
714
.pdf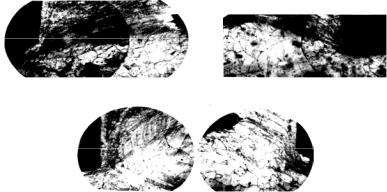
на различных скоростях резания с подачей на зубьях протяжки 0,06 мм/зуб (а) и 0,02 мм/зуб (б). Установлено, что с увеличением скорости резания и снижением подачи пластическая деформация уменьшается.
3. Электронно-микроскопическое исследование стружки и зоны резания: с помощью электронных и обычных микроскопов изучаются процессы изменения микроструктуры обработанной поверхности стружки. Например, на рис. 30 показана микроструктура поверхности металла после обработки на различных скоростях резания. При этом зона резания увеличилась более чем в 300 раз. Наглядно видно изменение зерен металла перед зоной резания, в самой зоне резания и в обработанной поверхности вследствие мощной пластической деформации.
а |
б |
вг
Рис. 30. Микрошлифы корней стружки при протягивании сплава ХН77ТЮР-ВД со скоростями резания 2 (а), 8 (б), 26 (в), 40 (г) м/мин (Sz = 0,1 мм/зуб, шлифы протравлены, ×300)
4.Киносъемка (скоростная и замедленная) процесса резания.
5.Поляризационно-оптическое изучение напряжений зоны ре-
зания.
6.Рентгено-структурный анализ зоны резания.
7.Метод координатной сетки.
61

2.1.3. Методы моделирования деформаций при изучении процессов резания
Исходные данные (рис. 31): V – скорость резания;
Vc – скорость перемещения стружки; a – толщина срезаемого слоя;
a1 – толщина стружки;
b – ширина срезаемого слоя (толщина образца); β – угол сдвига;
I – расстояние до торца.
Рис. 31. Кинематические параметры краевой зоны
Условия резания при протягивании
Свойства обрабатываемых материалов: σb = 500…1200 МПа; модуль упругости Е = 210 000 МПа; коэффициент трения µ = 0,3.
Режимы резания: V = 0,5…40 м/мин; Sz = 0,005…0,3 мм/зуб. Геометрия режущего клина инструмента: γ = –10°; 0°; +10°;
α = 3…8°; λ = 0…20°; радиус округления ρ = 0…0,02 мм.
62

Условия резания (деформирования), принятые при моделировании
Свойства обрабатываемых материалов: σb = 500…1200 МПа;
Е = 210 000 МПа; µ = 0,3.
Режимы резания: V = Vдеф → min; а = Sz = 0,1; 0,5; 1,0 мм; b = t > 10 мм.
Геометрия режущего клина инструмента: γ = –10°; 0°; +10°;
α = 5°; λ = 0°; ρ = 0; 0,3; 0,6 мм.
Объекты исследования
I – краевая зона обрабатываемой детали;
II– зона контакта стружки с инструментом; III – режущий клин инструмента.
Математическое моделирование деформации краевой зоны детали
Приведем пример математического моделирования деформации краевой зоны детали при выходе инструмента из заготовки
(рис. 32, 33).
Рис. 32. Схема краевой зоны при вы- |
Рис. 33. Расчетная схема дефор- |
ходе инструмента из заготовки: а – |
мирования краевой зоны |
толщина срезаемого слоя; β – угол |
|
сдвига; U – перемещение инструмента |
|
63

Математические зависимости
Характеристики напряженно-деформированного состояния
(НДС):
U(r) – поля векторов перемещения точек тела; r Ω – точка тела, заданная своим радиус-вектором; ε(r) – компоненты тензора деформации;
σ(r) – компоненты тензора напряжений; S(r) – степень деформации материала.
В образце реализуется плосконапряженное состояние:
σ33 = τ13 = τ23 = γ13 = γ23 = 0.
При деформировании должны выполняться следующие условия: |
|||
– уравнение равновесия dσij (r)= 0, |
r Ω ; |
||
– физические соотношения dσij (r)= Сijmn (r)dεmn (r), r |
|
; |
|
Ω |
|||
– геометрические соотношения |
dεij (r)= 1 (dUi, j (r)+ dU j, i (r)), |
2
r Ω;
– граничные условия:
для точек левой стороны области dU1 = dU2 = 0, r Γ1;
для точек свободной поверхности dF1 = dF2 = 0, r Γ2 ;
для точек, контактирующих с инструментом: dU2 = ∆U , dF1 = 0, r Γ3.
Результаты изменения предела прочности представлены на рис. 34.
64

I = 4 мм |
I = 3 мм |
I = 2 мм |
σb = 50 + 300S
σb = 50 + 200S
σb = 50 + 100S
Рис. 34. Влияние модуля упрочнения материала на степень деформации краевой зоны детали
2.2.Процесс стружкообразования
2.2.1.Типы стружек при резании пластичных
ихрупких материалов
В1870 году И.А. Тиме была предложена классификация типов стружек, образующихся при резании различных материалов. Классификация оказалась настолько удачной, что, несмотря на то, что со времен И.А. Тиме появились совершенно новые конструкционные материалы, обрабатывающиеся с иными режимами резания, ею пользуются и в настоящее время. Согласно классификации И.А. Тиме при резании конструкционных материалов в любых условиях обра-
зуются четыре вида стружек: элементная, суставчатая, сливная и стружка надлома. Элементную, суставчатую и сливную стружку называют стружками сдвига, так как их образование связано с напряжениями сдвига. Стружку надлома иногда называют стружкой отрыва, так как ее образование связано с растягивающими напряжениями. Внешний вид всех перечисленных типов стружки изображен на рис. 35.
65

a |
б |
в |
г |
Рис. 35. Типы стружек, образующихся при резании пластичных и хрупких материалов: а – элементная, б – суставчатая, в – сливная, г – стружка надлома
Элементная стружка (см. рис. 35, а) состоит из отдельных элементов 1 приблизительно одинаковой формы, несвязанных или слабо связанных друг с другом. Границу тп, отделяющую образовавшийся элемент стружки от срезаемого слоя, называют поверхностью скалывания. Физически она представляет собой поверхность, по которой в процессе резания периодически происходит разрушение срезаемого слоя.
У суставчатой стружки (см. рис. 35, б) разделения на отдельные части не происходит. Поверхность скалывания только наметилась, но она не пронизывает стружку по всей толщине. Поэтому стружка состоит как бы из отдельных суставов 1 без нарушения связи между ними.
Основным признаком сливной стружки (см. рис. 35, в) является ее сплошность (непрерывность). Если на пути движения сливной стружки нет никаких препятствий, то она сходит непрерывной лентой, завиваясь в плоскую или винтовую спираль, пока часть стружки не отламывается под действием собственного веса. Поверхность 1 стружки, прилегающую к передней поверхности инструмента, называют контактной стороной (поверхностью). Она сравнительно гладкая, а при высоких скоростях резания отполирована в результате трения о переднюю поверхность инструмента. Ее противоположную поверхность 2 называют свободной стороной (поверхностью) стружки. Она покрыта мелкими зазубринками-насечками и при высоких
66
скоростях резания имеет бархатистый вид. Стружка соприкасается с передней поверхностью инструмента в пределах площадки контакта, ширина которой обозначена через с, а длина равна рабочей длине главного лезвия. В зависимости от рода и свойств обрабатываемого материала и скорости резания ширина площадки контакта в 1,5…6 раз больше толщины срезаемого слоя.
Стружка надлома (см. рис. 35, г) состоит из отдельных, не связанных друг с другом кусочков различной формы и размеров. Образованию стружки надлома сопутствует мелкая металлическая пыль. Поверхность разрушения тп может располагаться ниже поверхности резания, в результате чего последняя покрыта следами от выломанных из нее кусочков стружки.
Тип стружки во многом зависит от рода и механических свойств обрабатываемого материала. При резании пластичных материалов возможно образование первых трех типов стружки, элементной, суставчатой и сливной. По мере увеличения твердости и прочности обрабатываемого материала сливная стружка переходит в суставчатую, а затем в элементную. При обработке хрупких материалов образуется или элементная стружка (чаще), или стружка надлома (реже). С повышением твердости материала, например чугуна, элементная стружка переходит в стружку надлома.
Из геометрических параметров инструмента наиболее сильно на тип стружки влияют передний угол и угол наклона главного лезвия. При обработке пластичных материалов влияние углов γ и λ принципиально одинаково: по мере их увеличения элементная стружка переходит в суставчатую, а затем в сливную. При резании хрупких материалов при больших передних углах может образовываться стружка надлома, которая по мере уменьшения переднего угла переходит в элементную. При увеличении угла наклона главного лезвия стружка постепенно превращается в элементную.
На тип стружки оказывают влияние подача (толщина срезаемого слоя) и скорость резания. Глубина резания (ширина срезаемого слоя) на тип стружки практически не влияет. Увеличение подачи (толщины срезаемого слоя) приводит при резании пластичных материалов
67
к последовательному переходу от сливной стружки к суставчатой и элементной. При резании хрупких материалов с увеличением подачи элементная стружка переходит в стружку надлома.
Наиболее сложно на тип стружки влияет скорость резания. При резании большинства углеродистых и легированных конструкционных сталей, если исключить зону скоростей резания, при которых образуется нарост (о чем речь пойдет ниже), по мере увеличения скорости резания стружка из элементной становится суставчатой, а затем сливной. Однако при обработке некоторых жаропрочных сталей и сплавов, а также титановых сплавов повышение скорости резания, наоборот, превращает сливную стружку в элементную. Физическая причина этого явления до настоящего времени полностью не выяснена. Повышение скорости резания при обработке хрупких материалов сопровождается переходом стружки надлома в элементную стружку с уменьшением размеров отдельных элементов и упрочнением связи между ними.
При применяемых в производстве геометрических параметрах инструментов и режимах резания основными типами стружки при резании пластичных материалов являются сливная (чаще) и суставчатая (реже). Основным типом стружки при резании хрупких материалов является элементная. В настоящее время наиболее подробно изучен процесс сливного стружкообразования. Образование элементной стружки при резании как пластичных, так и хрупких материалов изучено недостаточно.
2.2.2. Деформированное состояние зоны стружкообразования
при элементной и сливной стружке
Образование элементной стружки изучено значительно хуже, чем образование сливной. Кинограммы процесса резания и наблюдения за искажением ячеек делительной сетки n показывают, что прежде чем произойдет разрушение по плоскости скалывания тп (рис. 36) в объеме будущего элемента стружки, имеют место значительные деформации сжатия, вызывающие течение материала срезаемого слоя
68
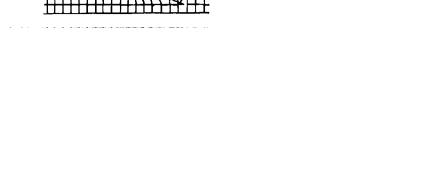
|
|
|
|
|
|
|
|
|
|
Рис. 36. Искажение делительной |
Рис. 37. Схема превращения срезае- |
сетки в элементе стружки |
мого слоя в элемент стружки |
по передней поверхности перпендикулярно и параллельно лезвию инструмента.
С учетом этого превращение срезаемого слоя в элемент стружки происходит следующим образом (рис. 37). При перемещении инструмента на расстояние ∆L передняя поверхность воздействует на некоторый объем срезаемого слоя, ограниченный параллелограмом
m0mnn0.
Когда напряжения сжатия превзойдут предел текучести материала обрабатываемой детали, начнется его течение по передней поверхности и точка m0 окажется не в точке k, куда она попадает при образовании сливной стружки, а в точке q. Одновременно происходит укорочение стороны параллелограмма m0n0 до размера qp. В результате этого параллелограмм m0mnn0 срезаемого слоя превращается в элемент стружки mnpq. Когда запас пластичности материала обрабатываемой детали будет исчерпан, происходит разрушение по плоскости скалывания, и сколотый элемент перемещается вверх по передней поверхности. Чем больше степень деформации срезаемого слоя, тем больше отличаются по длине стороны трапеции mn и qp и тем больше форма элементной стружки приближается к треугольной. Сжимающие деформации вызывают значительное уширение ос-
69
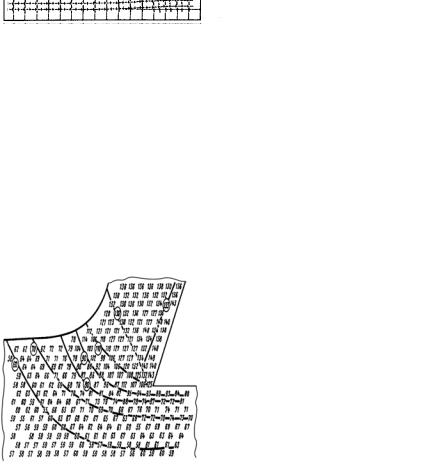
|
нования элемента стружки, на- |
|
|
много большее, чем уширение |
|
|
сливной стружки. |
|
|
Исследования, |
проведенные |
|
с помощью метода |
делительной |
|
сетки (рис. 38), а также измерение |
|
Рис. 38. Переходная зона, выявлен- |
микротвердости корней стружки |
|
(рис. 39) показали, что между сре- |
||
ная методом делительной сетки |
заемым слоем и образовавшейся |
стружкой существует более или менее отчетливо выраженная переходная зона.
Схема, поясняющая процесс образования сливной стружки, представлена на рис. 40. Режущий клин инструмента через площадку контакта шириной с действует на срезаемый слой толщиной а.
Рис. 39. Переходная зона, выявРис. 40. Зоны первичной и вторичной
ленная по изменению микротвер- |
деформации при превращении срезае- |
дости |
мого слоя в сливную стружку |
Сосредоточенная сила Р, с которой передняя поверхность инструмента давит на срезаемый слой, получила название силы стружкообразования. Линией ОK обозначена нейтральная линия, разграничивающая области сжимающих и растягивающих напряжений в обра-
70