
Учебное пособие 800490
.pdf
|
|
|
|
|
Значения коэффициента К |
|
|
|
Таблиц 2.3 |
|||||||||
|
|
|
|
|
|
|
|
|
|
|
|
|||||||
|
|
|
|
|
|
|
|
|
|
|
|
|
|
|
|
|
|
|
R/Dк |
0,3 |
0,4 |
0,5 |
0,6 |
0,7 |
0,8 |
0,9 |
1,0 |
1,1 |
|
1,2 |
1,3 |
|
1,4 |
1,5 |
1,6 |
|
|
К |
|
0,176 |
0,157 |
0,143 |
0,137 |
0,133 |
0,127 |
0,123 |
0,119 |
0,117 |
|
0,113 |
0,111 |
|
0,108 |
0,107 |
0,105 |
|
|
|
|
|
|
||||||||||||||
|
|
|
|
|
|
|
|
|
|
|
|
|
|
|
|
|
||
|
Коэффициент Ке |
учитывает влияние касательной нагрузки. Для строительных кранов, |
||||||||||||||||
работающих на открытых площадках, |
Ке = 1,1. |
|
|
|
|
|
|
|
|
|
||||||||
|
Коэффициент Кд |
учитывает динамику взаимодействия колеса с рельсом в зоне стыка |
||||||||||||||||
рельсов. Кд вычисляют по формуле |
Кд = 1 + а ·Vкр. |
|
|
|
|
|
(2.7) |
|||||||||||
|
|
|
|
|
|
|
|
|
|
|
|
|
||||||
|
Коэффициент а учитывает жесткость кранового пути, |
с/м; для рельсовых путей на |
шпалах на балластной призме принимают а = 0,1; для рельсов, уложенных на железобетонных балках, а = 0,2.
Vкр. - расчетная скорость передвижения крана, м/с.
В формуле (2.6) величину Dк принимают в см.
Полученные по формуле (2.6) напряжения σ не должны превышать допускаемых напряжений [σN] при приведенном числе оборотов колеса за нормативный срок службы:
|
σ ≤ [σN] =[σ0] 9 |
10000/ Nс |
θ . |
(2.8) |
|||
[σ0]- допускаемые напряжения при базовом числе оборотов колеса Nб ≤ 10000. Величина |
|||||||
[σ0] принимается в зависимости от выбранного материала |
и термообработки колеса по табл. |
||||||
2.4. |
|
|
|
|
|
Таблица 2.4 |
|
|
Значения допускаемых напряжений [σ0] |
||||||
|
|
|
|||||
|
|
|
|
|
|||
Вид заготовки |
Марка материала |
Термообработка, твердость НВ |
[σ0], МПа |
||||
|
Сталь 45 ГОСТ 1050 |
Нормализация, |
|
НВ 200 |
610 |
|
|
Поковка |
Сталь 50 ГОСТ 1050 |
Закалка, отпуск |
|
НВ 240 |
700 |
|
|
Сталь 75, сталь 65Г |
Сорбитизация |
|
НВ 300 |
800 |
|
||
|
ГОСТ 14959 |
Сорбитизация |
|
НВ 330 |
860 |
|
|
|
|
Сорбитизация |
|
НВ 350 |
890 |
|
|
Полное число оборотов колеса Nс |
за срок службы определяют по формуле |
||||||
|
Nс =36·104 ·Тмаш (Vкр·β/ πDк), |
|
|
(2.9) |
где Тмаш – машинное время работы колеса, час, за срок его службы. Для ориентировочных расчетов значение Тмаш принимают в зависимости от группы режима работы по табл. 2.5, в которой значения Тмаш соответствуют среднестатистической долговечности дорожки катания обода колеса.
51
|
Ориентировочные значения Тмаш |
Таблица 2.5 |
|
|
|
|||||||
|
|
|
|
|
|
|
|
|||||
|
|
|
|
|
|
|
|
|
|
|
|
|
|
Группа режима работы |
1М-2М |
|
3М-4М |
5М-6М |
|
|
|
|
|
||
|
Тмаш , ч |
1600 |
|
3200 |
12500 |
|
|
|
|
|
||
|
Срок службы обода, лет |
12 |
|
8 |
|
4-5 |
|
|
|
|
|
|
β – коэффициент, зависящий от времени неустановившегося движения крана. Его ве- |
||||||||||||
личину принимают по табл. 2.6. |
|
|
|
|
|
|
|
|
Таблица 2.6 |
|||
|
Значение коэффициентов β |
|
|
|
|
|||||||
|
|
|
|
|
|
|
|
|||||
Ориентировочное значение длины пробега крана , м |
|
Св. 80 |
80 |
40 |
|
20 |
до 20 |
|
||||
Отношение неустановившегося времени к полному |
0,2 |
|
0,4 |
0,6 |
0,7 |
1,0 |
|
|||||
времени передвижения |
|
|
|
|
|
|
|
|
|
|
|
|
Значения β |
|
|
|
0,9 |
|
0,8 |
0,7 |
0,6 |
0,5 |
|
Ориентировочный путь пробега башенных кранов можно принять при начальном проектировании ≈ 30 м.
θ – коэффициент приведенного числа оборотов ходового колеса принимают по табл. 2.7 в
зависимости от отношения минимальной нагрузки на колесо Рмин |
к максимальной Рмакс. |
||||||||
|
|
Значения θ для существующих кранов |
|
|
Таблица 2.7 |
||||
|
|
|
|
|
|
||||
|
|
|
|
|
|
|
|
|
|
Рмин / Рмакс |
0,2 |
0,3 |
0,4 |
0,5 |
0,6 |
|
0,7 |
|
0,8 |
Значения θ |
0,16 |
0,19 |
0,24 |
0,30 |
0,38 |
|
0,49 |
|
0,63 |
Для башенных кранов отношение Рмин / Рмакс можно принимать ≈ 0,4 - 0,5.
Если при принятых диаметре и материале колес действующие контактные напряжения будут превышать допускаемые, следует поменять материал колес, или их диаметр, или, при необходимости, увеличить количество колес в каждой ходовой тележке и снова провести проверку контактных напряжений.
2.3.3. Определение сопротивлений передвижению крана
При движении крана по рельсовым путям возникают и действуют следующие сопротивления: сопротивление от трения качению колеса по рельсу, сопротивление от трения цапфах колес, сопротивление от трения реборд колес о головку рельса, сопротивления от уклона пути, сопротивление от ветровой нагрузки. Полное сопротивление от трения в ходовых частях при взаимодействии колес ходовых тележек с рельсами можно вычислить по формуле
W |
= (G |
+G |
гр |
) |
µцdц + 2 f |
k |
p |
= w (G |
+G |
), кН, |
(2.10) |
|
|||||||||||
тр |
кр |
|
|
Dк |
|
кр |
|
гр |
|
||
|
|
|
|
|
|
|
|
|
|
|
где Gкр и Gгр – сила тяжести крана и сила тяжести груза; Dк и dц – диаметры колеса и его цапфы (геометрические размеры колес см. в табл. П.13); μц – коэффициент трения подшипников, приведенный к цапфе колеса (табл. 2.8); f – коэффициент трения качения колеса по рельсу (табл. 2.9); kр – коэффициент, учитывающий трение реборд колеса о рельс (для башенных кранов можно принять kр = 1,2). Обобщенный коэффициент сопротивления от трения в ходовых частях w для башенных кранов можно принять по табл. 2.10.
52
Таблица 2.8 Значения коэффициента трения подшипников скольжения и качения μц
|
Подшипник |
|
|
Смазка |
|
|
|
|
|
||||
|
|
|
|
|
|
отсутствует |
|
|
густая |
масляная ванна |
|
||
|
Сколь жения |
|
сталь по стали |
0,14 - 0,16 |
|
0,09 – 0,11 |
0,04 – 0.06 |
|
|||||
|
|
стали по бронзе |
0, 1 |
|
0,06 – 0,08 |
|
|||||||
|
|
|
стали по чугуну |
0,11 – 0,13 |
|
0,07 – 0,09 |
|
||||||
|
|
|
|
|
|
|
|
|
|
|
|
|
|
|
Качения |
|
|
шариковые |
|
|
|
0,01 – 0,015 |
|
|
|
||
|
|
|
роликовые |
|
|
|
0,015 – 0,02 |
|
|
|
|||
|
|
|
игольчатые |
|
|
|
0,05 – 0,07 |
|
|
|
|||
|
|
|
|
|
|
|
|
|
|
|
|
|
|
|
|
|
Коэффициент трения качения f, мм, |
|
|
|
|
Таблица 2.9 |
|||||
|
|
|
стального колеса по рельсу |
|
|
||||||||
|
|
|
|
|
|
|
|
|
|||||
Головка |
|
Диаметр ходового колеса, мм |
|
|
|
|
|
||||||
рельса |
|
200; 250; 320 |
|
400; 500; 560; |
630 |
|
710 |
800; 900 |
1000 |
||||
Плоская |
|
0,3 |
|
0,5 |
|
|
|
0,6 |
0,7 |
0,7 |
|||
Скругленная |
|
0,4 |
|
0,6 |
|
|
|
0,8 |
1,0 |
1,2 |
Таблица 2.10 Обобщенный коэффициент сопротивления движению w башенных кранов по ГОСТ 13994
|
Диаметр, мм |
|
Значения при подшипниках |
||
колеса |
оси |
|
скольжения |
качения |
|
От 200 |
до 400 |
От 50 до 65 |
0,018 |
0,015 |
|
От 400 до 600 |
От 65 |
до 90 |
0,016 |
0,01 |
|
От 600 до 800 |
От 90 |
до 100 |
0,013 |
0,006 |
Сопротивление движению от уклона пути Wу для строительных башенных кранов определяют исходя из предельно допустимой продольной разности отметок рельсовых нитей в соответствии с требованиями Правил устройства и безопасной эксплуатации грузоподъемных кранов. Предельная разность отметок рельсовых нитей в вертикальной плоскости на длине 10 м не должна превышать 50 мм, что соответствует уклону i = 0,005. Величина сопротивления движению на подъем может быть посчитана по формуле
Wу = (Gкр + Gгр)·i, кН. |
(2.11) |
Сопротивление движению от ветровой нагрузки принимается по результатам определения ветровой нагрузки при общем расчете крана. Величина полной фронтальной ветровой нагрузки рабочего состояния на кран с грузом Fфвр принимается по данным таблицы результатов расчета параметров крана в столбце 17 строки 20 [6,7].
Инерционные нагрузки определяют исходя из рекомендуемых величин ускорений для стреловых поворотных кранов при передвижении а ≈ 0,15÷0,2 м/с2 по формуле
Fин = (Gкр + Gгр)·a, кН. |
(2.12) |
53
|
2.3.4. Выбор электродвигателя |
|
||||||
Максимальную статическую мощность привода механизма передвижения |
с учетом |
|||||||
действия указанных сопротивлений определяют по формуле |
|
|||||||
|
|
W |
+W |
у |
+ F + F вр |
|
||
N |
пр |
= |
тр |
|
ин ф |
V , кВт, |
(2.13) |
|
|
|
|
|
|||||
|
|
|
|
|
|
кр |
|
|
|
|
|
|
|
ηтр |
|
ηтр – общий КПД механизма передвижения; ηтр = 0,7 ÷ 0,85.
Прежде чем выбирать конкретные типоразмеры двигателей, следует уточнить необходимое количество приводных тележек для надежного перемещения крана. При передвижении крана по рельсовому пути без буксования сила тяги механизма по сцеплению должна быть больше полного сопротивления передвижению крана:
Fт сц = φ ·ΣRвед ≥ (Wтр + Wу+ Fин + Fфвр). |
(2.14 ) |
Здесь φ – коэффициент сцепления при качении колеса по рельсу. Для башенных кранов, работающих на открытом воздухе,φ = 0,12.Для кранов, работающих в закрытом помещ е- нии, φ = 0,2. Rвед - реакция на ведущее колесо. Сначала проверяют возможность установки двух ведущих ходовых тележек. В этом случаеΣ Rвед = Gкр/ 2. Если при этом предыдущее условие не выполняется, то все четыре ходовые тележки должны быть ведущими и ΣRвед = Gкр. Если и в этом случае сила тяги по сцеплению будет недостаточна, то на кран устанавливают дополнительный балласт, чтобы увеличить сцепной вес и обеспечить выполнение указанного неравенства.
При двух ведущих тележках мощность каждого двигателя будет равна Nдв = Nпр / 2; при четырех - Nдв = Nпр/ 4. Двигатели мощностью до 5 кВт можно брать короткозамкнутые асинхронные серии МТКН или МТКF в соответствии с заданным режимом работы. При большей мощности каждого двигателя используют двигатели с фазным ротором серии МТF или МТН. Для дальнейшего расчета механизма передвижения потребуются следующие параметры электродвигателя: N, кВт– номинальная мощность двигателя при заданном ПВ,% ; nдв, об/мин - частота вращения вала двигателя; J, кг·м2 – момент инерции ротора двигателя; mдв – масса двигателя. Необходимые данные по электродвигателям приведены в табл. П.8.1
– П.8.2
2.3.5. Определение параметров трансмиссии
Ходовое колеса диаметра Dк, м, при заданной скорости передвижения крана Vкр, м/с, должно иметь частоту вращения nк, об/мин, определяемую по формуле
n |
= |
60Vкр |
. |
(2.15) |
|
||||
к |
|
πD |
|
|
|
|
к |
|
Общее передаточное число трансмиссии iтр при номинальной частоте вращения вала двигателя n получают по формуле
iтр = nдв / nк = iр · iоп, |
(2.16) |
где iр - передаточное число редуктора;
iоп - передаточное число открытой передачи.
54
Если конструкция ходовой тележки выполняется по рис. 2.8 или 2.11 и общее передаточное число трансмиссии позволяет применить стандартный редуктор с требуемым передаточным числом, то достаточно выбрать соответствующий типоразмер редуктора ВКУ с учетом вращающего момента на тихоходном валу редуктора Мкт и заданного режима работы механизма. В конструкции по рис. 2.5 применен редуктор типа Ц2. Необходимую величину вращающего момента на тихоходном валу определяют по формуле
Mкт = Nдв · iтр · ηтр / ωдв, кН·м, |
(2.17) |
где ωдв = π · nдв / 30, с-1.
Выбор втулочно-пальцевой муфты типа МУВП для соединения вала двигателя с редуктором осуществляется по крутящему моменту на валу двигателя с учетом коэффициента за-
паса kзм= 1,45. |
|
Mмд = Nдв · kзм / ωдв, кН·м. |
(2.18) |
В табл. П.11 приведены технические характеристики втулочно-пальцевых муфт, из которой выбирают типоразмер муфты, способный передавать расчетный Mмд или несколько больший крутящий момент.
Если предполагается конструкция ходовой тележки, как на рис. 2.1 – 2.3 с использованием приводного агрегата типа ПК-5, то передаточное число открытой передачи будет iоп = iтр / iр , где iр - передаточное число агрегата ПК-5 (табл. 2.1). Приводное зубчатое колесо, непосредственно передающее крутящий момент на ходовое колесо, своим диаметром окружности головок не должно превышать диаметр ходового колеса по дорожке его катания. Ориентировочное значение модуля m зубьев колеса можно взять в табл. П.13.2 для выбранного диаметра ходового колеса. Диаметр начальной окружности зубчатого колеса определяют по формуле dнк = Dк – 2m. Тогда диаметр начальной окружности шестерни будет dнш = dнк / iоп. В дальнейшем необходимо определить остальные геометрические параметры колеса и шестерни и провести проверку зубьев колес на изгибную и контактную прочность.
После выбора параметров трансмиссии необходимо проверить двигатели на время разгона крана до номинальной скорости вверх по уклону против ветра рабочего состояния для второго ветрового района:
|
|
|
|
|
|
|
|
|
|
(Q |
+Q ) D2 |
|
|
||||
|
|
|
n |
1,2 (J |
|
+ J |
|
)+ |
кр |
|
гр |
к |
|
|
|||
|
|
|
|
4 iтр2 |
ηтр |
z |
|
||||||||||
|
|
|
дв |
|
|
р |
|
м |
|
|
|
||||||
t |
р |
= |
|
|
|
|
|
|
|
|
|
|
|
|
, с. |
(2.19) |
|
|
|
|
|
|
|
|
|
|
вр |
|
|
||||||
|
|
|
|
|
|
|
|
|
|
|
|
|
|
|
|||
|
|
|
|
|
(Wтр +Wу + Fин + Fб |
) Dк |
|
||||||||||
|
|
9,55 |
M п − |
|
|
||||||||||||
|
|
|
|
|
|
|
|
|
|
|
|||||||
|
|
|
|
|
ср |
|
|
|
2 iтр ηтр z |
|
|
|
|
||||
|
|
|
|
|
|
|
|
|
|
|
|
|
|||||
В этой формуле: nдв - номинальная частота вращения вала двигателя, об/мин; |
Jр и Jм |
||||||||||||||||
- моменты инерции ротора двигателя и соединительной муфты, кг·м2 ; Qкр и Qгр - масса кра- |
|||||||||||||||||
на и масса груза, кг; Mсрп |
= 1,6·9550 Nдв / nдв |
- средний пусковой момент двигателя, Н·м; |
|||||||||||||||
Wтр, Wу , Fбвр, Fин - |
|
сопротивления движению, Н; |
z – количество приводных тележек; вре- |
мя разгона крана не должно превышать 6 ÷ 8 с.
55
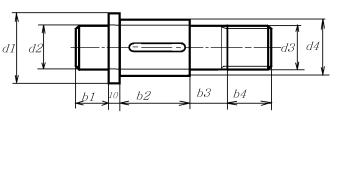
2.3.6. Выбор тормоза
Тормоз механизма передвижения выбирают из условия обеспечения тормозного момента для плавного торможения с нормативной величиной замедления. Величина замедления для строительно-монтажных и стреловых кранов не должна превышать а ≤ 0,15 м/с2.
При таком замедлении время торможения механизма будет составлять |
|
tт = Vкр / a, c. |
(2.20) |
Время торможения не должно превышать 5 ÷ 6 с.
Требуемый тормозной момент на валу двигателя при движении крана по ветру и под
уклон на прямолинейном участке пути вычисляют по формуле |
|
|
|
|
|
|
|
|
|||||||||||||||||
|
|
= (F вр +W |
|
|
) |
Dк |
|
ηо |
|
|
|
|
|
(Q +Q ) |
D2 |
η |
о |
|
|
nдв |
|
|
|
||
M |
|
|
−W |
|
+ 1,2 (J |
|
+ J |
|
)+ |
кр |
гр |
к |
|
|
|
|
, Н·м. |
(2.21) |
|||||||
|
|
2 i |
|
|
|
|
4 i |
|
z |
|
|
9,55 t |
|
||||||||||||
|
т |
б |
у |
тр |
|
|
z |
|
р |
|
м |
|
2 |
|
|
|
|
т |
|
||||||
|
|
|
|
|
|
тр |
|
|
|
|
|
тр |
|
|
|
|
|
|
|||||||
|
|
|
|
|
|
|
|
|
|
|
|
|
|
|
|
|
|
|
|
|
|
|
|
|
|
Здесь Fбвр – нагрузка ветра рабочего состояния, принимаемая по результатам общего расчета крана [6, 7]; остальные обозначения - как в предыдущих формулах. Нужный тип о- размер тормоза, позволяющий реализовать расчетный тормозной момент Мт, выбирают из прил. (табл. П.10.1 – П.10.2).
Результирующая проверка запаса сцепления ходовых колес с рельсами на отсутствие буксования при разгоне на подъем против ветра и на отсутствие юза при торможении механизма под уклон по ветру выполняют по формуле
|
|
(Gкр +Gгр ) |
(ϕ ± w) |
|
|||||
|
|
|
|
||||||
kсц = |
|
|
z |
|
|
|
|
≥1,1. |
(2.22) |
F |
±W |
±W |
у |
± F вр |
|||||
|
|
ин |
тр |
|
|
б |
|
В этой формуле знак «+» принимают при разгоне, знак «-» - при торможении. Силу инерции при разгоне определяют по формуле Fин=(Qкр + Qгр) Vкр/ tр , при торможении -
Fин=(Qкр + Qгр) Vкр/ tт.
По результатам расчета из подобранных унифицированных элементов выполняется компоновочный чертеж механизма передвижения по уже известной или оригинальной схеме. Рама ходовой тележки имеет, как правило, оригинальную конструкцию. Согласно требованиям Правил устройства и безопасной эксплуатации грузоподъемных кранов рама ходовой тележки должна иметь опорные детали на случай поломки ходовых колес или их осей. Опорные детали должны отстоять от головок рельсов не более чем на 20 мм.
2.3.7. Расчет на прочность вала ходового колеса
|
При проектировании механизма передвиже- |
|
ния по рельсовым путям в курсовом проекте |
|
необходимо выполнить расчет на прочность и |
|
долговечность вала ходового колеса и при- |
|
водной шестерни открытой зубчатой переда- |
|
чи (рис. 2.1 и 2.6). На рис. 2.14приведен рас- |
|
четный эскиз вала ходового колеса приводной |
Рис. 2.14. Расчетный эскиз вала ходового |
двухколесной тележки. При определении |
колеса приводной тележки |
размеров вала в начале проектирования ру- |
|
ководствуются следующими соображениями. |
56
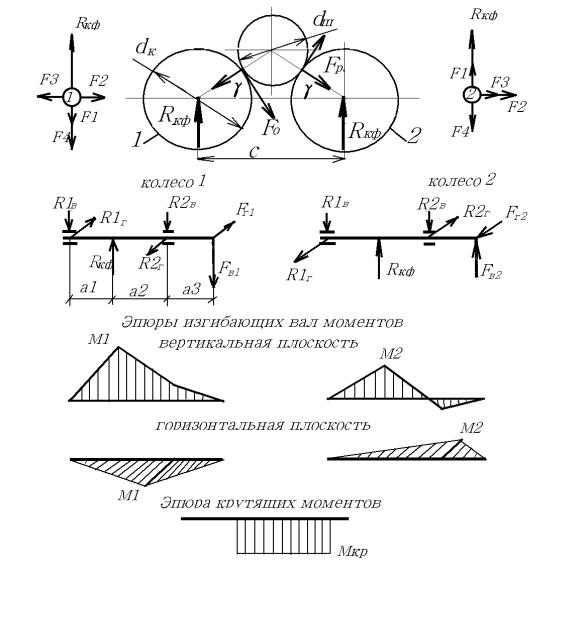
Размер d4 принимают по размеру отверстия dхк выбранного ходового колеса (табл. П.12.1). Диаметр d1= d4+8 мм. Длину b2 вала принимают на 2-3 мм короче, чем ширина L ступицы колеса. Диаметры d2 должны быть меньше d4 на 3-4 мм и быть кра тными 5 для обеспечения посадки k7 роликового сферического подшипника. При нагрузке на колесо Rкф должно выполняться условие Rкф ≤ 2 [Fстп], где [Fстп] – допускаемая статическая нагрузка на подшипник, по которой осуществляется его предварительный выбор. Размеры: b1 = bn – 2 мм; b3 = bn + 10 мм, где bn - ширина подшипника. Длину шлицевой части вала b4 с полным профилем шлицов можно принять b4 ≈ d3. Расчет вала на прочность и долговечность выполняют в соответствии с расчетной схемой (рис. 2.15).
Рис. 2.15. Схема действия сил и их моментов на валы ходовых колес
Кинематическая связь ходовых колес тележки осуществляется зубчатой шестерней с количеством зубьев не менее 17. Ходовые колеса комплектуются серийными зубчатыми колесами, у которых диаметр начальной окружности равен диаметру ходового колеса по дорожке катания (табл. П.13.2). Размер «с» на рис. 2.15 назначают так, чтобы обеспечить удобную установку приводного агрегата (см. рис. 2.4). Величину максимальной окружной силы F0, действующей в зацеплении шестерни с колесами, принимают из условия возможного буксования ходового колеса Fо = Rкф · φ (см. п. 2.3.4). Возникающие в зубчатом зацеплении радиальные силы можно вычислить по формуле
57

Fр = Fо · tg α,
где α = 20° – угол зацепления.
Для удобства дальнейших расчетов окружную Fо и радиальную Fр силы, действующие на валы ходовых колес, разлагают на вертикальные и горизонтальные составляющие.
Схема действия сил на валы ходовых колес, представленная на рис. 2.15, соответствует движению тележки вправо. При движении тележки налево схема действия сил на валы будет аналогичной, только номера валов поменяются местами. Силы, действующие на валы, пр и- нимают сосредоточенными и приложенными в середине опорных поверхностей подшипников и колес. Размеры плеч действующих на вал сил определяют по следующим выражени-
ям: |
|
а1 = (b1+b2) / 2 +10 мм; a2 = (b2 + b3) / 2; а3 = (b3 +b4) / 2. |
(2.23) |
Как видно из эпюр изгибающих моментов, наибольшие нагрузки действуют на вал заднего колеса по ходу движения (колесо 1). Величина наибольшего изгибающего момента в
вертикальной плоскости будет |
М1в = R1в· а1, |
(2.24) |
|
|
|
||
где R1 = |
Rкф a2 + Fв1 а3 |
; Fв1 = F1+F4. |
(2.25) |
|
|||
в |
а1+ а2 |
|
|
|
|
|
Для определения сил F1 и F4 (см. рис. 2.15) угол γ определяют из конструктивного размещения ходовых колес (размер с) так, чтобы количество зубьев шестерни zш было не менее 17. Тогда dш = zш · m. Модуль m можно предварительно принять по серийно выпускаемым блокам ходовых колес (табл. П.13.2).
γ = arc cos |
|
|
c |
|
||
|
|
|
. |
(2.26) |
||
dø |
+ dê |
|||||
Расчетный изгибающий момент в горизонтальной плоскости будет равен |
|
|||||
Мрг = R1г· a1, |
(2.27) |
|||||
где - R1 = |
Fг a3 |
; |
Fг = F2 – F3. |
(2.28) |
||
|
||||||
г |
a1+ a2 |
|
|
|
||
|
|
|
|
Суммарный изгибающий момент в опасном сечении
|
|
|
|
|
|
|
|
М |
из |
= М1 2 |
+ М |
2 . |
(2.29) |
||
|
|
в |
|
рг |
|
Крутящий момент на валу колеса
Мкр = Fо· dк / 2. |
(2.30) |
Расчет на статическую прочность сводится к определению запаса прочности по отношению к пределу текучести по нормальным и касательным напряжениям
n |
= |
σТ |
, |
n |
= |
τT , |
(2.31) |
|
Тσ |
|
σ |
из |
|
Tτ |
|
τ |
|
|
|
|
|
|
|
|
|
58

σиз = |
М |
из ; τ = |
Мкр |
. |
(2.32) |
|
Wкр |
||||
|
Wиз |
|
|
Предел текучести по касательным напряжениям можно условно принимать по соотношению τТ ≈ 0,6 σТ. Формулы для определения моментов сопротивления валов наиболее распространенных видов поперечных сечений приведены в табл. П.15.
Запас прочности при совместном действии нормальных и касательных напряжений
n |
= |
|
nTσ nTτ |
|
|
[n |
]. |
(2.33) |
|
|
|
|
|
||||||
T |
|
|
n |
2 + n |
2 |
|
T |
|
|
|
|
|
|
|
|
|
|||
|
|
|
Tσ |
Tτ |
|
|
|
|
|
В табл. 2.11 приведены минимально допускаемые коэффициенты запаса прочности по пределу текучести [nT] для деталей механизма передвижения.
Таблица 2.11
Коэффициенты запаса прочности по пределу текучести [nT]
Группа режима работы |
1М, 2М |
2М, 3М |
4М, 5М |
6М |
Механизмы передвижения крюковых кранов |
1,2 |
1,3 |
1,4 |
1,6 |
Если полученный коэффициент запаса оказался меньше допускаемого, следует применить более прочную сталь (табл. П.6.1).
Расчет на выносливость заключается в определении коэффициента запаса прочности по пределу выносливости для опасного сечения. Опасными сечениями обычно являются сечения, где имеют место концентраторы напряжений (шпоночные канавки, галтели, шлицы, соединения с другими деталями и пр.). Напряжения для этих сечений определяют по формуле
σ = |
Кσ |
Миз |
2 + Мкр |
2 |
|
, |
(2.34) |
|
W |
|
|
||||
|
|
|
|
|
|
|
где W – момент сопротивления при изгибе рассматриваемого сечения (табл. П.15);
Кσ – среднее значение коэффициента концентрации напряжений для этого сечения. Предварительно можно принять:
-для шпоночных канавок, выточек и галтелей при r / d ≈ 2 Кσ = 2;
-для прямоугольных шлицов Кσ = 2,5;
-для эвольвентных шлицов и валов-шестерен Кσ = 1,7;
-при посадке подшипников с натягом Кσ = 3.
Общий запас прочности по усталости определяется по формуле
n = |
|
nσ nτ |
|
|
≥ [n], |
(2.35) |
|
|
|
|
|
|
|||
|
|
nσ |
2 + nτ |
2 |
|
|
|
где nσ, nτ – коэффициенты запаса прочности по выносливости при изгибе и кручении; n
– коэффициент запаса прочности по выносливости. В табл. 2.12 приведены наименьшие допустимые коэффициенты запаса прочности по выносливости для механизмов передвижения.
59
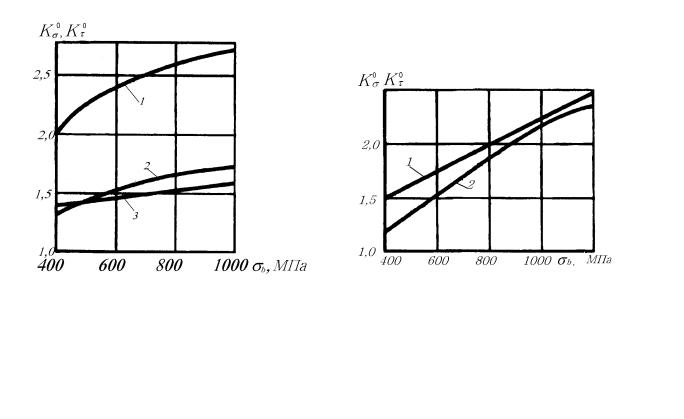
Таблица 2.12
Коэффициенты запаса прочности по выносливости [n]
Группа режима работы |
|
|
|
|
1М, 2М |
|
|
2М, 3М |
4М, 5М |
6М |
|
||||||
Механизмы передвижения крюковых кранов |
|
|
1,3 |
|
|
|
|
|
|
1,4 |
1,6 |
1,7 |
|
||||
При симметричном цикле изменения напряжений (вращающиеся детали) коэффициен- |
|||||||||||||||||
ты nσ, nτ вычисляют по формулам |
σ−1 |
|
|
|
|
|
τ−1 |
|
|
|
|
|
|||||
nσ = |
|
|
|
; nτ = |
|
|
|
. |
|
(2.36) |
|||||||
|
Кο' |
σ |
|
|
|
Kτ' |
|
τ |
|
|
|||||||
|
|
β εσ |
|
αE |
|
|
|
β ετ |
|
|
αE |
|
|
|
В этих формулах приняты следующие обозначения:
σ-1, τ-1 – пределы выносливости стали при изгибе и кручении при симметричном цикле изменения напряжений; σ-1 = 0,43 σb; τ-1 = 0,22 σb. σb – предел прочности стали при растяжении.
К'σ , К'τ – коэффициенты концентрации напряжений для рассчитываемого сечения вала при изгибе и кручении.
К'σ = К0σ + Кnσ - 1; |
(2.37) |
К'τ = К0τ + Кnτ –1, |
|
где К0σ, К0τ - эффективные коэффициенты концентрации для шлицов, шпоночных канавок, галтелей. Их значение определяют по графикам на рис. 2.16, 2.17, 2.18.
Рис. 2.16. Значения К0σ и К0τ для шлицов: |
Рис.2.17. Значения К0σ и К0τ |
||
1 |
– К0τ для прямобочных; |
в шпоночной канавке: |
|
2 |
– К0σ для прямобочных и эвольвентных |
1 |
- К0σ ; |
3 |
– К0τ для эвольвентных |
2 |
- К0τ |
60