
- •CONTENTS
- •FOREWORD
- •INTRODUCTION
- •SUMMARY OF CHANGES
- •100 GENERAL
- •102 DESIGN CRITERIA
- •103 CRITERIA FOR PRESSURE DESIGN OF PIPING COMPONENTS
- •104 PRESSURE DESIGN OF COMPONENTS
- •105 PIPE
- •106 FITTINGS, BENDS, AND INTERSECTIONS
- •107 VALVES
- •108 PIPE FLANGES, BLANKS, FLANGE FACINGS, GASKETS, AND BOLTING
- •110 PIPING JOINTS
- •111 WELDED JOINTS
- •112 FLANGED JOINTS
- •113 EXPANDED OR ROLLED JOINTS
- •114 THREADED JOINTS
- •115 FLARED, FLARELESS, AND COMPRESSION JOINTS, AND UNIONS
- •116 BELL END JOINTS
- •117 BRAZED AND SOLDERED JOINTS
- •118 SLEEVE COUPLED AND OTHER PROPRIETARY JOINTS
- •119 EXPANSION AND FLEXIBILITY
- •120 LOADS ON PIPE SUPPORTING ELEMENTS
- •121 DESIGN OF PIPE SUPPORTING ELEMENTS
- •122 DESIGN REQUIREMENTS PERTAINING TO SPECIFIC PIPING SYSTEMS
- •123 GENERAL REQUIREMENTS
- •124 LIMITATIONS ON MATERIALS
- •125 MATERIALS APPLIED TO MISCELLANEOUS PARTS
- •126 MATERIAL SPECIFICATIONS AND STANDARDS FOR STANDARD AND NONSTANDARD PIPING COMPONENTS
- •127 WELDING
- •128 BRAZING AND SOLDERING
- •129 BENDING AND FORMING
- •130 REQUIREMENTS FOR FABRICATING AND ATTACHING PIPE SUPPORTS
- •131 WELDING PREHEAT
- •132 POSTWELD HEAT TREATMENT
- •133 STAMPING
- •135 ASSEMBLY
- •136 INSPECTION AND EXAMINATION
- •137 PRESSURE TESTS
- •138 GENERAL
- •139 OPERATION AND MAINTENANCE PROCEDURES
- •140 CONDITION ASSESSMENT OF CPS
- •141 CPS RECORDS
- •Figures
- •Tables
- •102.4.3 Longitudinal Weld Joint Efficiency Factors
- •MANDATORY APPENDICES
- •Table A-4 Nickel and High Nickel Alloys
- •Chart D-1 Flexibility Factor, k, and Stress Intensification Factor, i
- •Chart D-2 Correction Factor, c
- •Fig. D-1 Branch Connection Dimensions
- •NONMANDATORY APPENDICES
- •INDEX
- •ASME B31.1 INTERPRETATIONS VOLUME 45
- •B31.1 — Cases No. 35
B31.1 — Cases No. 35
A Case is the official method of handling a reply to an inquiry when study indicates that the Code wording needs clarification, or when the reply modifies the existing requirements of the Code or grants permission to use new materials or alternative constructions.
ASME has agreed to publish Cases issued by the B31 Committee concerning B31.1 as part of the update service to B31.1. The text of proposed new and revised Cases appear on the ASME Web site at http://cstools.asme.org/csconnect/CommitteePages.cfm for public review. New and revised Cases, as well as announcements of annulments, then appear in the next update. As of the 1992 and later editions, all Cases currently in effect at the time of publication of an edition are included with it as an update.
This update, Cases No. 35, which is included after the last page of the 2010 Edition and the Interpretations Volume 45 that follow, contains the following Cases:
175 |
176 |
177 |
182 |
183 |
The page numbers for the Cases supplements start with C-1 and continue consecutively. The Cases affected by this supplement are as follows:
Page |
Location |
Change |
C-4 |
Case 176 |
Annulled |
C-5 |
Case 177 |
Annulled |
C-8 |
Case 183 |
In the Reply, paras. (d) and (f) revised |
--`,,```````,,```,`,`,,,,`,`,`,`-`-`,,`,,`,`,,`---
C-1
Copyright ASME International
Provided by IHS under license with ASME
No reproduction or networking permitted without license from IHS
ASME B31.1 CASES
B31 CASE 175
ASTM B 16 (UNS C36000) and B 453 (UNS C35300) in ASME B31.1 Construction
Approval Date: September 12, 2003
Reaffirmation Date: August 7, 2007
Inquiry: May brass alloys rods and bars conforming to ASTM B 16 (UNS C36000) and B 453 (UNS C35300) be used for ASME B31.1 construction?
Reply: It is the opinion of the Committee that brass alloys rods and bars conforming to ASTM B 16 (UNS C36000) and B 453 (UNS C35300) may be used for B31.1 construction provided:
(a)These materials shall not be used for boiler external piping except where specifically permitted by Section I. See para. 100.1.2(A).
(b)The maximum permissible design temperature shall not exceed 406¡F (208¡C).
(c)The maximum permissible size of finished product shall not exceed NPS 3.
(d)These materials shall not be welded.
(e)These materials shall be used only in the soft anneal (O60) temper.
(f)Limitations for use of these materials for flammable liquids and gases shall be in accordance with paras. 122.7, 122.8, and 124.7.
(g)Material conforming to ASTM B 16 alloy UNS C36000 shall not be used in primary pressure relief valve applications.
(h)A representative finished model of each product size and design shall be tested to determine the presence of residual stresses which might result in failure of individual parts due to stress corrosion cracking. Tests shall be conducted in accordance with ASTM B 154 or ASTM B 858M.
(i)Materials shall be tested to determine the presence of residual stresses which might result in failure of individual parts due to stress corrosion cracking. Tests shall be conducted in accordance with ASTM B 154 or ASTM B 858M. The test frequency shall be as specified in B 249.
(j)Heat treatment after fabrication or forming is neither required nor prohibited.
(k)The allowable stress values shown in Table 1 shall apply. These allowable stress values are based on a tensile strength factor of safety 4.0. These stress values may be interpolated to determine values for intermediate temperatures.
(l)The specified minimum tensile and yield strengths shown in Table 1 shall apply.
(m)This Case number shall be referenced in the documentation and marking of the material and recorded on the ManufacturerÕs Data Report.
--`,,```````,,```,`,`,,,,`,`,`,`-`-`,,`,,`,`,,`---
C-2
Copyright ASME International
Provided by IHS under license with ASME
No reproduction or networking permitted without license from IHS

ASME B31.1 CASES
Table 1
|
|
|
|
|
|
|
|
Maximum Allowable Stress Values in Tension, ksi, |
|
|||||
|
|
|
Specified |
Specified |
|
|
|
for Metal Temperature, °F, Not Exceeding |
|
|
||||
|
|
|
E |
|
|
|
|
|
|
|
|
|
||
|
|
|
|
|
|
|
|
|
|
|
|
|||
|
UNS |
Size or |
Minimum |
Minimum |
|
−20 |
|
|
|
|
|
|
|
|
Spec. |
Alloy |
Thickness, |
Tensile, |
Yield, |
or |
|
to |
|
|
|
|
|
|
|
No. |
No. |
in. |
ksi |
ksi |
F |
100 |
150 |
200 |
250 |
300 |
350 |
400 |
450 |
|
|
|
|
|
|
|
|
|
|
|
|
|
|
|
|
Rod |
|
|
|
|
|
|
|
|
|
|
|
|
|
|
B 16 |
C36000 |
1 and under |
48 |
20 |
1.00 |
13.3 |
12.6 |
12.0 |
11.5 |
11.1 |
10.7 |
5.3 |
2.0 |
|
|
C36000 |
Over 1 to 2 |
44 |
18 |
1.00 |
12.0 |
11.3 |
10.8 |
10.4 |
10.0 |
9.7 |
5.3 |
2.0 |
|
|
C36000 |
Over 2 |
40 |
15 |
1.00 |
10.0 |
9.4 |
9.0 |
8.7 |
8.3 |
8.1 |
5.3 |
2.0 |
|
B 453 |
C35300 |
Under 1⁄2 |
46 |
16 |
1.00 |
10.7 |
10.1 |
9.6 |
9.2 |
8.9 |
8.6 |
5.3 |
2.0 |
|
|
C35300 |
1⁄2 to 1 |
44 |
15 |
1.00 |
10.0 |
9.4 |
9.0 |
8.7 |
8.3 |
8.1 |
5.3 |
2.0 |
|
|
C35300 |
Over 1 |
40 |
15 |
1.00 |
10.0 |
9.4 |
9.0 |
8.7 |
8.3 |
8.1 |
5.3 |
2.0 |
|
Bar |
|
|
|
|
|
|
|
|
|
|
|
|
|
|
B 16 |
C36000 |
1 and under |
44 |
18 |
1.00 |
12.0 |
11.3 |
10.8 |
10.4 |
10.0 |
9.7 |
5.3 |
2.0 |
|
|
C36000 |
Over 1 |
40 |
15 |
1.00 |
10.0 |
9.4 |
9.0 |
8.7 |
8.3 |
8.1 |
5.3 |
2.0 |
|
|
|
|
|
|
|
|
|
|
|
|
|
|
|
|
--`,,```````,,```,`,`,,,,`,`,`,`-`-`,,`,,`,`,,`---
C-3
Copyright ASME International
Provided by IHS under license with ASME
No reproduction or networking permitted without license from IHS
ASME B31.1 CASES
B31 CASE 176
Use of 20Cr–18Ni–6Mo (UNS S31254) for ASME B31.1 Constructions
Annulment Date: July 12, 2010
Reason for Annulment: Code Case was incorporated into the Code.
--`,,```````,,```,`,`,,,,`,`,`,`-`-`,,`,,`,`,,`---
C-4
Copyright ASME International
Provided by IHS under license with ASME
No reproduction or networking permitted without license from IHS
ASME B31.1 CASES
B31 CASE 177
Alternate Rules for Preheat of P-No. 5B Materials
Annulment Date: September 23, 2009
Reason for Annulment: Code Case was incorporated into the Code.
C-5
--`,,```````,,```,`,`,,,,`,`,`,`-`-`,,`,,`,`,,`---
Copyright ASME International
Provided by IHS under license with ASME
No reproduction or networking permitted without license from IHS
ASME B31.1 CASES
B31 CASE 182
Use of 1.15Ni–0.65Cu–Mo–Cb in ASME B31.1 Construction
Approval Date: November 10, 2006
Inquiry: May A 335-05a P36 Class 1 and Class 2, and A 182-05a F36 Class 1 and Class 2, be used for B31.1 construction?
Reply: It is the opinion of the Committee that A 335-05a P36 Class 1 and Class 2, and A 182-05a F36 Class 1 and Class 2, may be used for B31.1 construction provided that all of the following requirements are met:
(a)All applicable requirements of ASME B31.1 shall be met.
(b)The maximum allowable stress values and other data shown in Table 1 or 1M apply.
(c)Separate weld procedure and performance qualifications shall apply for both classes of this material. The postweld heat treatment of the Class 1 and Class 2 material shall be in accordance with the rules specified in Table 2 or 2M.
(d)After either cold bending to strains in excess of 5% or any hot bending of this material, the full length of the component shall be heat treated in accordance with the requirements specified in the material specification. (See PG-19 of Section I for method for calculating strain.)
(e)Postweld heat treatment is mandatory under all conditions.
(f) This Case number shall be referenced in the documentation and marking of the material, and recorded on the ManufacturerÕs Data Report (if applicable).
CAUTIONARY NOTE: Corrosion fatigue occurs by the combined actions of cyclic loading and a corrosive environment. In piping systems, corrosion fatigue is more likely to occur in portions of water systems with low strain rates (<1.0%/sec), higher temperatures [above 300°F (150°C)], and higher dissolved oxygen (>0.04 ppm), with a preference toward regions with increased local stresses. While the mechanisms of crack initiation and growth are complex and not fully understood, there is consensus that the two major factors are strain and waterside environment. Strain excursions of sufficient magnitude to fracture the protective oxide layer play a major role. In terms of the waterside environment, high levels of dissolved oxygen and pH excursions are known to be detrimental. Historically, the steels applied in these water-touched components have had the minimum specified yield strengths in the range of 27 ksi to 45 ksi (185 MPa to 310 MPa) and minimum specified tensile strengths in the range of 47 ksi to 80 ksi (325 MPa to 550 MPa). As these materials are supplanted by higher strength steels, some have concern that the higher design stresses and thinner wall thicknesses will render components more vulnerable to failures by corrosion fatigue. Thus, when employing such higher strength steels for water systems, it is desirable to use “best practices” in design by minimizing localized strain concentrations, in control of water chemistry and during lay-up by limiting dissolved oxygen and pH excursions, and in operation by conservative startup, shutdown, and turndown practices.
C-6
--`,,```````,,```,`,`,,,,`,`,`,`-`-`,,`,,`,`,,`---
Copyright ASME International
Provided by IHS under license with ASME
No reproduction or networking permitted without license from IHS
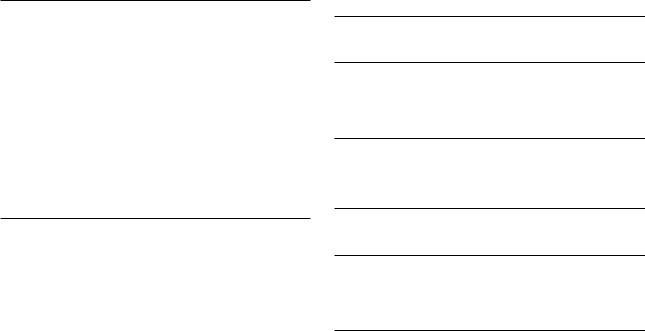
ASME B31.1 CASES
Table 1 Maximum Allowable Stress Values
|
|
Maximum Allowable |
|
For Metal Temperature |
|
Stress Values, ksi |
|
|
|
|
|
|
|
|
|
Not Exceeding, °F |
Class 1 |
Class 2 |
|
|
|
|
|
−20 to 100 |
25.7 |
27.3 |
|
200 |
25.7 |
27.3 |
|
300 |
25.1 |
26.6 |
|
400 |
25.1 |
26.6 |
|
500 |
25.1 |
26.6 |
|
600 |
25.1 |
26.6 |
|
700 |
25.1 |
26.6 |
|
|
|
|
|
Table 2 Requirements for Postweld Heat Treatment (PWHT)
|
PWHT |
|
|
Temperature, |
|
Class |
°F |
Holding Time |
11,100–1,200 2 in. and less thickness: 1 hr/in., 15 min
minimum
Over 2 in.: add 15 min for each additional inch of thickness
21,000–1,150 1 hr/in., 1⁄2 hr min.
Table 1M Maximum Allowable Stress Values
|
|
Maximum Allowable |
|
For Metal Temperature |
|
Stress Values, MPa |
|
|
|
|
|
|
|
|
|
Not Exceeding, °C |
Class 1 |
Class 2 |
|
|
|
|
|
−30 to 40 |
177 |
188 |
|
100 |
177 |
188 |
|
150 |
173 |
183 |
|
200 |
173 |
183 |
|
250 |
173 |
183 |
|
300 |
173 |
183 |
|
350 |
173 |
183 |
|
371 |
173 |
183 |
|
|
|
|
|
Table 2M Requirements for Postweld Heat Treatment (PWHT)
|
PWHT |
|
|
Temperature, |
|
Class |
°C |
Holding Time |
1595–650 50 mm and less thickness: 1 hr/25 mm,
15 min minimum
Over 50 mm: add 15 min for each additional 25 mm of thickness
2540–620 1 hr/25 mm, 1⁄2 hr min.
---`,,`,,`,`,,`-`-`,,```````,,```,`,`,,,,`,`,`,`--
C-7
Copyright ASME International
Provided by IHS under license with ASME
No reproduction or networking permitted without license from IHS
ASME B31.1 CASES
B31 CASE 183
Use of Seamless 9Cr–2W in ASME B31.1 Construction
Approval Date: April 26, 2007
Inquiry: May seamless 9CrÐ2W tubes, pipes, and forgings, with the chemical analysis shown in Table 1 and minimum mechanical properties as shown in Table 2 that otherwise conform to the specifications listed in Table 3, be used for ASME B31.1 construction?
Reply: It is the opinion of the Committee that seamless 9CrÐ2W tubes, pipes, and forgings, with the chemical analysis shown in Table 1 and minimum mechanical properties as shown in Table 2 that otherwise conform to the specifications listed in Table 3, may be used for ASME B31.1 construction provided the following requirements are met:
(a)The material shall be austenitized within the temperature range of 1,900¡F to 1,975¡F (1 040¡C to 1 080¡C), followed by air cooling or accelerated cooling, and tempered within the range of 1,350¡F to 1,470¡F (730¡C to 800¡C).
(b)The material shall not exceed a Brinell hardness number of 250 (Rockwell C 25).
(c)The maximum allowable stress values for the material shall be those given in Table 4. Maximum temperature of application shall be limited to 1,150¡F
(621¡C), except that tubing used in applications up to and including 31Ú2 in. (89 mm) outside diameter may be used up to 1,200¡F (649¡C).
(d)Separate weld procedure qualification shall be conducted. For the purpose of performance qualifications, the material shall be considered P-No. 15E,
Group 1. The procedure and performance qualifications shall be conducted in accordance with Section IX. Postweld heat treatment for this material is mandatory, and the following rule shall apply: The PWHT requirements shall be those given for P-No. 15E, Group 1 materials in Table 132.
(e)Except as provided in para. (f), if during the manufacturing any portion of the component is heated to a temperature greater than 1,470¡F (800¡C), then the component must be reaustenitized and retempered in its entirety in accordance with para. (a), or that portion of the component heated above 1,470¡F (800¡C), including the heat-affected zone created by the local heating, must be replaced, or must be removed, reaustenitized, and retempered, and then replaced in the component.
(f)If the allowable stress values to be used are less than or equal to those provided in Table 1A of Section II, Part D for Grade 9 (SA-213 T9, SA-335 P9, or equivalent product specifications) at the design temperature, then the requirements of para. (e) may be waived, provided that the portion of the component heated to a temperature greater than 1,470¡F (800¡C) is reheat treated within the temperature range 1,350¡F to 1,425¡F (730¡C to 775¡C).
(g)This Case number shall be shown on the ManufacturerÕs Data Report.
(h)This Case number shall be shown in the material certification and marking of the material.
---`,,`,,`,`,,`-`-`,,```````,,```,`,`,,,,`,`,`,`--
C-8
Copyright ASME International
Provided by IHS under license with ASME
No reproduction or networking permitted without license from IHS

ASME B31.1 CASES
Table 1 Chemical Requirements
Element |
Composition Limits, % |
|
|
Carbon |
0.07–0.13 |
Manganese |
0.30–0.60 |
Phosphorus, max. |
0.020 |
Sulfur, max. |
0.010 |
Silicon, max. |
0.50 |
Chromium |
8.50–9.50 |
Molybdenum |
0.30–0.60 |
Tungsten |
1.50–2.00 |
Nickel, max. |
0.40 |
Vanadium |
0.15–0.25 |
Columbium |
0.04–0.09 |
Nitrogen |
0.030–0.070 |
Aluminum, max. |
0.02 |
Boron |
0.001–0.006 |
Titanium, max. |
0.01 |
Zirconium, max. |
0.01 |
|
|
Table 2 Mechanical Property Requirements
Property |
Min. Value |
|
|
|
|
Tensile strength |
90 |
ksi |
Yield strength |
64 |
ksi |
Elongation in 2 in. [Note (1)] |
20% |
|
|
|
|
NOTE:
(1) For longitudinal strip tests, a deduction from the basic values of 1.00% for each 1⁄32-in. decrease in wall thickness below
5⁄16 in. shall be made. Below are the computed minimum elongation values for each 1⁄32-in. decrease in wall thickness. Where the wall thickness lies between two values shown below, the minimum elongation value shall be determined by the following equation:
E p 32t + 10.0
where
E p elongation in 2 in., %
t p actual thickness of specimen, in.
|
|
|
|
Elongation in 2 in., |
|
|
Wall Thickness, in. |
|
min., % |
|
|
|
5Ú16 (0.312) |
20.0 |
|
||
|
9Ú32 (0.281) |
19.0 |
|
||
|
1Ú4 (0.250) |
18.0 |
|
||
|
7Ú32 (0.219) |
17.0 |
|
||
|
3Ú16 (0.188) |
16.0 |
|
||
|
5Ú32 |
(0.156) |
15.0 |
|
|
|
1Ú8 (0.125) |
14.0 |
|
||
|
3Ú32 |
(0.094) |
13.0 |
|
|
|
1Ú16 |
(0.062) |
12.0 |
|
|
|
0.062 to 0.035, excl. |
11.6 |
|
||
|
0.035 to 0.022, excl. |
10.9 |
|
||
|
0.022 to 0.015, incl. |
10.6 |
|
||
|
|
|
|
|
|
Table 3 |
Specifications |
Product Form |
Spec. No. |
|
|
Forgings |
SA-182 |
Forged pipe |
SA-369 |
Pipe |
SA-335 |
Tube |
SA-213 |
|
|
Table 4 Maximum Allowable Stress Values for Tube and Pipe
|
|
Maximum Allowable Stress |
|
|
|
|
Values, ksi |
|
|
|
|
For Metal Temperature |
|
|
Forgings, Pipe, |
Not Exceeding, °F |
Tube |
Forged Pipe |
|
|
|
|
|
−20 to 100 |
25.7 |
25.7 |
|
200 |
25.7 |
25.7 |
|
300 |
25.3 |
25.3 |
|
400 |
24.5 |
24.5 |
|
500 |
23.8 |
23.8 |
|
600 |
23.2 |
23.2 |
|
650 |
22.8 |
22.8 |
|
700 |
22.4 |
22.4 |
|
750 |
21.9 |
21.9 |
|
800 |
21.4 |
21.4 |
|
850 |
20.8 |
20.8 |
|
900 |
20.1 |
20.1 |
|
950 |
19.2 |
19.2 |
|
1,000 |
18.3 |
18.3 |
|
1,050 |
16.1 |
15.7 |
|
1,100 |
12.3 |
12.0 |
|
1,150 |
8.9 |
8.6 |
|
1,200 |
5.9 |
5.6 |
|
|
|
|
|
GENERAL NOTE: The allowable stress values are based on the revised criterion for tensile strength at temperature divided by 3.5, where applicable.
C-9
--`,,```````,,```,`,`,,,,`,`,`,`-`-`,,`,,`,`,,`---
Copyright ASME International
Provided by IHS under license with ASME
No reproduction or networking permitted without license from IHS
--`,,```````,,```,`,`,,,,`,`,`,`-`-`,,`,,`,`,,`---
INTENTIONALLY LEFT BLANK
Copyright ASME International
Provided by IHS under license with ASME
No reproduction or networking permitted without license from IHS
INTENTIONALLY LEFT BLANK
-`-`,,```````,,```,`,`,,,,`,`,`,`-- |
permitted without license from IHS |
No reproduction or networking`,,`,,`,`,,` |
|
Copyright ASME International |
|
Provided by IHS under license with ASME |
|
--- |
|
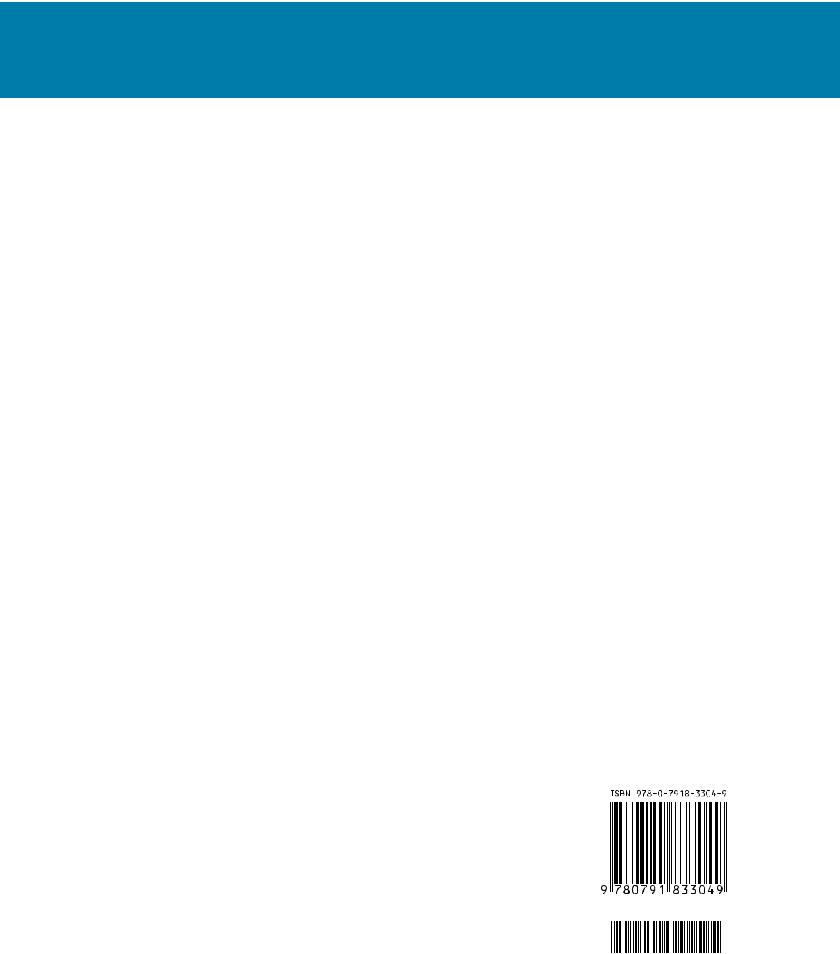
ASME B31.1-2010
A05810
--`,,```````,,```,`,`,,,,`,`,`,`-`-`,,`,,`,`,,`---
Copyright ASME International
Provided by IHS under license with ASME
No reproduction or networking permitted without license from IHS