
3360
.pdf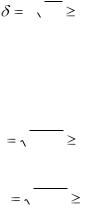
25.3. Расчет основных конструктивных параметров редукторов
Для удобства сборки корпус редуктора выполняется составным – основание и крышка. Основание с помощью лап или пояса крепится к фундаменту или раме. Для точной установки крышки на основание корпуса пользуются коническими штифтами.
Корпус редуктора должен быть прочным и жестким, т.к. его деформации могут вызвать перекос валов и неравномерное распределение нагрузки по длине зубьев. Для повышения жесткости корпуса его усиливают наружными или внутренними ребрами.
Корпусы редукторов обычно выполняют литыми из серого чугуна (СЧ 15-32/ СЧ 18-36) средней прочности. Для передачи больших мощностей или ударных нагрузок корпусы отливают из высокопрочного чугуна или стали. В индивидуальном и мелкосерийном производствах корпусы редукторов изготавливают сварными из листовой стали.
Основные размеры корпуса – длина, ширина и высота – применяются в зависимости от размеров зубчатых колес. Другие размеры находятся по империческим формулам. Например, толщина (δ) стенок чугунных литых оснований корпуса равна:
24M 6 мм.
Толщина стенок крышек:
δK = 0,9δ.
где: М – момент на тихоходном валу, 10 Н·м Диаметры болтов крепления крышки:
d 3 20M 10 мм.
Диаметры фундаментных болтов:
dФ 3 40M 12 мм.
Толщина фундаментных лап:
SФ=1,5dФ.
69
Ширина пояса или лап для расположения болтов принимается из соотношения:
bП = (2,1 … 2,5)d.
d – диаметр болта данного пояса.
Рекомендуемый ряд крутящих моментов на тихоходных валах редукторов в соответствии с проектом международного стандарта составляет по нормальному ряду чисел со знаменателем 2 в диапазоне 1-125 Н·м и со знаменателем 1,41 в диапа-
зоне 125–1000000 Н·м.
Передаточные числа редукторов выбирают по нормальному ряду чисел со знаменателем 1,25 (1-й предпочтительный ряд) или со знаменателем 1,12 (2-й ряд) (ГОСТ )
Межосевые расстояния быстроходной (αWБ) и тихоходной (αWT) ступеней двух и трехступенчатых редукторов зубчатых цилиндрических должны соответствовать ГОСТ
Валы, как правило, подвергают улучшению до твердости НВ 270 – 300. Валы d ≤ 80 мм допускается изготавливать из стали 45; диаметром d = 80-125 – из стали 40X; а валы d = 125 – 200 мм – из стали 40ХН; 35ХМ. Тихоходные валы имеют выходной конец, в котором напряжения кручения составляют около 28 МПа концы валов целесообразно выполнять коническими.
Опоры валов редукторов ВЫПОЛНЯЮТСЯ в виде подшипников качения. Обычно в опорах устанавливается по одному подшипнику качения. При малых и средних нагрузках применяют шарикоподшипники, при средних и больших – роликоподшипники. В редукторах с шевронной передачей быстроходный вал передачи устанавливают на плавающих, обычно, цилиндрических роликоподшипниках. Это обеспечивает самоустановку вала по оси и одинаковую нагрузку полушевронов.
В редукторах с конической передачей для лучшей фиксации зубчатых колес в осевом направлении валы передачи рекомендуется устанавливать на радиально-упорных, чаще конических роликоподшипниках.
Смазка зацепления при V ≤ 12,5 м/c рекомендуется картерная (окунанием). Емкость масляной ванны назначают из расчета
70
0,35 – 0,7 литра на I кВт передаваемой мощности (большие значения – при большей вязкости масла и наоборот). Зубчатые колеса следует погружать в масло на глубину 3-4 модуля. Тихоходные колеса (2-й и 3-й ступени) при необходимости допустимо погружать на величину до 1/3 диаметра колеса. В редукторах с быстроходными передачами применяют струйную или циркуляционную смазку, осуществляемую под давлением. Масло, прокачиваемое насосом, проходит через фильтр и при необходимости через охладитель, а затем поступает к зубьям через трубопровод и сопла. При окружной скорости V ≤ 20 м/c для прямозубых передач и при V ≤ 50 м/с для косозубых масло подается непосредственно в зону зацепления. При V > 50 м/c (V > 20 м/c) , во избежание гидравлического удара, масло подается раздельно на шестерню и колесо и на некотором расстоянии от зоны зацепления.
Смазка подшипников редуктора при V > 4 м/c может осуществляться тем же маслом, что и зубчатых колес, путем разбрызгивания масла. При V < 4 м/с предусматривается самостоятельная (консистентная) смазка. При больших скоростях и нагрузках на подшипники предусматривается смазка под давлением, осуществляемая от общей системы.
Расчет зубчатого редуктора состоит из расчета его элементов – передач, валов, шпонок, подшипников. Для редукторов большой мощности производится тепловой расчет. При расчете зубчатых передач редукторов, выполненных в виде самостоятельных агрегатов, основные параметры этих передач должны быть согласованы с соответствующими ГОСТ.
Червячные колеса с целью экономии цветных металлов выполняются с венцом из антифрикционных материалов и стальным или чугунным центром.
- бандажированная конструкция, в которой бронзовый обод (венец) посажен на стальной центр с натягом. Рекомендуется легкопрессовая реже прессовая посадки. Чтобы исключить возможность сдвига венца, ввертывают в стыкуемые поверхности винты. Конструкция применяется для колес относительно небольших размеров и ненапряженных в тепловом отношении (рис. 25.2).
71
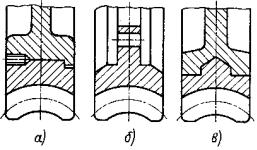
-болтовая конструкция, в которой бронзовый венец, выполненный с фланцем, прикрепляется болтами к ступице колеса. Применяется для колес больших и средних диаметров.
-биметаллическая конструкция, бронзовый венец, который отлит в форму с предварительно вставленным в нее центром. Конструкция наиболее рациональна и применяется в редукторах серийного производства.
Рис.25.2. Типовые конструкции зубчатых венцов червячных колес
В червячных передачах, как правило, применяются подшипники качения.
Смазка червячных передач с нижним расположением червяка (рис. 25.3) осуществляется окунанием. Уровень масла таков, чтобы погружался в масло на глубину, близкую к высоте витка. Если червяк расположен сверху, то уровень масла роли не играет (при средних и небольших скоростях). В быстроходных передачах этого типа применяют циркуляционную – принудительную смазку.
72
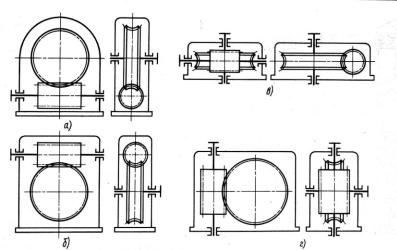
Рис.25.3. Схемы червячных редукторов: а) с нижним; б) с верхним; в, г) с боковым расположением червяка
26. ВАЛЫ И ОСИ
Учебные вопросы
1.Общие вопросы
2.Классификация валов и осей
3.Элементы вала
4.Материалы для изготовления валов и осей
5.Критерии работоспособности валов и осей
6.Расчетная схема и расчетные нагрузки
7.Расчет осей и валов на статическую прочность
8.Расчет осей и валов на выносливость
9.Расчет валов на жесткость
10.Расчет валов на колебания
73
26.1. Общие вопросы
Вращающиеся детали (шкивы, зубчатые колеса) машин устанавливаются на осях или валах, которые обеспечивают постоянное положение их оси вращения.
ОСИ – детали машин, которые служат лишь для поддержания вращающихся на них деталей. Они не передают полезного крутящего момента и работают только на изгиб.
Валы в отличие от осей не только поддерживают вращающиеся детали, но и передают по всей длине или на отдельных участках крутящий момент.
Как и оси, валы передают на опоры силы, возникающие в передачах (например, силы в зацеплении зубчатых колес и т.д.), т.е. они подвержены действию изгибающих моментов.
Некоторые валы не поддерживают вращающиеся детали (карданные валы автомобилей, валки прокатных станков и др.) поэтому работают только на кручение.
26.2. Классификация валов и осей
Оси бывают вращающиеся и неподвижные и представляют собой прямые стержни.
Валы подразделяются:
а) по назначению – валы передач, на которых устанавливаются зубчатые колеса, звездочки, муфты и др. детали передач и коренные валы, несущие кроме деталей передач рабочие органы машин – колеса или диски турбин, кривошипы, маховики и др.
б) по форме геометрической оси – прямые и коленчатые. в) по форме сечений – гладкие, шлицевые и профильные.
Прямые валы подразделяются на валы постоянного диаметра (трансмиссионные, судовые); валы ступенчатые (большинство валов); валы с фланцами для соединения по длине, а также валы с нарезанными шестернями или червяками.
Форма вала по длине определяется распределением нагрузок по длине, т.е. эпюрами изгибающих и крутящих моментов; условиями восприятия осевых нагрузок и условиями технологии изготовления и сборов.
74
Эпюры моментов по длине вала неравномерны. Крутящий момент обычно передается не на всей длине, изгибающие моменты на опорах вала равны нулю. Поэтому целесообразно конструировать валы переменного сечения, приближающимися к телам равного сопротивления. Ступенчатая форма валов удобна в изготовлении и сборке.
Кроме того, валы могут быть полыми.
Полый вал с отношением dотв: dнар. = 0,75 при равной прочности и жесткости получается легче сплошного на 50%. Полые валы применяются при жестких требованиях к весу, при необходимости пропуска сквозь других деталей.
26.3. Элементы вала
а) посадочные поверхности (под ступицы зубчатых колес, шкивов, звездочек и т.п.) характеризуются шероховатостью и величиной диаметра. Диаметры выбираются из стандартного ряда посадочных размеров. Диаметры под подшипники качения – из стандартного ряда внутренних диаметров подшипников. Переход диаметров ступеней определяется: стандартными диаметрами посадочных поверхностей под ступицы и подшипники, возможностью восприятия осевых сил и условиями сборки.
Шпонки на валах, по возможности следует располагать в одной плоскости
б) цапфы (шейки) вала.
Участок вала, которым он опирается на подшипник и воспринимает радиальную нагрузку, называется цапфой. Цапфы осей и валов, работающих в подшипниках скольжения, бывают: цилиндрическими (а), с буртами (б), коническими (в) и шаровыми (г).
Наиболее широкое распространены цилиндрические цапфы. Для предотвращения осевых смещений цапфы делают с буртами. Для регулирования зазора в подшипниках или осевого фиксирования вала рекомендуется коническая цапфа. При необходимости угловых смещений вала применяют шаровую цапфу.
75
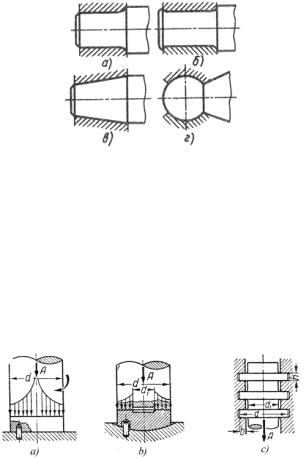
Рис. 26.1. Цапфы осей и валов, в подшипниках скольжения а) цилиндрические, б) с буртами, в) конические, ш) шаровые
Цапфы валов для подшипников качения выполняют цилиндрическими с малой длиной.
в) пяты – участки валов, которыми они опираются на подшипник и воспринимают осевую нагрузку.
Пята может быть сплошной (а); кольцевой (b); гребенчатой (c). Подшипник в этом случае называют подпятником.
г) устройства для передачи осевых нагрузок.
Рис. 26.2. Конструкции подпятников а) сплошная; b) кольцевая; c) гребенчатая
Тяжелые нагрузки передаются упором деталей в ступы на валу или посадкой этих деталей с натягом.
Средние осевые нагрузки передают гайками, штифтами и другими устройствами.
Легкие осевые нагрузки передаются стопорными винтами или пружинными кольцами.
76
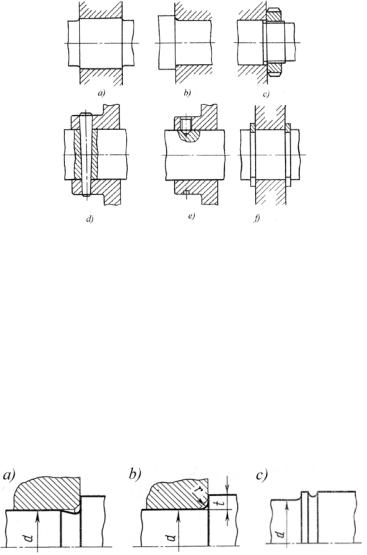
Рис. 26.3. Устройства для передачи осевых нагрузок a) посадка детали с натягом; b) упор детали в уступ;
c) передача нагрузки гайкой; d) передача нагрузки штифтом; e) передача нагрузки стопорным винтом; f) передача нагрузки пружинными кольцами; д) переходные участки валов
1. Канавки для выхода шлифовальных кругов обычно выполняются для валов Ø 10…50 мм, шириной в = 3 мм и глубиной
е = 0,25 мм, а для валов Ø 50…100 мм в = 5 мм; е = 0,5 мм.
Канавки должны иметь максимальные радиусы. Канавки существенно повышают стойкость шлифовальных кругов, но вызывают значительную концентрацию напряжений и понижают прочность валов при переменных напряжениях.
Рис. 26.4. Переходные участки валов канавка; b) галтель; c) разгрузочная канавка
Канавки также необходимы на концах участков с резьбой для выхода резьбонарезного инструмента.
г) галтель постоянного радиуса.
77
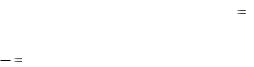
Радиус «r» галтели выбирают меньше радиуса закругления (r1) насаживемых деталей.
Для шеек под подшипники качения рекомендуется |
t |
3 ; |
|
r |
|||
|
|
r
d
( 0,02...0,04 )
где d – диаметр меньшей из сопрягаемых ступеней; t – высота уступа.
з) разгрузочная канавка выполняется путем удаления малонапряженного материала. При этом напряжения распределяются более равномерно и концентрация их снижается.
26.4. Материалы для изготовления валов и осей
Выбор материала и термообработки валов и осей определяется их критериями работоспособности, в том числе критериями работоспособности цапф с опорами. Основными материалами для изготовления валов и осей служат углеродистые и легированные стали, благодаря их прочности, большому модулю упругости, хорошей способности к упрочнению.
Для валов и осей, подчиненных критерию жесткости и неподвергающихся термообработке применяются стали: ст.5; ст 6. Для большинства валов применяют термически обрабатываемые стали 45, 40Х. Для высоконапряженных валов ответственных машин применяют легированные стали: 40ХН, 40 ХР2МА; 30ХГТ и др.
Быстроходные валы, вращающиеся в подшипниках скольжения, требуют весьма высокой твердости цапф. Их изготавливают из цементуемых сталей 12Х, 12ХН3А; 1ХХГТ.
Заготовками для стальных валов Ø до 150 мм служит круглый прокат, а для валов большего диаметра – поковки.
Шероховатость поверхности под подшипники качения назначается преимущественно по 7-8 кл. шероховатости (Ra 1,25-0,63), а подшипники скольжения в зависимости от условия работы от 7 до 9 кл. и выше (Ra 1,25-0,63-0,32).
78