
Логистика
..pdf
Рис. 1.7. Графическое отображение параметров моделирования работы системы с фиксированным размером заказа (три сбоя в поставках)
Таблица 1 . 7
Расчет параметров системы с фиксированным интервалом времени между заказами
№ |
Показатель |
Порядок расчета |
п/п |
|
|
1 |
Потребность S, шт. |
18 000 |
2 |
Интервал между заказами, дней |
260 : (18 000 : 750) = 11 |
3 |
Время поставки tп, дней |
4 |
4 |
Возможная задержка tзп, дней |
3 |
5 |
Экономический заказ, шт. |
750 |
6 |
Дневное потребление λ, шт./день |
18 000 : 260 = 69,2 |
7 |
Срок расходования заказа, дней |
750 : 69,2 = 10,8 |
8 |
Максимальное потребление за время постав- |
(3+4) · 69,2 = 484 |
|
ки, шт. |
|
9 |
Гарантийный запас, шт. |
3 · 69,2 = 208 |
10 |
Максимальный желательный запас, шт. |
208 + 750 = 958 |
11 |
Срок расходования по ПУ, дней |
(958 – 485) : 69,2 = 6,8 |
21

Рис. 1.8. Графическое отображение параметров системы с фиксированным интервалом времени между заказами
Рис. 1.9. Графическое отображение моделирования работы системы с фиксированным интервалом времени между заказами (определение времени заказа)
22
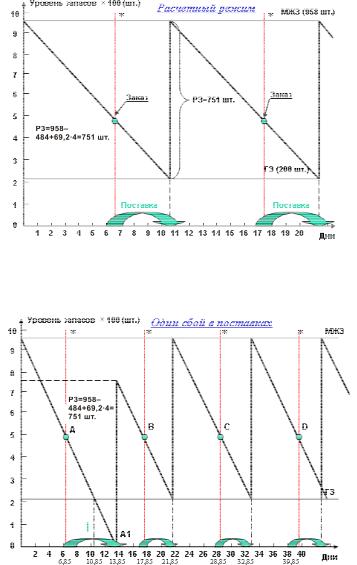
Рис. 1.10. Графическое отображение моделирования работы системы с фиксированным интервалом времени между заказами (расчетный режим)
Рис. 1.11. Графическое отображение моделирования работы системы с фиксированным интервалом времени между заказами
(один сбой в поставках)
23
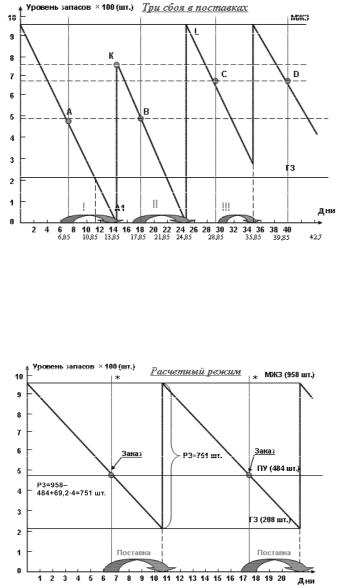
Рис. 1.12. Графическое отображение моделирования работы системы с фиксированным интервалом времени между заказами
(три сбоя в поставках)
Для системы с установленной периодичностью пополнения запасов до постоянного уровня используется комбинация параметров первых двух систем.
Рис. 1.13. Графическое отображение моделирования работы системы с установленной периодичностью пополнения запасов до постоянного уровня (расчетный режим)
24
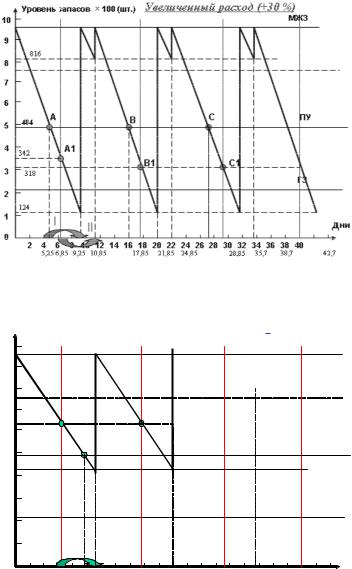
Рис. 1.14. Графическое отображение моделирования работы системы |
|||||||||||||||||||
с установленной периодичностью пополнения запасов до постоянного |
|||||||||||||||||||
|
|
|
|
|
|
уровня (увеличенный расход) |
|
|
|
|
|||||||||
|
Уровеньзапасов × 100 (шт.) Уменьшенный расход ( |
|
35 %) |
||||||||||||||||
10 |
|
|
|
|
L |
M |
|
|
|
|
|
|
|
|
|
МЖЗ |
|||
|
|
|
|
|
|
|
|
|
|
|
|
|
|
|
|||||
9 |
|
|
|
|
|
|
|
|
|
|
|
|
|
|
|
|
|
|
|
|
|
794 |
|
|
|
|
|
|
|
|
|
|
|
|
|
|
|
|
|
8 |
|
|
|
|
|
|
|
|
|
|
|
|
|
|
|
|
|
|
|
7 |
650 |
|
А |
|
|
|
B |
|
|
|
|
|
|
|
|
|
|
||
|
|
|
|
|
|
|
|
|
|
|
|
|
|
|
|||||
6 |
|
|
|
|
|
|
|
|
|
|
|
|
|
|
|
|
|
|
|
5 |
484 |
|
|
|
А1 |
|
|
|
|
|
|
|
|
|
|
|
|
ПУ |
|
|
|
|
|
|
|
|
|
|
|
|
|
|
|
|
|
|
|
||
|
|
|
|
|
|
|
|
|
|
|
|
|
|
|
|
|
|
|
|
|
470 |
|
|
|
|
|
|
|
|
|
|
|
|
|
|
|
|
|
|
4 |
|
|
|
|
|
|
|
|
|
|
|
|
|
|
|
|
|
|
|
3 |
|
|
|
|
|
|
|
|
|
|
|
|
|
|
|
|
|
|
ГЗ |
|
|
|
|
|
|
|
|
|
|
|
|
|
|
|
|
|
|
|
|
2 |
|
|
|
|
|
|
|
|
|
|
|
|
|
|
|
|
|
|
|
1 |
|
|
I |
|
|
|
|
|
|
|
|
|
|
|
|
|
|
|
Дни |
|
|
|
|
|
|
|
|
|
|
|
|
|
|
|
|
|
|
||
0 |
2 |
4 |
6 |
8 |
10 |
12 |
14 |
16 18 |
20 |
22 |
24 26 |
28 |
30 |
32 34 |
36 |
38 |
40 |
||
|
|||||||||||||||||||
|
|
|
6,85 |
10, 53 10,85 14,53 |
17,85 |
21,85 |
24,85 |
|
28,85 |
35,7 |
|
38,7 |
42,7 |
||||||
Рис. 1.15. Графическое отображение моделирования работы системы |
|||||||||||||||||||
с установленной периодичностью пополнения запасов до постоянного |
|||||||||||||||||||
|
|
|
|
|
уровня (уменьшенный расход) |
|
|
|
|
25
Обстоятельства, влияющие на выбор системы управления запасами:
1.Система с фиксированным размером заказа:
•большие издержки управления запасами;
•ограничения минимального размера закупки.
2.Система с фиксированным интервалом времени между заказами:
•территориальная близость поставщика;
•поставка в установленные сроки;
•использование услуг третьего лица для перевозки.
3.Система с установленной периодичностью пополнения запасов до постоянного уровня:
•незначительные издержки на управление запасами;
•необходимость быстрого реагирования на изменения сбыт
26

2. ЛОГИСТИКА СНАБЖЕНИЯ И ЗАКУПОК В СИСТЕМЕ
ХОЗЯЙСТВЕННОЙ ДЕЯТЕЛЬНОСТИ ПРЕДПРИЯТИЯ
2.1. Содержание функции материально>
технического обеспечения производства
Деятельность, связанная с планированием и поддержкой производственного процесса, требует составления графиков
икалендарных плановвыпуска продукции, хранения незавершенного производства, обработки, транспортировки и своевременного пополнения запасов материалов и комплектующих. Включает хранение запасовнапроизводственныхплощадках.
Главная задача – максимальная координация между производством и физическим распределением в пространственном
ивременном аспектах.
2.2. Система MRP – планирование
потребностей в сырье
Это планирование зависимой потребности в материалах (зависимый спрос).
Исходная информация:
•основной график производства;
•ведомость спецификации материалов для каждого продукта (комплектность);
•учетная документация по запасам продуктов и мате-
риалов на складе.
Основной график производства должен быть разработан заранее (основной недостаток, увеличивающий затраты на реализацию и снижающий возможность рыночного маневра).
27

Ведомость спецификации материалов – наличие информации о каждой единице материалов и ее положении в иерархии конструкции изделия. Для этих целей используются цифровые индексы. Уровень готового изделия имеет индекс «0», уровень узлов – индекс «1» ит.д. Дополнительно указывается комплектность.
Пример планирования поставок с использованием MRP
Компания получила заказ на изготовление 14 тележек через 5 недель. Тележка состоит из кузова (1), колес (4) и комплекта крепежа. На складе имеется 2 готовых тележки, 3 кузова, 12 колес и 3 комплекта крепежа. Технологический процесс изготовления тележек, независимо от количества, занимает 2 недели. Время получения кузовов – 1 неделя с момента направления заказа, колес – 2 недели, крепежа – 1 неделя.
Структурная схема изделия показана на рис. 2.1.
Рис. 2.1. Структурная схема изделия
Обобщенная процедура MRP показана схематически на рис. 2.2
Рис. 2.2. Обобщенная процедура MRP
Процедура расчета выполняется, как правило, в табличном виде.
28
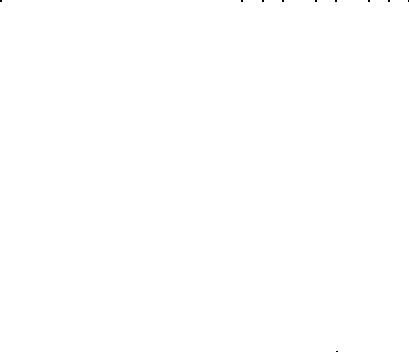
Количество таблиц соответствует количеству номенклатурных позиций запасов (рис. 2.3–2.6). Валовая потребность определяется исходя из текущего производственного задания. Срок по валовой потребности устанавливается в соответствии со сроком сдачи готового изделия.
Информация по исходному запасу берется из ведомостей складского учета и другой документации в соответствии с процедурой MRP.
Чистая потребность = валовая потребность – имеющийся запас – размещенные заказы
Неделя |
1 |
|
2 |
|
3 |
|
4 |
|
5 |
|
|
|
6 |
7 |
|||||
Валовая потребность |
|
|
|
|
|
|
|
|
|
|
14 |
|
|
|
|
|
|||
Исходный запас |
2 |
|
2 |
|
2 |
|
2 |
|
2 |
|
|
|
|
|
|
||||
Чистая потребность |
|
|
|
|
|
|
|
|
|
|
12 |
|
|
|
|
|
|||
Начало сборки |
|
|
|
|
|
12 |
|
|
|
|
|
|
|
|
|
|
|
|
|
Плановое завершение |
|
|
|
|
|
|
|
|
|
|
12 |
|
|
|
|
|
|||
Рис. 2.3. Процедура расчетов по MRP. Уровень «О». Тележки |
|
|
|||||||||||||||||
Валовая потребность = 9 · 1 = 9 |
|
|
|
|
|
|
|
|
|
|
|
|
|
|
|
|
|
|
|
Неделя |
|
|
|
1 |
|
2 |
|
3 |
|
4 |
|
|
5 |
|
6 |
7 |
|||
Валовая потребность |
|
|
|
|
|
|
|
12 |
|
|
|
|
|
|
|
|
|
|
|
Исходный запас |
|
|
|
3 |
|
3 |
|
3 |
|
|
|
|
|
|
|
|
|
|
|
Чистая потребность |
|
|
|
|
|
|
|
9 |
|
|
|
|
|
|
|
|
|
|
|
Начало сборки |
|
|
|
|
|
9 |
|
|
|
|
|
|
|
|
|
|
|
|
|
Плановое завершение |
|
|
|
|
|
|
|
9 |
|
|
|
|
|
|
|
|
|
|
|
Рис. 2.4. Процедура расчетов по MRP. Уровень «1». Кузова |
|
|
|
||||||||||||||||
Валовая потребность = 12 · 4 = 48 |
|
|
|
|
|
|
|
|
|
|
|
|
|
|
|
|
|
|
|
Неделя |
|
1 |
|
|
2 |
|
3 |
|
|
4 |
|
|
5 |
|
6 |
|
7 |
||
Валовая потребность |
|
|
|
|
|
|
|
48 |
|
|
|
|
|
|
|
|
|
|
|
Исходный запас |
|
12 |
|
|
12 |
|
12 |
|
|
|
|
|
|
|
|
|
|
||
Чистая потребность |
|
|
|
|
|
|
|
36 |
|
|
|
|
|
|
|
|
|
|
|
Начало сборки |
|
36 |
|
|
|
|
|
|
|
|
|
|
|
|
|
|
|
|
|
Плановое завершение |
|
|
|
|
|
|
|
36 |
|
|
|
|
|
|
|
|
|
|
Рис. 2.5. Процедура расчетов по MRP. Уровень «1». Колеса
29

Валовая потребность = 9 · 1 = 9
Неделя |
1 |
2 |
3 |
4 |
5 |
6 |
7 |
Валовая потребность |
|
|
12 |
|
|
|
|
Исходный запас |
3 |
3 |
3 |
|
|
|
|
Чистая потребность |
|
|
9 |
|
|
|
|
Начало сборки |
|
9 |
|
|
|
|
|
Плановое завершение |
|
|
9 |
|
|
|
|
Рис. 2.6. Процедура расчетов по MRP. Уровень «1». Крепеж
В результате менеджеры получают информацию о необходимых действиях и сроках их выполнения (аналогия с цикловым графиком сборки сложного изделия в условиях позаказного метода организации производственных процессов). Существенным недостатком метода является отсутствие включения факторов оптимизациизагрузкипроизводственныхмощностей ирежимов поставки.
Расширение возможностей MRP
MRP подчиняется основному производственному графику, который на практике часто меняется. Вследствие этого операционные возможности поставок не справляются с изменившимся спросом на материалы.
Возникает необходимость введения обратной связи от MRP к планированию использования мощностей (производственных ресурсов) MRP II.
Особенности концепции MRP II
MRP II – Manufactory Resource Planning (система производ-
ственного планирования, или система планирования производственных ресурсов) – это расширенная версия MRP с обратной связью.
Объектыпланирования – всересурсыпромышленнойфирмы. Принимаемые решения должны быть взаимосвязаны
с бюджетом, планируемыми инвестициями и т.д.
Достоинства системы MRP II состоят, в частности, в сокращении производственной составляющей логистического цикла, сокращении запасов и других преимуществах гибких систем планирования и управления.
30