
714
.pdf
а б
Рис. 74. Тензорезисторы: а – с чувствительным проволочным элементом; б – с чувствительным фольговым элементом: b – база
которое передает деформацию чувствительному элементу. На объекте исследования основу закрепляют также посредством связующего.
|
Особенность тензорезистора состоит в том, что его чувствитель- |
|||
ный элемент |
(решетка), как правило, имеет механическую |
связь |
||
с |
объектом |
исследования по |
всей длине измерительной |
базы |
(а |
не только |
по концам базы). |
Чувствительность тензорезистора |
к деформациям характеризуется отношением изменения его сопротивления под действием деформации к величине относительной деформации. Широкое распространение тензорезисторов как универсального средства измерения деформаций объясняется возможностью: измерения деформаций при разных размерах базы, начиная с десятых долей миллиметра; дистанционных измерений в большом числе точек; измерений в широком диапазоне температур при самотермокомпенсации или автоматической схемной компенсации; измерений при самых различных внешних условиях (влажность, давление, ионизирующие излучения и др.), неблагоприятных для других измерительных средств; измерения многокомпонентных деформаций на локальных участках объекта исследования. Они также имеют незначительную массу, широкий частотный диапазон, включающий статические деформации и низкий порог реагирования, высокую надежность и сравнительно низкую стоимость.
131

Тензорезисторам свойственны и некоторые недостатки:
–невозможность индивидуальной градуировки;
–возможность только однократного использования (исключение составляют тензорезисторные преобразователи механических величин);
–относительно невысокая чувствительность и относительно низкий абсолютный уровень выходных сигналов.
Однако эти недостатки не помешали широкому использованию тензорезисторов как самого массового и универсального средства экспериментальных исследований в машиностроении.
По количеству измерения составляющих рассматриваются одно-, двух- и трехкомпонентные тензорезисторы.
Принцип действия трехкомпонентного тензорезисторного динамометра (рис. 75) для измерения сил резания состоит в следующем.
Составляющие силы резания Рх, Ру, Pz измеряются при помощи динамометра, устанавливаемого на суппорте токарного станка. Механическая часть динамометра представляет собой упругую систему, состоящую из державки 5, связанной с корпусом трубчатой формы 4,
вкотором расположены тензодатчики (схема расположения тензодатчиков представлена на рис. 76). Под действием вертикальной составляющей усилия резания Рz корпус 4 изгибается в вертикальной
Рис. 75. Динамометр для измерения трех составляющих силы резания: 1 – сменный модуль закрепления пластин; 2 – твердосплавная режущая пластина Т15К6; 3 – прижимная пластина; 4 – модуль расположения тензодатчиков; 5 – державка; 6 – разъем PLD-40
132
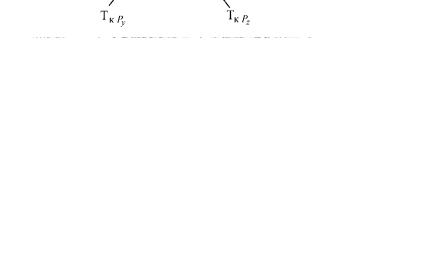
плоскости. Этот пропорциональный величине силы Pz прогиб корпуса регистрируется активным тензодатчиком ТаPz и компенсационными ТкPz, ТкPx (см. рис. 76). Под действием радиальной составляющей Pу корпус 4 сжимается, как балка, заделанная с двух концов (см. рис. 75), корпус перемещается параллельно своей оси на расстояние, пропорциональное величине Ру; это перемещение регистрируется активным ТаPy и компенсационным ТкPy тензодатчиками.
Рис. 76. Схема расположения тензодатчиков в корпусе динамометра (Та – активный тензодатчик; Тк – компенсационный тензодатчик)
Осевая составляющая Рх вызывает изгиб корпуса в горизонтальной плоскости. Прогиб корпуса в горизонтальной плоскости, пропорциональный силе Рх, регистрируется активным тензодатчиком ТаPx и компенсирующим тензодатчиком.
Электрическая схема динамометра (рис. 77) включает три независимых моста для замера сил Рх, Ру и Рz.
133

Рис. 77. Электрическая схема динамометра
Каждый из мостов имеет два плеча с индуктивными сопротивлениями, представляющими собой дроссели, намотанные на Ш-образные кольцевые сердечники, находящиеся в усилителе ТА-5. Один датчик активный (ТаPz, ТаPу, ТаPх); другой компенсационный (ТкPz, ТкPy, ТкPx). Компенсационные – вторые, симметричные активным датчикам (плечи моста), – используются для установки равновесного состояния моста, т.е. для установки прибора на нуль при настройке его перед замером.
Разомкнутые стороны магнитопроводов и дросселей-датчиков обращены к трубчатому корпусу в местах упругих перемещений.
134
Изменение деформаций изменяет индуктивное сопротивление дросселя и ведет к разбалансированию моста.
Сопротивления R4-R5, R6-R7, R8-R9 являются вторыми парами плеч мостов.
Сопротивления R10-R11-R12, R13-R14-R15, R16-R17-R18, включаемые последовательно в цепи гальванометров, служат для изменения
чувствительности динамометра при переключении диапазонов измерения.
Сопротивления R1-R2 и R3 служат для установления оптимальных режимов работы мостов.
Для устранения влияния колебаний напряжения сети на показания динамометра в цепь прибора включается феррорезонансный стабилизатор напряжения, дающий на выходе 16 В.
2.4.7.Вибрации и шум при обработке резанием
Впроцессе обработки могут возникать периодические колебания отдельных элементов системы станок–приспособление–инстру- мент–деталь большой частоты, называемые вибрациями. Вибрации вызывают повышенный износ и выкрашивание инструмента, ухуд-
шение качества |
обработанной поверхности, понижают точность |
и долговечность |
оборудования и приспособления; все это ведет |
к снижению производительности обработки.
Возникновение вибраций при обработке резанием характеризуется возмущающими силами и свойствами упругой системы; соотношение между этими параметрами определяет как возможность возникновения вибраций, так и их амплитуду и частоту.
Возмущающие силы в зависимости от физического существа механизма возбуждения вибраций могут создавать колебания различных видов и, прежде всего, вынужденные колебания и автоколебания.
Кроме того, при отдельных видах механической обработки существенное значение иногда приобретают другие виды колебаний, обусловленные изменением одного из параметров системы станок– приспособление–инструмент–деталь, например жесткости по време-
135
ни (параметрическое возбуждение колебаний), а также собственные затухающие колебания, возникающие при мгновенном приложении и снятии силы. Это происходит при врезании или выходе режущей кромки инструмента из обрабатываемого материала.
Вынужденные колебания возникают вследствие наличия в системе станок–приспособление–инструмент–деталь внешней периодической силы, вызывающей колебательный процесс с частотой, равной частоте действия возмущающей силы. Эти силы могут быть разделены на две группы:
1)переменные силы, обусловленные процессом резания, например силы, возникающие при снятии неравномерного припуска, прерывистом характере резания и т.д.;
2)переменные силы, возникающие в системе станок–приспо- собление–инструмент–деталь вне зоны резания. К ним относятся колебания, вызванные дефектами передач станка (перекос осей, погрешность зубчатых колес, люфты), дисбалансом его отдельных вращающихся частей – заготовок, приспособлений, инструментов,
атакже колебания, передаваемые на станок извне от других работающих машин.
Общим признаком вынужденных колебаний является отсутствие зависимости интенсивности действия возмущающей силы от процесса резания. Поэтому для гашения этих колебаний возможно использование наиболее простого и эффективного способа – ликвидации вызывающих их причин.
Наибольшие затруднения при обработке резанием вызывают самовозбуждающиеся колебания – автоколебания. Отличительной особенностью вибраций этого вида является отсутствие внешней периодической силы, возмущающей колебательный процесс. Частота вибраций при этом, как правило, не зависит от режимов резания, геометрии инструмента и равна собственной частоте системы.
Условиями возникновения автоколебаний при обработке резанием являются:
1)наличие в системе станок–приспособление–инструмент–де- таль физического явления, создающего механизм возбуждения коле-
136
баний (источник энергии, колебательная система и стабилизатор амплитуд);
2) определенные соотношения между возмущающими силами, создаваемыми механизмом возбуждения в процессе резания, и характеристиками самой системы (жесткость, сопротивление и масса). Оно должно быть таким, чтобы при некоторых деформациях системы работа сил возмущения превышала работу, расходуемую системой.
Установлено большое число физических явлений, создающих в системе станок–приспособление–инструмент–деталь механизм возбуждения колебаний и обуславливающих возникновение автоколебаний. В настоящее время большинство машиностроительных предприятий активно оснащаются высокопроизводительными станками с ЧПУ и обрабатывающими центрами с компьютерным управлением отечественного и зарубежного производства. В Пермском крае это: ОАО «Новомет», ОАО «Протон», ОАО «Пермский моторный завод», ОАО «Инкар», ОАО «Редуктор» и др. Стоимость новых станков достаточно велика – достигает 2–3 млн евро за станок. Значительно выросла (в десятки раз) и стоимость режущих сборных инструментов. Непредвиденный выход из строя этого оборудования и инструмента по различным причинам приводит к большим издержкам производства на машиностроительных заводах. Поэтому резко вырос уровень активности исследований в области контроля процессов механической обработки и инструмента в нашей стране и за рубежом. Диаграммы, изображенные на рис. 78, показывают, что основная деятельность разработчиков диагностических систем направлена на контроль износа инструмента или интенсивности его износа в любой текущий момент времени процесса обработки резанием.
Интенсивные исследования в области контроля станков и инструмента ведутся во всем мире: в США – НИСТ, национальная лаборатория Лоуренса в Ливерморе, Окриджская национальная лаборатория, Мичиганский университет, Иллинойский университет, университет шт. Мэриленд, фирмы «Монтроникс», «Ингерсолл миллинг машин» и TPS; в Канаде – Национальный исследовательский совет Канады, университет британской Колумбии, университет Виктории
137

Рис. 78. Использование различных диагностических признаков в анализе процессов, происходящих при механической обработке материалов резанием
|
– акустическая эмиссия; |
– силы резания; – виб- |
|
||
|
рации и помехи; – температура;
– другие признаки
и фирма «Мемекс электроникс». В Европе в области контроля станков и инструмента активные программы: в Германии – RWTH Aachen, университет Пассау, институт Фраунгофера, фирмы «Роберт Бош», «Прометек», исследовательский институт WZL и Ганноверский лазерный центр; в Испании – фирмы «Текникер», «Соралюче», «Икерлан», «Данобат», «Идеко»; во Франции – фирмы Giat и Objectif; в Греции – фирмы «Грау» и «Эпсилон»; в Италии – фирмы «Фидия» и ТХТ; в Великобритании – Лидский, Бирмингемский и Ноттингемский университеты; в Швейцарии – фирмы «Кистлер Инструменте» и «Гиндель Гирс»; в Венгрии – Венгерская академия наук. В Японии активные программы имеют следующие организации: университет Нагойи, университет Кобе, университет Кейо, исследовательский центр материалов фирмы «Мицубиси», компания «Хитачи сейки машин тул» и фирма NTN.
В США использование систем данного класса позволило (в среднем):
–на 30 % повысить производительность обработки;
–на 50 % увеличить срок службы станков (в первую очередь – элементов шпиндельной бабки);
–на 30 % увеличить износостойкость инструмента.
138
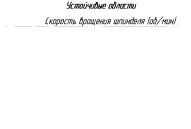
Вчастности, использование таких систем позволило при создании самолета F18 сэкономить 1 млрд долларов за 10 лет.
Компании, успешно применяющие вибродиагностические сис-
темы в своем производстве: Boeing, Ingersoll, Tool Company, Caterpillar, General Electric, Rolls Royce, Kovosvit A.S. и др.
ВРоссии исследования процесса резания проводятся практически во всех технических вузах страны и в отраслевых НИИ машиностроения. В наибольшей степени это Станкин, ВНИИТС, завод «Салют» г. Москвы. Однако для измерения сил резания, температуры резания, вибрации, мощности применяются различные методы, приборы, датчики часто без преобразования электрического сигнала
вцифровой, т.е. без использования персонального компьютера для анализа, записи и воспроизведения данных на современном уровне.
Особенности применяемых систем вибродиагностики
Назначение:
–измерение и анализ частотных характеристик системы станок– приспособление–инструмент–деталь и ее отдельных элементов;
–измерение и анализ сигнала виброакустической эмиссии в зоне резания;
–вычисление на основании собранной информации оптимальных виброустойчивых режимов обработки, (скорости шпинделя, глубины резания, подачи).
Диаграмма стабильности (рис. 79) – основа алгоритма выбора оптимальных режимов резания.
Диаграмма стабильности позволяет выявить зоны в пространстве параметров обработки (скорость шпинделя – глубина
резания), работа в которых обес- |
Рис. 79. Типичная диаграмма |
печит наибольшую производи- |
стабильности |
139 |
|

тельность, виброустойчивость процесса и, как следствие, требуемое качество обработки. Схемы измерений вибраций и шума при резании различных исследователей для выбора виброустойчивых режимов резания на станках с ЧПУ представлены на рис. 80 и 81.
Рис. 80. Схема получения частотных характеристик вибрации инструмента (установлен в шпиндель): 1 – шпиндель; 2 – фреза; 3 – акселерометр; 4 – импульсный молоточек; 5 – кабель к АЦП; 6 – ноутбук; 7 – питание
Рис. 81. Анализ сигнала виброакустической эмиссии (шума) в зоне резания: 1 – микрофон; 2 – виброакустический сигнал; 3 – зона резания; 4 – ноутбук; 5 – микрофонный вход звуковой платы
Очевидно, что эффективность диагностики в основном определяется информативностью используемых диагностических признаков, их зависимостью от условий обработки. Традиционно для диагностики процесса резания применялись его статические температур- но-силовые параметры, в большинстве случаев недостаточно инфор-
140