
Методы и инструменты поиска инновационных решений
..pdf
ми, – это защитное устройство, благодаря которому дефекты просто не образуются. Следует отметить, что основные положения этой концепции широко применялись компанией Ford еще в 1908 г.
Известно множество способов и приемов предупреждения ошибок, начиная с простых переделок и изменений, вносимых в оборудование и процессы изготовления продукции, и заканчивая серьезной модернизацией конструкции изделий. Например, написание инструкций для исполнителей, к которым они смогут обращаться в будущем; предупредительные надписи и предупреждающие сигналы; повторение подчиненными полученных заданий для обеспечения их правильного понимания и т.д. (рис. 4.10).
Рис. 4.10. Пример использования простого приема защиты от ошибок: а – исходный процесс монтажа; б – процесс монтажа после применения приема защиты от ошибок
В цехе, несмотря на статистику, маркировку и контроль, постоянно повторяются две одинаковые ошибки: деталь А при монтаже блока часто оказывается в окошке 2, и, наоборот, деталь В оказывается в окошке 1.
Простой прием защиты от ошибок – «пока-ёкэ» – позволяет найти решение, делающее невозможной любую ошибку. Конфигурации окошка 1 и монтажного элемента А так изменены, что замена при монтаже даже теоретически невозможна.
Правила применения приемов защиты от ошибок
1. Как можно ближе подойти к источнику проблемы, туда, где проблема действительно возникла и где она снова может появиться.
241
2.Ввести сразу все необходимые виды контроля и меры предотвращения повторного появления проблемы.
3.При разработке и конструировании использовать сложные методы и техники устранения проблемы, а в производстве применять простые и быстрые решения.
4.Улучшения в производстве проводить быстро, без сложных анализов и таким образом, чтобы все люди были включены
врешение общих проблем и устранение несоответствий.
Дополнительная информация
1.Большинство устройств по защите от ошибок являются простыми и недорогими.
2.Программа по улучшению только тогда может быть успешной, когда все сотрудники – от операторов до старших менеджеров – пройдут обучение методам защиты от ошибок и будут напрямую участвовать в их внедрении.
3.Применение командного подхода к внедрению способов защиты от ошибок позволяет учитывать интересы как производственных подразделений, так и потребителя.
Достоинства метода. Последовательное применение различных способов и приемов предупреждения ошибок позволяет значи-
тельно сократить их число, что способствует снижению затрат и повышению удовлетворенности потребителей.
Недостатки метода. Встречающееся сопротивление при принудительном внедрении в действующее производство устройств по защитеотошибокчастосводитнанетусилияпоулучшениюпроцесса.
4.15. ИНТЕГРИРОВАННАЯ РАЗРАБОТКА ПРОДУКЦИИ И ПРОЦЕССОВ
Интегрированная разработка продукции и процессов
(Integrated Product and Process Development – IPPD) – метод управ-
ления и организации работ на промышленном производстве. Термин введен в США в 80-е гг. ХХ в. Метод применяется для оптимизации производства и повышения конкурентоспособности [99].
242
Цель метода– интегрированная разработка продукции и процессов. Это подход, направленный на интеграцию процесса производства продукта, благодаря которому все необходимые подпроцессы гармонично объединены. В результате происходит статистическое управление качеством, в котором объединены современные системы бухгалтерского учетаи модульноепроизводство продукции.
При этом подходе используются межфункциональные команды разработчиков в целях интегрированного и параллельного применения всех необходимых инструментов и методов для производства конкурентоспособной продукции. Управление проектами при помощи межфункциональных команд связано с тем, что ни одна команда не будет работать эффективно, если она действует сама по себе без связи с другими функциональными командами. С этим принципом тесно связана присущаяяпонскому менеджменту ротация.
4.16. «КАЙДЗЕН»
«Кайдзен» (от японских слов Kai – «изменение» и Zen – «хороший», «к лучшему») – японская философия, которая фокусируется на непрерывном совершенствовании процессов производства, вспомогательных бизнес-процессов и управления, а также всех аспектов жизни [53].
Впервые философия кайдзен была применена в ряде япон-
ских компаний (Toyotа, Nissan, Canon, Honda, Komatsu, Matsushita)
в период восстановления после Второй мировой войны и с тех пор распространилась по всему миру. Термин «кайдзен» стал широко известен благодаря книге Масааки Имаи (1986, Kaizen: The Key to Japan’s Competitive Success). Начиная с 1986 г. термин «кайдзен» был принят в качестве обозначения одной из ключевых концепций менеджмента.
Процесс совершенствования состоит во внесении множества маленьких улучшений, из которых складывается большой эффект. Западные компании обычно практикуют иной подход к совершенствованию (революционные изменения технологии), связанный
243
с отказом от постепенного совершенствования продукта, оборудования, технологии, производственных и организационных процессов. Зачем заниматься небольшими улучшениями, когда можно приобрести суперсовременное и сверхпроизводительное оборудование и за счет этого получить преимущество перед конкурентами. В отличие от такого западного подхода, кайдзен – это философия постепенного, эволюционного совершенствования.
Цель подхода – производство без потерь за счет постоянного улучшения и стандартизации производственных действий
ипроцессов.
Вяпонском языке слово кайдзен означает непрерывное совершенствование. Исходя из этой стратегии в процесс совершенствования вовлекаются все – от менеджеров до рабочих, причем ее реализация требует относительно небольших материальных затрат. Философия кайдзен предполагает, что наша жизнь в целом (трудовая, общественная и частная) должна быть ориентирована на постоянное улучшение.
Технология кайдзен. Существуют два подхода к непрерывным улучшениям:
–создание системы подачи кайдзен-предложений;
–проведение регулярных кайдзен-мероприятий.
Способы подачи предложений могут быть различными по форме. На японских предприятиях обычно применяется следующая система. Работник делает руководству предложение по улучшению. Это предложение рассматривается назначенной руководством рабочей группой. Далее эта группа принимает решение, внедрять данное предложение или нет. Затем руководство организует внедрение этого предложения в производственный процесс, а работник поощряется за выдвижение плодотворной идеи. При этом вы-
деляют кайдзен системы и кайдзен процесса. Кайдзен системы или потока, ориентированный на поток создания ценности в целом, это обычно зона ответственности менеджеров. Кайдзен процесса, ориентированный на отдельные процессы, это зона ответственности рабочих команд.
244
Принципы кайдзен
1.Фокус на клиентах. Для компании, использующей кайдзен, важно, чтобы их продукция (услуги) удовлетворяла потребности клиентов.
2.Непрерывные изменения – принцип, характеризующий саму суть кайдзен, т.е. непрерывные малые изменения во всех сферах организации: снабжении, производстве, сбыте, личностных взаимоотношениях и т.д.
3.Открытое признание проблем. Все проблемы открыто выносятся на обсуждение.
4.Пропаганда открытости. Малая степень обособленности между отделами и рабочими местами.
5.Создание рабочих команд. Каждый работник становится членом рабочей команды и соответствующего кружка качества.
6.Управление проектами при помощи межфункциональных команд. Ни одна команда не будет работать эффективно, если она действует только в одной функциональной группе. С этим принципом тесно связана присущая японскому менеджменту ротация.
7.Формирование «поддерживающих взаимоотношений». Для организации важны не только и не столько финансовые результаты, сколько вовлечённость работников в ее деятельность и хорошие взаимоотношения между работниками, поскольку это приведет организацию к высоким результатам.
8.Развитие по горизонтали. (Личный опыт должен становиться достоянием всей компании.)
9. Развитие самодисциплины – умение контролировать себя и уважать как самого себя, так и других работников и организацию
вцелом.
10.Самосовершенствование.
11.Информирование каждого сотрудника. Весь персонал должен быть полностью информирован о своей компании.
12.Делегирование полномочий каждому сотруднику – передача определённого объёма полномочий каждому сотруднику.
245
13.Управлять – значит начать с планирования и сравнить план с результатом.
14.Анализ происходящего на предприятии и действие на основе фактов.
15.Устранениеосновнойпричиныипредотвращениерецидивов.
16.Встраивание качества в процесс как можно раньше.
17.Стандартизация.
4.17. КАРТА ПОТОКА СОЗДАНИЯ ЦЕННОСТИ
Карта потока создания ценности – форма представления це-
почки стоимости компании для организации и оптимизации этого процесса. Это инструмент такого метода управления, как бережли-
вое производство [20].
Цель метода – оптимизация процессов производства, оказания услуг или поставки продукции клиентам.
Даже если компания только продает товары массового производства, необходимо грамотно организовать процесс предоставления услуги «продажа». Товар должен быть вовремя заказан, оплачен, доставлен, распакован, выставлен, оформлено место продажи; при покупке должны быть предложены товары-дополнения, консультации; выписаны документы; произведена проверка; оформлена гарантия; упаковка; выдача документов; купонов и бонусов; предложено и обеспечено обслуживание или ремонт; обеспечена реакция на запросы клиентов; приняты соответствующие претензии или благодарности. Это поток создания потребительской ценности.
Если такой прописанной системы работы с клиентами и их запросами в компании нет, то результатом, как правило, являются убытки и потеря потребителей. Только оптимизировав все процессы и операции потока, можно добиться полного и качественного удовлетворения потребителя. Выполнение этого принципа может обеспечить только хорошо отлаженный поток создания ценности. Кроме этого, компания добивается минимальной себестоимости продукта/услуг, используя при этом инструменты бережливого
246
производства. Карта потока создания ценности служит основой для построения такого оптимального процесса производства и оказания услуг клиентам компании.
На карте обязательно присутствует описание потребительской ценности и характеристик потребления. Обозначены информационные потоки от потребителя к поставщикам и количественные характеристики каждой операции. Операции выстроены в одну цепь. Если есть «притоки», они тоже могут быть обозначены или описаны отдельно (рис. 4.11).
Основное назначение карты потока создания ценности – оптимизация существующих процессов в организации и обучение сотрудников. Назовем основные отличия от других схем бизнеспроцессов.
1.Обучение и оптимизация в бережливом производстве происходит непрерывно, поэтому по каждому потоку всегда существуют две карты: «как есть» и «как должно быть».
2.Схема – результат командной работы всех участников процесса. Поэтому она и является актуальной основой для совершенствования.
3.На схеме обязательно описываются основные параметры потребительской ценности, влияющие на процесс (суть ценности, частота заказов, объем заказа).
4.Процесс рассматривается как «вытягивающий», т.е. процесс запускается только при поступлении заказа от потребителя.
5.Очень подробно описывается каждая операция и то, что происходит между операциями. На карту заносятся показатели, полностью или частично отсутствующие в других схемах описания процессов: время цикла, коэффициент эффективности производственного цикла, частота поставок, минимальное количество заказа, способ доставки, средний уровень запасов между операциями, время ожидания между операциями, время переналадки оборудования, готовность оборудования, размер партии, количество операторов, количество вариантов изделия, параметры упаковки, рабочее время, процент брака, информационные потоки.
247
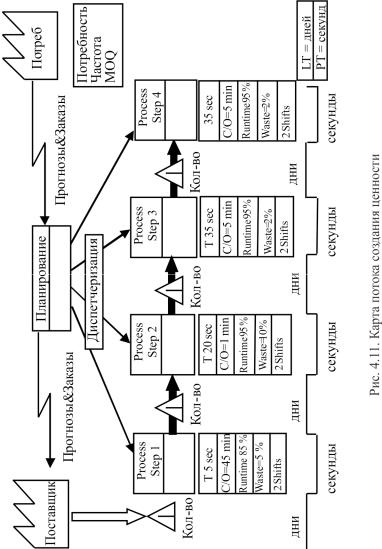
248
6. При достижении высокого уровня оптимизации внутри компании описывают и оптимизируют весь поток создания ценности от добычи сырья до конечного пользователя, т.е. карта потока может включать процессы, происходящие за пределами компании.
В бережливом производстве все, что не вносит вклад в создание ценности, считается потерями: лишние запасы, перемещения, ожидания, транспортировки, брак. На карте потока почти все потери запротоколированы. На потери тратятся ресурсы, материалы и время. Если устранить потери, то увеличится скорость процесса, сократятся расходы на материалы, ресурсы, оплату рабочего времени. При этом полностью сохранится и даже улучшится качество созданной ценности.
Технология составления карты потока создания ценно-
стей на примере оптимизации внутрицеховых процессов. Исходные данные:
–в цехе № 1 деталь подвергается трем процессам обработки на трех рабочих местах;
–на рабочем месте № 1 деталь отрезается по размеру;
–на рабочем месте № 2 деталь проходит токарную обработку;
–на рабочем месте № 3 детальпроходитфрезерную обработку;
–в цехе № 2 на рабочем месте № 4 деталь собирается в сборочную единицу и передается на склад готовой продукции.
Составление карты потока создания ценности начинается со склада готовой продукции и заканчивается рабочим местом № 1. Общая продолжительность производственного процесса обработки детали составляет 69 700 с. Процесс состоит из пятнадцати операций. Заметим, что оперативное время, т.е. время создания ценности детали, составляет 4 150 с. Это значит, что большая часть процесса выполняется непроизводительно. Производственные потери настолько велики, что исследуемый процесс имеет явную необходимость оптимизации во времени и пространстве. Самое значительное непроизводительное время выпадает на операцию хранения – она длится 56 000 с и занимает 80,3 % общего времени процесса.
249
На этой основе составляется карта потока создания ценности при параметрах будущего состояния производственного процесса обработки детали. При этом следует учитывать, что необходимо сократить выявленные потери в виде непроизводительных затрат времени, материальных ресурсов и пространства. С целью обобщения полученных результатов строится таблица целевых показателей, в которую заносятся данные параметров текущего состояния и будущего (табл. 4.1).
Таблица 4 . 1
Сравнительный анализ параметров текущего и будущего состояния производственного процесса
Параметры |
Ед. |
Текущее |
Будущее |
|
измер. |
состояние |
состояние |
||
|
||||
Время создания ценности |
с |
4150 |
3400 |
|
Транспортировка |
с |
4690 |
420 |
|
м |
325 |
50 |
||
|
||||
Контроль |
с |
1900 |
1850 |
|
Переналадка |
с |
2580 |
1500 |
|
Хранение |
с |
56 000 |
10 000 |
|
Общее время выполнения операции |
с |
69 700 |
17 170 |
|
Запасы |
шт. |
965 |
10 |
|
НЗП |
шт. |
250 |
20 |
|
Количество операторов |
чел. |
15 |
6 |
|
Экономический эффект |
|
|
|
Здесь возникает вопрос, за счет каких изменений могут быть получены улучшения производственного процесса. Единого рецепта успеха нет. Насколько каждая организация уникальна, настолько уникальны решения.
В приведенном примере результаты были достигнуты посредством того, что все рабочие места, задействованные в обработке детали, были выстроены в U-образную ячейку, которую территориально расположили в цехе № 1 (рис. 4.12).
250