
3607
.pdf22.4. Обозначение подшипников
Обозначение подшипников составляется из цифр, условно характеризующих размеры его отверстия, серию, тип и конструктивные особенности.
Две первые цифры справа (умноженные на 5) – это внутренний диаметр подшипника (d = 20…495 мм).
Третья цифра справа – серия подшипника 1 – особо легка; 2 – легкая; 3 – средняя; 4 – тяжелая и т.д. Четвертая справа – тип подшипника
0– радиальный шариковый однорядный,
1– радиальный шариковый двухрядный сферический,
2– радиальный с короткими цилиндрическими роликами,
3– радиальный роликовый двухрядный сферический,
4– роликовый с длинными цилиндрическими роликами,
5– роликовый с витыми роликами,
6– радиально-упорный шариковый,
7– роликовый конический,
8– упорный шариковый,
9– упорный роликовый.
Пятая или пятая и шестая справа цифры (не для всех подшипников) обозначают конструктивные особенности.
Например: 60 205 – подшипник шариковый (0 – четвертая цифра) радиальный однорядный с одной защитной шайбой (6)
– пятая цифра. Внутренний диаметр d = 05×5 = 25 мм. Цифры 6, 5, 4, 2, которые ставятся перед обозначением через тире (5- 60205) обозначающий класс точности. Нормальный класс точности обозначается цифрой «0», которая не указывается.
22.5. Точность подшипников качения
Определяется:
а) точностью основных размеров; б) точность вращения.
Точность основных размеров определяется отклонениями размеров внутреннего и наружного диаметров и ширины коль-
219

ца. Отклонения размеров диаметров определяет характер посадки.
Точность вращения характеризуется радиальным и боковым биением дорожки качения. В РФ подшипники качения выпускаются следующих классов в порядке возрастания точ-
ности: |
|
|
|
|
|
Класс точности |
0 |
6 |
5 |
4 |
2 |
Радиальное биение |
|
|
|
|
|
Внутреннего кольца, мкм |
20 |
10 |
5 |
3 |
2,5 |
Для большинства осей и валов общего назначения применяются подшипники класса точности «0» (нормального).
22.6.Причины выхода подшипников из строя
икритерии расчета
1.Усталостное выкрашивание рабочих поверхностей. Это явление связано с образованием в поверхностных слоях контактирующих тел знакопеременных напряжений. Образуются трещины, которые после расклинивания их смазкой, приводят
квыкрашиванию. Обычно это характерно для внутренних колец. Усталостное выкрашивание – основная причина выхода из строя подшипников.
2.Разрушение колец и тел качения. Это механический вид разрушения. Наблюдается скалывание буртов колец роликоподшипников (из-за перекосов). При больших динамических нагрузках разрушаются кольца и шарики (раздавливаются).
3.Износ колец и тел качения. Наблюдается при работе подшипников в абразивной среде (транспортные и с/х машины). Необходимо совершенствовать конструкцию уплотнений.
4.Образование вмятин на рабочих поверхностях (бринеллирование) наблюдается при динамических и больших статических нагрузках без вращения.
5.Разрушение сепараторов вызывается силами и воздействием на сепаратор тел качения.
Подшипники рассчитывают по критерию статической грузоподъемности и по критерию выносливости.
220

22.7. Расчет подшипников качения на долговечность
Экспериментально установлено:
C
L ,
Q
где L – ресурс подшипника – суммарное число миллионов оборотов до появления признаков усталости;
C – динамическая грузоподъемность. Это постоянная радиальная нагрузка, которую подшипник может выдержать в течение 10 оборотов;
Q – приведенная нагрузка, воспринимаемая подшипни-
ком.
α – показатель степени для шарикоподшипников α = 3, для роликоподшипников α = 3,3.
Подшипники явились первой группой деталей для которой был введен расчет на долговечность.
22.8. Определение приведенной нагрузки и подбор подшипников качения
Подшипники часто подвергаются действию осевой и радиальной нагрузок. А сама нагрузка может быть статической или динамической. Вращаться может наружное или внутреннее кольцо, а температура подшипника может быть нормальной, повышенной или пониженной. Все эти факторы должны быть учтены при выборе приведенной нагрузки.
Приведенную нагрузку (радиальную) для радиальных шарикоподшипников и радиально-упорных шарико- и роликоподшипников определяют по формуле
Q = (X·Kk·Fr + Y·Fa)Kб·КТ.
где Fr – постоянная по величине и направлению радиальная нагрузка на подшипник;
Fa – постоянная по величине и направлению осевая нагрузка на подшипник;
221
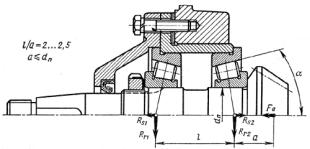
Х, Y – коэффициенты радиальной и осевой нагрузки;
Kk – коэффициент вращения: Kk = 1 (вращается внутреннее кольцо), Kk = 1,2 (вращается наружное кольцо).
КТ – температурный коэффициент. Вводится только при tº > 100º.
КТ |
1,05 |
1,1 |
1,25 |
tºС |
1,25 |
150 |
200 |
Для подшипников с короткими цилиндрическими роликами приведенная нагрузка равна:
Q = Fr·Kб·КТ·Кк.
Приведенная осевая нагрузка для упорно-радиальных шарико- и роликоподшипников:
Q = (X· Fr + Y·Fa)Kб·КТ.
При расчете радиально-упорных шарико- и роликоподшипников необходимо читывать, что в них радиальном нагружении и отсутствии осевого зазора и натяга возникает дополнительная осевая сила. Тогда, осевая нагрузка Fa действующая на радиально-упорный подшипник определяется с учетом осевой составляющей S радиальной нагрузки Fr, действующей на опоры.
Рис. 22.2. Схема нагружения радиально-упорного подшипника
Для радиальных и радиально-упорных шарикоподшипников
S= е Fr.
222

Для конических роликоподшипников
S= 0,83 е Fr.
где е – вспомогательный коэффициент.
Величина коэффициента е выбирается по таблицам ка-
талога подшипников в зависимости от соотношения A ,
C0
где А – осевая нагрузка (А = Fa);
С0 – статическая грузоподъемность подшипника
Отношение |
A |
выбирается согласно типу предвари- |
|
|
|||
C0 |
|||
|
|
тельно принятого подшипника по таблице каталога подшипников.
Зная S1 = е Fr1 |
и S2 = е Fr2, можно определить расчетные |
|||
осевые нагрузки Fa1 |
и Fa2 |
с учетом значений S1 |
и S2. |
|
Величины Fa1 |
и Fa2 |
определяют по формулам в зависи- |
||
мости от схемы нагружения принятых подшипников. |
||||
Например, для радиально-упорных подшипников. |
||||
|
|
|
|
Таблица 27.1 |
Условия нагружения |
|
Осевые нагрузки |
||
1. S1 > S2; Fa > 0 |
|
|
Fa1 = S1; |
|
2. S1 < S2; Fa ≥ S1 – S2 |
|
Fa2 = S1+ Fa |
(Fa = А) |
|
3. S1 < S2; Fa ≤ S1 – S2 |
|
Fa1 = S2 – Fa |
|
|
|
|
|
Fa2 = S2 |
|
22.9. Подбор подшипников качения
По вычисленной приведенной нагрузке (Q) и расчетному
ресурсу L |
60n |
L |
миллионов оборотов на основе исходной |
||
|
|
||||
|
106 |
|
h |
|
|
|
|
|
|
||
зависимости |
|
C |
|
L определяемую требуемую динамиче- |
|
|
|
|
|
||
|
Q |
|
|||
|
|
|
|
скую грузоподъемность:
223

C QL1 / ,
Lh – ресурс подшипника, в час.
Зная «С» по каталогу выбирают подшипник.
Часто подшипники подбирают по конструктивным соображениям, тогда расчетом проверяют их ресурс
106 C
Lh 60n Q ,
где Lh – ресурс подшипника в часах n – частота вращения, об/мин.
В общем машиностроении ресурс подшипника принима-
ют Lh = 2500…10000 час.
Подшипники, работающие при переменных режимах подбирают по эквивалентной нагрузке. Под эквивалентной нагрузкой понимают нагрузку, которая вызывает такой же эффект усталости, что и весь комплекс действительных нагрузок.
|
Q3L |
Q3L |
... Q3L |
|
Qэкв |
1 1 |
2 2 |
n n |
, |
3 |
|
|
|
|
|
|
L |
|
|
где Q1 – постоянная нагрузка, действующая в течение L1 миллионов оборотов;
Q2 – постоянная нагрузка, действующая в течение L2 миллионов оборотов;
L – общее число миллионов оборотов, в течение которого действуют нагрузки Q1, Q2, …, Qn.
Суммирование производят по числу режимов работы. Если нагрузка на подшипник изменяется по линейному
закону от Qmin до Qmax , то
Qэкв Qmin 32Qmax .
224

22.10. Статическая грузоподъемность подшипников
Подшипники качения грузоподъемных транспортных и других машин периодически подвержены нагрузкам без вращения. В этом случае основной характеристикой подшипника является его статическая грузоподъемность, т.е. нагрузка на невращающийся подшипник. Статическая грузоподъемность выбирается из условия, при котором общая остаточная деформация тела качения и кольца не должна превышать величину, заметно влияющую на работу подшипника.
Например, статическая грузоподъемность радиальных и радиально-упорных подшипников равна:
C0 K0 i
Z
dm2
Cos ,
где К0 – коэффициент, равный для радиальных и радиальноупорных подшипников К0 = 1,25;
i, Z – число рядов и число тел качения в ряду; dm – диаметр шарика, мм;
β – номинальный угол контакта.
22.11. Распределение нагрузки между телами качения
Если рассматривать распределение нагрузки R, действующей на радиальный шарикоподшипник, то окажется, что эта нагрузка распределяется между телами качения неравномерно. Нагруженная зона составляет не более 180º.
Для упрощения предположим, что тела качения занимают симметричное положение относительно нагрузки, тогда
R = P0 + 2P1Cosγ + 2P2Cos2γ,
где γ , 2γ, …nγ – углы между направлением силы R и радиальной плоскостью соответствующего шарика.
Осевая сила при точном изготовлении и отсутствии взаимного перекоса колец распределяется между телами качения практически равномерно.
225

В шарикоподшипниках начальный контакт между шариком и кольцами происходит в точке. После приложения нагрузки зона контакта принимает эллиптическую форму. При этом необходимо, чтобы контактное напряжение в центре этой площадки не превышало допустимого значения (ζH max ≤ [ζ]H), [ζ]H = 5000 МПа.
Рис. 22.3. Распределение нагрузки между телами качения
Потери на трение складываются из следующих составляющих:
а) трение между телами качения и кольцами. Этот вид трения состоит из трения качения и дополнительного трения скольжения. Качение в наиболее чистом виде характерно для цилиндрических роликоподшипников. В этом случае все точки линии контакта по длине ролика имеют одинаковую окружную скорость. В шарикоподшипниках и сферических роликоподшипниках контактов в поперечном сечении происходит по дуге. Окружные скорости точек линии контакта различны, что приводит к проскальзыванию и потерям на трение скольжения.
б) трение скольжения тел качения (роликов) в конических роликоподшипниках. В этом случае трение скольжения имеет место между торцевой поверхностью ролика и буртом внутреннего кольца.
в) трение, связанное с погрешностями формы тел качения и колец, переносом роликов и т.д.
г) трение тел качения о сепаратор и сепаратора о кольца д) сопротивление масла
226
е) трение в уплотнениях (встроенные уплотнения).
При малых нагрузках основное значение имеют сопротивления, связанные со смазкой и трением в сепараторе, а при более высоких – трение на площадке контакта между телами качения и кольцами.
Момент трения в подшипниках обычно представляется простейшими зависимостями.
M = 0,5·fR·R·d или M = 0,5·fA·A·d,
где R и A – радиальная и осевая нагрузки;
fR и fA – приведенные коэффициенты трения; d – диаметр вала.
Более точно момент трения в подшипнике определяется по формуле:
M = 0,5(T + f0R)d,
где T = cd – сила сопротивления, не зависящая от нагрузки. Значения коэффициентов fR , fA, f0, и с при окружных скоростях на шейке вала до 10 м/с и умеренной смазке находят из таблицы.
22.12. Смазка подшипников качения
Смазка подшипников необходима для уменьшения трения, для усиления теплоотвода, для предотвращения коррозии и уменьшении шума. В качестве смазки подшипников применяют пластичные смазки и минеральные масла.
Пластичные смазки целесообразно применять для подшипников, труднодоступных для повседневного обслуживания, работающих в загрязненной среде. Применение пластичных смазок целесообразно для подшипников, работающих с
окружной скоростью на валу V≤ 7 м/с при температуре tсро ≤
70…100 ºС. С этой целью широко применяют различные вазелины, солидолы и более тугоплавкие смазки. Эти смазки экономичны, способны длительное время (до года) работать без замены, лишь с периодическим (через 3 мес.) пополнением. В корпусе подшипника для пластичной смазки предусматривают
227
некоторое свободное пространство (стенки крышек располагают не вплотную к подшипнику). Это пространство первоначально заполняют на 2/3 от свободного объема при n ≤ 1500
об/мин и на 1/3…1/2 при n > 1500 об/мин.
Однако сейчас все больше применение находят герметизированные подшипники с одноразовой смазкой. Пластичные смазки герметизируют уплотнения подшипников:
ЦИАТИМ-201 – до 90 ºС, Литол-24 – до 100 ºС, ЦИАТИМ-221 – до 150 ºС.
Жидкие смазки применяют, когда требуются минимальные потери на трение и при высоких температурах. В качестве жидкой смазки применяют минеральные масла.
К недостатками жидких смазок следует отнести их меньшую экономичность, больший расход и применение более сложных уплотнений. Вязкость жидкой смазки выбирают:
–тем выше, тем больше t° среды, для предупреждения ее чрезмерного разжижения;
–тем выше, чем больше нагрузки, т.к. прочность пленки расчет с увеличением вязкости;
–тем ниже, чем выше частота вращения (воизбежание повышения потерь на трение).
Индустриальные жидкие масла И-Л-А7 – маловязкие; И-Л-А27 – маловязкие; И-Г-А-32 – средневязкие.
Существуют следующие способы смазки жидкими маслами: а) смазка окунанием в масляную ванну – для подшипни-
ков горизонтальных валов при n ≤ 10000 об/мин.
Уровень масла не выше центра нижнего шарика, а при n > 3000 об/мин еще ниже.
б) смазка разбрызгиванием из общей масляной ванны – для подшипников горизонтальных валов редукторов, коробок передач. Масло захватывается и разбрызгивается одним из зубчатых колес, специальной шестерней или дисками. В корпусе создается туман. Ставят маслоотражательные кольца.
228