
714
.pdfзуется суставчатая стружка, расчет угла сдвига, очевидно, нужно вести не по коэффициенту усадки стружки Kl, найденному измерением длины стружки, а по расчетному коэффициенту усадки:
Kl = Kl/Kξ.
То же самое нужно сказать и об определении относительного сдвига по формуле (2).
Коэффициент усадки стружки можно определить двумя методами: измерением длины стружки и взвешиванием стружки. При использовании первого метода длину стружки ограничивают разделением слоя на отдельные части. Например, в опытах при точении на заготовке делают один или несколько пазов и фиксируют расстояние между ними. При прохождении лезвия инструмента через паз процесс резания прерывается. Стружку собирают и измеряют ее длину по контактной стороне.
Коэффициент усадки стружки не может служить количественным показателем степени деформированности срезаемого слоя. Хотя с увеличением коэффициента усадки в пределах его значений, встречающихся при применяемых режимах резания, относительный сдвиг при постоянном переднем угле γ возрастает, но при различных передних углах одному и тому же коэффициенту усадки соответствует различная величина относительного сдвига. Если для оценки степени деформации срезаемого слоя пользоваться коэффициентом усадки стружки, то при Kl = 1 можно прийти к выводу, что деформация при резании отсутствует, хотя срезаемый слой и превратился в стружку. Это противоречит элементарным законам механики, согласно которым при Kl = 1 относительный сдвиг не равен нулю, имея тем большую величину, чем меньше передний угол инструмента. Таким образом, коэффициент усадки стружки может являться лишь внешним и только качественным показателем тех деформационных процессов, которые происходят в срезаемом слое.
На коэффициент усадки стружки основное влияние оказывают род и механические свойства материалов обрабатываемой детали, передний угол инструмента, толщина срезаемого слоя, скорость резания и применяемая смазочно-охлаждающая жидкость. При резании
91

пластичных материалов коэффициент усадки больше, чем при резании материалов хрупких (рис. 52). Например, Kl при резании углеродистых сталей колеблется в пределах 2…6, а при резании чугуна – в пределах 1,5…2,5. Чем прочнее и тверже материал обрабатываемой детали, тем меньше коэффициент усадки. Принципиальное влияние скорости резания на коэффициент усадки стружки представлено на рис. 52. Кривая 1 соответствует резанию материалов, не склонных к наростообразованию. В этом случае по
мере увеличения скорости резания коэффициент усадки стружки вначале быстро, а затем более медленно уменьшается. Указанное влияние скорости резания на Kl объясняется уменьшением коэффициента трения между стружкой и передней поверхностью при увеличении температуры на передней поверхности вследствие возрастания скорости резания. При резании материалов, склонных к наростообразованию (кривая 2), скорость резания на Kl влияет немонотонно. Вначале при увеличении скорости резания коэффициент усадки уменьшается, достигает минимальной величины при определенном значении скорости резания, а затем вновь возрастает. При достижении скоростью резания значения V3 возрастание коэффициента Kl прекращается, и при скоростях резания V > V3 кривая 2 ведет себя так же, как и кривая 1. Немонотонное изменение коэффициента Kl при увеличении скорости резания связано с действием на процесс стружкообразования нароста. Кривая 3 на рис. 52 показывает изменение высоты нароста в интервале скоростей резания от V1 до V2.
92

Возрастание скорости резания от V1 до V2 сопровождается увеличением переднего угла инструмента, вследствие чего степень деформации срезаемого слоя уменьшается. При скорости резания V2 фактический передний угол имеет максимальную величину и коэффициент Kl достигает минимума. При возрастании скорости резания от V2 до V3 высота нароста уменьшается так же, как и величина фактического переднего угла, стремящегося к величине переднего угла заточки. Это вызывает увеличение коэффициента усадки стружки. При скоростях резания V > V3 нарост отсутствует и скорость резания влияет на коэффициент Kl только через изменение коэффициента трения.
Влияние переднего угла на коэффициент Kl представлено на рис. 53. По мере увеличения угла γ коэффициент усадки стружки уменьшается, а горбы на кривых Kl = f(V) сглаживаются. Кроме того, чем больше величина переднего угла, тем при большем значении скорости резания кривая Kl достигает вторичного максимума. Последнее вполне естественно, так как при увеличении переднего угла исчезновение нароста происходит при больших скоростях резания. При углах γ > 30° скорость резания практически не влияет на коэффициент усадки стружки.
На рис. 54 представлено влияние на коэффициент усадки стружки толщины срезаемого слоя. Кривые Kl = f(V) имеют горбообразный вид, причем для меньших толщин срезаемого слоя вершины горбов сдвинуты в область более высоких скоростей резания. Из рисунка видно, что при постоянном переднем угле инструмента максималь-
93

Рис. 54. Влияние толщины срезаемого слоя на коэффициент усадки стружки KL при различных скоростях резания (сталь 20Х; γ = 0°; (ϕ = 45°; t = 1 мм): 1 – а = 0,31 мм; 2 – а = 0,15 мм; 3 – а = 0,08 мм;
4 – а = 0,04 мм
ные значения коэффициента усадки стружки не зависят от толщины срезаемого слоя, но Kl достигает максимальной величины при различных скоростях резания.
Смазочно-охлаждающие технологические средства снижают величину коэффициента трения, уменьшают коэффициент усадки стружки, причем эффект от влияния жидкости тем сильнее, чем меньше толщина срезаемого слоя и скорость резания.
Рис. 55. Влияние толщины среза а, главного угла в плане ϕ, угла резания δ и радиуса при вершине резца R на коэффициент продольной усадки стружки Kl
Влияние на усадку стружки толщины среза или подачи, углов в плане, угла резания и радиуса при вершине резца показано на рис. 55.
2.2.5.Методы завивания
идробления сливной стружки
Образование сливной стружки часто сопровождается нежелательными и опасными последствиями. Выход стружки в виде ленты из-под резца может привести к травме рабочего (порезу на теле или руках). Образование клубка запутанной сливной стружки на станке
94
с ЧПУ без вмешательства рабочего может привести к заклиниванию резца, заготовки, поломке режущего инструмента и приспособлений.
Впрактике обработки резанием применяют различные методы борьбы с этими явлениями.
1.Образование радиусных поверхностей на передней поверхно-
сти резца. В результате стружка завивается в виде спирали и под действием собственного веса опускается в корыто станка или обламывается на отдельные спиральные отрезки. Радиусные поверхности образуются в процессе изготовления при спекании неперетачиваемых пластинок или при заточке на заточных станках.
2.Установка стружколомов на передней поверхности резца.
Врезультате сливная стружка резко изгибается поверхностью стружколома и ломается на отдельные кусочки, которые ссыпаются в корыто станка.
3.Виброподача резца. На станке в резцедержателе устанавливается виброголовка, имеющая продольные, вдоль оси заготовки, колебания. В результате продольных колебаний резца в момент подачи сливная стружка имеет переменное поперечное сечение. В местах наименьшего сечения стружка ломается и в виде сегментов падает в корыто станка.
2.3.Контактные явления, трение
инаростообразование при резании материалов
2.3.1.Контактные явления и трение на передней
изадней поверхностях инструмента
Вобщем случае поверхность трения на передней поверхности шириной с (рис. 56 и 57) состоит из двух участков: участка I (пласти-
ческого контакта) шириной c1 и участка II (упругого контакта).
На участке I расположен заторможенный слой, в пределах которого стружка движется не по передней поверхности, а по заторможенному слою, и сопротивление, оказываемое движению стружки, определяется сопротивлением сдвигу в контактном слое стружки. На этом участке внешнее трение скольжения отсутствует и заменяется
95

Рис. 56. Два участка трения на пе- |
Рис. 57. Схема сил, действующих |
редней поверхности и эпюры распре- |
на передней поверхности инстру- |
деления нормальных и касательных |
мента |
напряжений, полученные с помощью |
|
разрезного резца |
|
«внутренним» трением между |
отдельными слоями стружки. |
На участке II стружка контактирует непосредственно c передней поверхностью. Здесь осуществляется внешнее трение скольжения, и сопротивление движению стружки определяется силой трения между стружкой и передней поверхностью. Ширина c1 пластического контакта зависит от переднего угла инструмента, толщины срезаемого слоя и коэффициента усадки стружки. Н.Г. Абуладзе предложил формулу определения ширины пластического контакта
с1 = a [KL(1 – tg γ) + sec γ],
из которой видно, что с1 растет при увеличении Kl и а и уменьшается при увеличении угла γ. Если инструмент имеет угол наклона лезвия, то при увеличении угла λ ширина пластического контакта уменьшается. Отношение не превышает 0,7 и для обычных конструкционных материалов чаще всего составляет 0,5.
96
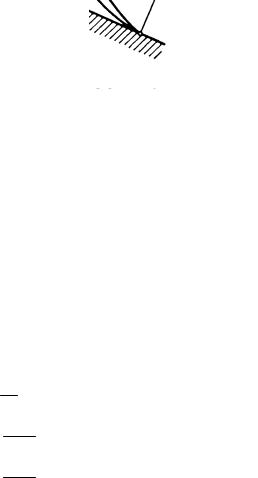
Эпюр касательных контактных напряжений τFп имеет экстремальный характер (рис. 56 и 58). На участке I вначале по мере удаления от лезвия напряжения τFп возрастают, достигают максимума, а затем начинают уменьшаться. На участке II касательные напряжения непрерывно уменьшаются до нуля.
Суммируя в пределах площадки контакта нормальные контактные напряжения, получим среднюю нормальную силу N, которую можно считать приложенной на расстоянии с/4 от лезвия инструмента. Суммируя контактные касательные напряжения, получим среднюю силу трения F (см. рис. 57).
При свободном резании с углом λ = 0 силы N и F можно определить, если будут известны действующие на срезаемый слой сила Рz′, совпадающая с вектором скорости резания, и сила Рx′, ей пер-
пендикулярная (см. рис. 57). Равнодействующая сил Р′z и Р′x является силой стружкообразования Р, наклоненной к направлению резания
под углом действия ω = arctg Рx′′ . На основании рис. 57 имеем
Рz
N = cosР′zωcos(ω+ γ) ,
F = cosРz′ωsin(ω+ γ) .
Средний коэффициент трения µ вычисляется на основании закона трения Амонтона:
F = µ/N tg(ω + γ).
Таким образом, угол трения ς на передней поверхности связан с передним углом γ инструмента и углом действия ω зависимостью
97
ς = ω + γ.
Из формулы следует, что при постоянном переднем угле инструмента угол действия увеличивается при росте среднего коэффициента трения (угла трения). Таким образом, интенсивность трения на передней поверхности через угол действия оказывает влияние на деформационные процессы, происходящие в срезаемом слое. На величину среднего коэффициента трения кроме механических и теплофизических свойств обрабатываемого и инструментального материалов основное влияние оказывают передний угол инструмента, толщина срезаемого слоя (подача), скорость резания, применяемая смазочноохлаждающая технологическая среда.
Величина среднего коэффициента трения для трущейся пары стружка–передняя поверхность определяется склонностью к адгезионному взаимодействию обрабатываемого и инструментального материалов. Образование интерметаллических связей между стружкой
иинструментом находится в прямой зависимости от способности контактирующих материалов образовывать между собой химические соединения и твердые растворы. Чем сильнее интерметаллические связи, возникшие в результате действия сил адгезии между стружкой
иинструментом, тем больше средний коэффициент трения. С повышением механических свойств обрабатываемого материала средний коэффициент трения уменьшается. Но так как при этом одновременно возрастают и средние нормальные, и средние касательные контактные напряжения, то при постоянной температуре средний коэффициент трения изменяется сравнительно мало. Например, при реза-
нии без смазочно-охлаждающей жидкости при γ = 20°, а = 0,15 мм и S = 0,2 м/мин средние коэффициенты трения для таких различных материалов, как медь, стали 10, 20Х, 1Х13, Х18Н9Т, колеблются в пределах 0,76…0,78.
Интенсивность адгезионного схватывания инструментального материала с обрабатываемым во многом определяется склонностью первого к образованию на нем под действием кислорода воздуха окисных пленок, препятствующих схватыванию. Для инструмен-
98

тальных материалов, склонных к образованию более прочных окисных пленок, средний коэффициент трения меньше. В связи с этим средний коэффициент трения для однокарбидных сплавов больше, чем для двухкарбидных, а для быстрорежущей стали больше, чем для однокарбидных сплавов. С увеличением в твердом сплаве содержания карбидов титана средний коэффициент трения уменьшается.
Если резание происходит с применением смазочно-охлаждаю- щей технологической среды, способной образовывать граничный смазочный слой между стружкой и передней поверхностью, то передний угол инструмента и толщина срезаемого слоя на средний коэффициент трения существенного влияния не оказывают.
Если смазочно-охлаждающая технологическая среда отсутствует, уменьшение переднего угла и увеличение толщины срезаемого слоя уменьшают средний коэффициент трения. Своеобразное действие, оказываемое в этом случае передним углом и толщиной срезаемого слоя на µ, связано с изменением среднего нормального контактного напряжения σN на передней поверхности. При увеличении σN средний коэффициент трения µ уменьшается. Поэтому все те факторы режима резания и геометрические параметры инструмента, которые увеличивают среднее нормальное контактное напряжение, снижают средний коэффициент трения, и наоборот.
Экспериментально проверенное влияние γ и а на µ при наличии или отсутствии смазочно-охлаждающей технологической среды можно объяснить следующим образом. Средний коэффициент трения можно выразить через средние нормальные и касательные контактные напряжения σN и τF на площадке контакта с·b:
µ= F = τF сb = τF .
N σN сb σN
Если резание производится с жидкостью, создающей смазочный слой, препятствующий образованию интерметаллических соединений, и заторможенный слои на передней поверхности отсутствует, то вся площадка контакта состоит из одного участка II упругого контак-
99
та стружки с передней поверхностью. В этом случае трение между стружкой и передней поверхностью является внешним кинетическим, трением, подчиняющимся закону трения Амонтона. При внешнем трении средние касательные напряжения пропорциональны нормальным напряжениям τF = KσN, а поэтому средний коэффициент трения не зависит от σN, являясь константой для трущейся пары. Поэтому средний коэффициент трения почти не зависит ни от переднего угла, ни от толщины срезаемого слоя. Если образовавшийся заторможенный слой охватывает всю ширину площадки контакта, то внешнего трения нет и средний коэффициент трения будет характеризовать процессы пластической деформации, происходящие в контактном слое стружки. Сопротивление движению стружки в этом случае будет определяться величиной касательных напряжений в заторможенном слое, равной или пропорциональной пределу текучести материала стружки на сдвиг. Из рис. 56 видно, что на участке пластического контакта касательные напряжения по величине изменяются сравнительно мало, и в первом приближении их можно считать постоянными. Тогда, принимая τF = const, получим выражение для определения среднего коэффициента трения при наличии заторможенного слоя в виде µ = сonst/σN.
Из выражения следует, что возрастание средних нормальных контактных напряжений уменьшает средний коэффициент трения. Как отмечалось выше, при резании в большинстве случаев имеет место смешанный контакт: упругий и пластический. Поэтому влияние σN на µ должно быть менее сильным, чем при полном отсутствии упругого контакта. Но и в этом случае установленная закономерность между µ и σN сохраняется. Влияние скорости резания на средний коэффициент трения cказывается следующим образом. По мере увеличения скорости резания средний коэффициент трения изменяется подобно коэффициенту усадки стружки: вначале уменьшается, затем возрастает и, достигнув при некотором значении скорости резания максимума, опять уменьшается. Так же как и Kl, максимальная величина µ почти не зависит от толщины срезаемого слоя (подачи), но получает это значение при различных скоростях резания, тем боль-
100