
Металлургия технология угля и неметаллических полезных ископаемых3
..pdfганца (20—30%), хрома ( — 15%); никель и молибден не окис ляются.
Продолжительность плавки сокращается в связи с отсутствием окислительного периода и уменьшением длительности восстано вительного периода.
На плавках с применением кислорода допускается более вы сокое содержание углерода в шихте. Кратковременное кипение ванны обеспечивает также снижение содержания водорода и азота в стали.
Комбинированные способы плавки
Для сокращения расхода электроэнергии или при отсутствии качественного стального лома для электропечей сталь выплавляют комбинированными процессами, сочетая работу нескольких агрега тов. Поэтому в зависимости от условий оказывается экономически выгодным использовать дуплекс-процесс: кислородный конвертер — дуговая электропечь или триплекс-процесс: вагранка — конвер тер — электропечь.
При дуплекс-процессе, когда электропечь работает на жидком полупродукте, ее производительность удваивается, расход элек троэнергии снижается до 250—320 квт-ч/т, расход электродов уменьшается до 2,5—3,0 кг/т. В этом случае оказывается также возможным уменьшить мощность трансформатора на 40% и, сле довательно, снизить стоимость печи.
Технико-экономические показатели
Для электропечей, работающих на твердой завалке, технико экономические показатели характеризуются следующими дан ными:
Емкость печи, m ................. |
|
5—100 |
Число рабочих суток в году . |
|
330—345 |
Производительность, гп/ч . |
|
1—12 |
Выход годного металла, % |
|
89—91 |
Расход на 1 пг стали; |
. |
550—1200 |
электроэнергия, к в т-ч . . |
||
электроды графитированные, |
кг |
4—9 |
изложницы и поддоны, кг . |
|
40—50 |
огнеупорный кирпич, кг . . |
|
10—13 |
порошки для заправки, кг . |
|
35—45 |
Дуговые электропечи большой емкости работают экономичнее, чем малые печи.
В структуре себестоимости слитков электростали необходимо отметить высокую стоимость металлошихты ( — 77%), в том числе ферросплавов ( — 37%).
§ 7. Выплавка стали в индукционных электропечах
Индукционная однофазная электропечь состоит из индуктора, внутри которого находится тигель с металлом (рис. 33). Индуктор выполняет роль первичной цепи, а расплавленный металл — вто
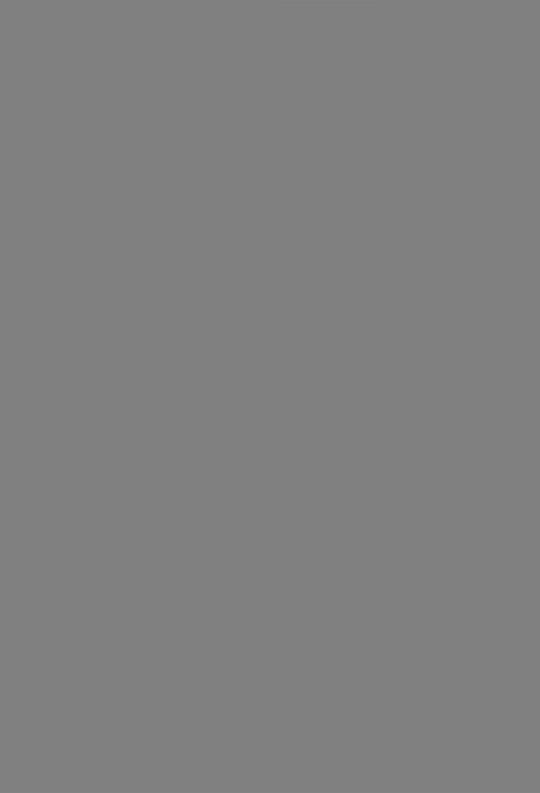
Глава //
МЕТАЛЛУРГИЯ МЕДИ |
|
§ 1. Общие сведения |
|
Медь, как и железо, находит широкой |
Про |
мышленности. Она обладает хорошей ковкостью и высокой' тягу честью, плотность ее 8,95 г/см? (при / = 20°С), температура плав ления 1083° С, температура кипения 2360° С, теплота'плавления 51 ккал/кг. Медь хорошо проводит тепло и электричество. Тепло проводность меди при t = 20° С составляет ..0,921 кал/см-сек^градг электросопротивление 0,018 ом-мм2/м.
Ме д ь |
и ее |
с п л а в ы |
используются для сооружений линий |
электропередач |
и связи, |
в электромашиностроении'..:*!^.приборо |
|
строении, |
в холодильной |
технике (производств^ теплообменни |
|
ков, змеевиков) |
и химическом машиностроении, Около 50%^(дсец.. |
меди расходуется электропромышленность^-.
Широко используются сплавы меди типа оловянных (.4—33%, Sn), свинцовых (~30% РЬ), алюминиевых (5—Д1 % А1:)Укремние вых (4—5% Si) и сурьмяных бронз.
Бронзы и сплавы меди с цинком (латунь)^применяются .в ма шиностроении, химической, бумажной и пищевой промышленности. Для изготовления электродов и электроконтактов ^ используют сплавы меди с хромом и вольфрамом. ВвёйёниёмеДи ’Йаль по вышает ее коррозионную стойкость.
§ 2. Медные руды и способы их переработки
Ме д ь в п р и р о д е встречается главным образом в виде различных соединений. Медные руды подразделяют на сульфид ные, окисленные и смешанные. Сульфидные руды содержат медь в виде сернистых соединений (халькопирит CuFeS2, халькозин Cu2S, ковеллин CuS); окисленные руды содержат медь в виде окислов (куприт Си20, мелаконит СиО).
Содержание меди в промышленных рудах обычно составляет 1—6%. Руды с меньшим содержанием' меДй (0,6—0,8%) подвер гают глубокому обогащению методом флотации, удаляя пустую породу (Si02, AI2O3 и СаО) и пирит. В результате1получают мед ный концентрат, содержащий И —35% Си (табл. 9). При селек тивной флотации медных руд, которые обычно комплексны, удаетсд получить, наряду с медным, также свинцовый, цинковый, никеле вый, молибденовый или коллективные концентраты. Из медно цинковых руд путем селективной флотации удается извлечь в мед ный концентрат 80—90% Си, а в ц и н к о в ы й — 65—70% Zn.
Ме д ь и з в л е к а ю т из руд плавкой или выщелачиванием. Широкое распространение получил пирометаллургический метод, который наиболее эффективен при переработке ''концентратов. Схема пирометаллургии меди приведена на рис. 34.
Первой стадией этого процесса является плавка на штейн {сплав сульфидов), осуществляемая в шахтной, отражательной
или электрической печах. Вторая |
стадия — конвертирование штей |
||||||||||
на для |
окисления |
воздухом сернистого |
железа, перевода |
его в |
|||||||
|
|
|
|
шлак и выделения черновой меди |
|||||||
Подмотовка руд к плавке |
(98—99% Си; менее 0,1% S; менее |
||||||||||
0,04% |
Fe). |
Третья |
стадия — рафини |
||||||||
(обомащшние. обжим) |
рование (очистка от примесей) чер |
||||||||||
|
|
|
|
новой меди. |
|
|
|
|
|
||
|
|
|
|
Флотационные концентраты порош |
|||||||
|
|
|
|
кообразны, поэтому для их плавки на |
|||||||
|
|
|
|
штейн |
применяют отражательные |
или |
|||||
|
|
|
|
электрические |
печи. |
Перед |
плавкой |
||||
|
|
|
|
концентраты обычно обжигают в окис |
|||||||
Конвертирование штейна |
лительной среде для удаления из них |
||||||||||
(лровувка воздухом) |
около 50% серы. Использование обож |
||||||||||
Чернобае |
|
Конвертера |
женных и нагретых до температуры |
||||||||
|
|
мый |
шлак |
550—600° С |
|
концентратов |
позволяет |
||||
|
|
|
|
снизить расход топлива в отражатель |
|||||||
Рафинирование |
ной печи в два раза и получить при |
||||||||||
Г |
|
— |
1 |
плавке богатый белый штейн, близкий |
|||||||
|
по составу к полусернистой меди (80% |
||||||||||
Отходы |
Медь |
||||||||||
|
|
|
|
Си). |
|
медных |
концентратов |
осу |
|||
Переработка для иа~ |
Обжиг |
||||||||||
влечения Agju.8e,Te иди |
ществляют в многоподовых обжиговых |
||||||||||
|
|
|
|
печах непрерывного действия, с меха |
|||||||
Рис. 34. |
Упрощенная |
техноло |
ническим |
перегребанием. |
Эта |
печь |
|||||
гическая |
схема |
пирометаллур |
представляет |
собой |
вертикальный |
по |
|||||
|
гий |
меди |
|
лый цилиндр, |
футерованный |
шамот |
|||||
|
|
|
|
ным |
кирпичом. По |
высоте |
печь |
раз |
делена полками (подами) из шамотного кирпича, расположен ными на расстоянии 0,8 м один от другого; обычно изготовляют 8—12 подов. Через центр печи проходит вертикальный пустотелый вал, на котором крепятся лопаткообразные гребни. При вращении
Состав медных руд и концентратов, % |
Т а б л и ц а |
9 |
||||||
|
|
|
||||||
Руды и концентраты |
Си |
Fe |
S |
Zn |
Si 0 2 |
A I 2O S |
CaO |
MgO |
Руды: |
1—6 |
8—40 |
9—46 |
1 - 6 |
5—55 |
2—12 0 ,3 - |
0 ,3 - |
|
сульфидные |
||||||||
окисленные . |
2 |
1 |
0,1 — |
|
|
|
4,0 |
1,5 |
|
60 -6 8 10—16 0,3— |
0,3— |
||||||
Концентраты: |
|
|
0.2 |
|
|
|
0,7 |
0,7 |
|
|
30—43 |
2—7 |
|
|
|
|
|
медно-цинковых руд . |
11—20 |
25 -37 |
3—5 |
3—7 |
0,5— |
— |
||
окисленных руд . |
20—35 |
16—27 |
|
|
5—25 |
5—8 |
2,0 |
|
|
|
0—3,0 |
|
84
вала (2—3 об/мин) гребни перемещают материал на одних пол ках от центра к периферии, а на других в обратном направлении. Таким образом, концентрат движется сверху вниз по зигзагооб разному пути в противотоке горячего воздуха.
В последнее время для обжига медных концентратов получают широкое распространение печи с кипящим слоем.
Сульфиды, нагретые до температуры воспламенения (325— 810°С), сгорают в воздухе с выделением тепла
2Me S + 3 0 2 = 2Me О + 2S02 + Q.
Температуру обжига поддерживают не выше 850° С с тем, что бы избежать спекания шихты. С этой целью также ограничивают допустимое содержание серы в шихте (не выше 27%) и в неко торых случаях вводят флюсы, необходимые для последующей плавки (известняк, кварц и др.) и различные оборотные мате риалы.
Сернистый газ частично окисляется избыточным кислородом до SO3, который образует с некоторыми окислами сульфаты (свин ца и кальция).
Окислы обжигаемого концентрата взаимодействуют между со бой, образуя ферриты, силикаты и другие соединения.
Отходящие из печи газы обычно используют для производства серной кислоты. Предварительно газы очищают от пыли обжи гаемого материала, унос которого с газами доходит до 5—15%.
Медь получают также из вторичного сырья, представляющего собой лом и отходы меди и ее сплавов. Отходы различных сортов латуней и бронз перерабатывают раздельно, корректируя их со став при плавке соответствующими добавками.
§ 3. Выплавка медных штейнов
Медный штейн, представляющий собой полупродукт для по следующего производства черновой меди, состоит в основном (на 80—90%) из сульфидов меди и железа, а также окислов железа, кремния, алюминия и кальция.
Медные руды, содержащие благородные металлы (Au, Ag) целесообразно обогащать способами, позволяющими перевести их в медный концентрат. Такие концентраты переплавляют в отра жательной или электрической печах. При этом золото и серебро практически полностью переходят в штейн и извлекаются затем при рафинировании меди.
Сырые кусковатые медные руды переплавляют на штейн в шахтных печах. В зависимости от состава руд и технологических условий процесса различают медно-серную, пиритную и полупиритную плавки.

кает непрерывно в шлаковозные ковши, а штейн выпускают пе риодически.
Ши х т о в ы е м а т е р и а л ы загружают в печь отдельными порциями — колошами, составленными из кусковой медной руды, известняка, кокса и оборотных продуктов. Расход кокса состав ляет 10—12% от массы шихты.
П р о ц е с с м е д н о - с е р н о й п л а в к и характеризуется од новременным протеканием реакции окисления сульфидов и горе ния кокса с образованием СО2, SO2 и окислов металлов, реакций взаимодействия между закисью меди и сульфидом железа и реак ции образования силикатов железа и кальция (шлакообразования).
В нижней части печи у фурм при температуре около 1500° С протекают следующие процессы:
С -I- 0 2 = С02 (горение углерода);
2FeS + 302 = 2FeO + 2S02 (окисление сульфида);
2FeO + Si02 = (Fe0)2-Si02 (шлакообразование).
Образующиеся газы (С02, SO2, 0 2, N2) поднимаются вверх, обеспечивают передачу тепла твердой шихте и взаимодействуют с твердым углеродом кокса:
С02 f С = 2СО; 2S02 4- 5С = 4GO + CS2; S02 + 2С = COS + СО; S02 + С = С02 + - у S2.
В верхних горизонтах шахты происходит разложение пирита и в газы переходят пары серы.
, В результате плавки, получается штейн, содержащий всего 5—15% Си и к и с л ы й железистый шлак (30—35% Si02; 50—55% FeO и 6—8% СаО). Для повышения содержания меди в штейне последний подвергают сократительной плавке в шахтной печи с кварцем, известняком и. коксом ('/—8%). Продуктом этой операции является штейн, содержащий 25—40% Си. Газы сократительной плавки имеют низкое содержание серы и используются для про изводства серной кислоты1.
В ы п л а в к а шт е й н а без и з в л е ч е н и я с е р ы отли чается тем, что основное тепло, необходимое для плавки, полу чается за счет реакций окисления пирита и других сульфидов. В этом случае процесс ведут с меньшим расходом кокса. В ре зультате создается окислительная среда и образуются шлаки с повышенным содержанием закиси железа (до 55% FeO и до 40% S 1O2 ), что делает необходимым осуществлять процесс в печи,
1 См. часть III.
стены которой выполнены из водоохлаждаемых кессонов без огне упорной футеровки. Плавку ведут на гарнисаже из проплавляемых материалов.
При содержании в руде серы не менее 37% на плавку расхо дуется 2—4% кокса. Такая плавка называется пирит ной . В этом случае окислителем служит SO2:
|
С-Ь S02 = СО2+ ~ S2. |
Плавку руд с |
меньшим содержанием серы, когда вводится |
кокс в количестве |
6—10%. иногда до 12%, называют полупи - |
р и тн о й. |
|
При пиритной и полупиритной плавках получают штейн, со держащий 15—50% меди.
Выплавка штейна из концентратов
Плавку концентратов производят в отражательных и электри ческих печах. При использовании обожженных концентратов печи для их обжига располагают в непосредственной близости от от ражательных печей для утилизации тепла огарков.
Отражательные печи (рис. 36) отапливают мазутом, природ ным газом или каменным углем.
Стены печи выкладывают из динасового кирпича, а свод — издинаса или магнезитохромитового кирпича. Лещадь печи наби вают кварцевым песком и сваривают при температуре 1500— 1600° С.
Температура газов у передней стенки достигает 1550—1600° С, а в хвостовой части снижается да 1200—1250° С.
Шихту загружают в печь через бункера, установленные над отверстиями в своде вблизи боковых стен по длине печи. Шихта располагается на откосах печи, предохраняя кладку от воздейст вия шлака и горячих газов. Жидкий конвертерный шлак вводят в печь через окно в передней торцовой стенке.
Штейн и шлак выпускают по мере их накопления через спе циальные отверстия.
В результате взаимодействия окислов меди с сернистым же лезом получается сульфид меди, образующий штейн:
6CuO + FeS = ЗСи20 + S02 + FeO; Cu20 + FeS = Cu2S + FeO.
Таким образом, в ходе процесса штейн обедняется сульфидом железа и обогащается сульфидом меди; суммарный процесс может быть представлен реакцией
2 [FeS] + 2CU 20 + Si02 = (2Fe0Si02) + 2 lCu2S].
Состав первичных штейнов изменяется в следующих пределах: 15—55% Си; 15—50% Fe; 20—30% S; 2—3% Zn; незначительные
Рис. |
,'$б. Отражательная |
печь |
подвесным |
сводом для выплавки медного штейна: |
/ — огж |)сп<я Д.( загрузки |
шихты; 2 -- шлаковое |
окно; |
.9 — шнуровые отверстия для выпуска шгейна; 4 — запасное шпуровое отверстие. |
|
■& |
|
5 — окна для фурм |
или горелок |
количества Au и Ag. Шлак содержит не фолее 0,3—0,4% Си-и состоит в основном из Si02, FeO, СаО и AI2O3. Извлечение меди и благородных металлов в штейн достигает 96—99% .
§ 4. Конвертирование медного штейна
Для получения черновой меди осуществляют продувку медных штейнов воздухом в конвертере с боковым дутьем (рис. 37).
Фурмы для вдувания воздуха расположены по образующей
Рис. 37. Конв.ертер для продувки медного штейна
поверхности конвертера. Заливку расплавленного штейна, подачу кварцевого флюса (70—80% Si02), слив продуктов плавки и уда ление газов осуществляют через горловину конвертера, располо женную в средней части корпуса.
Процесс продувки состоит из двух периодов. Первый период (получение белого штейна) характеризуется окислением сульфи дов, шлакованием закиси железа кремнеземом и выделением сер нистого газа:
2 [FeS] + 302 = 2 (FeO) + 2S02;
2 [Cu2S] + 302 = 2 (Cu20) + 2S02
2 (FeO) + (Si02) = (Fe0)2.Si02.
По мере накопления шлака его частично удаляют и заливают в конвертер новую порцию штейна, поддерживая определенный уровень ванны. Этот период длится от двух часов до двух суток в зависимости от содержания меди в штейне.
Во втором периоде, продолжительностью 2—3 ч, из белого штейна образуется медь
Cu2S + 2CU 20 = 6Cu + S02.