
Металлургия технология угля и неметаллических полезных ископаемых3
..pdfпоступающим с температурой 550—600° С в |
печь |
через |
щелевые |
отверстия распределительного клапана. |
|
|
шахты — |
Образующийся полукокс поступает в нижнюю часть |
|||
в. зону охлаждения и выпускается из печи |
через |
разгрузочные |
|
устройства. |
|
|
|
Рис. 57. Печь с внутренним обогревом шахтного типа для полукоксования угля:
1 — шахта печн; |
2 — |
распределительный |
канал; |
3 — загрузочная короб |
ка; 4 — разгрузочные |
устройства для полукокса; |
5 — патрубок для вы |
||
вода из печи |
паро- и газообразных |
продуктов полукоксования |
Парообразные и газообразные летучие вещества с температу
рой 100—150° С выпускаются |
из печи через |
патрубок в верхней |
части шахты. |
летучих веществ |
подвергают охлаж |
П а р о г а з о в у ю с ме с ь |
дению и конденсации, в результате чего получают первичный газ, первичную смолу, газовый бензин и подсмольную воду.
Шахтные печи применяются для полукоксования неспекающихся каменных углей и бурых углей крупностью не менее 10 мм. Производительность печи составляет примерно 12 т/сутки на 1 м2 сечения шахты.
Продукты полукоксования
Выходы и качество продуктов полукоксования зависят от мно гих факторов.
Существенное влияние на ход процесса полукоксования и ка чество получаемых продуктов оказывает верхний предел и ско рость нагрева угля. При медленном нагреве угля продукты его разложения и поликонденсации удаляются, не успевая подверг нуться вторичному разложению, чем обеспечиваются высокие вы ходы жидких продуктов.
При быстром нагреве угля первичные продукты подвергаются вторичному разложению, в результате чего выход жидких продук тов уменьшается вследствие увеличения выхода газа, и ухуд шается их качество.
На качество полукокса скорость нагрева угля не оказывает заметного влияния.
В значительной мере выход и качество продуктов полукоксо вания зависят от крупности перерабатываемого угля и его грану
лометрического |
состава. Например, |
с уменьшением крупности |
угля увеличивается выход первичной смолы. |
||
П о л у к о к с |
представляет собой |
мелкий, хрупкий продукт, |
«обладающий высокой реакционной способностью. Выход летучих веществ на горючую массу 10—15%. Весовой выход полукокса 55—75% от исходного угля. Полукокс характеризуется следую
щим химическим составом в % |
(но М. В. Гофтману): |
|
||||
Продукт |
Vv |
S r |
Сг |
Нг |
(O fN )r |
ккал/кг |
Уголь . |
30—75 |
1,5—4,568—84 3,8—7,5 |
12—24 |
6300—8500 |
||
Полукокс |
8—15 |
1—4 |
84—91 |
1,6—4,4 |
5—12 |
7700—8300 |
Бурые угли распадаются при полукоксовании и образуют мелкий полукокс с большим содержанием пыли, поэтому обычно буроугольный полукокс подвергают окускованию (брикетирова нию, грануляции). Наиболее прочный и плотный полукокс обра зуют коксующиеся угли, однако они применяются для полукоксо вания в ограниченных количествах. Полукокс используется как энергетическое топливо для промышленности и быта, а также в качестве отощающей присадки в шихты для коксования1.
1 Если полукокс используется в качестве отощающей присадки, процесс по лукоксования ведут при / = 400—450° С, чтобы выход летучих веществ в полу коксе был не ниже 15%,
П е р в и ч н а я с м о л а представляет собой темно-бурую вяз кую жидкость, содержащую парафиновые, нафтеновые, аромати ческие и другие соединения. Смола является сырьем для произ водства светлых моторных топлив (бензина, керосина), смазочных масел, парафина и ряда других продуктов. Фенолы первичной смолы полукоксования используют для производства пластмасс. Выход первичной смолы зависит от качества исходного сырья, конструкции и режима печей для полукоксования. Средний вы ход ее из землистых бурых углей составляет 10—40% (на сухой уголь). Разгонка смолы дает до 40% бензино-керосиновых фрак ций (из них бензиновой фракции около 10%).
При исследовании различных температурных фракций смолы полукоксования молодых бурых углей Южного Урала наблюда
лось следующее: плотность |
смолы возрастала с 0,86—0,88 (до |
230° С) до 1,02—1,06 г/см3 |
(выше 350° С); содержание органиче |
ских оснований колебалось в пределах 0,24—1,35%, содержание карбоновых кислот уменьшалось с 0,88—1,25 (до 230° С) до 0,18 —
0,31 % (при 300—350° С), содержание фенолов |
уменьшалось с |
13,2—20,3 до 3,6—5,4%. |
углеводородов |
П е р в и ч н ы й газ состоит из непредельных |
(1—6%), двуокиси (1—20%) и окиси (1—15%) углерода, водо рода (10—30%). Характерной особенностью газа является высо кое содержание в нем метана: в буроугольном газе до 25%, в каменноугольном до 70%. Теплота сгорания газа колеблется в за висимости от исходного сырья в пределах 3500—8200 ккал/л1*\ средний выход его 10—35% в зависимости от свойств исходных углей. Этот газ используют для отопления печей установок полу коксования, как сырье для химического синтеза, для коммуналь ных и промышленных целей.
Г а з о в ы й б е н з и н получают промывкой первичного газа. Он представляет собой в основном легкие погоны первичной смо лы. Выход газового бензина доходит до 1% от веса исходного угля. Является высококачественным жидким топливом и хорошим растворителем.
П о д с м о л ь н а я в о д а существенного применения не нахо дит.
§3. Коксование
Ко к с о в а н и е каменных углей имеет своим назначением по
лучение из углей кокса (доменного, литейного, генераторного и др.), коксового газа и ценных химических продуктов.
Для коксования используются смеси каменных углей (шихты), дающие прочный кусковой кокс.
Процесс коксования протекает в камере коксовой печи в не сколько последовательных стадий. В начальной стадии нагрева
угля |
(100—110° С) из |
него |
удаляется |
гигроскопическая влага и |
часть |
сорбированных |
газов |
(кислород, |
метан, азот и др.); при |
300—350° С начинается частичная деструкция неустойчивых боко вых цепей макромолекул угля и функциональных групп с отщеп
лением низкомолекулярных |
соединений; |
при 320—480° С происхо |
|||||||
дит |
интенсивное выделение |
паров |
|
смолы и газа и образование |
|||||
пластической массы |
из спекающихся |
углей; при 480—550° С |
про |
||||||
|
|
|
|
должается |
деструкция первич |
||||
|
|
|
|
ных твердых остатков с обра |
|||||
|
|
|
|
зованием |
и выделением |
жид |
|||
|
|
|
|
ких и газообразных продуктов, |
|||||
|
|
|
|
образуется |
твердый полукокс: |
||||
|
|
|
|
при |
550—1000° С — полукокс |
||||
|
|
|
|
подвергается дальнейшей дест |
|||||
|
|
|
|
рукции и усадке с образовани |
|||||
|
|
|
|
ем твердого продукта — высо |
|||||
|
|
|
|
котемпературного |
кокса. |
|
|||
|
|
|
|
|
Переход |
угля в пластиче |
|||
|
|
|
|
скую |
массу и разложение его |
||||
|
|
|
|
с |
образованием |
газообразных |
|||
|
|
|
|
и |
парообразных |
летучих |
ве |
||
|
|
|
|
ществ, с последующим превра |
|||||
|
|
|
|
щением пластической массы в |
|||||
|
|
|
|
полукокс и полукокса в кокс |
|||||
|
|
|
|
происходит в камере коксовой |
|||||
|
|
|
|
печи |
послойно (рис. 58). |
|
|||
|
Зона темпера- смол°й |
|
|
Пластические слон, образую |
|||||
|
тур 350~5uG° |
|
|
щиеся у стен, движутся внутрь |
|||||
Рис. |
58. Схематический |
разрез уголь |
угольной загрузки с двух про |
||||||
ной |
загрузки в камере |
коксовой |
печи |
тивоположных |
сторон — от |
||||
|
|
|
|
стен камеры к центру загрузки. |
Скорость перемещения пластических слоев, определяющая скорость коксования угля, в основном зависит от температуры, развиваемой в отопительных простенках сгорающим газом, т. е. от температуры обогрева камеры коксования, равномерности обо грева ее по длине и высоте, теплопроводности огнеупорной кладки, толщины стенок камеры.
Тепло внутрь угольной загрузки передается и поступает через слой кокс—полукокс. С увеличением толщины этого слоя количе ство тепла, поступающего в. единицу времени, и скорость пере мещения пластического слоя уменьшаются.
В конце процесса коксования, когда пластические слои, пере мещающиеся с двух противоположных сторон камеры, сливаются, образующийся в центре угольной загрузки общий пластический слой получает тепло с двух сторон, и скорость коксования угля возрастает.
Таким образом, возрастание температур в разных точках угольной загрузки различно. Чем ближе слой угля находится от стенок нагрева, тем раньше в нем наступает подъем температуры и тем интенсивнее он происходит.
Важным фактором хода процесса коксования является обра зование летучих веществ и их удаление.
В начальный период коксования, до перехода угля в пласти ческую массу, летучие вещества, представляющие преимуществен но пары воды и газы, не встречая сопротивления направляются внутрь угольной загрузки.
С момента образования пластического слоя направление дви
жения летучих веществ изменяется. |
массе, |
при температурах до |
|
Образующиеся |
в пластической |
||
500° С, первичные |
газообразные и |
жидкие |
продукты разложения |
угля встречают, с одной стороны, большое сопротивление в плас тической массе мало проницаемого слоя полукокса, а с другой стороны, большое сопротивление слоя угля, пропитанного смолой. В связи с этим основная масса летучих веществ из пластического слоя выходит в подсводовое пространство камеры по трещинам полукокса, подвергаясь при этом вторичному разложению.
Полукокс постепенно превращается в кокс. Из слоя готового кокса заметного выделения летучих веществ не наблюдается.
Первичные продукты разложения при вторичном разложении образуют высокотемпературные продукты — коксовый газ, смолу, аммиачную воду, сырой бензол.
Угольная шихта для коксования
Производственные угольные шихты для коксования представ ляют смеси различных марок углей. Пригодными для коксования являются угли марок К, К2, ОС, ГЖ, Ж» КЖ, Г и СС, из них угли марок Ж, КЖ, ОС и К называются основными коксующимися углями, а остальные угли — присадочными, т. е. в отдельности для производства кокса они не пригодны, но могут быть использованы в угольной шихте. Угли с различными свойствами разбиты на тех нологические типы, которые при коксовании в одинаковых усло виях должны образовывать кокс, аналогичный по своим физико механическим свойствам, и могут быть взаимозаменяемыми в кок совых шихтах.
При подборе угольных шихт исходят из назначения продук тов коксования. Например, для получения доменного кокса под бирают угли, дающие механически прочный кусковой кокс; в ших ту для коксогазовых заводов вводят угли, дающие максимальный выход коксового газа. Минимальная величина пластического слоя
(у) угольной шихты для получения кокса хорошего качества должна быть 16—19 мм.
При самостоятельном коксовании только коксовые и Коксовые жирные угли способны образовывать кокс необходимого каче ства; жирные угли при самостоятельном коксовании, как правило, образуют хрупкий и мелкий кокс; газовые угли повышенной (у> >14 мм) и средней (у=10—14 мм) спекаемости образуют также мелкий трещиноватый кокс. Из отощенных спекающихся углей
(r/= 10—13 мм) при самостоятельном коксовании образуется сильно истирающийся крупнокусковой кокс; остальные отощенные угли кускового кокса не образуют.
Типовой состав щнхт для коксования из углей Донбасса при веден в табл. 21
Т а б л и ц а 21
Типовой состав шихт для коксования
из углей Донбасса (в |
%) |
|
|
Кокс |
|
Марка угля |
|
|
|
доменный |
литейный |
Г |
25—30 |
13-15 |
ж |
33—38 |
38—50 |
к |
17—20 |
22—35 |
ос |
16—19 |
<20 |
т |
< 2 |
<10 |
Антрацит |
— |
<10 |
В Кузбассе в шихты для литейного кокса входят до 40% угля марки Гб, 26% — ОС + СС, 17—19% — К2, 16—8% — 1Ж26. Из углей Печорского бассейна в шихты для доменного кокса входят •до 60% угля марки ЖЮ, до 30% — Ж19 и до 16% кузнецкого угля марки ОС.
В последние годы в состав коксовых шихт входят все в боль ших количествах газовые, слабоспекающиеся и тощие угли. Ввод в шихты для коксования повышенных количеств газовых углей сопровождается значительным увеличением выработки химиче ских продуктов (смолы, бензола и коксового газа). Введение в шихты углей марки СС — экономит дефицитный уголь марки К, а ввод тощих углей, как правило, позволяет снизить содержание серы в коксе. Испытывается возможность широкого применения в коксовых шихтах длиннопламенных углей.
Подготовка угольной шихты
Технологические схемы подготовки угольной шихты для коксо вания в углеподготовительном цехе коксохимического завода определяются характеристикой углей, применяемых для коксо вания. На завод могут поступать угольные концентраты, рядовые чистые угли, не нуждающиеся в обогащении, и угли, подлежащие обогащению. В последнем случае в состав углеподготовительного цеха должна входить обогатительная фабрика.
Технологическая схема углеподготовительного цеха без обога тительной фабрики приведена на рис. 59.
Разгрузка угля из ж.-д. составов производится, стационарными круговыми вагоноопрокидывателями 1. Из бункера вагоноопрокп-
IНаугольную башнюын
Рис. 59. Технологическая схема углеподготовитсльиого цеха без обогатительной фабрики
дывателя уголь питателем 2 подается на ленточный конвейер 3 и транспортируется на магнитный сепаратор 4 для отделения от угля случайно попавших в него металлических предметов, затем уголь конвейером 5 направляется в зубчатые дробилки 6, где он дробится до крупности 0—40 мм, и далее конвейерами 7, 8, 9 с разгрузочными тележками направляется в приемные бункера. Прием угля производится по маркам и шахтогруппам, т. е. по группам, объединяемым по показателям коксуемости и химиче ским характеристикам (зольности и содержанию серы). Из бун керов уголь определенных марок и шахтогрупп в заданной про порции подается автоматическими дозаторами 10 на сборные конвейеры 11. Одним из конвейеров транспортируется смесь твер
дых, |
другим — смесь мягких |
углей. Твердые угли |
конвейерами |
12 и |
13 транспортируются в |
молотковые дробилки |
14. Мягкие |
угли конвейерами 15 и 16 транспортируются в молотковые дро билки 17. Измельченные до крупности <3 мм мягкие и твердые угли объединяются на сборном конвейере 18 и транспортируются конвейерами 19 и 20 в смесительное отделение, где шихта смеши вается в смесительных устройствах 21 и распределяется по уголь ным башням системой транспортных устройств 22—29.
Данная схема подготовки угольной шихты характерна тем, что предусматривает дифференцированное измельчение ее ком понентов, предотвращая переизмельчение мягких углей. На неко торых коксохимических заводах, не имеющих обогатительных фабрик, применяют схему углеподготовки, предусматривающую составление шихты после дробления ее угольных компонентов.
Выбор метода обогащения углей для коксования зависит |
от |
их физико-механических и химических свойств и требований |
по |
требителя к качеству кокса.
На обогатительных фабриках при коксохимических заводах наибольшее распространение имеет схема (рис. 60), предусмат ривающая обогащение средних и крупных классов гравитацион ными методами, обычно в отсадочных машинах, и угольной мело чи (<1 мм) — методом флотации.
Коксовые печи
Для коксования применяются коксовые печи различных видов, отличающиеся между собой главным образом отопительными си стемами. Конструктивно коксовые печи состоят из трех основных узлов — камеры коксования, обогревательных простенков камеры и устройства для утилизации тепла отходящих газов.
Для централизованных подводов к печам отопительного газа, распределения шихты, отвода и улавливания химических продук тов коксования коксовые печи объединяются в большие группы, называемые батареями. Число печей в батарее составляет от 45 до 77.
Общий вид коксовой печи показан на рис. 61. Камера коксо-
Рис. 60. Технологическая схема углеподготоиительного цеха с обогатительной фабрикой:
/ — нагоноопрокпдынатель |
для |
прием;! |
угля; 2 — отделение для удаления |
|
из угля инородных предметов (дробление—грохо |
||||||||
чение); 3 — приемные бункера |
для угля; |
|
4 — главный |
корпус обогатительной |
фабрики; |
5 — бункера |
для |
крупного |
и мелкого |
||||
концентрата; 6 — сушильное отделение; |
7 — бункера для |
флотоконцептрата; |
8 |
отделение измельчения |
(раздельно |
крупного |
|||||||
и мелкого концентратов); |
9 — смесительное |
отделение; |
10— угольные башни |
(верх); |
11, |
12 — бункера |
для |
породы и |
промнро- |
||||
|
|
дукта; |
13 — |
шламовые отстойники; 14 — перегрузочные |
станции |
|
|
, |
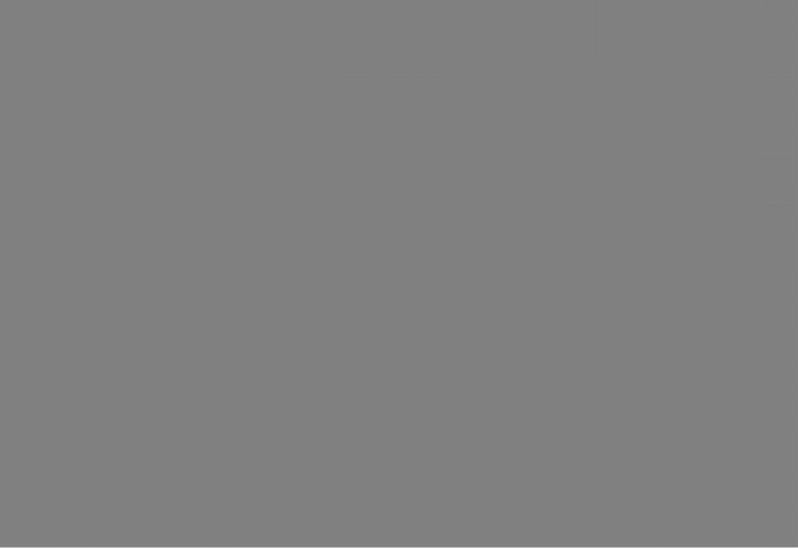