
3607
.pdfним относятся заклепочные, сварные, клеевые соединения, а также соединения с гарантированным натягом. Неразъемные соединения осуществляются силами молекулярного сцепления (сварка, пайка, склеивание) или механическими средствами (клепка, вальцевание, прессование).
Разъемными называют соединения, которые можно многократно собирать и разбирать без повреждения деталей. К разъемным относятся резьбовые, шпоночные и шлицевые соединения, штифтовые и клиновые соединения.
Проектирование соединений является очень ответственной задачей, поскольку большинство разрушений в машинах происходит именно в местах соединений.
К соединениям в зависимости от их назначения предъяв-
ляются требования прочности, плотности (герметичности) и жесткости.
При оценке прочности соединения стремятся приблизить его прочность к прочности соединяемых элементов, т.е. стре-
мятся обеспечить равнопрочность конструкции.
Требование плотности является основным для сосудов и аппаратов, работающих под давлением. Уплотнение разъемного соединения достигается за счет:
1)сильного сжатия достаточно качественно обработанных поверхностей;
2)введения прокладок из легко деформируемого мате-
риала.
При этом рабочее удельное давление q в плоскости стыка должно лежать в пределах q = (1,5…4)p, p – внутренне давление жидкости в сосуде.
Экспериментальные исследования показали, что жесткость соединения во много раз меньше жесткости соединяемых элементов, а поскольку жесткость системы С0:
1С0=1С1+1С2+1С3 ,
всегда меньше жесткости наименее жесткого элемента, то именно жесткость соединения определяет жесткость системы.
19
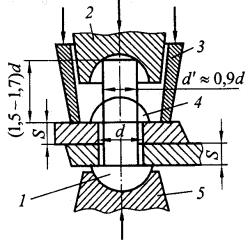
3.2. Заклепочные соединения. Общие сведения
Заклепкой называется стержень круглого сечения с заранее изготовленной закладной головкой на одном конце и замыкающей головкой на другом, образующейся в процессе клѐпки.
Заклѐпки применяются для соединения таких деталей машин и сооружений, которые представляют собой полосы, листы, прокатные профили и др.
Сопрягаемые детали 1 и 2 (рис. 3.1) стягиваются заклѐпкой, которая состоит из стержня 3 круглого сечения и закладной головки 4. Заклѐпку вставляют в совмещѐнные отверстия d0 и, осаживая выступающий конец стержня, образуют вторую замыкающую головку 5. Формирование этой головки производится с помощью обжимки 6. Закладная головка устанавливается в поддержке 7. Процесс образования замыкающей головки называется клѐпкой.
Рис. 3.1 Схема клепки
При диаметре стальных заклѐпок до d = 12 мм, применяют холодную клѐпку, при большем диаметре – горячую. Для обеспечения ввода заклѐпки отверстие в склѐпываемых деталях делают несколько больше диаметра стержня заклѐпки.
20
Клѐпку проводят вручную или машинами. При машинной клѐпке отверстие заполняется металлом лучше, что благоприятно сказывается на работе заклѐпочного соединения. Во избежание химической коррозии в соединениях заклѐпки ставят из того же материала, что и соединяемые детали. Заклѐпки изготавливают из стали (ст.2; ст.3; ст.10; ст.20), алюминия, латуни и меди. Материал заклѐпки должен быть достаточно пластичным.
Заклѐпочные соединения до сих пор применяются в ответственных конструкциях, воспринимающих интенсивные вибрационные или большие повторные ударные нагрузки (самолѐты, уникальные мосты). Кроме того, заклѐпочные соединения применяются в конструкциях, не допускающих применение сварки, из-за опасности коробления, отпуска термообработанных деталей или при склѐпывании не свариваемых деталей.
Соединение деталей машин или сооружения осуществляемого группой заклѐпок называется заклепочным (рис. 4).
К недостаткам заклѐпочных соединений относятся большой расход металла и повышенную трудоѐмкость. Вес заклѐпок составляет 4% от веса конструкции (вес сварных швов – 1,5%).
3.3. Классификация заклепок и заклепочных швов
Основные виды заклѐпок общего назначения стандартизованы. Различают следующие основные виды заклѐпок:
-заклѐпки с полукруглой головкой ГОСТ 14797-85 и
10299-80 (Рис. 3.2, а);
-заклѐпки с плоской головкой ГОСТ 14801-85 (Рис.
3.2, б);
-заклѐпки с потайной головкой ГОСТ 14798-85, 14799-69, 10300-80 (Рис. 3.2, в);
-заклѐпки полупустотелые ГОСТ 12641-80, 12643-80 (Рис. 3.2, г, д, е);
-пустотелые со скруглѐнной ГОСТ 12638-80 и потайной ГОСТ 12640-80 головками (Рис. 3.2, ж, з, и).
21

Рис. 3.2 Стандартные стальные заклепки
Пустотелые заклѐпки применяются для того, чтобы использовать их отверстие в заклѐпочном соединении для пропуска электрических проводников, крепѐжных или других деталей.
Полупустотелые заклѐпки применяются в тех случаях, когда не желательно или не допустимо заклѐпочные соединения подвергать ударам.
В отдельных случаях применяют специальные заклѐпки, например взрывные.
Заклѐпочные швы подразделяются: По конструкции:
-швы внахлѐстку (Рис. 3.3, а, г);
-швы встык с одной накладкой (Рис. 3.3, б);
-швы встык с двумя накладками (Рис. 3.3, в). По расположению заклѐпок:
-однорядные (Рис. 3.3, а, б, в);
-многорядные:
-а) рядовым построением (Рис. 3.3, г);
-б) шахматным построением.
По числу заклѐпок работающих на срез:
-односрезные (Рис. 3.3, а, б, г);
-двухсрезные (Рис. 3.3, в);
-многосрезные.
22

По назначению:
-прочные (узлы машин);
-плотные (паровые котлы, баки и т. п.).
Рис. 3.3 Типы заклепочных соединений:
а– нахлесточные; б – стыковые с одной накладкой;
в– стыковые с двумя накладками; г – нахлесточные многорядные
23

3.4.Расчет прочных заклепочных швов
Впрочных швах герметичность соединений не требуется, поэтому силы, действующие на соединяемые детали могут быть больше сил трения, развиваемых между этими деталями. Таким образом, при работе прочного шва возможен и допустим сдвиг одной детали относительно другой. Поэтому заклѐпки прочных швов рассчитываются на срез и на смятие.
Для данного заклѐпочного шва можно записать следующие условия прочности (рис. 3.4).
Рис. 3.4 Расчетные схемы односрезного (а – б); двухсрезного (в) заклепочного соединения
24
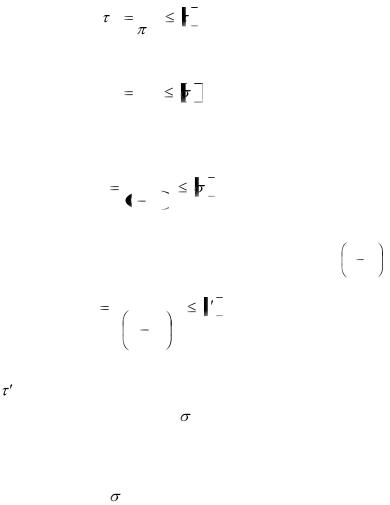
На срез заклѐпки:
|
4F1 |
|
; |
(3.1) |
cp |
d 2 |
cp |
||
|
|
|
|
На смятие между заклѐпкой и листом:
σсм |
F1 |
|
см ; |
|
|
(3.2) |
|||||||||
d S |
|
|
|||||||||||||
|
|
|
|
|
|
|
|
|
|
||||||
На растяжение (разрыв) листа в сечении, ослабленном |
|||||||||||||||
отверстиями под заклепки: |
|
|
|
|
|
|
|
||||||||
σP |
|
|
F1 |
|
|
Р ; |
|
|
(3.3) |
||||||
|
t |
d S |
|
|
|
||||||||||
|
|
|
|
|
|
|
|
|
|||||||
На срез листа одновременно по двум сечениям до кромки |
|||||||||||||||
листа, в предположении, что срез происходит по длине |
|
|
d |
: |
|||||||||||
2 |
|||||||||||||||
|
|
|
|
|
|
|
|
|
|
|
|
||||
τ' |
|
|
F1 |
τ |
|
; |
|
(3.4) |
|||||||
|
|
|
|
|
|
|
ср |
|
|||||||
ср |
|
|
|
d |
|
|
|
|
|
|
|
|
|||
|
2 |
|
S |
|
|
|
|
|
|
|
|||||
|
2 |
|
|
|
|
|
|
|
|||||||
|
|
|
|
|
|
|
|
|
|
|
|
||||
здесь: F1 – сила, действующая на участок шва шириной t; |
|
|
|
||||||||||||
[ ср ] – допускаемое напряжение на срез для листов. |
|
|
|
||||||||||||
Из уравнений (а) и (б) при |
cp.= 1,6 ηcp. получим: |
|
|
|
|
||||||||||
|
|
|
D = 2s = 2 |
|
|
|
|
|
|
Из уравнений а и в при
[ ]cp.= [η]cp. ; d = 2S;
следует, что
t = 2,6d;
Принимают t = 3d
Из уравнений (а) и (г) при [η’]cp = 0,8 [η]cp; получим
ℓ ≈ 1,5d;
25

Принимают
ℓ ≈ (1,5…2)d;
Аналогично получаются подобные соотношения параметров для других типов швов. Зная размеры заклѐпочного вала, надо проверить заклѐпки на срез
τ |
4F1 |
|
ср n π d 2 |
ср |
и на смятие
σсм |
F1 |
|
|
см . |
|
|
||
|
n d Smin |
Здесь: F1 – сила, действующая на одну заклѐпку; n – число срезов заклѐпки.
При симметрично действующей силе F необходимое число заклѐпок (z) определяется из соотношения:
Ζ |
4F |
; |
|||
|
|
|
|||
n π d |
2 |
[τ] |
|||
|
|
||||
|
|
|
ср |
|
Полученное число заклѐпок Z проверяют расчѐтом заклѐпок на смятие:
σсм |
F |
[σσсм ; |
|
|
|||
Ζ d Smin |
|||
|
|
При действии на заклѐпочный шов знакопеременных нагрузок, допускаемые напряжения для низкоуглеродных сталей ст. 2, ст. 3, сталь 10, сталь 20 понижают умножением на коэффициент γ:
γ
1
1 0,3 pmin
pmax
26

где: pmin и pmax – соответственно минимальное и максимальное значение нагрузки, взятое со своим знаком.
Действительные напряжения в листе, в сечении, ослабленном отверстиями под заклепки равно:
F
σ p1 t d S ;
а в неослабленном сечении по основному металлу:
|
σ p2 |
F |
|
; |
|
|||
|
t S |
|
||||||
|
|
|
|
|
||||
Отношение |
σ p1 |
называется коэффициентом прочно- |
||||||
σ p2 |
||||||||
|
|
|
|
|
|
|
||
сти шва. |
|
|
|
|
|
|
|
|
|
|
|
|
t |
d |
; |
||
|
|
|
|
|
|
t |
||
|
|
|
|
|
|
|
Так как расчѐт соединяемых заклѐпками деталей производится по сечению, ослабленному отверстиями, то при этом следует учитывать коэффициент θ.
Например, площадь поперечного сечения (брутто) детали, работающей на растяжение от силы F
F
S [ ][ ]P ;
здесь: [θ] – допускаемый коэффициент прочности шва. Величиной [θ] задаются в пределах 0,6…0,85; затем ус-
танавливается тип шва.
Определяют его параметры d, t и f.
Если окажется, что предварительно принятая величина [θ] значительно отличаются от действительной величины θ, то расчѐт уточняется.
27
4. СВАРНЫЕ СОЕДИНЕНИЯ
4.1. Общие сведения
Сварные соединения относятся к неразъемным соединениям. Сварка – это технологический процесс соединения металлических деталей, основанный на использовании сил молекулярного сцепления. Сварка осуществляется при сильном местном нагреве деталей до расплавленного состояния сварка плавлением, или до пластического состояния с применением механического усилия сварка давлением.
Сварка является одним из самых распространѐнных современных способов получения различных машиностроительных, строительных и других конструкций, сваркой изготавливаются станины, рамы, барабаны, фермы, зубчатые колѐса, шкивы, звѐздочки, маховики и др. Затвердевший после сварки металл, соединяющий сваренные детали, называется сварным швом.
По сравнению с клѐпаными и литыми, сварные конструкции обеспечивают значительную экономию металла и снижение трудоѐмкости. Применение сварки вместо клѐпки даѐт экономию в весе конструкции до 10…20% . Экономия в весе сварных конструкций по сравнению с чугунными литыми доходит до 50%, а по сравнению со стальными литыми – до 30%.
В связи с этим в настоящее время сварные конструкции, за исключением некоторых случаев, вытеснили клѐпанные как из машиностроения, так и из строительства.
4.2. Недостатки сварных соединений:
а) возникновение остаточных напряжений в свариваемых элементах после окончания сварки;
б) коробление; в) плохое восприятие переменных и особенно, вибраци-
онных нагрузок; г) сложность контроля качества сварного шва.
28