
3360
.pdf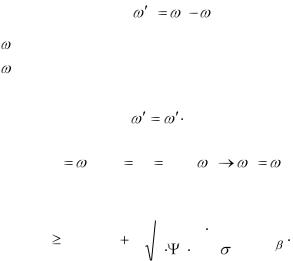
го, то при одинаковых материалах колес достаточно рассчитать только внешнее (наружное) зацепление.
Особенности расчета заключаются в следующем:
1. При определении допускаемых напряжений коэффициенты долговечности КHL и КFL находят при вращении колес только относительно друг друга:
|
1 |
1 |
Н , |
где |
1 - угловая скорость солнечной шестерни; |
||
|
Н - угловая скорость водила. |
|
|
|
Угловая скорость сателлитов: |
|
|
|
2 |
z1 / z2 ; |
V |
|
mz1 |
V |
mz2 |
|
|
|
|
1 |
z1 . |
||||||
|
|
|
|
|
|
|
|
|
|
|
|
|
|
|||
1 |
1 2 |
2 |
|
|
2 2 |
|
2 |
z2 |
||||||||
2. Межосевое расстояние: |
|
|
|
|
|
|
|
|
|
|||||||
|
|
|
|
|
|
|
|
|
|
|
|
|
|
|
|
|
aW |
49,5(U |
/ |
1)3 |
|
|
|
Kc T1 |
|
|
KH |
|
KHV , |
||||
|
|
c |
a |
U / [ ]2 |
|
|
||||||||||
|
|
|
|
|
|
|
|
|
H |
|
|
|
|
где U= z2/z1 – передаточное число рассчитываемой пары колес; Кс = 1,1…1,2 коэффициент неравномерности распределе-
ния нагрузки между сателлитами; Т1 – крутящий момент на солнечной шестерне, Н·мм;
Ψа – коэффициент ширины венца, Ψа = 0,5 при U ≤ 6,3,
Ψа= 0,4 при U/ > 6,3 (шире делают сателлиты). [ζ]H – допускаемое контактное напряжение, МПа;
КНβ – коэффициент, учитывающий неравномерное распределение нагрузки по длине зуба;
с – число сателлитов.
Полученное значение aW округляют до стандартного значения.
3. Ширина корончатого колеса:
в3 = Ψа · аW,
49
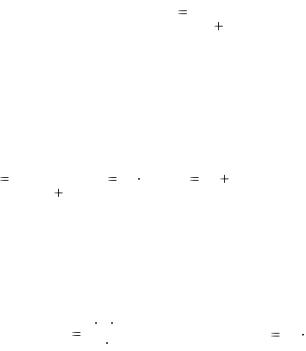
а ширину сателлитов и солнечной шестерни принимают на 2…4 мм больше в3.
4. Размеры солнечной шестерни:
d |
2aw |
. |
|
||
1 |
U / 1 |
|
|
Модуль зацепления:
m = d1 / z1.
Полученное значение округляют до ближайшего стандартного значения.
5. Уточняют числа зубьев колес:
z1 |
2aw |
; z2 |
z1 U |
/ |
; z3 |
z1 |
2z2 |
из условия соосности. |
m(U / 1) |
|
6.Проверка условий сборки (выступы зубьев попадают во впадины) и соседства (сателлиты не задевают друг за друга).
7.Проверяются действительные контактные напряже-
ния.
8.Усилия в зацеплении:
окружное: |
|
радиальное: |
|||
F |
2 T1 Kc |
; |
F |
F |
tga . |
|
|||||
t |
c d1 |
|
r |
t |
w |
|
|
|
|
|
22.9. Выбор зазоров в исполнительных механизмах
В передаточных механизмах роботов большое внимание уделяют точности позиционирования. В длинных кинематических цепях суммарное действие зазора может привести к значительным кинематическим ошибкам при перемещении исполнительного органа. Зазоры в зацеплении зубчатых колес и кинематических парах могут стать причиной появления неустойчивых режимов, вызвать повышенные вибрации, большие динамические нагрузки и усталостные поломки.
50
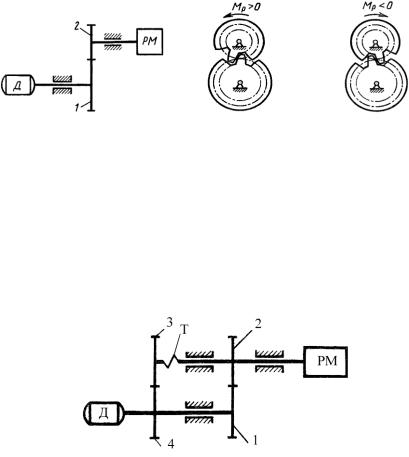
Для устранения таких негативных явлений необходима принудительная выборка зазоров в передаточных целях исполнительных механизмов.
Наибольшее практическое применение получил способ выбора (устранения) зазора с помощью замыкающих кинематических цепей, содержащих упругий элемент.
а |
б |
в |
Рис. 22.5. Образование зазора в зацеплении при нагружении передачи
а) схема передачи; б) Мр > 0; в) Мр < 0
При Мр > 0 контактируют профили зубьев слева, а при Мр < 0 – справа. Всякий раз. Когда реактивный момент меняет знак, кинематическая связь колес 1, 2 разрывается, пока не входит в зацепление профили зубьев с противоположной стороны. Боковой зазор должен компенсировать, в том числе и температурное расширение.
Рис. 22.6. Схема принудительной выборки зазора в зубчатой передаче
Для принудительной выборки зазора используют дополнительный замыкающий контур, цель, состоящую из торсиона Т и дополнительных колес 1/ и 2/.
51
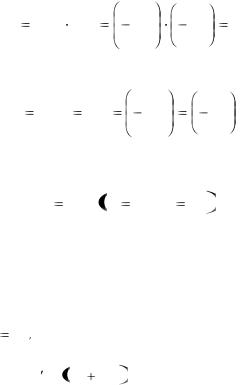
Момент загрузки торсиона обозначим через МТ. Он будет постоянным, если будет сохраняться относительный угол закручивания концов «а» и «в» торсиона. Концы торсиона будут двигаться одинаково, если круговое передаточное число Uз.к. замкнутого контура, состоящего из колес 2/, 1/, 1 и 2 будет равно единице:
U з.к. |
U 2/1/ |
U1 2 |
|
z1/ |
|
|
|
z2 |
|
1, |
||||
|
z |
2 |
/ |
|
|
|
z1 |
|||||||
|
|
|
|
|
|
|
|
|
||||||
|
|
|
|
|
|
|
|
|
|
|
|
|
|
|
отсюда |
|
|
|
|
|
|
|
|
|
|
|
|
|
|
U / / |
U з.к. |
U |
|
|
|
z1/ |
|
|
z1 |
, |
||||
|
|
21 |
|
|
|
|
|
|
|
|
|
|||
2 1 |
|
U1 2 |
|
|
|
z |
|
|
|
|
|
z2 |
|
|
|
|
|
|
|
|
2 |
/ |
|
|
|
|
|||
|
|
|
|
|
|
|
|
|
|
|
|
|
|
иначе говоря – передаточное число замыкающей цепи должно равняться передаточному числу основной цепи:
U з.ц. Uо.ц. z1/ |
z1 ; z2/ |
z2 . |
Это условие должно выполняться для любых замыкающих цепей, содержащих торсионы.
22.10.Схема механизма
сзамыкающей кинематической цепью
Если U12 U2 1, то концы торсиона будут двигаться одинаково. Приняв момент торсиона МТ достаточно большим можно всегда обеспечить М p
М р МТ > 0. При этом, зазор в зацепле-
нии всегда будет выбираться левым участком профилей зубьев. В качестве люфтовыбирающих устройств могут приме-
няться пружины, которые устанавливают между элементами разрезного зубчатого колеса. Пружина 3 одним концом упирается в колесо 1, а другим в колесо 2, обеспечивая постоянное прижатие колес 1 и 2 к обоим профилям шестерни.
Такие устройства устанавливают в каждой паре кинематических элементов.
52
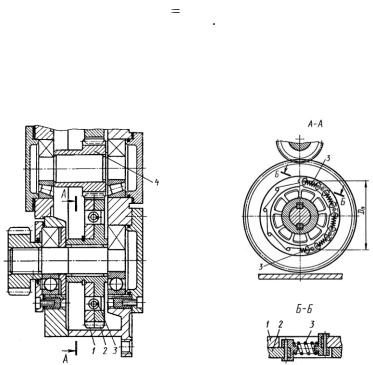
Общее усилие пружин должно превышать окружное усилие, действующее на диаметры установки пружин. Каждая из них должна обеспечивать усилие:
F |
2,5M кр |
, |
|
|
|
||
np |
DП |
ш |
|
|
|
где Мкр – максимальный крутящий момент, действующий на зубчатое колесо;
DП – диаметр, на котором установлены пружины; ш – число пружин.
б
а в
Рис. 22.7. Конструкция зубчатой передачи с выборкой зазора посредством пружин передача(а); сечение А-А (б); сечение Б-Б (в)
Выбирать люфт можно за счет установки жестких элементов, осуществляющих предварительное смещение кинематических элементов с последующей их фиксацией с помощью винтов и т.п.
В червячной передаче разрезанное на две половинки по ширине червячное колесо прижимается эксцентриками к обоим профилям витков червяка и фиксируется в этом положении винтом.
53
23. ВОЛНОВЫЕ ПЕРЕДАЧИ
Учебные вопросы
1.Волновые передачи. Общие сведения
2.Схема волновой передачи
3.Достоинства волновых передач
4.Недостатки волновой передачи
Волновые зубчатые передачи находят широкое применение в электромеханических приводах лучших зарубежных и российских промышленных роботах.
Они выгодно отличаются тем, что имеют малое значение мертвого хода, постоянное передаточное число, малые габариты и массу при высокой удельной нагрузочной способности.
Волновые передачи изобретены недавно (В. Мессер, 1959 г.). У волновых передач преобразование движения осуществляется за счет перемещения волны деформаций гибкого звена. Наибольшее практическое применение получили зубчатые волновые передачи (хотя они могут быть выполнены и фрикционными и резьбовыми). Кинематически они представляют собой планетарные передачи с одним из колес в виде гибкого (деформируемого) венца. Передача состоит из трех звеньев: H – генератора волн; 1 – гибкого колесa, выполненного в виде тонкостенного стакана с внешними зубьями (Z2); 2 – неподвижного зубчатого колеса с внутренними зубьями (Z3), (рис. 24.1).
Ведущим звеном является генератор волн H, который деформирует гибкое колесо 1, создавая две волны зацепления с неподвижным колесом 2. При отсутствии генератора волн зубья гибкого колеса не входят в зацепление с зубьями неподвижного колеса 2, и между зубьями имеется равномерный зазор.
При установленном генераторе волн H деформированный зубчатый венец 1 образует как бы два сателлита (две области зацепления), расположенные по большей оси эллипса. На меньшей оси эллипса зацепление колес 1 и 2 отсутствует.
54
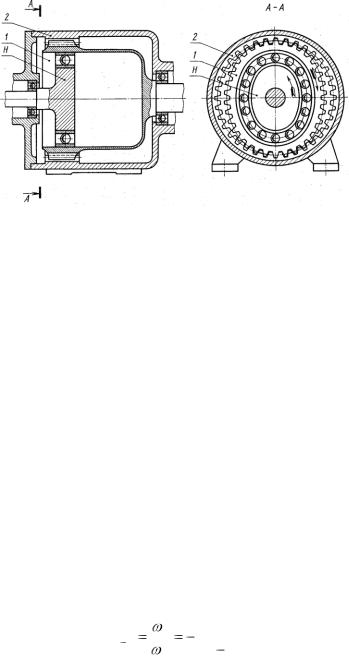
Рис. 23.1. Схема волновой передачи
При вращении генератора волн H гибкое зубчатое колесо 1 обкатывается по неподвижному колесу 2 (образуя две движущиеся волны (двухволновый генератор)) в направлении, противоположном вращению генератора волн H. Возможно применение трехволновых генераторов, но у них выше напряжения изгиба гибкого колеса.
Из-за большой многопарности зацепления (одновременно в зацеплении находятся 25…30% зубьев гибкого колеса 1) волновая передача позволяет существенно повысить плавность зацепления, несущую способность и кинематическую точность. Поэтому волновые передачи в последнее время стали применяться в приводах промышленных роботов.
Передачи, выполненные по рассмотренной схеме (вращается гибкое колесо 1),могут работать в качестве редуктора (КПД 80…90%) или мультипликатора (КПД …70%). Передаточные числа волновых редукторов находятся в диапазоне U ≈
80…300.
Передаточные числа волновой передачи определяется также, как и для планетарных передач по уравнению Виллиса. При неподвижном жестком колесе z3:
1 |
|
z1 |
. |
|
U1 2 |
|
|
|
|
|
|
z2 z1 |
||
2 |
|
|
55
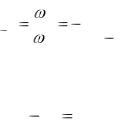
Знак «минус» указывает на разное направление вращения ведущего и ведомого звеньев.
При неподвижном гибком колесе 2:
1 |
|
z2 |
. |
|
U1 3 |
|
|
|
|
|
|
z2 z1 |
||
3 |
|
|
Разность зубьев колес должна быть равна (или кратна) числу волн:
z2 z1 kzU ,
где U – число волн (обычно U = 2);
kz – коэффициент кратности, обычно kz = 1:
при U < 70, kz = 2; при U < 45, kz = 3.
Волновые передачи (с неподвижным гибким колесом) передают вращение в герметизированное пространство через непроницаемую стенку без применения уплотнений или специальных диафрагм. Это позволяет применять передачу в приводах летательных аппаратов и изолированных химически агрессивных сред.
23.1.Достоинства волновых передач
1.Большая несущая способность на единицу массы (в 3…4 раза выше, чем у передач зубчатых).
2.Возможность получать большие передаточные числа в одной ступени.
3.Плавность и бесшумность работы.
4.Высокая кинематическая точность.
5.Надежность зацепления и малые габариты (при многопарном зацеплении поломка зуба не нарушает работоспособность и точность передачи).
6.Возможность передачи движения в герметизированное пространство.
56
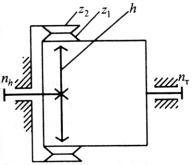
Рис. 23.2. Обозначение волновой передачи на кинематических схемах
23.2.Недостатки волновой передачи
1.Сложность конструкции генератора волн.
2.Повышенные требования к материалу для изготовления гибкого колеса (из-за непрерывного и значительного деформирования).
3.Сравнительно невысокая мощность передачи (до 3…30 КВт).
4. Невысокий КПД (в силовых передачах η ≈ 0,75…0,9). Несмотря на отмеченные недостатки, волновые передачи
все шире применяются в технике и в первую очередь в приводах летательных аппаратов, луноходах, атомных реакторах, прецизионных приборах, промышленных роботах.
24. ПОНЯТИЕ О СИСТЕМЕ ДОПУСКОВ И ПОСАДОК
Учебные вопросы
1.Понятие о взаимозаменяемости
2.Допуски размеров, посадок
3.Квалитеты
4.Система отверстия и система вала
5.Предельные отклонения формы и расположения
57
24.1. Понятие о взаимозаменяемости
При производстве, эксплуатации и ремонте изделий особое значение имеет принцип взаимозаменяемости. Взаимозаменяемость – это свойство конструкции, составной части изделия, обеспечивающее возможность ее применения вместо другой без дополнительной доработки… Патроны, болты, чайки – примеры полной взаимозаменяемости.
Имеет место также групповая взаимозаменяемость. При групповой взаимозаменяемости изготовленные детали сортируют по размерам на несколько групп (допуски деталей в каждой группе уменьшаются). Затем производят сборку изделия из деталей в пределах одной группы. Такая групповая взаимозаменяемость (селективная сборка) широко применяется в шарикоподшипниковой промышленности. При сборке изделий высокой точности этот метод является единственно экономически целесообразным методом обеспечения требуемой точности.
Метод регулирования предполагает сборку с регулирование положения или размеров определенной детали, называемой компенсатором.
Взаимозаменяемость базируется на стандартизации. Допуски и посадки нормируются стандартом ЕСДП – «Единая система допусков и посадок» (ГОСТ 25346-82). Допуски и посадки указывают на чертежах. На их основе разрабатывают технологические процессы изготовления и контроля.
24.2. Допуски размеров, посадок
На рабочем чертеже в первую очередь проставляют габаритные, присоединительные, посадочные, номинальные размеры, предельные отклонения размеров, условные обозначения полей допусков и квалитеты.
Номинальный размер определяет конструктор расчетным или конструктивным путем и назначает из нормального ряда линейных размеров (ГОСТ 6636-69), который ограничивает число применяемых размеров (качество режущего и мерительного инструмента), удешевляя производство.
58