
книги / Научные основы технологической подготовки группового производства
..pdf
2.Межцентровые расстояния шпинделей в каждой из головок:
1)в четырехшпиндельной головке минимальное межцентровое расстоя ние 10- мм, максимальное 52 мм;
2) в трехшпиндельной головке минимальное 15 мм, максимальное
65мм;
3)в двухшпиндельной головке минимальное межцентровое расстоя ние 15 мм, максимальное 92 мм;
3.Максимальный вылет шпинделей в любой из головок от общей оси 15 мм.
4.Допустимая высота обрабатываемой детали 100 мм..
5.При подводе головок к обрабатываемым деталям должна быть обес печена их точная фиксация относительно вертикальной оси стола.
6.Подача осуществляется за счет
подъема столика, на котором установ лена обрабатываемая деталь.
7. Настройка станка должна быть простой, доступной сверловщику 3-го разряда и производиться в течение 15—20 мин.
Одновременно с составлением техни ческих условий на проектирование агре гатносверлильного станка технолог под готавливает исходные данные и состав ляет задание конструктору на проекти рование групповых кондукторов для каждой группы деталей.
Перейдем к рассмотрению схемы агре гатносверлильного станка (рис. VI. 61).
На сварном столе 1 установлена плита 2, |
Рис. VI. 61. Схема агрегатносверлиль |
|
в которой закреплена колонка 6. На |
ного станка |
|
колонке на двух радиальных и трех |
|
на нем |
упорных подшипниках вращается корпус 4 с закрепленными |
||
четырьмя головками 5; в случае необходимости на корпусе можно |
устано |
вить до восьми головок. На каждой головке имеется шкив 10, на котором сходятся клиновые ремни 11, идущие от всех шпинделей данной головки.
На колонке 6 в верхней ее части с помощью кронштейна 7 смонтирован электродвигатель 8 мощностью 0,7 кет с числом оборотов 2800 об/мин. На валу электродвигателя закреплен электромагнитный патрон 9, полу чающий питание независимо от электродвигателя. Каждая головка, поворачиваясь, располагается осью своего шкива под осью электромагнит ного патрона. На верхней части каждого шкива находится диск 28, имею щий возможность подниматься вверх на 2—3 мм и смещаться в любую сторону на 1—1,5 мм; боковое смещение предусмотрено на случай несовпа дения осей шкива и электромагнитного патрона.
Первая головка несет на себе четыре шпинделя с минимальным меж центровым расстоянием сверления 10 мм и с максимальным диаметром сверления 3,5 мм. У второй головки имеется два шпинделя с минимальным межцентровым расстоянием 15 мм и с максимальным диаметром сверления 7 мм. Третья и четвертая головки несут по три шпинделя с минимальным межцентровым расстоянием 15 мм и с максимальным диаметром сверления 7 мм. Эти две головки в основном используются для зенкерования отвер стий; для установки зенкеров по высоте они имеют на шпинделях специаль ный регулирующий механизм. На остальных головках в шпинделях имеется винт, который служит опорой для сверл; сверла крепятся в гильзах.
Все шпиндели 16 вращаются в индивидуальных вилках 15. Вилки перемещаются и крепятся на кронштейне 27, который, в свою очередь, прикрепляется к головке. Для перемещения вилок при настройке каждая из них имеет по два винта 25; перемещение производится в двух взаимно перпендикулярных направлениях. Шпиндели в вилках вращаются на шариках, соединяясь через простейший карданный телескопический валик 14 с валиком, вращающимся в верхней части головки и несущим шкив 13.
Для трущихся поверхностей применена капельная смазка веретенным маслом.
Для фиксации головок в рабочем положении на корпусе 4 закреплено кольцо 3 с четырьмя фиксирующими пазами, в которые входит фиксатор 26, установленный на плите 2 и приводимый в движение ножной
педалью 22 или связанной с ней рукояткой 24.
1? |
В целях безопасности и для предохранения от брызг масла, |
||||||||
а также для предохранения вращающихся частей от загрязнения |
|||||||||
w |
|||||||||
каждая головка закрывается литым силуминовым кожухом 12. |
|||||||||
8 |
|
|
Под головкой, |
находящейся в рабо |
|||||
|
|
чем положении, |
вмонтирован в |
плиту |
|||||
|
|
|
|||||||
6 |
|
|
подъемный стол 18, на котором кре |
||||||
|
у 1 |
|
пятся |
кондукторы. Внутри стола нахо |
|||||
|
|
дится |
пневматическая |
камера с диаф |
|||||
........................................... .. |
рагмой, обеспечивающая |
закрепление |
|||||||
деталей в кондукторе. При сверлении |
|||||||||
20 |
40 60 80 |
100 120 140 160 п |
подъемный стол через рейку и шестерню |
||||||
|
|
|
поднимается вверх; подъем производится |
||||||
Рис. VI. 62. График |
изменения штуч |
рукояткой 17 |
|
установка |
стола |
||||
ного времени в зависимости от вели |
Предварительная |
||||||||
чины партии деталей при обработке |
по высоте осуществляется |
винтом 21 |
|||||||
на сверлильном (1) и агрегатносвер- |
независимо от механизма подъема стола. |
||||||||
лильиом (2) |
станках |
К подъемному столу через рычаг под вешен противовес 23.
Для того чтобы можно было сверлить или зенкеровать отверстия на заданную глубину, на станке имеется четырехпозиционный упор 20 (по числу головок станка), а на рукоятке подъемного стола расположен винтупор 19. В случае сверления сквозных отверстий и зенкерования на определенную глубину можно пользоваться и одной позицией четырех позиционного упора. Все сверла и зенкеры устанавливаются с таким рас четом, чтобы, доводя рукоятку подъема стола до одного и того же упора, получать при сверлении сквозные отверстия, а при зенкеровании на дру гих головках — заданную глубину выемки.
Рукоятка подъема стола выполняет на станке еще одну функцию. Вал электродвигателя вращается все время независимо от того, сверлят детали или производят их съем и установку, а электромагнитный патрон начинает получать питание только в тот момент, когда рукоятка подъема стола отводится от своего исходного положения. Немедленно электро
магнитный патрон притягивает к себе диск 28 |
и, вращая |
его вместе |
со шиквом, передает движение на шпиндели |
головки, |
находящейся |
в рабочем положении. Возвращаясь в исходное положение, рукоятка выключает ток, питающий электромагнитный патрон, включает ток обратного направления (для размагничивания) и после этого полностью отключает патрон. Такой принцип работы отвечает требованиям техники безопасности и уменьшает износ вращающихся с большой скоростью шпинделей.
На станке могут быть использованы обычные и групповые кондукторы, {конструкции которых были рассмотрены ранее. Устанавливаемый на
подъемный стол станка групповой кондуктор соединяется со штоком диа фрагмы, которая при подаче воздуха обеспечивает закрепление детали.
Для установки шпинделей на заданные межцентровые расстояния используются кондукторные планки.
Конструкция станка позволяет сверлить двенадцать или шесть отвер стий и зенкеровать их без съема детали. Постоянное положение кондуктора облегчило труд рабочего, а пневматическое крепление деталей резко со кратило время на их закрепление и освобождение.
На рис. VI. 62 дан график, показывающий изменение штучного (/шт) времени в зависимости от величины партии (п) деталей при сверлении систем отверстий на двухшпиндельном и агрегатносверлильном станках. Из графика видно, что при партии деталей свыше пятидесяти штук при обработке на агрегатном станке tlum меньше, чем при обработке на двухшпиндельном.
8. ЭФФЕКТИВНОСТЬ ГРУППОВОЙ ОБРАБОТКИ НА СВЕРЛИЛЬНЫХ СТАНКАХ
Практика работы показала, что применение группового метода при обработке деталей на сверлильных станках позволяет не только сокращать время на обработку, но и снижать затраты на проектирование и изготовле ние оснастки. Например, при переводе на групповую обработку 250 типов деталей, скомплектованных в шесть групп, получены данные, приведен ные в табл. VI. 5.
Т а б л и ц а VI. 5
Сравнительные данные по обработке деталей при индивидуальном и групповом методе
|
Метод обработки |
|
Показатели |
индивидуальный |
групповой |
|
||
Количество кондукторов |
250 |
6 |
Количество сменных комплектов |
— |
250 |
Стоимость в руб.: |
30 |
|
одного кондуктора |
110 |
|
одного сменного комплекта |
— |
12 |
Время проектирования в ч: |
|
40 |
одного кондуктора |
12 |
|
одного сменного комплекта |
— |
4 |
Черный вес металла в кг: |
7 |
|
на один кондуктор . |
12 |
|
на один сменный комплект |
— |
1,5 |
На основании материала таблицы построен ряд графиков, характери зующих время и стоимость подготовки производства при индивидуальной и групповой обработке деталей.
На графике рис. VI. 63 представлена картина изменения средних затрат времени на проектирование индивидуальной и групповой оснастки в за висимости от количества наименований деталей, для которых эта оснастка проектируется (до 250 типов деталей).
На графике рис. VI. 64 показано изменение средней стоимости изготов ления оснастки для обработки тех же деталей при индивидуальном и груп повом методах.
Рис. VI. 63. График средних затрат вре мени на проектиро вание кондукторов:
/ —специальных; 2 — групповых со сменны ми наладками
Стоимость*руб
время, мин
Рис. VI. 64. График средней стоимости изготовления кон дукторов:
/ —специальных; 2— групповых со смен ными наладками
Рис. VI. 65. График средних затрат металла |
Рис. VI. 66. Сравнительный график затрат времени при груп |
на изготовление кондукторов: |
повой и индивидуальной обработке в зависимости от количе |
1 — специальных; 2 — групповых со сменными |
ства деталей в партии |
наладками |
|
При применении групповых кондукторов вместо индивидуальных время на проектирование оснастки сокращается на 40—60% и примерно на столько же уменьшается стоимость их изготовления.
На графике рис. VI. 65 показаны затраты металла, необходимого на изготовление оснастки. При изготовлении групповых кондукторов вместо индивидуальных достигается экономия металла (60—80%).
Применение групповой обработки обеспечивает и более высокую производительность труда, так как повышается серийность производства, а следовательно, и возможность применения более совершенной и быстро действующей оснастки (шесть групповых кондукторов для 250 наименова ний деталей).
На рис. VI. 66 представлен сравнительный график изменения ТшпикУ Твсп и ТП' Эпри групповой и индивидуальной обработке в зависимости от количества деталей в партии. При построении графика Тмаш принято одинаковым в обоих случаях, так как обработка выполняется с одними и теми же режимами резания.
Практика работы показала, что при групповой обработке на сверлиль ных станках производительность труда повышается на 20—40%.
ГЛАВА VII
возможности ИСПОЛЬЗОВАНИЯ АГРЕГАТНЫХ СТАНКОВ ПРИ ГРУППОВОМ МЕТОДЕ
ОБРАБОТКИ ДЕТАЛЕЙ
Для комплексной механизации и автоматизации производства необхо димо оснащение заводов большим количеством высокопроизводительного автоматизированного оборудования.
До последнего времени почти все выпускаемое автоматизированное оборудование создавалось как оборудование специальное, предназначен ное для обработки какого-либо одного вполне конкретного изделия.
Это приводило к невозможности использования его в случае смены объекта производства. Кроме того, высокая стоимость и длительный пе риод создания специальных станков часто делали применение их нерента бельным даже в условиях массового и крупносерийного производства. В условиях же мелкосерийного производства, для которого характерны многономенклатурность, частая сменяемость объектов производства и малая серийность, применение специального оборудования оказывается совершенно не экономичным. Поэтому в мелкосерийном машиностроении и приборостроении приходилось в основном применять малопроизводи тельное универсальное оборудование.
За последнее время проведены большие работы в направлении создания агрегатированных конструкций специальных и специализированных стан ков, а также автоматических линий из нормализованных узлов.
Нормализованными узлами агрегатных станков являются силовые головки, столы, несущие узлы и др.
Силовые головки (основные агрегаты станков) предназначены для сообщения режущему инструменту вращательного и возвратнопоступатель ного движения. Различают головки с механическим, гидравлическим и пневмогидравлическим приводом подачи.
Столы подразделяются на делительные и поворотные, прямоугольной, круглой, кольцевой и барабанной формы. Приводы механизмов перемеще ния этих столов могут быть электрическими, пневматическими, пневмогидравлическими и гидравлическими.
Несущие узлы (станины, основания, кронштейны, колонны и др.) служат опорами для устанавливаемых на них узлов и деталей.
На рис. VII. 1 показан пример компоновок агрегатных полуавтомати ческих станков из нормализованных узлов, разработанных НИАТом.
Существующие разнообразные формы специальных и специализирован ных агрегатных станков, создаваемых из нормализованных узлов идеталей, можно разделить на четыре основные группы:
1) станки с одновременной работой всех силовых головок при непод вижно закрепленной обрабатываемой детали;
2) станки с вертикальной осью вращения поворотно-делительного стола и с последовательно-параллельной работой силовых головок;
3) станки с горизонтальной осью вращения поворотно-делительного стола и с последовательно-параллельной работой силовых головок;
4) станки с поступательным движением делительного стола и последо вательно-параллельной работой силовых головок.
в
Рис. VII. 1. Схема компоновки агрегатного станка из нормализованных узлов:
1 |
— станина; |
2 — пульт управления; |
3 — фильтр масленки; |
4 — горизонтальный кронштейн; |
|
5 |
— промежуточная плита (специальный узел); 6 — насадка фрезерная НФ-2; |
7 — насадка фрезер |
|||
ная НФ -1; 8 — многошпиндельная сверлильная насадка; 9 — силовая головка; |
10 — вертикальный |
||||
кронштейн; П |
— командный аппарат; |
12 — разборная станина; |
13 — стол с |
автоматическим де |
|
|
|
|
лением |
|
|
Любая из указанных четырех групп может быть скомпонована из нор мализованных узлов с подбором соответствующего типажа последних.
Современные агрегатные станки имеют широкие технологические воз можности. На них можно производить следующие работы:
1) центрирование, сверление, рассверливание, зенкерование, зенкование, растачивание отверстий, а с применением различных насадок — фрезерование плоскостей, пазов и фазонных поверхностей; подрезание наружных и внутренних торцов, растачивание кольцевых канавок, обта чивание наружных поверхностей, нарезание и накатывание резьб и пр.;
2)сверление глубоких отверстий с многократным автоматическим вы водом сверла;
3)зенкерование, зенкование и другие виды работ, с остановкой режу щего инструмента в конце прохода по жесткому упору;
4)сверление, зенкерование и развертывание с прерывистым резанием (рабочая подача, ускоренный подвод, снова рабочая подача и т. д.);
5) сверление, |
рассверливание, зенкерование и другие виды работ |
с автоматическим |
изменением величины подачи (например, уменьшение |
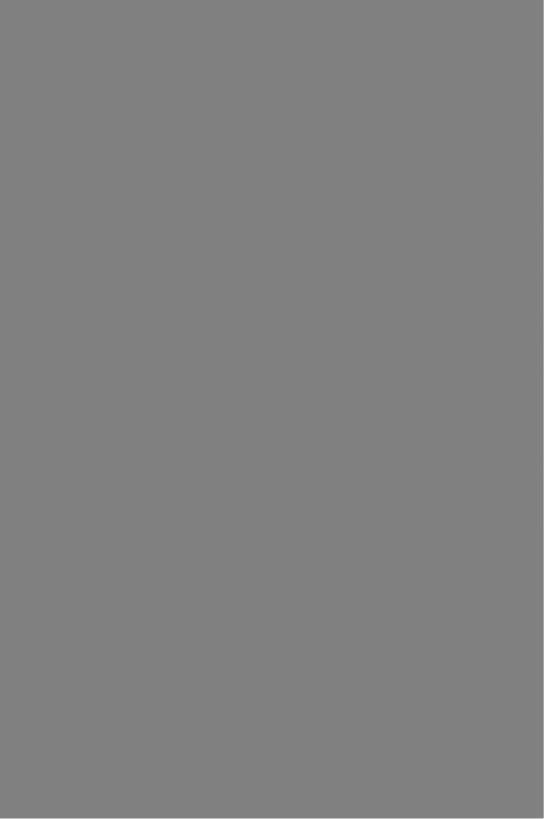
