
714
.pdfное движение (профильное круглое врезное шлифование); VIII – три вращательных движения (зубофрезерование спирально-конических колес). Наибольшее распространение получили принципиальные кинематические схемы: с одним прямолинейным движением и с одним прямолинейным и одним вращательным движением.
В зависимости от соотношения угловых и линейных скоростей движений, сообщаемых инструменту и детали, возникают различные методы обработки.
1.2.Геометрия режущей части инструмента
1.2.1.Конструкция, части и поверхности токарного резца
Токарный резец представляет собой наиболее простой режущий инструмент в ряду других инструментов. Поэтому изучение конструкций режущих инструментов начинают с изучения его конструкции.
Токарный резец обычно имеет стержневую форму и состоит из двух частей: головки и тела резца. Головка резца является рабочей режущей частью резца. Она образуется в результате заточки на заточных станках и служит для срезания стружки с заготовки при точении. Тело резца (обычно прямоугольной формы в поперечном сечении) служит для установки и закрепления в резцедержателе токарного станка. Характерными размерами тела резца являются стандартизованные высота и ширина поперечного сечения.
Для того чтобы режущий инструмент мог осуществлять процесс резания, его режущая часть должна быть очерчена определенными поверхностями. Рассмотрим эти поверхности резца (рис. 2). Поверх-
ность 1 называют передней поверхностью. Это такая поверхность инструмента, по которой в процессе резания сходит стружка. По-
верхность 2 называют главной задней поверхностью. Это такая по-
верхность инструмента, которая обращена к заготовке в сторону подачи резца и примыкает к поверхности резания. Поверхность 3 назы-
вают вспомогательной задней поверхностью. Это такая поверхность инструмента, которая обращена к обработанной поверхности в про-
21
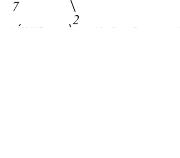
|
тивоположную от подачи резца |
||||||
|
сторону. Передняя и задняя по- |
||||||
|
верхности |
инструмента |
могут |
||||
|
быть |
вогнутыми, |
выпуклыми |
||||
|
поверхностями, |
плоскостями |
|||||
|
или их комбинациями. Пересе- |
||||||
|
чение передней и главной зад- |
||||||
|
ней |
поверхностей |
образует |
||||
|
главное лезвие 4, а пересечение |
||||||
|
передней |
и вспомогательной |
|||||
Рис. 2. Рабочая часть резца: 1 – перед- |
задней поверхностей – вспомо- |
||||||
няя поверхность; 2 – главная задняя |
гательное лезвие 5. |
|
|
|
|||
поверхность; 3 – вспомогательная зад- |
|
Между главным и вспомо- |
|||||
няя поверхность; 4 – главная режущая |
|
||||||
гательным лезвиями располага- |
|||||||
кромка; 5 – вспомогательная режущая |
|||||||
кромка; 6 – вершина резца; 7 – пере- |
ется переходное лезвие 6, кото- |
||||||
ходная поверхность |
рое |
образовано пересечением |
|||||
|
передней |
поверхности |
с |
пере- |
ходной задней поверхностью 7. Для простоты изготовления инструмента переходное лезвие очерчивают дугой окружности или прямой линией. У некоторых инструментов переходное лезвие отсутствует, и тогда главное и вспомогательное лезвия пересекаются в точке, называемой вершиной инструмента.
На переходном лезвии вершиной инструмента называют ту точку лезвия, которой инструмент при его установке на станке коснется обработанной поверхности. В зависимости от типа инструмента вспомогательных задних поверхностей на нем может быть больше чем одна (например, отрезной резец), а может и не быть совсем (например, осевая цилиндрическая фреза).
1.2.2. Геометрические параметры резца (углы заточки)
При используемых в технологии изготовления резцов приемах заточки и контроля поверхности и лезвия режущей части резца целесообразно ориентировать резец относительно прямоугольного трех-
22
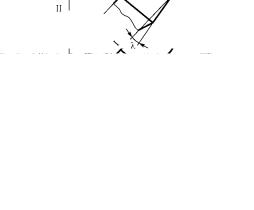
гранника, образованного тремя взаимно перпендикулярными плоскостями I, II, III (рис. 3). Плоскость I согласно ГОСТ 25762–83 – координатная плоскость, проведенную через рассматриваемую точку режущей кромки перпендикулярно направлению вектора скорости главного движения называют основной плоскостью. Плоскость II, перпендикулярную к ней, прилегающую к боковой установочной поверхности тела резца, называют боковой плоскостью. Плоскость III, рабочая, перпендикулярна первым двум плоскостям, параллельна продольной подаче резца и касательна к обработанной поверхности. Резец положен на основную плоскость, его боковая сторона совмещена с боковой плоскостью, а вершина касается рабочей плоскости III. Тем самым резец получил определенную ориентацию относительно трехгранника. Эта система координат называется статической. Кроме статической системы координат в теории резания рассматривают инструментальную и кинематическую системы координат. Плоскость IV – координатная плоскость, касательная к режущей кромке и перпендикулярная основной плоскости I в данной точ-
ке, называется плоскостью резания.
Статическая система координат (ССК) – прямоугольная сис-
тема координат с началом в рассматриваемой точке режущей кромки, ориентированная относительно направления главного движения V.
Рис. 3. Геометрические параметры резца
23
ССК применяется для приближенных расчетов углов резания в процессе резания и для учета изменения этих углов после установки на станок. Она является переходной от инструментальной системы координат к кинематической.
Кинематическая система координат (КСК) – прямоугольная система координат с началом в рассматриваемой точке режущей кромки, ориентированная относительно направления скорости результирующего движения резания Vе. Кинематическая система координат предусматривает изменение углов инструмента в момент резания с учетом всех движений формообразования.
Инструментальная система координат (ИСК) – прямоугольная система координат с началом в вершине лезвия, ориентированная относительно геометрических элементов режущего инструмента, принятых за базу. Предназначена для установки и контроля геометрических параметров режущих инструментов в процессе их изготовления. ИСК применяется для изготовления и контроля инструмента.
Для изображения положения передней и задней поверхностей резец рассекают плоскостью N–N, называемой главной секущей плоскостью. Главная секущая плоскость перпендикулярна проекции главного лезвия на основную плоскость. Положение передней поверхности в сечении N–N определяют передним углом γ. Передним углом резца называют угол между передней поверхностью или плоскостью, к ней касательной, и основной плоскостью. Передний угол характеризуют абсолютной величиной и знаком. Если передний угол располагается вне тела инструмента (сечение а), то условились считать его положительным, а если в теле инструмента (сечение б) – отрицательным.
Положение задней поверхности в сечении N–N определяют главным задним углом. Главным задним углом α резца называют угол между главной задней поверхностью или плоскостью, к ней касательной, и плоскостью резания IV, проходящей через главное лезвие перпендикулярно основной плоскости по касательной к поверхности резания. Задний угол по знаку должен быть только положительным. В противном случае лезвие резца при работе не коснется поверхности резания.
24

В сечении главной секущей плоскости принято обозначать еще два угла – угол резания и угол заострения, или угол клина. Углом резания δ называется угол между передней поверхностью и плоскостью резания. Углом заострения β называется угол между передней и задней поверхностями. Эти углы в главной секущей плоскости связаны следующими соотношениями:
α + β + γ = 90°, т.к. α + β = δ, то δ + γ = 90°.
Для изображения положения вспомогательной задней поверхности резец рассекают плоскостью N1–N1, перпендикулярной к проекции вспомогательного лезвия на опорную плоскость. Плоскость N1–N1
называют вспомогательной секущей плоскостью. Положение вспо-
могательной задней поверхности определяют вспомогательным зад-
ним углом. Вспомогательным задним углом α1 резца называют угол между вспомогательной задней поверхностью или плоскостью, к ней касательной, и плоскостью, проходящей через вспомогательное лезвие перпендикулярно основной плоскости. Положение главного лезвия относительно основной плоскости определяют углом, расположенным в плоскости резания, проходящей через главное лезвие перпендикулярно основной плоскости. Этот угол называют углом наклона главного лезвия λ (рис. 3 и 4). Угол λ есть угол между главным лезвием или касательной к нему и основной плоскостью М–М, проходящей через вершину резца. Так же, как и передний угол, угол λ должен характеризоваться не только абсолютной величиной, но и знаком. Если вершина резца является наинизшей точкой главного лезвия, то угол λ условились считать положительным, а если наивысшей – отрицательным. Угол λ, изображенный на рис. 3, имеет положительный знак.
Рис. 4. Угол наклона главной режущей кромки
25
Углы в плане. При рассмотрении геометрии токарного резца на виде сверху или в плане различают следующие углы резца (см. рис. 3): главный угол и вспомогательный углы в плане, угол между кромками и радиус при вершине резца. Положение главного лезвия определяют главным углом в плане ϕ. Главным углом в плане резца называют угол между проекцией главного лезвия на основную плоскость и плоскостью, перпендикулярной к основной и боковым плоскостям, совпадающей с направлением подачи резца. Положение вспомога-
тельного лезвия определяют вспомогательным углом в плане ϕ1.
Вспомогательным углом в плане резца ϕ1 называют угол между проекцией вспомогательного лезвия на основную плоскость и рабочей плоскостью, перпендикулярной к основной и боковой плоскостям в данной точке режущей кромки. Угол между главной и вспомогательной режущими кромками обозначают буквой ε. Радиус при вершине резца обозначают буквой R.
Любой режущий инструмент нужно рассматривать с двух точек зрения: как некоторое геометрическое тело определенной формы
иразмеров и как орудие труда, с помощью которого осуществляется определенный метод обработки. Соответственно этому и геометрические параметры инструмента целесообразно разделять на параметры инструмента как геометрического тела, нужные при изготовлении инструмента (так называемые статические углы, или углы заточки),
ипараметры инструмента в процессе резания, определяющие условия протекания процесса (так называемые рабочие углы, или углы движения).
Статические углы, или углы заточки инструмента, рассматриваемого как некоторое геометрическое тело, для сокращения будем называть просто геометрическими параметрами. Углы движения или рабочие углы инструмента, образующиеся в процессе резания, будем называть рабочими геометрическими параметрами. Как будет показано ниже, рабочие углы некоторых инструментов при определенных условиях обработки могут по величине очень сильно отличаться от углов заточки. Сообщив инструменту при его работе те или иные движения или изменив соотношение скоростей этих движений, мож-
26
но при неизменных углах заточки получить различные по величине рабочие углы.
При рассмотрении инструмента как геометрического тела отсчетные плоскости или поверхности, относительно которых фиксируются в пространстве положения его режущих поверхностей и лезвий, должны быть такими, чтобы обеспечить при существующих технологических средствах наибольшую простоту изготовления и контроля инструмента после его изготовления. Так как различные типы инструментов имеют различные конструктивные формы и технологию изготовления, то и отсчетные плоскости или поверхности тоже могут быть различными. Но если инструмент рассматривается в процессе резания, то в этом случае его режущие поверхности необходимо ориентировать относительно той поверхности, с которой срезается слой материала, т.е. от поверхности резания или образующих ее траекторий относительного рабочего движения инструмента.
1.2.3. Изменения углов заточки режущих инструментов при установке и в процессе резания
Процесс резания осуществляется перемещением режущего инструмента относительно поверхности обрабатываемой детали. В зависимости от положения плоскости резания в процессе обработки углы инструмента могут изменяться, что наблюдается, когда плоскость резания занимает иное положение, чем в статической системе координат. Кроме того, геометрические параметры режущей части инструментов, полученные после заточки, изменяются, или трансформируются, в результате изменения положения резца относительно основной плоскости; при установке вершины резца выше или ниже оси центра станка или детали; вследствие изнашивания рабочих поверхностей инструмента.
Предположим, что процесс резания осуществляется по схеме, указанной на рис. 5, где в качестве инструмента используется призматический брусок со статическими углами γ = 0°, α = 0°. На рис. 5, а отсутствует движение подачи, плоскость резания при обработке совпадает со статической, поэтому кинематические углы соответствуют
27

статическим. Инструмент имеет угол α = 0°, в результате чего увеличивается трение между задней и обрабатываемой поверхностями. Для уменьшения трения необходимо на инструменте создать положительный задний угол α.
а б
Рис. 5. Схема изменения статических углов резца в процессе резания: а – α = 0°; б – α ≠ 0°
В данном случае траекторией движения рассматриваемой точки лезвия является наклонная прямая ОB, параллельная вектору скорости резания Ve.
Теперь предположим, что инструменту сообщается одновременно два движения резания (см. рис. 5, б). Одно из движений (главное) совершается со скоростью V, второе (движение подачи) – со скоростью VS. Результирующей скоростью будет скорость Ve. Эта прямая – след плоскости резания в процессе обработки. Таким образом, плоскость резания занимает иное положение, чем в статике, так как след плоскости резания в статике – прямая ОА. Статический передний угол γ = 0°, кинематический передний угол γк приобретает положительное значение. Статический задний угол α = 0° (в процессе резания он имеет отрицательное значение). В этом случае осуществление процесса резания возможно лишь при условии смятия, пластического деформирования и выдавливания задней поверхностью слоя С материала обрабатываемой детали, препятствующего движению по направлению вектора Ve. Чтобы создать нормальные условия резания, необходимо обеспечить задний угол α больший, чем угол η:
28

tg η = VVS .
На рис. 6 упрощенно показана работа резца при продольном то-
чении с ϕ = 90° и λ = 0°.
а |
б |
в |
Рис. 6. Изменение углов резца в процессе работы: а – продольное точение; б – поперечное точение; в – развертка траектории точки режущей кромки резца
Режущая кромка резца установлена на уровне оси заготовки: B–В – положение плоскости резания при вращении заготовки и отсутствии подачи (точки режущей кромки описывают окружности, касательная к ним занимает вертикальное положение); А–А – положение плоскости резания, касательной к винтовой поверхности резания, при работе с включенной подачей; αк – кинематический задний угол; η – угол между направлениями скоростей результирующего движения резания и главного движения, называемый углом скорости резания.
Поверхность резания в кинематике будет ближе к задней поверхности резца. В результате изменения положения плоскости резания задний угол уменьшается: αк = α – η.
Если развернуть на плоскость окружность вращения и винтовую траекторию точки режущей кромки, мы получим треугольник, в котором катетами будут подача и окружность вращения, а гипотенузой – винтовая траектория, отсюда η = arctg(So/πD).
29
С увеличением подачи увеличивается наклон винтовой траектории точки режущей кромки (эти траектории образуют поверхность резания), а кинематический задний угол уменьшается. Разные точки режущей кромки находятся на различных диаметрах заготовки, а следовательно, наклон их винтовых траекторий будет различным. Чем меньше диаметр заготовки, тем значительнее уменьшается задний угол в процессе работы, так как наклон винтовой траектории больше.
Если резец имеет угол в плане ϕ = 90°, направление подачи и секущей плоскости, в которой измеряется угол α, совпадает. Если угол ϕ ≠ 90°, угол между положениями плоскости резания, измеренный в главной секущей плоскости, можно определить по формуле tg ηϕ = tg η · sin ϕ, кинематический задний угол в главной секущей
плоскости αк = α – ηϕ.
При поперечном точении, при отрезании детали точки режущей кромки описывают архимедову спираль, следовательно, касательная к поверхности резания и плоскость резания также будут отклоняться от касательной к окружности вращения и кинематический задний угол резца будет меньше.
Чем больше подача и меньше диаметр, на котором расположена точка режущей кромки, тем больше угол между положениями плоскости резания. Следовательно, кинематический задний угол при поперечном точении
αк = α – ηϕ,
где tg ηϕ = tg η · sin ϕ.
При обычно употребляемых при точении подачах угол η незначителен, и изменением заднего угла в процессе работы можно пренебречь. В процессе работы с большими подачами (при затыловочных работах, нарезании резьбы, обработке ходовых винтов) необходимо учитывать изменение заднего угла резца, угол его заточки должен быть больше на угол ηϕ.
Передний угол резца γ в этом случае увеличивается на угол ηϕ, так как основная плоскость изменяет свое положение (см. определение переднего угла). Угол заострения резца β остается постоянным.
30