
Учебное пособие 800490
.pdf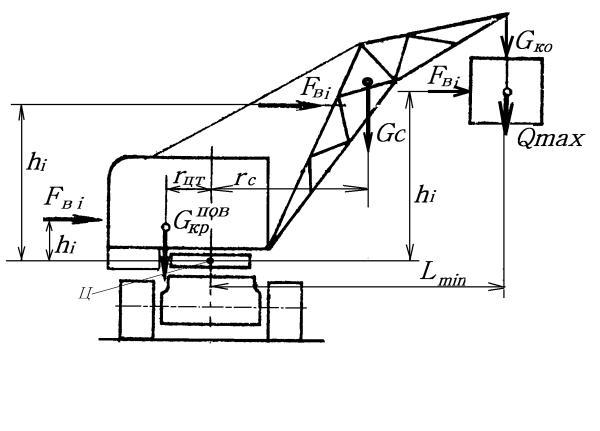
|
Рис. 3.10. Схема нагружения крана расчетными силами при определении |
|
|
|
момента сопротивления повороту от сил трения в ОПУ |
Mвр |
ф пов |
– фронтальный момент сил ветра рабочего состояния, действующий только на |
|
поворотную часть крана (включая стрелу и груз) относительно точки Ц ОПУ в плоскости подвеса стрелы. Mврф пов = Σ(Fврфi· hi).
Значения Fфвр принимают по данным таблицы общего расчета крана для поворотных частей крана, включая стрелу и груз;
hi – расстояния от геометрических центров фронтальных площадей поворотных частей крана до плоскости, проходящей через центры тел качения ОПУ;
rцт – расстояние от оси вращения крана до центра тяжести поворотной платформы с механизмами.
Знак «+» в формуле (3.4) принимают при расположении центров тяжести поворотной платформы и стрелы по одну сторону от оси вращения крана; знак « - » - по разные стороны.
Сопротивление вращению от давления ветра Мвс определяют в соответствии с расчетной схемой (рис. 3.11). Статическую составляющую ветровой нагрузки, действующую на
каждый расчетный элемент крана, определяют по формуле |
|
Fвi = qрi · Sбрi · kс, Н, |
(3.5) |
где qрi – распределенное давление ветра на элемент крана в зоне высоты до 10 м;
kс – коэффициент сплошности конструкции; kс≈0,4 для ферм из прямоугольных
профилей; kс≈0,3 для ферм из труб; kс≈1,3 для механизмов; kс≈ 1 для кабин и противовесов;
Sбрi – площадь брутто i-го расчетного элемента, ограниченная контуром его конструкции. Ее принимают по эскизному чертежу, разработанному в результате общего расчета крана.
Распределенное давление ветра на каждый элемент крана вычисляют по формуле |
|
qрi = q0 ·ki · ci, Па, |
(3.6) |
71
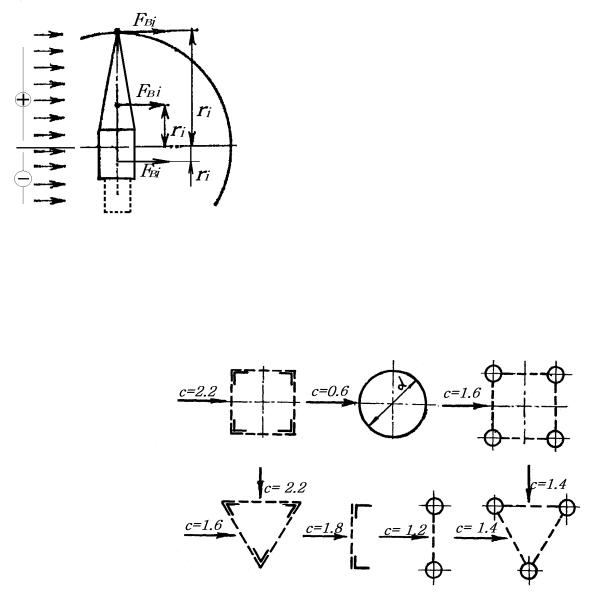
где q0 = 125 Па - скоростной нормативный напор ветра рабочего состояния независимо от места установки для строительных и самоходных кранов общего назначения.
ki - коэффициент, учитывающий изменение динамического давления ветра по высоте, принимаемый по табл. 3.1.
Таблица 3.1 Коэффициент изменения динамического давления ветра по высоте сооружения
Высота элемента над уровнем земли, м |
10 |
20 |
40 |
60 |
100 |
200 |
350 |
Коэффициент k |
1 |
1,25 |
1,55 |
1,75 |
2,10 |
2,60 |
3,10 |
Рис. 3.11. Расчетная схема для
определения момента сопротивления повороту от сил ветрового давления (в плане)
ci – коэффициент аэродинамической силы. Величину аэродинамического коэффициента в зависимости от вида конструкции и направления действия ветра можно принять
по рис. 3.12. |
|
Наветренную площадь груза можно |
принять по |
табл.3.2. |
|
Максимальный расчетный ветровой момент сопротив- |
|
ления повороту определяют по формуле |
|
Мвс = Σ(± Fвi ) ri, Н·м. |
(3.7) |
Знак «+» или «-» силы ветрового давления принимают в зависимости от расположения относительно оси вращения ветровой площади (см. рис. 3.11). Если величина получается отрицательной, то ее в дальнейших расчетах используют как положительную.
Рис. 3.12. Схемы поперечных сечений типичных элементов некоторых
крановых конструкций и их аэродинамические коэффициенты
72
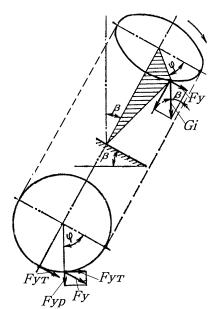
Таблица 3.2
Расчетная наветренная площадь грузов
Qмах, т |
2,0 |
3,2 |
5,0 |
10,0 |
16,0 |
20,0 |
25,0 |
32,0 |
63,0 |
100,0 |
Sбр, м² |
4,0 |
5,6 |
7,1 |
10,0 |
14,0 |
16,0 |
18,0 |
20,0 |
28,0 |
36,0 |
Момент сопротивления вращению Мус при расположении крана на опорной поверхности с уклоном β определяют в соответствии с расчетной схемой рис. 3.13 по формуле
Рис. 3.13. Схема для расчета сил
сопротивления повороту при расположении крана на уклоне
Мус = Σ(±Gi · ri ) · sin β · sin φ. |
(3.8) |
В этой формулеβ° – угол наклона опорной поверхности крана к горизонту; φ° – угол поворота продольной плоскости крана к плоскости, соответствующей максимальному углу ската опорной поверхности. На расчетной схеме обозначены:
Gi – сила тяжести элемента крана;
Fу - составляющая силы тяжести элемента от уклона опорной поверхности;
Fур и Fут - радиальная и касательная составляющие силы Fу при угле поворота крана φ°.
Максимальная величина момента сопротивления повороту от уклона опорной поверхности соответствует повороту стрелы крана на подъем на угол φ = 90°. Минимальная величина – при достижении углаφ = 270°, когда поворотная часть крана движется под уклон.
С учетом принятых сил по рис. 3.13 максимальный момент сопротивления повороту при работе на уклоне β° и угле поворота φ = 90° будет
Мус = (Qмакс· g + Gко) · sin β · Lмин + Gс sin β · rс – Gкрпов · sin β · rцтпов, кН. |
(3.9) |
Если величина Мус получается со знаком « - », то в дальнейших расчетах ее используют как положительную величину.
Суммарный момент сопротивления вращению поворотной части
Мсмакс = Мсопу + Мсв + Мсукл . |
(3.10) |
3.2.2. Определение мощности двигателя механизма
Необходимая расчетная мощность двигателя механизма поворота с учетом переменности действия сил ветра и угла поворота платформы крана может быть определена по формуле
N = |
(Мопус |
+ 0,7Мвс + 0,7Муклс ) nкр |
, кВт. |
(3.11) |
|
9,55ηмп |
|||
|
|
|
|
73
По табл. П.8 выбирают электродвигатель переменного тока с фазным ротором серии МТF, имеющий необходимую мощность Nдв, кВт, при заданным режиме работы крана. Для дальнейших расчетов механизма требуются следующие данные:
частота вращения вала двигателя nдв, об/мин; максимальный момент двигателя Мдвмакс, кН·м; момент инерции ротора Jр, кг·м².
Номинальный момент, развиваемый этим двигателем, вычисляют по формуле
Мдвном = 9,55 Nдв / nдв , кН·м. |
(3.12) |
Выбранный двигатель необходимо проверить по условиям пуска по методике, приведенной в главе 5.
3.2.3. Определение параметров трансмиссии
Общее передаточное механизма поворота
uмп = nдв / nкр . |
(3.13) |
По табл. П. 9.5 выбирают унифицированный механизм поворота с передаточным числом uр, позволяющий передавать расчетную мощность Nдв, или проектируют удовлетворяющий конструктивно редуктор с оригинальной или известной кинематической схемой. При необходимости можно составить механизм поворота из 2-3-х унифицированных механизмов с суммарной мощностью их двигателей равной расчетной. Нет необходимости стремиться подобрать редуктор с общим передаточным числом uмп. Требуемая величина передаточного числа достигается за счет открытой зубчатой передачи.
Передаточное число открытой зубчатой передачи, состоящей из зубчатого колеса опорно-поворотного устройства и ведущей шестерни на выходном валу механизма поворота, получают по формуле
uоп = uмп / uр. |
(3.14) |
При известном модуле mопу и количестве зубьев zк колеса ОПУ можно получить параметры ведущей шестерни. Количество зубьев ведущей шестерни
zш = zк / uоп . |
(3.15) |
Диаметр начальной окружности
dш = zш · mопу , мм. |
(3.16) |
Шестерню с полученными параметрами необходимо проверить на возможность подрезания ножки зуба и интерференцию профиля шестерни и профиля колеса ОПУ.
Ширину шестерни назначают на 10-12 мм шире зубьев колеса ОПУ:
bш = bк опу + 10 мм. |
(3.17) |
В дальнейшем необходимо выбрать марку стали шестерни и провести проверку зубьев шестерни на контактную и изгибную прочность с учетом динамических нагрузок. Для этого
74
вычисляется избыточный момент двигателя, приведенный к оси вращения платформы крана при работе на горизонтальной местности в безветренную погоду:
Мизб = Мдвмакс · uмп· ηмп - Мсмакс , кН·м. |
(3.18) |
Моменты инерции вращающихся масс, приведенные к оси вращения поворотной платформы крана:
момент инерции ротора двигателя
Jр пр = 1,25 · Jр ·uмп ² · ηмп , кг·м²; |
(3.19) |
|||||
момент инерции поворотной платформы, рассматриваемой как точечная масса, |
|
|||||
|
|
Jпп = mкрпов · rцт2, кг·м2; |
|
(3.20) |
||
момент инерции стрелы |
|
|
(rшс2 |
+ L2мин +rшс Lмин ) |
|
|
J |
|
= m |
, кг·м²; |
(3.21) |
||
с |
|
|
||||
|
c |
|
3 |
|
|
|
|
|
|
|
|
|
|
момент инерции груза как точечной массы |
|
|
||||
|
|
Jгр = Q · Lмин² · 10³, кг·м2. |
(3.22) |
Суммарный момент инерции вращающихся масс относительно оси вращения поворотной части крана
Jсум = Jр пр+ Jпп + Jc |
+ Jгр , кг · м2. |
(3.23) |
||
Угловое ускорение определяют по формуле |
|
|
|
|
ε = Мизб |
/ Jсум, 1/ с2 . |
(3.24) |
||
Время разгона механизма поворота в этом случае будет |
|
|||
tр = |
π nкр |
, с. |
(3.25) |
|
30 ε |
||||
|
|
|
Время разгона механизма поворота может составлять 4-8 с. При использовании в механизме поворота асинхронных короткозамкнутых двигателей с временем разгона значительно менее 3 с следует применить двигатель меньшей мощности, при t >> 10 c следует установить двигатель большей мощности. При двигателях с фазным ротором следует соответственно увеличить или уменьшить число пусковых ступеней.
Расчет элементов механизма поворота на прочность следует вести с учетом динамического коэффициента. Его величина без учета колебательных процессов может быть определена по формуле
Кд = 1+ Мизб / Мсмакс. |
(3.26) |
75
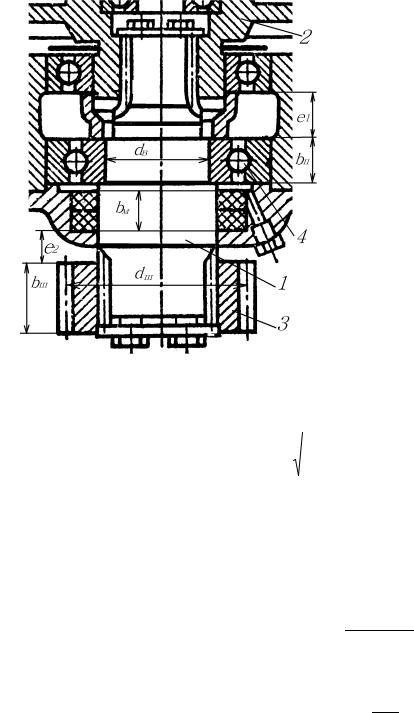
3.2.4. Расчет на прочность вала ведущей шестерни
При использовании в механизме поворота крана унифицированного редуктора необходимо проверить на прочность выходной вал редуктора и ведущую шестерню, взаимодействующую с зубчатым венцом опорно-поворотного устройства. На рис. 3.14 показан фрагмент установки выходного вала в редукторе механизма поворота крана КС-3571.
Сборочный чертеж всего механизма поворота этого крана показан на рис. 3.4. Вал 1 на рис. 3.14 представляет собой двухопорную, одноконсольную балку. Со стороны зубчатого колеса 2 второй ступени редуктора на шлицевой конец вала действует только крутящий момент Мкр, передаваемый валом на выходную ведущую шестерню 3. На консольном конце вала, кроме крутящего момента Мкр, действует радиальная сила Fр, возникающая в зацеплении шестерни с колесом опорно-поворотного устройства. Порядок предварительного определения геометрических размеров вала можно принять следующим. Исходя из геометрических размеров ведущей шестерни и расчетного момента сопротивления повороту, определяют передаваемый выходным валом крутящий мо-
мент Мкр.
Рис. 3.14. Чертеж выходного вала механизма
поворота крана КС-3571
Мкр = |
Мс dш |
Kд , (3.27) |
|
||
|
dопу |
где dопу – диаметр начальной окружности зубчатого колеса ОПУ.
Минимальный диаметр вала, опирающегося на подшипник 4, из расчета только на кручение вычисляют по формуле
dв = 3 |
|
Mкр |
|
|
, |
(3.28) |
|
0,2[τ |
] |
||||||
|
|
|
|
где [τ] – допускаемые касательные напряжения при кручении. Для стали 45, имеющей предел текучести при растяжении σт р = 315 МПа, предел текучести при кручении τт = 0,6 σт р. Для деталей механизмов крюковых кранов, работающих в режиме 4М-5М, с учетом выносливости [τ] = 0,6 τт ≈ 110 МПа. Расчетная схема вала показана на рис.3.15.
Радиальная нагрузка, действующая в зацеплении прямозубых цилиндрических колес
F = 2Mкр tgα .
рад dш
Здесь α = 20° - стандартный угол зацепления. Окружное усилие на шестерне
Fокр = dМс .
опу
(3.29)
(3.30)
76
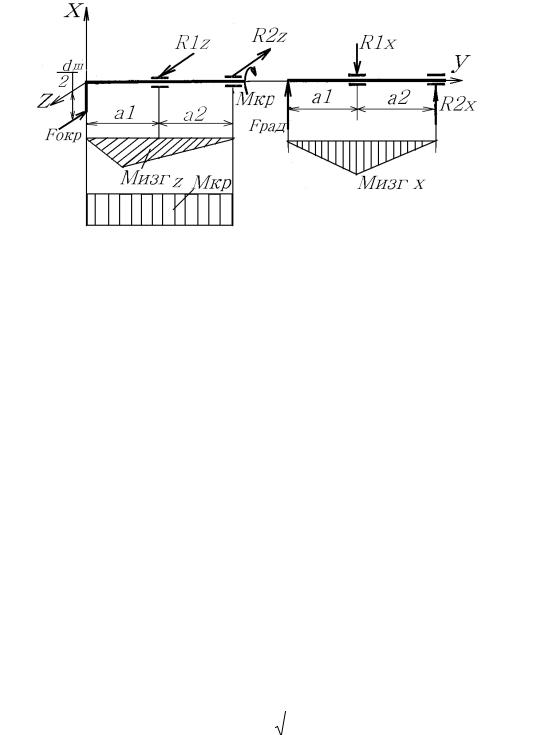
Рис. 3.15. Расчетная схема выходного вала редуктора механизма поворота
к рис. 3.14 (на расчетной схеме вал условно показан горизонтально)
Длины шеек вала а1 и а2 предварительно выбирают так, чтобы получить их минимальную длину:
а1 = bш /2 + e2 +b. м + (4÷6)мм+ bп /2; а2 = bп + е1. |
(3.31) |
Размер е2 учитывает зазор между шестерней и крышкой (15 - 18 мм) и толщину стенки крышки (8 -10 мм) корпуса редуктора. Размер bм определяется толщиной уплотнительных манжет. Толщина их практически не зависит от диаметра вала и составляет 8, 10, 12 мм. Для надежного уплотнения обычно ставят 2-3 манжеты. Ширину bп подшипника предварительно принимают по диаметру вала. Размер е1 выбирают конструктивно. Его можно принять равным диаметру вала dв или меньше. По принятым размерам вычисляют опорные реакции, действующие на подшипники, и наибольшие изгибающие моменты в плоскостях Z – Y (формулы 3.32) и X – Y (формулы 3.33).
R1 |
= |
|
Fокр (a1 |
+ a2) |
; |
R2 |
z |
= |
|
Fокр a1 |
|
; |
M |
изг z |
= F |
|
a1;. |
|
|
|
|
|
|
||||||||||||||
z |
|
|
a2 |
|
|
|
|
|
|
a2 |
|
|
окр |
|
||||
|
|
|
|
|
|
|
|
|
|
|
|
|
|
|
|
|||
R1 |
= |
Fрад (a1+ a2) |
; |
R2 |
x |
= |
Fрад a1 |
; |
M |
изг х |
= F |
рад |
a1. |
|||||
|
|
|||||||||||||||||
x |
|
|
a2 |
|
|
|
|
|
|
a2 |
|
|
|
|
||||
|
|
|
|
|
|
|
|
|
|
|
|
|
|
|
|
Суммарный изгибающий момент в расчетном сечении
|
|
|
|
|
Мизг = Мизг2 |
х + Мизг2 |
z . |
(3.32)
(3.33)
(3.34)
Проверка статической прочности и проверка на выносливость вала ведется по методике, изложенной в пп 2.3.7, по формулам (2.31 – 2.38) с использованием графиков и таблиц указанного пп.
3.2.5. Проверочный расчет приводной шестерни ОПУ
Приводная шестерня 3 (рис. 3. 14) образует с зубчатым венцом опорно-поворотного устройства открытую зубчатую передачу. Она должна быть проверена на выносливость по напряжениям изгиба. Проверка контактной прочности не имеет смысла, так как абразивный
77
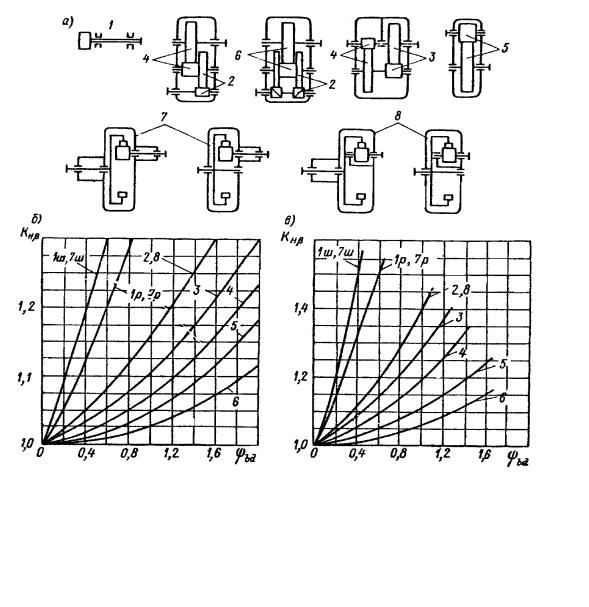
износ поверхностей зубьев шестерни происходит быстрее, чем их разрушение от действия переменных контактных напряжений. Проверочный расчет выполняется по формуле
|
2 |
103 F |
K |
Fα |
K |
Fβ |
K Y |
|
|
|
σF1 = |
|
окр |
|
|
Fv F |
≤ [σF1 |
]. |
(3.35) |
||
|
bшdшm |
|
|
|||||||
|
|
|
|
|
|
|
Fокр определяют по формуле (3.30);
KFα – коэффициент, учитывающий неравномерность распределения нагрузки между зубьями. Для прямозубых передач без коррекции зубьев KFα = 0,75;
KFβ – коэффициент, учитывающий неравномерность распределения нагрузки по ширине при расчете на изгибную прочность. С некоторым повышением запаса прочности его можно принять KFβ = KНβ, где KНβ - коэффициент, учитывающий неравномерность распределения нагрузки по ширине при расчете на контактную прочность [8]. KНβ определяют по графику на рис. 3.16 в зависимости от вида передачи, твердости рабочих поверхностей зубьев и отношения ψbd ширины bш шестерни к ее начальному диаметру dш.
Рис. 3.16. Ориентировочные значения КНβ для цилиндрических передач: а – виды пере-
дач; б – КНβ при твердости НВ рабочих поверхностей зубьев любого из взаимодействующих колес ≤ 350; в – при твердости НВ рабочих поверхностей зубьев обоих колес > 350; 1 – 8 – кривые, соответствующие видам передач на рис. а (1ш, 7ш и 1р, 7р – для передач соответственно на шарико- и роликоподшипниках)
78
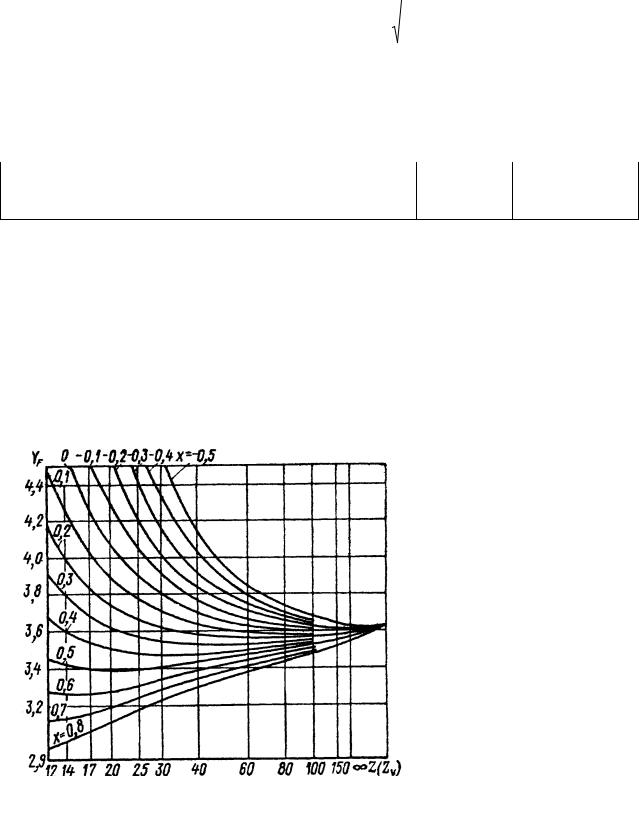
Вид передачи, соответствующий установке ведущей шестерни по рис. 3.14, на рис. 3.16, а обозначен позициями 1 и 7.
KFv – коэффициент, определяют по формуле
|
4,76 10−4δ |
|
g |
|
v |
|
aw |
|
b |
d |
|
|
|
|
|
|
uon |
|
|
|
|
||||||||
КFv =1+ |
|
F |
|
0 |
ш |
|
ш |
|
ш |
(3.36) |
||||
|
|
|
|
|
|
|
|
|
|
|
. |
|||
|
Fокр |
KFβ |
|
|
|
|
|
|||||||
|
|
|
|
|
|
|
|
|
|
|||||
δF и g0 принимают из табл. 3.3 и 3.4. |
|
|
|
|
|
|
|
|
|
|
|
Таблица 3.3 |
||
Значение коэффициента δF |
|
|
|
|
|
|
||||||||
|
|
|
|
|
|
|
|
|||||||
|
|
|
|
|||||||||||
Твердость поверхностей зубьев шестерни Н1 и колеса Н2 |
Вид зубьев |
δF |
||||||||||||
Н2 ≤ НВ350 (или Н1 и Н2 ≤ НВ350) |
|
|
|
|
|
|
прямые |
0,016*; 0,011** |
|
|||||
Н1 и Н2 > НВ350 |
|
|
|
|
|
|
прямые |
0,016*; 0,011** |
|
* Без модификации головки; ** С модификацией головки.
|
|
|
Значения коэффициента g0 |
|
Таблица 3.4 |
|||
|
|
|
|
|
|
|||
|
|
|
|
|
|
|
|
|
Модуль m, мм |
|
Значения g0 |
при степени точности колес |
|
|
|||
5 |
|
6 |
|
7 |
8 |
9 |
|
|
3,5 < m ≤ 10 |
31 |
|
42 |
|
53 |
61 |
82 |
|
m > 10 |
37 |
|
48 |
|
64 |
73 |
100 |
|
Окружная скорость на шестерне vш = π dш nш / 60. |
|
(3.37) |
Значение YF для прямозубых зубчатых колес с внешними зубьями определяют по графику на рис. 3.17 в зависимости от количества зубьев шестерни и коэффициента коррекции зуба.
Межцентровое расстояние аw для открытой передачи ОПУ с внутренним зацеплением рассчитывают по формуле
|
aw= (zк - |
zш )m / 2. |
(3.38) |
|
Допускаемое |
напряжение |
при |
|
расчете на изгиб определяют по |
||
|
формуле |
|
|
|
σ |
|
|
Рис 3.17. Значения коэффициента YF для зубчатых |
[σF ]= ([nFF0])KFC KFL . |
(3.39) |
|
колес с внешними зубьями |
Предел выносливости σF0 |
при |
|
|
изгибе и коэффициент запаса [nF] |
||
|
выбирают в табл. 3.5. |
|
79
КFC учитывает характер изгибной нагрузки. При реверсивной симметричной нагрузке для нормализованных и улучшенных колес КFC = 0,65; при твердости поверхностей зубьев более 45
НRС - КFC = 0,75.
Таблица 3.5 Значения пределов выносливости σF0 и коэффициентов запаса [nF] сталей
Марки сталей и вид термообработки |
Твердость зубьев НRС |
σF0 |
[nF] |
|||
поверхности |
сердцевины |
|
|
|||
20ХН2М, 12ХН2, 12ХН3А и др. (цементация) |
51 |
– 63 |
32 |
– 45 |
959 |
1,7 |
18ХГТ, 30ХГТ, 12Х2Н4А и др. (цементация) |
57 |
- 63 |
32 |
- 45 |
800 |
1,7 |
25ХГМ (нитроцементация) |
57 |
- 63 |
32 |
- 45 |
1000 |
1,7 |
25ХГТ, 30ХГТ и др. (нитроцементация) |
57 |
- 63 |
32 |
- 45 |
750 |
1,7 |
Стали типа 55ПП и др (закалка ТВЧ) |
58 |
- 62 |
28 |
- 35 |
900 |
1,7 |
60ХВ, 60Х, 60ХН и др. (закалка ТВЧ) |
54 |
- 60 |
25 |
- 35 |
700 |
1,7 |
35ХМА, 40Х, 40ХН и др. (закалка ТВЧ) |
48 |
– 60 |
25 |
- 35 |
600 |
1,7 |
35ХМА, 40Х, 40ХН и др. (нормализация или |
|
|
|
|
350 - |
1,65 |
улучшение) |
|
180 – 350 НВ |
570 |
|
КFL учитывает режим нагружения зубьев колес. При твердости рабочих поверхностей зубьев Н ≤ 350 НВ коэффициент КFL принимают не более 2. При Н > 350 НВ значения КFL ≤ 1,6. Если число нагружений зубьев больше 4·106, то принимают КFL = 1.Число нагружений зубьев шестерни за нормативный срок службы крана вычисляют по формуле
Nцш = Z0 tмп (nкр uоп / 60). |
(3.40) |
Время работы механизма поворота tмп при среднем угле поворота φ° в течение одного рабочего цикла крана
tмп = 2 (φ° / 60 nкр + 6), с |
(3.41) |
4.Механизм изменения вылета груза
4.1.Классификация механизмов изменения вылета груза
Вылетом груза (стрелы) в стреловых кранах называют расстояние по горизонтали от оси вращения крана до грузоподъемных канатов. Изменение вылета в стреловом кране можно осуществлять тремя способами: изменением угла наклона стрелы к горизонту, перемещением грузовой тележки по балочной стреле с помощью канатной тяги, удлинением стрелы телескопической конструкции. На рис. 4.1 – 4.4 показаны принципиальные схемы механизмов для осуществления плавного изменения вылета груза.
80