
2835.Проблемы разработки месторождений углеводородных и рудных полезных и
..pdf
Секция 6. Горные и нефтепромысловые машины и оборудование
ВЛИЯНИЕ ЗАБОЙНОЙ МОЩНОСТИ НА ТЕМПЕРАТУРНЫЙ РЕЖИМ ИМПРЕГНИРОВАННОЙ АЛМАЗНОЙ КОРОНКИ «02И4»
И.Т. Кондрашков
Научный руководитель – канд. техн. наук, профессор Ю.А. Лагунова Уральский государственный горный университет
Проводится оценка эффективности применения алмазных коронок по мерзлым породам, рационализация процесса бурения по структурным критериям. Рассматривается контактная температура как основа оптимизации процесса.
Ключевые слова: алмазные коронки, контактная температура, конвективный теплообмен, мерзлые породы, технология бурения.
Важным критерием оценки рационального выбора технологической схемы отработки скважины являются затраты энергии на ее конструкцию. В свою очередь, эта задача является многофакторной и включает в себя ряд основных параметров. Из этого следует, что реализация математических моделей не всегда совпадает с практикой.
В большей степени на температурный градиент оказывают влияние геометрические параметры алмазной коронки: суммарная площадь контактов алмазов с забоем, площадь поперечного сечения матрицы, площадь поперечного сечения корпуса коронки. Также на показатель интенсивности темплообмена коронки с очистным агентом оказывают влияние аэродинамические свойства бурильных труб. При варьировании геометрии можно добиться оптимальной структуры, добавляя выточки в теле бурового инструмента.
Следует также отметить, что физико-механические свойства применяемых материалов должны соответствовать определенным горно-геологическим условиям.
Опираясь на научные труды Б.И. Воздвиженского, Г.А. Воробьева, Л.К. Горшкова, Н.Н. Рыкалина, А.Н. Резникова, Ю.Е. Будюкова, проанализируем импрегнированную алмазную коронку «02И4» (табл. 1).
Предполагается, что эксплуатируют алмазную коронку в породах 10–12-й категорий по буримости. Также принимаем, что грунт трещиноват и абразивен из-за воздействия окружающей среды.
Для упрощения расчета контактной температуры бурового инструмента принимаем установившийся режим бурения, так как оценить влияние конвективного теплообмена очистного агента с алмазной коронкой в данном случае будет наиболее рациональным решением (табл. 2).
|
|
Таблица 1 |
|
|
Импрегнированная алмазная коронка «02И4» (исходные данные) |
||
|
|
|
|
№ |
Параметр |
Значение |
|
п/п |
|||
|
|
||
1 |
Наружный диаметр коронки, мм |
76,0 |
|
2 |
Внутренний диаметр коронки, мм |
59,0 |
|
3 |
Кол-во промывочных каналов, шт |
6,0 |
471
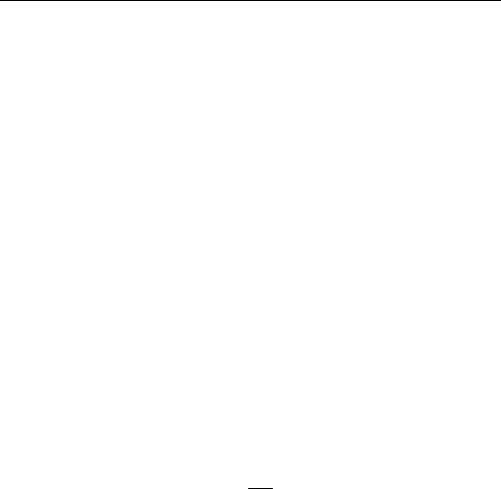
Проблемы разработки месторождений углеводородных и рудных полезных ископаемых
|
|
|
Окончание табл. 1 |
||||
|
|
|
|
|
|
|
|
№ |
Параметр |
|
|
|
|
Значение |
|
п/п |
|
|
|
|
|||
|
|
|
|
|
|
|
|
4 |
Длина промывочного канала, мм |
|
|
|
|
25,0 |
|
5 |
Ширина промывочного канала, мм |
|
|
|
|
15,0 |
|
6 |
Ширина матрицы, мм |
|
|
|
|
12,0 |
|
7 |
Высота матрицы, мм |
|
|
|
|
25,0 |
|
8 |
Кол-во объемных алмазов, шт/карат |
|
|
|
|
200 |
|
9 |
Кол-во подрезных алмазов, шт/карат |
|
|
|
|
40,0 |
|
10 |
Выступ алмазов из матрицы, мм |
|
|
|
|
0,5 |
|
11 |
Средний условный диаметр алмаза, мм |
|
|
|
|
0,9 |
|
|
|
|
|
|
Таблица 2 |
||
|
Параметры процесса бурения |
|
|
|
|
||
|
|
|
|
|
|
|
|
Параметры процесса бурения в зависимости |
425 |
450 |
475 |
|
500 |
||
|
от частоты вращения, об/мин |
|
|||||
|
|
|
|
|
|
|
|
Механическая скорость, м/ч |
0,046 |
0,049 |
0,052 |
|
0,055 |
||
Величина углубки за один оборот, мм/об. |
0,0182 |
0,0182 |
0,0182 |
|
0,0182 |
||
Забойная мощность, кВт |
11,906 |
12,606 |
13,307 |
|
14,007 |
||
Осевое усилие, Н |
8360 |
8360 |
8360 |
|
8360 |
||
Расход очистного агента, кг/мин |
2,1 |
2,1 |
2,1 |
|
2,1 |
||
Температура очистного агента на подходе |
0 |
0 |
0 |
|
0 |
||
к забою, °C |
|
||||||
|
|
|
|
|
|
||
Контактная температура, °C |
487 |
520 |
554 |
|
580 |
Контактную температуру алмазов можно представить в виде линейной зависимости от затрачиваемой на забое мощности N, Вт:
ta = k0−1k p N + k p N +σH +t0 , Gcp
где kр – безразмерный коэффициент распределения теплового потока между коронкой и породой; G – расход очистного агента кг/с; ср – удельная теплоемкость очистного агента, Дж/(кг·°C); t0 – температура очистного агента в нисходящем потоке на подходе к буровой коронке,°C; H – глубина скважины, м; k0 – показатель интенсивности теплообмена алмазной коронки с очистным агентом, который определяется геометрией коронки, насыщенностью алмазами и является функцией коэффициентов конвективной теплоотдачи, °C/Вт [1].
k0 |
= |
|
|
|
|
|
|
λa fa m |
|
|
|
|
|
|
+1 − |
|
fa |
× |
||
|
λк fк |
|
|
|
|
|
|
|
|
|
|
|
|
|
||||||
|
|
|
|
|
|
nh |
n(h−ha ) |
|
|
−n(h−ha ) |
|
|
fм |
|||||||
|
|
2 p |
|
|
φ+ 2ne |
|
− n e |
|
+ e |
|
|
|
|
|
|
|
||||
|
|
λм fм |
|
|
|
|
|
|
|
|
||||||||||
|
|
|
|
|
|
|
|
|
|
|
|
|
|
|
|
|
|
|
||
|
× λa fa m |
|
|
|
|
|
|
λa fa m |
|
|
|
|
|
|
|
, |
||||
|
|
|
λк fк |
|
|
|
nh |
|
|
n(h−ha ) |
|
−n(h−ha ) |
||||||||
|
|
|
|
2 p |
|
φ+ |
2ne |
|
− n e |
|
|
− e |
|
|
||||||
|
|
|
λм fм |
|
|
|
|
|||||||||||||
|
|
|
|
|
|
|
|
|
|
|
|
|
|
|
|
|
|
|
|
472
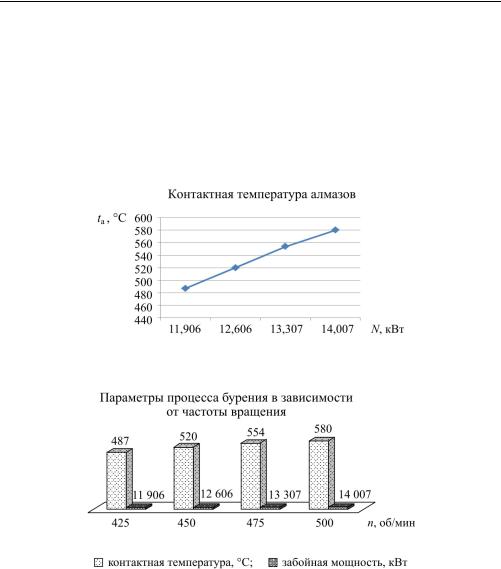
Секция 6. Горные и нефтепромысловые машины и оборудование
где λа, λм, λк, – теплопроводность соответственно алмазов, материала матрицы
икорпуса коронки, Вт (м·°C); fа, fм и fк – площади поперечных сечений соответственно контактов алмазов с забоем, матрицы и корпуса, м2; h – высота
матрицы, м; hа – выпуск объемных алмазов из матрицы, м; φ – отношение значений температуры нагрева верхней части матрицы (на границе с корпусом)
иторца (при бурении с продувкой сжатым воздухом – 0,8); m, n, p – коэффициенты зависящие от геометрических параметров коронки, вида и расхода очистного агента, м–1 [2].
Рис. 1. Зависимость ta = f (N):
Рис. 2. Зависимости N = f (n) и ta = f (n):
Список литературы
1.Расчет показателя интенсивности теплообмена алмазной буровой коронки
спромывочной средой при бурении скважины / А.А. Кожевников, А.Ю. Дреус, С.В. Гошовский, И.И. Мартыненко // Изв. вузов. Горный журнал / Урал. гос. горн.
ун-т. – 2007. – № 6. – С. 85–89.
2. Кудряшов Б.Б., Яковлев А.М. Бурение скважин в мерзлых породах. – М.:
Недра, 1983. – С. 22–25.
473
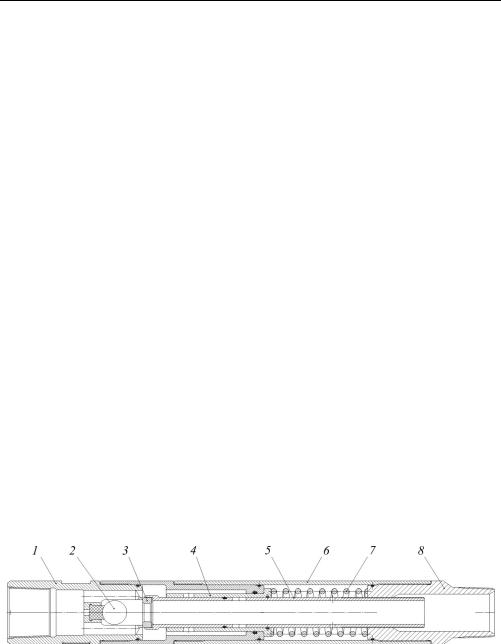
Проблемы разработки месторождений углеводородных и рудных полезных ископаемых
УСТРОЙСТВО ДЛЯ АВТОМАТИЧЕСКОГО УДАЛЕНИЯ ГАЗА ИЗ ПОГРУЖНОГО НАСОСА ПРИ СРЫВЕ ЕГО ПОДАЧИ
Д.Н. Лебедев
Научный руководитель – д-р физ.-мат. наук С.Н. Пещеренко Пермский национальный исследовательский политехнический университет
Проблема свободного газа при интенсификации добычи нефти является актуальной и имеет множество путей решения, таких как установка предвключенных устройств в работу УЭЦН, однако эти устройства бессильны при срыве подачи и образовании газовой пробки в УЭЦН. Данное устройство решает проблему запуска УЭЦН после срыва подачи по газу.
Ключевые слова: клапан, срыв подачи, борьба с газом, УЭЦН.
В настоящее время одним из способов интенсификации нефтедобычи является увеличение депрессии на пласт за счет снижения давления на приеме насоса, что приводит к появлению в добываемой жидкости нерастворенного газа, который негативно влияет на работу УЭЦН.
Для борьбы с нерастворенным газом существует множество устройств, таких как газосепараторы, диспергаторы, мультифазные насосы. Все эти устройства имеют критическую величину газосодержания (βкр), выше которой происходит срыв подачи насоса [1]. Для запуска насоса после срыва подачи необходимо провести промывку насоса с поверхности с привлечением бригады КРС, что приведет к существенному увеличению эксплуатационных затрат.
Для устранения последствий срыва подачи насоса по газу разработано и запатентовано устройство для удаления газа из погружного насоса [2]. Основной задачей данного устройства является осуществление автоматической промывки сразу после остановки насоса и выполнение функций обратного клапана при опрессовке колонны НКТ.
Внешний вид устройства представлен на рисунке.
Рис. Устройство для удаления газа из погружного насоса: 8, 1 – верхняя и нижняя присоединительные части с резьбами для крепления к колонне НКТ; 2 – шар; 3 – седло; 4 – подвижный полый поршень с отверстиями в верхней части; 5 – направляющий шток с отверстиями в средней части и резьбой в нижней
части; 6 – цилиндрический корпус; 7 – пружина
Устройство для удаления газа монтируется на выходе из УЭЦН. Работает устройство для удаления газа следующим образом: когда происходит срыв подачи
474

Секция 6. Горные и нефтепромысловые машины и оборудование
УЭЦН по газу, погружной электродвигатель отключается, а газ, попавший в насос, образует газовую пробку. В этот момент на клапан сверху действует давление жидкости, находящейся в лифте НКТ, в частности оно действует на подвижный полый поршень 4, который начинает перемещаться вниз, сжимая пружину 7 вплоть до того момента, пока не совместятся отверстия в полом поршне 4 и в штоке 5, образуется канал, по которому жидкость будет поступать из лифта НКТ в насос, в результате чего происходит промывка УЭЦН. В ходе промывки сливается около 20 % жидкости, находящейся в лифте НКТ, после чего давление на полый поршень 4 уменьшается, пружина возвращает его в верхнее положение, канал, образованный между отверстиями в полом поршне 4 и штоке 5, перекрывается. Далее возможно производить запуск УЭЦН.
Второй функцией устройства для удаления газа является удержание жидкости в лифте НКТ при проведении опрессовки труб НКТ. В этом случае давление, создаваемое на устье скважины при помощи наземного оборудования, превышает давление столба жидкости, находящейся в лифте НКТ. В этом случае в клапане в начальный момент времени возникает утечка через канал, образованный отверстиями в полом поршне 4 и штоке 5, однако при увеличении давления происходит перекрытие отверстий путем смещения подвижного полого поршня 4 вниз по штоку 5 и производится опрессовка лифта НКТ.
Для проверки работоспособности устройства для удаления газа был составлен план испытаний. Его цель – установить величину давления, при котором происходит открытие, и сравнить ее с расчетной, закладываемой при проектировании устройства. Для этого на выход устройства для удаления газа подавалось давление с УЭЦН, имитирующее давление жидкости в лифте НКТ. По обе стороны от устройства были установлены манометры для контроля давления и определения момента открытия канала между полым поршнем 4 и штоком 5.
В ходе эксперимента установлено, что открытие канала между отверстиями вполомпоршне4 иштоке5 осуществляетсяприрасчетномдавлении200 атм, чтосоответствует положению «промывка», а при давлении 300 атм происходит перекрытие отверстийвполомпоршне4 иштоке5, чтосоответствуетположению«опрессовка».
Данное устройство для удаления газа из погружного насоса прошло приемочные испытания и готово к отправке на опытно-промышленные испытания (ОПИ), в ходе которых будет получено заключение о работоспособности устройства в скважинных условиях.
Список литературы
1.Пещеренко М.П., Перельман О.М., Рабинович А.И., Каплан А.Л. Повышение эффективности эксплуатации УЭЦН путем применения мультифазных насо-
сов // Бурение и нефть. – 2014. – № 4. – С. 56–60.
2.Пат. № 2508489 РФ. Устройство для удаления газа из погружного насоса / Антипин М.Н., Лебедев Д.Н., Меретяков И.П., Пещеренко С.Н., Талдытов Р.Р.;
заявл. 25.10.2012; опубл. 27.02.2014.
475

Проблемы разработки месторождений углеводородных и рудных полезных ископаемых
СОВЕРШЕНСТВОВАНИЕ ИСПОЛНИТЕЛЬНЫХ ОРГАНОВ ПРОХОДЧЕСКО-ОЧИСТНЫХ КОМБАЙНОВ «УРАЛ»
Л.А. Лоскутов
Научный руководитель – канд. техн. наук, доцент Д.И. Шишлянников Пермский национальный исследовательский политехнический университет
Обоснованы технические решения по модернизации рабочих органов проход- ческо-очистных комбайнов «Урал», обеспечивающие уменьшение энергозатрат при разрушении калийного массива, перемещении и погрузке отбитой руды исполнительными органами. Показана эффективность схемы пересекающихся резов.
Ключевые слова: проходческо-очистной комбайн, исполнительный орган, удельные энергозатраты, кинематическая схема привода, калийная руда.
Эффективность работы предприятий, осуществляющих добычу калийной руды подземным способом, определяется техническим уровнем средств механизации основных технологических процессов. Существенное снижение себестоимости калийной руды может быть обеспечено посредством разработки и внедрения высокопроизводительных комбайнов, осуществляющих разрушение калийного массива и погрузку горной массы с небольшими удельными энергозатратами
ималым выходом мелких классов.
Внастоящее время на калийных рудниках России и стран ТС наибольшее распространение получили проходческо-очистные комбайны «Урал» производства ОАО «КМЗ» (г. Копейск, Челябинская обл.), оснащенные комбинированными исполнительными органами бурового типа и гусеничным ходовым оборудованием.
Одним из недостатков планетарных исполнительных органов комбайна «Урал» является разрушение массива последовательными расходящимися радиаль- но-тангенциальными резами переменной глубины (рис. 1). Известно, что на энергетические показатели процесса разрушения массива и выход мелких классов наибольшее влияние оказывает глубина резов h, оптимальное значение которой по данным экспериментальных исследований составляет для калийной руды 13–18 мм. Каждой глубине реза соответствует оптимальный шаг резания, определяемый отношением t/h = 3,0…4,5. Особенность планетарных органов комбайна «Урал» состоит в том, что в первой половине резов глубина и шаг увеличиваются, а во второй – глубина уменьшается, а шаг увеличивается до максимального значения (см. рис. 1, а). Следовательно, значительная часть забоя разрушается блокированными резами при отношении t/h > 7. Этот недостаток устраняется при установке дисков на валах редукторов с наклоном в сторону переносного движения [1].
По сравнению с исполнительными органами комбайнов «Урал» планетарные органы с наклоном осей резцовых дисков в сторону переносного движения имеют следующие преимущества. Глубина резов изменяется от нуля до максимального значения по синусоидальному закону. По такому же закону изменяется шаг резания, поэтому по всей траектории движения резцов отношение t/h остается постоянным (см. рис. 1, б). Следовательно, может быть получено оптимальное или близкое к оптимальному значение t/h, при котором обеспечиваются наименьшие
476
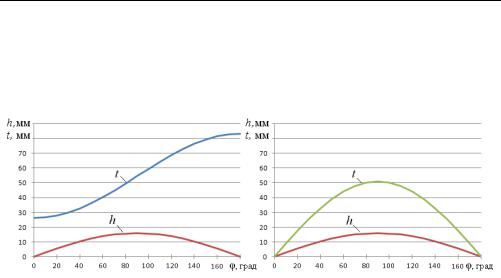
Секция 6. Горные и нефтепромысловые машины и оборудование
энергозатраты на разрушение. За счет уменьшения угла контакта породоразрушающего инструмента с забоем улучшаются условия для поворота резцов, что положительно сказывается на сроке их службы. Создание на забое сетки пересекающихся резов обеспечивает снижение удельных энергозатрат процесса разрушения калийного массива и уменьшение выхода мелких классов руды [1, 2].
а |
б |
Рис. 1. Графики изменения толщины стружки и шага резания в зависимости от угла поворота резцового диска: а – планетарного исполнительного органа комбайна «Урал-20Р»; б – планетарного исполнительного органа с наклоном дисков в сторону переносного движения
Сотрудниками кафедры ГЭМ разработаны способы и устройства для реализации схемы перекрестного резания, проведены экспериментальные исследования, подтверждающие ее эффективность [3]. Предложенные конструкции планетарнодисковых исполнительных органов предусматривают необходимость внесения изменений в кинематические схемы приводов и компоновку редукторов при установке на комбайны «Урал». Наименьшие отличия от серийно выпускаемых исполнительных органов имеет пространственный планетарный орган с наклоном режущих дисков относительно плоскости симметрии (рис. 2). Конструкция предлагаемого исполнительного органа состоит из дисков 1 и 3, вращающихся в противоположные стороны и установленных под углом к плоскости симметрии 2, образованной продольной осью органа разрушения и прямой, проведенной через центры резцовых дисков. Резцы 7 поворотного диска 3 разрушают массив последовательными тангенциально-радиальными резами, идущими от периферии к центру забоя. Резцы диска 1 реализуют радиально-тангенциальные резы от центра к периферии забоя. Вращающий момент на диски 1, 3 передается раздаточным редуктором 4 и поворотными редукторами 5. Центральная часть забоя отрабатывается забурником 6.
Техническим результатом способа разрушения является создание на поверхности калийного массива сетки пересекающихся резов за счет разнонаправленного вращения и переносного движения наклонно установленных дисков и снижение напорного усилия комбайна и необходимой тяговой способности гусеничного органа перемещения [3].
477
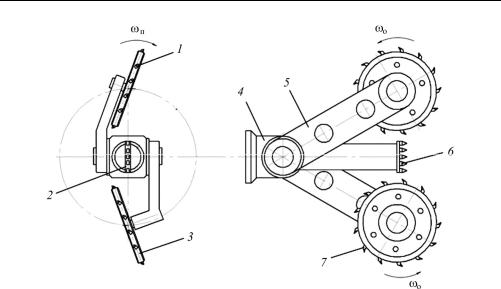
Проблемы разработки месторождений углеводородных и рудных полезных ископаемых
Рис. 2. Планетарно-дисковой исполнительный орган с наклоном резцовых дисков относительно плоскости симметрии
Резцы отбойного устройства и бермового органа комбайна разрушают массив резами небольшой глубины с повышенными энергозатратами и выходом мелких фракций. Удельный расход энергии в 2,0–2,5 раза больше, чем при использовании резцовых дисков.
Повышение эффективности процесса разрушения массива вспомогательными органами возможно обеспечить посредством перехода с последовательной схемы разрушения массива полублокированными резами на шахматные резы. Для реализации шахматной схемы резания необходимо использовать двухзаходные шнеки. Результаты экспериментальных исследований показывают, что при разрушении массива шахматными резами глубиной 5 мм, по сравнению с последовательными резами той же глубины, удельные энергозатраты снижаются с 6 до 3,2 кВт·ч/м3, выход мелких классов сокращается с 6,5 до 5 % [2].
При движении комбайна вверх по пласту и работе с номинальной производительностью наблюдается проскальзывание гусениц, сопровождающееся ухудшением качества руды, снижением производительности комплекса, увеличением удельных энергозатрат на разрушение массива. Область работы комбайна без проскальзывания гусениц расширяется при изменении направления вращения отбойного устройства на противоположное (от почвы выработки к кровле). При этом силы реакции забоя на резцы будут иметь направления, при которых уменьшается напорное усилие комбайна, а сила прижатия гусениц к почве увеличивается. Кроме того, при попутном направлении вращения отбойного устройства снижается вероятность выхода крупных негабаритных кусков руды с кровли выработки.
Мощность одного привода бермового органа составляет 75 кВт. На основании расчетов установлено, что на отбойку руды шнеком и фрезой затрачивается
478

Секция 6. Горные и нефтепромысловые машины и оборудование
мощность, не превышающая 35 кВт. Следовательно, основная часть энергии привода затрачивается на перемещение и погрузку горной массы. Значительные энергозатраты на перемещение свидетельствуют о том, что груз перемещается с очень большим сопротивлением, при котором происходит интенсивное измельчение горной массы. Наиболее неблагоприятные условия погрузки руды создаются при работе комбайна в выработках с отрицательными углами наклона (движение вниз) вследствие снижения производительности конвейера.
Замена однозаходных шнеков комбайна «Урал-20Р» на двухзаходные обеспечит более равномерное поступление горной массы на конвейер комбайна, снижение ее циркуляции и затрат энергии на переизмельчение руды. Повышение эффективности погрузки руды может быть обеспечено посредством установки за шнеком вспомогательных зачистных устройств – лемехов.
Таким образом, использование перспективных конструкций планетарнодисковых исполнительных органов, реализующих перекрестную схему разрушения, и переход с последовательной на шахматную схему резания вспомогательными исполнительными органами позволит существенно снизить удельные энергозатраты процесса разрушения калийного массива и уменьшить количество необогатимых классов в отбитой руде.
Список литературы
1.Долгов В.Л. Совершенствование плоско-планетарных исполнительных органов проходческих комбайнов // Горная электромеханика и механизация горных работ. – М.: Недра, 1969. – С. 188–193.
2.Харламова Н.А. Исследование механизма разрушения соляных горных пород резцовым инструментом: дис. … канд. техн. наук / Перм. гос. техн. ун-т. –
Пермь, 1998. – 173 с.
3.Чекмасов Н.В., Шишлянников Д.И. Способы и устройства для реализации процессов разрушения калийных пластов перекрестными резами // Горное оборудование и электромеханика. – 2013. – № 11. – С. 2–5.
479

Проблемы разработки месторождений углеводородных и рудных полезных ископаемых
ПОВЫШЕНИЕ ДЕБИТОВ И ДОЛГОВЕЧНОСТИ КРЕПИ СКВАЖИН РАЗРАБОТКОЙ И ВНЕДРЕНИЕМ ЩАДЯЩИХ РЕЖИМОВ ВТОРИЧНОГО ВСКРЫТИЯ ПРОДУКТИВНЫХ ПЛАСТОВ
М.С. Марданов
Научный руководитель – д-р. техн. наук, профессор Н.И. Крысин Пермский национальный исследовательский политехнический университет
Предложен щадящий метод вторичного вскрытия продуктивных пластов щелевой гидропескоструйной перфорацией (ЩГПП). Разработана конструкция гидропескоструйного перфоратора с управляемым с поверхности клапанным механизмом.
Ключевые слова: щелевая гидропескоструйная перфорация (ЩГПП), гидроперфоратор, насосно-компрессорные трубы (НКТ), опрессовка, продуктивная зона пласта (ПЗП), вторичное вскрытие продуктивных пластов.
Применяемая в настоящее время технология первичного и вторичного вскрытия продуктивных пластов не способствует получению потенциальных дебитов скважин из-за отрицательного воздействия на призабойную зону продуктивного пласта буровых и тампонажных растворов, жидкостей перфорации и глушения.
Промышленно используемые методы вторичного вскрытия с применением кумулятивных и других типов перфораторов не позволяют снять напряженное состояние в призабойной зоне продуктивных пластов. Высокие ударные нагрузки на обсадную колонну (70–100 МПа) при использовании данных перфораторов практически повсеместно приводят к нарушению цементного камня за эксплуатационной колонной в интервале 50 м ниже и 50 м выше перфорируемого пласта, что на 30–40 % является причиной обводнения скважин.
Одним из перспективных методов вторичного вскрытия продуктивных пластов является щелевая гидропескоструйная перфорация (ЩГПП).
Метод заключается в создании в ПЗП каналов фильтрации с использованием кинетической энергии и абразивного воздействия струи жидкости, имеющей в своем составе кварцевый песок.
Высокоскоростная затопленная струя жидкости с песком, исходящая из сопел аппарата (в дальнейшем – гидроперфоратор) в направлении стенки скважины под высоким давлением 15–30 МПа, интенсивно разрушает (просверливает) в заданном интервале ПЗП металл обсадной колонны, проникает в цементное кольцо и породу, создавая канал, по которому происходит сообщение скважины с пластом [2].
С помощью гидроперфоратора проводят щелевые вскрытия, создающие в ПЗП каналы значительно большей площади, в виде щелей определенной ориентации и глубины.
Врезультате этих процессов при каждом резе и использовании перфоратора
счетырьмя насадками образуются четыре щели, расположенные под углом 90°, длиной 200–300 мм, глубиной 400–450 мм, шириной 30–40 мм.
480