
(рис. 4.3). |
|
|
|
При планировании производст- |
||
|
|
|
венных процессов часто встречаются задачи поиска так называемого критического пути в сетевом графике. Сетевой график представляет собой ориентированный граф, в котором, как правило, одна исходная вершина (обычно подразумевающая начало производственного про- цесса) и одна конечная вершина (её используют для обозначения
окончания производственного процесса). |
|
|
|
|||
|
U4 |
Сетевой график обладает |
||||
U1 |
той особенностью, что все пу- |
|||||
2 |
ти в нем возможны только в |
|||||
1 |
||||||
|
|
одном направлении, а именно, |
||||
U2 |
U3 |
от начальной вершины |
к ко- |
|||
нечной. Каждая вершина соот- |
||||||
3 |
|
|||||
|
ветствует |
некоторому |
этапу |
|||
|
|
производственного |
процесса. |
|||
Р и с. 4.3 |
|
Каждая дуга такого ориенти- |
||||
|
|
рованного |
графа |
показывает |
порядок выполнения этапов. Вес дуги показывает время, требуемое для перехода от одного этапа работ (законченного результата) к дру- гому этапу (законченному результату). В сетевом графике также воз- можны дуги с нулевым весом. Они показывают лишь, что одну работу нельзя выполнить до окончания другой.
Всетевых графиках представляет интерес так называемый кри- тический путь.
Он показывает общее время выполнения всего проекта и наибо- лее важные работы, задержка выполнения которых приводит к срыву срока окончания проекта.
Сетевой график выполняется с соблюдением определённых пра-
вил.
Вчастности, он должен иметь только одно исходное состояние (источник сети) и одно конечное (сток сети) – окончание работы комплекса. Прежде чем строить сети, надо составить подробный список работ комплекса, в отношении каждой работы выяснить её
47
технологические связи с другими работами, место работы в комплек- се, конечные результаты (события) каждой работы.
В сетевом графике дугами изображается работа.
Работа – это определенный процесс, который может иметь раз- личное содержание. Прежде всего , это реальные хозяйственные и технологические процессы, требующие затрат времени и ресурсов для их осуществления. Но под работой подразумеваются и процессы, требующие только затрат времени. Например, сушка материалов, процесс твердения бетона требует не материальных затрат и трудо- вых ресурсов, а определенного времени.
Наконец, работами называют и процессы, не требующие затрат ни времени, ни ресурсов. Это так называемые зависимости или фик- тивные работы. Они показывают, что какое-либо событие не может совершиться раньше какого-либо другого. На сетевых графиках их
изображают пунктирными линиями Событие – это результат (промежуточный или конечный) вы-
полнения одной или нескольких работ. Оно фиксирует момент вре- мени, когда выполнены все работы, входящие в это событие, и могут быть начаты все непосредственно следующие работы. На сетевых графиках события обозначаются кружками либо другими геометри- ческими фигурами.
Различаются следующие терминологические события сетевого графика:
–исходное событие – результат, в отношении которого условно предполагается, что он не имеет предшествующих работ;
–завершающее событие – результат, в отношении которого предполагают, что он является конечной целью выполнения всего комплекса работ;
–начальное событие – событие, непосредственно предшест- вующее данной конкретной работе;
–конечное событие – событие, непосредственно следующее за данной работой.
Путь сетевого графика – любая последовательность работ, свя- зывающая какие-либо два события. При этом пути, связывающие исходное и завершающее события, считаются полными, а все другие пути – неполными. Каждый путь характеризуется своей продолжи- тельностью, которая равна сумме продолжительностей составляю- щих его работ.
Полный путь, имеющий наибольшую продолжительность, назы-
48
вается критическим путем.
Работы и события, лежащие на критическом пути, называются соответственно критическими работами и критическими событиями.
Критический путь – это путь, не имеющий резервов и включаю- щий самые напряженные работы комплекса.
Полная продолжительность выполнения всего комплекса работ, отображенная сетевым графиком, равна продолжительности крити- ческого пути. На графике критический путь выделяется жирной ли- нией.
4.2. Временные параметры сетевого графика
С каждым событием i сетевого графика ассоциируется два сро- ка наступления события: ранний срок наступления события tp (i) и
поздний – tп (i) .
Если принимать i =1, т.е. считать, что номер исходного события равен 1, то tp (1) = 0 . Обозначим продолжительность выполнения ра-
боты (i, j) сетевого графика t (i, j) .
Тогда ранние сроки наступления событий могут быть определе- ны по формуле:
é |
ù |
(4.1) |
tp ( j) = max ëtp (i) + t (i, j)û |
для всех работ (i, j) . Для того, чтобы формализовать процесс вычис- лений, следует пронумеровать события сетевого графика таким обра- зом, чтобы для всех работ (i, j) сетевого графика выполнялось усло- вие i < j . Это может быть достигнуто при использовании следующих правил нумерации:
1)исходному событию присвоить номер 1;
2)пометить все работы, выходящие из пронумерованных собы-
тий;
3) пронумеровать события, в которые входят только помеченные работы.
Пункты 2 и 3 повторять до тех пор, пока не будут пронумерова- ны все события.
Соблюдение приведенных правил при нумерации событий даёт возможность определить по формуле (4.1) значения ранних сроков наступления событий в порядке возрастания их номеров, начиная с
49