
3360
.pdf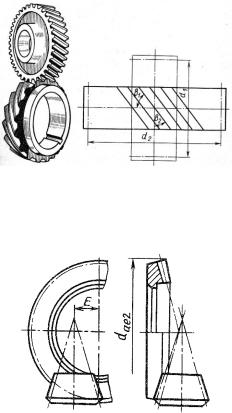
а |
б |
Рис. 19.3. Винтовая зубчатая передача: а) общий вид; б) схема
Рис. 19.4. Гипоидная передача
Таким образом, варьирование передаточного числа винтовой передачи возможно путем изменения диаметров и углов наклона зубьев. Наиболее высокий КПД получается при β1 = β2.
Материалы колес винтовой передачи должны обладать достаточно хорошими антифрикционными свойствами. Применяют следующие сочетания материалов: текстолит-чугун, текстолит-закаленная сталь, чугун-бронза. При необходимости передать сравнительно большие нагрузки оба колеса изготавливают из закаленной стали, с применением противозадирной смазки.
9
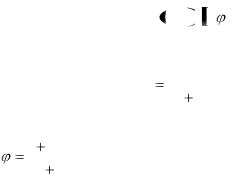
Расчет винтовых передач производится по имперической формуле, определяющей максимальное усилие в нормальном к зубьям направлении по условию предупреждения заедания:
Pn Cd1 2 R
,
где: Cd1 – приведенный диаметр шестерни,
C |
2d2 |
, |
d1 d2 |
[R] – условное допускаемое напряжение, МПа;
1 |
0,5VC |
- скоростной коэффициент; |
|
1 |
VC |
||
|
VC – скорость скольжения, м/с.
Для обеспечения большей плавности работы колес число зубьев шестерни рекомендуется принимать больше 20.
Гипоидные или конические винтовые передачи осуществляются коническими колесами с перекрещивающимися осями
(рис.19.4).
Гипоидные колеса, как правило, выполняют с круговыми зубьями, а передаточное число назначают в диапазоне от 1 до 10. Кроме высокой плавности в работе и возможности выводить валы за пределы передачи в обе стороны, гипоидные передачи обладают повышенной несущей способностью. Это связано с тем, что в отличие от винтовых передач здесь в зацеплении обеспечивается контакт, близкий к линейному, а скорости скольжения значительно меньше. Кроме того, зубья в гипоидной передаче хорошо притираются и не подвержены существенным искажениям вследствие достаточно равномерного скольжения по рабочей поверхности зубьев. В зацеплении одновременно находятся несколько пар зубьев, поэтому гипоидные передачи можно применять в механизмах высокой точности (делительные передачи прецизионных зуборезных станков).
Значительное распространение гипоидные передачи получили в автомобилях (благодаря расположению оси шестерни ниже оси колеса достигается понижение центра тяжести авто-
10
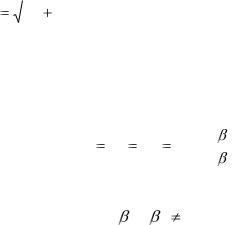
мобиля) и других транспортных машинах, в бумагоделательных, текстильных и других машинах.
Недостатком гипоидных передач является повышенная опасность заедания, связанная с наличием скольжения вдоль контактных линий. Средством повышения сопротивления заеданию являются специальные противозадирные смазки. Опасность заедания тем меньше, чем меньше гипоидное смещение (т.е. межосевое расстояние E, рис.19.4).
При проектировании гипоидных передач обычно выбирают гипоидное смещение в пределах E = (0,2 … 0,3)dez, а для транспортных машин
|
|
|
|
E ≤ (0,1 … 0,2)mteZC, |
|
|
|
|
|
где Z |
C |
Z 2 |
Z 2 . |
|
|
1 |
2 |
|
|
Углы |
наклона зубьев шестерни выбирают обычно |
β1= 50°, а колеса β2 = 30°-35°.
Число зубьев шестерни назначают в пределах: Z1 = 6… 16. Передаточное число гипоидных передач по аналогии с
винтовыми цилиндрическими передачами:
U |
n1 |
|
Z2 |
|
d2 cos |
2 |
, |
n2 |
|
Z1 |
|
d1 cos |
1 |
||
|
|
|
|
где: β1 и β2 – углы наклона зубьев шестерни и колеса, причем:
1 2 90 .
Геометрический расчет гипоидных передач аналогичен расчету конических колес с круговыми зубьями, но имеет свою специфику.
19.2. Волновые передачи
Кинематические волновые передачи представляют собой планетарные передачи с одним из колес, выполненным в виде гибкого вала. Как и планетарная, волновая передача состоит из трех основных звеньев (рис.19.5): неподвижного жесткого колеса 2 с внутренними зубьями, гибкого колеса 1, представ-
11
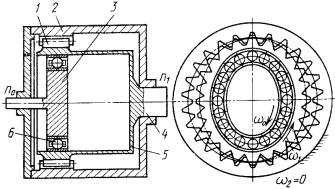
ляющего собой упругий тонкостенный стакан, основание которого соединено с ведомым валом 4, и генератора волн 3, деформирующего в радиальном направлении гибкое колесо I. На обоих колесах I и 2 нарезаны зубья одинакового модуля, однако число зубьев неодинаково – у гибкого колеса число зубьев Z 1 на два меньше, чем у жесткого Z2. Наибольшее распространение получили передачи с числом волн 2. В свободном состояний (без генератора 3) колеса находятся в центрическом положении с равномерным зазором между зубьями жесткого и гибкого колеса. Установленный внутри гибкого колеса генератор волн деформирует гибкое колесо в радиальном направлении, придавая ему эллипсообразную форму.
Рис. 19.5. Схема волновой передачи
При этом по большей оси эллипса зубья зацепляются на полную рабочую высоту, а по малой оси – между вершинами зубьев образуется зазор.
Передаточное число одноступенчатого волнового редуктора достигает Up= 60…300 и более. Это основной качественный показатель волновых передач, выгодно отличающий их от других зубчатых передач, в том числе и планетарных. К тому же нужно отметить, что в зацеплении у волновой передачи находится одновременно 25 – 30% зубьев. Это и обеспечивает высокие кинематическую точность и нагрузочную способность на единицу массы. Еще одним положительным качеством вол-
12
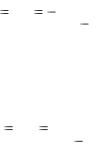
новой передачи является ее высокая демпфирующая способность (в 4 – 5 раз больше, чем у обычной зубчатой передачи).
К недостаткам волновых передач можно отнести ограниченные частоты вращения ведущего вала генератора волн при больших диаметрах колес, мелкие модули зубчатых колес (0,15
– 2,0 мм), сложность изготовления гибкого колеса и генератора волн в индивидуальном производстве. Однако при серийном изготовлении в специализированном производстве волновые передачи дешевле планетарных.
Волновые передачи могут работать в качестве редуктора (КПД 80 – 90%) и мультипликатора (КПД 60 – 70%). В первом случае ведущим звеном является генератор волн, во втором – вал гибкого или жесткого колеса.
При неподвижном жестком колесе передаточное число волновой передачи определяется выражением.
|
n0 |
|
Z1 |
|
U |
|
|
|
. |
n1 |
Z2 Z1 |
Знак минус указывает на разные направления вращения ведущего и ведомого звеньев.
При неподвижном гибком колесе:
U |
n0 |
|
Z2 |
, |
n2 |
|
Z2 Z1 |
где: n0, n1, n2 – частота вращения ведущего и ведомых звеньев; Z1, Z2 – числа зубьев гибкого и жесткого колес.
Разность зубьев жесткого и гибкого колес должна быть равна или кратна числу волн, т.е.:
Z1 – Z2 = RZ
где: U – число волн, обычно равное 2;
RZ – коэффициент кратности, обычно равный 1,0, но при
U < 70 RZ = 2, а при U < 45 RZ = 3.
Необходимое максимальное радиальное перемещение ω0 при отсутствии бокового зазора (если зубчатые венцы нареза-
13

ны без смещения производящего контура) должно равняться полуразности диаметров начальных (делительных) окружностей:
n 0 |
0,5 dW |
dW |
0,5 Z2 Z1 0,5 RZU . |
|
2 |
1 |
Иногда применяют в качестве кинематической волновую передачу с двумя зубчатыми венцами на гибкой оболочке, соответствующую планетарной с двумя внутренними зацеплениями. КПД такой передачи низкий – 5%, а передаточное чис-
ло велико U = 3600 – 9000.
Экспериментальные исследования показывают, что волновые передачи становятся неработоспособными по следующим причинам:
1.Разрушение подшипников генератора волн от нагрузки
взацеплении или из-за значительного повышения температуры. Повышение температуры может вызвать недопустимое уменьшение зазора между генератором волн и гибким зубчатым венцом, что в свою очередь может привести к недопустимому изменению первоначальной формы генератора волн, гибкого и жесткого зубчатого венцов.
2.Проскок генератора волн при больших крутящих моментах (по аналогии с предохранительной муфтой). Это явление наступает тогда, когда зубья на входе в зацепление упираются один в другой поверхностями вершин. При этом генератор волн сжимается, а жесткое колесо распирается в радиальном направлении. Для предотвращения проскока радиальное упругое перемещение предусматривают больше номинального, а зацепление собирают с натягом.
3.Поломка гибкого колеса от трещин усталости, появляющихся вдоль впадин зубчатого венца. С увеличением толщины гибкого колеса напряжения в нем от полезного передаваемого момента уменьшаются, а от деформирования генератора волн уменьшаются. Поэтому есть оптимальная толщина.
Долговечность гибкого элемента легко обеспечивается при U >120 и чрезвычайно трудно при U < 80.
14

Анализ причин вывода из стоя волновых передач показывает, что при U > 120 несущая способность обычно ограничивается стойкостью подшипника генератора волн, при U 100
– прочностью гибкого элемента. Максимальный допустимый крутящий момент связан с податливостью звеньев
20. ЧЕРВЯЧНЫЕ ПЕРЕДАЧИ
Учебные вопросы
1.Червячные передачи. Общие сведения
2.Классификация червячных передач
3.Материалы. Критерии работоспособности и расчета червячных передач
4.Расчет основных геометрических параметров червячных передач
Червячная передача применяется для передачи движения между перекрещивающимися осями валов. Она состоит из червяка (винт) и червячного колеса (зубчатое колесо с зубьями особой формы). Представляет собой разновидность винтовой зубчатой передачи и отличается от нее тем, что число зубьев (заходов) червяка мало и контакт не точный, а линейный. Для увеличения длины контактных линий наружную поверхность червячного колеса делают вогнутой, охватывающей червяк в пределах угла 2δ ≈ 100°.Червячные передачи изобрел Архимед.
Достоинства передач:
- возможность осуществления больших передаточных чи-
сел:
u = 6 … 80, а в отдельных случаях u ≈ 500
-плавность, бесшумность работы, компактность.
-возможность самоторможения.
Недостатки передач:
-низкий КПД (0,65 … 0,91)
-нагрев при непрерывной работе, что требует дополнительных устройств для охлаждения,
15
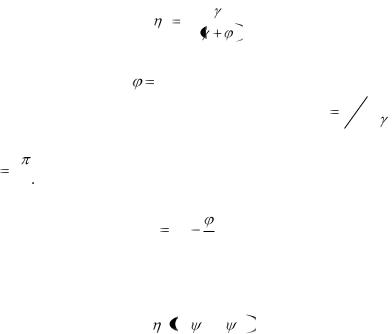
-необходимость применения для колес дорогих антифрикционных (обладающих низким коэффициентом трения, хорошей прирабатываемостью, теплопроводностью и стабильностью свойств) материалов,
-ограниченная передаваемая мощность (от долей КВТ до 200 КВТ, как правило, до 50 КВТ).
Однако благодаря своей компактности, бесшумности в работе и больших передаточных чисел, червячные передачи широко применяются в подьемно-транспортных машинах, станках, автомобилях и др. машинах, а также в качестве делительных механизмов.
КПД в червячном зацеплении определяются по зависимостям, полученным для винтов:
|
|
tg |
, |
|
|
|
|
3 |
|
|
|
|
|
|
tg |
|
|
|
||
|
|
|
|
|
||
|
|
|
|
|
|
|
где: γ – угол подъема витков червяка, |
|
|
|
|||
θ – угол трения |
arctgf (f – коэффициент трения). |
|||||
В зависимости то скорости скольжения Vcm |
V1 |
cos |
, по |
|||
|
||||||
|
|
|
|
|
|
табл. 20. находят “f” и “θ” для червячной передачи. Причем,
V1 |
d1n1 |
|
м/c, (V1 |
– окружная скорость червяка). Для мало- |
|
60 100 |
|||||
|
|
|
заходных передач Vck ≈ V1. Значение η3 растет с ростом угла подъема γ до величины 45 2 ; при этом значении η3 = max.
При дальнейшем росте угла подъема КПД начинает падать. Обычно червячные передачи имеют углы подъема γ ≤ 27°. Общий КПД червячной передачи:
3 1
П
Р ,
где: ψП – потери в подшипниках; ψР – потери на разбрызгивание и перемешивание масла.
Обычно ψp ≤ 0,01 и этой величиной можно пренебречь.
16

КПД червячных передач ниже, чем других механических передач. Среднее значение η с учетом потерь в опорах:
|
|
|
Таблица 20.1 |
|
|
|
|
Z1 |
1 |
2 |
4 |
η |
0,65–0,8 |
0,83–0,87 |
0,89–0,91 |
Классификация червячных передач
Червячные передачи различают по следующим призна-
кам:
-по форме основного червяка – цилиндрические и глобо-
идные;
-по форме профиля витков червяка – архимедовы, эвольвентные, конволютные, с вогнутым профилем;
-по расположению червяка относительно колеса с нижним, верхним и боковым расположением червяка,
-по конструктивному оформлению корпуса: открытые и закрытые,
-по точности изготовления: 12 степеней точности;
-по назначению: силовые с нерегулируемым и кинематические с регулируемым взаимным расположением червяка и колеса.
20.1. Эвольвентный червяк
Образуется при нарезании его витков резцом, вершина которого может быть установлена выше или ниже оси. При
S
этом d0 , (α = 20°). В поперечном сечении такого чер-
4 tg
вяка получим эвольвенту, а в сечении плоскостями, касательными к боковой поверхности некоторого цилиндра диаметром d0 прямолинейные образующие боковых сторон профиля витка. Боковая поверхность его витков представляет собой эвольвентную винтовую поверхность.
Архимедов червяк – образуется при нарезании его витков резцом, вершина которого установлена по оси заготовки. В по-
17
перечном сечении такого червяка получим Архимедову спираль. В сечении осевой плоскостью – прямые образующие боковых сторон профиля витка (трапецеидальный профиль в осевом сечении).
Боковая поверхность витков такого червяка представляет собой Архимедову винтовую поверхность. Архимедовы червяки широко распространены, т.к. наиболее просты в изготовлении и обеспечивают достаточно высокую точность червячной передачи.
Коволютный червяк образуется при нарезании его витков резцом, главная режущая кромка которого устанавливается перпендикулярно направлению впадины или витков червяка. В поперечном сечении червяка получим конволюту (удлиненная, или укороченная эвольвента), а в сечении плоскостью, номинальной к направлению впадины или витков – прямые линии, которые являются образующими боковых сторон профиля витков в этом сечении. Боковая поверхность витков такого червяка – представляет собой конволютную винтовую поверхность.
Стандартный (ГОСТ) угол профиля (α) принят α = 20: у архимедовых червяков – в осевом сечении, у конголютных – в нормальном сечении к направлению впадины или витков, а у эвольвентных – в нормальном сечении косозубой рейки, сцепляющейся с червяком.
20.2.Материалы. Критерии работоспособности
ирасчета червячных передач
Основными причинами выхода из строя червячных передач являются поверхностные разрушения; схватывание и износ зубьев. Схватывание особенно опасно, если колесо изготовлено из твердых бронз и чугуна. Частицы материала колеса привариваются к червяку и затем усиливают износ зубьев колеса. При мягких материалах колеса схватывание имеет менее опасную форму: материал колеса (бронза) "намазывается" на червяк.
Усталостное выкрашивание наблюдается, главным образом, у колеса, выполненного из стойких против заедания бронз.
18