
Учебное пособие 800490
.pdf
|
z4 + z6 |
=ζ , |
(1.47) |
|
c |
||
|
|
|
|
где полученное ζ – обязательно должно быть |
целым числом. |
Если вышеуказанные условия не выполняются, то производят корректировку количества зубьев на зубчатых колесах z4, z5, z6 . Аналогичная коррекция должна быть проведена и для первой ступени редуктора после того, как будут определены геометрические размеры выходной ступени. Геометрические размеры зубчатых колес определяют расчетом на выносливость рабочих поверхностей зубьев по контактным напряжениям. Вращающие моменты на зубчатых колесах с учетом ранее принятых кинематических соотношений вычисляют по формулам:
на центральном колесе z1 – М1 = Мб / iр;
на центральном колесе замыкающей ступени z4 – М4 = М1 (z3/z1 + 1); |
|||||
на колесе z3 |
– |
М3 |
= М1 |
· z3/z1 |
; |
на колесе z6 |
– |
М6 |
= М1 |
· z6/z4 |
· (z3/z1 + 1). |
Чтобы предварительно определить размер наибольшего колеса редуктора (в рассматриваемом варианте кинематической схемы - колесо z6), необходимо задать для него марку стали, способ упрочнения и знать при этом получаемые прочностные характеристики.
1.4.9.Стали для зубчатых колес
Втермически необработанном состоянии механические свойства большинства сталей, применяемых в машиностроении, различаются незначительно. Способность стали в той или иной степени воспринимать термическую обработку, называется прокаливаемостью, которая характеризуется глубиной проникновения закаленного слоя. За глубину закалки приближенно принимают расстояние от поверхностного слоя до слоя полумартенситной структуры (50% мартенсита и 50% троостита). Углеродистые стали имеют низкую прокаливаемость, легированные – лучшую. Прокаливаемость стали существенно повышается при ее легировании хромом, никелем, марганцем, молибденом. В планетарных передачах грузоподъемных машин рекомендуется применять низколегированные стали с термообработкой на улучшение и закалку токами высокой частоты или цементации зубьев быстроходных колес: стали
40Х, 40ХН, 20ХН2М, 25ХГМ. Механические свойства этих сталей приведены в табл. П.6.1.
Межцентровое расстояние а4-5 цилиндрических прямозубых колес z4 и z5 |
из условия |
||||||||||
контактной прочности рабочих поверхностей зубьев вычисляют по формуле |
|
||||||||||
|
|
|
|
|
|
|
|
|
|
||
|
|
|
|
315 |
2 |
|
M p |
|
|||
|
3 |
|
|
|
|
|
|
|
|
|
|
a4−5 = (i4−5 +1) |
|
|
[σ |
к |
] i |
|
с ψ , мм, |
(1.48) |
|||
|
|
|
|
4−5 |
|
|
|
|
|
|
где i4-5 = z5 / z4;
[σк] – допускаемые контактные напряжения для выбранного материала зубчатых колес, МПа. Для зубчатых колес небольшого диаметра назначают низколегированные цементируемые стали 20ХНМ, 25ХГМ и др. с закалкой до HRC 56 -63.
31
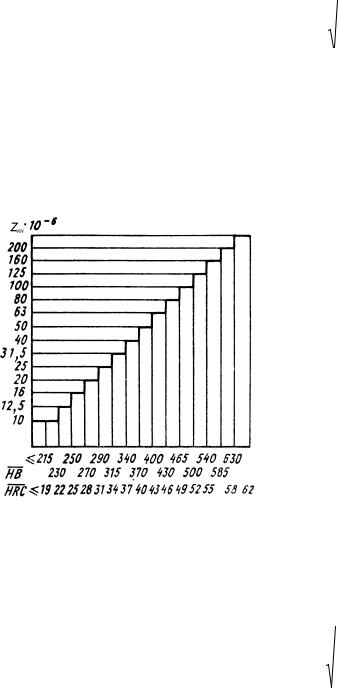
[σк ]= |
σk0 |
lim |
, МПа, |
(1.49) |
|
|
|||
|
Sk |
|
где σк0lim - предел длительной выносливости стали по контактным напряжениям; Sк –
коэффициент безопасности (табл. П.6.2).
Мр - расчетный момент на шестерне z4, Н·мм. Мр = М4· Кд· Кнг.
Коэффициент долговечности Кд = Кэн 3 |
Zц |
4 |
|
|
≤1. |
|
|
(1.50) |
|||||||||
Zкн |
|
|
|||||||||||||||
|
|
|
|
|
|
|
|
|
|
|
|
|
|||||
Коэффициент эквивалентности нагрузки Кэн определяют по формуле (1.1). |
и ско- |
||||||||||||||||
Наработка шестерни за нормативный срок службы крана при заданной высоте |
|||||||||||||||||
рости подъема груза, числе сателлитов с = 3 может быть определена по формуле |
|
||||||||||||||||
Zц4 = Zнс· tпо· nб · ( z6 /z4) · c, |
|
|
(1.51) |
||||||||||||||
где Zнс подсчитывают по формуле (1.2) |
|
|
|
|
|
|
|
|
|
|
|
|
|||||
|
Среднее время работы механизма подъема за |
||||||||||||||||
|
один цикл tпо определяют по формуле |
(1.23). |
|
||||||||||||||
|
|
Zкн – базовое число циклов контактных напряже- |
|||||||||||||||
|
ний для принятой твердости |
поверхностей зубьев, |
|||||||||||||||
|
определяют по графику на рис. 1.26. |
|
|
||||||||||||||
|
|
|
Коэффициент нагрузки |
Кнг |
вычисляют по |
||||||||||||
|
формуле |
|
|
|
|
|
|
|
|
|
|
||||||
|
|
|
|
|
|
|
|
|
|
|
|
|
Кнг = Кα·Кβ·Кυ, |
|
(1.52) |
||
|
|
|
где Кα - коэффициент распределения нагрузки. |
||||||||||||||
|
Для прямозубых передач Кα = 1. |
|
|
||||||||||||||
|
|
|
|
|
|
|
Кβ - коэффициент концентрации нагрузки. |
||||||||||
|
Для прямозубых цилиндрических планетарных пе- |
||||||||||||||||
|
редач |
с твердостью рабочих поверхностей зубьев |
|||||||||||||||
|
НRС ≥ |
40 |
на начальной стадии проектирования |
||||||||||||||
|
можно принять Кβ = 2,5. |
|
|
|
|||||||||||||
Рис. 1.26. График для выбора |
|
|
|
|
|
|
Кυ - коэффициент динамичности для зуб- |
||||||||||
чатых передач всех видов определяют в зависимости |
|||||||||||||||||
базового числа циклов |
|||||||||||||||||
от скорости, степени точности и твердости |
рабо- |
||||||||||||||||
контактных напряжений |
|||||||||||||||||
чих поверхностей зубьев по табл. 1.6. |
|
|
|||||||||||||||
|
|
|
|||||||||||||||
При проектном расчете окружную скорость цилиндрической передачи, у которой |
|||||||||||||||||
взаимодействующие колеса подвергались цементации, определяют по формуле |
|
||||||||||||||||
|
n4 |
|
|
|
|
|
|
|
|
|
|
|
|
||||
v' = |
|
|
|
|
|
М4 |
|
|
, м/с, |
|
|
(1.53) |
|||||
|
103 С |
v |
3 z5 |
ψ |
|
|
|
|
|
|
|||||||
|
|
|
|
|
z4 |
|
|
|
|
|
|
||||||
|
|
|
|
|
|
|
|
|
|
|
|
|
|
|
|||
где n4 – частота вращения шестерни z4, об/мин; |
Сv принимают из табл.1.5 в зависимо- |
||||||||||||||||
сти от термообработки шестерни и колеса; |
ψ – коэффициент ширины колеса. Предваритель- |
но можно принять ψ = 0,4. Коэффициент динамичности Кυ принимают из табл. 1.6.
32
Таблица 1.5 Значения коэффициента Сv для прямозубых цилиндрических передач
Передачи |
|
|
|
Вид термообработки колеса и шестерни |
|
|
|
||||||||||
прямозубые |
|
Уш – Ук |
ТВЧш – Ук |
Цш – Ук |
|
ТВЧш – ТВЧк , Зш – Зк |
|
Цш – Цк |
|||||||||
|
Сv |
|
13 |
|
14 |
15.5 |
|
|
|
17,5 |
|
|
21 |
||||
Обозначения: У – улучшение; ТВЧ – поверхностная закалка токами высокой частоты; |
|||||||||||||||||
Ц – цементация; З – объемная закалка; индекс: к - колесо; ш - шестерня |
|
|
|
||||||||||||||
|
|
|
Значении коэффициента динамичности Кυ |
|
Таблица 1.6 |
||||||||||||
|
|
|
|
|
|
|
|
|
|||||||||
|
|
|
для прямозубых колес 8-ой степени точности |
|
|
|
|||||||||||
|
|
|
|
|
|
|
|
|
|
|
|
|
|
|
|
|
|
|
Твердость |
|
|
|
|
|
|
|
|
v, |
м/с |
|
|
|
|||
|
поверхностей зубьев |
|
1 |
2 |
|
4 |
|
6 |
|
8 |
|
10 |
|
|
|||
|
НВ ≤ 350 |
|
|
|
1,04 |
1,08 |
|
1,16 |
1,24 |
|
1,32 |
|
1,4 |
|
|||
|
НRС ≥ 40 |
|
|
|
1,03 |
1,06 |
|
1,1 |
1,16 |
|
1,22 |
|
1,26 |
|
Полученное по формуле межцентровое расстояние а4-5 |
позволяет определить ориентиро- |
|||
вочный модуль зубчатых колес передачи |
2a4−5 |
|
|
|
m = |
, мм. |
(1.54) |
||
|
||||
|
z4 + z5 |
|
ГОСТ 9563-80 рекомендует применять модули зубчатых колес из следующего основного ря-
да: 1; 1,25; 1,5; 2; 2,5; 3; 5; 6; 8; 10; 12; 16; 16; 20; 25; 32; 40; 50, мм.
Из этого ряда принимают ближайшее большее стандартное значение модуля mст и уточняют с ним межцентровое расстояние колес z5 - z4:
а4-5=0,5(z4 + z5 ) mст, мм. |
(1.55) |
Далее необходимо определить наибольший размер центрального колеса с внутренним зацеплением z6. Делительный диаметр колеса
dd6 = mcm · z6 , мм. |
(1.56) |
Наружный диаметр колеса
D0 = dd6 + 8 mcm, мм. |
(1.57) |
Чтобы колесо с наружным диаметром D0 возможно было разместить внутри барабана лебедки, необходимо выполнение условия
D0 ≤ Dб - 2δ. |
(1.58) |
Если это условие не выполняется, необходимо провести корректировку кинематического расчета, начиная с п. 1.4.3. Корректировку следует начинать с изменения кратности полиспаста, которую следует увеличить на одну или две единицы. Это ведет к уменьшению усилия в канате. Диаметр барабана следует увеличить, отступив от принятого соотношения
Dб / dк , что повышает долговечность каната. Диаметр барабана должен быть
33
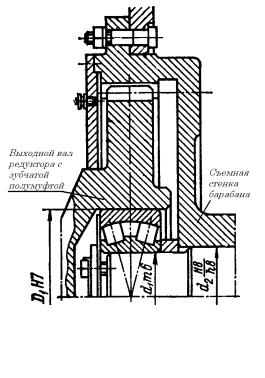
Dб* = 2 Мб / Fф*. |
(1.59) |
В этом выражении используют ранее вычисленное по формуле (1.41) значение Мб. Такая корректировка ведет к изменению частоты вращения барабана, изменению передаточного числа редуктора. Эти параметры пересчитывают по формулам (1.16), (1.42) соответственно и далее по изложенной выше методике. После того как будут получены положительные результата для размещения планетарного редуктора внутри барабана, необходимо провести проверочный расчет зубьев колес всех ступеней редуктора на долговечность по контактным и изгибным напряжениям.
1.4.10. Выбор муфты
Муфты в механизме подъема используют для соединения вала двигателя с входным валом редуктора и для соединения выходного вала редуктора с барабаном. В первом случае обычно используют муфты упругие втулочнопальцевые с тормозными шкивами (по ОСТ 24.848.0379). Технические данные таких муфт приведены в табл.
П. 11. Во втором случае применяют зубчатые муфты. Если барабан лебедки имеет две собственные опоры, применяют зубчатые муфты по ГОСТ 5006-83. При использовании выходного вала редуктора в качестве одной из опор барабана применяют зубчатые муфты специального исполнения, представленные на рис. 1.27. Технические данные по этим муфтам указаны в табл. П.9.5, как элемента выходного вала редуктора.
Для выбора муфты в общем случае необходимо знать:
- диаметры и типы соединяемых валов; - величину указанного в каталоге крутящего но-
минального момента Мн, который может передавать муфта, Н·м;
Рис. 1.27.Чертеж соединения |
- величину максимального расчетного крутящего |
||
момента, передаваемого муфтой, |
Ммакс , Н·м; |
||
элементов барабана с зубчатой |
|||
полумуфтой редуктора |
- требуемую компенсационную и демпфи- |
||
рующую способность; |
|
||
|
|
||
|
- компоновочное решение механизма. |
||
Муфты выбирают по максимальному расчетному моменту: |
|
||
|
Ммакс · п ≤ Мн, |
(1.60) |
где п = п1· п2 · п3 .
п1 - учитывает степень ответственности механизма; п2 - учитывает режим работы механизма;
п3 - учитывает допустимое угловое смещение соединяемых валов.
Для механизма подъема груза принимают п1 = 1,4; п2 принимают из табл. 1.7; п3 – из табл. 1.8.
34

|
|
Коэффициент учета режима работы n2 |
|
|
Таблица 1.7 |
||||
|
|
|
|
|
|
||||
|
|
|
|
|
|
|
|
|
|
Режим работы |
1М - 3М |
|
4М - 5М |
|
|
6М - 8М |
|||
п2 |
1,3 |
|
1,4 |
|
1,5 |
|
|||
|
|
|
|
|
|
|
|
Таблица 1.8 |
|
Коэффициент учета углового смещения соединяемых валов зубчатых муфт |
|||||||||
|
|
|
|
|
|
|
|
|
|
Угол перекоса |
|
0,25° |
0,5° |
|
1,0° |
|
1,5° |
|
|
п3 |
|
1 |
1,25 |
|
1,5 |
|
1,75 |
|
|
Для остальных типов |
муфт п3 = 1. |
|
|
|
|
|
|
|
|
Максимальный расчетный момент на выходном валу редуктора механизма подъема |
|||||||||
груза определяют из условия подъема испытательного груза. |
|
|
|
|
|||||
|
|
Ммакс =1,25 п · Fф · Dб / 2 ·η ≤ Мн . |
(1.61) |
Если выходной вал выбранного редуктора выполнен в виде зубчатой полумуфты, то дополнительных расчетов на передаваемый крутящий момент не требуется.
1.4.11. Выбор тормоза
Тормоза выбираются по тормозному моменту, величина которого должна быть достаточной для надежного удержания груза на весу. Согласно правилам Ростехнадзора надежное удержание груза должно обеспечиваться гарантированным коэффициентом запаса по тормозному моменту. Требуемый момент тормоза, устанавливаемый на быстроходном валу редуктора, можно вычислить по формуле
М |
тм |
≥ k |
зт |
Fф Dб |
η |
р |
, кН·м, |
(1.62) |
|
||||||||
|
|
2 iр |
|
|
где kзт принимают в зависимости от режима работы из табл. П1.3.
Типоразмер тормоза выбирают по табл. П.10.1. Выбранный тормоз проверяют на обеспечение оптимального времени торможения по формуле
tт = |
1,2(J р + J м ) nдв +91 Q Vгр2 |
η0 |
/ nдв |
, с |
(1.63) |
|||
9,55[M т −Q g Dб |
η0 |
/(2 |
ip iп )] |
|||||
|
|
|
где Jр, Jм- моменты инерции ротора двигателя и муфты с тормозным шкивом;
ηо – общий КПД механизма подъема, равный ηо = ηп ηб ηр ηм, где учтены соответственно КПД полиспаста, барабана, редуктора, тормозной муфты. Их величины можно принять
согласно прил. 2. Размерность величин параметров J - кг·м2; nдв - об/мин; Q - кг; Vгр - м/с; Dб – м. Время торможения должно быть в пределах 1,5 – 3 с.
Механизм подъема груза проверяют с выбранным двигателем также и на время пуска
по формуле |
1,2(J |
|
|
|
) n |
|
|
|
|
|
р |
+ J |
м |
+91 Q V 2 |
/η n |
|
|||
tп = |
9,55[Mсрп −Q g Dб /(2 ip iп ηо )] |
, с, |
(1.64) |
35
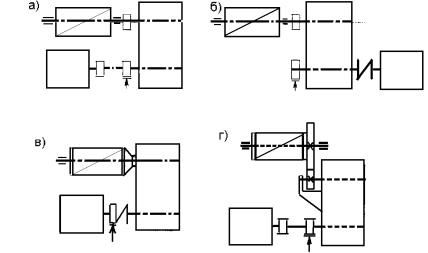
где Мпср = (9550 Nдв / nдв ) ψ. Здесь ψ – кратность среднего пускового момента двигателя. Для трехфазных двигателей с короткозамкнутым ротором ψ ≈ 2,3 ÷ 2,5; для двигателей с фазным ротором ψ ≈ 1,5÷ 1,6. Время пуска должно быть в пределах 1- 2 с.
1.5. Компоновка грузоподъемного механизма
После выбора стандартных узлов (двигателя, редуктора, муфты, тормоза), выбора конструкции и определения параметров специальных элементов (блоков, барабана) механизма приступают к его компоновке, т. е. определяют наиболее целесообразное расположение сборочных единиц относительно друг друга на специальной раме, удобной для дальнейшей блочной сборки машины. Выбор той или иной компоновочной схемы производится с учетом многих факторов: сборочно-разборочных, технологических, конструктивных особенностей всей машины, технико-экономических.
Компоновочный чертеж выполняют на миллиметровой бумаге в масштабе 1: 4 или 1: 5 в двух проекциях: план и вид сбоку. Эту работу удобно выполнять с помощью «габариток» - вырезанных в соответствующем масштабе из бумаги контуров основных элементов – двигателя, редуктора, барабана, муфт, тормоза. В принятом окончательно и утвержденном преподавателем варианте эти элементы закрепляют на листе миллиметровки и в дальнейшем подшивают в расчетно-пояснительную записку.
На рис. 1.28 представлены некоторые наиболее распространенные компоновочные схемы грузоподъемных лебедок. Схема на рис. 1.28, а наиболее удобная для монтажа. Наличие промежуточного вала между двигателем и редуктором и наличие муфты для соединения барабана с редуктором снижает требования к точности установки элементов лебедки и позволяет сократить время на сборочные операции.
Рис. 1.28. Схемы компоновки грузоподъемных лебедок
Схема на рис. 1.28, б также позволяет вести сборку достаточно просто, свободный доступ ко всем элементам лебедки упрощает ее обслуживание во время эксплуатации, но лебедка имеет значительные габариты из-за расположения двигателя и барабана по разные стороны редуктора. Схема на рис. 1.28, в отличается компактностью за счет использования тихоходного вала редуктора в качестве одной из опор барабана. Лебедка содержит наименьшее количество сборочных узлов, но требует их точной взаимной установки, что ведет
кувеличению времени сборочных работ.
Вкранах большой грузоподъемности и монтажных кранах при небольших скоростях подъема передаточное число редуктора должно быть достаточно большим и требуется при-
36
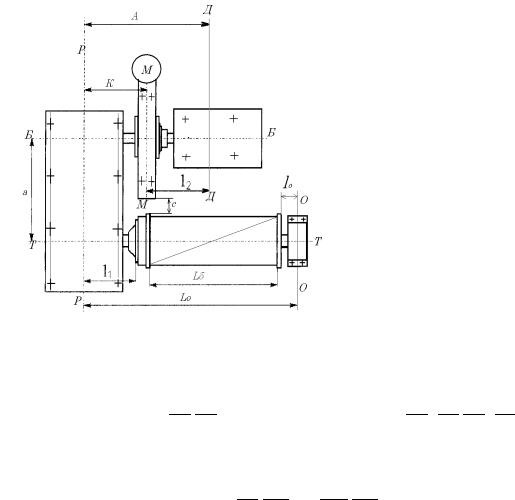
менение трехступенчатого редуктора. В этом случае для уменьшения габаритных размеров лебедки используют двухступенчатый редуктор с дополнительной открытой зубчатой передачей (рис. 1. 28, г).
Тормоза в механизмах устанавливаются в местах с наименьшим крутящим моментом и удобных для их обслуживания. Обычно это входной вал редуктора, присоединяемый к двигателю с помощью втулочно-пальцевой муфты, у которой редукторная полумуфта служит тормозным шкивом, а полумуфту с пальцами устанавливают на вал двигателя. Если конструктивно невозможно установить тормоз в указанном месте, применяют редуктор с двумя входными концами валов (рис. 1. 28, б). Тормоз в этом случае устанавливают на сводном конце вала редуктора.
Компоновка элементов механизма в плане начинается с нанесения их осевых линий, как на рис. 1.29. Определяющим началом являются осевые линии быстроходного (входного) и тихоходного (выходного) валов выбранного редуктора: линии ББ и ТТ соответственно. Линии элементов механизма – РР (редуктора), ММ (тормоза), ДД (двигателя), ОО (опоры барабана) являются осями симметрии точек крепления элементов. Взаимное расположение этих линий определяется справочными данными выбранных типоразмеров элементов, требованиями работоспособности механизма, требованиями возможности и удобства сборочноразборочных операций.
Взаимное расположение линий РР, ММ, ДД в первую очередь определяется требованием технических данных втулочно-пальцевой муфты: минимальный зазор b между полумуфтой редуктора и полумуфтой двигателя по ОСТ 24.8484.03-79 должен быть в пределах 1- 10 мм (прил. 11). Если полумуфты устанавливают на конусные валы с конусностью 1:10, а диаметры валов dм будут выполнены с реальной точностью ± 0,1 мм, то осевое взаимосмещение (размер b) полумуфт можно гарантировать с точностью ± 2 мм, что вполне укладывается в нормы ОСТ на муфты. При установке муфт на цилиндрические концы валов необходимый зазор b между полумуфтами можно обеспечить за счет простановки дистанционных шайб соответствующей толщины между буртиком вала и торцом устанавливаемой полумуфты. Расстояние А между осями редуктора и двигателя по обозначениям в прил. П.8 - П.11 (двигатели, редук-
торы, тормоза, муфты)
Рис. 1.29. Схема компоновки лебедки
в плане
A = (L3 – l1 – l) + (l + b + l1) + (l30 – l31 – l1 – l10 / 2), мм.
Редуктор (рис. П.9.1) Муфта (рис.П.11) Электродвигатель (рис.П.8)
Расстояние К между осью редуктора и о сью тормоза определяется положением тормозного шкива.
К = (L3 – l1 – l) + (l1 – Bт / 2), мм.
Редуктор Муфта
37
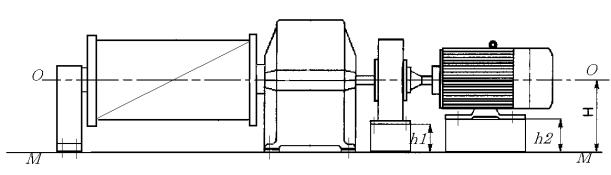
Аналогично можно определить и другие необходимые размеры, опираясь на справочные данные стандартных изделий (подшипники, торцевые шайбы, крышки и т. д.). Установка барабана определяется размерами зубчатой полумуфты на выходном конце вала редуктора и конструкцией торцевой стенки барабана, которая разрабатывается самим проектировщиком. Опора свободной оси барабана может быть сварной или литой. Здесь необходимо стремиться обеспечить минимальное расстояние l0 от торцевой стенки барабана до плоскости, проходящей через середину опорного подшипника. Одна из опор барабана должна удерживать его от осевых перемещений, а вторая опора должна быть плавающей для компенсации теплового расширения элементов барабана. Барабан устанавливается в опорах на сферических подшипниках для снижения требований к точности монтажа и облегчения сборочных операций.
При расположении двигателя и барабана с одной стороны редуктора должен быть обеспечен достаточный (не менее 30 мм) зазор между тормозом и ребордой барабана. Если такая установка тормоза невозможна, применяют вариант установки тормоза по рис. 1.28, б. Проектируя элементы лебедки на вертикальную плоскость (рис. 1.30), все оси вращающихся элементов лебедки располагают в горизонтальной плоскости, проходящей через оси вращения валов редуктора ОО. У некоторых элементов расстояние от плоскости осей ОО до их опорных площадок может быть различным.
Рис. 1.30. Схема компоновки лебедки в вертикальной плоскости
Монтажную плоскость настила ММ опорной рамы следует совместить с опорной поверхностью редуктора. Если редуктор имеет выступающие за опорную плоскость поверхности, в раме предусматривают соответствующие проемы. Для крепления других элементов на монтажную плоскость устанавливают платики или подставки необходимой высоты. Высота этих подставок будет соответственно h1 и h2 . Нестандартные элементы, такие как опора барабана, следует конструировать без подставок. Подставки следует выполнять по высоте с допуском в минус (h -1.5). Это позволяет компенсировать отклонения размеров элементов, получаемых с разных заводов, установкой регулировочных прокладок и снизить трудоемкость сборочных операций.
38
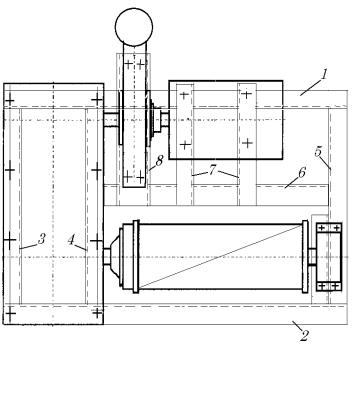
1.6. Компоновка опорной рамы лебедки
При разработке компоновочного решения одновременно необходимо проработать вариант исполнения опорной рамы лебедки. Рама должна быть прочной и жесткой в продольном и поперечном направлении, удобной для монтажа на ней узлов лебедки.
Опорные рамы выполняют сварными из прокатных профилей. Обычно для этих целей используют швеллеры с высотой стенки hст ≈ 0,1 L, где L – длина рамы. Высота стенки обозначена в сортаменте как № швеллера в сантиметрах. Другим решающим фактором для выбора № швеллера может быть ширина его полки, позволяющая удобно работать ключом при завинчивании гаек болтовых креплений узлов. Швеллеры в раме располагают так, чтобы средние линии полок проходили через наибольшее количество точек крепления элементов механизма к опорной раме. Швеллеры располагают полками наружу для удобства крепления узлов механизма. Если полки швеллеров имеют уклоны, то под головки болтов подкладывают косые шайбы. Угловые стыки швеллеров рамы следует организовать так, чтобы подготовка стыковочных поверхностей была наименее трудоемкой. На рис. 1. 31 показан вариант расположения швеллеров на компоновочном чертеже лебедки.
|
|
Основу |
рамы |
составляют |
||
|
|
продольные швеллеры 1 и 2, кото- |
||||
|
|
рые связаны поперечными швел- |
||||
|
|
лерами 3, 4 и 5. Швеллер 6 вспомо- |
||||
|
|
гательный, служит опорой |
для |
|||
|
|
подставок 7 двигателя и подставки |
||||
|
|
8 тормоза. Конфигурация рамы |
||||
|
|
может быть разной. Это зависит в |
||||
|
|
первую очередь от формы элемен- |
||||
|
|
тов, которые на ней монтируются. |
||||
|
|
Существенное |
влияние |
на |
форму |
|
|
|
рамы оказывает также и высота |
||||
|
|
осей вращающихся элементов ме- |
||||
|
|
ханизма над их опорными площад- |
||||
|
|
ками, которые необходимо привя- |
||||
Рис. 1. 31. |
Схема компоновки рамы лебедки |
зывать к монтажной плоскости. |
||||
Условия установки на грузоподъ- |
||||||
|
|
|||||
|
|
емную машину собранного агрега- |
та могут выдвигать свои особые требования к конфигурации рамы. Ранее на рис. 1. 4 и 1. 8 были показаны другие варианты рам лебедок.
На конструкцию опоры барабана влияет количество болтов ее крепления к раме. Количество болтов определяют расчетом. Задаваясь диаметром болтов из условия их удобного размещения на полке швеллеров рамы, рассчитывают их количество. В строительных кранах болты обычно работают на растяжение с предварительной затяжкой, исключающей появление зазора в соединении при подъеме испытательного груза.
39
2. МЕХАНИЗМЫ ПЕРЕДВИЖЕНИЯ ПО РЕЛЬСАМ
2.1. Конструкция механизмов передвижения башенных кранов
Строительные грузоподъемные краны по своему предназначению должны работать в условиях строительных площадок, отличающихся большим разнообразием решаемых с помощью кранов задач и разнообразием опорных поверхностей, по которым им необходимо перемещаться. Выбор типа крана для выполнения грузоподъемных и монтажных работ определяется в первую очередь техническими возможностями того или иного крана и возможностями их работы в условиях конкретной строительной площадки. Ограничения для возможности применения крана нужной грузоподъемности, высоты подъема и вылета груза могут возникнуть из-за недостаточной несущей способности рабочей площадки, ограниченности размеров площадки, наличия недопустимых для работы крана уклонов площадки, наличия на площадке котлованов и траншей, наличия линий электропередач, наличия работающих вблизи других кранов, из-за ограничения зоны перемещения грузов.
Современные строительные краны для перемещения по строительной площадке монтируют на рельсовом, гусеничном или пневмоколесном ходу. В условиях городского строительства при возведении зданий повышенной этажности предпочтение отдают башенным кранам на рельсовом ходу. На площадках с низкой несущей способностью используют краны на гусеничном ходу со стреловым или башенно-стреловым оборудованием. На объектах с небольшим объемом грузоподъемных работ используют стреловые краны на автомобильном или специальном пневмоколесном ходу.
В настоящей главе рассматриваются вопросы, связанные с проектированием механизма передвижения по рельсовым путям башенного крана как специализированного крана для промышленного и гражданского строительства. Проектирование гусеничного или пневмоколесного механизма передвижения обычно изучается в курсе транспортных машин и здесь рассматривается в самых общих чертах.
Современная конструкция механизмов передвижения башенных кранов, передвигающихся по рельсовым путям, базируется на использовании унифицированных деталей, узлов и агрегатов. Для механизмов передвижения башенных кранов используют унифицированные двухколесные балансирные тележки грузоподъемностью 40 и 60 т. Тележки грузоподъемностью 90 т состоят из тележки грузоподъемностью 60 т и присоединенного к ней ведомого колеса с помощью балансирной рамы. Тележки грузоподъемностью 120 т состоят из двух тележек грузоподъемностью 60 т, объединенных балансирной рамой. Приводные тележки комплектуются приводным унифицированным агрегатом ПК-5. Технические характеристики ведущих ходовых тележек и приводных агрегатов приведены в табл. 2. 1.
На рис. 2.1, а показан общий вид двухколесной унифицированной ходовой тележки с приводным агрегатом, а на рис. 2.1, б – ее кинематическая схема. Тележка состоит из сварной рамы 1, приводного агрегата 2, ходовых колес 3. Рама оборудуется плужкамисбрасывателями 4 и противоугонным захватом 5. Приводной агрегат состоит из двигателя 6, двухступенчатого редуктора 7, тормоза 8. Непосредственная передача крутящего момента от редуктора на валы ходовых колес 3 осуществляется валом 9 через открытую зубчатую передачу, состоящую из шестерни 10 и колес 11. На раме ходовой тележки шарнирно установлен шкворень 12, создавая балансирное присоединение тележки к ходовой раме крана для обеспечения равномерной нагрузки на ходовые колеса. На рис. 2. 2 и 2. 3 показан общий вид унифицированных ходовых тележек грузоподъемностью 90 и 120 т.
40