
714
.pdf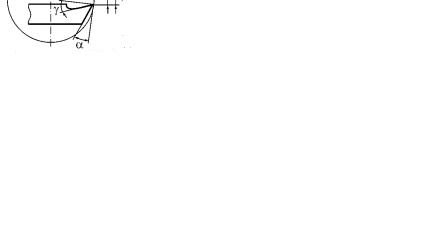
Таким образом, во время работы резец в главной секущей плоскости будет иметь кинематический передний угол γк = γ + ηϕ. Для обеспечения в процессе работы оптимального заднего угла его затачивают, увеличивая на ηϕ. Это уменьшает угол заострения β и ухудшает условия работы резца. Чтобы сохранить их оптимальными, передний угол можно уменьшить на ηϕ.
Иногда необходимо установить режущую кромку ниже или выше оси заготовки. Наличие положительного или отрицательного угла наклона режущей кромки также приводит к тому, что точки режущей кромки располагаются ниже или выше оси заготовки. При этом будет изменяться положение касательной плоскости резания к поверхности резания на величину ±τϕ (из-за выпуклости или вогнутости поверхности резания). Фактические передний γф и задний αф углы будут равны (рис. 7): γф = γ ± τϕ; αф = α ± τϕ.
а |
б |
в |
г |
д |
е |
Рис. 7. Схемы изменения углов резца при установке выше или ниже центра заготовки при наружном точении – а, б, в и расточке – г, д, е
31

В результате при установке выше центра (см. рис. 7, а) передний угол увеличивается, а задний уменьшается. При установке ниже центра (см. рис. 7, в) передний угол уменьшается, а задний увеличивается. Это необходимо учитывать при расчетах сил и температур резания.
Если угол ϕ = 0°, то α = arcsin (h/R). Если угол ϕ ≠ 0°, то tg τϕ = = tg τ · сos ϕ.
Таким образом, во время работы резец в главной секущей плоскости будет иметь кинематические углы
αк = α – ηϕ ± τϕ; γк = γ + ηϕ ± τϕ.
|
Главный ϕ и вспомогательный |
|
|
ϕ1 углы в плане могут быть различ- |
|
|
ными в зависимости от установки |
|
|
резца по отношению к оси обрабаты- |
|
|
ваемой детали. Указанное изменение |
|
|
углов ϕ и ϕ1 показано на рис. 8. |
|
Рис. 8. Схема изменения углов ϕ |
При сверлении кинематический |
|
и ϕ1 в плане в зависимости от |
задний угол уменьшается, а перед- |
|
установки резца относительно |
ний – |
увеличивается на η (рис. 9). |
оси детали при точении |
Угол |
η различен для разных точек |
|
режущей кромки: tg ηx = Sо/2·πDx; αк = α – η, где Dx – диаметр сверла на расстоянии х от центра сверла.
При сверлении углы заточки сверла также изменяются (рис. 9). Чем ближе точка режущей кромки лежит к оси сверла, тем меньше диаметр воображаемой цилиндрической поверхности, по которой
Рис. 9. Передний и задний углы сверла в процессе резания: 1 – развернутая винтовая линия; 2 – развернутая окружность
32
проходит траектория точки режущей кромки, и тем значительнее в процессе работы уменьшается задний угол сверла. Уменьшение зазора между задней поверхностью сверла и поверхностью резания (заднего угла) или отсутствие его приводит к повышенному трению и изнашиванию или делает дальнейшую работу сверла невозможной.
Даже при малых подачах уменьшение заднего угла в процессе работы для точек, находящихся вблизи оси сверла, весьма существенно. Это уменьшение компенсируют, увеличивая задний угол при заточке: αз = α + η. Если заднюю поверхность сверла заточить по плоскости с одинаковым задним углом во всех точках режущей кромки, учитывающим максимальное уменьшение его в процессе работы αз = α + ηmax, процесс заточки упростится. Но у сверла изменить (уменьшить) передний угол невозможно, а на периферии он достаточно велик. Поэтому при больших задних углах угол заострения β на периферии сверла будет малым, а прочность и теплоотвод – низкими.
В связи с этим при заточке приходится обеспечивать такое увеличение заднего угла, которое необходимо для каждой точки режущей кромки, т.е. затачивать задний угол переменной величины. Наибольшим задний угол должен быть у оси сверла, наименьшим – на периферии. При этом обеспечивается примерное равенство углов заострения вдоль режущей кромки сверла.
1.2.4. Формы передней поверхности резцов
Плоская передняя поверхность резца, изображенная на рис. 10 и 11, во многих случаях резания не является оптимальной. Если резец изготовлен из быстрорежущих сталей, то в зависимости от рода обрабатываемого материала и условий работы рекомендуют три формы передней поверхности (см. рис. 10).
Форма I – криволинейная с фаской f; предназначена для резцов всех типов, кроме фасонных со сложным контуром, обрабатывающих пластичные материалы с подачей более 0,2 мм/об. Передняя по-
33
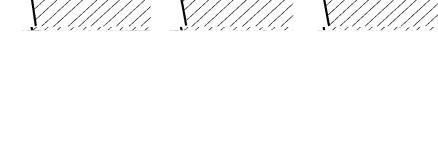
верхность состоит из фаски, параллельной опорной плоскости резца, и выкружки, очерченной дугой окружности радиуса R. В точке пересечения выкружки с фаской касательная к ней образует с плоскостью, параллельной опорной плоскости, передний угол γ.
Рис. 10. Формы передней поверхности резцов из быстрорежущих сталей
Размеры выкружки: R = (10…15)·Sо для проходных и расточных резцов и R = (50…60)·Sо для прорезных и отрезных резцов; l = 2R sin× ×(γ – γп.р), где γп.р – угол, под которым опорная плоскость быстрорежущей пластинки наклонена относительно опорной плоскости резца.
Форма II – плоская с фаской; предназначена для резцов всех типов, обрабатывающих пластичные материалы с подачей более
0,2 мм/об.
Форма III – плоская; предназначена для резцов всех типов, обрабатывающих хрупкие материалы, а также пластичные материалы, если подача равна или меньше 0,2 мм/об.
Ширина фаски для форм I и II f = (0,8…1)·Sо, а величина переднего угла зависит от механических свойств обрабатываемого материала, уменьшаясь при увеличении его твердости и прочности. Для форм I и II передней поверхности угол γ изменяется в пределах 25–30°, а для формы III в пределах 5…25°.
При оснащении резца пластинкой твердого сплава рекомендуют также три аналогичные формы передней поверхности (см. рис. 11), имеющие те же названия, что и у резцов из быстрорежущих сталей.
34
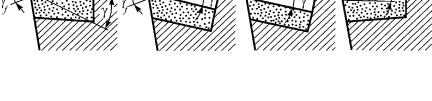
В отличие быстрорежущих резцов у твердосплавных угол γf наклона фаски не равен нулю и имеет отрицательный знак.
а б
Рис. 11. Формы передней поверхности резцов с пластинками твердых сплавов
На рис. 11 форма I предназначена для резцов, обрабатывающих пластичные материалы с пределом прочности на растяжение σb ≤ 80 кгс/мм2 при получистовом режиме резания (Sо < 0,3 мм/об.). Выкружка выполняет функцию стружкозавивального элемента резца; ее размеры: l = 2…2,5 мм; R ≈ 2l.
Форма II применяется в тех же случаях, что и форма I, а также для резцов, обрабатывающих хрупкие материалы, но при прерывистом резании и при обработке деталей, имеющих литейную корку.
Форма III, а предназначена для резцов, обрабатывающих хрупкие материалы, а также для резцов, обрабатывающих пластичные материалы с σb ≤ 80 кгс/мм2 при чистовом режиме резания с малыми глубинами резания и подачами.
Форма III, б предназначена для резцов, обрабатывающих пластичные материалы с σb > 80 кгс/мм2, а также при резании пластичных материалов любой прочности, но при прерывистом резании.
Ширина фаски I колеблется в пределах 0,2…0,5 мм, а угол ее наклона γf = –(3…5°). Передний угол резца с формой I передней поверхности равен 15…20°, а передний угол резцов с формами II и III зависит от прочности и твердости материала обрабатываемой детали, уменьшаясь и переходя в область отрицательных значений при увеличении σb и НВ. Для формы II и III, а передний угол колеблется в пределах 8…15°, а для формы III, б – в пределах –5…–10°.
35

Величина заднего угла резца мало зависит от механических свойств материала обрабатываемой детали и определяется величиной подачи. У резцов из быстрорежущих сталей при Sо < 0,2 мм/об. задний угол α = 12°, а при Sо ≥ 0,2 мм/об. задний угол α = 8°. У резцов из твердых сплавов при Sо < 0,3 мм/об. задний угол α = 10…12°, а при Sо ≥ 0,3 мм/об. задний угол α = 6…8°.
Величина вспомогательного заднего угла у проходных, расточных и подрезных резцов делается равной величине заднего угла.
Величины главного ϕ и вспомогательного ϕ1 углов в плане зависят от назначения резца и жесткости технологической системы. Угол ϕ лежит в пределах 30…90° и угол ϕ1 – в пределах 5…30°. При непрерывном резании угол наклона главного лезвия у резцов из быстрорежущих сталей делается равным λ = 4° при черновых работах и λ = –4° при работах чистовых (см. рис. 4). У резцов с пластинками
|
|
твердых сплавов знак угла λ всегда |
|||
|
|
положителен и его величина лежит |
|||
|
|
в пределах 0…5°. При прерывистом |
|||
|
|
резании, независимо от рода инст- |
|||
|
|
рументального |
материала, |
резцы |
|
|
|
имеют положительный угол накло- |
|||
|
|
на главного лезвия, величина кото- |
|||
|
|
рого лежит в пределах 10…30°. |
|||
а |
б |
|
Переходное лезвие, сопрягаю- |
||
щее |
главное и |
вспомогательное |
|||
Рис. 12. Формы переходного лез- |
лезвия, очерчивают у резцов по ду- |
||||
вия резца: а – дуговая; б – прямо- |
ге |
окружности |
или по |
прямой |
|
|
линейная |
(рис. 12). |
|
|
Если переходное лезвие выполнено по прямой, то оно образует переходный угол в плане ϕ0. При дуговой форме переходного лезвия величина радиуса R равна: у резцов из быстрорежущих сталей 1…5 мм и у твердосплавных резцов 0,5…3 мм. При формах а и б передней поверхности должно соблюдаться неравенство
36
R ≤ |
|
|
|
f |
|
. |
|
2 |
|
ϕ+ϕ |
|
||
|
2sin |
|
1 |
|
||
|
|
|
2 |
|
Длина переходного лезвия f0 = 0,3…2 мм, а переходный угол в плане ϕ0 = 15…20° для проходных, расточных и подрезных резцов и ϕ0 = 45° для резцов отрезных.
1.3. Классификация видов обработки резанием
По виду инструментов обработка резанием делится на точение, фрезерование, сверление, протягивание, шлифование и др.
Точение: режущие инструменты – токарные резцы различного назначения для различных токарных операций.
Фрезерование: режущие инструменты – фрезы различных конструкций для обработки плоскостей, канавок уступов, профильных поверхностей.
Сверление: режущие инструменты – сверла для обработки отверстий.
Протягивание: режущие инструменты – протяжки для обработки внутренних и наружных поверхностей.
Шлифование: режущие инструменты – шлифовальные круги, шлифовальные ленты, шлифовальные пасты.
Обработка резанием также классифицируется по признакам: свободное и несвободное, прямоугольное и косоугольное, однолезвийное и многолезвийное, непрерывное и прерывистое.
Если в работе участвует только одно главное лезвие, то такое резание называют свободным (рис. 13, б); если же в работе помимо главного лезвия принимают участие переходное и вспомогательное лезвия, то резание называют несвободным (рис. 13, а). Углы, под которыми поверхности и лезвия инструмента расположены в пространстве, называют геометрическими параметрами инструмента.
Существующее в настоящее время разнообразие обработки резанием, конструкций и геометрии инструментов, свойств обрабатываемых материалов, широкие пределы изменения режимов резания
37

обусловливают практически бесконечное число возможных комбинаций условий резания. Однако все они могут быть сведены к сравнительно небольшому числу основных случаев работы режущего лезвия. Их классификация может быть проведена по следующим признакам.
аб
Рис. 13. Несвободное (а) и свободное (б) резание
1. По количеству участвующих в резании режущих кромок – свободное и несвободное. При свободном резании в работе принимает участие только одна режущая кромка (рис. 14, а, б). В этом случае все участки режущей кромки находятся практически в одинаковых условиях, а направления перемещения всех частиц стружки практически одинаковы.
а |
б |
в |
Рис. 14. Примеры свободной (а, б) и несвободной (в) обработки резанием
38

Но гораздо чаще приходится иметь дело с процессом несвободного резания (рис. 14, в), при котором вспомогательная режущая кромка в зависимости от радиуса вершины резца R, вспомогательного угла в плане ϕ1 и подачи Sо принимает большее или меньшее участие. Оно создает так называемое побочное резание в дополнение к главному, осуществляемому главной режущей кромкой. При этом процесс образования стружки является весьма сложным, так как здесь отдельные элементы стружки стремятся передвигаться по передней поверхности резца в различных направлениях.
2. По ориентации режущей кромки относительно вектора скорости главного движения – прямоугольное и косоугольное. Если режущая кромка перпендикулярна к направлению главного движения резания, оно является прямоугольным, а если не перпендикулярна – косоугольным (рис. 15). Положение режущей кромки относительно направления движения характеризуется углом наклона режущей кромки λ. В зависимости от формы главной режущей кромки и ее расположения относительно оси заготовки образуются различные формы сечения среза, а следовательно, и стружки. Сечение среза при свободном резании резцом с прямолинейной режущей кромкой, расположенной перпендикулярно к оси заготовки (см. рис. 15, a; 16, а), имеет форму прямоугольника. В данном случае толщина среза постоянна и равна подаче, ϕ = 90°.
а |
б |
Рис. 15. Прямоугольная (а) и косоугольная (б) обработка резанием
Если прямолинейная режущая кромка при свободном резании расположена по отношению к оси заготовки под углом ϕ ≠ 90°
39

(см. рис. 15, б; 16, б), сечение среза имеет форму параллелограмма, а толщина, как и в первом случае, постоянна, но меньше подачи.
Несвободное резание применяется при работе резцом с прямолинейной режущей кромкой и с радиусом вершины R (рис. 16, в). В этом случае сечение среза сложное по форме. На участке аb оно имеет форму параллелограмма, а на участке bc – форму запятой, при этом на участке аb толщина постоянна, но меньше подачи, а на участке bc – переменна, но тоже меньше подачи.
аб
вг
Рис. 16. Формы сечения срезаемого слоя при свободной (а, б) и несвободной (в, г) обработке резанием
При несвободном резании резцом с криволинейной режущей кромкой (рис. 16, г) сечение среза имеет форму запятой, а толщина, измеряемая по нормали к режущей кромке, переменна и меньше подачи.
40