
2835.Проблемы разработки месторождений углеводородных и рудных полезных и
..pdf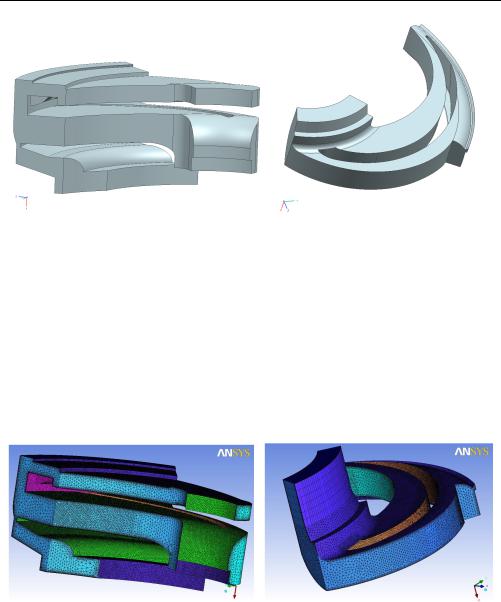
Секция 6. Горные и нефтепромысловые машины и оборудование
а |
б |
Рис. 1. Проточная область ступени насоса: |
|
а – рабочее колесо; б – направляющий аппарат |
|
Для построения объемной сетки проточной области использовалась программа ANSYS ICEM CFD (рис. 2). Ячейки расчетной сетки представляют собой тетраэдры, крупные в ядре потока и имеющие сгущение в пристеночной области. Для описания пограничного слоя вблизи твердых стенок рабочего колеса и направляющего аппарата был создан призматический слой. Общее количество элементов расчетной сетки насоса для точного расчета составило ~2,3 млн элементов (рабочее колесо ~1,4 млн, направляющий аппарат ~0,85 млн); для быстрого ~850 000 элементов (рабочее колесо ~630 000, направляющий аппарат ~220 000).
а |
б |
Рис. 2. Расчетная сетка проточной области (быстрый расчет): а – рабочее колесо; б – направляющий аппарат
Для проведения расчетов использовался газогидродинамический пакет ANSYS CFX. На входе в расчетную область (рис. 3) задавался массовый расход Q, на выходе – полное давление. Режим течения турбулентный. Для замыканий уравнений Рейнольдса использовалась стандартная k–ε-модель турбулентности. В качестве рабочей жидкости выбиралась вода. Задавалась частота вращения рабочего колеса. Указывалось условие периодичности, условие прилипания жидкости к стенкам.
461
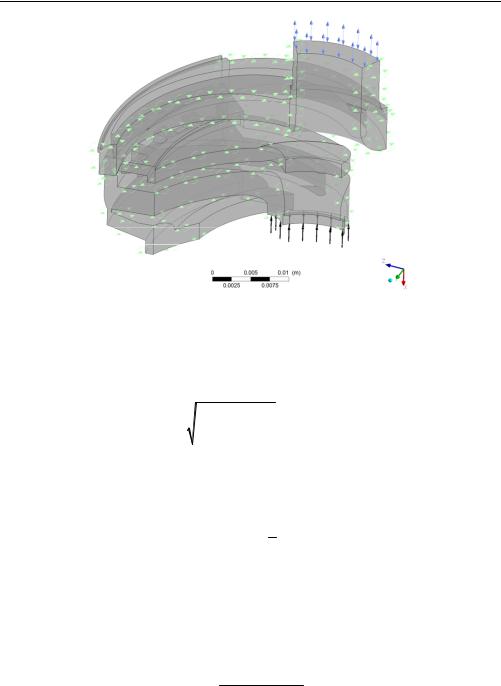
Проблемы разработки месторождений углеводородных и рудных полезных ископаемых
Рис. 3. Расчетная модель проточной части
Задавались следующие параметры решателя:
– критерий сходимости: сходимость расчета контролировалась по невязкам компонентов скорости в объеме расчетной области:
∑ |
(u − u |
i −1 |
)2 |
i |
≤ 10−4 , |
||
n |
n |
|
|
где ui – компоненты скорости на i-й итерации по времени; n – количество элементов в объеме;
– шаг по времени
∆ t≤ 0,3 h , u
где h – минимальный размер ячейки в расчетной сетке; u – средняя скорость потока. Характерное время ∆ t= 3 10−4 с – для точного расчета, ∆ t= 1 10−3 с – для быстрого расчета.
Характеристики ступени (напор иКПД) вычислялись по следующим формулам:
– напор
H = Ptot _ вх − Ptot _ вых ,
ρg
где Ptot_вх – осредненное по расходу полное давление на входе в рабочее колесо; Ptot_вых – осредненное по расходу полное давление на выходе из направляющего аппарата; ρ – плотность жидкости;
462

Секция 6. Горные и нефтепромысловые машины и оборудование
– гидравлический КПД
= ρgQH
ηГ ω ,
M
где ρ – плотность жидкости; Q – подача; H – напор; ω – циклическая частота,
ω= 2πf ; M – крутящий момент относительно оси вращения рабочего колеса.
Втаблице приведено сравнение двух методик – быстрой и точной. В качестве примера рассматривалась ступень ВНН 2А-30Э. Сравнивались относительная погрешность по напору и время, затрачиваемое на расчет.
Сравнение быстрого и точного расчетов (ступень ВНН 2А-30Э)
Подача, |
|
КПД, % / Напор, м |
Погрешность, % |
Расчетноевремя, мин |
||||
Эксп. |
|
Точный |
Быстрый |
Точный |
Быстрый |
Точный |
Быстрый |
|
м3/сут |
|
|||||||
|
|
|
расчет |
расчет |
расчет |
расчет |
расчет |
расчет |
15 |
31/3,17 |
|
49,46/2,96 |
52,54/3,04 |
7,1 |
4,3 |
148 |
10 |
20 |
39/3,03 |
|
55,92/2,88 |
59,36/3,01 |
5,2 |
0,7 |
106 |
7 |
25 |
45/2,83 |
|
61,88/2,76 |
62,7/2,88 |
2,5 |
1,7 |
60 |
6 |
30 |
49/2,58 |
|
64,92/2,51 |
63,45/2,69 |
2,8 |
4,1 |
135 |
10 |
35 |
50/2,26 |
|
63,42/2,33 |
62,87/2,46 |
3,0 |
8,1 |
67 |
4 |
40 |
46/1,84 |
|
60,43/1,93 |
58,95/2,12 |
4,7 |
13,2 |
67 |
4 |
45 |
38/1,31 |
|
49,28/1,43 |
51,17/1,68 |
8,4 |
22,0 |
60 |
4 |
Из таблицы видно, что для точного расчета имеет место хорошее согласование по напору численных расчетов и испытаний на стенде (относительная погрешность на номинальной подаче не более 3 %). Расчеты по быстрой методике занимают примерно 5–10 мин. В дальнейшем это время планируется сократить до 1 мин.
Список литературы
1.Агеев Ш.Р., Григорян Е.Е., Макиенко Г.П. Российские установки лопастных насосов для добычи нефти и их применение: энциклопед. Справочник / ООО
«Пресс-Мастер». – Пермь, 2007. – 645 с.
2.Пат. 2232297 РФ. МПК F04D13/08, F04D1/06. Ступень центробежно-
вихревого насоса / Перельман О.М., Рабинович А.И. [и др.]; заявл. 24.06.2002;
опубл. 10.17.2004.
3.Пат. 2253756 РФ. МПК F04D13/10. Ступень погружного многоступенчатого насоса / Гусин Н.В., Рабинович С.А., Перельман О.М. [и др.]. – № 26234; опубл.
20.02.2005.
4. Пат. 2468259 РФ. МПК F04D29/44. Радиальный направляющий аппарат /
Рабинович А.И., Гилев В.Г. [и др.]; заявл. 05.07.2011; опубл. 27.11.2012.
463

Проблемы разработки месторождений углеводородных и рудных полезных ископаемых
МАТЕМАТИЧЕСКАЯ МОДЕЛЬ ВЗАИМОДЕЙСТВИЯ ПОДЪЕМНОГО СОСУДА С ПРОВОДНИКАМИ
В.Ю. Зверев
Научный руководитель – д-р техн. наук, доцент Г.Д. Трифанов Пермский национальный исследовательский политехнический университет
Описана основная проблема эксплуатации жесткой армировки при повышении производительности шахтного подъема. Предложена модель, позволяющая оценить динамические нагрузки в системе подъемный сосуд – жесткая армировка при прохождении подъемным сосудом дефектного стыка между проводниками.
Ключевые слова: шахтный подъем, подъемный сосуд, скип, жесткая армировка, дефект, проводник, динамические нагрузки.
Одним из путей повышения производительности рудника является увеличение интенсивности шахтного подъема, применение сосудов с большей грузоподъемностью и сокращение времени доставки руды на поверхность. При этом возникает проблема резкого снижения срока службы сосудов и элементов армировки из-за накопления усталостных напряжений в их конструкциях вследствие появления сверхнормативных переменных нагрузок. Это приводит к исчерпыванию ресурса усталостной прочности оборудования, увеличению затрат на эксплуатацию и снижению безопасности подъема.
Даже на небольших скоростях подъема жесткая армировка шахтного ствола испытывает нагрузки со стороны подъемного сосуда по ряду следующих причин:
–вращение скипа под действием раскручивающего момента подъемного каната [1];
–удары от колебаний скипа при загрузке и изменение скорости движения [2] от аэродинамической силы в месте встречи сосудов [1];
–удары при движении скипа через участи подъема, имеющие дефекты в конструкции армировки.
Как показывают результаты математического моделирования процессов воздействия скипа на армировку, даже самые большие возникающие при этом нагрузки не превышают 3 % от веса сосуда [2], а при проектировании считаются второстепенными, в расчетах их рекомендуют учитывать коэффициентом запаса
в10 % [3].
При увеличении скорости подъема скип активнее вступает в процесс стационарных колебаний, обусловленный динамическими свойствами упругой системы. На нагрузки большое влияние начинает оказывать поперечная жесткость проводников и состояние армировки. Удары и нагрузки, возникающие при прохождении скипом непрямолинейностей поверхности проводников, возрастают до 17 % от веса сосуда и оказывают существенное воздействие на состояние элементов подъема [4].
По результатам исследований работы подъемных установок известно, что наибольшие динамические нагрузки возникают при ударе направляющих скипа
464
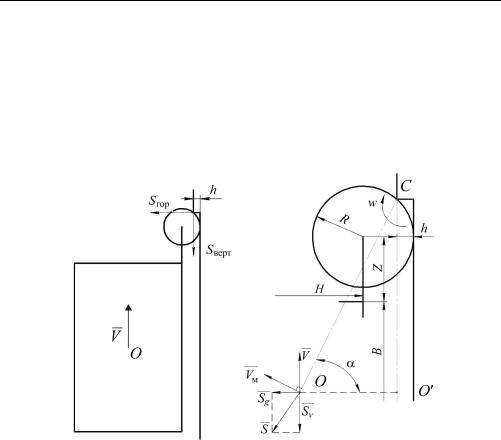
Секция 6. Горные и нефтепромысловые машины и оборудование
о стык между проводниками одной нитки, когда другое направляющее устройство, расположенное на том же поясе, с проводником не взаимодействует [5].
Чтобы оценить нагрузки, возникающие при наличии дефектов армировки, рассмотрим модель движения подъемного сосуда и определим удар в лобовом направлении, возникающий в результате взаимодействия направляющего ролика скипа с несоосным стыком между проводниками соседних ярусов (рис. 1). Скип представим в виде прямоугольного тела, имеющего одно роликовое направляющее устройство, перекатывающегося через уступ.
Рис. 1. Взаимодействие роликового направляющего скипа со стыком между проводниками
В модели учтем основные геометрические параметры подъемного сосуда: высота скипа B – расстояние между рамами верхних и нижних роликовых направляющих; ширина скипа H – расстояние между осями роликов одного пояса; R – радиус роликов направляющего устройства; z – высота рамы направляющего устройства, а также масса груженого скипа m (сведена к его центру тяжести в т. O, определенному с учетом массы груза) и скорость подъема V.
Для решения этой задачи используем метод, предложенный А.Ю. Прокоповым [1]: движение сосуда разбивается на прямолинейное равномерное движение до удара (I) и вращательное движение в момент удара (II), когда сосуд с роликом перекатываются через уступ.
Кинетический момент импульса относительно точки соприкосновения ролика с уступом до удара
LI = m·V·OO'.
Кинетический момент инерции относительно оси С в момент удара
465
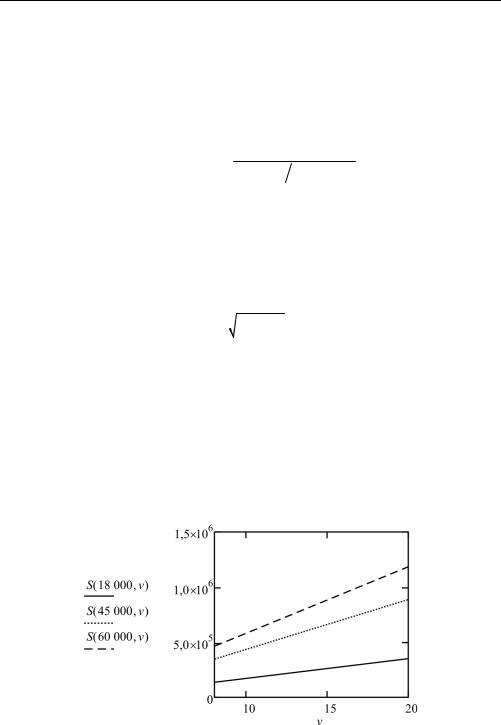
Проблемы разработки месторождений углеводородных и рудных полезных ископаемых
L = ω· I |
с |
= |
VII |
· ( m · |
B2 + H 2 |
+ m · (OC)2 ), |
|
|
|||||
II |
|
OC |
12 |
|
где Iс – моментинерциисосудаотносительнооси C дляпрямоугольноготела, кг·м2.
Приравнивая кинетические моменты инерции до и в момент удара, выразим линейную скорость вращения центра масс сосуда относительно точки С:
L = L VII = |
V · OO' · OC |
. |
(1) |
|
B2 +H 2 12 + (OC)2 |
||||
I II |
|
|
По закону сохранения количества движения вертикальная и горизонтальная составляющие удара, а также полный ударный импульс, который испытывает подъемный сосуд при прохождении стыка между проводниками, находятся по формулам
Sv = m· (0 – sinа·VII ); |
(2) |
Sg = m· (V – cosа·VII ); |
S = Sv2 +Sg 2 .
График зависимости ударного импульса от скорости подъема при отклонении между проводниками на 15 мм представлен на рис. 2.
Результатом предложенной математической модели взаимодействия роликового направляющего скипа со стыком между проводниками является зависимость ударного импульса от скорости подъема и массы груженого сосуда при заранее предполагаемой величине дефекта. Нагрузка на рассматриваемые элементы подъема прямо пропорциональна массе подъемного сосуда и скорости его движения. По зависимости (см. рис. 2) виден рост нагрузки на армировку и скип при увеличении интенсивности подъема.
Рис. 2. Зависимость ударного импульса от скорости подъема при различных массах груженого сосуда
466

Секция 6. Горные и нефтепромысловые машины и оборудование
В рассмотренной модели взаимодействия подъемного сосуда с жесткой армировкой шахтного ствола учтено реальное положение роликовых направляющих на скипе, что больше соответствует фактическому взаимодействию сосуда с армировкой. В расчете не учитывается влияние массы и положение центра тяжести ролика, так как они сравнительно малы по отношению к массе скипа.
Пользуясь предложенным алгоритмом расчета, по формулам (1) и (2) можно определить динамическую нагрузку, возникающую при взаимодействии роликового направляющего со стыком между проводниками. Анализ полученных результатов позволяет оценить ударный импульс, испытываемый скипом и армировкой, в зависимости от массы груженого скипа и скорости подъема.
Список литературы
1. Прокопов А.Ю. Нагрузки и воздействия на жесткую армировку вертикальных стволов. – Ростов-н/Д: Изд-во журн. «Изв. вузов. Сев.-Кавк. регион», 2008. –
210с.
2.Степанов А.Г. Динамика машин / УрО РАН. – Екатеринбург, 1999.
3.Баклашов И.В. Расчет, конструирование и монтаж армировки стволов шахт. –
М.: Недра, 1973. – 248 с.
4.Стационарные установки шахт / под общ. ред. Б.Ф. Братченко. – М.: Недра,
1977. – 440 с.
5. Ильин С.Р., Ильина С.С., Самуся В.И. Механика шахтного подъема: монография / Мин-во образ. и науки Украины; Нац. горн. ун-т. – Днепропетровск: Изд-во НГУ, 2014. – 247 с.
467

Проблемы разработки месторождений углеводородных и рудных полезных ископаемых
ПОДВОДНЫЕ КОМПЛЕКСЫ – ПЕРСПЕКТИВНЫЙ ШАГ
ВБУДУЩЕЕ НА ПУТИ ОСВОЕНИЯ ЗАЛЕЖЕЙ НЕФТИ
ИГАЗА АРКТИЧЕСКИХ МОРЕЙ
Е.Д. Кожухарь
Научный руководитель – доцент Н.Ф. Лямина Астраханский государственный технический университет
Освещена технология освоения месторождений нефти и газа подводным способом. Также рассмотрены технологии подводной сепарации нефти, газа и газового конденсата. Предложена модель сверхзвукового сепаратора, который отличается от ранее разработанных тем, что в одном компактном устройстве происходит адиабатическое охлаждение и циклонная сепарация. Уникальность сверхзвукового сепаратора заключается в том, что его можно использовать для подготовки попутного и природного газа на месторождениях суши, на газодобывающих морских платформах, для подводной сепарации газа.
Ключевые слова: морская эксплуатация скважин, подводная сепарация, сопло Лаваля, закручивающее устройство, устройство отбора газожидкостной смеси, сверхзвуковая скорость, газовый поток, газоконденсат.
Сегодня все труднее становится удовлетворить возрастающий спрос на углеводородное сырье только за счет разработки континентальных месторождений, из-за их истощения. Основная масса крупных материковых месторождений уже открыта, разведаны их запасы и многие из них разрабатываются. Мировая тенденция такова, что добыча нефти и газа постепенно перемещается с континента на шельф. Возрастающее значение подводных технологий обусловлено относительной удаленностью месторождений от берега, а также суровыми климатическими условиями. Ледовые поверхности многометровым слоем скрывают водную поверхность, исключая возможность вести добычу традиционными способами. В таких условиях реализация поставленных задач по добыче нефти, газа и газового конденсата шельфовой зоны арктических морей возможна лишь с использованием подводных добычных комплексов.
При освоении Киринского месторождения впервые на российском шельфе была применена технология подводной добычи газа, обеспечивающая его передачу от скважин непосредственно на берег без каких-либо надводных конструкций. Сооружение морского добычного комплекса Киринского месторождения включает в себя шесть скважин с подводным расположением устьев, сборный манифольд, систему трубопроводов и шлангокабелей и береговую площадку управления. Центральным звеном комплекса является размещенный на глубине манифольд – особый газосборный узел, работающий в автономном режиме. Это один из самых сложных элементов. Добытый газ собирается на манифольде и затем транспортируется по морскому трубопроводу на береговой комплекс. Манифольд и скважины надежно защищены специальными противотраловыми конструкциями.
468
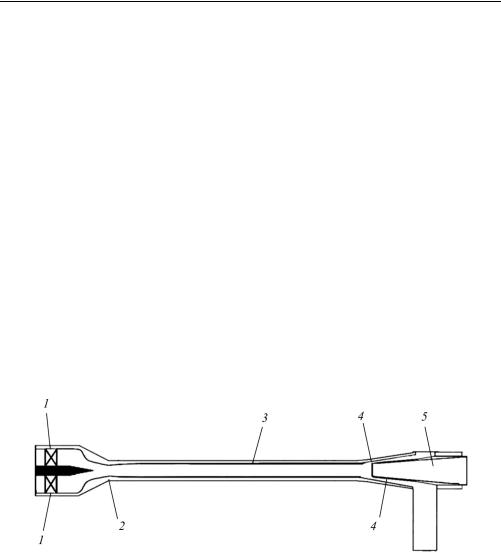
Секция 6. Горные и нефтепромысловые машины и оборудование
Преимущества такого способа добычи следующие:
–возможность добывать углеводороды всложнейших климатических условиях;
–не требуется строительства платформ и иных надводных конструкций;
–не требуется непосредственного присутствия обслуживающего персонала;
–экономическая эффективность по сравнению с морскими платформами. Добываемый природный газ содержит такие примеси, как песок, углекислый
газ и воду. Эти компоненты способны в условиях транспортировки конденсироваться с образованием гидратов в трубопроводах. В связи с этим актуальной задачей является применение сепараторов для подводной эксплуатации газоконденсатного месторождения.
В качестве авторской хотелось бы выдвинуть идею о возможности применения подводного сверхзвукового сепаратора для Киринского ГКМ. Сверхзвуковой сепаратор совмещает в одном компактном устройстве адиабатическое охлаждение и циклонную сепарацию. Адиабатическое охлаждение достигается в сопле. На рис. 1 представлена технология сепарации. Входной поток закручивается неподвижными лопатками в камере 1 и подается в сопло 2, где разгоняется до сверхзвуковой скорости. Далее в рабочей камере 3 происходит сильное охлаждение газа. Выделившаяся при охлаждении жидкость центробежными силами с ускорением, достигающим 106 м/с2, отбрасывается к стенкам выходного раструба 4, а газ выходит через диффузор 5.
Рис. 1. Принципиальная схема сверхзвукового сепаратора:
1 – закручивающие устройства; 2 – до/сверхзвуковое сопло; 3 – рабочая часть; 4 – устройство отбора газожидкостной смеси; 5 – диффузор
Данный сепаратор обладает рядом следующих преимуществ:
–основным достоинством сепаратора является возможность одновременно проводитьосушку, отделение конденсата и извлечение газоконденсатных жидкостей;
–малые габариты;
–работа без применения химических реагентов;
–отсутствие движущихся частей, как следствие – надежность. Принципиальная схема подводной установки подготовки газа с технологией
сверхзвуковой сепарации приведена на рис. 2.
469

Проблемы разработки месторождений углеводородных и рудных полезных ископаемых
Рис. 2. Принципиальная схема подводной установки подготовки газа к транспорту: 1 – устье скважины; 2 – десендер; 3 – клапан; 4 – теплообменник; 5 – дроссель; 6 – сепаратор; 7 – манифольд; 8 – конденсатосборник; 9 – насос; 10 – компрессор
Газ из скважины с давлением 14–15 МПа поступает в десендер, где происходит очистка от песка, затем в подводный теплообменник Т-1, где охлаждается водой. Подводный теплообменник представляет собой набор из 200 изогнутых стальных трубок диаметром 50,8 мм (2 дюйма) длиной 140 м. Газ в подводном теплообменнике охлаждается до температуры 2,5–3,0 °С. После этого газовый поток дросселируется в Др-1 до давления 6–8 МПа. Затем газ подается в подводный сепаратор С-1, где газовый поток отделяется от сконденсировавшейся жидкости. После подводных сепараторов газ поступает в манифольд, а жидкость на подводную компрессорную станцию. После чего продукция отправляется на береговой комплекс.
Список литературы
1.Полстянов Д.Е. Низкотемпературная сепарация // Пути развития. Вузовская наука – Северо Кавказскому региону: материалы XII регион. науч.-техн. конф. Т. 1. Естественные и точные науки. Технические и прикладные науки / СевКавГТУ. – Ставрополь, 2008. – 298 с.
2.7 Marco Betting, Hugh Epsom. Supersonic separator gains market acceptance //
World Oil. – 2007. – April. – Рр. 197–200.
3. Хистяев А.А. Подводные технологии на шельфе России // Oil & Gas Journal. – 2012. – № 6.
470