
3607
.pdf
5.2. Расчет шпоночных соединений
При проектировании шпоночного соединения ширину в и высоту h шпонок принимают по соответствующему ГОСТ, в зависимости от диаметра d вала. Длину ℓ шпонки принимают в зависимости от длины ступицы и согласовывают с ГОСТом на шпонки. Достаточность принятых размеров проверяют расчѐтом на прочность. Следовательно, расчѐт шпоночных соединений на прочность осуществляется как проверочный.
Призматические шпонки рассчитываются на смятие и на
срез:
|
2 м |
|
; |
|
см |
|
см |
||
d pk |
||||
|
|
|
|
2 м |
ср ; |
|||
ср |
|
|
|||
d pв |
|||||
|
|
|
|||
где: М – передаваемый момент р |
2м |
; |
|||
d |
|||||
|
|
|
|
d- диаметр вала;
К- глубина врезания шпонки в ступицу K = 0,4 h;
ℓp – рабочая длина шпонки со скруглѐнными торцами. При плоских торцах ℓp = ℓ . Здесь: ℓ – длина шпонки.
Поскольку при расчете шпонок принята упрощенная схема нагружения (не учитывается перекос шпонки в пазу вала и кромочные давления, рис.5.3), то допускаемые напряжения назначают с коэффициентом запаса 1,5…2,0 по отношению к пределу текучести наиболее слабого материала соединения.
Для упрощения расчѐтов принимают, что плечо сил, действующих на шпонку относительно осевой линии вала, равно радиусу вала d2. Призматические шпонки – врезные. Рабочими гранями являются их боковые более узкие грани. Для облегчения сборки предусматривается радиальный зазор. Призматические шпонки по сравнению с клиновыми обеспечивают большую точность, а по сравнению с сегментными – меньше ослабляют вал, т.к. врезаются на меньшую глубину.
39
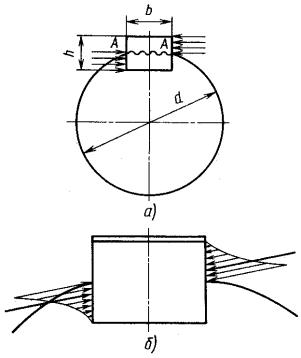
Рис. 5.3 Схема нагружения шпоночного соединения
В табл. 5.2 приведены стандартные посадки призматической шпонки в пазы вала и ступицы.
|
|
|
|
|
Таблица 5.2 |
|
Посадки шпоночных соединений |
||||
|
Паз втулки |
|
|
Паз вала |
|
|
|
|
|
|
|
|
Соединение |
|
|
Соединение |
|
|
|
|
|
|
|
подвижное |
неподвижное |
реверсивное |
реверсивное |
неревнерсивное |
|
|
|
|
|
|
|
D10h9 |
Is9h9 |
P9h9 |
P9h9 |
|
N9h9 |
|
|
|
|
|
|
40

5.3.Сегментные шпонки
Всвязи с ослаблением вала шпоночным пазом под сегментную шпонку, такие шпонки применяют для передачи относительно небольших моментов, их отличает устойчивое положение в соединении.
Так же, как и призматические, сегментные шпонки (рис. 7.5) рассчитываются на смятие:
|
|
2 м |
|
|
; |
|
см |
|
см |
||||
d k |
||||||
|
|
|
|
|
||
и на срез: |
|
|
|
|
||
|
|
2 м |
|
; |
|
|
|
|
|
ср |
|
||
ср |
d в |
|
||||
|
|
|
|
|
Рис. 5.4 Соединение сегментной шпонкой
|
|
Таблица 7.3 |
Примеры обозначений шпоночных соединений |
||
Вид соединения |
Обозначение |
|
1. Призматическая шпонка со |
ШПОНКА |
18×11×100 |
скругленными торцами |
ГОСТ 23360-70 |
|
2. Призматическая шпонка с пло- |
ШПОНКА |
2-18×11×100 |
скими торцами |
ГОСТ 23360-70 |
|
3. Шпонка сегментная |
ШПОНКА |
сегм. 6×10 |
|
ГОСТ 24071-80 |
|
41 |
|
|

Клиновые шпонки в отличие от призматических ставятся с зазором по боковым граням. Клиновые шпонки создают напряжѐнное соединение, способное передавать не только Мкр, но
иосевое усилие. Однако эти шпонки вызывают радиальное смещение оси ступицы на величину посадочного зазора и контактных деформаций. Это увеличивает биение насажанной детали. Применение клиновых шпонок резко сократилось. Достоинством является отсутствие зазоров и поэтому хорошее восприятие радиальных нагрузок.
Для упрощения расчѐта принимают, что при передачи
момента Мкр напряжения смятия по ширине поверхности контакта рабочих граней шпонки с валом и ступицей распределяются по закону треугольника. В этом случае передаваемый крутящий момент складывается из:
амомента нормальной силы давления N между ступицей
ишпонкой;
б момента силы трения Nq между ступицей и валом; в момента силы трения Nq между ступицей и валом.
Приближѐнно можно принять q = q/ и плечо силы Nq равняется радиусу вала. При таком условии:
|
|
M |
|
|
N |
в |
N |
|
d |
N |
|
d |
; q q |
||
|
|
кр |
|
q |
|
|
q |
|
|||||||
|
|
|
6 |
|
2 |
|
|
2 |
|
||||||
|
|
|
|
|
|
|
|
|
|
|
|||||
Или: M |
|
N |
в |
N |
d ; |
|
|
|
|
|
|
|
|||
кр |
|
|
|
|
|
|
|
|
|||||||
|
|
6 |
q |
|
|
|
|
|
|
|
|
|
|||
|
|
|
|
|
|
|
|
|
|
|
|
|
|
||
Откуда: 6Mкр |
Nв |
|
6Nqd ; |
|
|
|
|
N6M кр
в6qd
При принятом законе распределения напряжений смятия по ширине шпонки следует, что:
N |
1 |
в |
|
2 |
см |
||
|
|
|
Откуда:
42
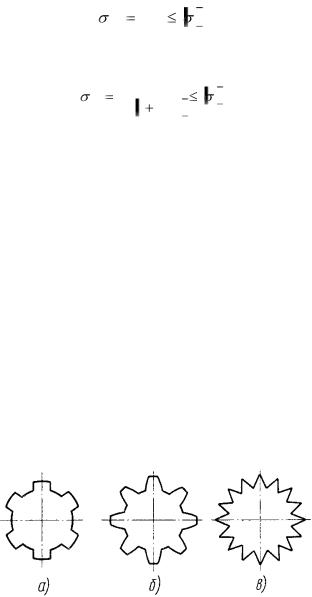
|
2N |
|
см |
|
см . |
|
||
|
в |
Подставив значение N из а, получим:
|
12M кр |
см . |
|
мс |
в в |
6qd |
|
|
|
Шпонку на диске рассчитывают так же как и клиновую.
5.4. Конструкция и расчет шлицевых соединений
Соединение ступицы с валом вместо шпонки может осуществляться с помощью шлицов. Такое соединение ступицы с валом называется зубчатым или шлицевым.
В зависимости от формы профиля зубьев различают соединения с прямобочными, эвольвентными и треугольными зубьями (шлицами) (рис.7.6). Достоинства шлицевых соединений:
а) возможность передачи больших моментов благодаря значительно большей поверхности контакта соединяемых деталей и более равномерному распределению давления по этой поверхности;
б) более точное центрирование ступицы по валу, в) лучшее направление при перемещении ступицы по валу, г) большая прочность вала.
Рис. 5.5 Основные типы зубчатых (шлицевых) соединений: а – прямобочное; б – эвольвентное; в – треугольное
43

Прямобочные (ГОСТ 1139-80) шлицевое соединение наиболее распространено. Соединение выполняется с центрированием ступицы: по боковым сторонам зубьев в, по наружному диаметру D, по внутреннему диаметру d (рис. 7.7)
Центрирование по “ в ” (рис. 7.7, а) не обеспечивает точной соосности ступицы и вала. Поэтому его рекомендуют при передачи больших моментов. Центрирование по “D” и “d” применяется, когда требуется точность совпадения осей соединяемых деталей (рис. 7.7, б,в).
Рис. 5.6 Виды центрирования прямобочных зубчатых соединений:
а– по боковым граням; б – по наружному диаметру;
в– внутреннему диаметру; г – форма сечения ступицы; д, е – форма сечений вала исполнений б, в
Эвольвентное шлицевое соединение (ГОСТ 6033-80) различают с центрированием ступицы по боковым сторонам “S” (рис. 7.8, а) и по наружному диаметру “D” (рис. 7.8, б). Центрирование по “S” наиболее распространено.
Достоинства эвольвентных шлицевых соединений: более высокая прочность зубьев, вследствие их утолщения к основанию; высокая технологичность и более низкая стоимость изготовления шлицевых валов.
44

Рис. 5.7 Эвольвентное зубчатое зацепление:
а – центрирование по боковым граням; б – центрирование по наружному диаметру
Вследствие высокой стоимости протяжек для изготовления шлицев в ступицах малых и средних размеров – эвольвентные шлицевые соединения применяются реже прямобочных.
Таблицы 7.4 Примеры обозначения шлицевых соединений
Обозначение |
Способ центрирования |
|
|
Прямобочные шлицевые соединения |
|
|
|
D – 8×36×40H8h7×7F10h9 |
по внешнему диаметру |
|
|
d – 8×36H7e8×40H12a11×7D9f8 |
по внутреннему диаметру |
|
|
b – 8×36×40H12a11×7D9h8 |
по ширине шлиц |
|
|
Эвольвентные шлицевые соединения |
|
|
|
50×2×9H9g |
по эвольвенте |
|
|
50×H7g6×2 |
по внешнему диаметру |
|
|
Треугольное зубчатое соединение применяется только в качестве неподвижного при передаче небольших моментов. Центрирование такого соединения осуществляется только по боковым граням. Применяются также конические шлицевые соединения (конусность 1 : 16).
45

Число Z и размеры шлицев принимаются в зависимости от диаметра вала по соответствующему ГОСТ. Длина зубьев определяется длиной ступицы, а если ступица подвижная – величиной хода еѐ перемещения.
Расчѐт шлицевых соединений производится обычно как проверочный.
Шлицевые соединения рассчитываются на смятие по формуле:
|
|
2М |
; |
|
см |
|
|
см |
|
d c |
|
|||
|
Zh |
|
где: ζсм – расчѐтное напряжение смятия на рабочих поверхностях шлицев;
М– передаваемый момент;
dc – средний диаметр шлицевого соединения; Z – число шлиц;
h – высота поверхности контакта шлицев, принимаемая равной длине ступицы;
ψ – коэффициент, учитывающий неравномерность распределения нагрузки между шлицами, принимаемый равным
0,7…0,8;
[ζ]см – допускаемое напряжение смятия для рабочих поверхностей шлицев.
Размеры dc и h определяют из выражений: прямозубных шлицев:
d |
|
D d |
; h |
D d |
2q ; |
|
c |
2 |
2 |
||||
|
|
|
||||
|
|
|
|
Для шлицев эвольвентного профиля с центрированием по
S: dc = dд = mz и h = m = dд/z;
где: dд – диаметр делительной окружности; m – модуль закрепления;
для шлицев эвольвентного профиля с центрированием по D : dc = dд = mz и h = 0,9m = 0,9 dд/z;
для шлицев треугольного профиля:
46

dc = dд = mz и h = [D – da];
Допускаемое напряжение на смятие [ζ]см для шлицевого соединения при среднем режиме работы можно принимать: для неподвижного с термической обработкой шлицев [ζ]см = 100…140 МПа и без термической обработки [ζ]см = 60…100 МПа.
При лѐгком режиме работы значение этих напряжений можно увеличить на 20…40%, а при тяжелом режиме их необходимо снизить на 30…50%.
В последнее время начали применять шариковые шлицевые соединения (рис. 5.9), требующие очень малых усилий для перемещения ступиц. При перемещении последних под нагрузкой несущая способность шариковых шлицевых соединений в несколько раз больше, чем обыкновенных шлицевых соединений. Так как шариковые шлицевые соединения по конструкции сложнее и дороже обыкновенных, то применение их ограничено.
Рис. 5.8 Шариковое шлицевое соединение
Допускаемый момент (Нм) для шарикового шлицевого соединения (твердость вала и ступицы не менее 60 НRС):
Т = 0,016 Zшл ℓ d Dср ,
где Zшл – число рабочих выступов (шлиц); ℓ – рабочая длина соединения, мм;
d, Dср – диаметры шариков и окружности расположения центров шариков, мм.
47
6. СОЕДИНЕНИЯ С НАТЯГОМ
6.1. Общие сведения
Соединения с натягом относятся к группе неразъѐмных соединений и представляют собой напряжѐнные соединения, в которых натяг создаѐтся необходимой разностью посадочных размеров сопрягаемых деталей, а сами детали удерживаются в проектном положении за счѐт сил упругости.
Соединения с натягом можно разделить на две группы:
-соединение деталей по цилиндрическим или коническим поверхностям (здесь отсутствуют какие-либо специальные соединительные детали);
-соединения деталей по плоскости с помощью стяжных колец или планок.
Основное применение в машиностроении имеют соединения первой группы (по цилиндрическим поверхностям).
Общим достоинством соединений с натягом является возможность их выполнения для очень больших нагрузок и хорошая работа при ударном нагружении. Взаимное смещение деталей в соединениях с натягом предотвращается силами трения на поверхности контакта.
Характерной особенностью соединений с натягом является то, что они могут воспринимать произвольно направленные силы и моменты, а соединения по цилиндрическим и коническим поверхностям дополнительно обеспечивают хорошее центрирование и не требует специальных крепѐжных деталей.
К недостаткам соединений с натягом необходимо отне-
сти:
-сложность сборки и разработки (особенно внутри неразъѐмного корпуса), возможность ослабления посадки и повреждения посадочной поверхности при разборке;
-большое рассеивание прочности соединения в связи с рассеиванием посадочных размеров в предела допуска.
48