
714
.pdf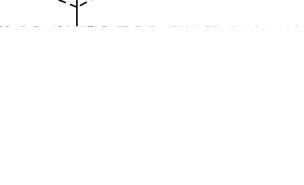
Длина врезания зависит от геометрии инструмента и его конструктивных особенностей: при точении l1 = t · ctg ϕ + (0,5...2) мм; при сверлении l1 = (D/2 · tg ϕ) + (0,5…2) мм; при фрезеровании цилиндрической фрезой l1 = [t(D – t)]1/2 + (0,5...2) мм; при симметричном фрезеровании торцовой фрезой l1 = 0,5[D – (D2 – B2)1/2] + (0,5...2) мм.
Значение 0,5...2 мм принимается для обеспечения свободного подхода инструмента к обрабатываемой поверхности.
Перебег при работе на проход составляет 1...5 мм в зависимости от размеров обработки. При работе в упор он равен нулю.
Формулы для расчета to применительно к различным процессам обработки приводятся в справочной литературе.
Во время обработки режущий клин инструмента срезает с поверхности резания слой материала определенных размеров и формы. На рис. 24 показан простейший случай обработки, когда инструмент с прямолинейным главным лезвием перемещается по плоской поверхности резания, срезая с нее слой размерами a и b. Толщиной а срезаемого слоя называют размер слоя (удаляемого с поверхности резания), измеренный по нормали между соседними положениями поверхности.
Рис. 24. Срезание слоя при свободном резании: 1 – поверхность резания, полученная после предыдущего прохода инструмента; 2 – поверхность резания, по которой лезвие инструмента перемещается при последующем проходе резания; 3 – стружка
51

Шириной срезаемого слоя b называют размер слоя, удаляемого с поверхности резания, измеренный в направлении, нормальном к толщине слоя. Ширину b и толщину а принято называть физическими размерами срезаемого слоя.
Лезвие соприкасается с поверхностью резания на длине l. Этот размер называют рабочей длиной лезвия. В том случае, когда вектор V скорости резания неперпендикулярен лезвию инструмента, рабочая длина l лезвия больше ширины b срезаемого слоя. Если же вектор V перпендикулярен лезвию (угол λ = 0°), то рабочая длина лезвия равна ширине срезаемого слоя.
В результате перемещения инструмента срезаемый с поверхности резания слой превращается в стружку 3 (см. рис. 24). Если вектор V перпендикулярен лезвию, то толщина и ширина срезаемого слоя определяют толщину ac и ширину bc стружки, а также ширину и длину контактных площадок соприкосновения стружки и поверхности резания с передней и задней поверхностями инструмента. Если вектор V неперпендикулярен лезвию, то только толщина срезаемого слоя определяет толщину стружки, ширина же стружки определяется не шириной срезаемого слоя, а рабочей длиной лезвия.
Контрольные вопросы и задания
1.Дайте определение кинематическим элементам и характеристики резания при точении.
2.Что называется поверхностью резания, обрабатываемой и обработанной поверхностями?
3.Покажите на конкретном примере конструкцию и части токарного резца.
4.Дайте определение статической, инструментальной и кинематической системам координат.
5.Покажите схематично координатные плоскости в статической системе координат.
6.Как установка резца влияет на величины переднего, заднего углов и углов в основной плоскости?
52
7.Дайте определение элементам режима резания при точении, сверлении, фрезеровании: скорости резания, подаче, глубине резания, ширине фрезерования.
8.Дайте определение элементам и характеристики срезаемого слоя при точении, сверлении, фрезеровании; сечению, его формам
иразмерам. Что такое остаточное сечение при указанных видах обработки?
9.Каковы особенности классификации резания по признакам: свободное и несвободное, прямоугольное и косоугольное, однолезвийное и многолезвийное, непрерывное и прерывистое?
Глава 2 ДИНАМИКА ПРОЦЕССА РЕЗАНИЯ
2.1.Деформация и напряжения в процессе резания
2.1.1.Физическая сущность процесса резания
Врезультате экспериментальных и теоретических исследований установлено, что превращение срезаемого слоя в стружку при резании является одной из разновидностей процесса пластической деформации материала. Основным признаком пластической деформации является необратимое изменение формы тела под действием внешних сил без нарушения сплошности деформируемого тела.
Некоторые сведения о пластической деформации металла
Различают три основных вида деформированного состояния малого объема тела.
1. Растяжение (рис. 25, а), при котором вдоль одной из трех главных осей деформации наблюдается удлинение, а вдоль двух остальных главных осей – укорочение. Если две отрицательные деформации укорочения равны между собой, то растяжение называют простым.
53

2.Сжатие – такая деформация, при которой вдоль одной оси происходит укорочение, а вдоль двух других осей – уширение/удлинение.
3.Сдвиг (рис. 25, б), при котором деформация вдоль одной из трех главных осей отсутствует, вдоль второй главной оси наблюдается укорочение, а вдоль третьей главной оси – равное ему удлинение.
а
б
Рис. 25. Схемы деформации чистого (а) и простого (б) сдвигов
Разновидностями сдвига являются чистый сдвиг и простой сдвиг. При чистом сдвиге (см. рис. 25, а) происходит равномерное укорочение вдоль одной оси и равномерное удлинение вдоль другой оси, перпендикулярной к первой. Квадрат ABCD превращается в конгруэнтный ромб А1В1С1D1 при неизменном объеме тела. При простом сдвиге (см. рис. 25, б) деформация заключается в смещении всех точек тела в направлении, параллельном только одной оси, на расстояние, пропорциональное расстоянию точки тела от этой оси в направлении второй оси. В результате простого сдвига квадрат ABCD превращается в равновеликий параллелограмм с теми же размерами основания и высоты, что и у исходного квадрата.
54

Первые два вида (растяжение и сжатие) относятся к объемному деформированному состоянию, а третий (сдвиг) – к плоскому деформированному состоянию.
Рассмотрим более подробно деформацию простого сдвига на примере перехода срезаемого слоя в стружку при металлообработке, так как при b > > а практически все перемещения срезаемого слоя происходят в одной плоскости.
Рис. 26. Напряженные состояния в начальный и конечный моменты деформации простого сдвига
Частица срезаемого слоя, находящаяся далеко от режущего инструмента, свободна от напряжений и движется по направлению к инструменту с постоянной скоростью. По мере приближения к режущему инструменту напряжения в рассматриваемой частице возрастают, и, когда они превзойдут предел упругости обрабатываемого материала, частица получает пластическое смещение и изменяет направление своего движения (рис. 26). Эти изменения происходят за время пребывания частицы в некоторой переходной пластически деформированной зоне ABCD (рис. 27, а). Поскольку в результате отделения слоя металла толщиной а и превращения его в стружку часть единого тела движется параллельно передней поверхности лезвия инструмента, а оставшаяся часть продолжает движение в прежнем направлении, то в точке, соответствующей сопряжению передней и задней поверхностей инструмента, под углом β к направлению движения, называемого углом сдвига, произойдет разделение тела на стружку и обрабатываемую деталь.
55

Представим переходную пластически деформируемую зону
ввиде параллелограмма ABCD (см. рис. 27, а), а линии скольжения
вней примем за прямые. Обозначим толщину этой зоны через ∆х, а ее сдвиг через ∆s. Значение ∆s соответствует расстоянию (см. рис. 25, б), на которое сдвинулась верхняя сторона квадрата относительно нижней, и называется абсолютным сдвигом. В теории пластических деформаций для характеристики интенсивности сдвига пользуются величиной е, называемой относительным сдвигом. Он
равен отношению абсолютного сдвига ∆s к толщине слоя AJC, претерпевшего этот сдвиг, т.е. е = ∆s/∆x. Геометрически е равен тангенсу угла β наклона стороны квадрата к оси z, т.е. е = tg β (рис. 27, б).
а
б
Рис. 27. Схема определения относительного сдвига
Элемент срезаемого слоя ABCD под действием режущего клина инструмента деформируется и принимает форму параллелограмма EBCN. В треугольнике CDN (см. рис. 27, б)
56

МС = ∆х; |
СМD = 90°; KNC = γ; NDC =β; |
|
||||
|
ND = ∆s; |
FKC =β; NCK = θ; |
|
|||
ε = |
∆s |
= |
ND = |
MD + |
MN = ctgβ+ tg(β− γ). |
(1) |
|
||||||
|
∆x |
MC |
MC |
MC |
|
Анализ формулы показывает, что для определения относительного сдвига при определенном угле γ необходимо знать угол сдвига. Его можно определить по длине стружки. При перемещении инструмента на ∆l длина стружки будет ∆lc. Из ∆АВЕ (см. рис. 27, а)
∆lc |
= |
∆l |
= |
∆l |
и |
∆l |
= |
cos(β− γ) |
. |
|
sin β |
sin δ |
cos(β− γ) |
|
∆lc |
sin β |
Отношение ∆l/∆lc = Kl получило название коэффициента усадки, или укорочения стружки:
Kl = cos(β− γ). sin β
Данную формулу называют формулой И.А. Тиме. С ее помощью можно выразить угол сдвига через коэффициент Kl:
Kl = cosβcossinγ +βsin βsin γ = ctgβ+sin γ,
отсюда tg β = |
cos γ |
. |
|
Kl −sin γ |
|||
|
|
Несмотря на принятые допущения о замене зоны первичной деформации единственной плоскостью сдвига и идеализации процесса превращения срезаемого слоя в стружку, формула И.А. Тиме совершенно точно выражает связь между Kl и углом сдвига β, так как отражает условие сплошности материала стружки.
Таким образом, относительный сдвиг при резании зависит от угла сдвига β и переднего угла γ. Угол β можно определить, зная а и ас, а γ всегда известен. Практически ε = 2...5. Определим, при каком
57

β относительный сдвиг будет минимальным. Для этого возьмем первую производную уравнения (1), приравняем ее к нулю и решим уравнение относительно β:
ddβε = −cosec2 β+sec2 (β− γ)= 0.
Это условие справедливо при β = 90° – (β – γ). Тогда
[β]ε→min = 45° + 2γ .
Зная относительный сдвиг, можно определить скорость деформации (с–1), которая представляет собой отношение максимальной главной деформации εmax к ее продолжительности τдеф в единицу вре-
мени, т.е. Vдеф = εmax/τдеф.
В случае неравномерной деформации сдвига ее скорость, или
скорость относительного сдвига, определяется как относительный сдвиг в единицу времени Vдеф = dε/dτ.
От Vдеф зависит температура, сопровождающая процесс деформации: чем выше скорость деформации, тем меньше требуется энергии и меньше тепловыделение.
Пластические деформации материала срезаемого слоя при резании ограничиваются зоной стружкообразования. Наиболее интенсивно пластическая деформация протекает в очень узкой зоне, ширину которой для упрощения расчетов примем за прямоугольник толщиной ∆х. Время деформации обрабатываемого металла на этом
участке составит τдеф = ∆х/Vc = (∆хKl)/V, т.е. Vдеф = εV/∆хKl. Скорость деформации при резании очень высока, и даже самые
низкие скорости резания значительно превосходят скорости, достигаемые при испытаниях металлических образцов на удар. По экспериментальным данным, при обработке конструкционных материа-
лов обычного качества ∆х = 0,02...0,005 см; ε = 2...5; Kl = 2…4. При
скорости резания 60 м/мин = 100 см/с скорость деформации Vдеф ~ ~ 4000 с–1.
58

Высокие скорости деформации не позволяют установить четкую границу между хрупкими и пластичными материалами, поскольку один и тот же материал в зависимости от характера напряженного состояния при резании и скорости деформации может вести себя и как хрупкий, и как пластичный. Так, например, при точении чугуна стружка может быть сливной, при обработке вязких сталей – элементной.
2.1.2. Методы изучения и оценки пластической деформации
Существуют следующие методы исследования деформации
всрезаемом слое.
1.Визуальное наблюдение отполированной боковой поверхности обрабатываемого образца: изучение микрошлифов зоны резания (корни стружки); по светлым пятнам и границам потускнения части металла можно судить о характере пластической деформации при резании. Например, с увеличением скорости резания при протягивании сплава ЭИ437БУ-ВД размер зоны деформации протянутых образцов
уменьшается, а угол сдвига βх увеличивается, что свидетельствует
оснижении деформации (рис. 28).
ав
бг
Рис. 28. Микрошлифы корней стружек сплава ЭИ437БУ-ВД: а – 2 м/мин;
б – 0,13 м/с; в – 0,43 м/с; г – 0,67 м/с (Sz = 0,1 мм/зуб; шлифы не травлены)
59
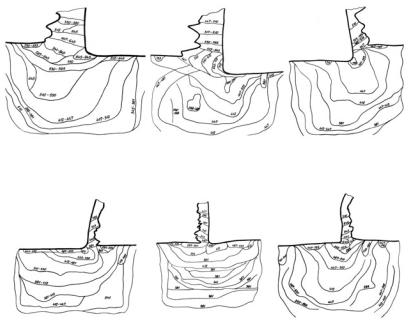
2. Метод измерения микротвердости и расчет напряжений в зоне резания. На полированной поверхности зоны резания и стружки наносят уколы алмазной иглой с помощью прибора микротвердомера ПМТ-3 с определенной нагрузкой. По глубине и ширине следа алмазной призмы вычисляют микротвердость в каждой точке. Затем переносят картину на бумагу, соединяют точки с одинаковой микротвердостью и рисуют схему пластической деформации в зоне резания. Например, на рис. 29 представлены результаты измерения микротвердости в зоне резания образцов из сплава ЭИ787-ВД, протянутых
V = 8 м/мин |
V = 26 м/мин |
V = 40 м/мин |
а
V = 8 м/мин |
V = 26 м/мин |
V = 40 м/мин |
б
Рис. 29. Распределение микротвердости в поверхностном слое образцов и корнях стружек из сплава ЭИ787-ВД (ХН35ВТЮ-ВД, НВ 388…412) после протягивания на различных скоростях резания с подачей 0,06 мм/зуб (а)
и 0,02 мм/зуб (б) протяжками из твердого сплава ВК8
60