
книги из ГПНТБ / Тюкина, Ю. П. Общая технология лесопильно-деревообрабатывающего производства учебник
.pdfНепрострожка прямолинейных деталей бывает из-за непрямолинейности фрезеруемых кромок или из-за неправильной установки линеек. В криволинейных деталях непрострожка может быть из-за неплотного прилегания заготовок к базовым поверхностям цулаги и упорному кольцу.
Средняя точность обработки, которой можно добиться на фре зерных станках, составляет от 0,3 до 1 мм в зависимости от шири ны фрезерования.
Т е х н и к а б е з о п а с н о с т и п р и р а б о т е на ф р е з е р ных с т а н к а х . Эти станки по показателям частоты и тяжести травматизма занимают среди других деревообрабатывающих стан ков одно из первых мест. Наибольший процент составляют травмы, получаемые от режущего инструмента. Режущий инструмент на современных фрезерных станках обязательно ограждают корпусом с патрубками для выброса стружки. С передней стороны корпуса делают открытый проем, который перекрывают щитком, укреп ленным на качающемся рычаге. При нажиме обрабатываемой дета ли на скос щитка последний поднимается и дает доступ к режуще му инструменту. Система щиток — рычаг уравновешена пружинойпротивовесом, возвращающей щиток в исходное положение после прохода детали. Ограждение сблокировано с пусковой системой для безопасной смены режущего инструмента, обслуживания и ремонта станка. Станки оборудованы электрическим устройством для быстрого торможения электродвигателя привода шпинделя. Работать на станке можно только при исправном ограждении и дей ствующей электроблокировке.
При фрезеровании по линейке заготовку необходимо прижимать к столу и линейке прижимными устройствами. В остальных случа ях при ручной подаче заготовку нужно подавать на режущий инст румент при помощи колодок, толкателей или шаблонов. Категори чески запрещается при криволинейном фрезеровании подавать заготовку против слоя, так как в этом случае возможен выброс за готовки.
СВЕРЛЕНИЕ КРУГЛЫХ ОТВЕРСТИЙ
Сверление круглых отверстий сквозных и несквозных (гнезд) можно производить на различных сверлильных станках с горизон тальным или вертикальным расположением рабочих шпинделей. Сверлильные станки могут быть одно- и многошпиндельные.
Режущим инструментом для сверления отверстий и гнезд явля ются спиральные сверла и торцовые фрезы. Диаметр сверла или фрезы определяет размер будущего отверстия. Кроме того, для сверления отверстий могут использоваться агрегатные силовые головки.
Заготовки, подлежащие сверлению, должны быть предваритель но точно оторцованы.
Наибольшее распространение имеют одношпиндельные верти кальные станки с ручной и автоматической подачей.
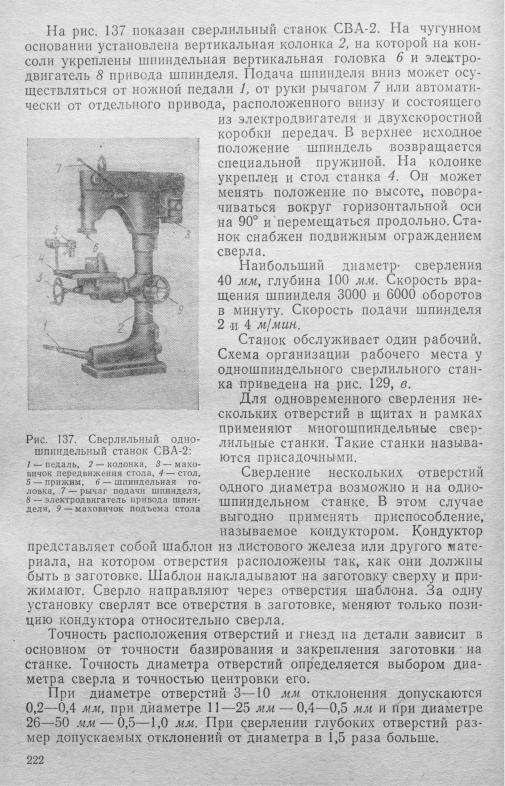
ВЫБОРКА ПРОДОЛГОВАТЫХ ГНЕЗД И ОТВЕРСТИЙ
Продолговатые гнезда и отверстия в заготовках можно получить на сверлильно-пазовальном и цепнодолбежном станках.
Режущим инструментом на сверлильно-пазовальном станке являются спиральные сверла или концевые фрезы. Концевые фрезы более производительны; чистота боковых поверхностей гнезд выше.
Выбираемые на сверлильно- |
|
|
|
|||||||||
пазовальном станке гнезда в |
|
|
|
|||||||||
плане имеют форму |
прямо |
|
|
|
||||||||
угольника |
с |
закругленными |
|
|
|
|||||||
торцовыми |
поверхностями |
|
|
|
||||||||
(рис. 138, а). |
|
|
|
|
|
|
|
|||||
на |
Порядок выборки гнезда |
|
|
|
||||||||
сверлильно-пазовальном |
|
|
|
|||||||||
станке с ручной подачей при |
а) |
|
<5) |
|||||||||
работе спиральным сверлом |
|
|
|
|||||||||
схематично показан на рис. |
Рис. 138. Форма получаемого гнезда на |
|||||||||||
139, а. Сначала высверлива |
сверлильно-пазовальном (а) |
и на цепно |
||||||||||
ют отверстия I я II по кош |
долбежном |
(б) станках |
||||||||||
цам гнезда, затем последо |
|
|
|
|||||||||
вательно |
III, |
IV, |
V |
,и |
VI. |
|
|
|
||||
После |
этого, |
не |
поднимая |
|
|
|
||||||
сверла, расчищают все гнез |
|
|
|
|||||||||
до. |
При |
работе |
концевой |
|
|
|
||||||
|
|
|
|
|||||||||
фрезой (рис. 139, б) приемы |
|
|
|
|||||||||
остаются те же. Фрезу сна |
|
|
|
|||||||||
чала |
углубляют |
на |
одном |
А; |
|
|
||||||
конце гнезда I, поднимают, |
|
|
||||||||||
затем |
углубляют в противо |
Рис. 139. Порядок |
выборки |
гнезда на |
||||||||
положном |
конце |
гнезда |
II |
|||||||||
сверлильно-пазовальном станке с ручной |
||||||||||||
и, |
не вынимая |
фрезы, мед |
подачей спиральным сверлом (а) и кон |
|||||||||
ленно передвигают ее к пер |
цевой фрезой (б) |
|
||||||||||
вому концу. |
За |
один |
прием |
|
|
|
можно фрезеровать гнездо глубиной не более двух диаметров фрезы.
Наиболее совершенным является горизонтальный сверлильнопазовальный станок СвПА-2 с автоматической подачей (рис. 140). На станине горизонтально при помощи шарнирной опоры закреплен электродвигатель с удлиненным валом, который служит одновре менно и шпинделем. В патроне 8 крепится концевая фреза. В вер тикальных направляющих станины на суппорте подвижно крепится стол 5, который может менять положение по высоте и передвигать ся по горизонтальным направляющим в сторону шпинделя и обрат но. Заготовка прижимается на столе двумя гидроприжимами 7 к упорному угольнику 6. Заготовка зажимается автоматически в начале движения стола к фрезе. Шпиндель, в котором крепится
223
концевая фреза, кроме вращательного, совершает еще колебатель ное движение в горизонтальной плоскости, поэтому на станке мож но высверливать продолговатое отверстие-паз глубиной до 80 .и длиной до 120 мм. Величина амплитуды колебания шпинделя регу лируется в зависимости от длины обрабатываемого паза. Колеба тельное движение шпиндель получает от гидродвигателя через кривошипно-шатунный механизм.
Рис. 140. Сверлильно-пазовальный станок |
Рис. 141. |
Цепнодолбежный ста |
|||||
|
СвПА-2: |
|
|
|
нок ДЦА-2: |
|
|
/ — педаль, |
2 —маховичок механизма установки |
1— педаль, |
2 — механизм передви |
||||
стола по |
высоте, 3 — золотник, |
4 — кронштейн, |
жения стола в продольном направ |
||||
5 — стол, 6 — упорный угольник, |
7 — гидроприжи |
лении, |
3 — стол, 4 — маховичок |
за |
|||
|
мы, 8 — патрон |
|
жима, |
5 — подпорный |
брусок, |
6 — |
|
|
|
|
маховичок |
механизма |
натяжения |
||
|
|
|
цепочки, 7 — суппорт рабочего орга |
||||
|
|
|
на, 8 — ограничитель |
перемещения |
|||
|
|
|
стола |
в продольном |
направлении, |
||
|
|
|
|
|
9 — золотник |
|
На станке работает один станочник. Схема организации рабоче го места приведена на рис. 129, г.
Производительность сверлильных станков в штуках гнезд в смену можно определить по формуле
,TKiKzti
А- ~ Г ~ '
где Т — продолжительность смены, мин; t — время, необходимое на выборку одного гнезда, мин; Ki — коэффициент использования
224
рабочего времени, равный 0,9; /С2 — коэффициент использования машинного времени станка.' с ручной подачей 0,3—0,4; с автомати-
ческой — 0,6—0,7; « — число гнезд, выбираемых на станке одновре менно.
На рис. 141 показан цепнодолбежный станок ДЦА-2. Режущий инструмент в цепнодолбежном станке — фрезерная цепочка, сколь зящая по направляющей линейке, приводится в движение звездоч кой, закрепленной на электродвигателе.
Станок имеет цельнолитую чугунную станину коробчатой формы. В верхней части станины по направляющим перемещается верти кальный суппорт 7, на котором установлен электродвигатель с ре жущей головкой. Режущая головка состоит из фрезерной цепочки, направляющей линейки с роликом и приводной звездочки на валу электродвигателя. На станине под режущей головкой закреплен рабочий стол 3, который может перемещаться в продольном и попе речном направлениях и устанавливаться под углом к горизонталь ной плоскости. Обрабатываемая заготовка на столе закрепляется быстродействующим зажимом. Рабочее и холостое перемещение суппорта по вертикали осуществляется гидравлическим приводом, конструкция которого предусматривает автоматическую работу суппорта режущей головки по жестким ограничительным упорам. Режущая головка опускается к заготовке на такую глубину, кото рая определена нижним упором, после чего автоматически возвра щается в верхнее исходное положение до верхнего упора. Режущая цепочка закрыта ограждением, которое является одновременно при
емником стружки и может быть через патрубок подсоединено к эксгаустерной сети.
Форма получаемого на цепнодолбежном станке гнезда в плане прямоугольная, углы дна закруглены (см. рис. 138, б), поэтому глубина гнезда делается с запасом по сравнению с длиной сопряга емого шипа. Наименьшие размеры гнезд определяются наименьши ми размерами фрезерных цепочек и их направляющих линеек.
При выборке длинного гнезда приемы работы цепочкой сходны с приемами работы концевой фрезой (см. рис. 139, б). Сначала опускают цепочку с одного конца гнезда, поднимают ее, затем опус кают с другого конца гнезда. Потом надвигают цепочку в направ лении первого углубления, фрезеруя промежуток. Следует знать, что цепочка должна работать восходящей ветвью.
Если в заготовке требуется выбрать одно гнездо или отверстие, в качестве приспособления используют один концевой упор. При не обходимости выборки двух одинаковых гнезд, расположенных в одну линию, можно работу выполнить с одним упором за две уста новки и с двумя упорами за одну установку. В первом случае упор устанавливается и выбирается первое гнездо у всей партии загото вок, затем упор переставляют в новое положение и выбирают вто рое гнездо. При работе с двумя упорами работа протекает следую щим образом (рис. 142). Упоры устанавливают с обоих концов заготовки с таким расчетом, чтобы правое гнездо выбиралось при крайнем левом положении заготовки у левого упора (I позиция), а
225
левое гнездо — при крайнем правом положении заготовки у право го упора (II позиция).
На цепнодолбежных станках возможен дефект обработки — скол края гнезда при выходе цепочки из древесины. Скол можно предот вратить, если на заготовке закрепить подпорный брусок. Недостат ком цепнодолбежного станка является также и то, что нельзя по лучить гнезда размером меньше 40X6 мм.
Точность обработки гнезд на сверлильно-пазовальном и цепно долбежном станках примерно одинаковая. Допускаемые отклонения по ширине гнезда и по расстоянию между кромками детали и гнез да — 0,4—1,0 мм.
1 позиция |
И позиция |
|
н - |
Рис. 142. Выборка в заготовке двух гнезд на цепнодол бежном станке
На станке ДЦА-2 можно обрабатывать заготовки шириной до 250, толщиной до 200 мм. Наибольшие размеры выбираемого пазагнезда: ширина 25, длина 430, глубина 140 мм. Станок обслужива ет один станочник. Схема организации рабочего места у станка ДЦА-2 показана на рис. 129, д.
Производительность цепнодолбежного станка определяется так же, как сверлильного.
ЗАЧИСТКА ПОВЕРХНОСТЕЙ
Заключительная операция механической обработки чистовых заготовок — зачистка поверхностей. Заготовки после обработки на строгальных, фрезерных, сверлильных и цепнодолбежных станках могут иметь волнистость, местные выколы, задиры и заусенцы на ребрах заготовок и на краях гнезд и отверстий, вмятины, ворсис тость и другие дефекты, которые не допускаются в изделии. Неров ности и дефекты устраняют циклеванием и шлифованием. Циклюют только твердые породы древесины и поверхности, предназначенные под высококачественную отделку полированием.
Циклевание — это строгание поверхности древесины специаль но заточенным ножом — циклей (рис. 143). Циклевание можно про изводить на циклевальных станках и вручную.
На рис. 144 показана схема устройства циклевального станка. Станок имеет стол 1, вальцовый механизм подачи 3 и циклевальный нож 4. Нож устанавливают лезвием вверх в специальной короб ке. Лезвие должно выступать над поверхностью стола на 0,1— 0,15 мм. При прохождении заготовки 2 через станок с нижней по
226
верхности снимается слой толщиной от 0,025 до 0,15 мм. На станке достигается шероховатость поверхности, соответствующая 9—10-му
классам.
При ручном циклевании заготовка базируется на верстаке обра батываемой поверхностью вверх. Степень заглубления цикли в
древесину зависит от прилагаемого рабочим |
усилия |
и твердости |
|
обрабатываемой древесины. Поэтому точ |
|
{0,05-0,15 |
|
ность ручного циклевания «иже машин |
|
||
ного. |
зачищают |
|
|
Окончательно поверхности |
|
|
|
шлифованием. Инструментом для шлифова |
|
|
|
ния служит шлифовальная шкурка, состоя |
|
|
|
щая из бумажной или тканевой основы, на |
|
|
|
которую наклеены мелкие абразивные зер |
|
|
|
на из стекла, кремния, гранита или других |
|
|
|
материалов повышенной твердости. |
|
|
|
Шлифуют древесину вдоль волокон или |
|
|
|
под небольшим углом. При поперечном шли |
|
|
|
фовании на древесине остаются |
царапины, |
а) |
5) |
портящие внешний вид изделия. Поэтому |
|
|
|
рамки, например, следует шлифовать по |
Рис. 143. Нож для ма |
||
диагонали, чтобы все бруски шлифовались |
шинного циклевания (а) |
||
под углом к направлению волокон. |
и ручная цикля (б) |
Шероховатость шлифованной поверхности в основном зависит от зернистости применяемой шкурки. Чем крупнее зерна шкурки, тем более грубой получается поверхность. Шкурки с мелкими зер-
ЖЖЖЖФ
W в
Рис. 144. Схема устройства циклевального станка:
/ — стол, 2 — заготовка, 5 — подающие вальцы, 4 — циклевальный нож
нами дают более чистую поверхность, но они менее производитель ны. Поэтому рекомендуется шлифование проводить в два-три эта па. Начинать надо более грубой шкуркой для быстрого уничтоже ния следов предыдущей обработки и заканчивать мелкозернистой для получения требуемой шероховатости поверхности.
В зависимости от требуемого класса шероховатости поверхнос ти рекомендуются следующие номера шлифовальных шкурок:
Класс шероховатости поверхно |
10 |
9 |
8 |
7 |
сти древесины.......................... |
||||
Номер шкурки........................... |
8—5 |
12—8 |
32—16 |
40—32 |
227
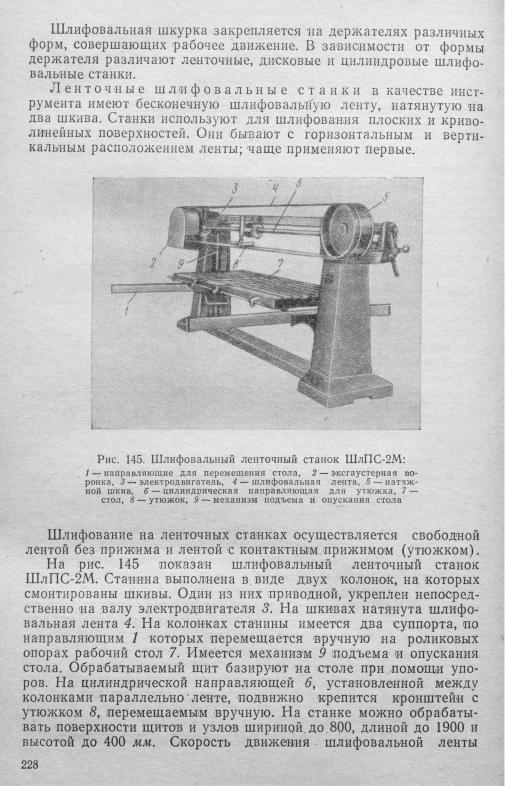
26,5 м/сек, ширина ленты 150 мм. Станок обслуживает один ста ночник. Схема организации рабочего места показана на рис. 146, а.
В д и с к о в ы х ш л и ф о в а л ь н ы х с т а н к а х шлифоваль ная шкурка надевается на плоскую поверхность чугунного диска, который может иметь вертикальное или горизонтальное располо жение. Обрабатываемые детали прижимаются к шкурке вручную или прижимами. Дисковые станки предназначены преимущественно для чернового шлифования, снятия провесов в собранных рамках, для шлифования мелких деталей по торцовым и продольным по верхностям.
IZ3
о) 5) б)
Рис. 146. Организация рабочих мест у шлифовальных станков:
а — ленточного, б — дискового с бобиной, в — трехдилиндрового
На рис. 147 показан дисковый шлифовальный станок ШлДБ-3, который имеет два рабочих органа, работающих самосто ятельно,—диск 3 и бобину 5. Бобина представляет собой цилиндр, вал которого через муфту соединен с электродвигателем. Привод бобины обеспечивает вращательное и вертикальное возвратно-по ступательное движение (осциллирующее). На бобине обрабатывают вогнутые поверхности криволинейных деталей. На цилиндре (бо бине) и диске закрепляют шлифовальные шкурки, которые выреза ют по шаблонам.
Станок имеет два рабочих стола. Стол 2 шлифовального диска крепится к станине шарнирно, это позволяет устанавливать его под углом до 45° к плоскости диска. На столе имеется продольный паз, в который вставляется крепление упорной линейки. Стол 6 бобины прикреплен к станине на двух качающихся секторах, что позволяет поворачивать его в обе стороны до 30°. Это требуется при шлифова нии конусных вогнутых поверхностей. Диск и бобина имеют само стоятельные приводы от электромоторов. Диск имеет ограждение, которое служит одновременно приемником для отвода древесной пыли в эксгаустерную сеть. Станок обслуживают двое станочников. Один шлифует детали на диске, другой.—на бобине. Схема орга низации рабочих мест показана на рис. 146, б.
Ц и л и н д р о в ы е ш л и ф о в а л ь н ы е с т а н к и |
применяют |
в основном для шлифования плоских щитов и плит, |
а также для |
снятия провесов у собранных рамок. Держателем шкурки являют
229
ся цилиндры-барабаны. Наибольшее распространение получили трехцилиндровые станки, у которых шлифовальные цилиндры вра щаются по-разному: первый и третий навстречу подаче, а второй — по ходу ее. Кроме вращательного, второй и третий цилиндры имеют осевое движение, примерно 150 двойных ходов в минуту при вели чине хода 10 мм. Трехцилиндровые станки бывают с вальцовой в гусеничной подачей.
Рис. 147. Шлифовальный дисковый станок с бобиной ШлДБ-3:
/ — станина, 2 — стол д и ска, |
3 — ш лиф овальный |
ди ск , 4 — отсос, 5 — бобина, |
6 — стол |
бобины, 7 — кнопки |
управления |
На рис. 148 показан трехцилиндровый шлифовальный станок ШлЗЦ-12-2. На станине 1 станка уложена горизонтальная плита — стол 8, на котором смонтирован гусеничный механизм подачи 3, 7. Стол может менять свое положение по высоте. Над столом распола гаются шлифовальные цилиндры, имеющие индивидуальные элек тродвигатели 4. Между цилиндрами располагаются прижимные вальцы. За третьим цилиндром укреплен барабан со щеткой для очистки шлифуемой поверхности от пыли. Шлифовальная шкурка навивается на цилиндры по спирали. На станке можно обрабаты вать щиты и рамки следующих размеров: ширина до 1250, толщина до 130, длина от 460 мм. Скорость подачи до 15 м/мин.
Трехцилиндровый шлифовальный станок обслуживают двое ра бочих. Станочник 5-го разряда управляет станком и подает в него детали, а станочник 2—3-го разряда с противоположной стороны станка принимает обработанные детали. Схема организации рабо чих мест у трехцилиндрового шлифовального станка дана на рис. 146, в.
230