
3360
.pdf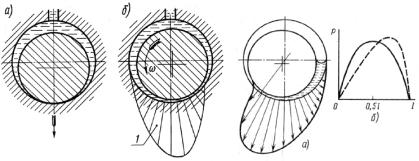
печивается износостойкость, сопротивление заеданию вала и высокий КПД. Для создания жидкостного трения необходимо, чтобы в масляном слое было избыточное давление, которое может быть гидродинамическим, создаваемым вращением вала или гидростатическим, осуществляемым от насоса.
Для получения условий жидкостного трения применяют обычно подшипники с гидродинамической смазкой. Сущность такой смазки следующая. Вал при своем вращении под действием внешних сил занимает в подшипнике эксцентричное положение и увлекает масло в зазор, образуется масляный клин, в котором создается гидродинамическое давление, обеспечивающее в подшипнике жидкостное трение. Эпюра распределения гидродинамического давления в подшипнике по окружности показана на рис.28.2 б. При перекосах вала эпюра по длине становится несимметричной.
Рис. 28.2. Эпюра гидродинамиче- |
Рис. 28.3. Эпюра |
ского давления в подшипнике |
давлений |
а) вращение вала отсутствует, |
а) по окружности, |
б) распределения давления по ок- |
б) по длине |
ружности подшипника |
|
28.2.Классификация
Взависимости от направления воспринимаемой нагрузки подшипники скольжения различают:
– радиальные (воспринимают радиальные нагрузки);
– упорные (подшипники) – воспринимают осевые нагрузки;
109

– радиально-упорные – одновременно воспринимают радиальные и осевые нагрузки.
28.3. Конструкции подшипников скольжения
Подшипники скольжения составляют из корпуса; вкладышей, поддерживающих вал; смазывающих и защитных устройств.
Корпус подшипника может быть отдельной, литой или сварной деталью, выполненной цельной или разъемной.
Вкладыши применяют для того, чтобы не выполнять весь корпус подшипника из дорогого антифрикционного материала и для облегчения ремонта.
Рис. 28.4. Конструкция вкладыша подшипника скольжения а) вкладыш-втулка; б) вкладыш из двух половин с заливкой
Износ вкладышей составляет десятые доли мм, но такой толщины вкладыши делать нельзя по условиям прочности и технологическим соображениям. Поэтому вкладыши делают биметаллическими: тонкий антифрикционный слой наплавляют на стальную, чугунную или бронзовую основу.
Толщина литого вкладыша
δВ = (0,035…0,05)d + 2,5 мм,
где d – диаметр вала
Толщина заливки δ1 = 0,01 d.
Вкладыши устанавливают в корпус с натягом и предохраняются от проворачивания установочными штифтами.
В случае большой деформации вала или невозможности точного монтажа применяют самоустанавливающиеся подшипники скольжения.
110
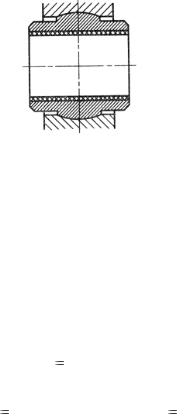
Вкладыши таких подшипников обычно выполняют сферическими.
Рис. 28.5. Конструкция самоустанавливающегося подшипника скольжения
Существенное значение в подшипниках скольжения имеет отношение длины (ℓ) подшипника к диаметру (d). С увеличением (ℓ) уменьшается среднее давление в подшипнике, резко возрастают кромочные давления и повышается температура.
Уменьшение длины подшипника ниже некоторого предела приводит к усиленному вытеканию масла и к снижению несущей способности.
Оптимальное отношение
|
|
|
|
|
0,6...1,0 , |
|
|
|
|
|
|
d |
|
|
|||
|
|
|
|
|
|
|||
У коротких |
|
0,3...0,4 |
; у длинных |
|
1,0...1,5 . |
|||
d |
d |
|||||||
|
|
|
|
|
|
В прецизионных подшипниках скольжения производят регулировку зазора. Оптимальный зазор устанавливают на за- воде-изготовителе, а компенсация выработки – при ремонтах.
Разъемные подшипники регулируют, сближая вкладыши, путем уменьшения толщины прокладок между ними или снятием слоя металла с поверхности контакта крышки и корпуса.
28.4. Подшипниковые материалы
Подшипниковые материалы выбирают исходя из условия работы со стальными цапфами валов. Стоимость валов
111
значительно выше стоимости подшипников и поэтому они должны изнашиваться меньше, чем вкладыши.
Подшипники работают тем надежнее, чем выше твердость валов. Для быстроходных валов шейки имеют твердость HRC 55…60 и изготавливаются из цементуемых сталей.
Комплексные требования к подшипниковым материалам:
–антифрикционность (низкий коэффициент трения скольжения);
–износостойкость и усталостная прочность.
Эти требования обеспечиваются следующими основными свойствами подшипниковых материалов:
а) теплопроводность – создает интенсивный теплоотвод от поверхностей трения и малый коэффициент линейного расширения во избежание больших изменений зазоров.
б) прирабатываемость – обеспечивает уменьшение кромочных давлений, связанных с упругими деформациями и погрешностями изготовления.
в) хорошая смачиваемость маслом и способность образовывать на поверхности стойкие и быстровосстанавливаемые масляные пленки.
По химическому составу антифрикционные материалы делятся на три большие группы:
–металлические – бабиты, бронзы, сплавы на цинковой основе, на алюминиевой основе, антифрикционные чугуны;
–металлокерамические (железографитовые, получаемые методом порошковой металлургии);
–неметаллические – пластмассы, древесные пластики,
резина.
28.5. Критерии работоспособности и расчета подшипников скольжения
Основными критериями работоспособности подшипников являются:
а) износостойкость – сопротивление абразивному изнашиванию и схватыванию;
б) сопротивление усталости при пульсирующей нагрузке.
112

Абразивное изнашивание возникает при недостаточной несущей способности масляного слоя и особенно при попадании со смазкой абразивных частиц, соизмеримых с толщиной масляного слоя.
Схватывание возникает при потере масляной пленки своей защитной способности из-за повышенных местных давлений и температур. Этому способствует повышение кромочных давлений как следствие перекоса вала в подшипнике. Конечной стадией отказа подшипника является полное захватывание цапфы в подшипнике в результате разогрева цапфы и выборке зазора в подшипнике до нуля.
Усталостные разрушения фрикционного слоя наблюдаются при значительной пульсации нагрузки: в поршневых машинах, в машинах ударного и вибрационного действия. При некачественной заливке вкладышей наблюдается отслаивание заливки.
Основным расчетом подшипников скольжения является расчет на жидкостное трение, который основывается на том, что масляный слой должен воспринимать всю нагрузку, а его толщина должна быть больше сумм неровностей обработки цапфы и вкладыша. Составной частью расчета является тепловой расчет, т.к. недопустимое повышение температуры приводит к изменению свойств смазки и выплавлению заливки вкладышей.
Кроме того, применяются условные расчеты.
28.6. Условные расчеты подшипников
Для подшипников жидкостного трения условные расчет применяются как предварительные, а для подшипников полужидкостного – как основные (т.к. других нет).
Расчет по допускаемым давлениям в подшипниках проводится по нагрузке, отнесенной к проекции цапфы.
P |
R |
[ P ] . |
||
|
|
|||
de |
||||
|
|
|||
|
113 |
|
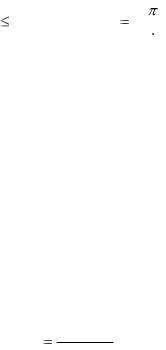
В подшипниках большинства стационарных машин [P] =
1…4 Н/мм2, для двигателя внутреннего сгорания [P] = 4…20
Н/мм2.
Расчет обычно используется, как проверочный, т.к. диаметр цапфы определяется при расчете вала.
Расчет по произведению давления в подшипнике на скорость скольжения
PV [ PV ] ; |
V |
dn |
м/с. |
|
|
|
|||
60 1000 |
Произведение PV в некоторой степени характеризует теплообразование и износ.
В подшипниках большинства стационарных машин принимают [PV] = (2…10) МПа·с/м, в поршневых авиационных двигателях [PV] = (30…50) МПа·с/м.
Значения [P] и [PV] в зависимости от материала вкладышей приводится в справочной литературе.
28.7. Тепловой расчет подшипников
Для современных быстроходных машин тепловой расчет подшипников имеет решающее значение. Расчет ведут на основе теплового баланса, т.е. приравнивание теплообразования в подшипнике к теплопередаче.
Теплообразование в подшипнике
W Mw3600 , ккал/ч.
427
Т.е. количество тепла, выделяющегося в подшипнике в единицу времени.
W = (W1 + W2).
Теплоотдача происходит: а) через корпус и вал;
б) через смазку, вытекающую из подшипника. в) через корпус и вал.
114
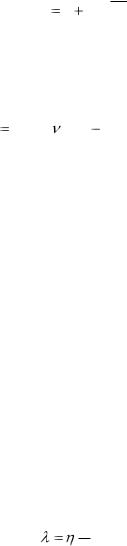
W1 = KTF(tM – t0), ккал/ч,
где F – свободная площадь подшипника,
KT – коэффициент теплоотдачи.
KT 6 10V
,
где Vβ – скорость омывания корпуса воздухом. Наименьшее
значение Vβ = 1 м/с.
(tM – t0) избыточная tº подшипника.
б) теплоотвод через смазку, вытекающую из подшипника
W2 60CQ ( tвых0 tвх0 ) , ккал/ч,
где Q – объем масла, прокачиваемого через подшипник,
л/мин;
ν – плотность масла, равная 0,87-0,89;
C – теплоемкость масла С = (0,4…0,5) ккал/кг
t0 |
; t0 |
– температура масла на входе и выходе в под- |
вых |
вх |
|
шипник.
Уравнение баланса
W = (W1 + W2).
Температура подшипника должна быть не выше 60…75 ºС
28.8. Проектировочный расчет подшипников жидкостной смазки
Заданными являются: нагрузка на опору R, а частота вращения вала n об/с, диаметр вала d. Отношением ℓ/ d обычно задаются (в пределах 0,8-1,0, нормальная длина).
Задача сводится к нахождению относительного зазора ψ, обеспечивающего наиболее надежную работу подшипника. С этой целью определяют характеристику режима:
Pn мм2
где η – динамическая вязкость масла, Па·с;
115
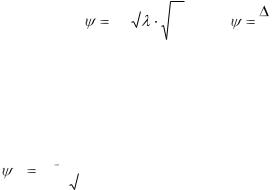
n – частота вращения вала, об/с;
Р – удельная нагрузка на материал вкладыша, Па (Р = R/ℓ· d). Величину оптимального зазора ψ находят по специальным
графикам, или по формуле
3,5 |
|
|
|
мм |
|
, |
|
|
|||||
|
|
d |
|
|||
|
|
|
|
d |
где – диаметральный зазор.
Валы устанавливают в подшипниках по посадкам:
|
|
|
|
|
|
H 7 |
; |
H 7 |
; |
|
H 7 |
; |
|
H 7 |
; |
H 7 |
. |
|
|
|
|
|
|
|
|
|
|
|
|
|
|||||
|
|
|
|
|
|
f 7 |
e7 |
|
|
e8 |
|
|
d8 |
|
c8 |
||
|
10 |
3 |
m |
– средний относительный зазор. |
|||||||||||||
ср |
|
|
|
|
|||||||||||||
|
|
d |
|||||||||||||||
|
|
|
|
|
|
|
|
|
|
|
|
|
|
|
|||
|
|
|
|
|
|
|
|
|
|
|
|
|
|
|
|
||
m – постоянная, зависящая от посадки |
|||||||||||||||||
Посадка |
|
|
|
|
с8 |
|
d8 |
|
|
e8 |
|
f7 |
|||||
m |
|
|
|
|
|
23 |
|
17 |
|
|
12 |
|
7,5 |
Величина коэффициента трения при жидкостной смазке находится в пределах 0,001…0,005. При неблагоприятных условиях (высокая вязкость масла, большие окружные скорости, малые зазоры) коэффициент трения возрастает до 0,01…0,03. У подшипников, работающих в условиях граничной смазки коэффициент трения достигает значений 0,1…0,2.
29. КОНСТРУИРОВАНИЕ ПОДШИПНИКОВЫХ УЗЛОВ
Учебные вопросы
1.Схемы установки подшипников
2.Конструирование опор валов конических шестерен
3.Конструирование опор валов-червяков
116
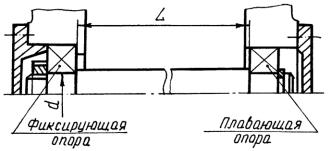
29.1. Схемы установки подшипников
Валы должны занимать вполне определенное положение
вопорах, которые могут быть фиксирующие и плавающие.
Вфиксирующих опорах ограничивается осевое перемещение вала в обоих направлениях, а в плавающих осевое перемещение вала в обоих направлениях не ограничивается.
Фиксирующая опора воспринимает радиальную и в любом направлении осевую нагрузку.
Плавающая опора воспринимает только радиальную нагрузку.
Всхемах на рис. 29.1 и 29.2 вал фиксируется в одной левой опоре одним или двумя радиальными или радиальноупорными подшипниками.
Рис. 29.1. Установка вала в фиксирующей и плавающей опорах
Схемы рис. 29.1 и 29.2 применяют при любом расстоянии между опорами, причем схема (рис. 29.2) характеризуется большей жесткостью фиксирующей опоры.
Осевая фиксация (рис. 29.1) широко применяется в коробках передач, редукторах и т.д. для валов цилиндрических зубчатых передач и приводов валов ленточных и цепных транспортеров.
Осевую фиксацию по схеме (рис.29.2) применяют в цилиндрических, конических и червячных передачах.
117
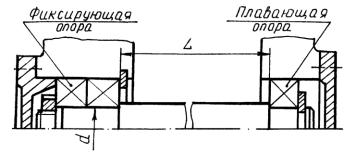
Рис. 29.2. Установка вала в технологичной фиксирующей опоре
При назначении фиксирующей и плавающей опор учитывают следующие рекомендации:
–подшипники обеих опор должны быть нагружены по возможности равномерно. Поэтому, если опоры нагружены кроме радиальной еще и осевой нагрузкой, то в качестве плавающей выбирают опору, нагруженную большей радиальной силой;
–при температурных колебаниях плавающий подшипник (вместе с валом) перемещается в осевом направлении, что под нагрузкой, изнашивает посадочную поверхность в корпусе. Поэтому, если на опоры действуют только радиальные нагрузки, то
вкачестве плавающей выбирают менее нагруженную опору;
–если выходной конец вала соединяется с другим валом муфтой, в качестве фиксирующей принимают опору в близи этого конца вала.
Применяют также схемы, в которых осевое фиксирование вала происходит в двух опорах, причем в каждой из них осевое перемещение вала ограничивается только в одном направлении.
Обе схемы (рис. 29.3, 29.4) применяют с определенными ограничениями и связано это с изменением зазоров в подшипниках вследствие нагрева при работе.
Из-за увеличения длины вала осевые зазоры в подшипниках (схема «враспор») еще больше уменьшаются.
118