
Учебное пособие 800490
.pdf
|
b ≥ Lб ctg (α / 2) . |
(1.11) |
||||||||
Толщинустенки барабана предварительно определяют поформуле с округлением до 1 мм: |
||||||||||
|
δ = |
Fфαn |
, мм, |
(1.12) |
||||||
|
[σ] t |
|
||||||||
где Fф - усилие в канате в Н, t – мм; |
αn =1,4 - при двухслойной навивке; |
|
||||||||
αn = 1- при однослойной навивке; |
|
|||||||||
[σ], МПа – допускаемые напряжения для материала барабана (см. табл. 1.1). |
|
|||||||||
Стенка барабана должна быть проверена на устойчивость по формуле |
|
|||||||||
|
n = |
|
σк |
|
|
≥ [n], |
(1.13) |
|||
|
|
|
|
|
||||||
|
|
ψ σф |
|
|
|
|||||
где n – коэффициент запаса устойчивости цилиндрической стенки. Для стальных бара- |
||||||||||
банов [n] ≥ 1,7; для чугунных - [n] ≥ 2,0; |
|
|
|
|
|
|
|
|
|
|
σк - критическое напряжение, |
МПа; σн – номинальные напряжения, МПа. |
|
||||||||
|
|
|
ЕкSк |
− |
1 |
|
|
|||
|
|
2 |
|
|
||||||
|
|
|
|
|
, |
(1.14) |
||||
|
|
|
|
|||||||
|
ψ = 1+ |
|
Е δ |
t |
|
|||||
|
|
|
б |
|
|
|
|
|
|
|
где Ек – модуль упругости канатов; Ек = 9·104 МПа – модуль упругости каната с органическим сердечником; Ек = 11·104 ,МПа - модуль упругости каната со стальным сердечником; Еб = модуль упругости стенки барабана; Еб = 19 · 104 МПа для стальных литых барабанов; Еб = 1·105 МПа – для чугунных барабанов; Sк - площадь сечения всех проволок в канате, мм2; δ,мм - расчетная толщина стенки барабана.
σ |
к |
= 0,92Е δ |
|
2δ |
|
, МПа; |
(1.15) |
|
D |
||||||||
|
δ l |
|
|
|
||||
|
|
|
|
б |
|
|
|
l – расстояние между торцевыми стенками барабана или кольцом жесткости и торцевой стенкой, мм.
Фактические напряжения в стенке барабана
|
|
σ |
|
= |
Fф |
, МПа. |
|
|
|
|
|
ф |
δ t |
|
|
|
|||||
|
|
|
|
|
|
|
|
|
||
|
Допускаемые напряжения для расчета барабанов |
Таблица 1.1 |
||||||||
|
|
|||||||||
|
|
|
|
|
|
|
||||
|
Допускаемые напряжения [σ], МПа, |
для режимов |
работы |
|||||||
Марка стали |
|
|
|
|
|
|
|
|
|
|
2М – 3М |
|
4М |
|
|
5М |
|
6М |
|||
|
|
|
|
|
||||||
|
|
|
|
|
|
|
|
|
||
ВМСт3сп |
170 |
|
150 |
|
|
130 |
|
110 |
||
|
|
|
|
|
|
|
|
|
||
20 |
180 |
|
160 |
|
|
140 |
|
120 |
||
|
|
|
|
|
|
|
|
|
||
09Г2С |
225 |
|
195 |
|
|
165 |
|
140 |
||
|
|
|
|
|
|
|
|
|
||
35Л-1 |
210 |
|
170 |
|
|
140 |
|
120 |
||
|
|
|
|
|
|
|
|
|
|
|
21
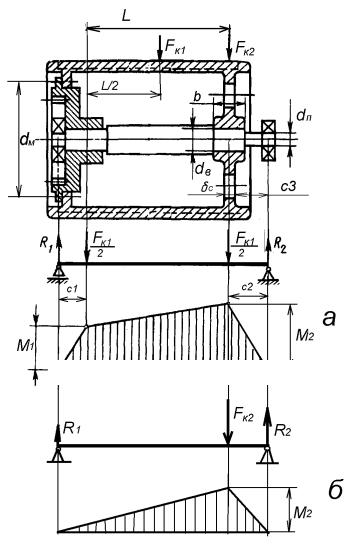
Частоту вращения барабана определяют исходя из заданной скорости подъема груза:
|
60V |
×i |
|
|
|
, мин – 1 |
|
Vгр |
×iп |
|
|
|
|
|
|
n = |
гр |
п |
|
|
= |
|
|
|
|
|
|
,с−1 . |
(1.16) |
||
б |
π(D + d |
к |
) |
|
|
π(D |
б |
+ d |
к |
) |
|
|
|||
|
б |
|
|
|
|
|
|
|
|
|
|
|
Ось барабана должна быть проверена расчетом в зависимости от его конструктивного исполнения. Наиболее распространенный вариант установки барабана на оси показан на рис. 1.22. Такой вариант применяют при использовании унифицированных редукторов, у которых выходной вал имеет зубчатую полумуфту. В строительных кранах грузовые лебедки чаще всего используют с одинарным полиспастом. В таких лебедках место приложения усилия грузоподъемного каната перемещается вдоль барабана при сматывании, (наматывании) каната. Расчет оси барабана на прочность следует рассмотреть для двух случаев.
Первый случай – канат на барабане располагается на одинаковом расстоянии от торцевых стенок барабана, опирающихся на ось. На барабан действует усилие Fк1= Fф. На ось в опорных точках от стенок барабана передаются усилия Fк1 / 2 (расчетная схема и эпюра изгибающих ось моментов показаны на рис. 1.22, а).
Второй случай – канат на барабане располагается над одной из торцевых стенок, опирающихся на ось. На ось от барабана передается усилие Fк2=Fф (расчетная схема и эпюра изгибающих ось моментовпредставлена рис. 1.22, б).
Геометрические размеры элементов оси и барабана, необходимые для определения опорных реакций на этом этапе проектирования, принимают по предыдущим расчетам и следующим рекомендациям. Расстояние между торцевыми стенками барабана равно расчетной длине Lб; толщина торцевых стенок δс ≈ 1,2 δ; длина ступицы b ≈ 3 δс; расстояние от торца ступицы до оси подшипника стараются сделать минимальным. Ориентировочно можно принять с3 ≈ 100 мм. С учетом этих размеров можно определить опорные реакции R1 и R2, и предварительно выбрать подшипник по допустимой статической нагрузке. Для опор осей барабанов обычно применяют роликовые сферические подшипники (ГОСТ 5721-85) для устранения изгибающих моментов в опорах и упрощения монтажных работ.
22
Реакцию R2 для первого случая нагружения оси определяют из суммы моментов сил
относительно точки опоры 1: |
|
0.5Fф(2c1 + L ) |
|
|
|||||
|
R2 = |
|
, кН. |
(1.17) |
|||||
|
|
|
с1 + с2 |
+ L |
|
||||
|
|
|
|
|
|
|
|||
Реакцию R2 |
для второго случая нагружения оси определяют аналогично: |
|
|||||||
|
R |
= |
Fф(c1 + L ) |
, кН. |
(1.18) |
||||
|
|
||||||||
|
2 |
|
|
с |
+ с |
+ L |
|
|
|
|
|
1 |
2 |
|
|
|
|
||
Реакцию R2 |
для каждого случая можно найти из суммы проекций сил на ось Y. |
|
|||||||
Изгибающие моменты М1 и М2 в каждом случае определяют как |
|
||||||||
|
М1 = R1· с1; |
М2 = R2· с2. |
(1.19) |
Диаметр оси барабана определяют по формуле (1.7). Величину допускаемых напряжений в этой формуле следует принимать с учетом симметричной циклической нагрузки, действующей на ось, определив их по упрощенной формуле
[σ−1]= |
σ−1 |
|
, |
(1.20) |
|
к |
[n |
] |
|||
|
о |
0 |
|
|
|
где к0 – коэффициент, учитывающий конструкцию детали (для валов и осей к0 = 2,0…2,8); [n0] – коэффициент запаса прочности, принимаемый по режиму работы механизма
(для режима работы 1М - 3М n0 =1,4; 4М n0 = 1,5; 5М n0 = 1,6; 6М n0 =1,7).
Для стали 45 с термообработкой на улучшение можно принять σ-1 = 260 МПа; для стали 40ХН с термообработкой на улучшение σ-1 = 440 МПа.
После определения диаметра оси уточняют возможность установки на ней выбранных подшипников. Окончательно выбранный типоразмер подшипника проверяют на долговечность в часах по формуле
|
C p |
106 |
≥ Тн. |
|
||
L |
= a |
|
|
(1.21) |
||
60n |
||||||
h |
|
P |
|
|
||
|
|
|
б |
|
|
Коэффициент а для сферических шариковых подшипников а = 0,5 - 0,6; для сферических роликовых - а = 0,3 – 0,4.
С – динамическая грузоподъемность подшипника по справочнику [2].
р – показатель степени в формуле долговечности: для роликовых подшипников р = 3.33; для шариковых р = 3; пб – частота вращения барабана, об/мин;
Р - эквивалентная динамическая нагрузка,
Р = (Х·V·Fр + Y·Fо)·Kб·Kт, H; |
(1.22) |
Х – коэффициент радиальной нагрузки (табл. 1.2); Y – коэффициент осевой нагрузки (табл. 1.2);
V – коэффициент вращения (табл. 1.2);
Fр - радиальная нагрузка на подшипник, Н; ее можно условно принять равной R2 по первому варианту нагружения оси: Fр= R2;
23
Fо - осевая нагрузка на подшипник при допустимом отклонении угла каната на нарезном барабане в 6° составит Fо = Fф sin 6°;
Kб - коэффициент безопасности. Для грузовых лебедок Kб = 1,2;
Кт – температурный коэффициент подшипника: при температуре до 125 °С – Кт = 1,05.
|
Значения коэффициентов X, Y, V, e |
для радиальных |
Таблица 1.2 |
|||||||||||||
|
|
|
||||||||||||||
|
сферических двухрядных подшипников |
|
|
|
|
|||||||||||
|
V |
|
|
|
|
X |
|
|
|
|
Y |
|
e |
|||
Внутреннее кольцо |
|
Fo |
|
|
|
Fo |
|
|
Fo |
|
Fo |
|
||||
|
|
|
|
|
≤ e |
|
|
> e |
|
|
|
≤ e |
|
|
> e |
|
вращается |
неподвижно |
|
|
|
|
|
|
|
|
|
|
|||||
F V |
|
|
F V |
F V |
|
F V |
|
|||||||||
|
|
|
p |
|
|
|
p |
|
|
p |
|
p |
|
|
||
1 |
1 |
|
|
1 |
0,65 |
|
0,42 ctg α |
0,65 ctg α |
0,42 ctg α |
Примечание: величина угла α° для каждого типоразмера подшипника приведена в справочнике [2]
Необходимую долговечность в часах Тн определяют по числу циклов работы механизма за нормативный срок службы Zнс (формула (1.2)). Если не заданы параметры цикла, ориентировочное время работы механизма подъема в течение цикла можно посчитать по формуле
tпо= 0,025·(Нгр / Vгр ) , мин. |
(1.23) |
|||||||||
Время работы механизма за нормативный срок службы будет |
|
|||||||||
Тн = (tпо · Zнс) / 60, часов. |
(1.24) |
|||||||||
1.4.7. Определение потребной мощности и выбор электродвигателя |
|
|||||||||
Статическая потребная мощность для подъема номинального груза массой Q(т) cо |
||||||||||
скоростью Vгр (м/с) может быть подсчитана по формуле |
|
|||||||||
N |
с |
= |
|
Q g Vгр |
, кВт, |
(1.25) |
||||
|
|
|
||||||||
|
|
|
η |
п |
η |
р |
|
|||
|
|
|
|
|
|
|
||||
где g – ускорение свободного падения, g = 9,81 м/с; |
|
|||||||||
ηп – КПД полиспаста, определяемый в зависимости от кратности полиспаста и |
КПД |
|||||||||
входящих в него блоков η по формуле |
|
|
|
|
|
|
|
|||
ηп = |
1−ηiп |
|
η . |
(1.26) |
||||||
i (1−η) |
||||||||||
|
|
|
|
п |
|
|
|
|
|
|
Среднее значение КПД блока на подшипниках качения при угле охвата его канатом 180° принимают равным η ≈ 0,98.
КПД редуктора зависит от типа редуктора и количества ступеней. КПД одной цилиндрической зубчатой пары в масляной ванне с валами на подшипниках качения принимают ηцп = 0,98; КПД конической зубчатой пары при работе в аналогичных условиях принимают ηкп = 0,97; червячная пара при однозаходном червяке имеет КПД ηчп = 0,74.
КПД двухступенчатого редуктора с цилиндрическими зубчатыми колесами в проектных расчетах можно принимать равным ηр = ηцп2 = 0,96. Аналогично определяют КПД редукторов с различной комбинацией типов передач.
Подбор электродвигателя ведут по предварительной мощности, которая учитывает назначение крана, режим работы механизма, вид управляющего устройства коэффициентом Кр. Механизмы подъема строительных кранов можно отнести к группе режима работы М2
– М5 с числом включений в час электропривода 60 - 150. В зависимости от вида двигателя и способа его регулирования коэффициент Кр принимает следующие значения (табл. 2).
24
|
Значения Кр |
для различных типов приводных двигателей |
Таблица 1.3 |
||||||||||
|
|
|
|
||||||||||
|
|
|
|
|
|
|
|
|
|
|
|
||
Тип дви- |
Двигатель |
асинхрон- |
Двигатель с фазным ро- |
Двигатель с фазным ро- |
|||||||||
гателя |
ный короткозамкну- |
тором, торможение про- |
тором, торможение ди- |
|
|||||||||
|
тый |
|
|
|
тивовключением |
|
намическое |
|
|
||||
Режимы |
М2, М3 |
|
М4 |
|
М5 |
М2, М3 |
М4 |
|
М5 |
М2, М3 |
М4 |
М5 |
|
Кр |
1,35 |
|
1,00 |
|
0,65 |
1,45 |
1,20 |
|
0,95 |
1,50 |
1,30 |
1,10 |
|
Предварительная мощность двигателя рассчитывается по формуле |
|
|
|
||||||||||
|
|
|
|
|
|
Nэ = Nc / Кр. |
|
|
|
(1.27) |
Основные технические данные крановых электродвигателей приведены в табл. П.8.2, П.8.3. Для механизма подъема груза при мощности до 5 кВт можно применять асинхронные короткозамкнутые двигатели. При больших потребных мощностях предпочтение отдается двигателям с фазным ротором. Двигатели серий МТF, MTH, 4МТН выполнены с фазным ротором, серии МТКF, МТКН – с короткозамкнутым ротором. Нужный двигатель выбирают по его мощности при соответствующей продолжительности включения ПВ(%). Режиму работы механизма М2, М3 соответствует ПВ( 25%), режиму М4 – ПВ(40%). Для дальнейших расчетов потребуются следующие данные выбранного электродвигателя:
-фактическая мощность Nфэ, кВт;
-частота вращения вала nдв, об/мин;
-максимальный момент Ммакс, Н·м;
-момент инерции ротора GD2, кг·м2;
-масса двигателя mдв, кг.
Методика проверки электродвигателя на нагрев с учетом режима работы механизма приведена в главе 5 настоящего пособия.
1.4.8. Выбор редуктора
Рациональный подход к проектированию механизмов заключается в максимально возможном использовании стандартных или серийно выпускаемых элементов, узлов, агрегатов. В табл. П.9.1 – П.9.5 приведены технические данные серийно выпускаемых редукторов с цилиндрическими колесами. Для выбора редуктора можно использовать и другие источники, приведенные в библиографическом списке. При выборе редуктора учитываются следующие факторы:
-относительное расположение входных и выходных валов, оговоренных исполнением редуктора;
-передаточное число iр;
-допустимые нагрузки на выходной вал: крутящие Мт, радиальные Fр;
-номинальная частота вращения входного (быстроходного) вала nдв;
-габаритные размеры корпуса редуктора L× В × Н, мм;
-коэффициент полезного действия ηр;
-уровень шума;
-относительная стоимость, руб./ Н·м.
Требуемое передаточное число редуктора iрт определяют по формуле
iрт = nдв / nб. |
(1.28) |
25
Крутящий момент на тихоходном валу вычисляют из условия действия усилия, приложенного к барабану грузоподъемным канатом при подъеме испытательного груза:
|
|
Мт =[1,25Fф (Dб + dк ) /2] Креж , кН·м, |
(1.29) |
||||||
Креж – коэффициент режима работы: Креж = Кдв Кпв Кс Км Крев; |
|
||||||||
Кдв = коэффициент, зависящий от вида двигателя. Для электродвигателей |
Кдв= 1;че- |
||||||||
тырех-, шестицилиндровых двигателей внутреннего сгорания Кдв = 1,2; |
|
||||||||
Кпв - коэффициент, зависящий от продолжительности включения (табл.1.4). |
|
||||||||
|
|
|
|
|
|
|
|
Таблица 1.4 |
|
|
Значения Кпв для различной продолжительности |
|
|||||||
|
|
|
включения привода ПВ, % |
|
|
|
|||
|
|
|
|
|
|
|
|
|
|
|
ПВ,% |
100 |
|
60 |
40 |
25 |
15 |
|
|
|
|
|
|
|
|
|
|
|
|
|
Кпв |
1,00 |
|
0,90 |
0,80 |
0,70 |
0,67 |
|
|
|
|
|
|
|
|
|
|
|
|
Кс = коэффициент, зависящий от продолжительности работы в течении суток.
Для башенных кранов, работающих на строительстве Кс = 1; работающих на погрузоч- но-разгрузочных работах Кс = 1,2;
Км - коэффициент, зависящий от характера работы приводимой машины. Работа ба-
шенного крана характеризуется умеренными толчками. Нагрузка в течение цикла не меняет-
ся, Км = 1,2.
Крев - коэффициент реверсивности. Хотя механизм подъема груза на кранах реверсируется, но фактически нагрузка на зубья колес редуктора всегда приложена с одной стороны:
Крев = 1,00.
Редуктор, выбираемый по табл. П.9.2, комплектуют с двигателем, имеющим частоту вращения вала 940 ÷ 875 об/мин, или с двигателем 720 ÷ 585 об/мин, что соответствует числу оборотов быстроходного вала редуктора nб 16 с-1 или 10 с-1.
Выбранный типоразмер редуктора обозначают по следующей форме, например: «Редуктор Ц2-350-31,5-11КвхМ». Это означает: редуктор с цилиндрическими колесами, двухступенчатый, межосевое расстояние входного и выходного валов 350 мм, передаточное число 31,5, вариант сборки 11, с коническим быстроходным валом и выходным валом под зубчатую муфту. Геометрические параметры редуктора приведены в табл. П.9.1. В табл. П.9.3 – П.9.5 содержатся геометрические параметры входных и выходных концов валов редукторов различных типоразмеров.
Передаточное число iр выбранного серийного редуктора часто точно не совпадает с требуемым iрт . В этом случае корректируют диаметр барабана с точностью ± 5 мм для
обеспечения заданной скорости подъема груза по формуле |
|
||||
D = |
60 Vгр iп |
− d |
к |
, |
(1.30) |
|
|||||
б |
π nбф |
|
|
||
|
|
|
|
где фактическая частота вращения барабана nбф = nдв / iрт .
Применение унифицированных узлов в проектируемых машинах не всегда позволяет получить конструкцию, в полной мере отвечающую технологическим, эксплуатационным, эргономическим и дизайнерским требованиям рынка грузоподъемной техники. Применение в трансмиссии грузоподъемных лебедок специальных дифференциальных вставок или
26

встроенных в канатный барабан планетарных редукторов позволяет значительно улучшить потребительские свойства таких агрегатов. Ранее (рис. 1.11 – 1.14) были показаны конструкции планетарных редукторов, применяемых в грузоподъемных лебедках. Определение передаточных чисел и угловых скоростей выходных звеньев в этих конструкция определяют следующим образом.
На рис. 1.23 приведена кинематическая схема дифференциальной вставки, используемая в приводе лебедки на рис. 1.11. На этой схеме обозначены: первая приводная центральная шестерня с числом зубьев z1 и угловой скоростью ω1; водило Н с угловой скоростьюωн ; сателлит с числом зубьев z2 ; центральное колесо, имеющее число зубьев z3 внутреннего зацепления и число зубьев z5 внешнего зацепления; вторая приводная шестерня z4 с угловой скоростьюω 4. С п о- мощь такого механизма можно получить несколько значений угловой скоростиω н выходного звена Н при заданных значениях угловых ско-
ростей ω1 и ω4.
Вариант 1. Скоростиω 1 и ω4 совпадают по направлению (вращение по часовой стрелке, если смотреть со стороны входа). В этом случае
Рис. 1.23. Расчетная кинематическая угловая скорость ωн выходного звена будет
схема дифференциальной вставки двухдвигательной лебедки
|
ω |
− |
z3 |
z4 |
ω |
4 |
|
|
||
|
|
|
|
|
|
|||||
1 |
|
z1 |
z5 |
. |
(1.31) |
|||||
ωí = |
|
|
|
|||||||
|
1+ |
z3 |
|
|
|
|||||
|
|
|
|
|
|
z1
Вариант 2. Скорость звенаω1 имеет противоположное направление относительно варианта 1; ω4 сохраняет прежнее направление. Для этого варианта скоростьω н выходного звена будет
|
|
−ω |
− |
z3 |
z4 |
ω |
4 |
|
|
|
|
|
|
|
|
|
|||||
ωí |
1 |
|
z1 |
z5 |
. |
(1.32) |
||||
= |
|
|
|
|||||||
|
1+ |
z3 |
|
|
|
z1
Вариант 3. Скорость звенаω 1 имеет направление вращения по варианту 1, а скорость ω4 имеет противоположное направление. Тогда
|
ω |
+ |
z3 |
z4 |
ω |
4 |
|
||
|
|
|
|
|
|||||
1 |
|
z1 |
z5 |
(1.33) |
|||||
ωí = |
|
|
|
||||||
|
1+ |
z3 |
|
|
|
||||
|
|
|
|
|
z1
Вариант 4. Звено с колесом z1 остановлено. Скорость ω1 = 0. В этом случае
27
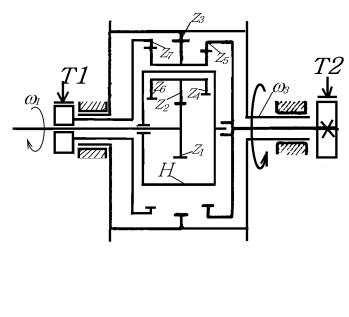
|
− |
z3 z4 |
|
ω |
|
||||||
|
|
|
|
|
|||||||
ωí = |
|
|
z1 z5 |
4 |
. |
(1.34) |
|||||
|
|
|
|
||||||||
|
|
|
|
|
|
||||||
|
|
|
1+ |
z3 |
|
|
|
|
|
||
|
|
|
z |
|
|
|
|
||||
|
|
|
|
|
|
|
|
|
|||
|
|
|
1 |
|
|
|
|
|
|||
Вариант 5. Звено с колесом z4 остановлено. Скорости ω3 = 0, ω4 = 0, |
|
||||||||||
ω5 = 0. В этом случае передача становится планетарной. |
|
||||||||||
ωí |
= |
|
z1 ω1 |
|
|
|
(1.35) |
||||
|
z1 + z3 |
|
|
|
|||||||
|
|
|
|
|
|
|
|
Использование канатного барабана как корпуса редуктора позволяет получить очень компактную грузоподъемную лебедку. Применение планетарного редуктора для такого конструктивного исполнения лебедки является весьма целесообразным для повышения долго-
|
вечности |
и надежности работы |
грузо- |
||
|
подъемного механизма. |
|
|||
|
Представленная на рис. 1.24 кинема- |
||||
|
тическая схема встроенного в барабан ле- |
||||
|
бедки |
редуктора |
представляет |
собой |
|
|
планетарный |
механизм. Конструктивной |
|||
|
особенностью |
этого механизма является |
|||
|
наличие |
у сателлита трех зубчатых вен- |
|||
|
цов z2, z4, z6 и двух нормально замкнутых |
||||
|
тормозов Т1 и Т2, позволяющих управ- |
||||
|
лять угловой скорость центральных колес |
||||
|
z5 и z7. При включении тормозов Т1 и Т2 |
||||
|
колес z5 |
и z7 |
освобождаются и механизм |
||
|
получает две степени свободы, т.е. стано- |
||||
Рис. 1.24. Кинематическая схема планетарного |
вится дифференциальным механизмом и |
||||
для практической |
работы неприменим. |
||||
редуктора, управляемого двумя тормозами |
При включении только тормоза Т1 осво- |
||||
|
|||||
|
бождается центральное колесо z7 (колесо |
z5 остановлено), механизм работает как планетарный с входным звеном z1 , звеньями z2 – z4, z5, водилом Н и выходным звеном z3. При отключении тормоза Т1 и включении тормоза Т2 освобождается центральное колесо z5 (колесо z7 остановлено), механизм работает как планетарный с входным звеном z1 , звеньями z2 – z6, z7, водилом Н и выходным звеном z3. Это дает возможность получить две скорости колеса z3, непосредственно вращающего барабан лебедки.
В первом случае номинальную угловую скорость барабана лебедки можно вычислить
по формуле |
|
|
|
|
|
z2 z5 |
|
|
|
|||||||
|
|
1− |
|
|
|
|
||||||||||
|
|
|
z3 z4 |
. |
(1.36) |
|||||||||||
ω |
=ω |
|
|
|
||||||||||||
|
|
|
|
|
|
|
||||||||||
3 |
1 |
1+ |
|
z2 |
z5 |
|
|
|
||||||||
|
|
|
z |
|
|
|
|
|
||||||||
|
|
|
|
|
|
z |
4 |
|
|
|
|
|
|
|||
|
|
|
|
|
1 |
|
|
|
|
|
|
|
|
|||
Во втором случае номинальную угловую скорость барабана рассчитывают по формуле |
||||||||||||||||
|
|
1− |
|
z2 |
z7 |
|
|
|
||||||||
ω |
=ω |
|
z3 |
z6 |
. |
(1.37) |
||||||||||
|
|
|
||||||||||||||
|
|
|
z2 |
|
||||||||||||
3 |
1 |
1+ |
|
z7 |
|
|
|
|||||||||
|
|
|
|
|
|
|||||||||||
|
|
|
|
|
|
z z |
6 |
|
|
|
|
|
|
|
||
|
|
|
|
|
1 |
|
|
|
|
|
|
|
|
28
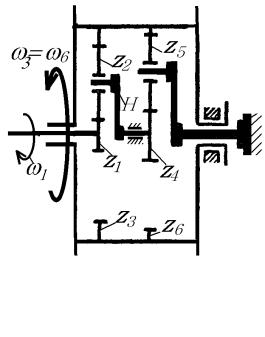
Рис. 1.25. Кинематическая схема
замкнутого дифференциального механизма
На рис. 1.25 показана кинематическая схема редуктора, установленного в барабане гидрофицированной лебедки, изображенной на рис. 1.14. Такойр е- дуктор относится к замкнутым дифференциальным механизмам. В нем можно условно выделить два механизма.
Первый механизм является дифференциальной передачей, состоящей из ведущего центрального колеса z1, сателлита z2, размещенного на водиле Н, и центрального колеса с внутренним зацеплением z3.
Второй механизм представляет собой простой редуктор, состоящий из центрального колеса z4, промежуточного колеса z5 с неподвижной осью и центрального колеса z6. Передаточное число такого редуктора будет
i4-6 = - z6 / z4. |
(1.38) |
Передача движения от первого механизма на второй осуществляется водилом Н на колесо z4. Вследствие чегоω н = ω4. При этом водило Н и центральное зубчатое колесо z3 замкнуты через зубчатую передачу z4, z5, z6, поскольку ω3 = ω6. Передаточное число первого механизма с учетом вышесказанного и при остановленном водиле Н можно вычислить по формуле
i1-3 = i1-3 (1 – iн-3) + iн-3. |
(1.39) |
Полное передаточное число всего механизма соответственно получим
ip = i1-6 |
= − |
z3 |
− |
z3 |
z6 |
− |
z6 |
. |
(1.40) |
||
z |
z |
z |
|
|
|||||||
|
|
|
4 |
|
z |
4 |
|
|
|||
|
1 |
1 |
|
|
|
|
|
Из полученного следует, что направление вращения выходного звена z3 - z6, которое единос барабаном лебедки, всегда противоположно направлению вращения входного звенаz1.
При проектировании лебедок со встроенным планетарным редуктором необходимо решать задачи по определению количества зубьев на колесах, модуля зубьев и, как следствие, диаметров колес, позволяющих вписать планетарный редуктор внутрь грузоподъемного барабана, обеспечив при этом прочность зубьев колес по изгибным и контактным напряжениям.
Для примера воспользуемся редуктором, кинематическая схема которого показана на рис. 1.25. Такой редуктор имеет высокий КПД и часто применяется в различных машинах с диапазоном передаточных чисел 10…60. Порядок решения поставленных задач может быть следующим.
Из предыдущего расчета используют следующие параметры: диаметр барабана Dб, окружное усилие на барабане Fф, частота вращения барабана nб, частота вращения вала двигателя nдв. При этом для реализации окружного усилия на барабане должен действовать вращающий момент
Мб = Fф · Dб / 2. |
(1.41) |
29
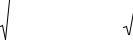
Требуемое передаточное число редуктора будет
iр = nдв / nб. |
(1.42) |
Для удобного конструктивного исполнения редуктора и упрощения кинематических расчетов можно принять одинаковым соотношение чисел зубьев колес дифференциальной z3/z1 и замыкающей z6/z4 частей. Обозначив кинематические соотношения
z3/z1 = z6/z4 = х,
выражение (1.40) можно записать в виде квадратного уравнения
х2 + 2х + iр = 0.
Решением этого уравнения будет выражение
|
2 |
|
22 |
|
|
|
|
|
|
х = − |
± |
−(−ip ) = −1+ 1+ip . |
(1.43) |
||||||
2 |
4 |
||||||||
|
|
|
|
|
|
|
Подставив в формулу (1.43) требуемое значение передаточного числа редуктора iр по формуле (1.38), получим передаточные отношения дифференциальной и замыкающей ступеней редуктора.
Количество зубьев на колесах замыкающей ступени редуктора определяем при следующих условиях. Для исключения подрезания зубьев колес принимаем минимальное число зубьев колес z1мин= z4мин= 17 для получения наименьших размеров редуктора с целью его размещения внутри барабана лебедки. Тогда
z3 = z6 = х · z4 мин. |
(1.44) |
При этом должно быть выполнено условие: z3 – z1 = z6 – z4 должно быть четным чис- |
|
лом. Если условие не выполняется, количество зубьев колес z6 |
следует уменьшить на 1. На |
изменение общего передаточного числа редуктора это существенно не повлияет. |
|
Для обеспечения эффективной работы планетарной передачи без значительного ее ус- |
|
ложнения обычно принимают число сателлитов с равное 3. |
Чтобы обеспечить принципи- |
альную возможность работы и изготовления планетарной передачи, ее необходимо проверить по условиям соседства сателлитов, соосности и сборки.
По условиям соосности центральных зубчатых колес число зубьев сателлитов z2 и z5 должно быть четным:
z5 |
= |
z6 − z4 |
; |
z2 |
= |
z1 − z3 |
. |
|
|
||||||
|
2 |
|
|
2 |
|
Условие соседства сателлитов гарантируется выполнением неравенства
sin |
π |
> |
z5 + 2 |
. |
c |
|
|||
|
|
z4 + z5 |
Условие сборки передачи проверяют отношением
(1.45)
(1.46)
30