
714
.pdf
в несколько раз превосходит среднюю температуру стружки. Температура контакта на передней поверхности приблизительно равна температуре контактной поверхности стружки; это свидетельствует о том, что температура различных слоев стружки по ее толщине неодинакова – убывает по мере приближения к свободной стороне стружки.
3.1.2.Понятие о тепловом поле
итемпературе резания
На рис. 83 представлено изменение температуры θx для различных точек площадки контакта на передней поверхности инструмента. Максимальная температура соответствует точке, лежащей приблизительно на половине ширины площадки контакта. К лезвию и к концу площадки температура убывает. На площадке контакта задней поверхности инструмента с поверхностью резания температура распределяется также неравномерно. Поэтому под температурой резания θ понимают среднюю температуру на поверхности контакта инструмента со стружкой и поверхностью резания. Если через θп.ср и θз.ср. обозначить средние температуры на площадках контакта передней и задней поверхностей, то температура резания
θ = (θп.ср.с + θз.ср.с2)/(с + с2).
Температуру резания иногда называют средней температурой контакта.
Для незатупленного инструмента ширина сз площадки контакта задней поверхности с поверхностью резания исчезающе мала, а поэтому температуру резания можно считать равной средней температуре на площадке контакта стружки с передней по-
Рис. 83. Изменение температуры θх по ширине площадки контакта с при точении стали 40 (t = 1,5 мм;
S = 0,21 мм/об.; V = 115 м/мин)
151

верхностью, т.е. θ = θп.ср. Передняя поверхность инструмента нагревается за счет тепла деформации и трения. Поэтому температура резания равна сумме двух температур: температуры деформации θд и средней температуры трения на передней поверхности θп.ср., т.е.
θ = θд + θп.ср.
Температура резания зависит от мощности тепловых источников в зоне деформации и на передней поверхности инструмента и интенсивности стоков тепла в деталь и инструмент. При резании определенного материала температура резания растет с увеличением скорости резания и размеров срезаемого слоя. Однако их влияние на температуру резания неодинаково. На основании измерений получена формула, связывающая температуру резания с толщиной, шириной срезаемого слоя и скоростью резания при работе различными инструментами:
θ = CθV manbq.
Коэффициент Cθ в формуле зависит от рода и механических свойств обрабатываемого материала, геометрических параметров инструмента и применяемой смазочно-охлаждающей жидкости. При любых видах обработки величины показателей т, п и q неодинаковы: m > n > q, т.е. на температуру резания наибольшее влияние оказыва-
|
ет скорость резания, затем толщина |
|||||
|
срезаемого слоя и наименьшее – ши- |
|||||
|
рина срезаемого слоя. Измерение тем- |
|||||
|
пературы резания при увеличиваю- |
|||||
|
щемся отношении b/a также свиде- |
|||||
|
тельствует об ее уменьшении: |
|||||
|
θ = |
|
Сθ′ |
. |
||
|
|
а p |
||||
|
|
|
||||
|
|
|
|
|
|
|
|
|
|
||||
|
|
b |
|
|
||
Рис. 84. Схема зависимости |
В чем причина |
неодинакового |
||||
влияния величин b и a на температуру |
||||||
площади контакта от ширины |
||||||
и толщины и срезаемого слоя |
резания? На рис. 84 |
изображены два |
||||
|
152 |
|
|
|
|
одинаковых резца, срезающих слои материала с одинаковой площадью поперечного сечения F = 2аb. Резец I срезает слой шириной 2b и толщиной а, а резец II срезает слой шириной b и толщиной 2a. Таким образом, на передней поверхности резцов на площади контакта 2bа действуют тепловые источники, мощность которых можно считать приблизительно одинаковой. Источники скользят по контактной поверхности стружки со скоростью, равной скорости стружки. Из расчетов Д.К. Иегера следует, что при увеличении отношения длины движущегося полосового источника тепла к его ширине средняя температура трения в пределах площади контакта непрерывно уменьшается. К этому следует добавить, что и условия отвода тепла через тело инструмента для резца I более благоприятны, так как источник тепла относительно более удален от вершины резца, что также способствует снижению температуры резания. Таким образом, резец I должен работать с меньшей температурой резания, нежели резец II.
Неодинаковое влияние ширины и толщины срезаемого слоя на температуру резания позволяет сделать следующий важный вывод: для уменьшения температуры резания при заданной площади сечения срезаемого слоя необходимо работать с возможно большим отношением b/a, т.е. с широкими и тонкими стружками.
Выражая физические размеры срезаемого слоя при точении в формуле через глубину резания, подачу и главный угол в плане, получим
θ = CθV mS nt q(sin ϕ)n–q.
Из выражения следует, что при точении подача и глубина резания на температуру резания влияют с той же интенсивностью, что и толщина и ширина срезаемого слоя. Следовательно, для снижения температуры резания при заданной площади сечения срезаемого слоя необходимо работать с возможно большим отношением t/S. При заданных глубине резания и подаче температуру резания можно уменьшить, уменьшая главный угол в плане резца. Последнее связано с тем, что при уменьшении угла ϕ отношение b/a возрастает.
153
Интенсивность влияния скорости резания на температуру при различных скоростях неодинакова. Чем выше скорость резания, тем меньшее влияние оказывает ее увеличение на возрастание температуры резания. Поэтому и величина показателя степени при скорости резания уменьшается с ее увеличением. Например, при
V < 100 м/мин т = 0,5…0,4, а при V > 100 м/мин т = 0,4…0,25.
Уровень температуры резания зависит от рода и механических свойств обрабатываемого материала. Чем больше работа, затрачиваемая на резание, тем при прочих равных условиях выше и температура резания. Поскольку средняя температура стружки при резании чугуна ниже, чем при резании стали, температура резания при обработке чугуна также ниже на 40…50 %. С увеличением твердости и прочности обрабатываемого материала температура резания возрастает.
При постоянной мощности тепловых источников температуру резания можно понизить, интенсифицируя отвод тепла в деталь и инструмент. Этого можно достигнуть, охлаждая деталь, стружку, инструмент струей смазочно-охлаждающей жидкости. Так как в большинстве случаев скорость стружки превышает скорость распространения тепла в материале обрабатываемой детали, то, направляя струю жидкости на отделяющуюся от детали стружку, можно добиться понижения температуры только ее слоев, прилегающих к свободной поверхности. Температура резания при этом понижается незначительно.
Значительно большой эффект можно получить, если струя жидкости будет омывать инструмент и тем самым повышать теплообмен между инструментом и окружающей средой. Чем больше тепла перейдет в инструмент и окружающую среду, тем ниже будет температура резания. Поэтому насадок, через который смазочно-охлажда- ющая жидкость попадает в зону резания, должен быть расположен так, чтобы струя жидкости омывала не только деталь и стружку, но, главным образом, инструмент.
Применение инструментальных материалов, обладающих высокой теплопроводностью, также способствует понижению температу-
154
ры резания. С более низкой температурой резания работают инструменты, имеющие внутреннее охлаждение режущей части.
3.1.3. Основные экспериментальные методы изучения тепловых явлений
Несмотря на значительные успехи, достигнутые в использовании аналитических методов для изучения тепловых явлений в зоне деформации и на контактных поверхностях инструмента, экспериментальные методы благодаря их надежности и простоте являются главным инструментом исследования.
Экспериментальные методы можно разбить на две группы: косвенные и непосредственные.
Перечислим косвенные методы:
1.Метод цветов побежалости. Несмотря на свою простоту этот метод дает значительные погрешности, связанные с тем, что определяется только температура окисленной поверхности стружки.
Кпримеру, при резании с обильным охлаждением цвета побежалости исчезают, в то время как температура в месте контакта стружки с инструментом очень высока.
2.Метод термокрасок. Для выявления температуры пользуются свойством специальных красок менять цвет при определенных температурах. Например, при 155 °С цвет из пурпурного переходит
вголубой, при 190 °С из белого – в зелено-коричневый, при 255 °С из зеленого – в темно-коричневый, при 305 °С из желтого – в краснокоричневый, при 440 °С из фиолетового – в белый. При использовании этого метода краска смешивается с алкоголями и наносится ровным слоем на грани исследуемых резцов. Некоторая погрешность
вданном случае заключается в том, что оттенок переходящих красок меняется в зависимости от продолжительности действия тепла. Этот метод применяется для определения температуры на поверхностях инструмента. Специальную термочувствительную краску наносят тонким слоем на поверхность инструмента. Тепло на поверхностях инструмента изменяет цвет краски. Определенная шкала «цвет– температура» позволяет определить температуру поверхности инст-
155
румента. Недостаток метода: при продолжительной работе оттенки краски изменяются и не соответствуют шкале.
3.Метод микроструктурного анализа. Основан на изменени-
ях, которые происходят в поверхностных слоях инструмента вследствие воздействия на них тепла, возникающего в процессе резания. Оригинальный способ измерения температуры в процессе резания путем анализа микроструктуры тончайшего слоя обработанной поверхности, претерпевающей заметные изменения при достаточно большом нагреве, применил Б.И. Костецкий. Но и этот метод пока не получил распространения, так как его можно использовать только при высоких режимах резания, когда поверхность резания или обработанная поверхность нагревается выше критических точек.
4.Калориметрический метод (предложен А.М. Даниеляном).
Данным методом определяется распределение тепла между стружкой, инструментом и обрабатываемой деталью, а также средняя температура стружки и инструмента с использованием специального калориметра.
Непосредственные методы измерения температуры являются более точными, так как позволяют получить результаты, более близкие к действительным.
К непосредственным методам относятся следующие.
1.Метод искусственной термопары Я.Г. Усачева (1914). Не-
достаток метода в том, что нельзя близко подойти к передней или задней поверхности. А самый большой интерес представляет температура на контактных поверхностях.
2.Метод полуискусственной термопары Я.Г. Усачева (1914– 1916). Проволока термопары изолирована от резца и контактирует лишь в месте расклепки.
3.Метод естественной термопары. При этом необходимо:
–иметь в виду, что снятие термоэлектродвижущей силы (ТЭДС) с вращающейся заготовки происходит с использованием токосъемника;
–применять цельные резцы;
–проводить тщательную тарировку.
156
4.Метод двух резцов. Разнородные материалы резцов образуют термопару (но этот метод неудобен).
5.Оптический метод. Используется при скоростной обработке
сприменением пирометров.
6.Радиационный метод. Основан на измерении теплоты лучеиспускания, но имеет ряд недостатков и поэтому малоприменим.
7.Метод бегущей термопары (точен, но трудоемок). Этот метод позволяет одновременно измерять температуры на контактных площадках «резец–стружка» и «резец–деталь». Резец перерезает защитную трубку, и проводники термопары образуют горячие спаи
двух искусственных термопар. Контакты К1 – К2 выводят на соответствующие приборы.
Наиболее распространен в настоящее время метод естественной термопары; при этом для определения температуры строится тарировочный график на основе тарировки резец–деталь.
Определить температуру резания можно и аналитически при помощи теоретических формул, предложенных проф. А.Н. Резниковым, С.С. Силиным, П.И. Бобриком и другими исследователями. Однако эти формулы являются, как правило, приблизительными из-за ряда допущений.
Основными объектами изучения являются: а) количество выделяемого при резании тепла и его распределение между стружкой, деталью и инструментом; б) температура, устанавливающаяся на контактных поверхностях инструмента; в) температурные поля в зоне деформации и режущем клине инструмента.
Калориметрический метод. Метод позволяет определить количество тепла, переходящего в стружку, деталь и инструмент. На рис. 85 изображена схема постановки опыта при определении количества тепла Q, переходящего при точении в стружку и резец, и их
средних температур θ. Внизу, перед передней поверхностью резца, установлен калориметр 1 с сеткой 2 для сбора стружки и ртутным термометром 3. Для обеспечения лучшего попадания стружки в калориметр резание производят при левом вращении шпинделя. Если обозначить через θсм – температуру смеси (воды в калориметре
157

|
после резания), в град.; Gв – массу |
|
|
воды в калориметре, в г; θв – началь- |
|
|
ную температуру воды в калоримет- |
|
|
ре, в град.; G – массу стружки или |
|
|
резца, в г; с – теплоемкость стружки |
|
|
или резца, в кал, то среднюю темпе- |
|
|
ратуру стружки или резца можно оп- |
|
|
ределить по формуле |
|
|
θ = θсм + Gв(θсм – θв)/сG, |
|
. |
Количество тепла, перешедшего |
|
в стружку и резец, определяют по |
||
|
||
Рис. 85. Применение калоримет- |
формуле |
|
ра для определения количества |
Q = (cг – снθн)G, |
|
тепла, переходящего в стружку, |
где сг – теплоемкость горячей струж- |
|
и ее средней температуры |
ки или резца, в кал; |
|
|
сн – теплоемкость ненагретой стружки или резца, в кал; θн – начальная температура стружки или резца.
Метод термопар. Для измерения средней температуры на контактных поверхностях инструмента и в различных точках контактных площадок применяют разнообразные термопары. На рис. 86 изо-
|
бражен метод искусственной тер- |
|
мопары, предложенный Я.Г. Усаче- |
|
вым. Резец, применяемый в опытах, |
|
представляет собой корпус, к кото- |
|
рому прижата режущая пластинка 2 |
|
из быстрорежущей стали или твердо- |
|
го сплава. В корпусе сделано отвер- |
|
стие, в которое вставлена изоляци- |
|
онная трубка 3. Стандартная термо- |
|
пара 4 (медь-константан, хромель- |
Рис. 86. Измерение температуры |
алюмель и др.) с гальванометром 5, |
передней поверхности искусст- |
подключенным к ее концам, вставле- |
венной термопарой |
на в изоляционную трубку так, что ее |
|
158 |
спай касается нижней плоскости пластинки 2. Спай термопары регистрирует температуру опорной плоскости пластинки.
Большим достоинством метода является возможность использования стандартных термопар с известными термоэлектрическими характеристиками, а потому не нуждающихся в специальной тарировке. Располагая отверстия в различных точках передней и задней поверхностей, можно составить представление о температурном поле в режущем клине инструмента.
Однако методу присущи и серьезные недостатки, ограничивающие область его применения. Измеряемая термопарой температура ниже температуры на контактных поверхностях инструмента, и разность температур зависит от расстояния спая термопары от указанных поверхностей, увеличиваясь при увеличении толщины режущей пластинки.
Практически не удается достигнуть толщины пластинки менее 1,5…2,0 мм, а поэтому из-за большого градиента температур измеряемая температура на 50…80° ниже действительной. При долговременном резании вследствие износа передней и задней поверхностей инструмента расстояние между спаем термопары и контактными поверхностями сокращается, что приводит к непрерывному возрастанию температуры. Наконец, метод искусственной термопары трудно использовать при вращающемся инструменте.
Более простым и совершенным является метод естественной термопары, предложенный Е. Гербертом и К. Готвейном. Метод основан на том, что в процессе резания (рис. 87, а) в месте соприкосновения передней поверхности инструмента со стружкой и задней поверхности с поверхностью резания естественным путем создаются термопары, электродами которых являются материал обрабатываемой детали и материал режущей части инструмента. Величина электродвижущей силы и направление термотока зависят от рода инструментального и обрабатываемого материалов, образующих термопару.
159
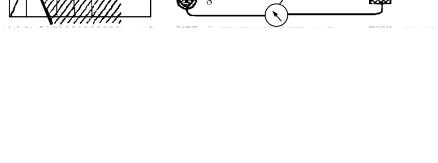
а |
б |
Рис. 87. Естественная термопара (а) и схема измерения температуры резания естественной термопарой (б)
Если обрабатываемую деталь и инструмент включить в замкнутую электрическую цепь, то величина термоэлектродвижущей силы, возникающей в термоэлементе, будет пропорциональна температуре скользящего «спая» образовавшейся термопары. Методом естественной термопары измеряют не максимальную, а некоторую среднюю контактную температуру на передней и задней поверхностях инструмента. Например, при обработке углеродистой стали инструмент является положительным электродом, если он изготовлен из быстрорежущей стали, и отрицательным, если он из твердого сплава.
Схема измерения температуры при точении методом естественной термопары изображена на рис. 87, б. Обрабатываемая заготовка 1 изолирована от патрона 3 и центра задней бабки эбонитовыми прокладками и пробкой 5. Цельный резец 2 из быстрорежущей стали или твердого сплава изолирован от резцедержателя эбонитовыми прокладками. Резец делают цельным для того, чтобы в месте приваривания или припаивания режущей пластинки к корпусу резца не образовались паразитные термопары. Заготовка медным проводником 10 соединена с гибким валом 6, закрепленным в эбонитовой втулке, установленной на конце шпинделя станка 4. Контактный наконечник 7 гибкого вала опущен в ванночку со ртутью 8. Милливольтметр 9 одной клеммой соединен с торцом резца, а вторым –
160