
2835.Проблемы разработки месторождений углеводородных и рудных полезных и
..pdf
Секция 6. Горные и нефтепромысловые машины и оборудование
уступов дорог общего назначения, расположенных в горной местности, наносящие значительный ущерб.
В связи с изложенным в условиях современной конкуренции в горнодобывающей отрасли для снижения издержек все более актуальным вопросом становится создание новой отечественной техники. На данный момент техника, предназначенная для транспортирования негабаритов и эффективной оборки откосов уступов, отсутствует. Авторами предлагается камнеуборочная машина (КМ), предназначенная для выполнения вспомогательных горных работ в карьере, а также работ специального назначения на дорогах в горной местности с целью обеспечения безопасности при выполнении оборки откосов уступов и ликвидации крупнокусковой горной массы.
Область функционального применения КМ:
–транспортирование негабаритов из рабочего поля карьера;
–разборка крупнообломочных отвалов;
–проведение оборки откосов уступов в карьере;
–зачистка откосов автомобильных и железных дорог в горной местности. Транспортные базы разрабатываемых КМ:
–КМ-а – на базе карьерного автосамосвала БелАЗ-7540 либо автосамосвала общего назначения типа КамАЗ-6511;
–КМ-г – на базе гусеничного автосамосвала типа MST 1500 VD (Morooka
Co. Ltd.);
–КМ-т – на базе колесного трактора типа Т-150КМ;
–КМ-жд – на платформе железнодорожного транспорта типа МПТ-6.
На сегодняшний день при выборе направления исследований были предложены концептуальные подходы для решения поставленных задач, в результате чего были получены патенты, определившие структуру дальнейших работ в области разработки специализированной техники [2, 3]. Также поданы на рассмотрение заявки на рабочий орган КМ – захватное устройство, посредством которого осуществляется внедрение, захват и перемещение кусков горной массы из откосов уступов.
Общий вид камнеуборочной машины КМ-а в процессе выполнения работ по оборке откоса уступа в карьере показан на рис. 1. Рабочим органом КМ является захватное устройство, определение параметров которого представляет важную задачу при проектировании. Величина силы внедрения в горную массу определяется размерами захвата, которые, в свою очередь, зависят от габаритов извлекаемого куска [4]. Связь между указанными параметрами захвата и куска можно установить при следующих допущениях:
1.Кусок горной массы располагается внутри условной сферы (рис. 2, а), диаметр D которой равен наибольшему габаритному размеру куска, т.е. его условной длине [4].
2.Отношение объема куска горной массы к объему шара диаметром D равняется коэффициенту неполноты kн (в первом приближении можно принять рав-
441
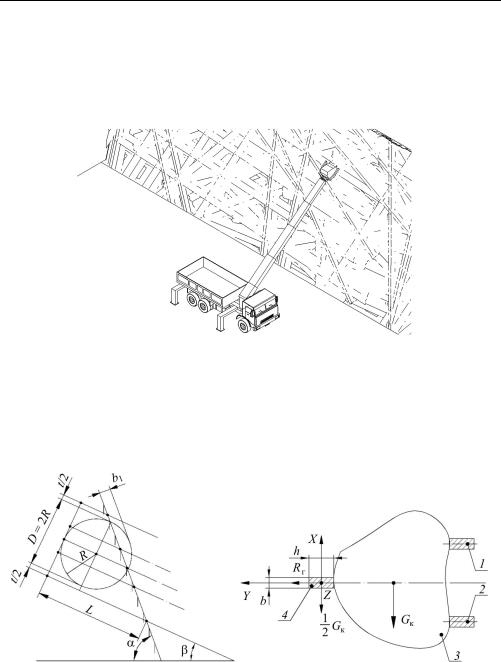
Проблемы разработки месторождений углеводородных и рудных полезных ископаемых
ным отношению объемов вписанного в рассматриваемую сферу куба и соответственно шара, т.е. kн ≈ 0,338).
3. Размеры захвата (т.е. длины зубьев захвата и расстояния между ними) должны обеспечить его свободное внедрение в горную массу вокруг сферы и последующее фиксирование куска внутри нее.
Рис. 1. КМ-а в процессе выполнения оборки откосов уступа в карьере
Принимаем, что продольные оси зубьев (задав количество зубьев, равное трем) в процессе переноса куска горной массы 3 захватом горизонтальны, сечения зубьев 1, 2, 4 имеют прямоугольную форму с переменными по длине зуба размерами h, b (рис. 2, б), т.е. зубья имеют форму балки переменного сечения.
а |
б |
Рис. 2. Расположение зубьев захватного устройства при внедрении и захвате куска горной массы
Удельную массу зуба по отношению к массе извлекаемого из откоса куска горной массы, в зависимости от параметров уступов и прочностных характери-
442
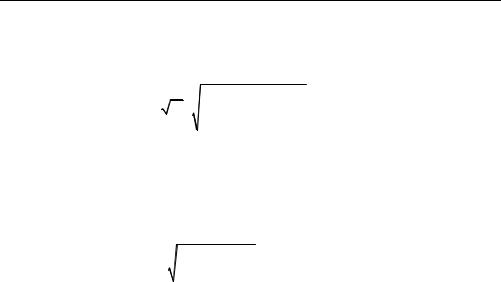
Секция 6. Горные и нефтепромысловые машины и оборудование
стик захвата (см. рис. 2, а, б), задав условие, что масса зуба составляет 5 % от массы куска, в результате некоторых предварительных расчетов можно определить из выражения
M |
З |
|
3 |
|
1 + kР / (2 fтр ) 2 |
||||
|
= |
|
3 |
18 3 |
|
|
kвн5/3 γЗ Gк2/9 g , |
||
Gк / g |
5 |
σ д |
|||||||
|
|
|
|
|
где МЗ – масса зуба захватного устройства при длине внедрения L, кг; Gк – сила тяжести куска горной массы, Н; g – ускорение свободного падения, м/с2; kP – коэффициент запаса, kP > 1; fтр – коэффициент трения между зубьями и куском породы; σд – допускаемые напряжения изгиба, Па; γЗ – плотность материала зуба, кг/м3;
|
|
3 |
|
1 |
|
1 |
+ sin(α − β) + cos(α− β) − kb |
|
||
коэффициент |
kвн = |
3 |
|
|
|
|
|
|
|
, |
|
|
|
|
π γ kн g |
|
|
|
sin(α − β) |
|
|
|
|
4 |
|
|
|
|
|
где γ – плотность куска горной массы, кг/м3; kн – коэффициент неполноты геометрической формы (отношение объема куска породы к объему шара диаметром D = 2R); α – угол откоса уступа, град; β – угол наклона стрелы (осей зубьев) к го-
ризонту, |
град. |
При |
|
|
этом |
|
длина |
внедрения |
зуба |
в |
откос |
|||||
|
R − b1 |
|
|
|
t |
|
cos(α |
− β) |
|
|
|
|
|
|||
L = |
|
|
+ R + R + |
|
|
|
|
|
|
|
при b1 |
= kb·R, t = 0 по рис. 2, а, согласно |
||||
sin(α − β) |
2 |
|
|
|
||||||||||||
|
|
|
|
|
sin(α |
− β) |
|
|
|
|
|
которому t/2 – условный зазор между осью зуба и сферой, м; b1 – условный размер части сферы, расположенной вне откоса (т.е. вне горной массы), м, b1 = kb·R.
Законы изменения размеров сечения зуба h (z), b (z) по его длине (см. рис. 2, б) из условия, что напряжения изгиба в любом сечении зуба одинаковы и равны допускаемым [5], принимают следующий вид:
|
WY |
+ RГ z / WX = σд , |
Gк z / 2 |
||
(Gк + RГ ) z |
/ WX = σд , |
|
|
|
|
где z – расстояние от края зуба до его поперечного сечения с размерами b×h , м; WY, WX – моменты сопротивления изгибу сечения зуба относительно соответствующих осей в системе координат OXYZ, м3; Rг – реакция со стороны куска, равная силе давления зуба на кусок из условия его удержания за счет сил трения между контактирующими поверхностями зубьев и куска, Н, Rг = kP Gк / 2 fтр.
Список литературы
1. Тарасов П.И., Андрюшенков Д.Н. Транспортирование негабаритов как альтернативный способ их ликвидации из рабочей зоны карьера // Известия вузов. Горный журнал / УГГУ. – Екатеринбург, 2014. – № 2. – С. 4–9.
443

Проблемы разработки месторождений углеводородных и рудных полезных ископаемых
2. Пат. 137515 РФ, МПК В60P 1/04. Платформа карьерного автосамосвала / Тарасов П.И., Андрюшенков Д.Н.; ИГД УрО РАН (RU). – № 2013136286; заявл.
01.08.13; рег. 20.02.14.
3. Пат. 141200 РФ. МПК В60P 1/04. Карьерный автосамосвал / Тарасов П.И., Андрюшенков Д.Н., Дерягин А.М.; ИГД УрО РАН (RU). – № 2013136291; заявл.
01.08.2013.
4.Кулешов А.А. Проектирование и эксплуатация карьерного автотранспорта: справочник / С.-Петерб. горн. ин-т. – СПб., 1995. – Ч. II. – 203 с.
5.Писаренко Г.С., Яковлев А.П., Матвеев В.В. Справочник по сопротивлению материалов. – Киев: Наукова думка, 1975. – 704 с.
444

Секция 6. Горные и нефтепромысловые машины и оборудование
ОБОСНОВАНИЕ РАЦИОНАЛЬНОЙ МЕТОДИКИ ДИАГНОСТИРОВАНИЯ ТЕХНИЧЕСКОГО СОСТОЯНИЯ ПРИВОДОВ ИСПОЛНИТЕЛЬНЫХ ОРГАНОВ КОМБАЙНОВ «УРАЛ-20Р»
С.А. Асонов
Научный руководитель – канд. техн. наук Д.И. Шишлянников Пермский национальный исследовательский политехнический университет
Предложен перспективный способ оценки технического состояния и остаточного ресурса элементов привода исполнительных органов комбайна «Урал-20Р». Представлены результаты экспериментальных исследований нагруженности привода комбайна.
Ключевые слова: диагностика, механическая трансмиссия, контроль мощности, бортовойрегистратор параметров, диагностика, проходческо-очистнойкомбайн.
Для предприятий, осуществляющих добычу калийной руды подземным способом с использованием проходческо-очистных комбайнов «Урал», актуальной остается задача повышения эффективности эксплуатации добычных машин: снижение затрат на техническое обслуживание и ремонт, уменьшение количества внезапных отказов и связанных с ними простоев. Решение данной задачи возможно на основе внедрения автоматизированных средств контроля параметров работы и оценки технического состояния узлов и деталей комбайнов «Урал», обоснования эффективных методик определения остаточного ресурса и диагностики деталей приводов исполнительных органов добычных машин.
На сегодняшний день универсальными оценочными параметрами, по которым контролируется техническое состояние трансмиссии, являются: измерение шума и вибрации, температура нагрева и состав масла, замеры мощности на выходе и входе механической системы [1].
В силу исторических причин наибольшее развитие получили методы вибрационного мониторинга с отработанной структурой средств измерения и математического анализа сигналов. Основное внимание в этих системах уделяется анализу высокочастотных составляющих вибросигнала, которые в отличие от низкочастотных возбуждаются малыми по величине колебательными силами, возникающими еще в начальной стадии развития дефектов [2].
Применение шумовых и вибрационных методов для диагностики проходче- ско-очистных комбайнов возможно только для уточнения неисправного состояния отдельного элемента по его вибрационным сигналам. Опыт ведущих отечественных и зарубежных горнодобывающих предприятий показывает, что метод достаточно трудоемок и требует специальных стендов. Он эффективно используется для установок, имеющих одну собственную частоту внутреннего возмущения (турбина), когда внешняя нагрузка почти не влияет на виброакустический сигнал или имеет постоянную частоту. У проходческо-очистных комбайнов основным источником шума и вибраций является случайный динамический характер внешней нагрузки, которая содержит практически все частоты в пределах до 10–15 Гц.
445

Проблемы разработки месторождений углеводородных и рудных полезных ископаемых
Оценка состояния трансмиссии по температуре масла и наличию в нем механических примесей является одним из классических и наиболее просто реализуемых методов технической диагностики. В то же время данный метод имеет ряд существенных недостатков. Температура масла в разных точках редукторов различна и определяется главным образом величиной потерь холостого хода и трением в кинематических парах трансмиссии. Изменение температуры и состава масла происходит после возникновения дефектов, характер которых может привести к аварийному отказу. Для забора проб масла необходимаостановка добычной машины [1].
Известно, что постепенные и внезапные отказы оборудования, вызванные изнашиванием, поломками и деформацией деталей, можно описать с единой энергетической точки зрения. Исследования усталостного разрушения металлов показывают, что объем материала детали разрушается при достижении критического значения внутренней энергии, т.е. каждый элемент трансмиссии добычного комбайна имеет свой энергоресурс, определяемый количеством энергии, затраченной на его разрушение. Из указанного следует, что одним из перспективных способов оценки технического состояния добычных машин является анализ характера изменения и величины мощности, потребляемой двигателями комбайна [3].
Исследование значений и характера нагрузок на приводы и трансмиссии исполнительных органов комбайнов «Урал» с целью определения возможности оценки технического состояния их элементов проведено сотрудниками кафедры ГНМ ПНИПУ совместно со специалистами ООО «РКЦ» (г. Пермь). Исследования осуществлялись в период с 2001 по 2008 г. посредством специально изготовленного измерительного, регистрирующего и программного комплекса «ВАТУР» на комбайнах, эксплуатируемых на рудниках ОАО «Уралкалий» [4].
Комплекс «ВАТУР» обеспечивает измерение и запись мгновенных значений тока нагрузки и напряжения, по измеренным значениям токов и напряжений рассчитываются мгновенные значения активной и полной мощности двигателей (рис. 1). Визуализация и обработка полученных данных осуществляется с помощью программы «Ватур-оф». Полученные записи активных трехфазных мощностей приводов обрабатывались с использованием методик спектрального анализа с целью выявления частотных составляющих, характеризующих колебания кинематической цепи исполнительный орган – редукторы – приводной двигатель.
На приведенном графике изменения активной мощности электродвигателей приводов относительного движения резцовых дисков можно выделить участки запуска (A–B), холостого хода (B–C), зарубки (C–D) и установившегося режима работы (D–E). Для участка установившегося режима определяются средние значения параметров работы двигателей комбайна – тока, напряжения, активной и полной мощности. Также следует отметить, что на графике активных мощностей двигателей относительного движения явно просматривается низкочастотная периодическая составляющая. За один оборот каждого исполнительного органа возникают два интервала с пиком нагрузки и два интервала с их падением. Падение нагрузки на приводах резцовых дисков и увеличение динамики обусловливается наличием общей зоны массива, разрушаемой дисками обоих исполнительных органов. Таким образом, при разрушении руды возникают циклические нагрузки
446
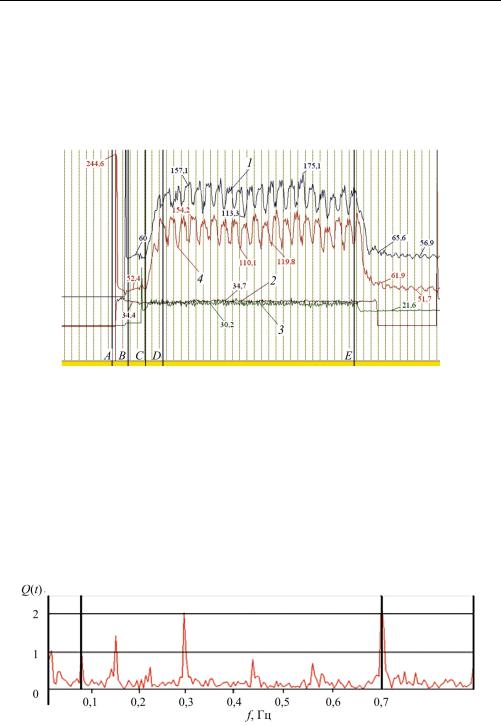
Секция 6. Горные и нефтепромысловые машины и оборудование
определенной амплитуды на режущий орган. Нагрузки воспринимаются всеми элементами цепочки режущий орган – электродвигатель и меняют свой частотный состав при прохождении через различные элементы комбайна. Это связано с тем, что каждый элемент комбайна воспринимает нагрузки с определенной частотой, зависящей от скорости его вращения. При изменении механических свойств того или иного элемента частота и амплитуда воздействия нагрузок на него изменяются.
Рис. 1. График активных трехфазных мощностей электродвигателей при средней скорости движения комбайна «Урал 20Р» 10,5 м/ч: 1, 4 – приводы относительного движения резцовых дисков; 2 – привод конвейера; 3 – привод отбойного устройства. Шаг линий сетки 5 с. Сносками обозначены мгновенные значения активных мощностей
Привод исполнительного органа частично фильтрует одни частоты и усиливает другие, поэтому корреляционная функция и спектральная плотность активной мощности (рис. 2) характеризуют его качество, так как позволяют определить частоты, на которых возникают резонансные явления, связанные с собственными колебаниями передач привода. Например, резкое сглаживание спектров нагрузок свидетельствует о значительных усилиях трения в элементах привода, т.е. об увеличении сопротивления в подшипниках и т.д.
Рис. 2. График спектральной плотности Q (t) активной мощности двигателя переносного вращения комбайна «Урал-20Р»
447

Проблемы разработки месторождений углеводородных и рудных полезных ископаемых
Способ контроля технического состояния комбайна посредством анализа записей токов, напряжений и активных мощностей приводов, в отличие от других способов диагностики, информативен, просто реализуем, позволяет осуществлять контроль на работающей в установившемся режиме добычной машине. Непрерывная запись активных мощностей приводов обеспечит реализацию рациональных режимов работы, прогнозирование ресурса комбайна и позволит минимизировать количество внезапных отказов, уменьшить число простоев добычных машин вследствие аварийных ремонтов.
Список литературы
1.Коломийцев М.Д. Эксплуатация горных машин и автоматизированных комплексов. – Л.: Изд-во ЛГИ, 1988. – 96 с.
2.Барков А.В., Баркова Н.А., Азовцев А.Ю. Мониторинг и диагностика роторных машин по вибрации / СПбГМТУ. – СПб., 2000. – 159 с.
3.Динамические процессы горных машин / А.В. Докукин, Ю.Д. Красников,
З.Я. Хургин [и др.]. – М.: Наука, 1972. – 150 с.
4.Исследование нагруженности и возможности прогнозирования энергоресурса приводов исполнительных органов комбайна «Урал-20Р» / Г.Д. Трифанов, А.А. Князев, Н.В. Чекмасов, Д.И. Шишлянников // Горное оборудование и элек-
тромеханика. – 2013. – № 2. – С. 41–44.
448

Секция 6. Горные и нефтепромысловые машины и оборудование
ОБЗОР И АНАЛИЗ СТАНКОВ-КАЧАЛОК, ИСПОЛЬЗУЕМЫХ В НЕФТЯНОЙ ПРОМЫШЛЕННОСТИ РОССИИ
М.В. Бажин
Научный руководитель – канд. техн. наук А.К. Муравский Пермский национальный исследовательский политехнический университет
Рассмотрены наиболее распространенные виды станков-качалок, используемых в нефтяной промышленности. Указаны их достоинства и недостатки. Обозначены перспективы использования станков-качалок.
Ключевые слова: станок-качалка, балансир, редуктор, электродвигатель, число качаний, добыча нефти, нефтяная промышленность, дебит скважины.
Примерно 66 % действующих скважин СНГ эксплуатируются штанговыми скважинными насосными установками (ШСНУ), дебит скважин от нескольких десятков килограмм до нескольких тонн в сутки [1].
Наиболее часто используются балансирные станки-качалки типа станоккачалка дезаксиальный (СКД), однако в последнее время также вводятся в эксплуатацию и другие типы, такие как станок-качалка тихоходный, станок-качалка без ременной передачи.
Уаксиальных станков-качалок время хода точки подвеса штанг (ТПШ) вверх
ивниз одинаково, поэтому такие станки-качалки называют симметричными. Однако нагружение ТПШ за время хода вниз и вверх разное, что обусловлено работой штангового насоса. При ходе вверх станок-качалка производит работу по поднятию колонны штанг и столба жидкости, а при ходе вниз штанговая колонна идет под собственным весом, а вес столба жидкости передается на трубы. Если средняя скорость движения ТПШ при ходе вверх будет меньше, чем при ходе вниз, то это позволяет уменьшить ускорения, а следовательно, и динамические нагрузки, действующие на колонну штанг при ходе вверх. Ввиду этого станкикачалки в настоящее время выполняют с небольшим дезаксиалом (рис. 1), у которых время хода вверх больше, чем вниз. Но слишком большое время хода ТПШ вверх тоже не желательно, так как возрастают утечки через плунжер.
Поскольку разница в кинематике конструктивно обеспечивается элементарными средствами, т.е. тем или иным расположением редуктора относительно балансира, и не требует специальных изменений конструкции, станки-качалки по отраслевому стандарту ОСТ 26-16-08–87 не отличаются от аналогичных по ГОСТ 5866–76.
Тихоходные станки-качалки (рис. 2) используются на малодебитных скважинах (дебит менее 5 м3/сут). Такие станки качалки работают в циклическом режиме. Использование циклического режима эксплуатации связано с целым рядом существенных неблагоприятных факторов, в числе которых неравномерная выработка пласта, неэффективное использование наземного и подземного оборудования, недостаточный межремонтный период по сравнению с непрерывно функционирующими скважинами, затруднения, возникающие в зимнее время.
449
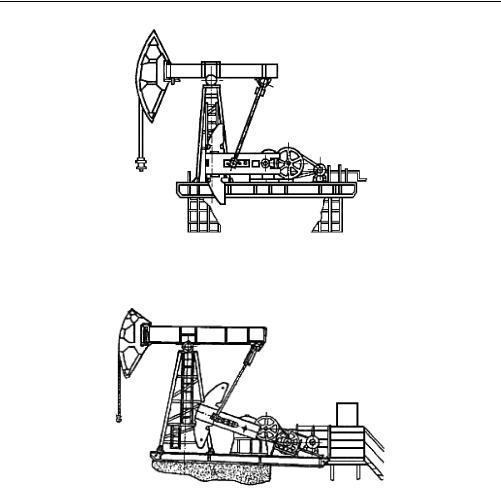
Проблемы разработки месторождений углеводородных и рудных полезных ископаемых
Рис. 1. Станок-качалка типа СКД с редуктором на раме и кривошипным уравновешиванием
Рис. 2. Тихоходный станок-качалка с дополнительной ременной передачей
Конструкция тихоходного станка-качалки с увеличенным передаточным числом за счет введения в трансмиссию дополнительной ременной передачи позволяет снизить частоту качаний балансира до 0,8–1,7 в минуту.
Для этого между электродвигателем и редуктором монтируется промежуточный вал с соответственно малым и большим по диаметру шкивами, установленными консольно. Компоновка промежуточного вала может быть вертикальной
игоризонтальной.
Вслучае горизонтальной компоновки раму станка-качалки приходится немного наращивать на величину межосевого расстояния дополнительной ременной передачи.
Конструктивное решение с дополнительной передачей отличается простотой, позволяет применять его к любому станку-качалке и допускает изготовление необходимых деталей силами добывающих предприятий.
450