
Учебное пособие 1878
.pdf2)они требуют более высокой точности установки валов, чем клиноременные передачи и более сложного ухода и регулирования;
3)передачи требуют установки в картерах;
4)сравнительно быстрое изнашивание шарниров цепи вследствие затруднительного подвода смазочного материала;
5)удлинение цепи из-за износа шарниров, что требует применения натяжных устройств;
6)скорость движения цепи, особенно при малых числах зубьев звездочек, не постоянна.
8.4. Детали цепных передач
Цепь является основным элементом, определяющим ее надежность и долговечность. Цепь состоят из шарнирно соединенных звеньев. Параметры цепей регламентированы стандартами. Характеристикой прочности цепи служит разрушающее усилие, величина которого устанавливается опытным путем на заводе-изготовителе.
Основными геометрическими характеристиками цепи является шаг «t» и ширина «b». По этим размерам и подбирают цепи.
Грузовые цепи (рис. 8.2, а, б) работают при малых скоростях (до 0,25 м/с) и больших нагрузках, их выполняют круглозвенными или простыми пластинчатыми и применяют для подвески, подъема и опускания груза в грузоподъемных устройствах.
Тяговые цепи (рис. 8.2, в) – работают при средних скоростях (до 2…4 м/с). Состоят из пластин простой формы и осей со втулками или без них. Эти цепи имеют большие шаги, т. к. Общая длина цепи значительна и их зубья взаимодействуют со звездочками, габариты которых нежестко ограничены. Применяются для перемещения грузов в транспортирующих устройствах.
Приводные цепи (рис. 8.2, г–л) – работают при значительных скоростях. Они выполняются с малым шагом для умень-
91
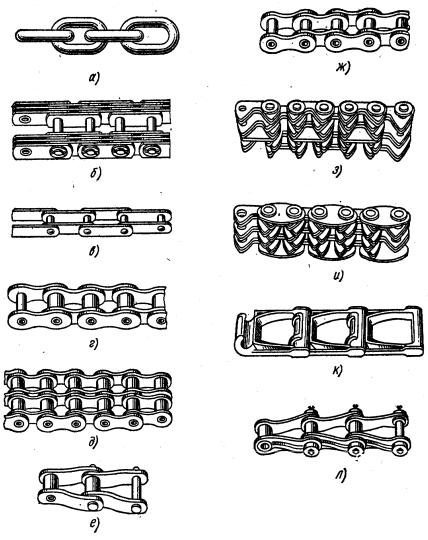
шения динамических нагрузок и с износоустойчивыми шарнирами для обеспечения необходимой долговечности цепи.
В настоящем разделе курса рассматриваются только
приводные цепи.
Рис. 8.2. Основные типы цепей [12]
92
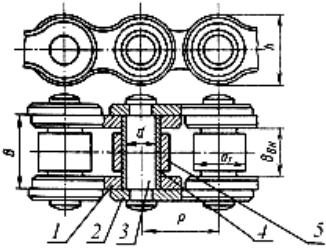
Различают приводные роликовые (рис. 8.3) и втулочные цепи (ГОСТ 13568-75).
Приводная роликовая (ПР) цепь состоит из последовательно чередующихся внутренних (1) и внешних (2) пластин (3 звеньев), шарнирно соединенных между собой. Каждый шарнир состоит из валика (3) диаметром «d», впрессованного во внешние пластины и втулки (4), впрессованной в отверстие внутренних пластин (рис. 8.3). Ролик (5) свободно вращается на втулке и предназначен для уменьшения износа звеньев звездочки. Концы цепи соединяются с помощью разборного дополнительного звена.
Рис. 8.3. Конструкция роликовой цепи [12]
Приводная втулочная (ПВ) цепь отличается от роликовой тем, что не имеет роликов (5). Вес цепи меньше, но износ зубьев звездочки больше за счет скольжения между втулками и зубьями.
Длина цепи кратна числу соединительных пластин. При их чётном числе для соединения цепи в кольцо применяются нормальные соединительные звенья (рис. 8.4, а), а при нечётном специальные переходные звенья (рис. 8.4, б).
93
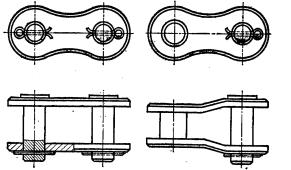
аб
Рис. 8.4. Соединительные звенья роликовой цепи: нормальные (а), переходные (специальные) (б) [12]
Для уменьшения размеров передачи при реализации больших усилий обычно применяют многорядные цепи с малым шагом. Их собирают из тех же элементов, за исключением валиков, длина которых равна общей ширине цепи. Чаще всего применяют 2-х (2ПР) и 3-х (3ПР) – рядные цепи.
Если передача работает в условиях ударной нагрузки, то применяют цепи с изогнутыми пластинами (ПРИ), благодаря чему в цепи возникают деформации изгиба и повышается податливость цепи (рис. 8.2, е). Деформирование пластин способствует гашению ударов.
Для пластин используется сталь 50 и 40Х, для втулок и валиков – сталь 20, 20Г, 20Х и др. при твердости HRC 47…55.
Зубчатая цепь (рис. 8.2, з, и) состоит из набора пластин, каждая из которых имеет по два зуба и впадину между ними для зуба звездочки. Цепи обеспечивают плавную и бесшумную работу. Для предотвращения смещения зубчатой цепи во время работы вдоль оси звездочки устанавливают направляю-
щие пластины.
Крючковые цепи (рис. 8.2, к) составляется из одних звеньев специальной формы без дополнительных деталей. Соединение звеньев производится при боковом перемещении их с наклоном звеньев друг к другу под углом 60°.
94
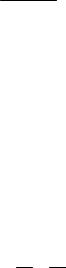
Втулочно-штырьевые цепи (рис. 8.2, л) собираются из чугунных звеньев с помощью стальных штырей, фиксируемых шплинтами. Эти цепи широко применяются в сельскохозяйственном машиностроении.
Зубчатые ремни изготавливают из резины, армированной стальными тросиками (0,3…0,8) мм. Основные размеры выбираются по нормали ОН6-07-5-63 в зависимости от моду-
ля m = 2, 3, 4, 5, 7, 10 мм.
8.5. Основные параметры цепных передач
Скорость цепи с частотой вращения звездочек ограни-
чивается износом цепи. Средняя скорость цепи определяется по формуле:
V Z U t м/с,
60 1000
где Z – число зубьев звездочки; U – частота вращения (об/мин); t – шаг цепи, мм.
Считается, что «U» ограничивается напряжениями при ударе цепи о звездочку. Рекомендуемые значения «n» в зависимости от типа цепи и величины шага «t» приводятся в справочной литературе.
Передаточное число (среднее) определяется из условия равенства средней скорости цепи на звездочках
Z, n, t = Z2·n2·t
U n1 Z2 n2 Z1
95

Передаточное число ограничивается допускаемыми габаритами передачи, углами обхвата и числами зубьев. Обычно U ≤ 7, но в тихоходных передачах U ≤ 10.
Числа зубьев звездочек. Минимальные числа зубьев звездочек отграничиваются износом шарниров, динамическими нагрузками и шумом передач. С уменьшением «Z» возрастают неравномерность скорости цепи и скорость удара цепи о звездочку. Минимальные числа зубьев в силовых передачах роликовыми цепями при максимальных частотах вращения: Zmin = 19…23; при средних Zmin = 17…19; при низких
Zmin = 13…15.
В передачах зубчатыми цепями Zmin увеличивают на 20…30 %. Следует выбирать нечетное число Z (особенно на малой звездочке), что в сочетании с четным числом звеньев цепи способствует ее равномерному износу.
Расстояние между осями звездочек и длина цепи. Ми-
нимальное межосевое расстояние определяется из условия, при котором угол обхвата цепью малой звездочки должен быть δ ≥ 120°.
При U ≤ 3.
amin |
|
De1 De2 |
30...50 , мм |
|
|||
|
2 |
|
При U > 3
amin De1 De2 9 U , мм
2 10
Оптимальное межосевое расстояние
a =(30…50)t
Максимальное межосевое расстояние
аmax = 80t
96
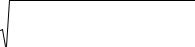
Количество звеньев цепи определяют по предварительно выбранному межосевому расстоянию amin; шагу t и Z1, Z2
Y |
Z Z |
2 |
2a |
Z |
2 |
Z |
2 |
t |
|||
1 |
|
W |
|
|
1 |
|
|
|
|||
|
|
t |
|
2 |
aW |
||||||
2 |
|
|
|
|
|
Первые два члена формулы определяют потребное число звеньев при Z1 = Z2, когда ветви цепи параллельны; Третий член учитывает наклон ветвей.
Число звеньев «Y», полученное по формуле округляется до ближайшего четного числа. Затем находится уточненное межосевое расстояние
|
|
t |
|
Z Z |
2 |
|
|
Z Z |
2 |
2 |
Z |
2 |
Z |
2 |
|||
a |
|
|
Y |
1 |
|
Y |
1 |
|
8 |
|
1 |
|
|
||||
|
2 |
|
|
|
|
2 |
|||||||||||
W |
|
4 |
|
|
|
2 |
|
|
|
|
|||||||
|
|
|
|
|
|
|
|
|
|
|
|
|
|
|
|
|
|
Полученное значение «а» необходимо уменьшить на (0,002…0,004)аW для обеспечения провисания цепи.
Шаг цепи является основным параметром цепной передачи. Цепи с большими шагами имеют большую несущую способность, но допускают меньшие частоты вращения, работают с большими динамическими нагрузками и шумом.
97
9. ОСИ И ВАЛЫ
9.1. Общие сведения
Вращающиеся детали (шкивы, зубчатые колеса) машин устанавливаются на осях и валах, которые обеспечивают постоянное положение их оси вращения.
Оси – детали машин, которые служат для поддержания вращающихся вместе с ними или на них различных деталей. Вращение оси вместе с установленной на ней деталью производится относительно ее опор, называемых подшипниками. Оси не передают крутящего момента. В любом случае оси работают только на изгиб.
Валы – детали машин, которые не только поддерживают вращающиеся детали, но и передают по всей длине или на отдельных его участках крутящий момент. В связи с тем, что передача крутящего момента связана с возникновением сил, передающихся на валы (например, сил на зубьях зубчатых колес, сил натяжения ремней и др.), то они подвержены дейст-
вию не только крутящих моментов, но также поперечных сил и изгибающих моментов.
Некоторые валы не поддерживают вращающиеся детали (карданные валы автомобилей, валки прокатных станов и др.) и поэтому работают только на кручение.
9.2.Проектный расчет валов и осей
9.2.1.Составление расчетных схем
Проектный расчет валов и осей начинается с установления расчетной схемы и определения внешних нагрузок.
Валы и оси рассматриваются как балки, лежащие на шарнирных опорах. Прежде всего, должны быть установлены расстояния между опорами и места расположения насаживаемых на вал или ось деталей.
98

Для валов, вращающихся в радиальных подшипниках качения, установленных в опорах по одному, центр опорного шарнира совмещается с серединой подшипника.
Силы на валы (оси) передаются через насаженные на них детали: шкивы, звездочки, зубчатые колёса, блоки и т.д.
При этом принимают, что насаженные на вал (ось) детали передают силы и моменты валу (оси) на середине длины посадочной поверхности. Величина и направление действующих нагрузок определяются характером работы и расположением сидящих на валу или оси деталей. Нагрузками от собственного веса вала (оси) и расположенных на нем деталей в проектном расчете обычно пренебрегают, хотя принципиально их учёт и не представляет трудностей.
9.2.2. Расчёт опасного сечения
Для расчета валов и осей необходимо вычислить изгибающие и крутящие моменты в опасных сечениях. Поскольку действующие на вал нагрузки в общем случае расположены в различных плоскостях, их следует разложить на составляющие, лежащие в двух заранее выбранных взаимно перпендикулярных плоскостях. Причем за одну из таких плоскостей целесообразно выбрать плоскость, в которой уже лежат несколько или хотя бы одна из действующих сил. После этого можно найти составляющие реакции опор и построить эпюры изгибающих и крутящего моментов.
Поясним это на примере расчёта промежуточного вала двухступенчатого трехосного редуктора. На рисунке представлены аксонометрическая схема этого вала и действую-
щих на него нагрузок схема нагружения и эпюры соответствующих моментов (рис. 9.1).
Для определения результирующего изгибающего момента моменты во взаимно перпендикулярных плоскостях складываются геометрически:
M и Мх2 Му2 .
99
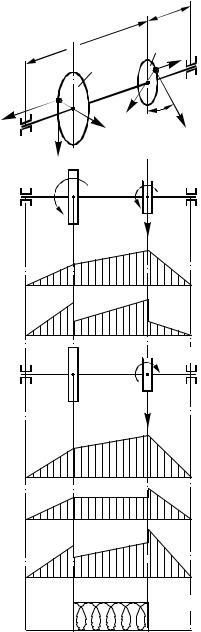
l2
l1
d1
Pa1
Pr1
P1
Mu1
Pr1
От сил
Суммарная
Mx
Pr1
От сил
Суммарная
My
Суммарная
Mu
Крутящий
момент
Mкр
|
l3 |
d2 |
Pa2 |
|
|
Pr2 |
P2 |
Pr2 cos
Mu2 cos
Mu1=(Pa1 d1)/2
Mu2 cos =(Pa2 d2 cos )/2
P2 sin
Mu2 sin =(P2 d2 sin )/2
P2 cos
Pr2 sin
Mкр=(P1 d1)/2=(P2 d2)/2
Рис. 9.1
100