
714
.pdfВ 1896 году вышла книга профессора Михайловской артиллерийской академии А.А. Брикса (1865–1900) «Резание металлов»,
вкоторой анализируются предшествующие исследования стружкообразования, делается попытка обобщить их и систематизировать идеи предшественников. А.А. Брикс ввел более точные формулировки понятий и явлений процесса резания, терминологии режущего инструмента.
Профессор Я.Г. Усачев (1873–1941) в 1912–1915 годах в книге «Явления, происходящие при резании металлов» представил результаты выдающихся исследований в области резания, опередившие аналогичные результаты ученых из Германии и США на 30–50 лет. Впервые для изучения процесса стружкообразования Я.Г. Усачев применил металлографический метод вместо ранее применявшегося визуального метода. Это позволило разработать весьма достоверную теорию наростообразования. Особенно ценными являются работы
вобласти теплообразования. Новый калометрический метод и использование искусственных термопар позволили экспериментально установить влияние режимов резания на величину температуры резания. Впервые появилась возможность управления процессом стружкообразования, силами резания, шероховатостью поверхности деталей машин. Эти результаты сегодня подтверждаются с помощью компьютерного моделирования тепловых процессов различными учеными у нас в стране и за рубежом.
Вэтот же период проводились многочисленные стойкостные эксперименты под руководством американского исследователя Ф.У. Тейлора. В 1906 году вышла его книга «Искусство обработки металлов», представляющая собой статистический набор данных по стойкости режущих инструментов для различных обрабатываемых материалов. В книге отрицалось теоретическое изучение процесса резания, а пропагандировалось лишь искусство мастера, создание банка данных, справочников и каталогов без объяснения физической природы явлений при резании. Сегодня это опытно-статистическое направление широко распространено за рубежом. Технологу выдается каталог с режимами резания, а дальше он должен заниматься до-
11
водкой режимов самостоятельно. Если возникают проблемы, то технологу нужно обращаться за отдельную плату на фирму, производящую станок или инструмент и выпускающую соответствующие каталоги. Несмотря на относительное удобство пользования каталогами, они не могут учесть все многообразие условий обработки, не могут учесть появление десятков новых обрабатываемых и инструментальных материалов, выбрать наиболее оптимальные режимы резания. Этих недостатков тейлоровской теории были лишены разработки наших ученых. Усилиями И.А. Тиме, К.А. Зворыкина и Я.Г. Усачева была создана отечественная школа резания материалов, намного обогнавшая зарубежные исследования в этой области.
Бурное развитие машиностроения в России в 20–30-х годах привело к созданию и открытию в России новых лабораторий резания на заводах, в отраслевых НИИ и в учебных заведениях. В 1936 году при техническом совете Наркомтяжпрома была создана комиссия по резанию металлов под председательством Е.П. Надеинской. Эта комиссия привлекла к научно-исследовательской работе лаборатории резания более 30 вузов, НИИ и заводов. За пять лет работы было выполнено более 300 исследований силовых и стойкостных зависимостей по единой методике. Это позволило значительно усовершенствовать существующие нормативы и почти на порядок увеличить производительность механообработки в годы Великой Отечественной войны.
Такого размаха исследовательской работы в области резания металлов не имела ни одна страна в мире. Накопленный фактический материал одновременно явился источником для дальнейших теоретических обобщений. В результате появился ряд работ большого научного значения, а их авторы заложили основы современной науки резания материалов: И.И. Семенченко (металлорежущий инструмент); А.И. Каширин (вибрации при резании); Г.И. Грановский (кинематика резания); Т.Н. Лоладзе (износ инструмента); В.А. Кривоухов, А.И. Исаев (качество поверхностного слоя); Н.Н. Зорев, М.И. Клушин (механика процессов резания); А.М. Даниелян, А.Н. Резников, А.Д. Макаров, С.С. Силин (теплофизика резания); А.А. Маталин, А.М. Сулима, В.Ф. Безъязычный, А.Г. Суслов (влия-
12
ние качества обработки на эксплуатационные свойства изделий) и др. Таким образом, трудами российских ученых создана современная передовая отечественная школа резания металлов, получившая мировое признание. Ее характеризует глубокое проникновение в суть физических явлений и использование установленных закономерностей на практике.
Сегодня исследования процесса резания продолжаются в связи
споявлением новых обрабатываемых материалов и новых изделий, широким применением вычислительной техники, созданием нового оборудования с ЧПУ, возможностью виртуального моделирования процесса резания, создания диагностических систем слежения за процессом резания, резким увеличением скоростей резания, применения новых конструкций режущих инструментов, инструментальных материалов с новыми видами покрытий и т.д. Дальнейшее развитие фундаментальных основ науки о резании материалов связано
сшироким применением ЭВМ и микропроцессорной техники и автоматизацией промышленного производства.
Автор данного учебного пособия по дисциплине «Резание материалов» считает необходимым дать студентам технических вузов современные профессиональные знания о физической сущности и основных теоретических закономерностях и технических особенностях процесса обработки материалов резанием, чтобы затем успешно решать любые проблемы на производстве.
Эти знания необходимы будущему специалисту – технологу, мастеру, конструктору машиностроительного предприятия – для технически грамотного назначения режимов резания, геометрии инструмента, связывающе-охлаждающих технологических средств (СОТС)
сцелью обеспечения высокой производительности труда, выполнения требований по точности и качеству изготовления деталей, снижения затрат и себестоимости при выполнении различных технологических операций механической обработки.
Вучебном пособии представлен как классический теоретический материал, основанный на разработках основоположников теории резания материалов, так и теоретические и практические мате-
13
риалы современных авторов, в том числе и материалы исследований автора.
К задачам изучения дисциплины «Резание материалов» относятся понимание и освоение основных закономерностей теории резания, физических явлений, происходящих в процессе резания – кинематики, динамики, теплофизики процесса резания, изнашивания и стойкости режущих инструментов, формирования качества поверхностного слоя. В учебном пособии предоставлена возможность понять особенности влияния технологических условий обработки материалов на формирование качества поверхностного слоя и эксплуатационные характеристики обрабатываемых деталей машин; понять сущность оптимизации и управления процессом резания; научиться выбирать рациональные режимы резания и режущий инструмент; получить знания о современных методах проектирования и применения процессов резания, об эффективном использовании природных ресурсов, материалов и энергии, о разработке и использовании методических, справочных и нормативных материалов, технической документации.
Предметом изучения дисциплины являются следующие объекты: конструктивные элементы режущих инструментов, инструментальные материалы, кинематика и динамика процесса резания, стружкообразование и тепловые явления при резании, износ и стойкость режущих инструментов, моделирование и оптимизация процессов резания, назначение рациональных режимов резания, качество поверхностного слоя обрабатываемых деталей, современные направления развития теории и практики процесса резания.
Дисциплина «Резание материалов» относится к циклу специальных дисциплин и федеральному компоненту рабочего учебного плана. Она взаимосвязана с такими специальными дисциплинами, как «Проектирование металлорежущего инструмента», «Металорежущие станки», «Технология машиностроения», «Проектирование приспособлений», «Автоматизация производственных процессов» и др.
14
Врезультате изучения дисциплины студент должен:
–иметь представление о сущности процесса резания, о закономерностях и взаимосвязях физических явлений, происходящих в зоне резания;
–знать общие закономерности превращения срезаемого слоя
встружку, физические основы износа и прочности режущего инструмента, сущность силового воздействия на процесс резания; тепловые явления на контактных поверхностях режущей части инструмента и заготовки; основы выбора оптимальных параметров режима резания и их влияние на производительность обработки, обрабатываемость материалов, качество обработанной поверхности, точность размеров обрабатываемой поверхности деталей;
–уметь назначать рациональные режимы резания различными способами, выбирать инструментальные материалы и геометрию режущего инструмента, определять силу и мощность резания, пользоваться нормативными справочниками, стандартами и инструкциями, выбирать СОТС для конкретных условий обработки резанием;
–уметь выполнять необходимые измерения геометрии режущего инструмента, проводить контроль геометрии обработанных деталей, измерения и расчеты силы резания, мощности и температуры резания;
–владеть методами автоматизированного контроля и управления процессом резания;
–иметь навыки анализа и устранения причин сбоев в технологическом процессе, организации и проведения необходимых мероприятий по отладке технологии изготовления и внедрению новых технологических процессов.
Вучебном пособии в отличие от других изданий приведены результаты исследования автором механических свойств обрабатываемых материалов в широком температурном диапазоне с определением температурных зон провала пластичности, результаты исследования влияния адгезионных явлений при резании на формирование физико-химических свойств поверхностного слоя деталей, приведены результаты исследования износа инструмента и процесса струж-
15
кообразования с привлечением электронной микроскопии, микрорентгеноспектрального химического анализа, скоростной киносъемки и т.д. Показана возможность применения статистических методов обработки результатов исследований, применения математического планирования экспериментов, использования методов математического моделирования процессов резания с использованием ПЭВМ.
Особенностью данного учебного пособия является и то, что в нем приведены основные результаты теоретических и экспериментальных исследований процесса резания, выполненные под руководством автора в ОАО «Пермский моторный завод» за последние 35 лет при производстве деталей и узлов современных авиационных двигателей. Автор выражает искреннюю признательность руководству завода, инженерам и сотрудникам лабораторий резания и шлифования экспериментально-технологического цеха за помощь в организации, постановке экспериментов и внедрение полученных результатов в производство.
Глава 1 КИНЕМАТИКА ПРОЦЕССА РЕЗАНИЯ
1.1.Основы кинематики резания
1.1.1.Виды движений при резании материалов
Кинематика резания (в отличие от кинематики станков) рассматривает движения, необходимые для срезания стружки с заготовки, то есть только главные движения в момент резания от начала контакта лезвия инструмента до прекращения этого контакта. Для того чтобы инструмент мог удалить с детали припуск, оставленный на обработку, инструменту и детали сообщают движения с определенными направлениями и скоростями. Одно из главных движений, сообщаемых инструменту или детали, называют движением резания,
а другое – движением подачи. Движение резания – такое движение,
которое необходимо для осуществления процесса превращения сре-
16
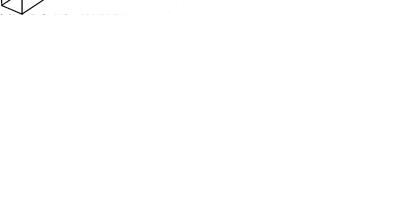
заемого слоя в стружку в данном сечении, точке или поверхности заготовки. Движение подачи – такое движение, при котором стружка срезается по всей длине заготовки. Для снятия всего припуска часто необходимо, чтобы указанный процесс совершался непрерывно или повторялся периодически. Отличительным признаком главного движения резания является также и то, что скорость этого движения во много раз превышает скорость движения подачи. Скорость движения резания называют скоростью резания; скорость движения подачи принято называть просто подачей.
На станке предусмотрены и вспомогательные движения, которые не участвуют в процессе срезания стружки – вращение ходового вала, ходового винта, подвод резца к заготовке, зажим и разжим заготовки, переключение скоростей и т.д.
На рис. 1 изображены схемы двух распространенных видов обработки: строгания и продольного точения. При строгании движением резания является прямолинейное движение резца, а движением подачи – прямолинейное движение детали, совершаемое после каждого двойного хода резца.
а |
б |
Рис. 1. Схемы обработки: а – строганием; б – точением: движение резания V; движение подачи Sм; результирующее движение W; обрабатываемая поверхность 1; обработанная поверхность 2; поверхность резания заготовки 3; траектория движения инструмента (при точении – за один оборот заготовки) 4
17
При продольном точении движением резания является вращательное движение детали, а движением подачи – то, которое происходит одновременно с движением резания, – прямолинейное движение резца вдоль оси детали.
Если движение подачи остановить, то обработка детали закончится после одного хода резца при строгании и одного оборота детали при точении.
Сущность того или иного метода обработки определяется только соотношением скоростей, осуществляемых при движении, и не зависит от того, сообщается ли движение резания и подачи инструменту или детали. Например, если при строгании движение резания сообщают резцу, то это соответствует обработке на поперечнострогальном станке, а если детали – то на продольно-строгальном станке.
При сверлении на сверлильном станке вращательное движение резания совершает сверло, а на револьверном станке – деталь. Соответственно движение подачи может совершать как инструмент, так и деталь. При некоторых методах обработки имеет место третье движение, являющееся вспомогательным движением формообразования и служащее для придания детали необходимой конфигурации. Таким третьим движением, например, при нарезании резьбы резцом, является его перемещение вдоль оси детали на расстояние, равное шагу резьбы за время одного оборота детали, а при фрезеровании венцов зубчатых колес червячно-модульными фрезами – поворот детали на один зуб за время одного оборота фрезы.
В зависимости от того, совершаются движения резания и подачи одновременно или в разное время, все инструменты делят на две группы: инструменты с простым и сложным рабочим движением.
Если движение подачи отсутствует в то время, когда совершается движение резания, то инструмент имеет простое рабочее движение. Если же движение резания и движение подачи совершаются одновременно, то инструмент имеет сложное рабочее движение. Очевидно, что строгальный резец, изображенный на рис. 1, а, совершает простое рабочее движение, а токарный резец, изображенный на
18

рис. 1, б, – сложное рабочее движение. Большинство режущих инструментов (токарные резцы, сверла, зенкеры, развертки, фрезы и др.) имеют сложное рабочее движение.
Инструментов с простым рабочим движением значительно меньше. К ним можно отнести строгальные и долбежные резцы, протяжки и некоторые другие инструменты. Если при сложном рабочем движении инструмента (см. рис. 1, б) векторы скорости резания V и подачи Sм сложить, то результирующий вектор W называют век-
тором истинной скорости резания. Так как вектор Sм весьма мал по сравнению с вектором V , то истинная скорость резания по величине мало отличается от скорости резания.
При простом рабочем движении, если отсутствует вспомогательное движение формообразования (см. рис. 1, а), понятия истинной скорости резания и скорости резания совпадают. Вектор истинной скорости резания всегда направлен по касательной к траектории рабочего движения инструмента, которая на рис. 1 обозначена цифрой 4. При строгании траекторией рабочего движения является прямая линия, а при точении – винтовая линия с осью, совпадающей
сосью детали.
1.1.2.Поверхности заготовки в процессе резания
Впроцессе срезания припуска на заготовке различают харак-
терные поверхности: обрабатываемую, обработанную и поверхность резания. Обрабатываемой поверхностью 1 (см. рис. 1) назы-
вают такую поверхность заготовки детали, с которой срезают стружку. Она исчезает в результате снятия припуска. Обработанной поверхностью 2 называют поверхность, образовавшуюся на детали после снятия стружки. Поверхностью резания 3 называют поверхность, непосредственно образуемую лезвиями инструмента в процессе резания. Эта поверхность является переходной между обрабатываемой и обработанной поверхностями, она существует только во время резания и исчезает после окончания обработки. Поверхность резания с геометрической точки зрения образована совокупностью
19
траекторий относительного рабочего движения инструмента. Поэтому ее форма определяется формой лезвий инструмента и сочетанием движений детали и инструмента в процессе резания. При строгании поверхность резания является плоскостью, а при продольном точении – конволютной винтовой поверхностью.
Реальная форма обработанной поверхности всегда отличается от той идеальной формы, которая задается чертежом детали.
Если формообразование детали рассматривать только с геометрической точки зрения, то форма обработанной поверхности будет зависеть от формы поверхности резания, так как обработанная поверхность детали образована несрезанными участками поверхности резания. Для рассматриваемых (см. рис. 1) методов обработки обработанная поверхность представляет собой совокупность гребешков, очерченных при строгании двумя плоскостями, а при точении – двумя винтовыми поверхностями.
1.1.3. Кинематические схемы резания
Как показал проф. МВТУ им. Н.Э. Баумана Г.И. Грановский, несмотря на большое число методов обработки и их разнообразие, все они могут быть определены принципиальными кинематическими схемами, которые выражают абсолютные движения, сообщаемые в процессе резания инструменту и обрабатываемой детали механизмами станка. Кинематика рабочих органов металлорежущих станков намного упрощается при использовании принципиальных кинематических схем, основанных на сочетании равномерных движений: прямолинейных и вращательных. В зависимости от числа и характера сочетаемых движений принципиальные кинематические схемы могут быть разделены на восемь групп: I – одно прямолинейное движение (строгание, протягивание); II – два прямолинейных движения (отрезка ленточными пилами); III – одно вращательное движение (круговая протяжка); IV – одно вращательное и одно прямолинейное движение (точение, фрезерование, сверление; V – два вращательных движения (шевингование); VI – два прямолинейных и одно вращательное движение (зубодолбление); VII – два вращательных и одно прямолиней-
20