
3607
.pdfКонструировать [construere] – значит создавать конст-
рукцию механизма, машин, сооружения с выполнением их проектов и расчетов.
Конструктор – лицо, занимающееся созданием конструкций различных устройств и их частей. Он специалист, знающий не только порядок, способы и методы этого создания, но и способы и методы изготовления его составных частей. По ГОСТ 2.101-68 изделием называется любой предмет или набор предметов производства, подлежащих изготовлению на предприятии
1.3. Стадии разработки конструкторской документации
Совокупность конструкторских документов, полученных в результате проектирования, называется проектом.
Правила проектирования и оформления проектов стандартизованы в Единой системе конструкторской документации (ЕСКД), которая устанавливает пять стадий разработки конструкторской документации на изделия всех отраслей промышленности, а именно:
техническое задание устанавливает основное назначение и технические характеристики, показатели качества и техникоэкономические требования, предъявляемые к разрабатываемому изделию;
техническое предложение – совокупность конструкторских документов, содержащих технические и технико-экономические обоснования целесообразности разработки документации изделия на основании анализа технического задания, сравнительной оценки возможных решений с учетом особенностей разрабатываемого и существующих подобных изделий, а также патентных материалов;
эскизный проект – совокупность конструкторских документов, содержащих принципиальные конструктивные решения, дающие общие представления об устройстве и принципе работы изделия, а также данные, определяющие его основные параметры и габаритные размеры;
технический проект – совокупность конструкторских документов, содержащих окончательные технические решения, дающие
9
полное представление об устройстве изделия и исходные данные для разработки рабочей конструкторской документации;
разработка технической документации включает чертежи узлов и деталей, спецификации, технические условия на изготовление, сборку, испытание изделия и др.
2.ТРЕБОВАНИЯ К ДЕТАЛЯМ МАШИН
2.1.Виды нагрузок, действующих на детали машин
Впроцессе эксплуатации каждая машина испытывает различные виды нагрузок. Познакомимся с некоторыми из них.
Рабочей нагрузкой называют силу или момент воспринимаемые детально или узлом в процессе эксплуатации изделия.
Рабочая нагрузка может быть постоянной или переменной в зависимости от характера ее изменения во времени. К постоянной можно отнести, например, нагрузку от собственного веса.
При эксплуатации детали машин, как правило, испытывают переменные нагрузки, характер которых зависит от систематических или случайных факторов, вызывающих эти нагрузки.
Взависимости от способа воздействия на деталь нагрузки могут быть статическими и динамическими.
Статические нагрузки обычно бывают постоянными без возникновения колебаний системы. Динамические нагрузки вызывают удар или колебания системы. В связи с переменным характером рабочих нагрузок вводят понятия о номинальной,
эквивалентной и расчетной нагрузках.
Максимальная или длительно действующая нагрузка в установившемся режиме называется номинальной. Номинальные мощность, момент, частота вращения, скорость и т.д.
Эквивалентной называется такая постоянная нагрузка, которой можно заменить фактические действующую переменную рабочую нагрузку, считая ее равноценной в отношении соответствующих критериев надежности.
10
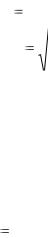
Для зубчатой передачи
Qэкв Qном Kдолг ,
Kд |
|
Nб |
|
m |
|
||
|
|
||
|
|
Nэкв |
|
где Кдолг – коэффициент долговечности, зависящий от графика изменения рабочей нагрузки и от того, какая из них принята в качестве номинальной.
Расчетной называется условная постоянная нагрузка, определяемая (рабочей нагрузкой) с учетом ее характера воздействия на объект. Она служит для определения размеров деталей машин. Учитывает местные условия.
Qрасч Qэкв Kк
Кд
Ку
где Кк – коэффициент, учитывающий неравномерность распределения нагрузки по контактным поверхностям;
Кд – коэффициент динамичности; Ку – коэффициент, зависящий от условий работы и пере-
дачи нагрузки (например, за счет сил трения, сцепления и т.д.).
Предварительные расчеты можно выполнять, принимая:
Qрасч ≈ Qном
2.2. Циклы напряжений и их параметры
Одним из главных факторов, определяющих величину напряжений, является вид и характер изменения во времени нагрузок, действующих на деталь.
Статистическое нагружение вызывает в материале детали постоянное напряжение, которое не изменяется в течение длительного времени ни по величине, ни по направлению.
Переменные нагрузки вызывают соответственно переменные напряжения. Детали, длительное время подвергающиеся повторно-переменной нагрузке, разрушаются при на-
11

пряжениях значительно меньших предела прочности материала при статистическом нагружении. Приблизительно 80% всех поломок и аварий, происходящих при эксплуатации машин, вызвано усталостными явлениями (цикличными нагрузками).
Циклические нагрузки наиболее явно выражены в машинах и механизмах с возвратно-поступательным движением звеньев (поршневые машины, кулачковые механизмы).
Однако и в механизмах вращательного движения циклические нагрузки неизбежны (зубчатые передачи, валы).
В современных машинах в большинстве случаев напряжения изменяются циклически с большей или меньшей частотой и амплитудой.
Различают следующие основные циклы изменения напряжений: асимметричный (рис. 2.1, а), отнулевой (рис. 2.1, б), симметричный (рис. 2.1, в). На рис. 2.1 приняты следующие обозначения: ζmin – минимальное напряжение цикла, ζmax – макчимальное напряжение цикла.
а |
б |
в |
Рис. 2.1 Циклы переменных напряжений
Алгебраическая полусумма наибольшего и наименьшего напряжений называется средним напряжением цикла
12

|
max |
|
min |
|
|
|
|
|
m . |
ср |
2 |
|
||
|
|
|
|
Полуразность этих напряжений называют амплитудой цикла
|
max |
min |
. |
a |
2 |
|
|
|
|
|
Отношение наименьшего напряжения к наибольшему, взятое с алгебраическим знаком, называется коэффициентом ассиметрии цикла (r):
r |
min |
; |
|
||
|
max |
Для отнулевого цикла ζmin = 0, тогда и r = 0. При постоянных нагрузках r = 1,0.
Пульсирующее нагружение в соответствии с отнулевым циклом (когда напряжения изменяются от нуля до максимума) имеют: зубья зубчатых колес при работе в одну сторону, толкатели и шатуны тихоходных механизмов с малой нагрузкой холостого хода, нереверсивные валы (напряжения кручения).
Знакопеременный симметричный цикл. Здесь наиболь-
шие и наименьшие напряжения противоположны по знаку и одинаковы по модулю (напряжения изгиба при вращении валов и осей).
Знакопеременный асимметричный цикл – это наиболее общий случай наружения деталей машин.
Число циклов нагружения, которые материал выдерживает до разрушения, зависит от максимального напряжения и амплитуды цикла. По мере уменьшения напряжений число циклов до разрушения детали увеличивается и при некотором достаточно малом напряжении становится неограниченно большим. Это напряжение называют пределом выносливости и кладут в основу расчета деталей машин, подверженным циклическим нагрузкам.
13

Предел выносливости для отнулевого цикла обозначают индексом «0» (ζ0 ; η0), для симметричного цикла – «-1» (ζ-1 ;η-1), то есть коэффициент асимметрии цикла «r» сопровождает обозначение предела выносливости (ζr ; ηr).
2.3. Диаграмма усталости. Процесс усталостногоразрушения
На основе большого числа экспериментальных работ построены кривые усталости, отражающие влияние числа циклов на напряжение, разгружающее образец (рис. 2.2): N1 N2 – число циклов нагружения до разрушения образца при напряжениях ζ1 и ζ2.
σ1 |
|
|
|
σr |
|
σ2 |
|
|
N1 |
N2 |
N |
σ |
σr |
σD |
lgN |
Рис. 2.2 Формы кривой усталости Кривые усталости показывают, что:
–разрушающее напряжение в области малых N близко к показателям статической прочности;
–по мере увеличения N величина разрушающих напряжений уменьшается и при некотором числе циклов стабилизируется
–ордината горизонтального участка кривой усталости
(ζD) является пределом выносливости.
Для большинства конструкционных сталей предел выносливости определяют при 106…107 циклов. Эти значения и
берут за базу испытаний. Для цветных металлов, например алюминия, даже при числе циклов 107…108 наблюдается дальнейшее медленное падение разрушающего напряжения. В этом случае говорят об ограниченном пределе выносливости (обыч-
но это 5 107).
14

Испытания на выносливость проводят при симметричных знакопеременных циклах (r = -1), у которых амплитуда напряжений наибольшая, а предел выносливости наименьший. С увеличением (r) пределы выносливости возрастают и при некоторых значениях (r), близких к единице (колебания малой амплитуды), становятся практически постоянными (верхняя линия) и равными показателям статической прочности.
σ |
r = 0,6…1,0 |
|
|
|
r = -0,5 |
|
r = -1,0 |
|
lgN |
Рис. 2.3 Влияние коэффициента асимметрии цикла на форму кривой усталости
2.4. Развитие усталостных повреждений
На первой стадии нагружения возникают в отдельных кристаллических объемах пластические сдвиги, необнаруживаемые обычными экспериментальными методами. Затем сдвиги охватывают все большие объемы и переходят в субмикроскопические сдвиги, наблюдаемые с помощью электронных микроскопов.
При определенном числе циклов и уровне напряжений (рис. 2.4 кривая 1) образуется множество трещин, видимых под оптическим микроскопом. Эта стадия характеризует порог трещинообразования (0,7…0,8) разрушающего напряжения для углеродистых и низколегированных сталей. С приближение напряжений к пределу выносливости развитие трещин вступает в критическую фазу (кривая 2). Далее микротрещины, прогрессивно расширяясь, превращаются в макротрещины, которые приводят к разрушению (кривые 3).
15
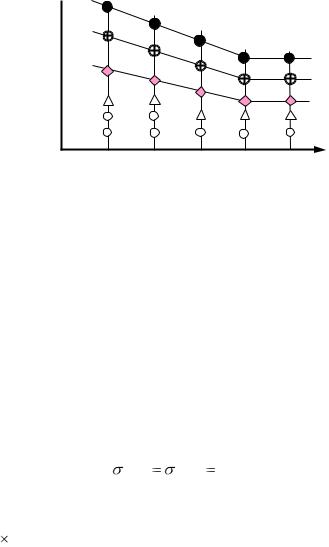
|
|
|
3 |
|
|
|
2 |
|
|
|
1 |
104 |
105 |
106 |
lgN |
Рис. 2.4 Развитие усталостных повреждений |
2.5. Учет переменного характера режима нагружения
Большинство зубчатых передач работают в условиях переменных режимов нагружения. Расчет таких передач по максимальным нагрузкам приводит в предположении их постоянного действия приводит к ненужному утяжелению передачи.
В настоящее время для расчета таких передач принято за
расчетную принимать максимальную рабочую нагрузку, а переменный характер нагружения учитывать соответствующим выбором допускаемых напряжений.
Из уравнения кривой Велера следует:
m N |
i |
m N |
0 |
cos t , |
i |
0 |
|
где N0 – число циклов нагружения до перегиба кривой усталости (базовое число циклов). При расчете на изгиб N0 =3 106; при расчете на контактную прочность N0 = 107;
ζ0 – предел выносливости;
ζi и Ni – напряжение и число циклов нагружения до разрушения;
m – показатель кривой усталости. Можно записать, что:
16

m |
N E |
m |
N0 |
или |
|
m |
|
N0 |
|
|
0 |
0 |
NE |
|
|||||
|
|
|
|
|
|
|
|
|
В этом случае:
KL |
m |
|
N0 |
|
, |
|
NE |
||||||
|
|
|
|
|
где [ζ] – допускаемое напряжение при переменном режиме нагружения с эквивалентным числом циклов нагружения NE;
[ζ]0 – допускаемое напряжение при длительной работе (здесь предел выносливости при отнулевом цикле, r = 0);
KL – коэффициент долговечности или режима нагрузки. Если NE > N0 , то деталь работает за перегибом кривой устало-
сти и KL =1,0;
NE – эквивалентное число циклов нагружения при напряжениях [ζ].
Эквивалентным называют расчетное (воображаемое) число циклов, которое при постоянной нагрузке дало бы такой же эффект усталости, что и действительная переменная нагрузка в течение фактического числа циклов.
2.6. Методы определения допускаемых напряжений
Существуют два метода выбора допускаемых напряжений а) табличный метод – конкретен, прост, удобен для
пользования. Широко используется в НИИ, на заводах, СКТБ…
В зависимости от материала, вида термической обработки, технологии изготовления, цикла нагружения приведены в таблицах заранее рассчитанные значения допускаемых напряжений для отдельных видов деталей.
б) дифференциальный метод, заключающийся в том, что допускаемое напряжение определяется по формуле, учитывающей основные факторы, влияющие на прочность детали.
Например: по ГОСТ 21354-75 допускаемые контактные напряжения [ζ]H определяют по формуле:
17
[ζН] = ζН· KНL· ZR· ZV /SH
где ζН – предел контактной выносливости при базовом числе циклов;
KНL – коэффициент долговечности;
ZR – коэффициент, учитывающий шероховатость сопряженных поверхностей;
ZV – коэффициент, учитывающий окружную скорость (при приближенном расчете ZR· ZV ≈ 1,0);
SH – коэффициент безопасности (1,1…1,3) в зависимости от термообработки.
3. СОЕДИНЕНИЯ. ТИПЫ СОЕДИНЕНИЙ И ИХ ХАРАКТЕРИСТИКА
3.1. Общая характеристика соединений
Каждая машина состоит из деталей, число которых зависит от сложности и размеров машины. Так автомобиль содержит около 16 000 деталей (включая двигатель), крупный карусельный станок имеет более 20 000 деталей и т.д.
Чтобы выполнять свои функции в машине детали соединяются между собой определенным образом, образуя подвиж-
ные и неподвижные соединения. Например, соединение колен-
чатого вала двигателя с шатуном, поршня с гильзой цилиндра (подвижные соединения). Соединение штока гидроцилиндра с поршнем, крышки разъемного подшипника с корпусом (неподвижное соединение).
Подвижные соединения определяют кинематику машины, а неподвижные – позволяют расчленить машину на отдельные блоки, элементы, детали.
С точки зрения общности расчетов все соединения делят на две большие группы: неразъемные и разъемные соединения.
Неразъемными называют соединения, которые невозможно разобрать без разрушения или повреждения деталей. К
18